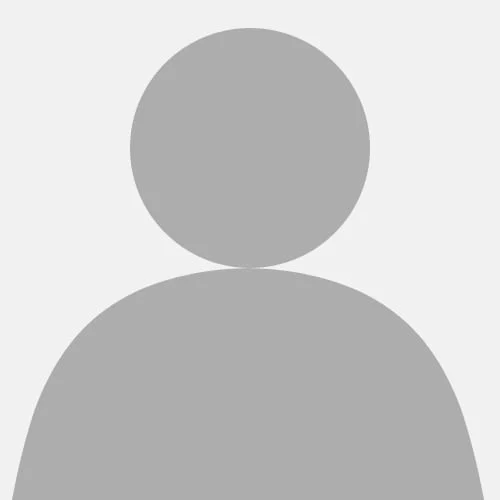
Matthew Worthington
This paper’s focus is the 5S process, incorporating an industry example of how it positively affects business change management and continuous improvement. A Lean Manufacturing approach, 5S was created to shape workplace management. Originating in Japan, it includes 5 steps: sort, set, shine, standardise, and sustain. The benefits of 5S implementation in a manufacturing business focus on everyday work with a holistic approach that brings order both in the material environment and the ethical values that support it. This work will investigate the wider aspects of engineering management practice before analysing specific questions on manufacturing process improvement, particularly focussing on the impact 5S has on workshop organisation, changing operator and technician culture. This is framed in an industry relevant project. The project is entitled Soffit Plate Project, a batch production project where a quantity of 282 Soffit plates are assembled with over 100 components in each, totalling thousands of components that are managed throughout the contract with added paperwork and manufacturing process management requirements. Conclusions show that a normal approach is insufficient or unsustainable for profitability. 5S should be implemented from the beginning, which is the subject of the discussion along with impacts on engineering business management.
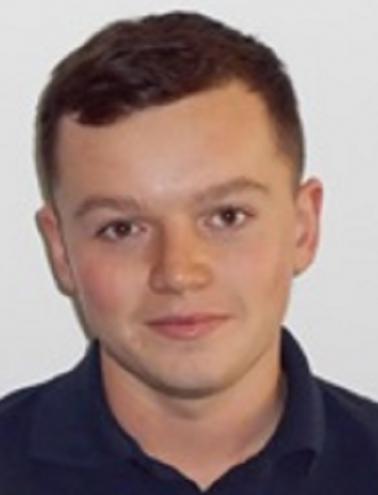
Matthew Worthington
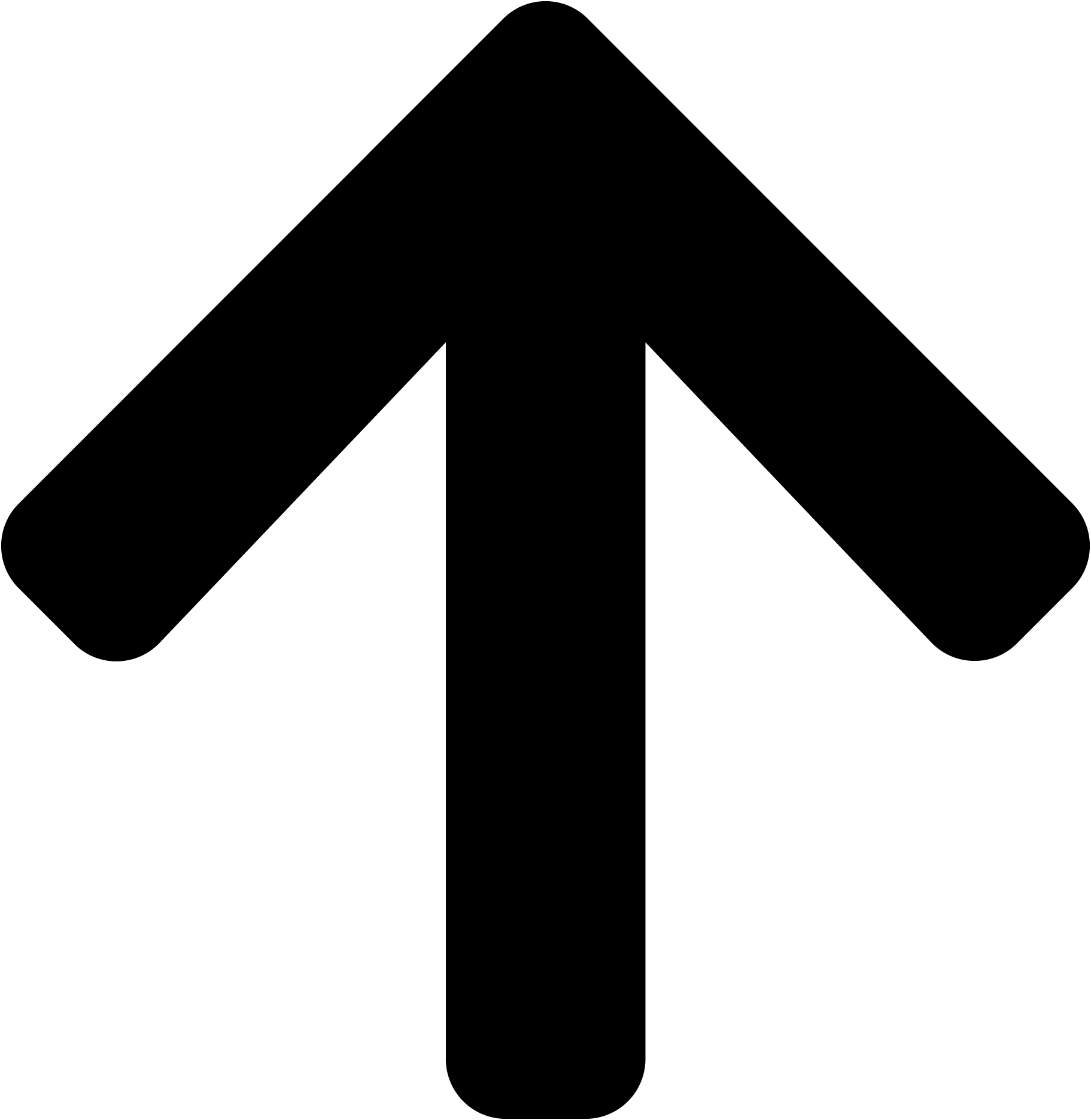
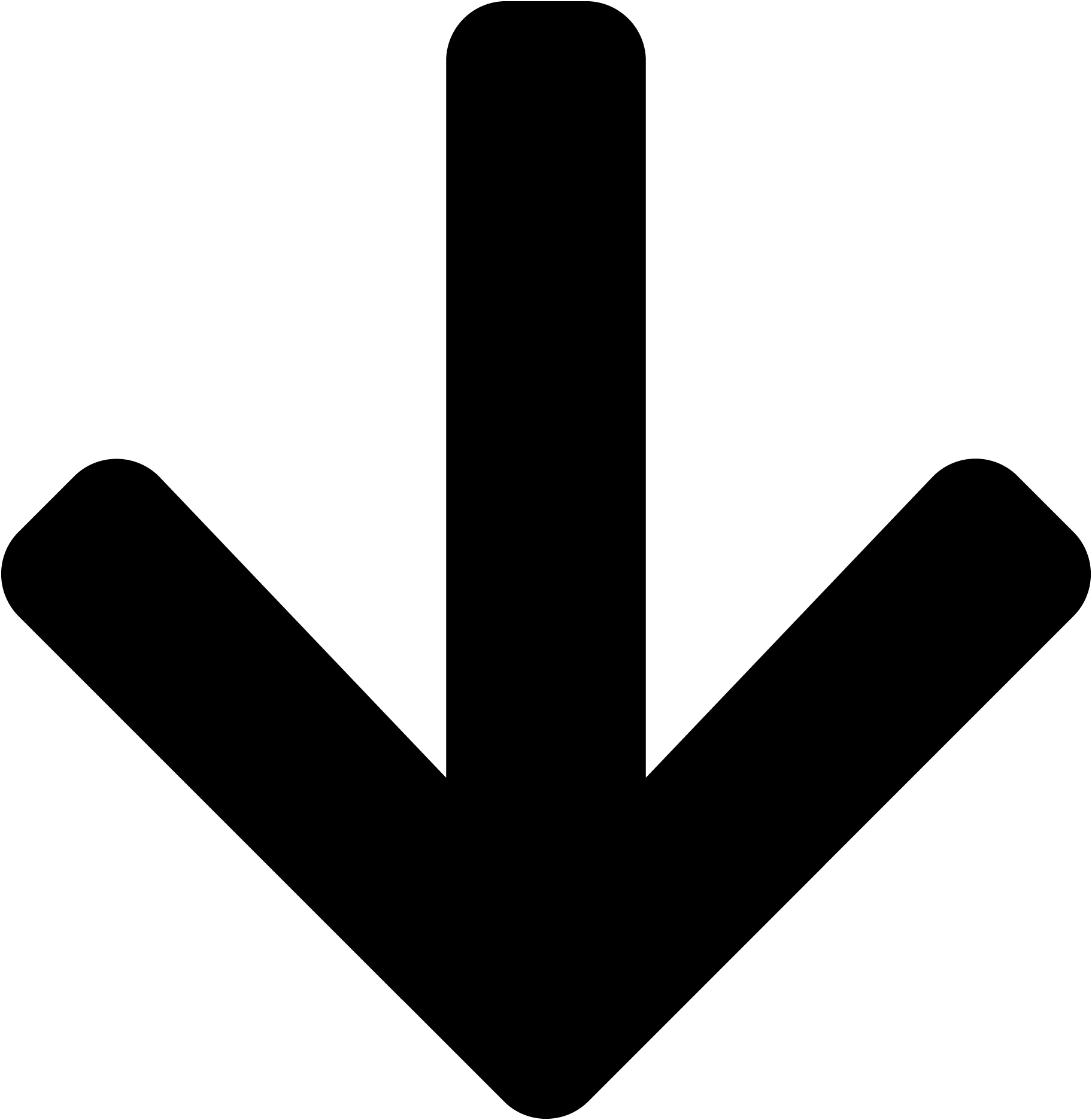
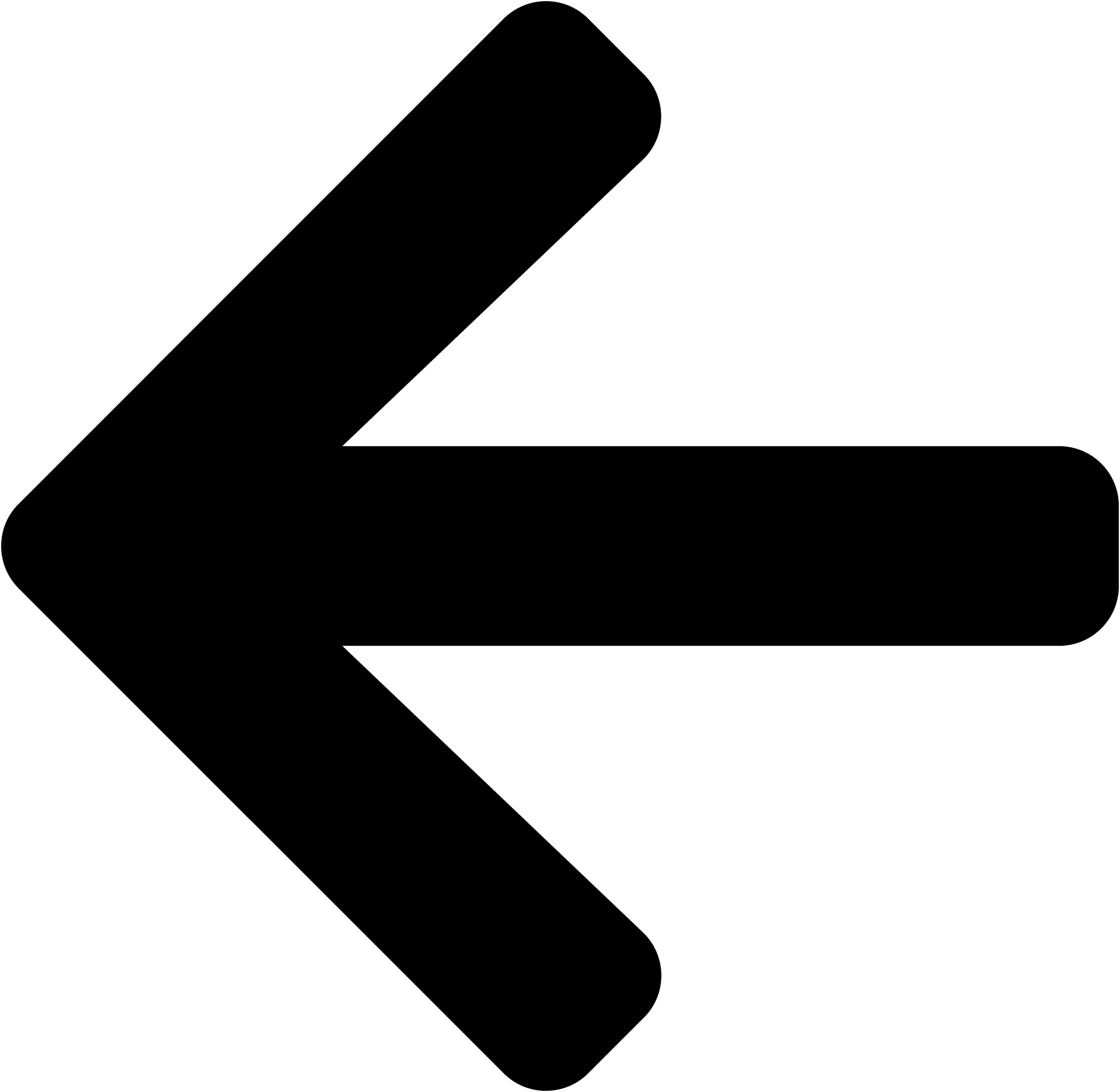
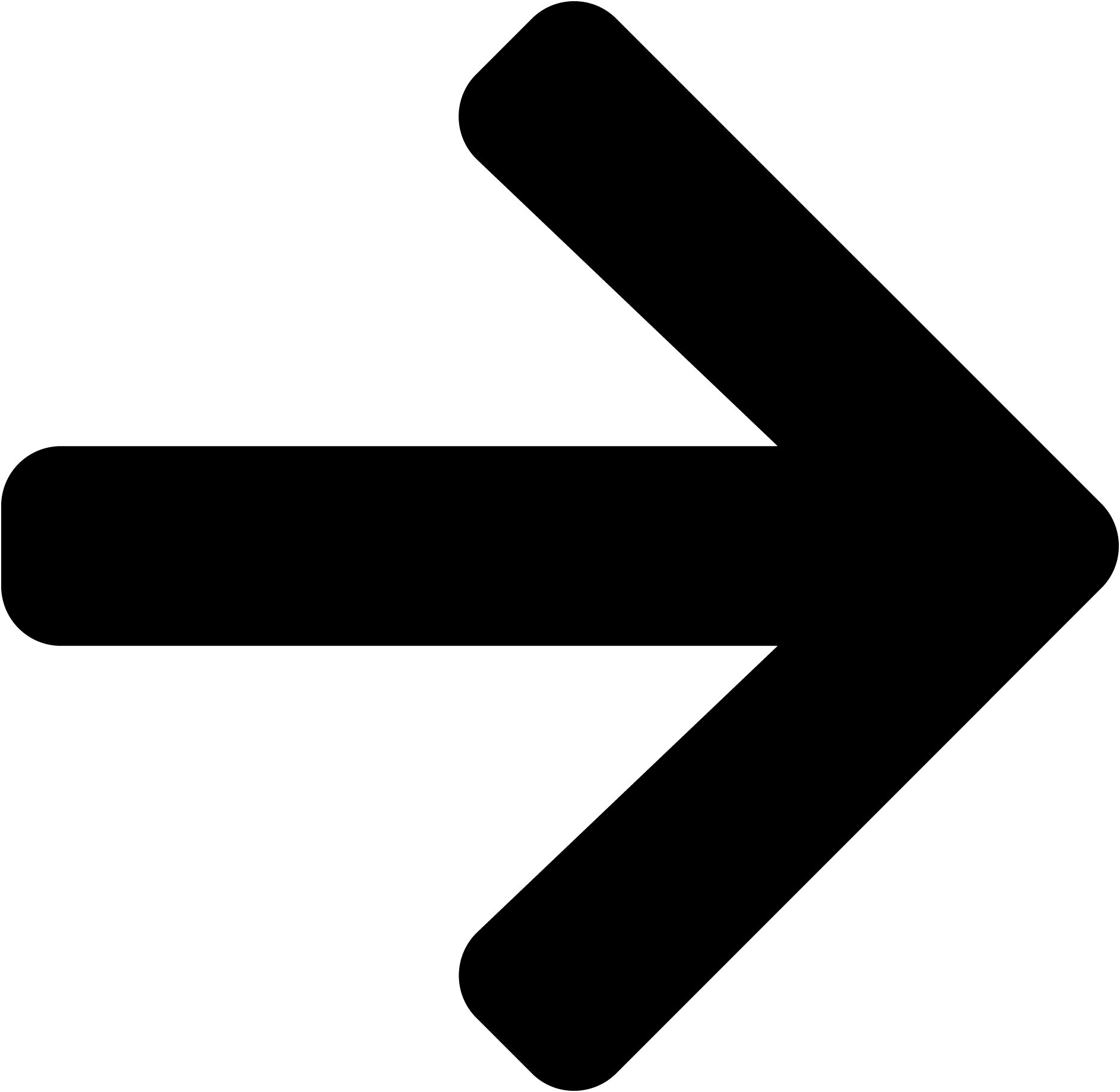
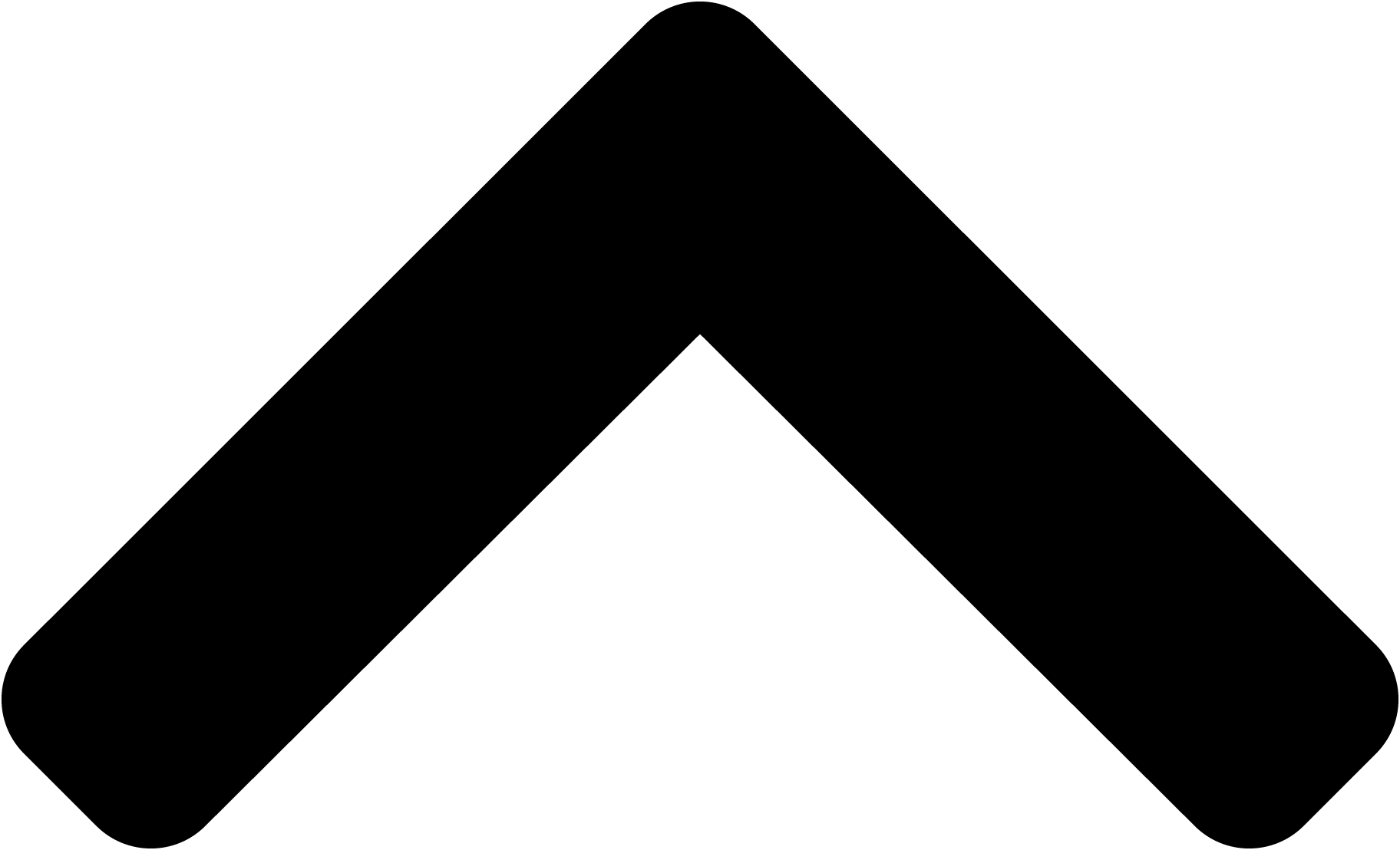

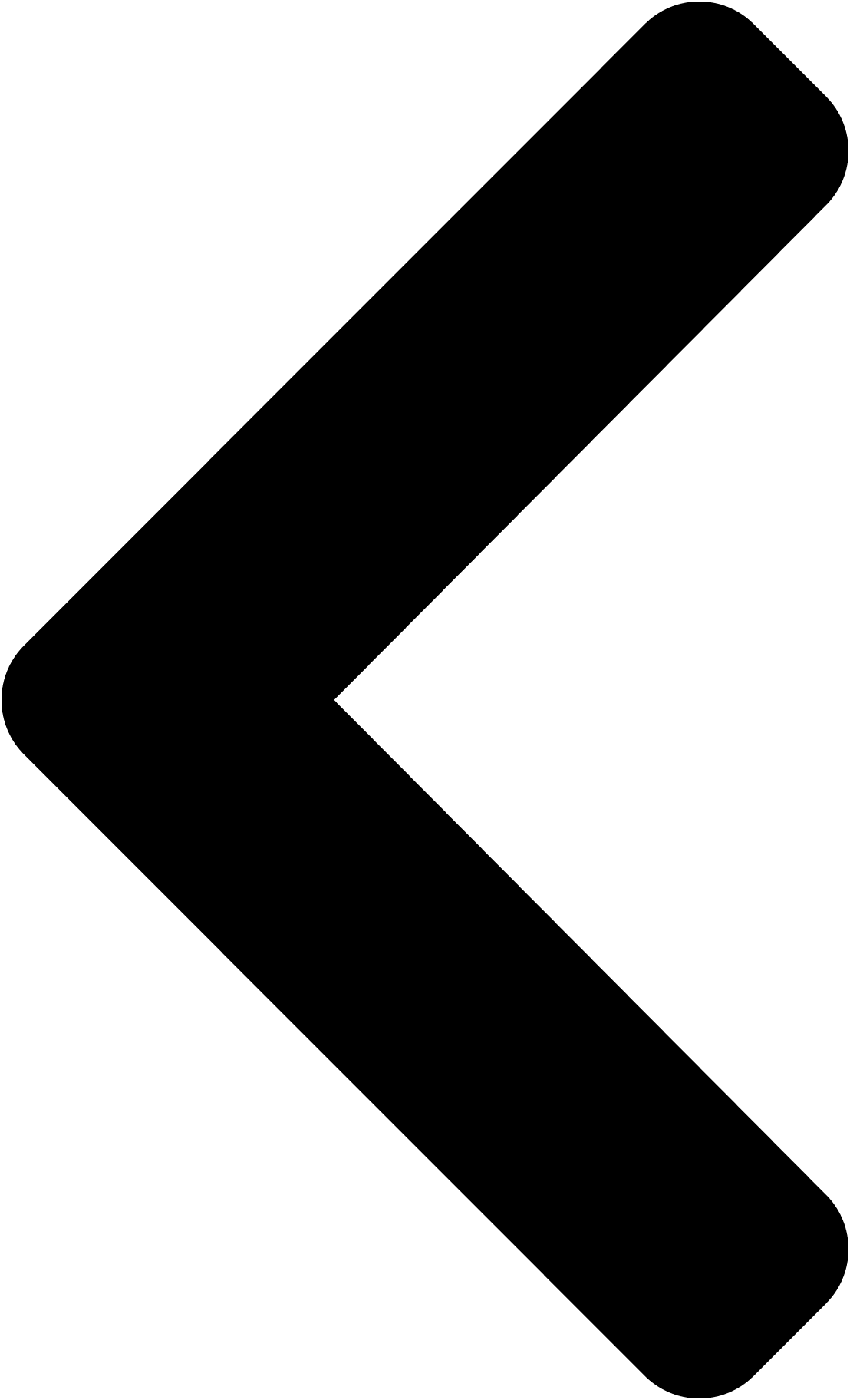
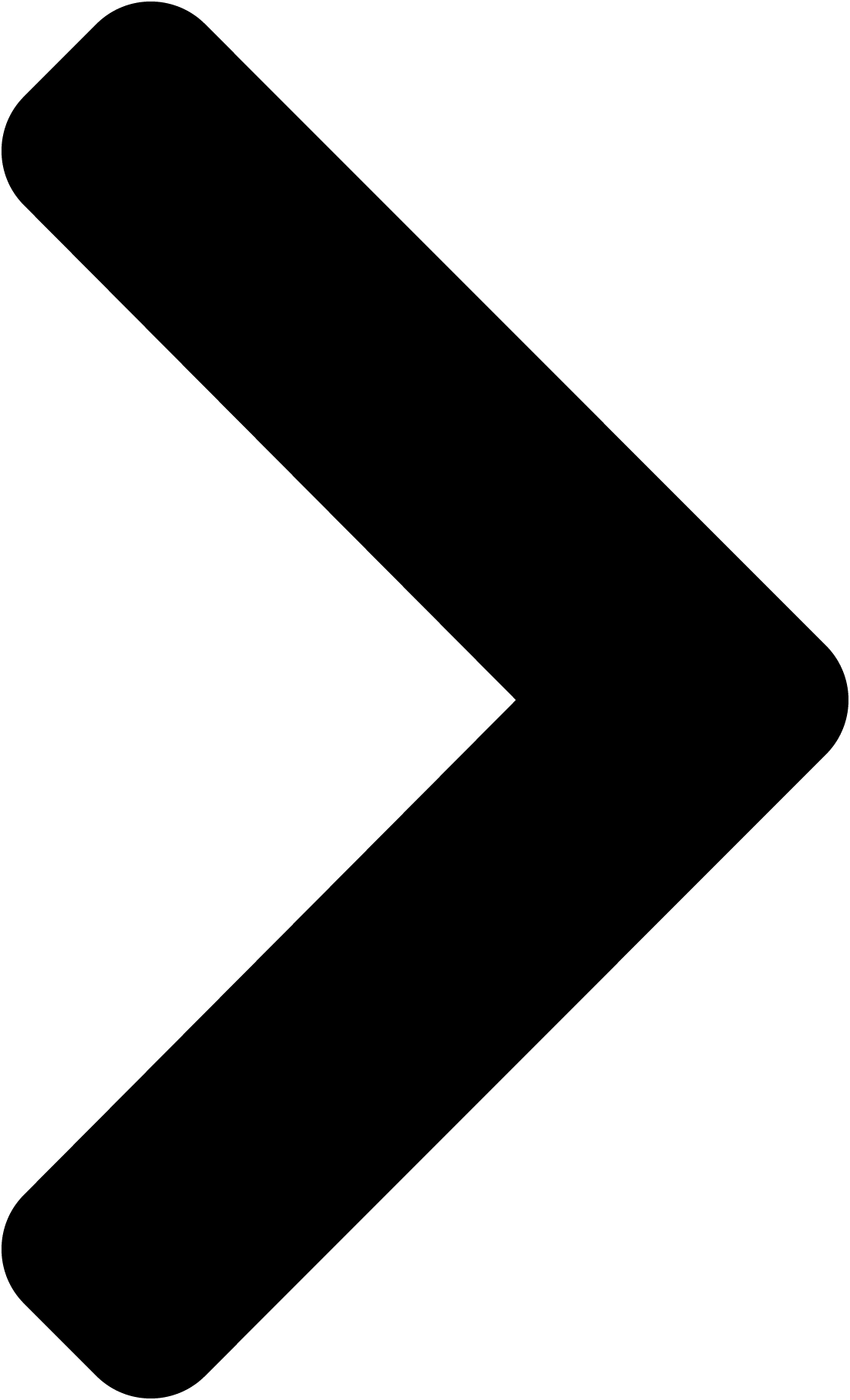
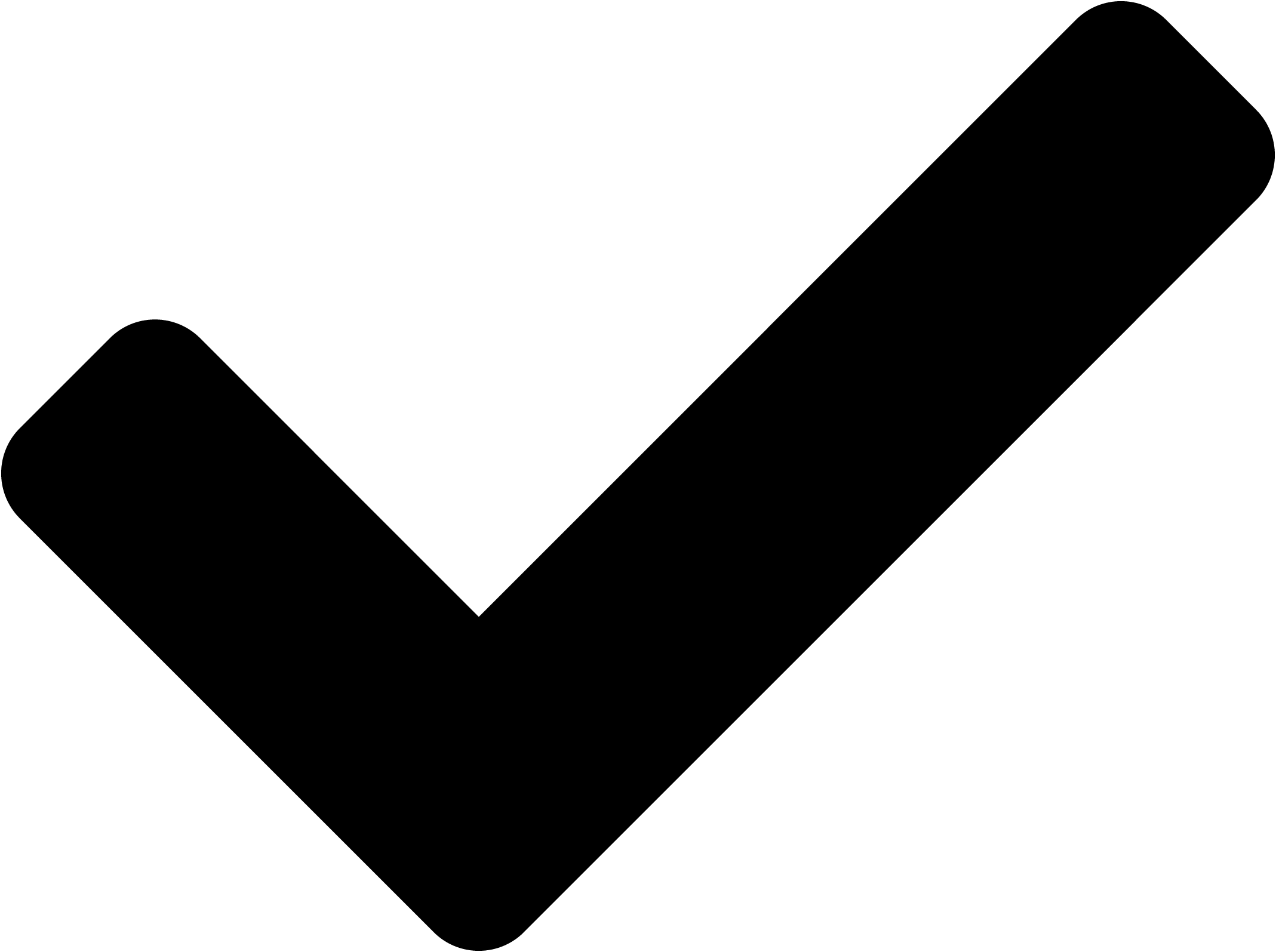
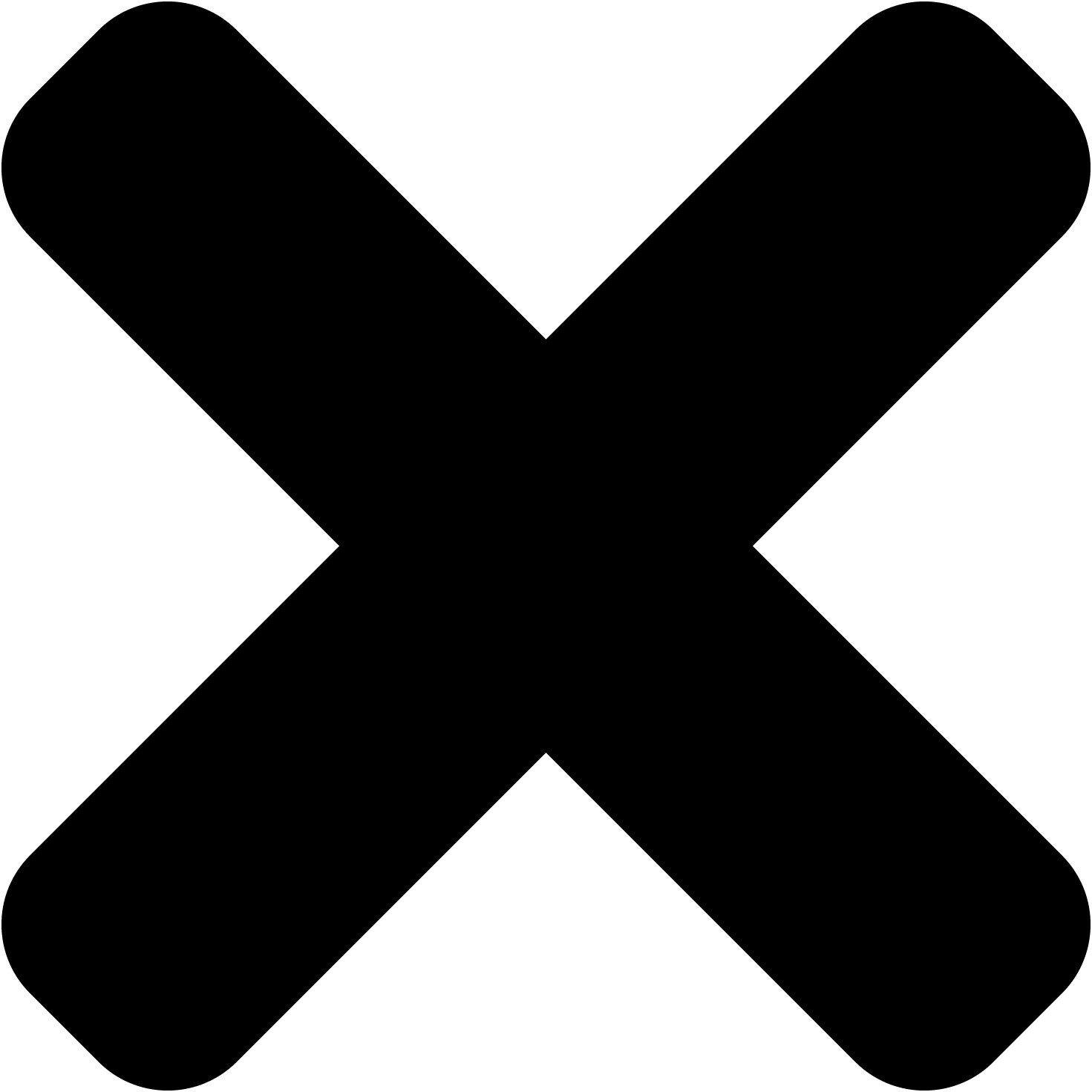
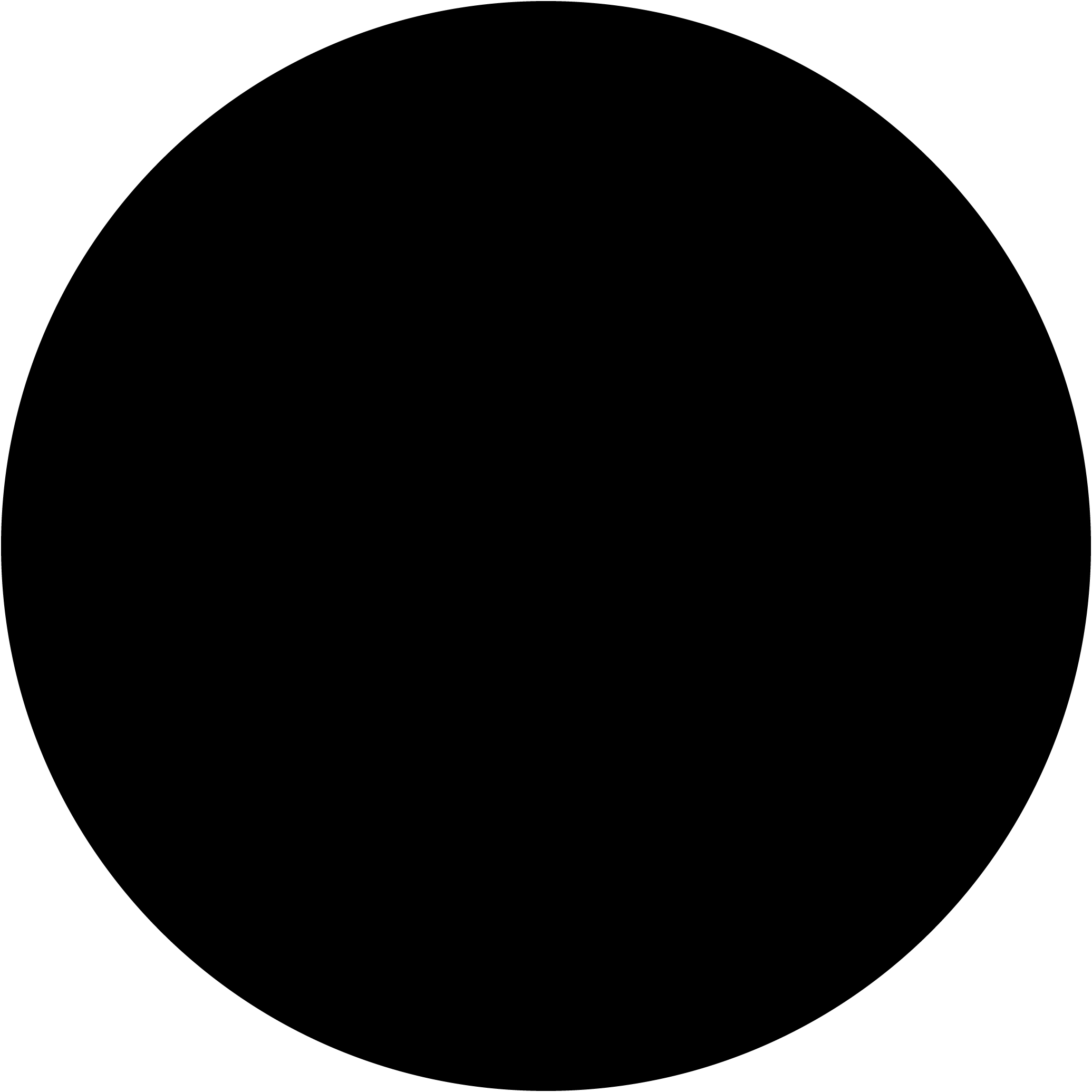
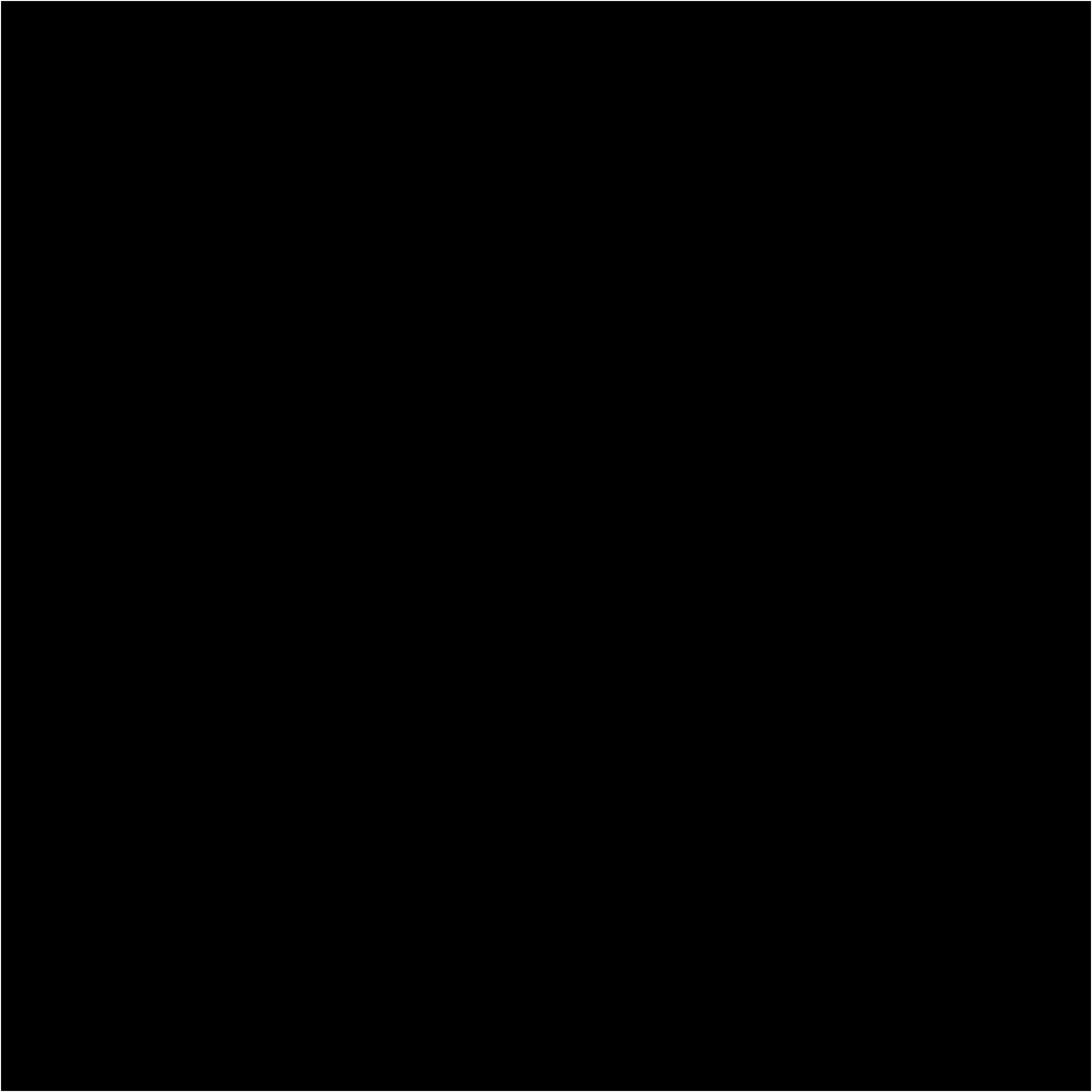
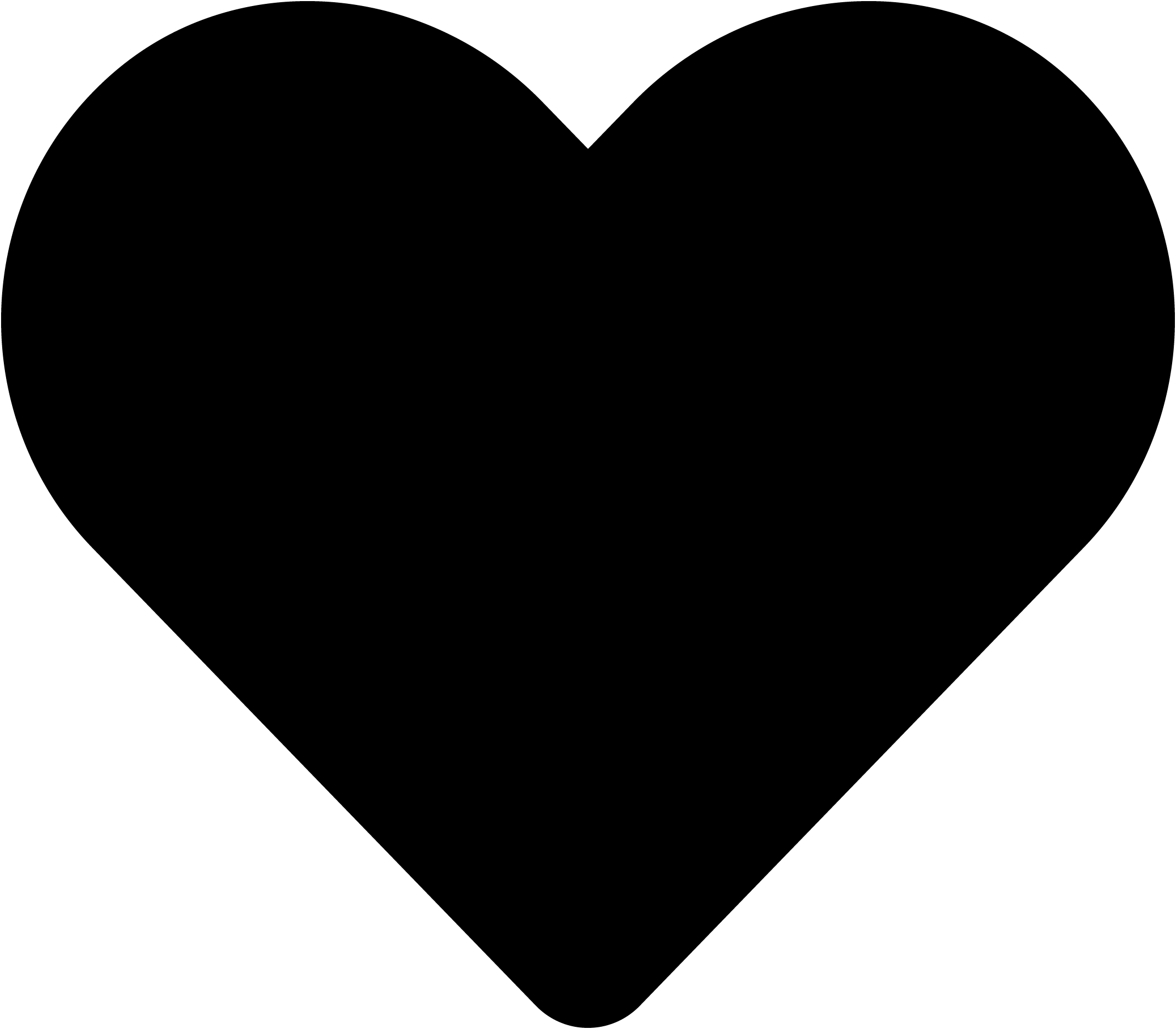

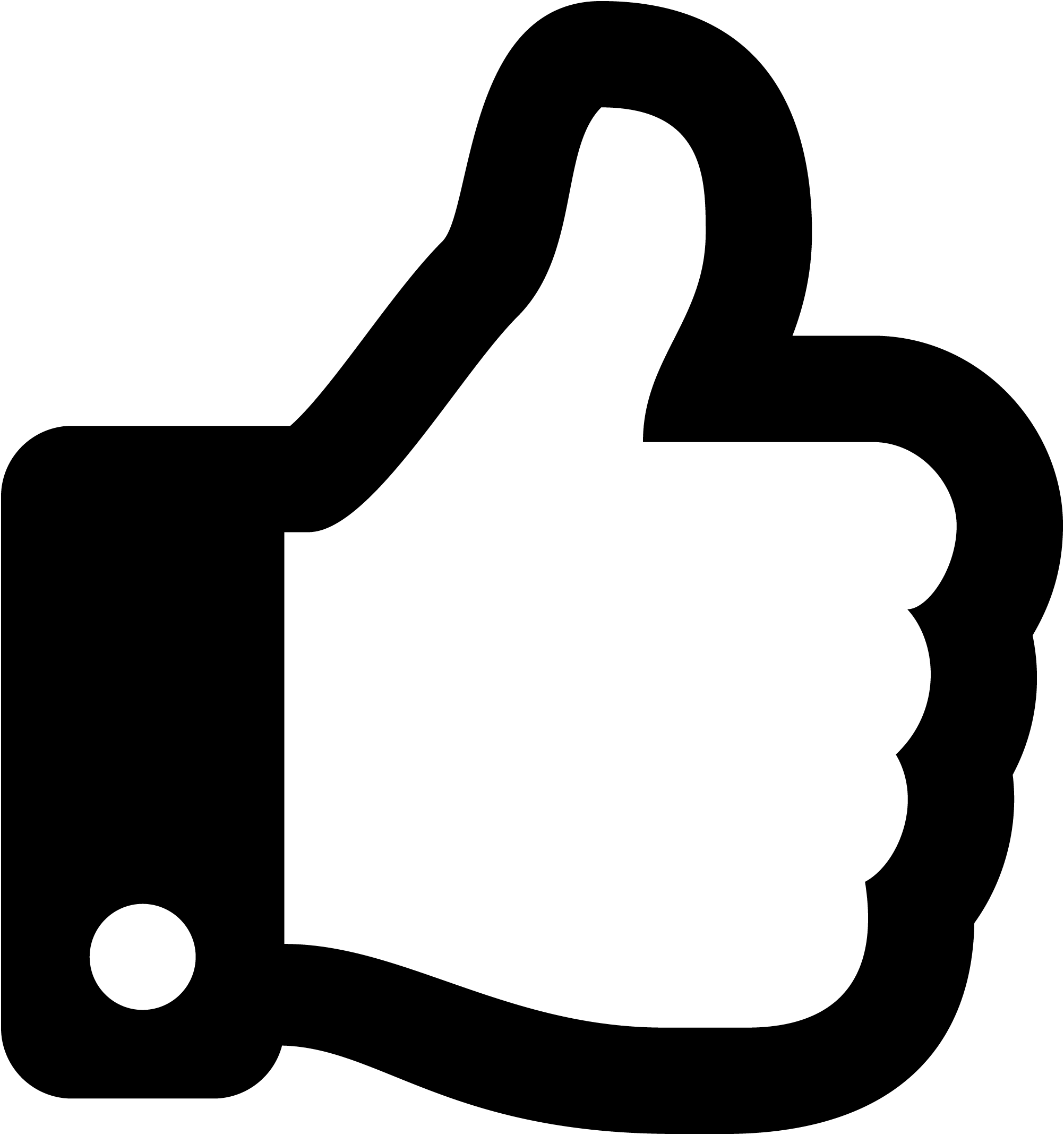
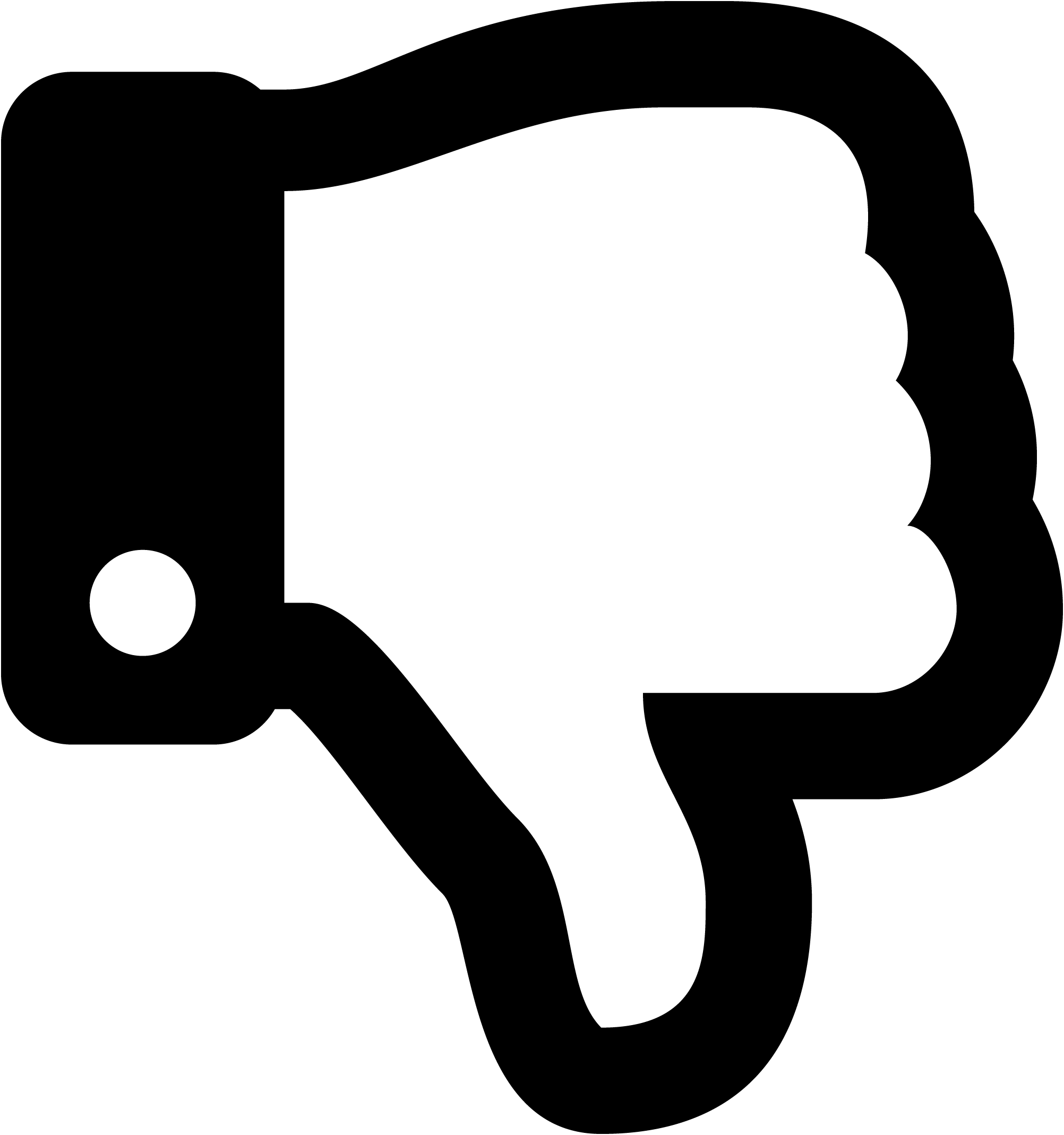
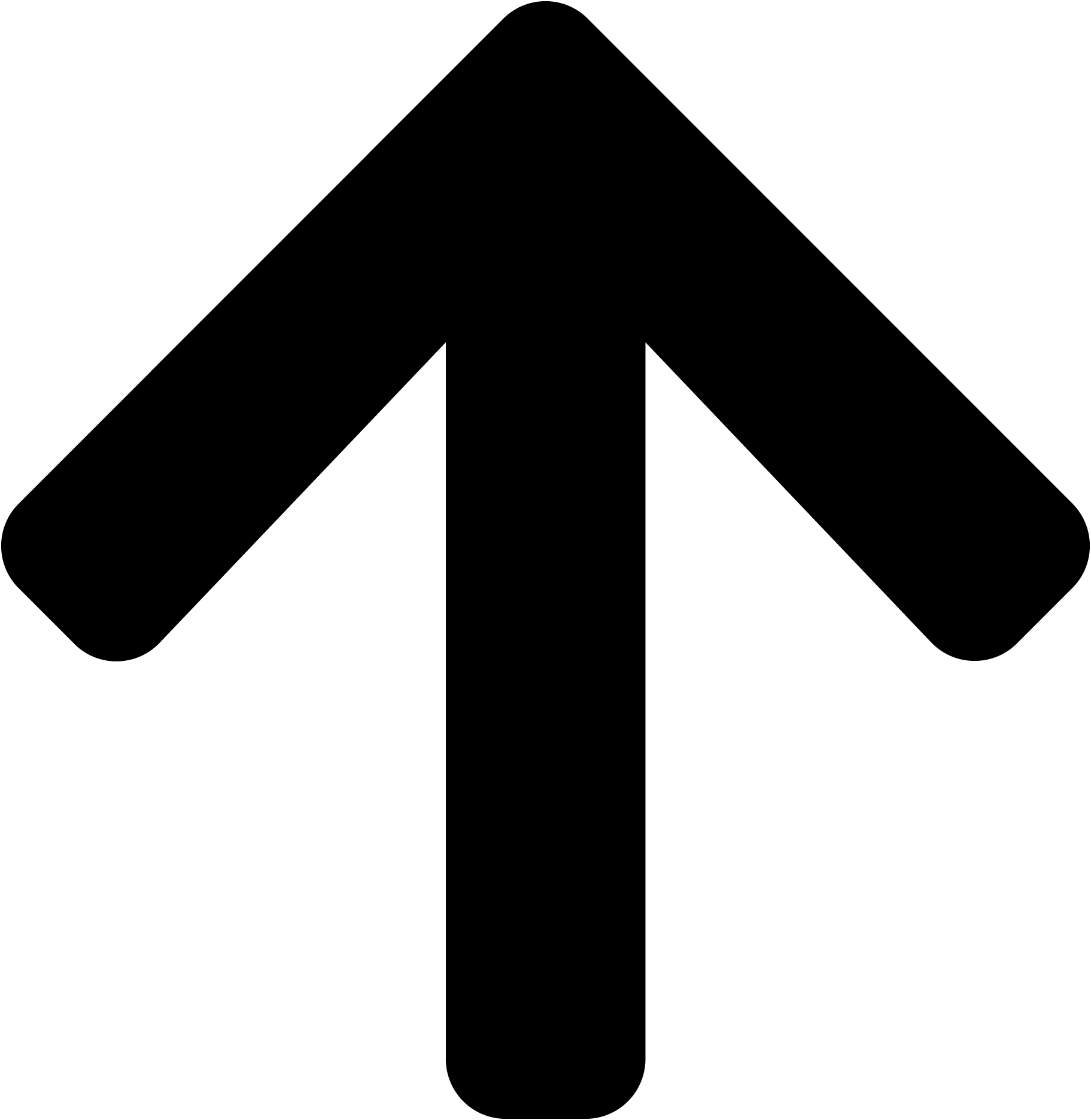
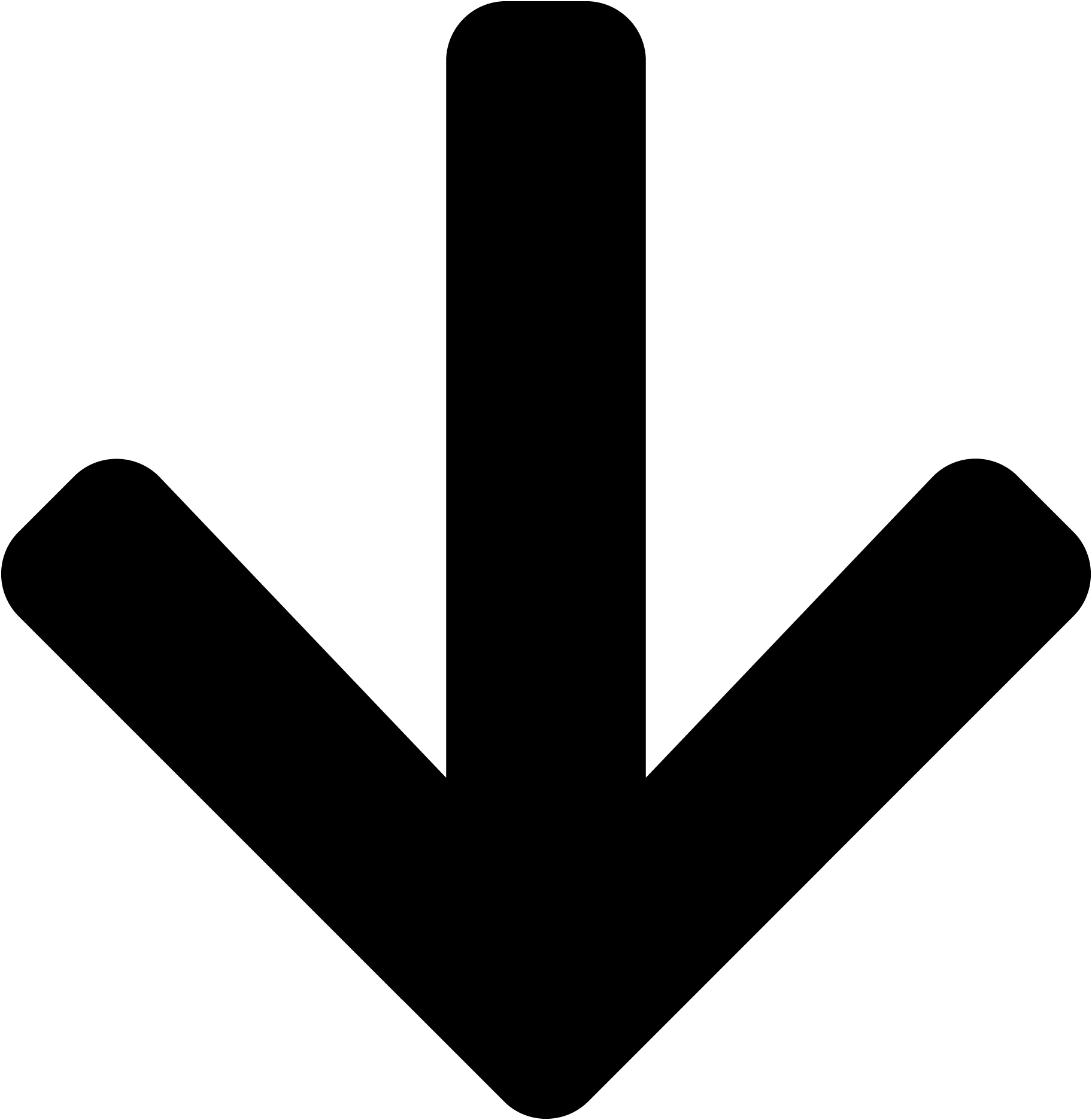
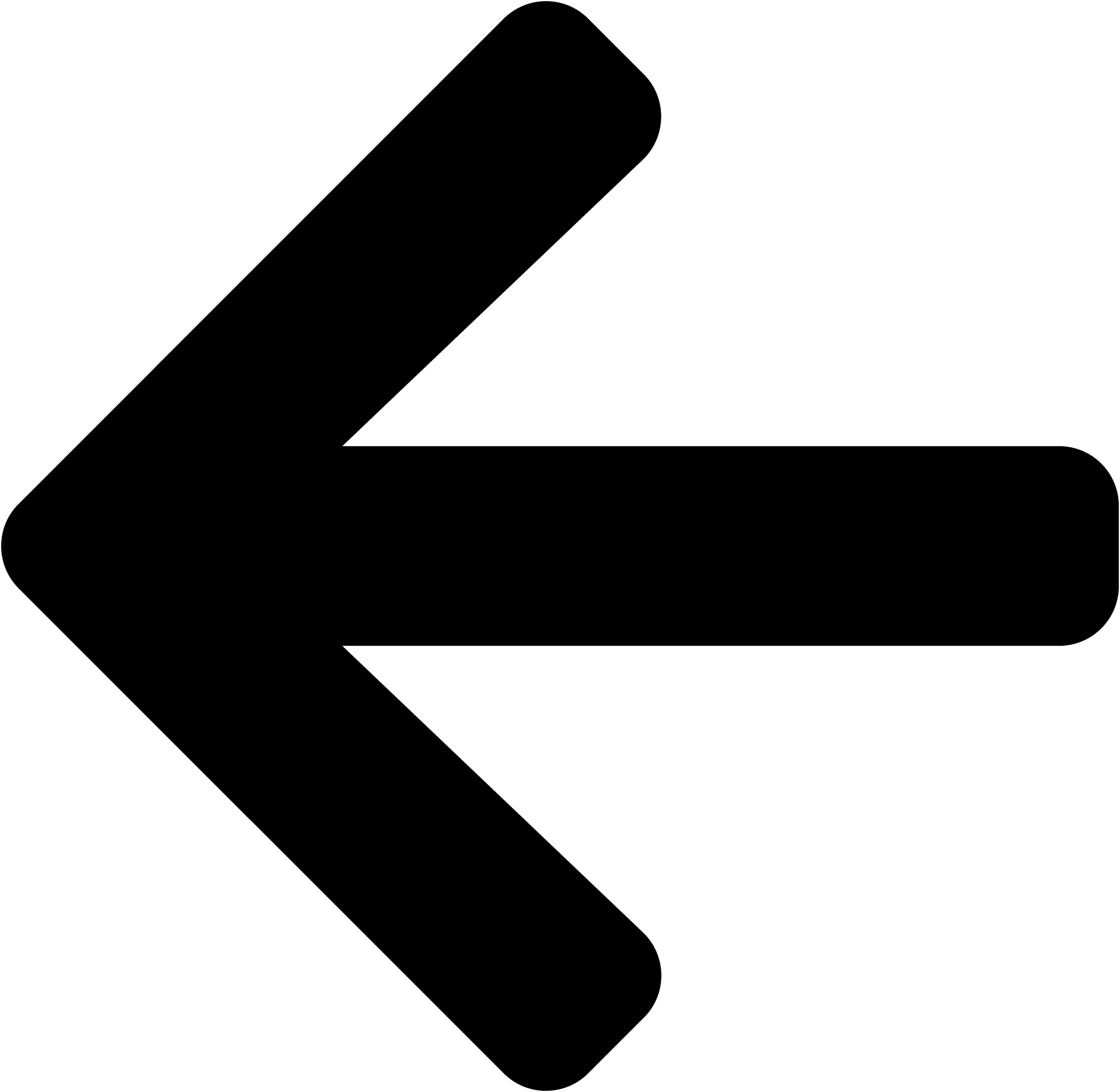
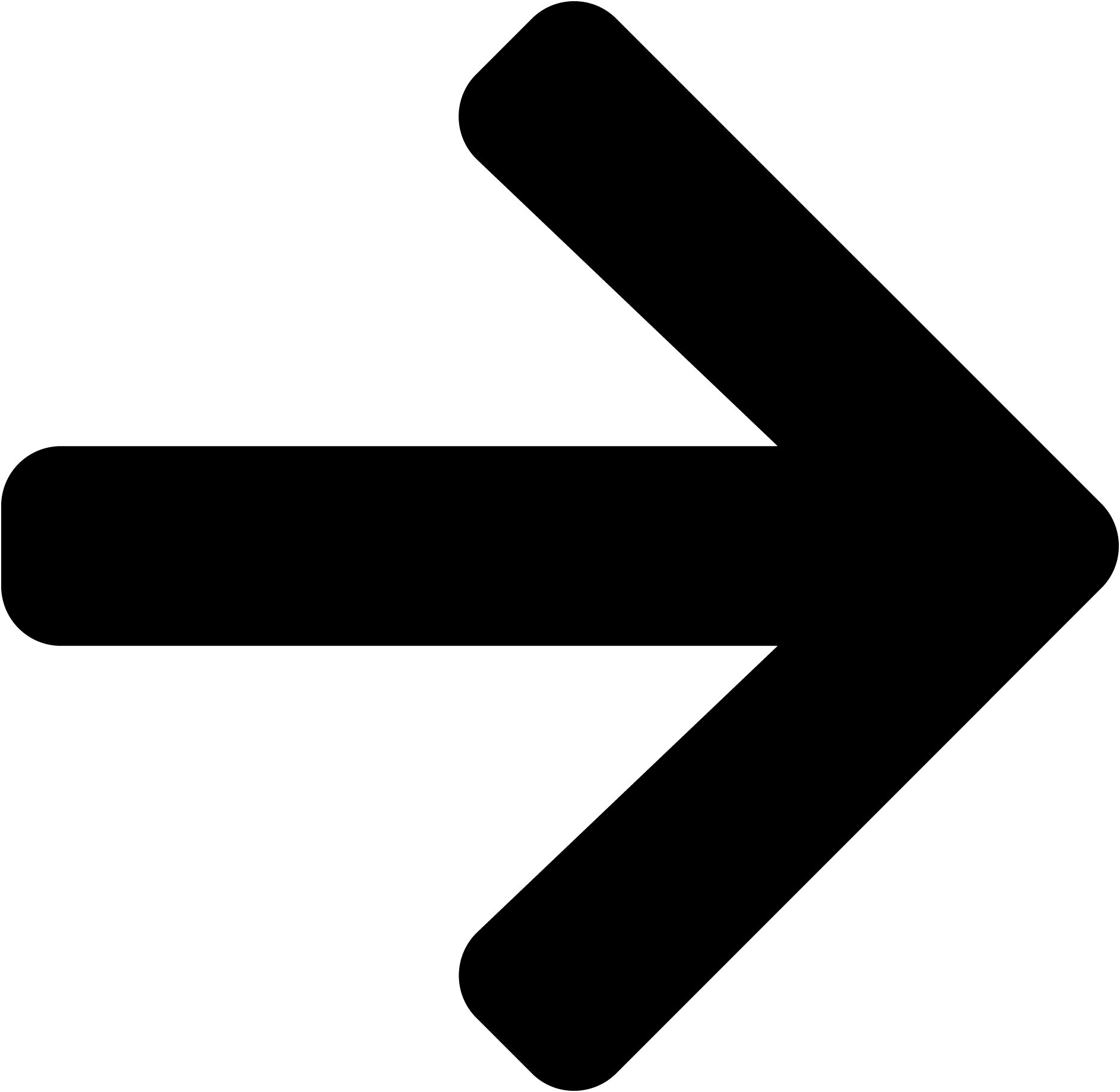
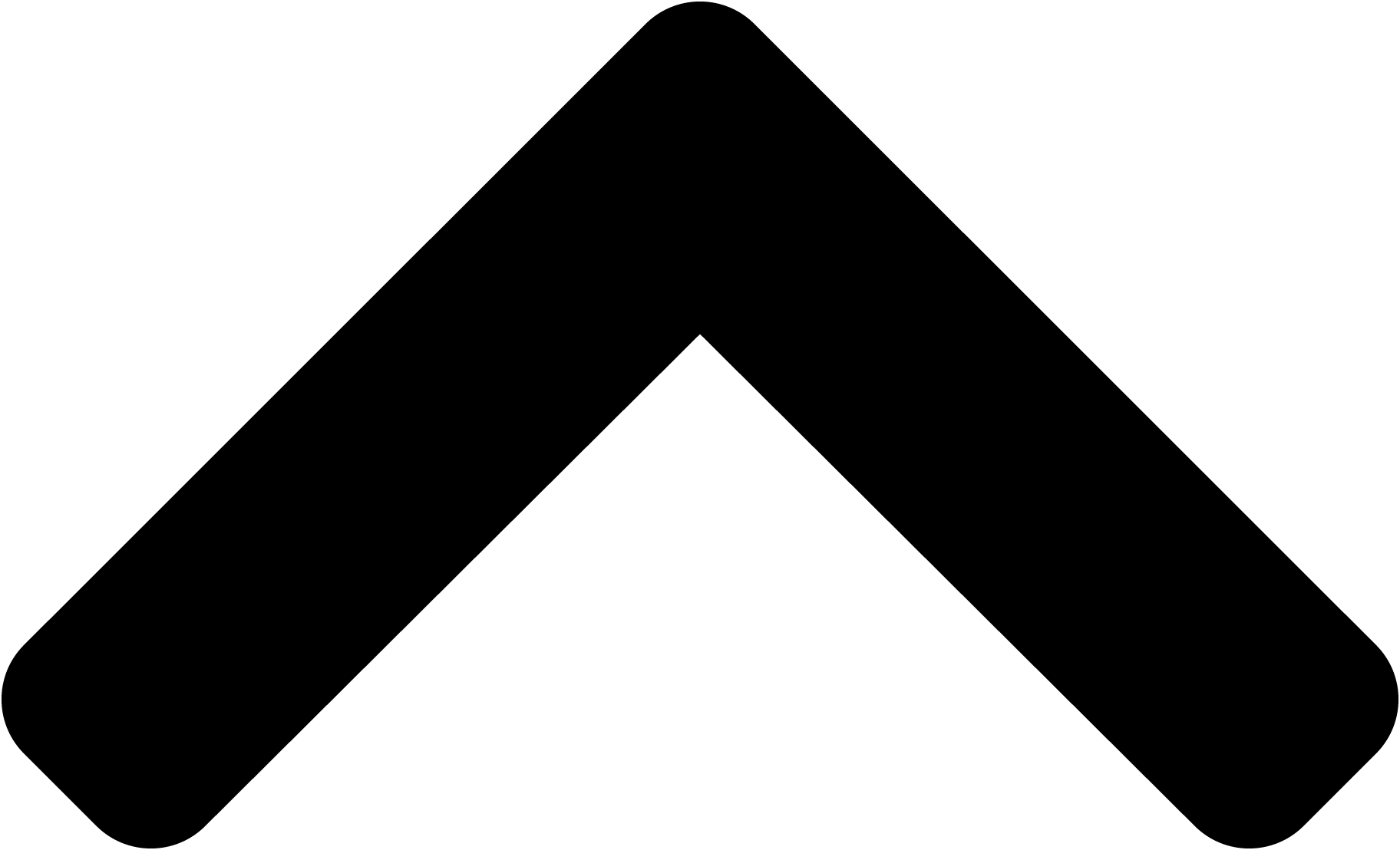

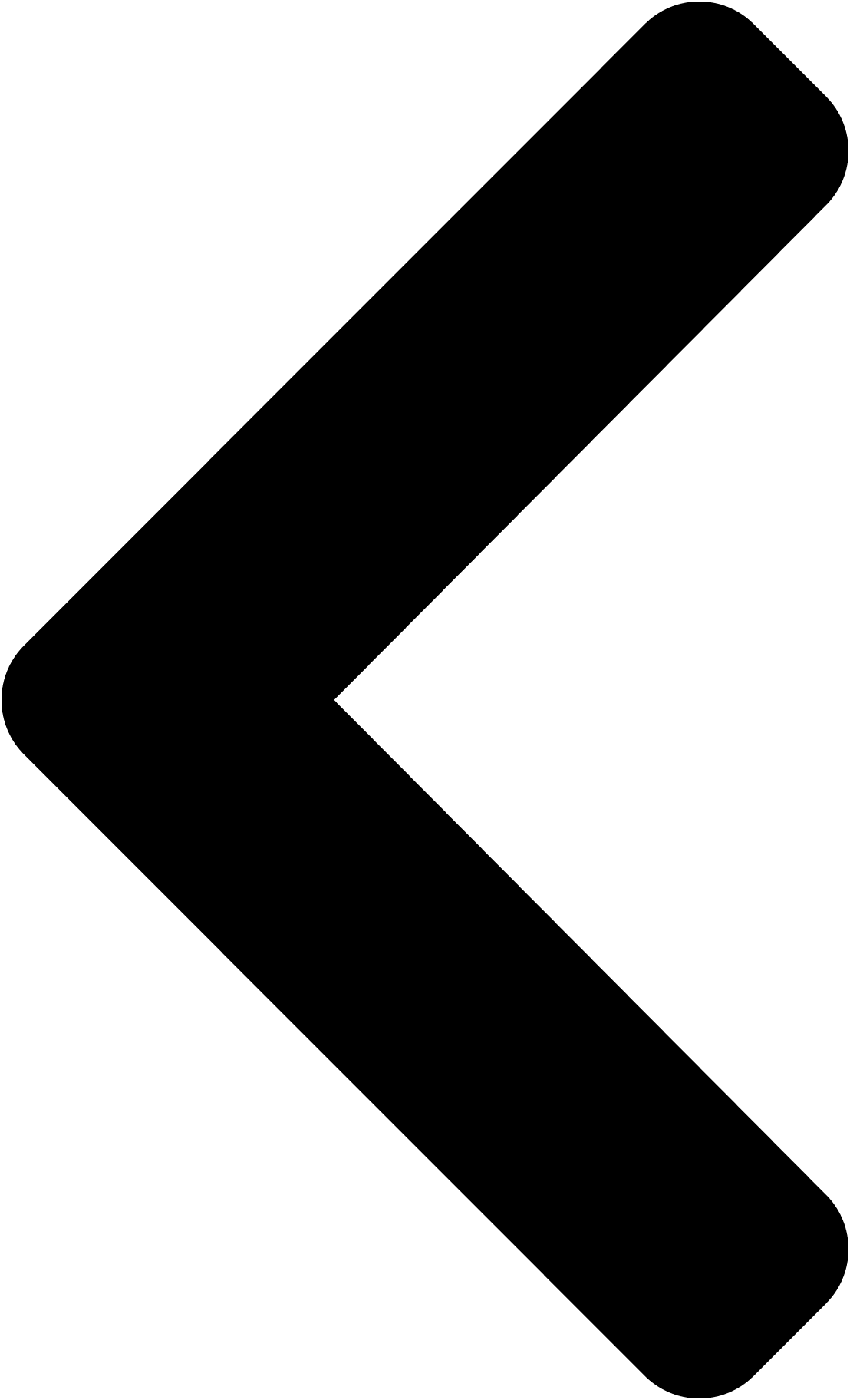
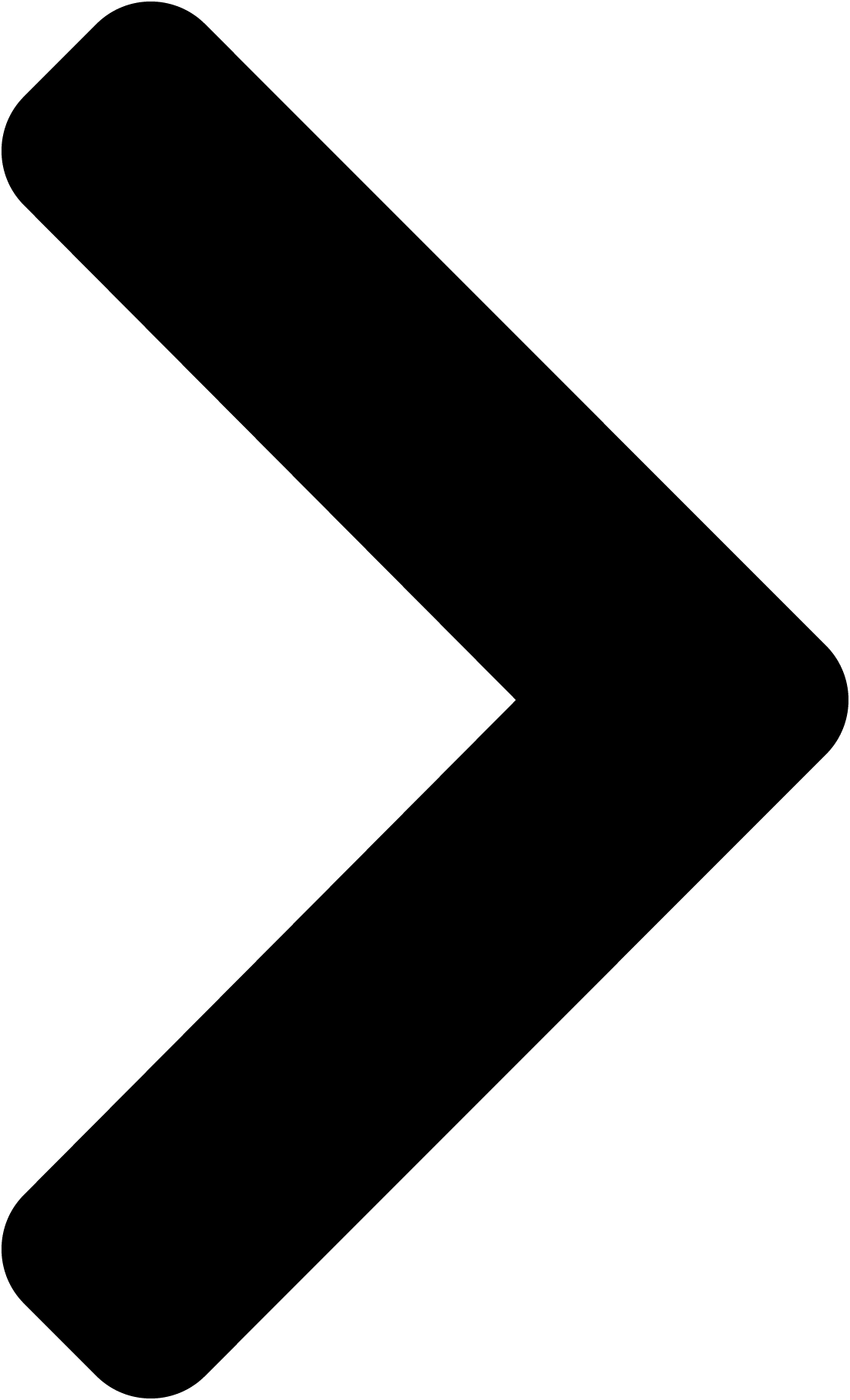
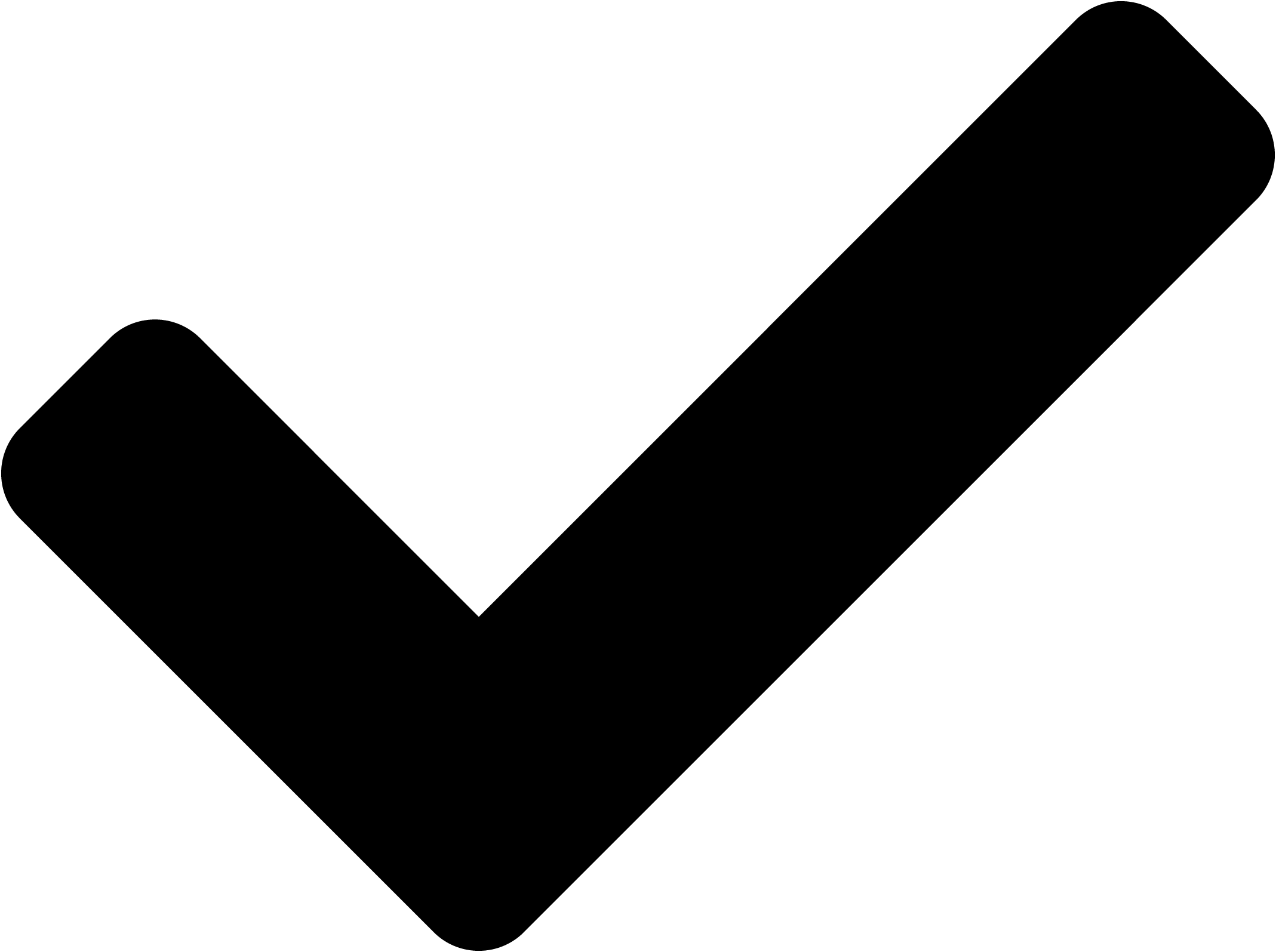
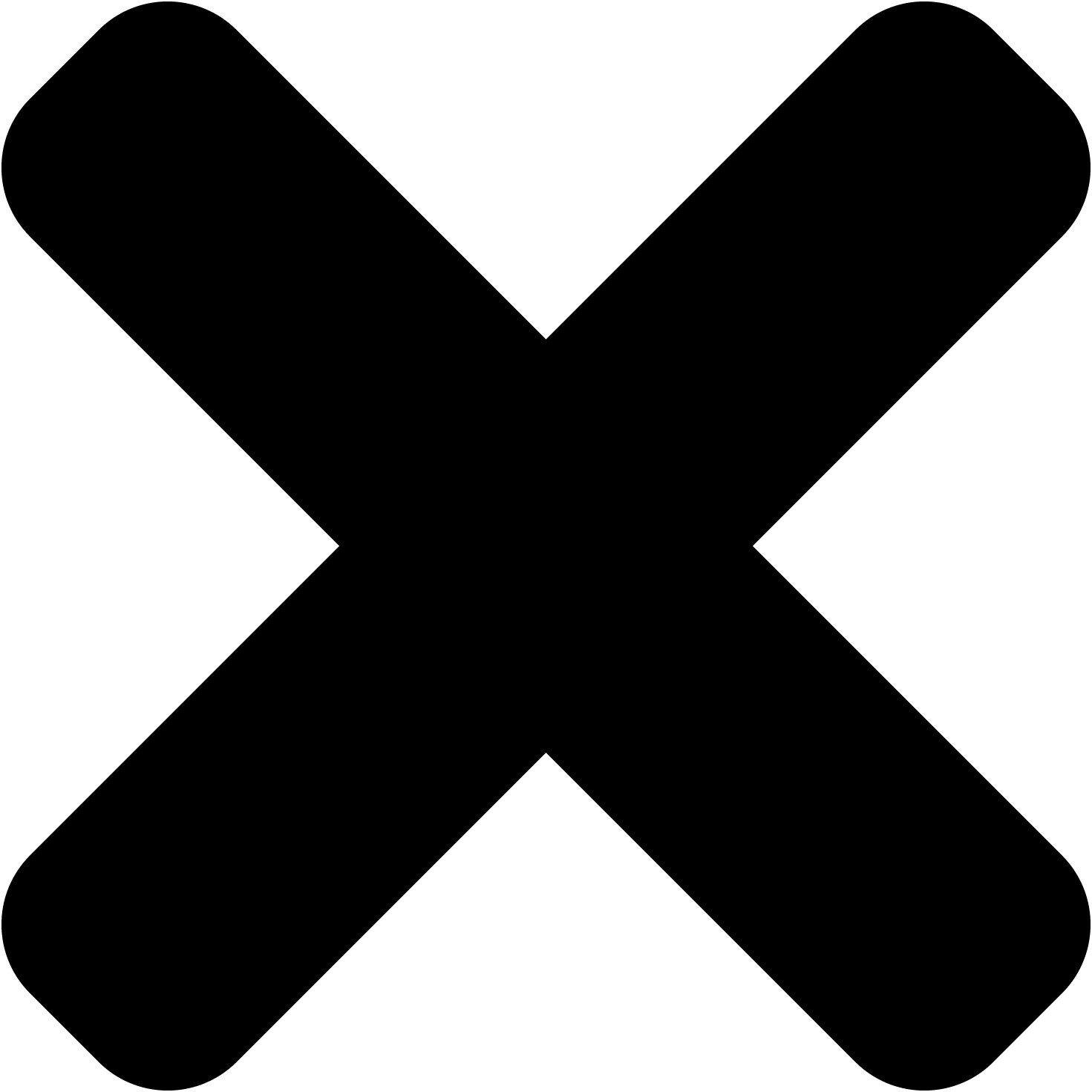
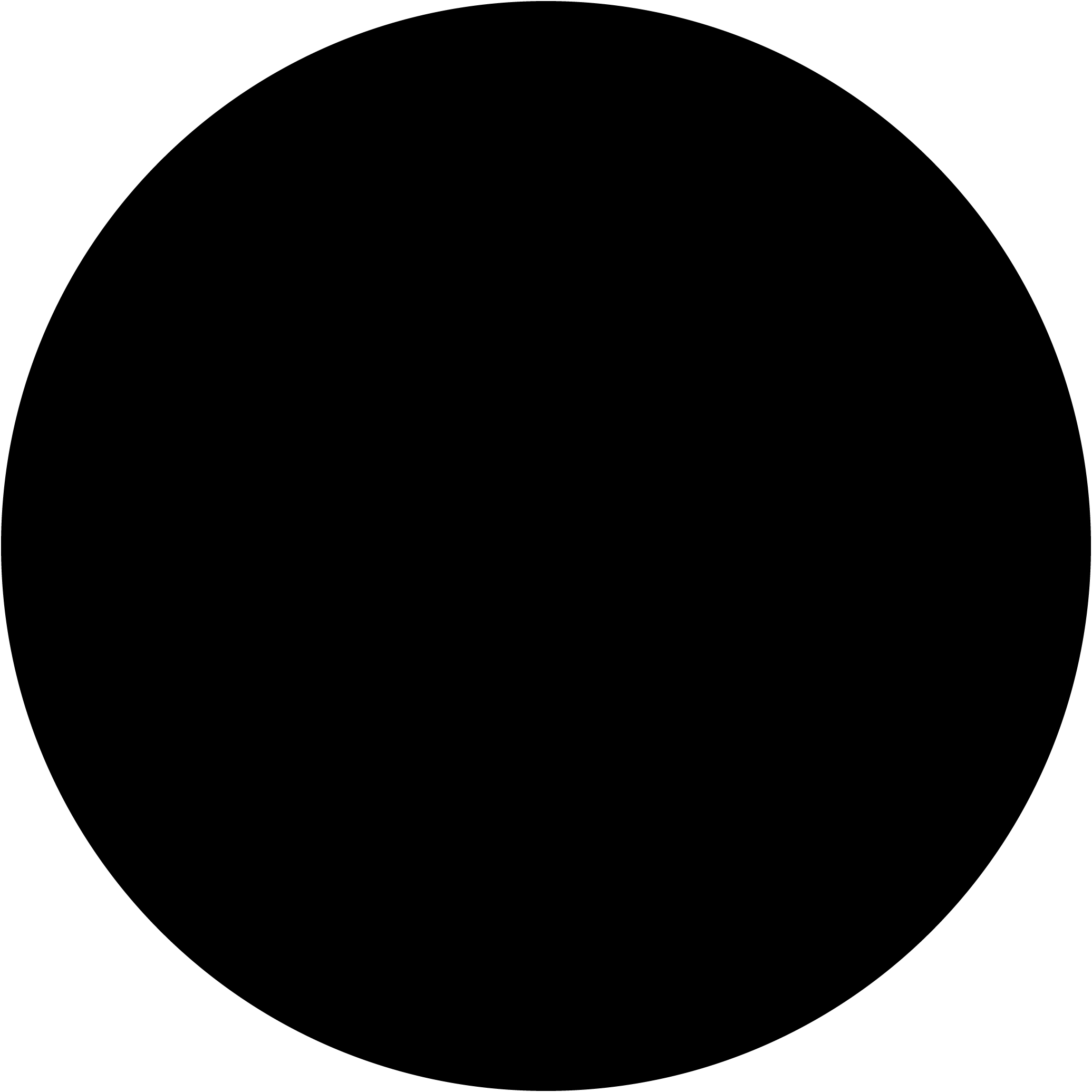
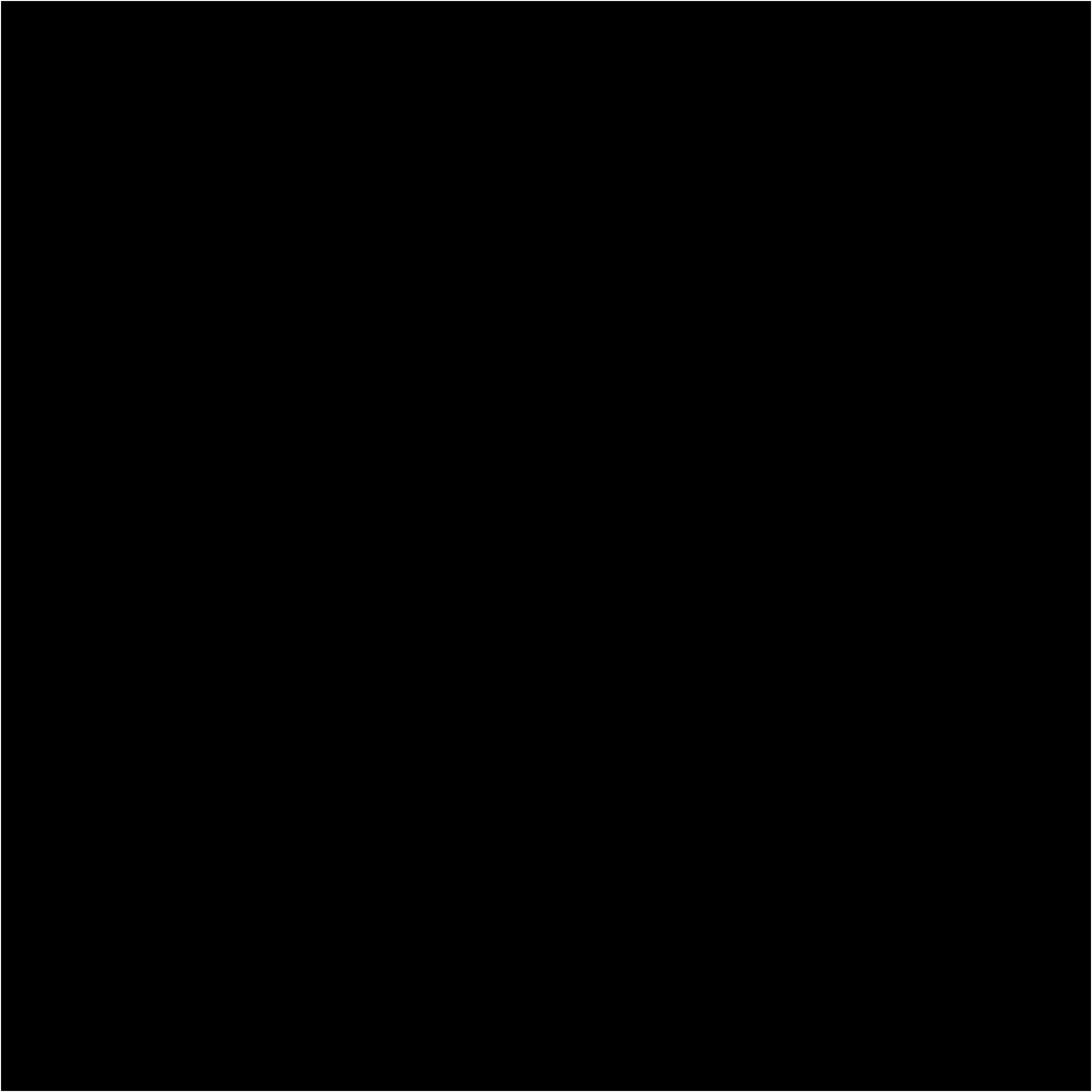
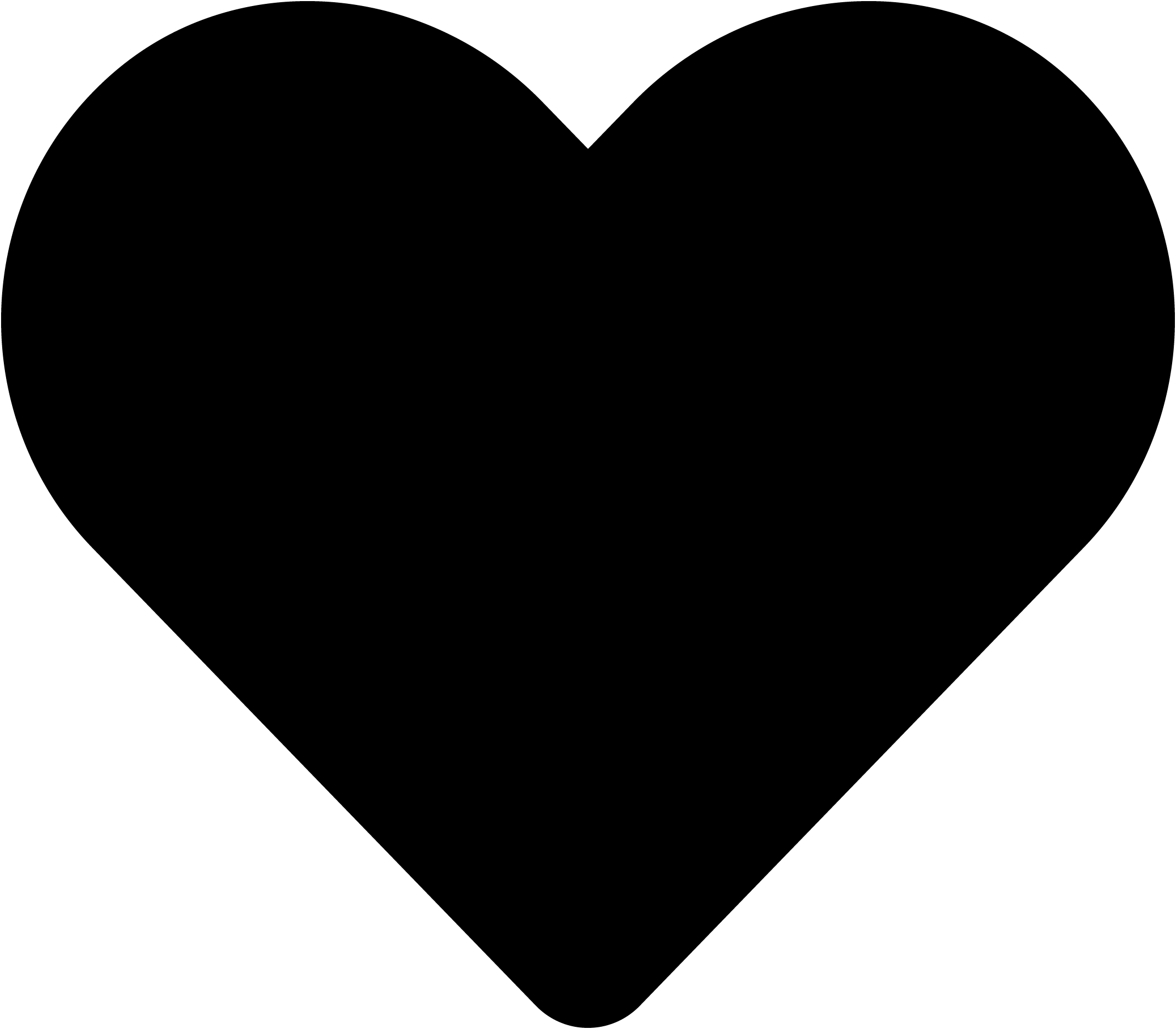

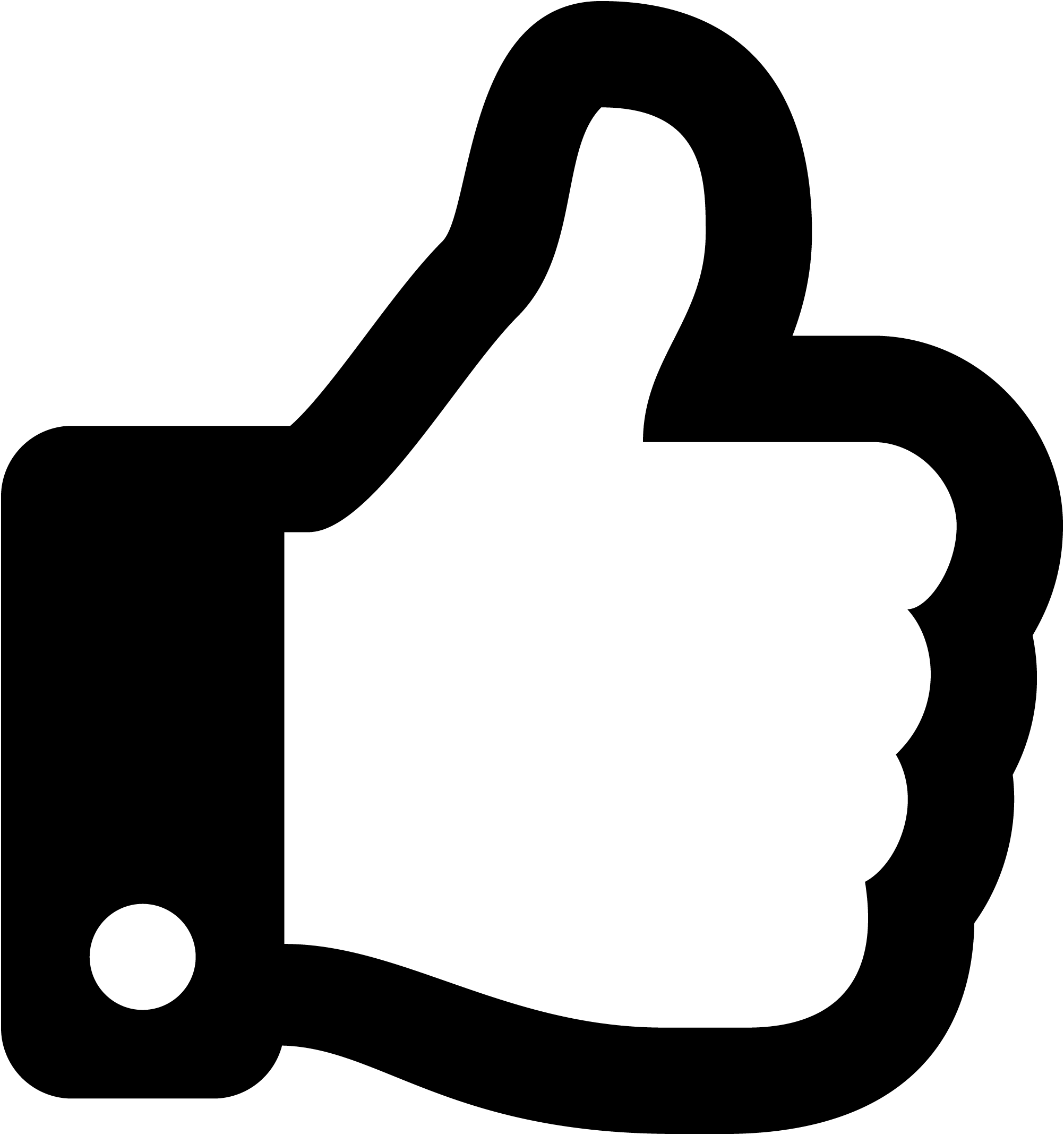
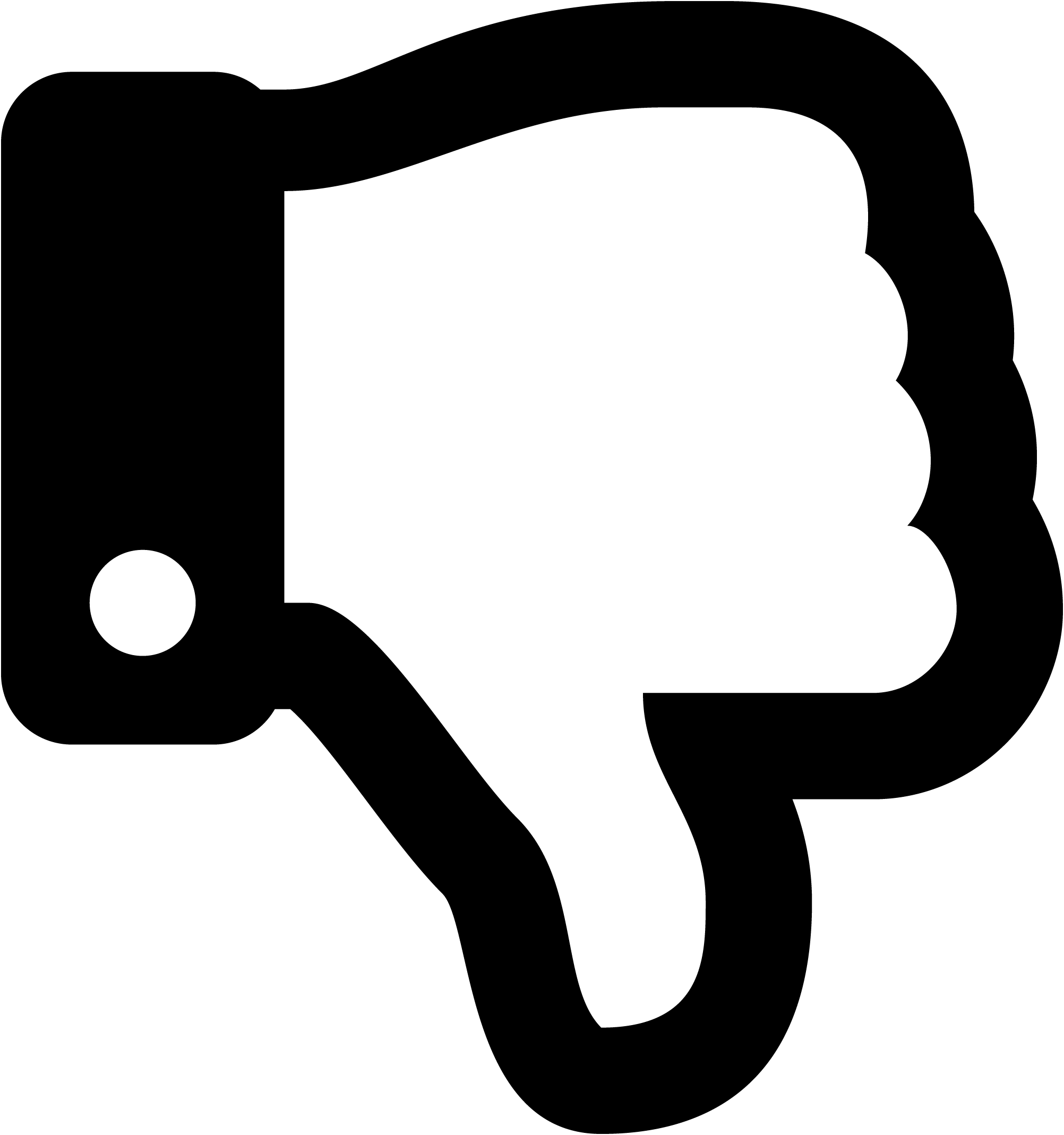
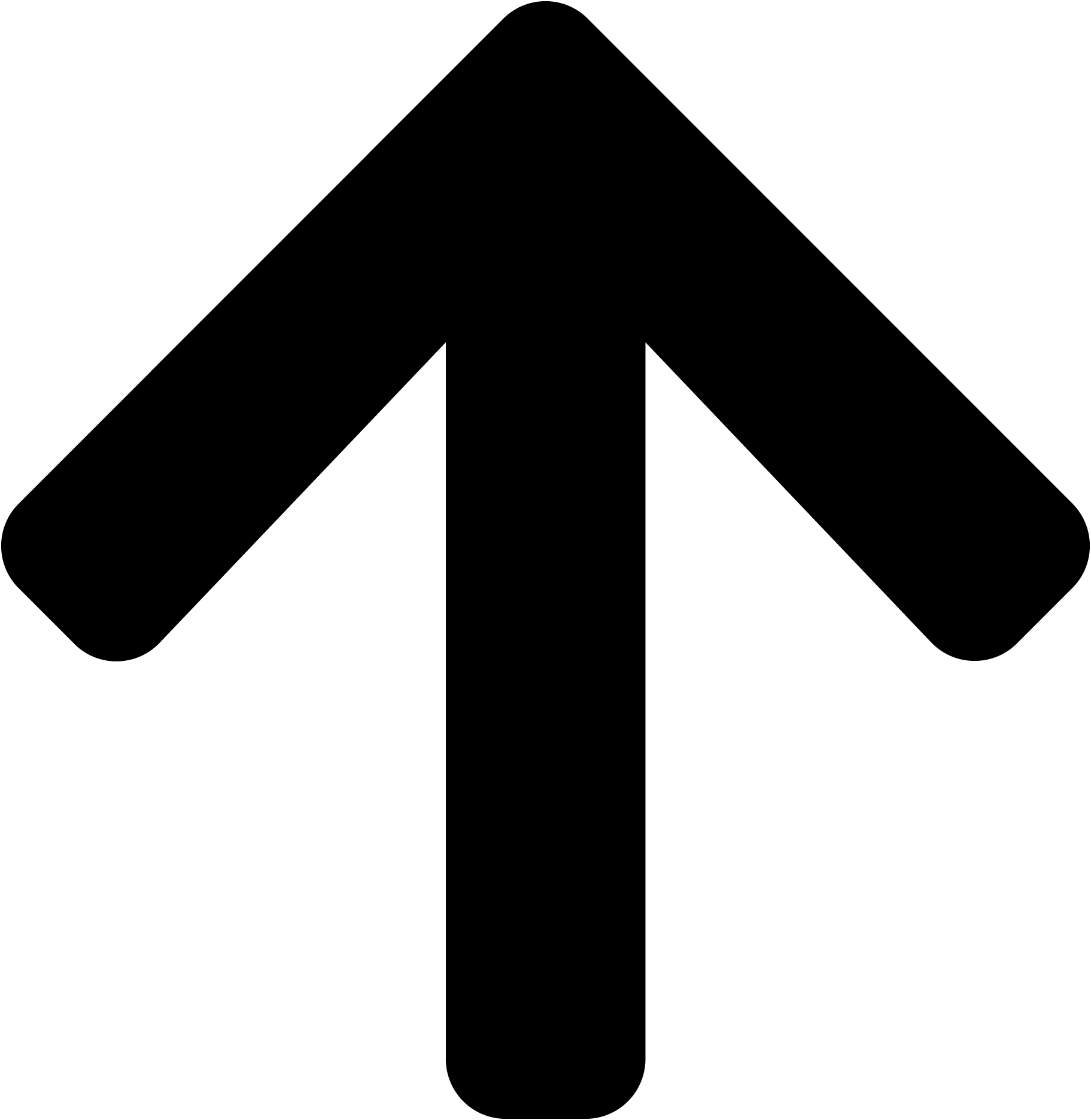
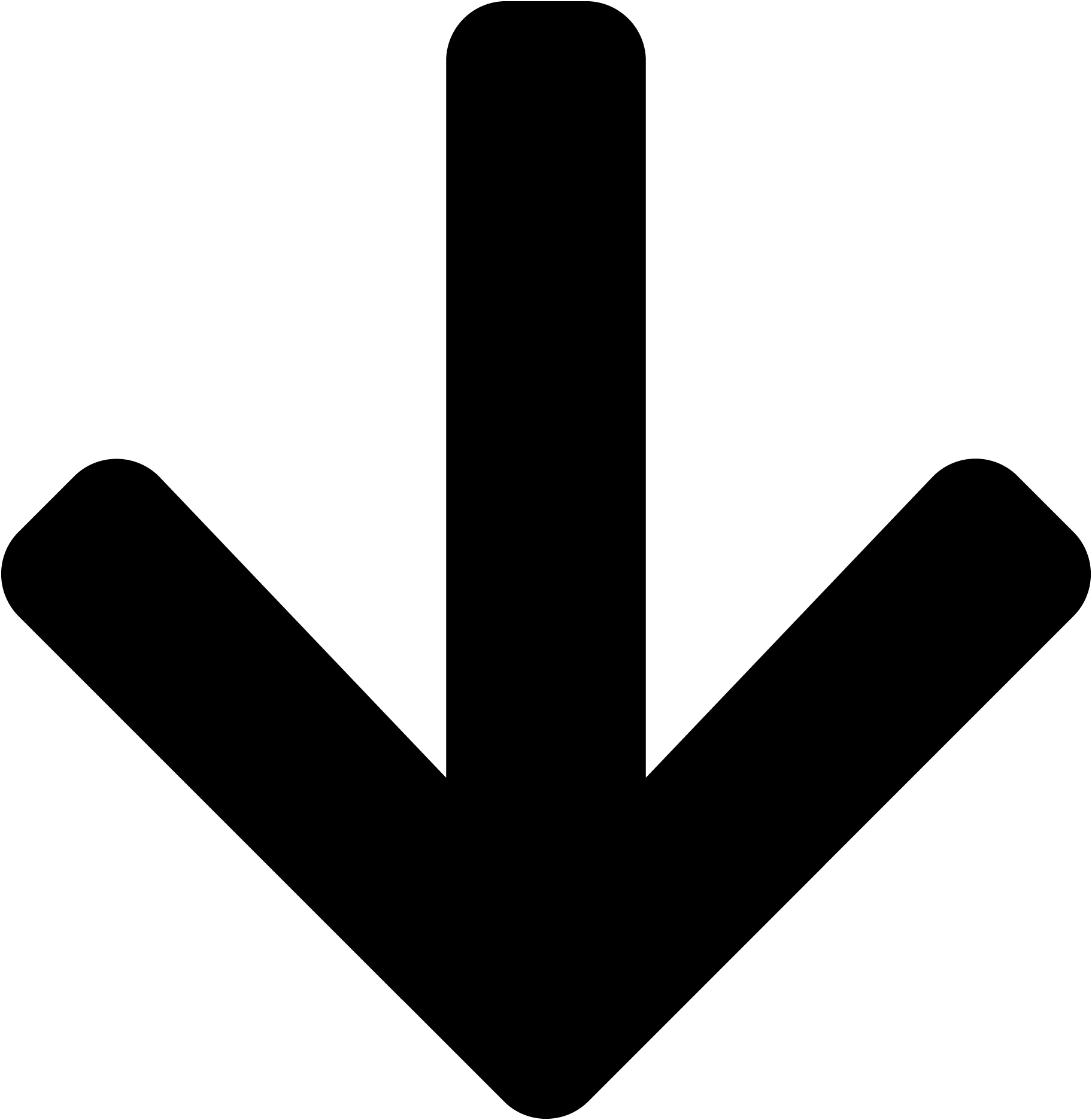
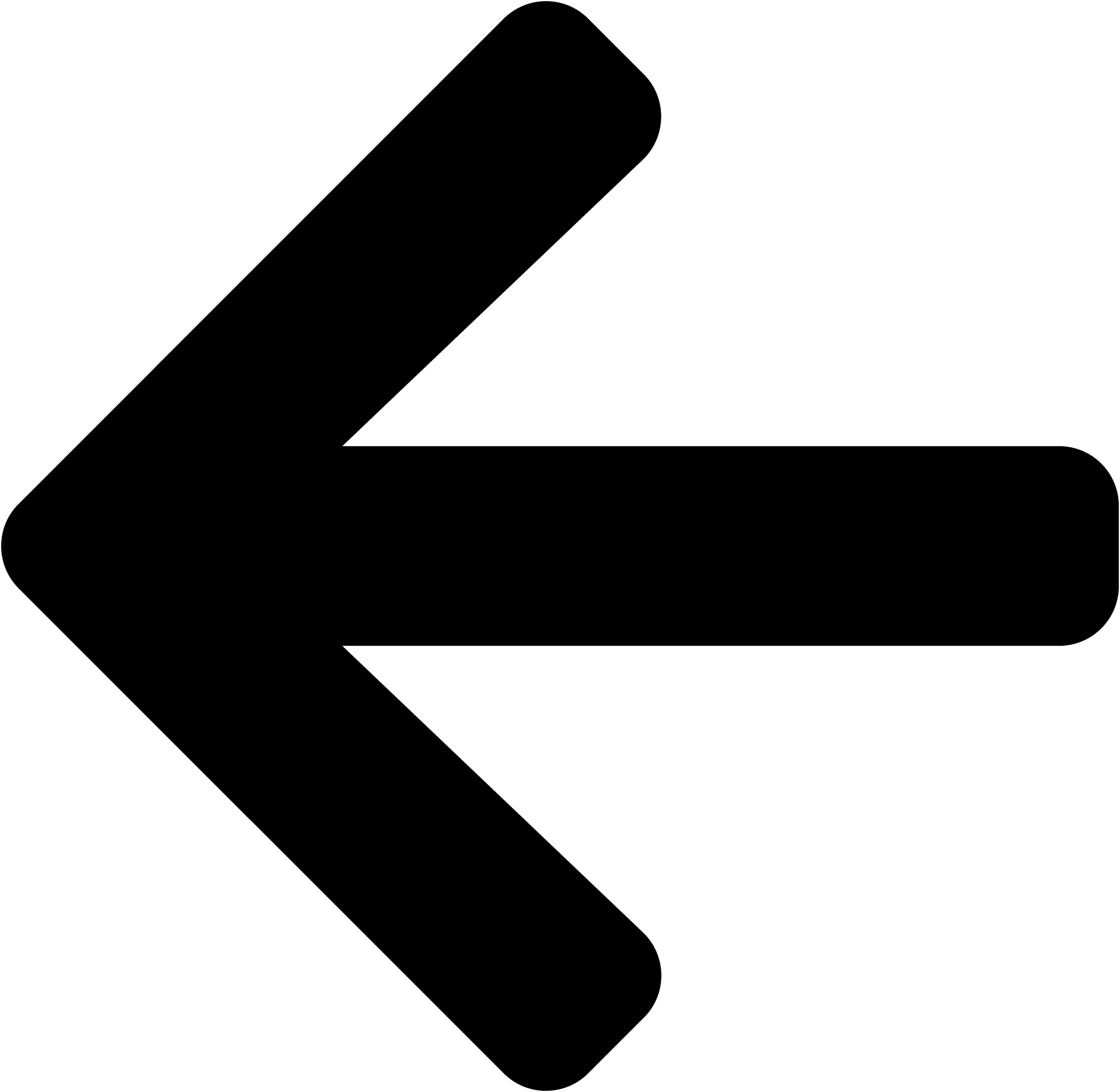
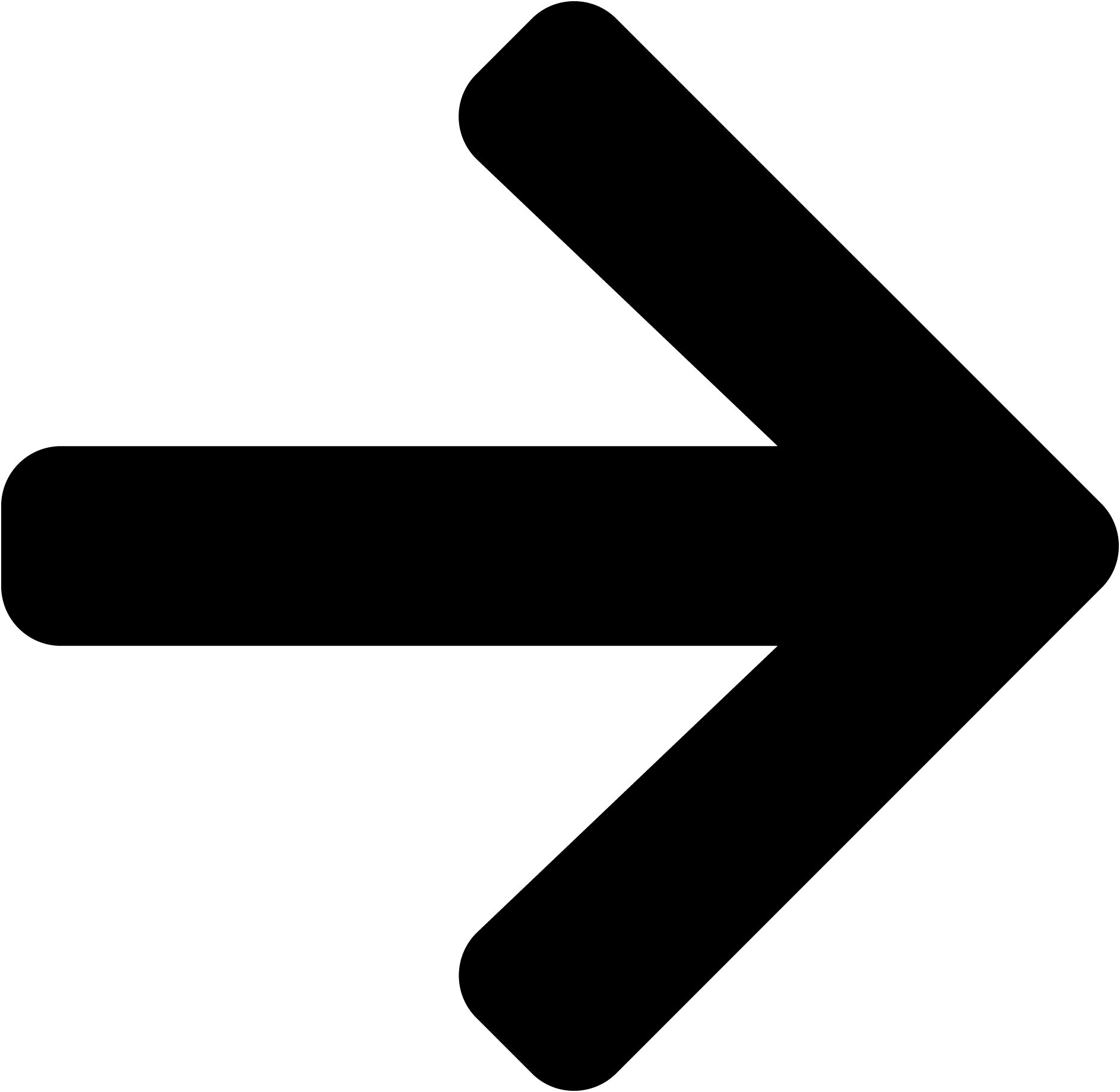
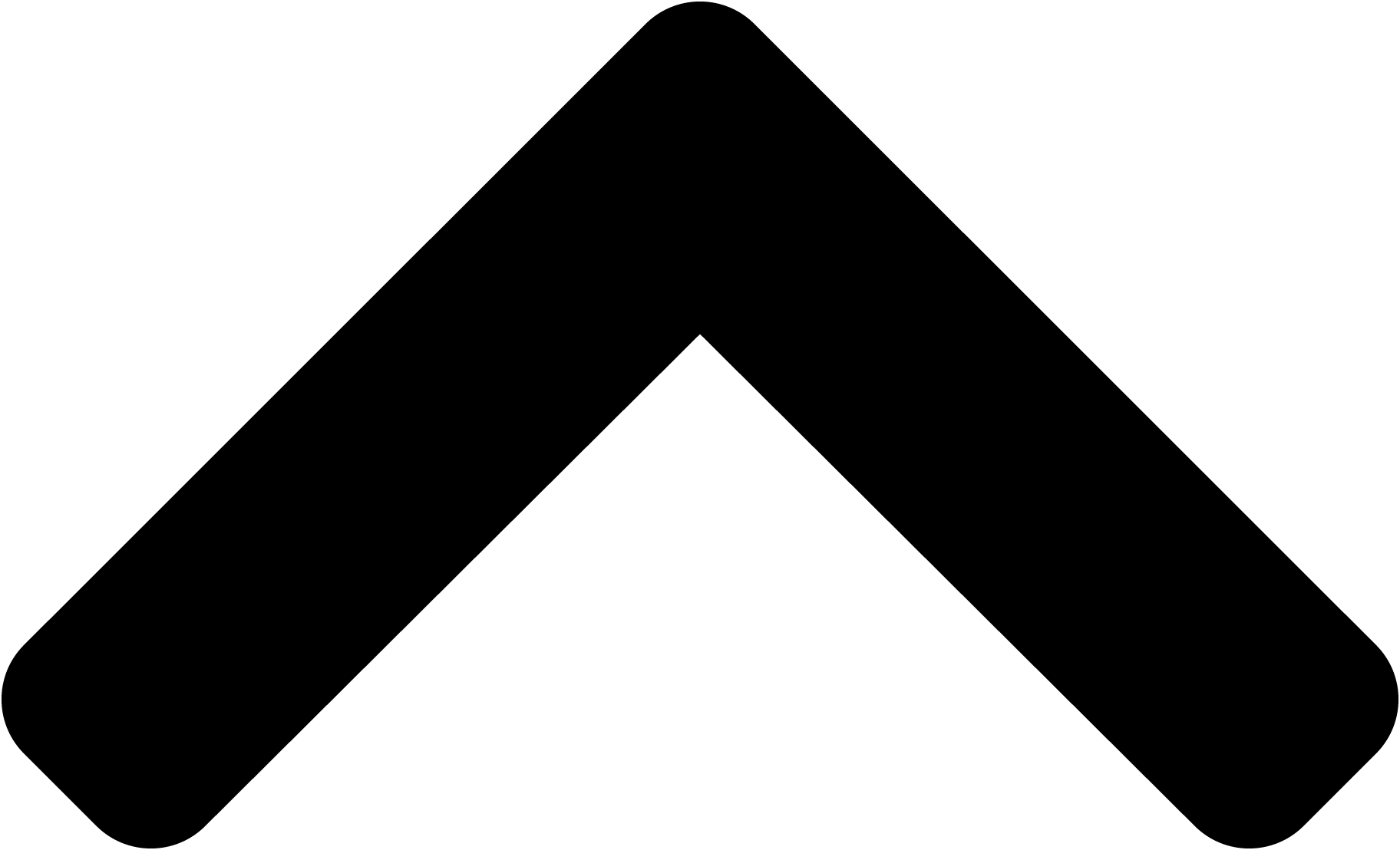

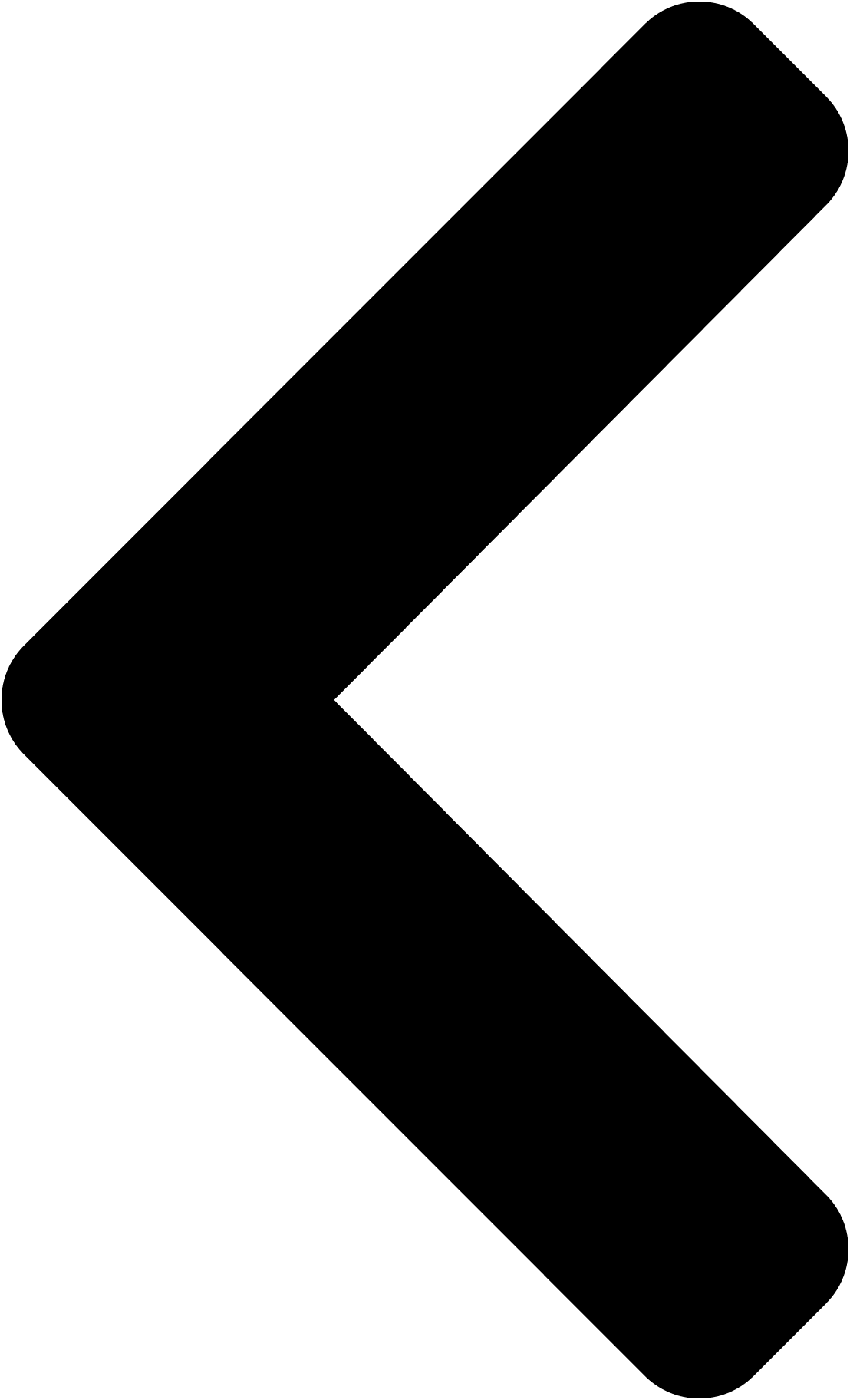
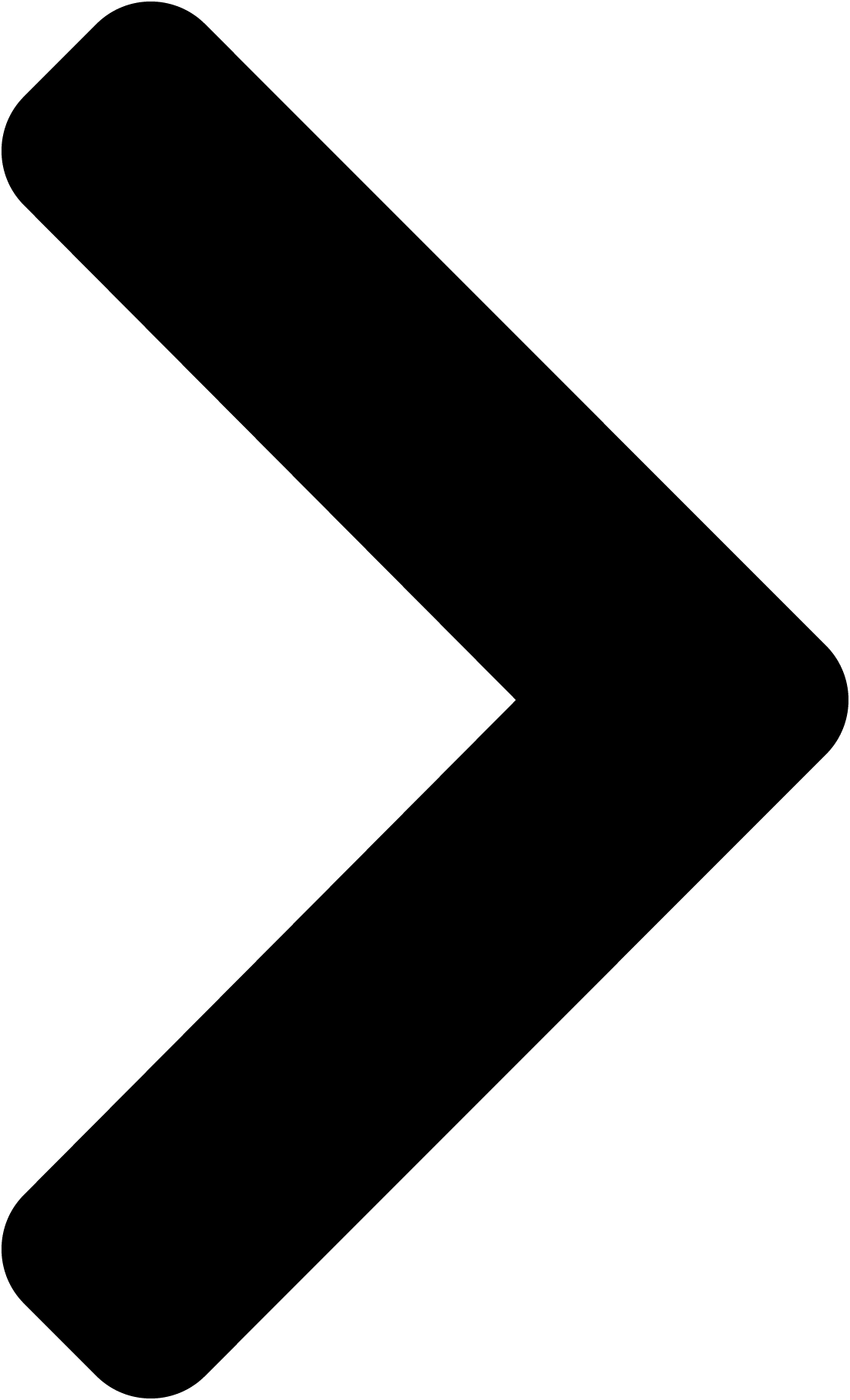
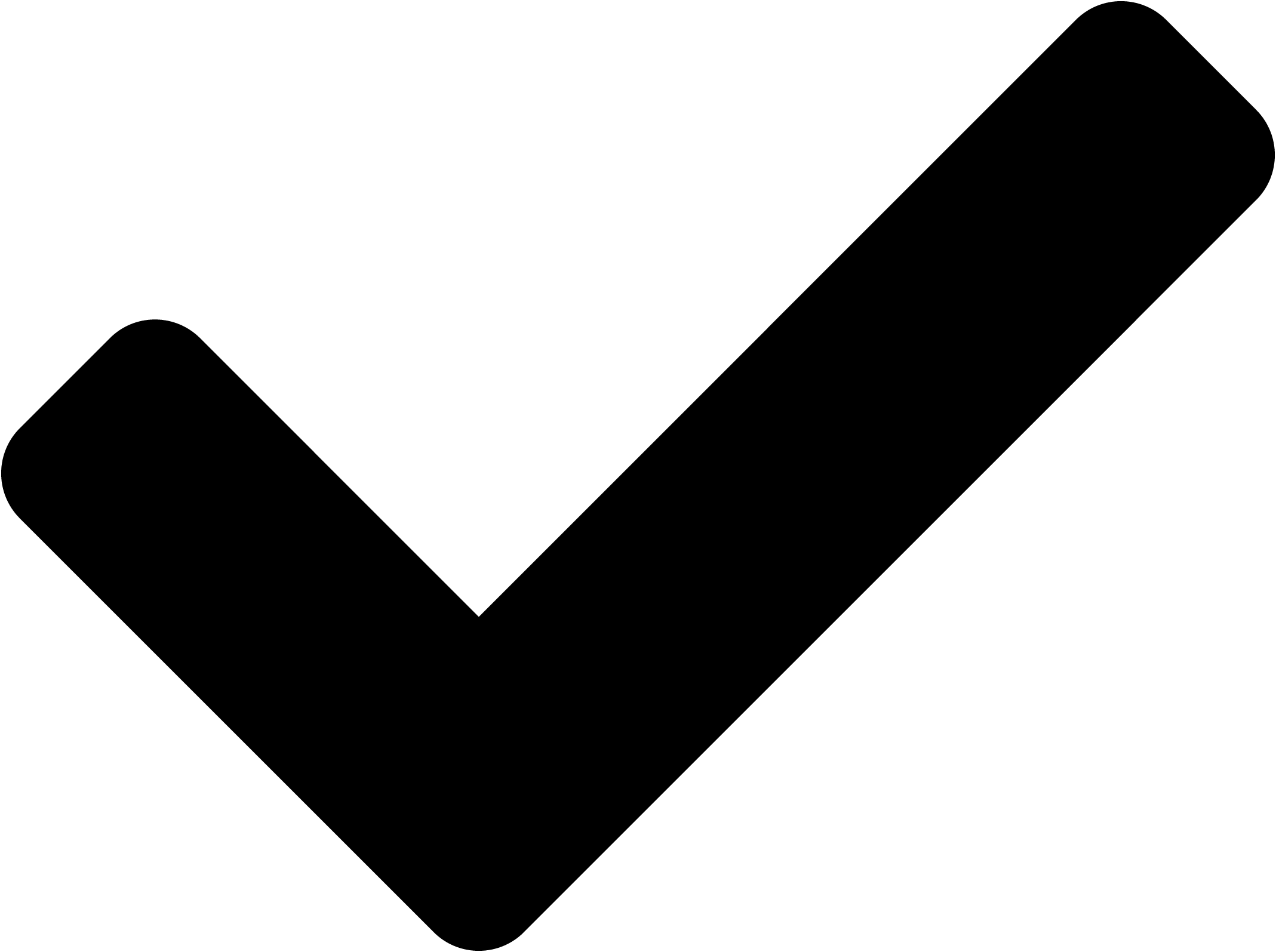
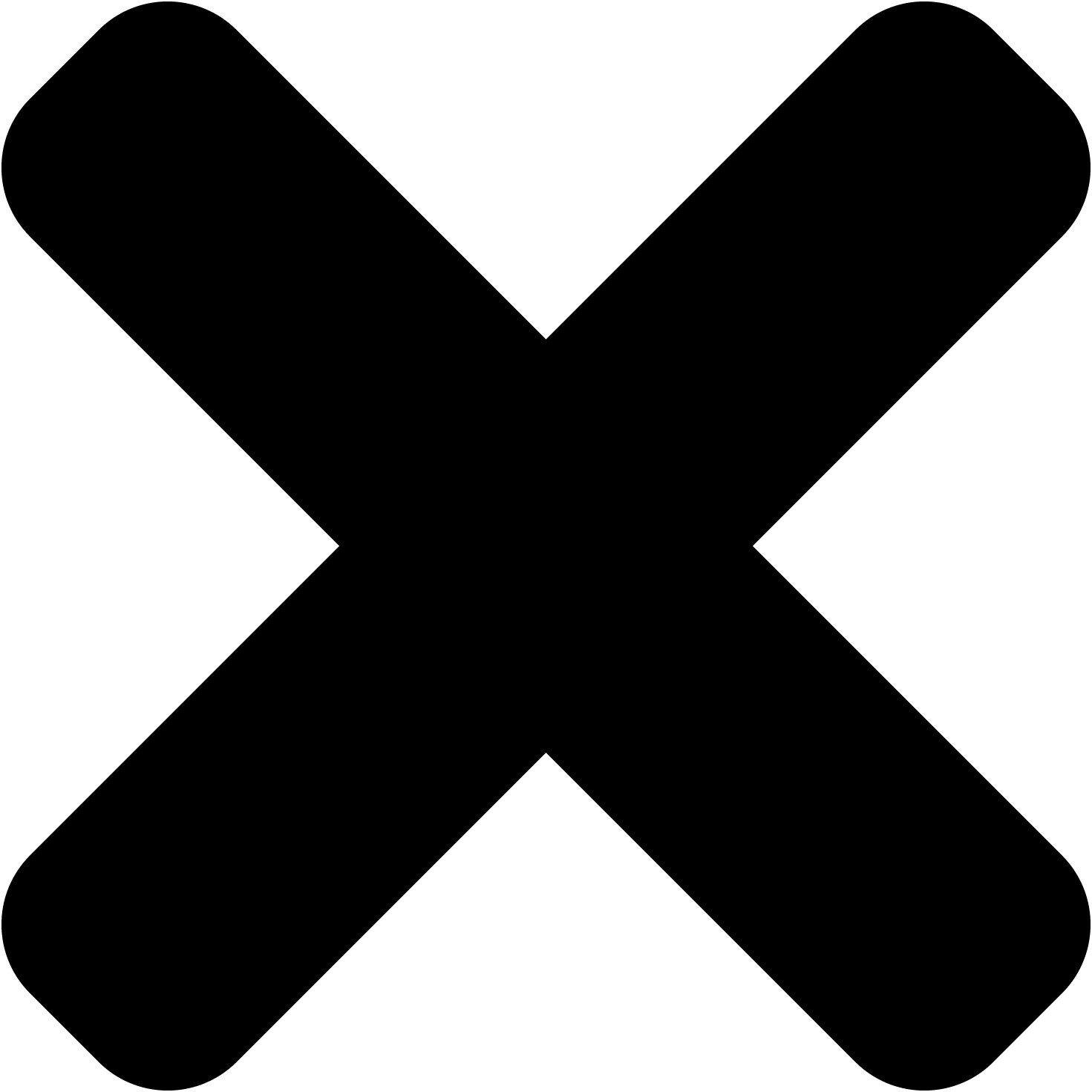
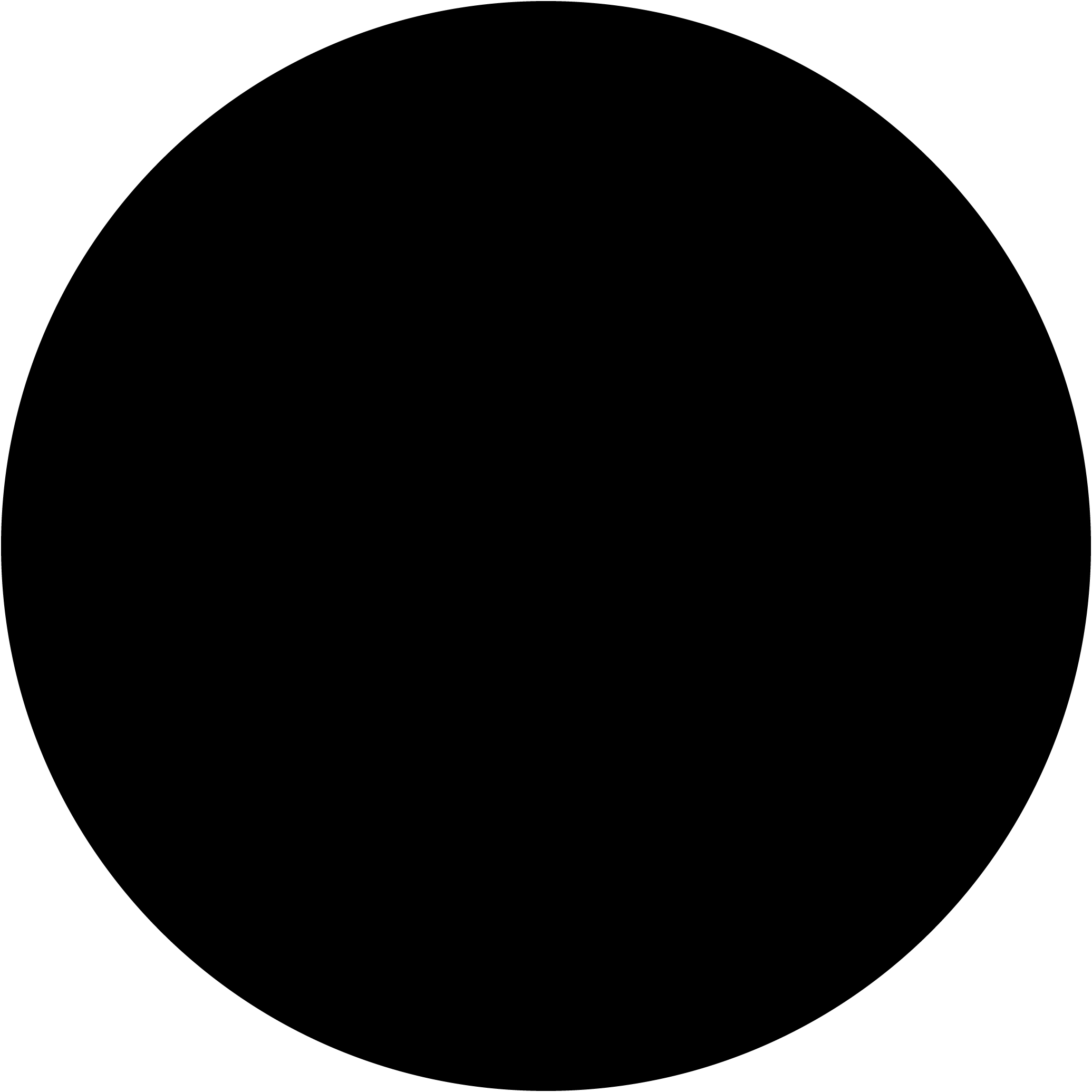
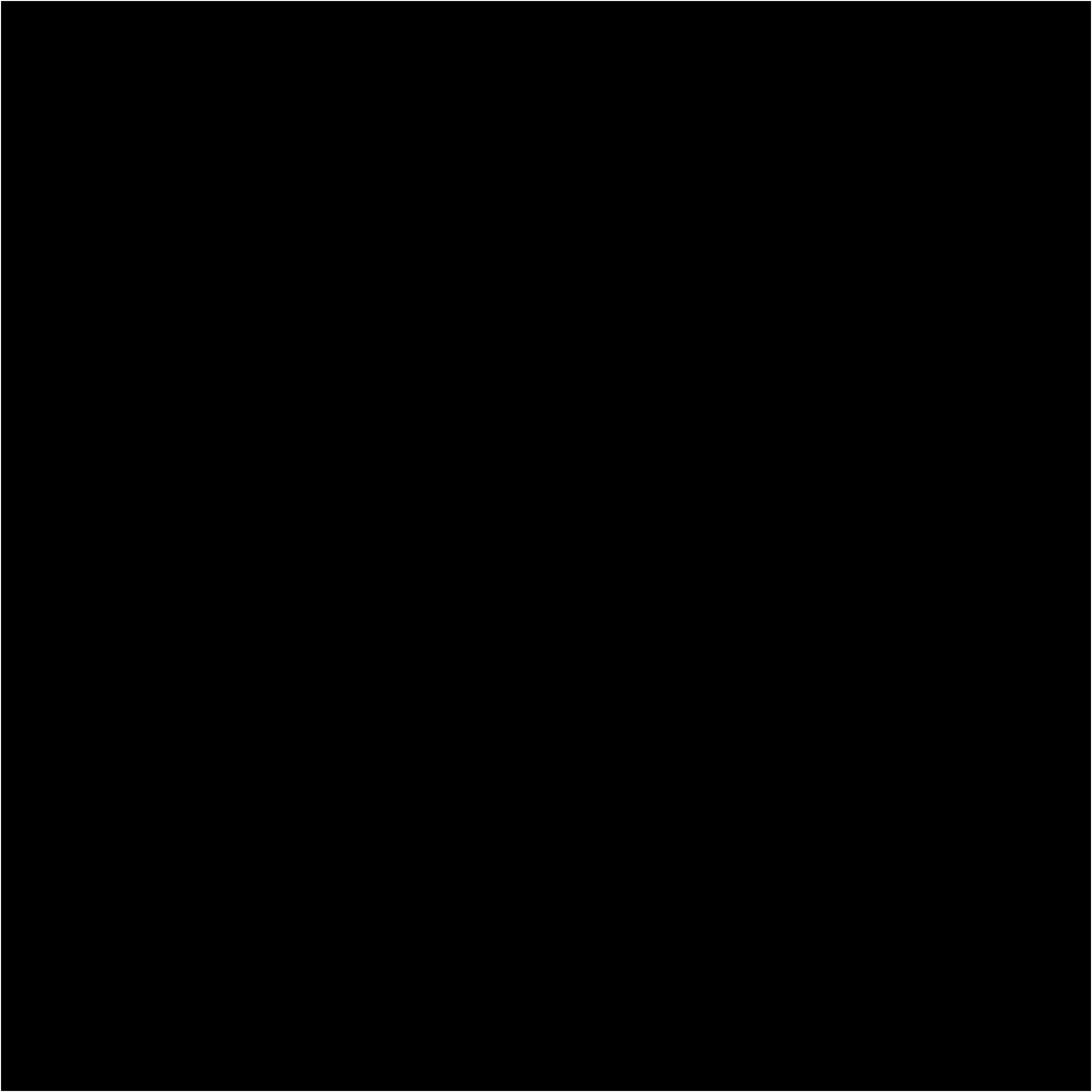
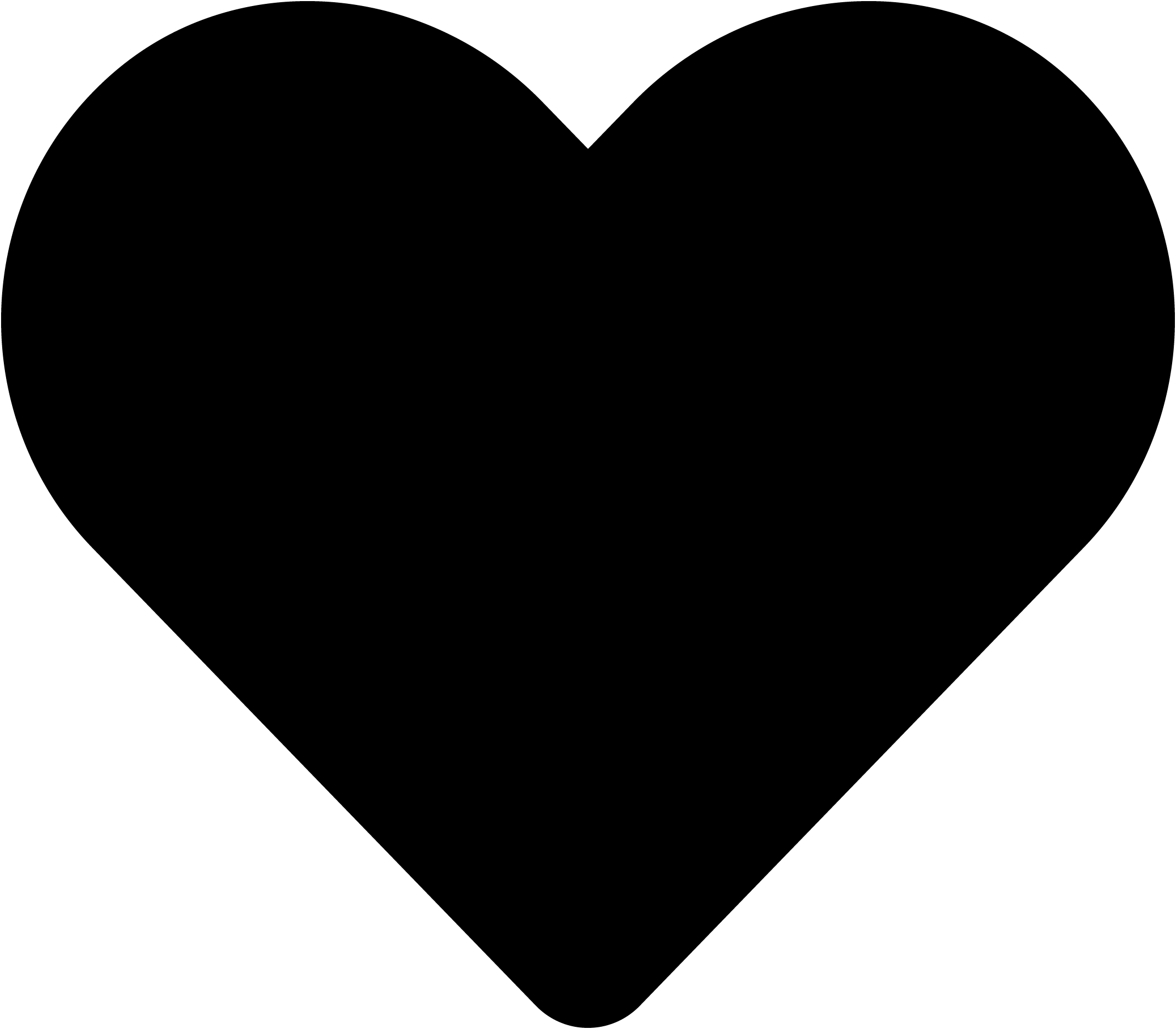

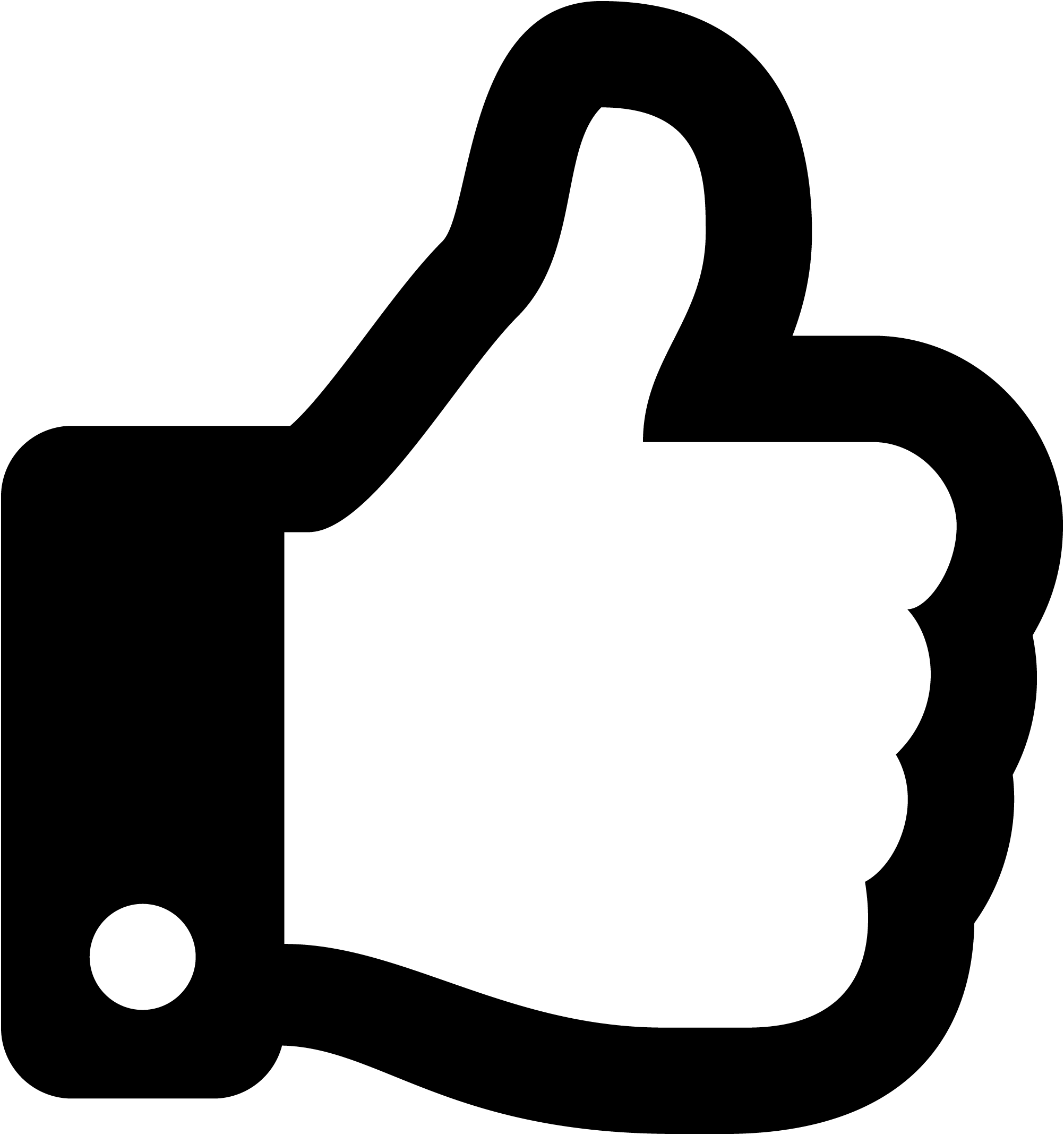
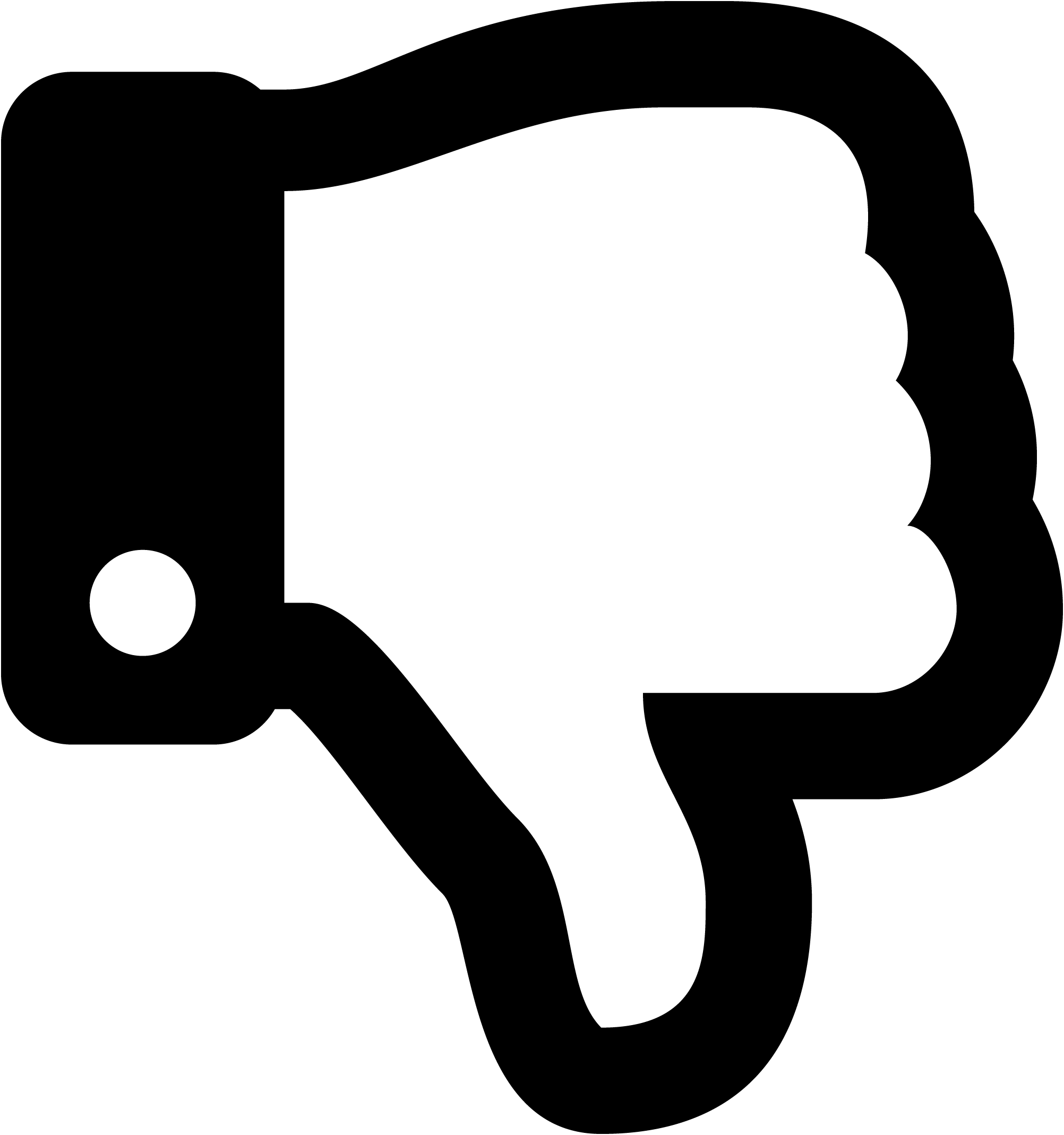
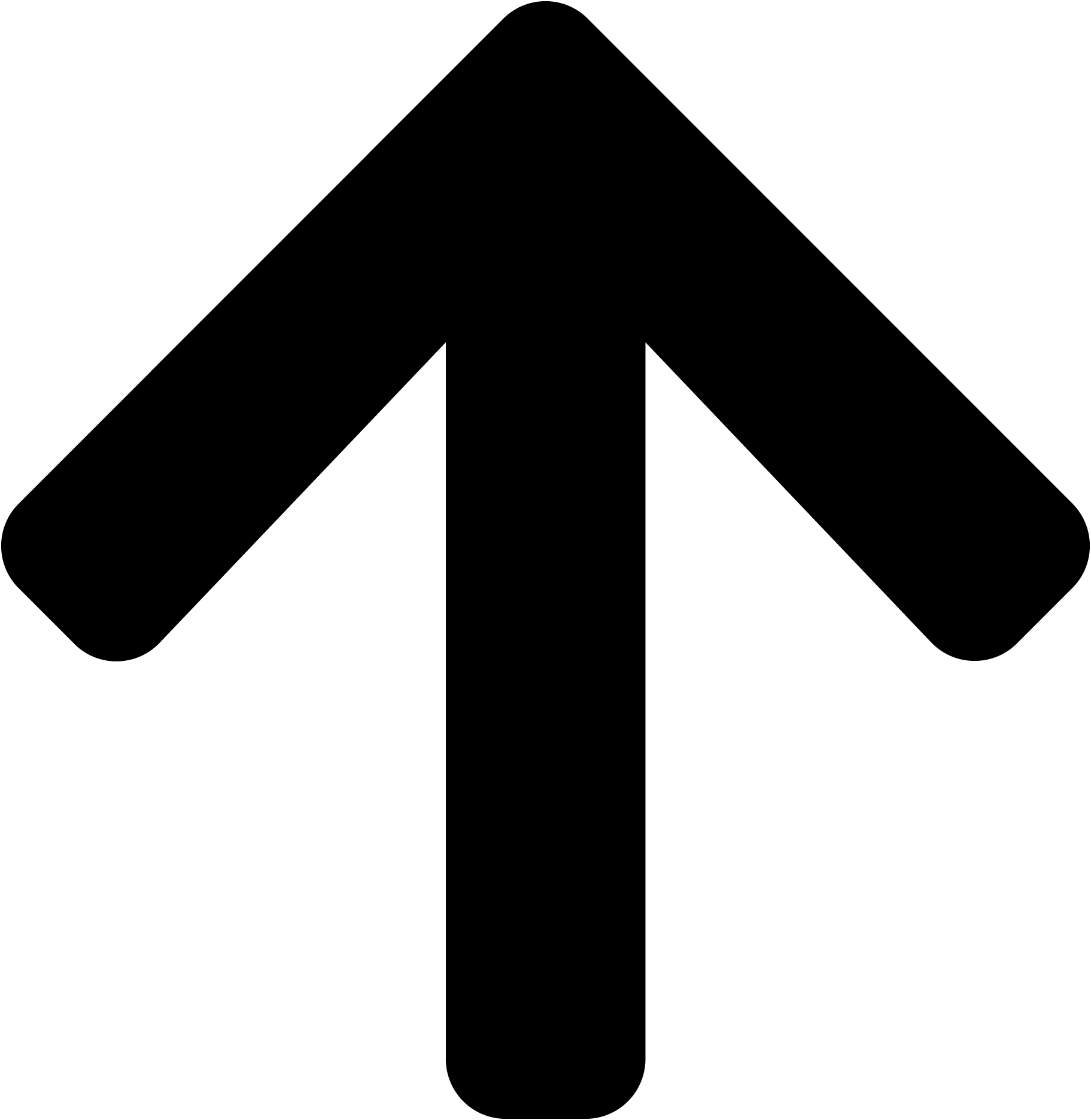
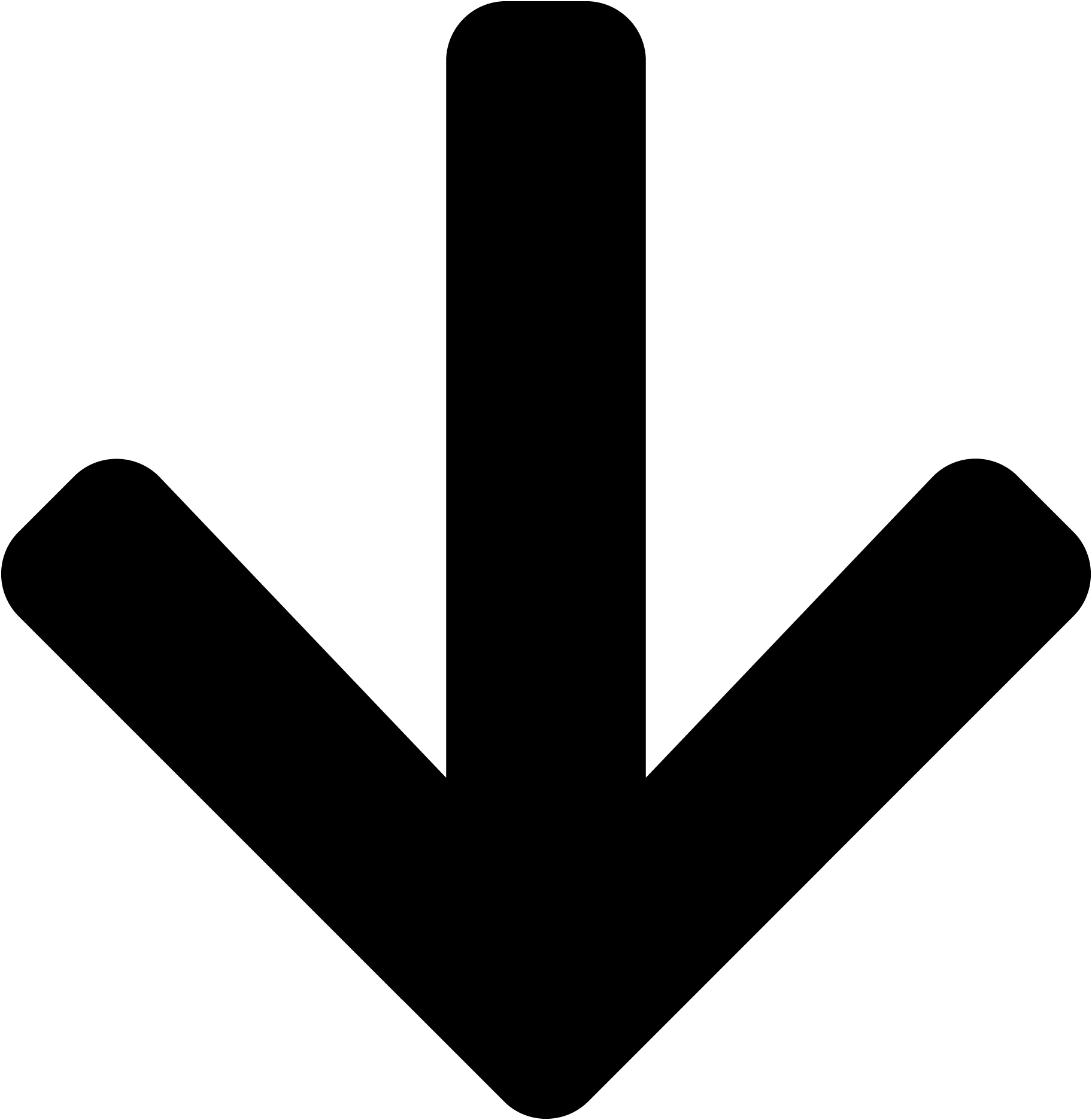
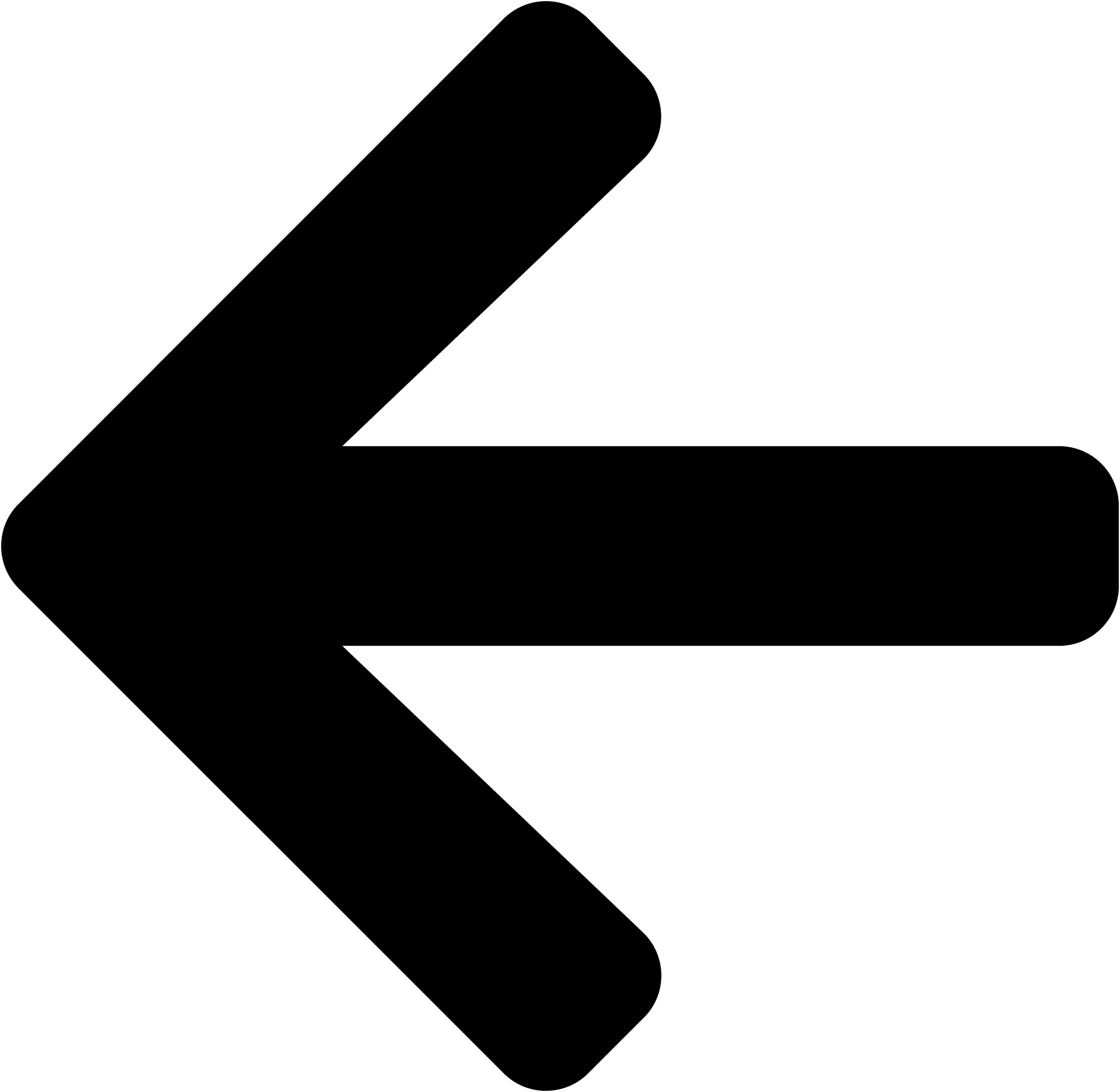
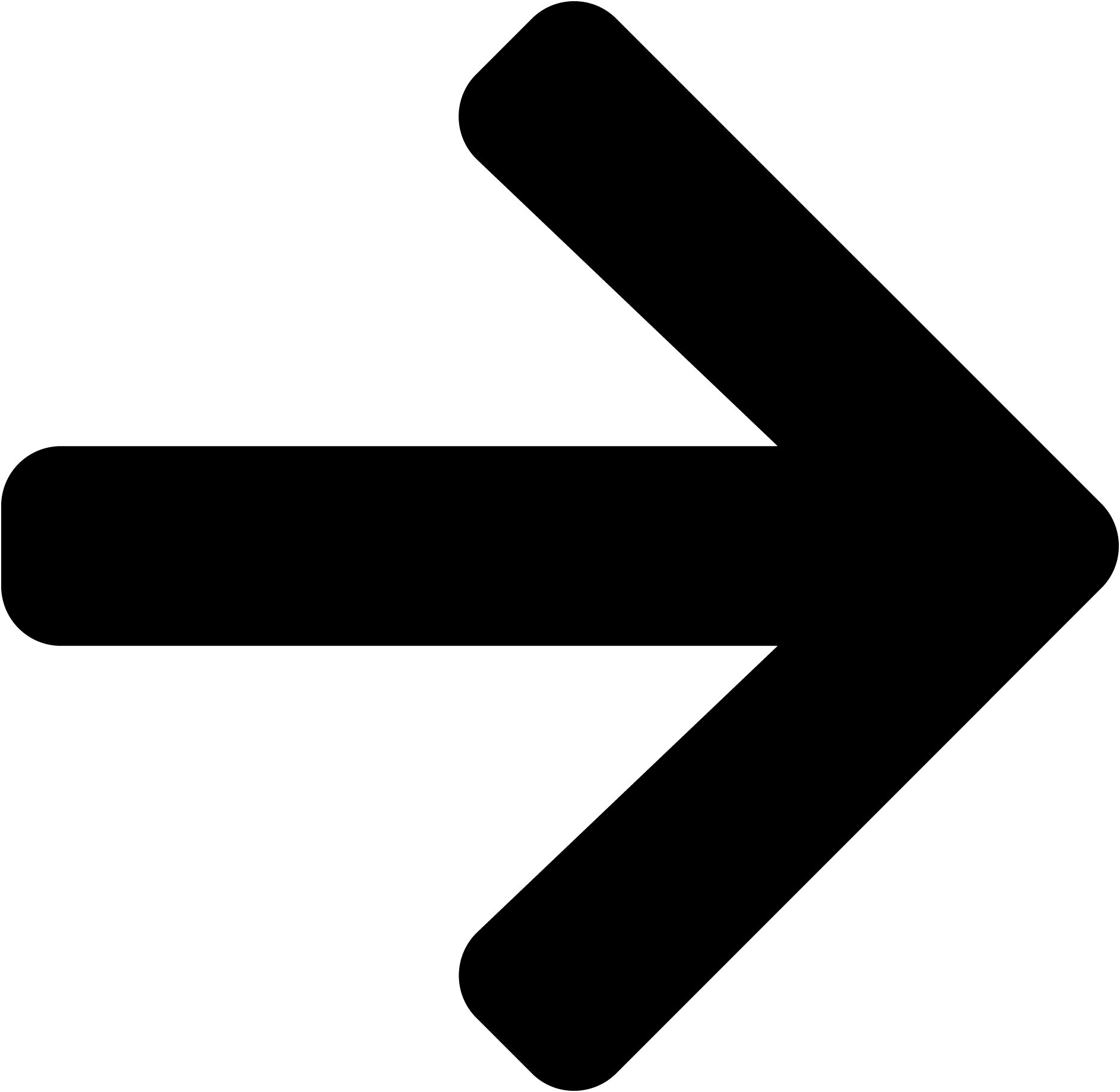
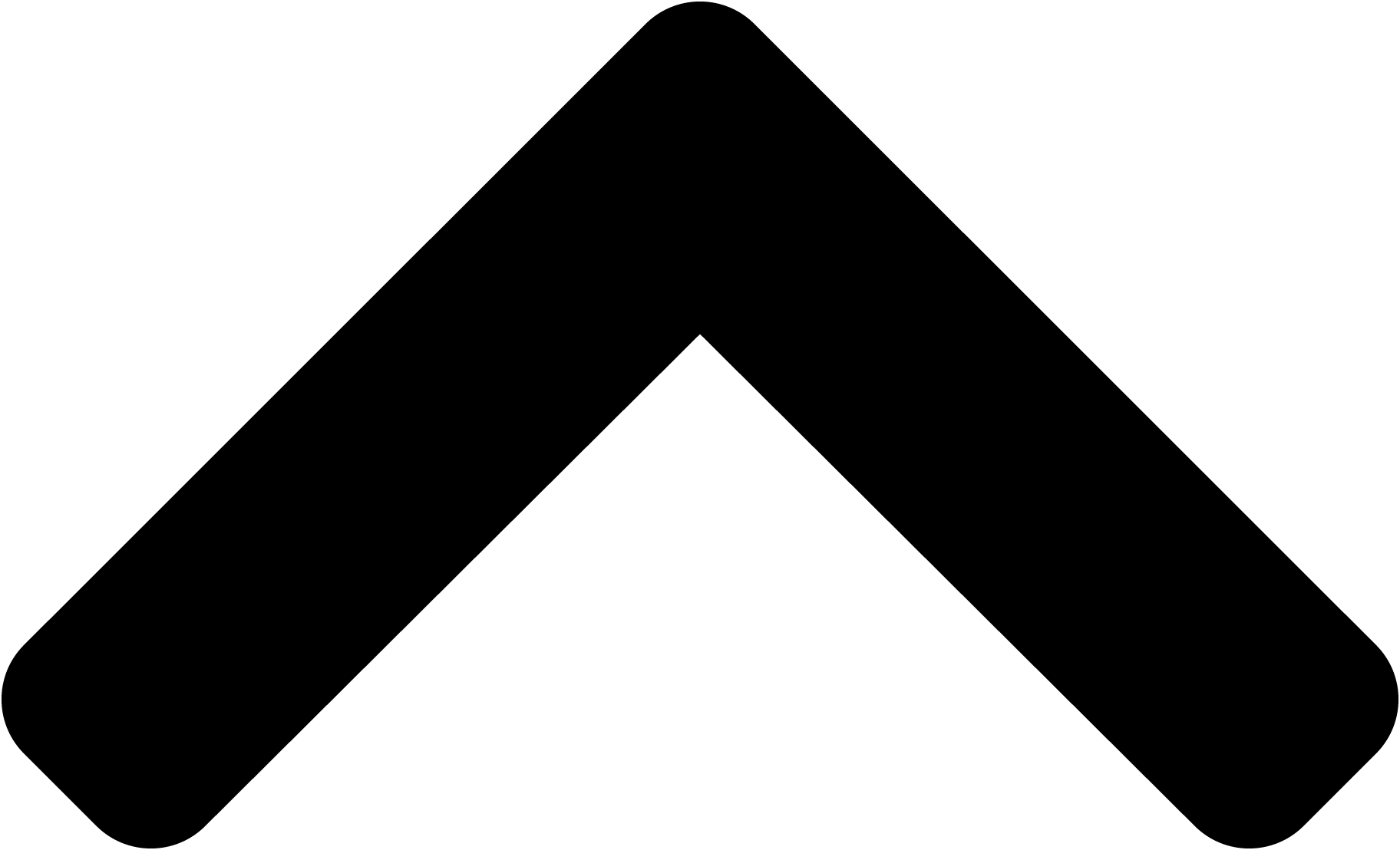

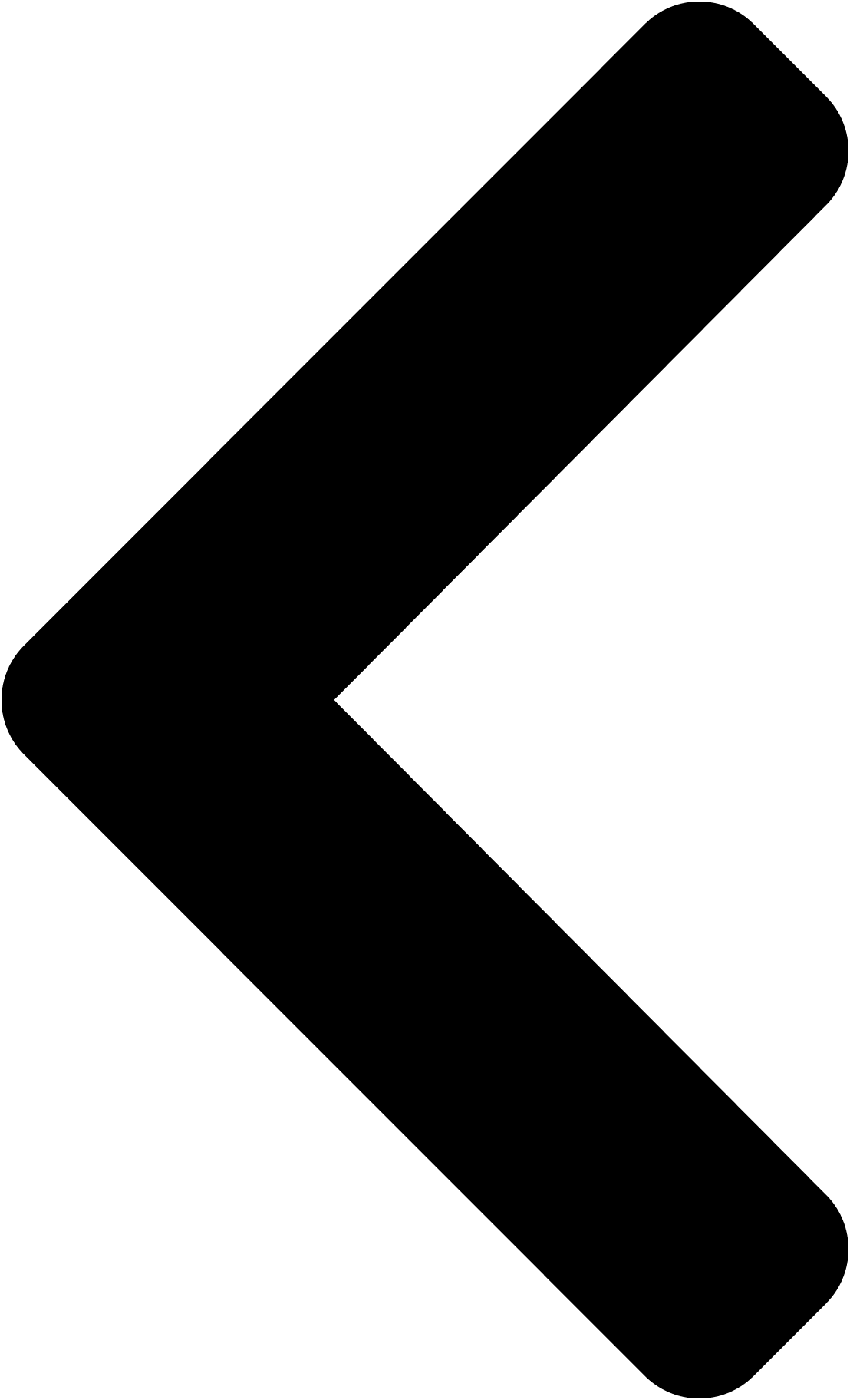
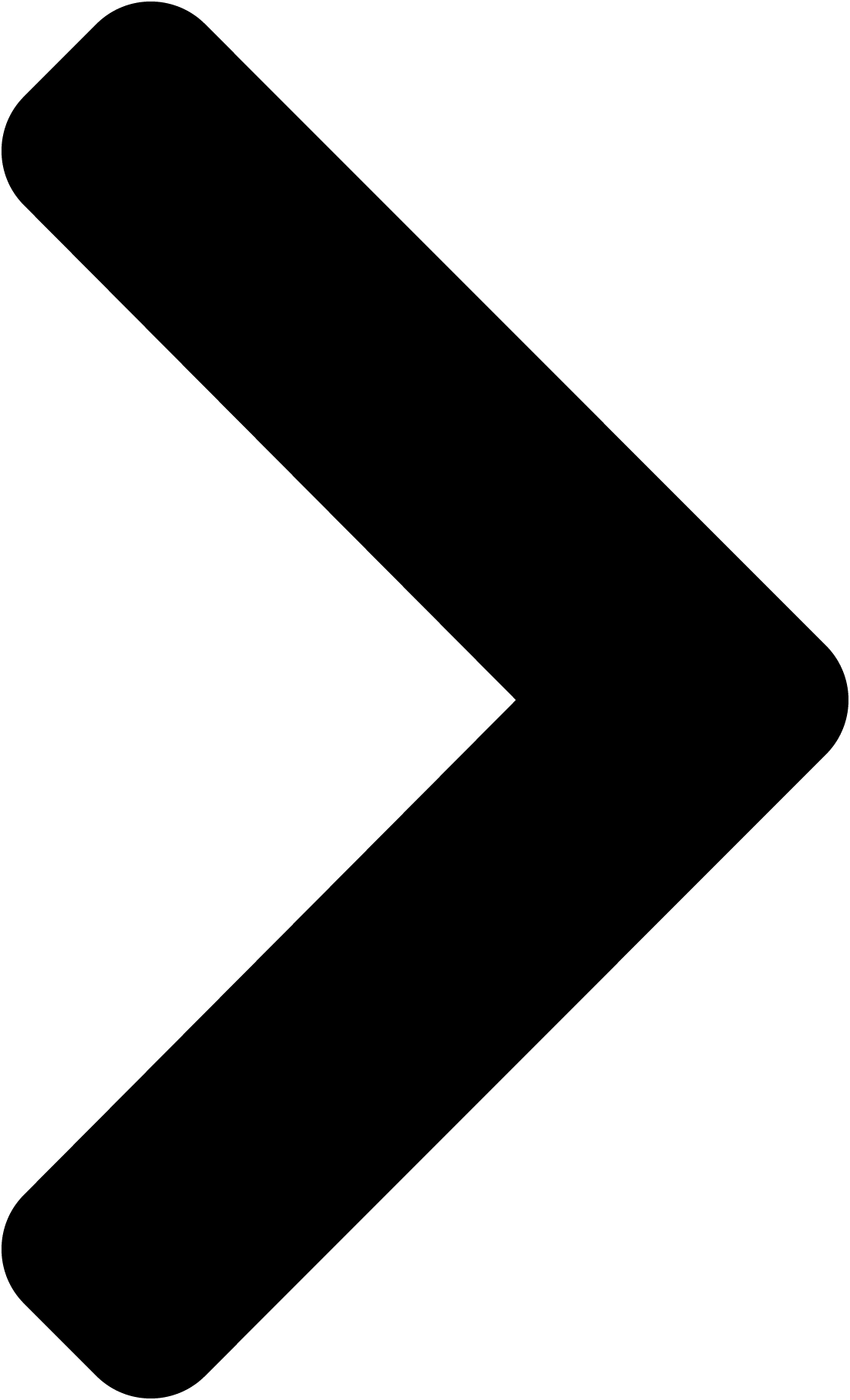
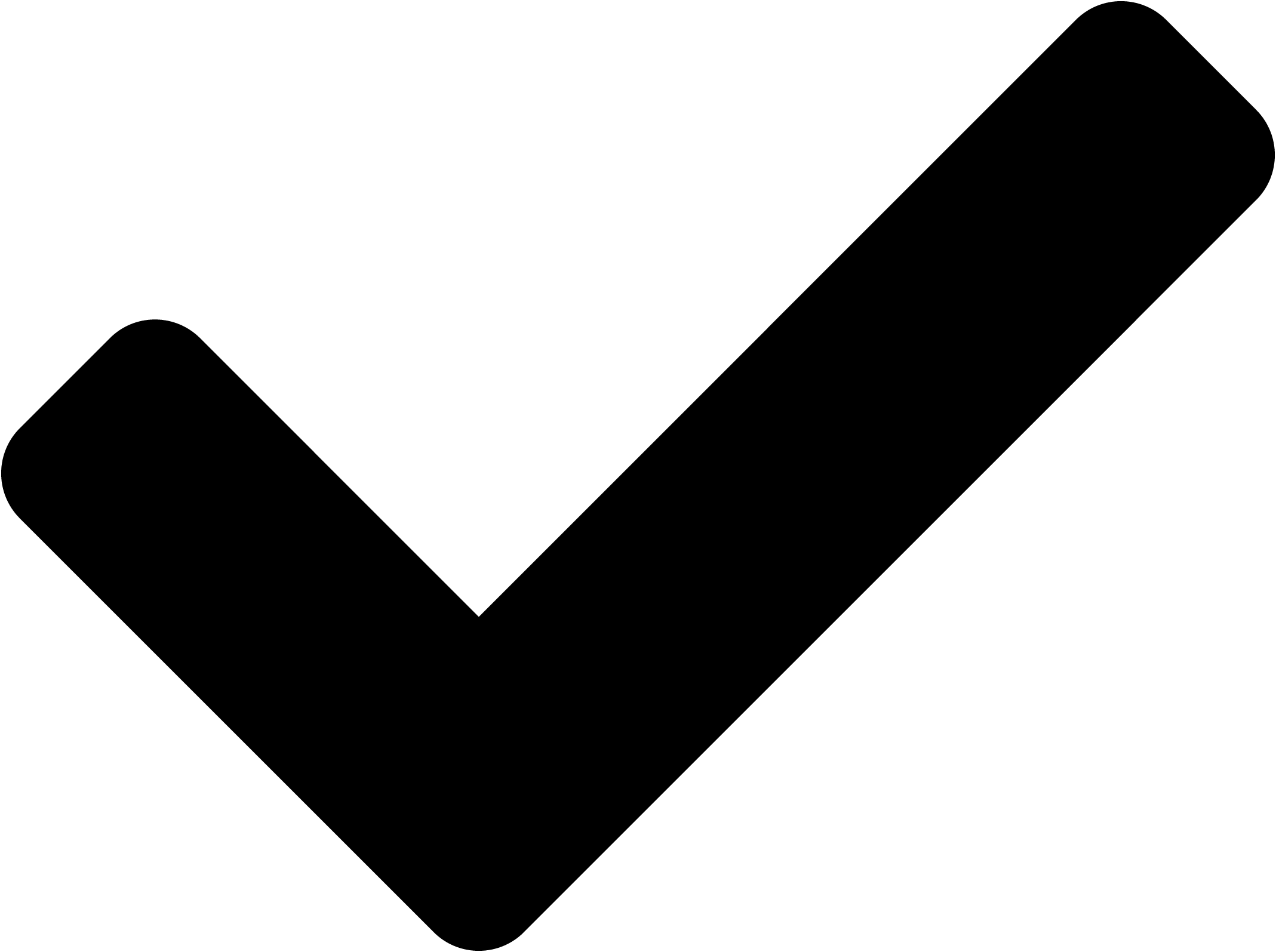
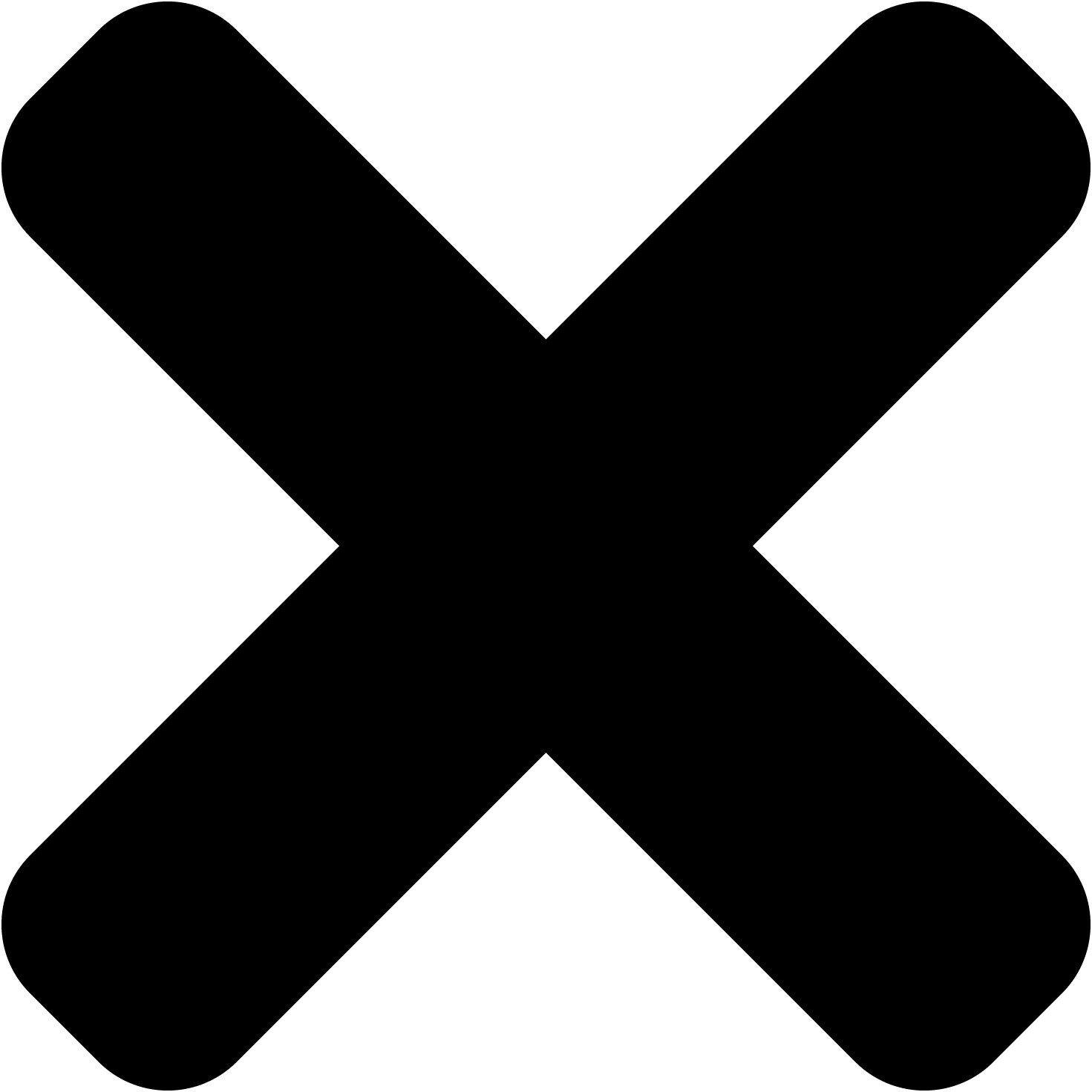
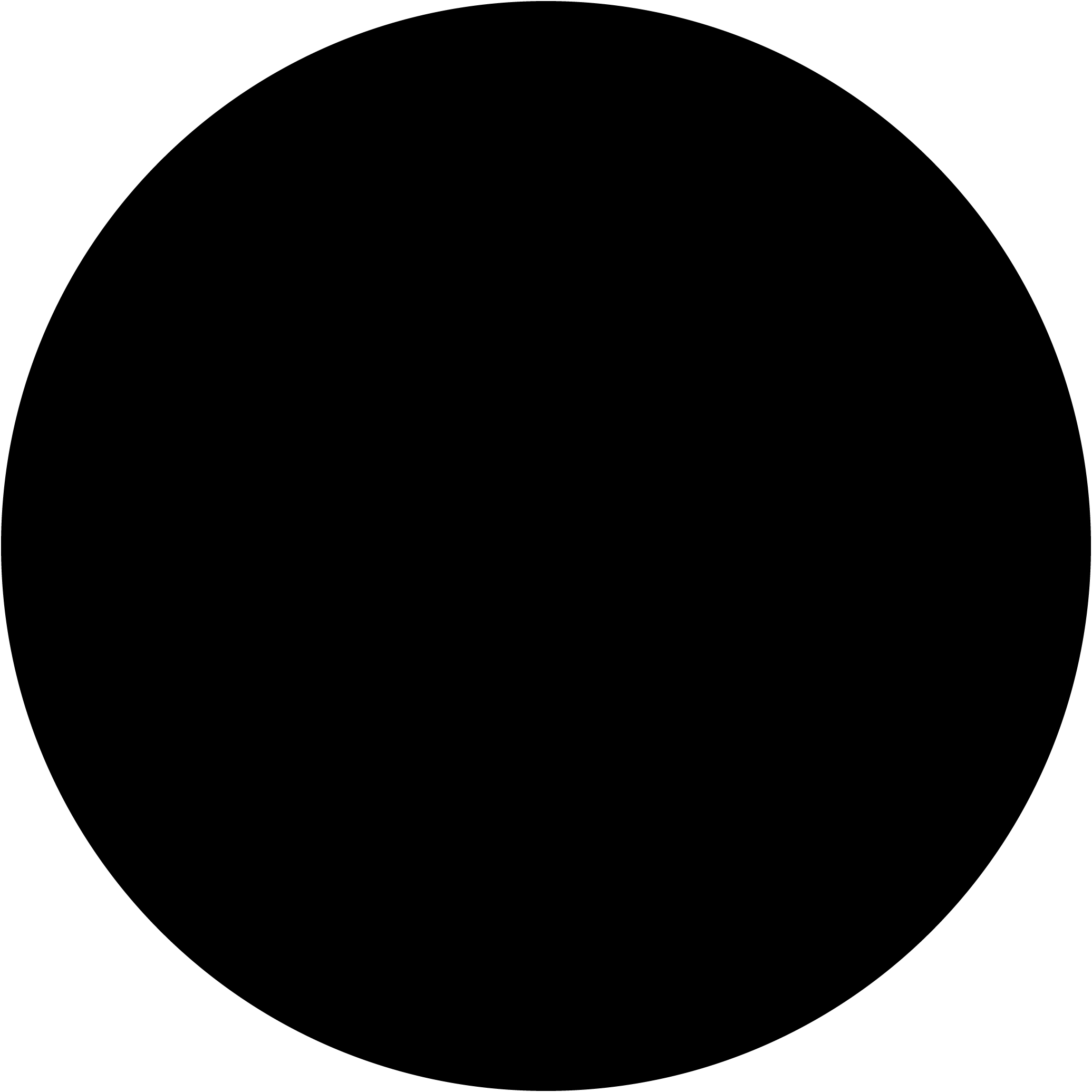
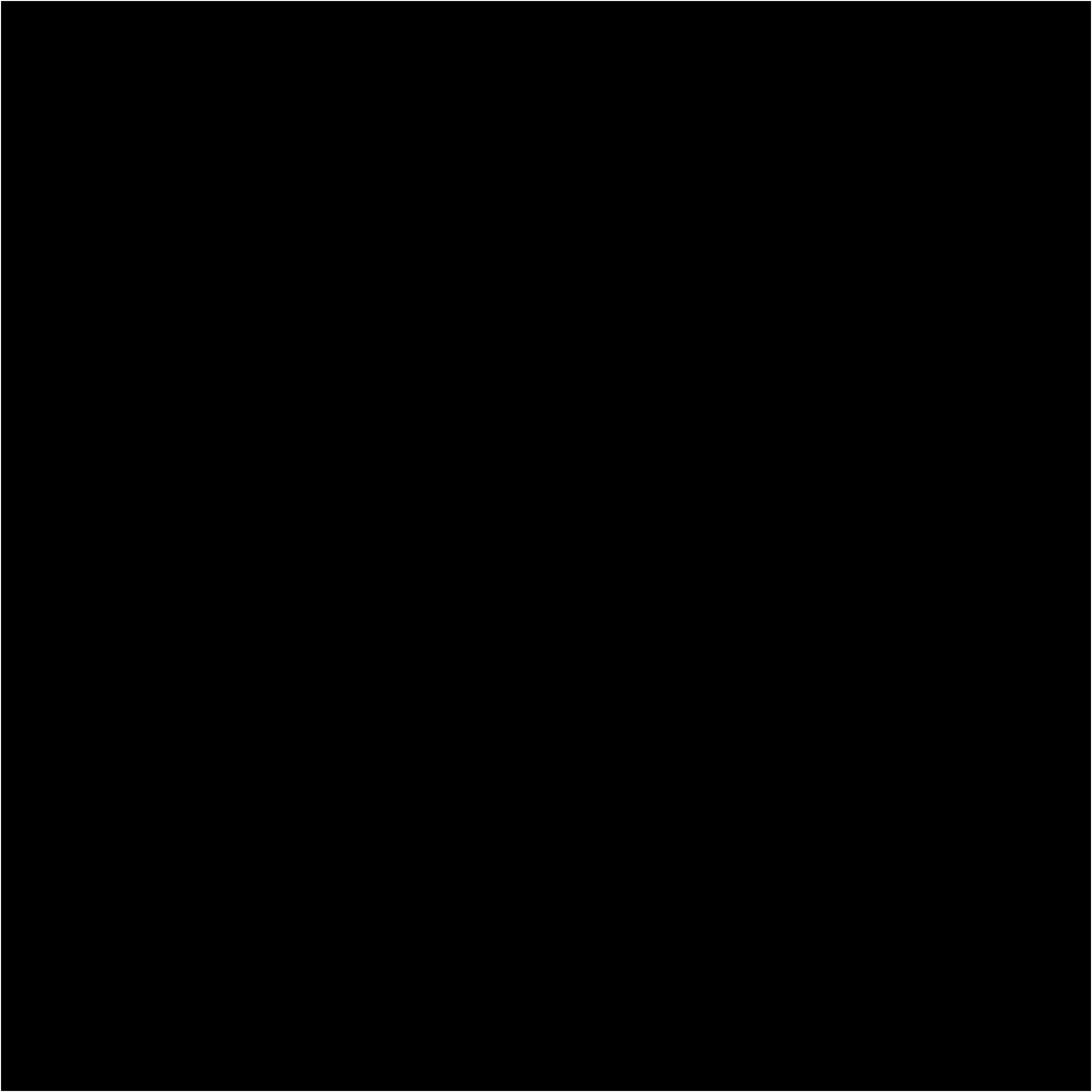
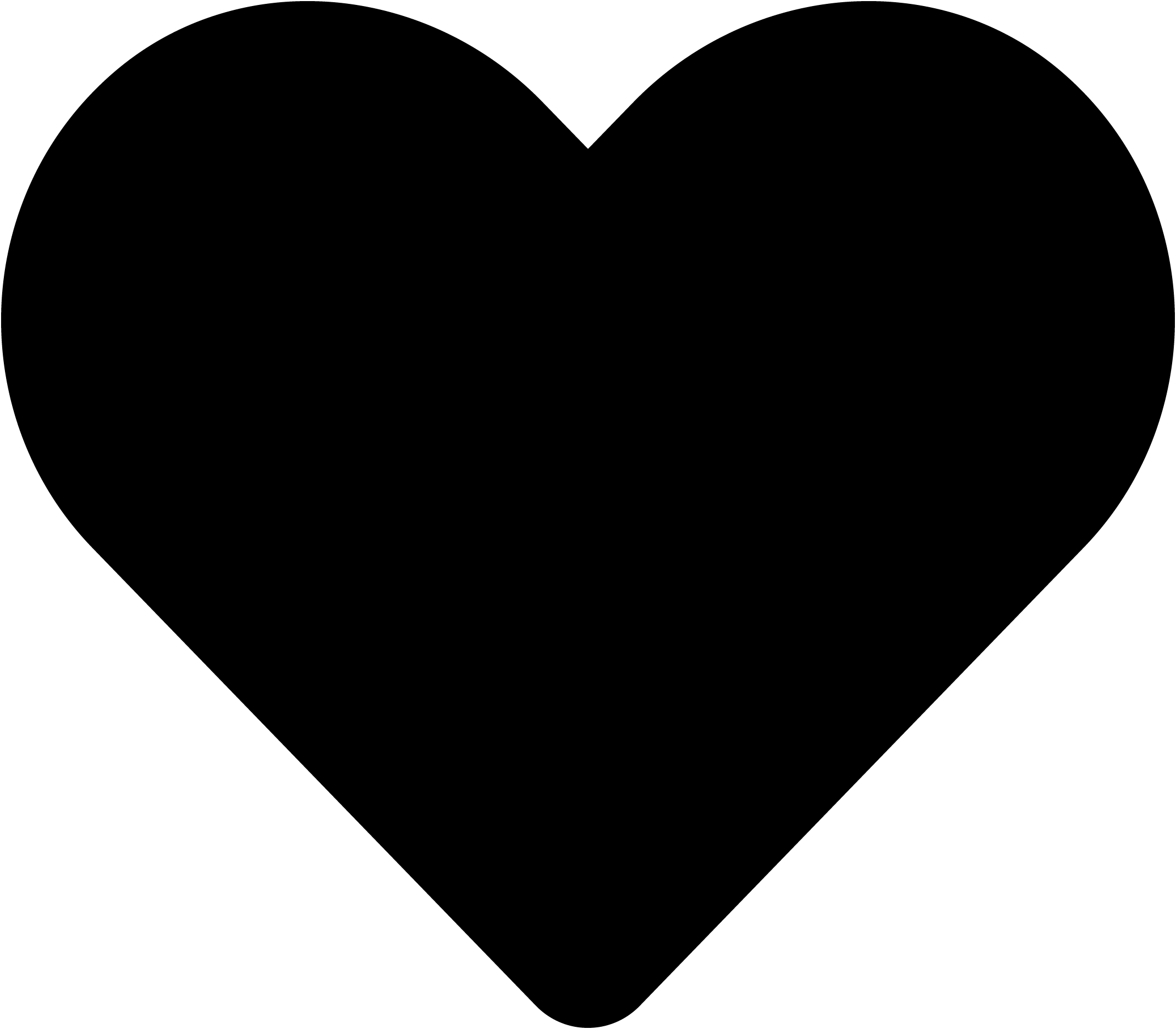

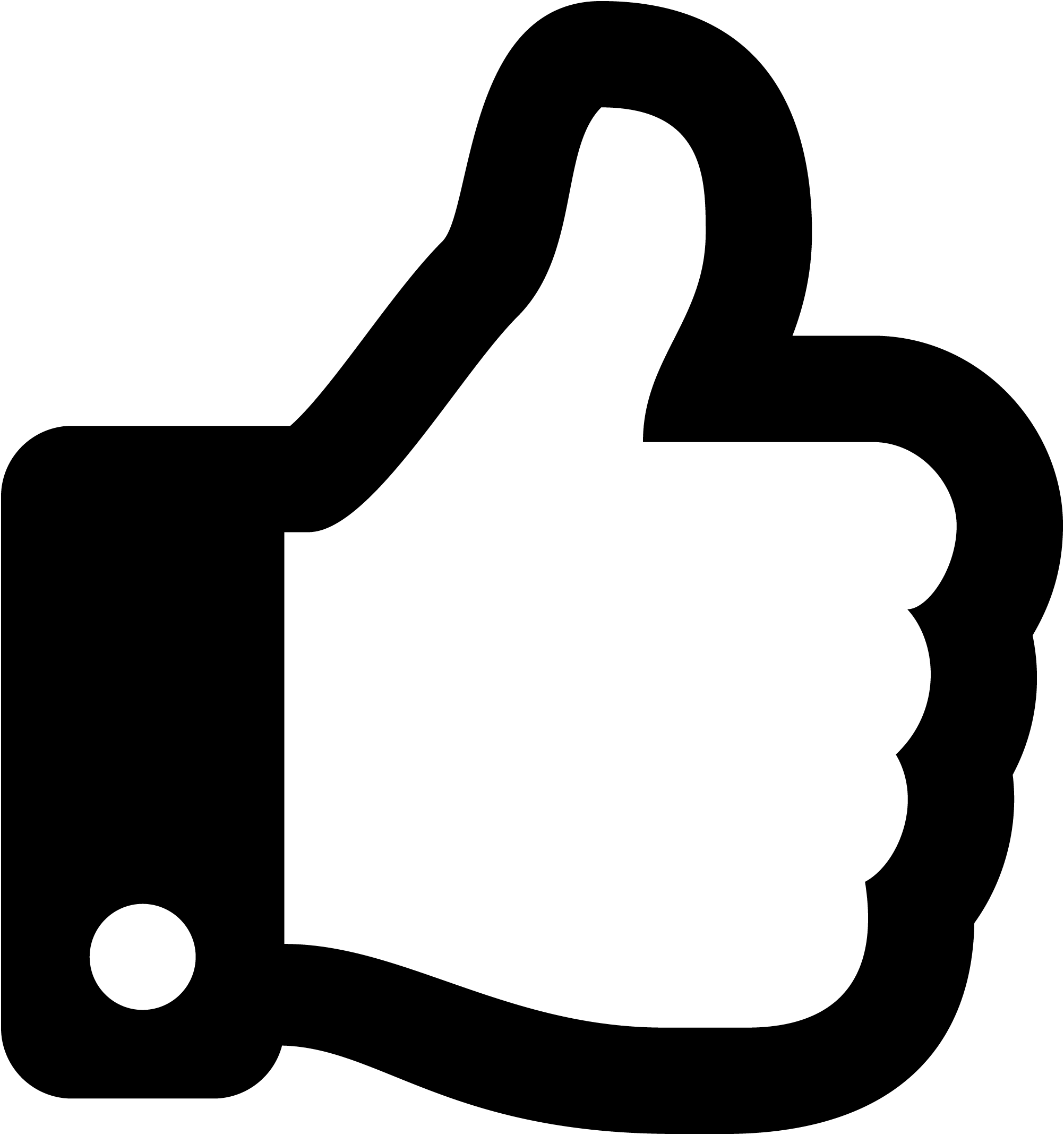
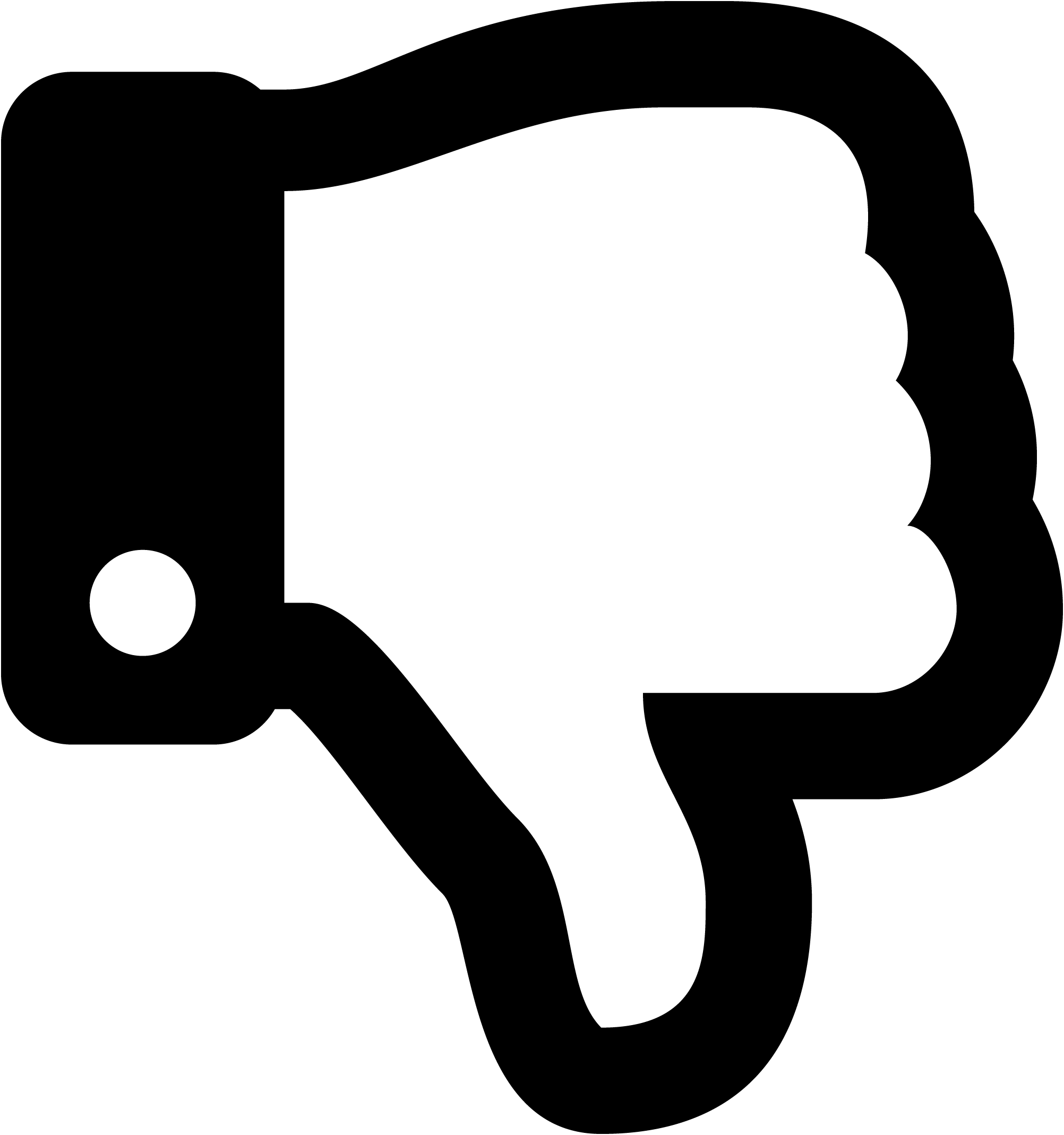
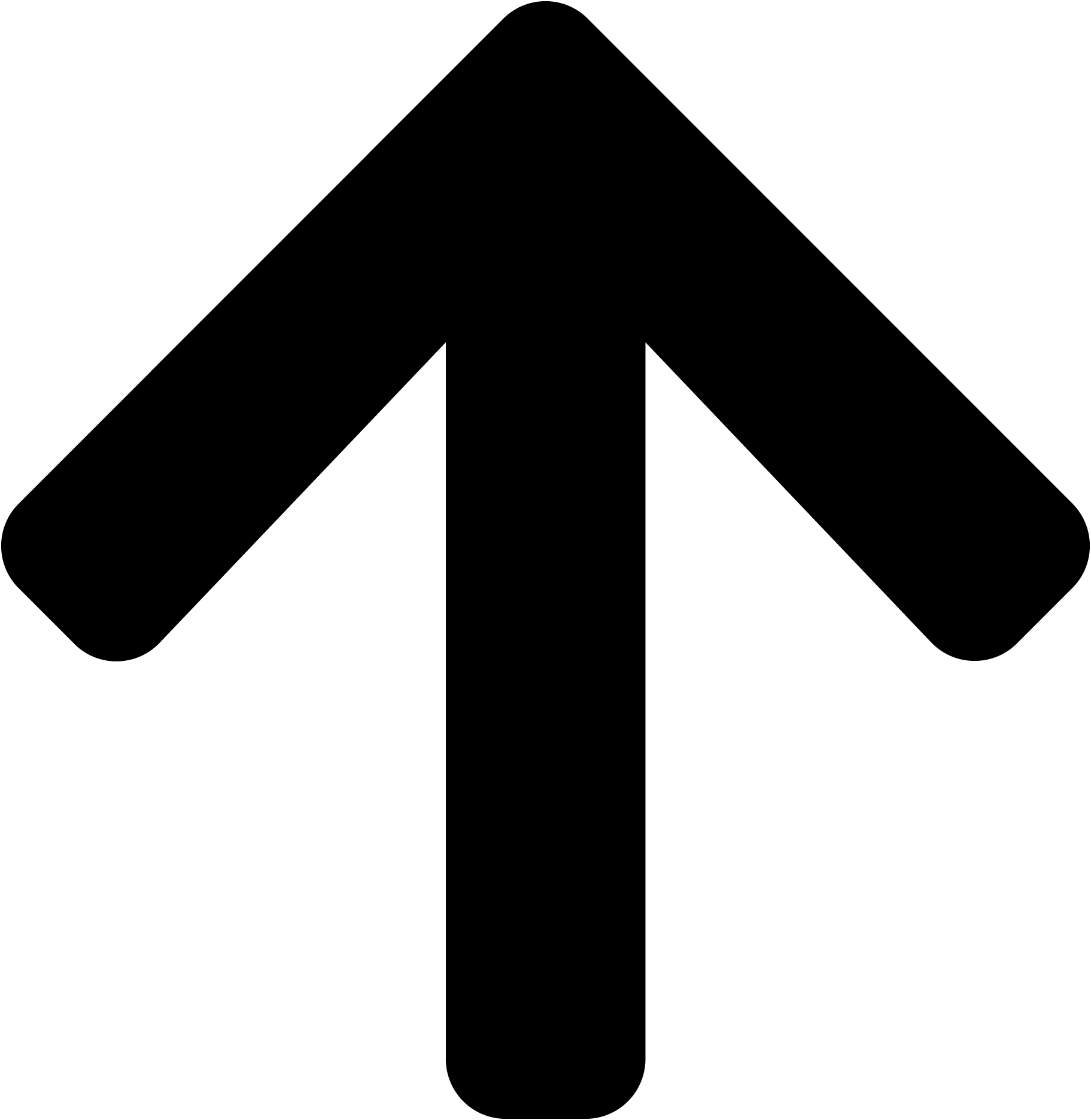
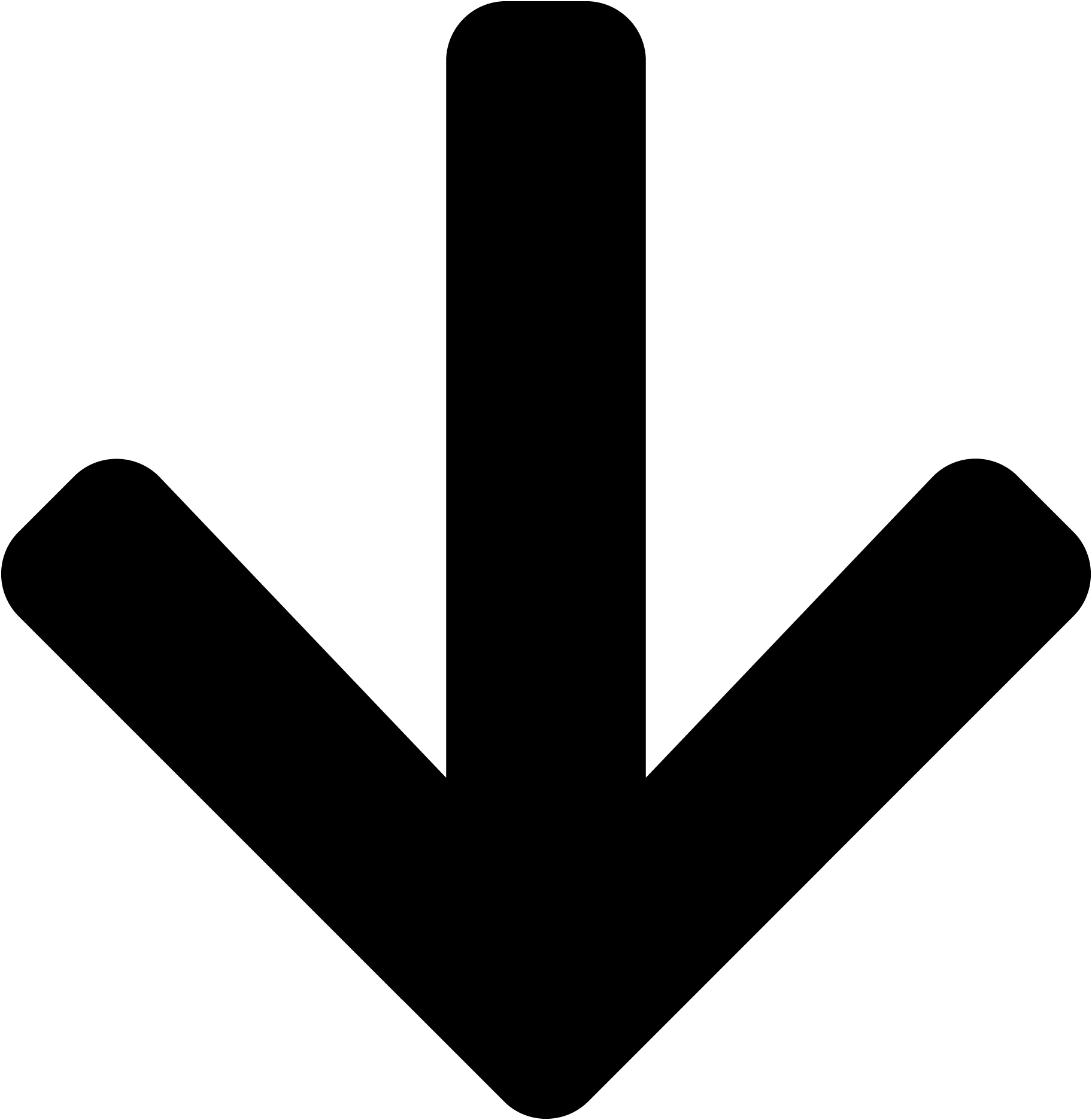
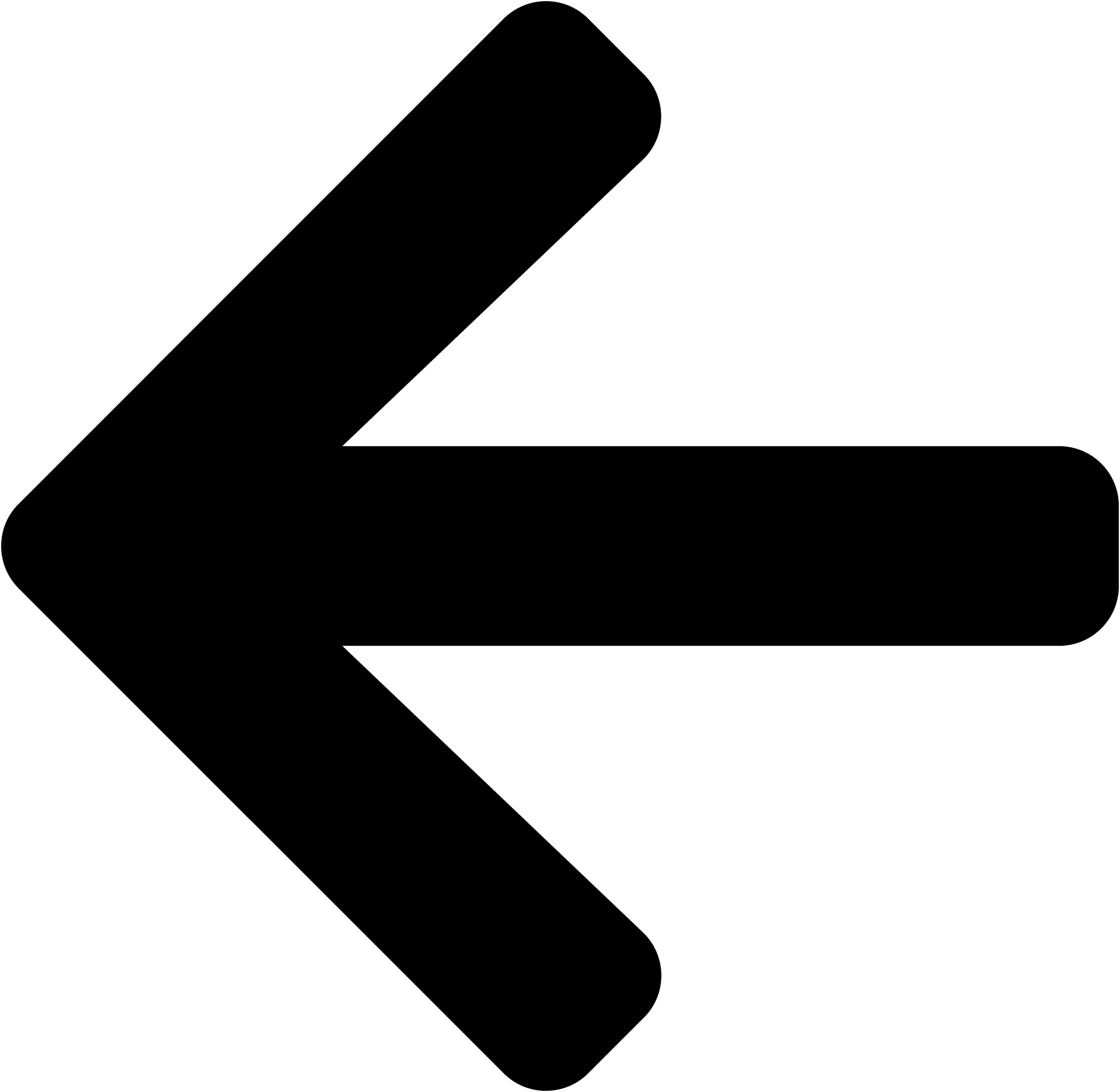
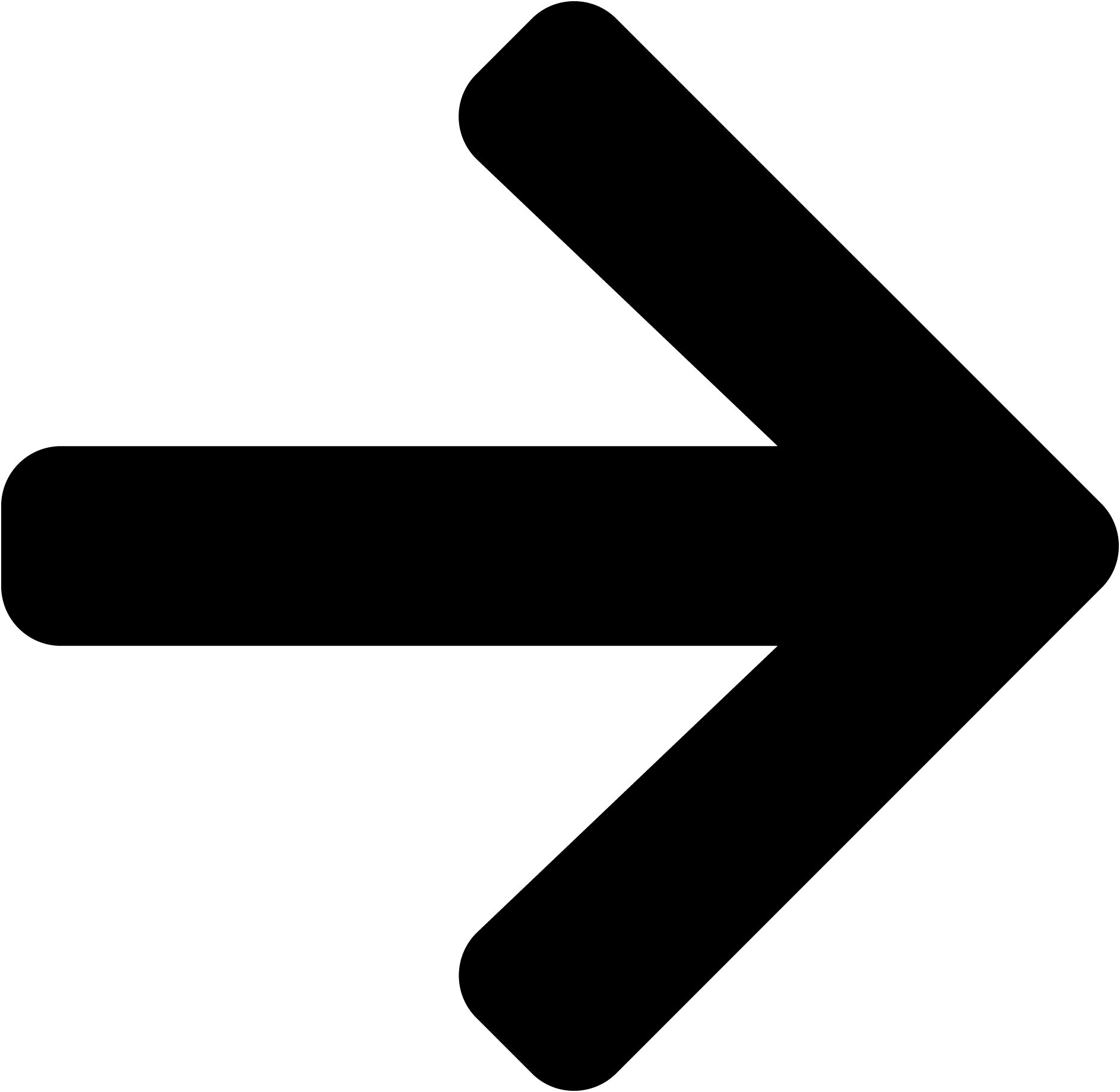
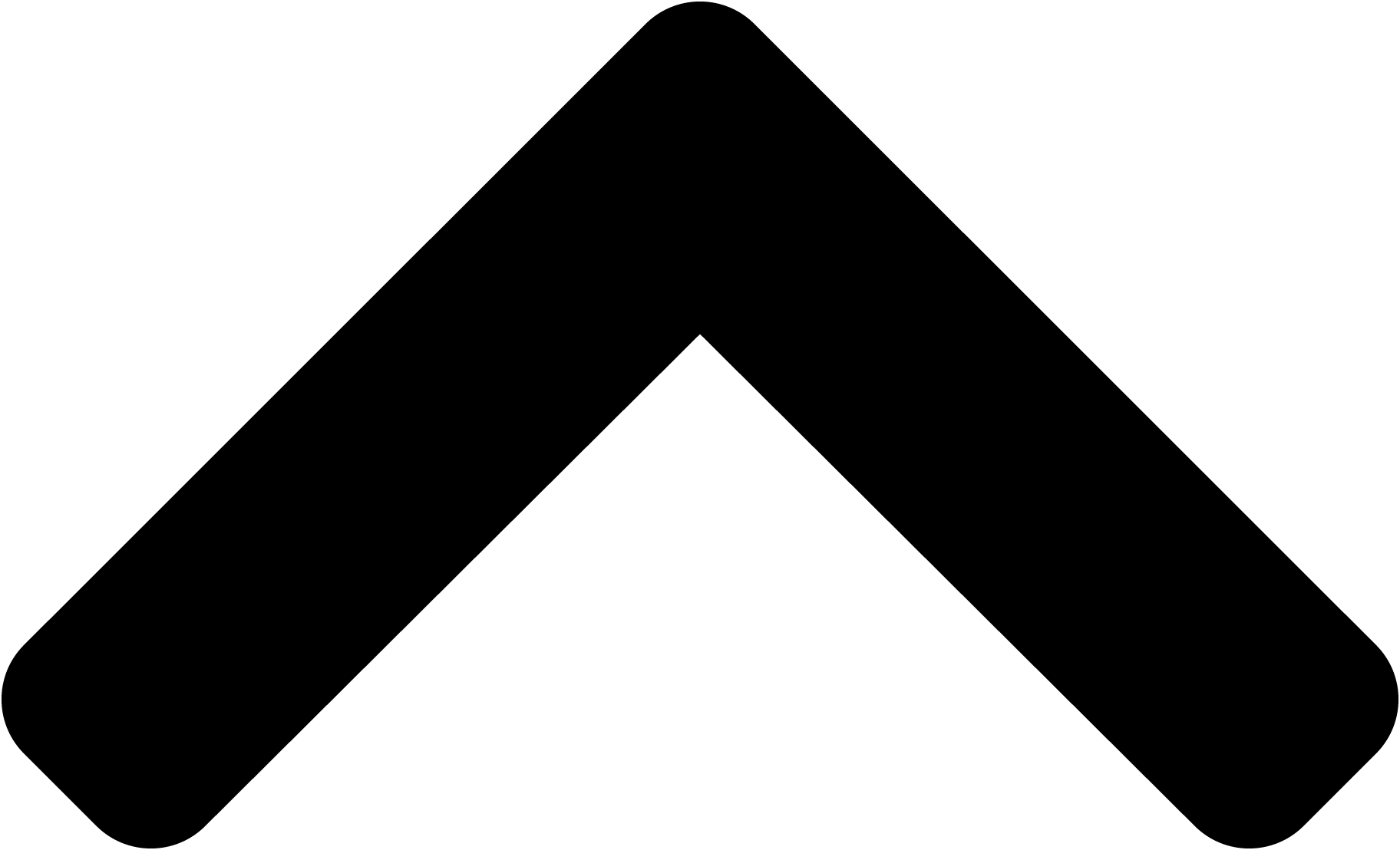

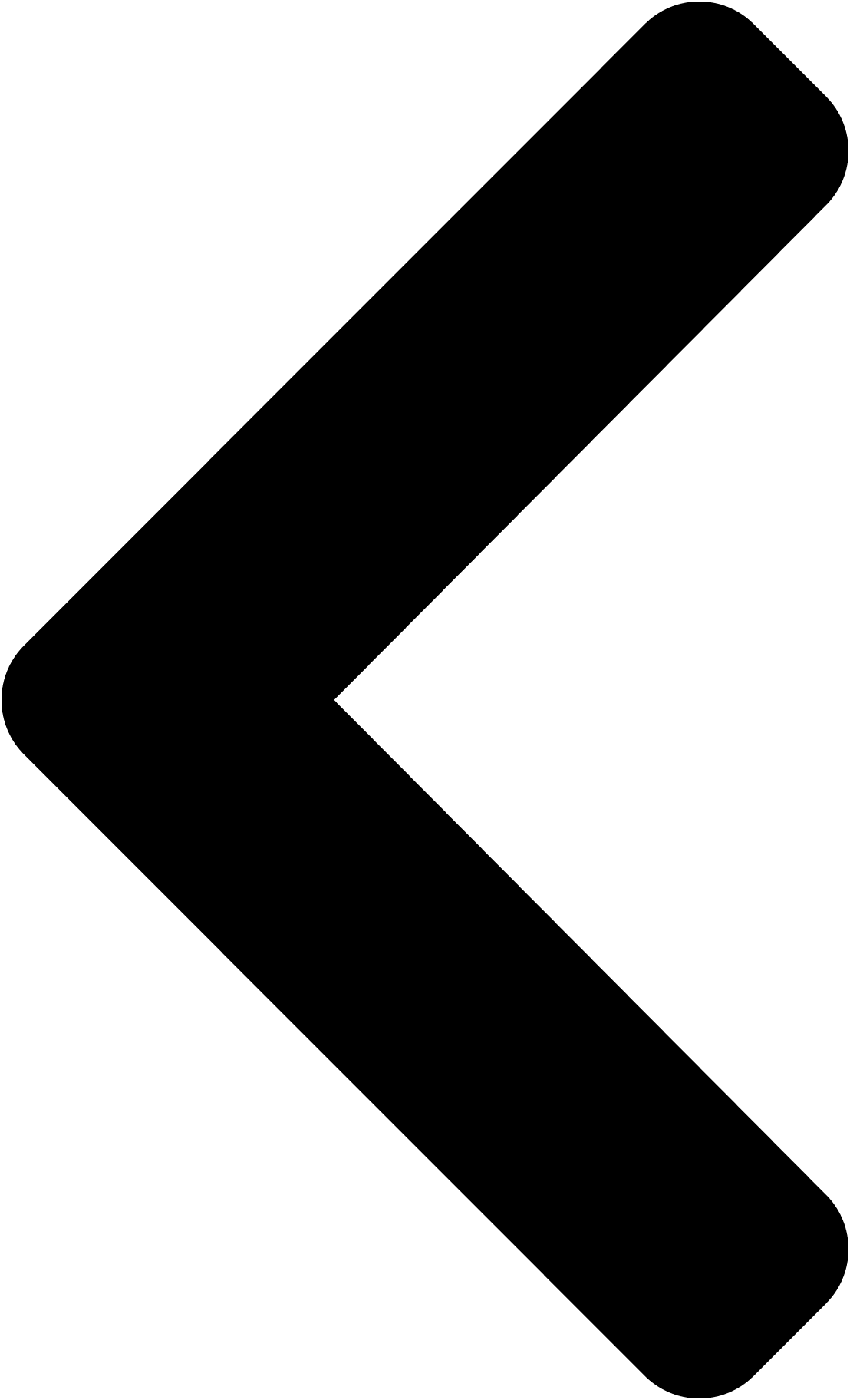
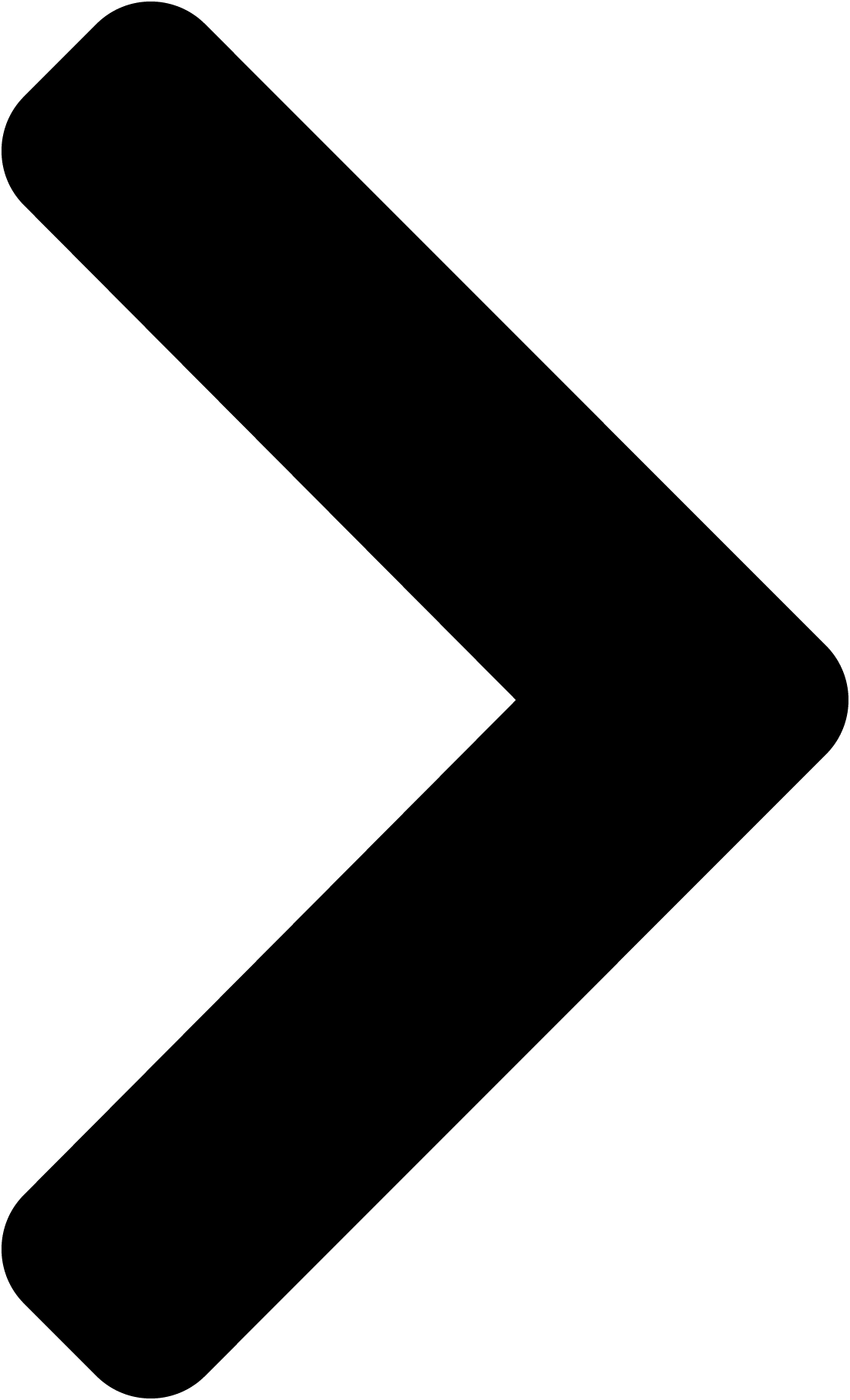
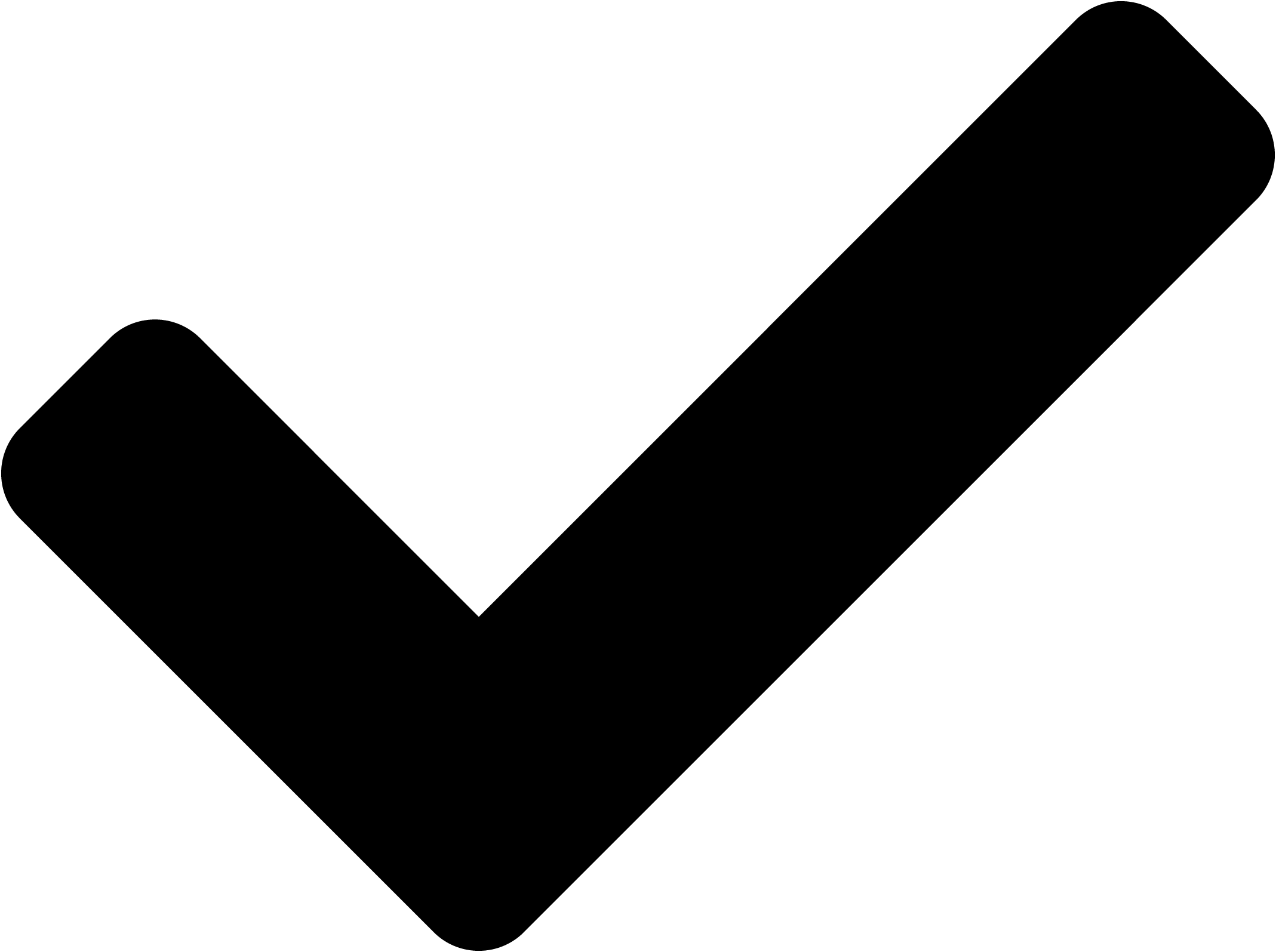
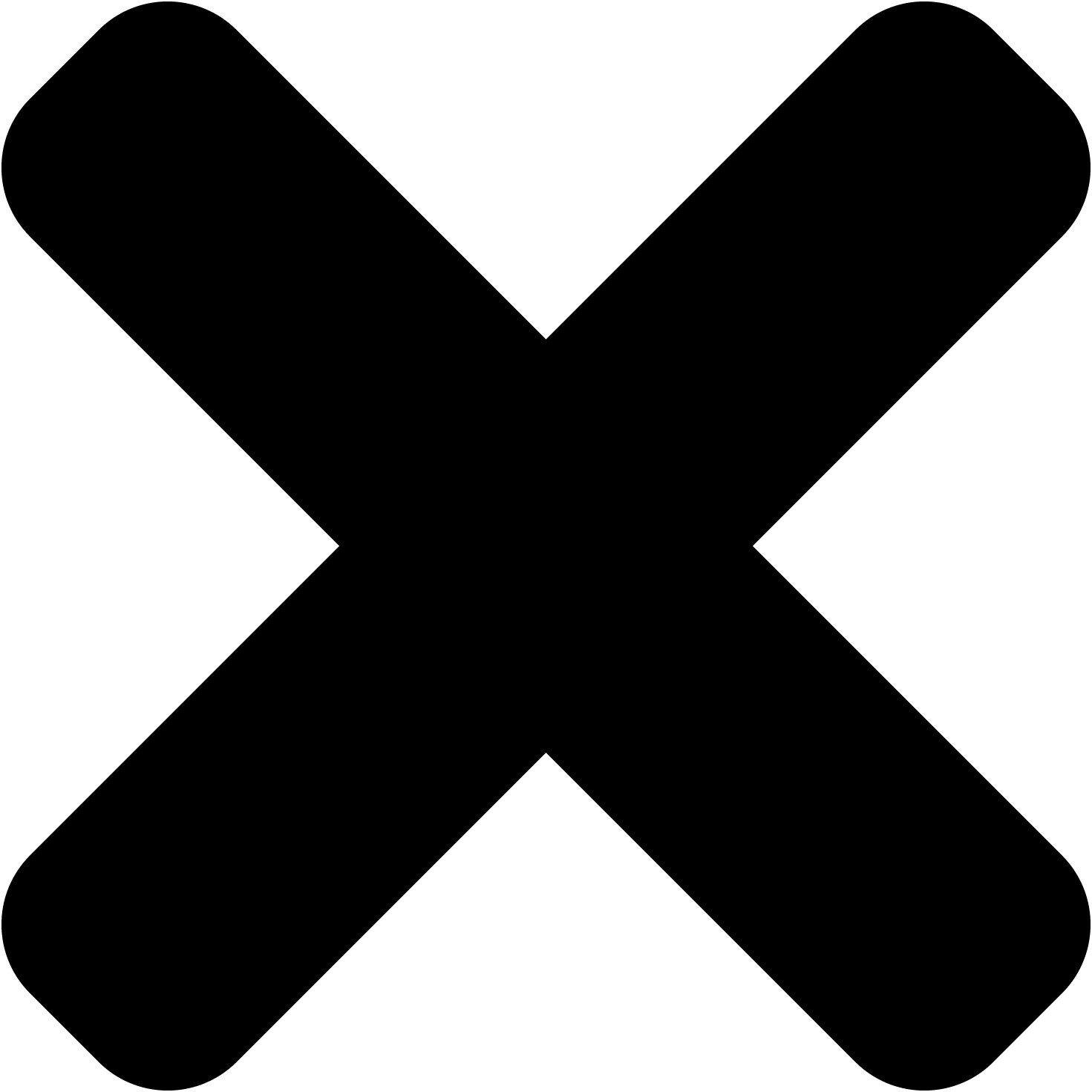
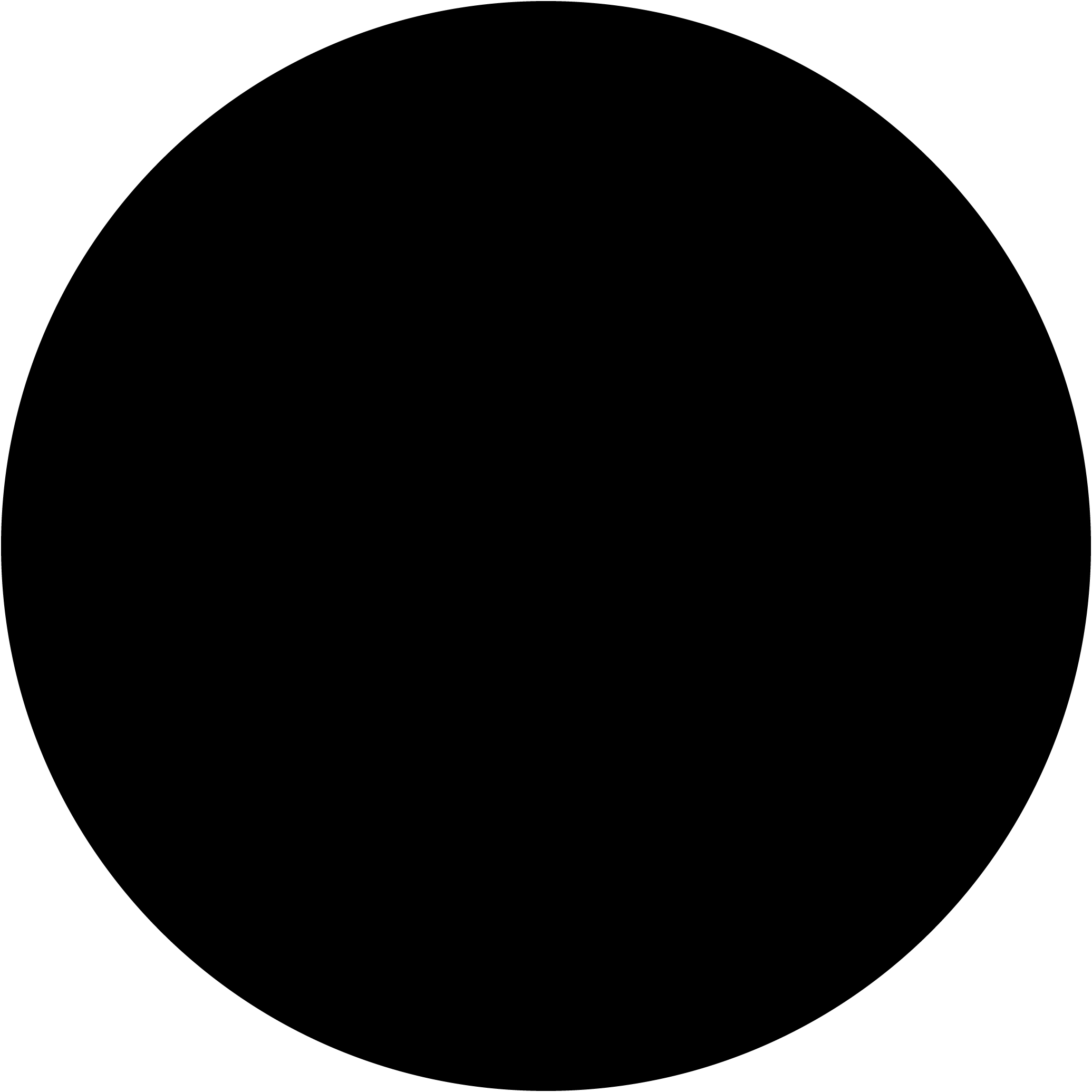
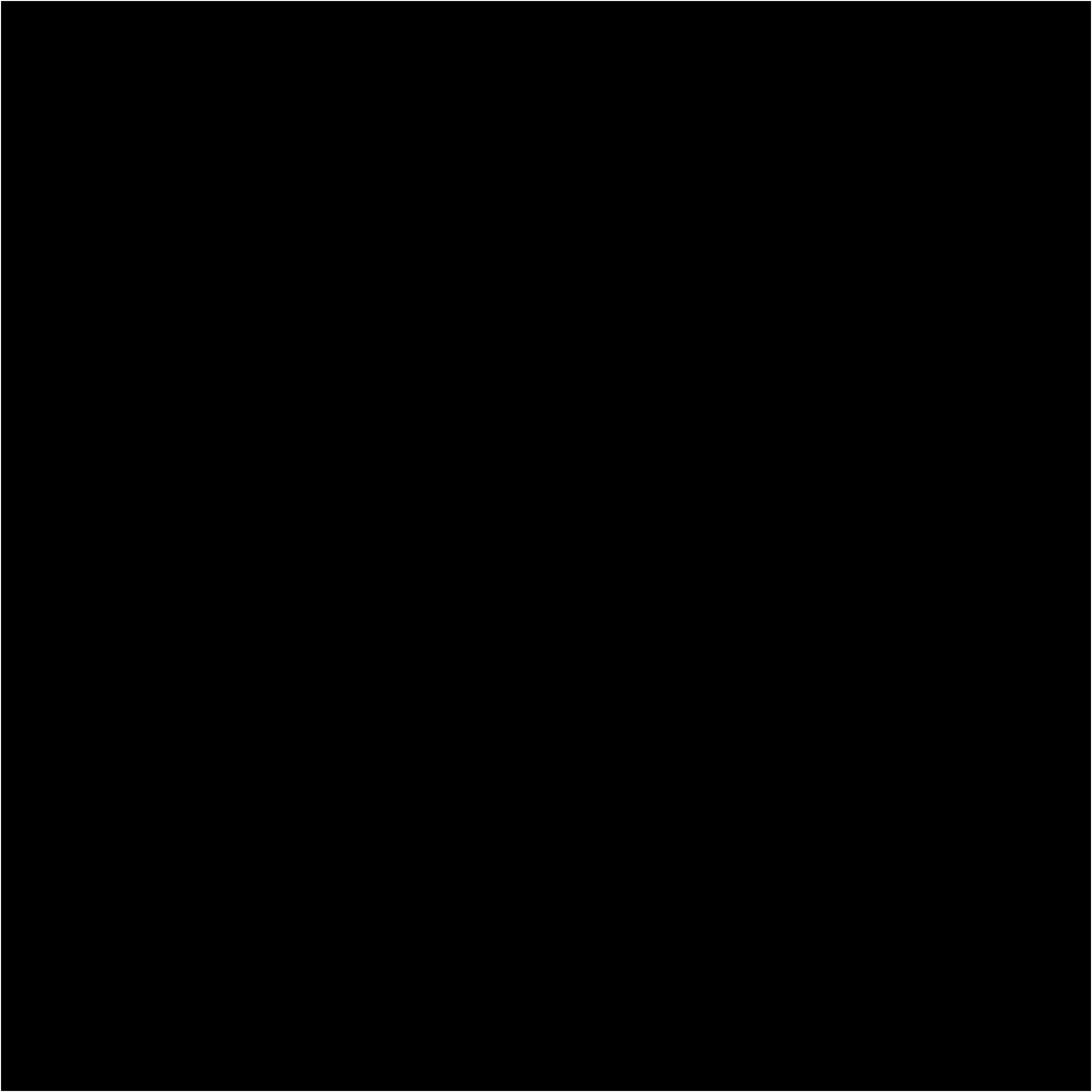
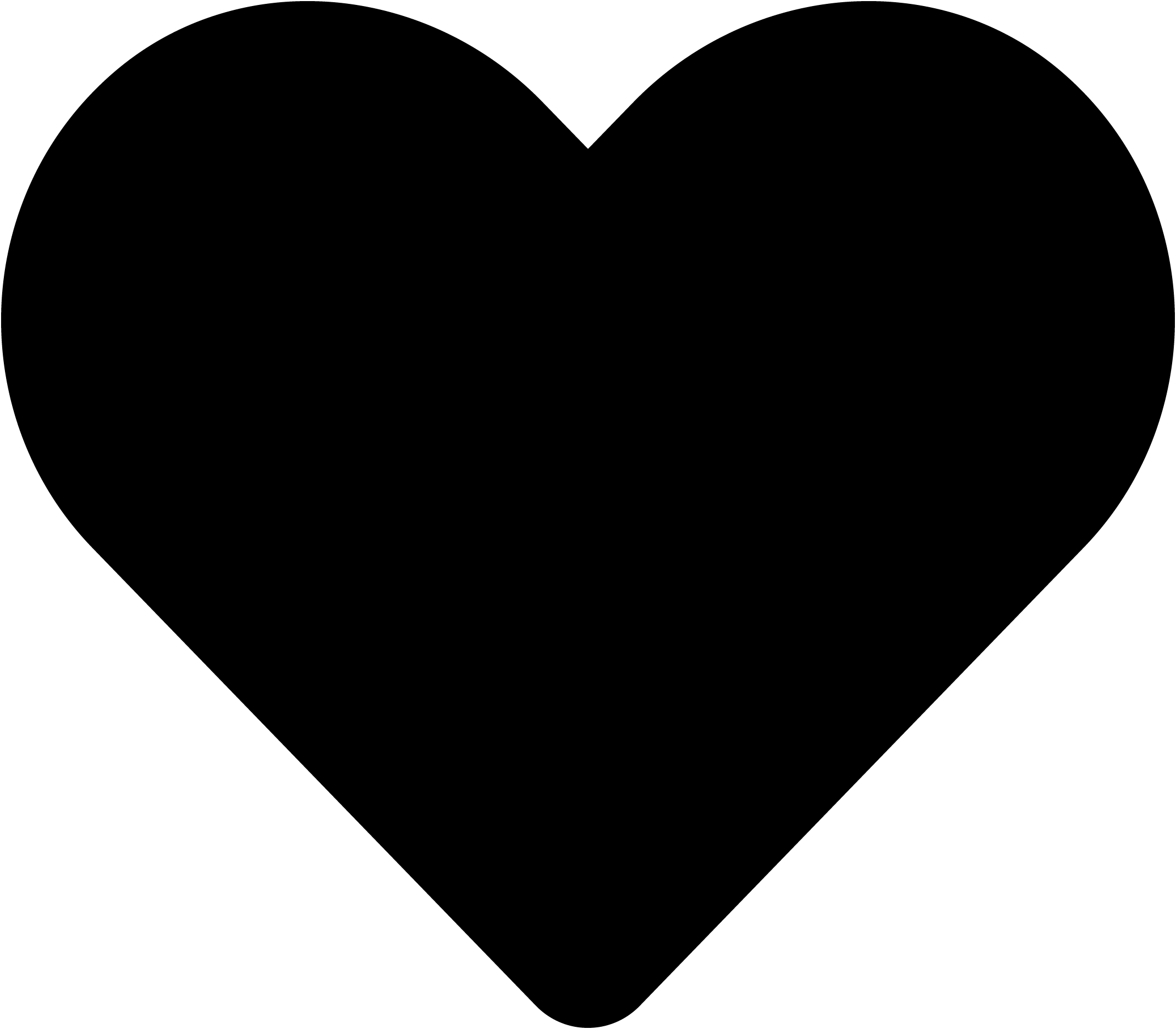

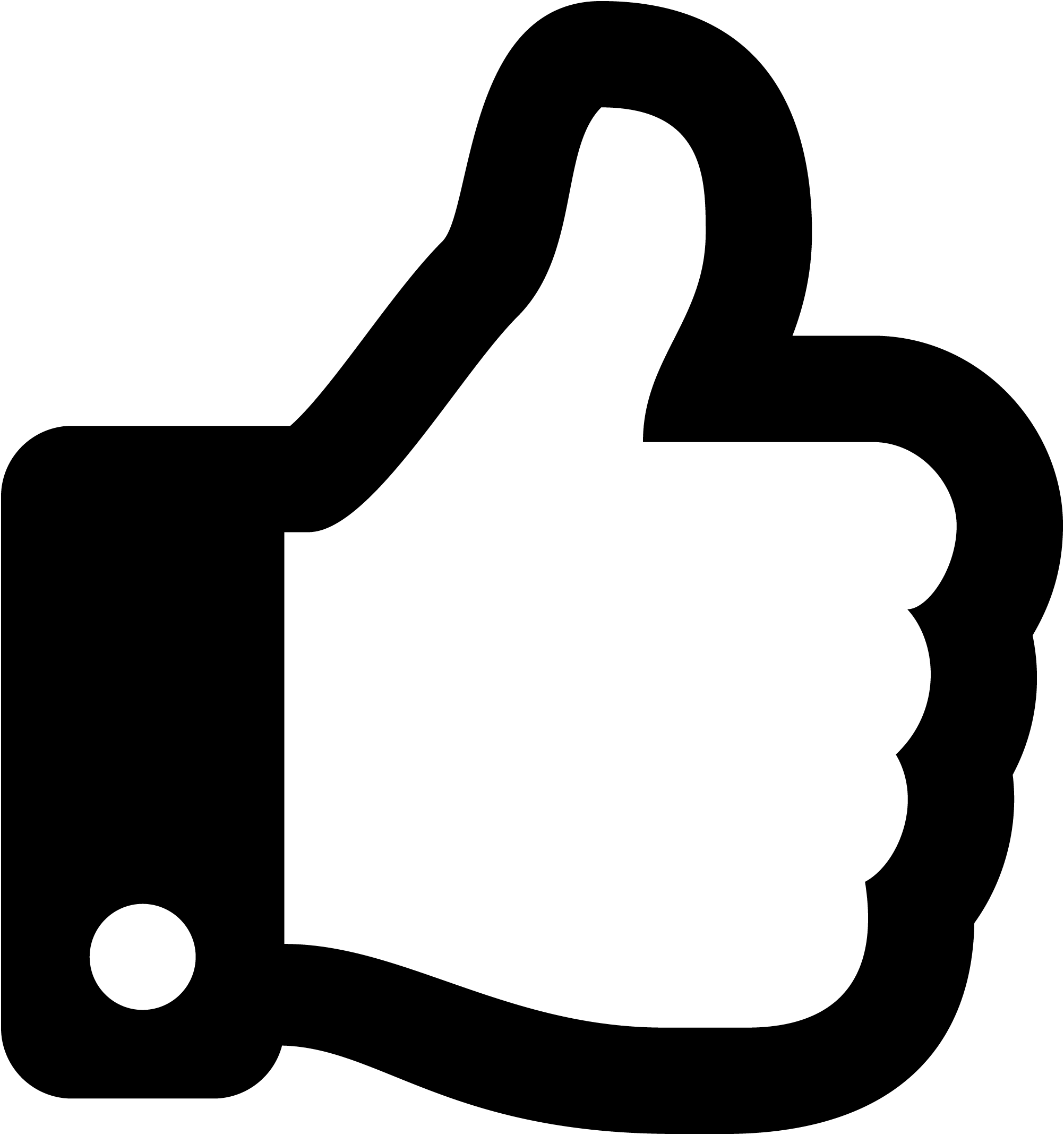
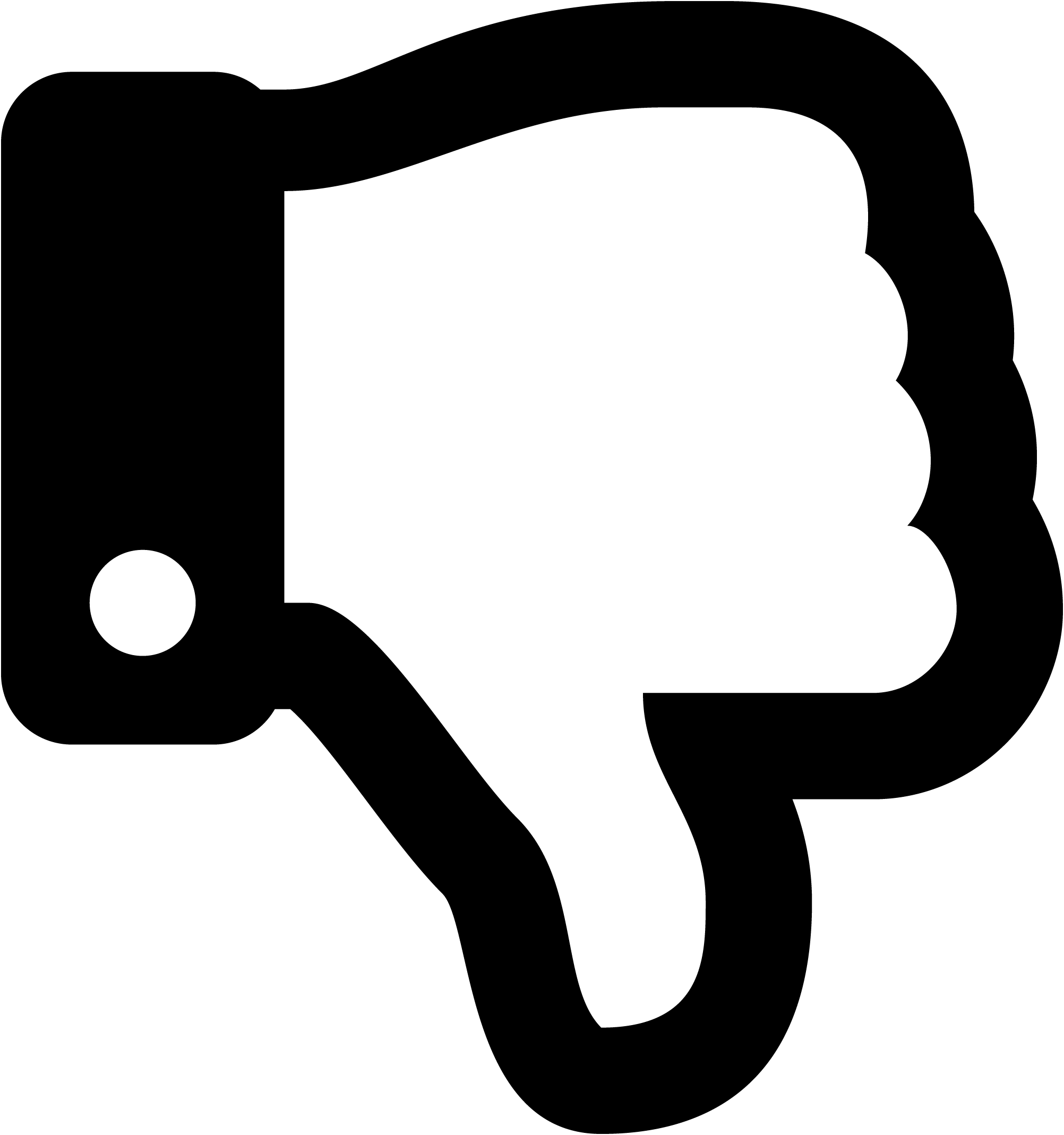
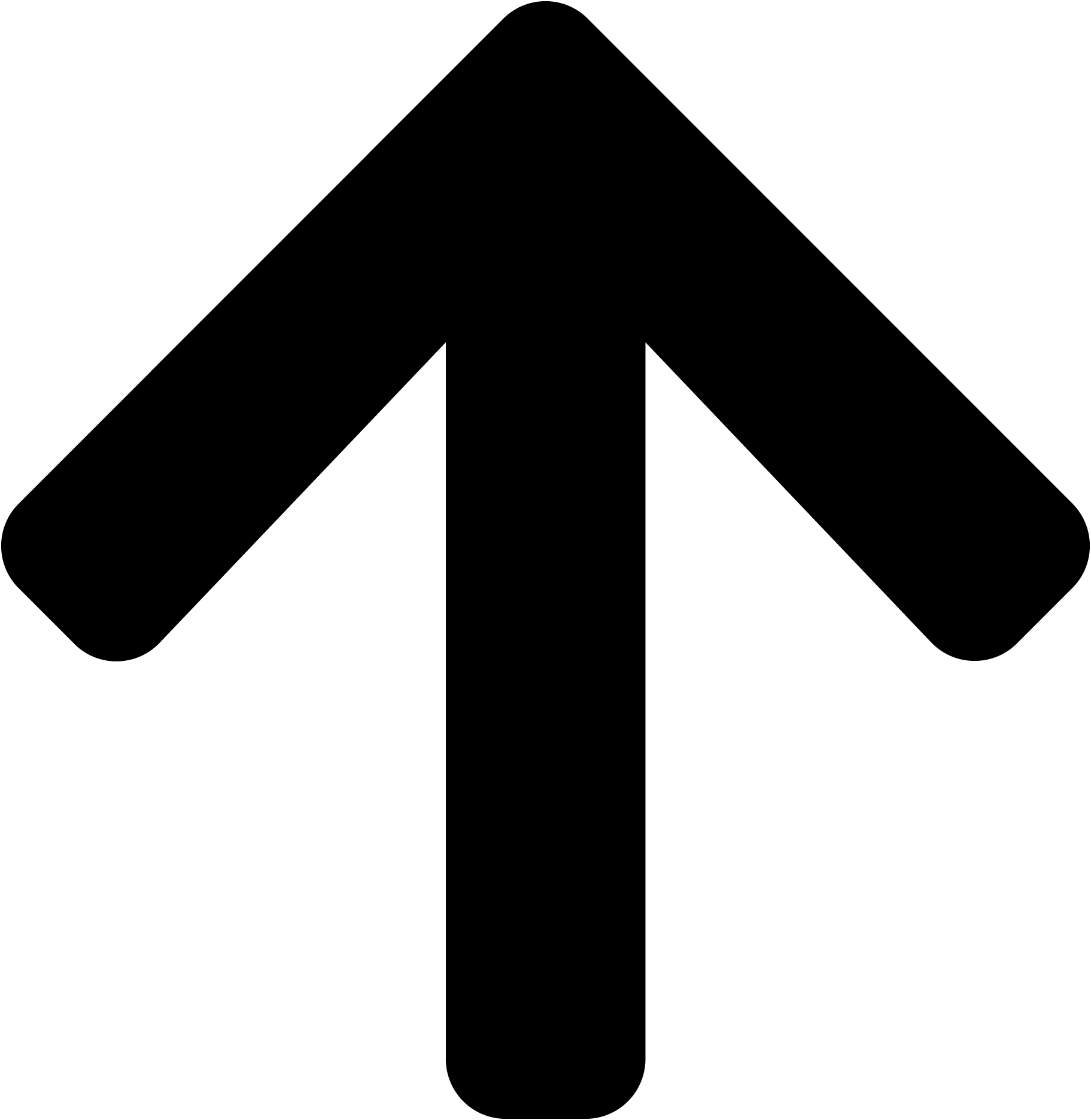
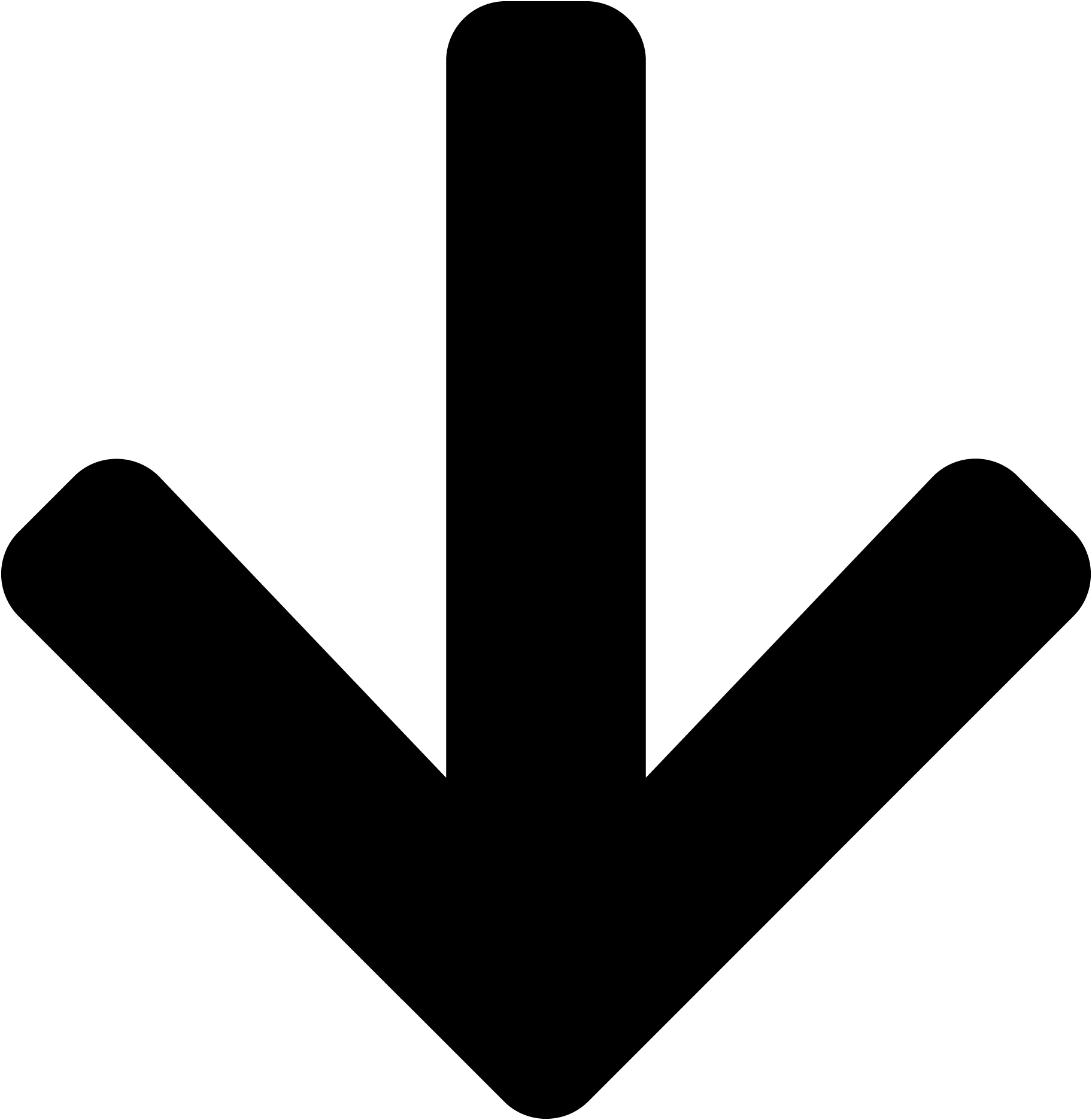
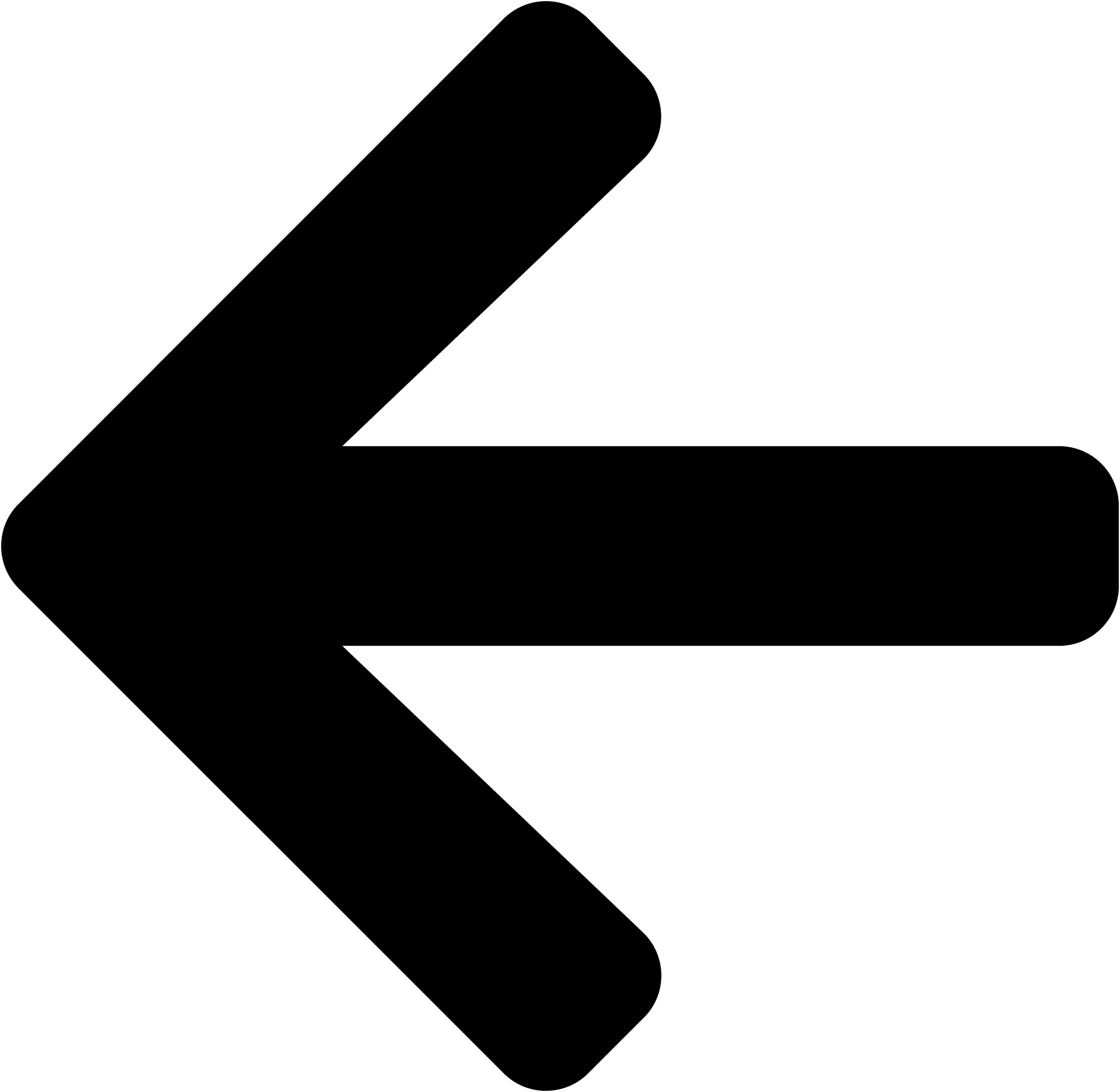
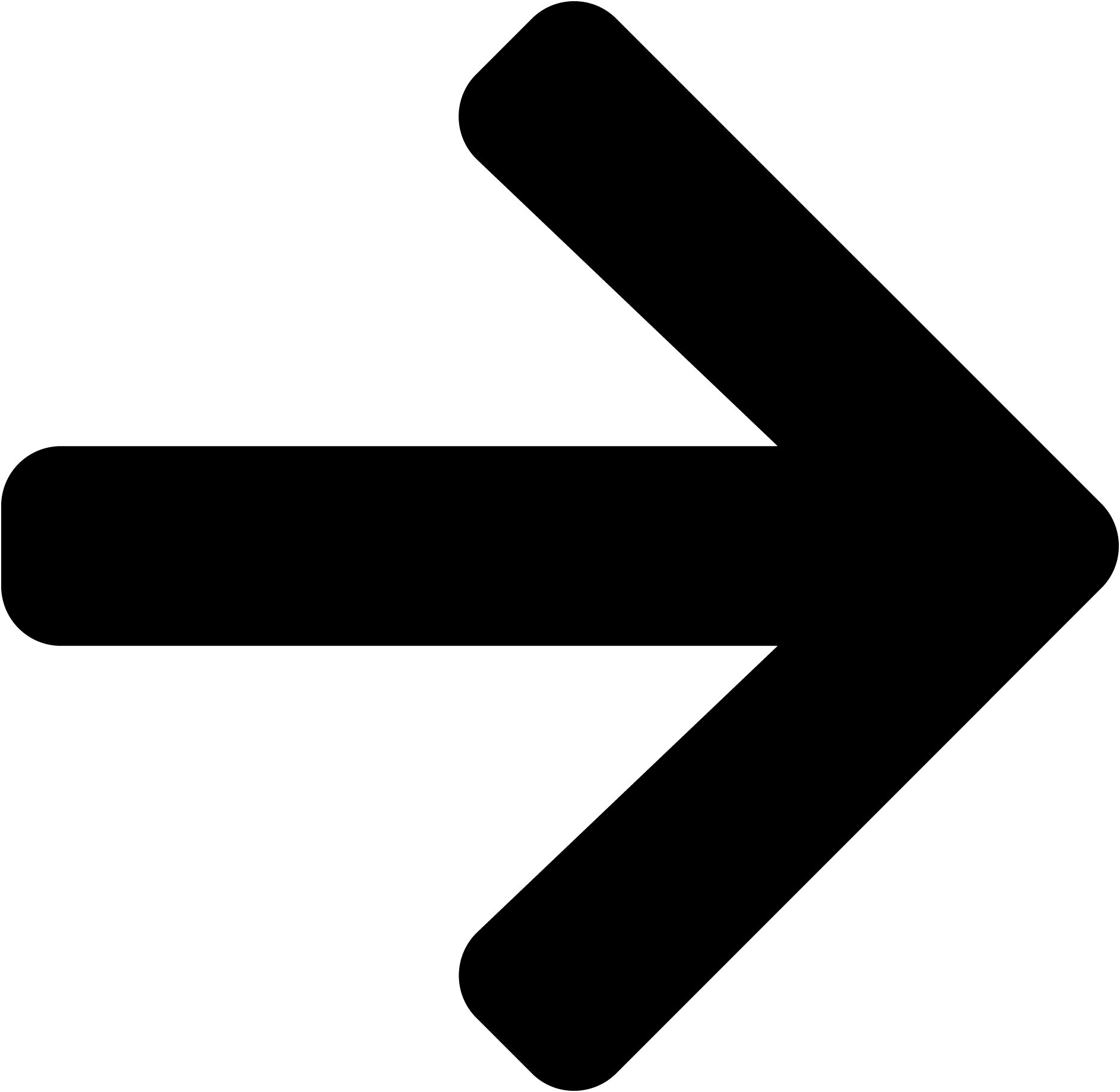
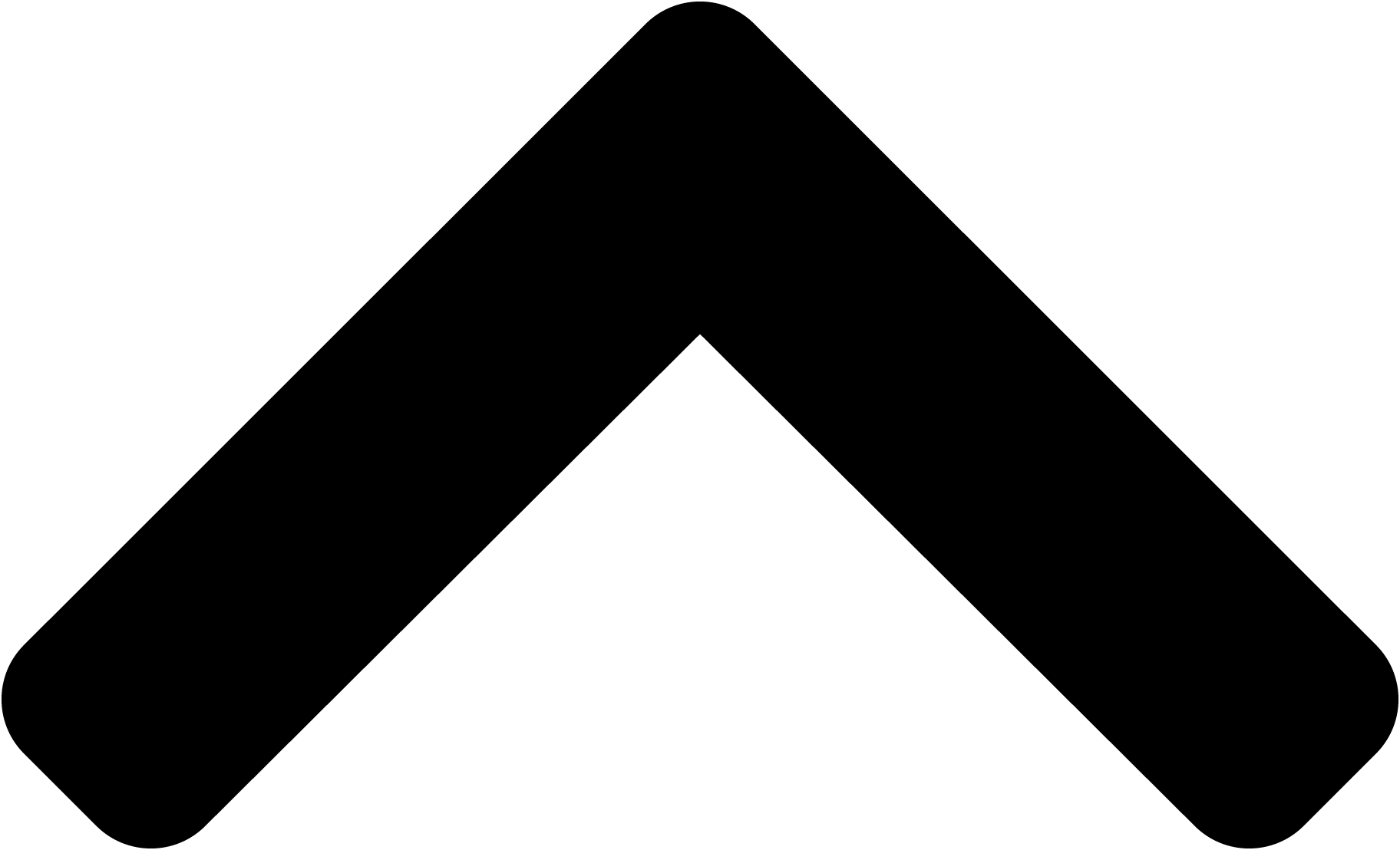

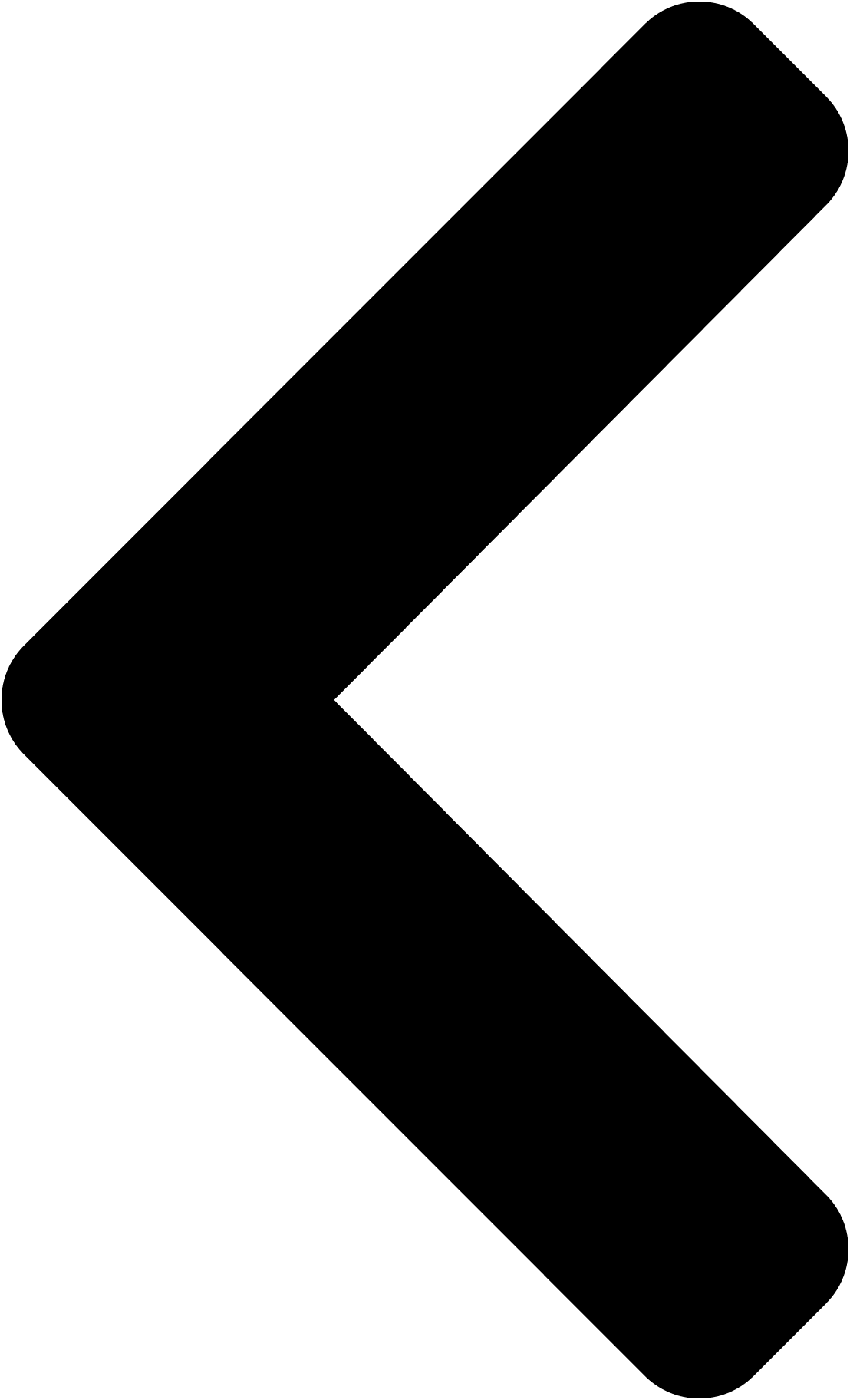
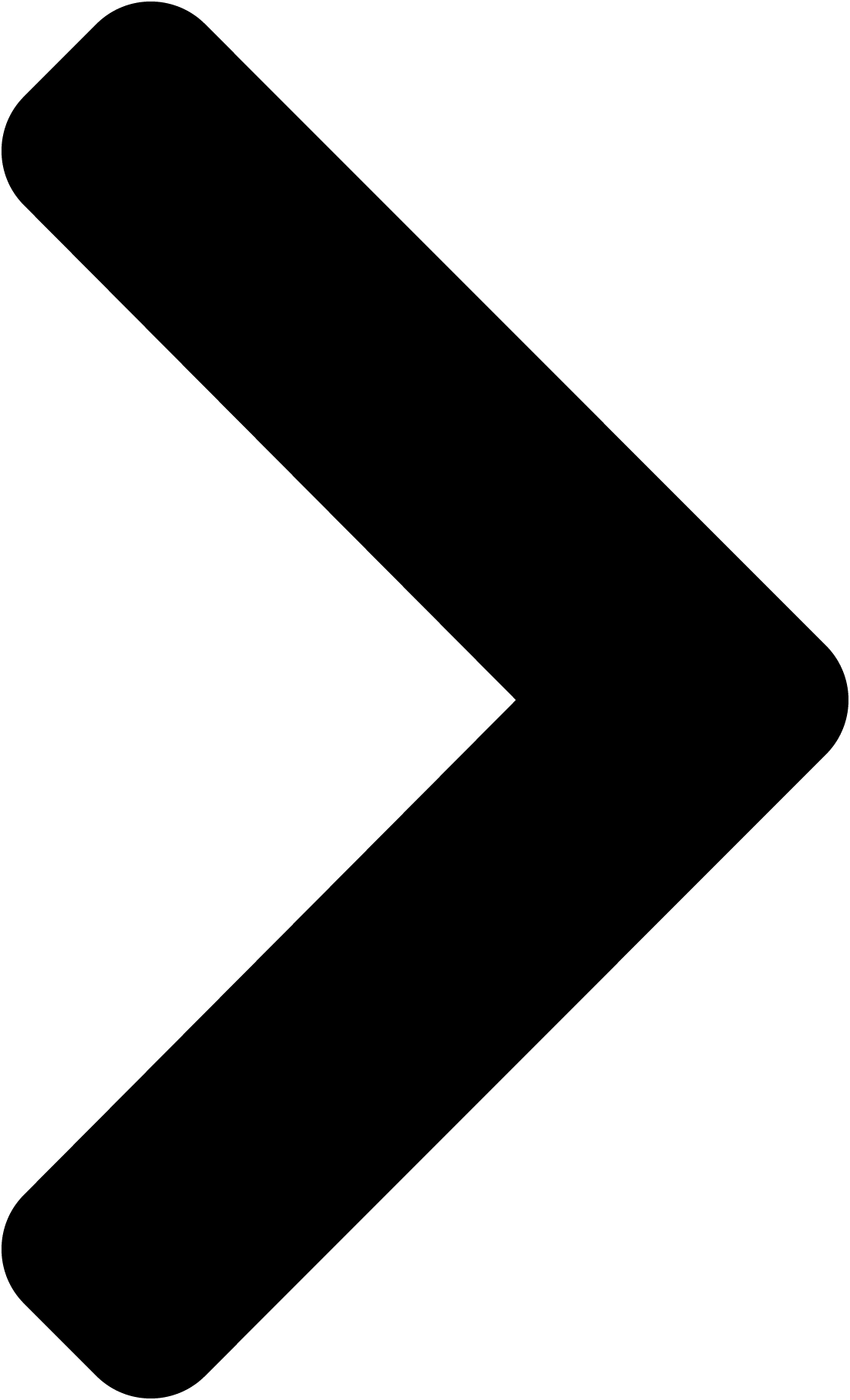
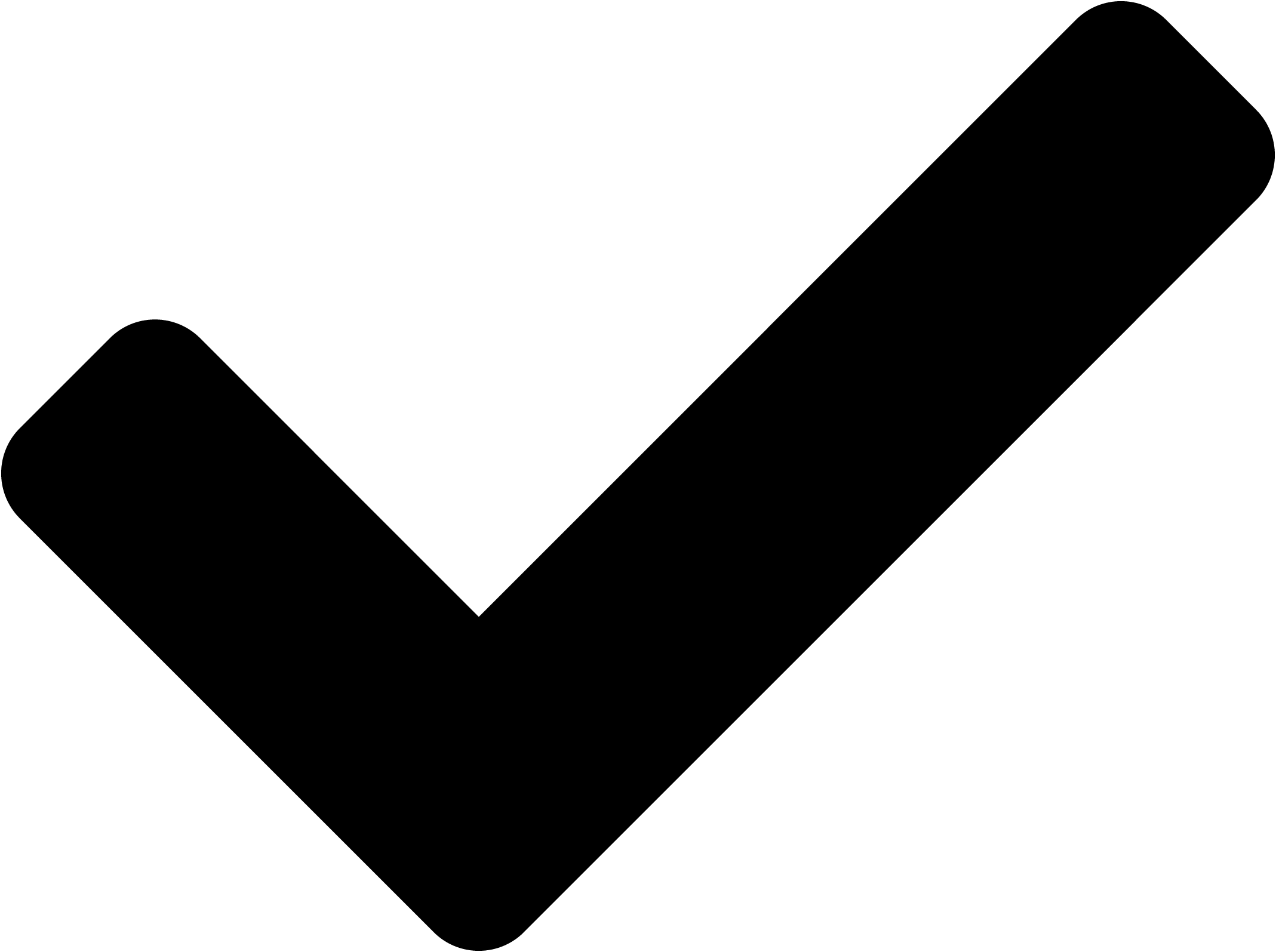
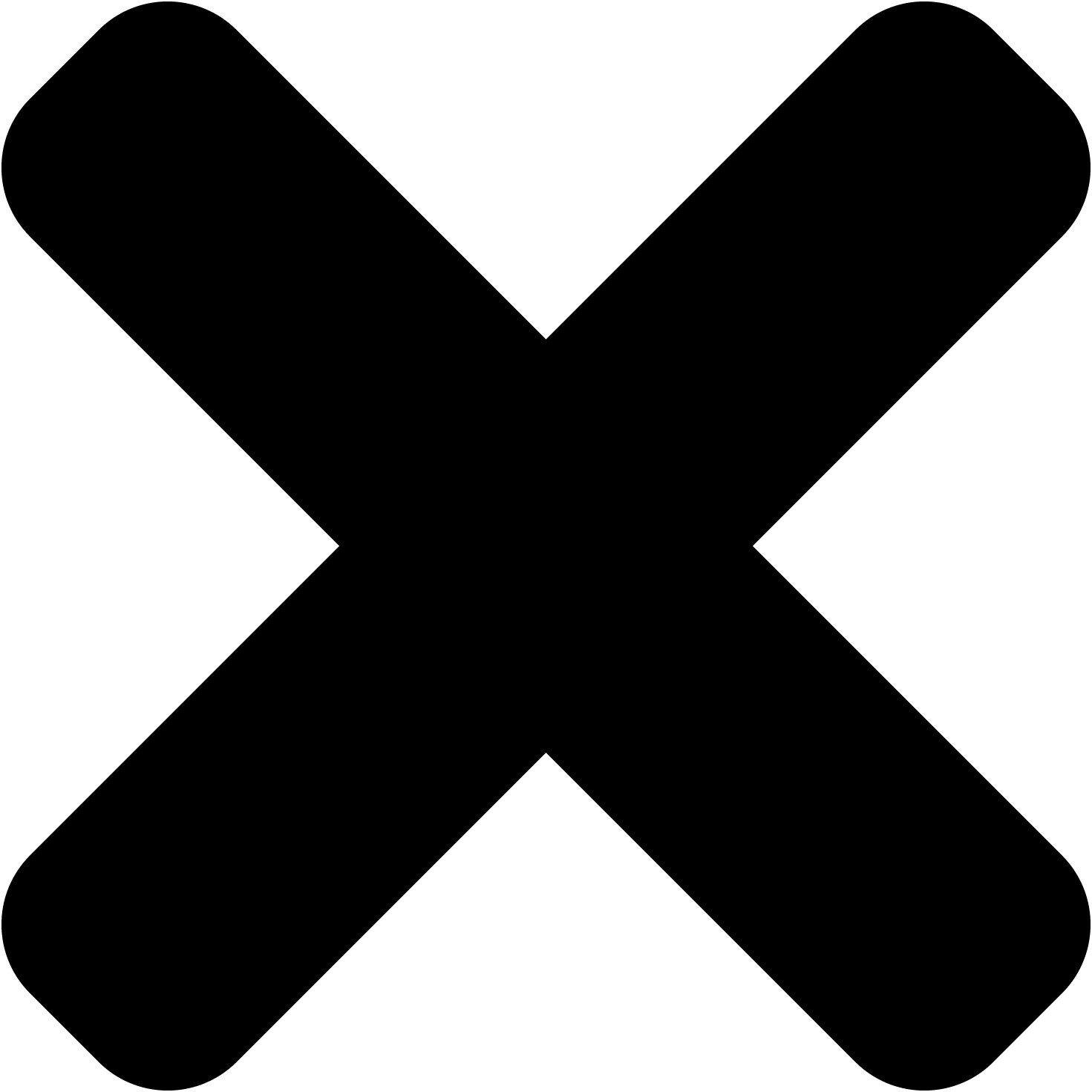
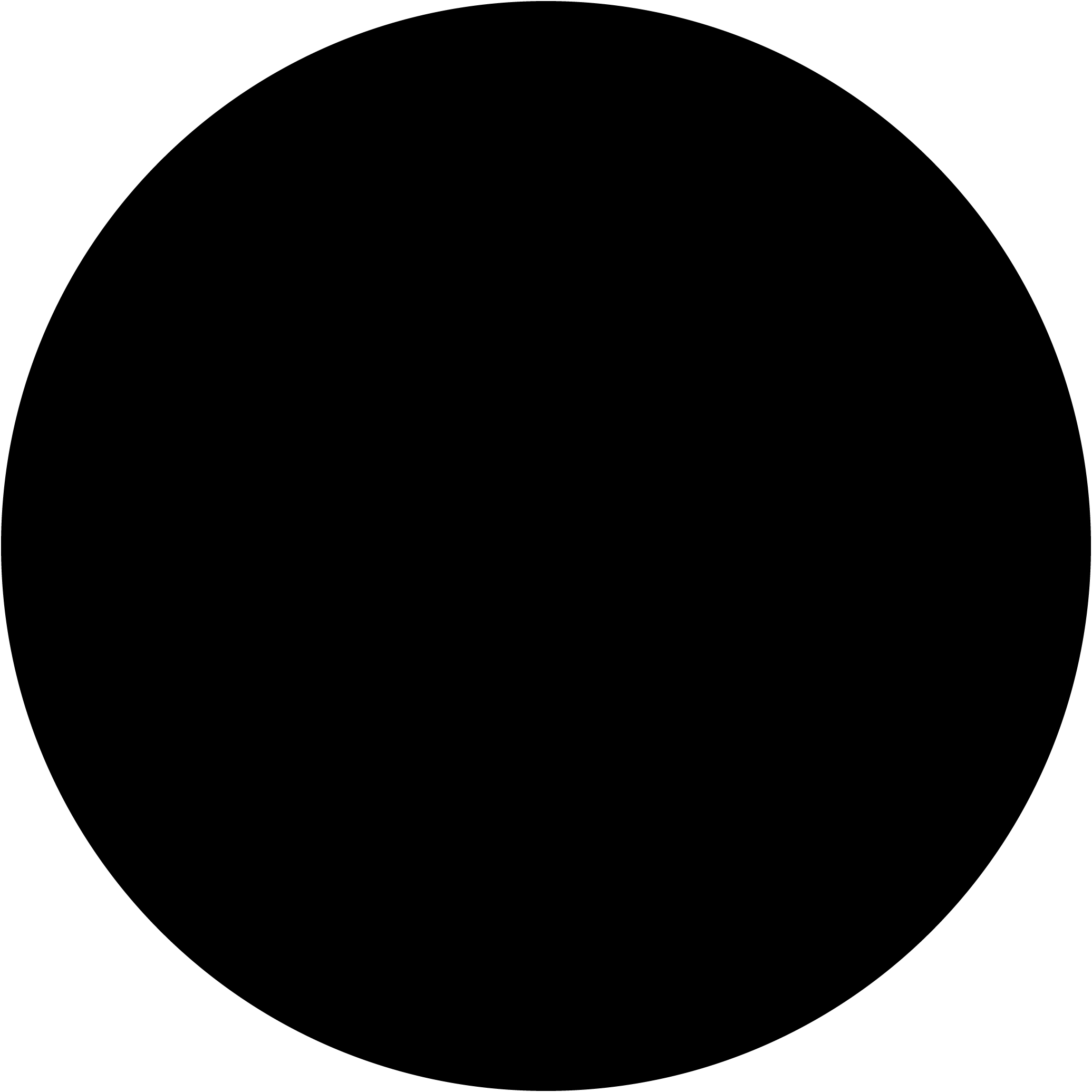
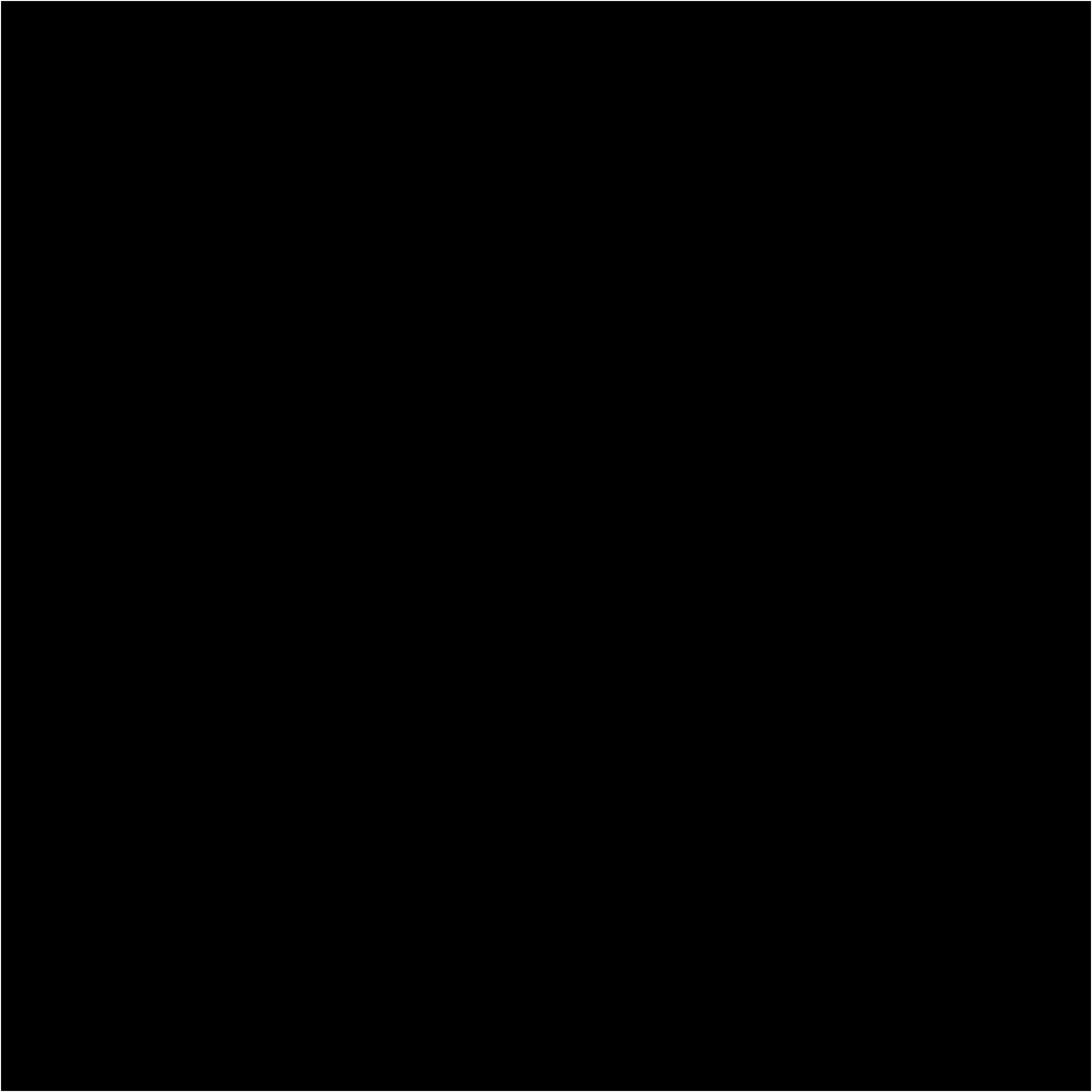
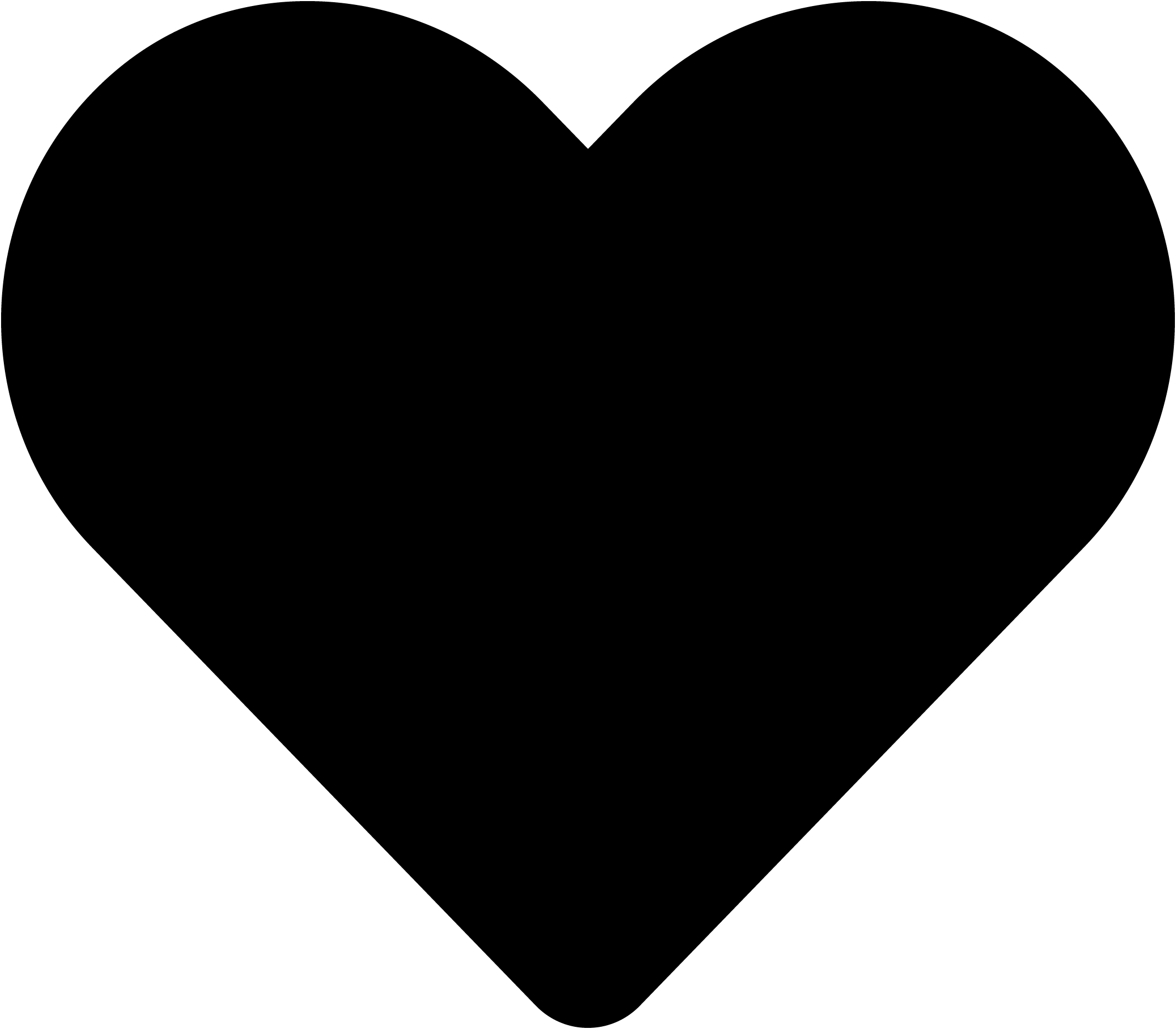

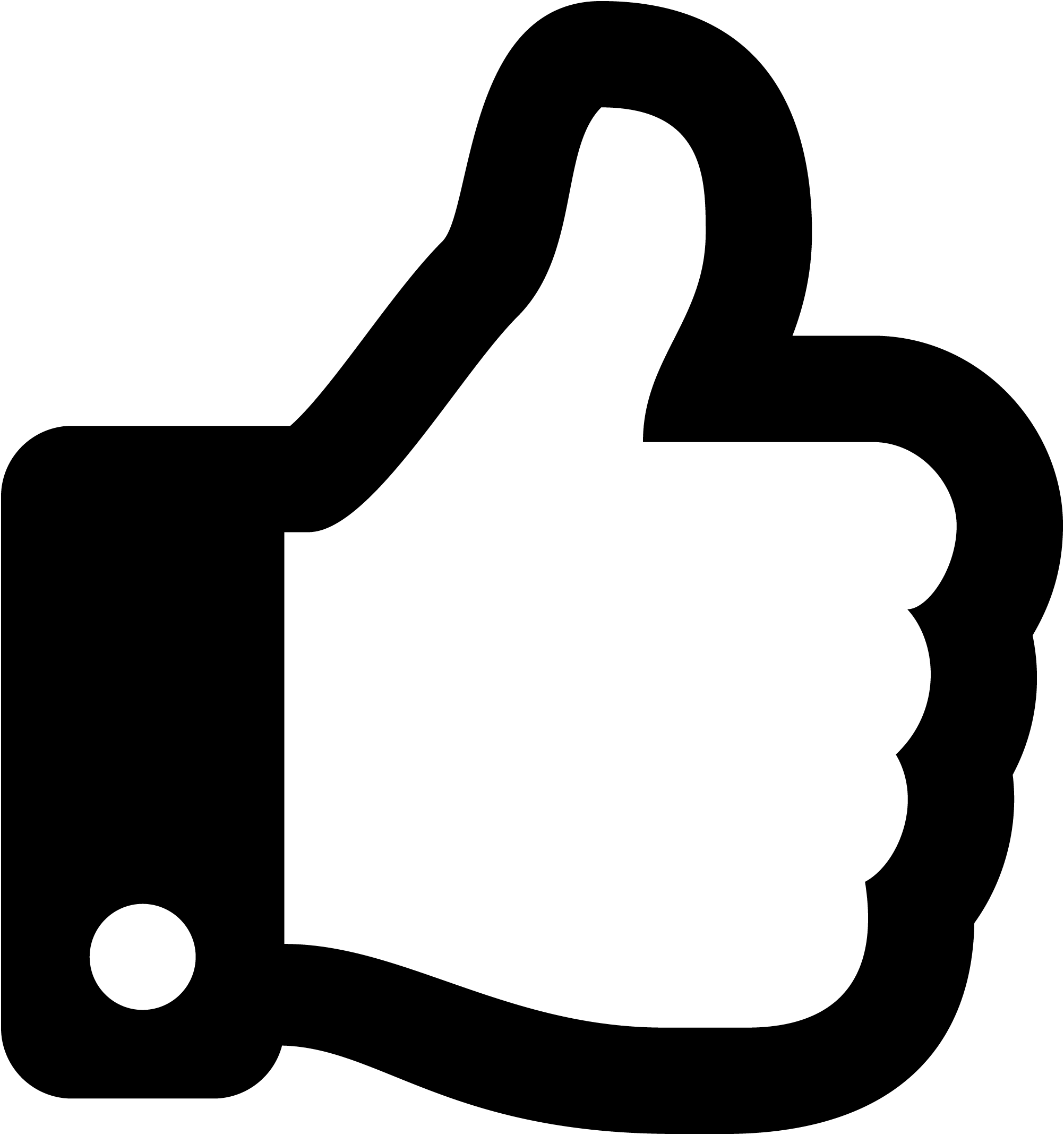
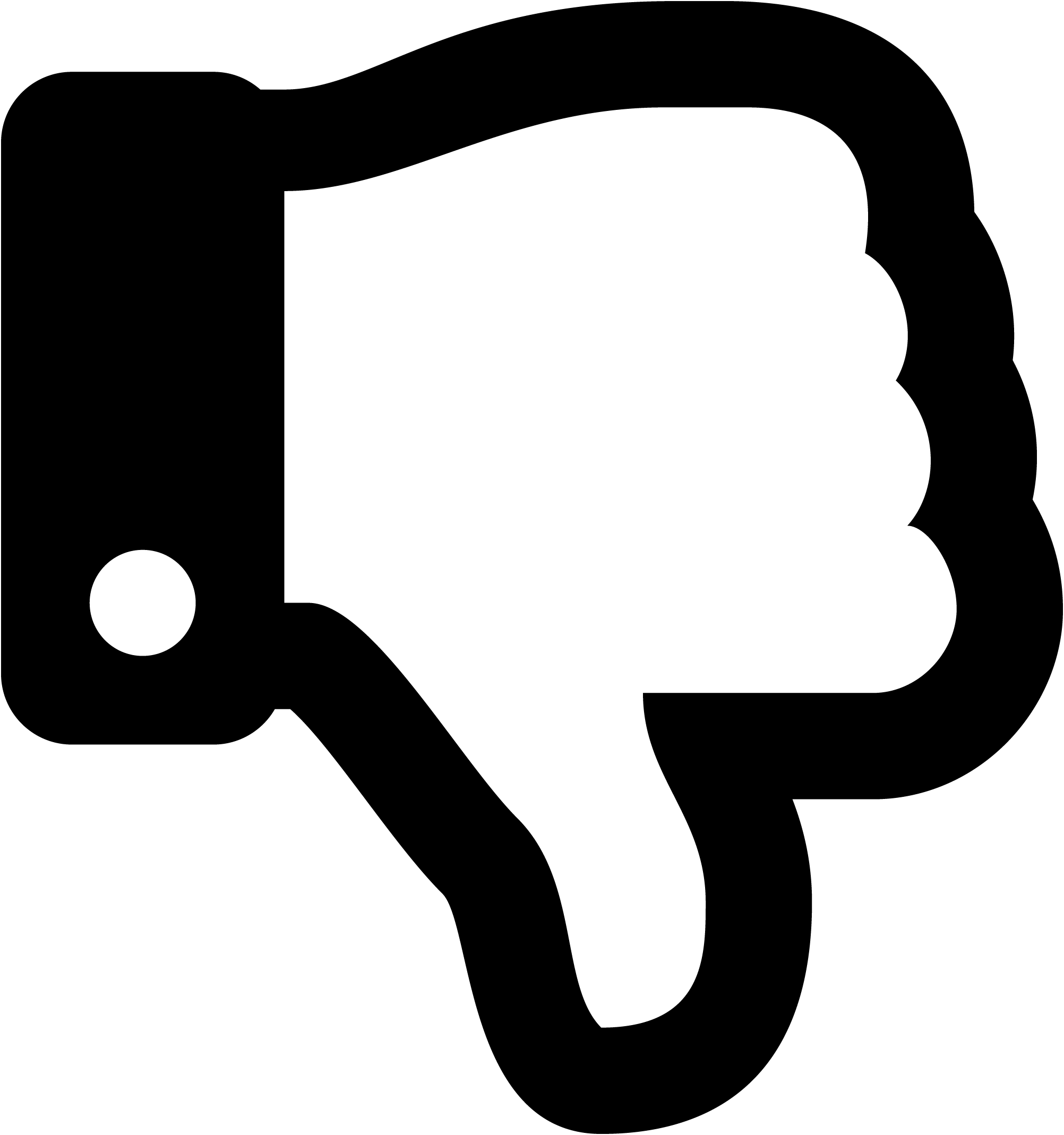
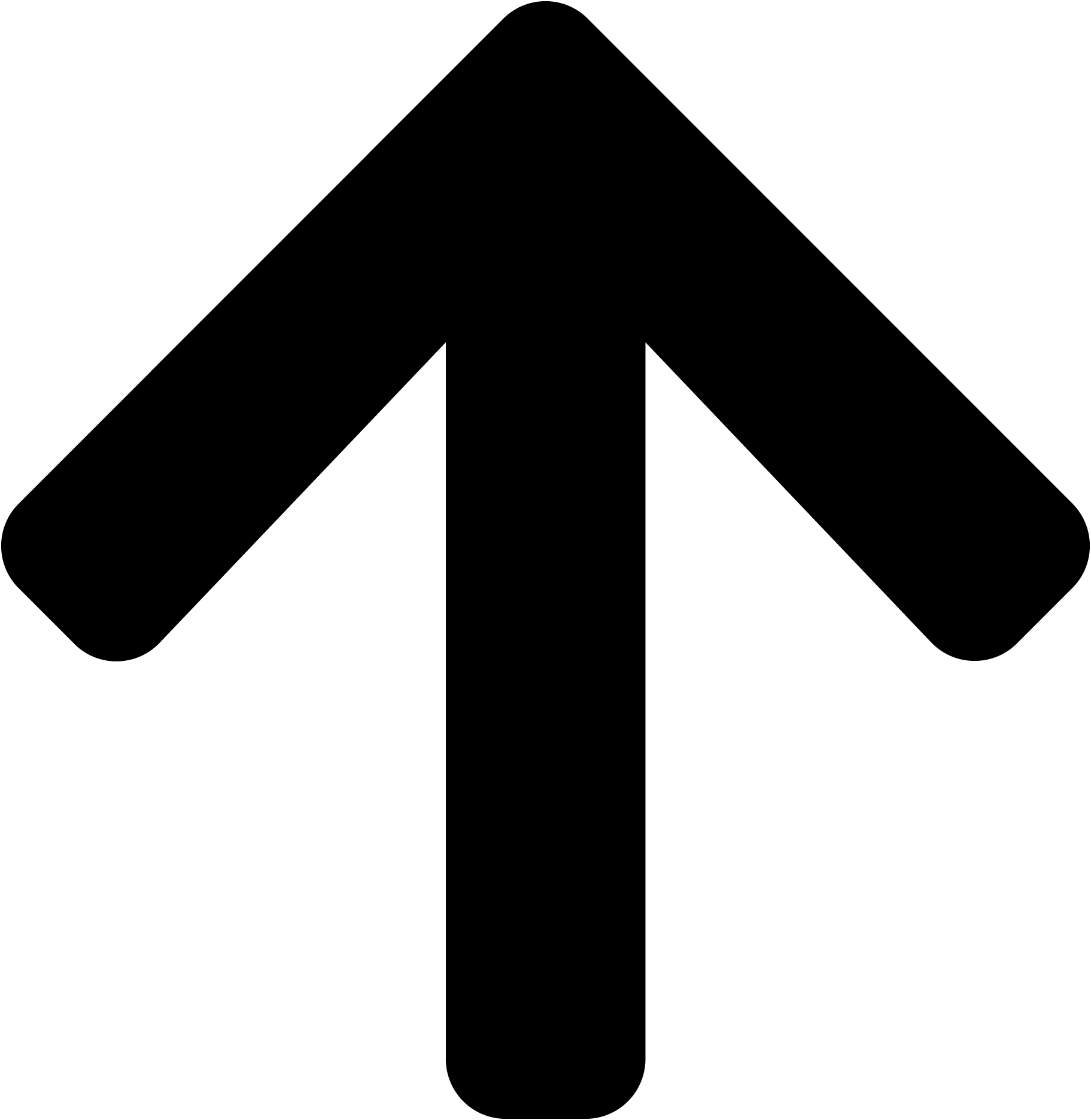
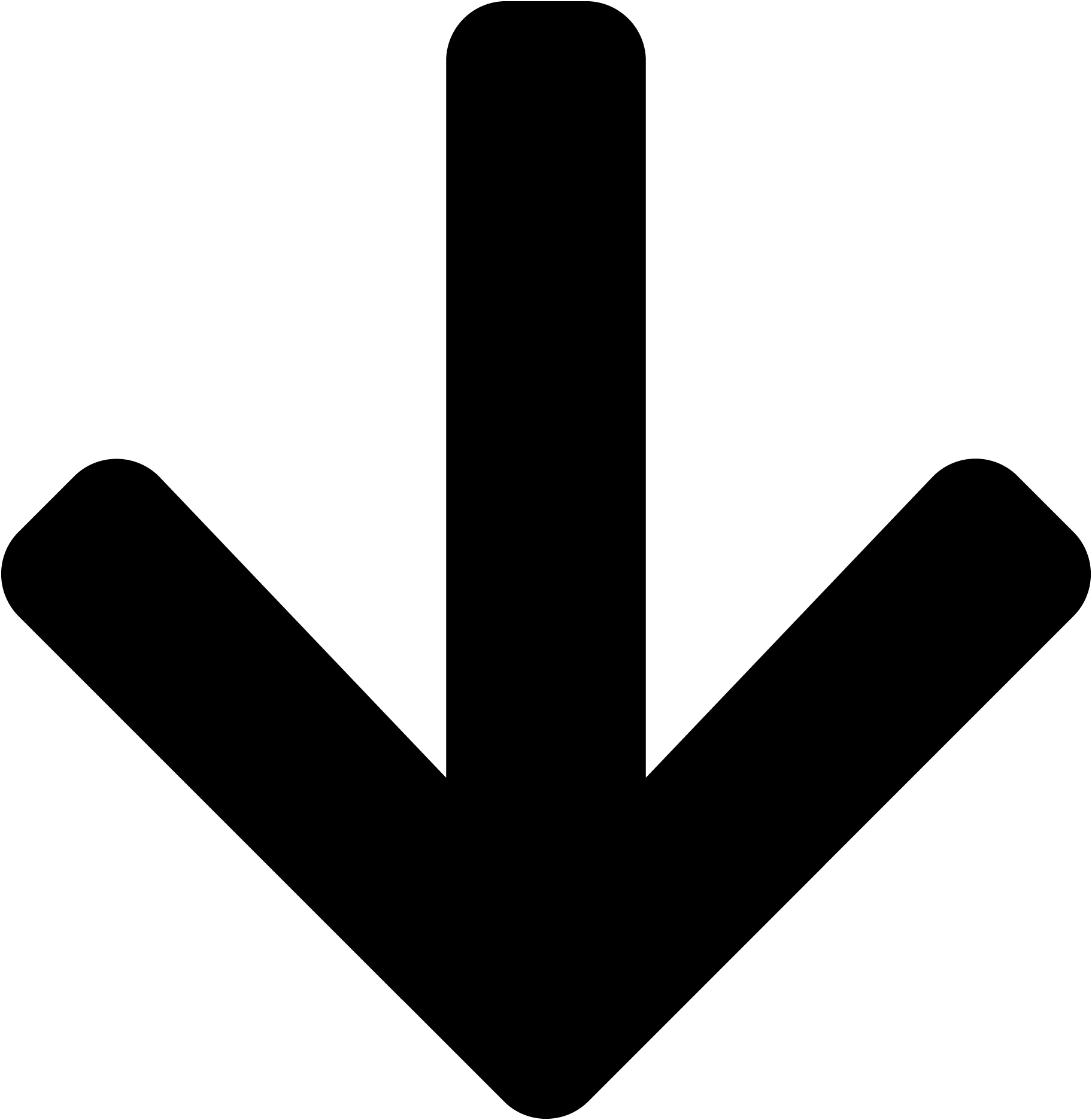
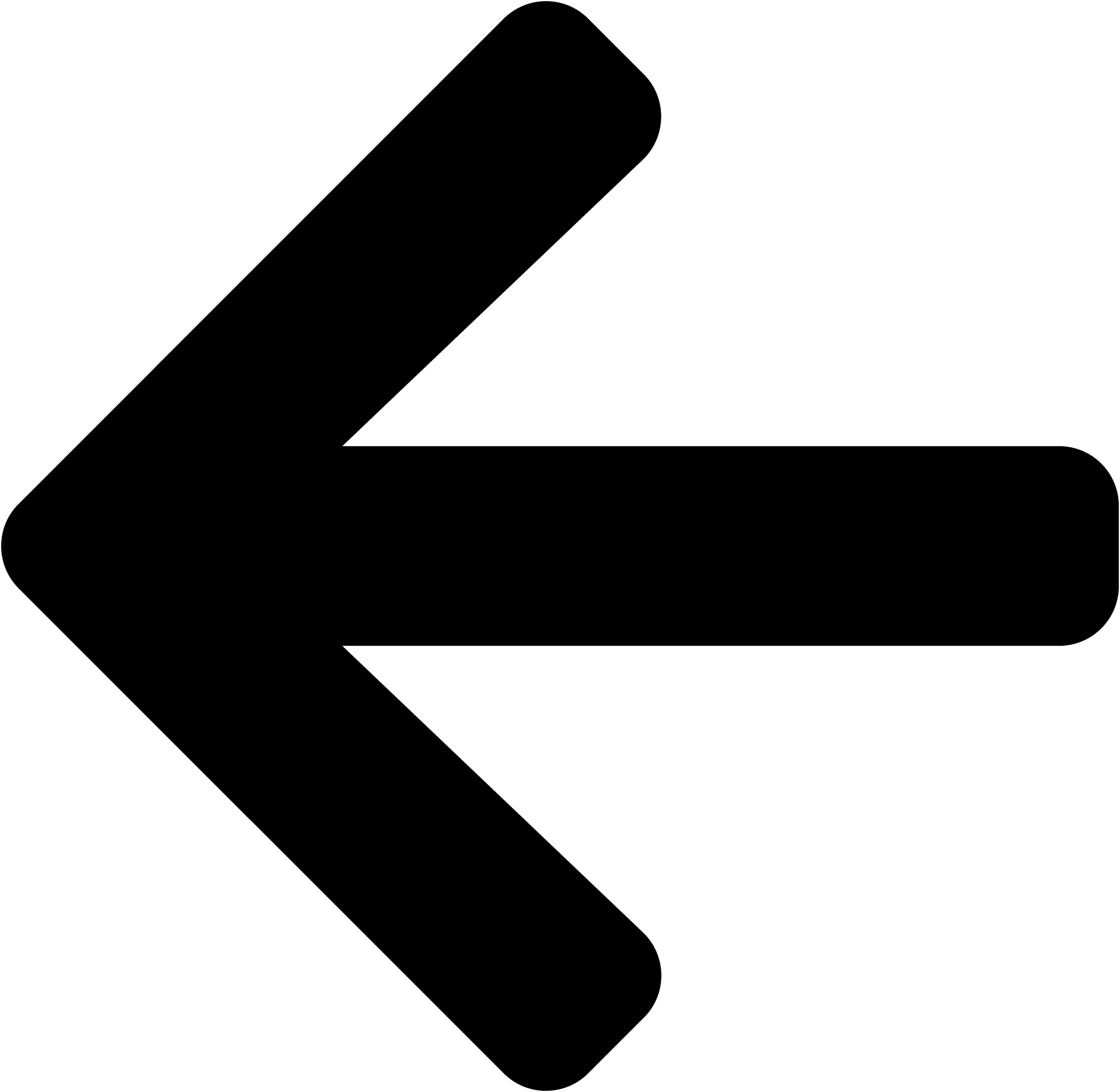
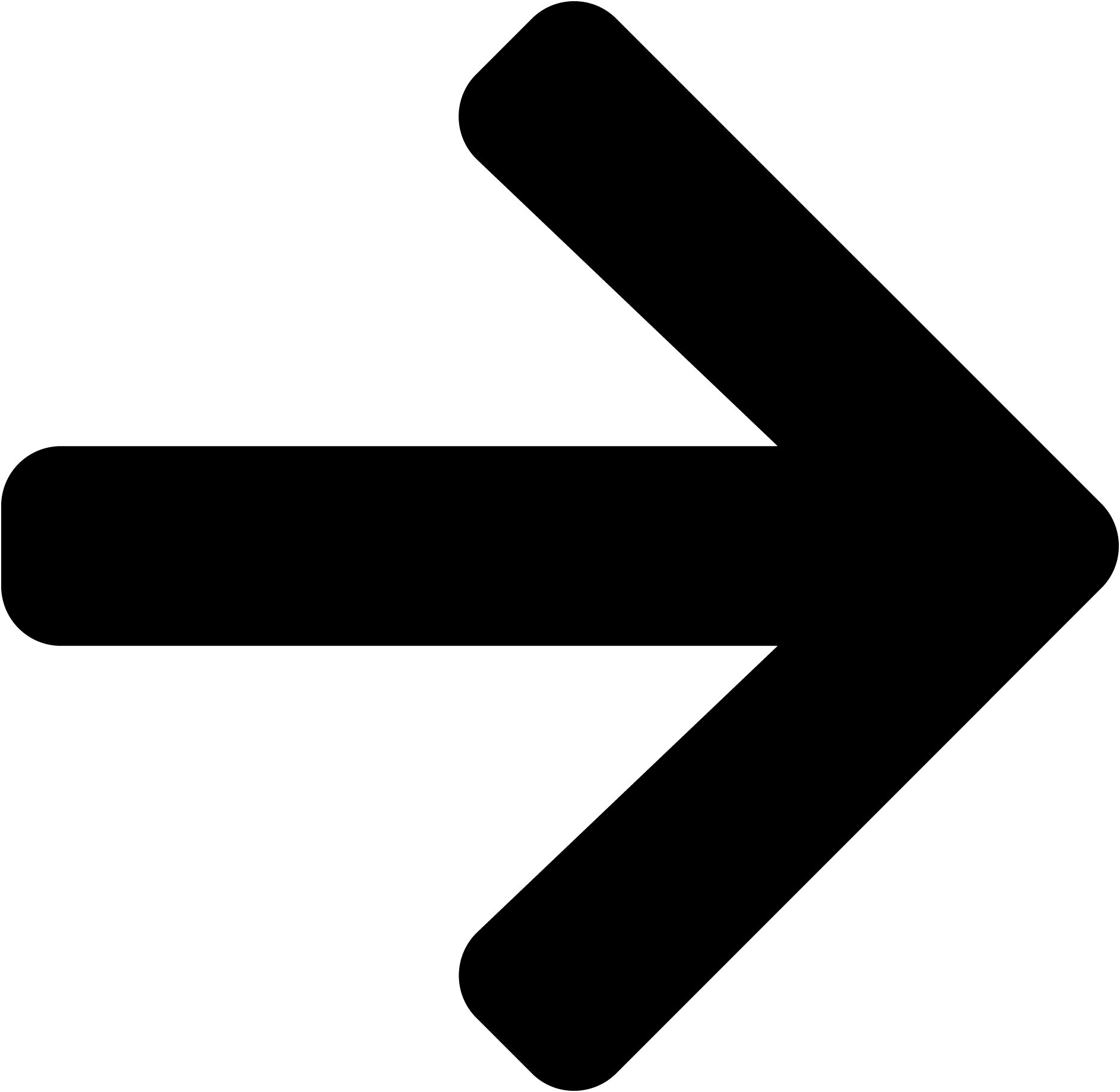
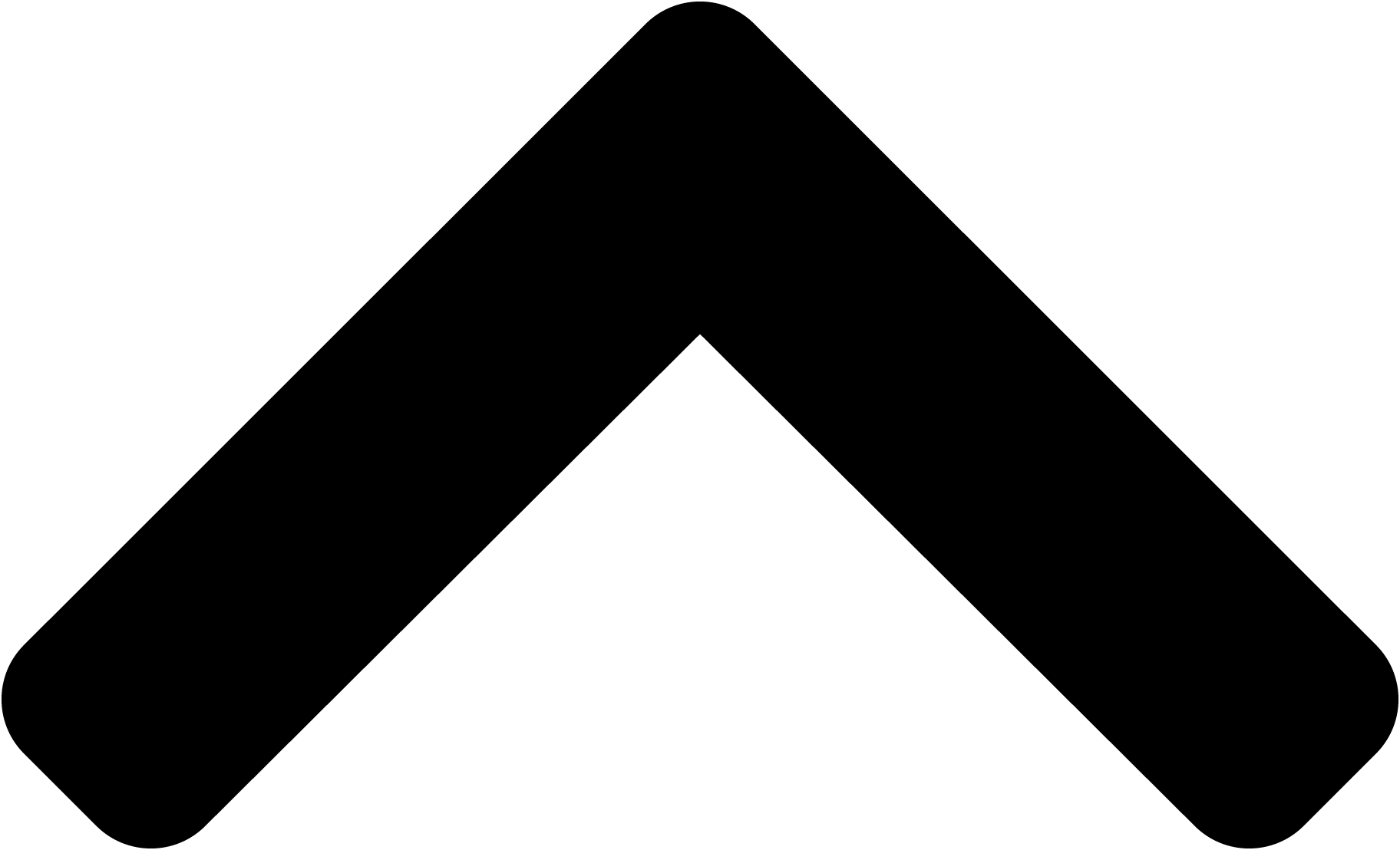

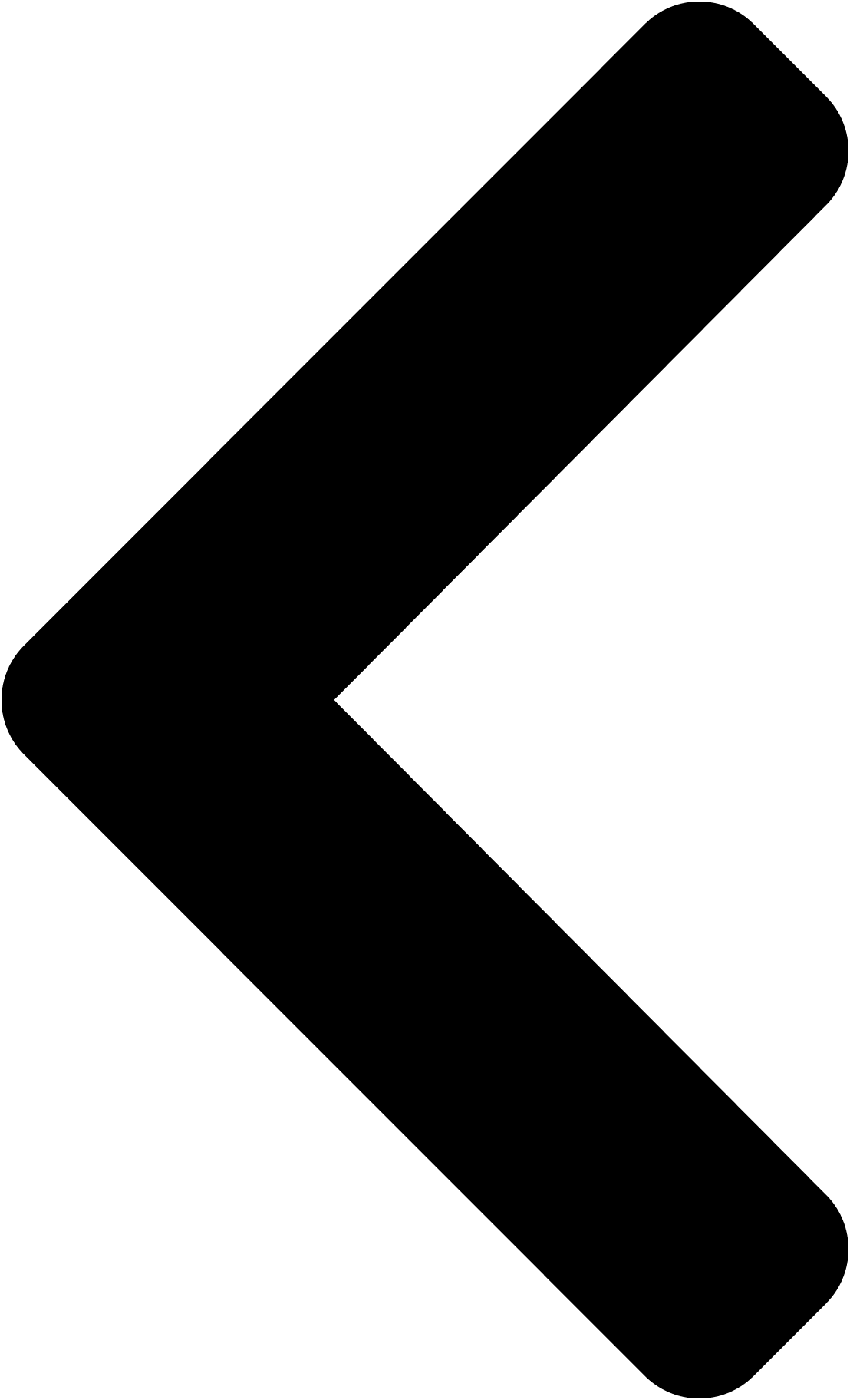
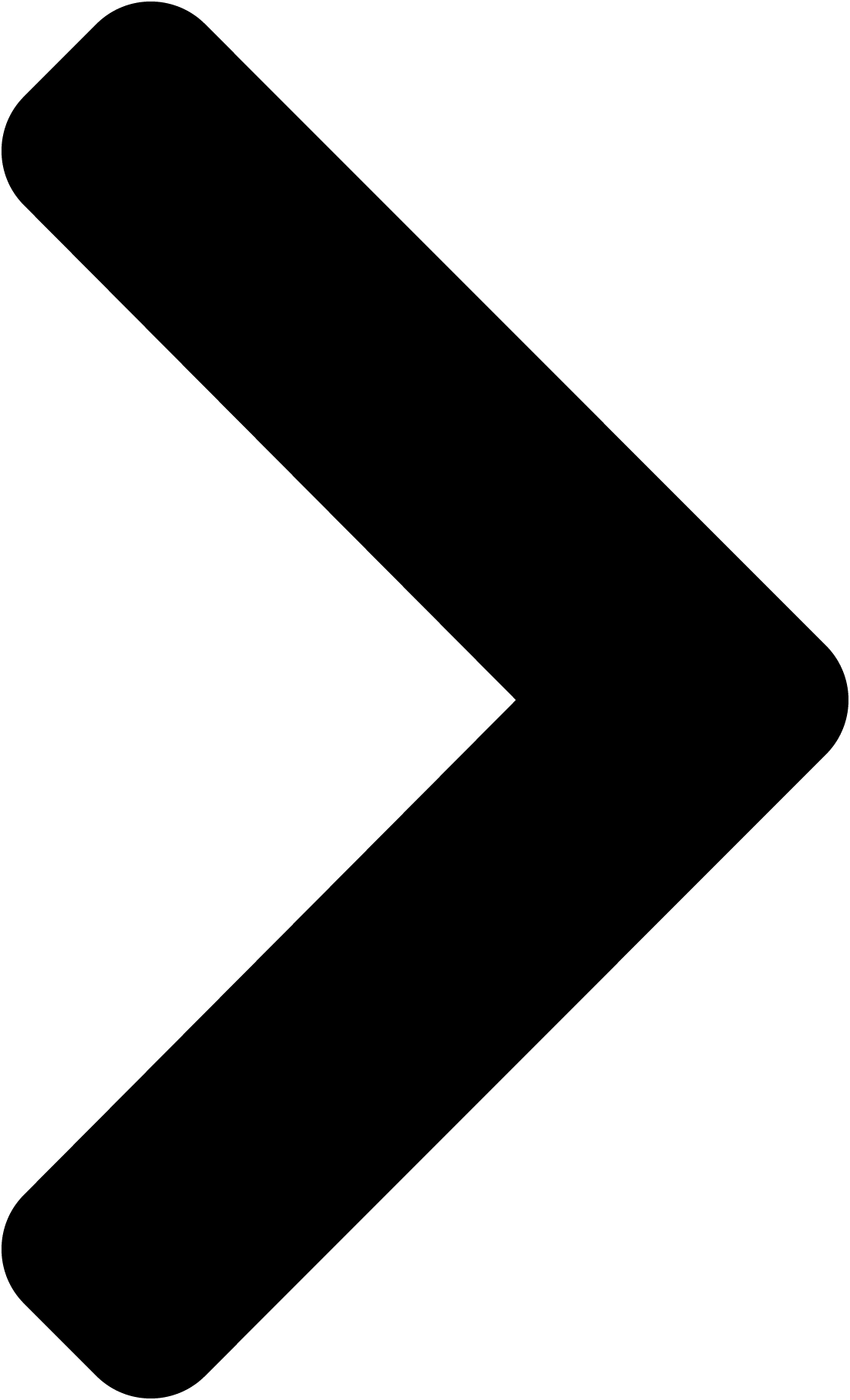
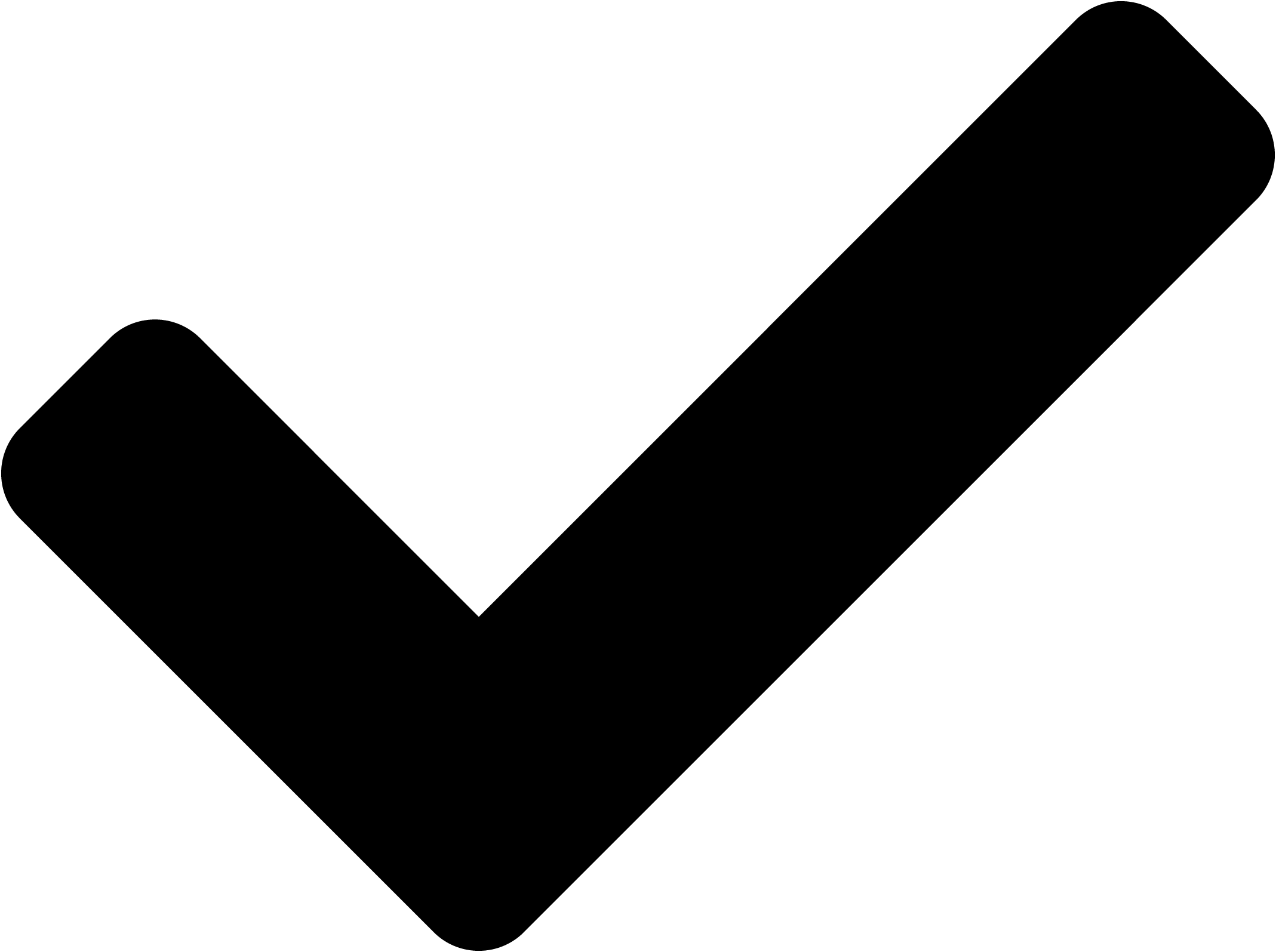
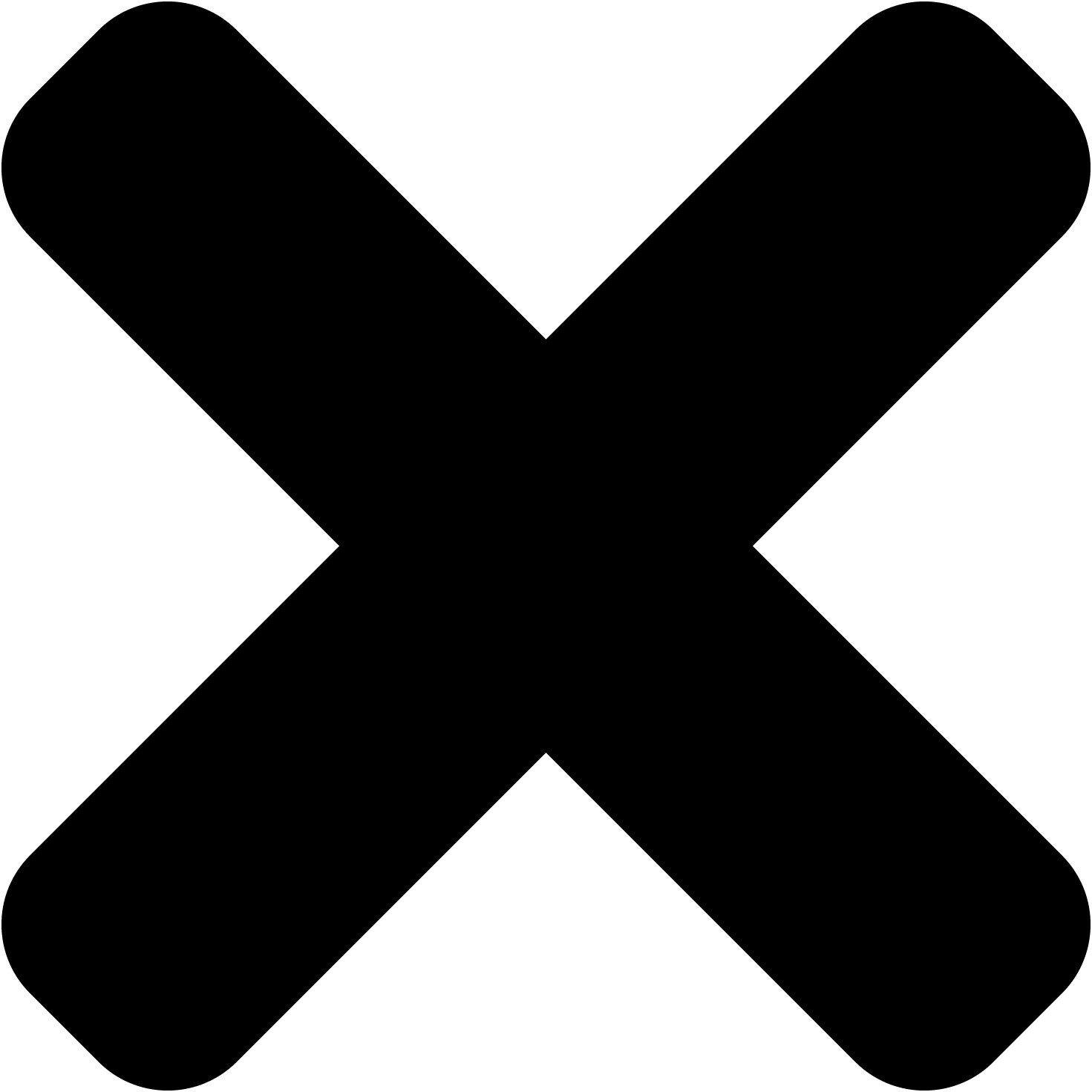
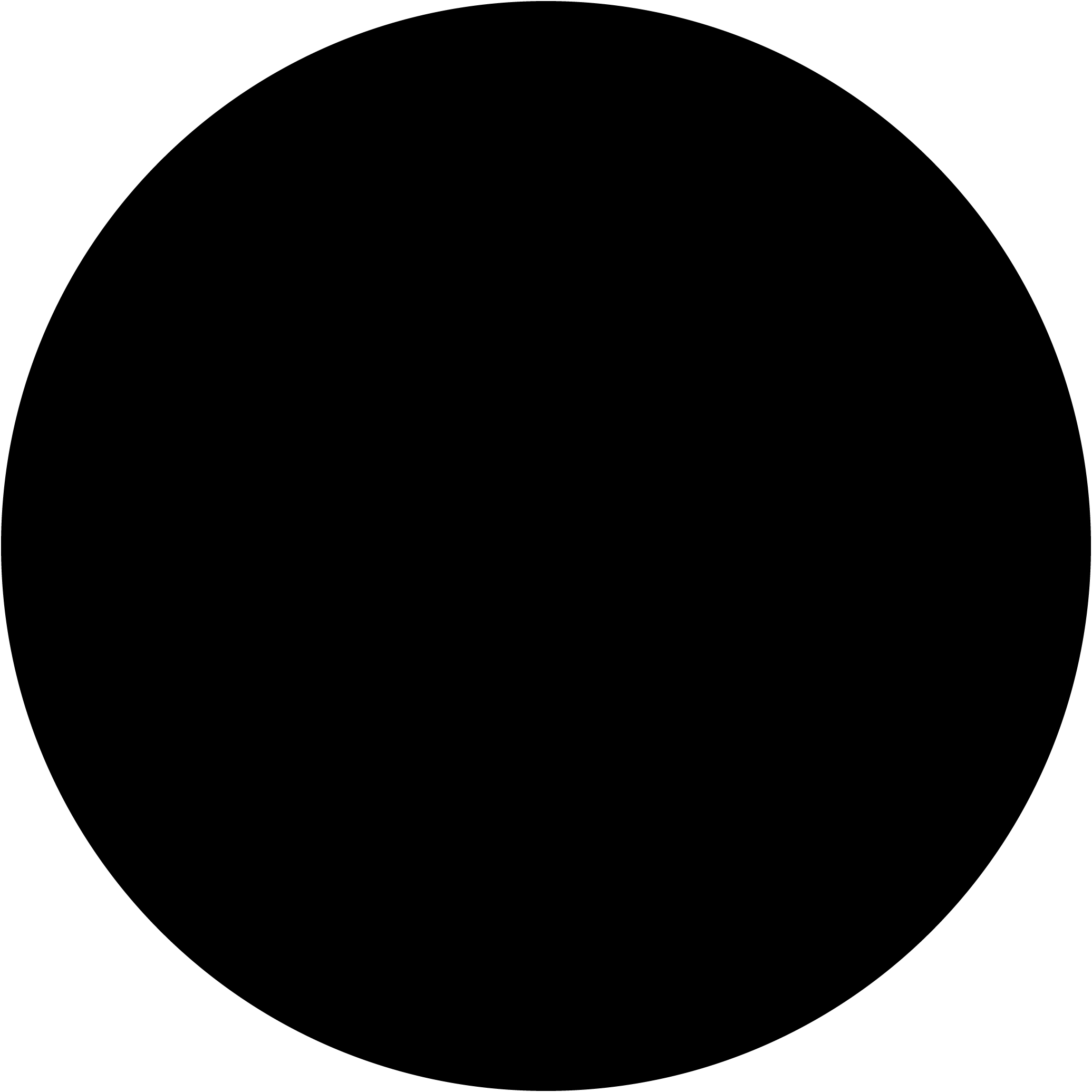
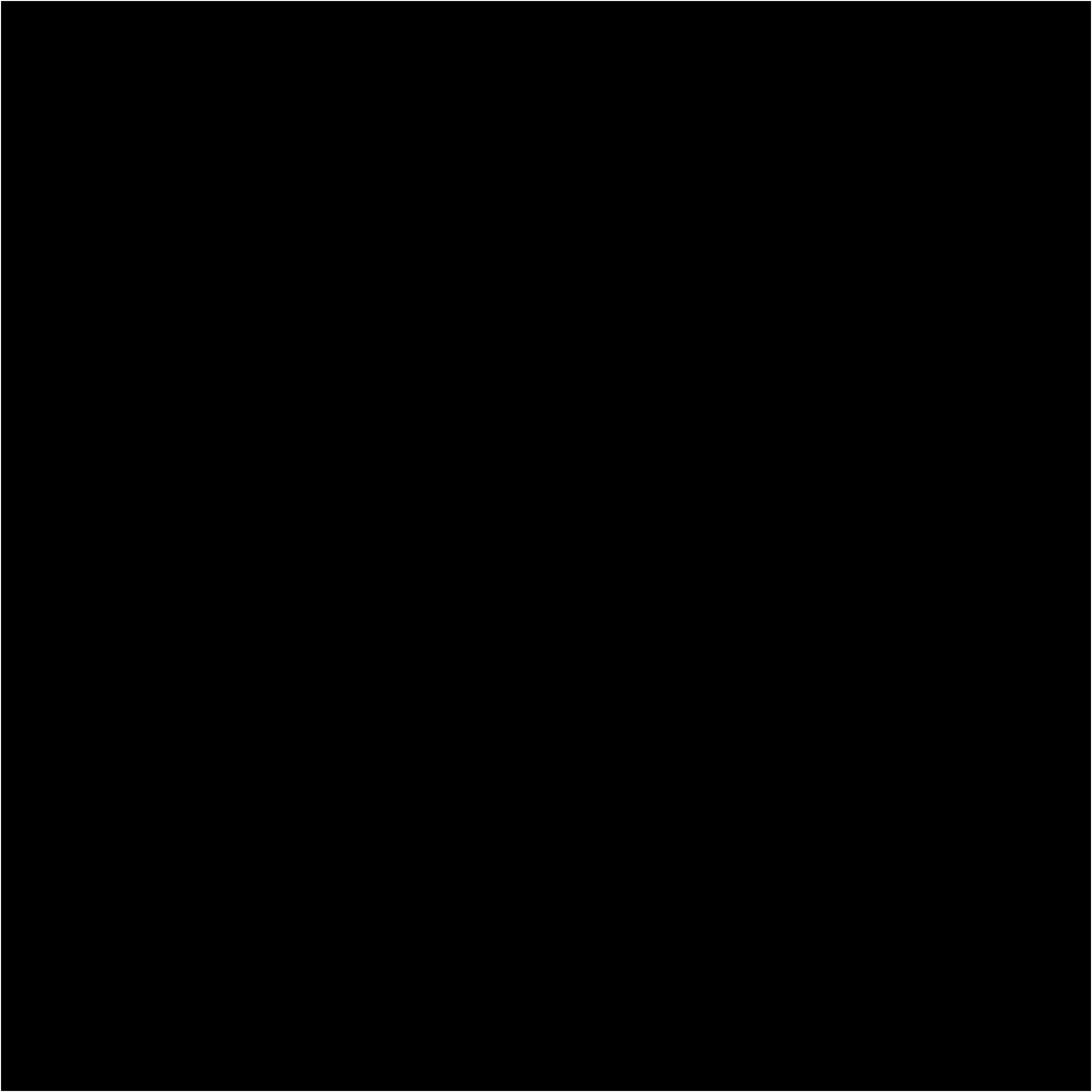
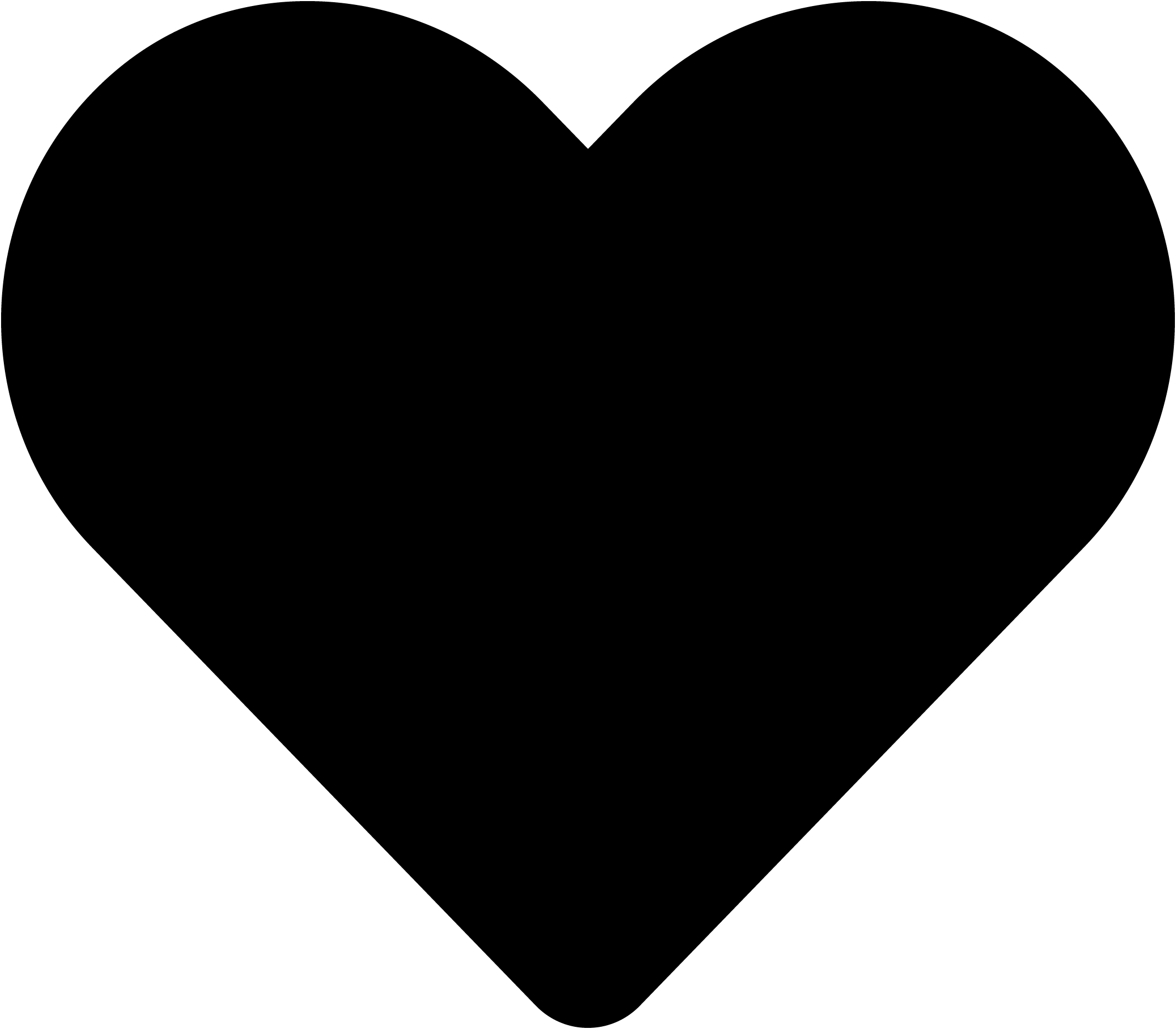

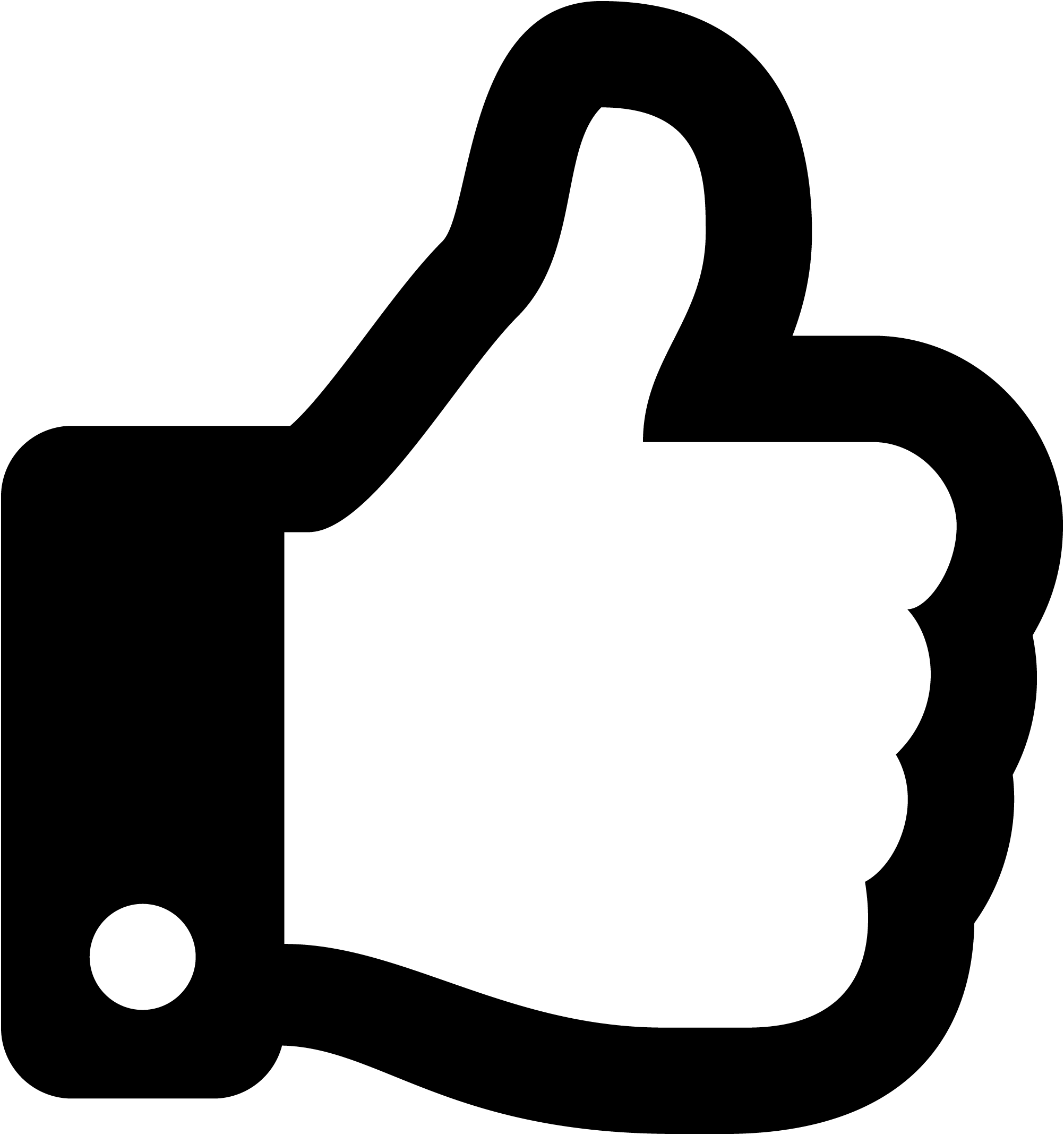
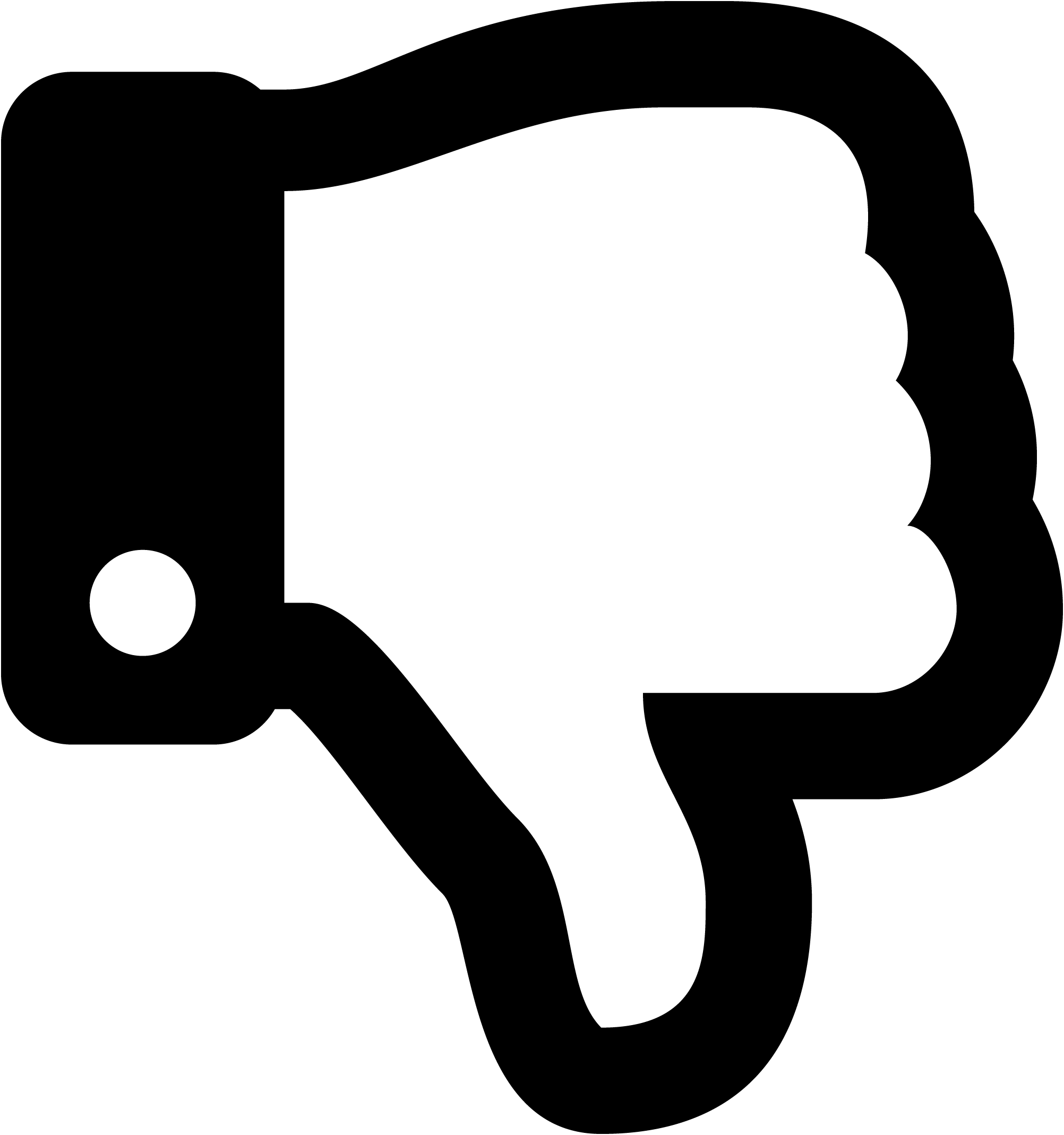
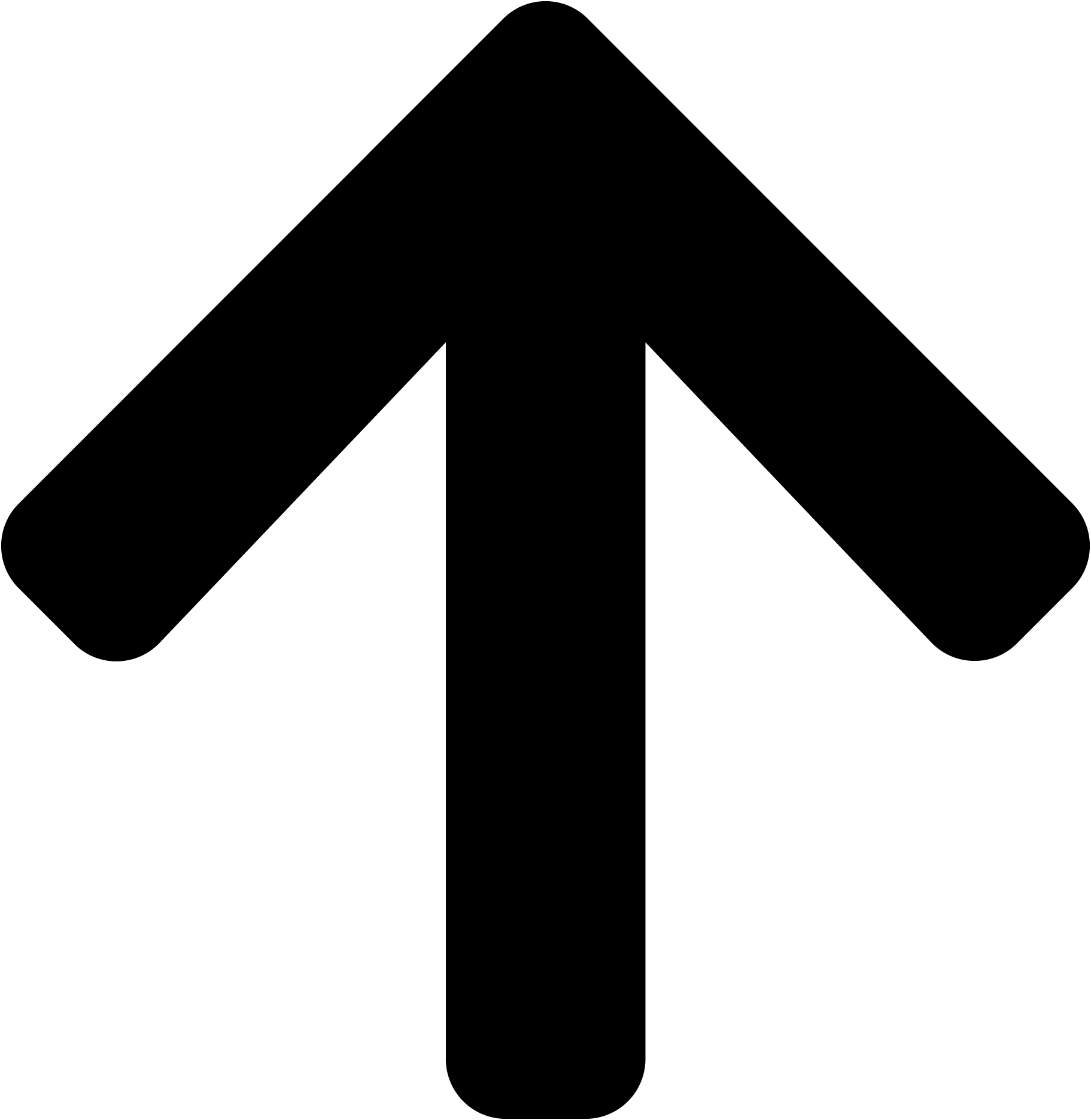
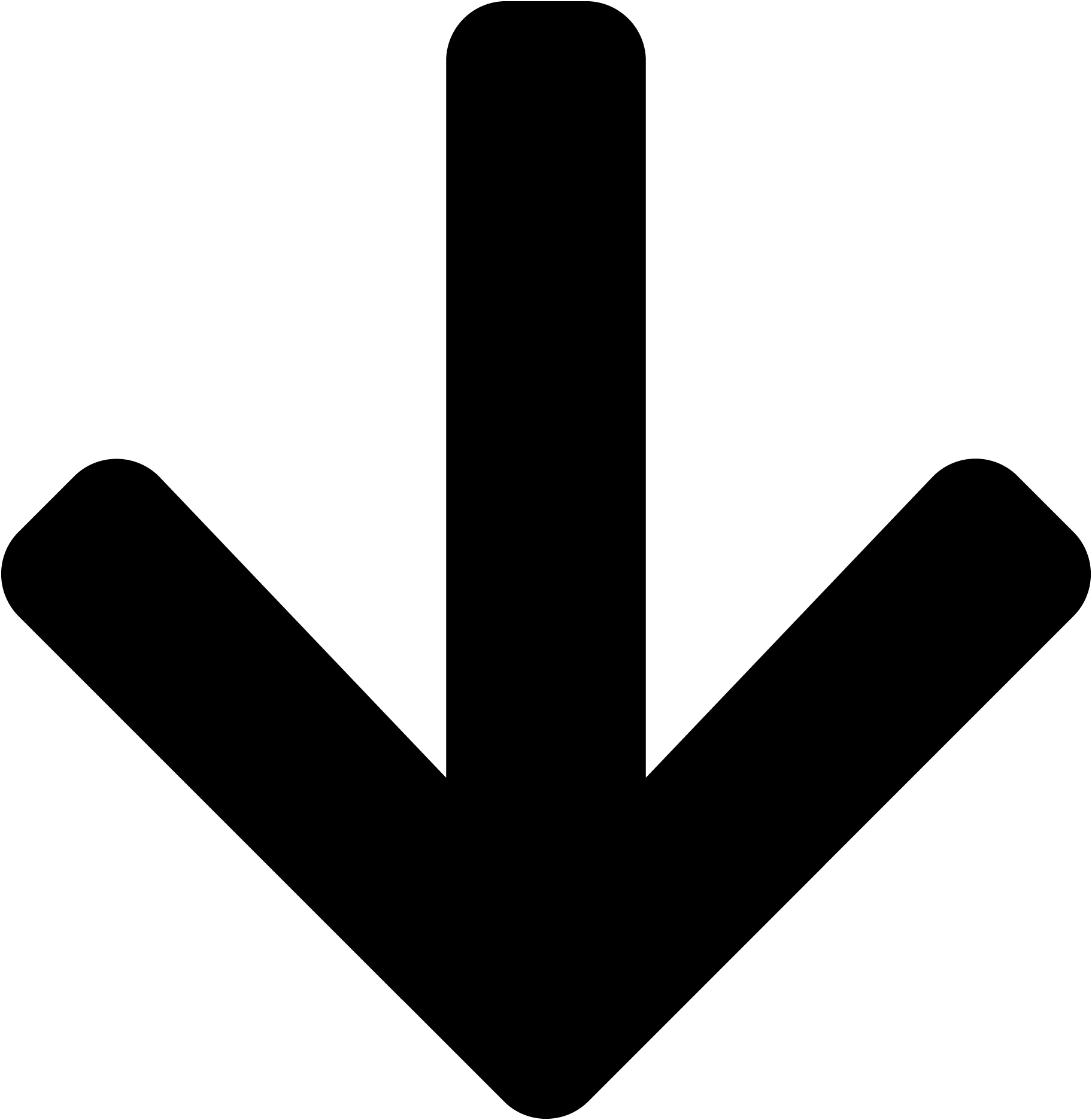
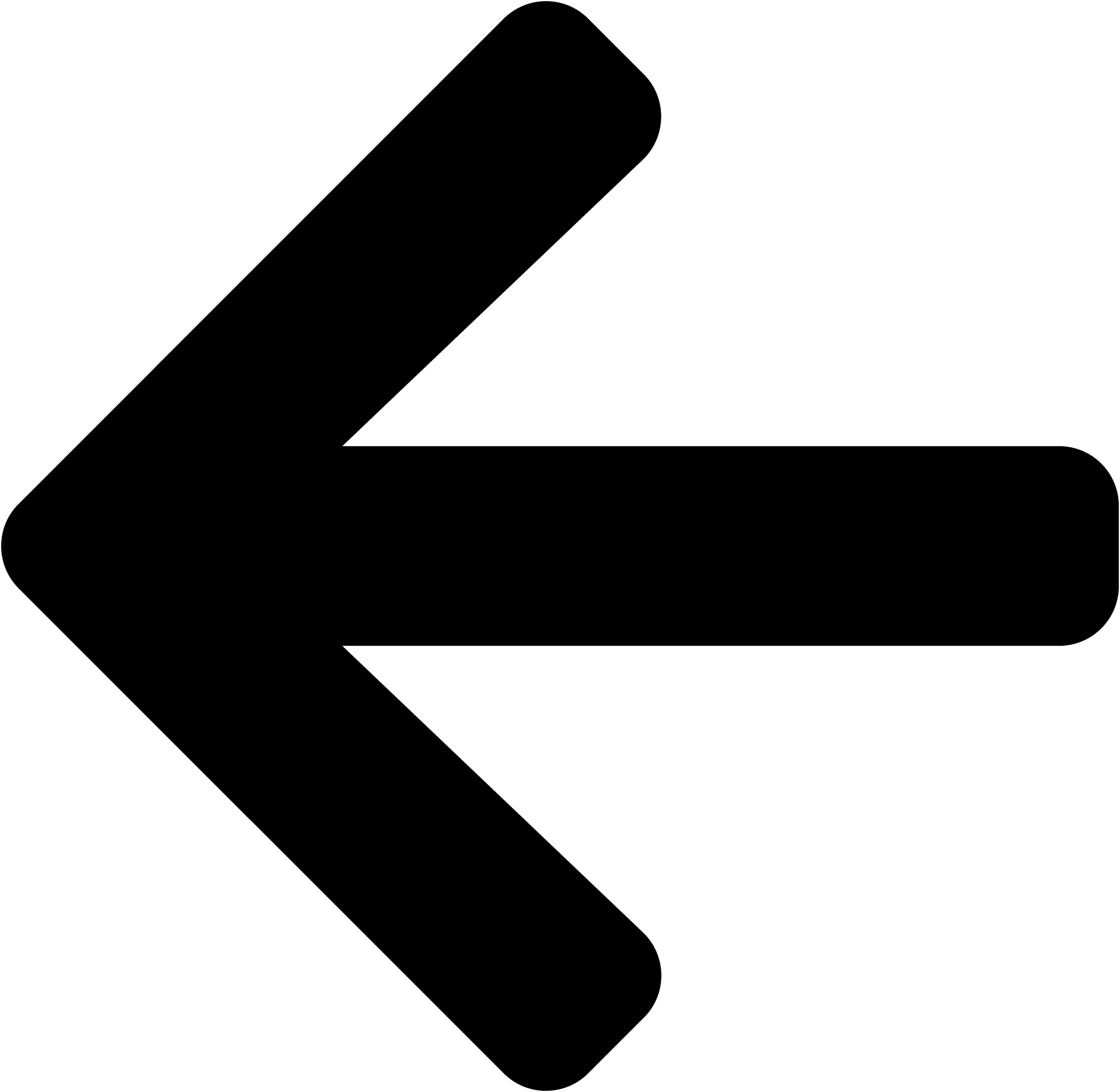
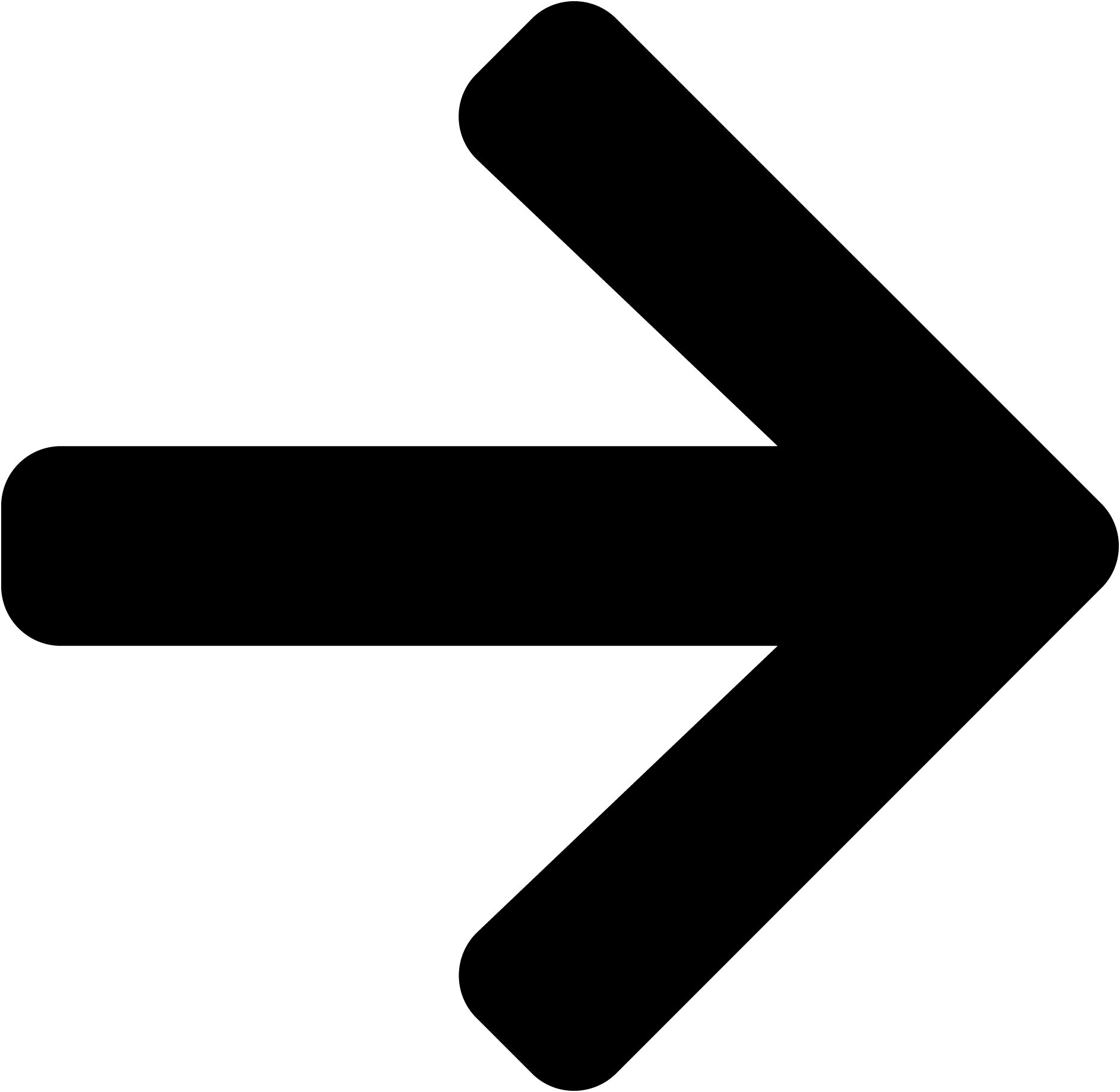
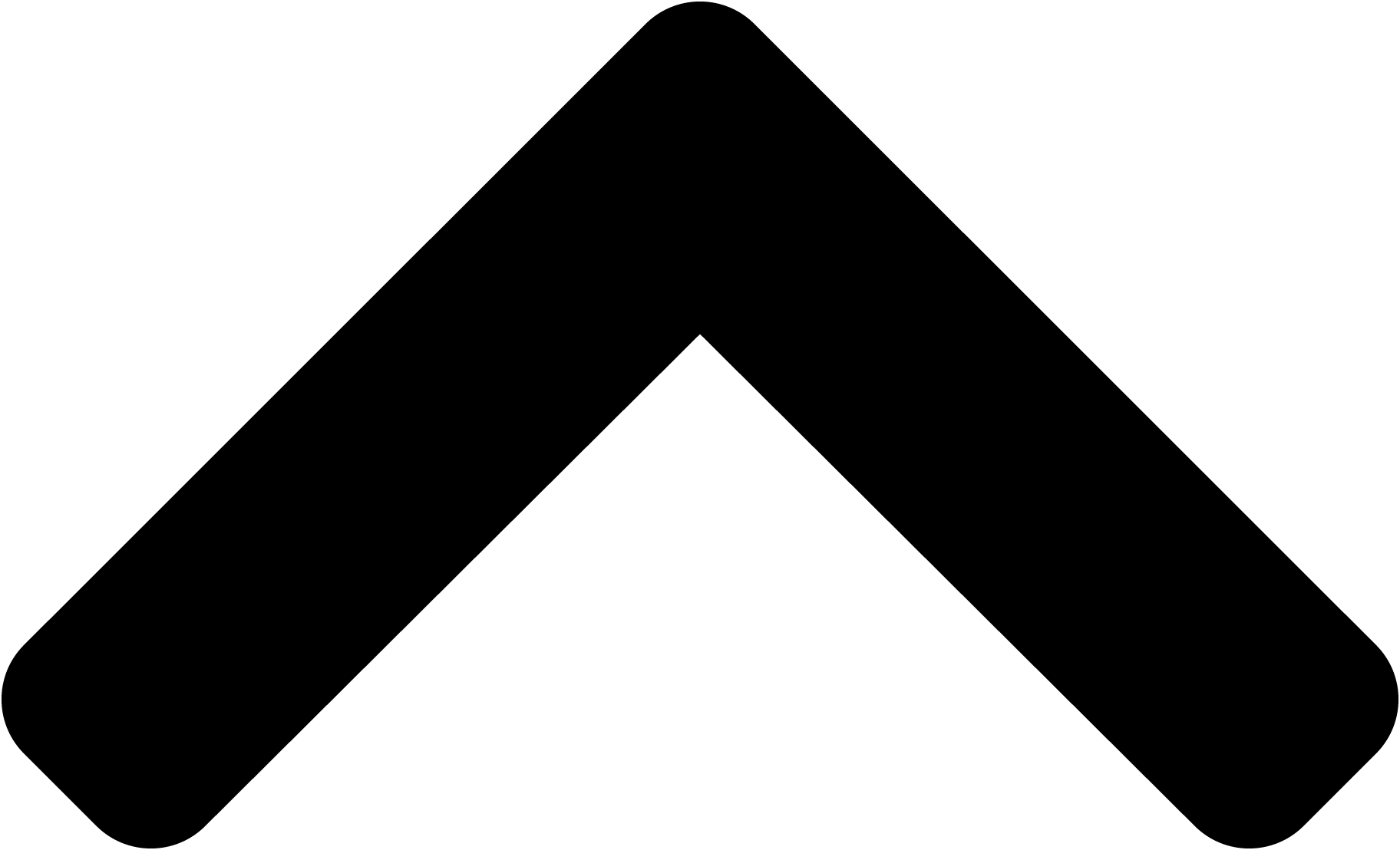

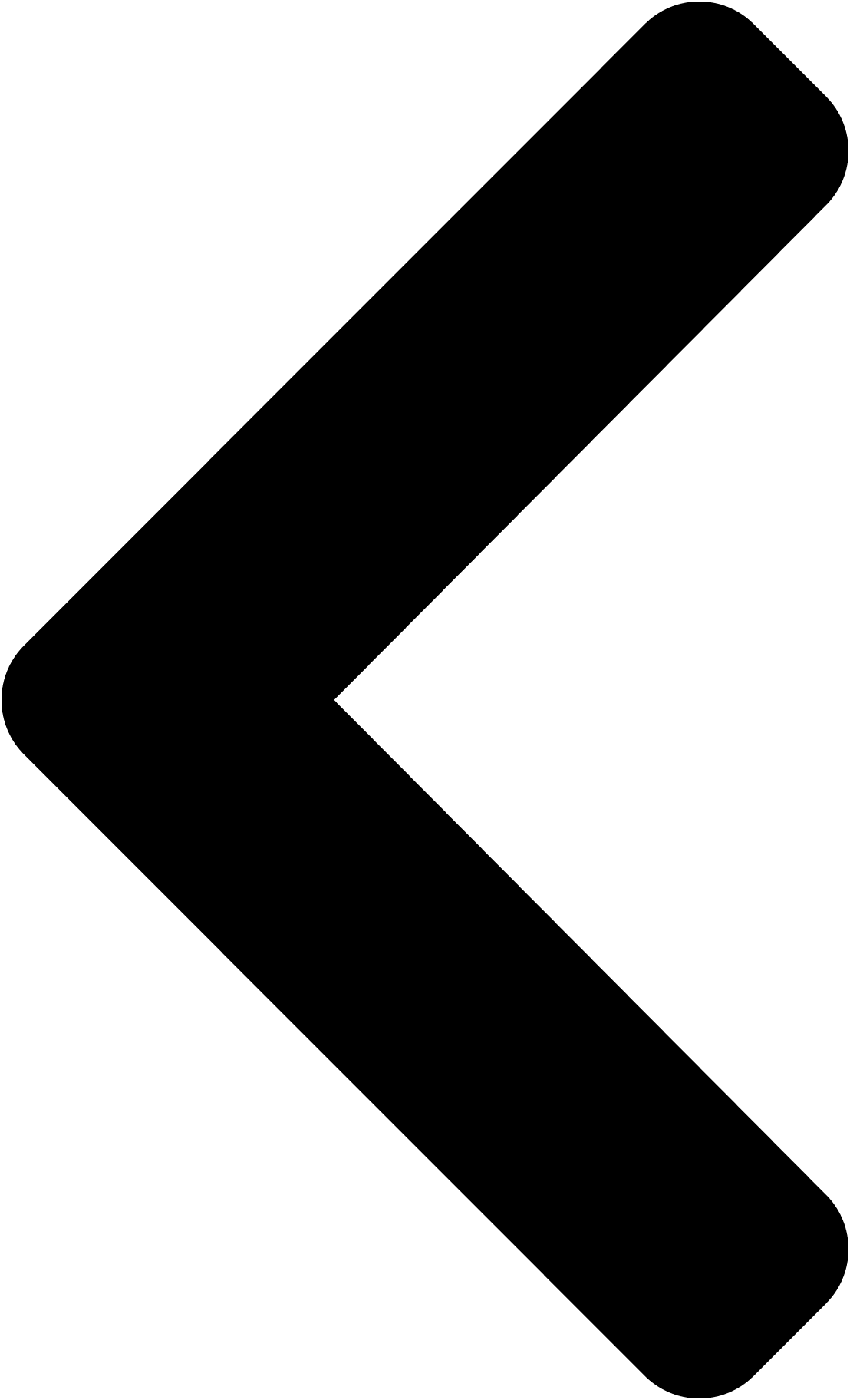
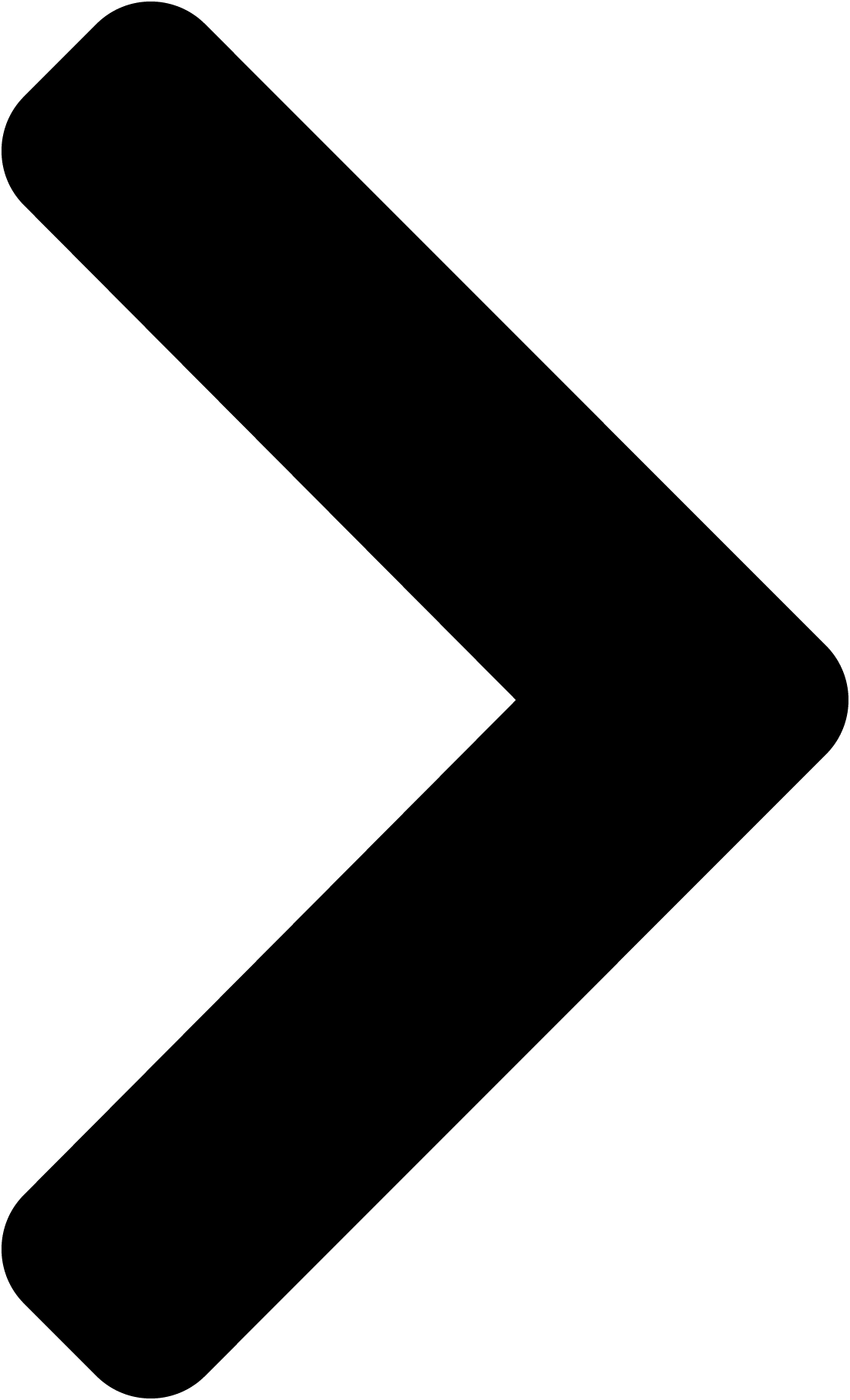
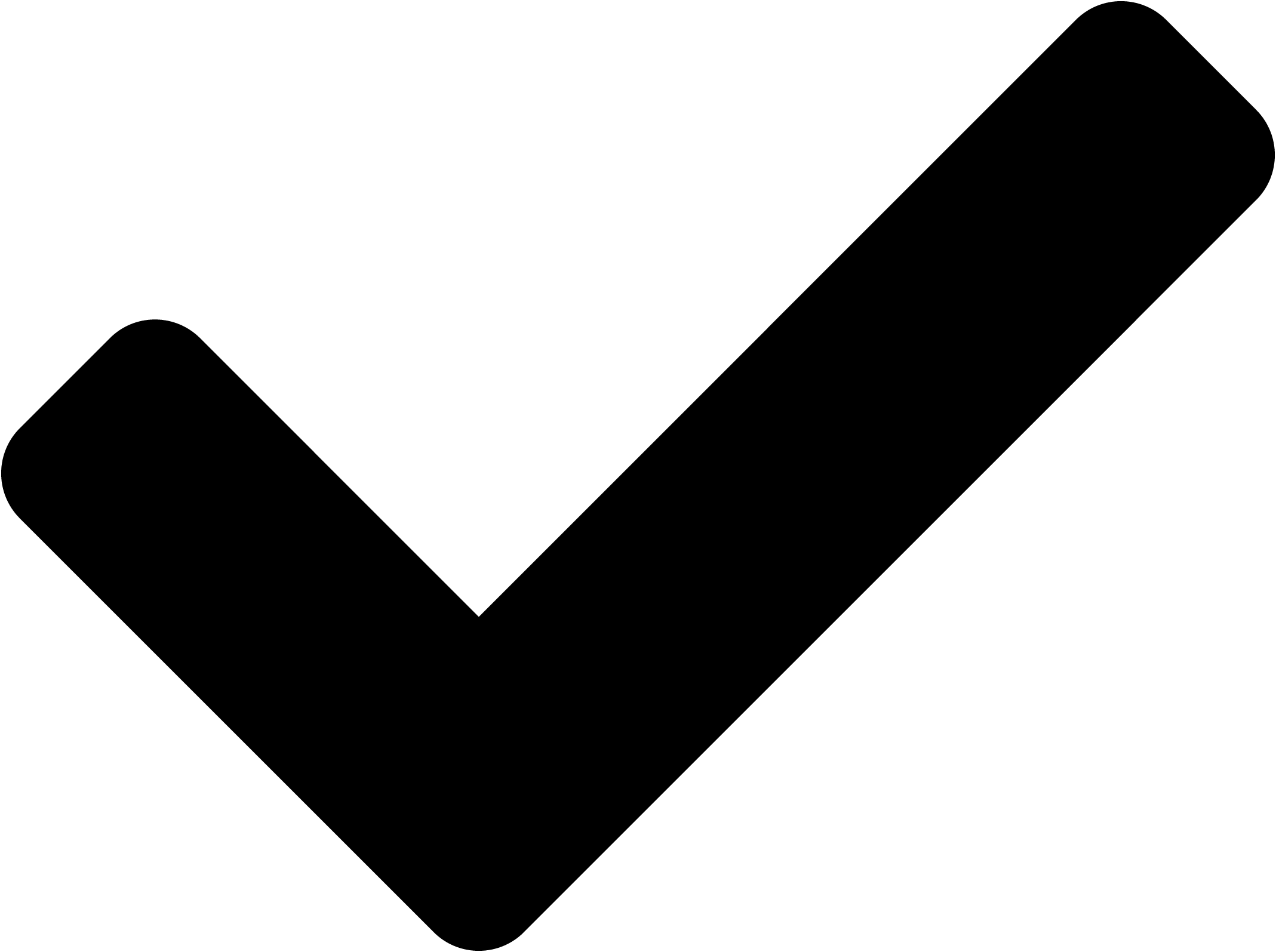
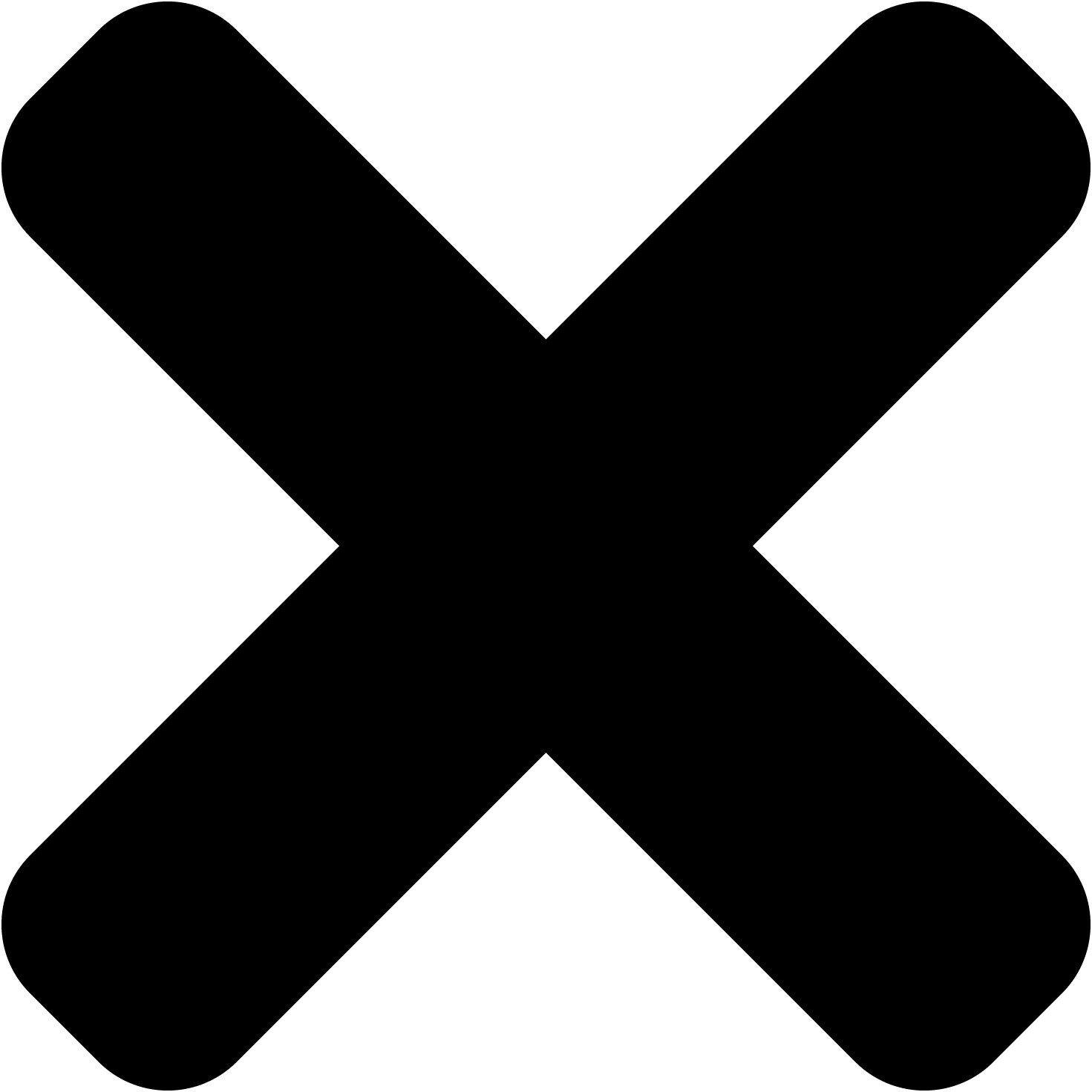
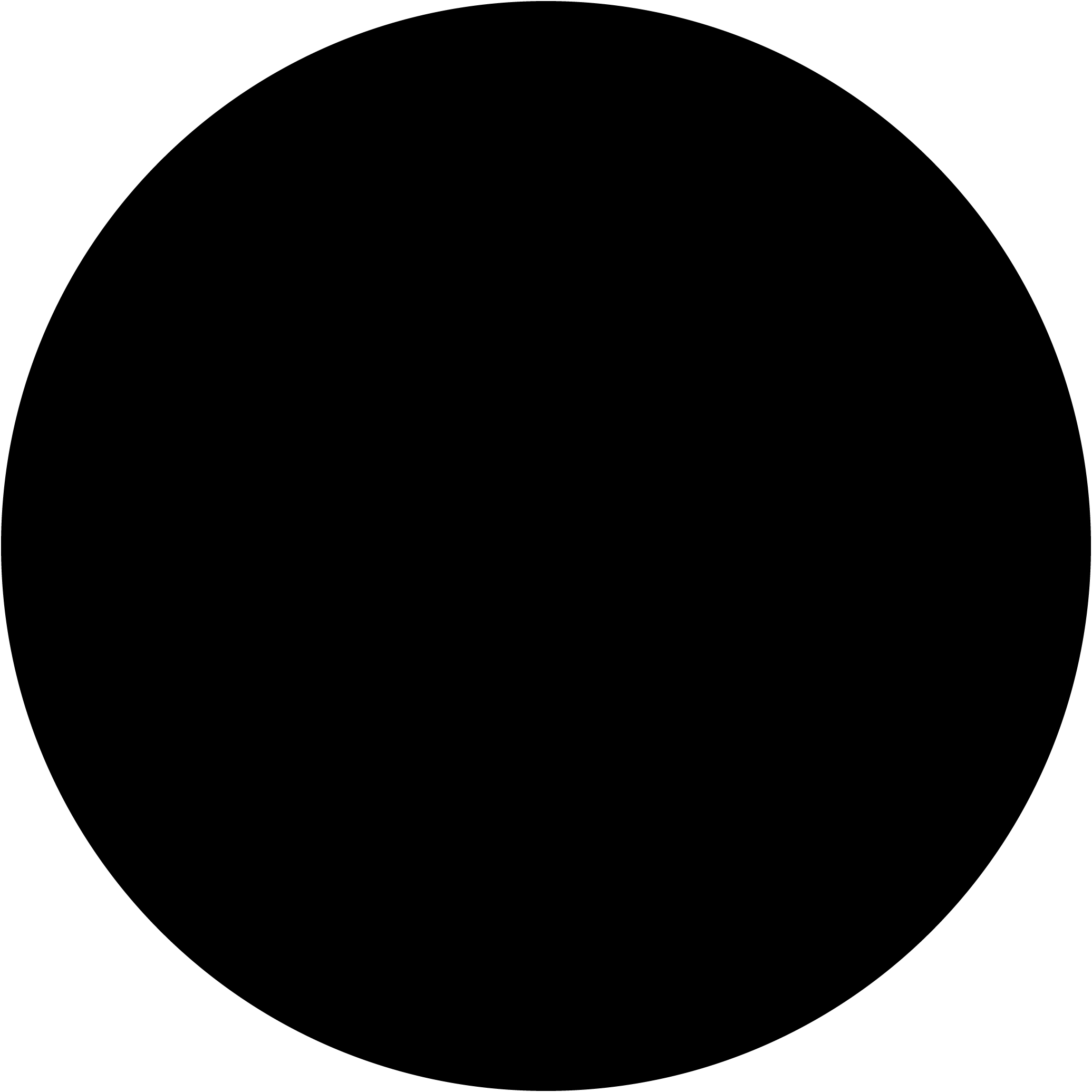
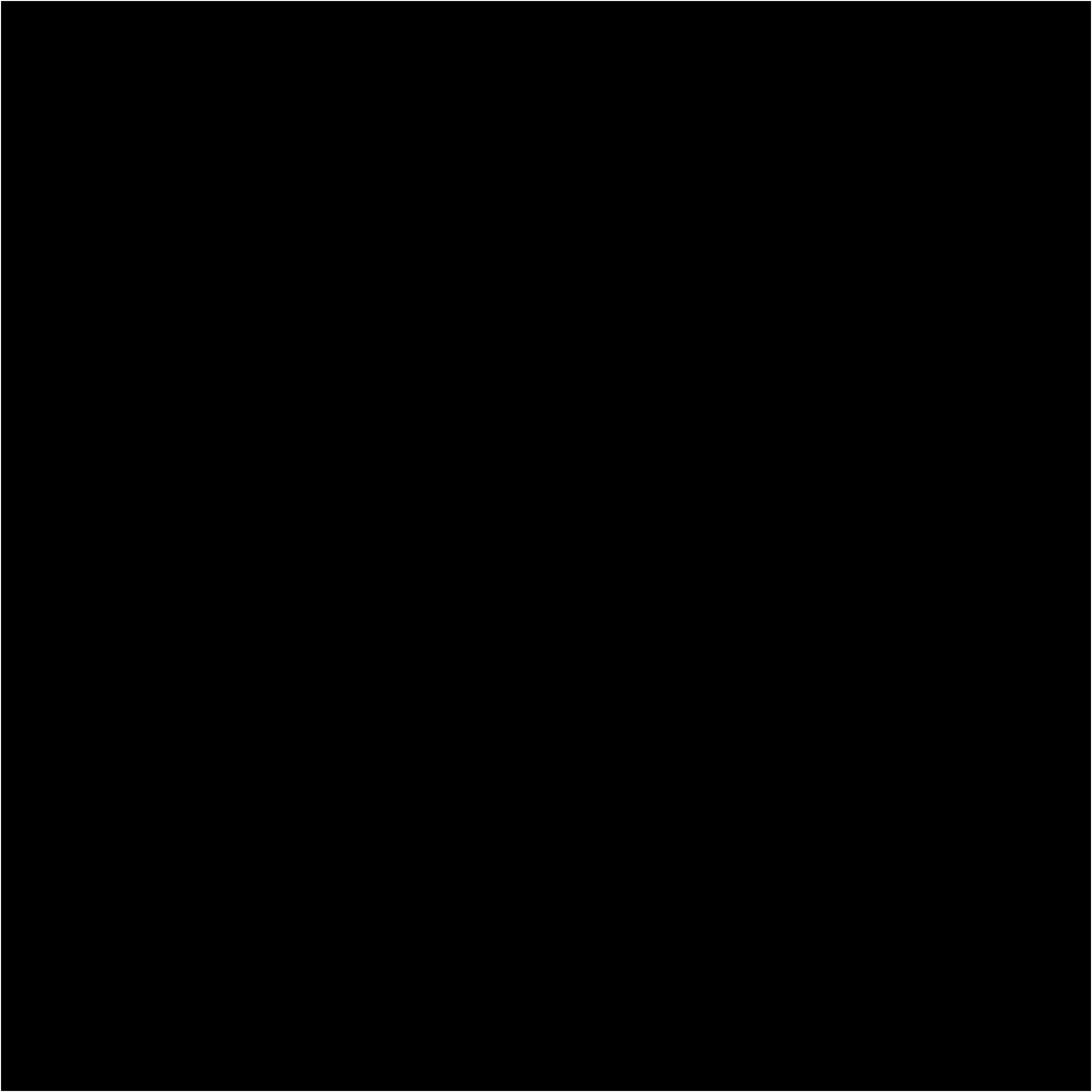
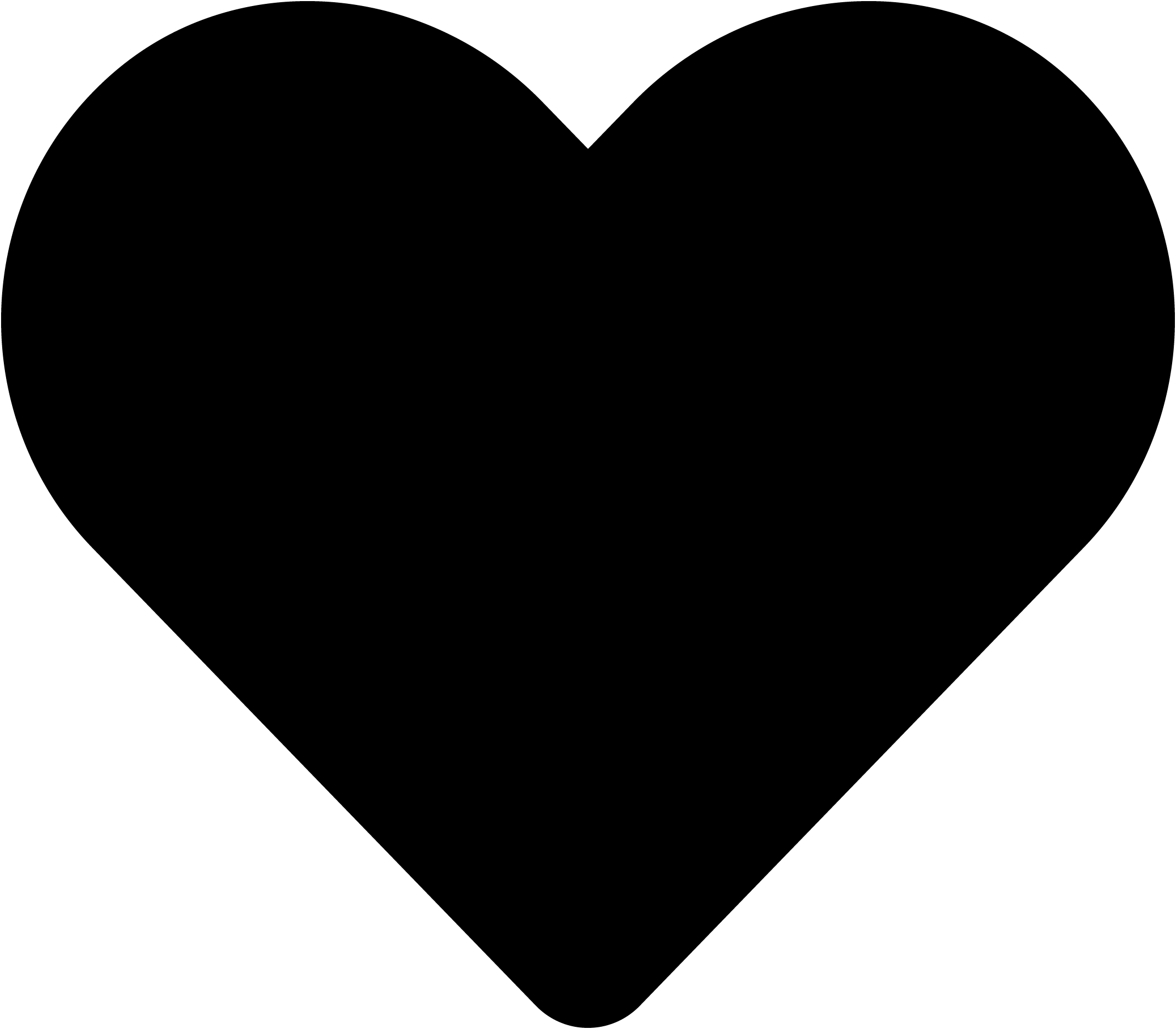

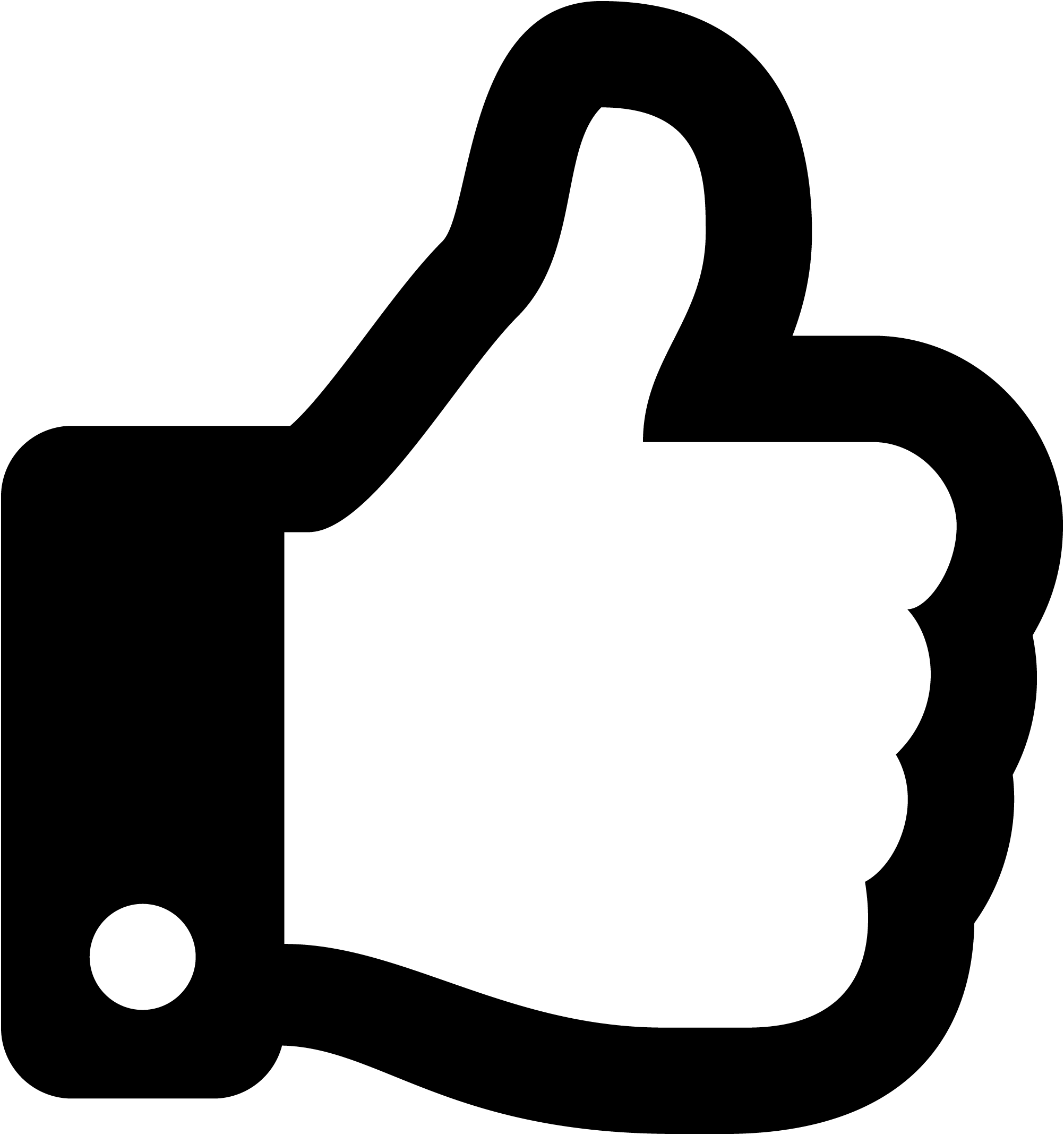
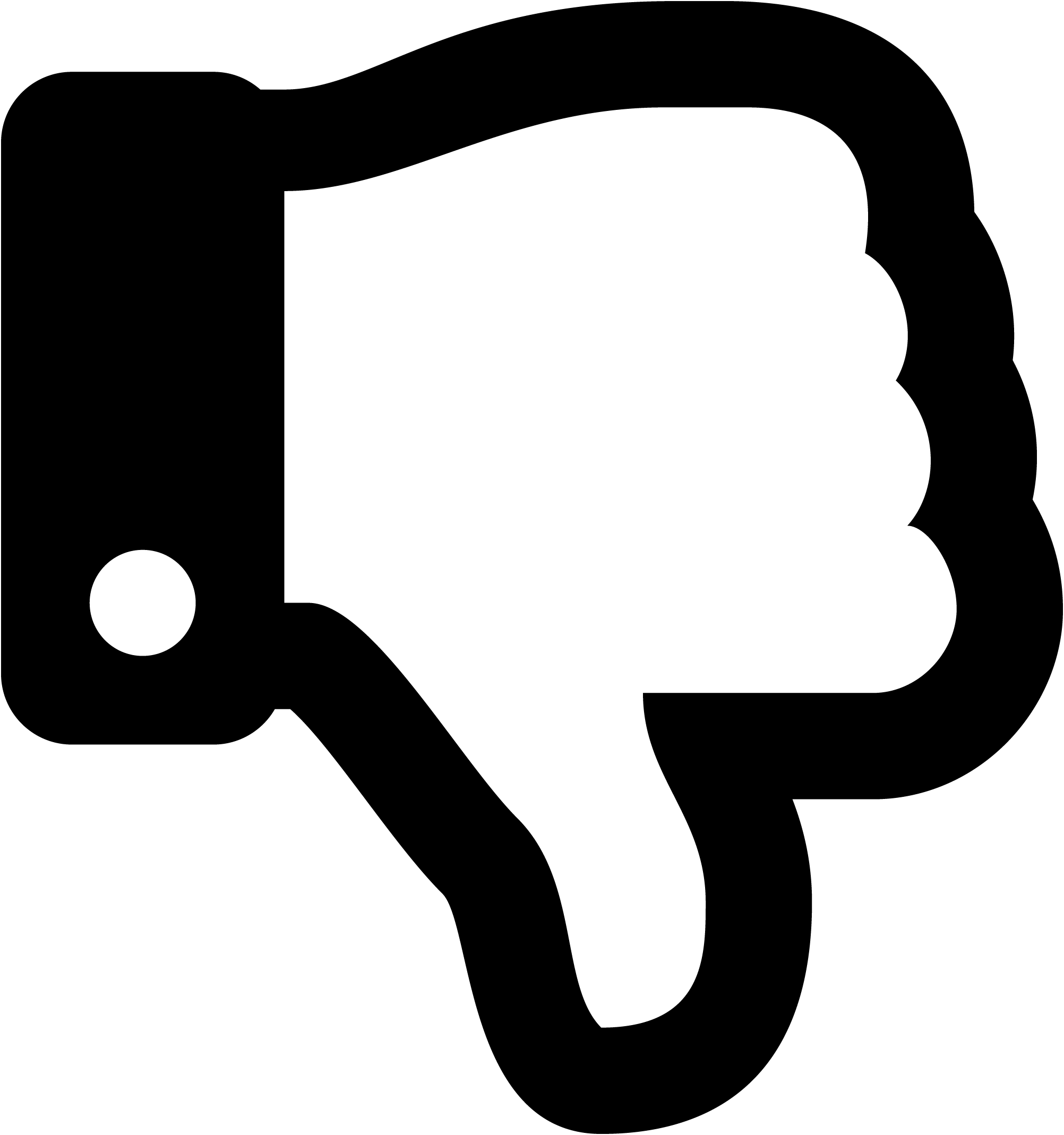
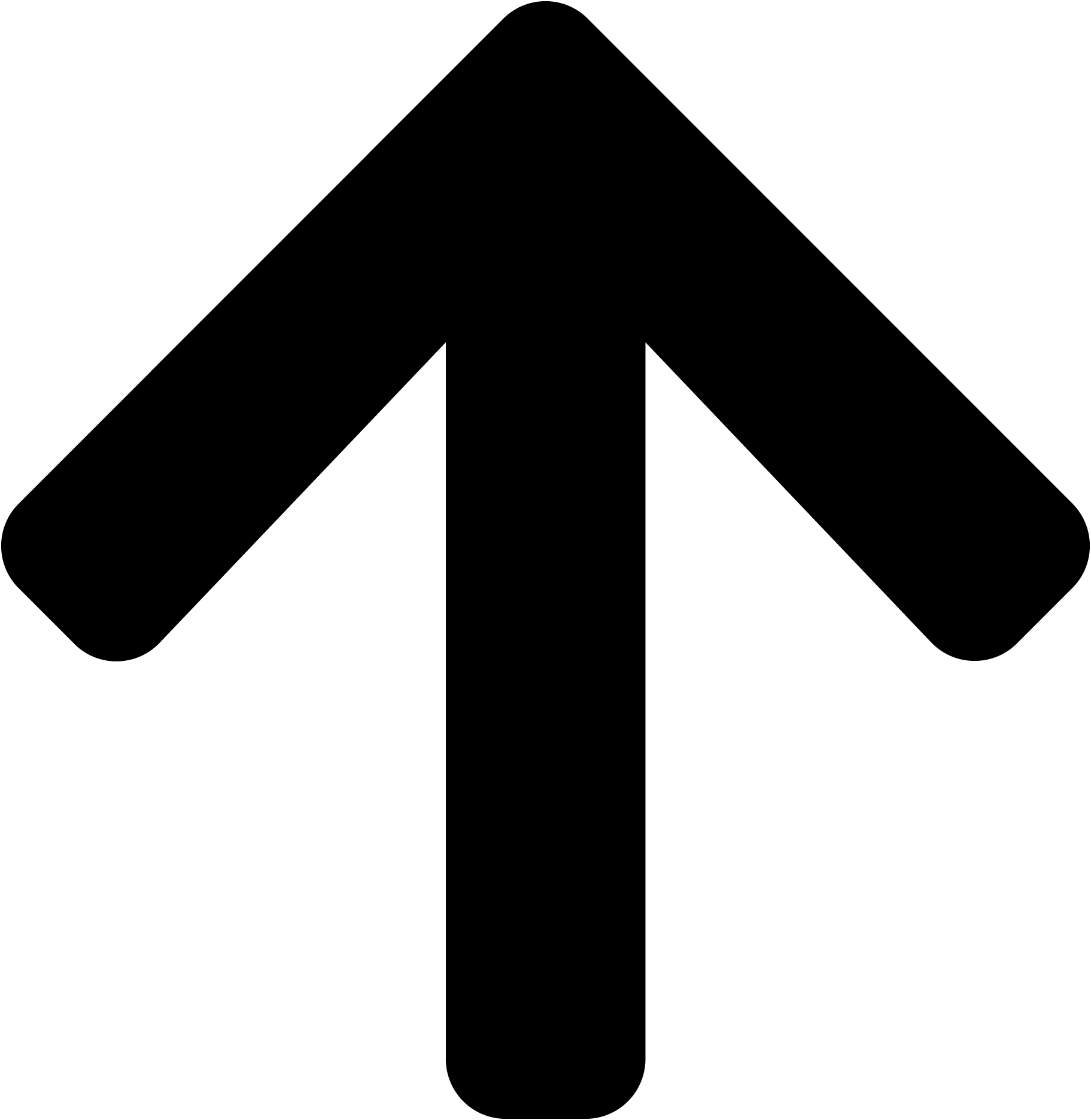
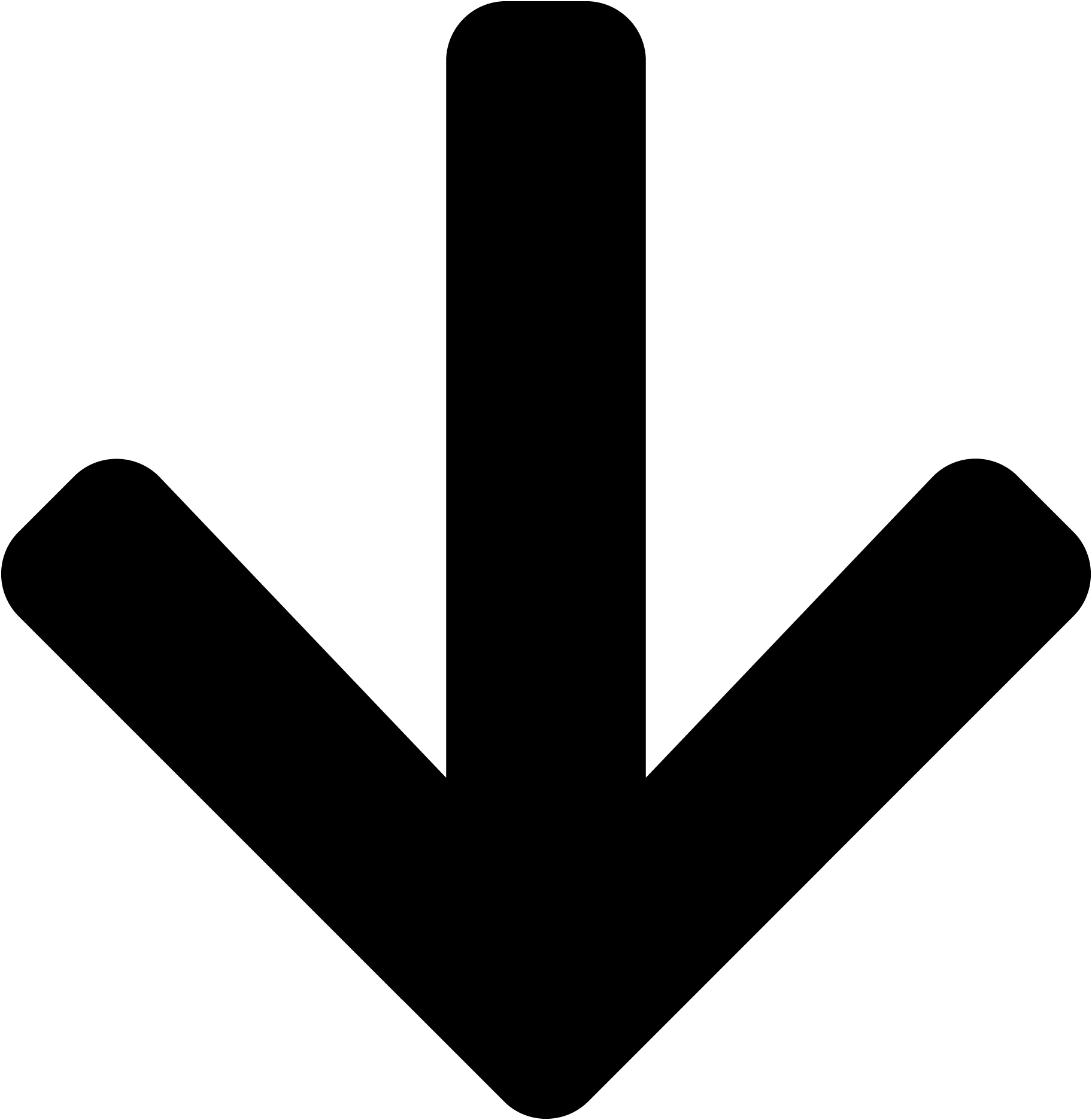
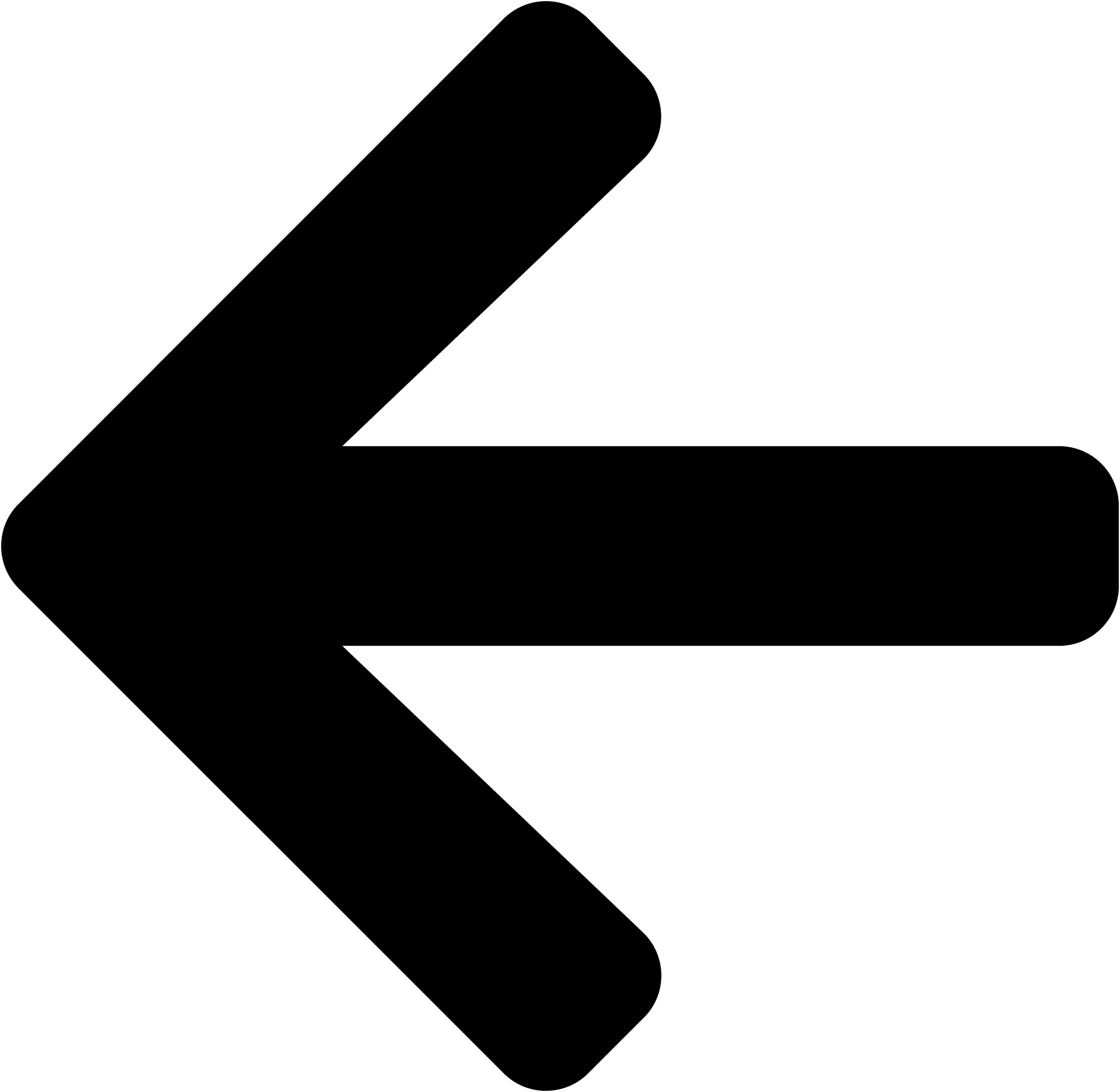
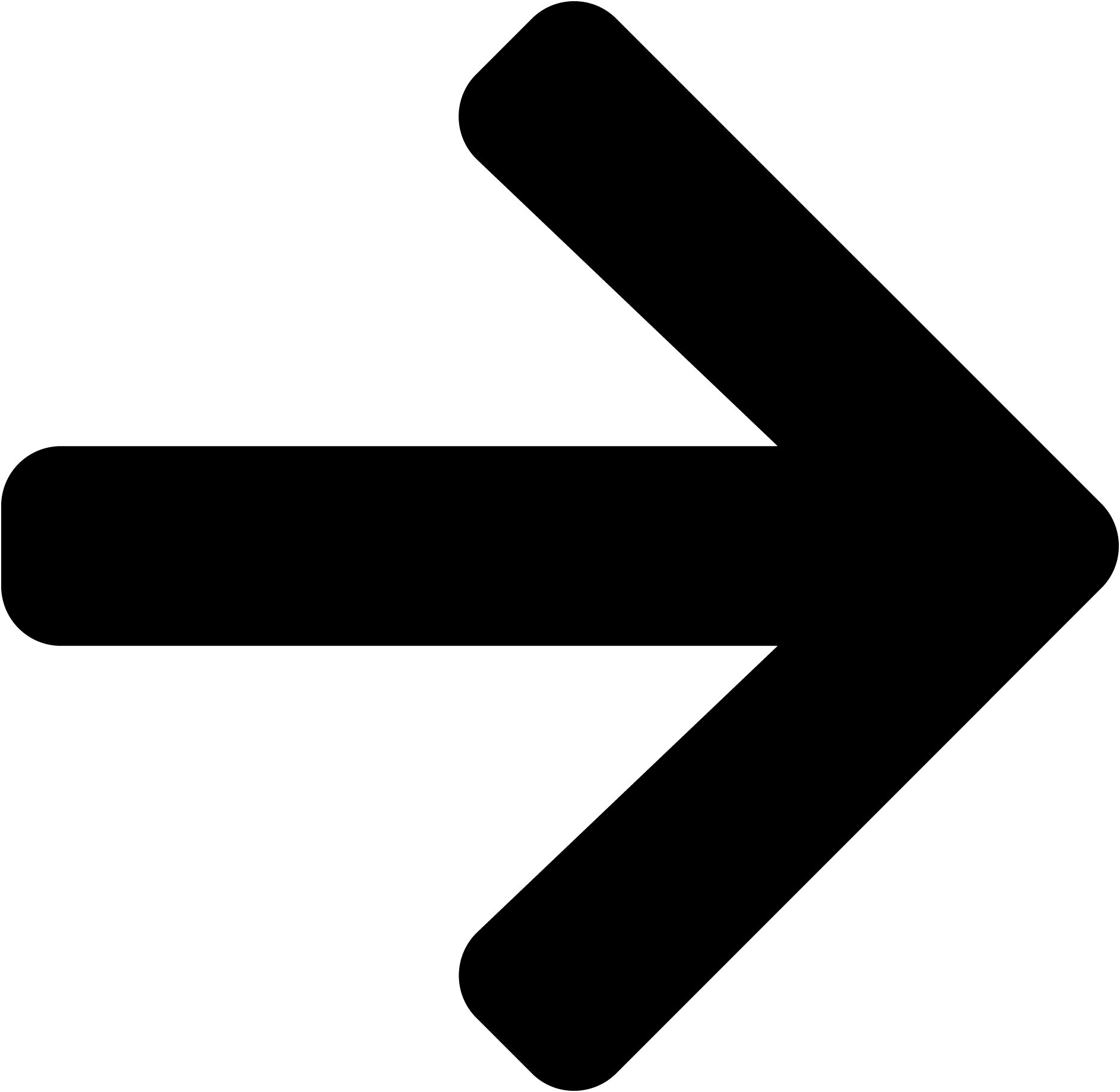
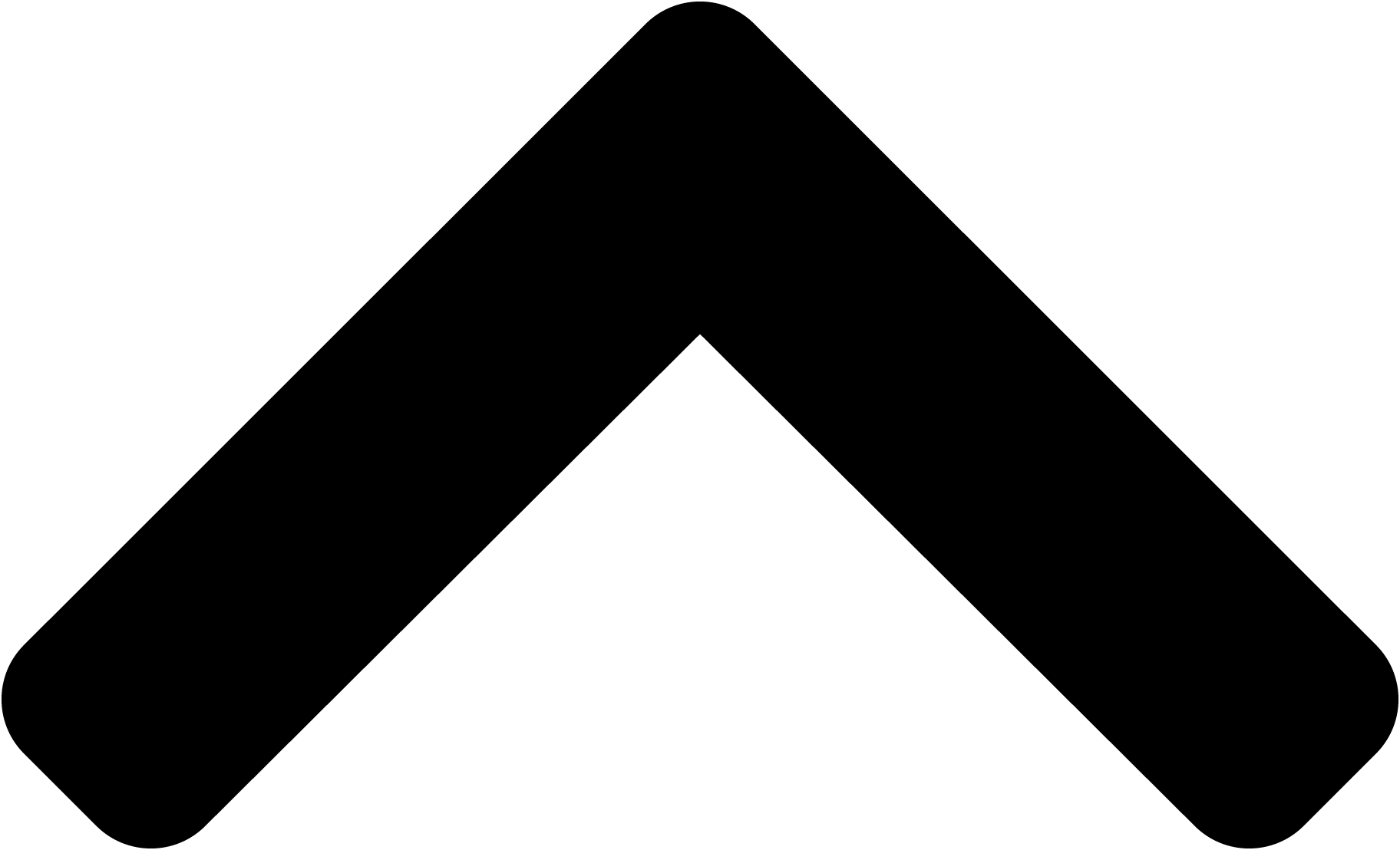

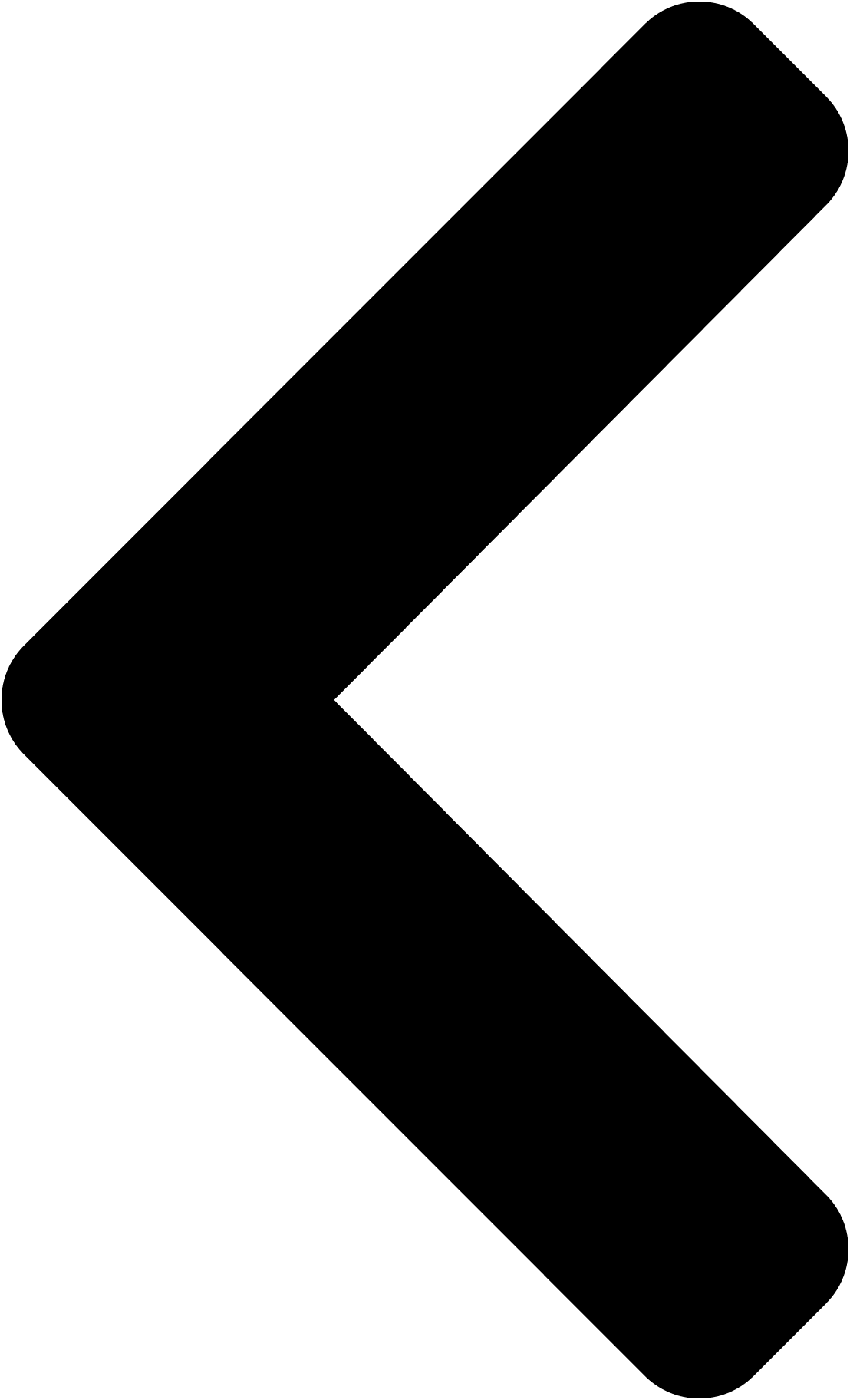
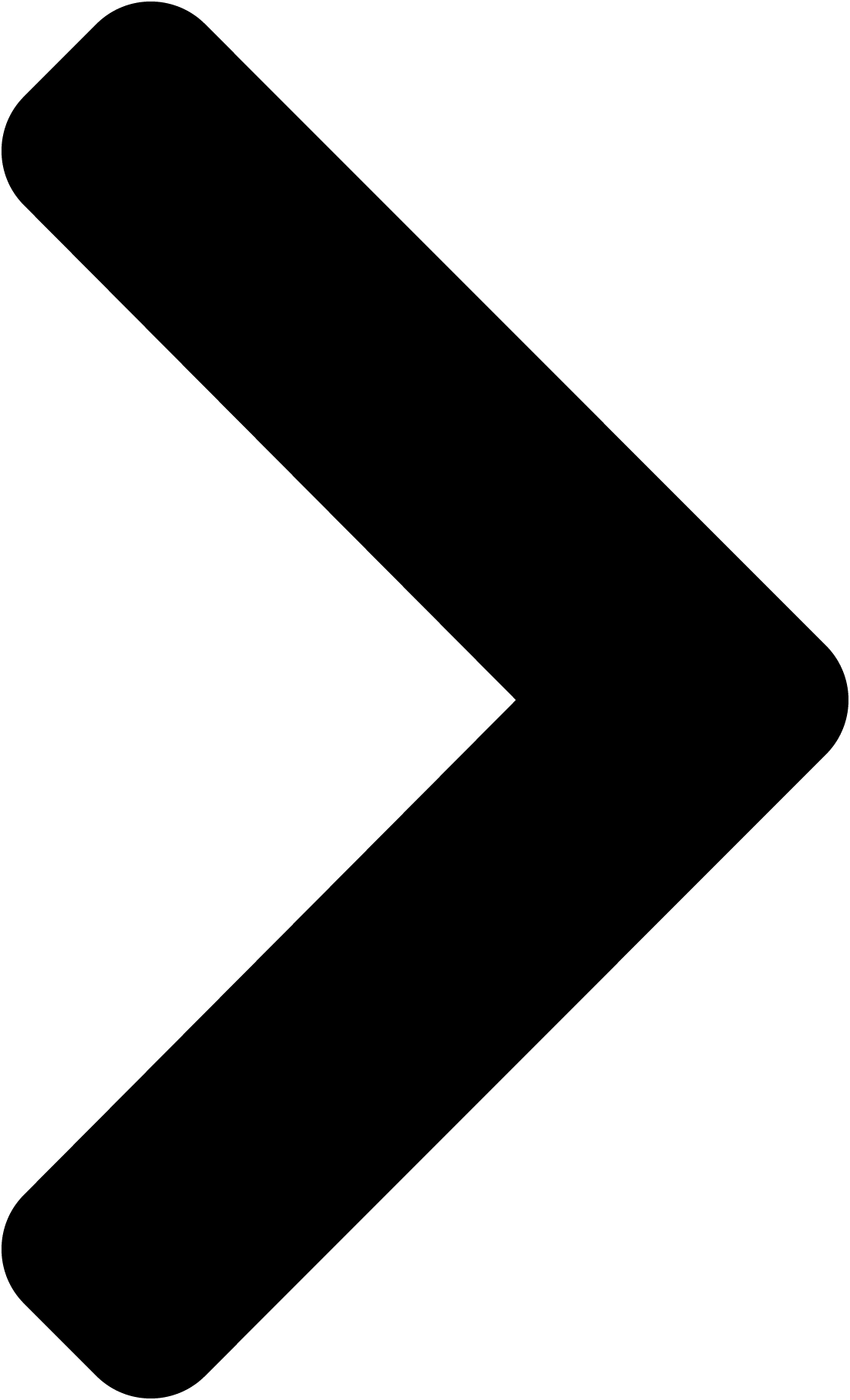
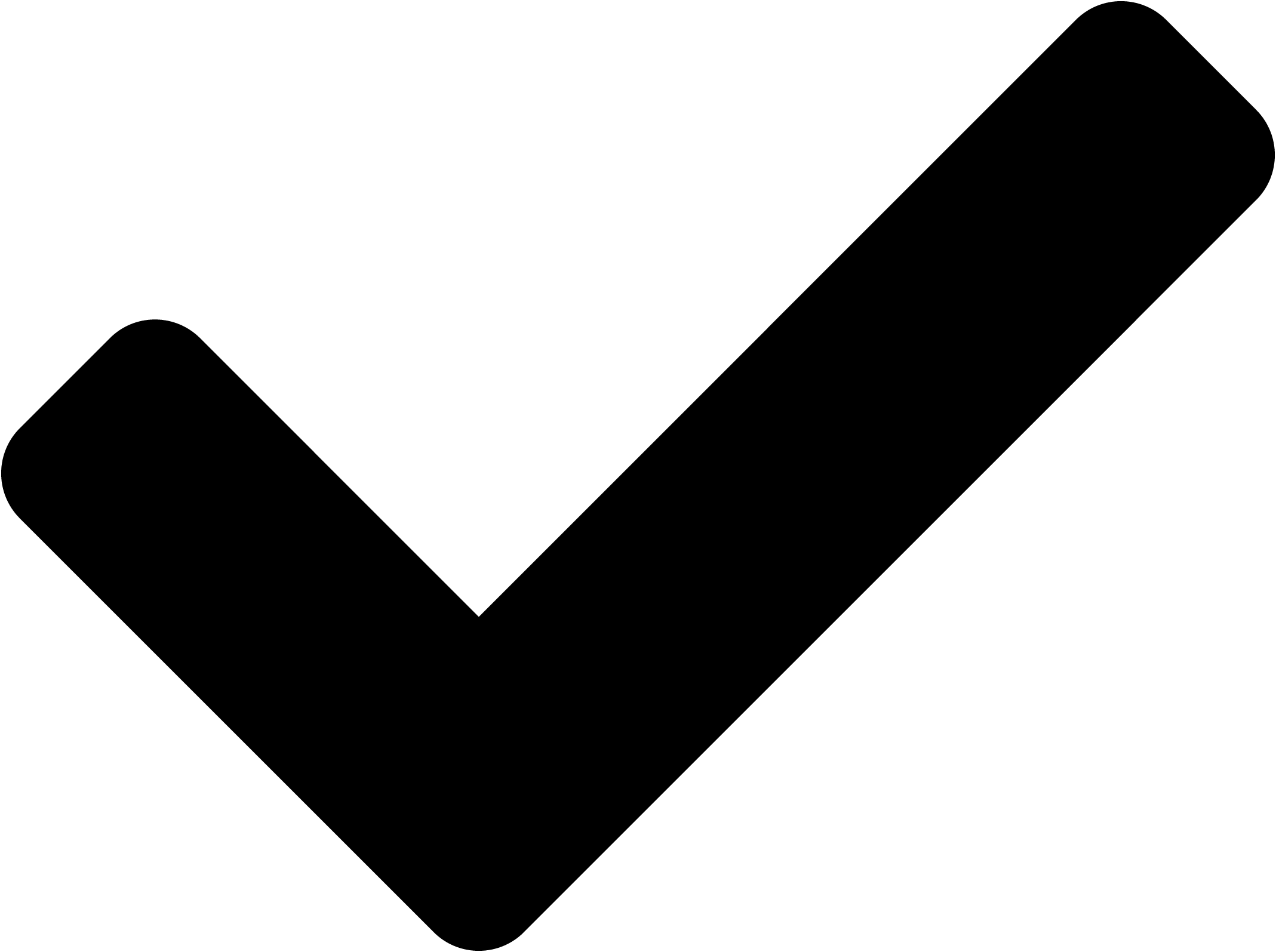
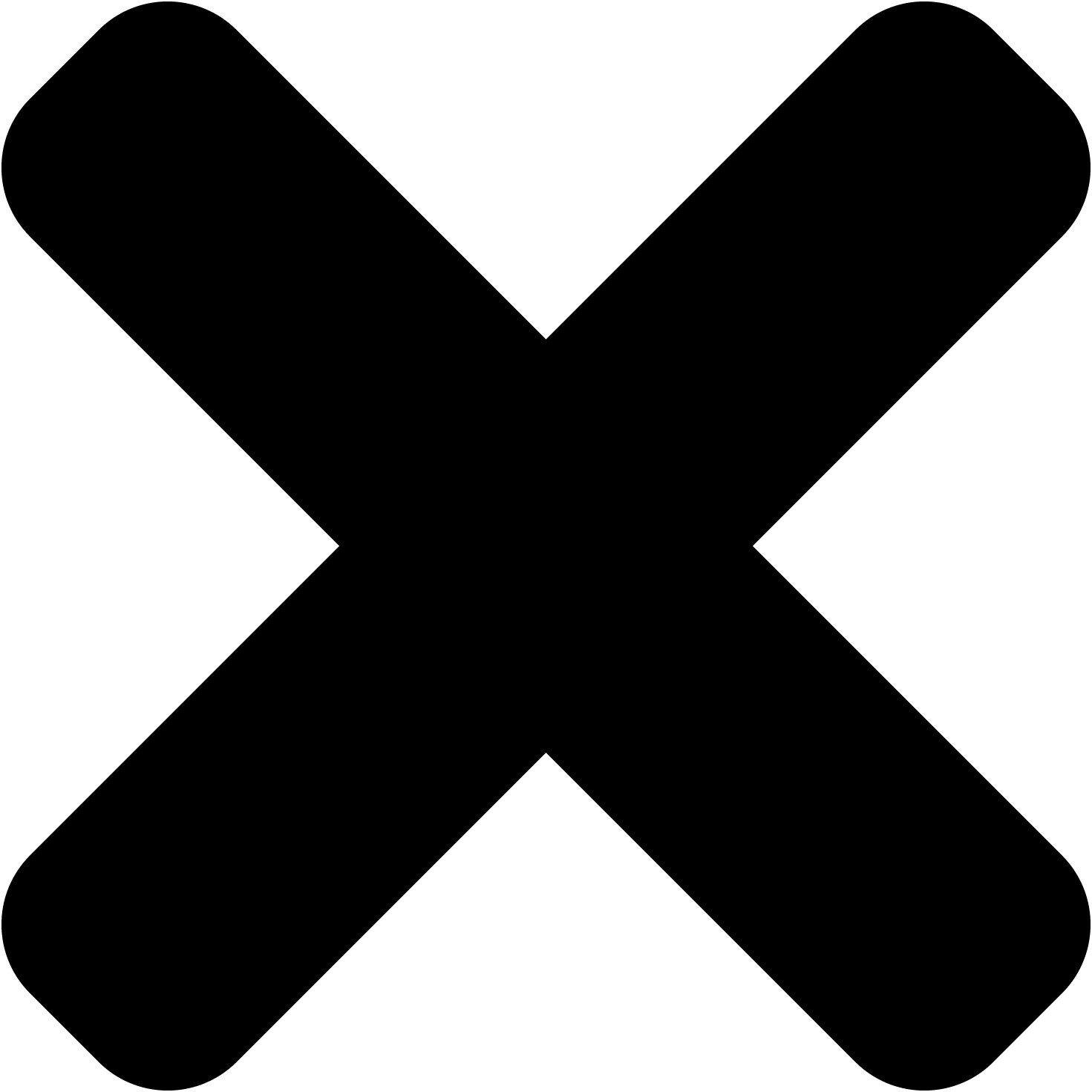
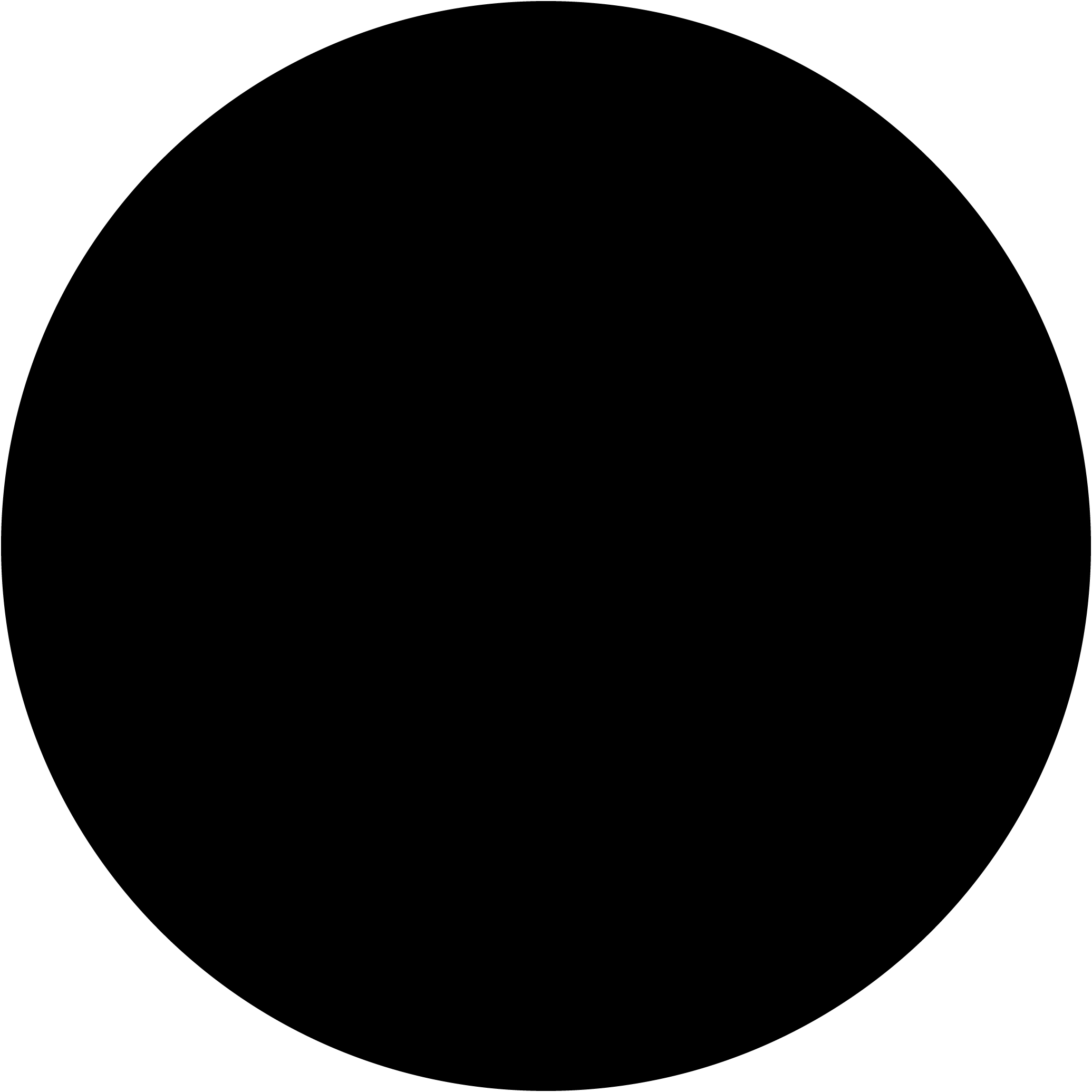
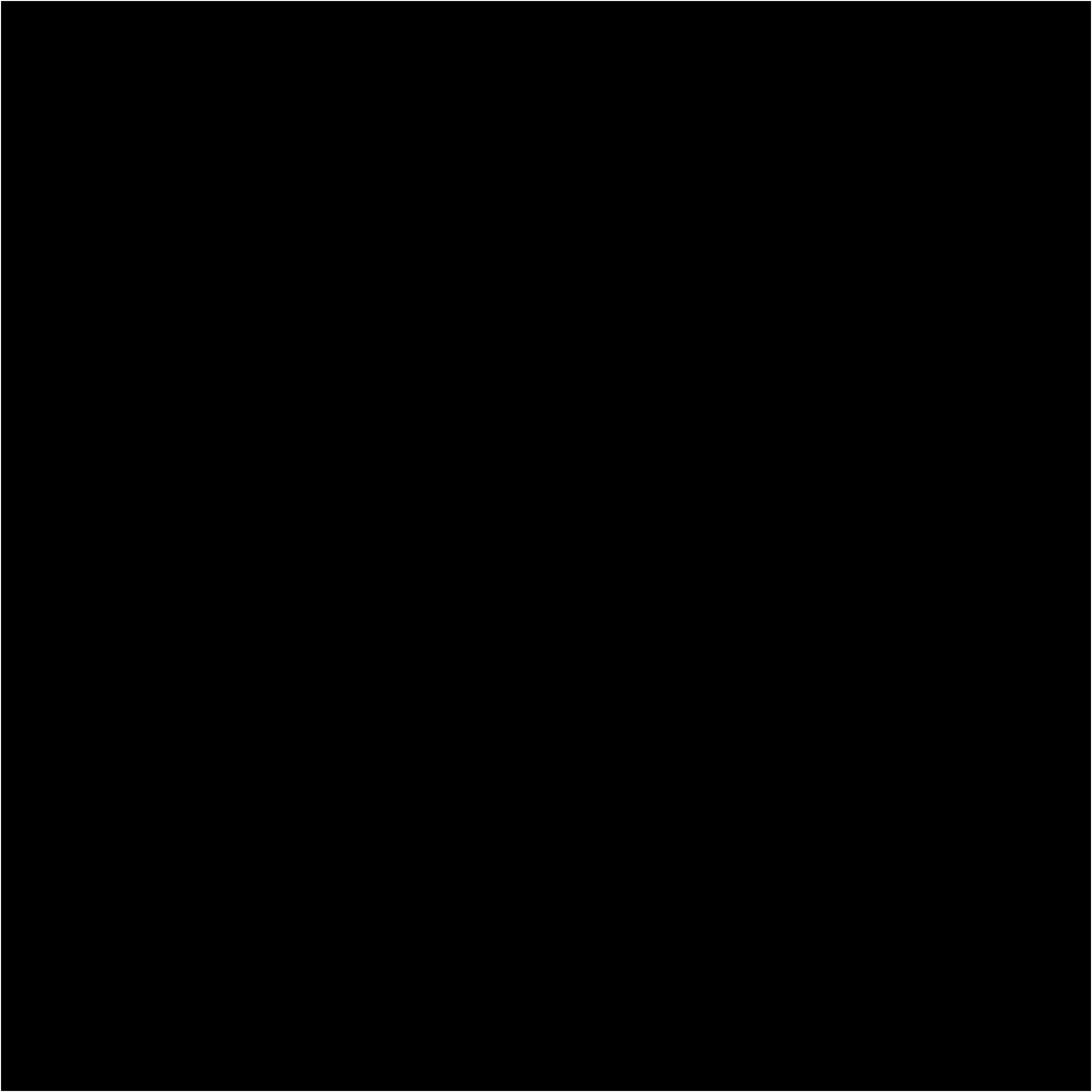
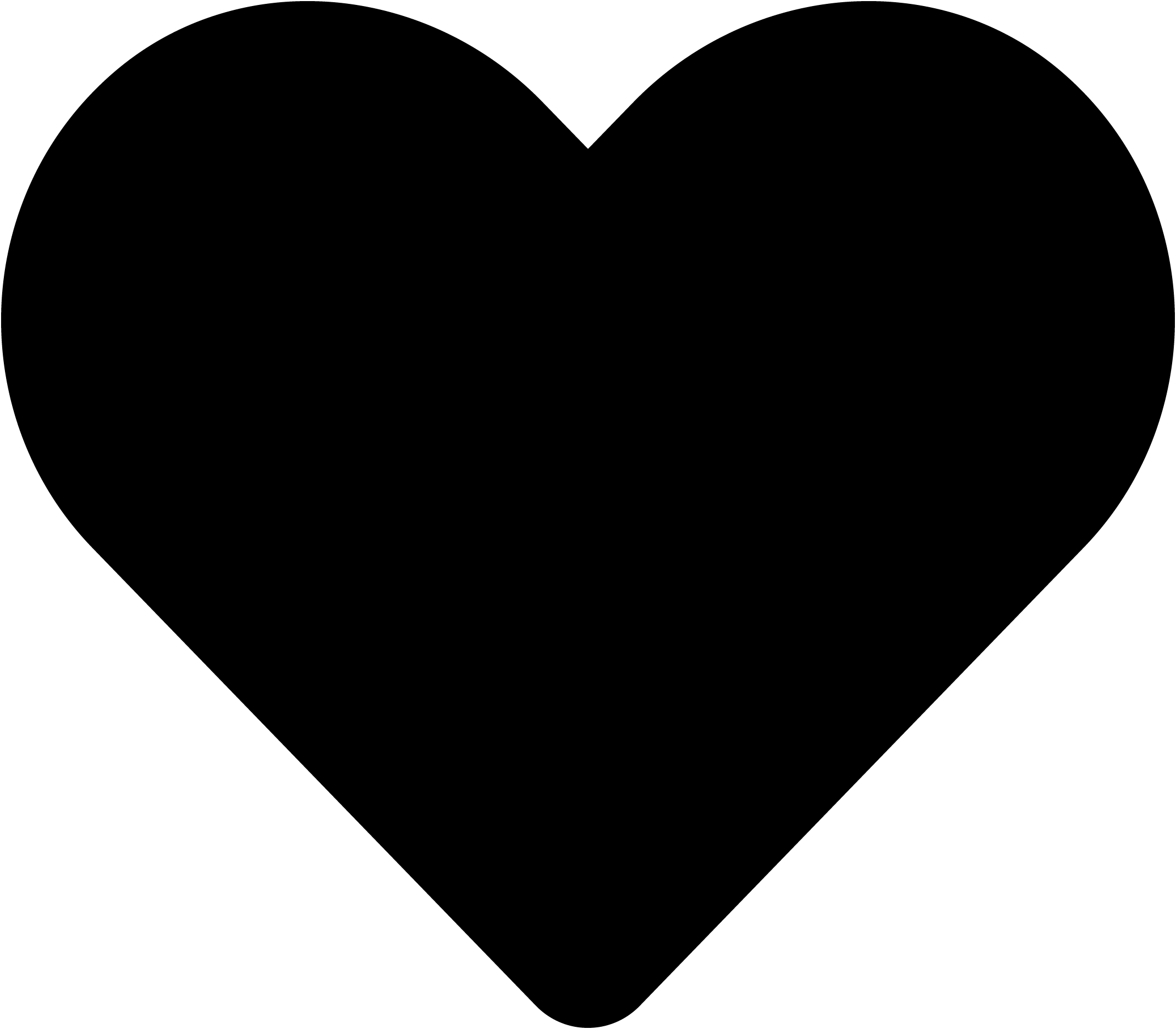

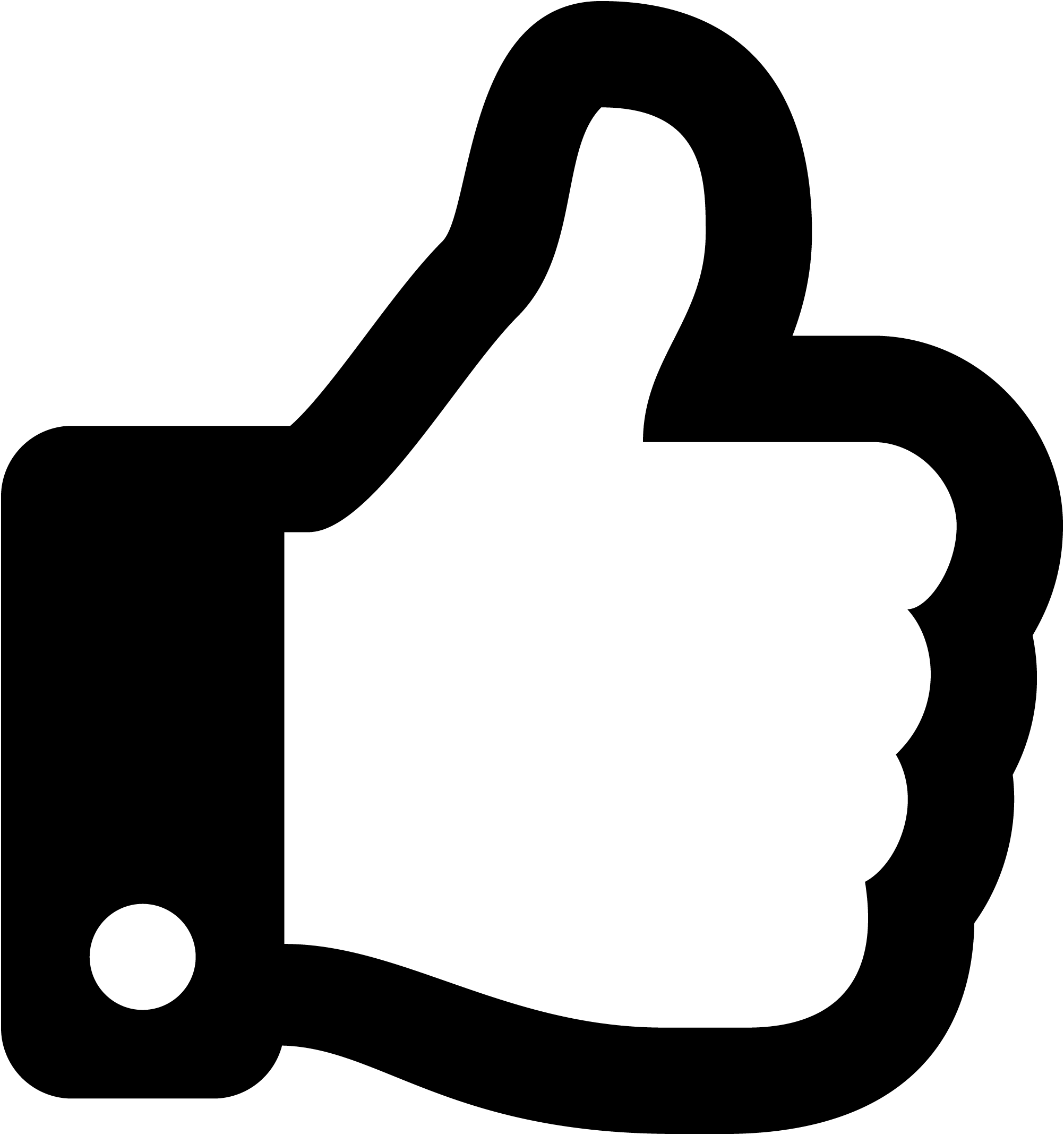
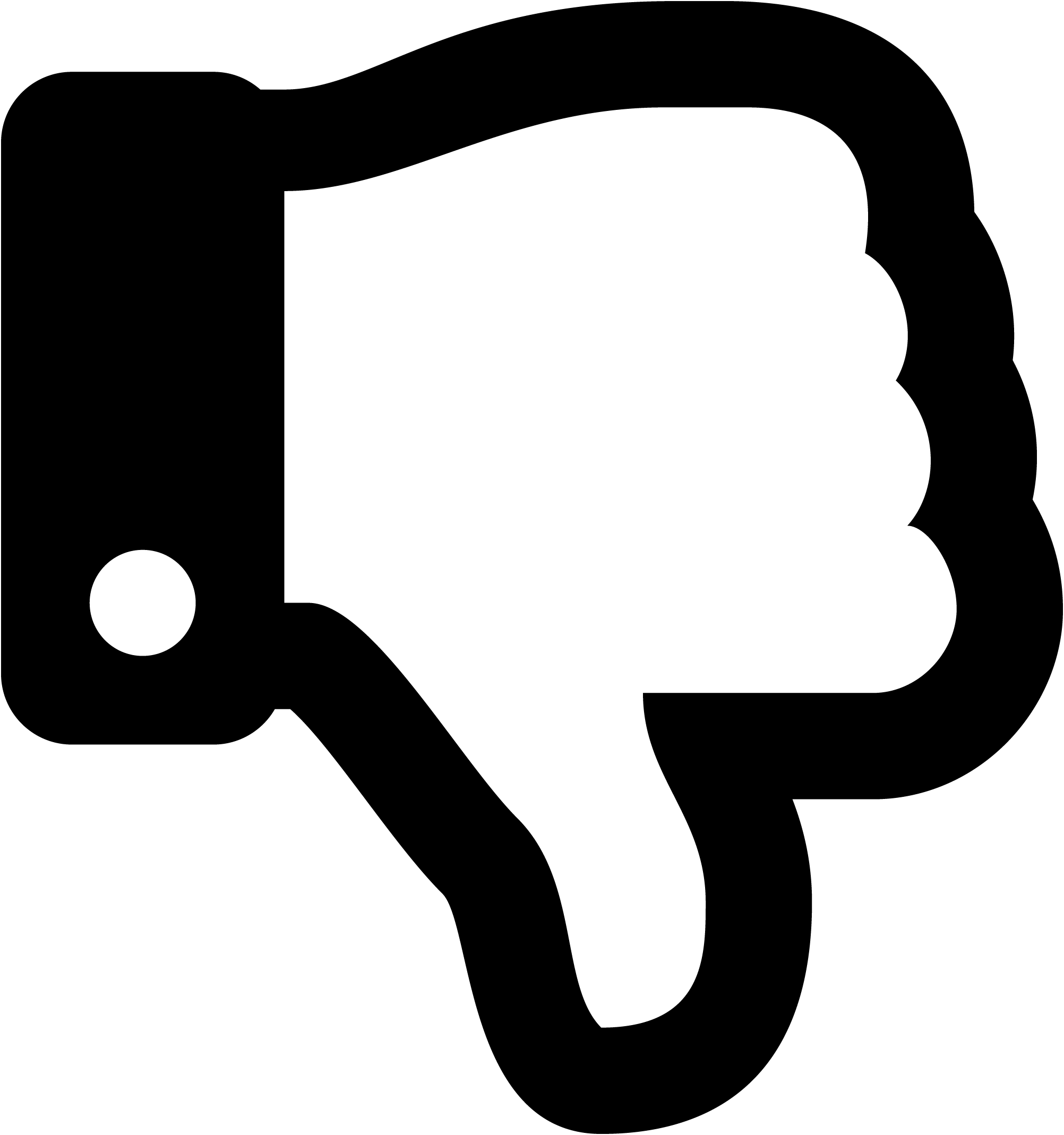
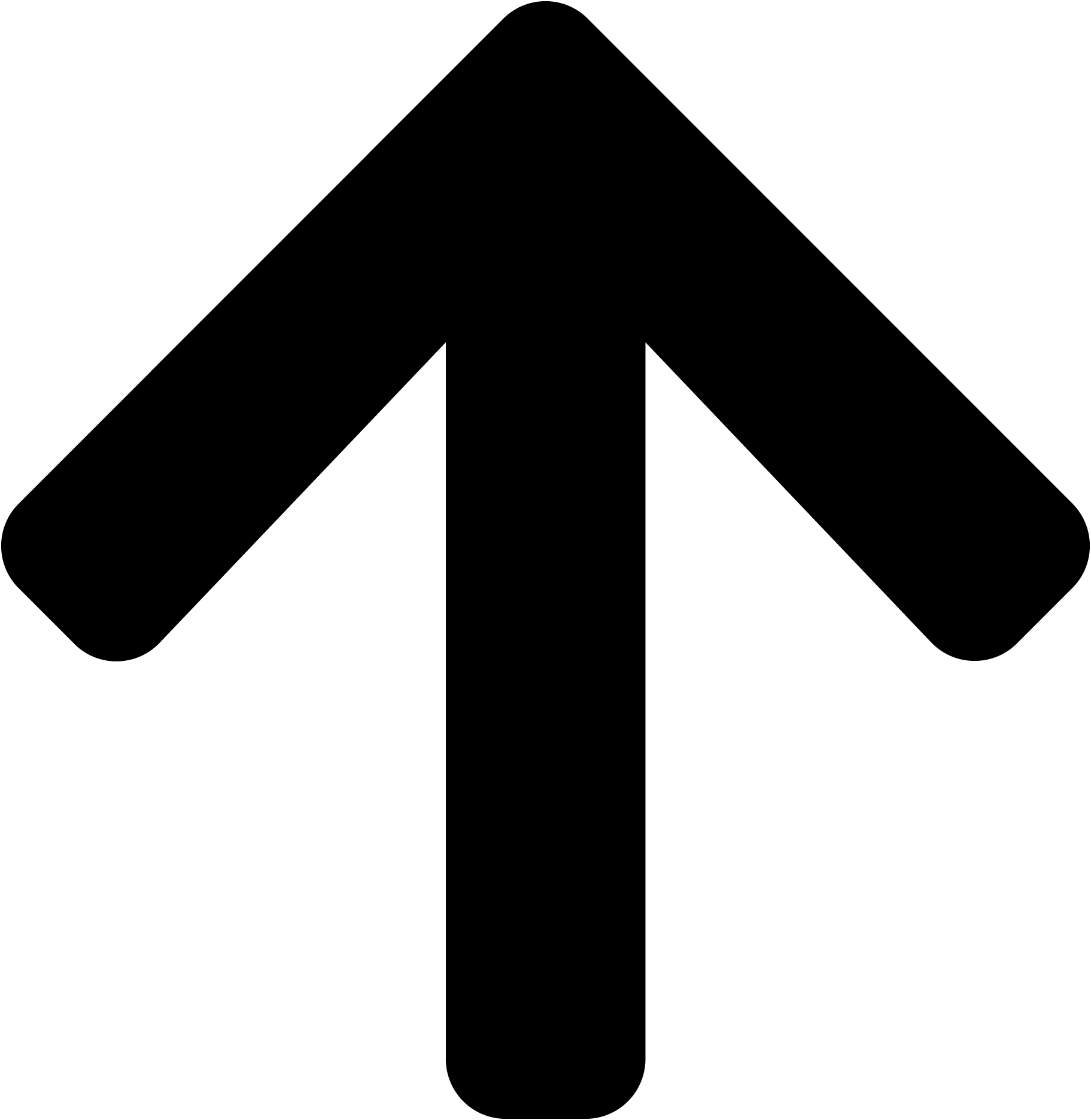
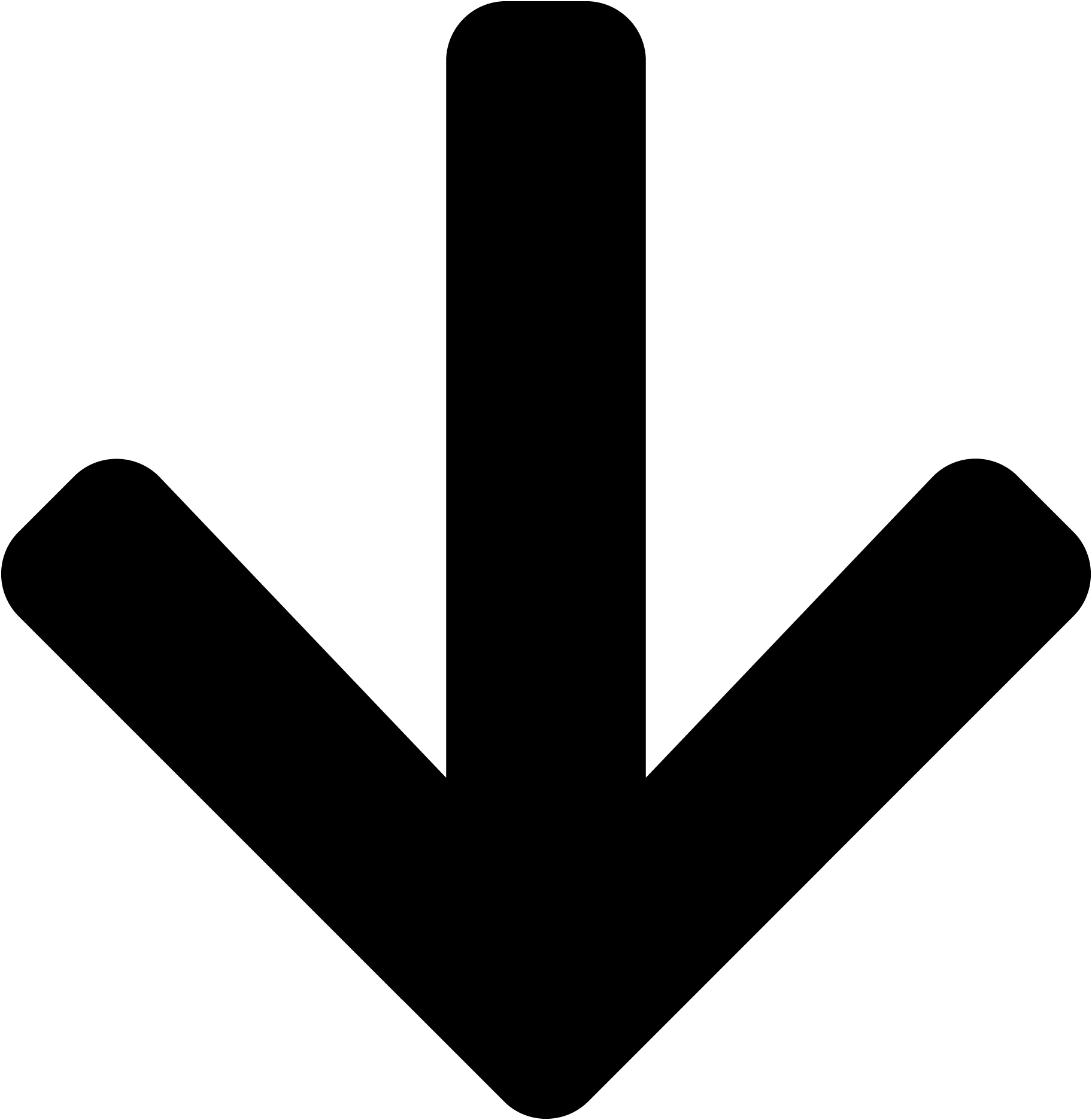
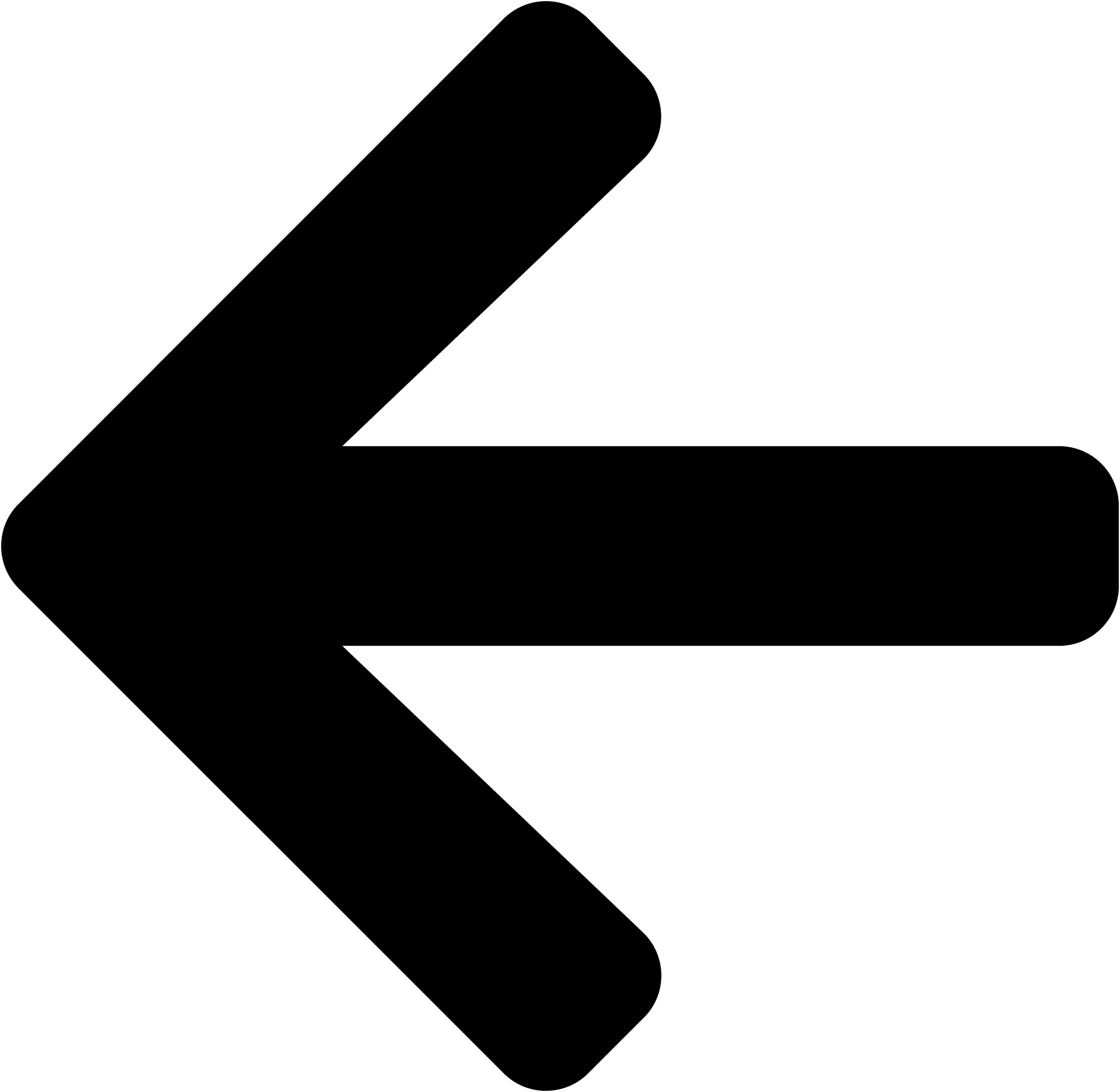
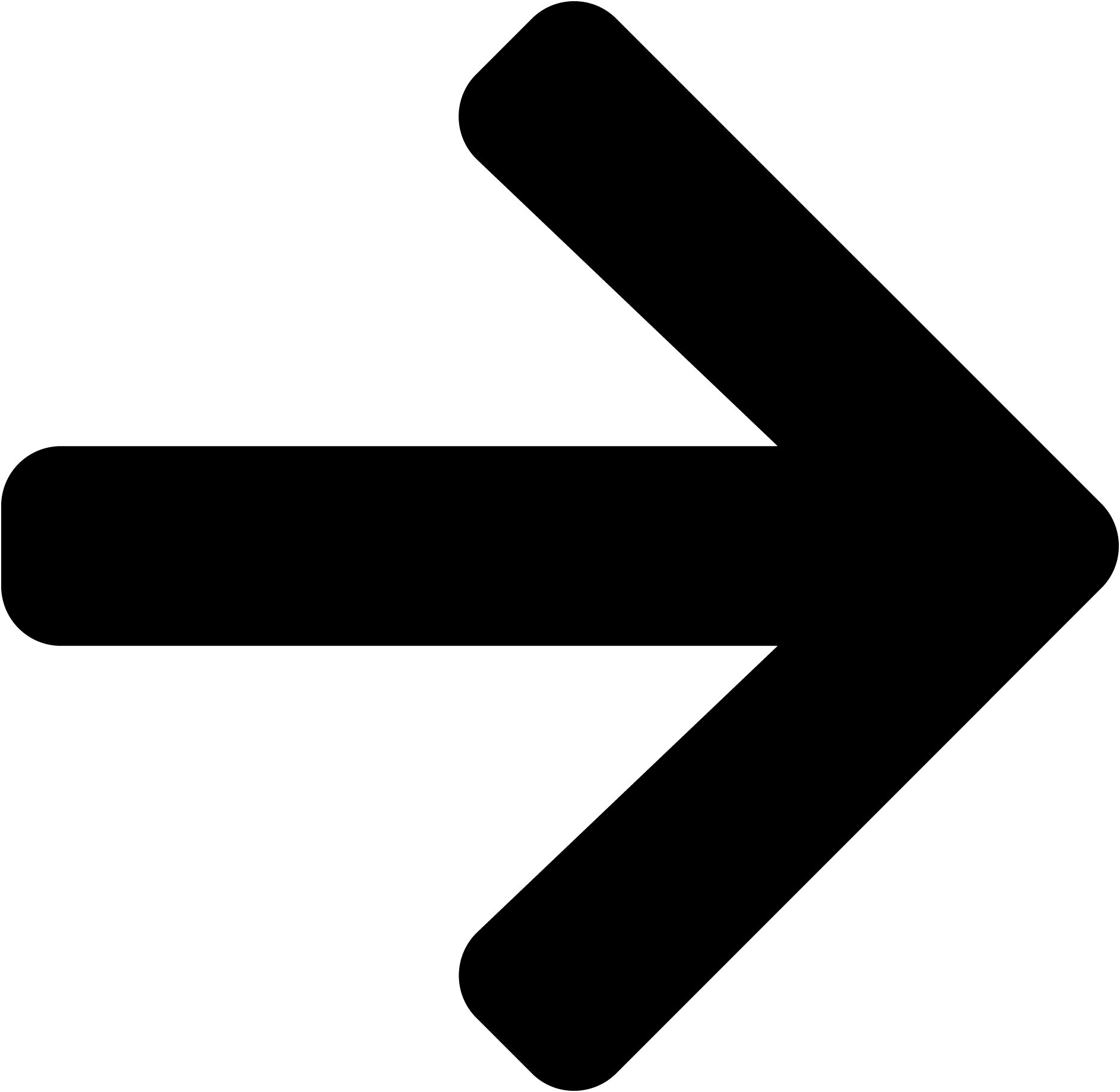
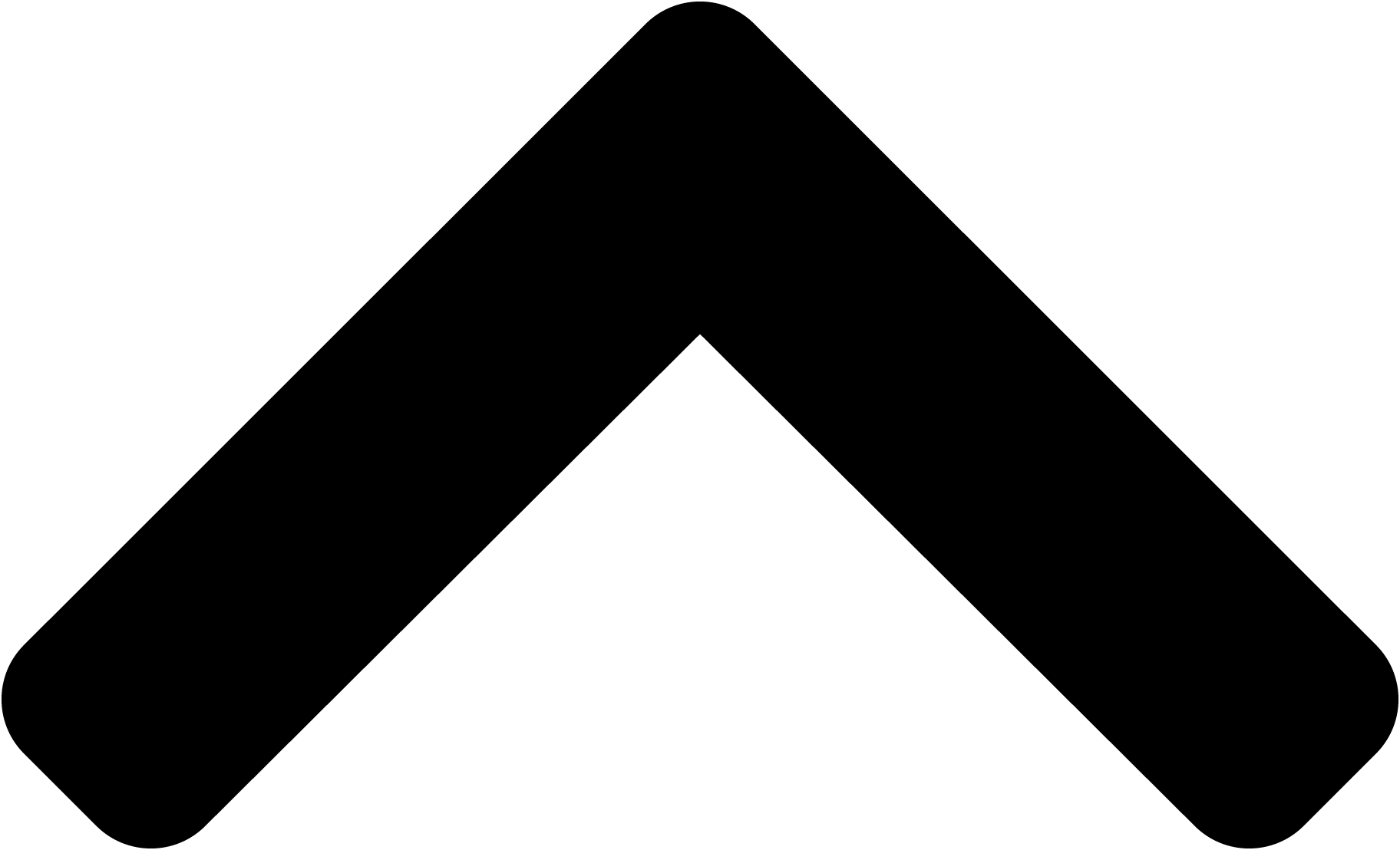

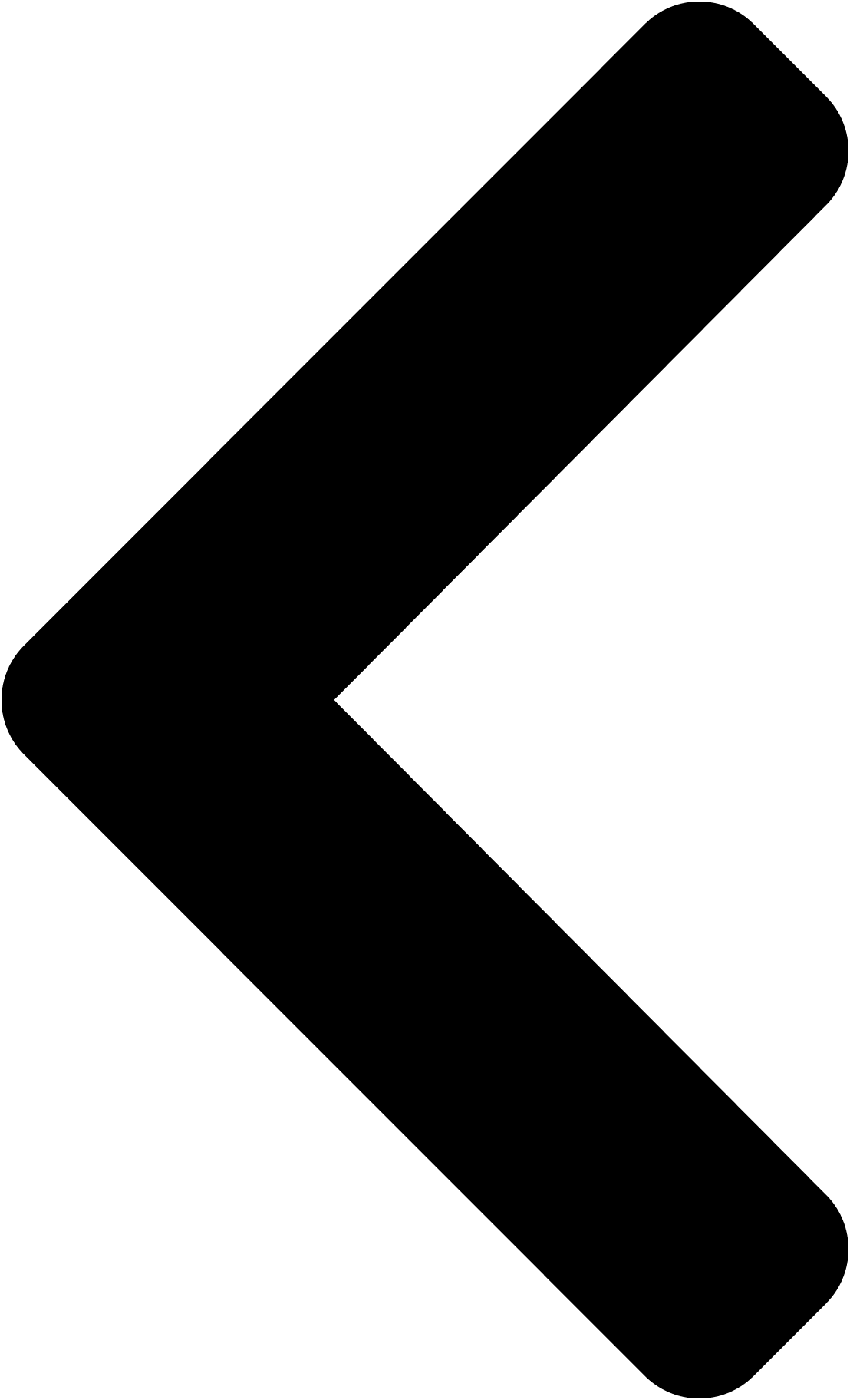
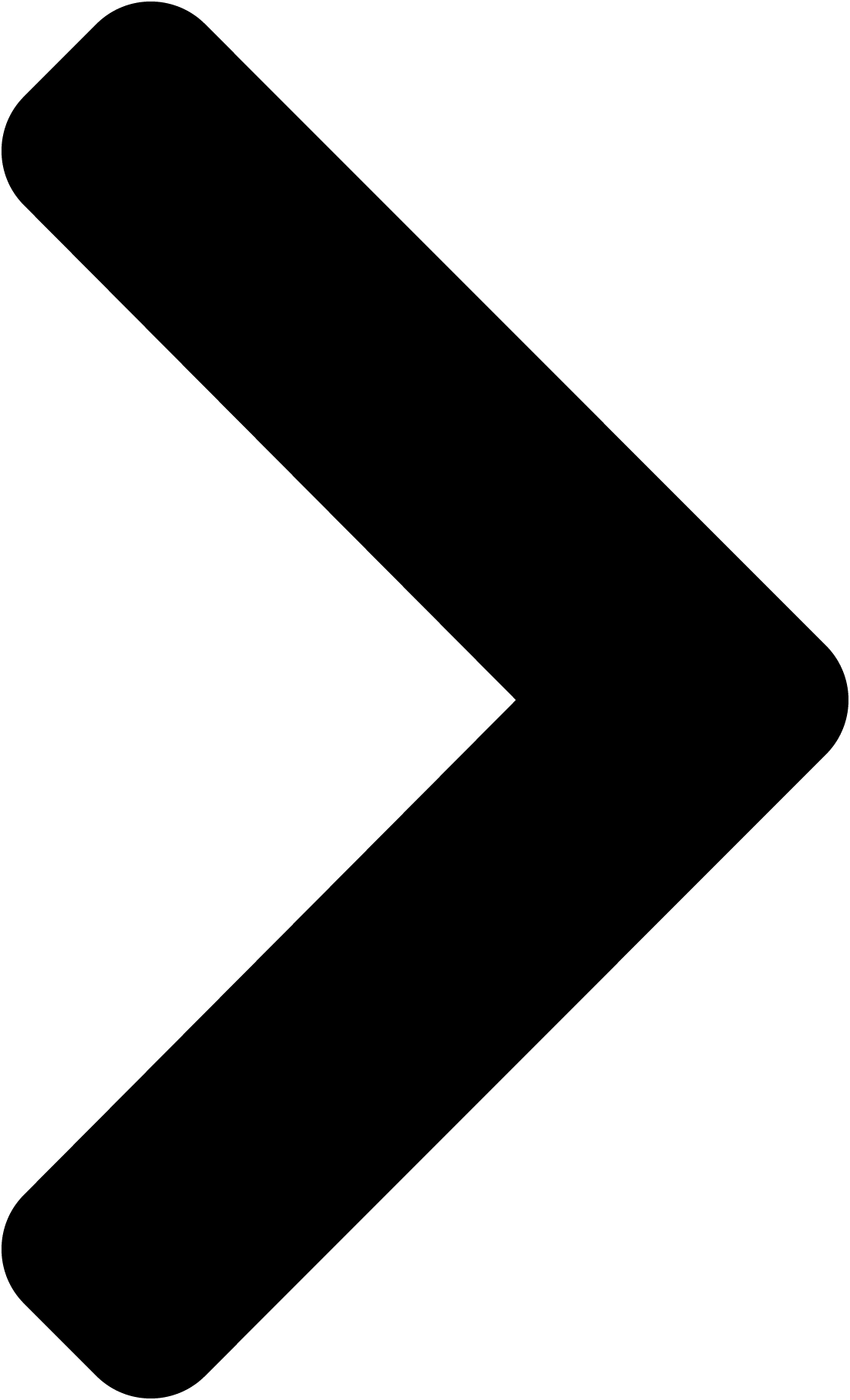
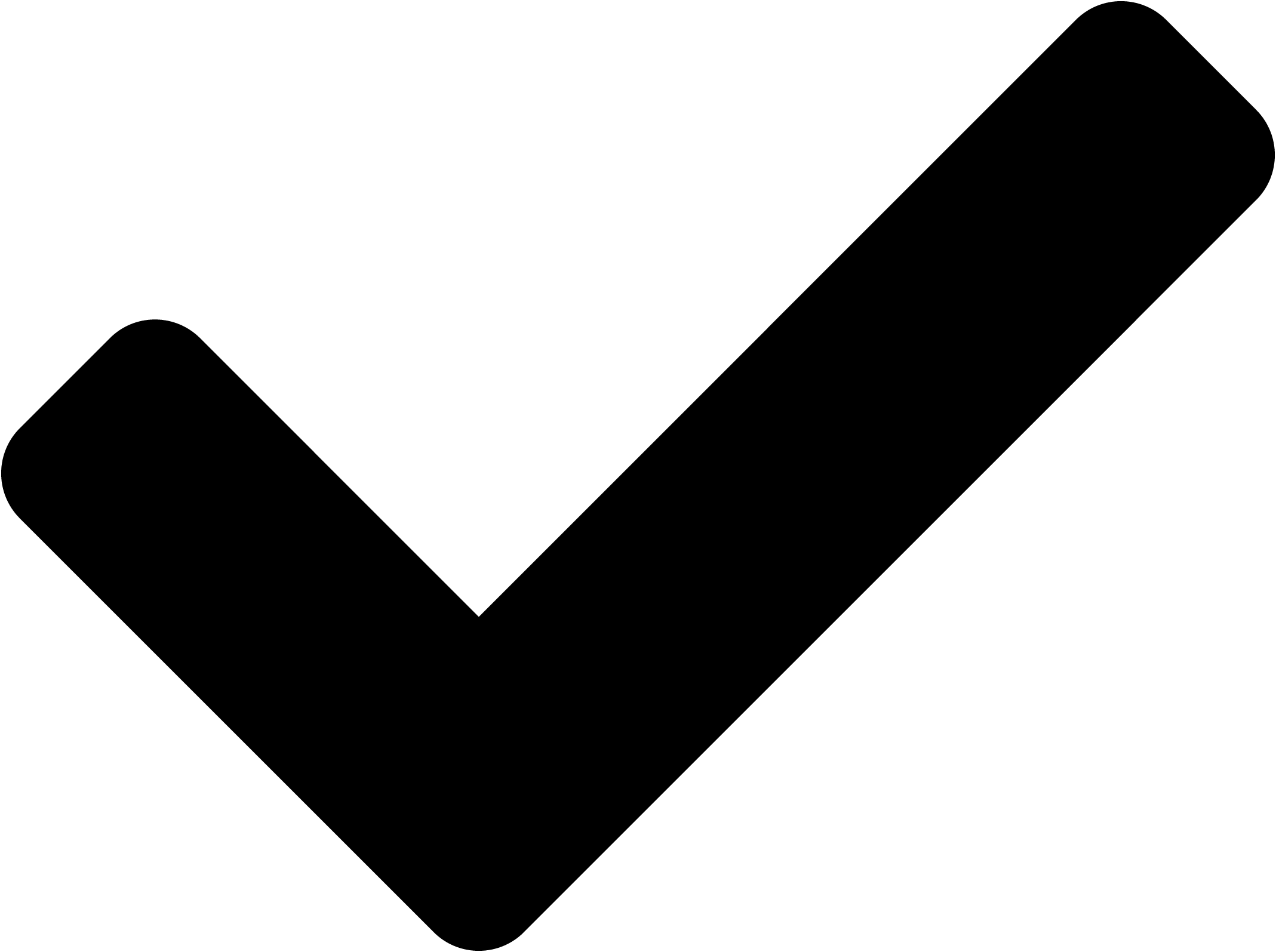
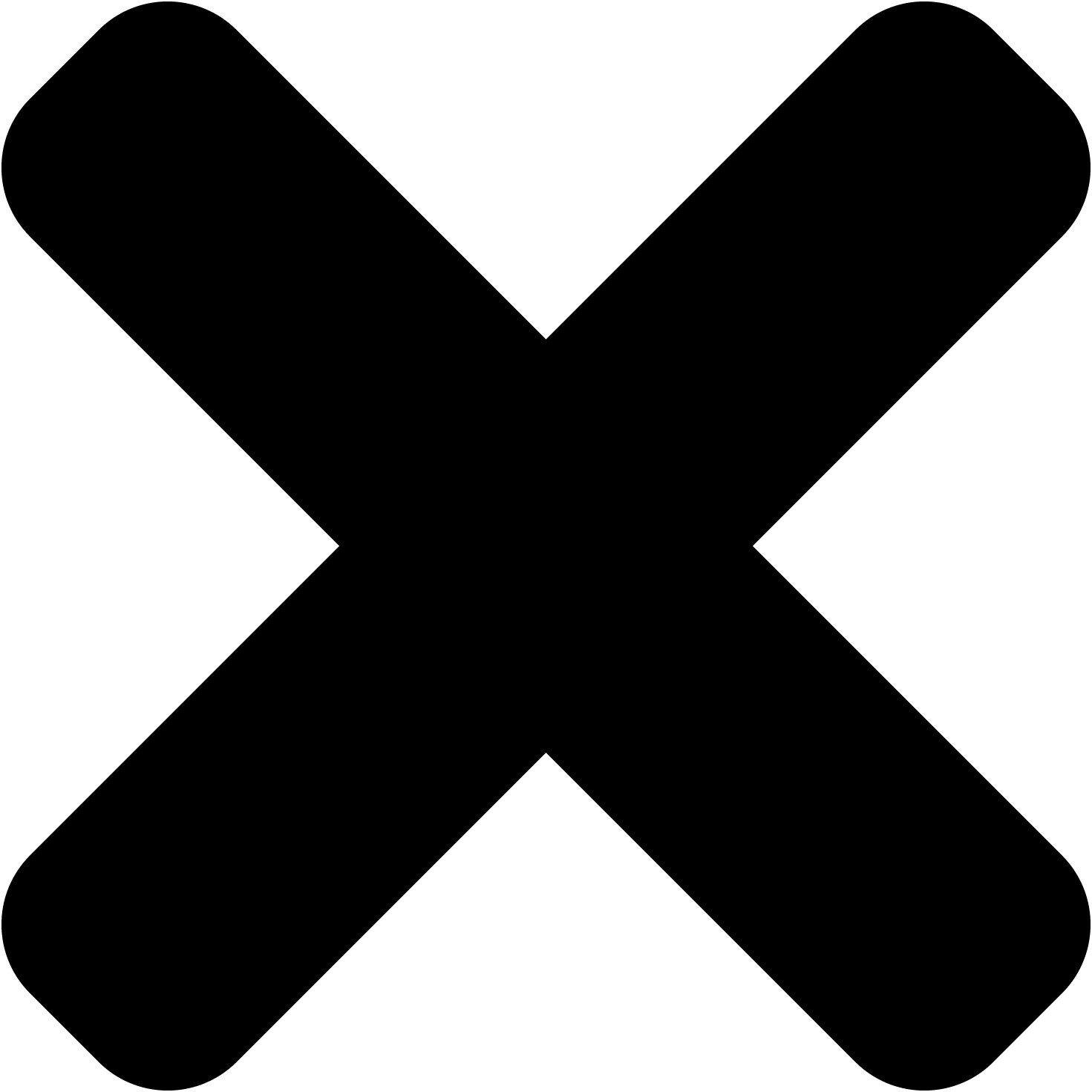
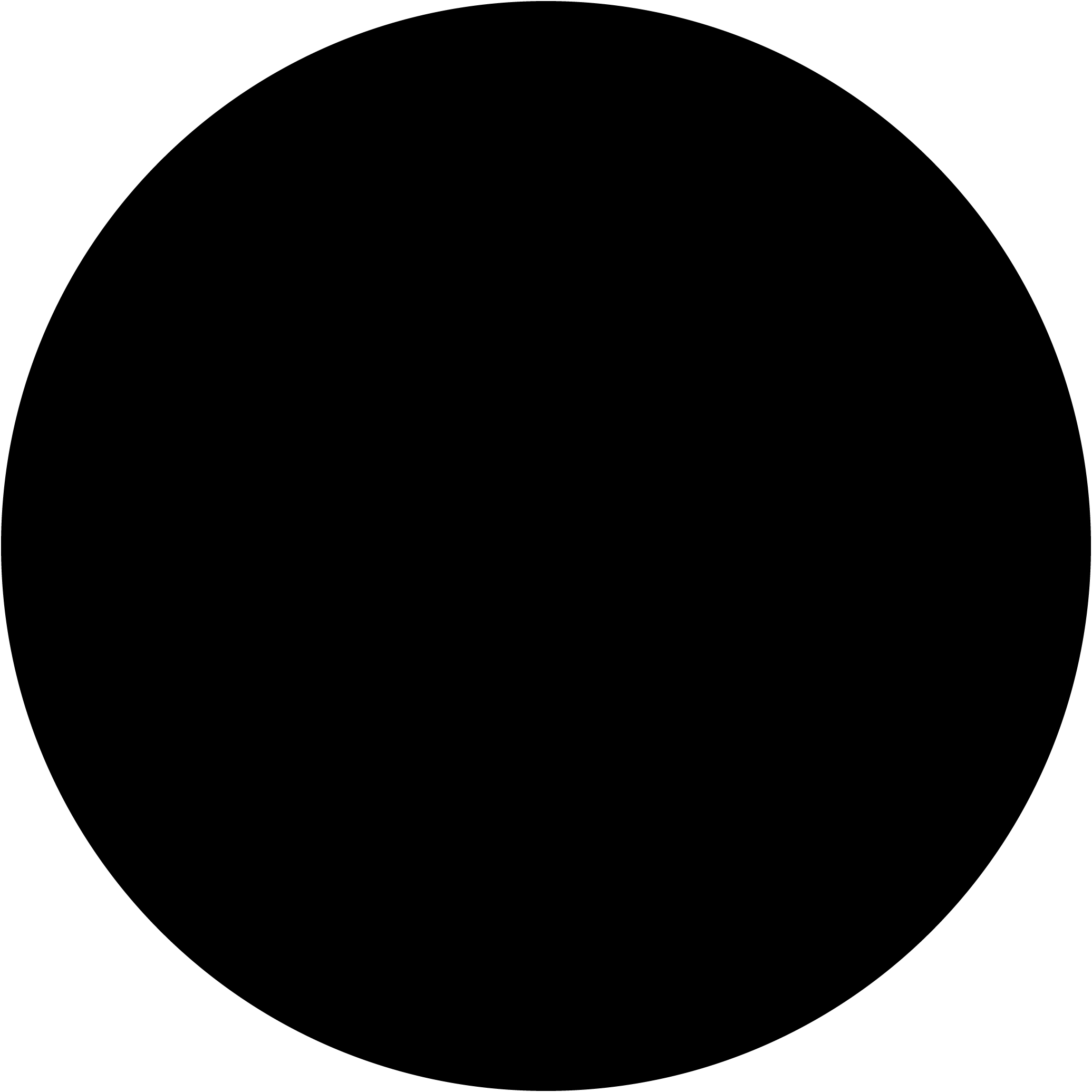
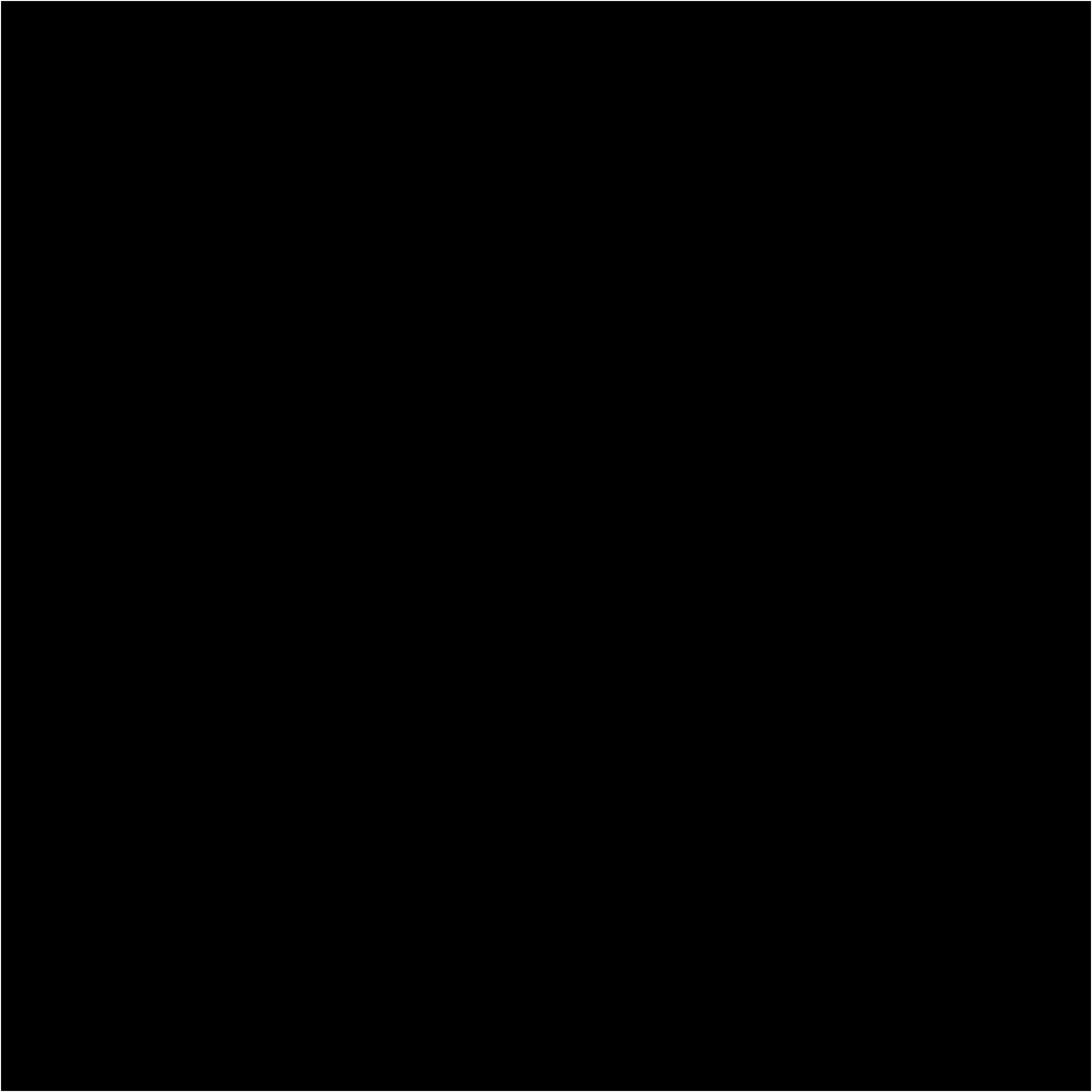
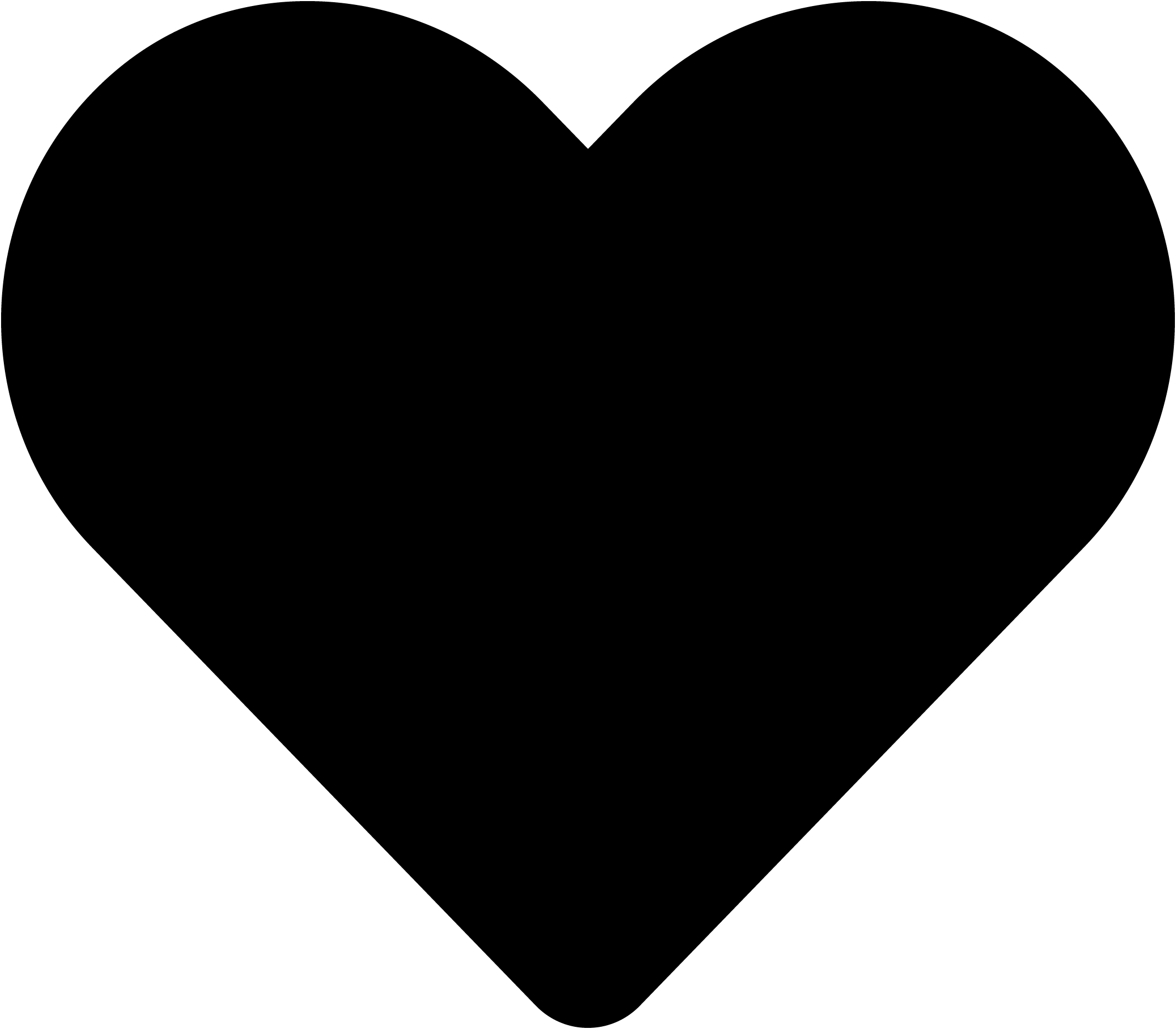

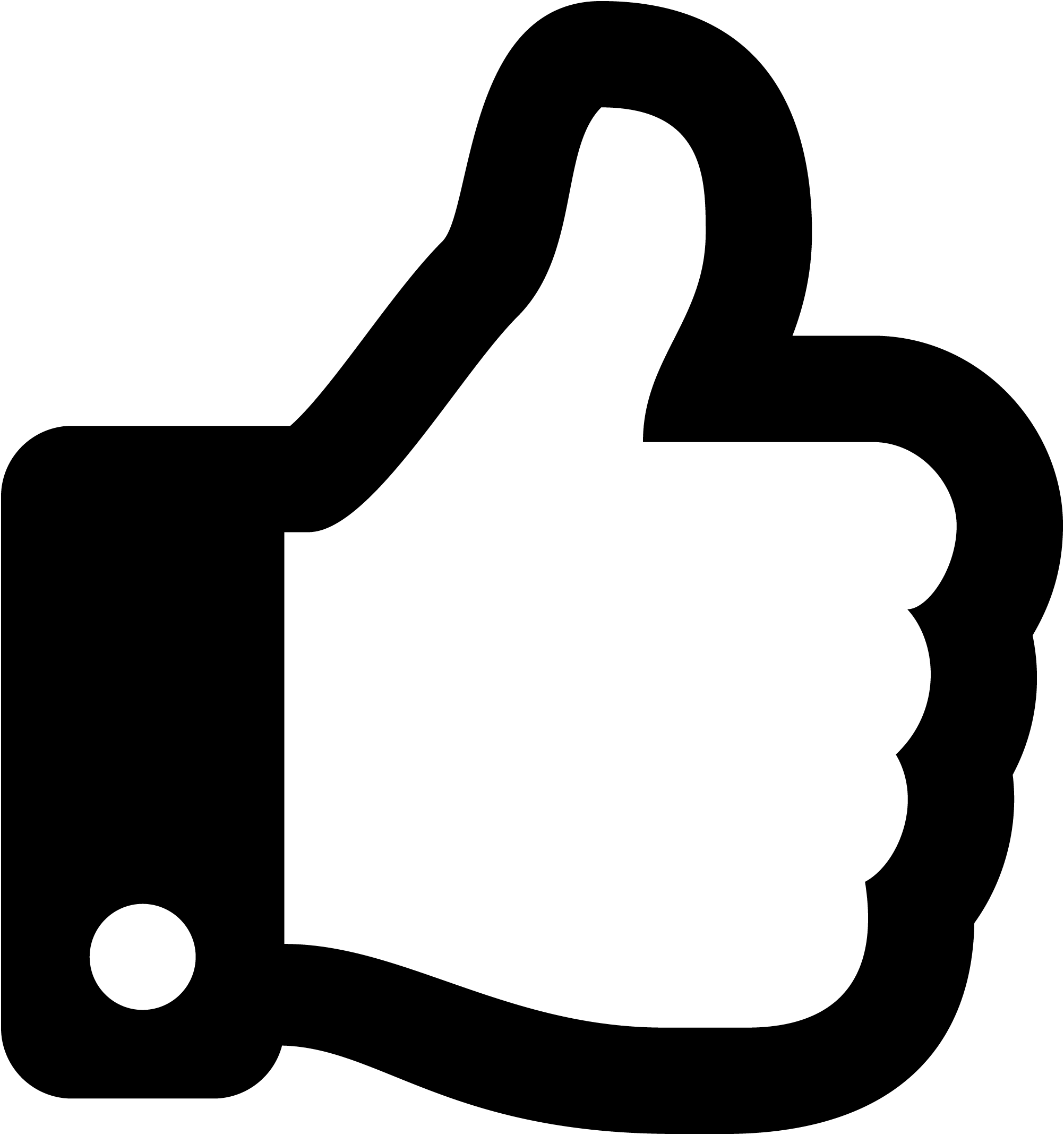
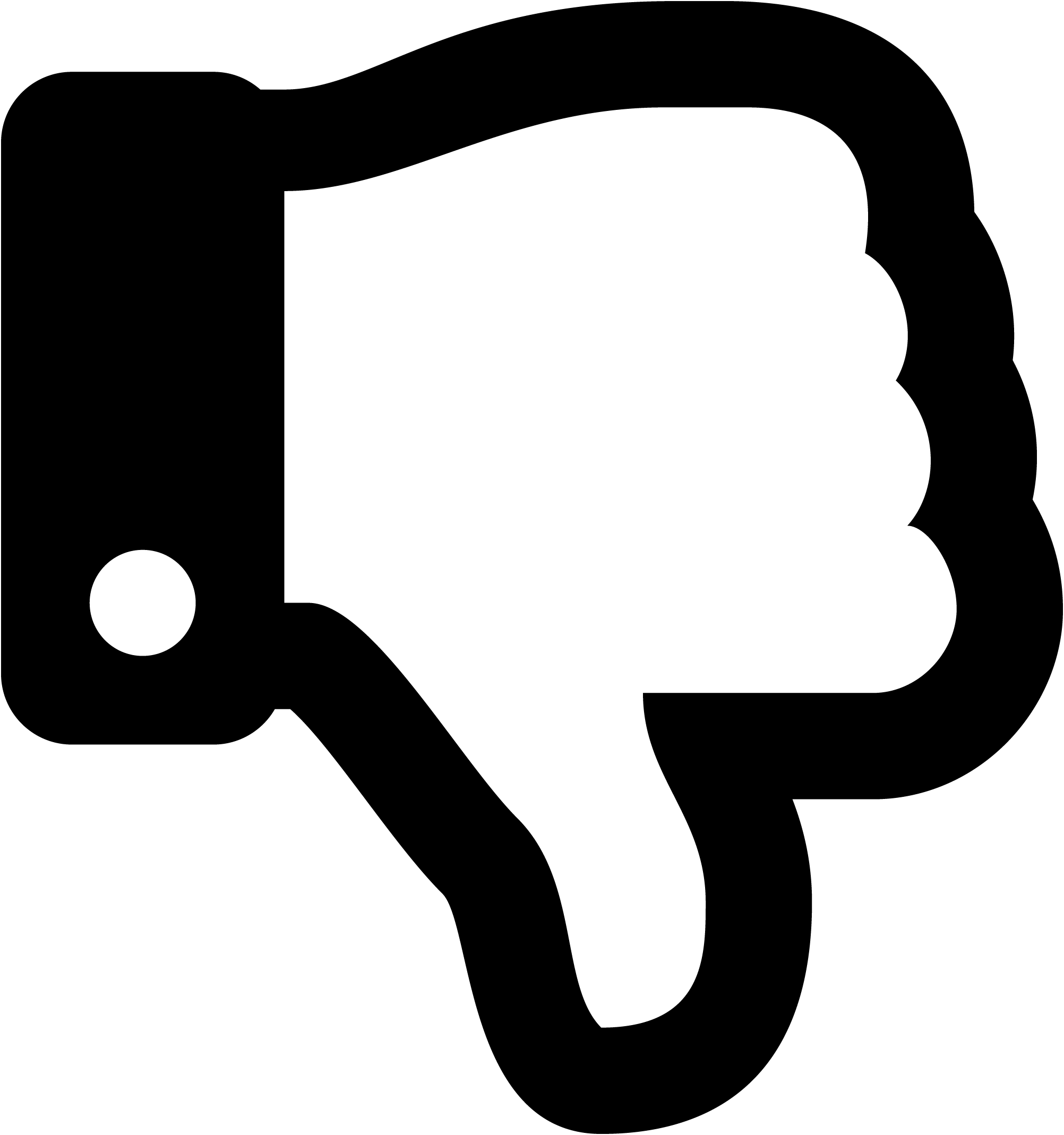
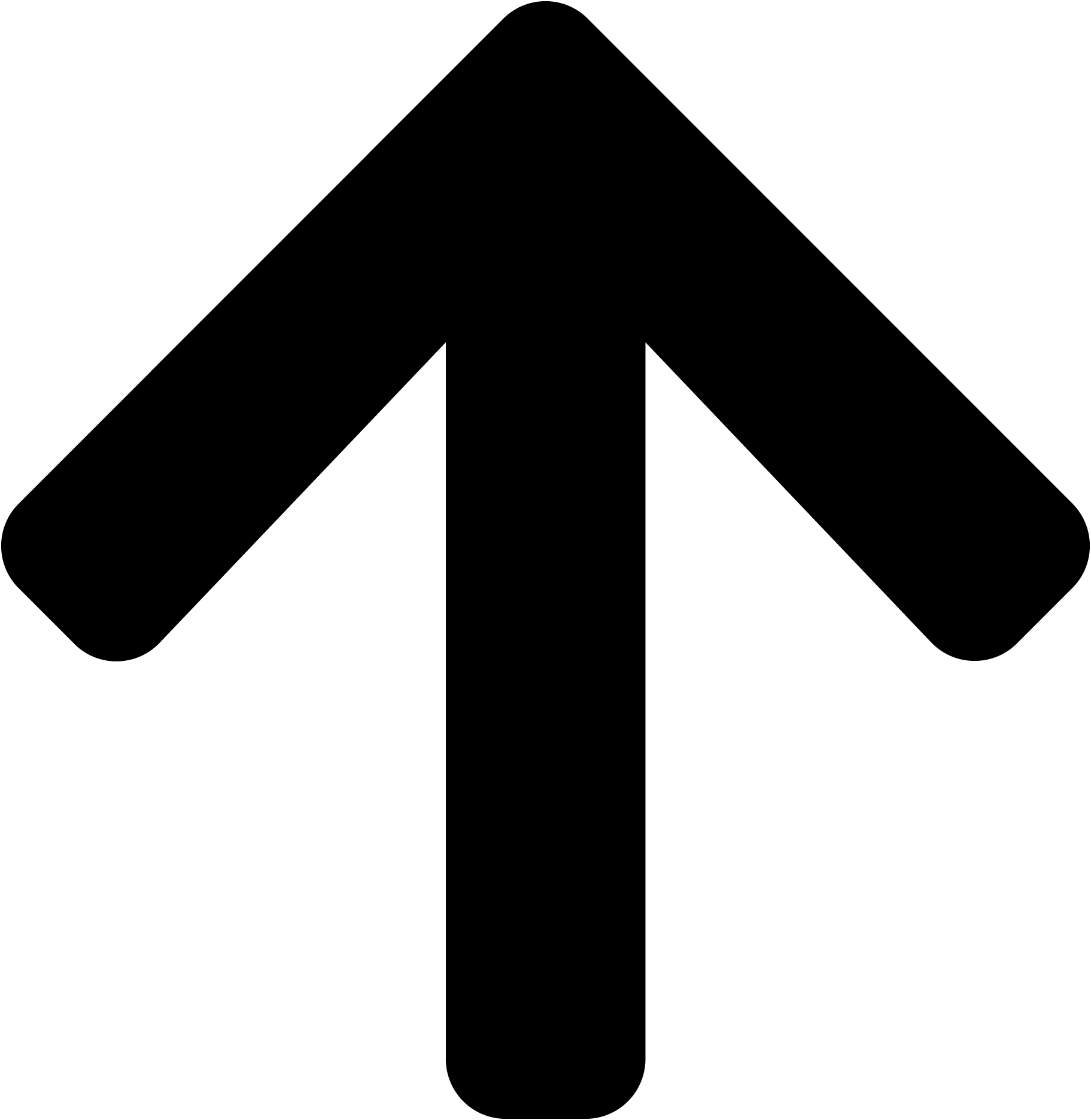
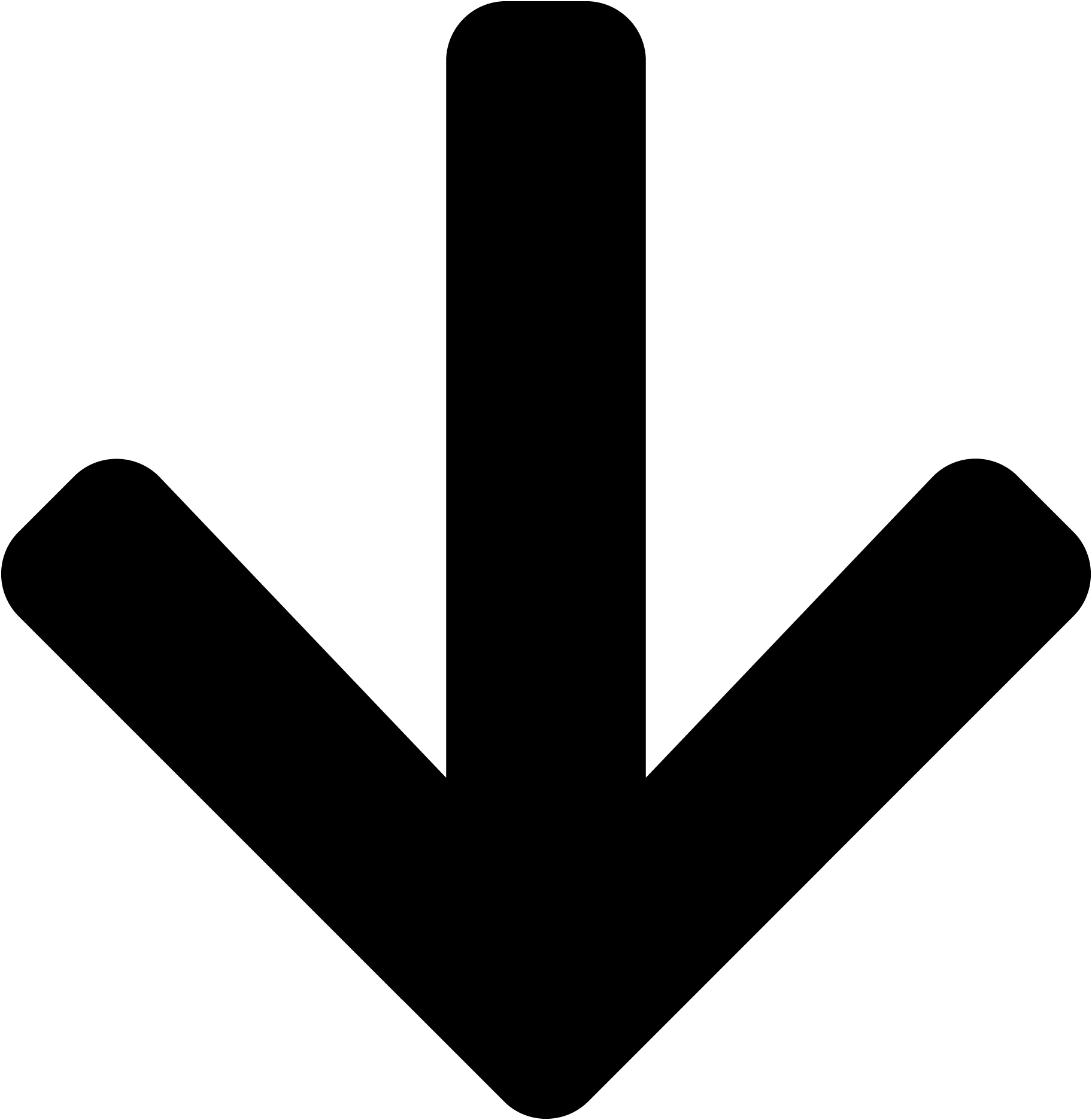
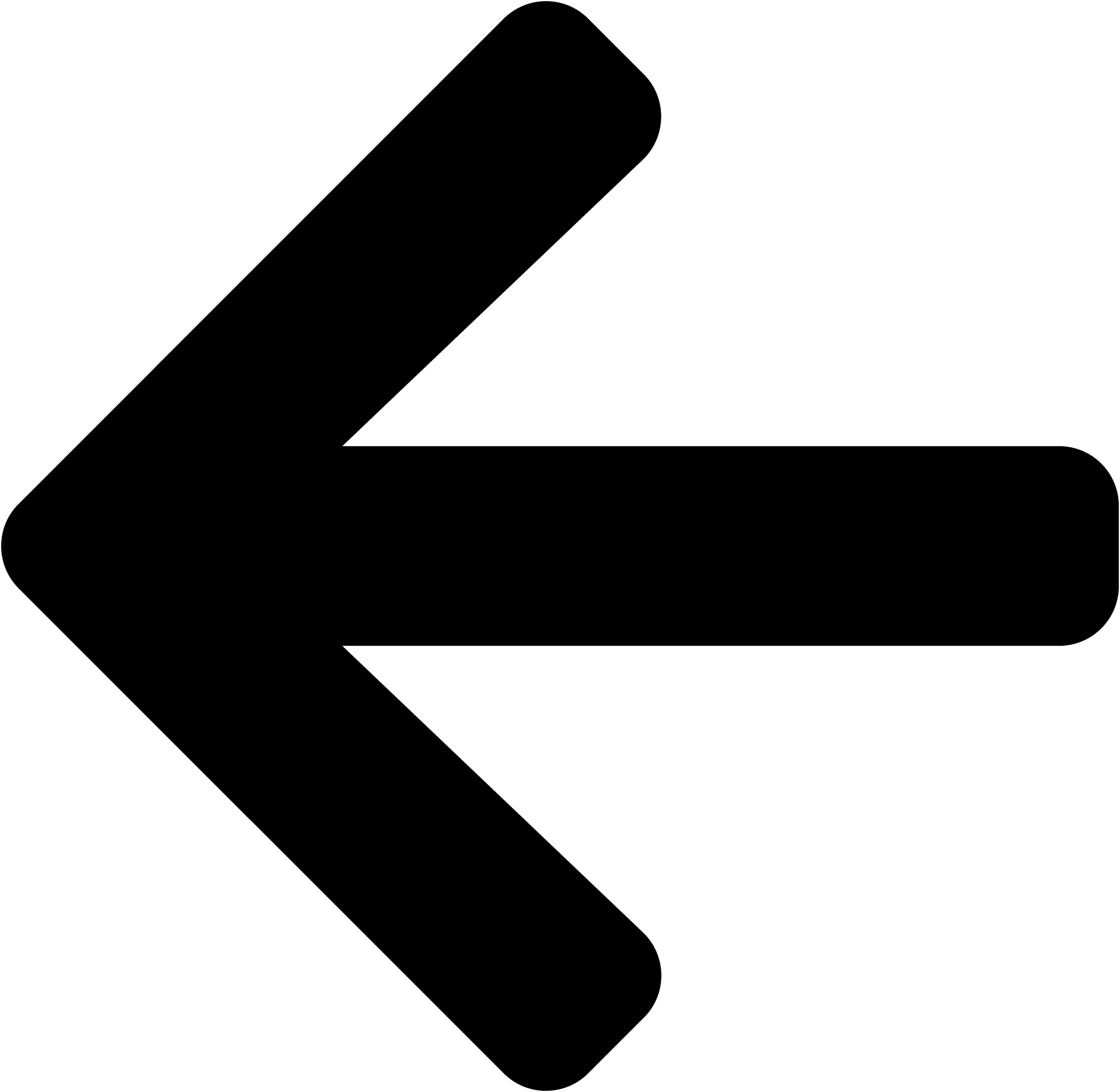
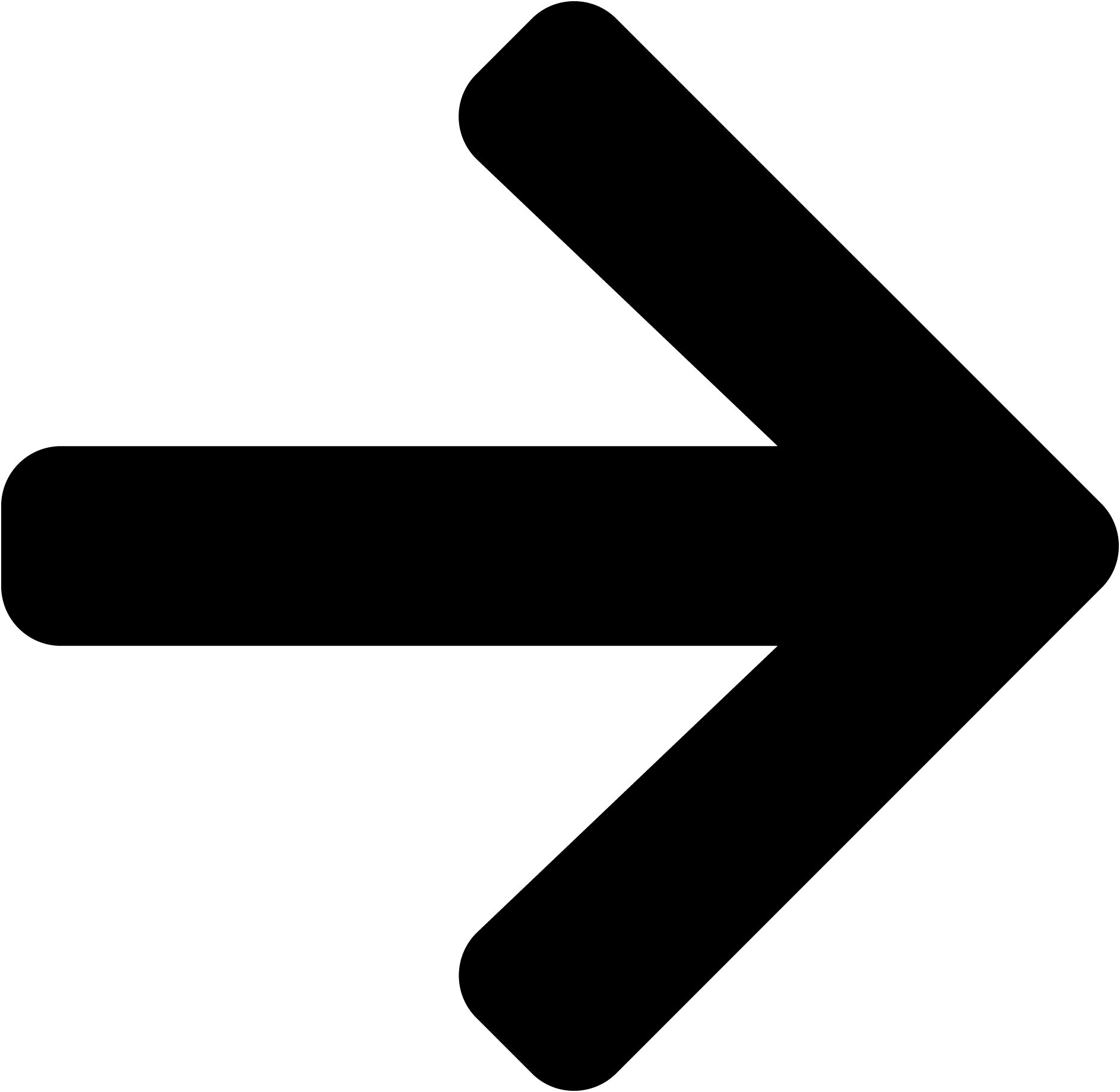
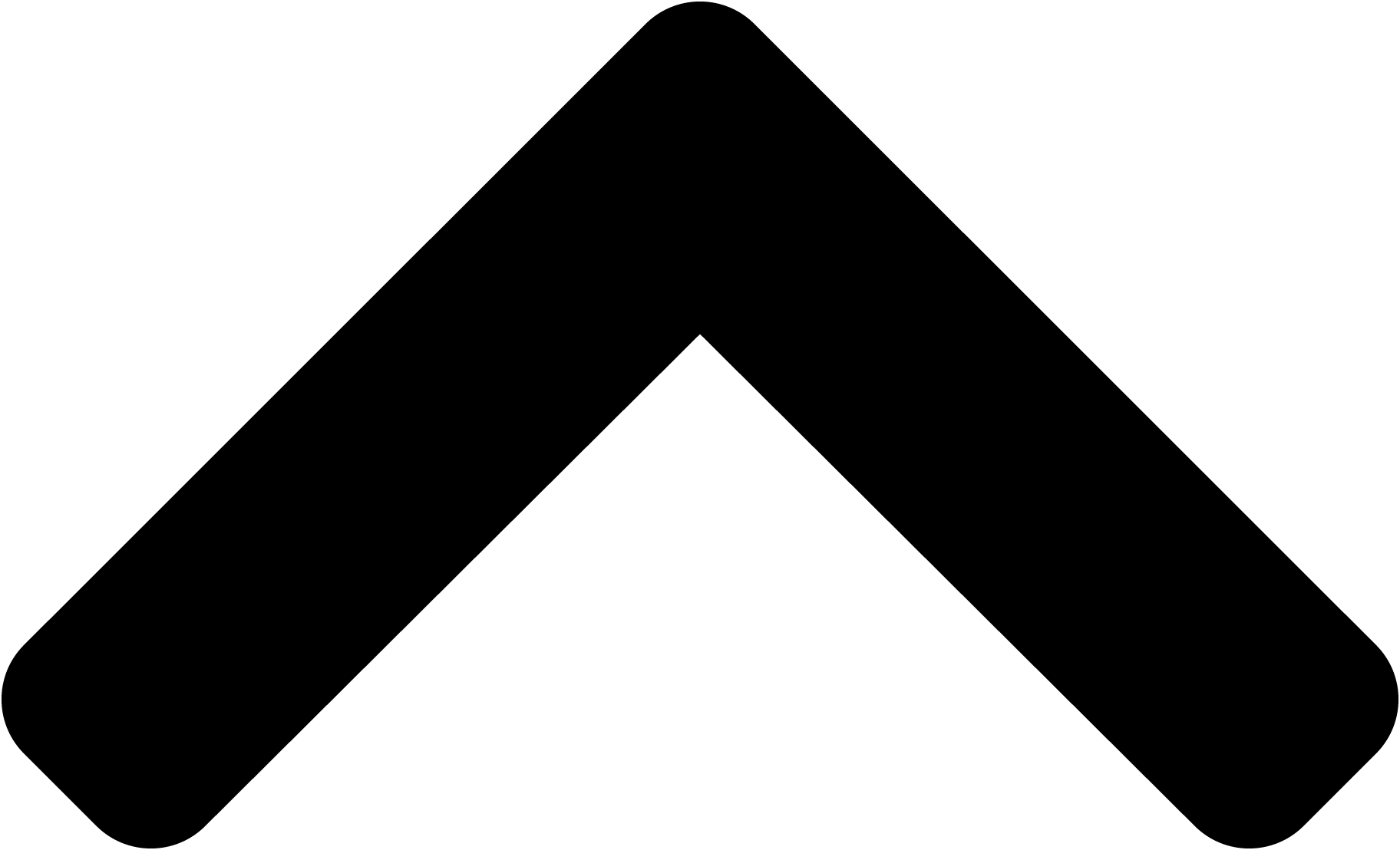

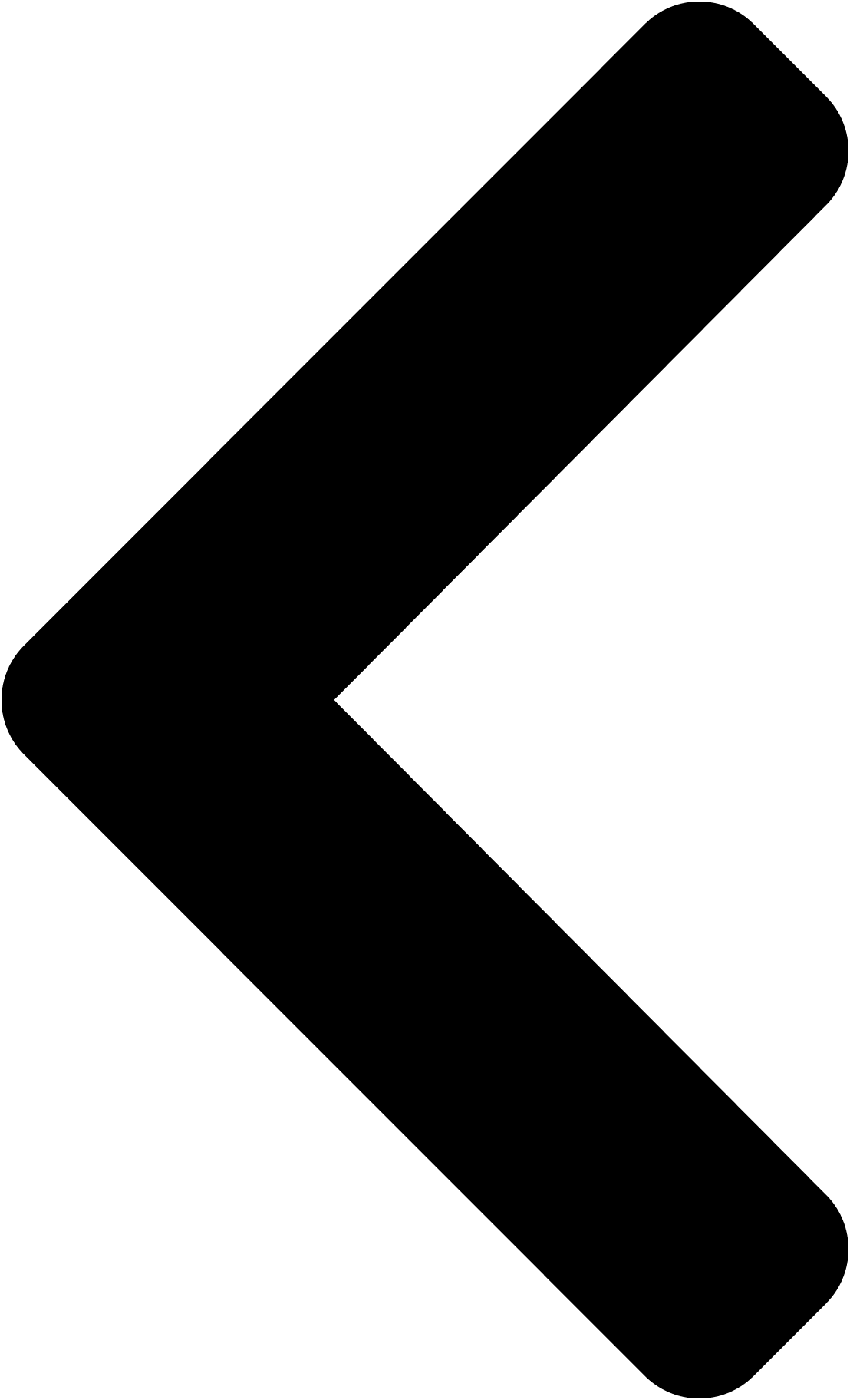
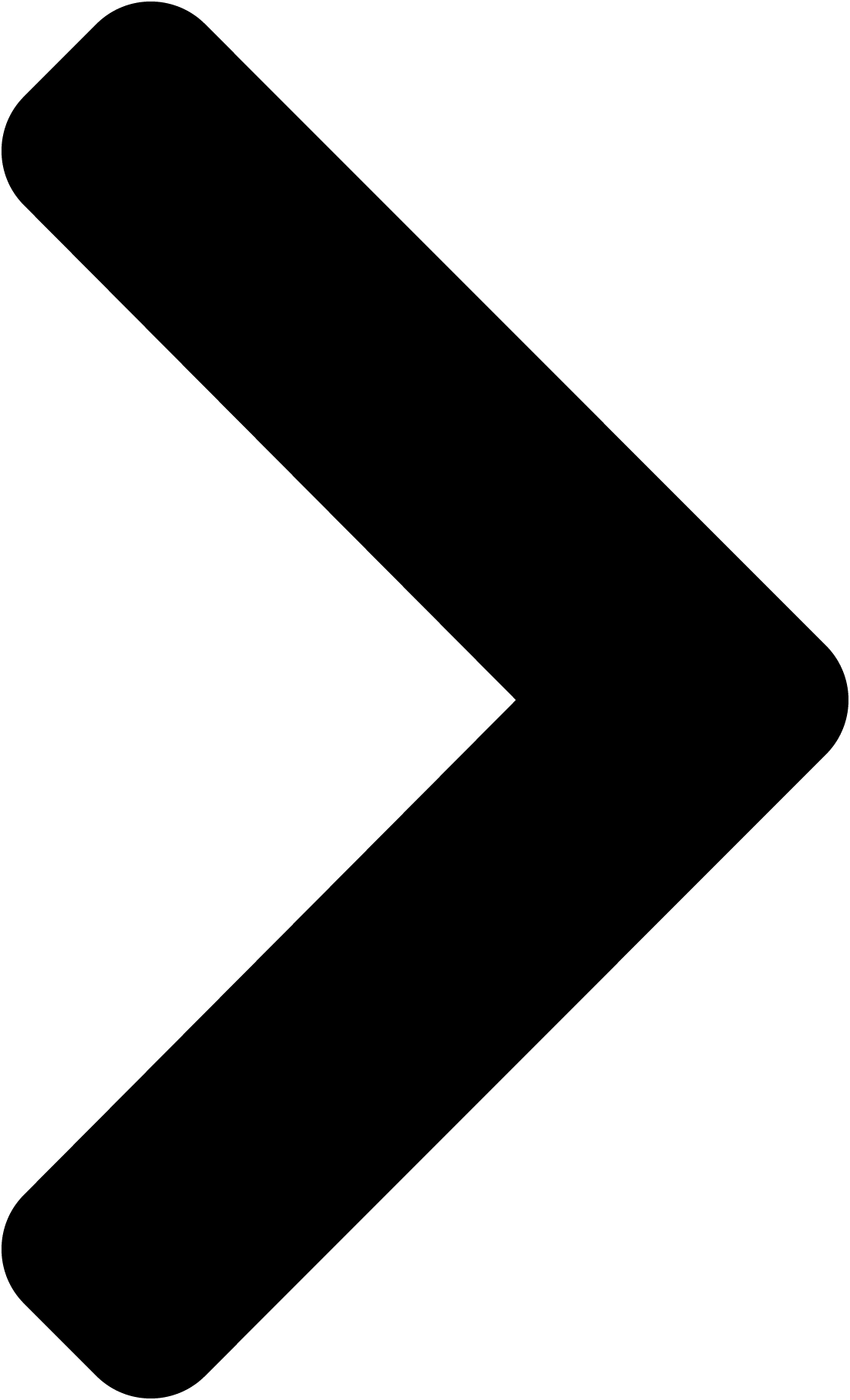
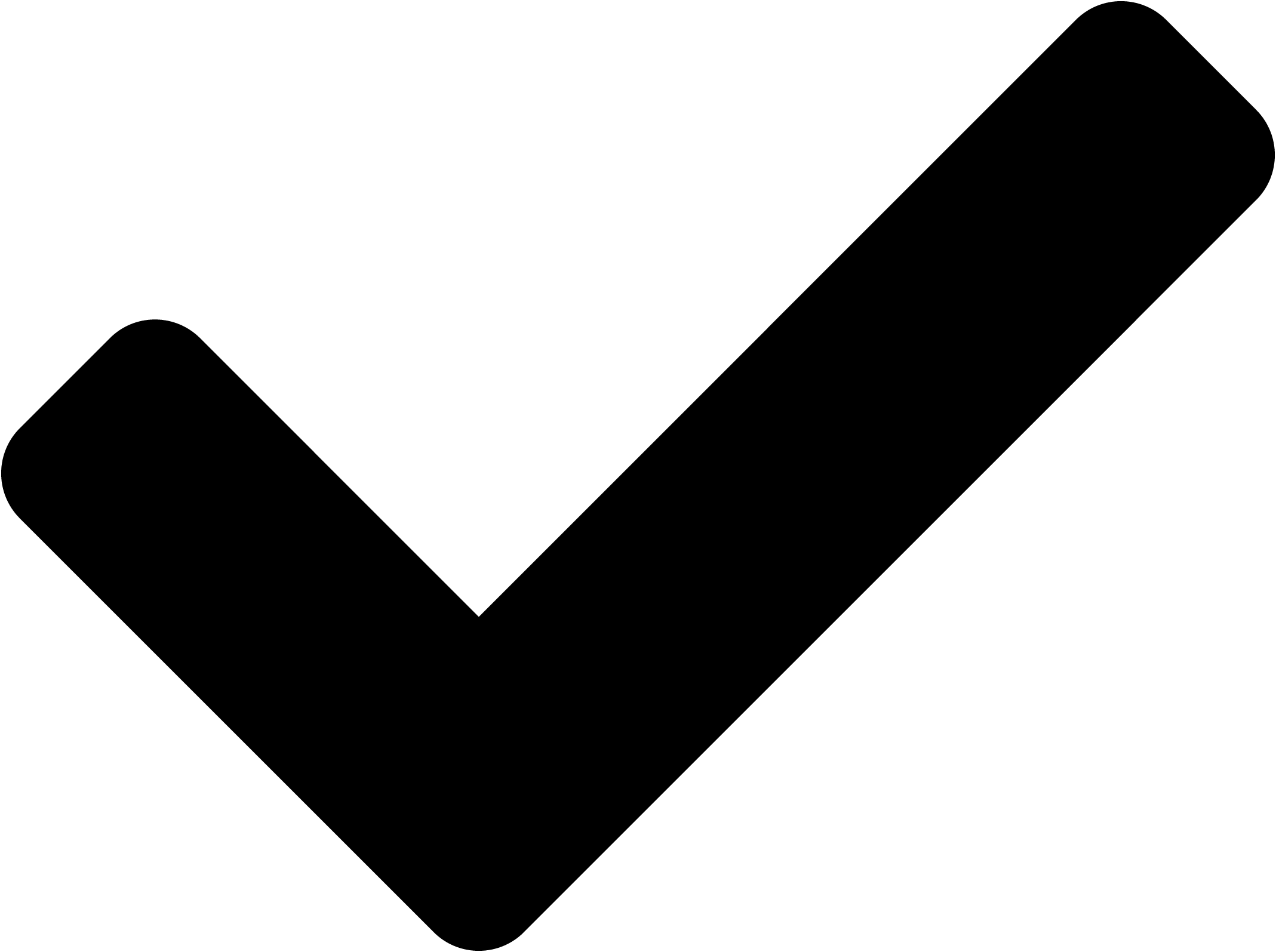
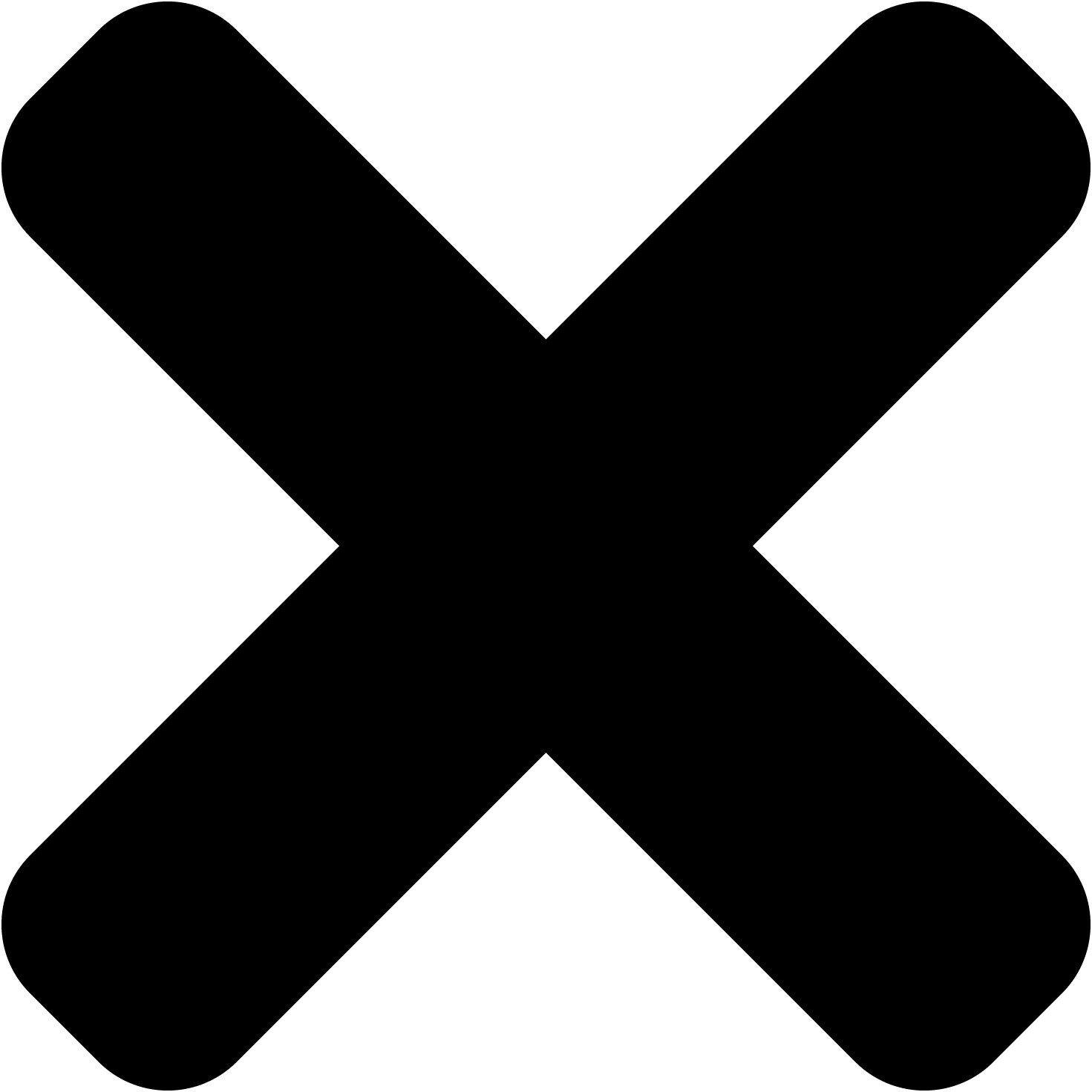
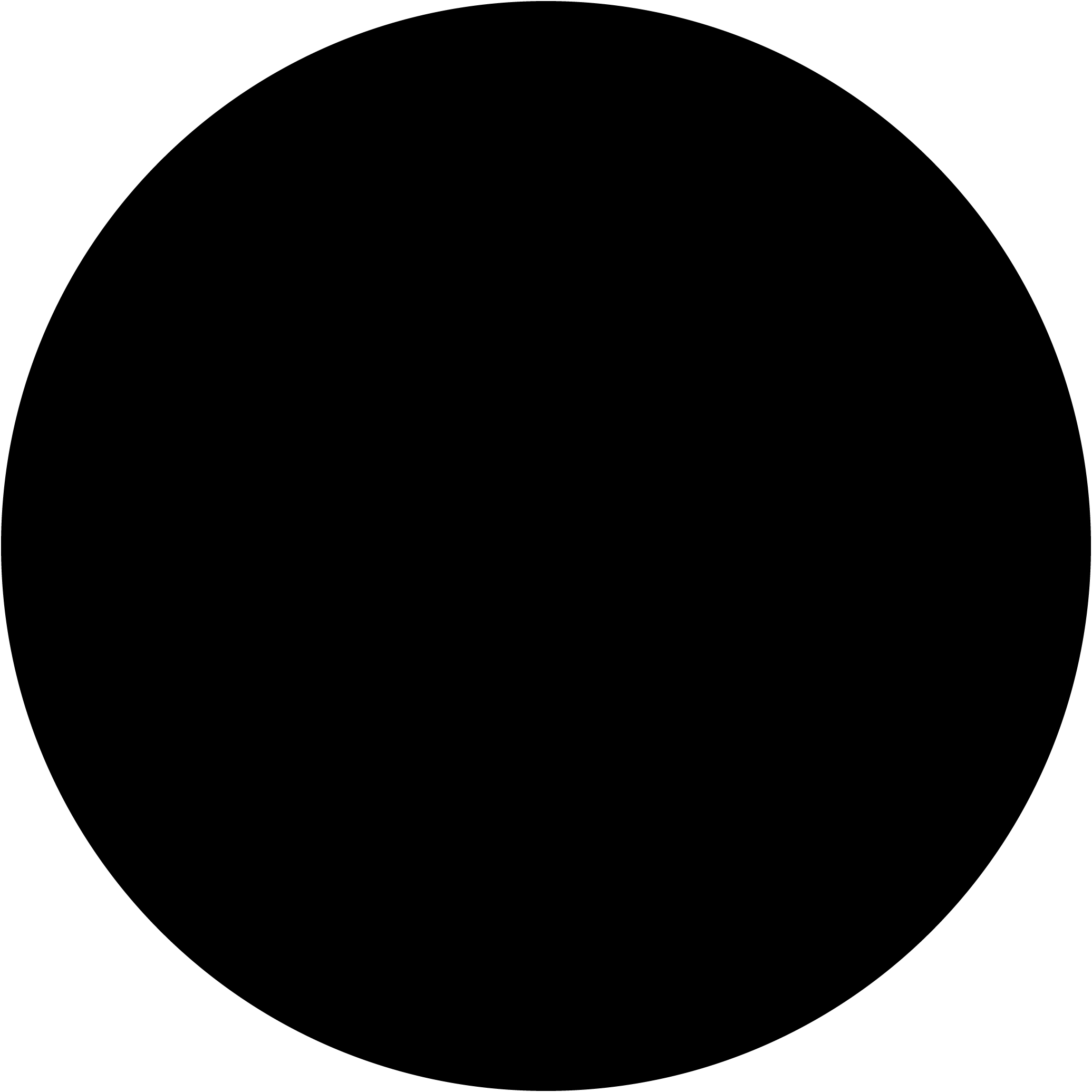
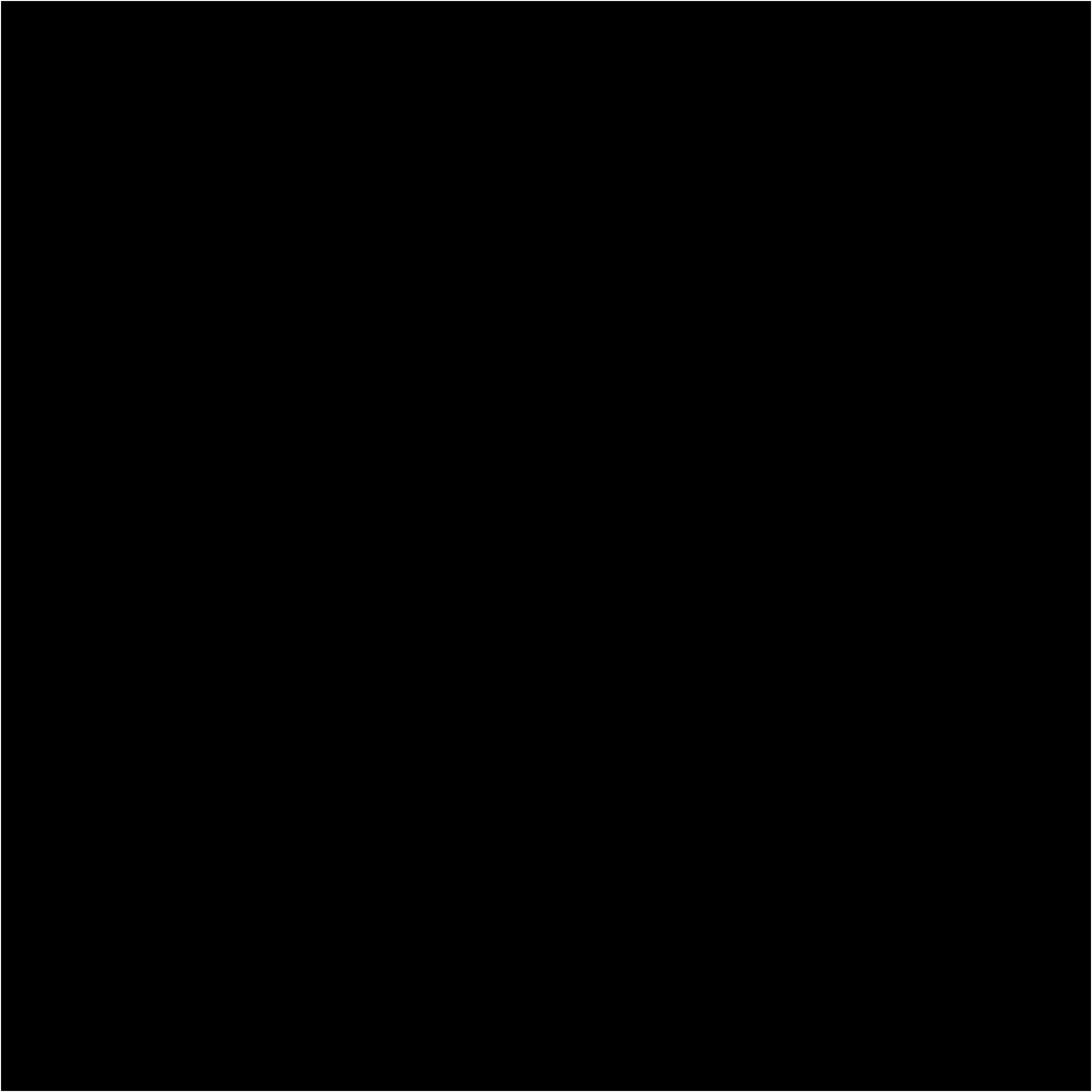
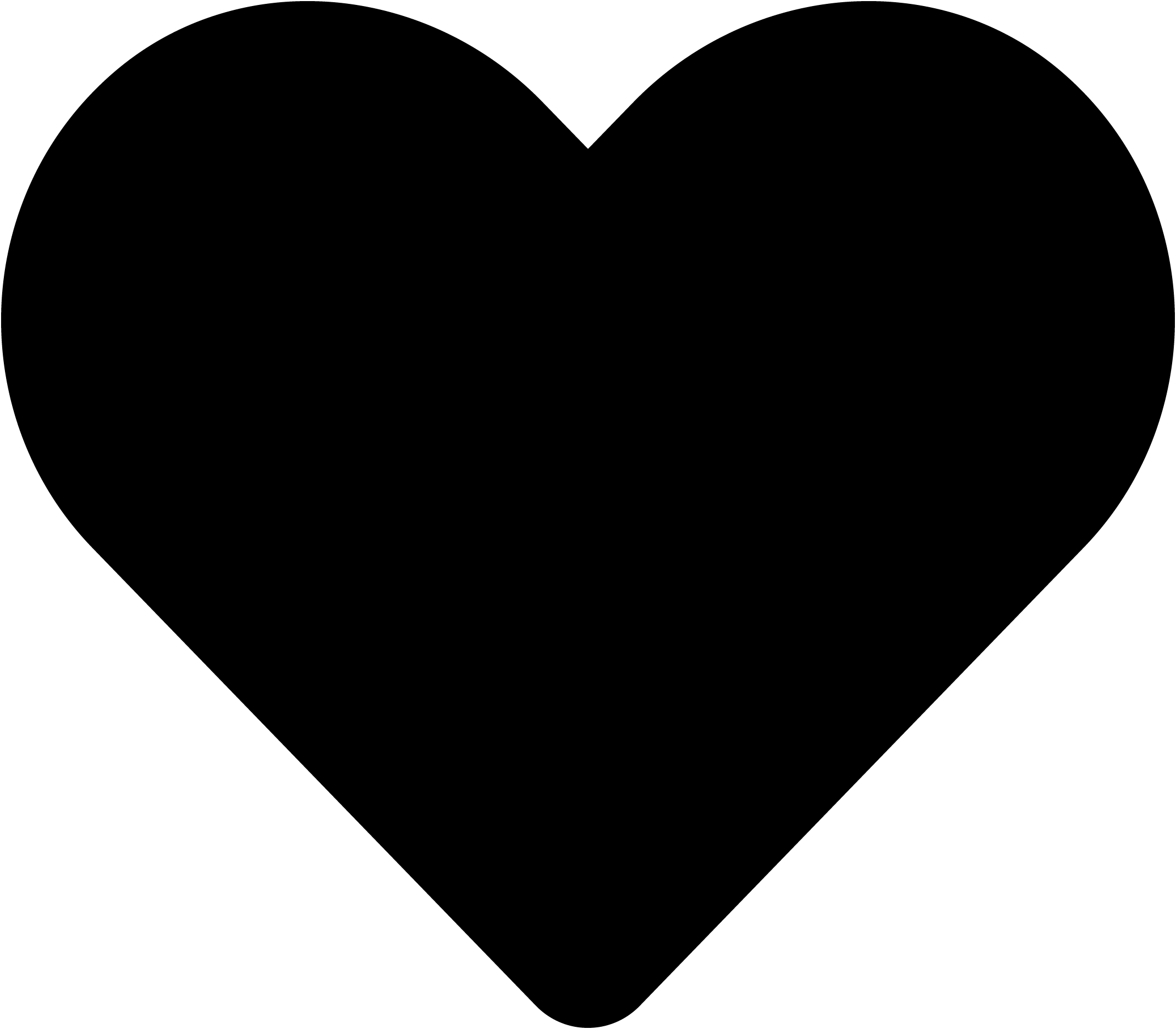

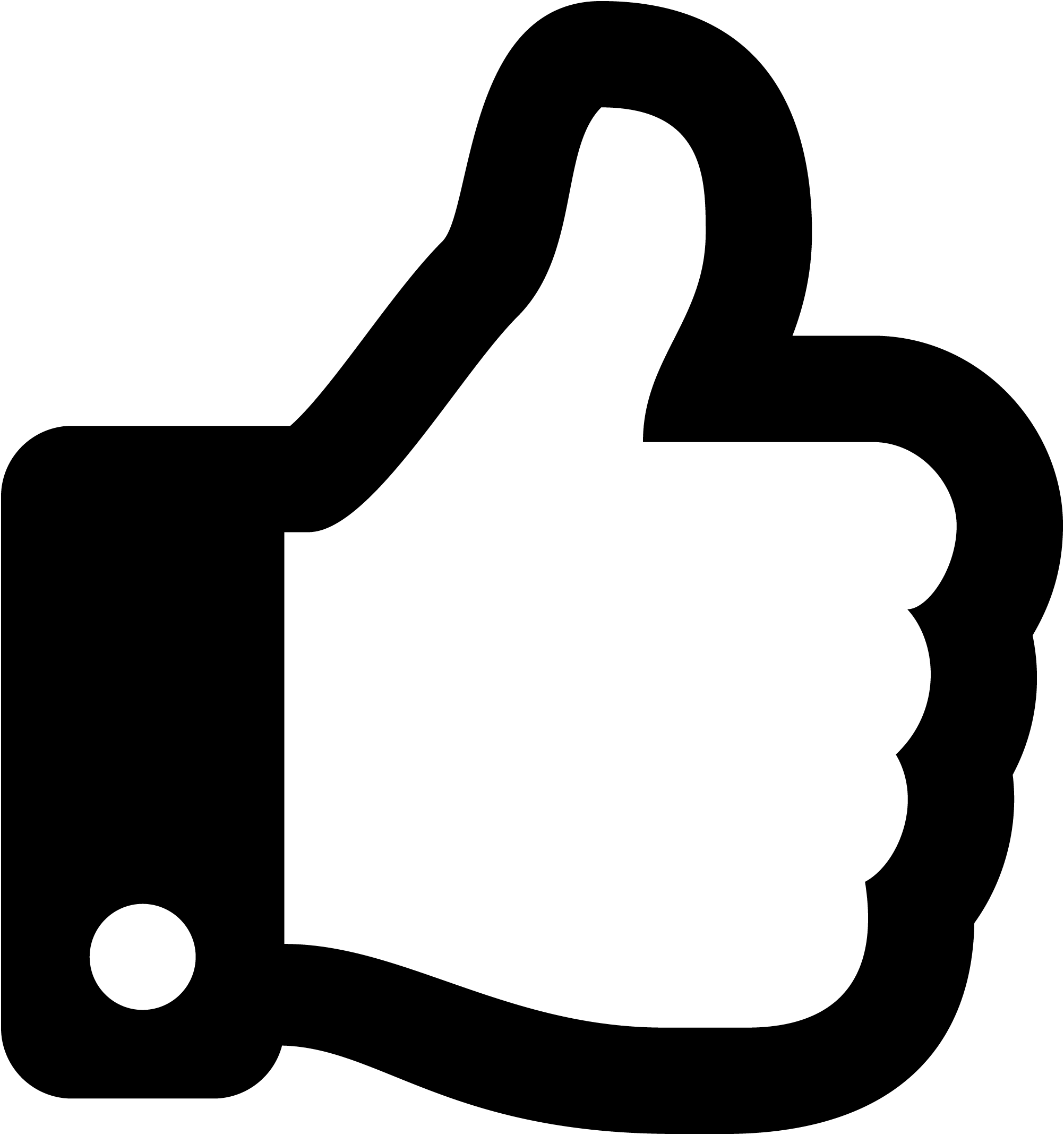
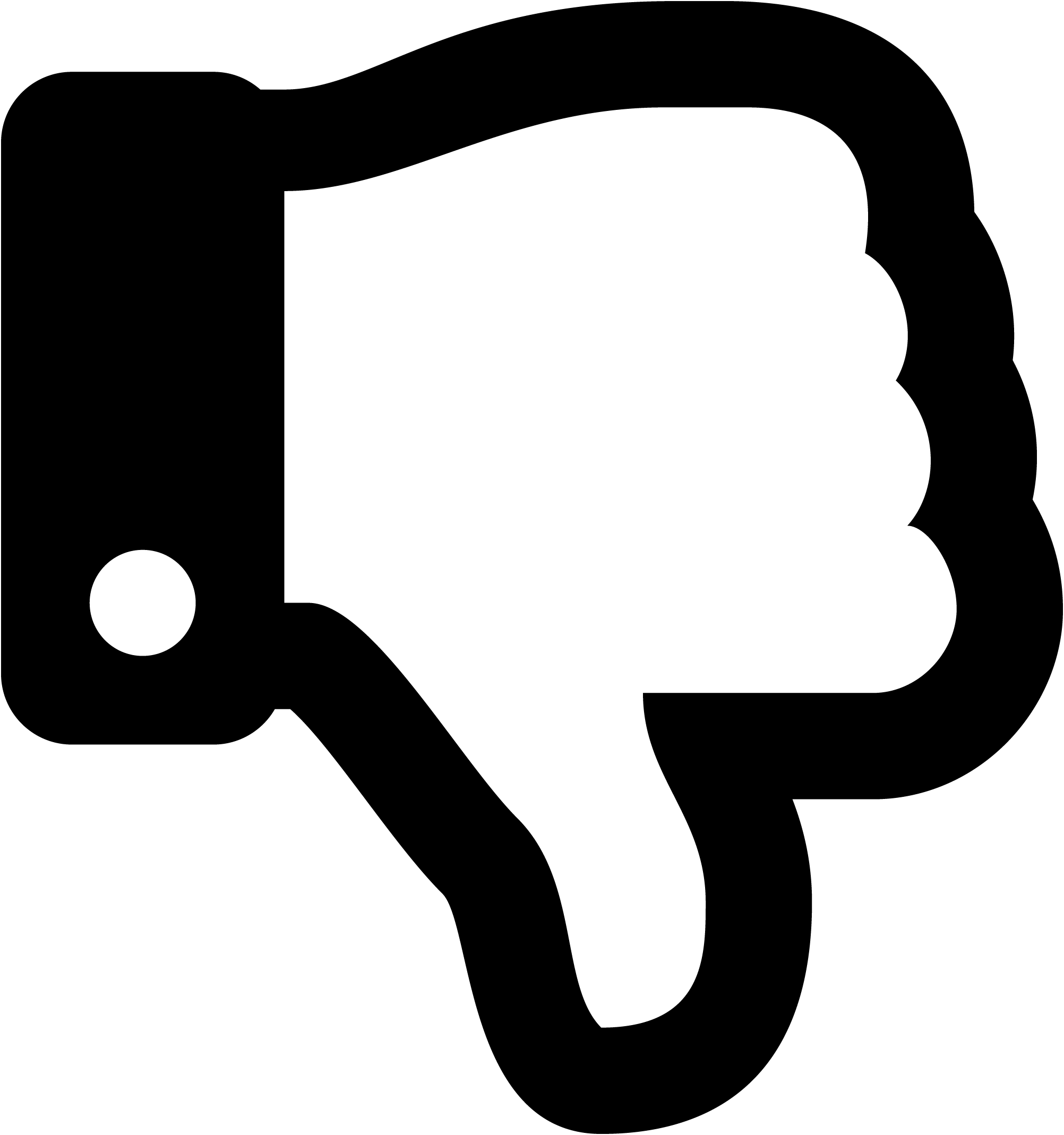
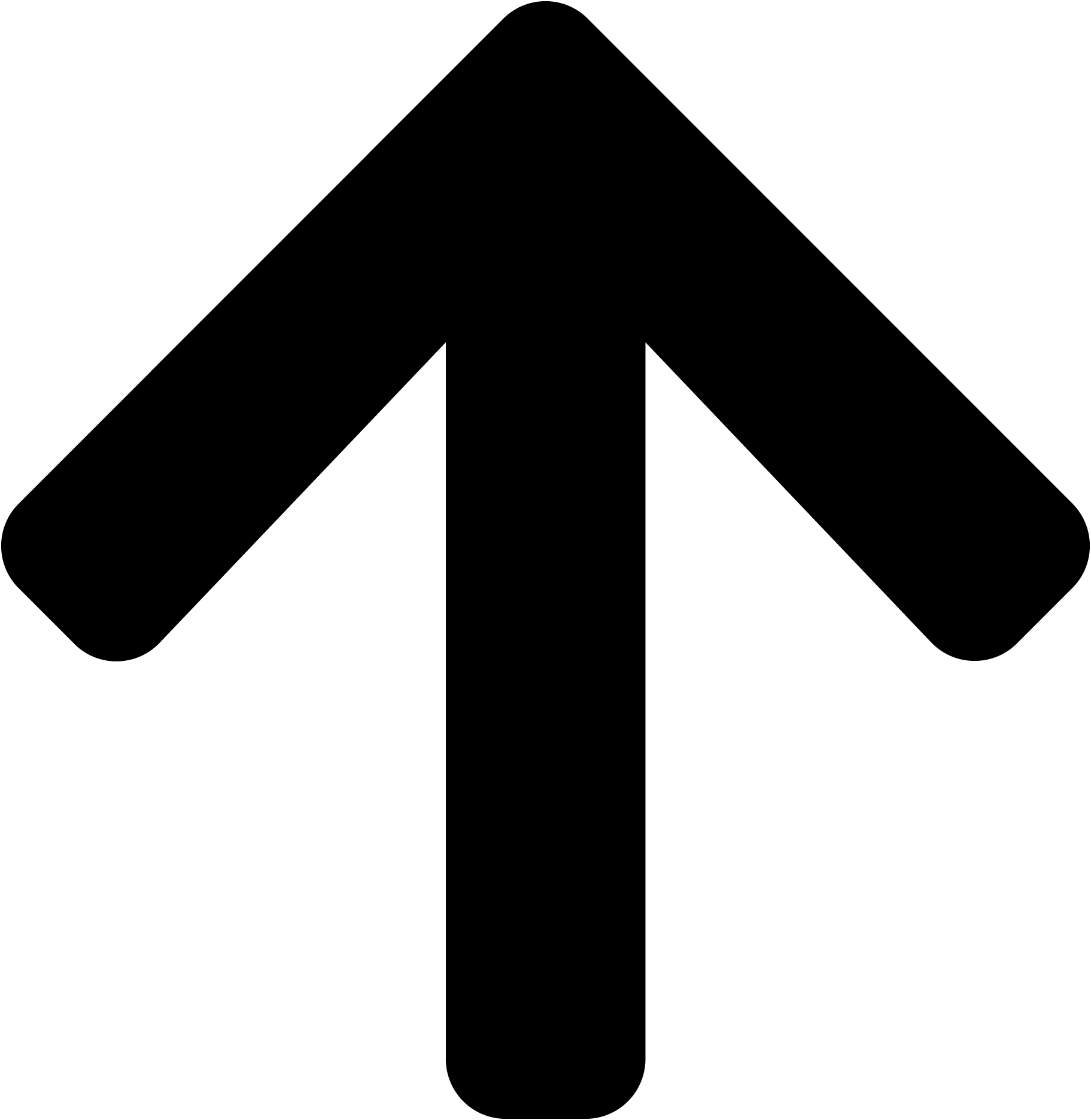
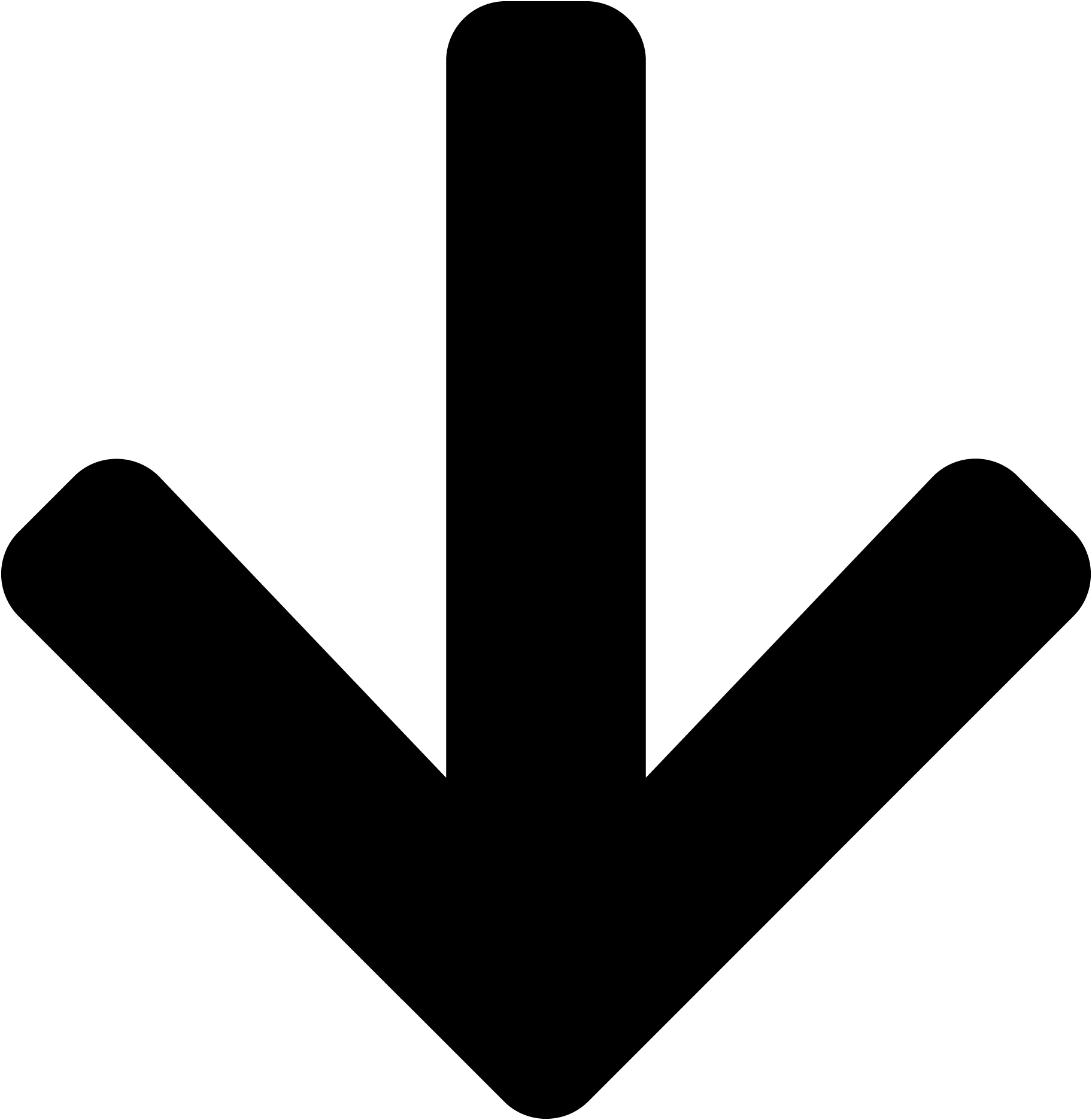
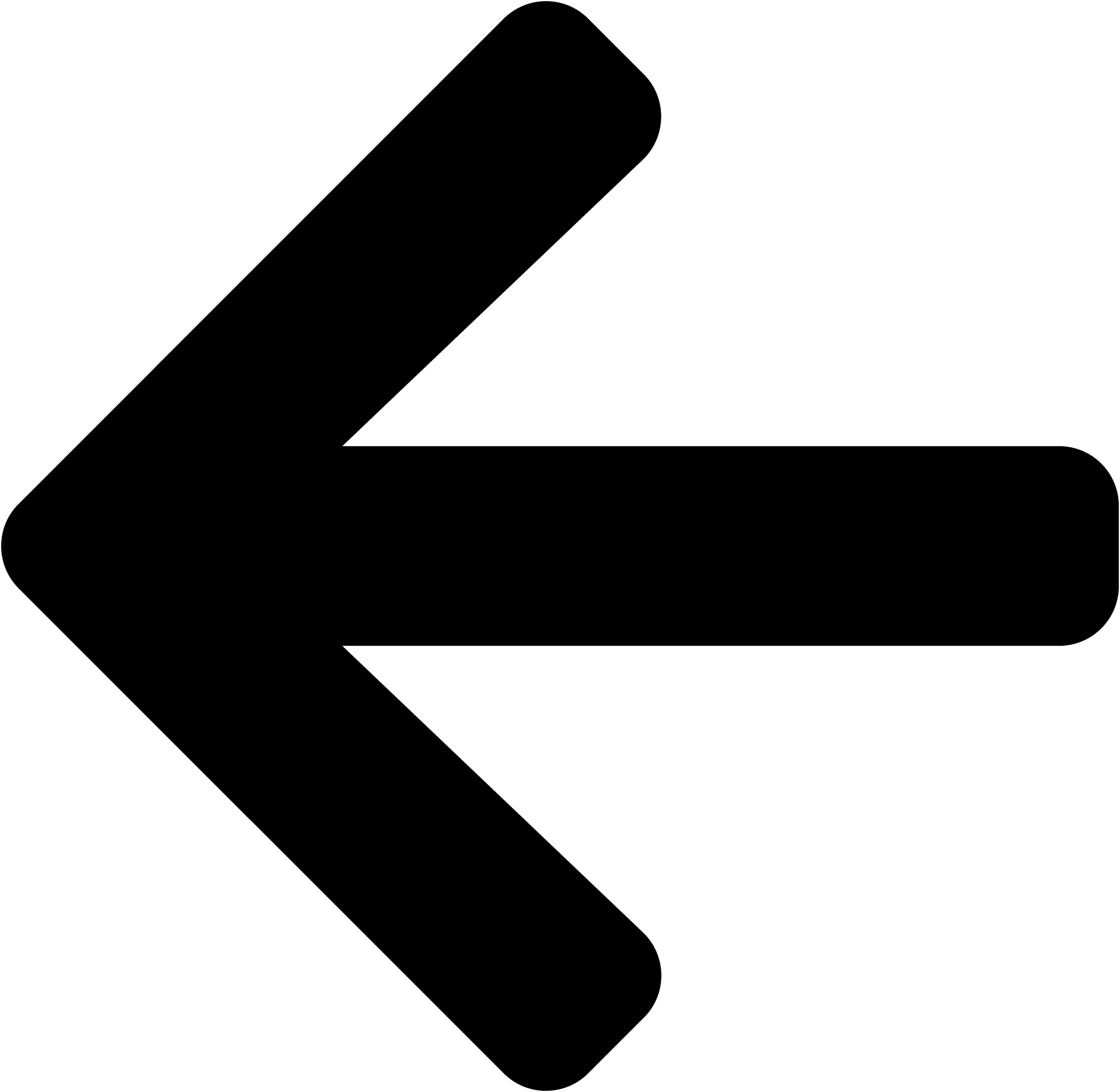
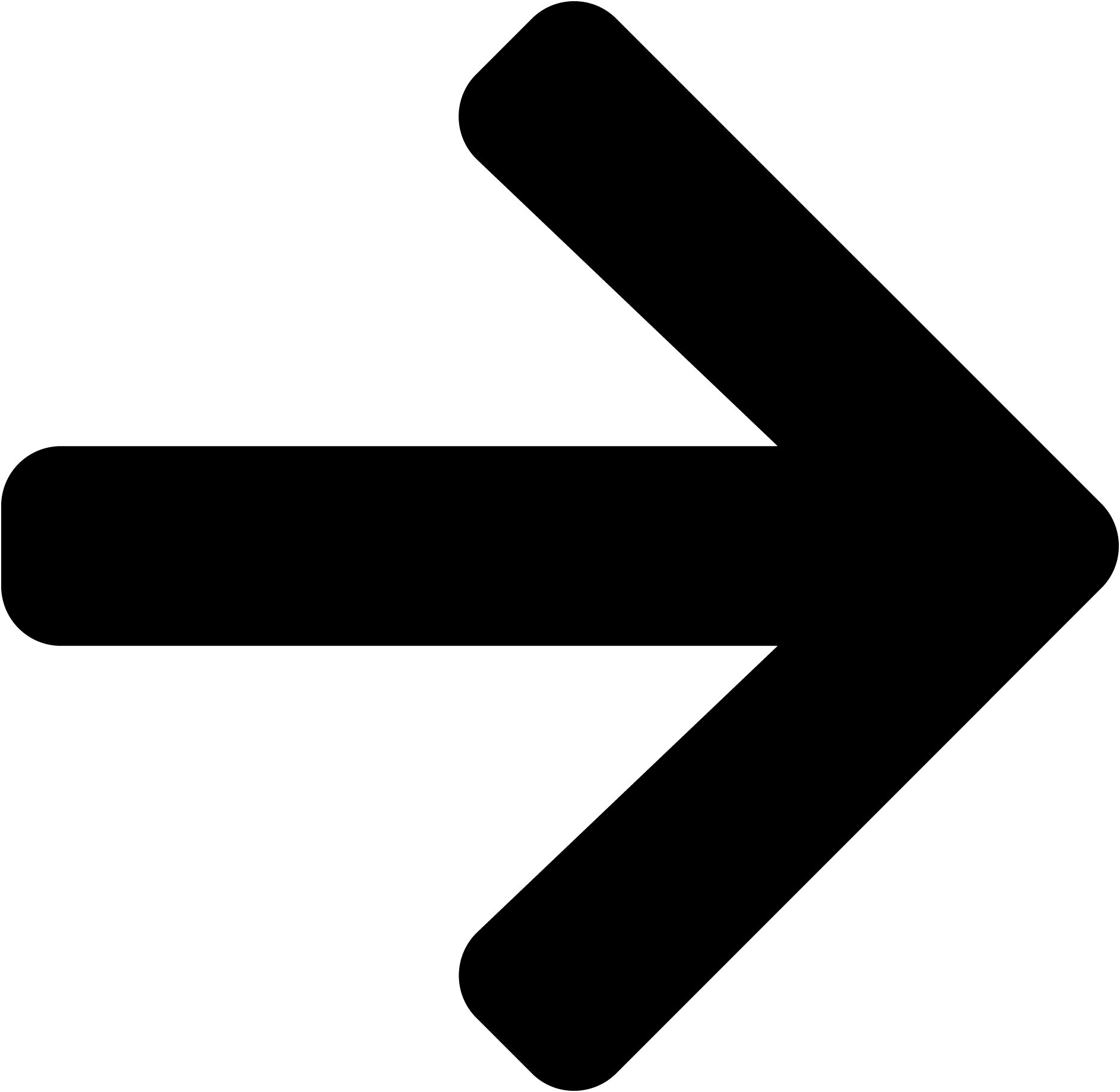
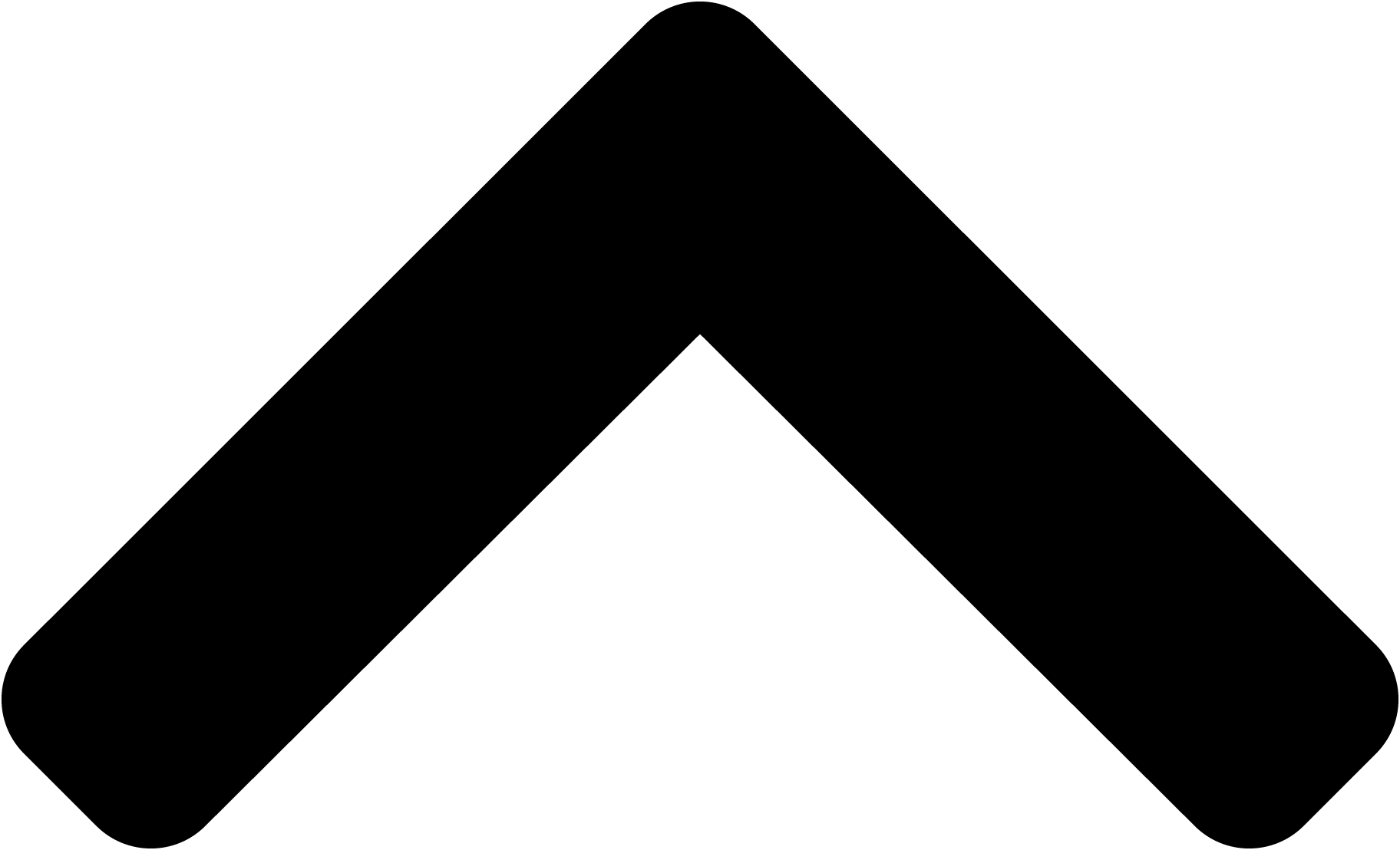

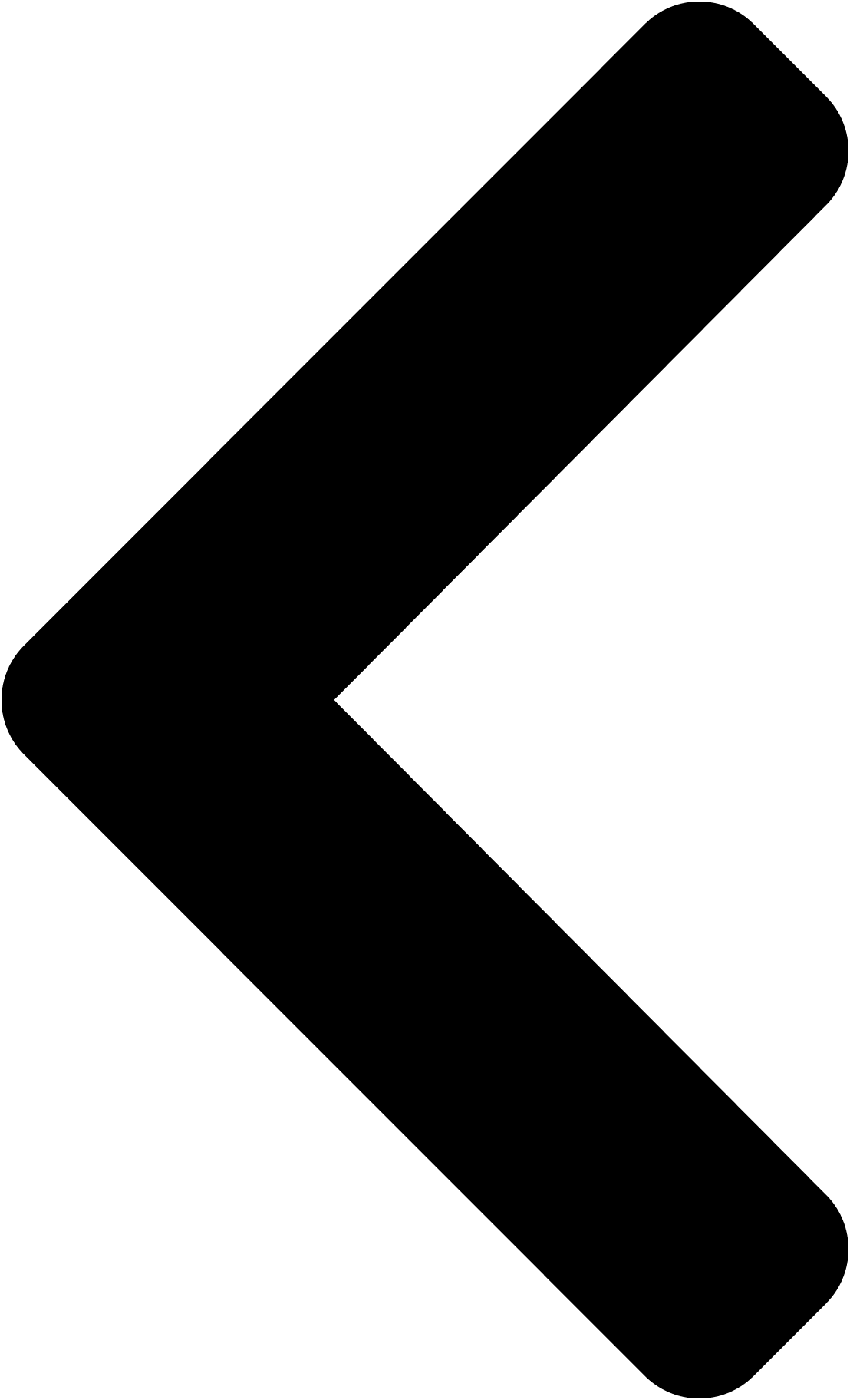
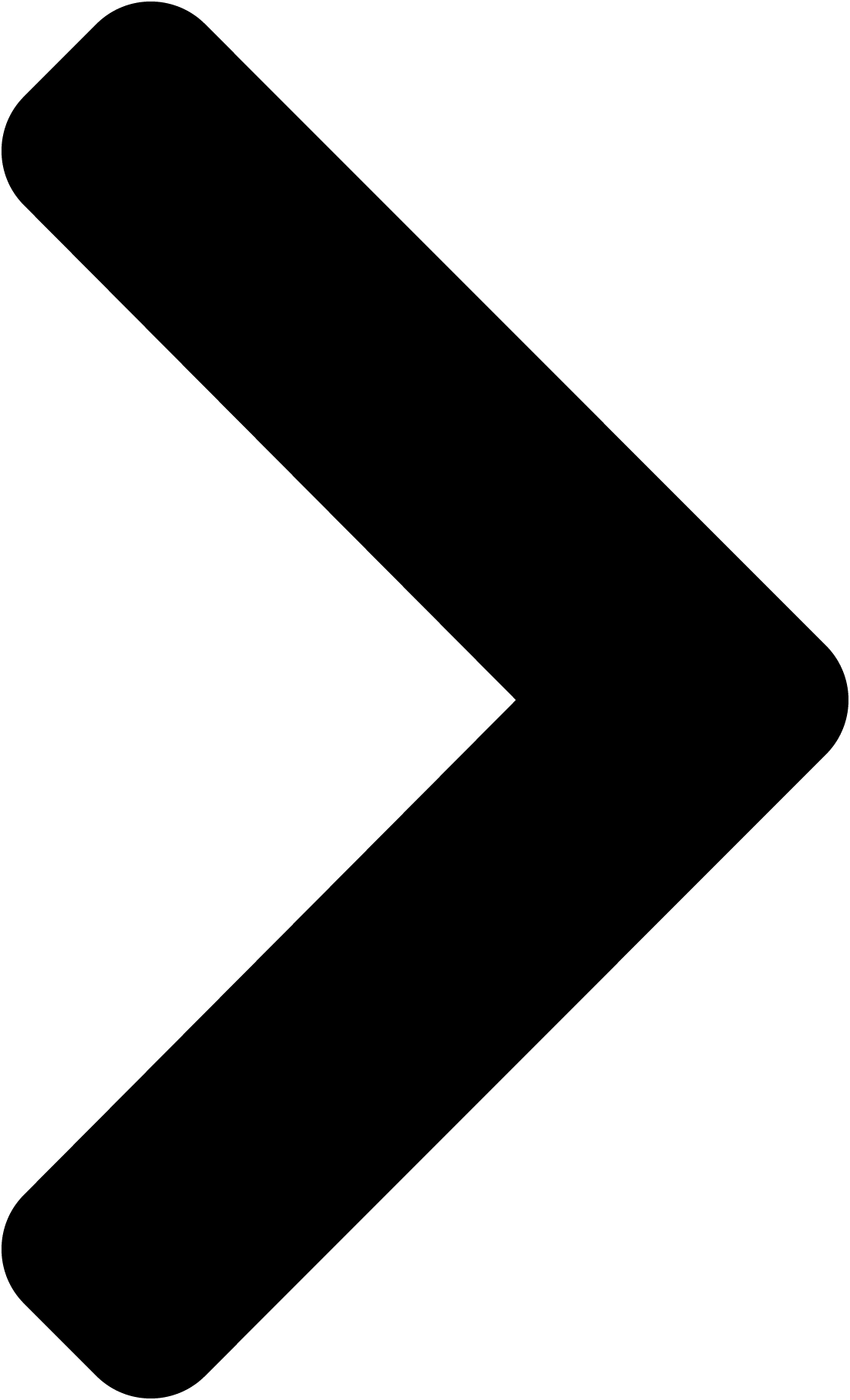
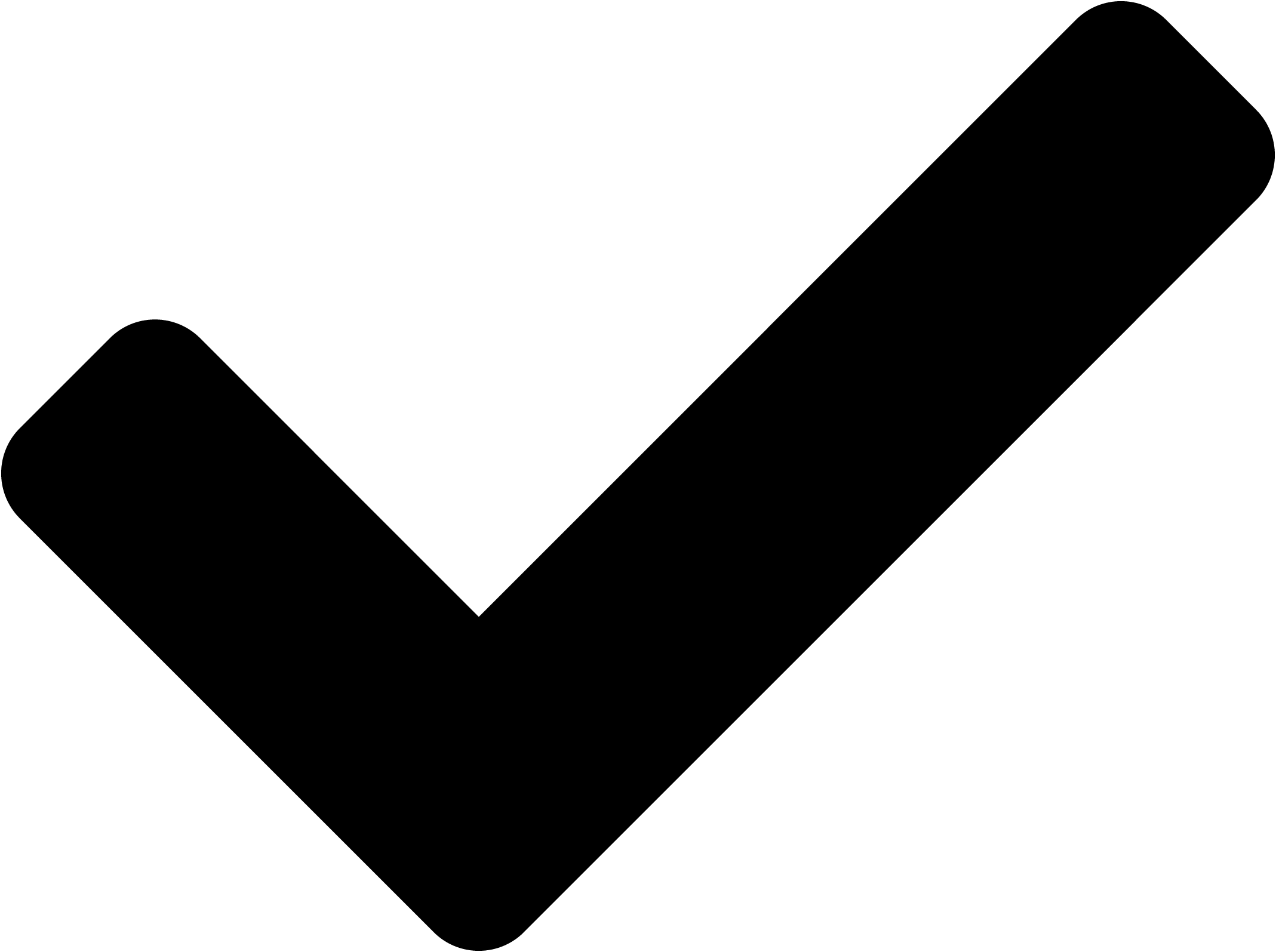
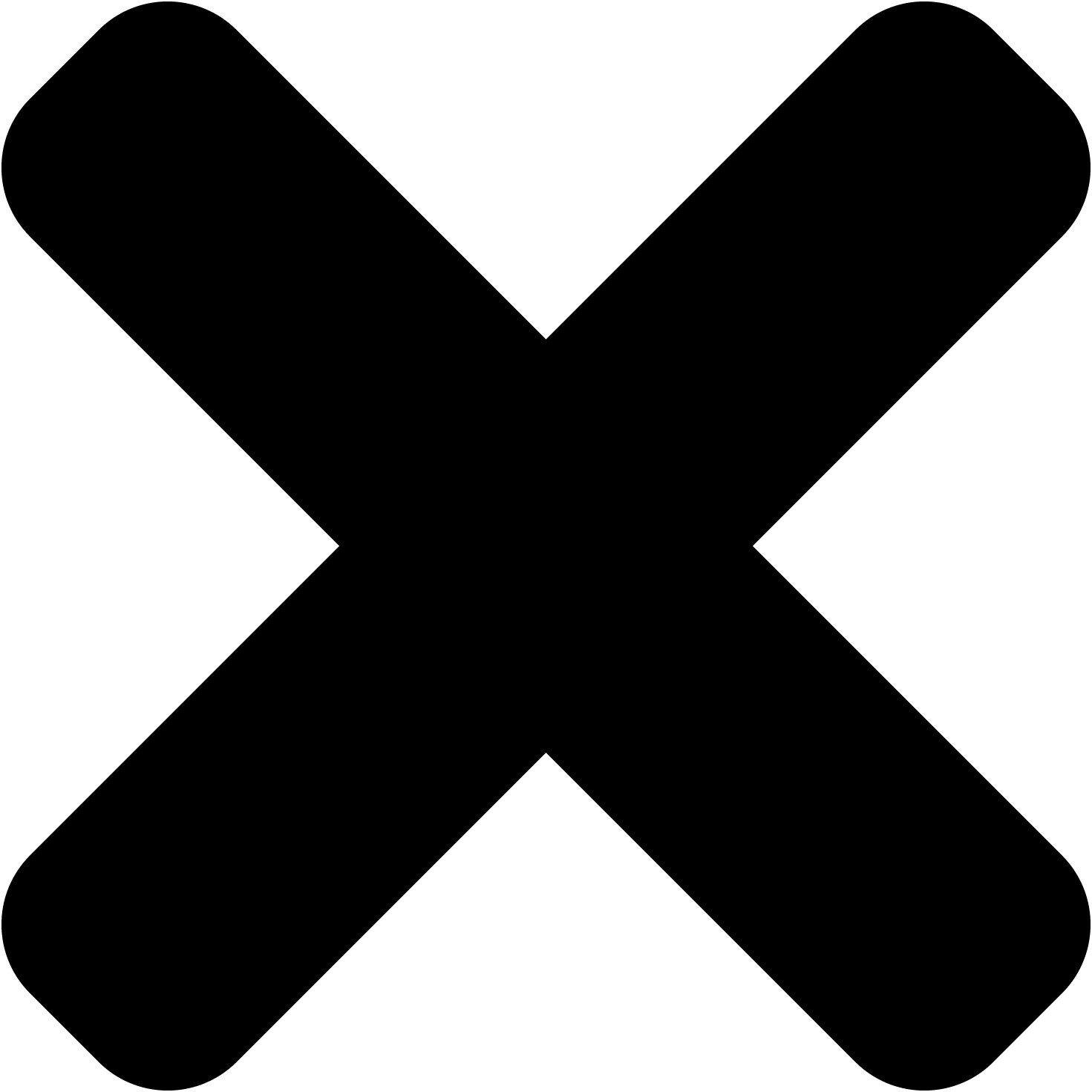
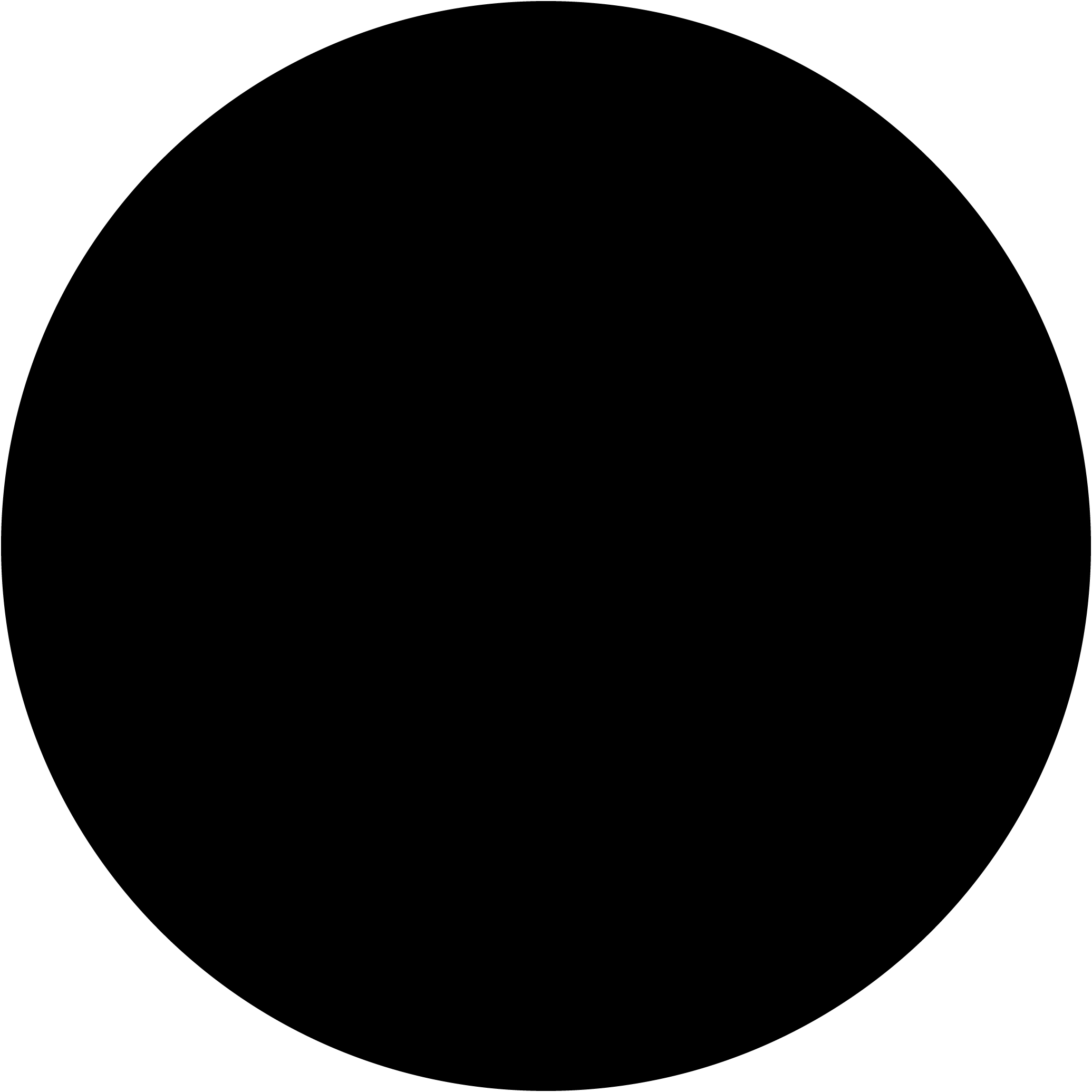
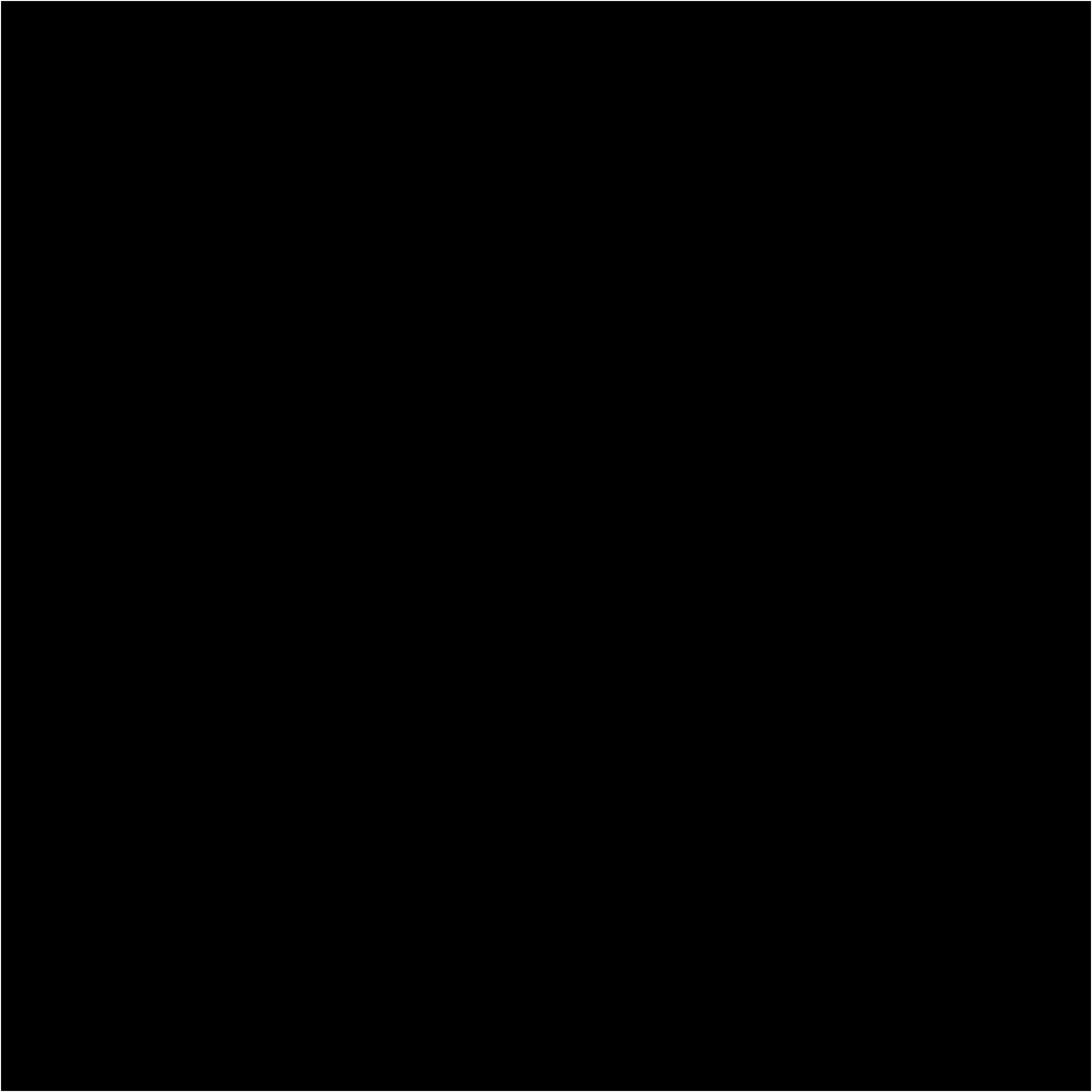
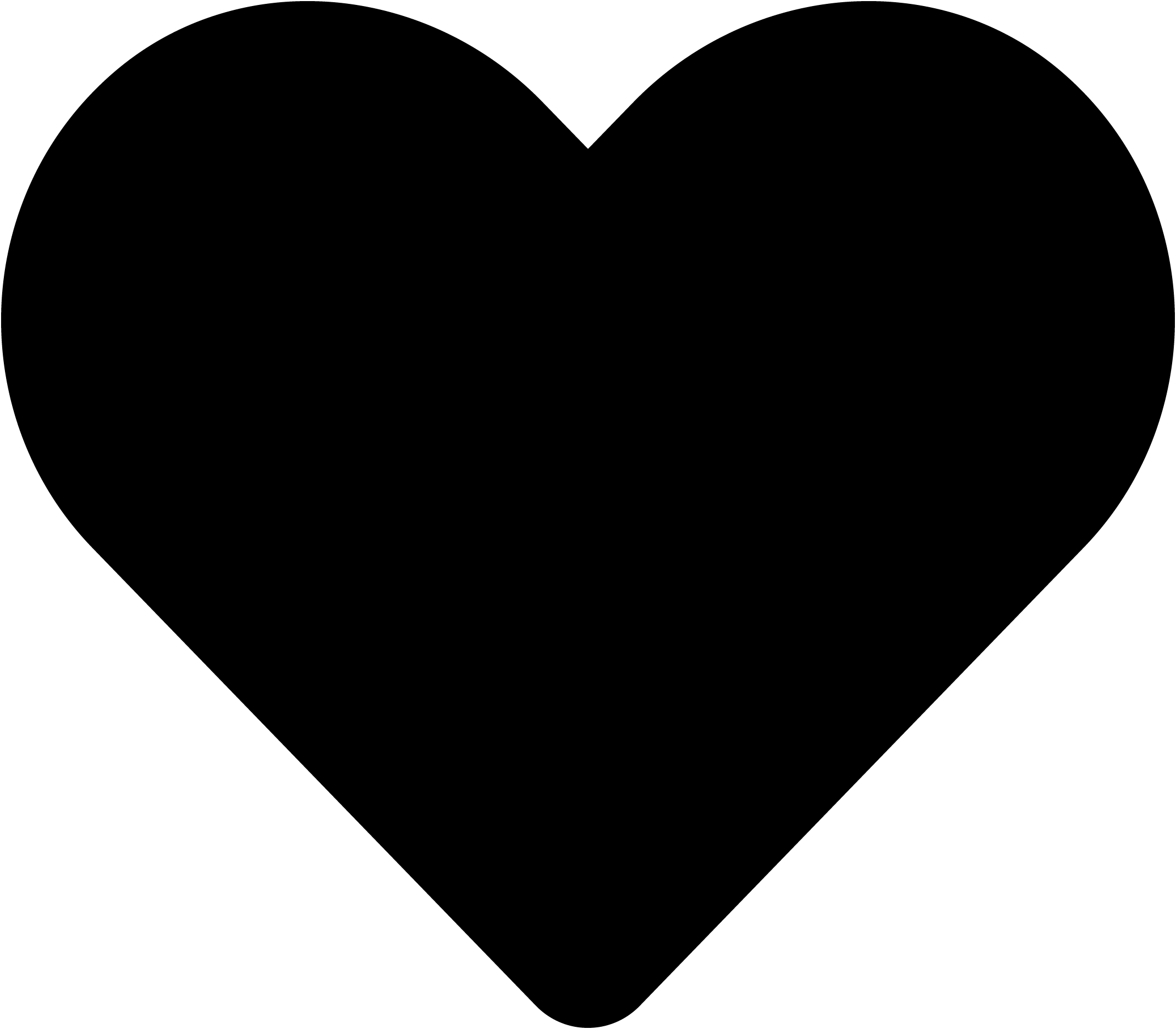

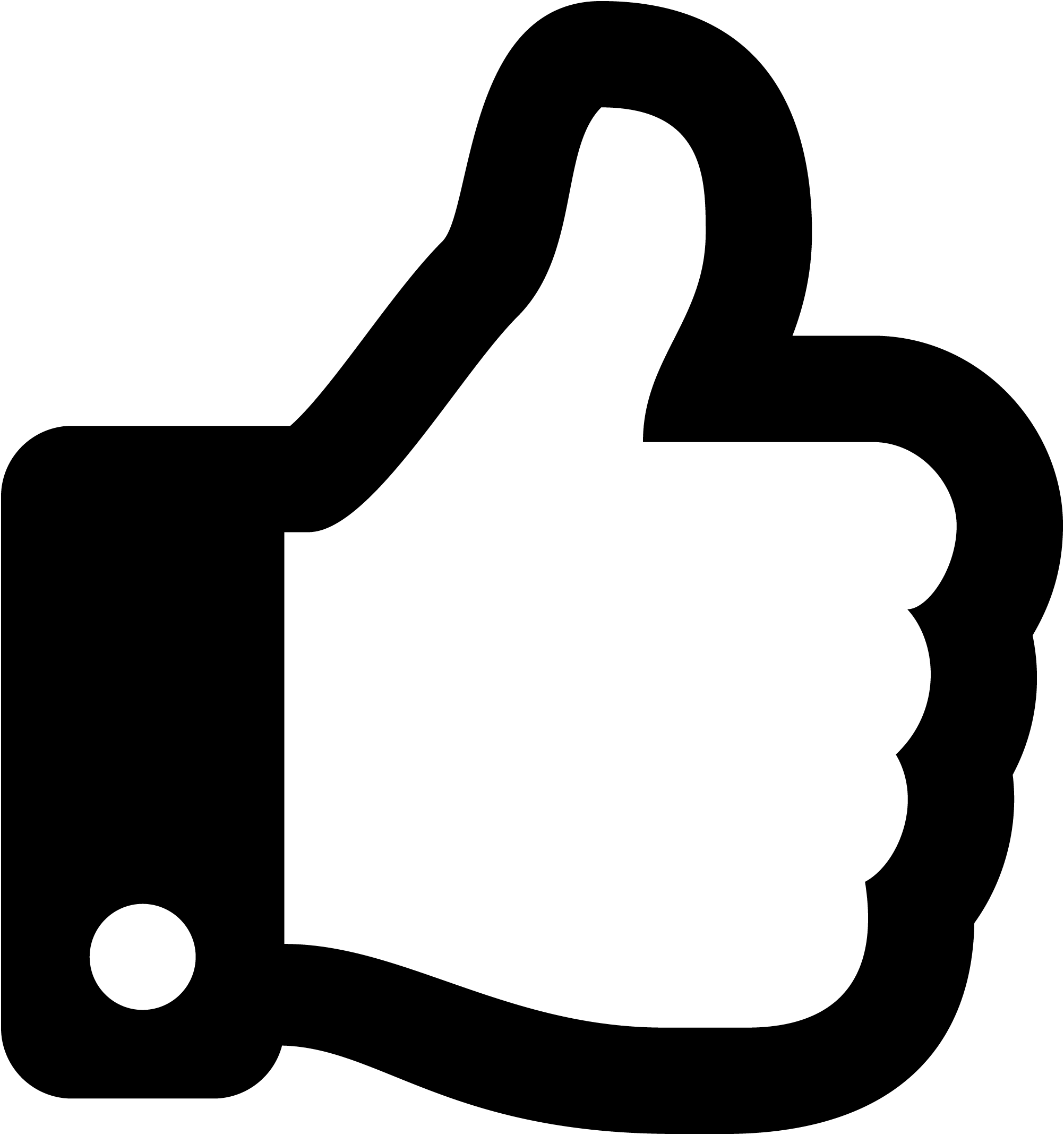
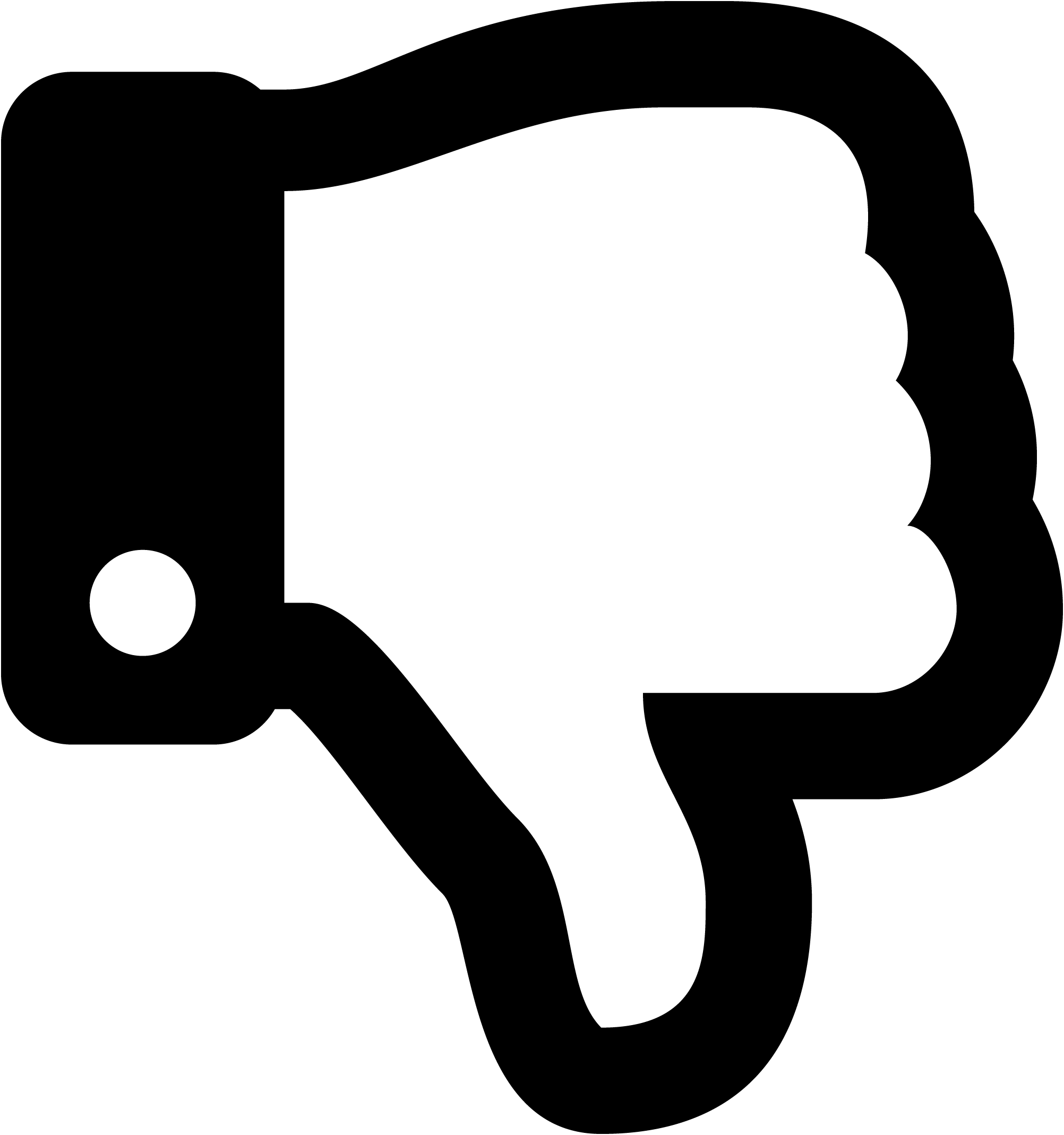
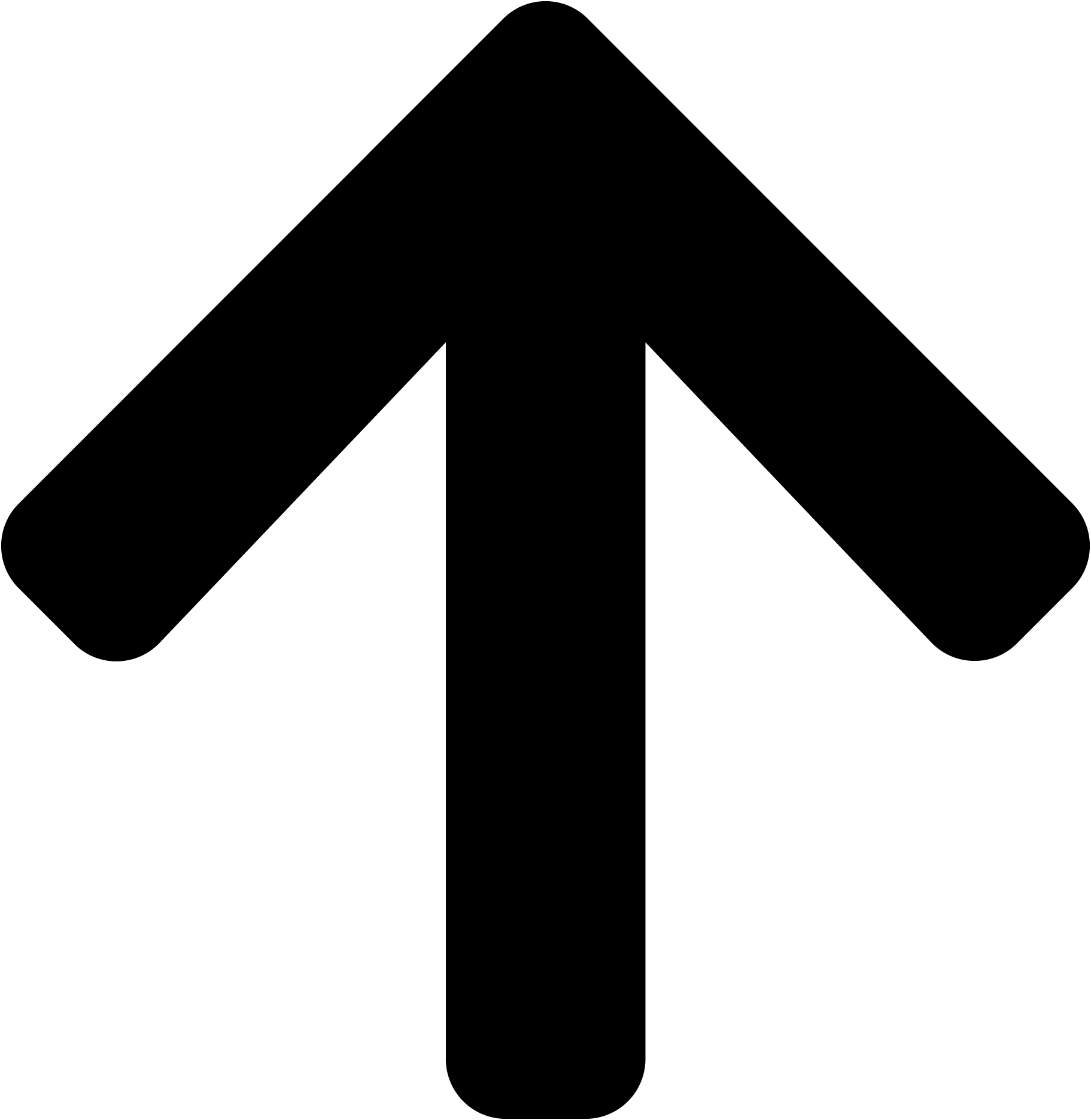
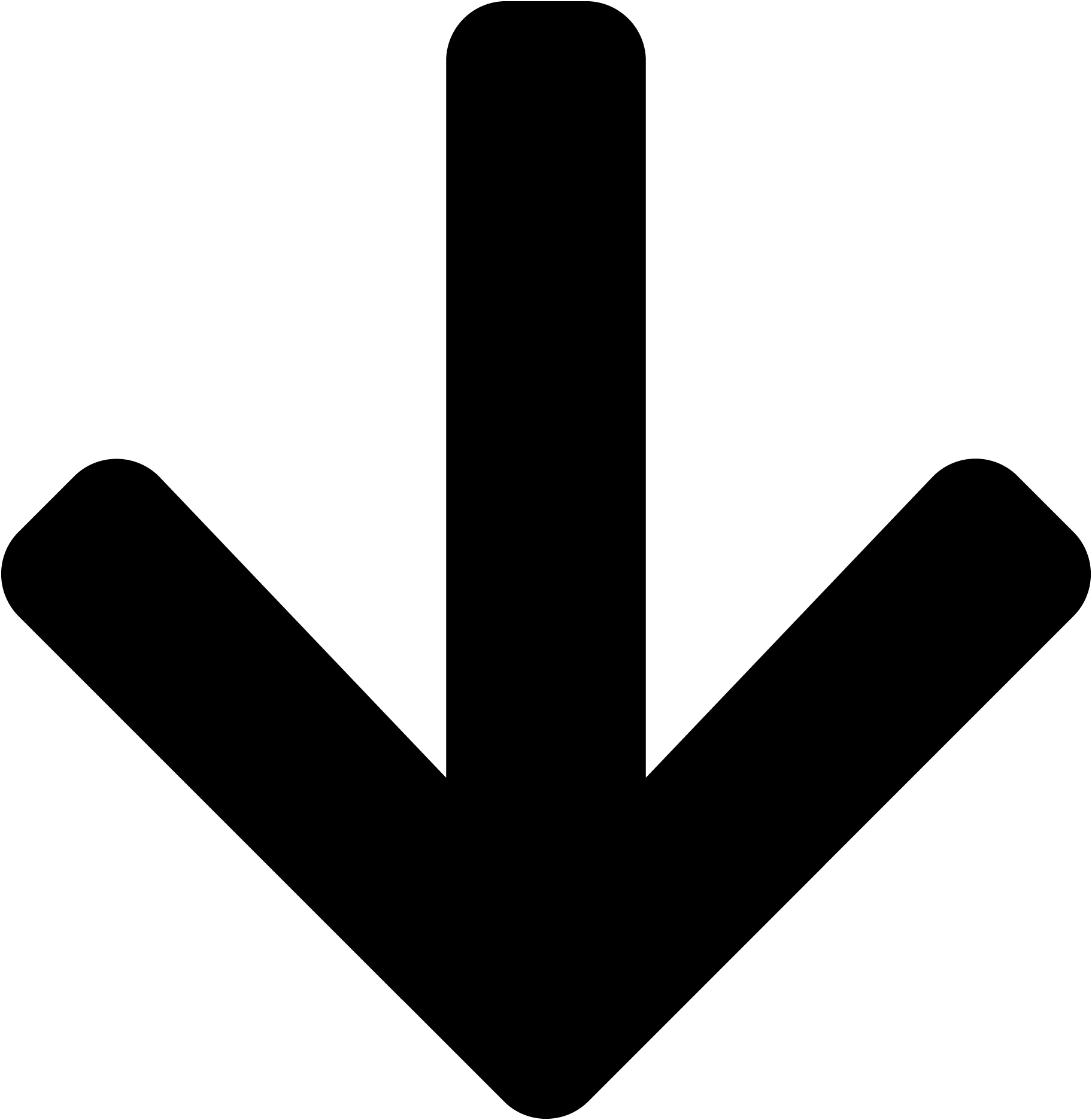
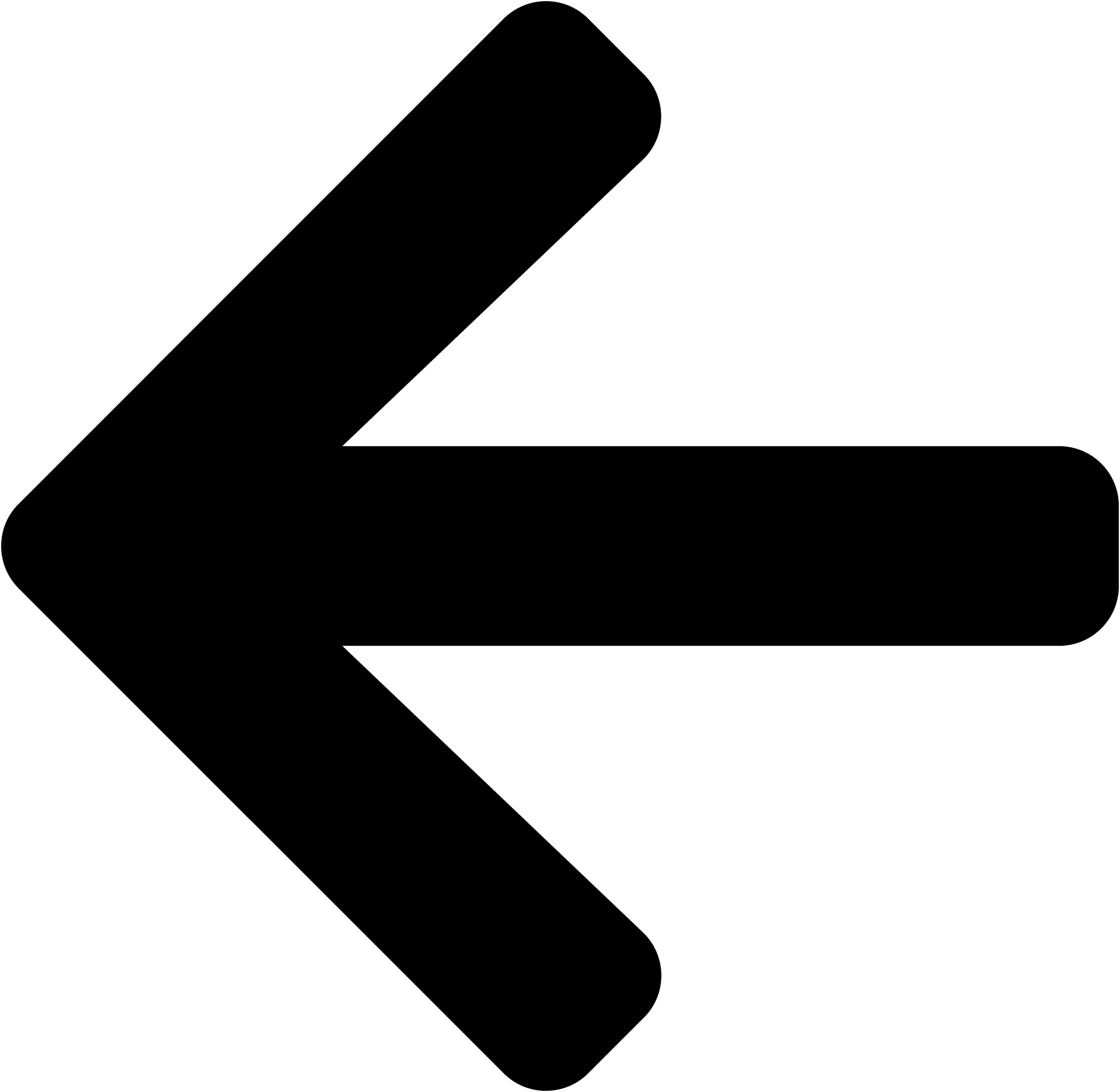
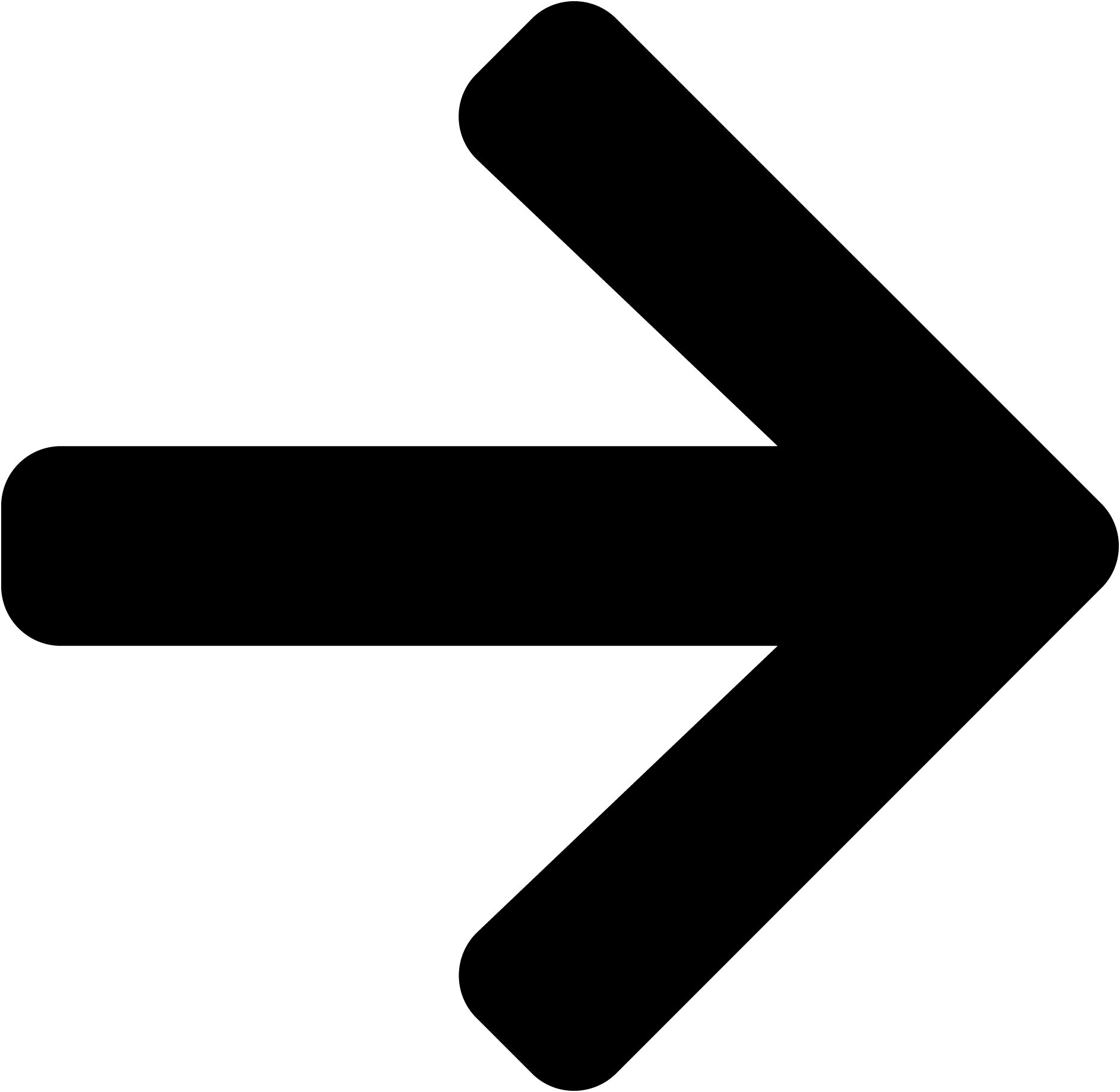
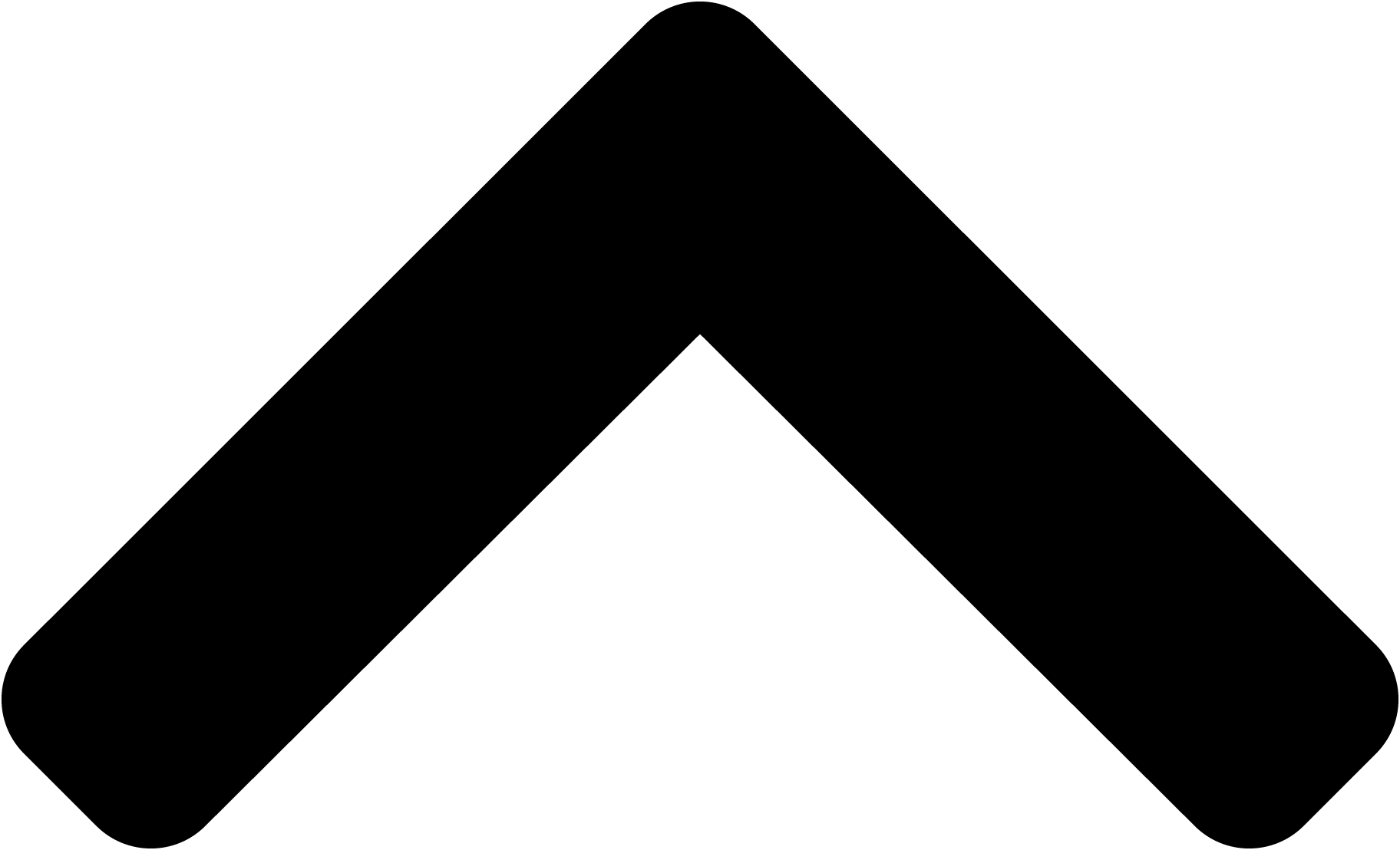

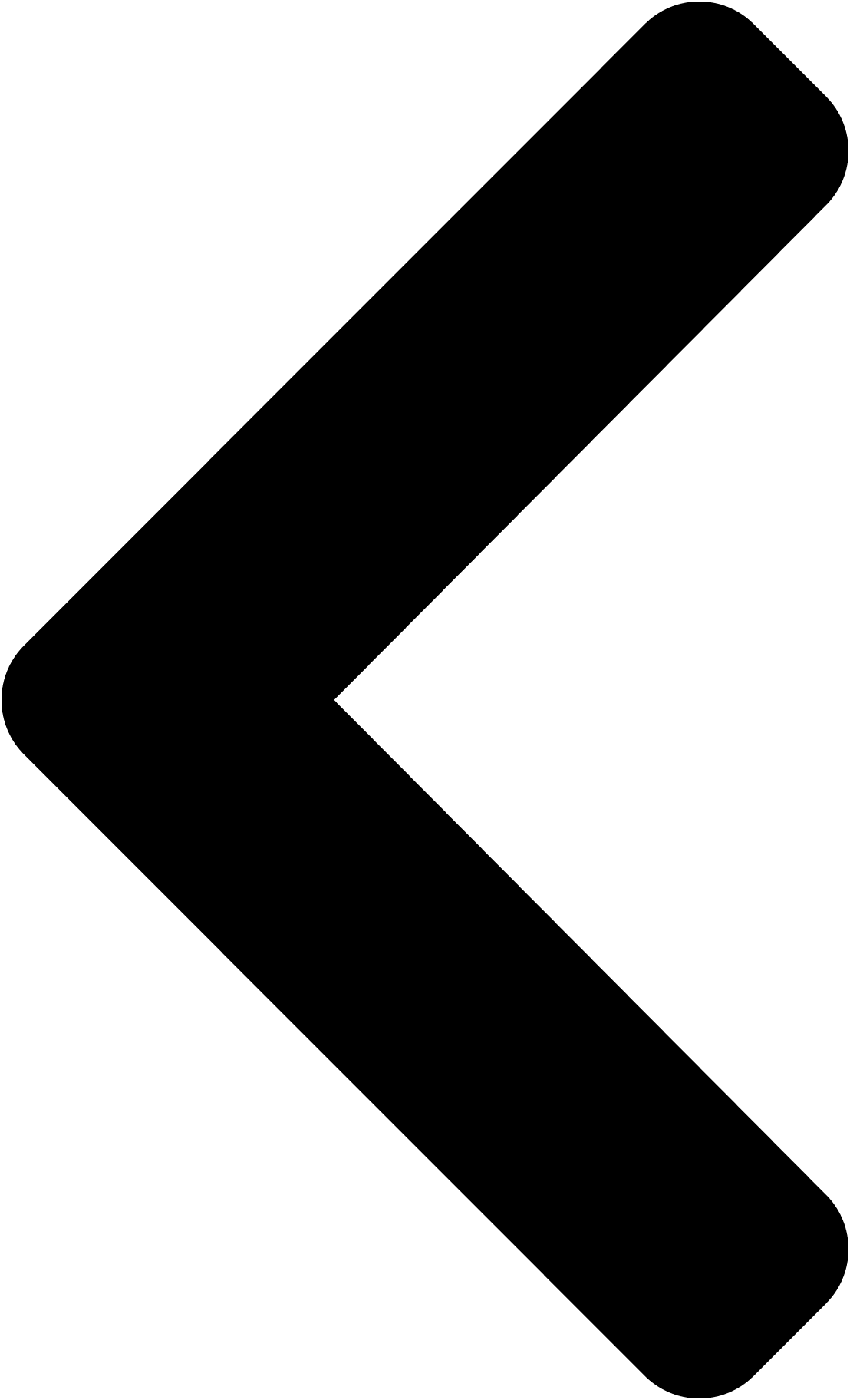
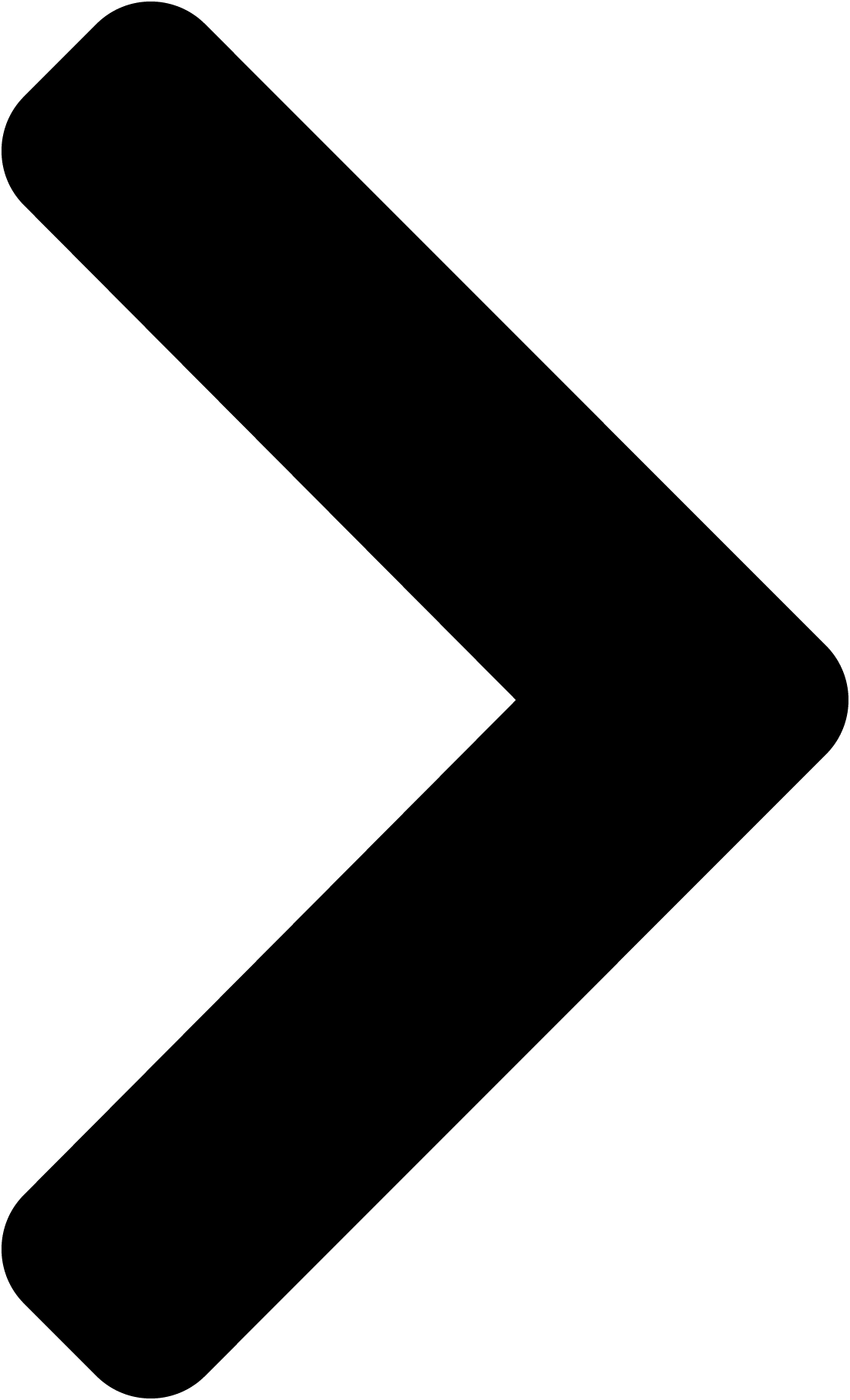
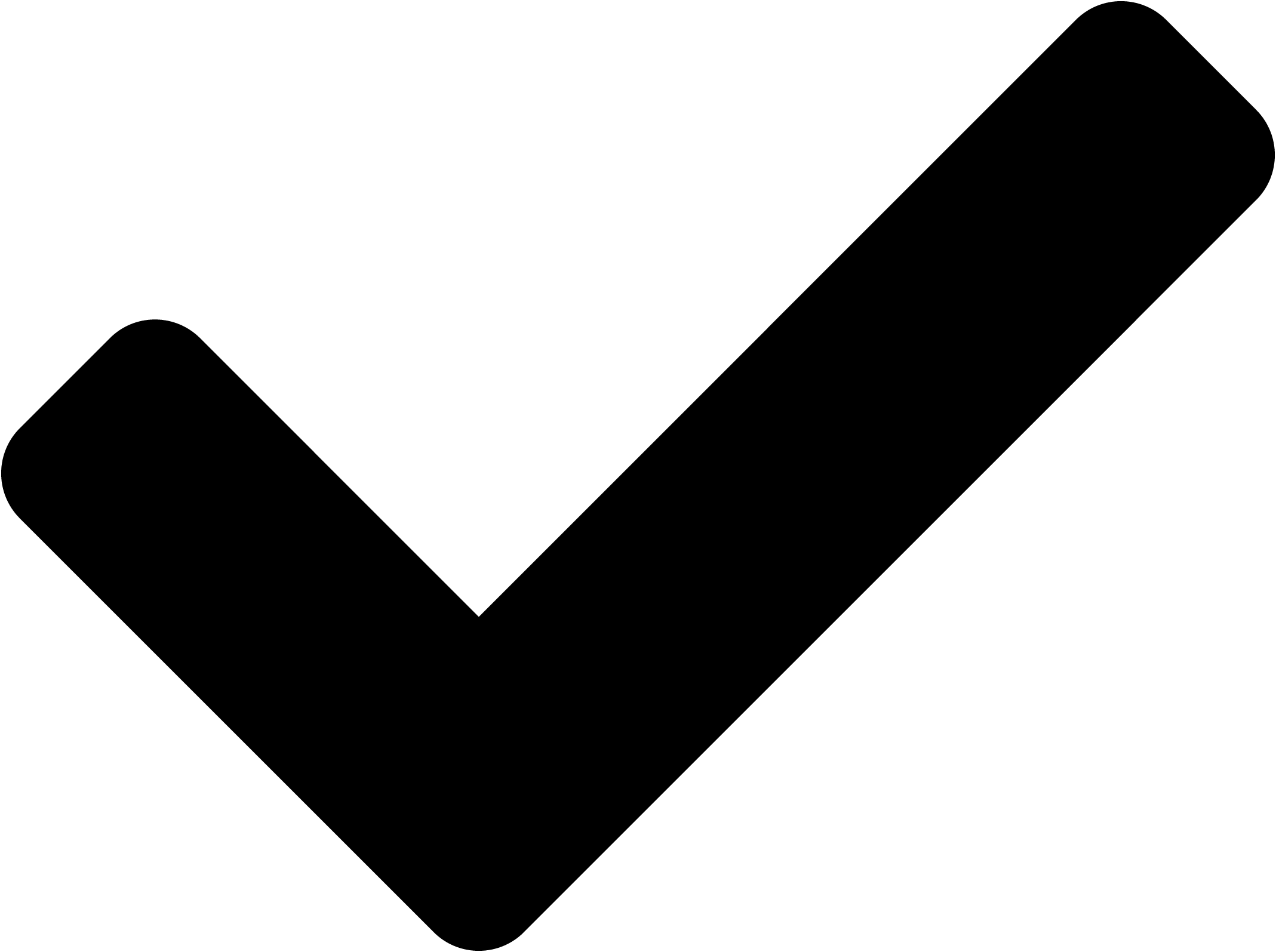
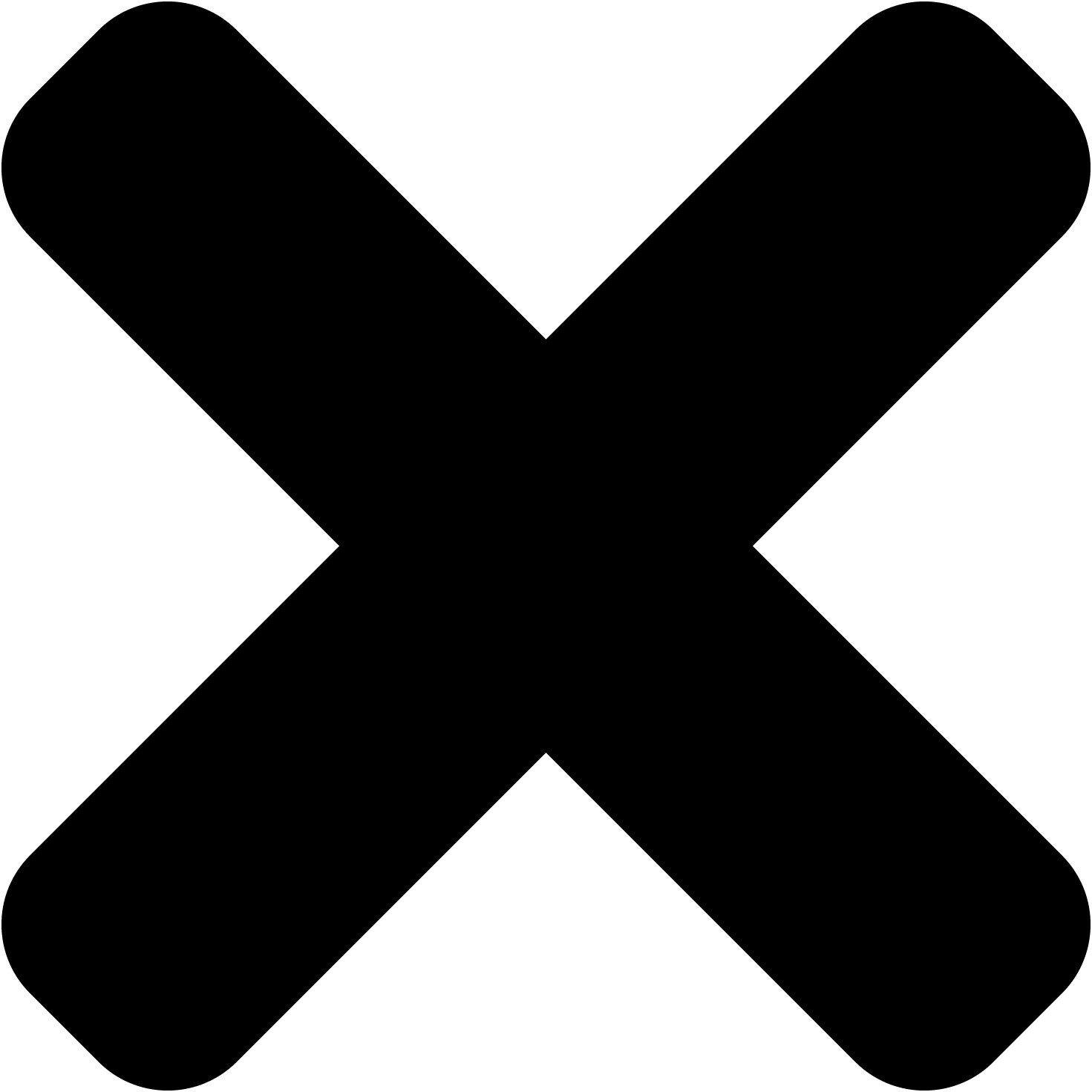
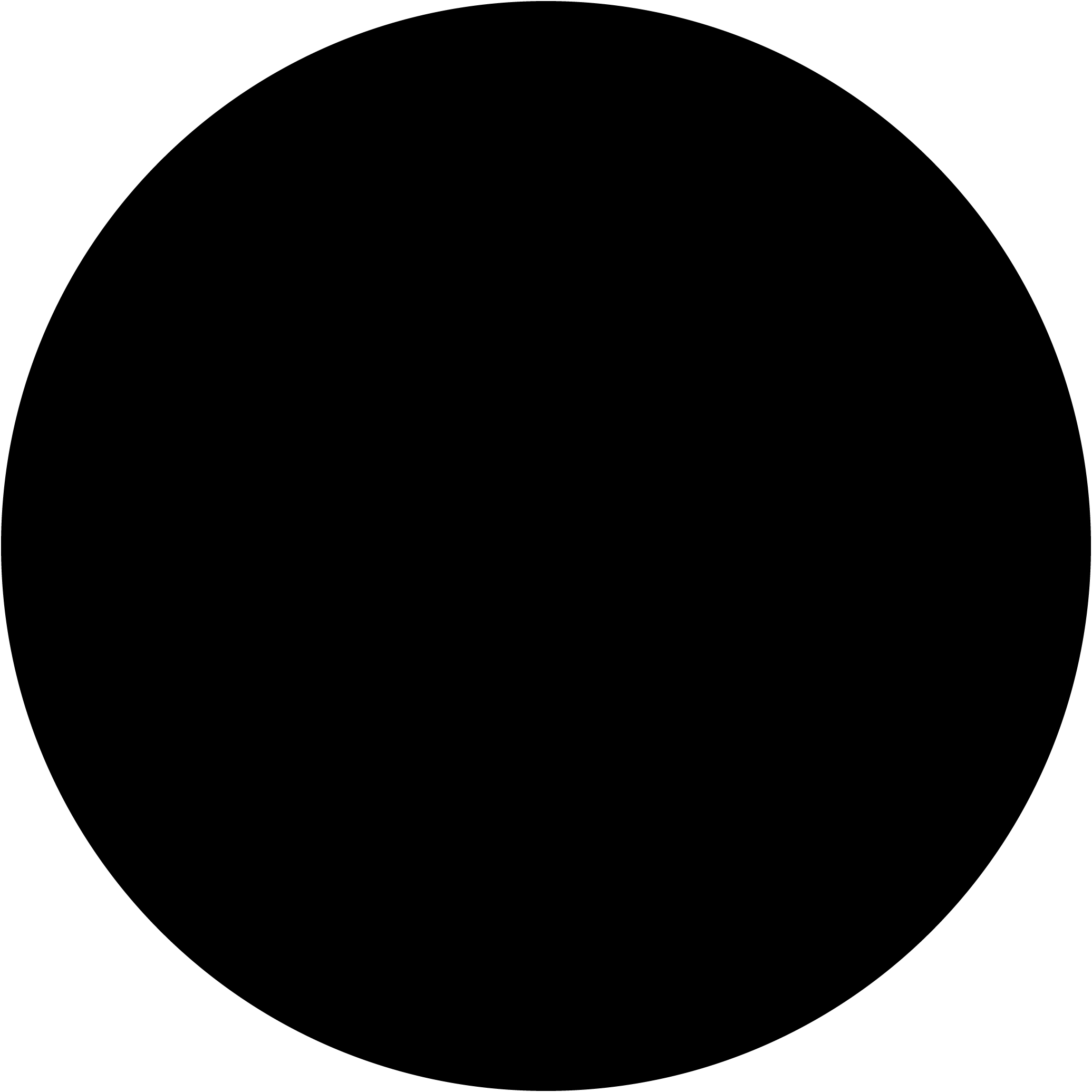
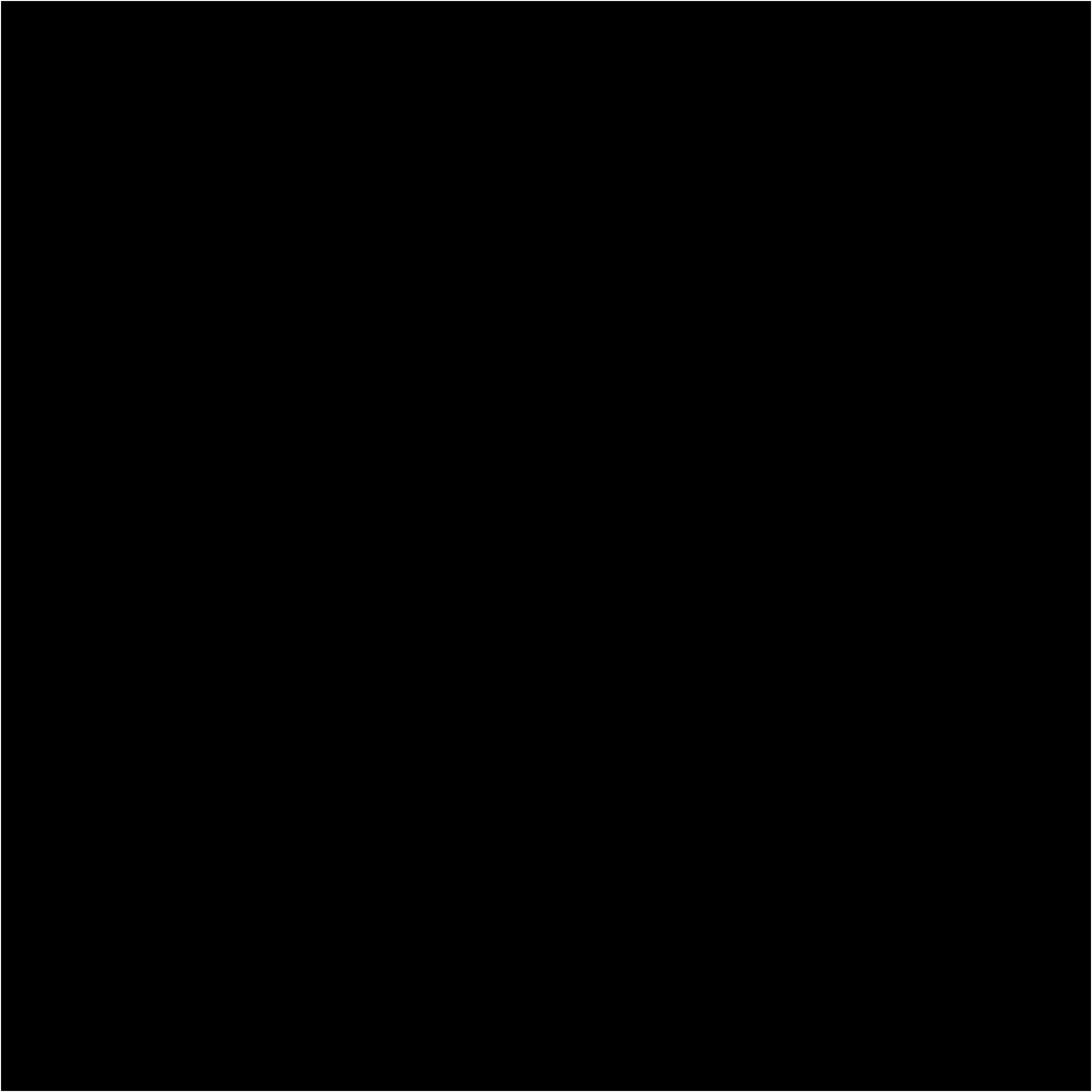
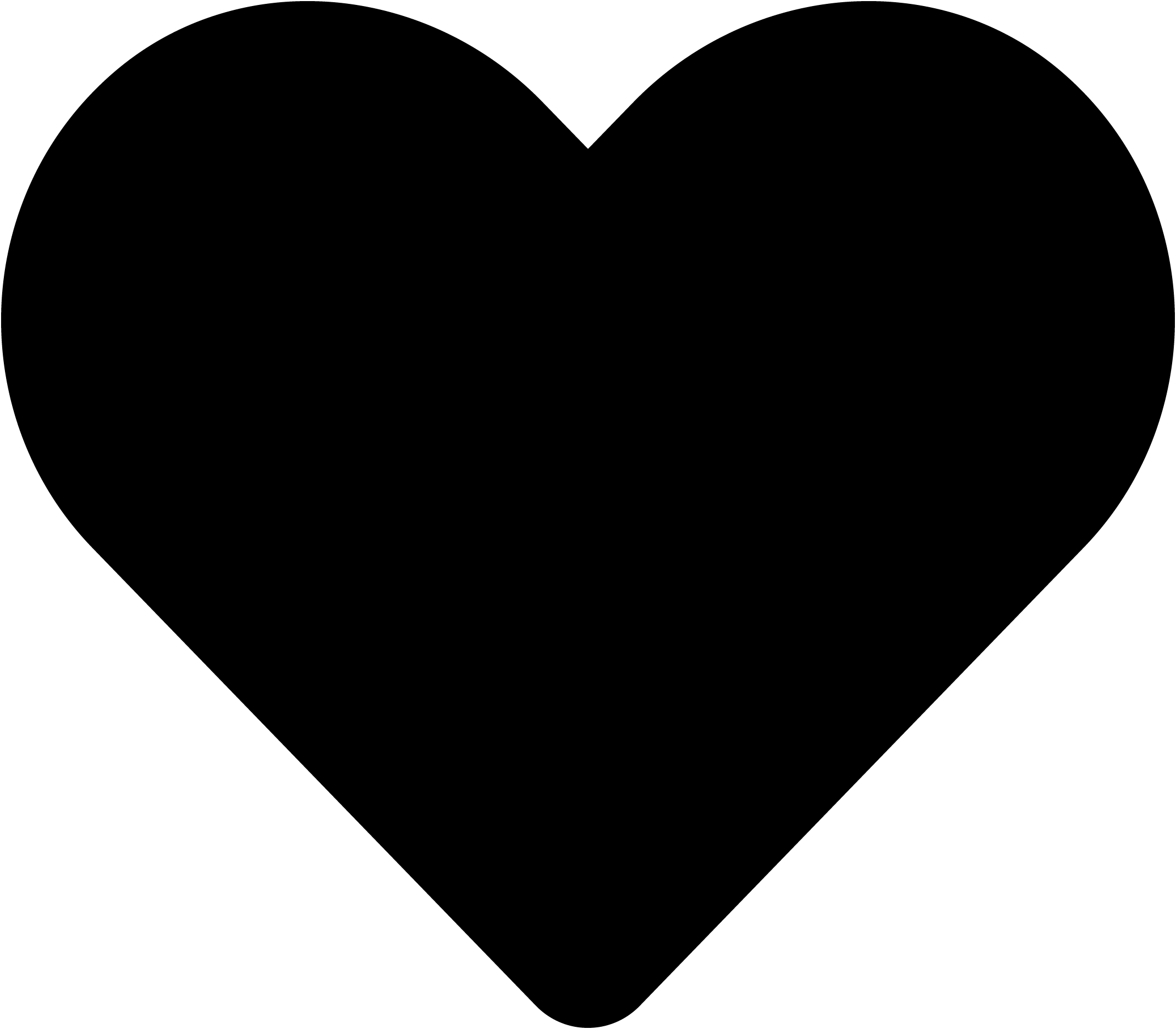

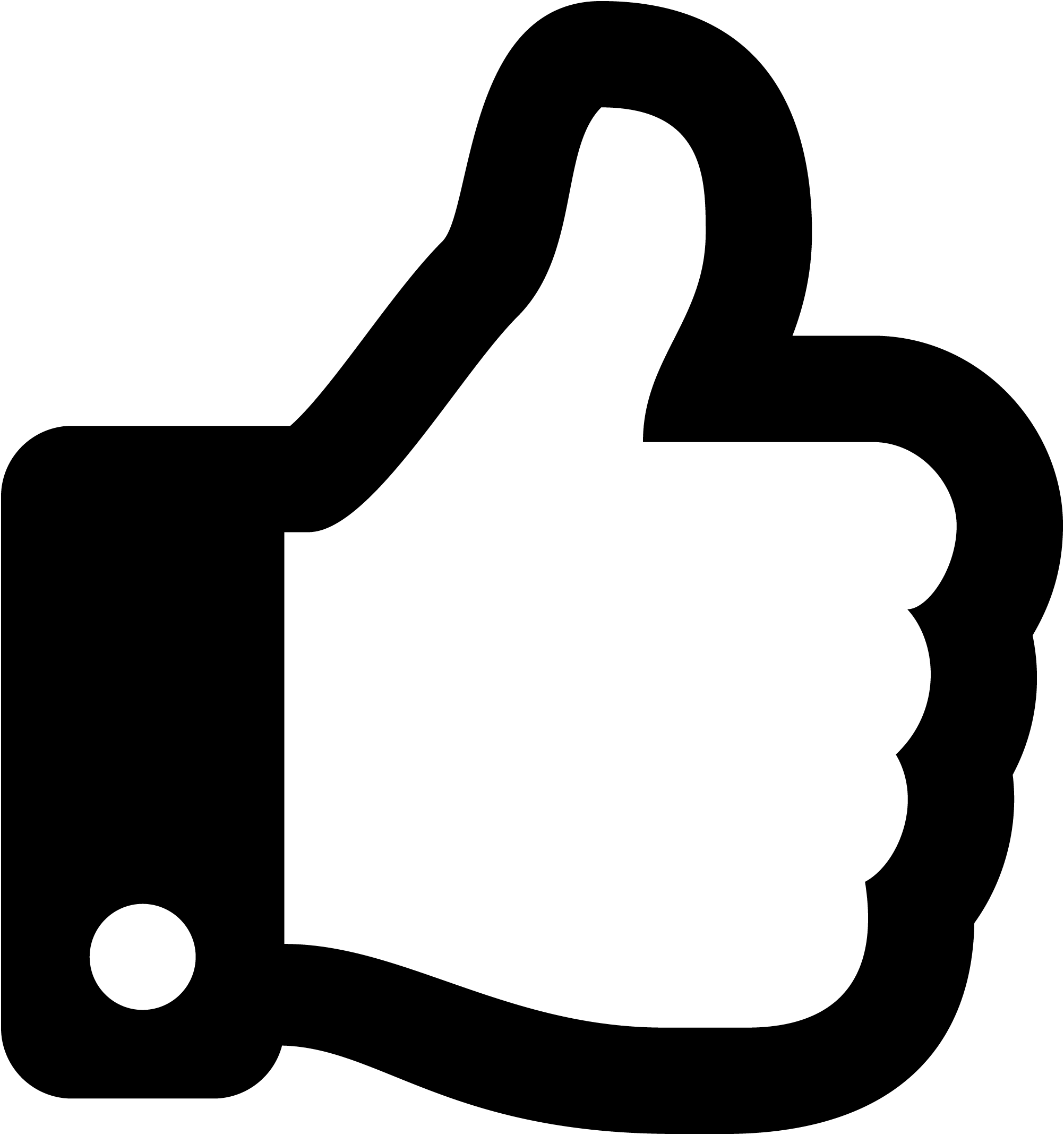
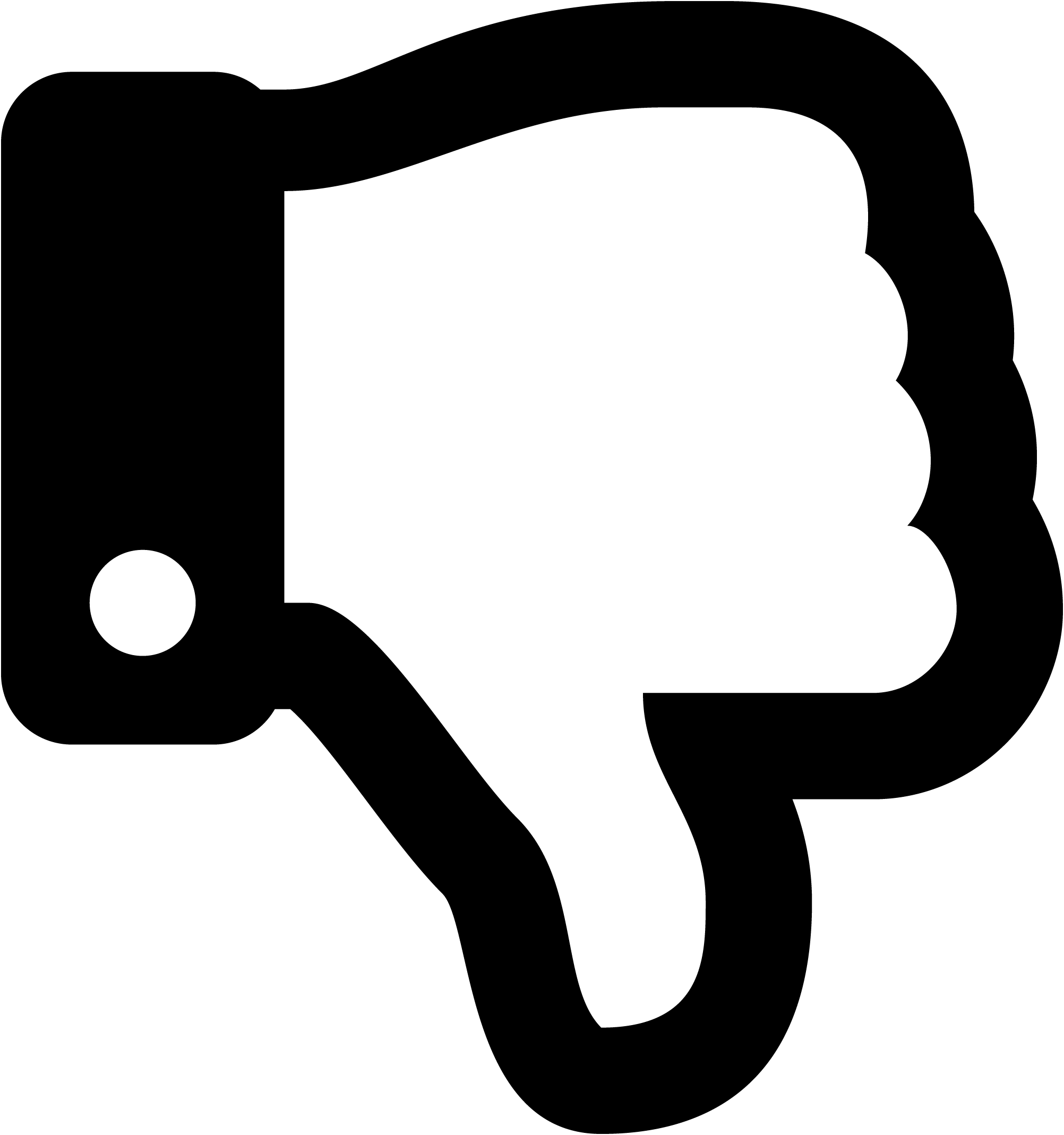
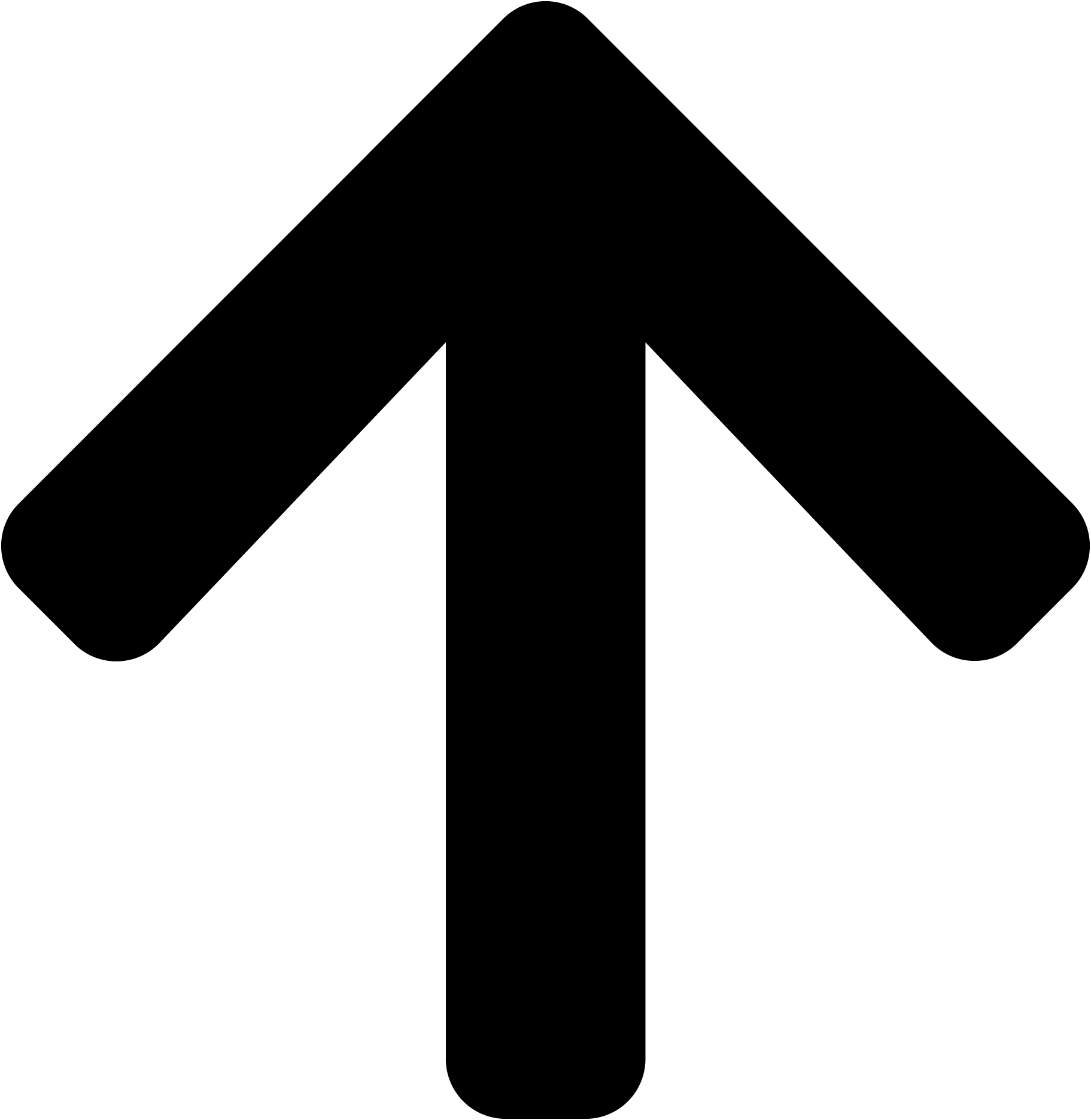
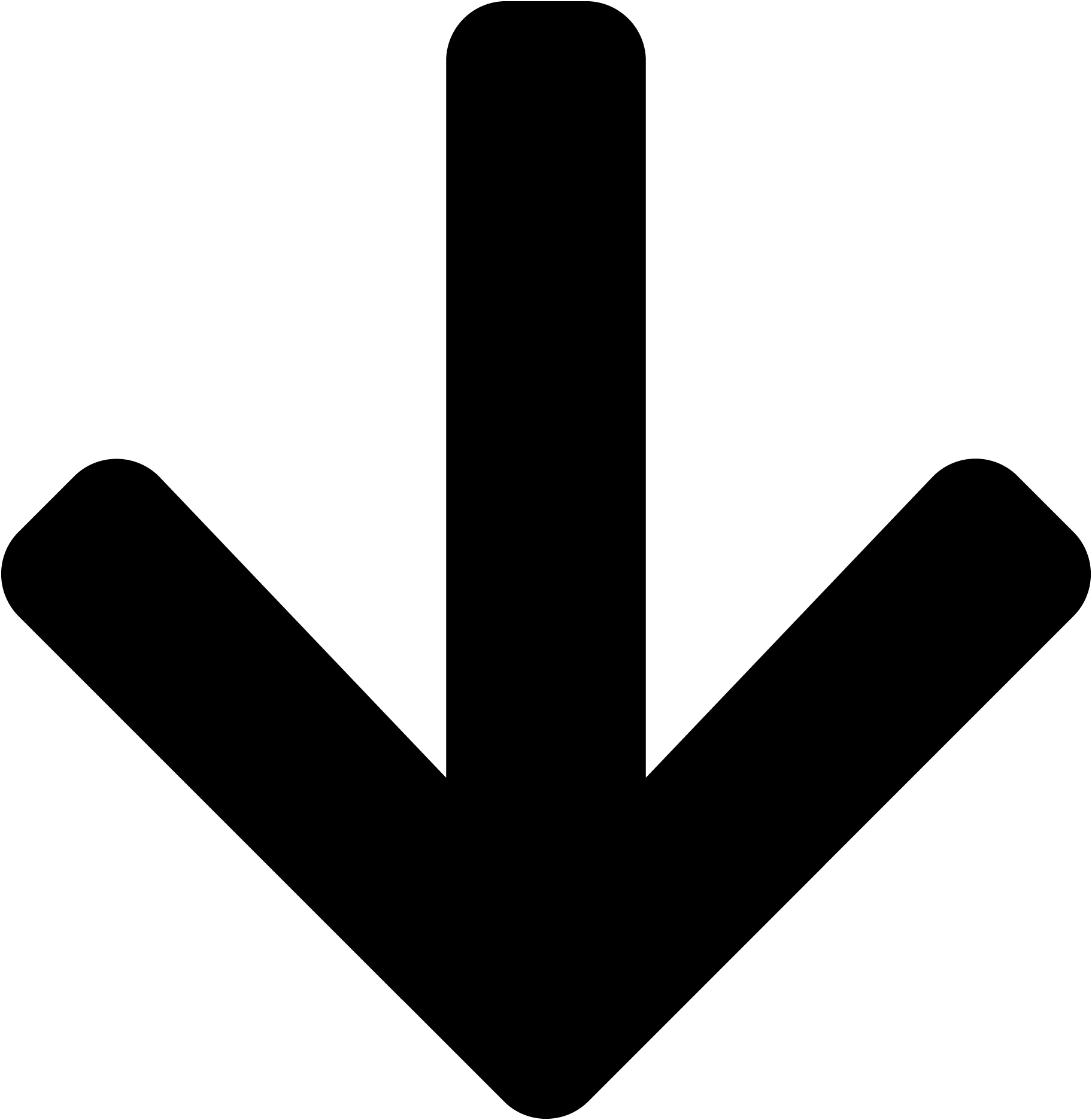
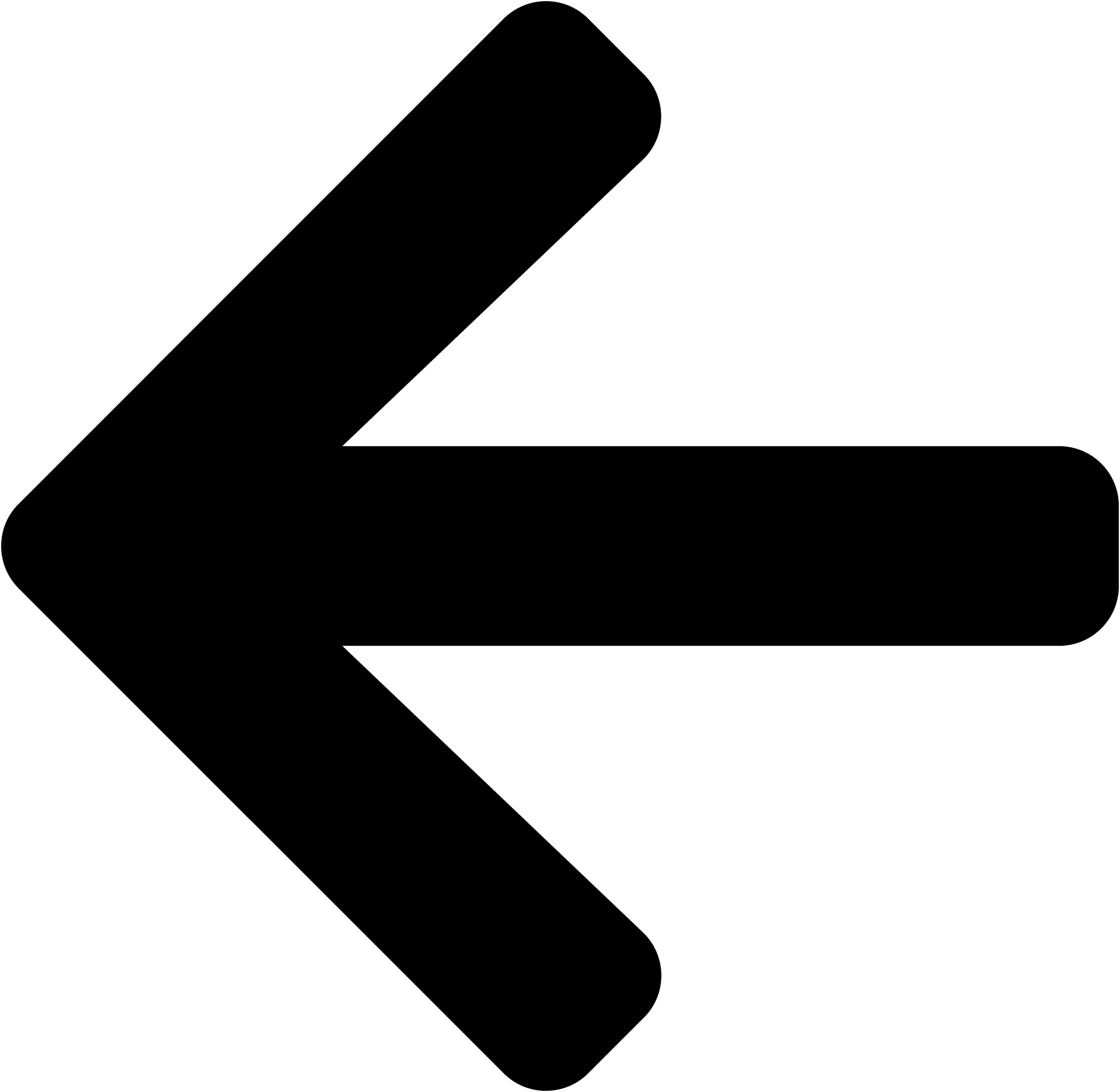
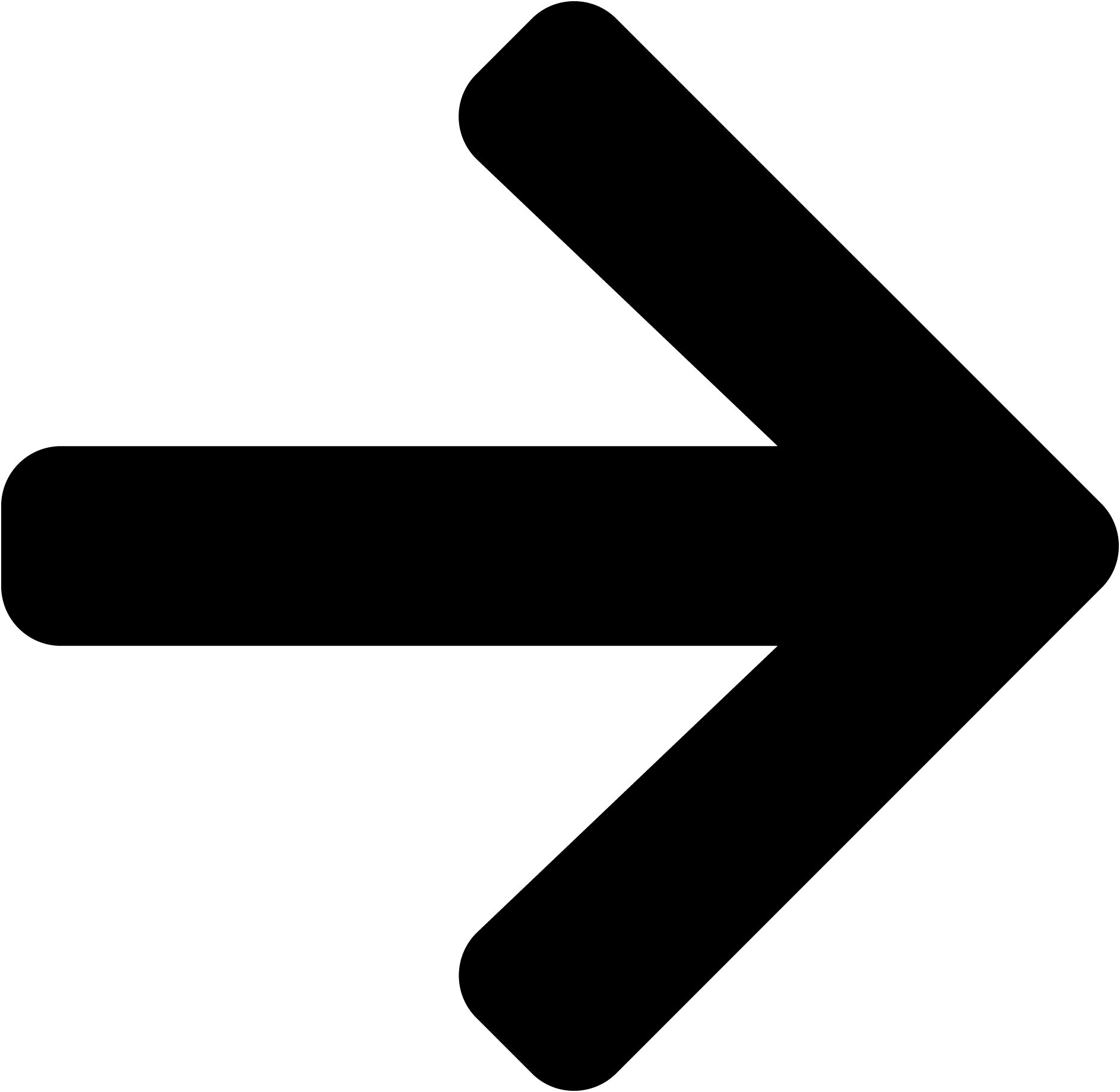
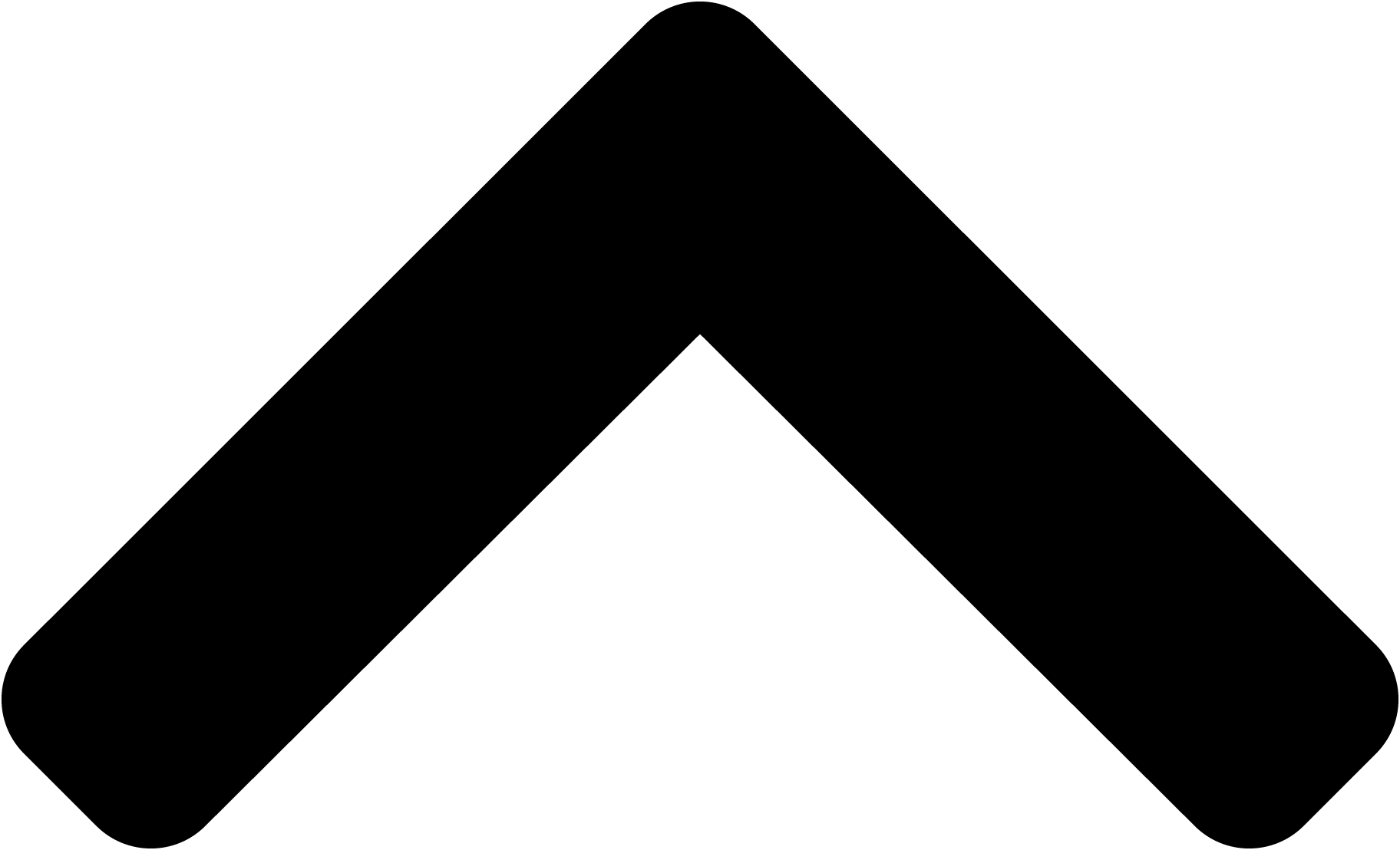

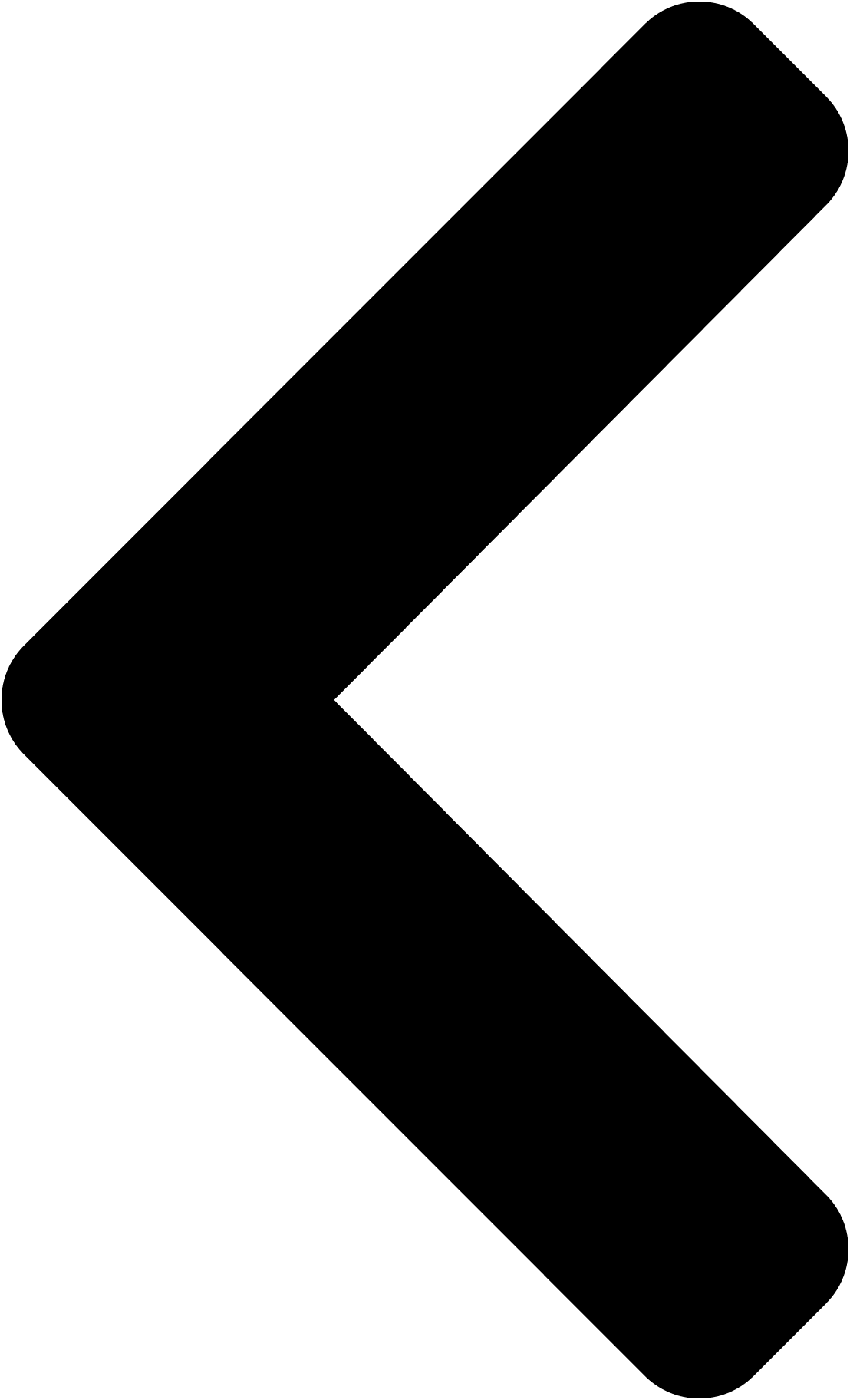
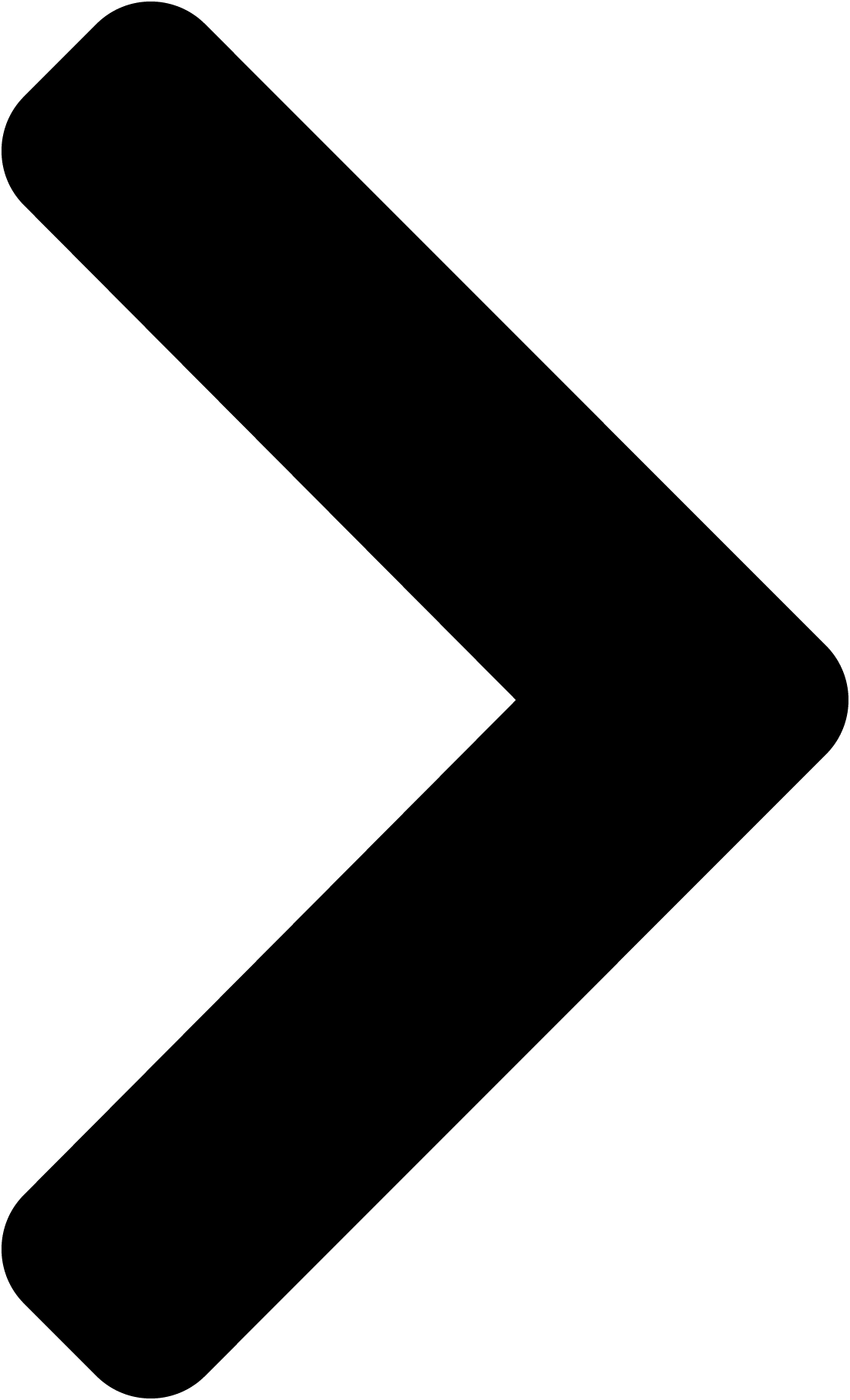
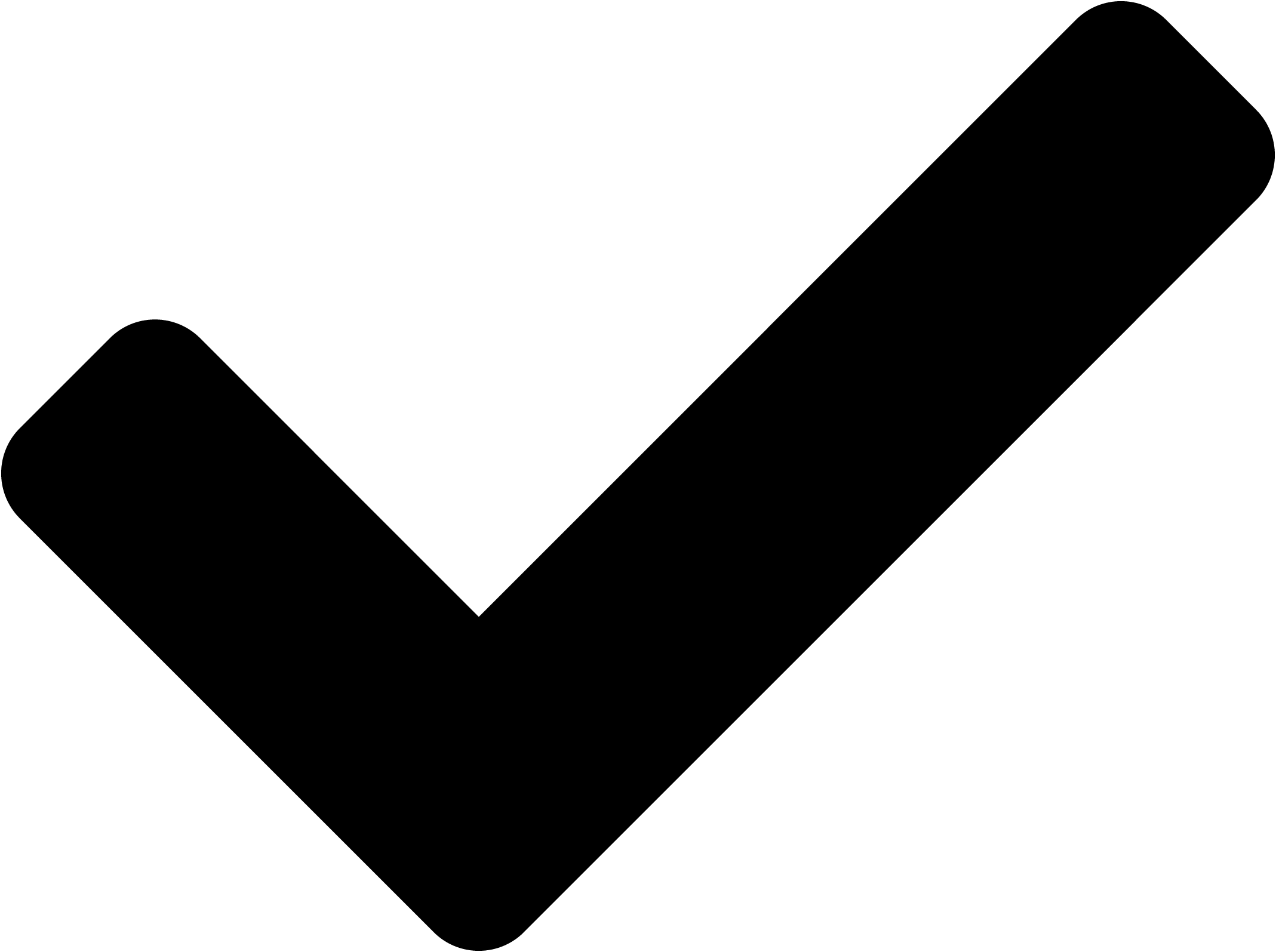
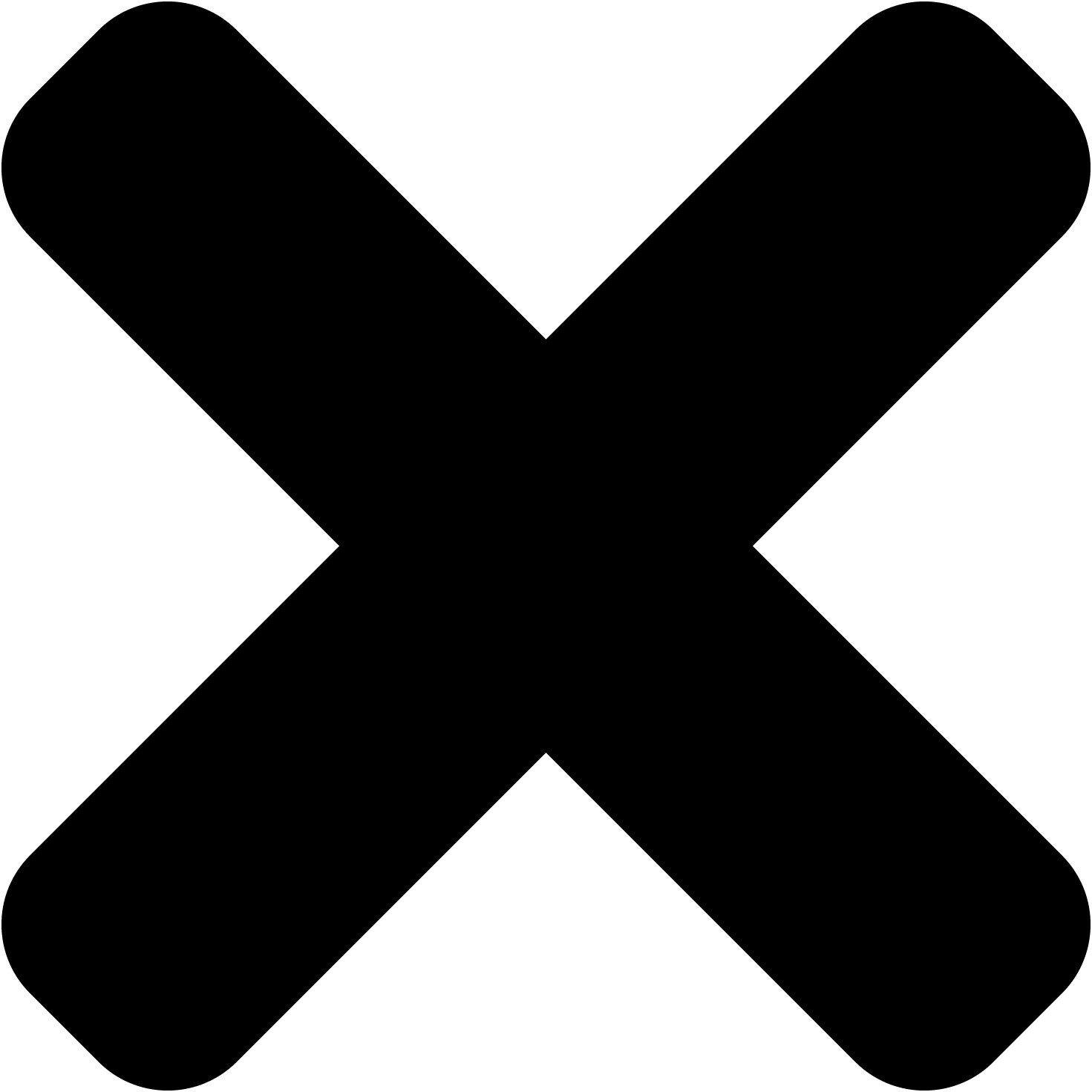
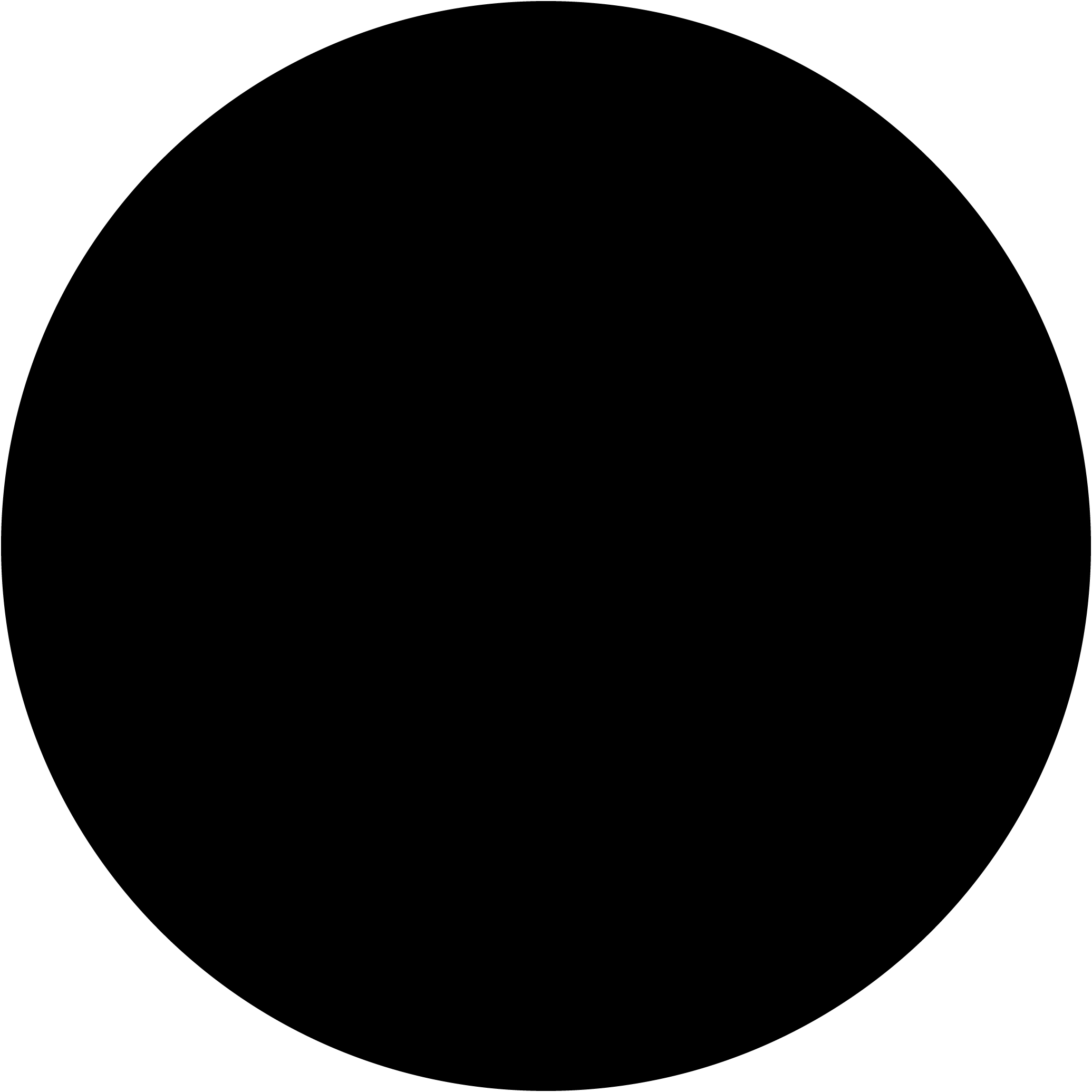
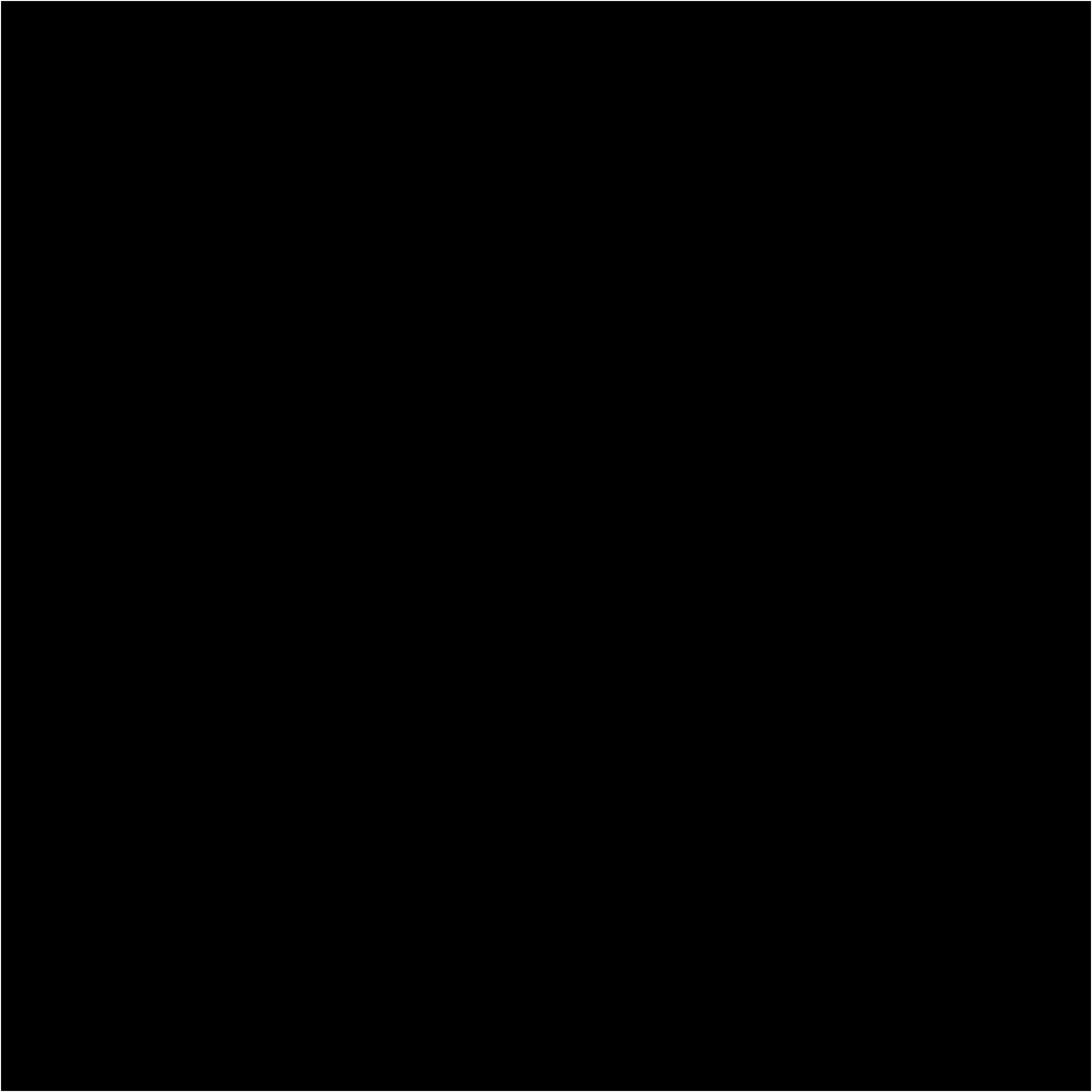
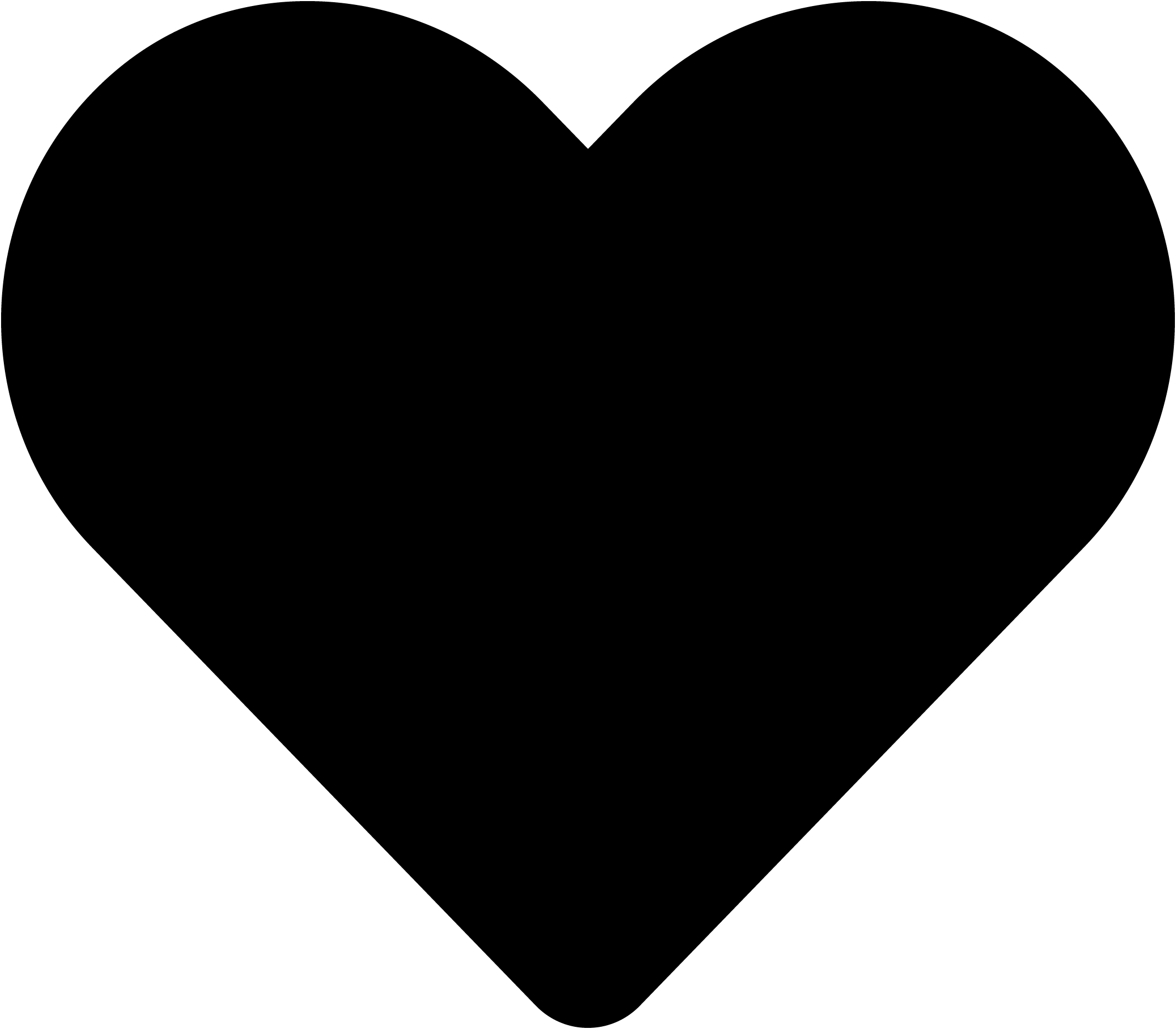

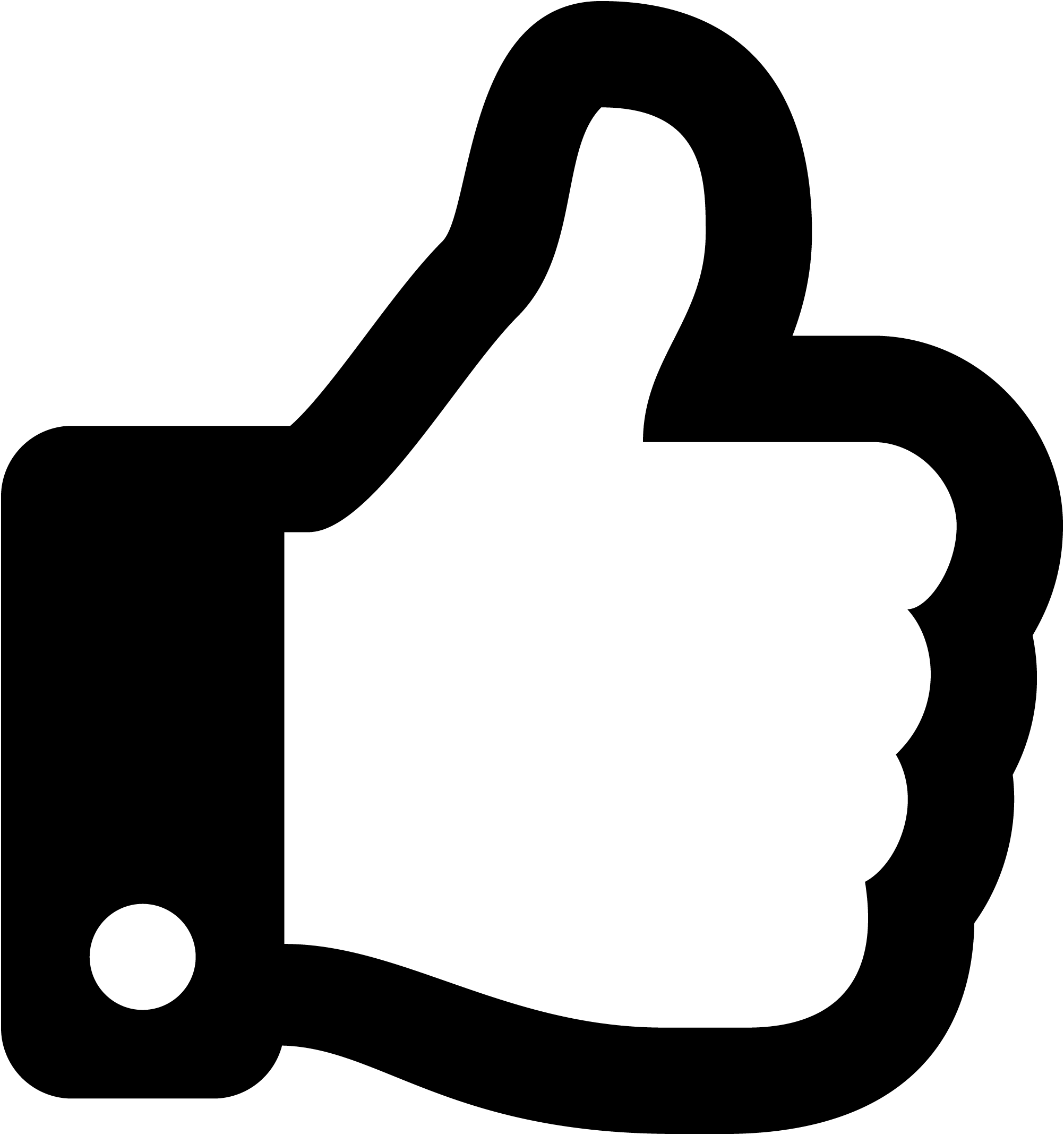
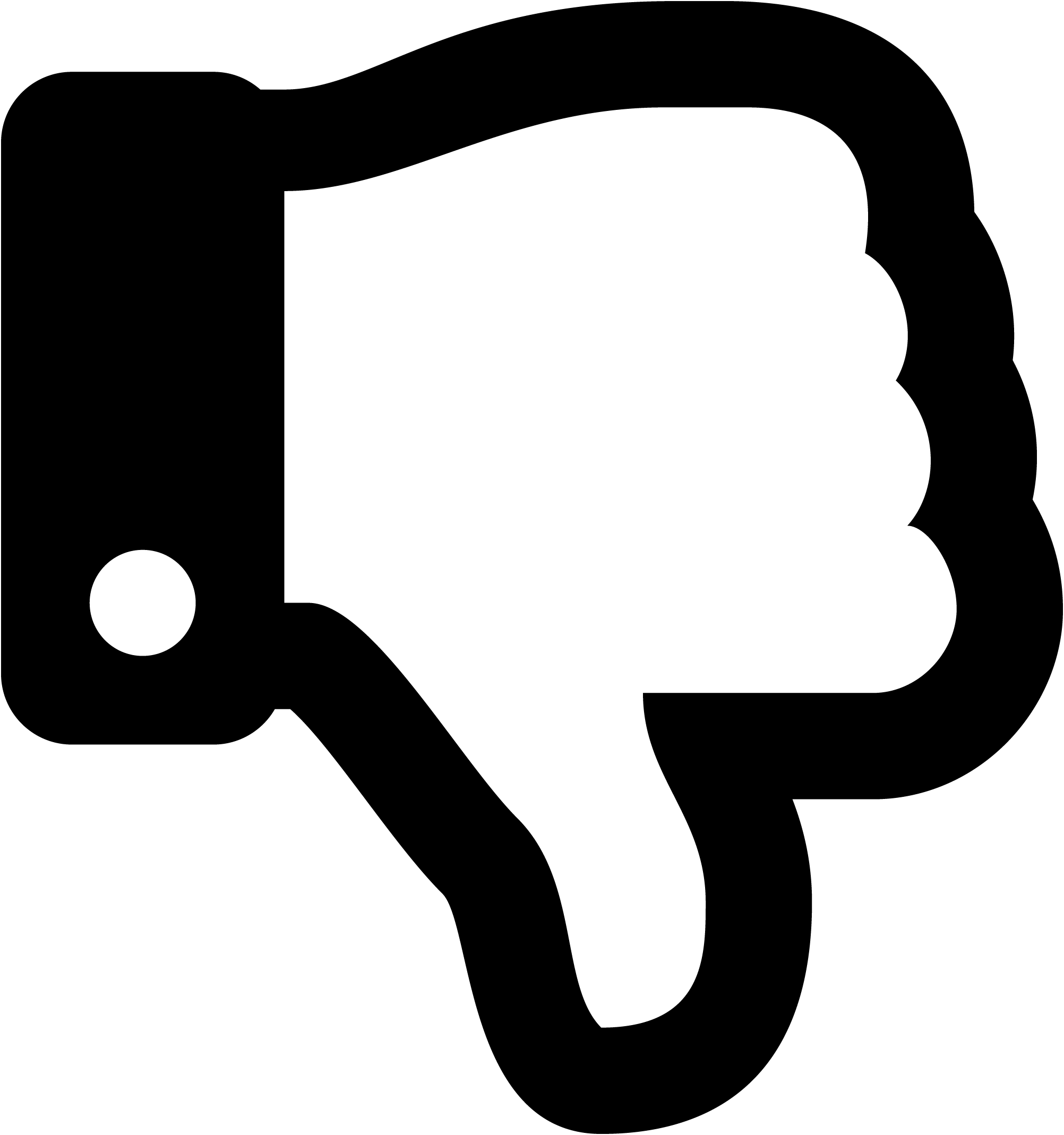
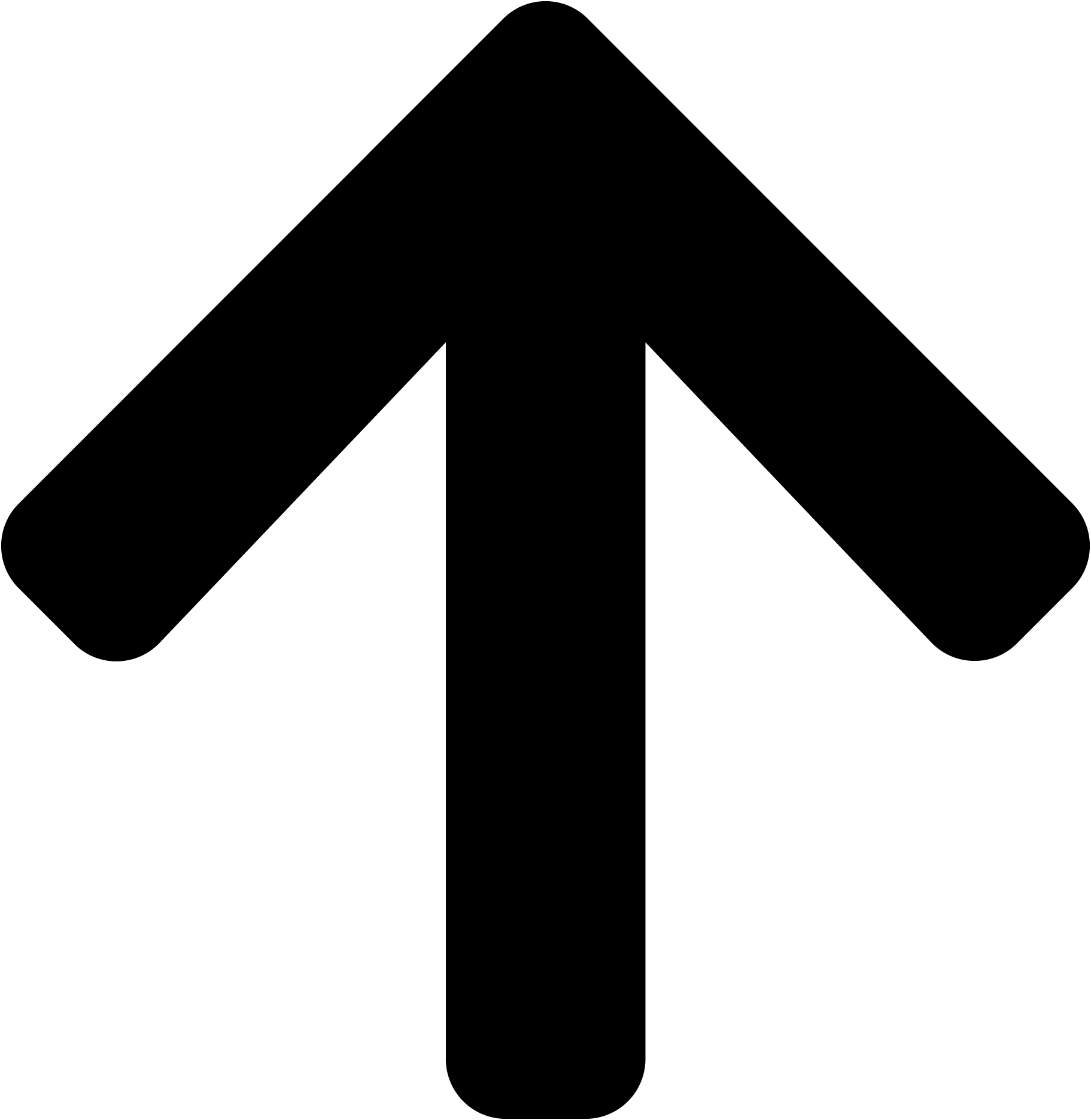
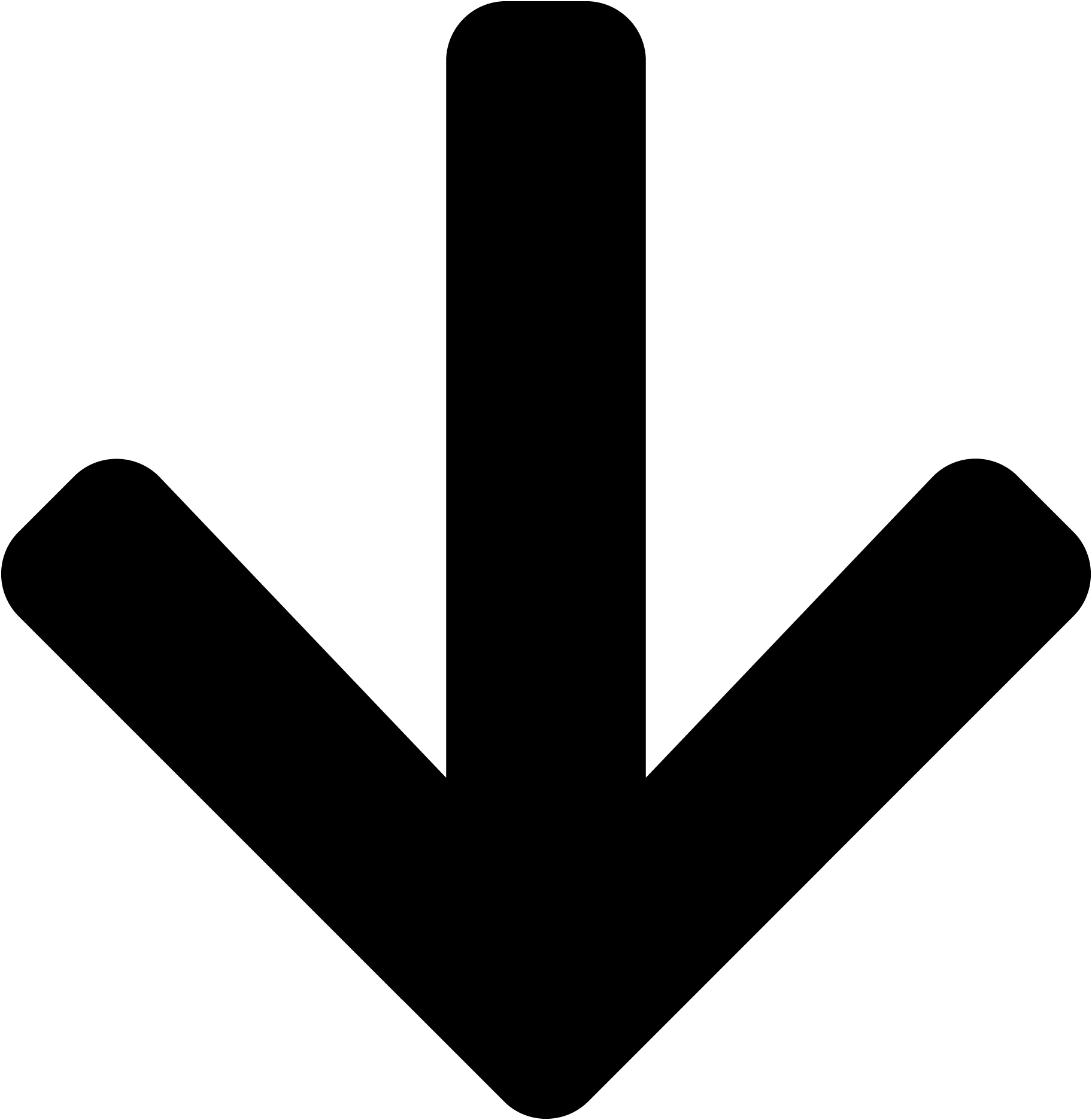
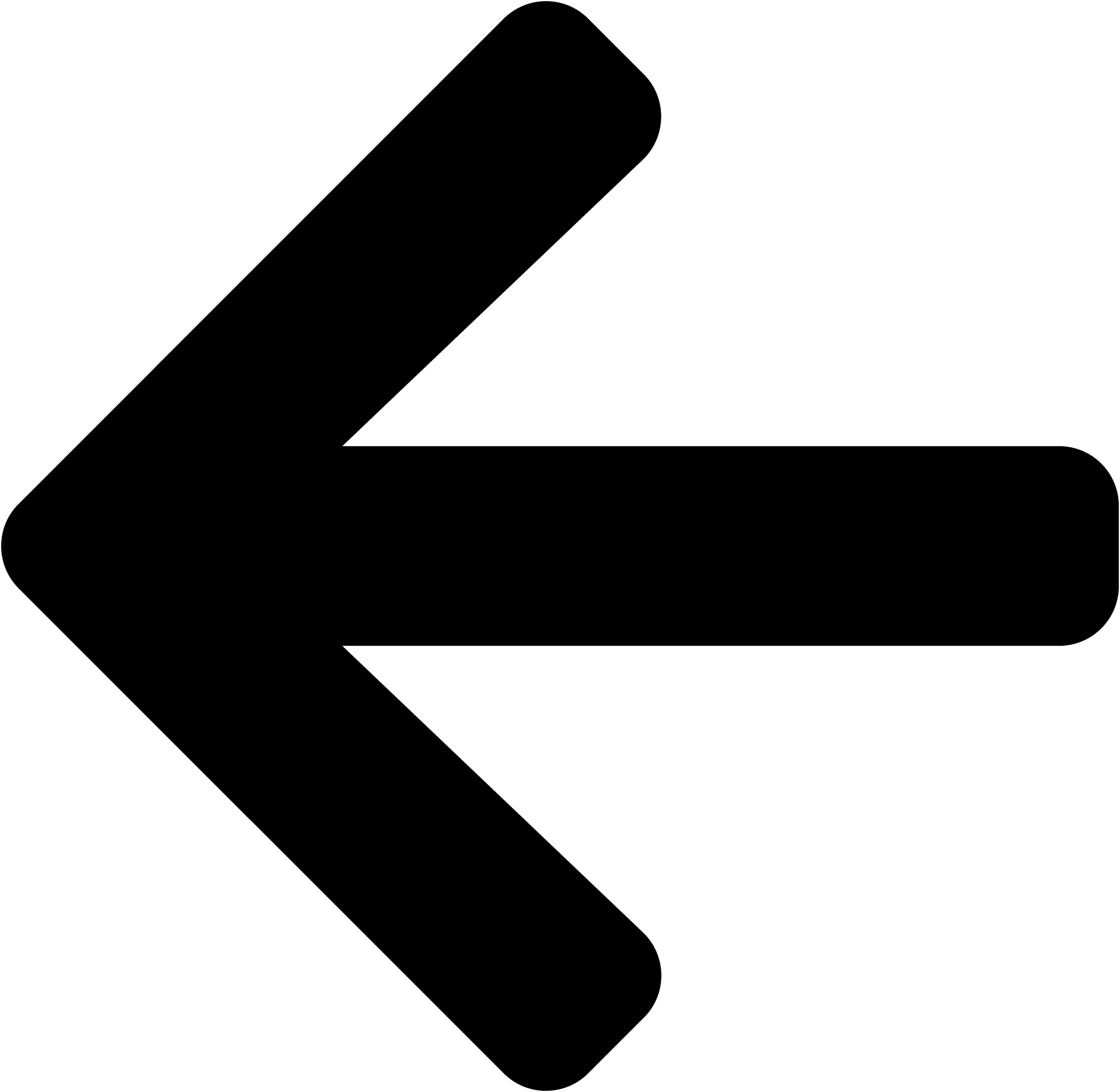
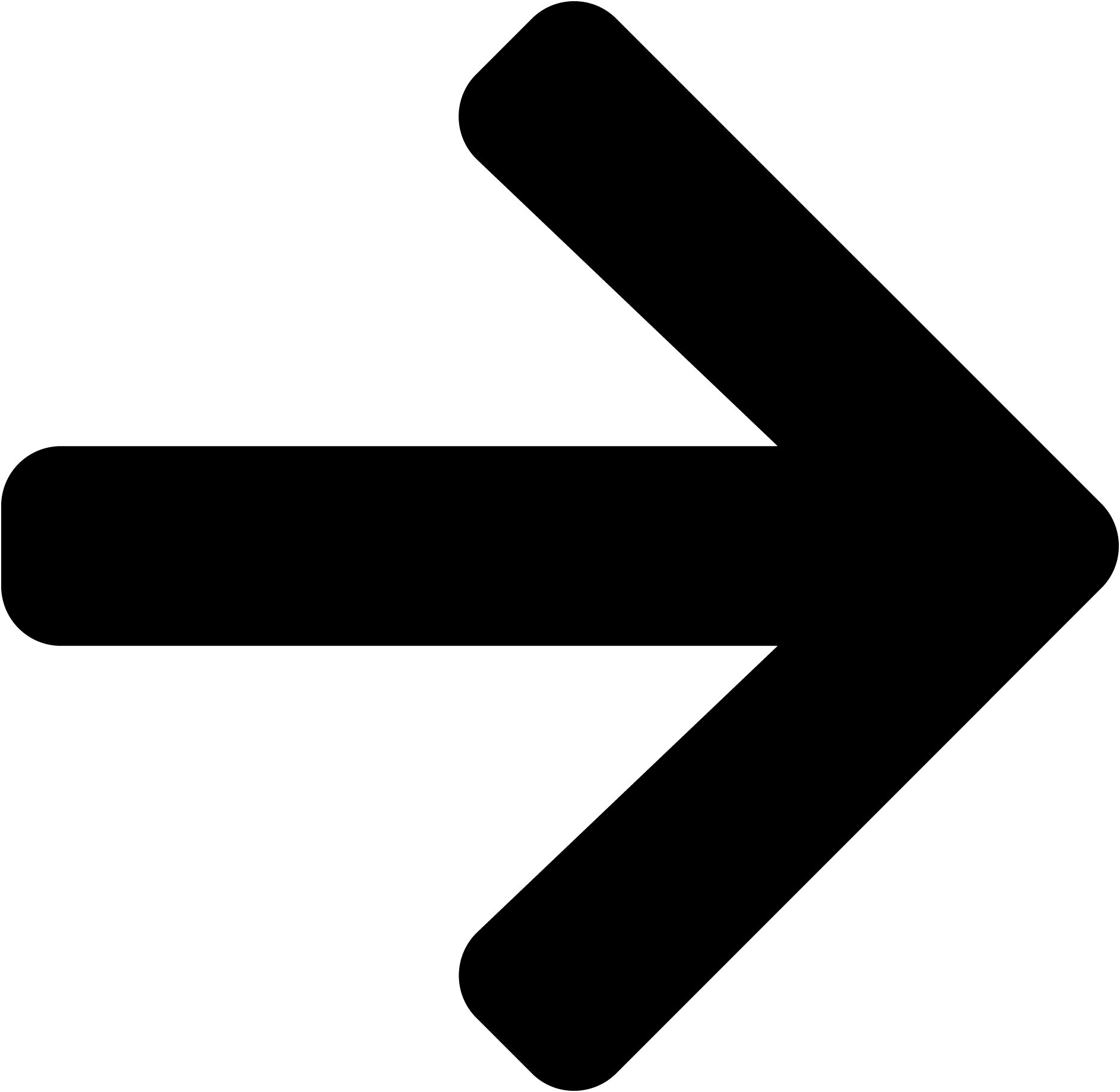
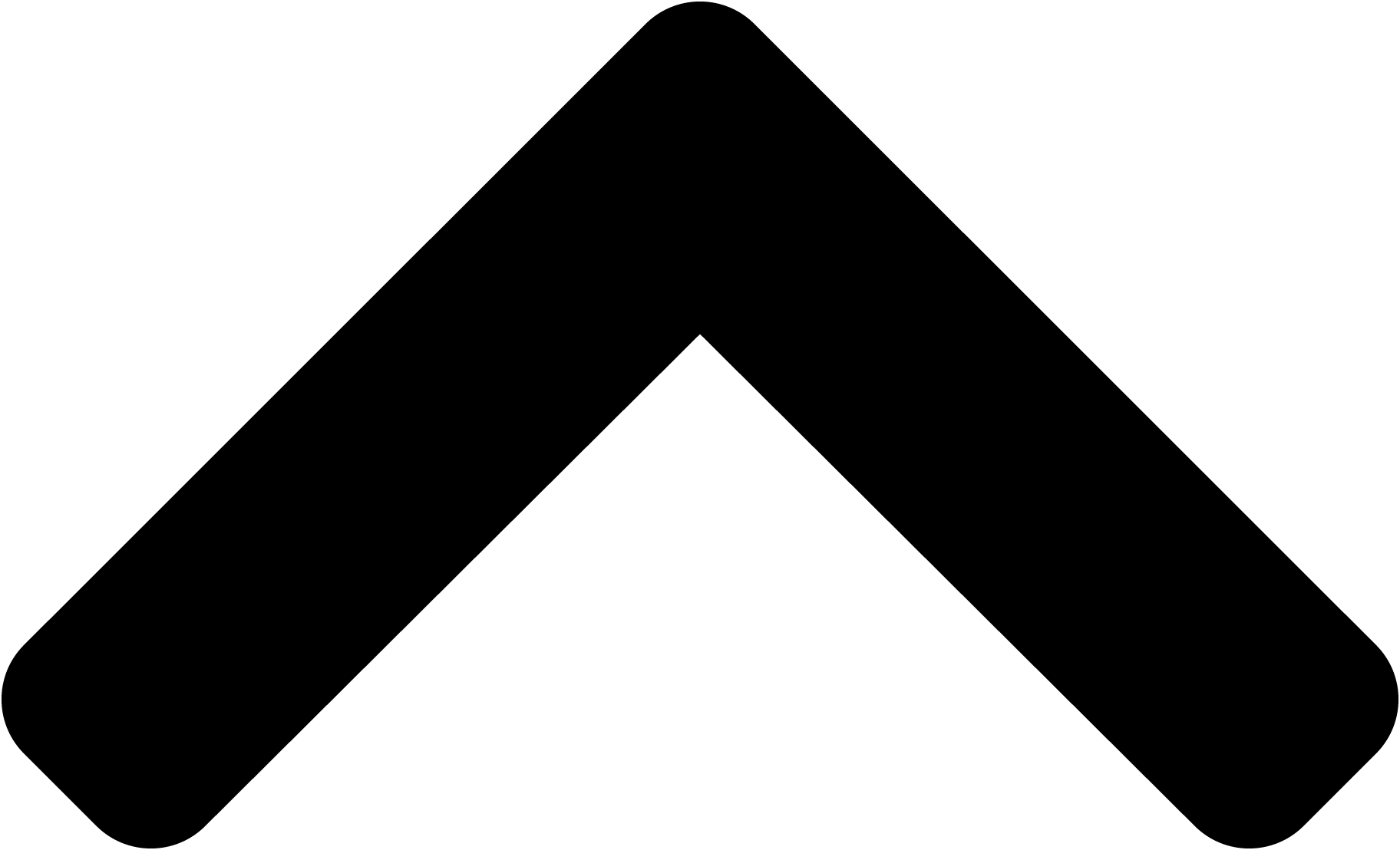

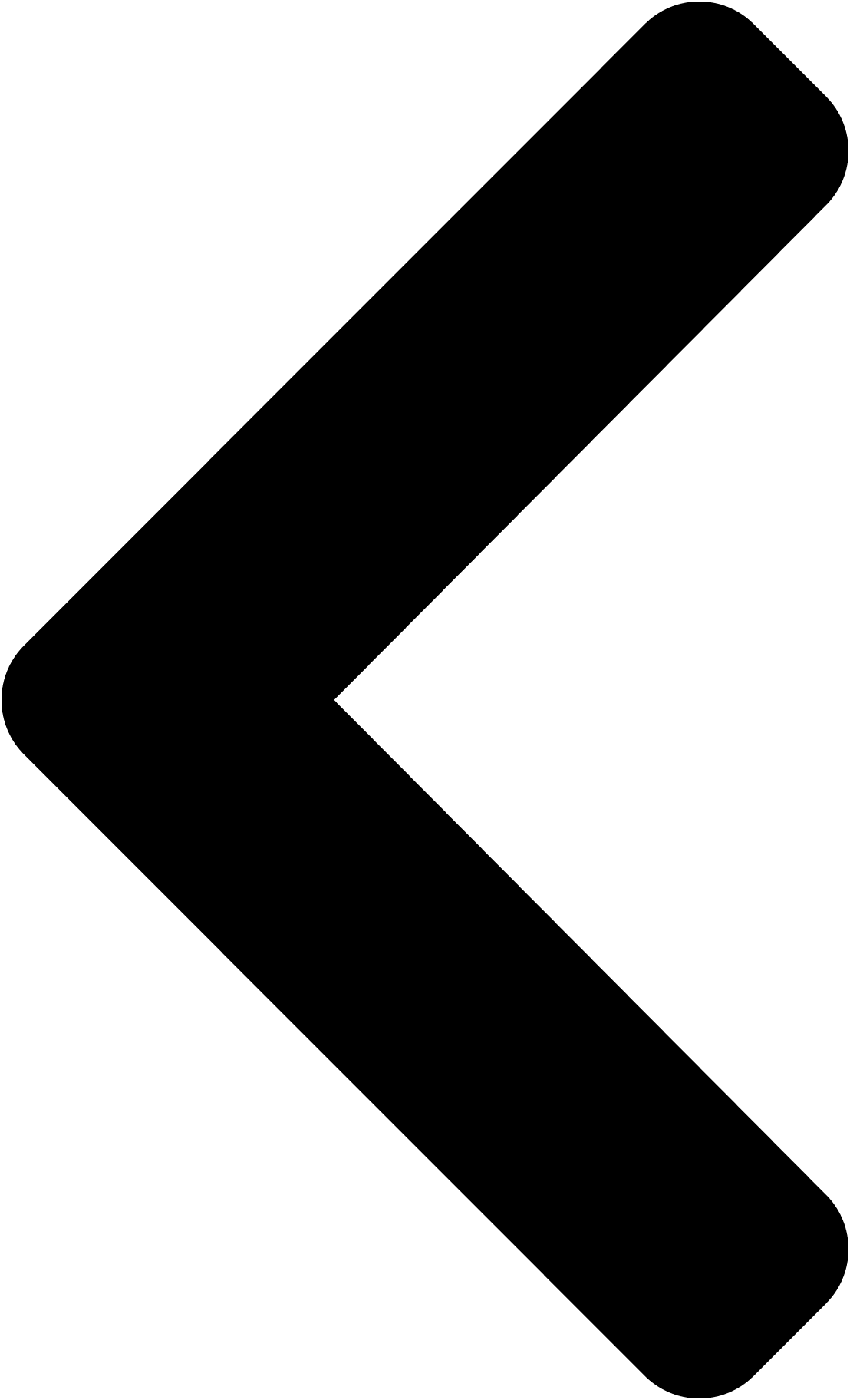
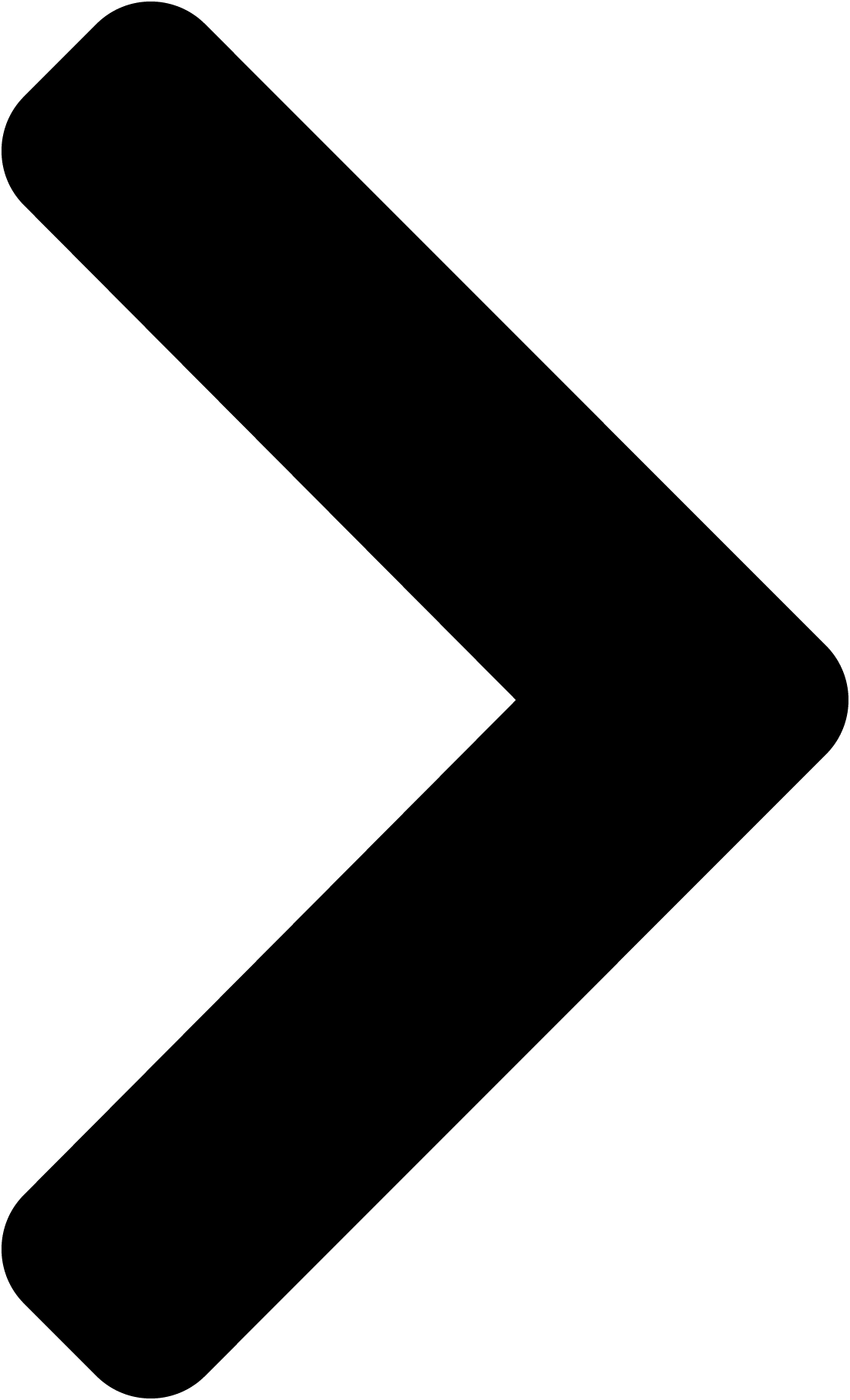
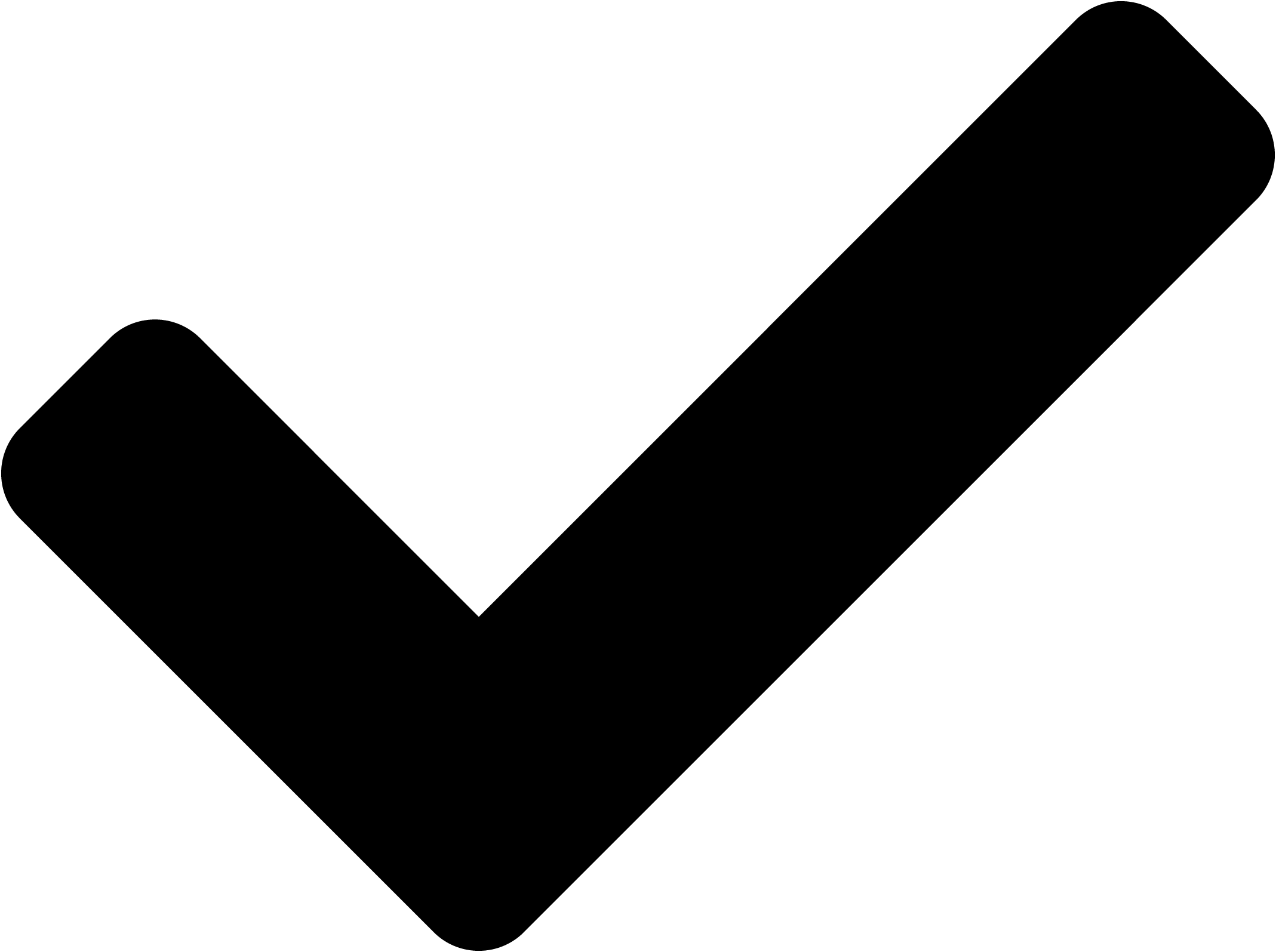
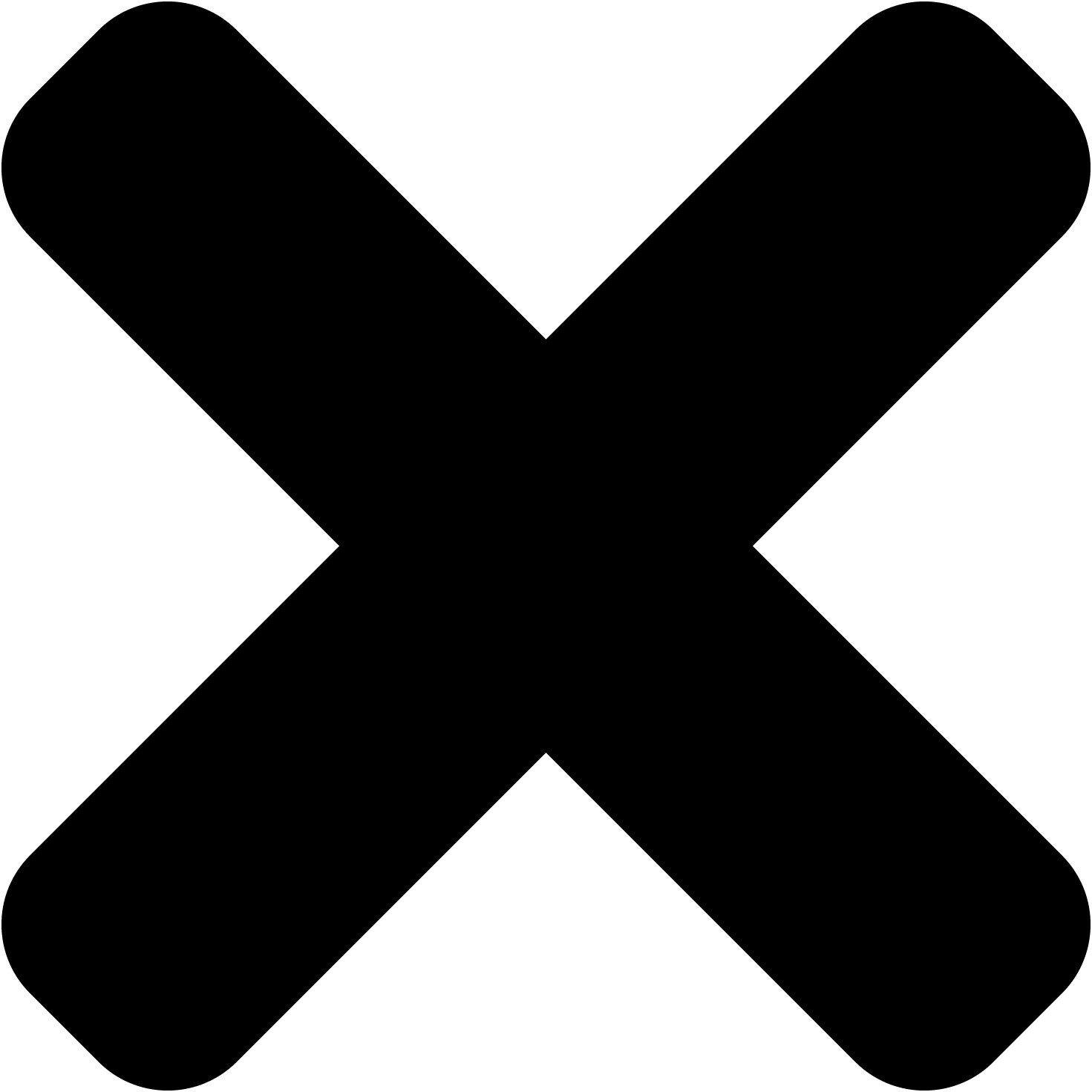
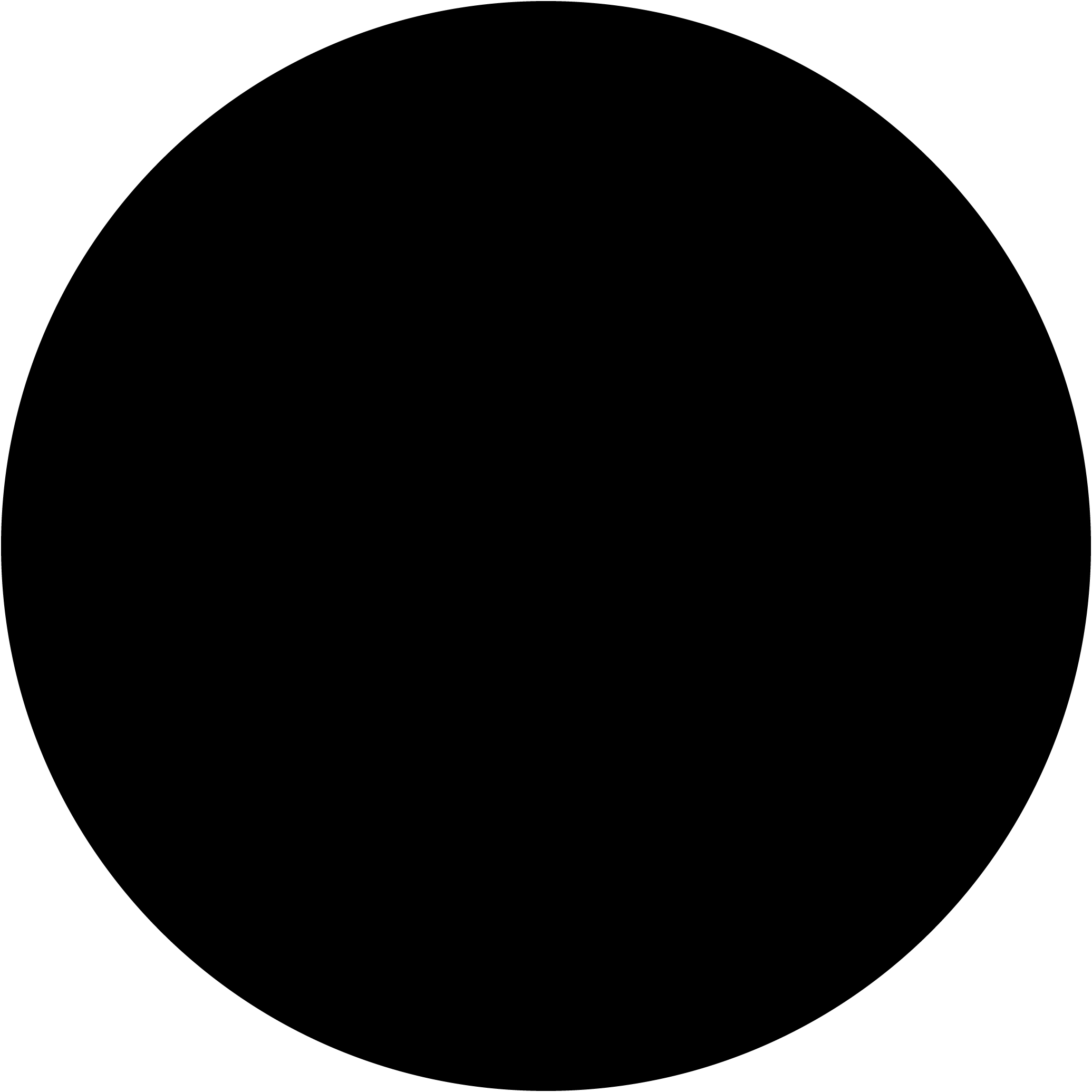
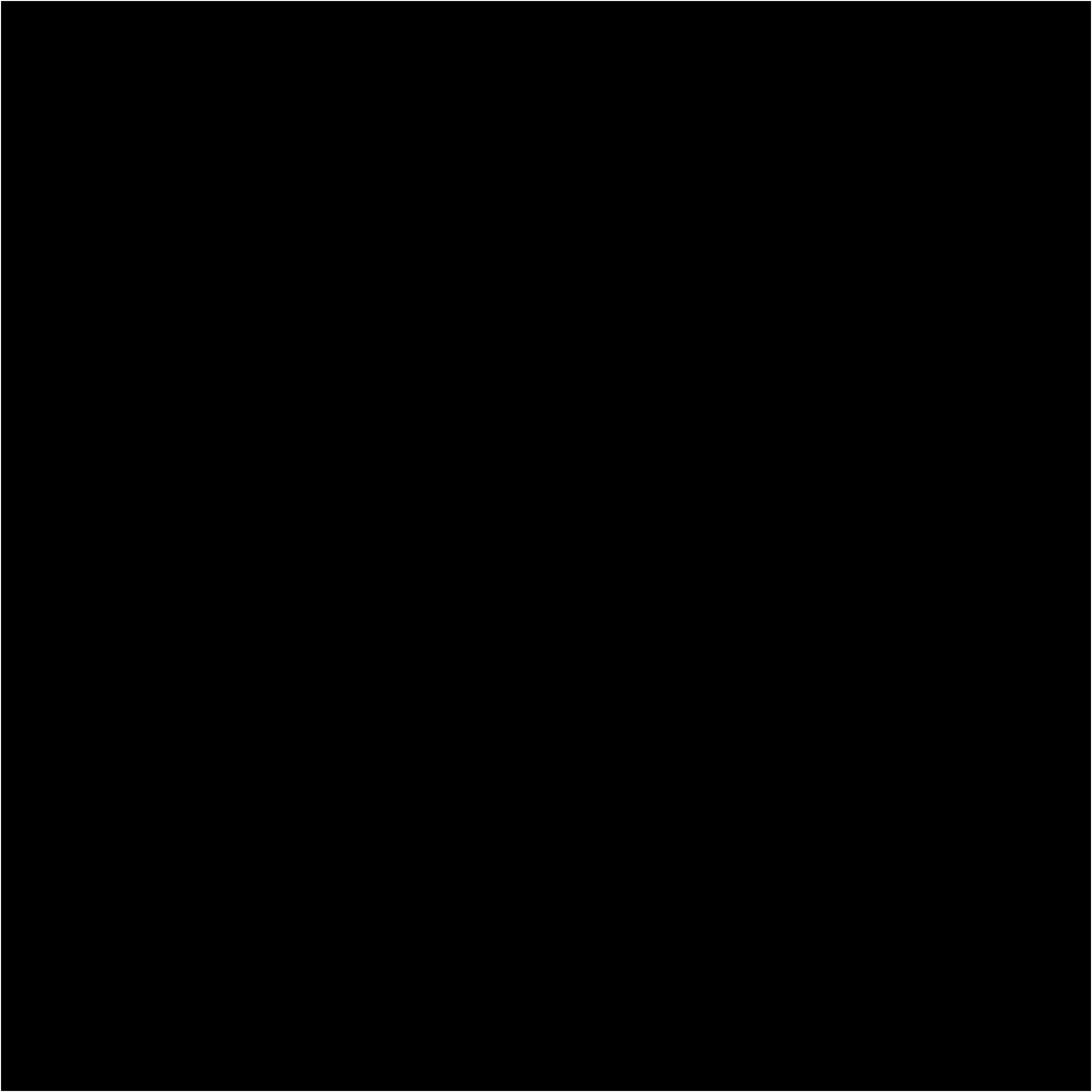
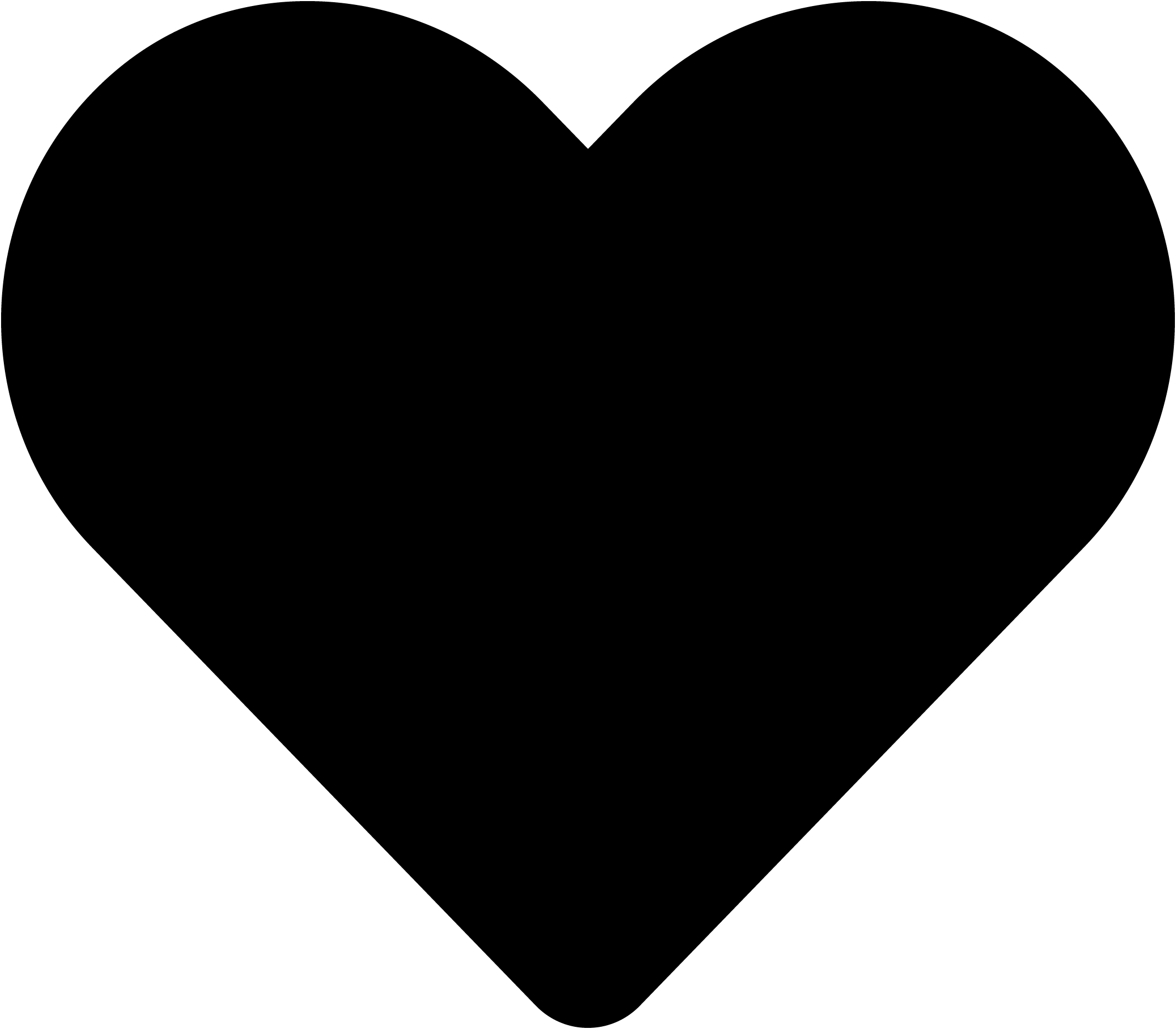

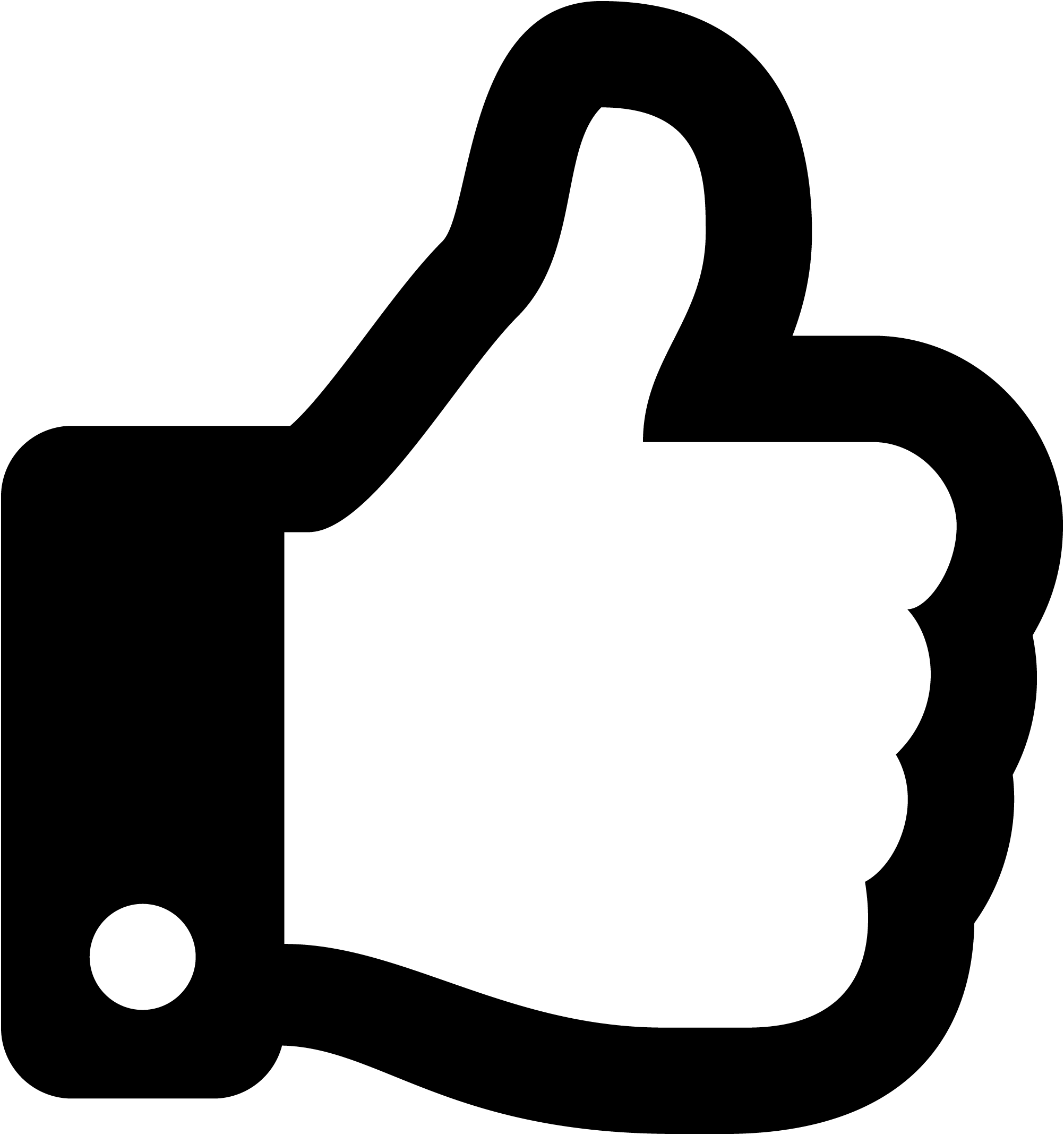
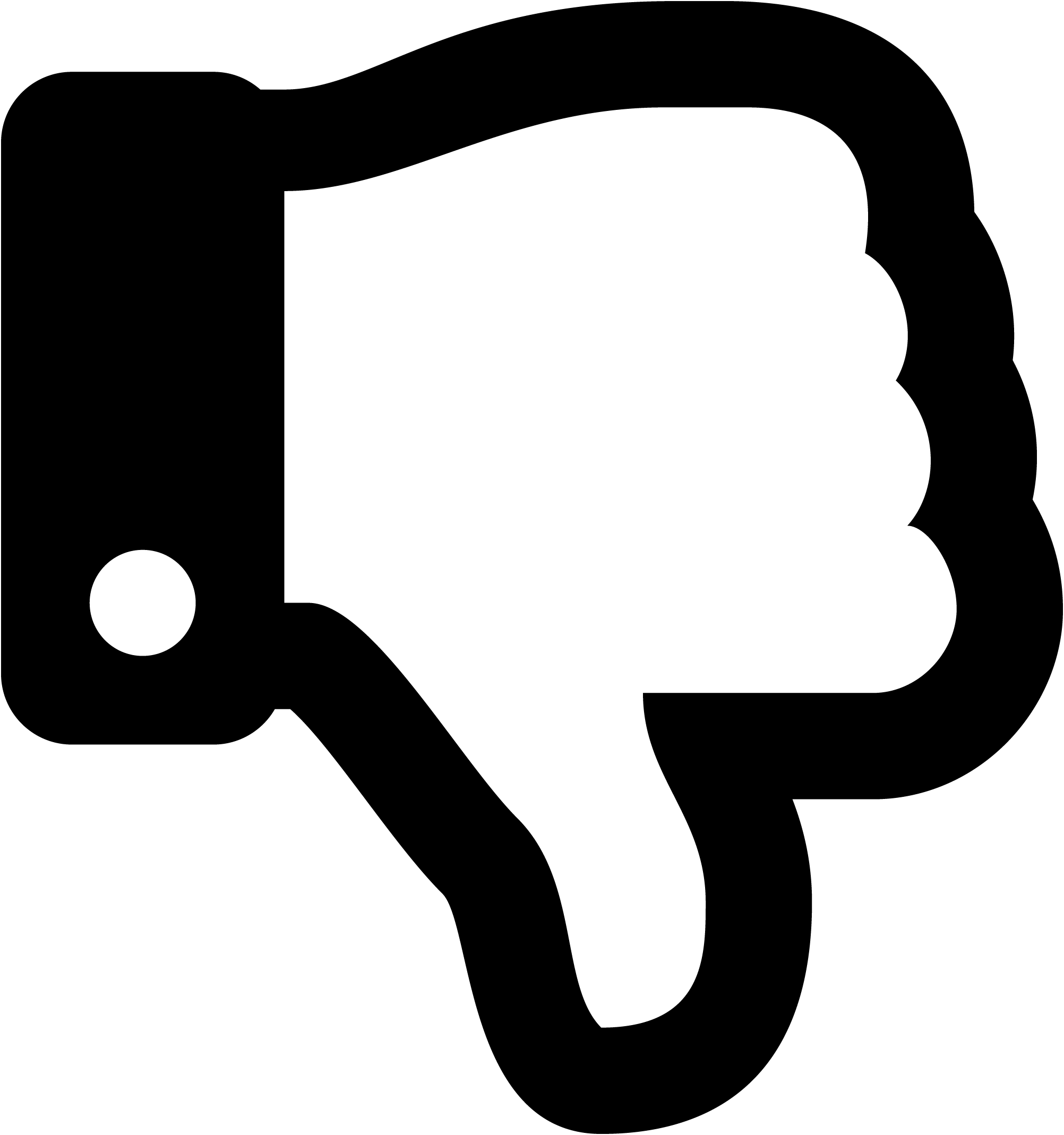
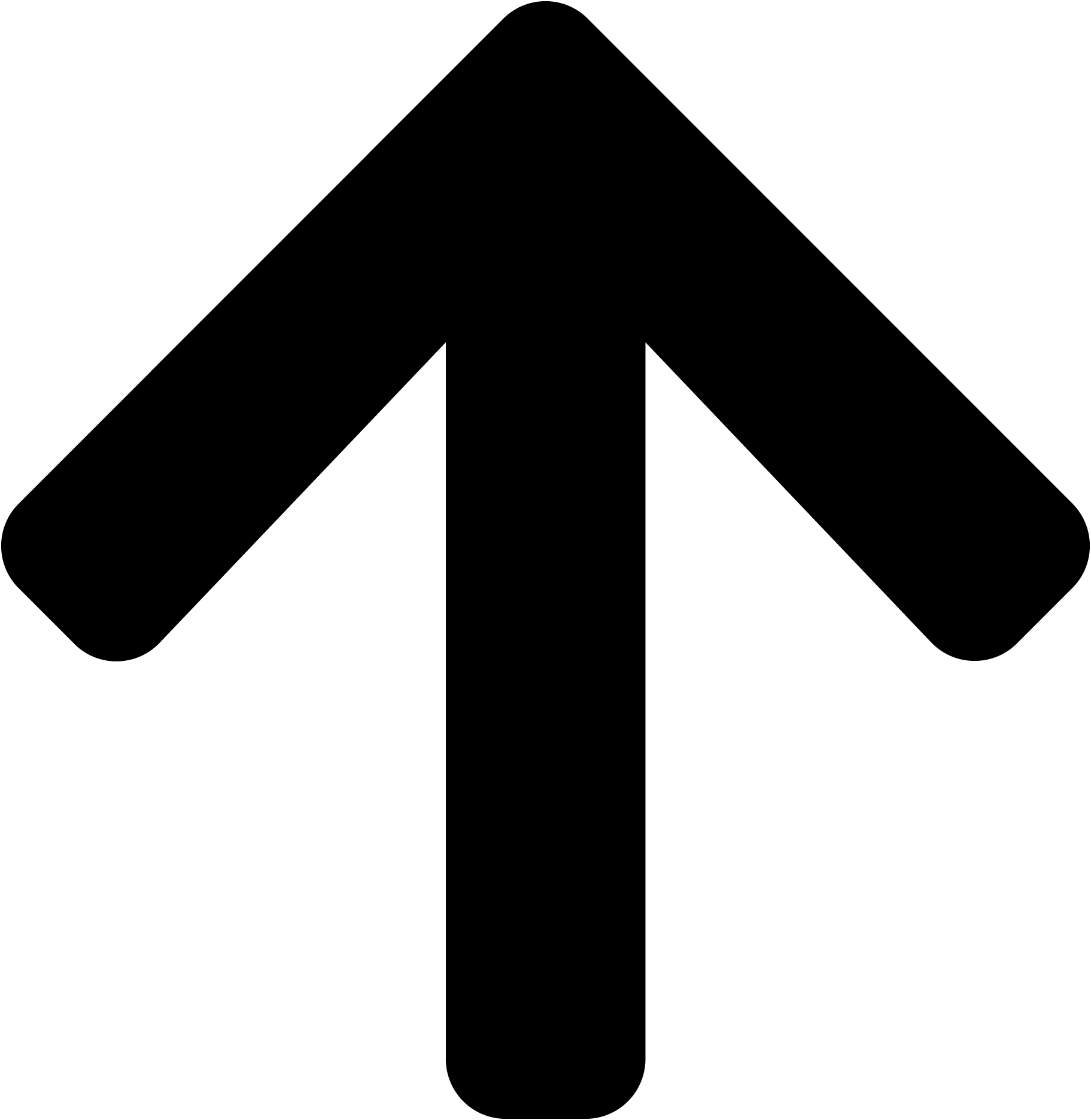
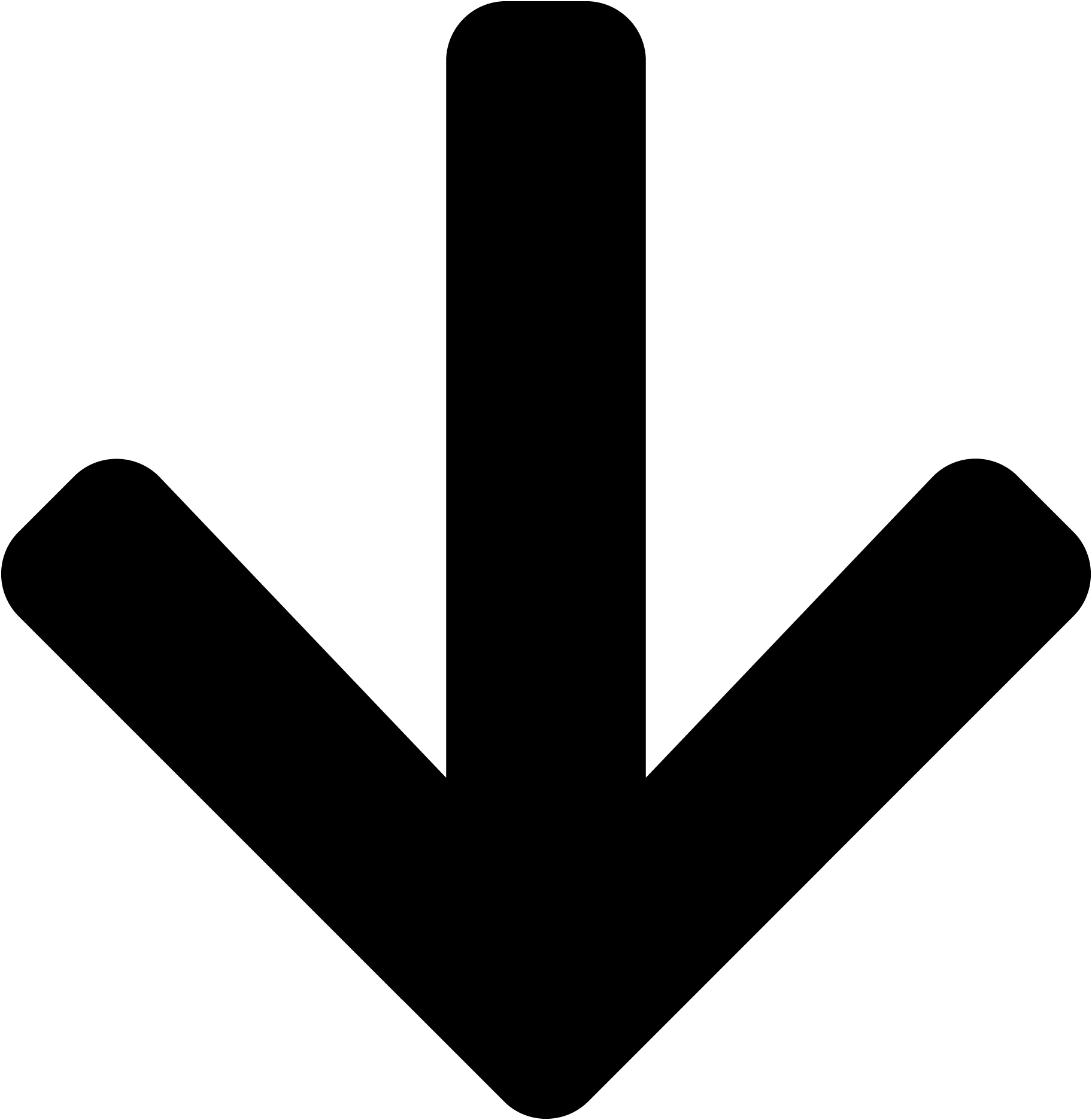
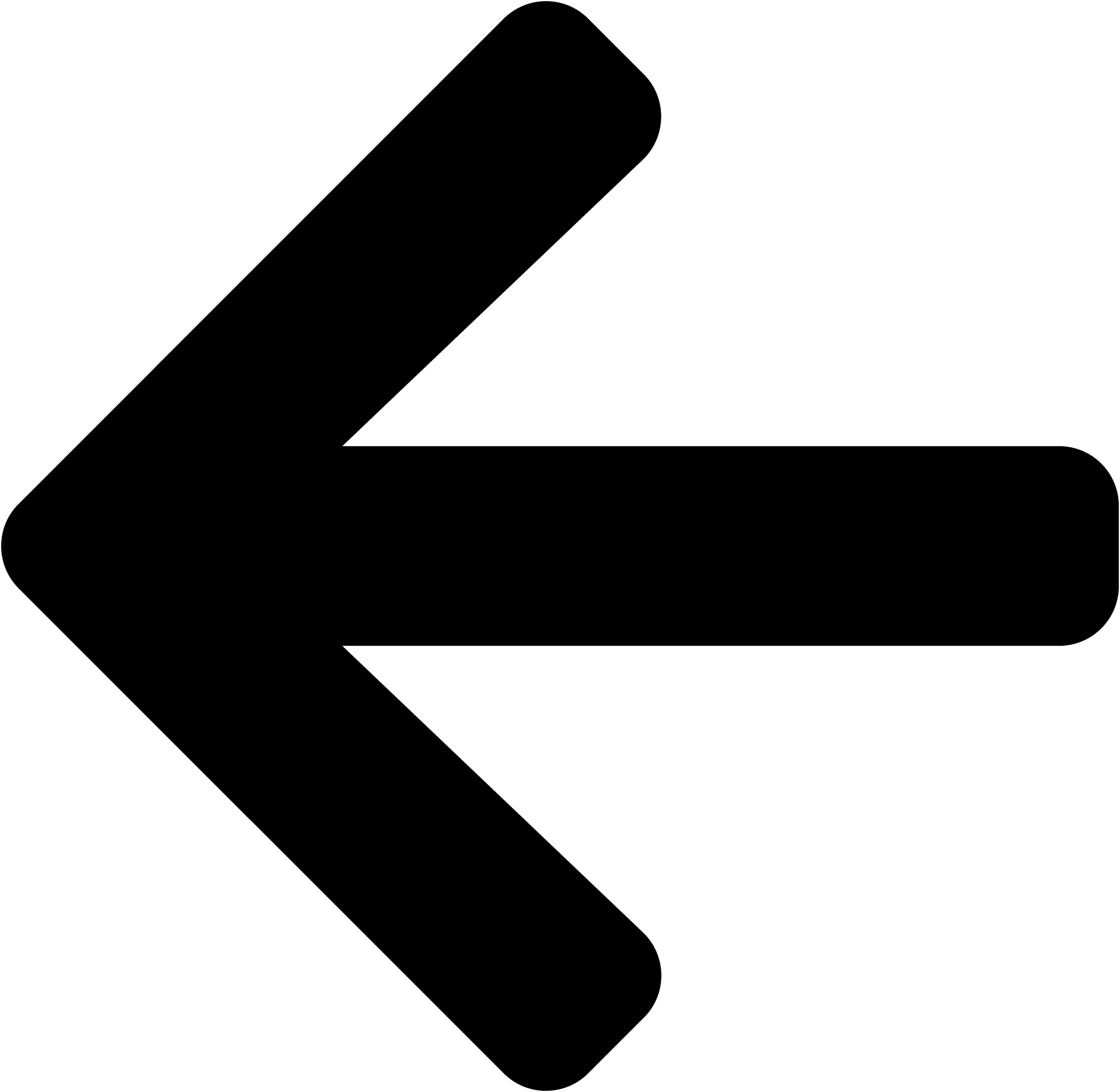
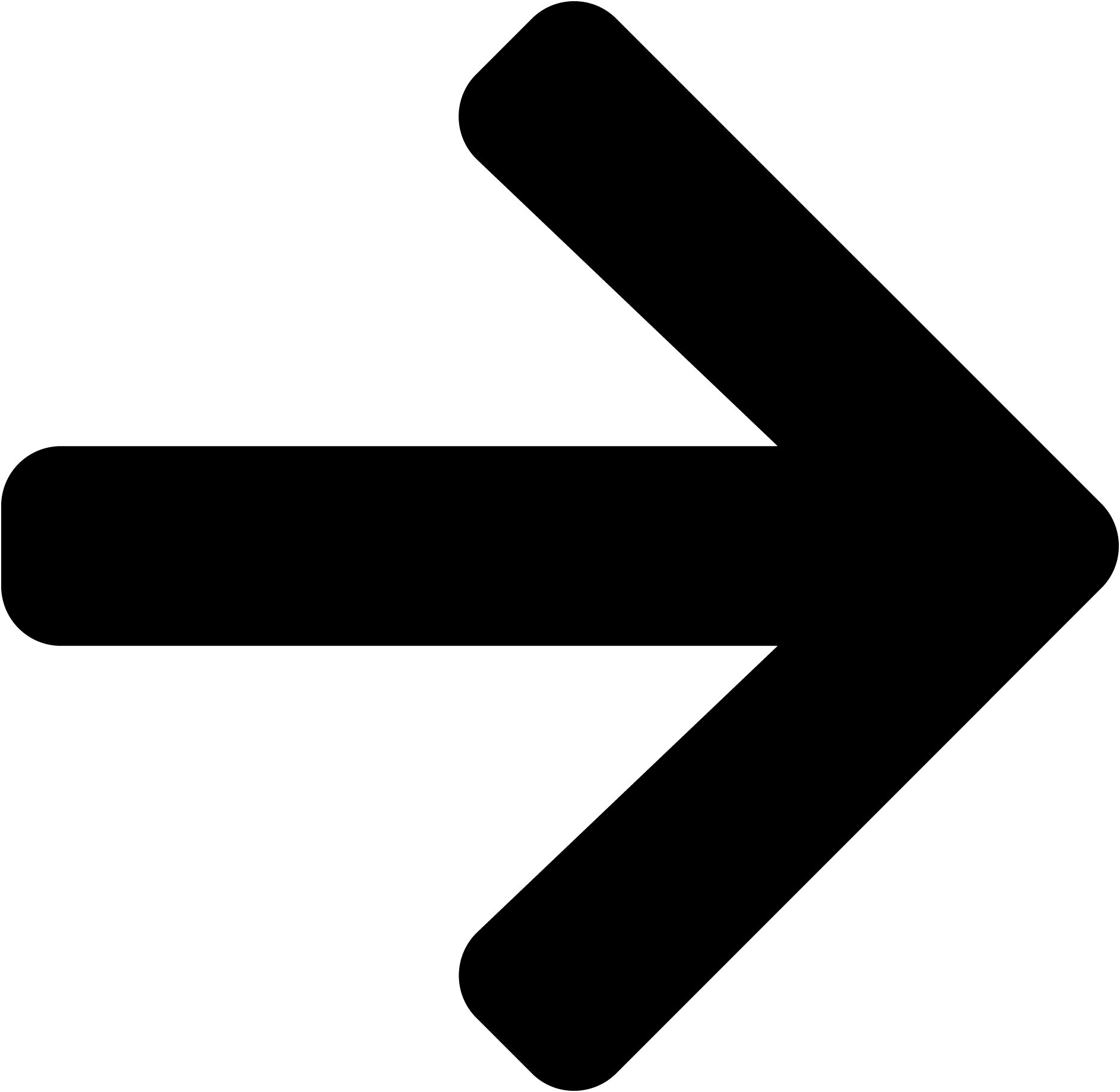
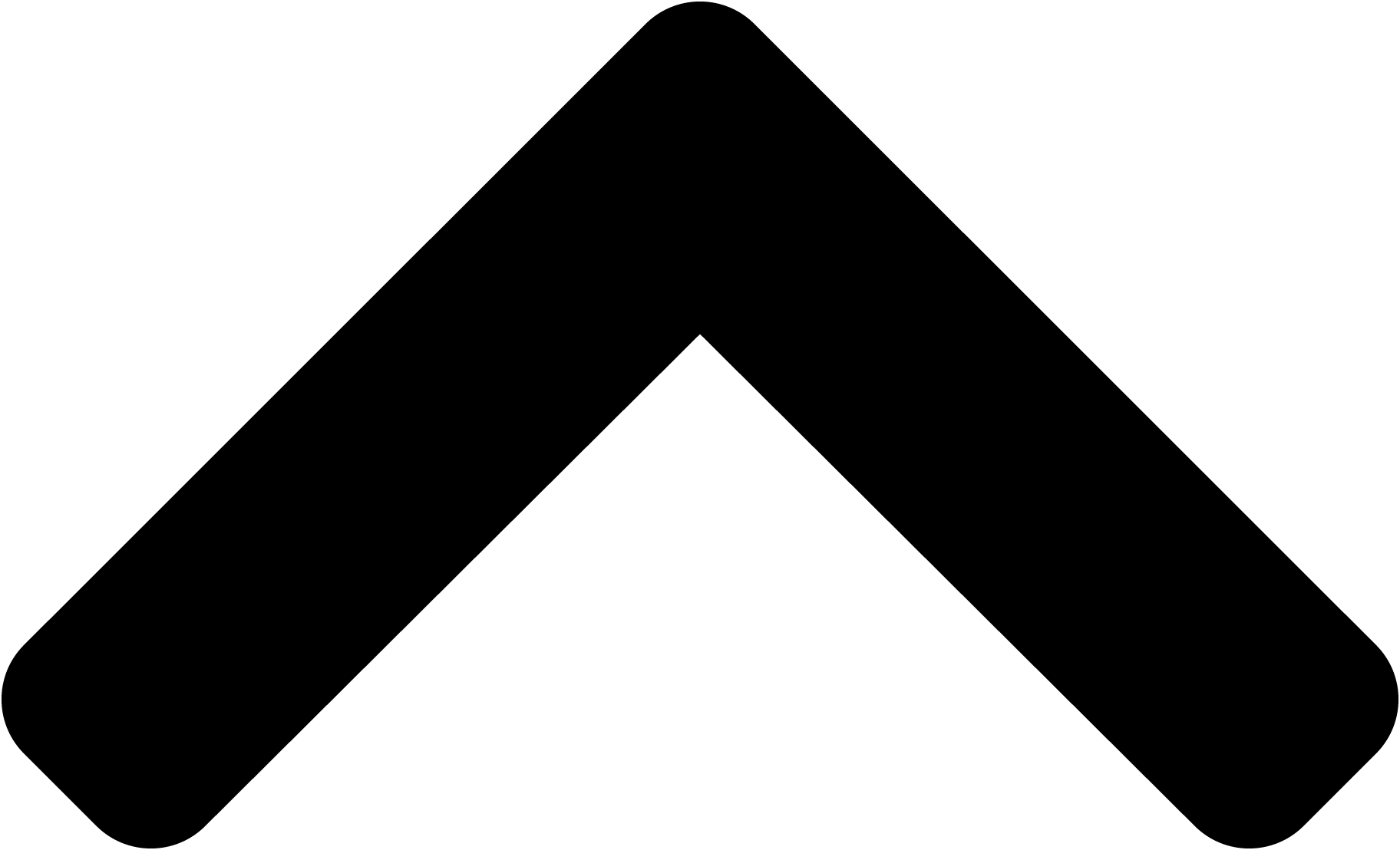

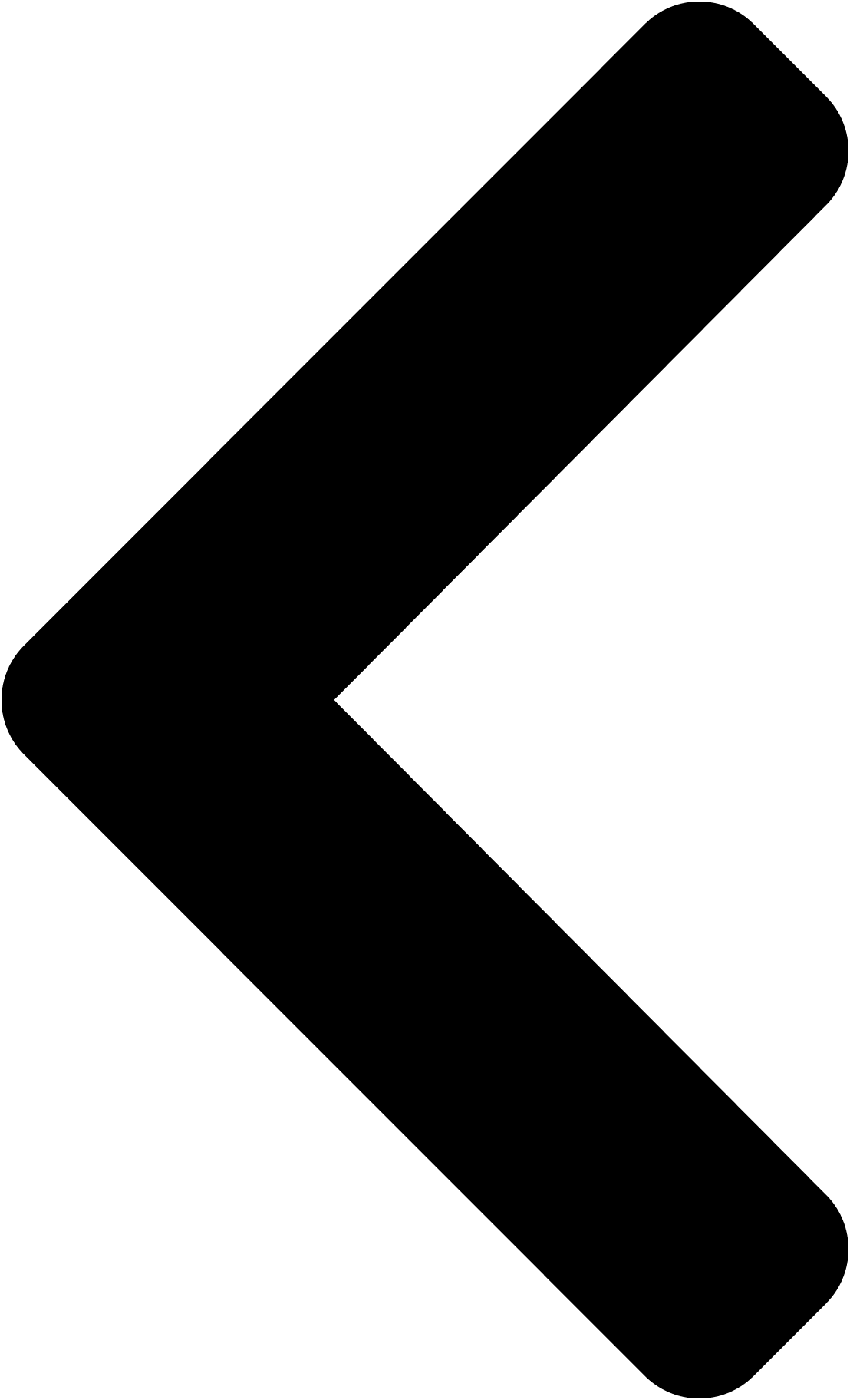
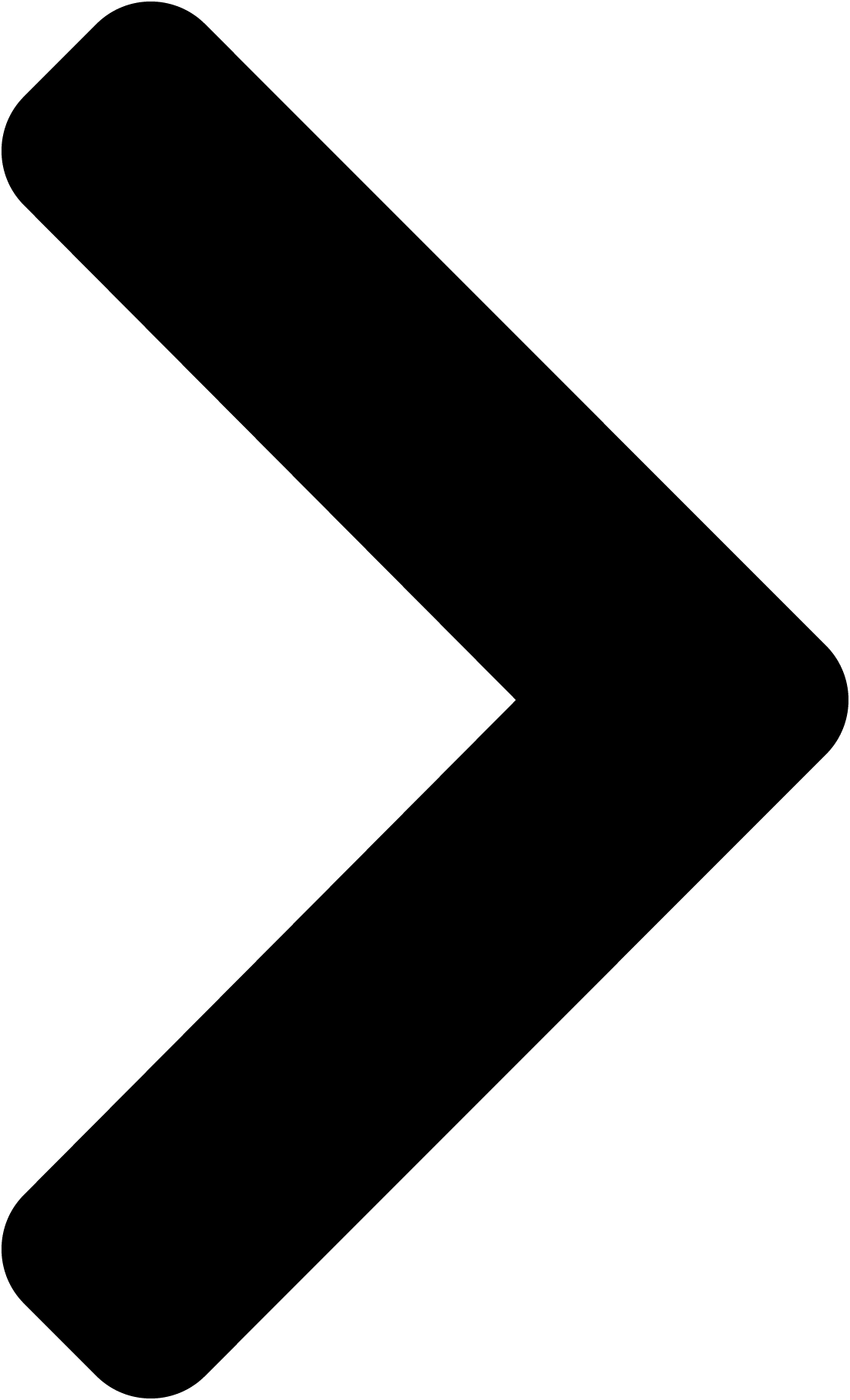
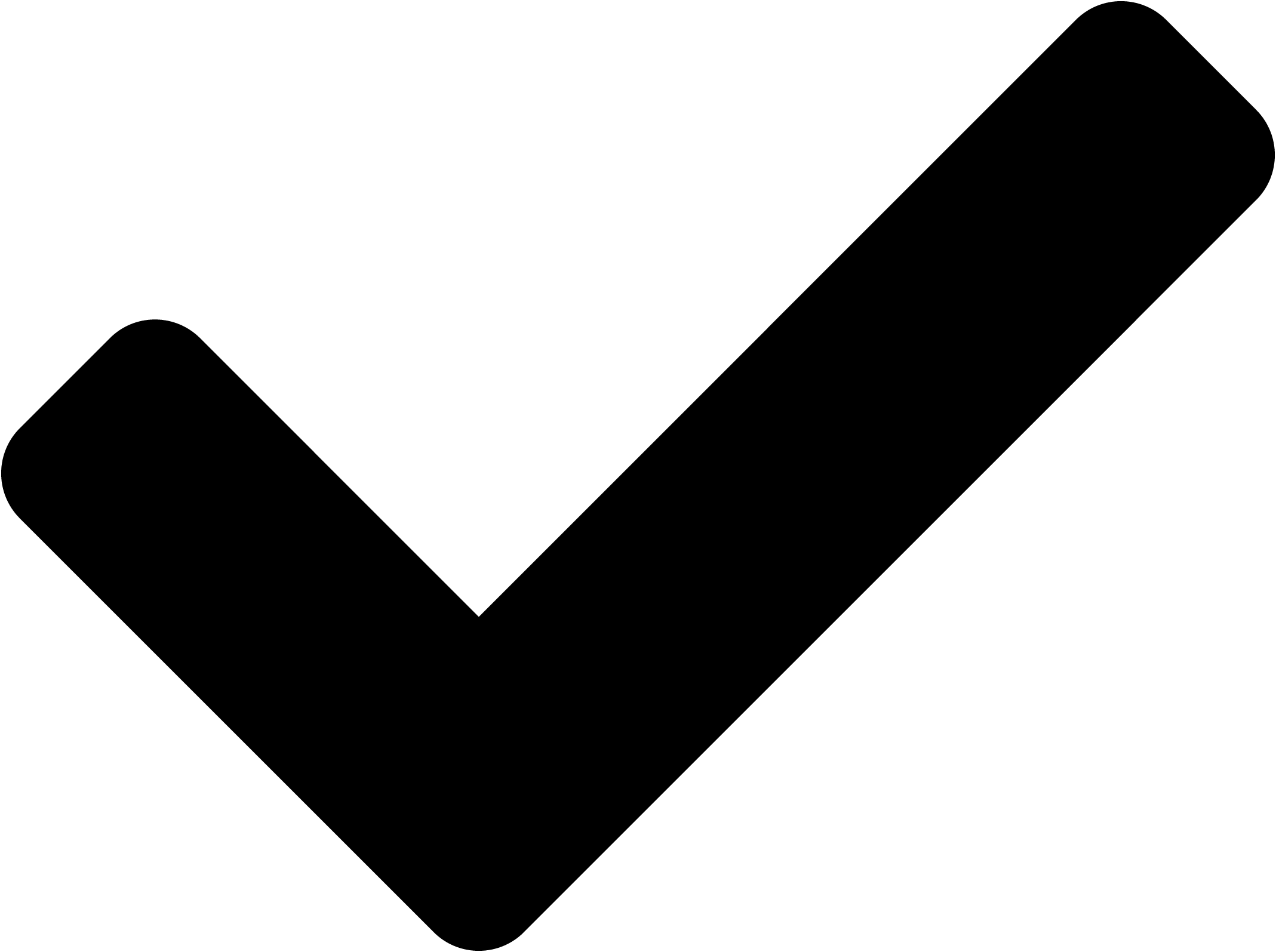
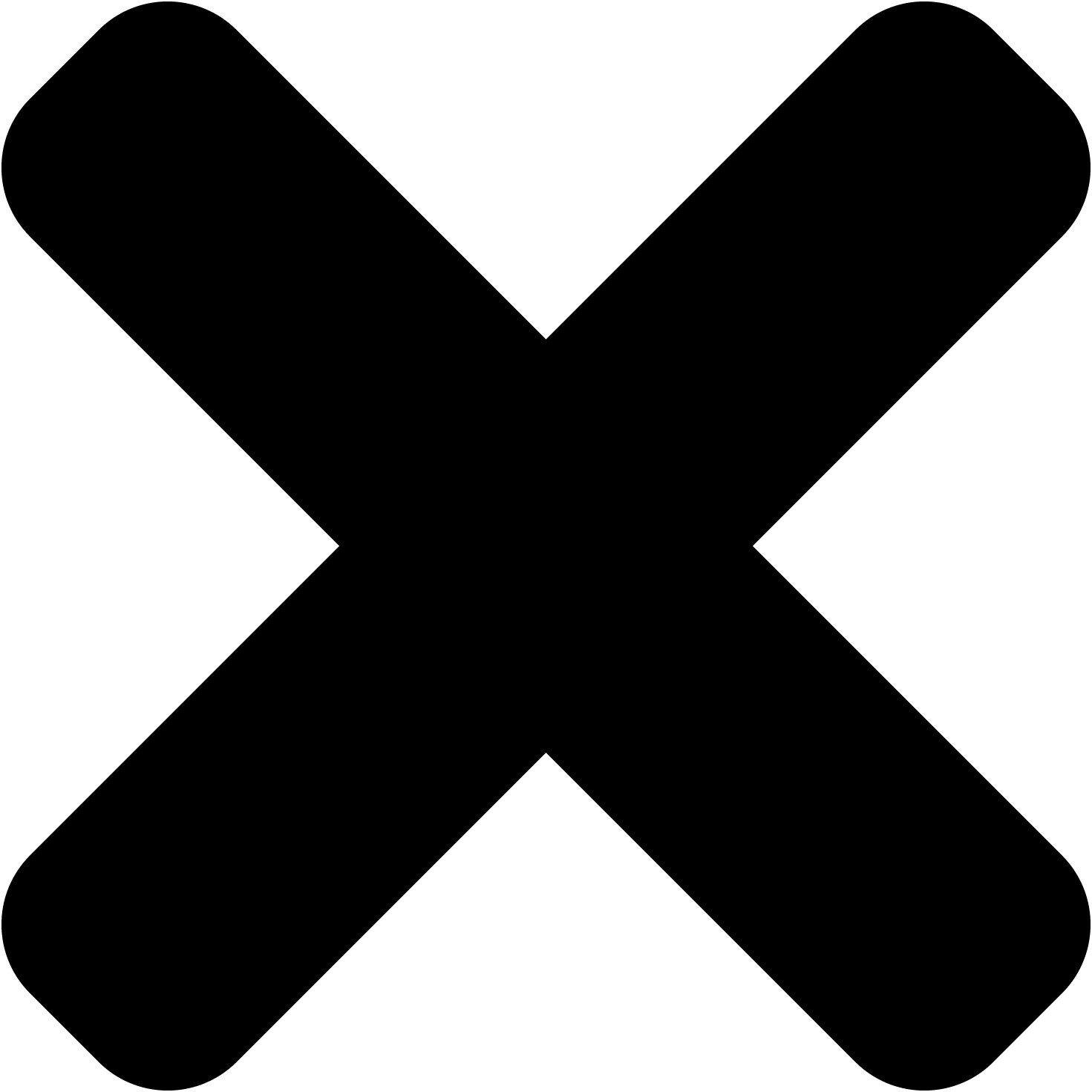
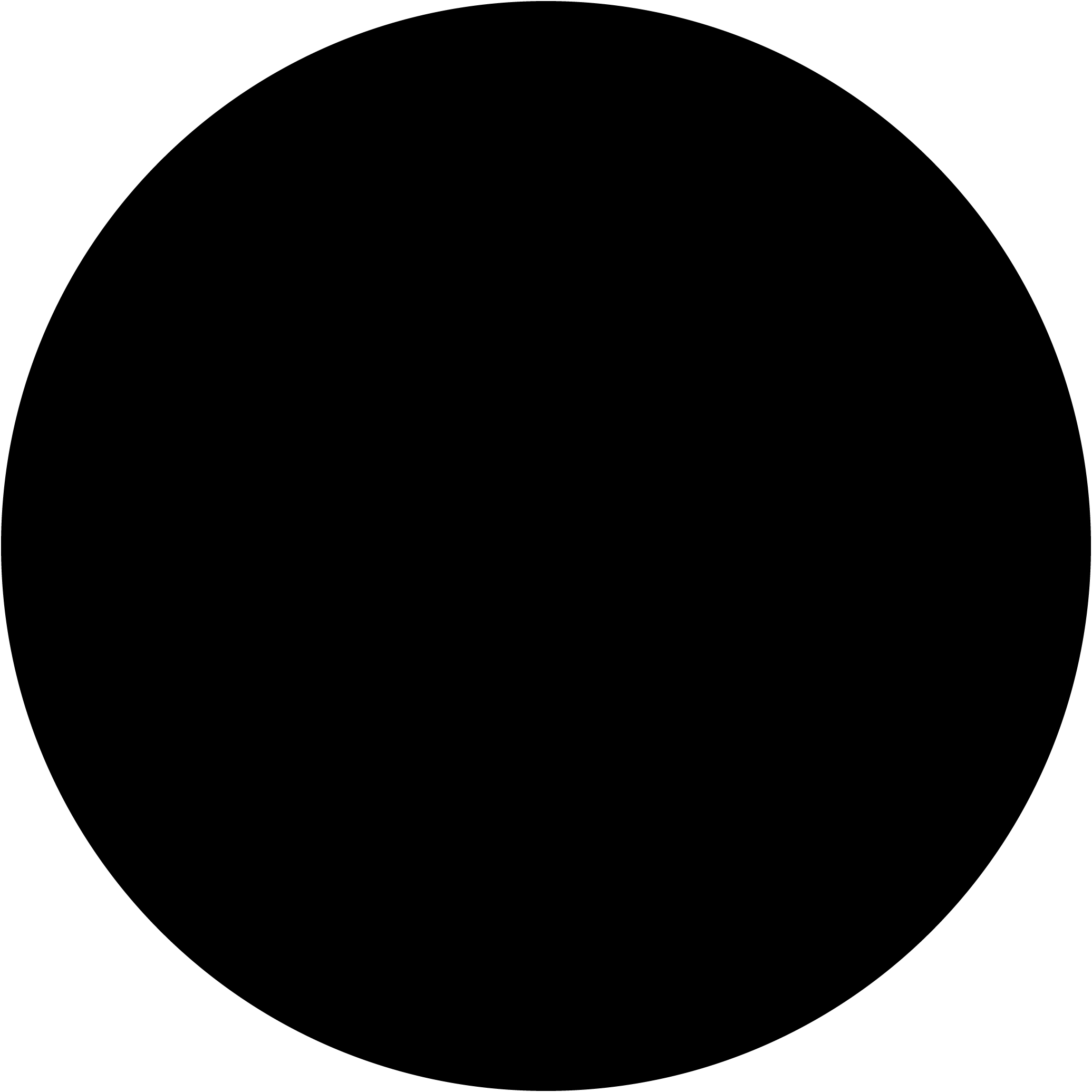
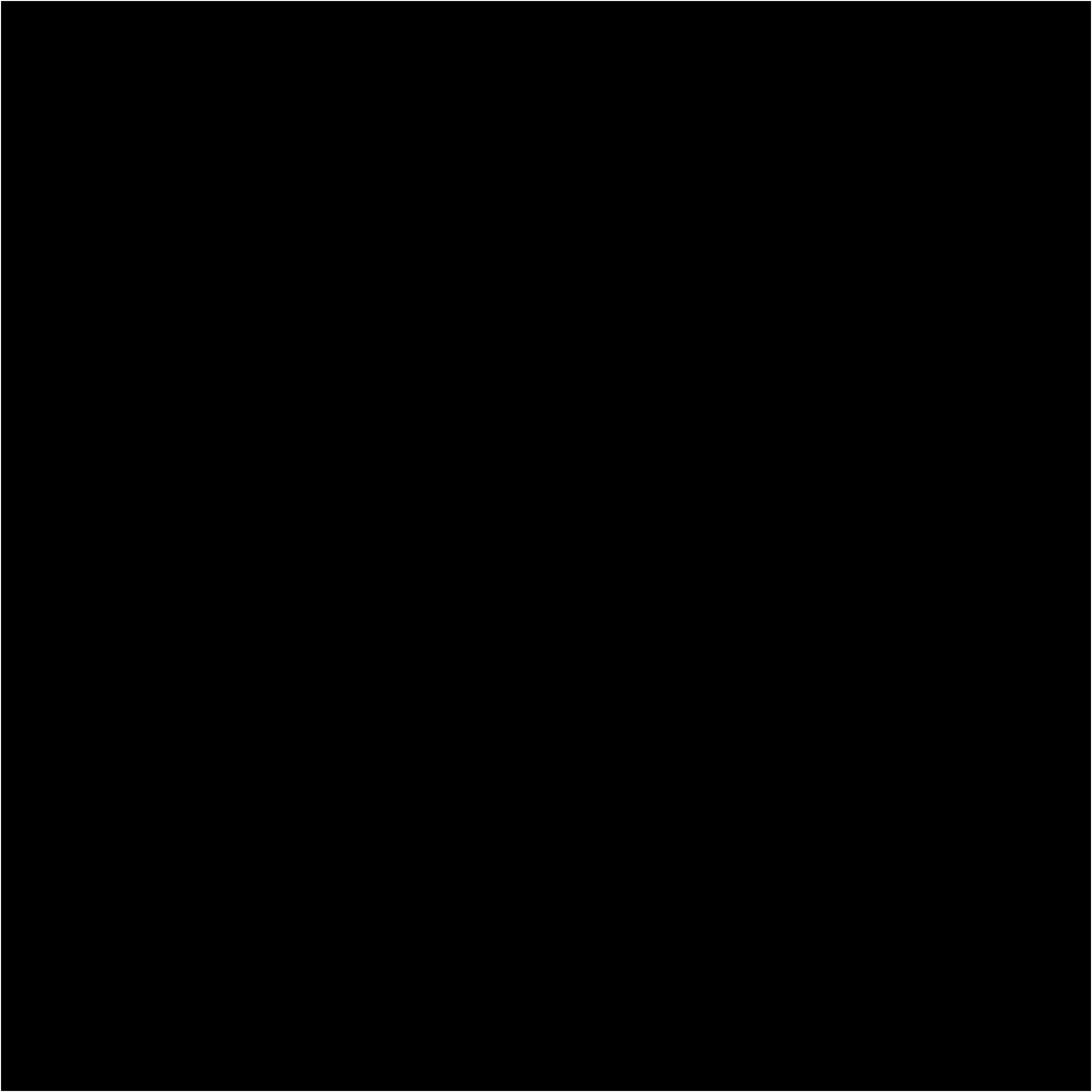
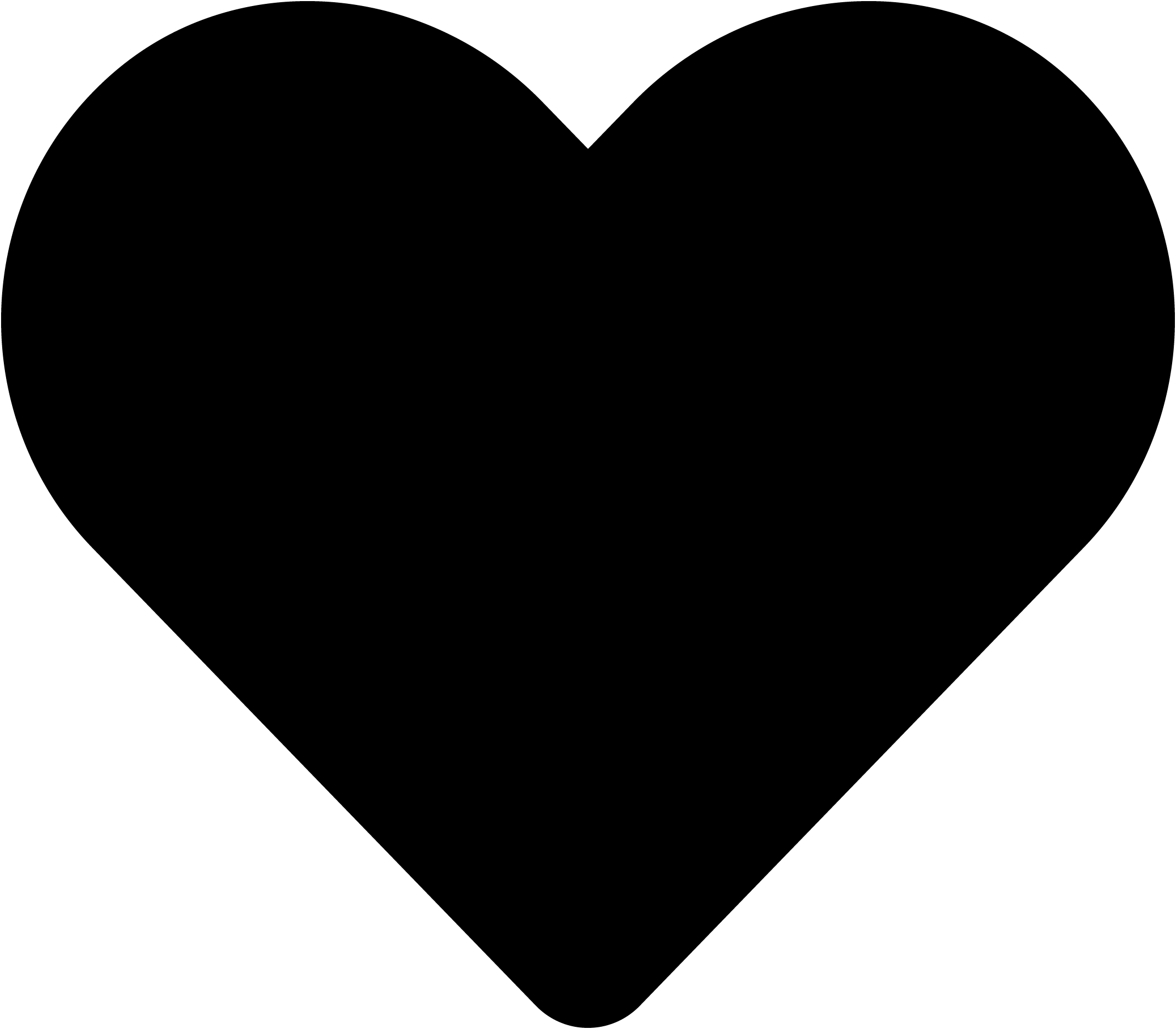

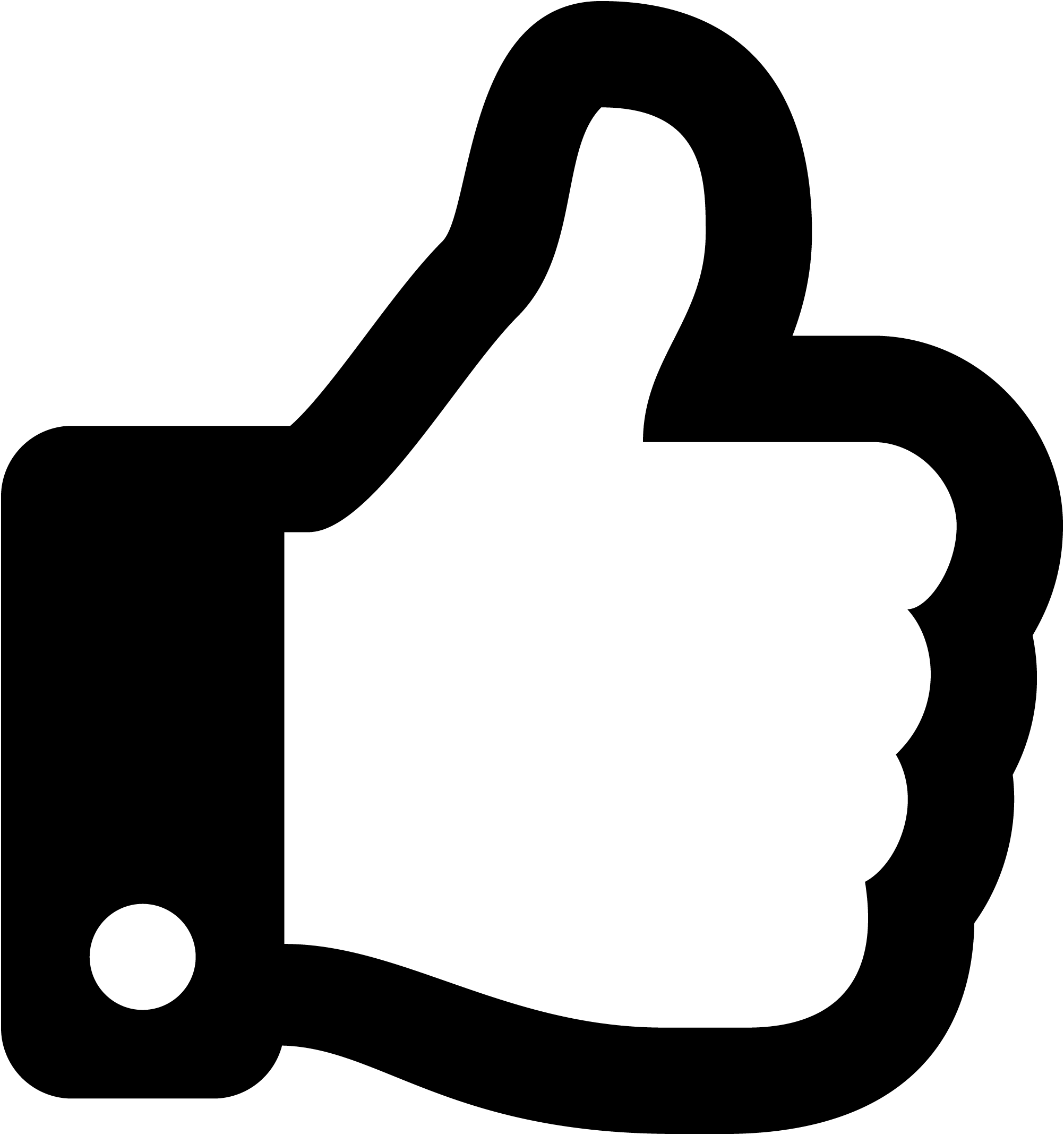
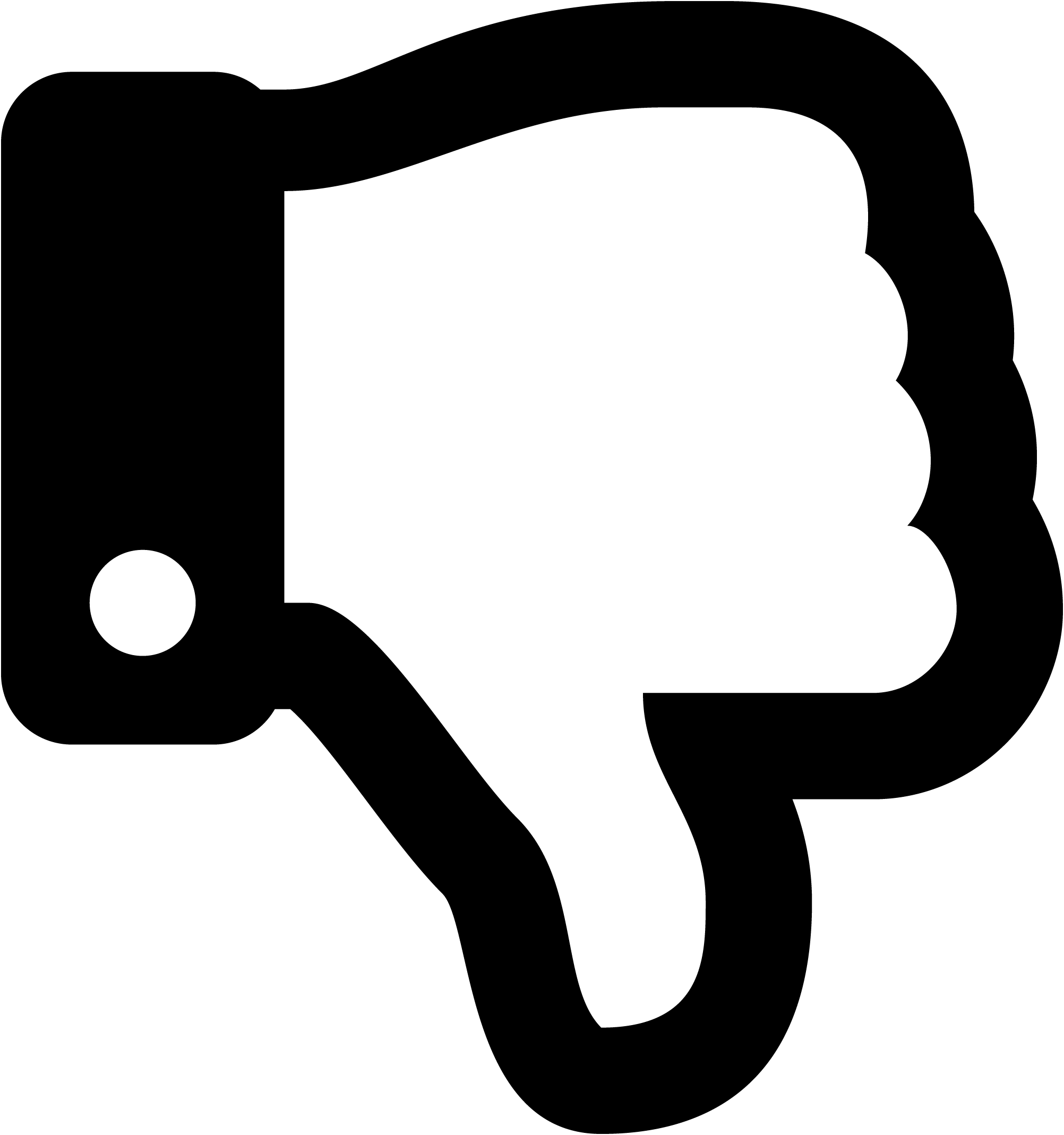
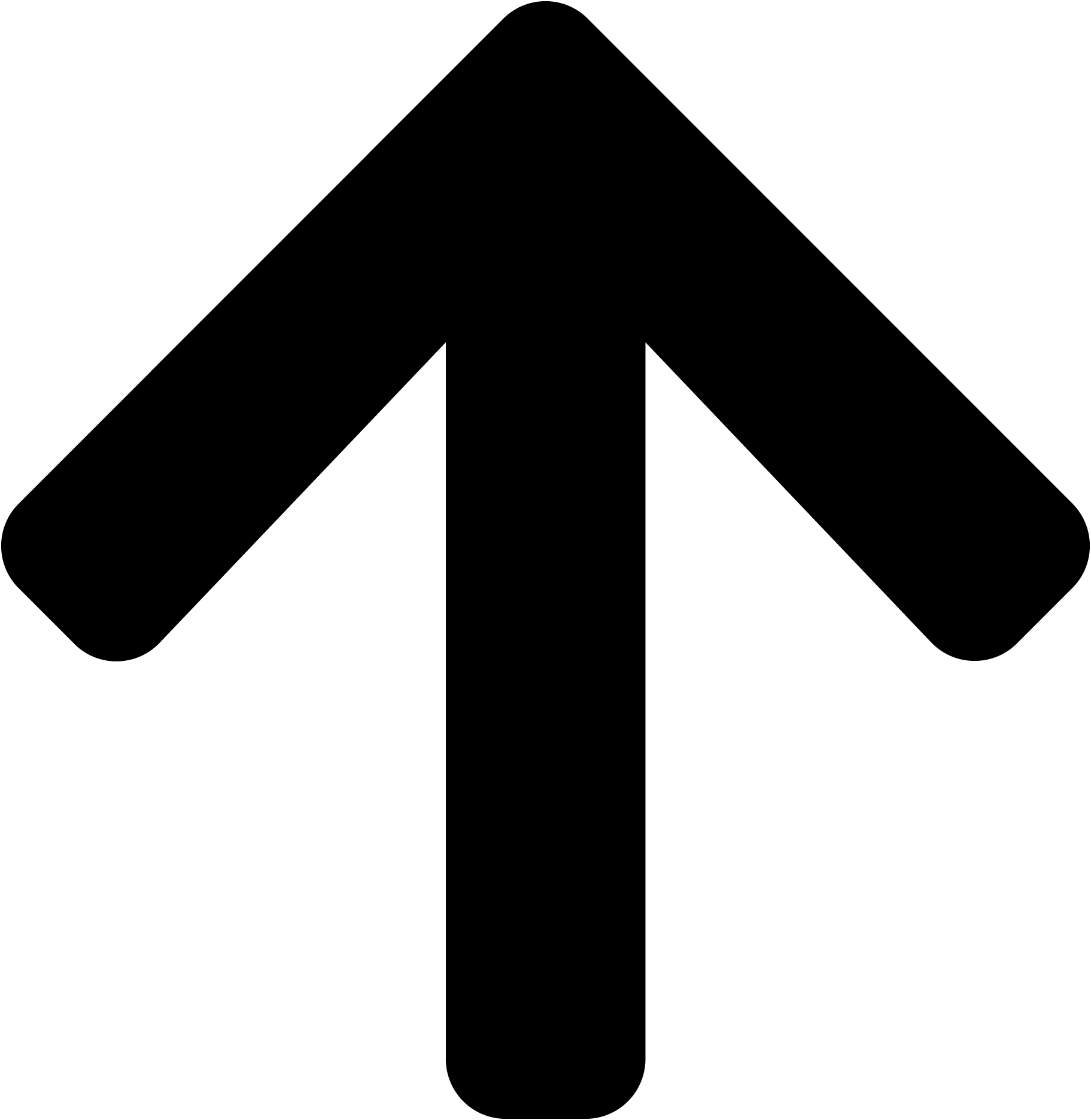
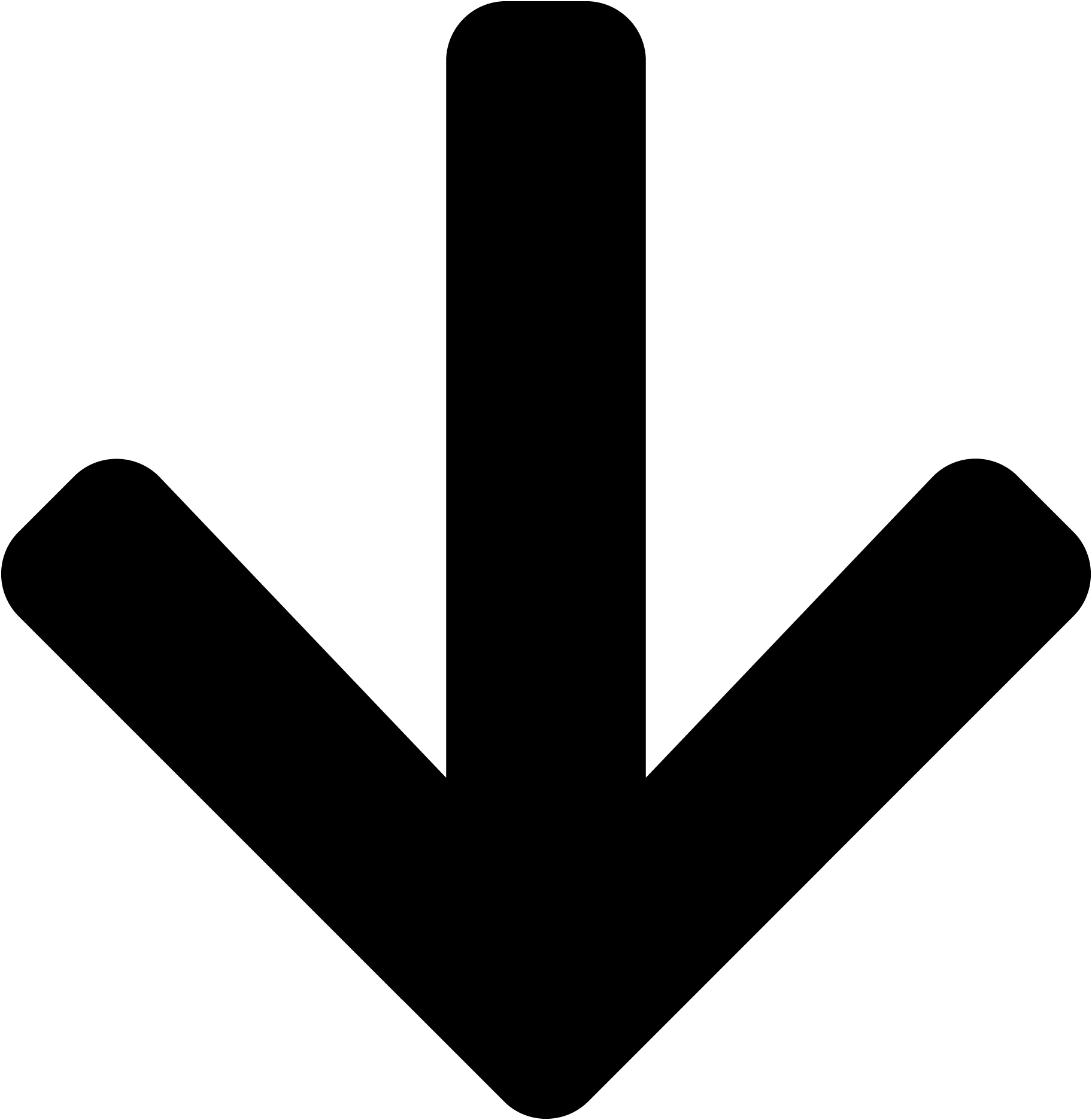
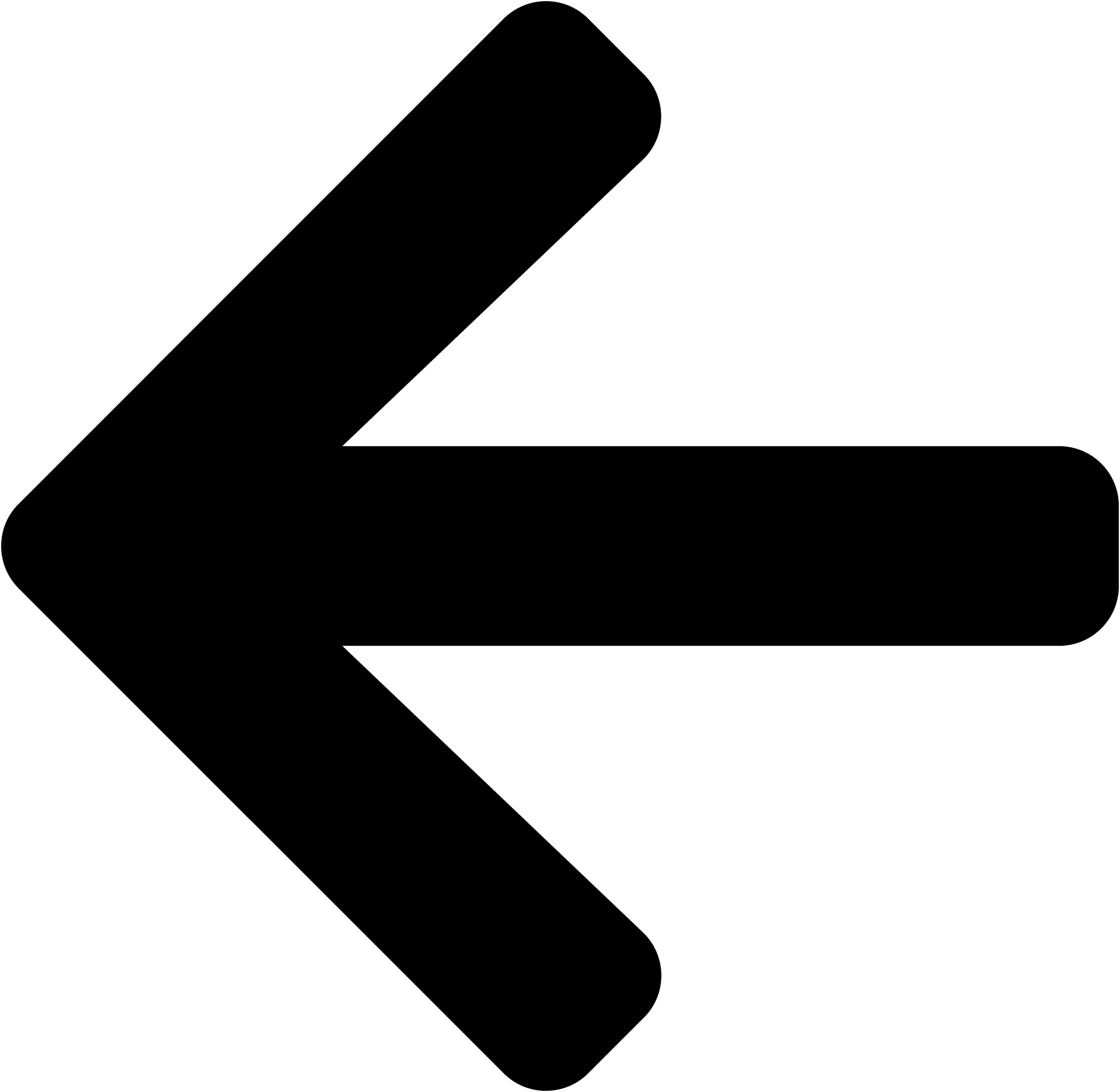
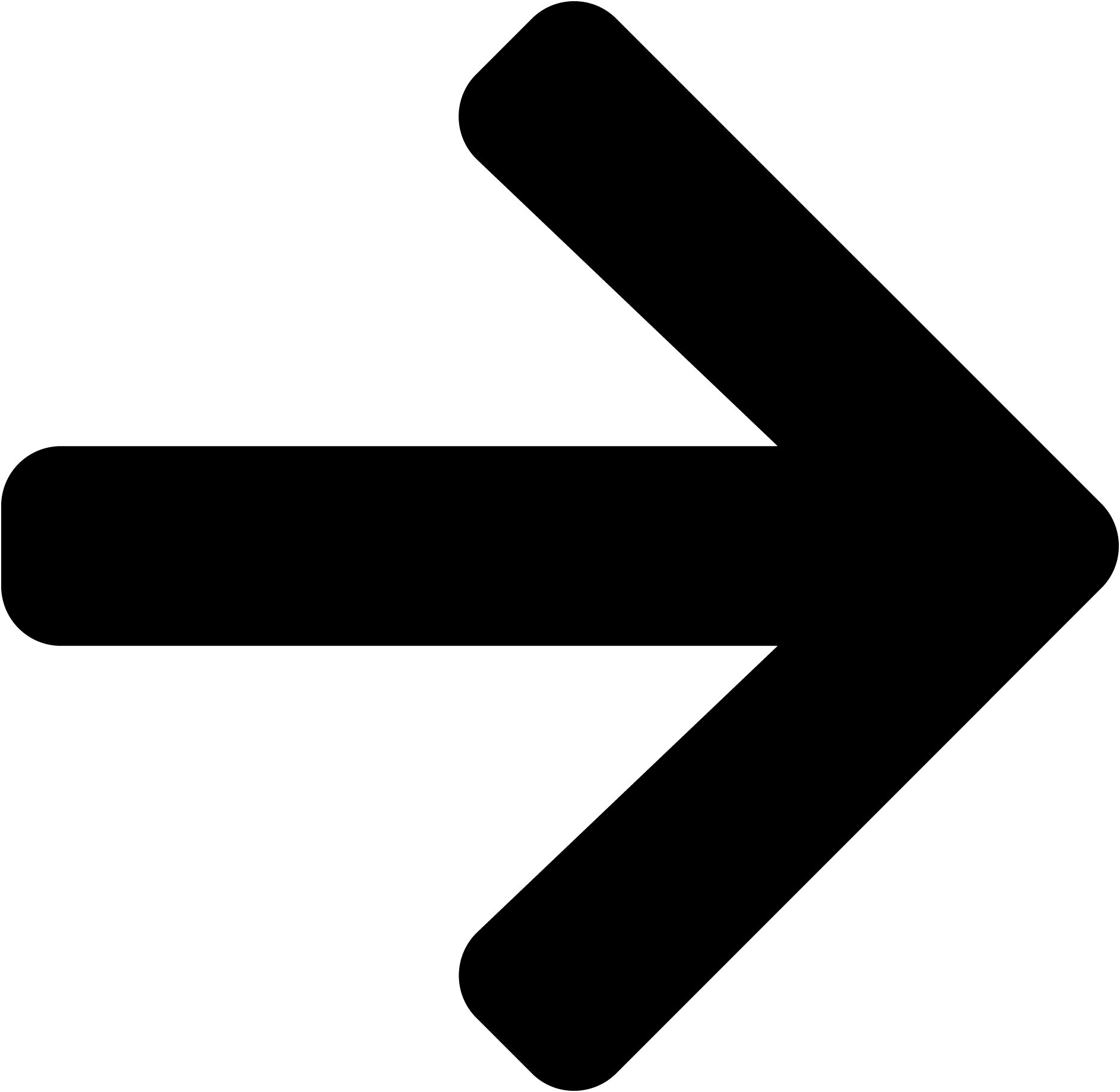
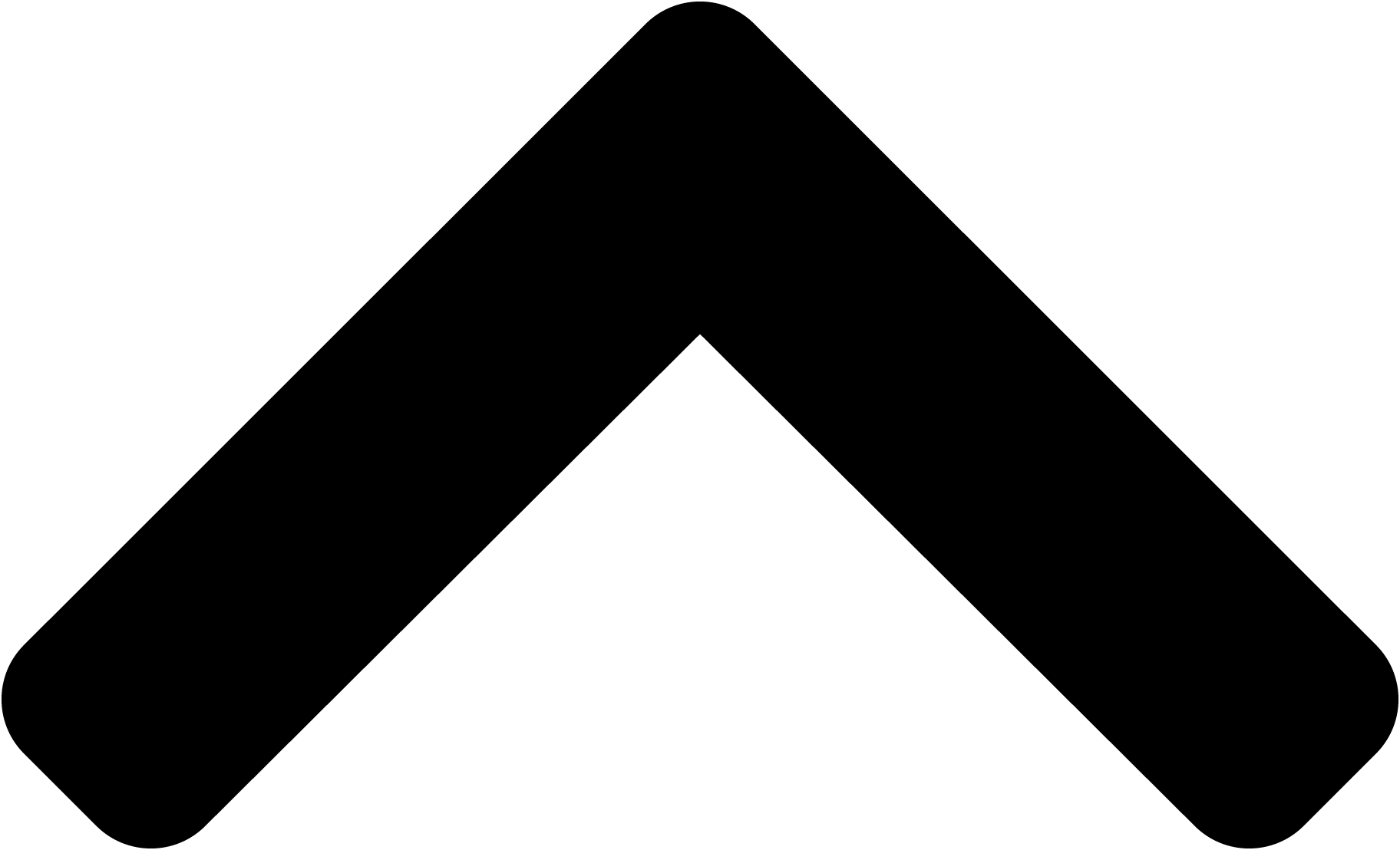

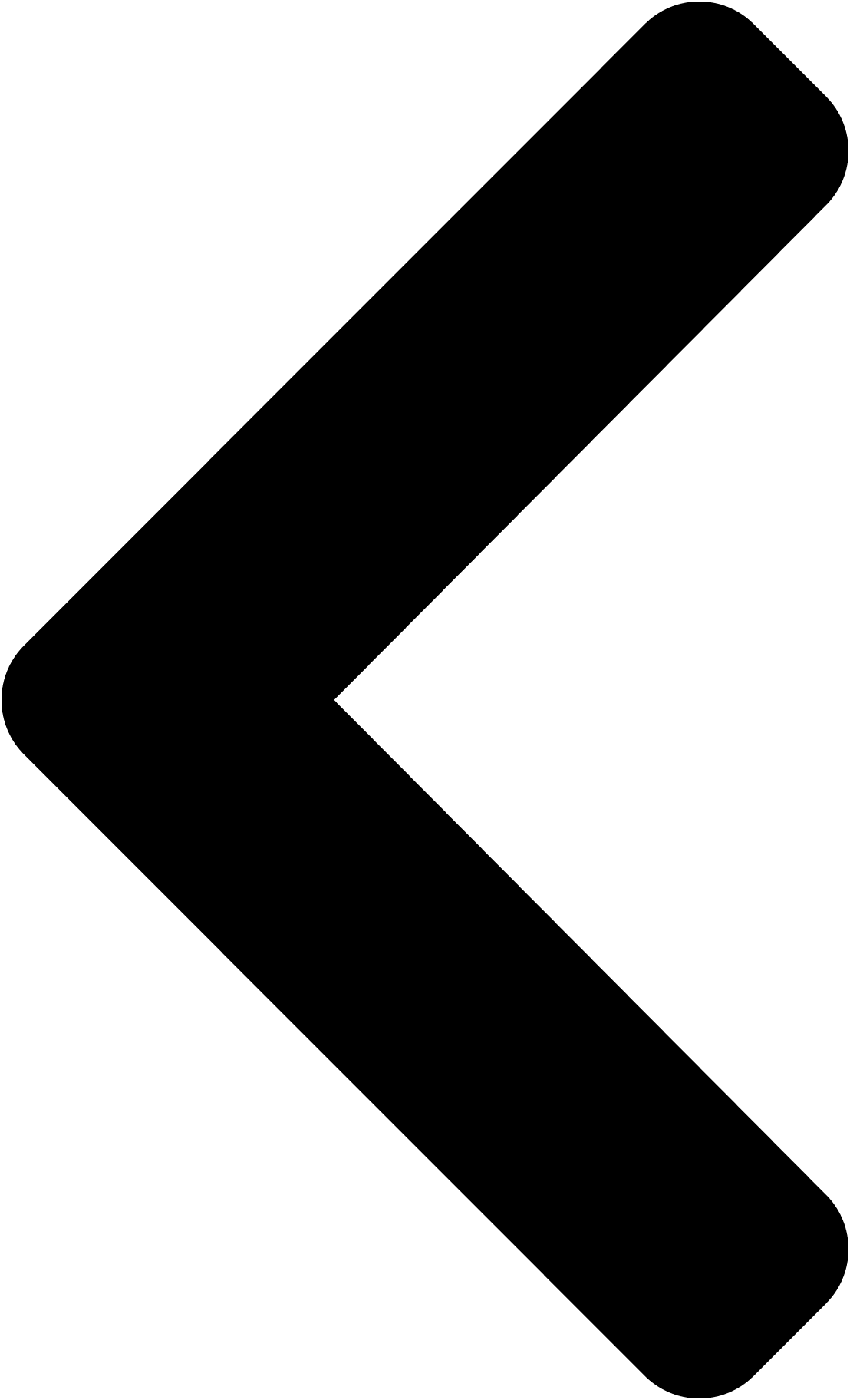
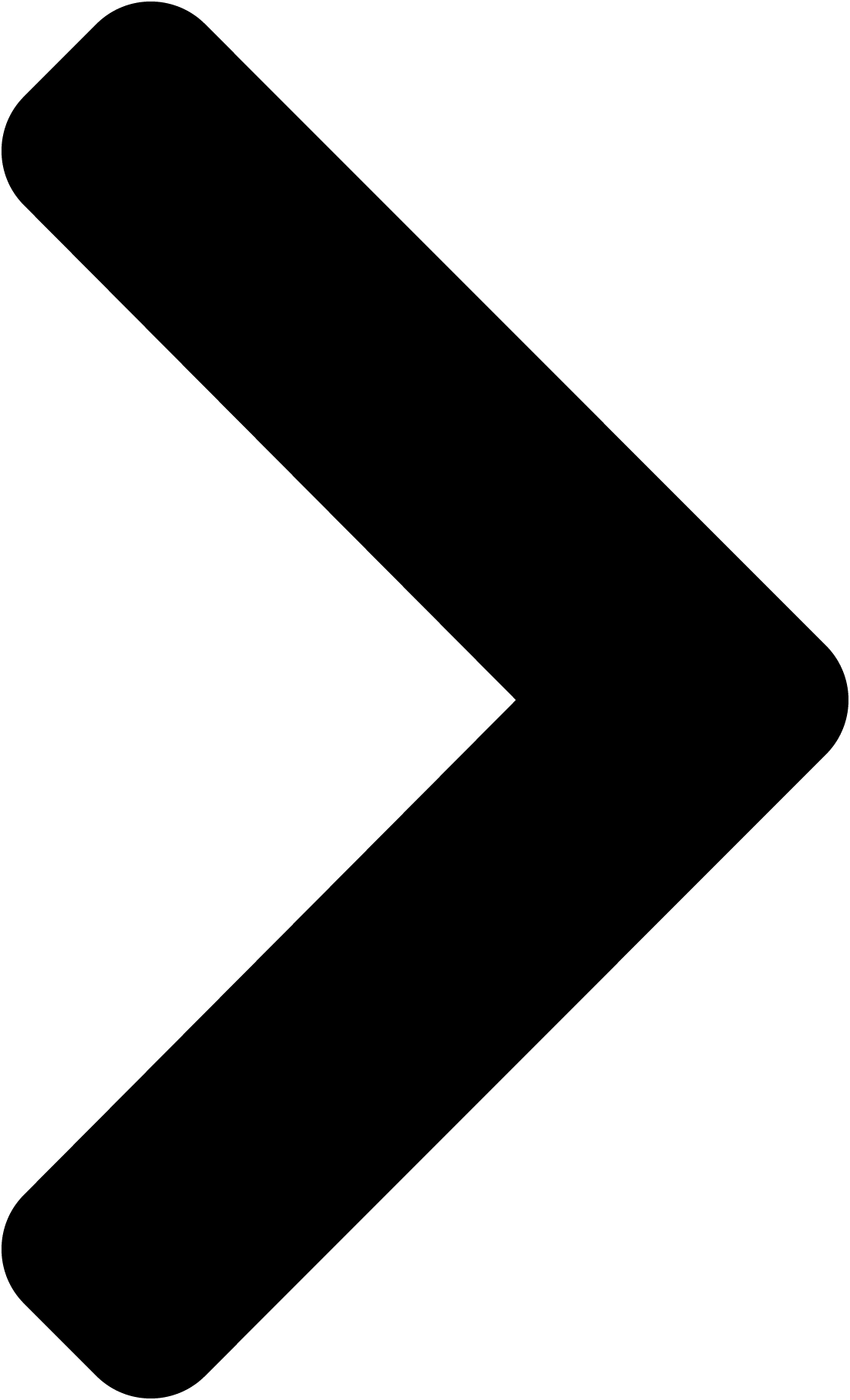
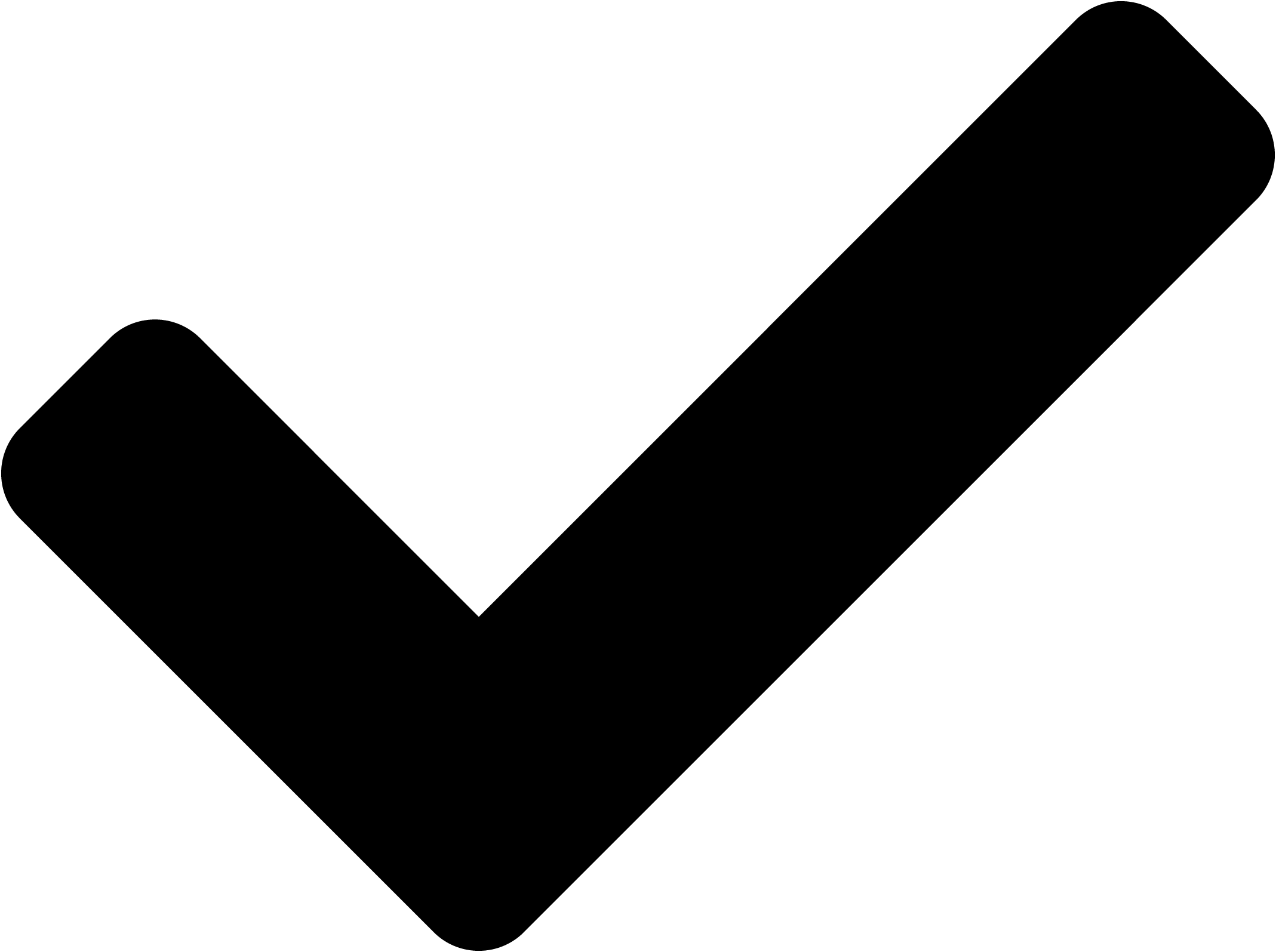
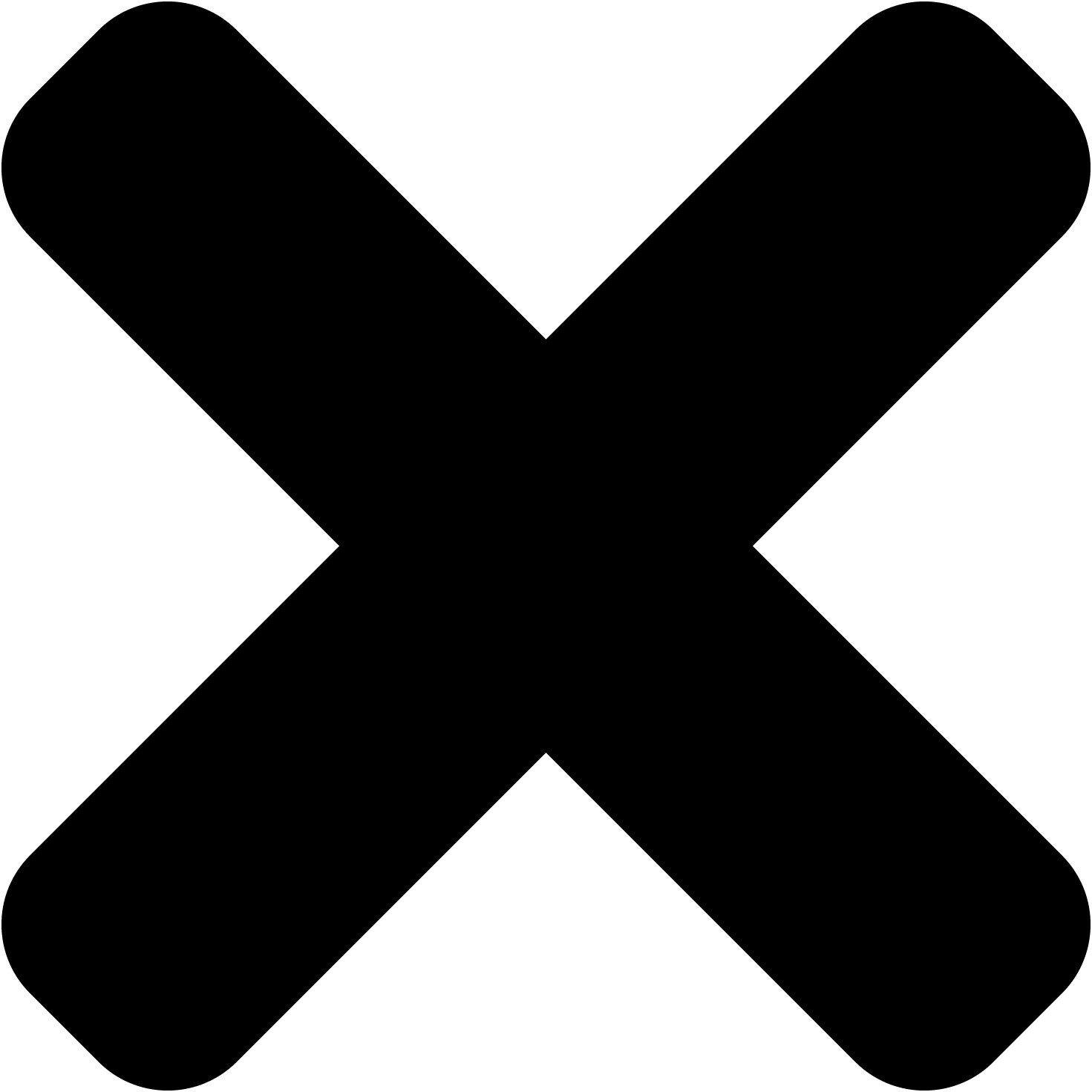
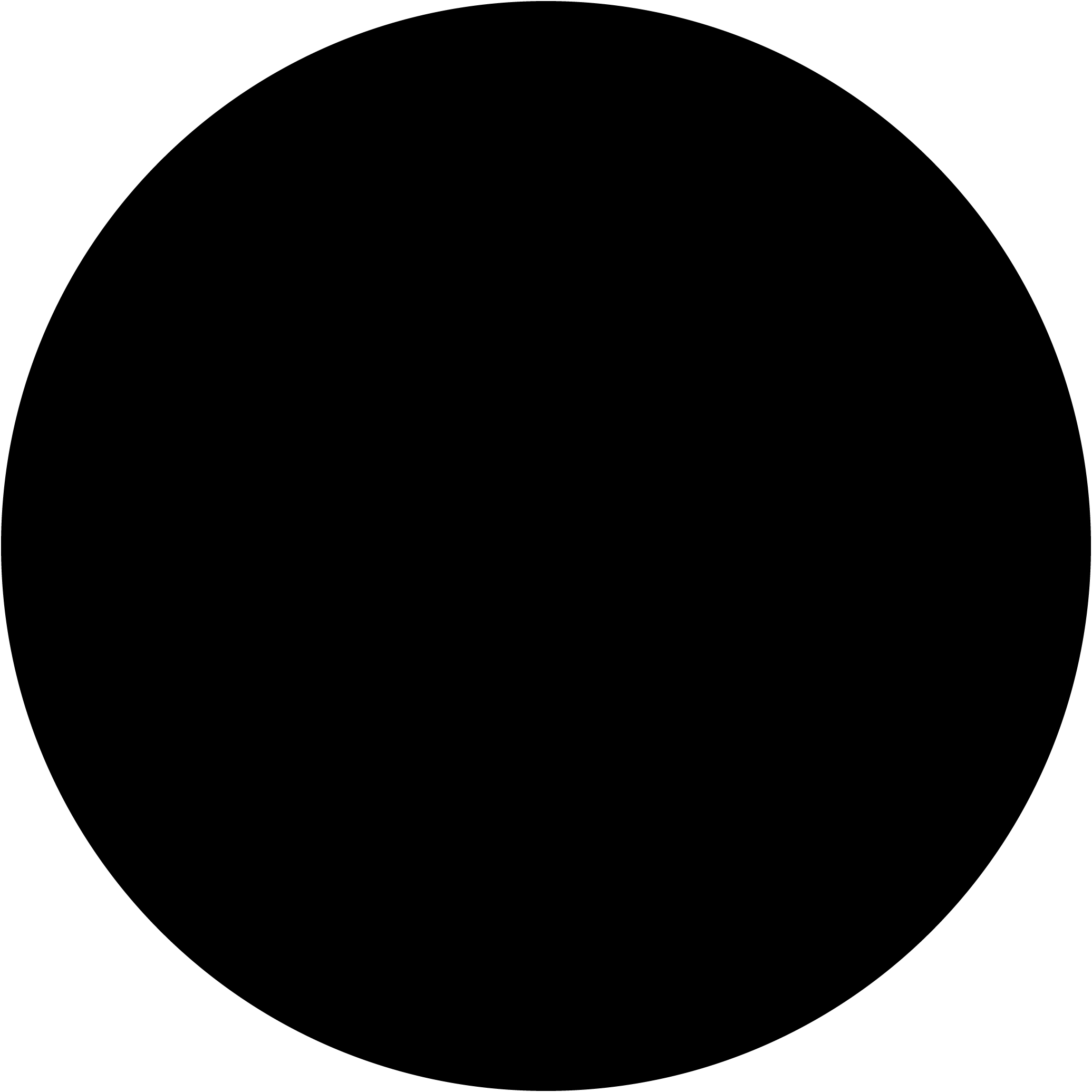
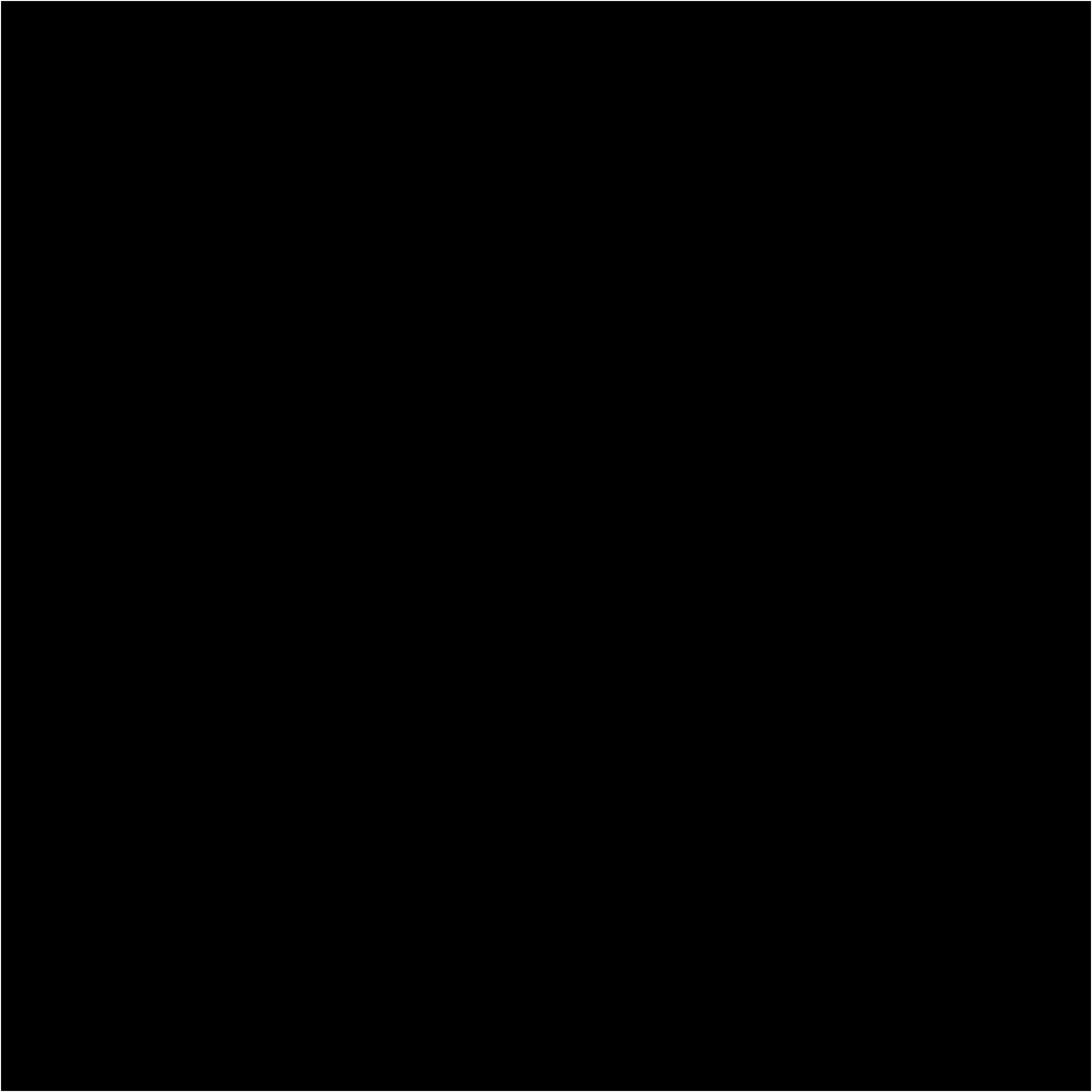
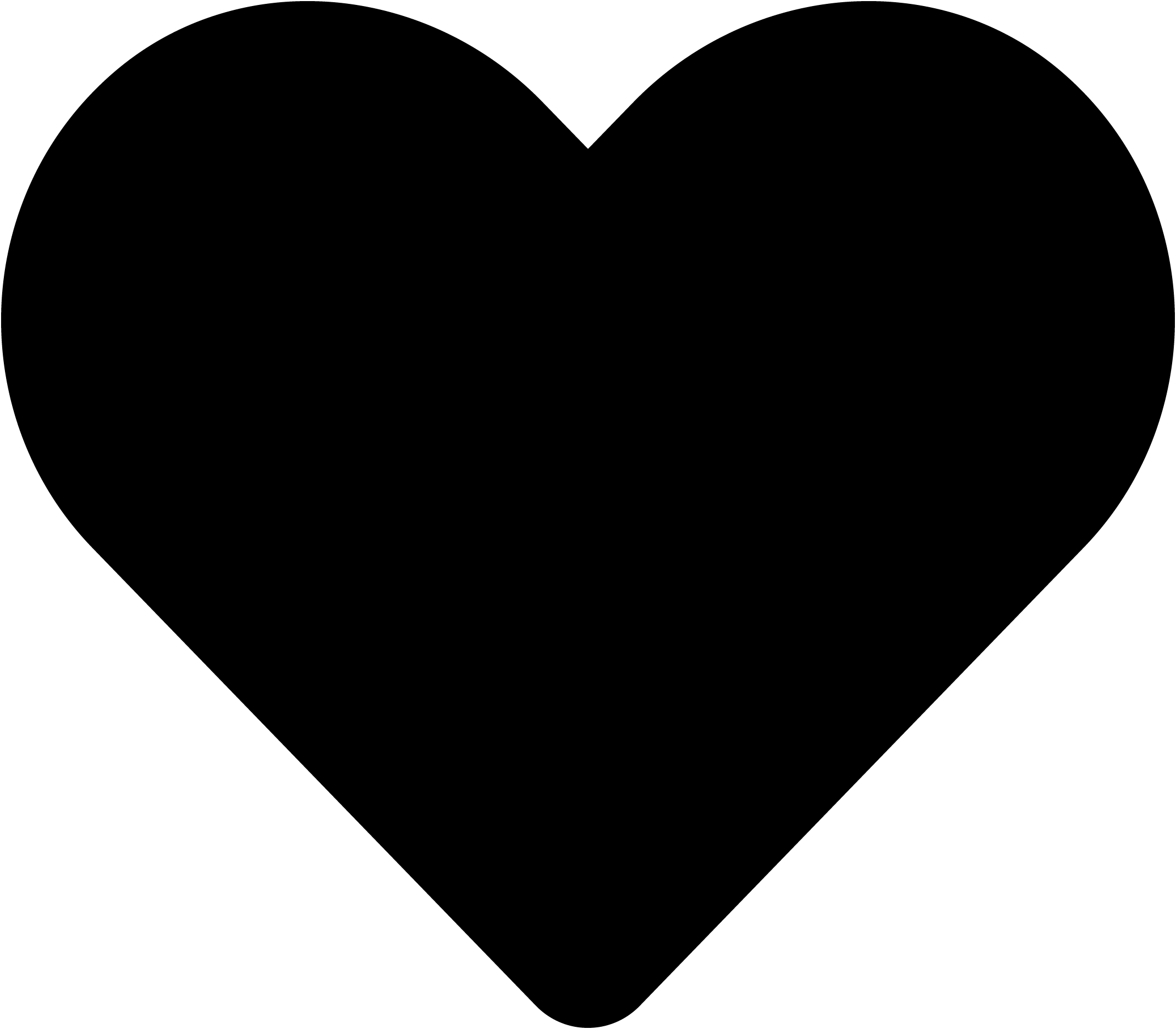

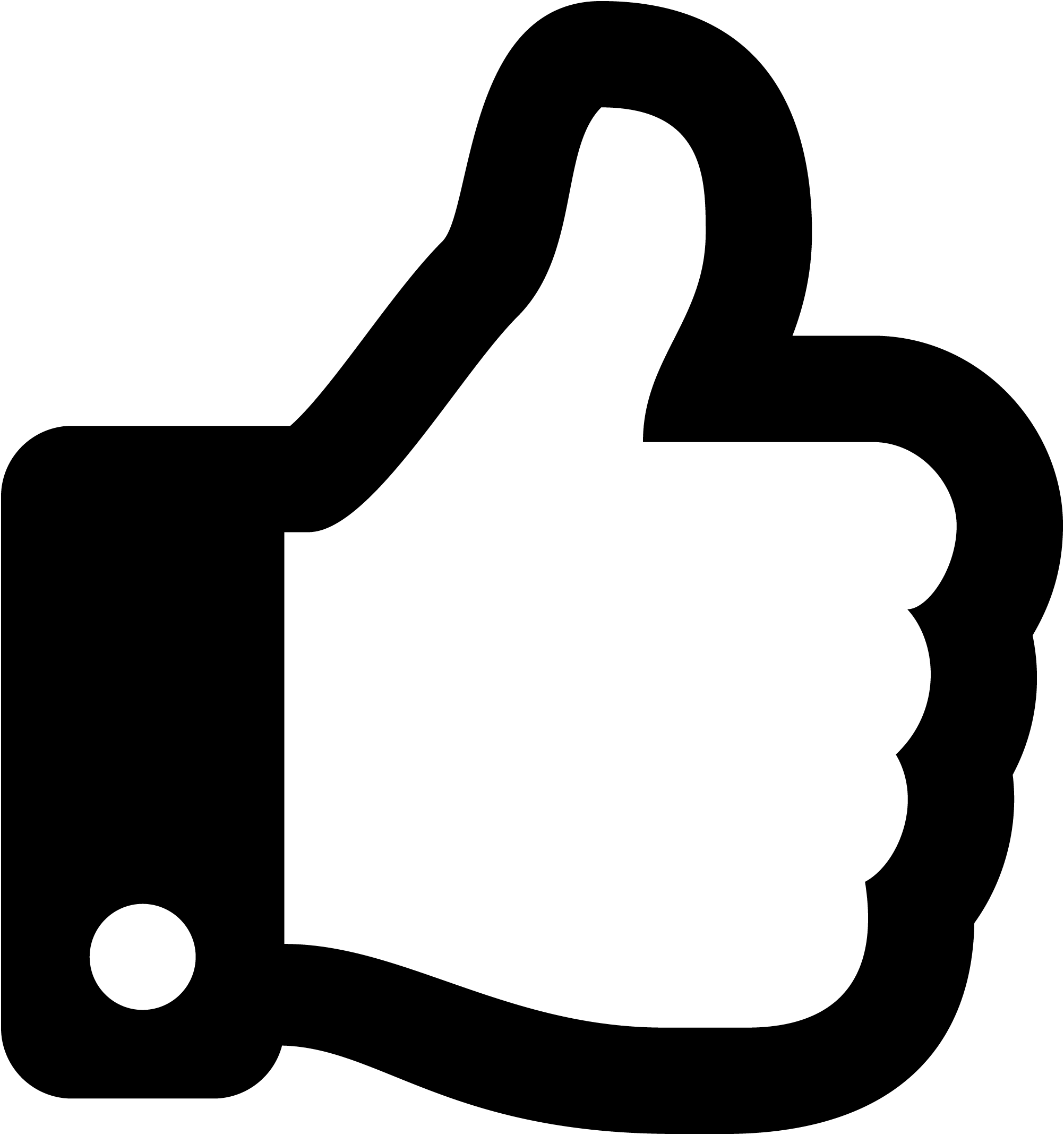
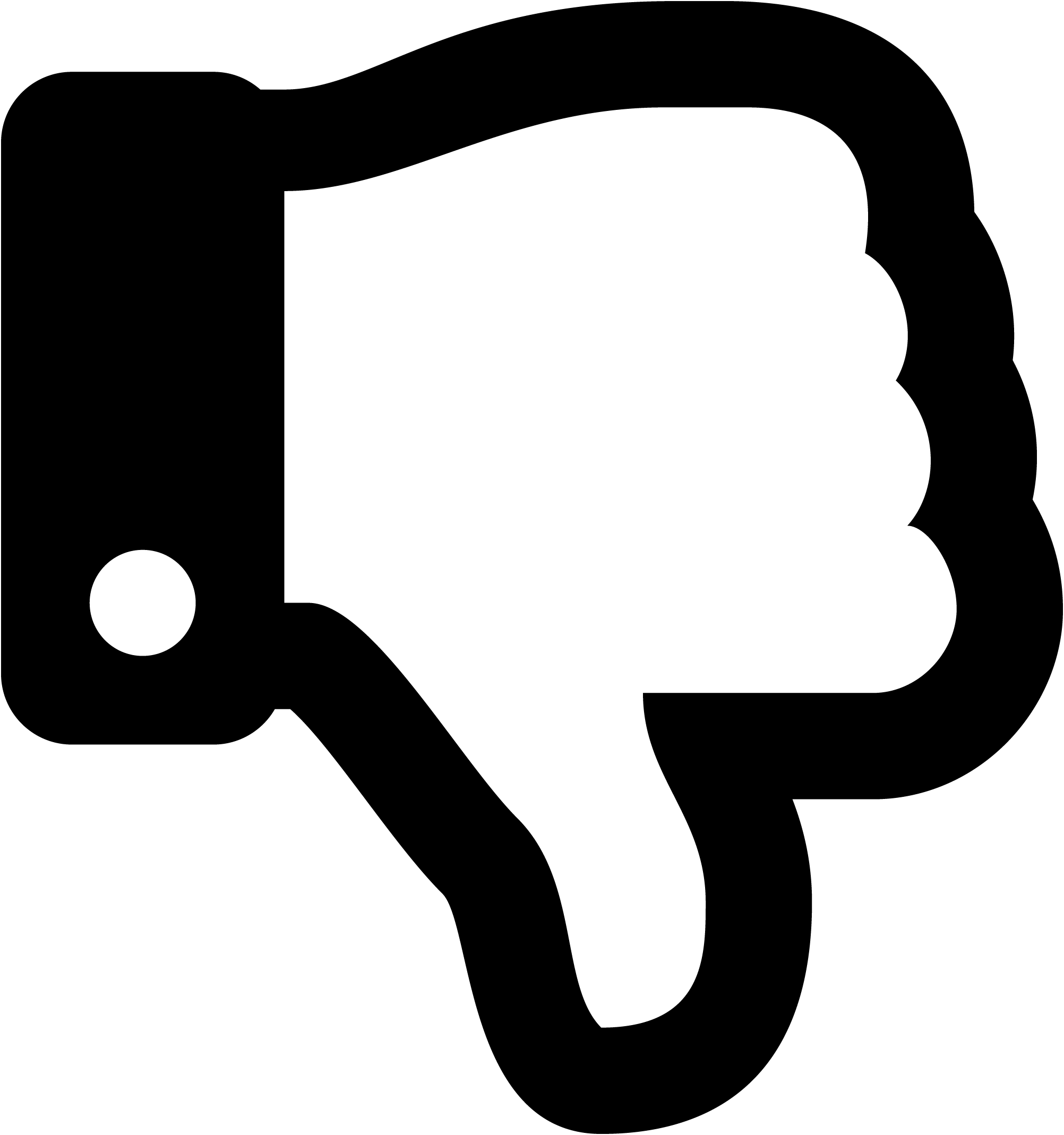
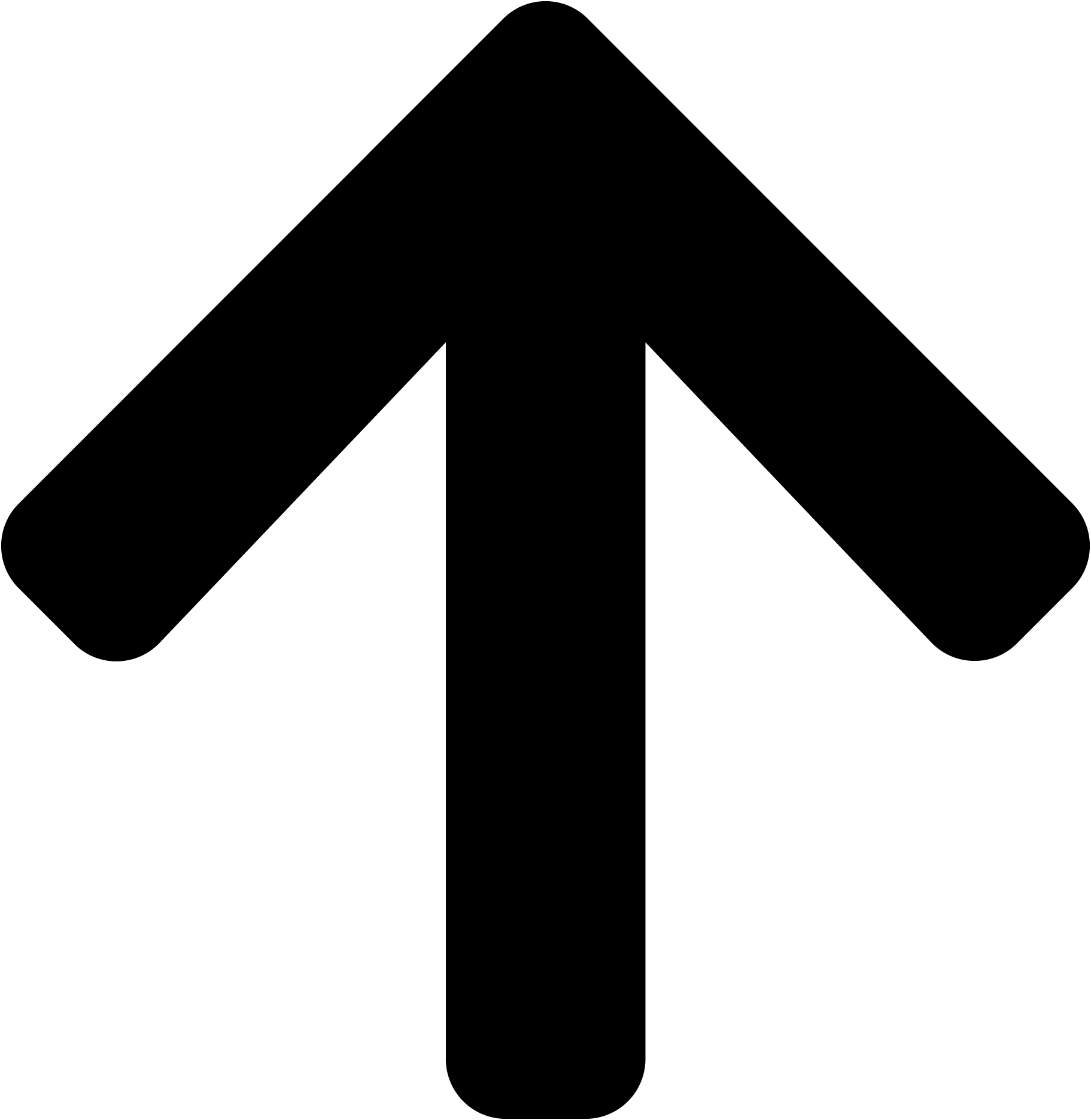
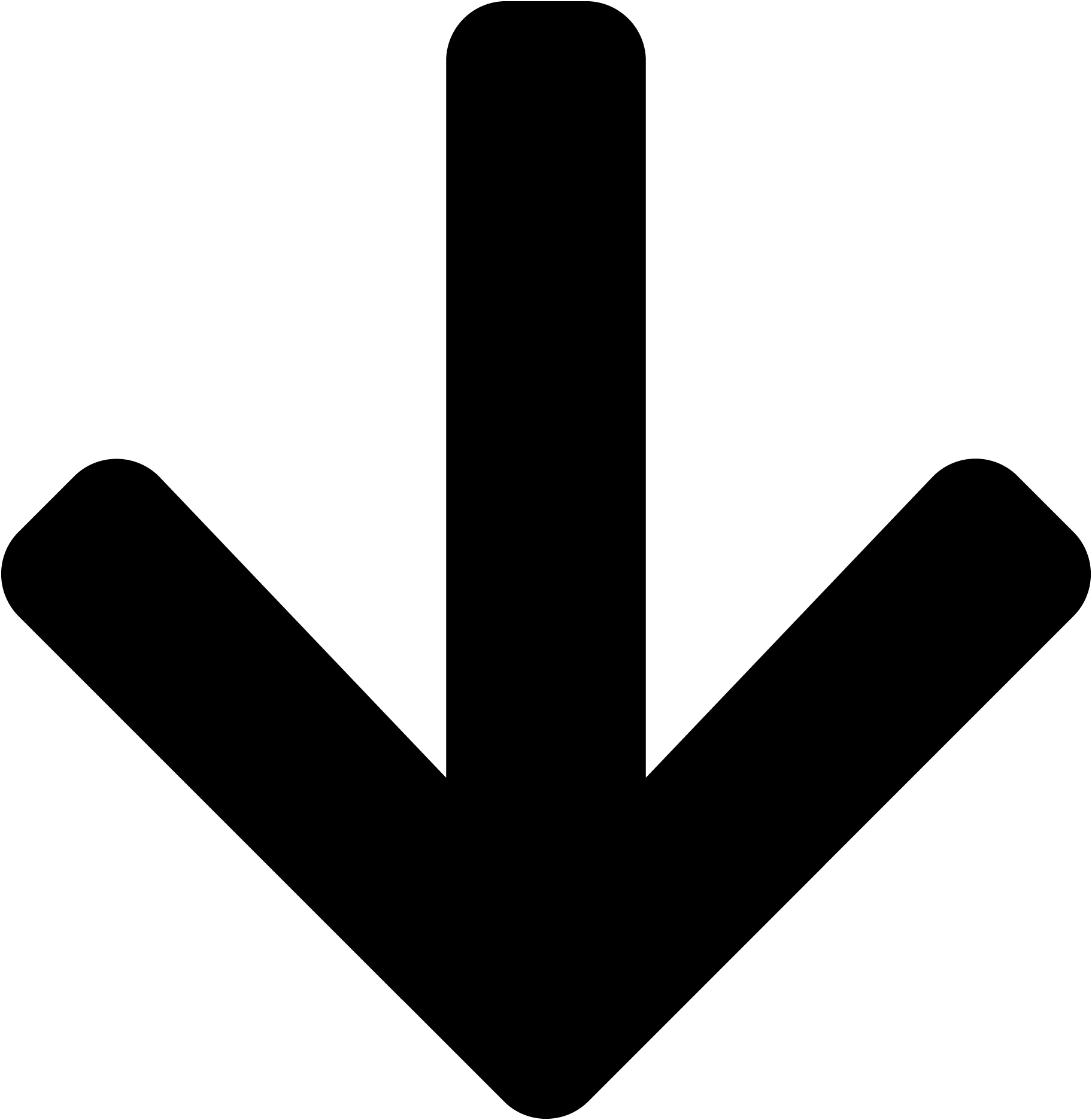
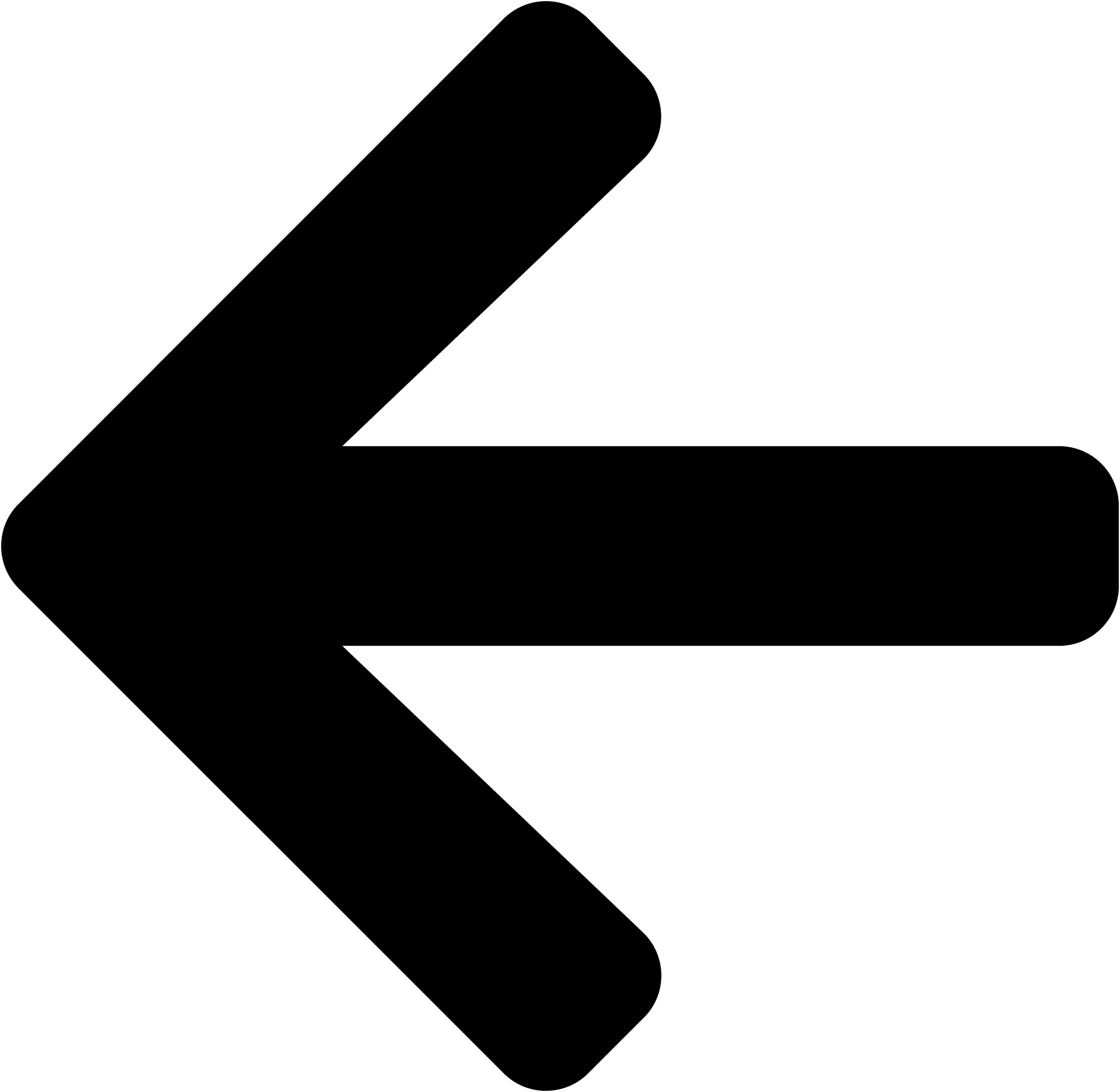
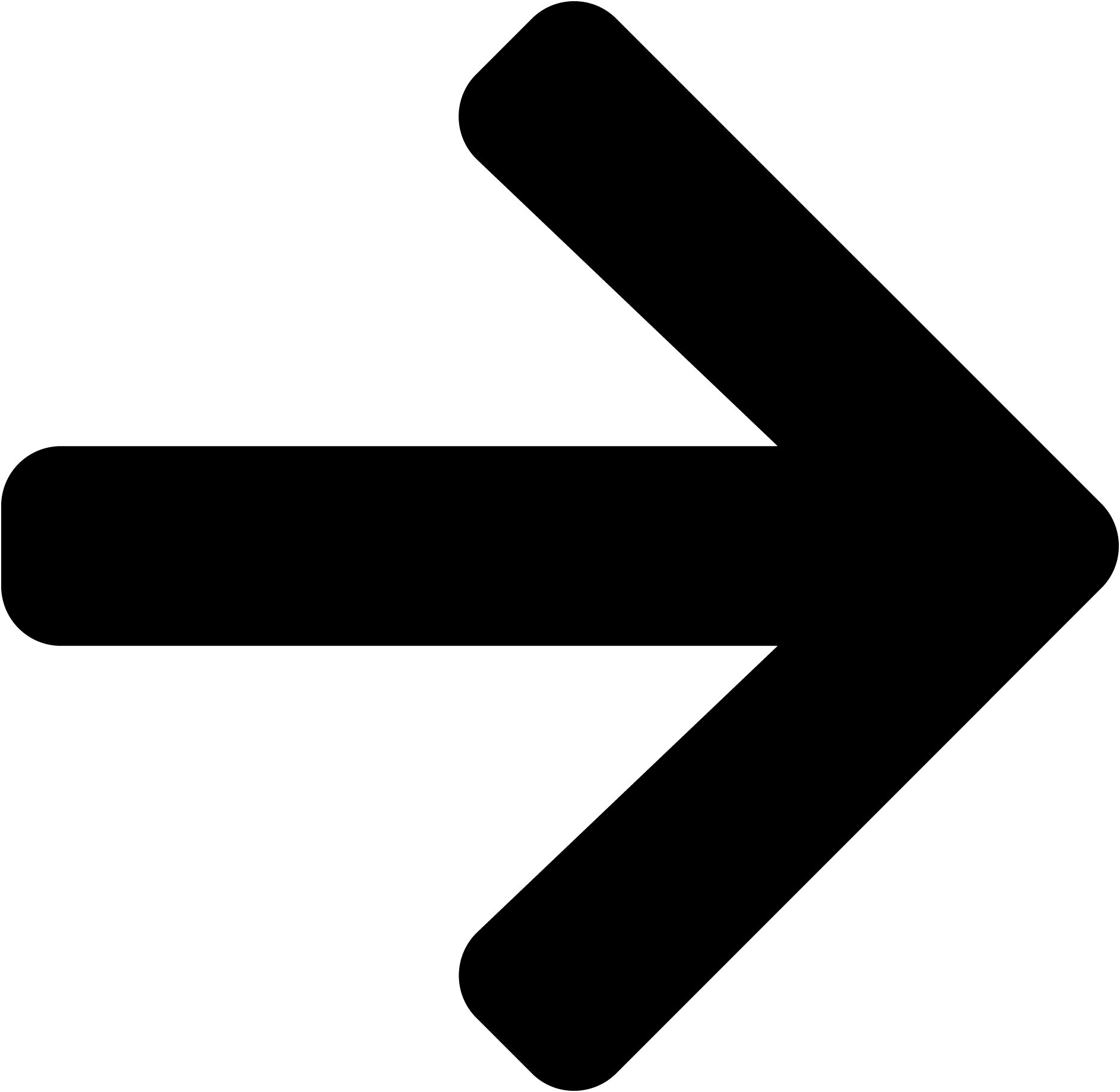
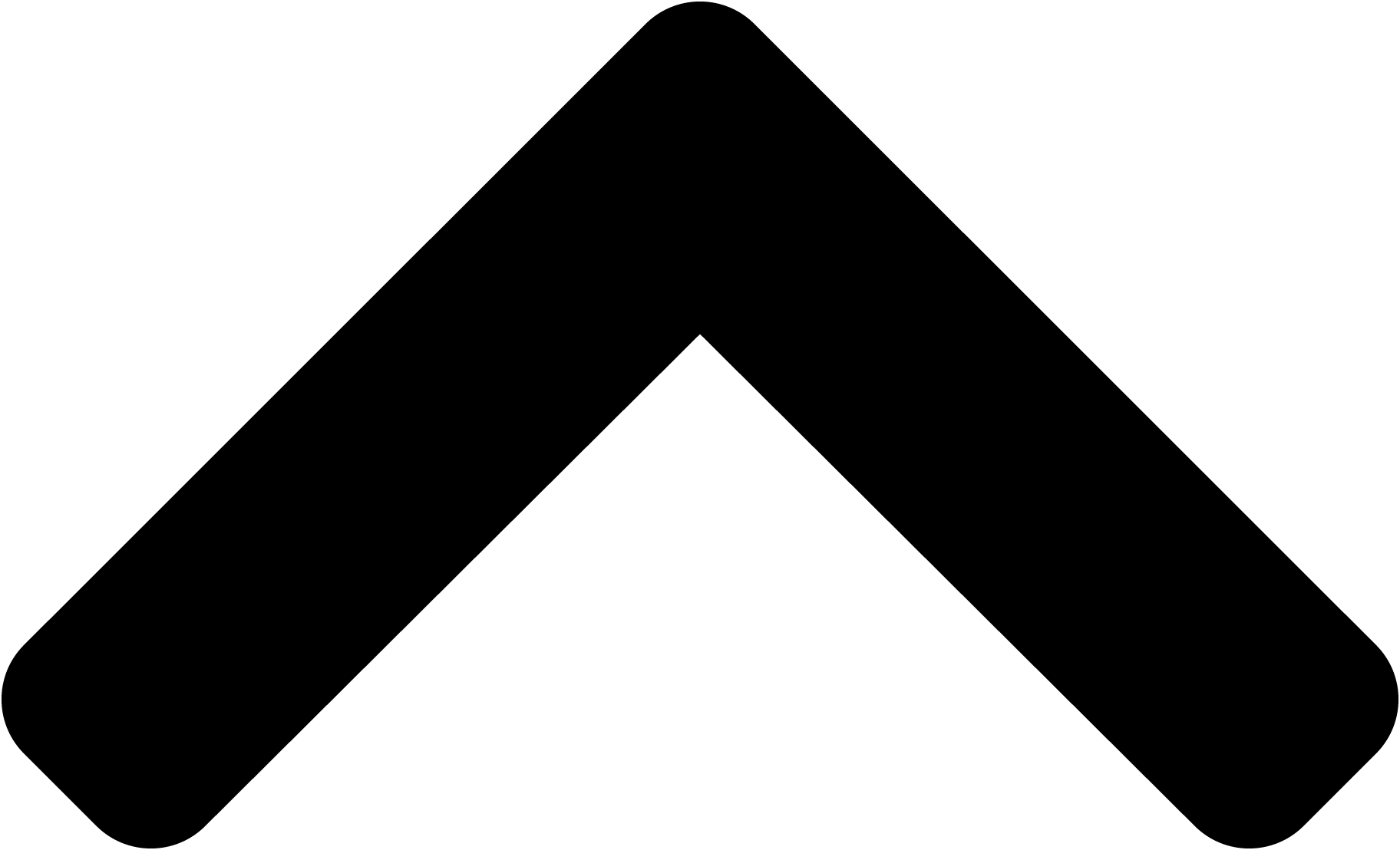

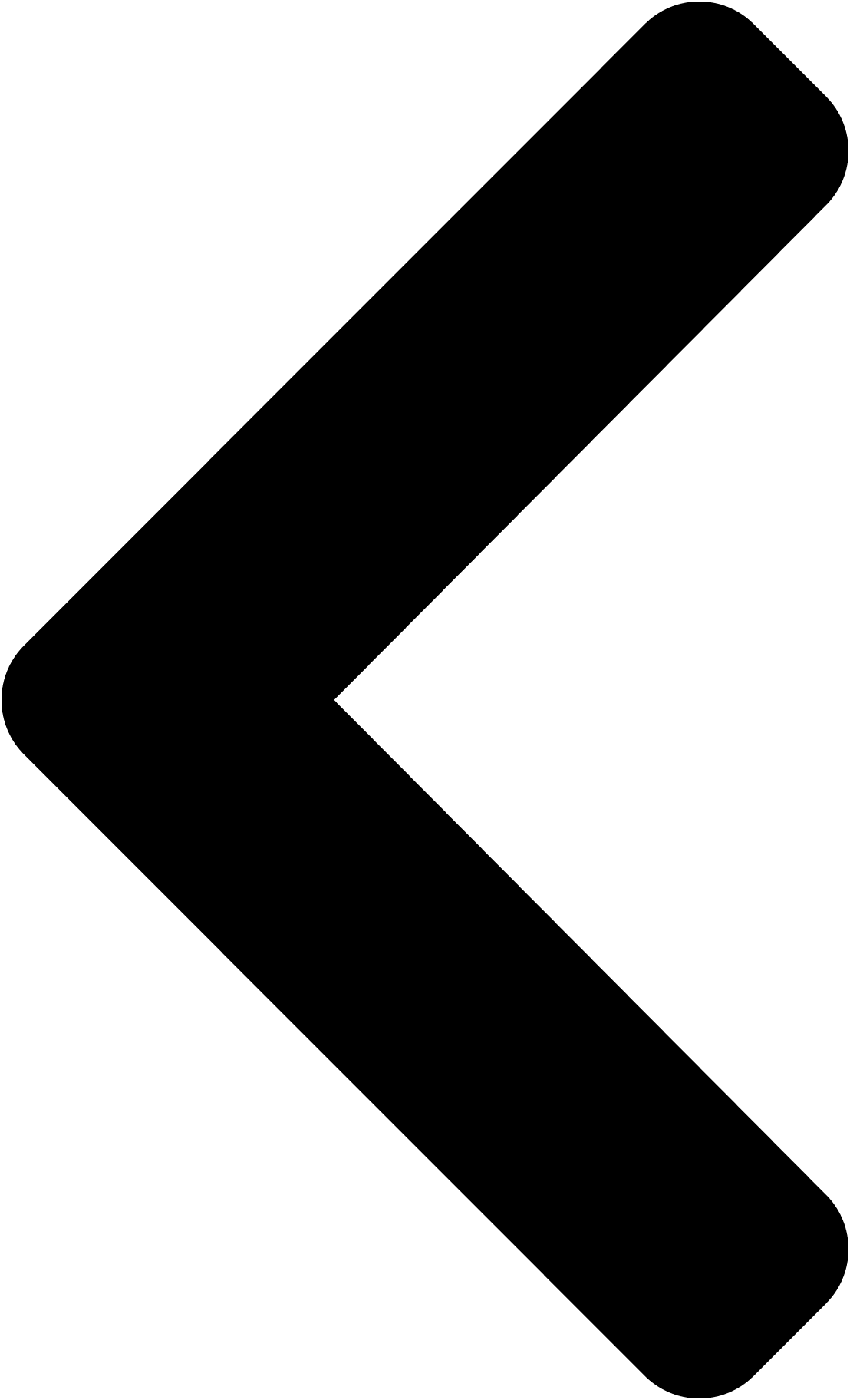
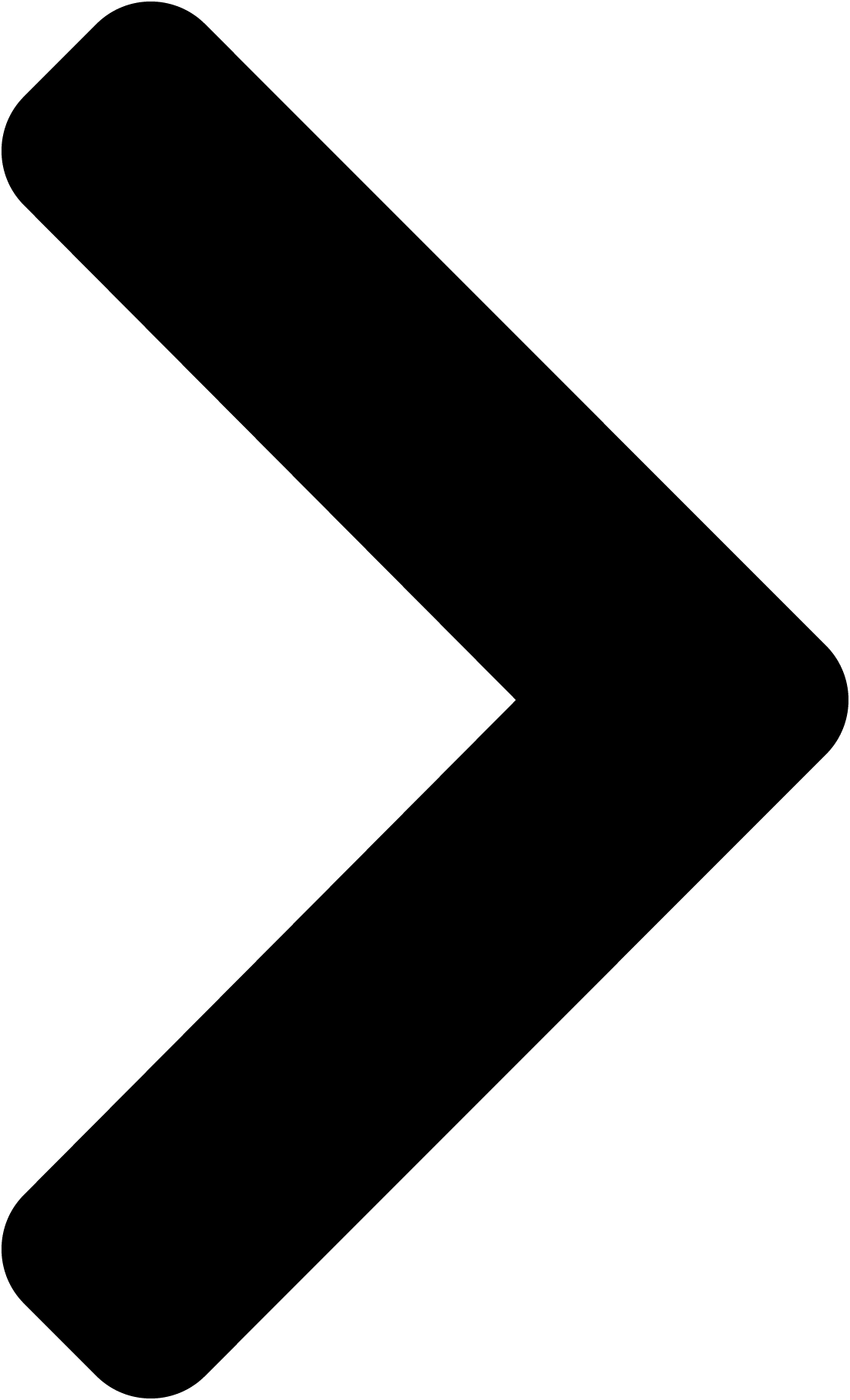
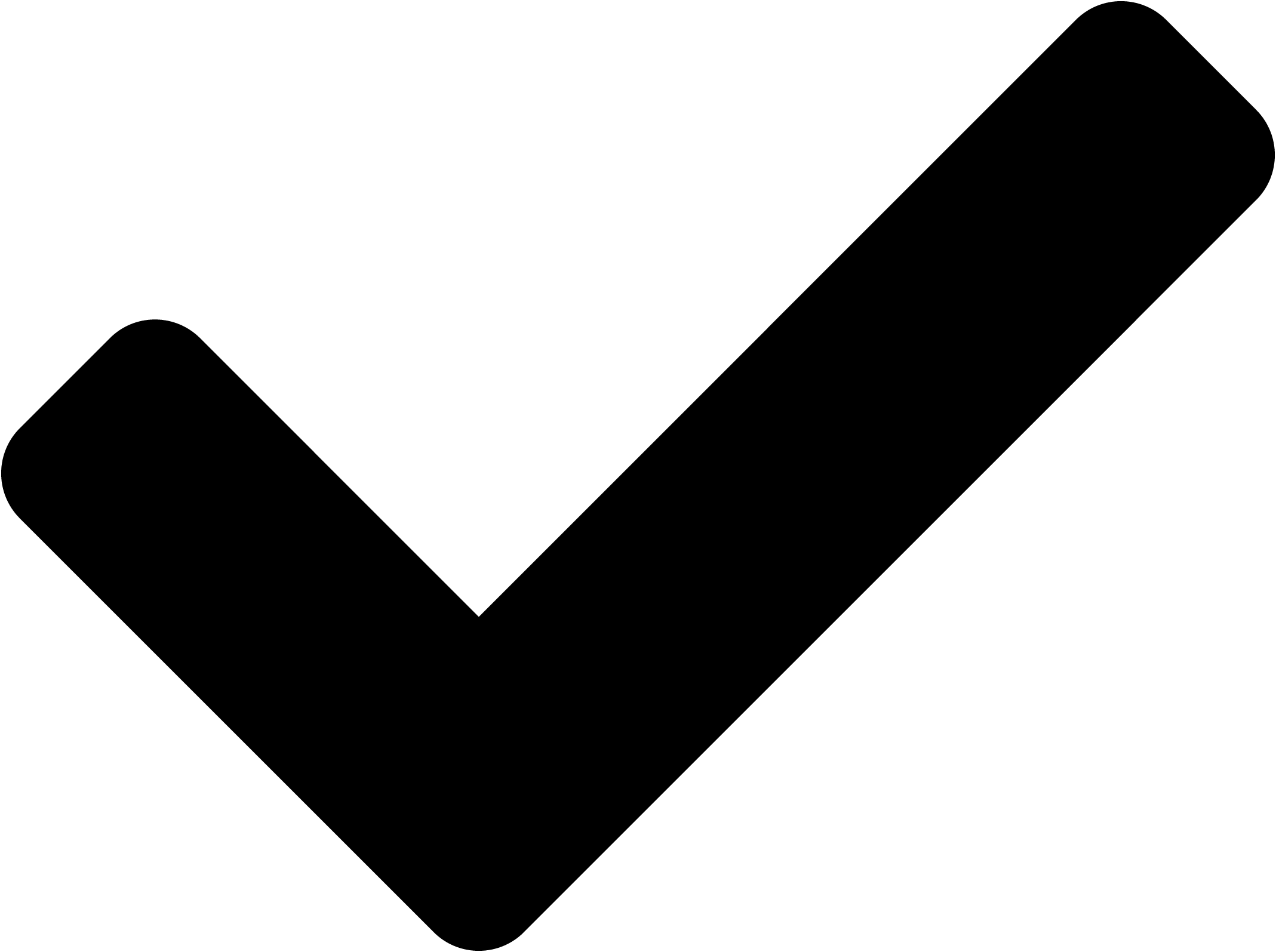
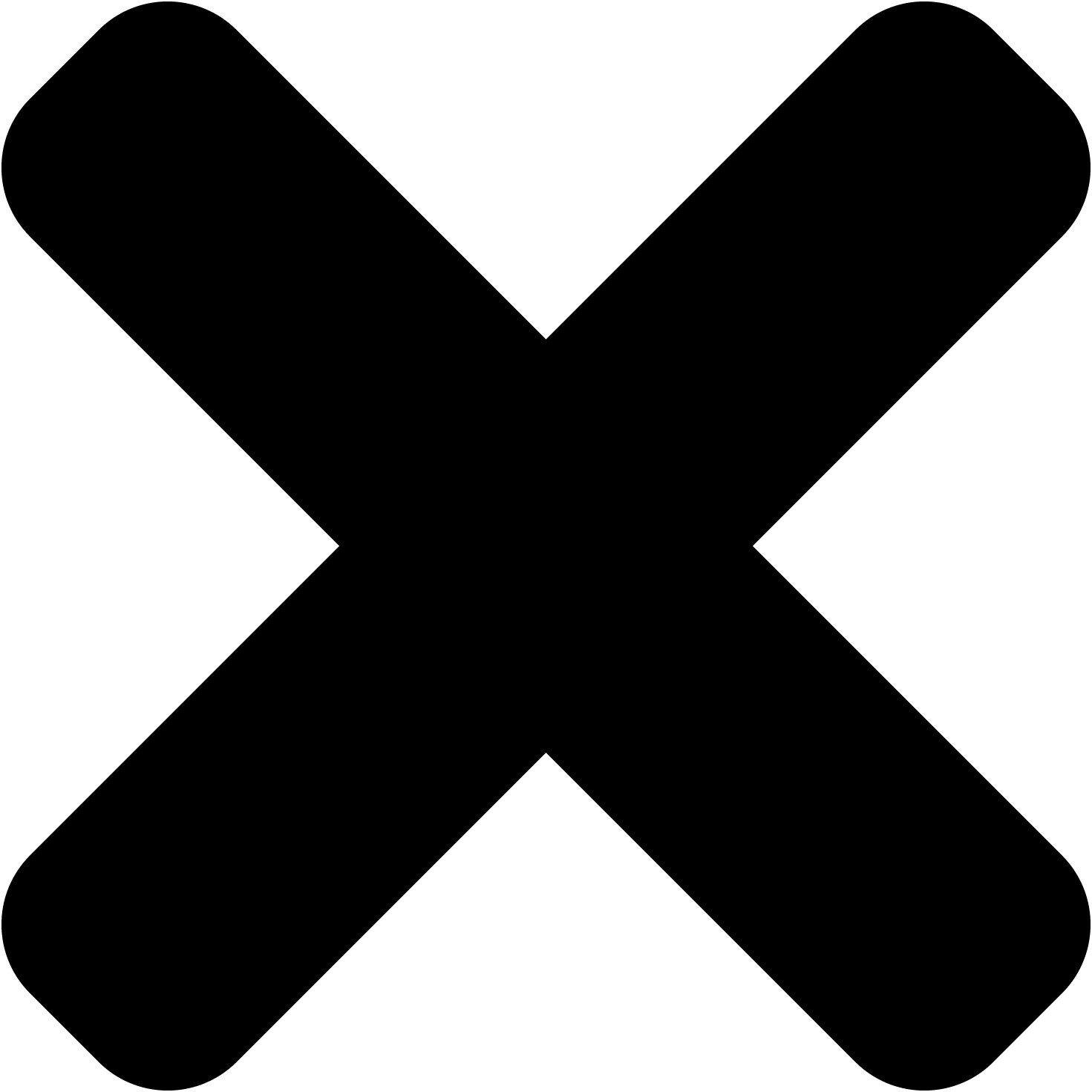
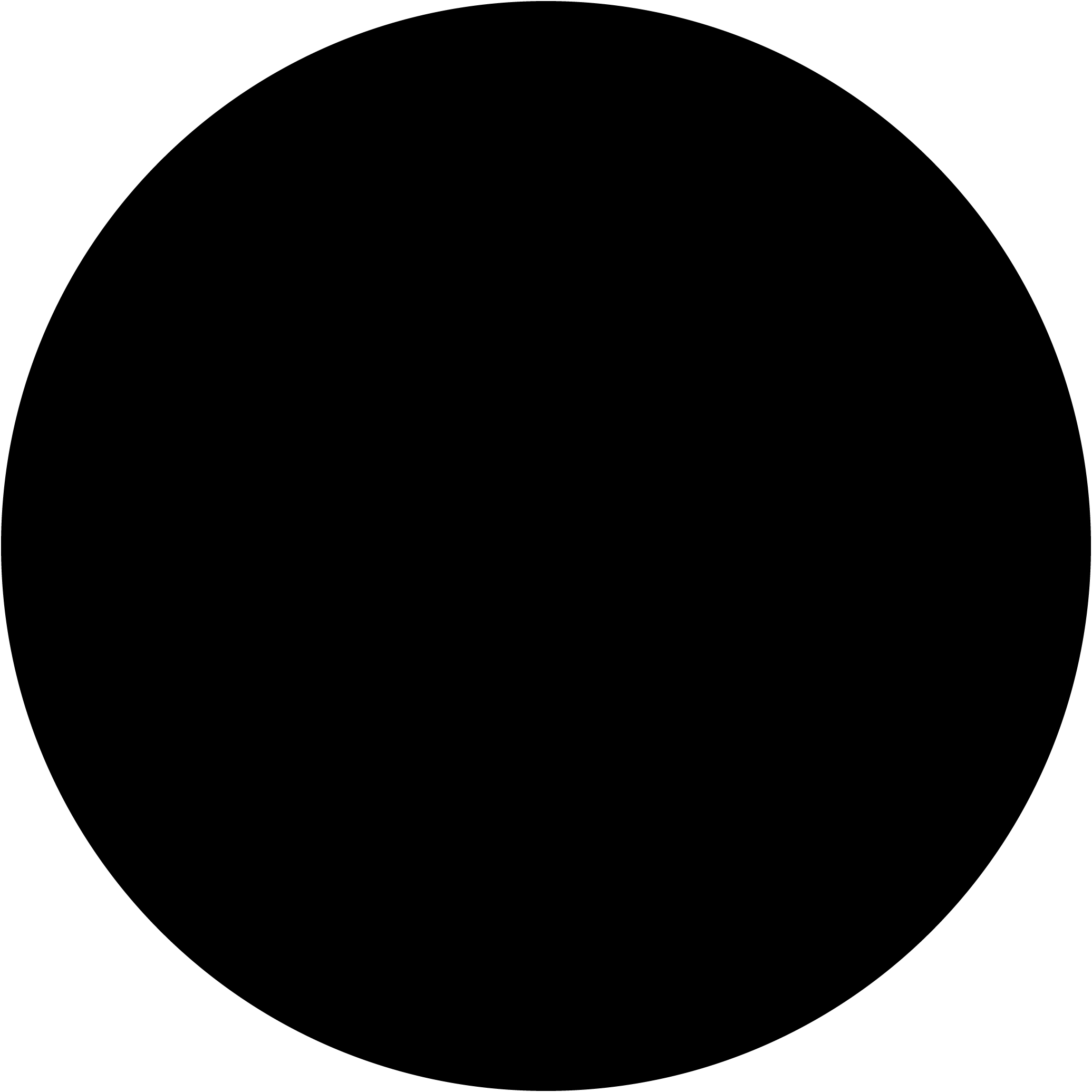
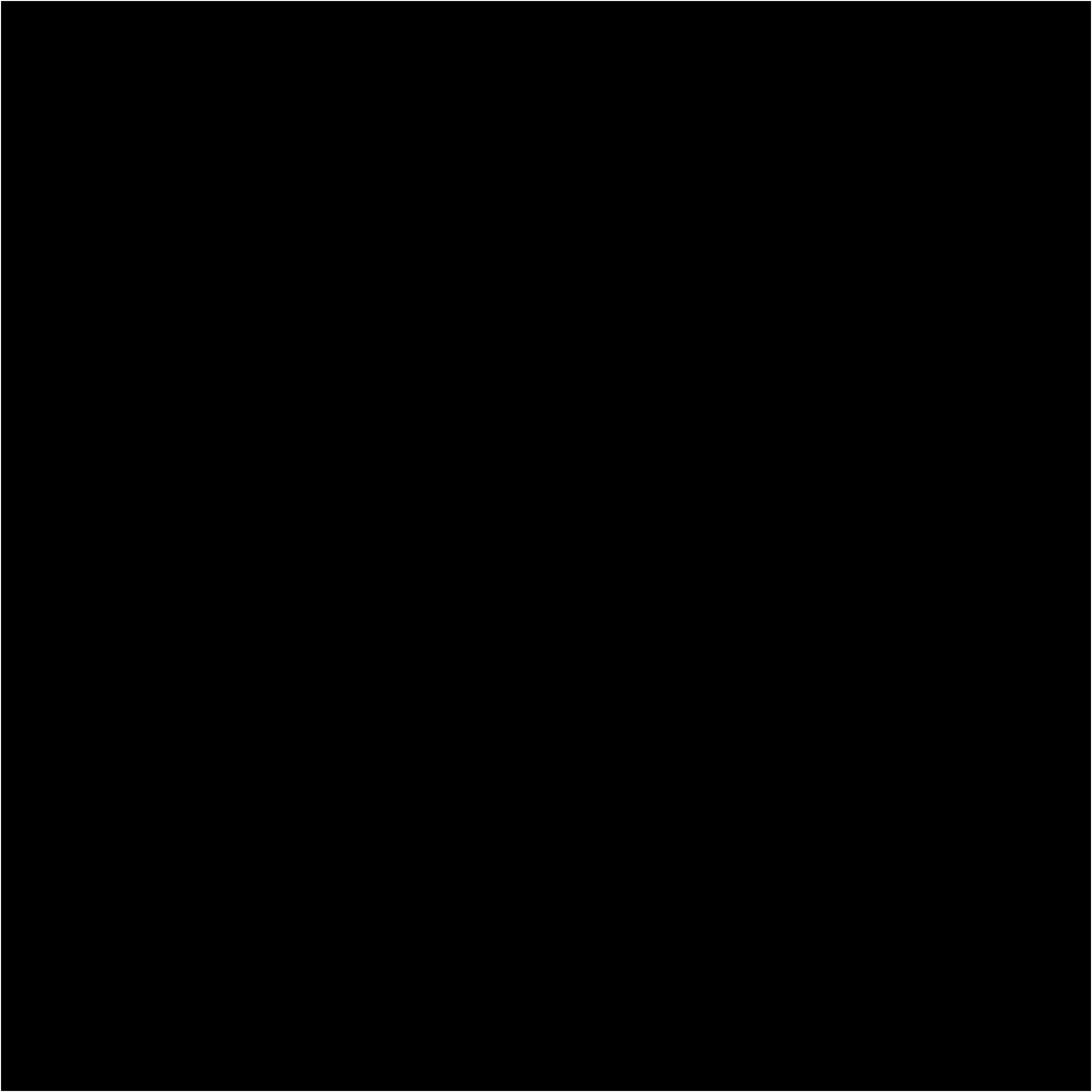
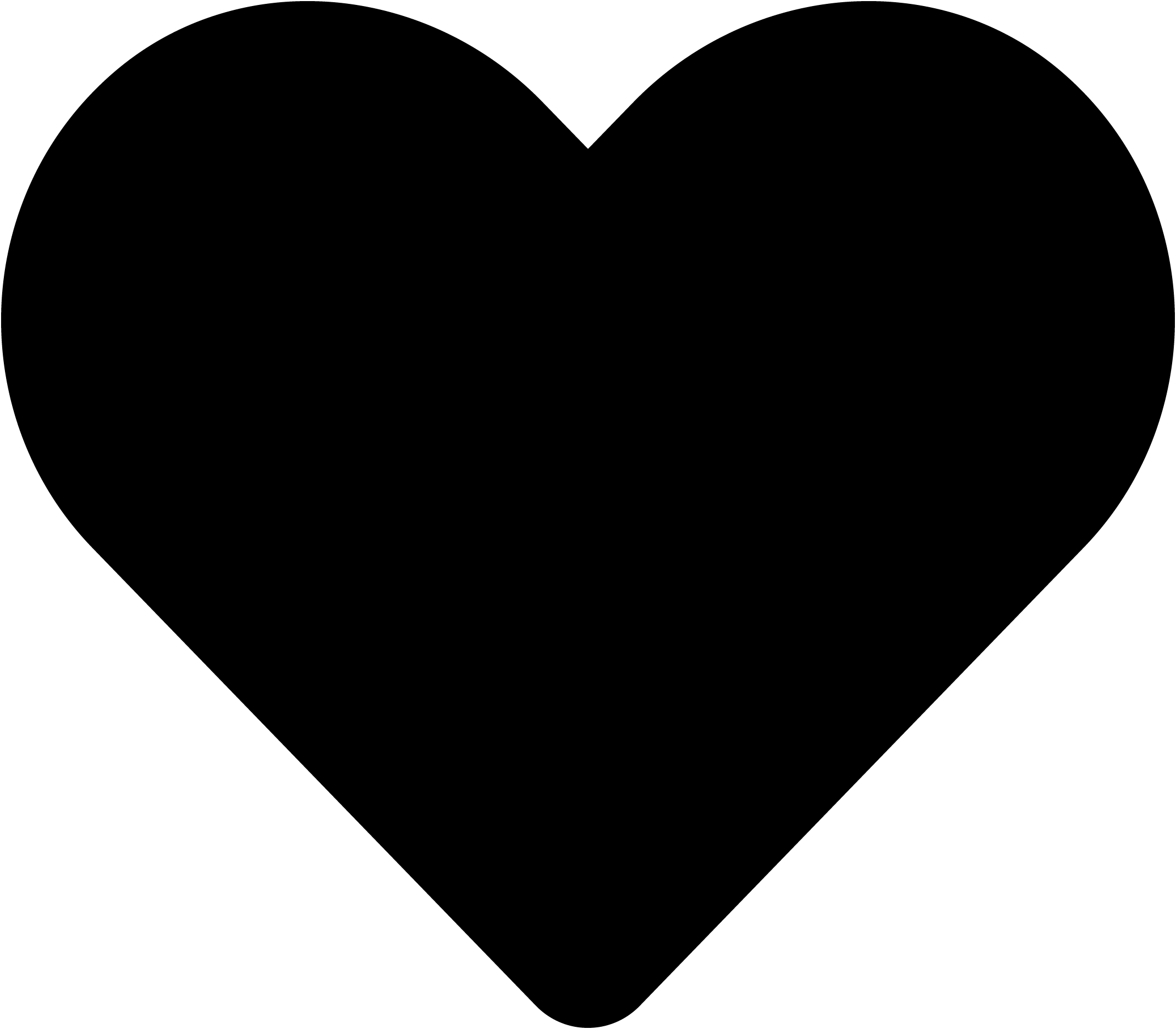

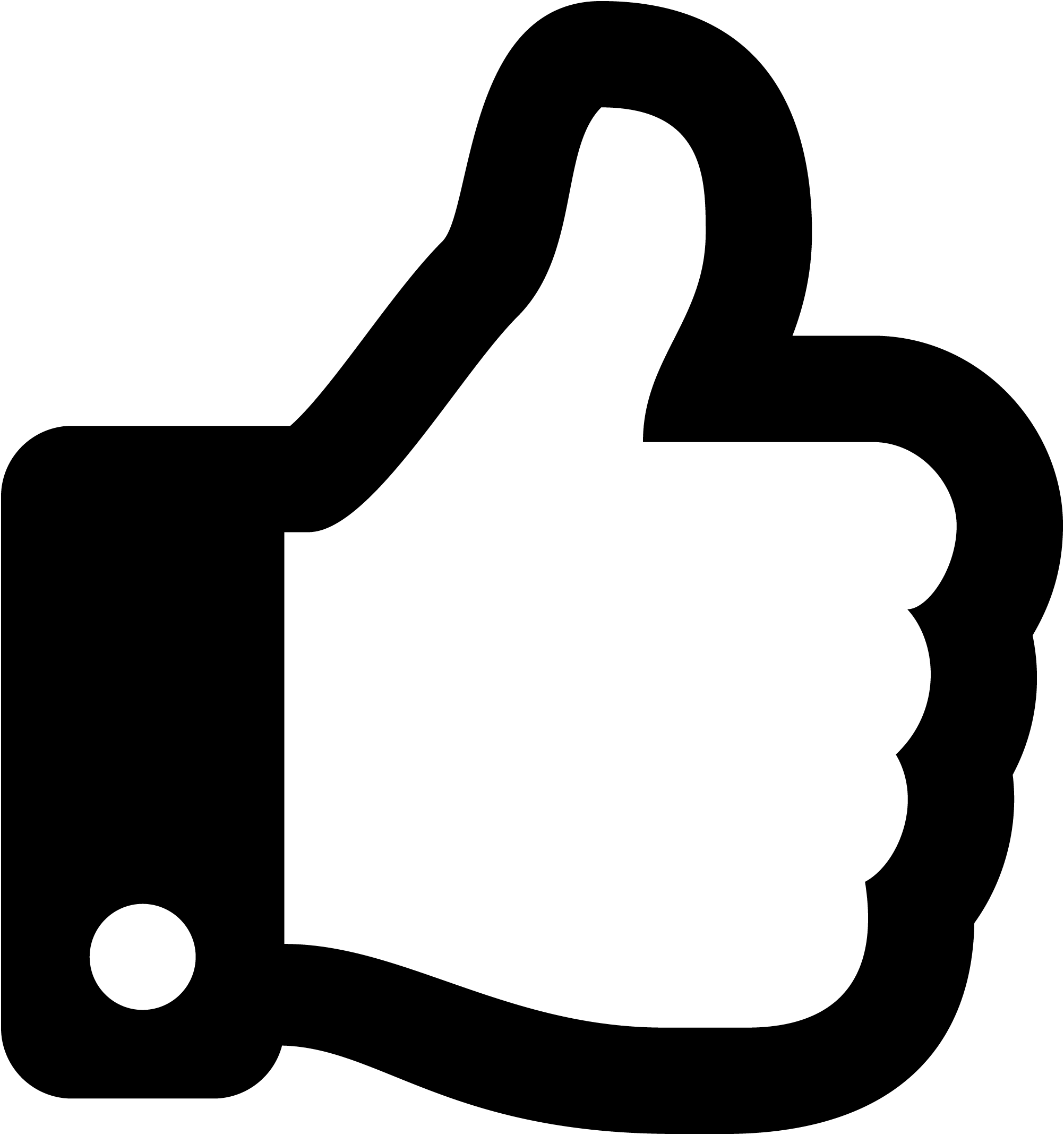
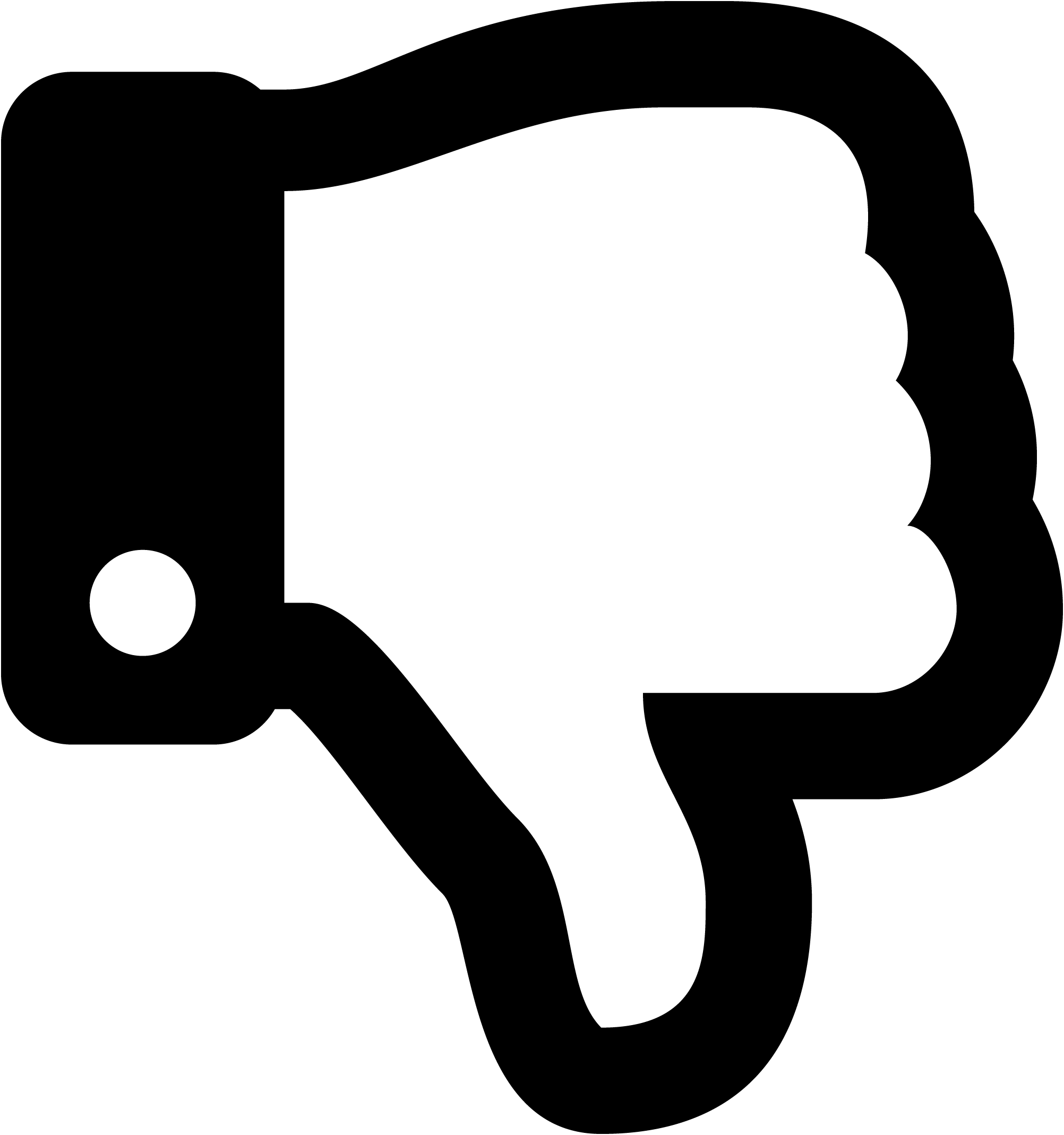
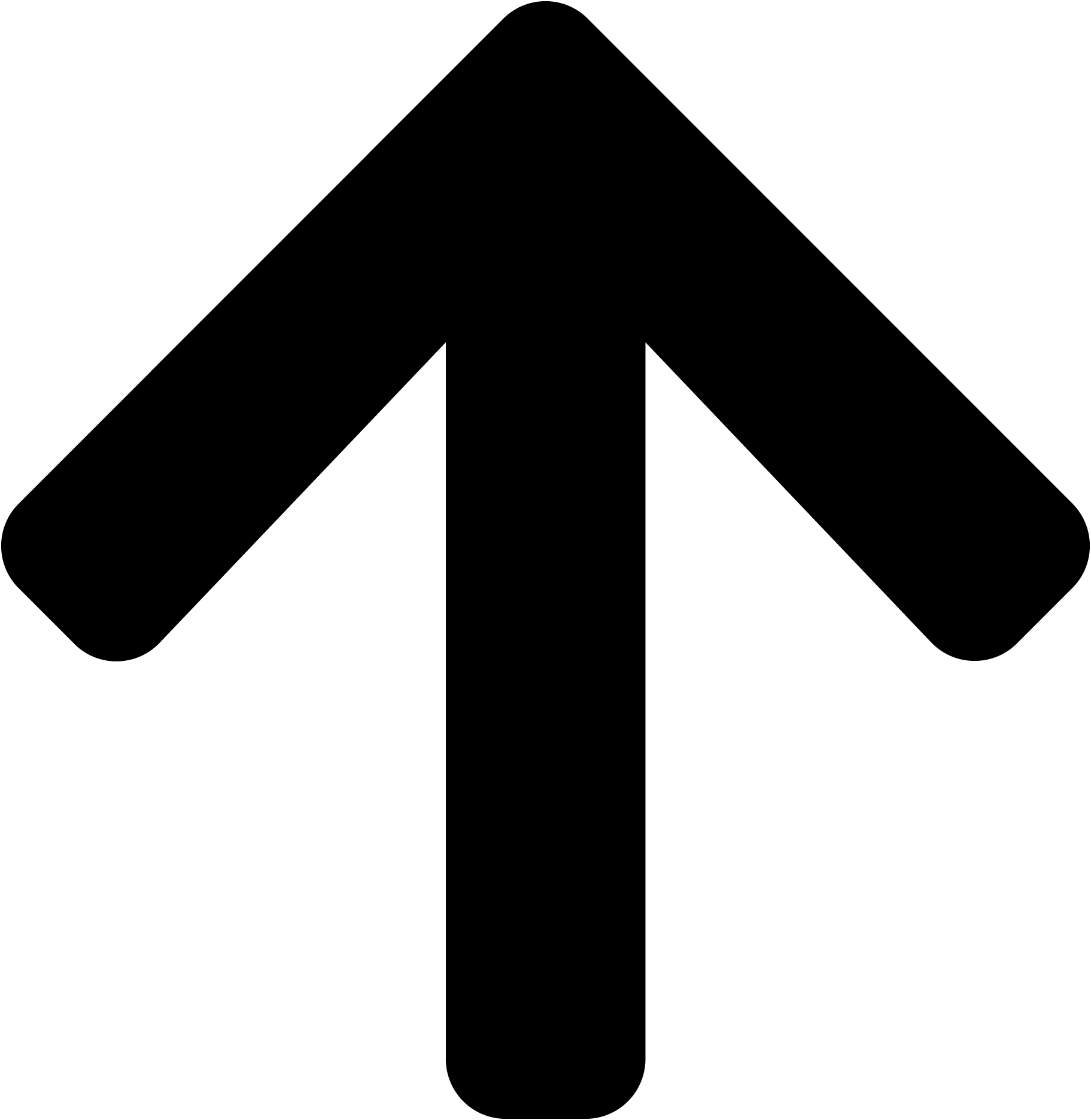
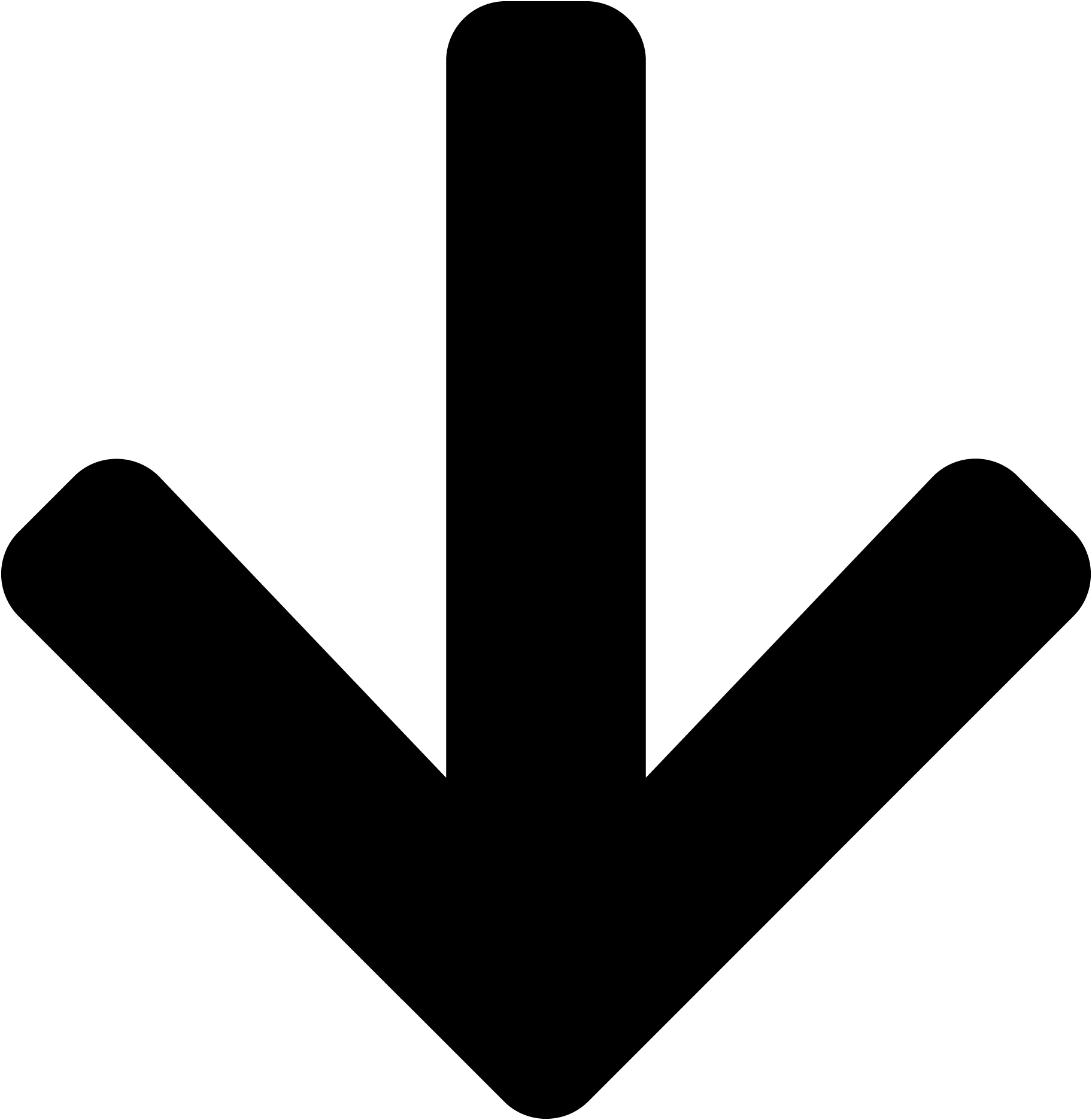
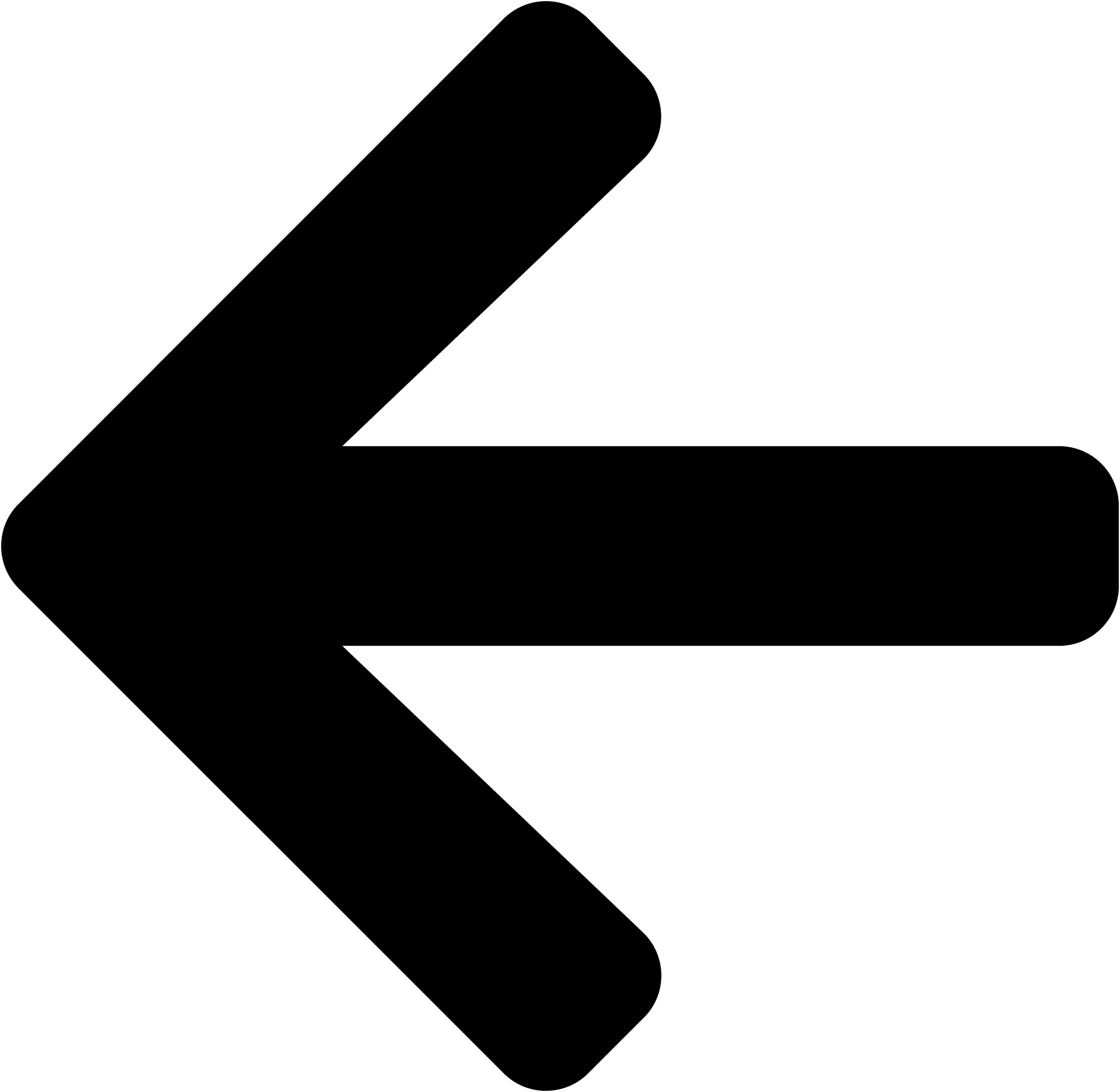
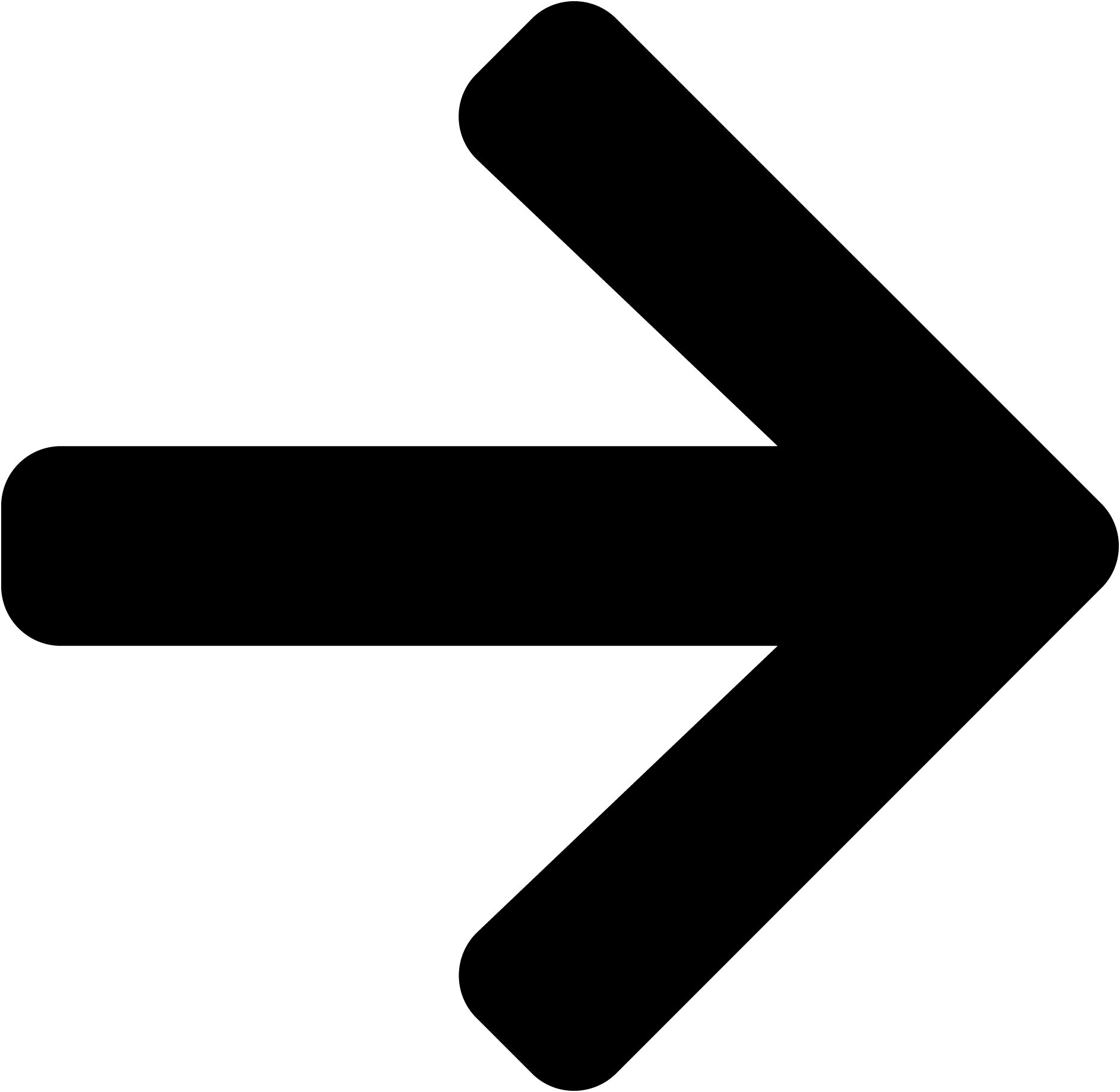
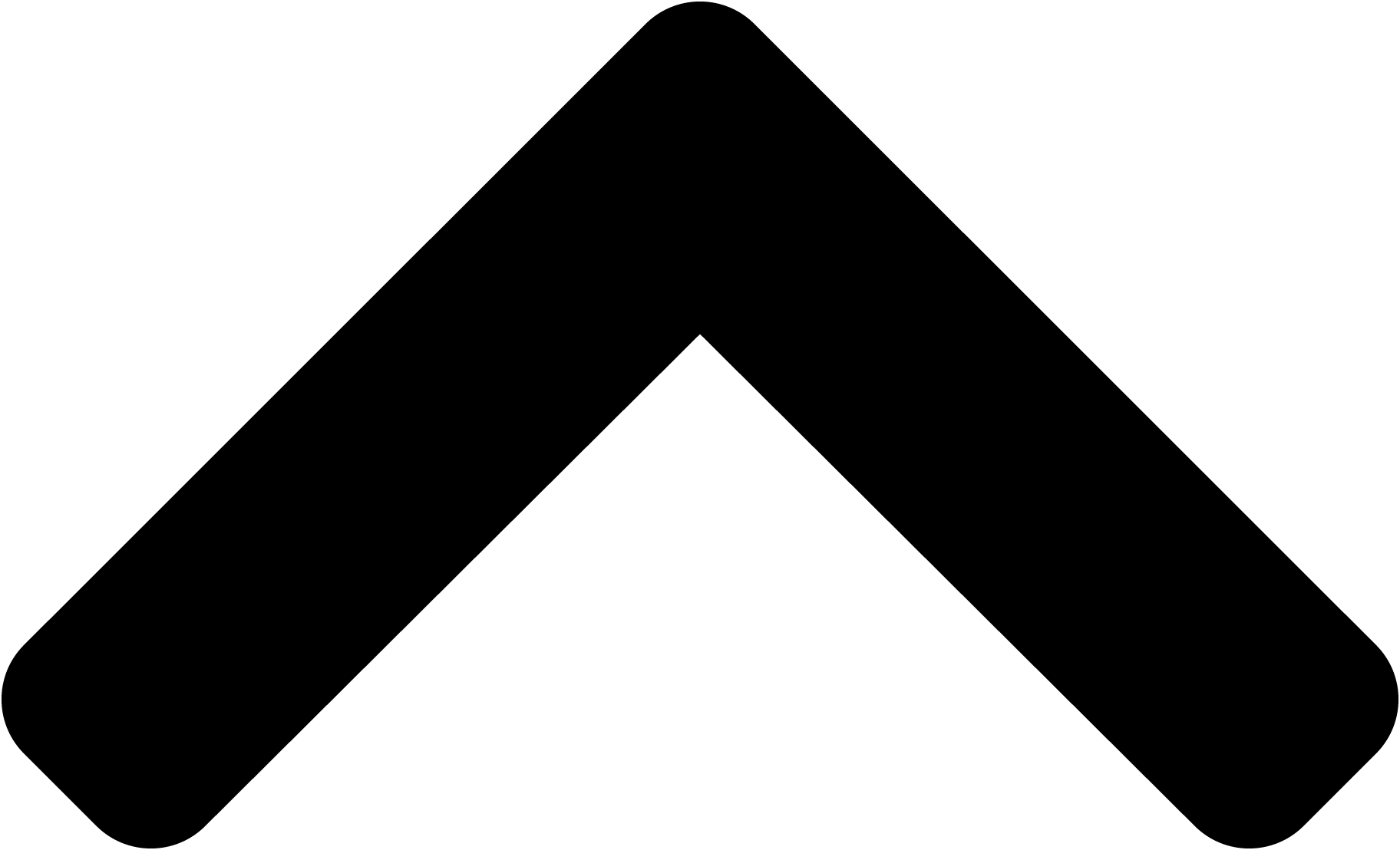

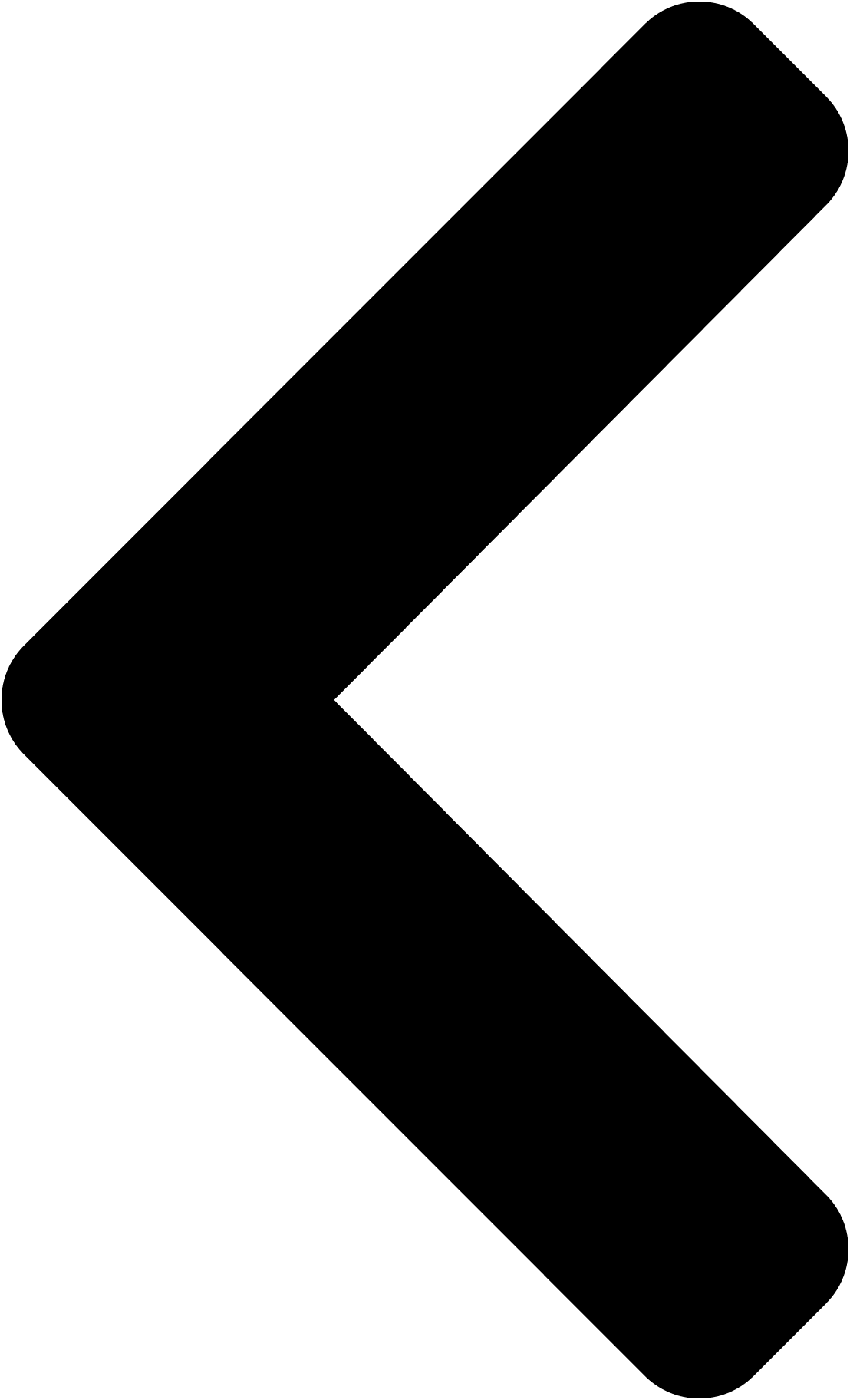
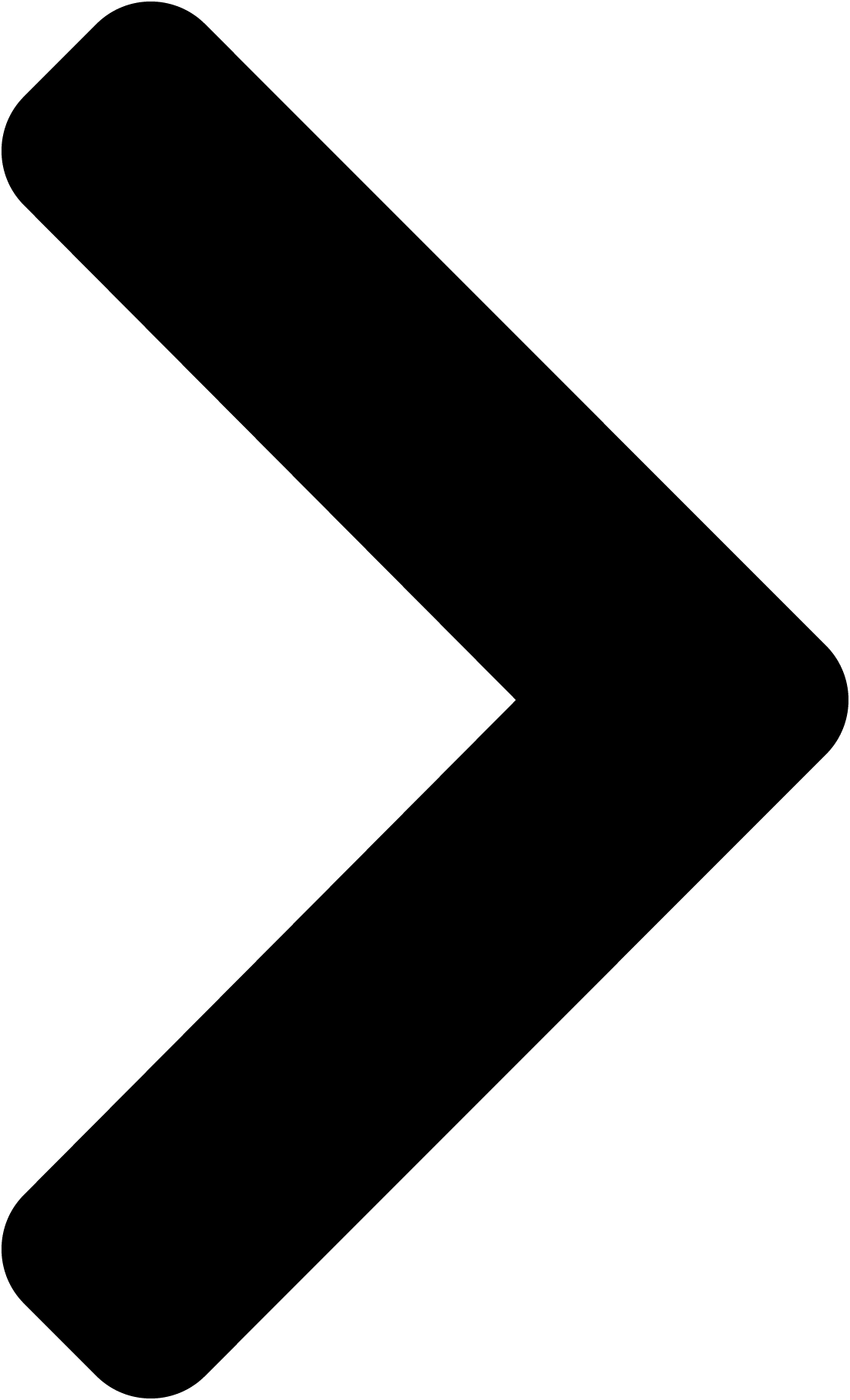
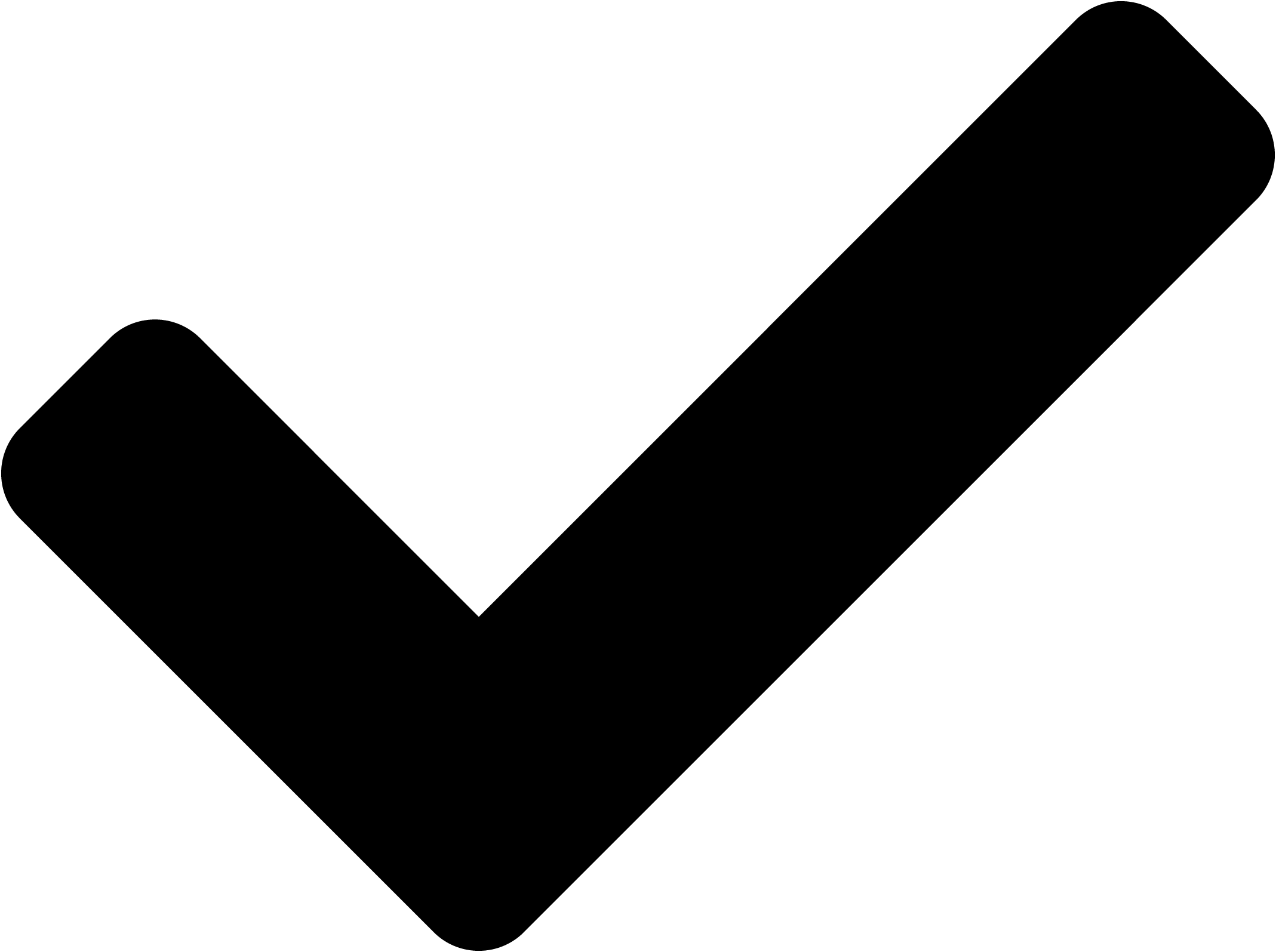
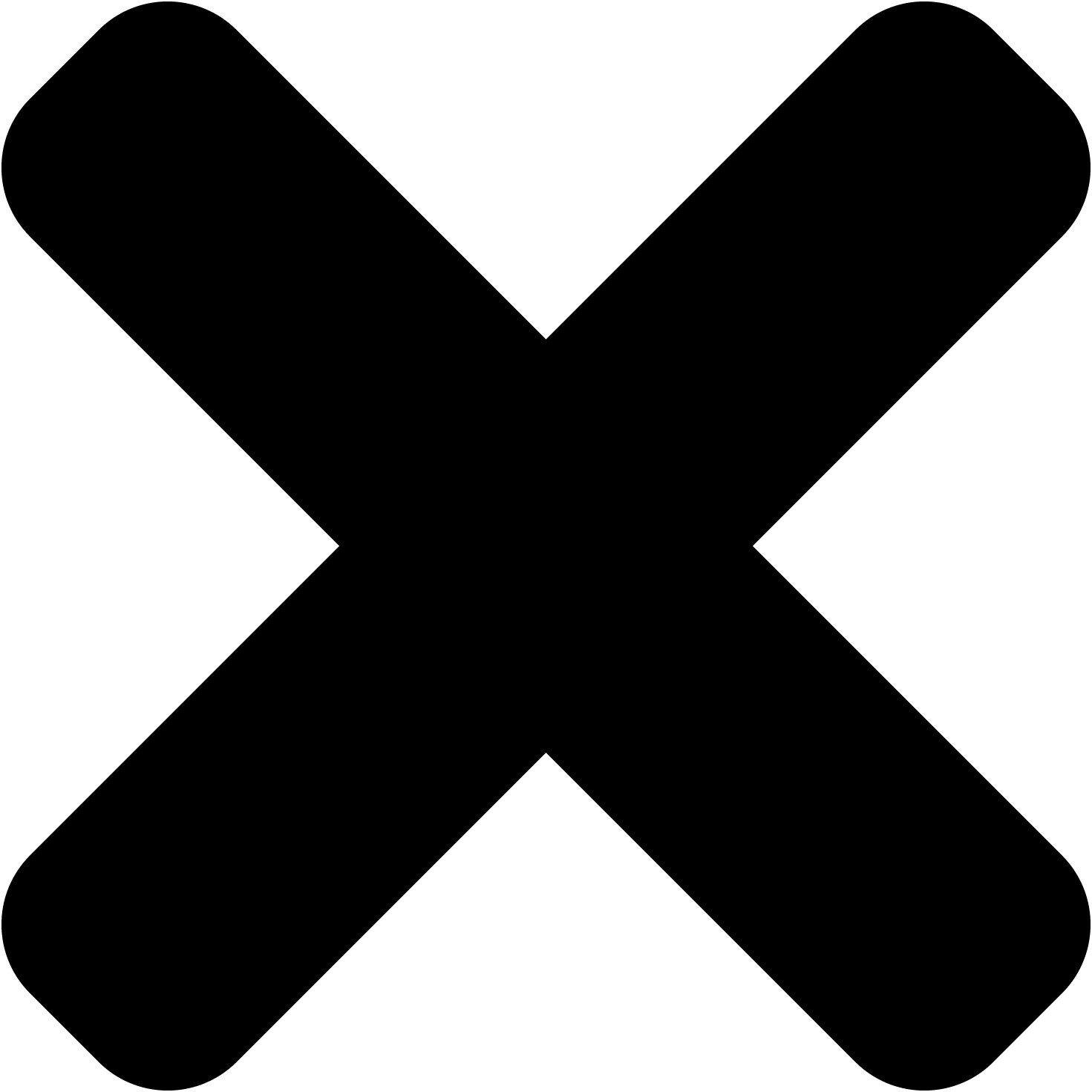
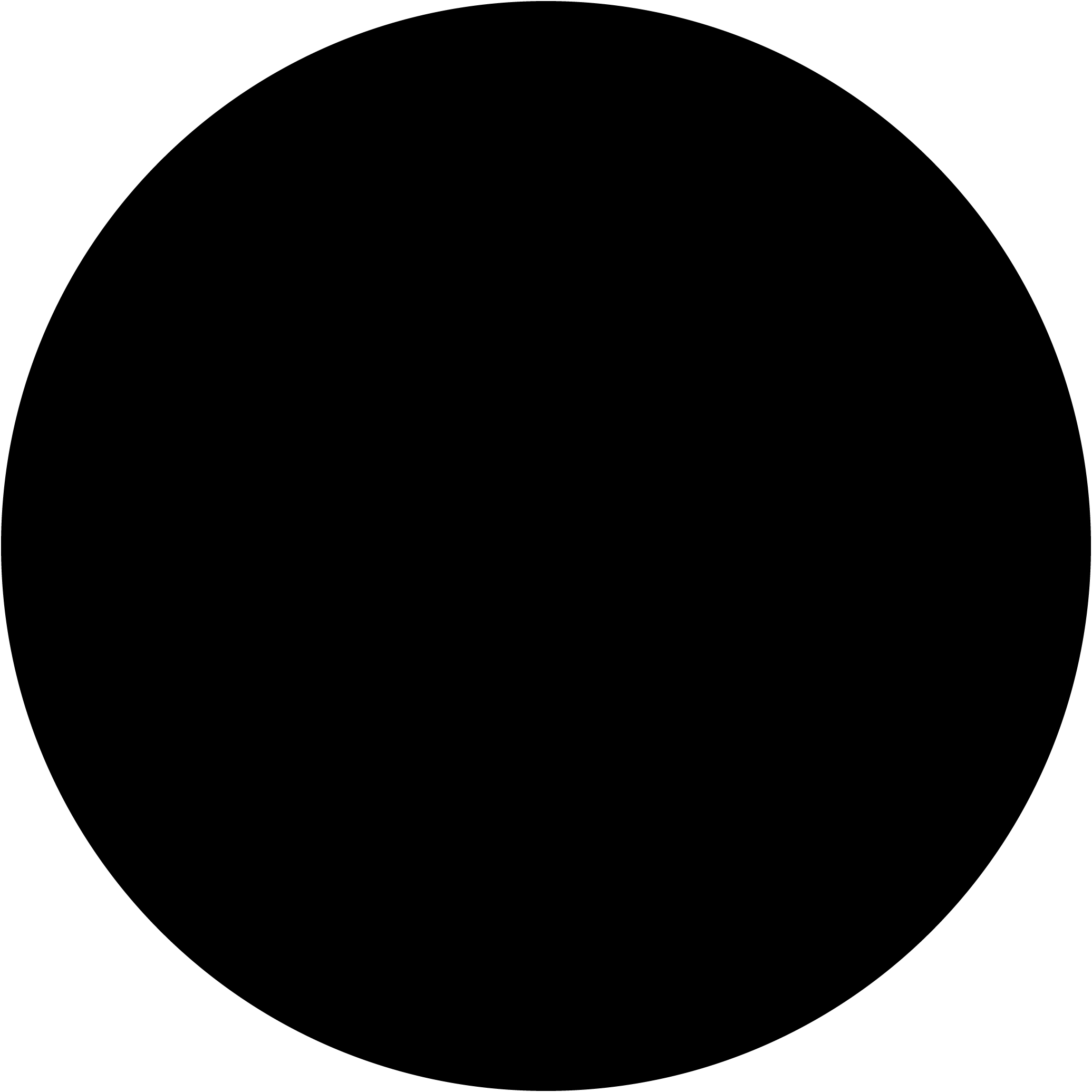
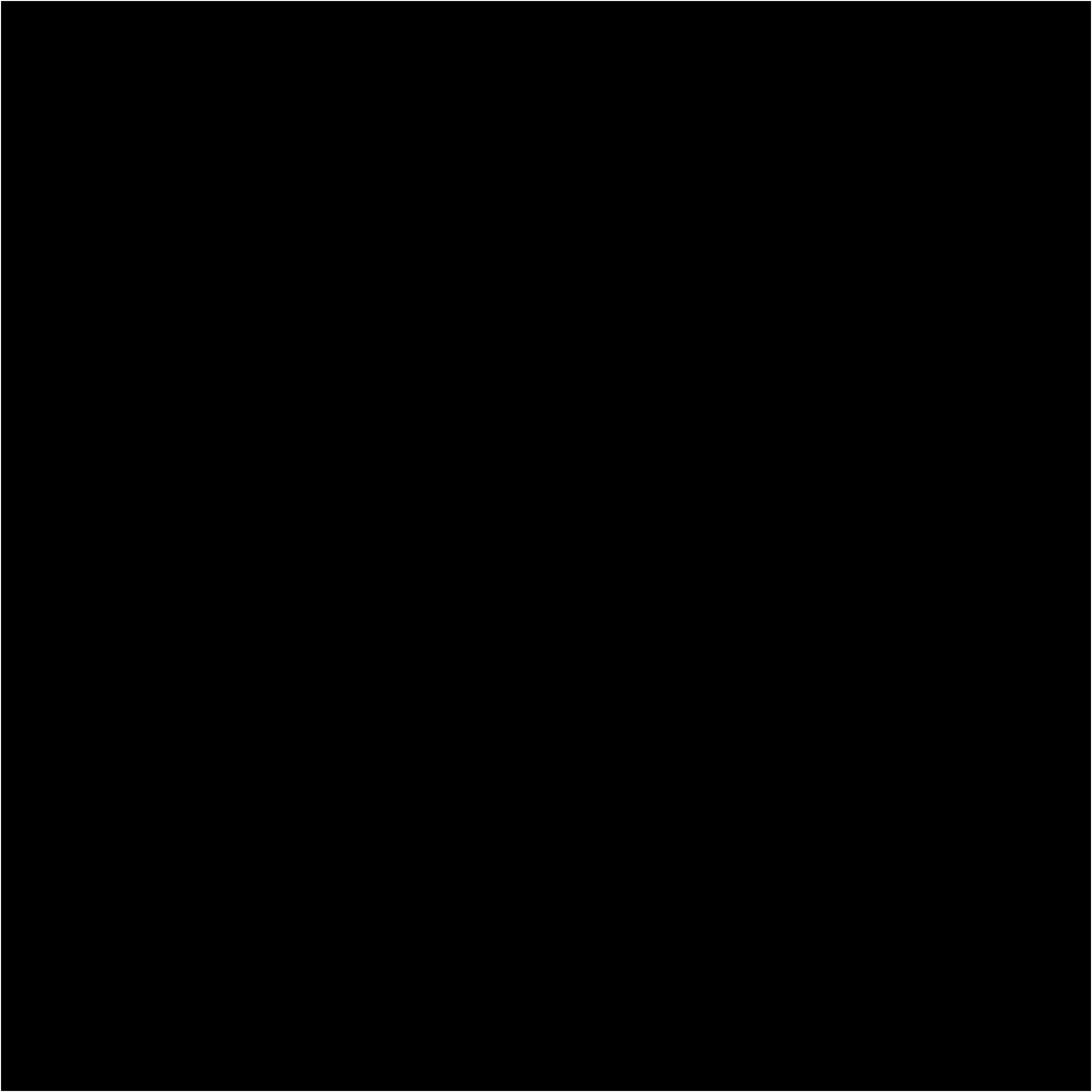
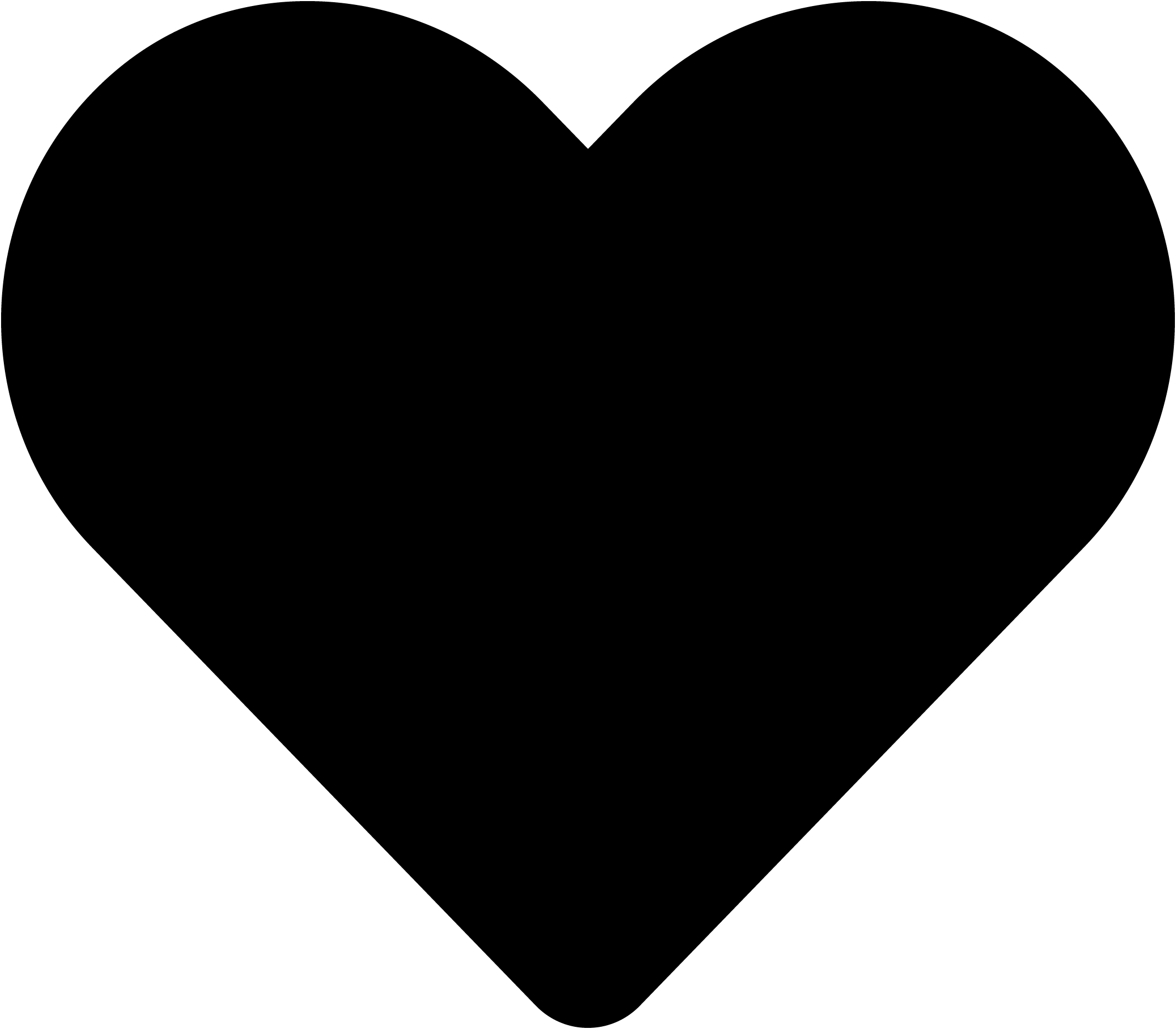

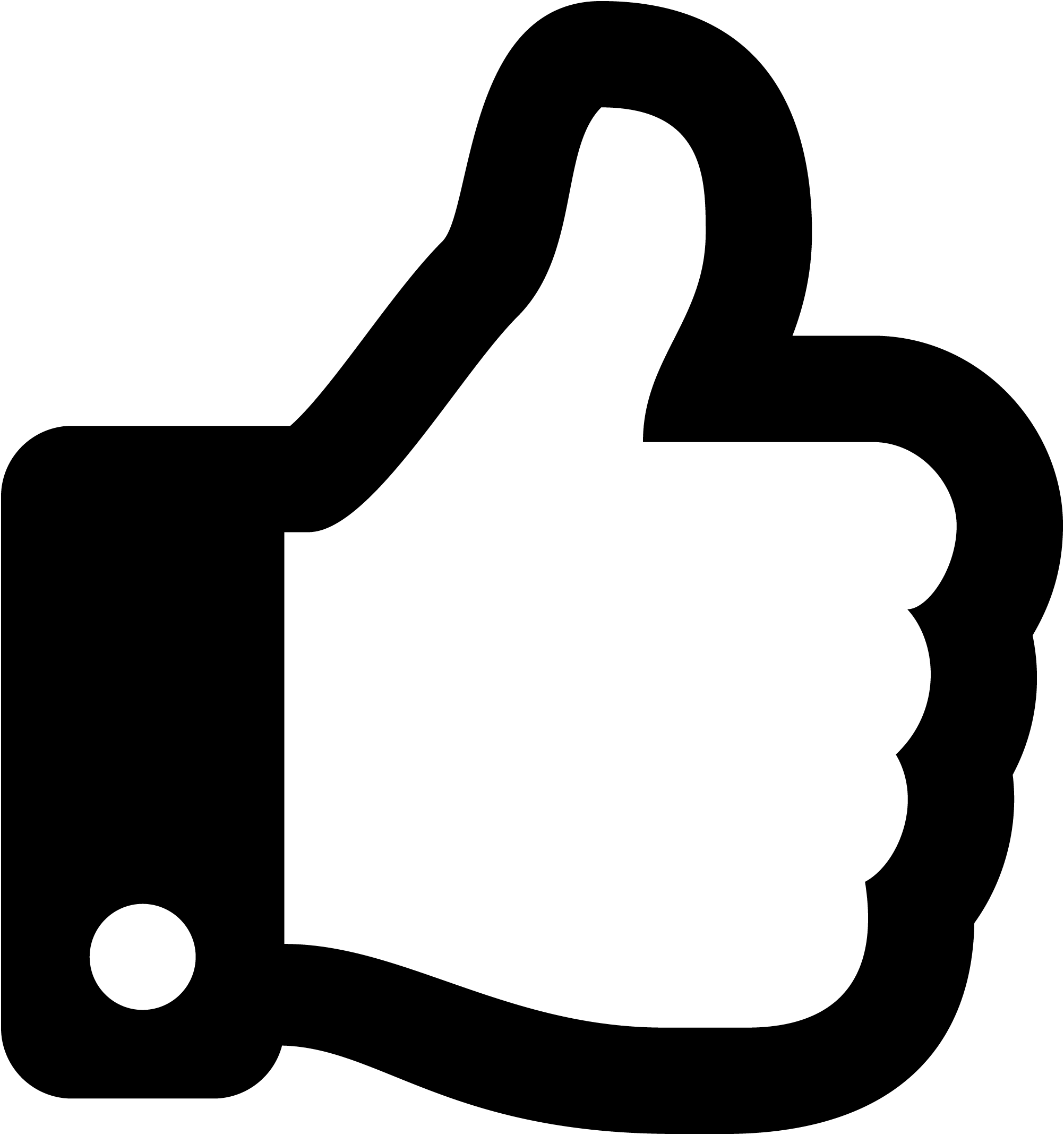
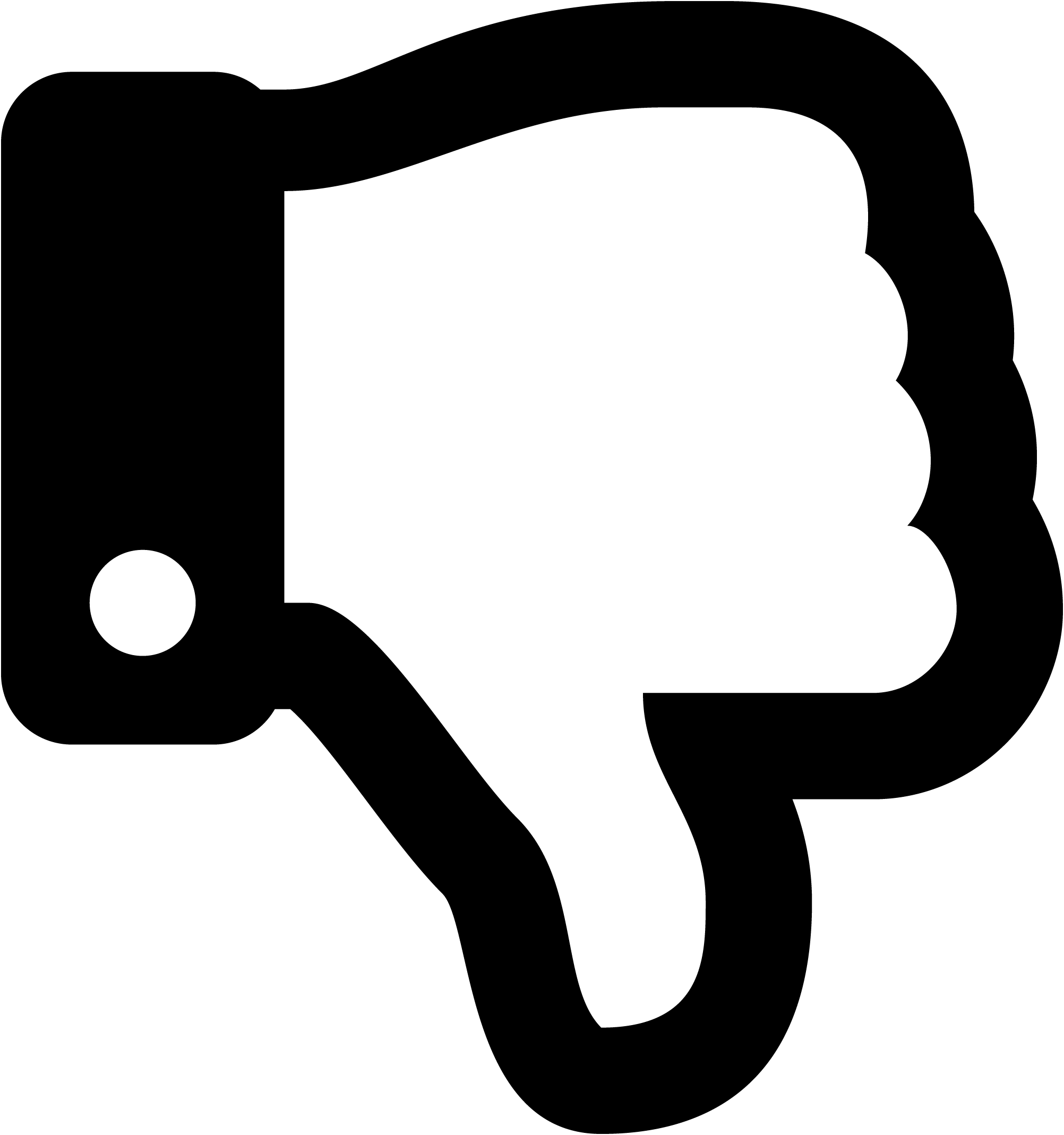
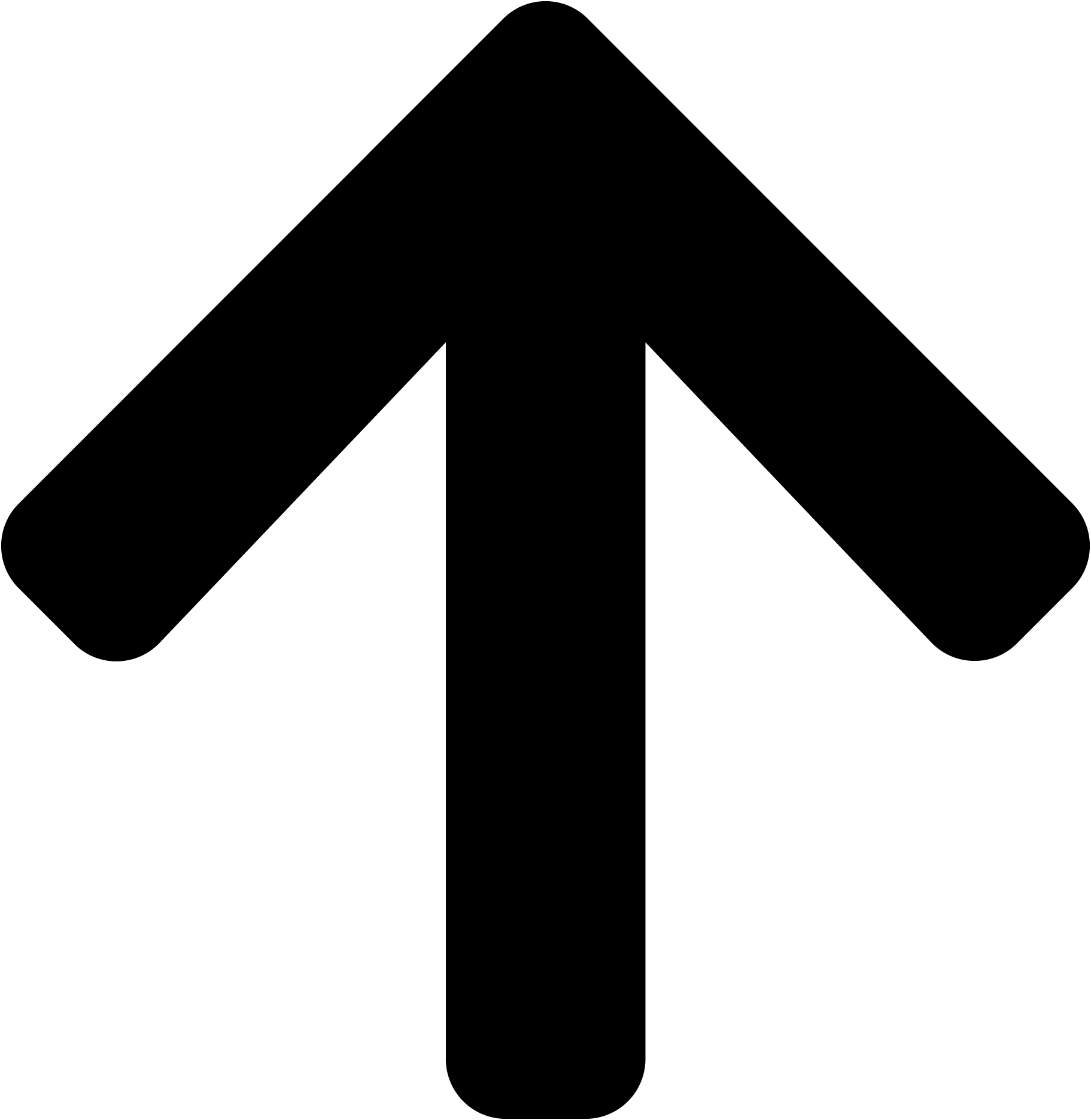
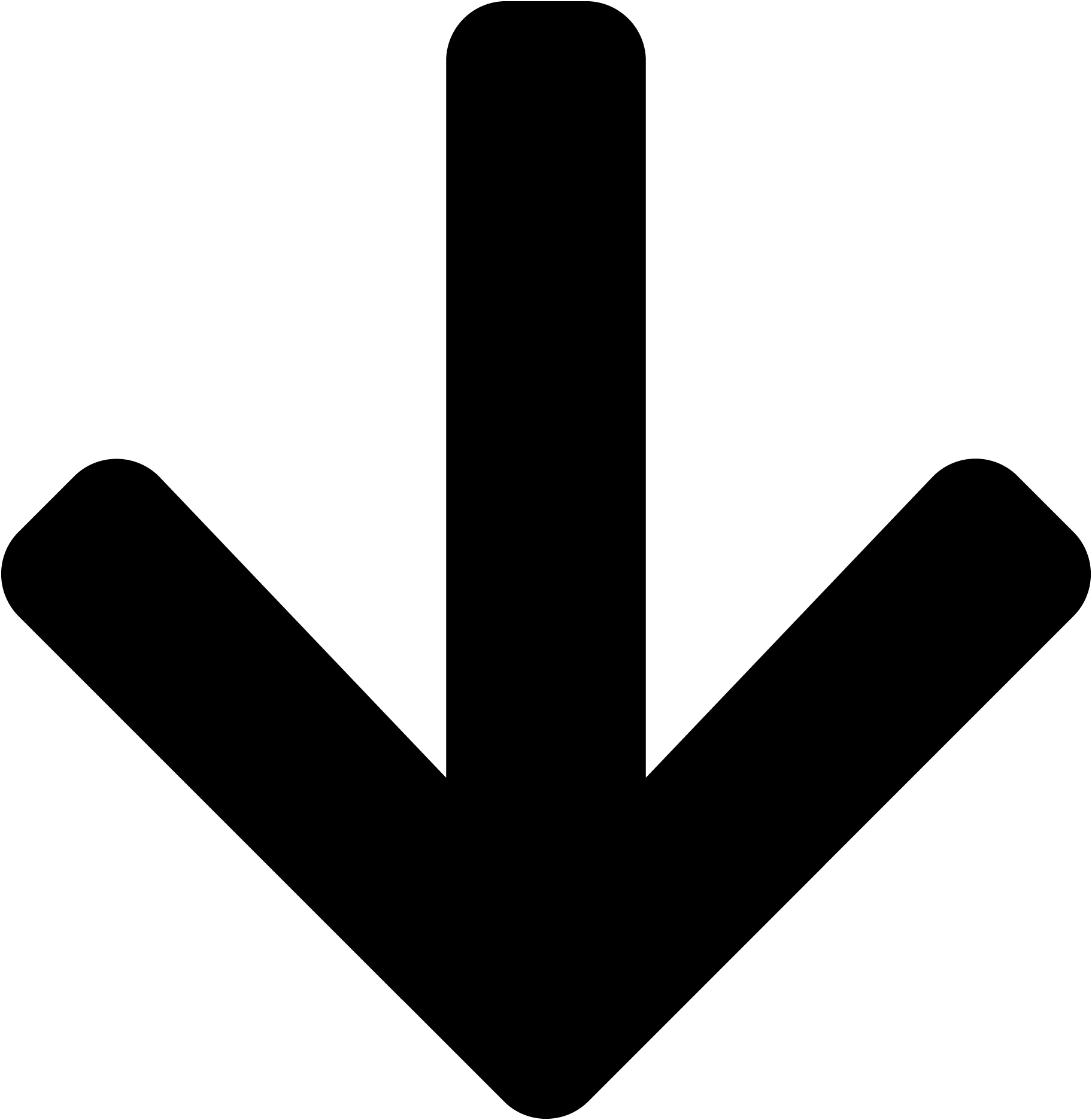
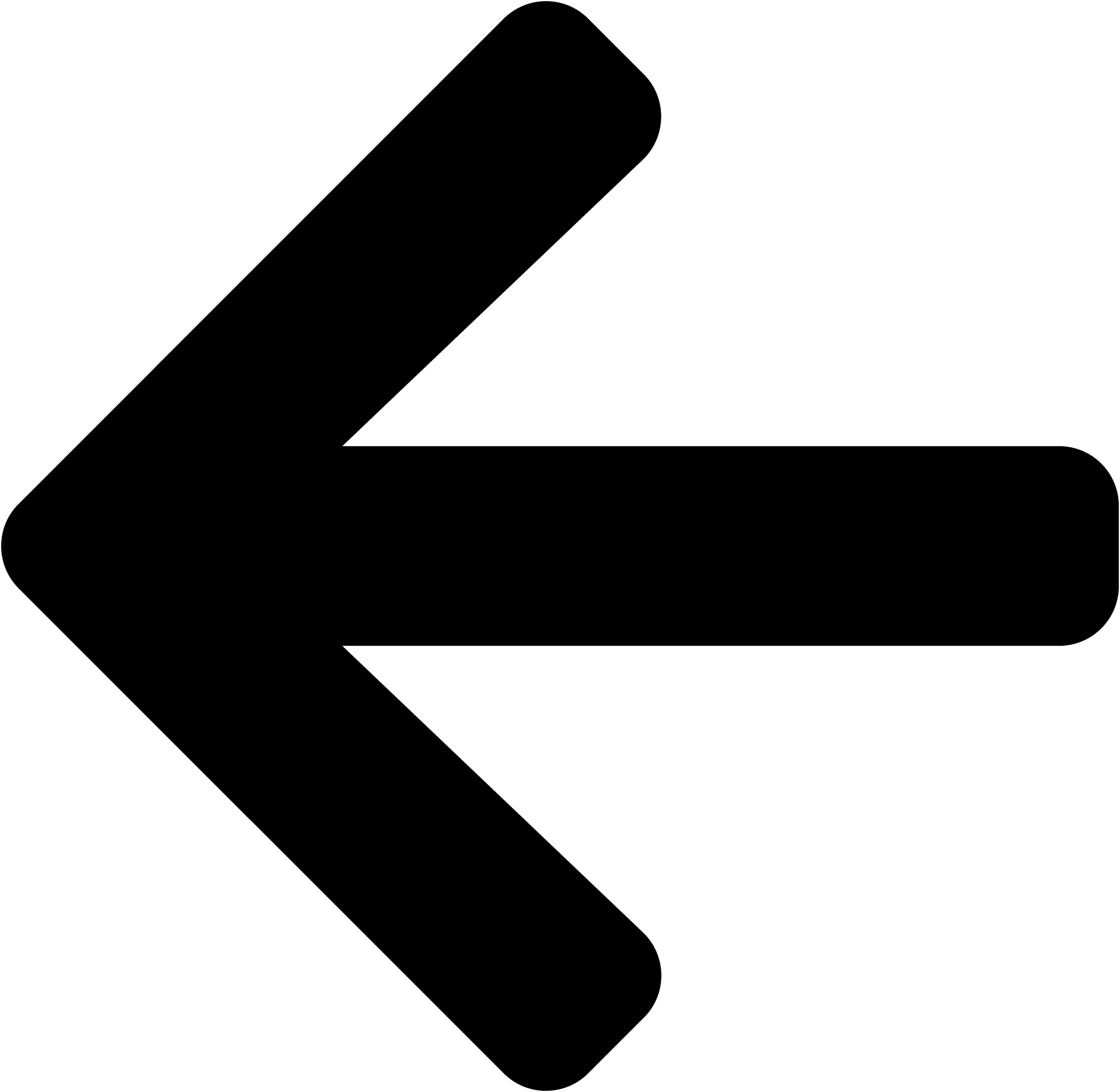
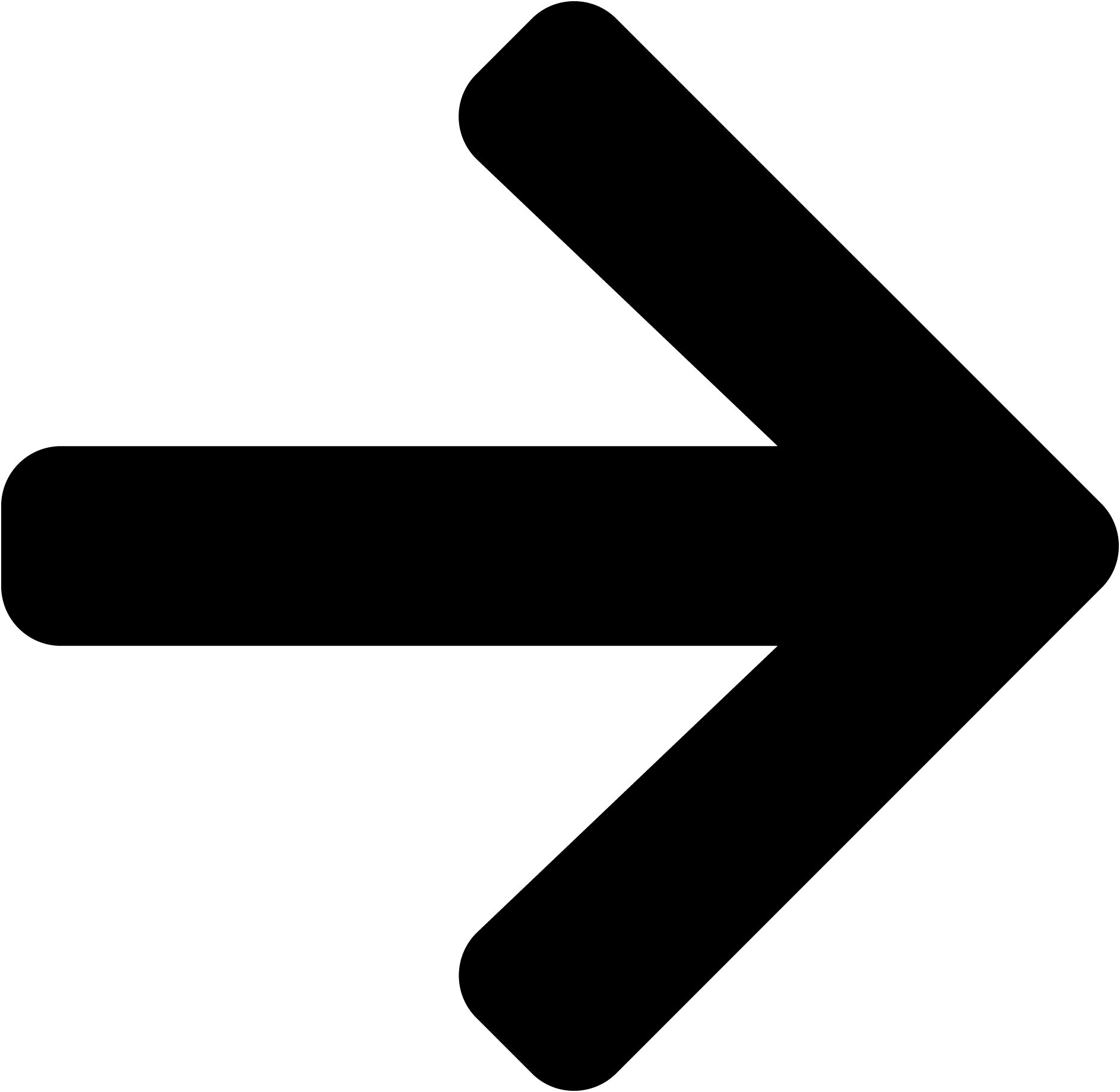
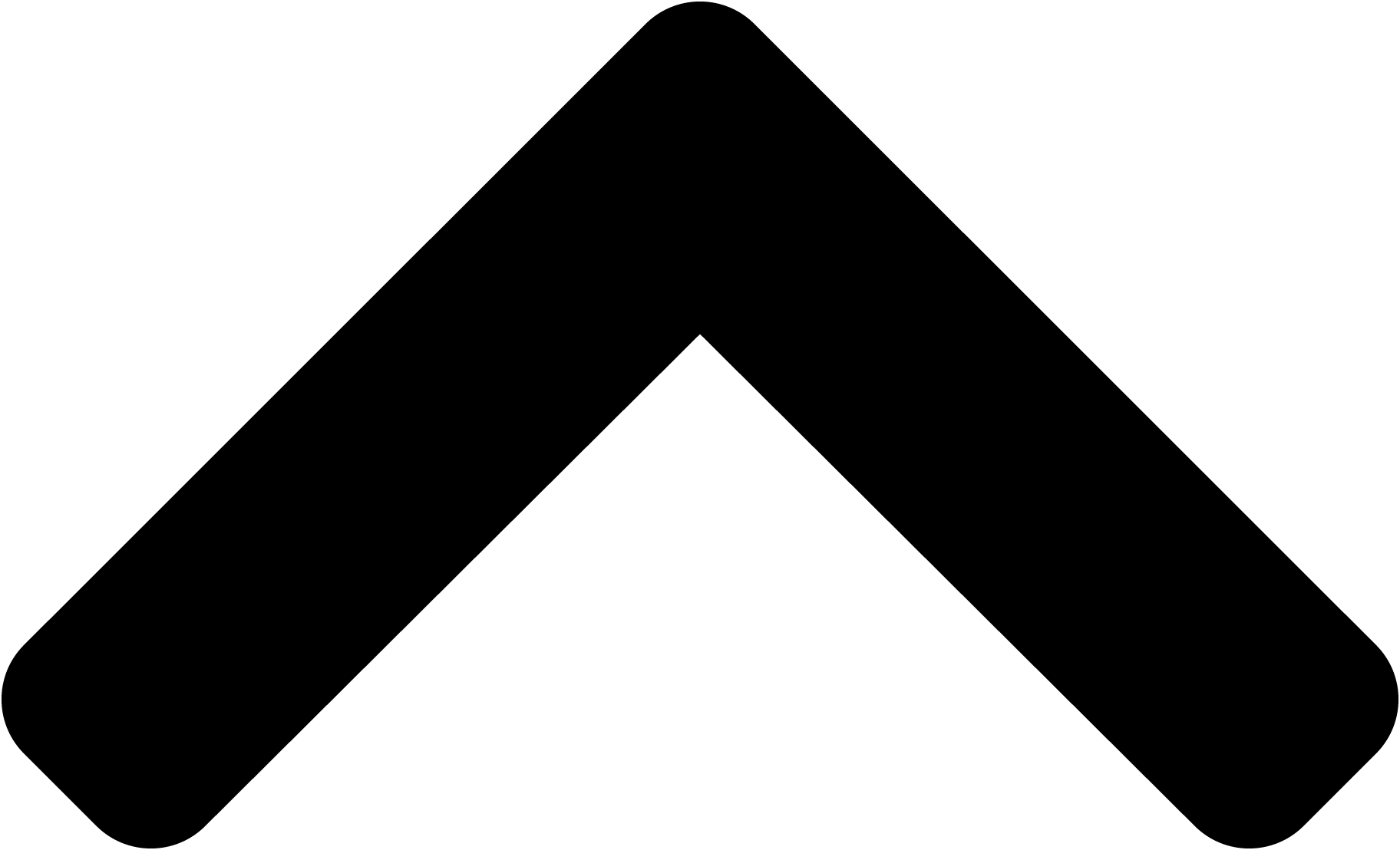

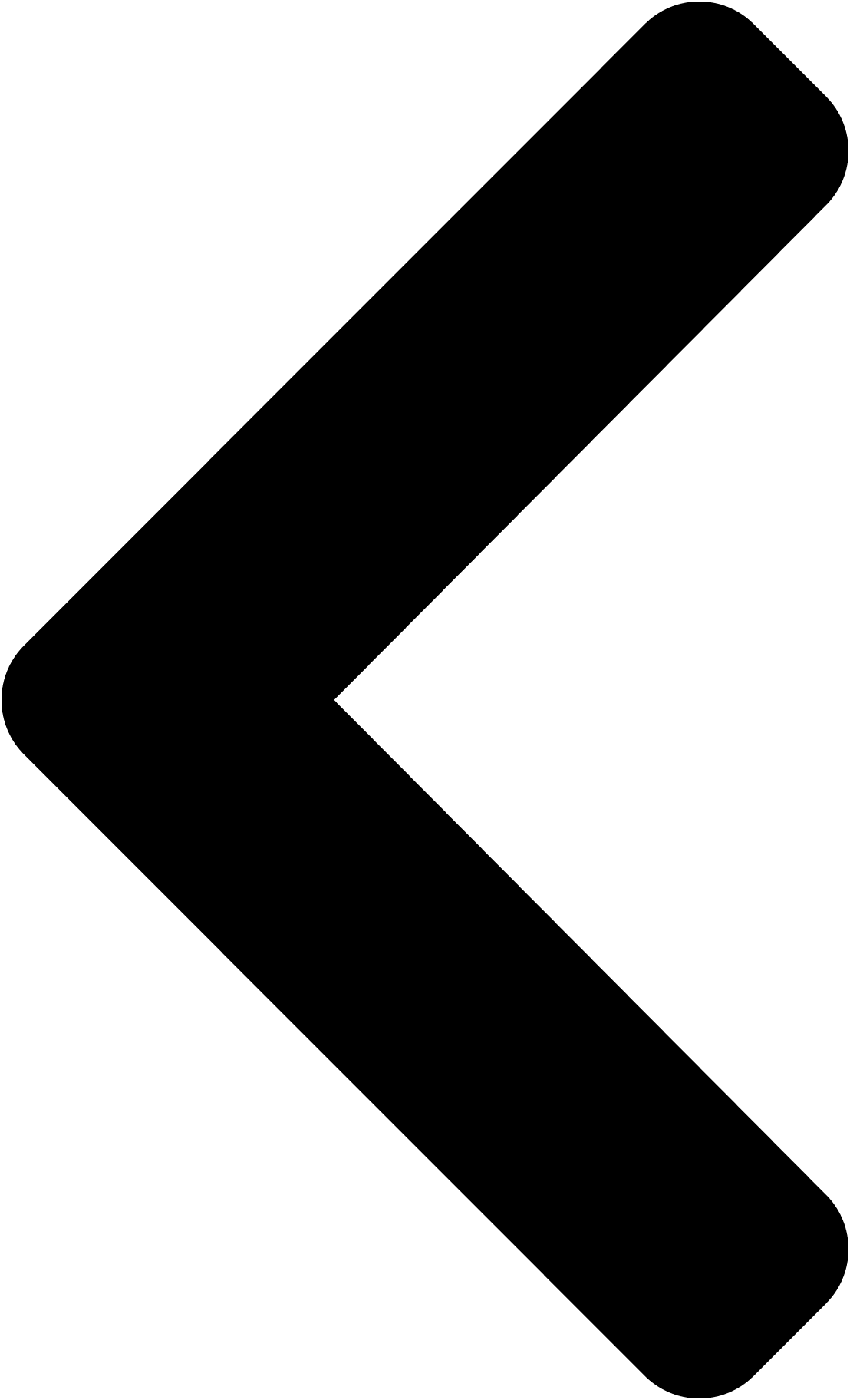
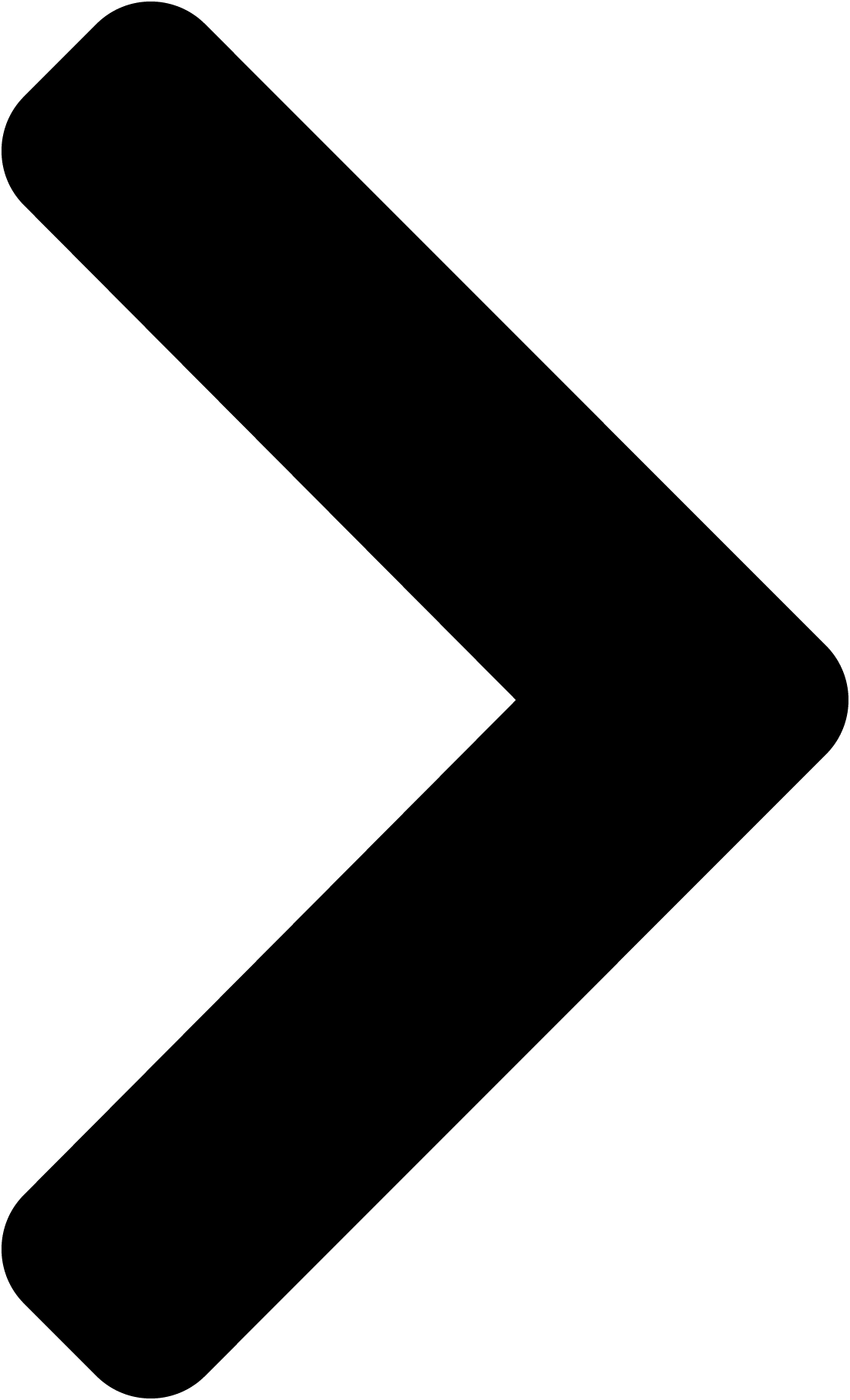
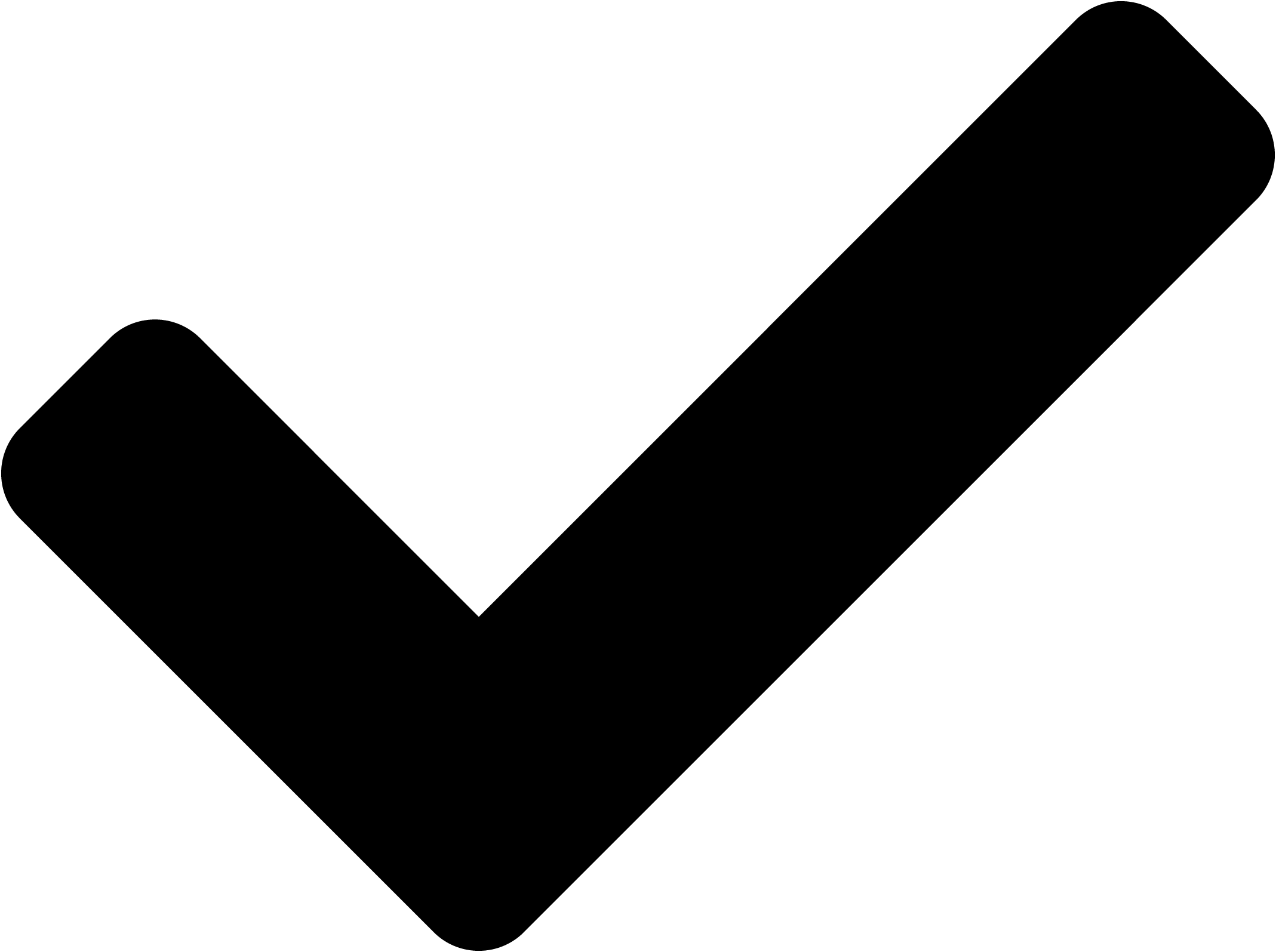
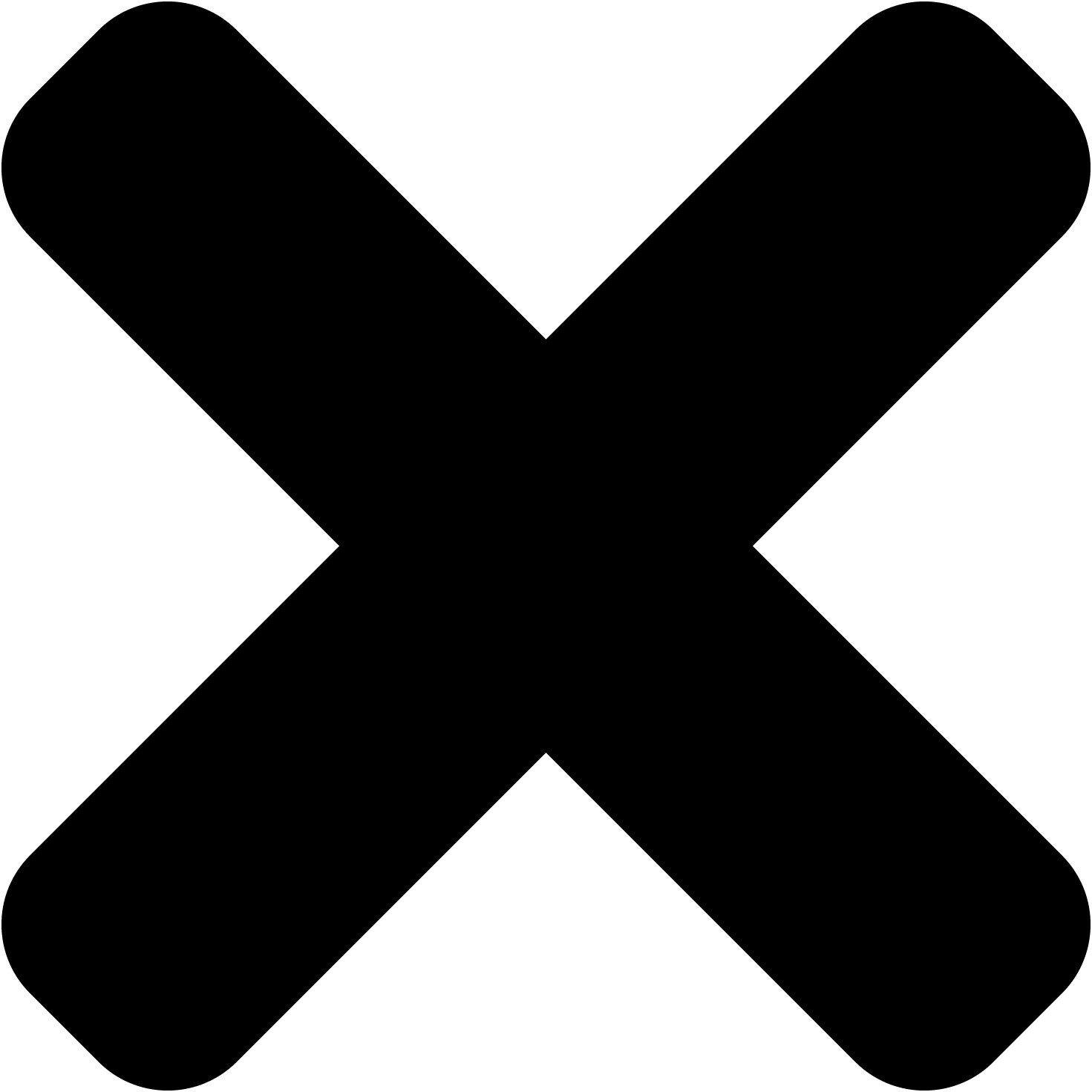
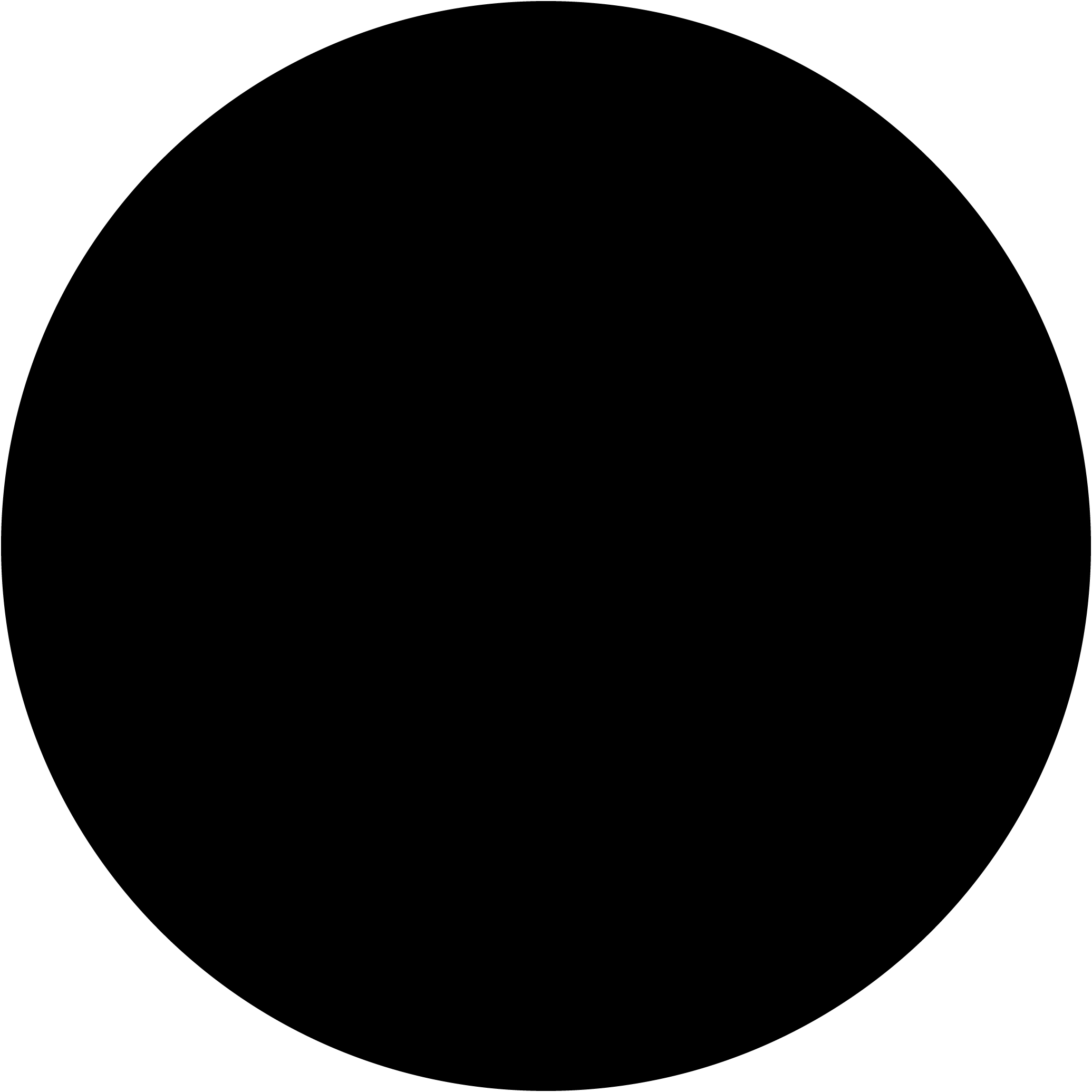
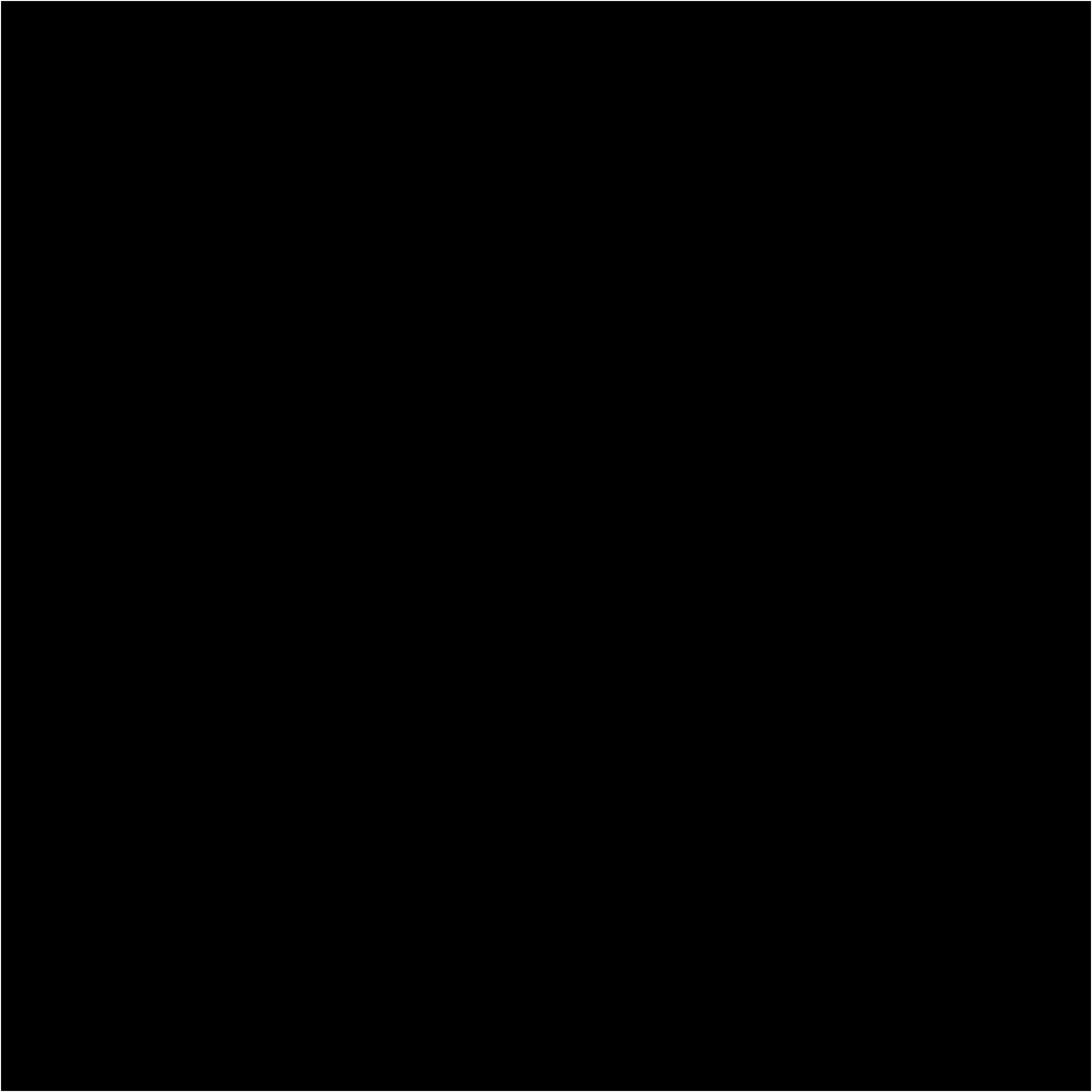
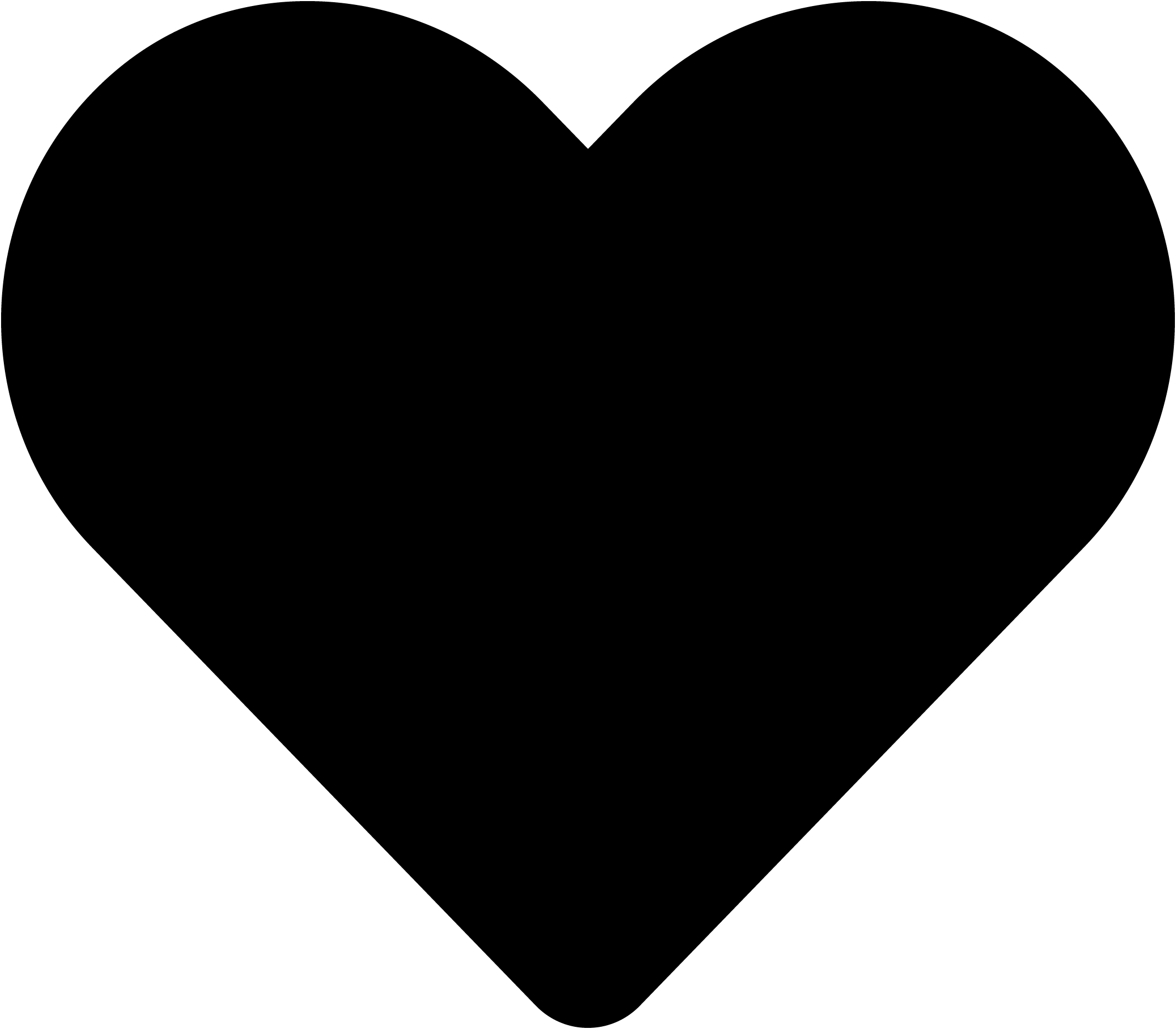

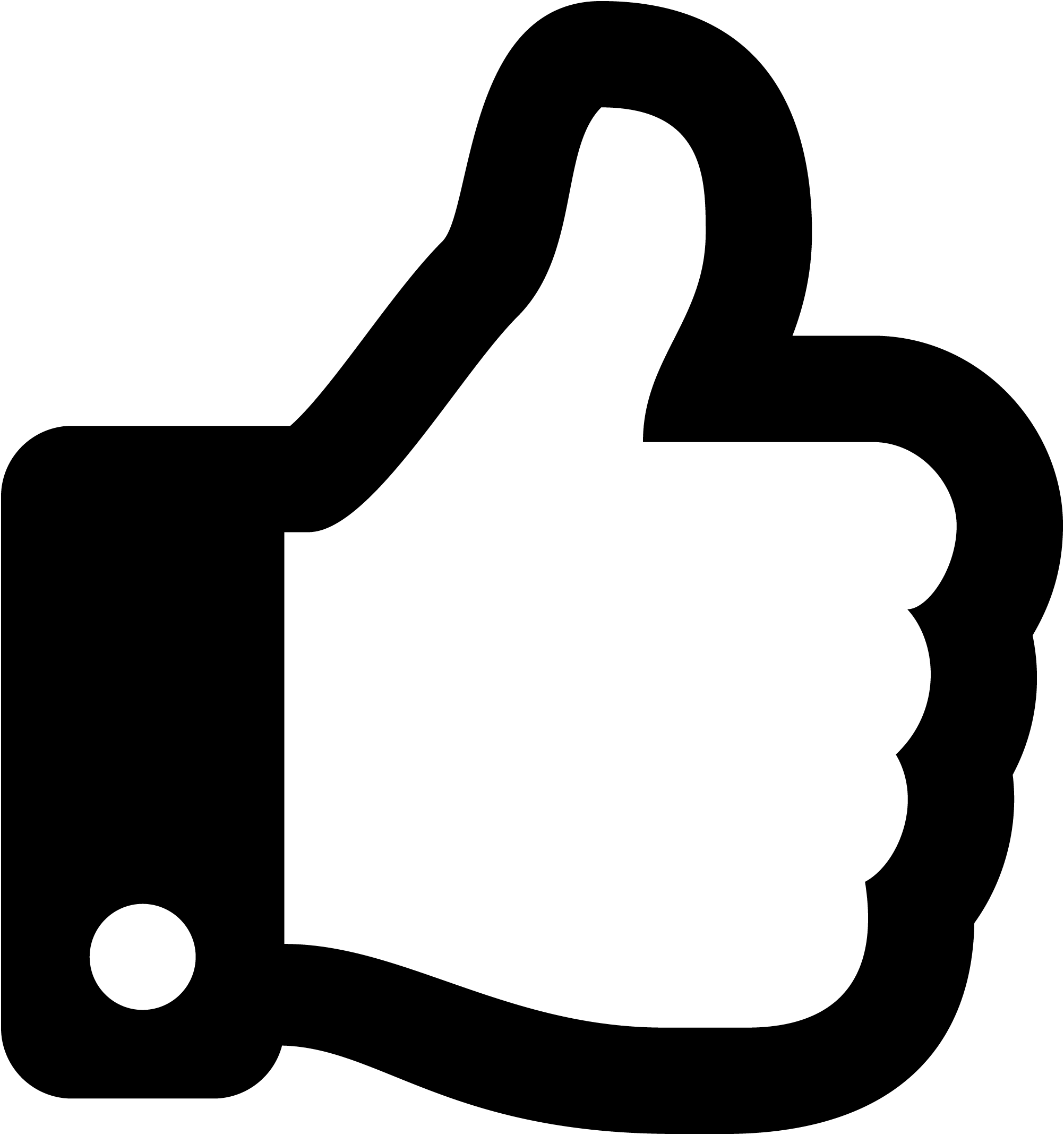
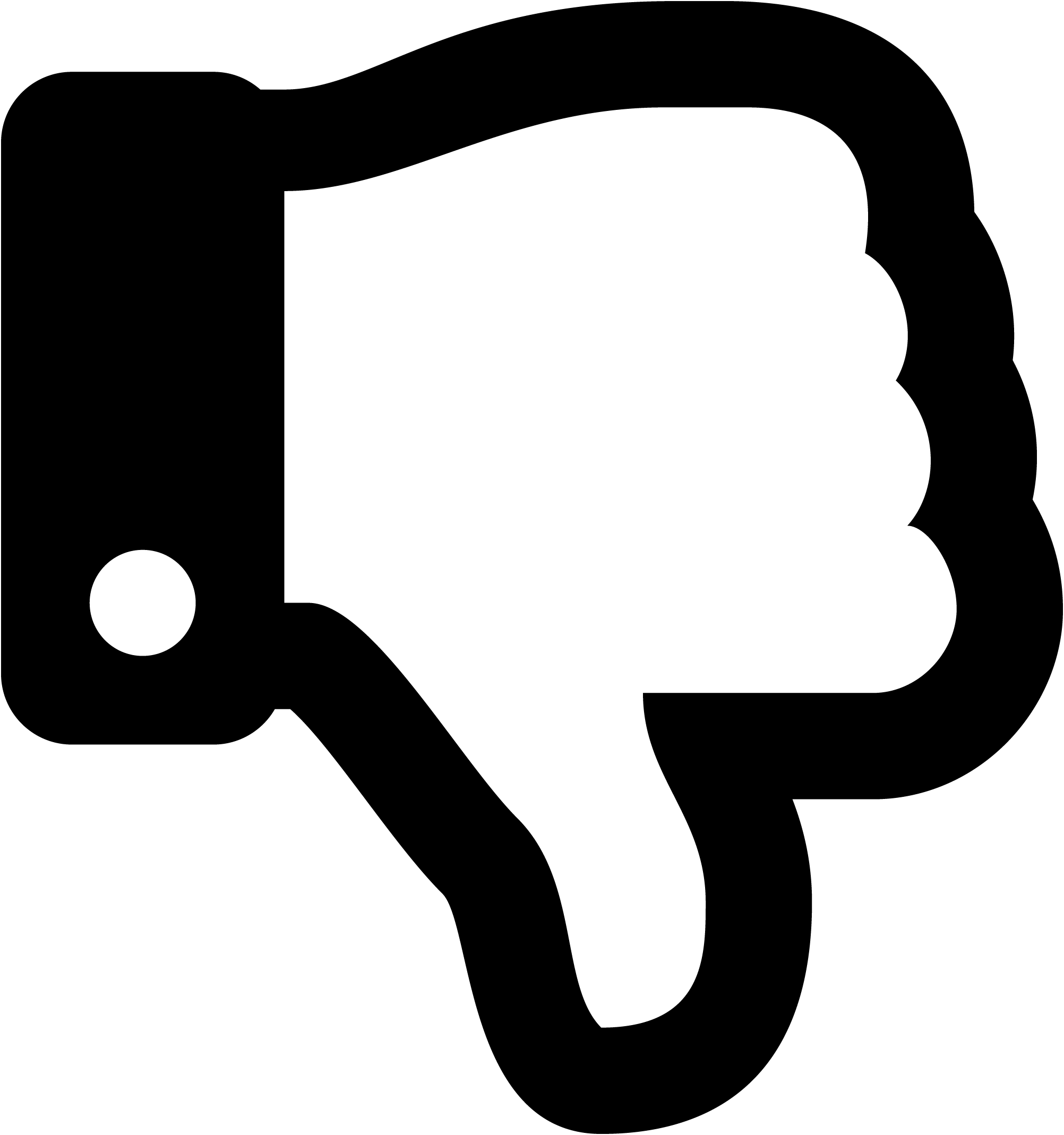
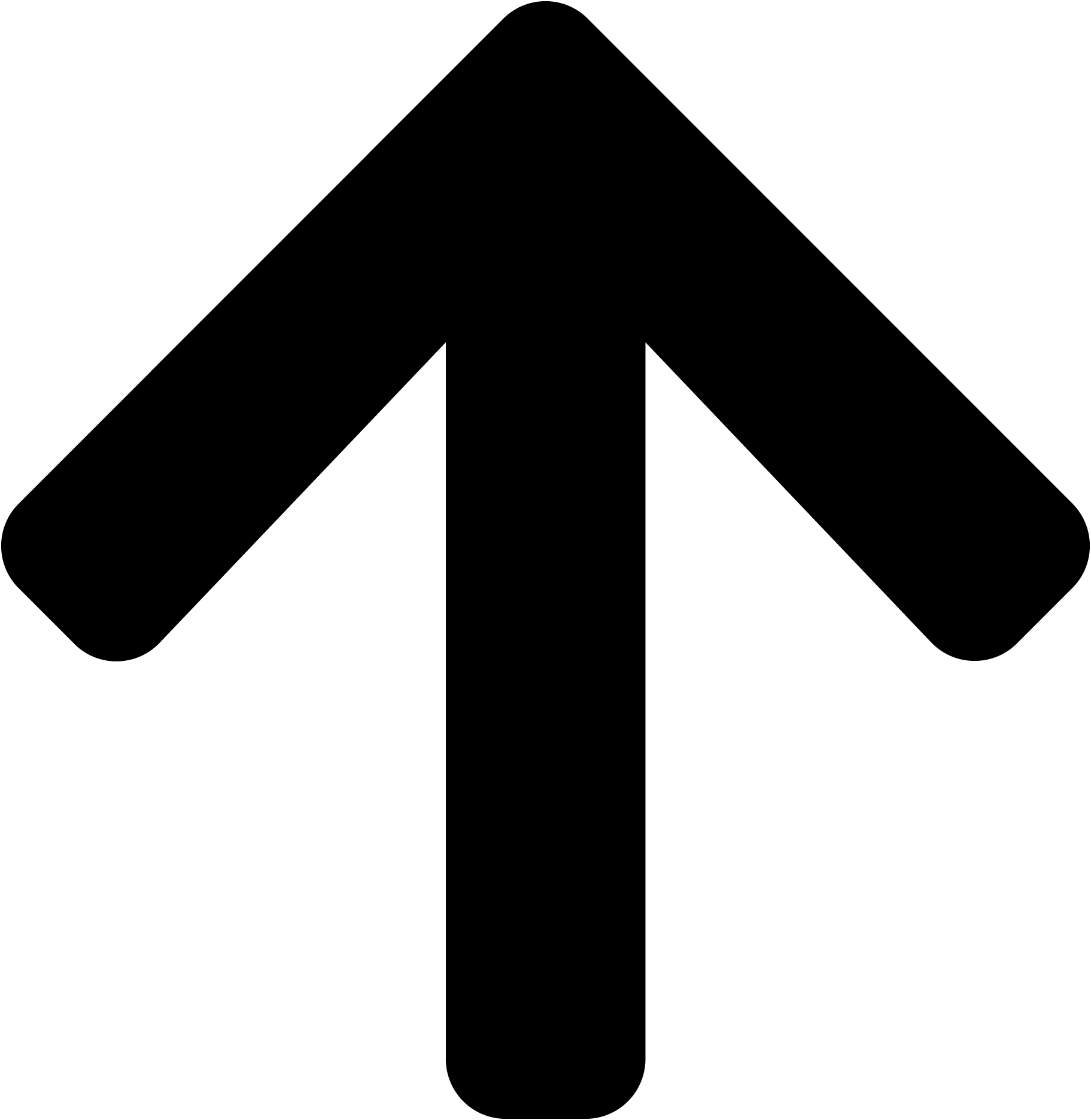
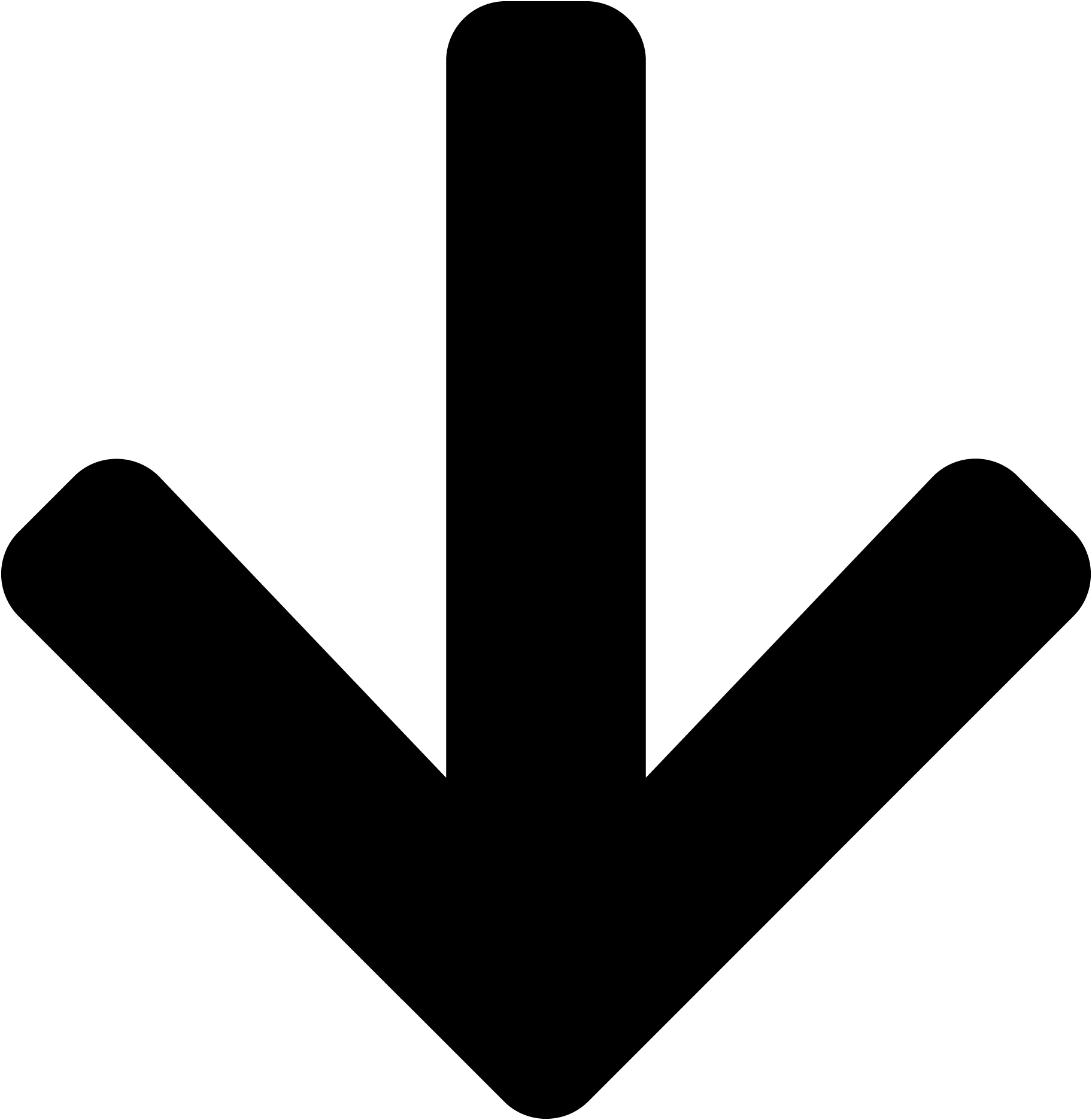
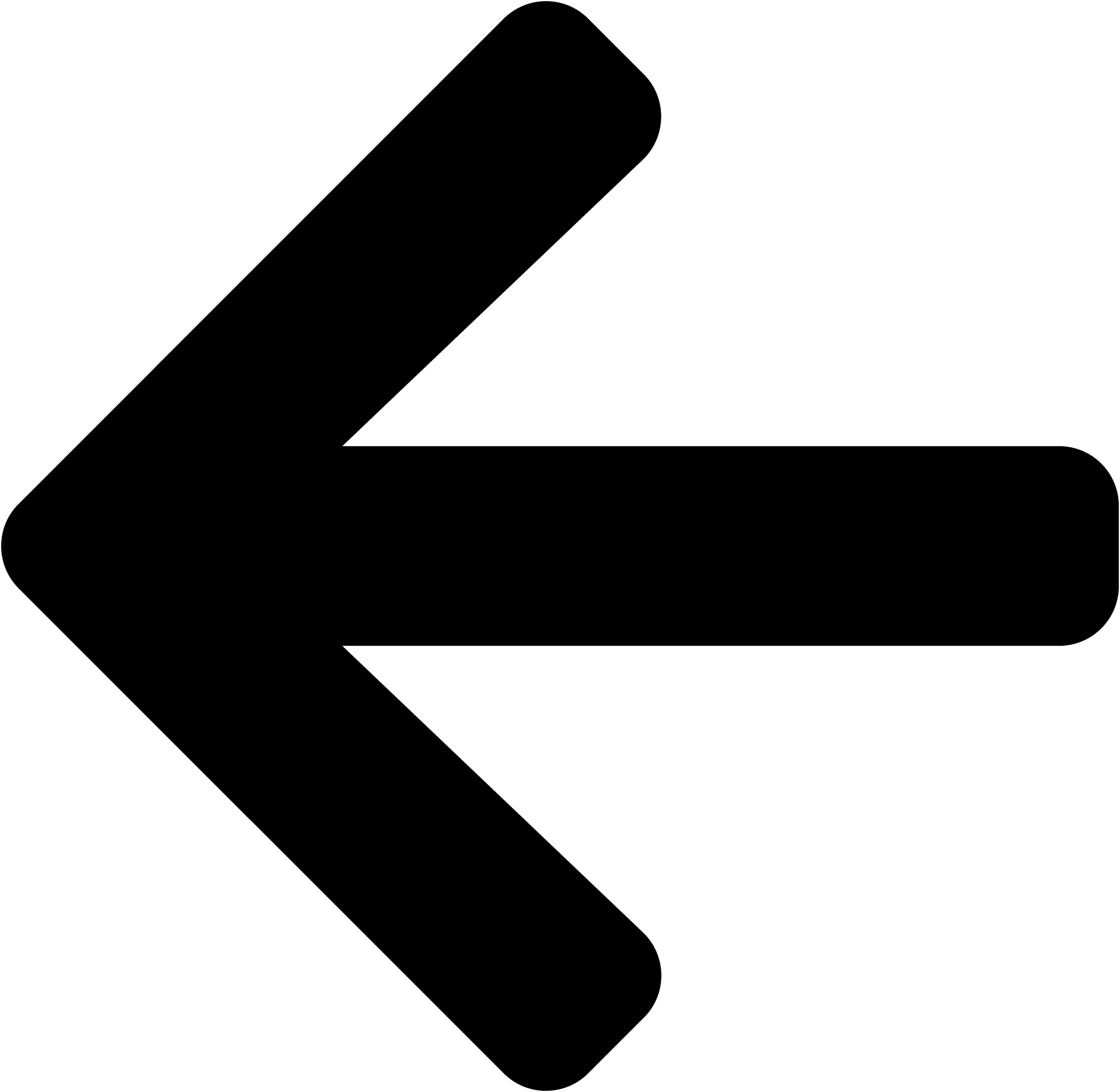
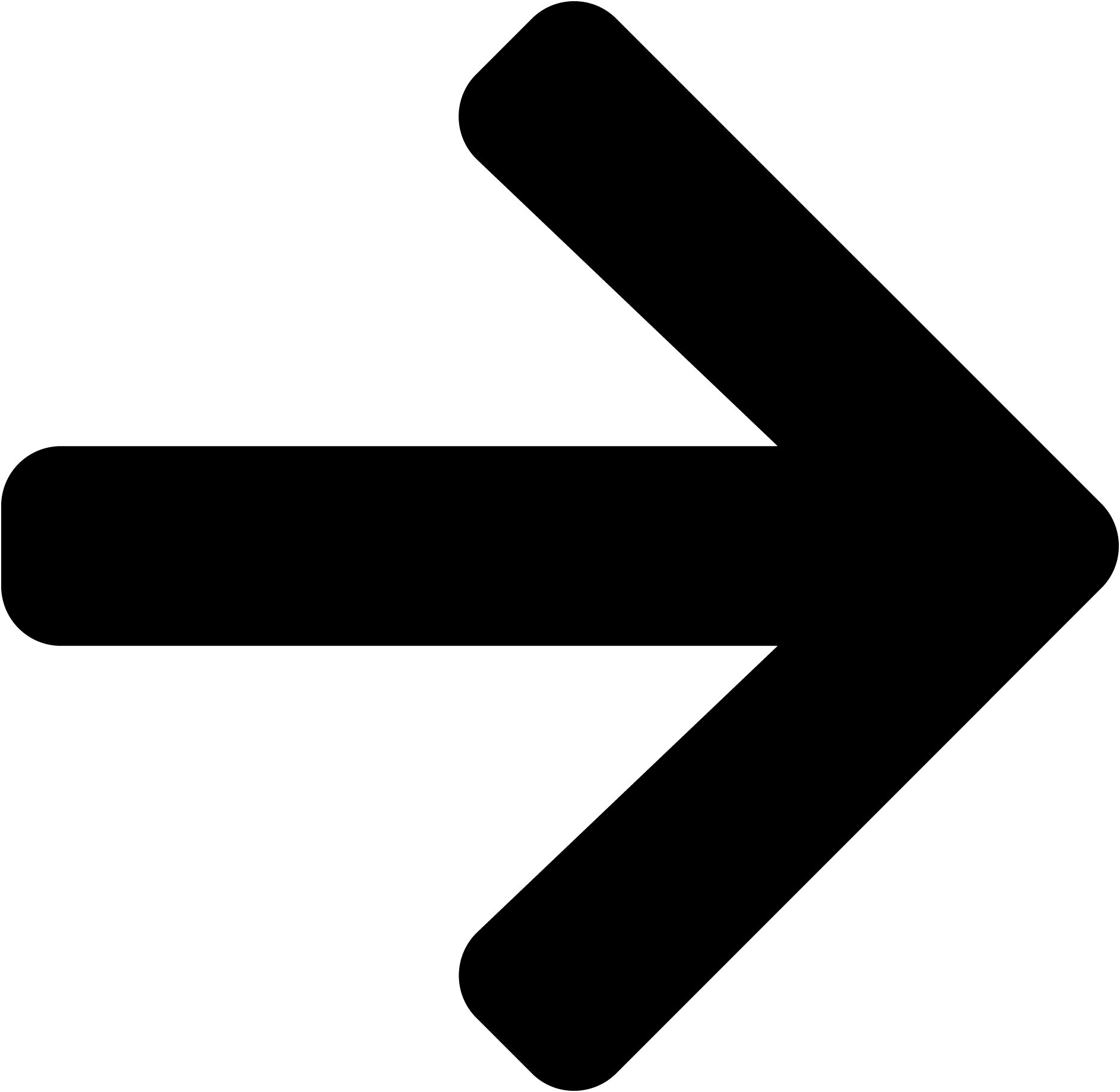
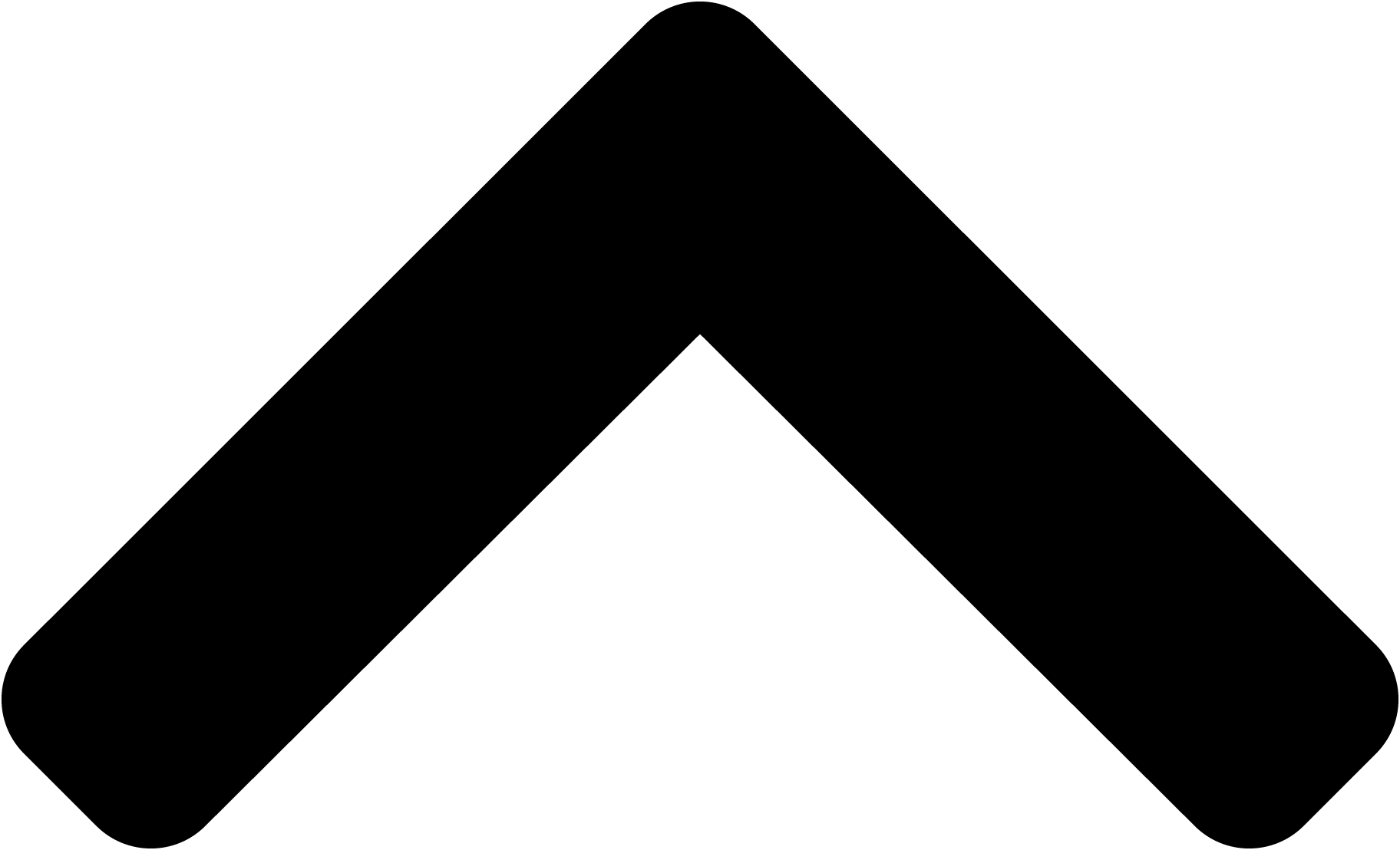

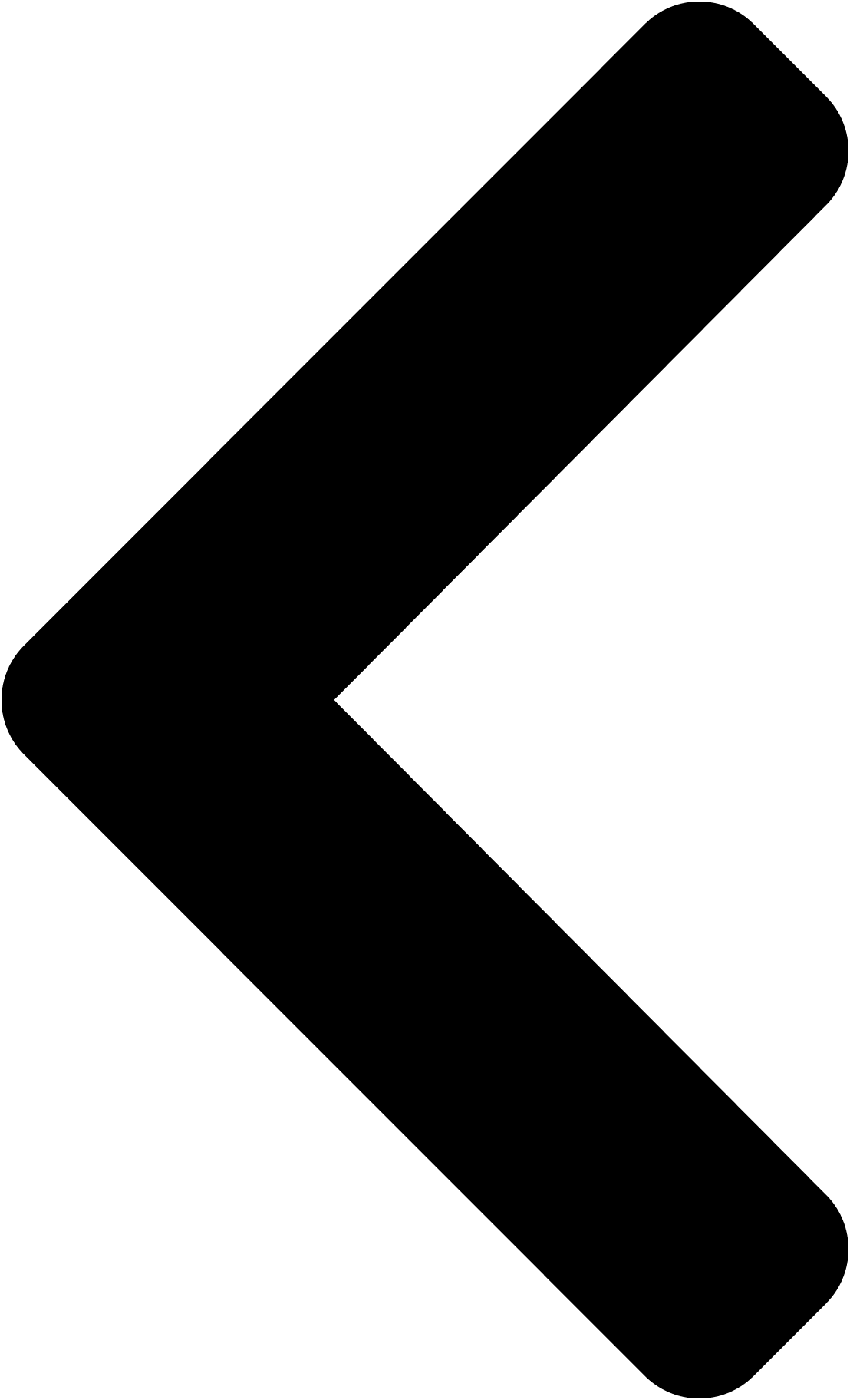
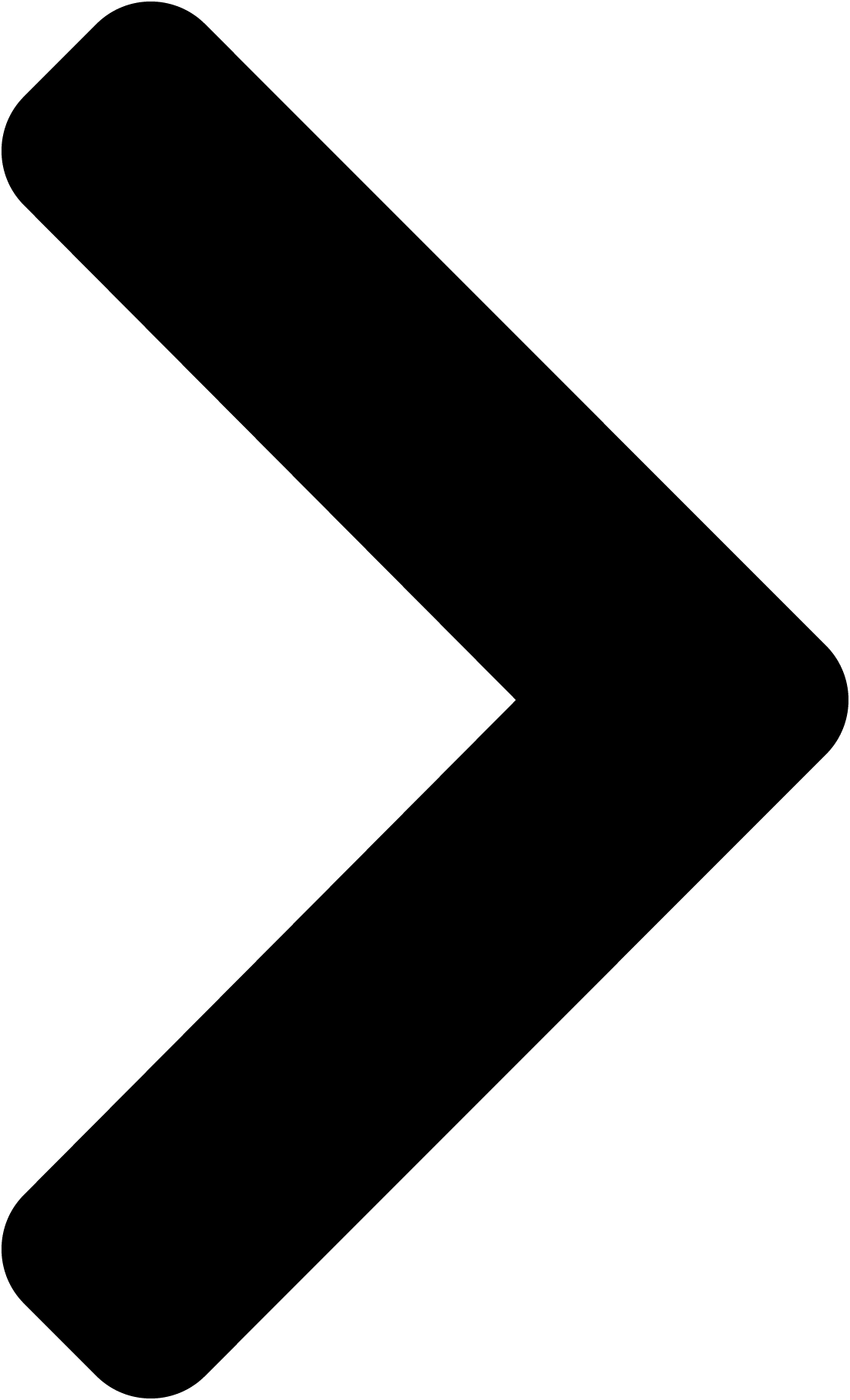
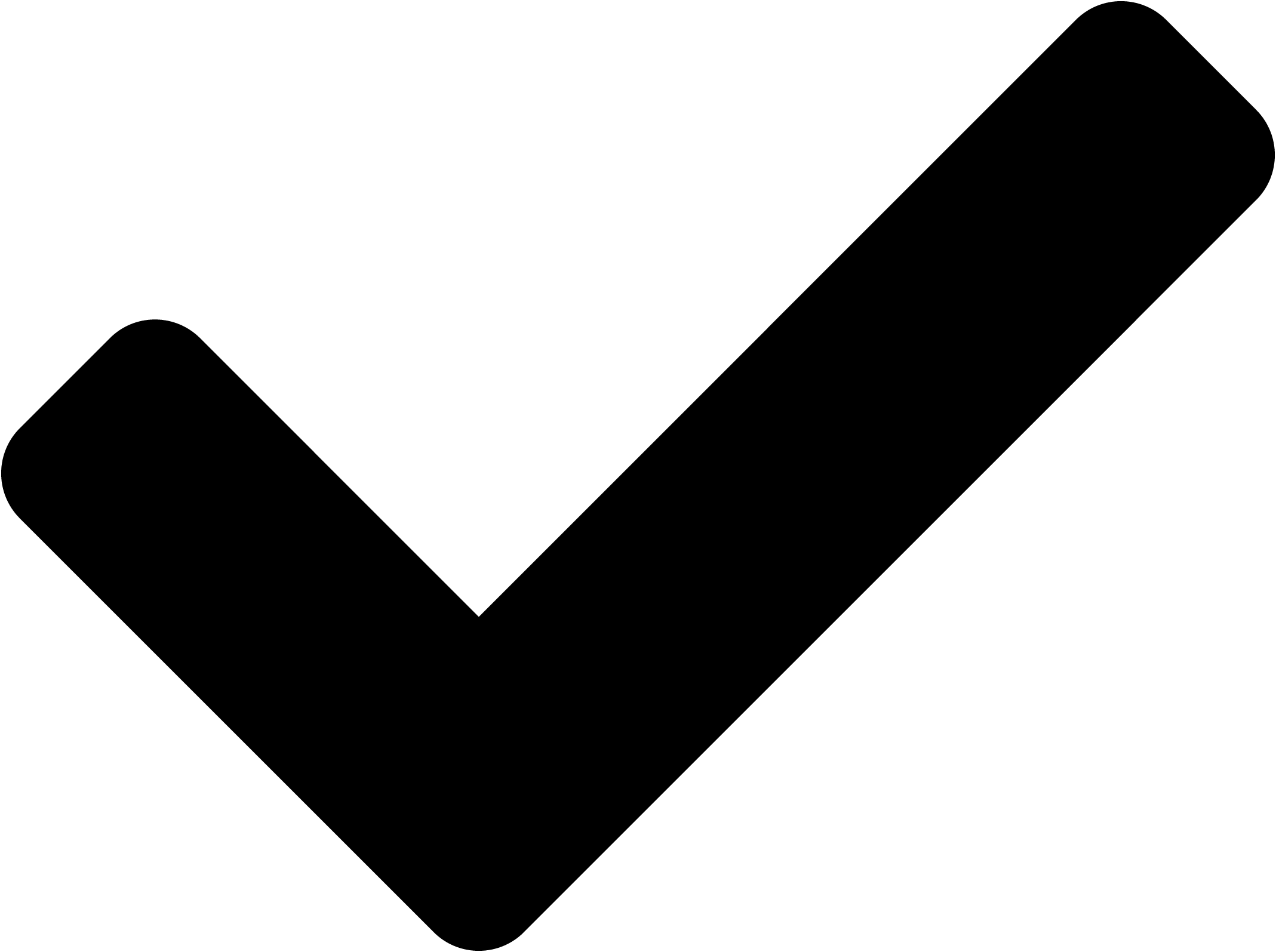
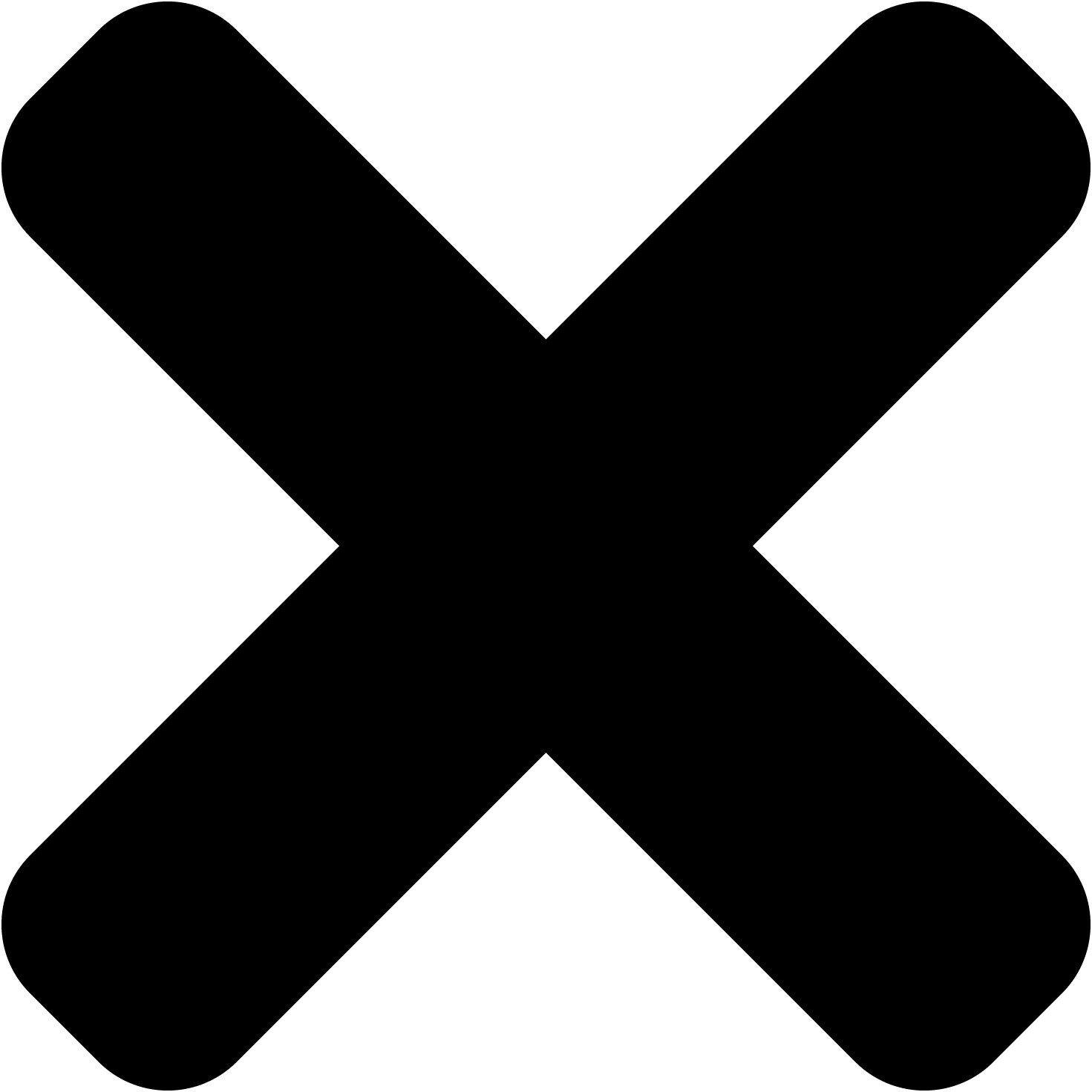
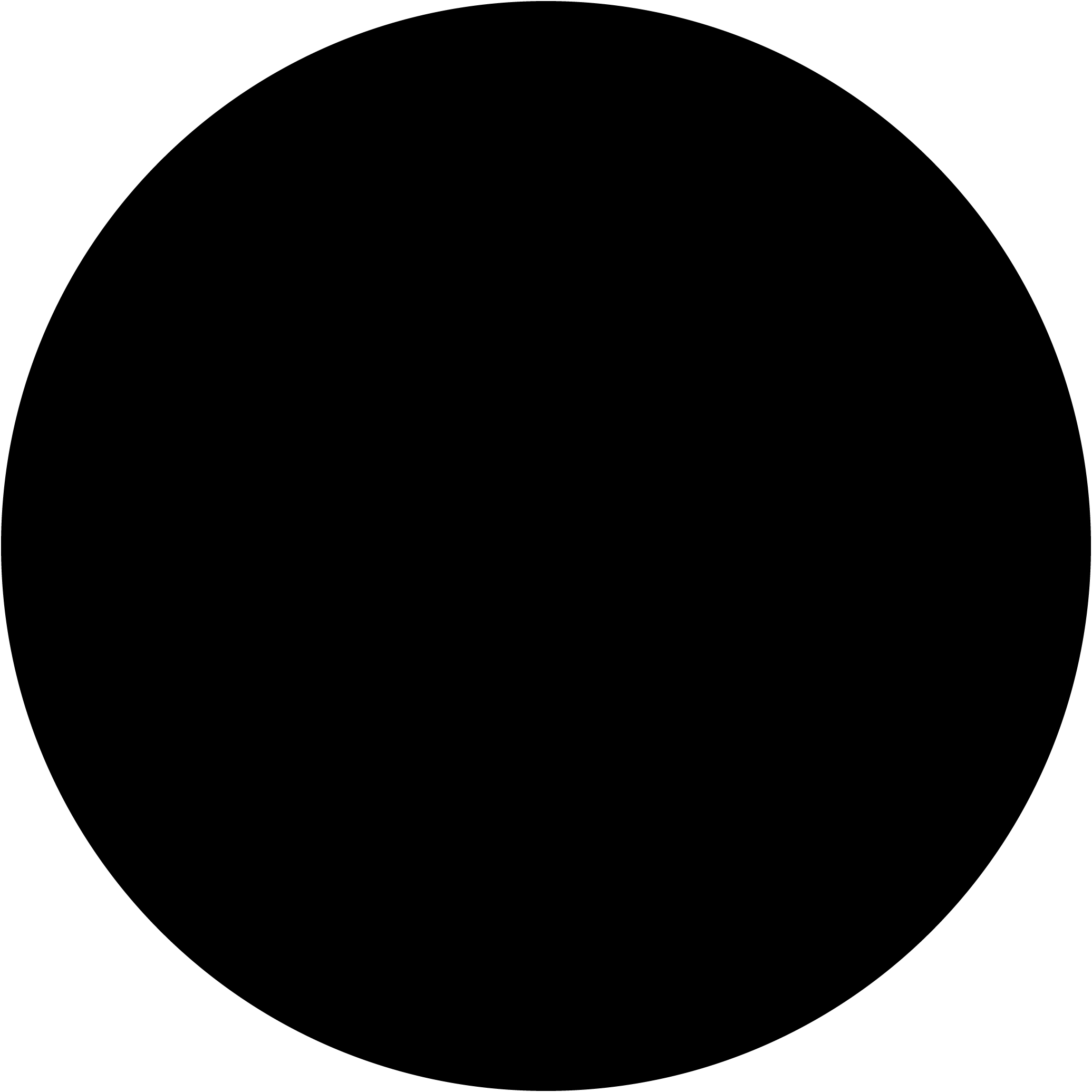
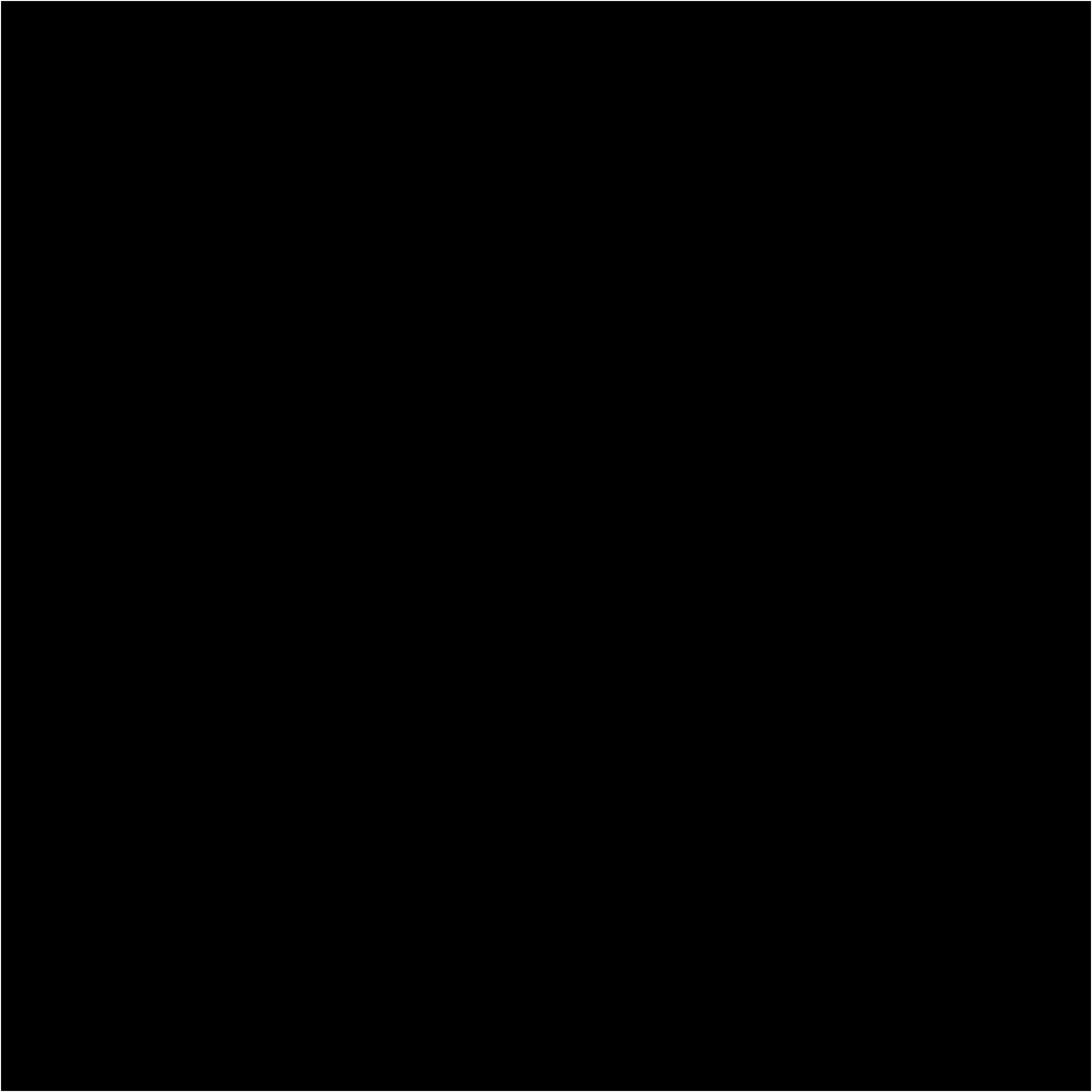
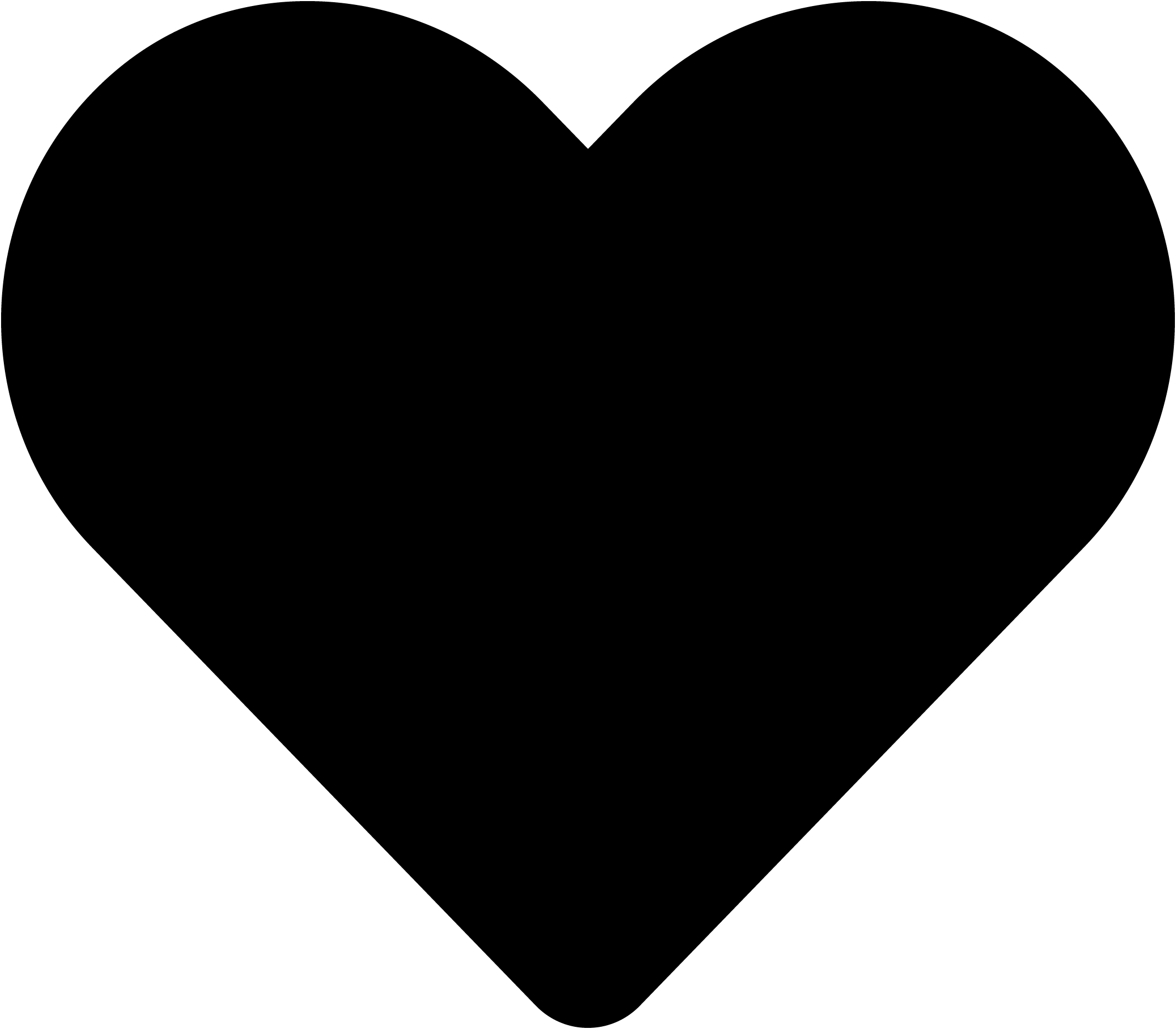

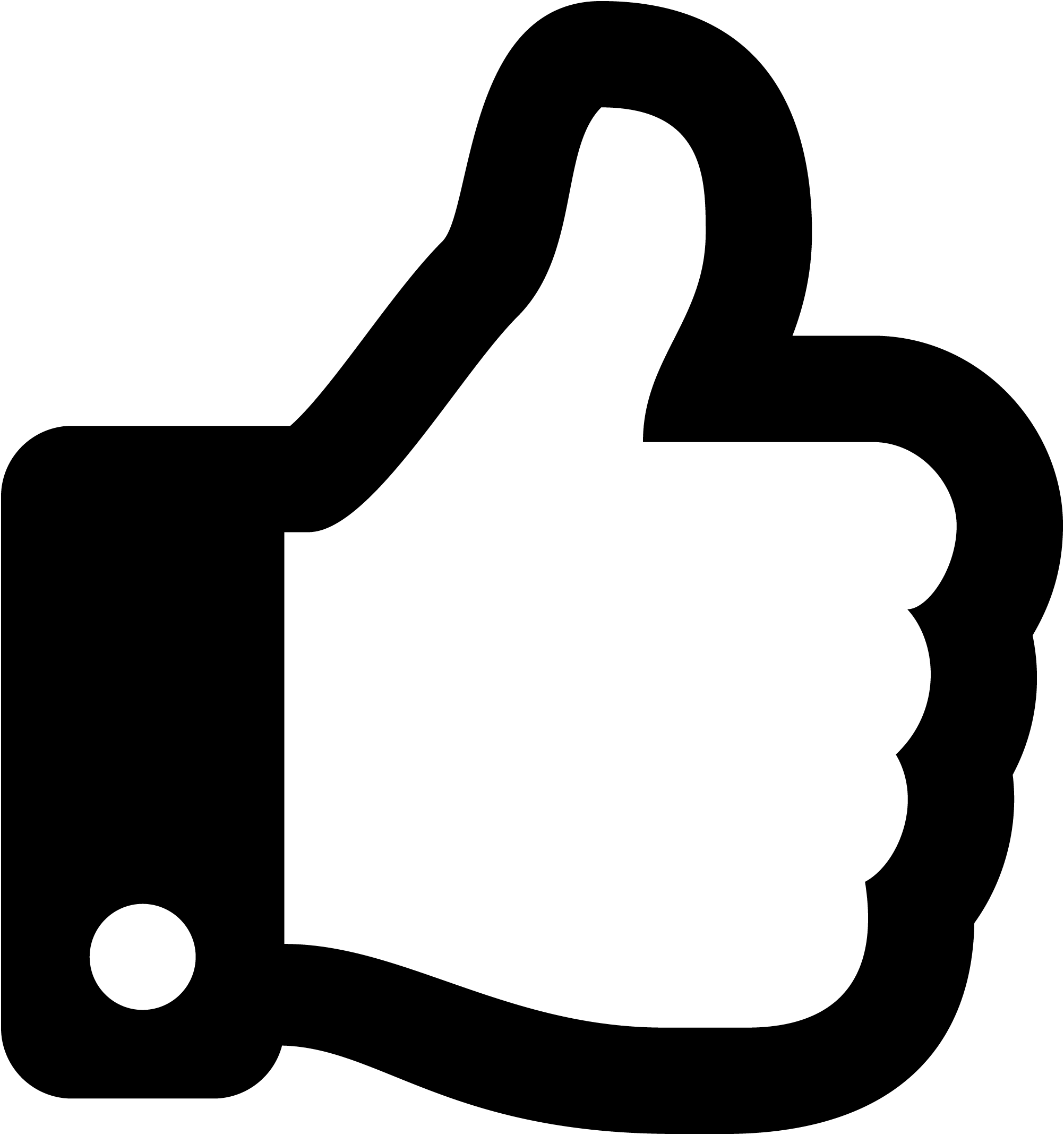
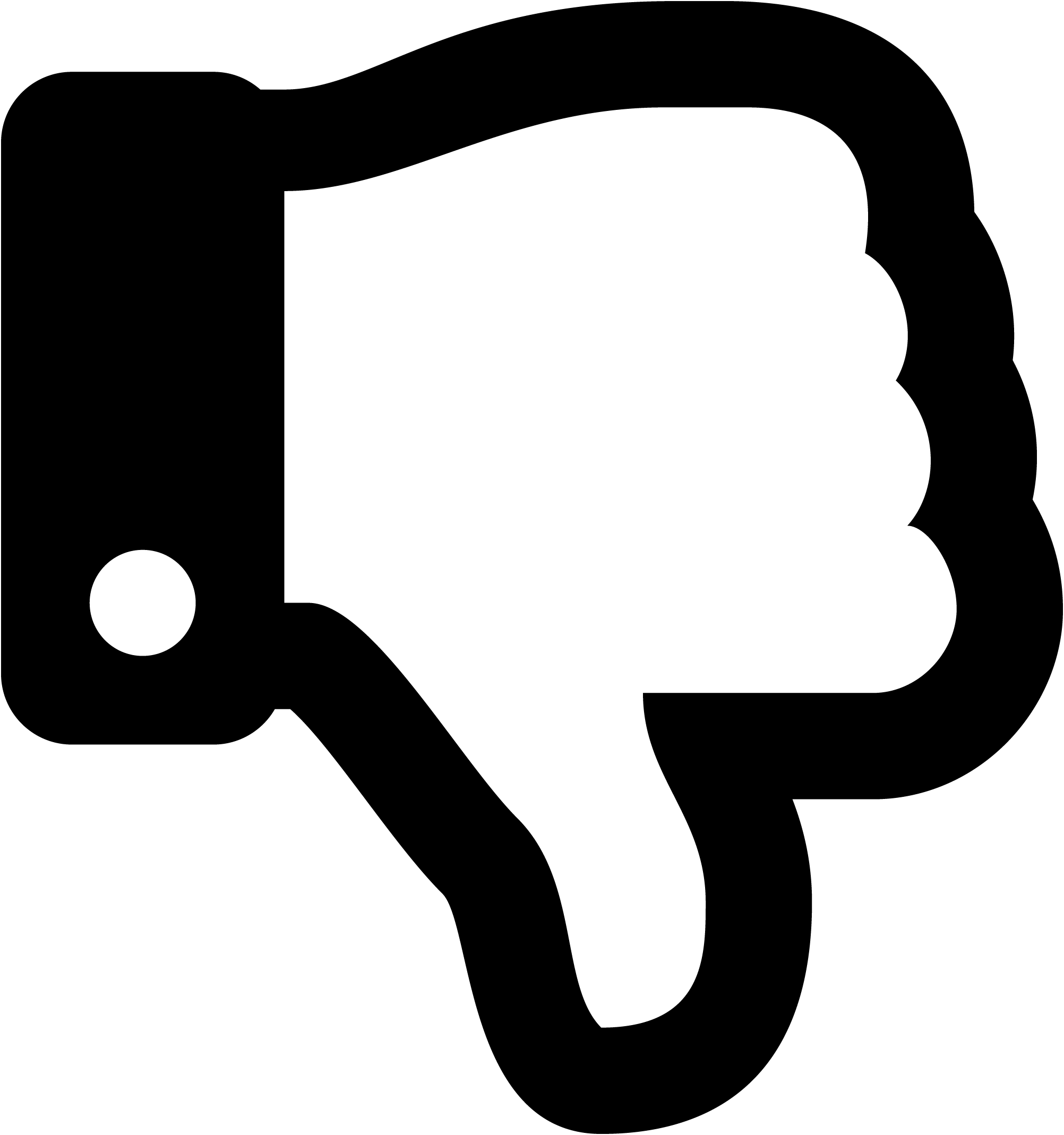
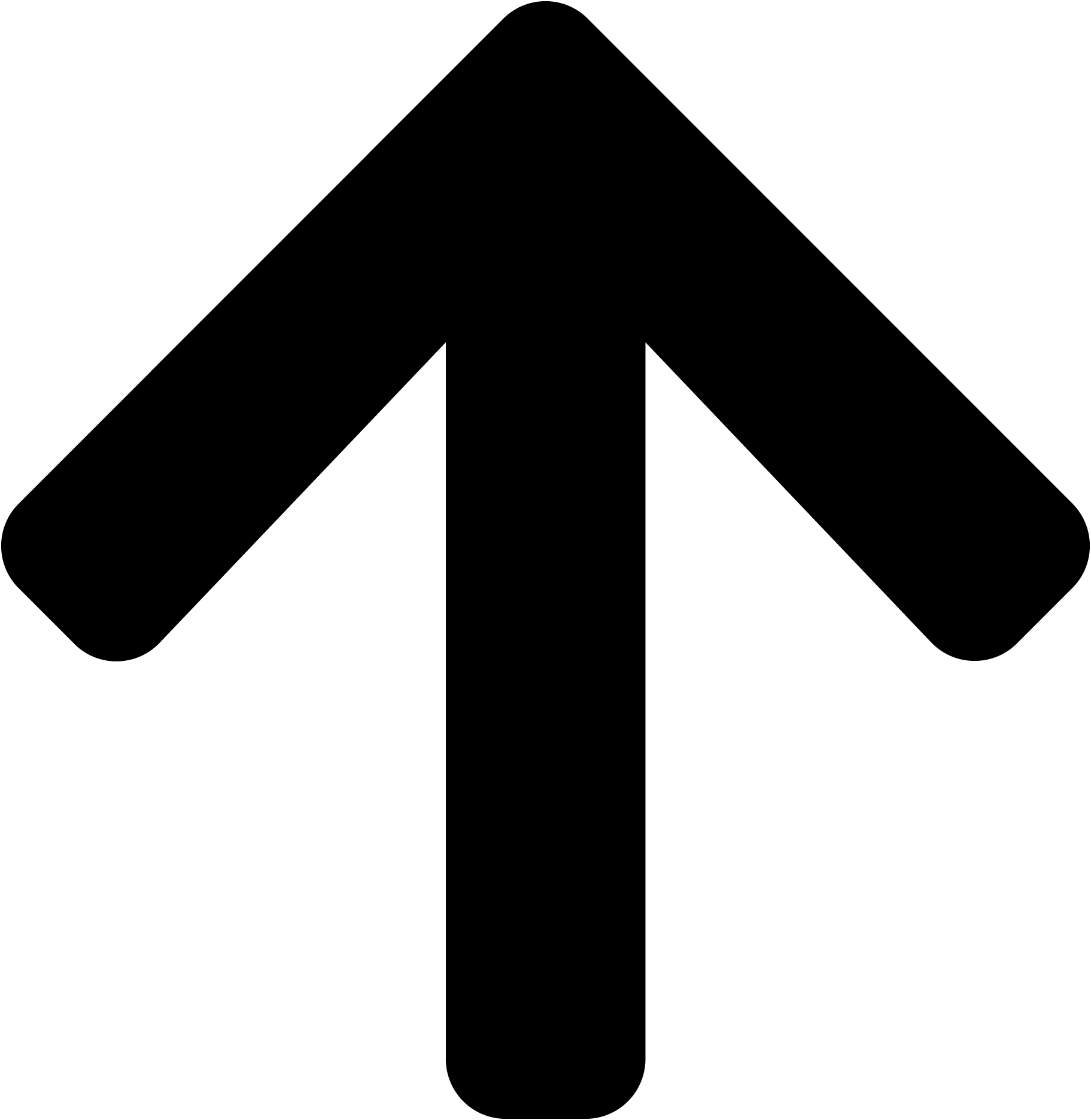
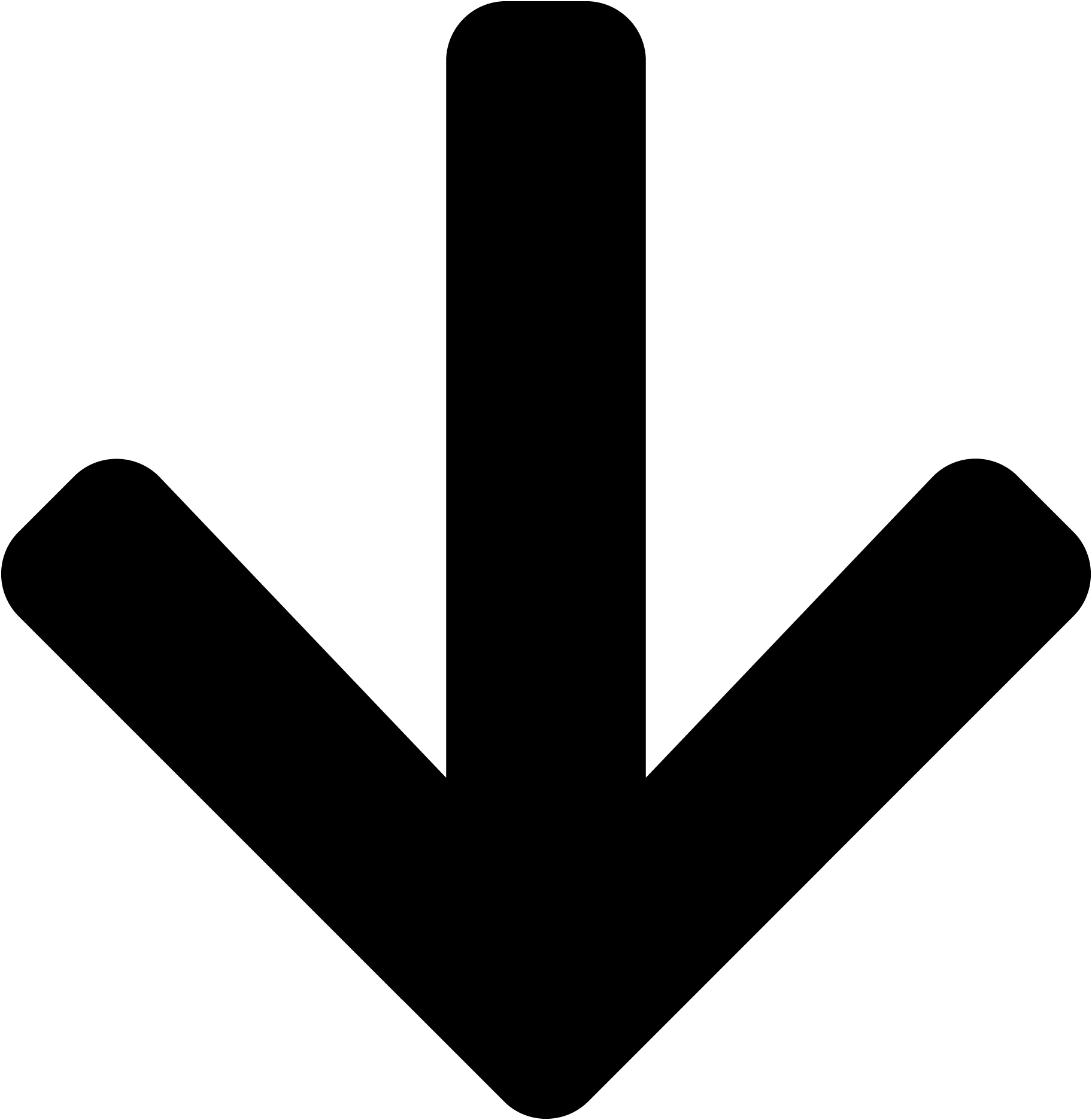
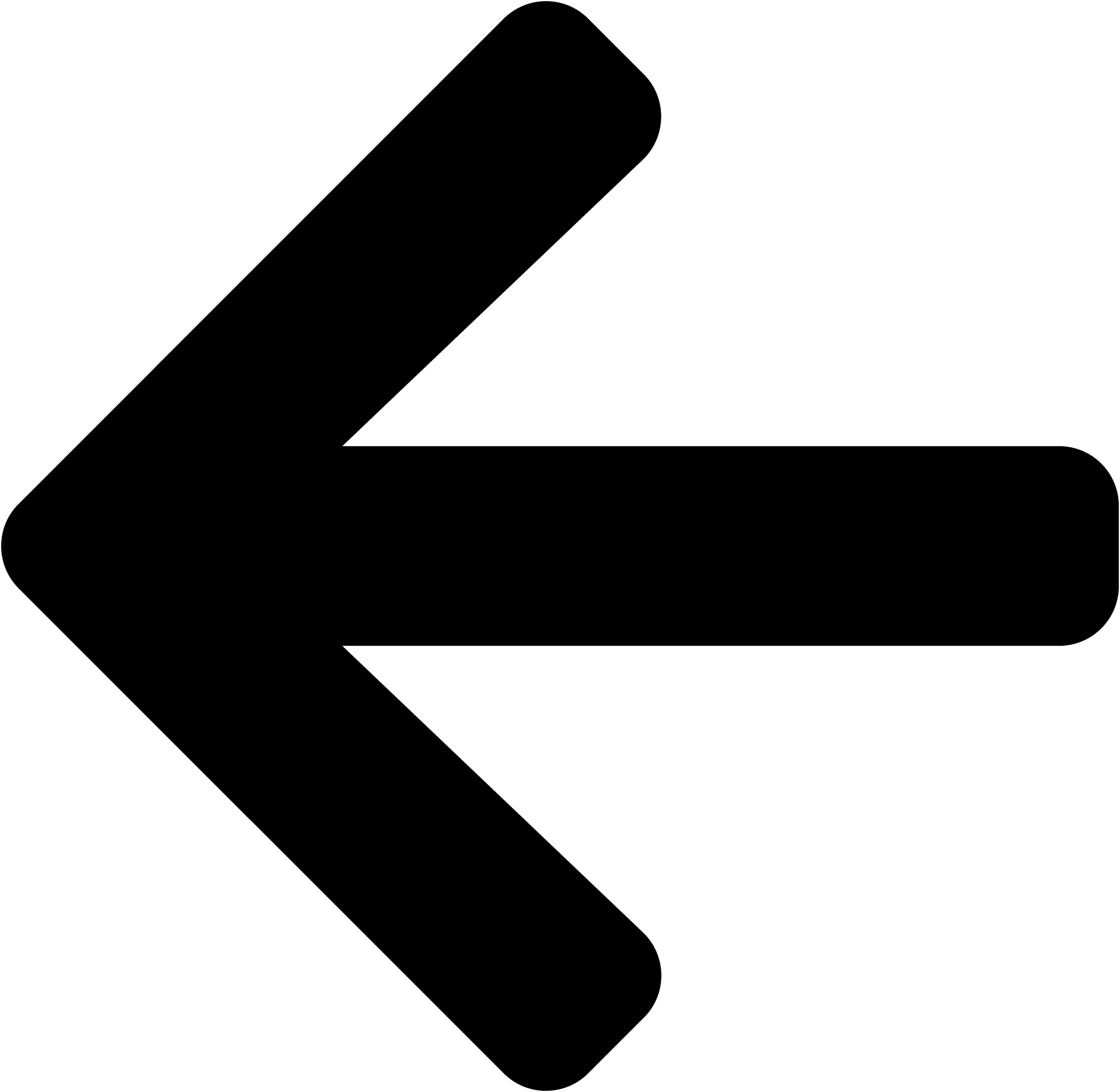
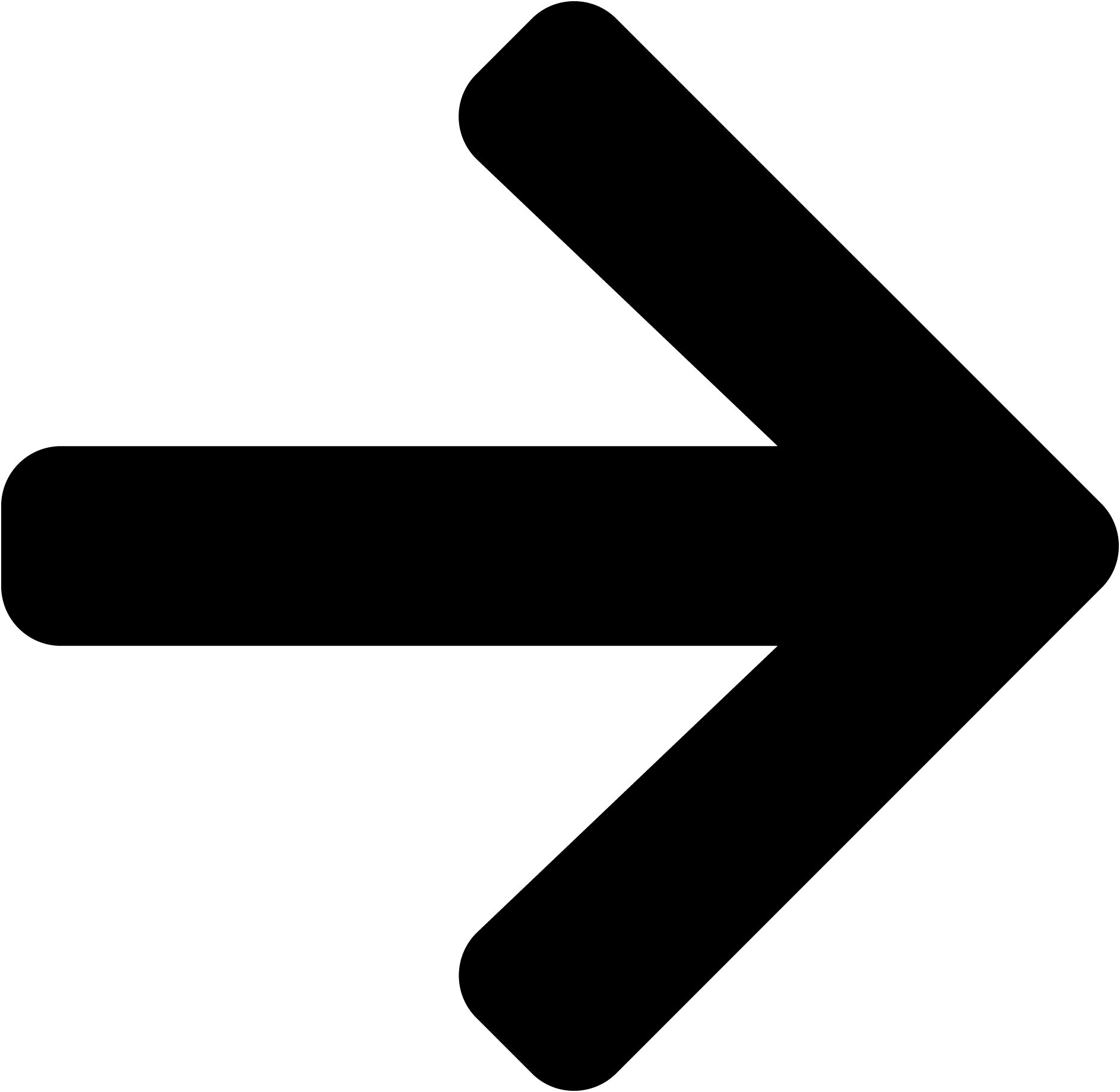
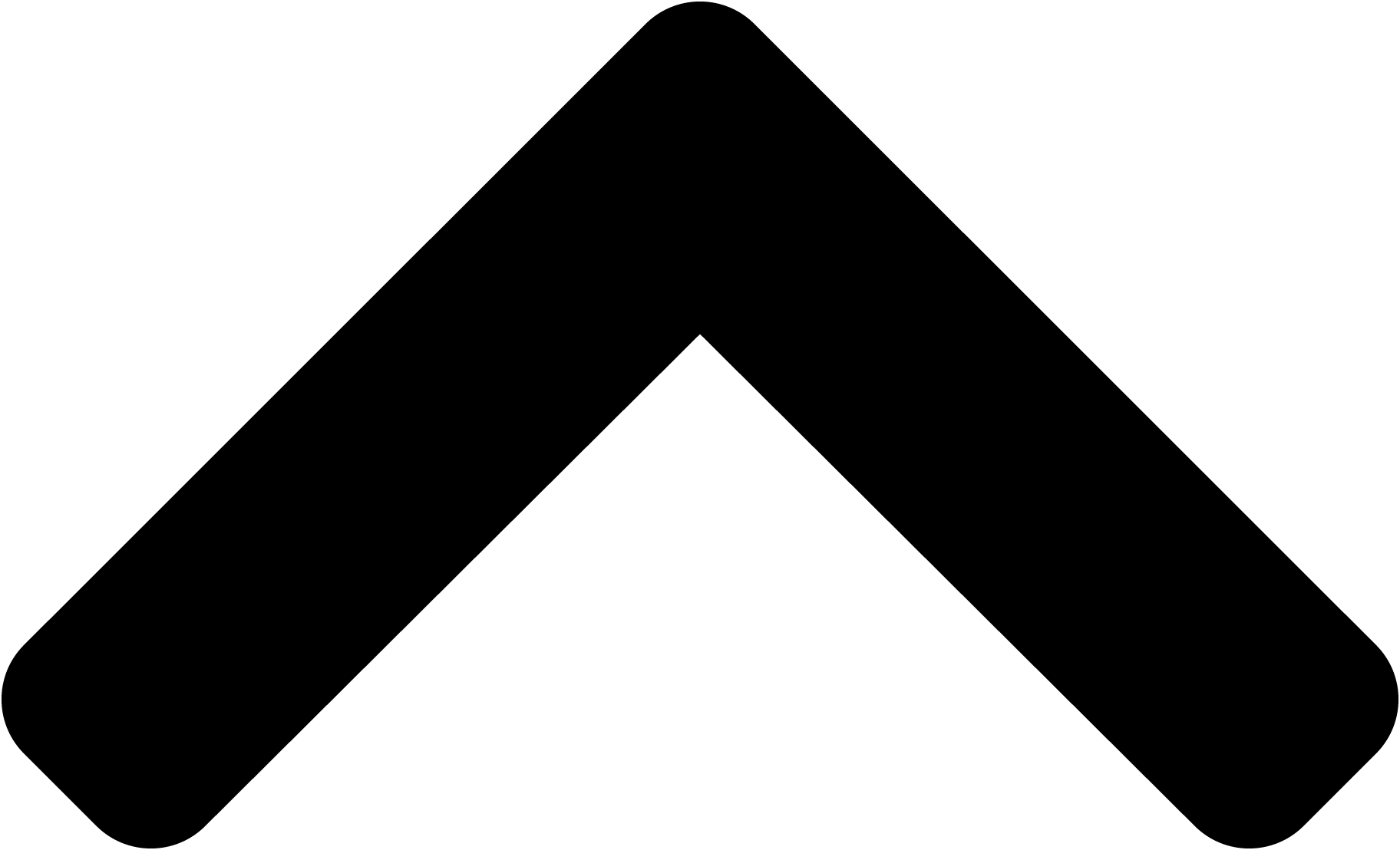

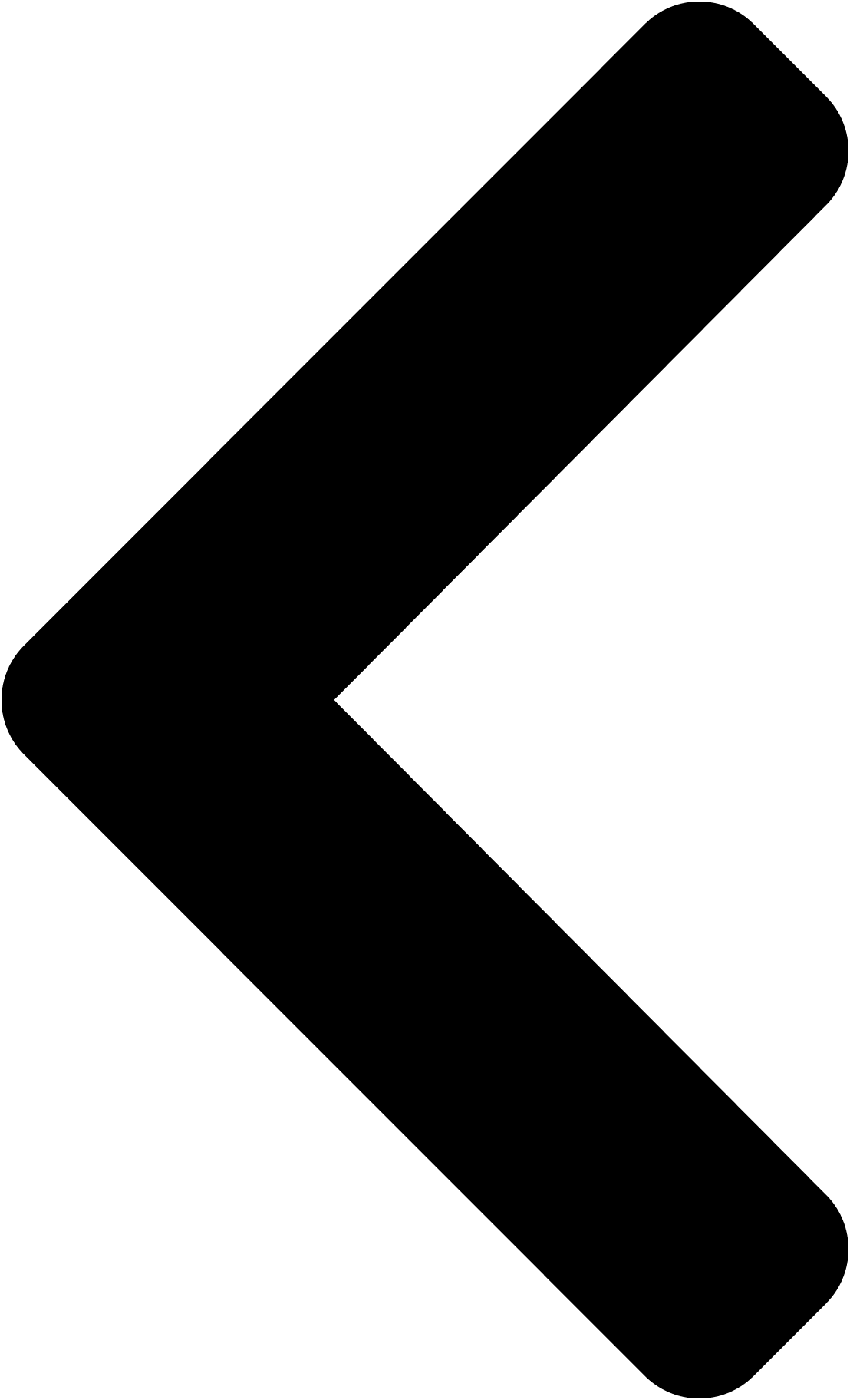
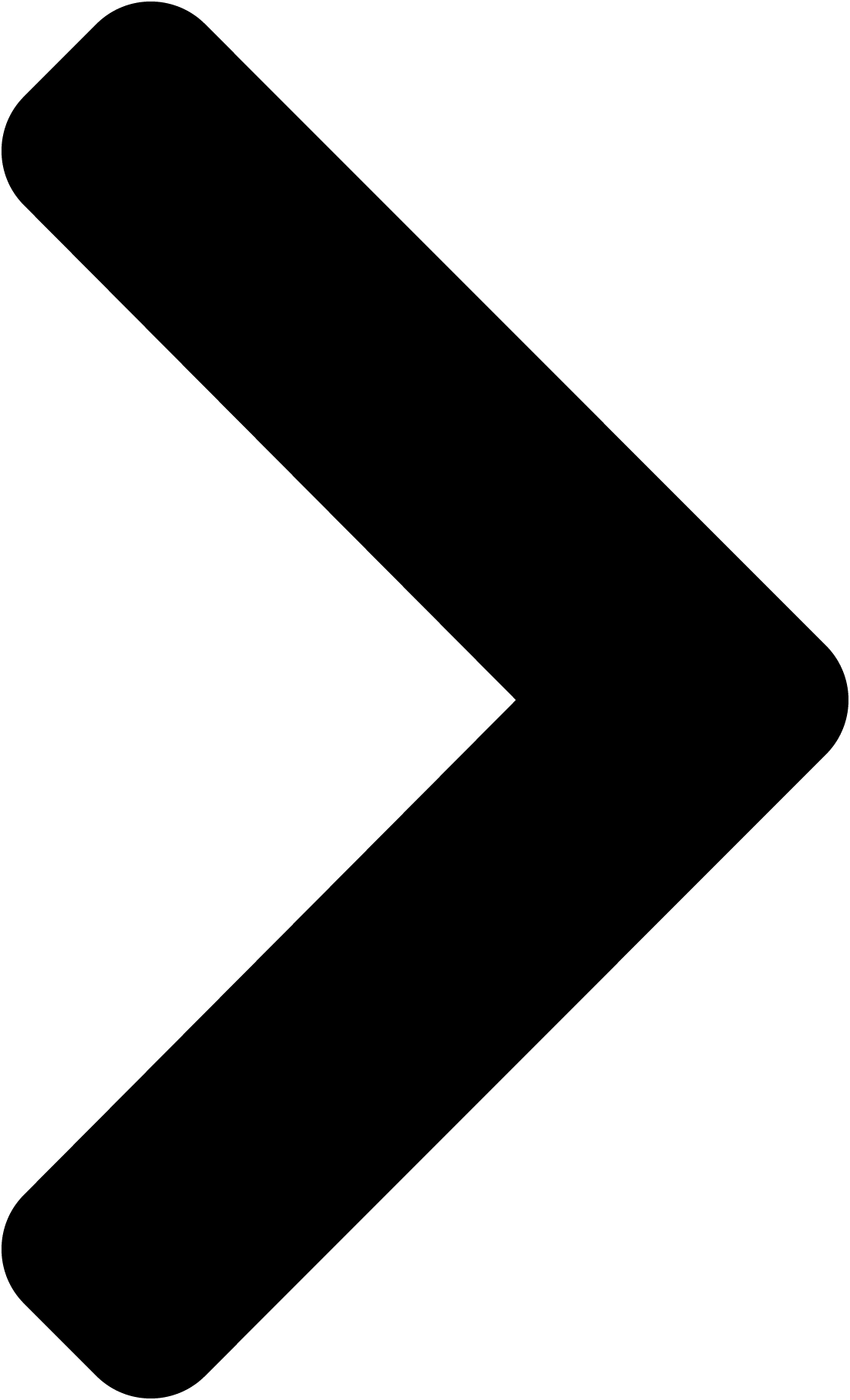
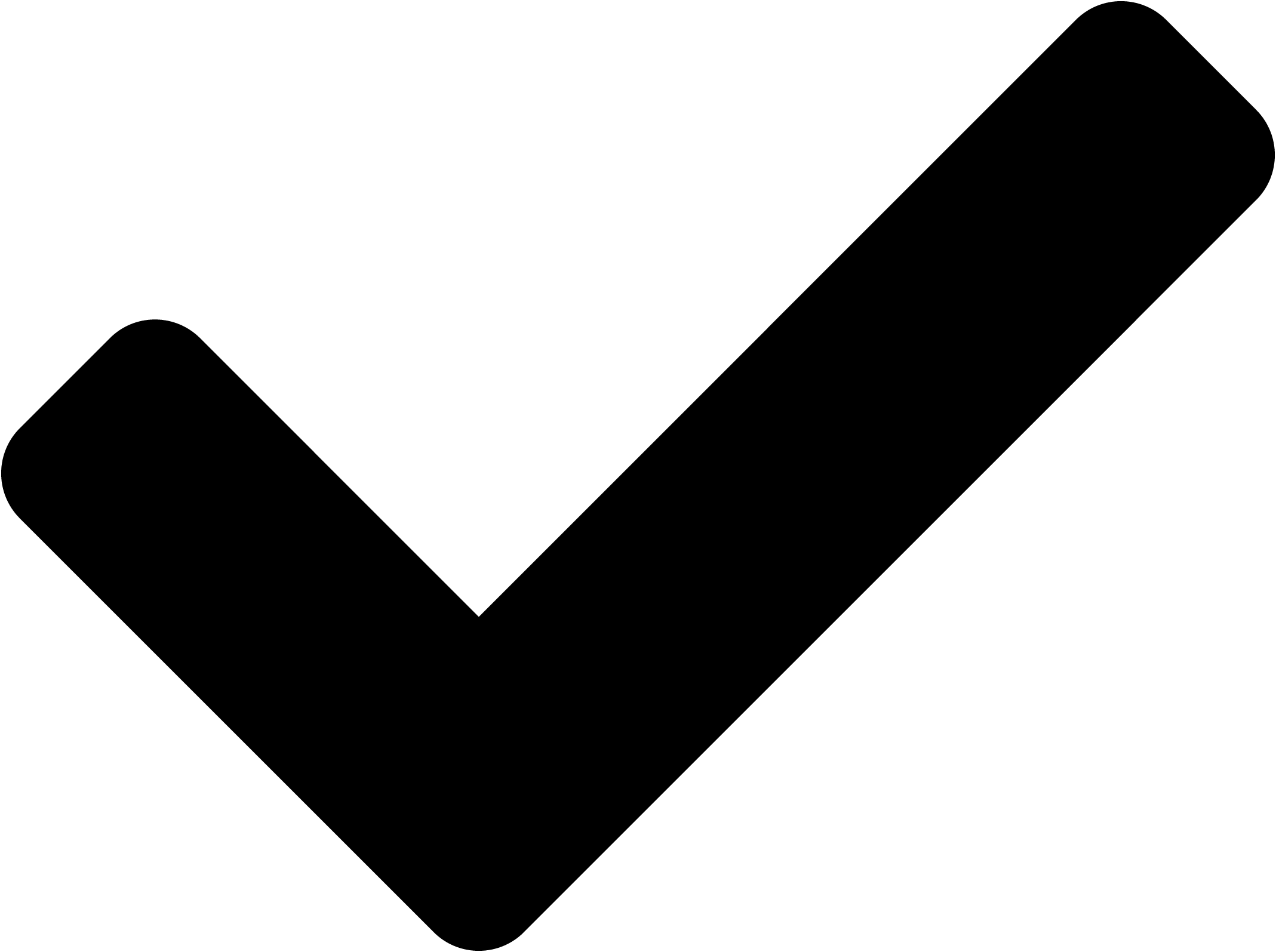
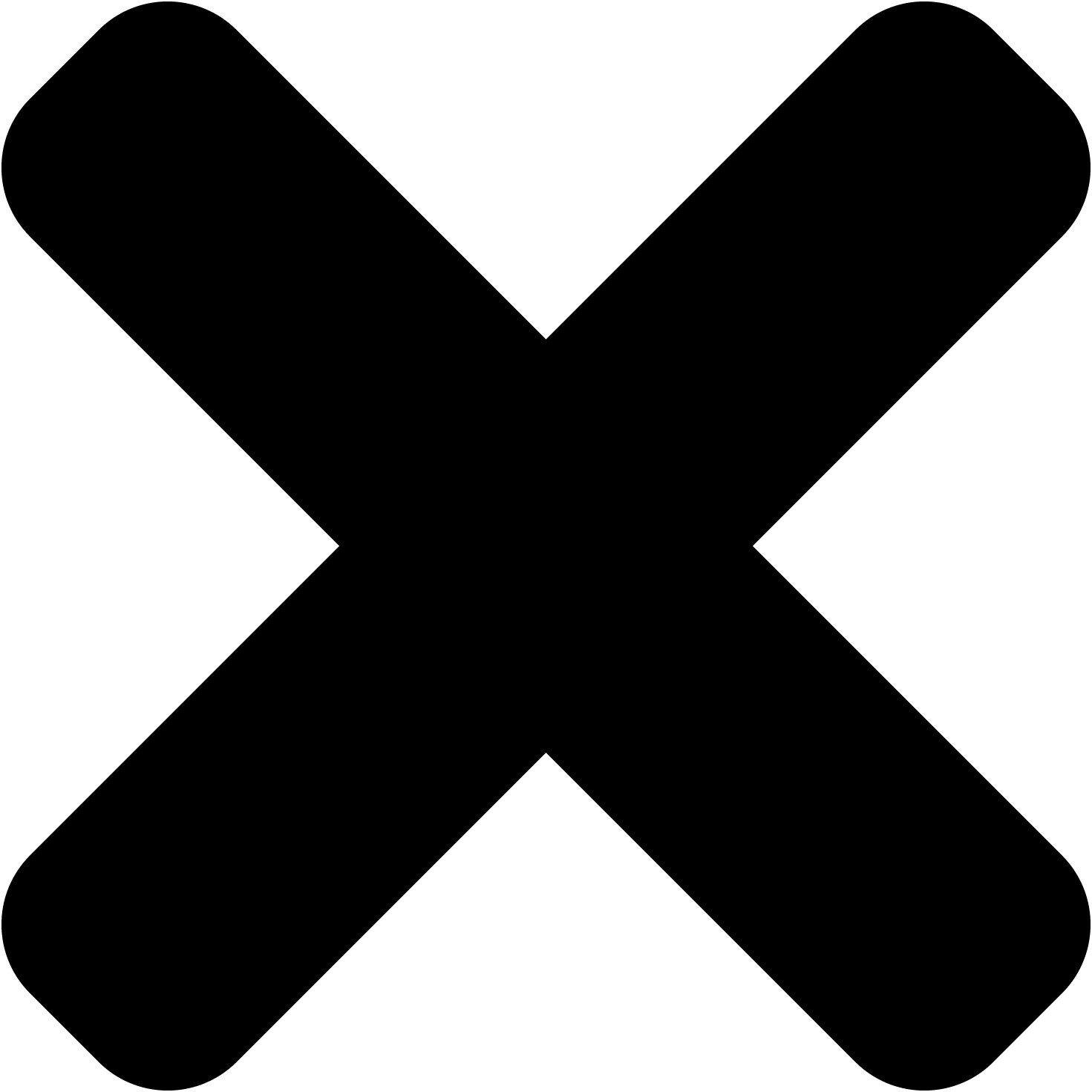
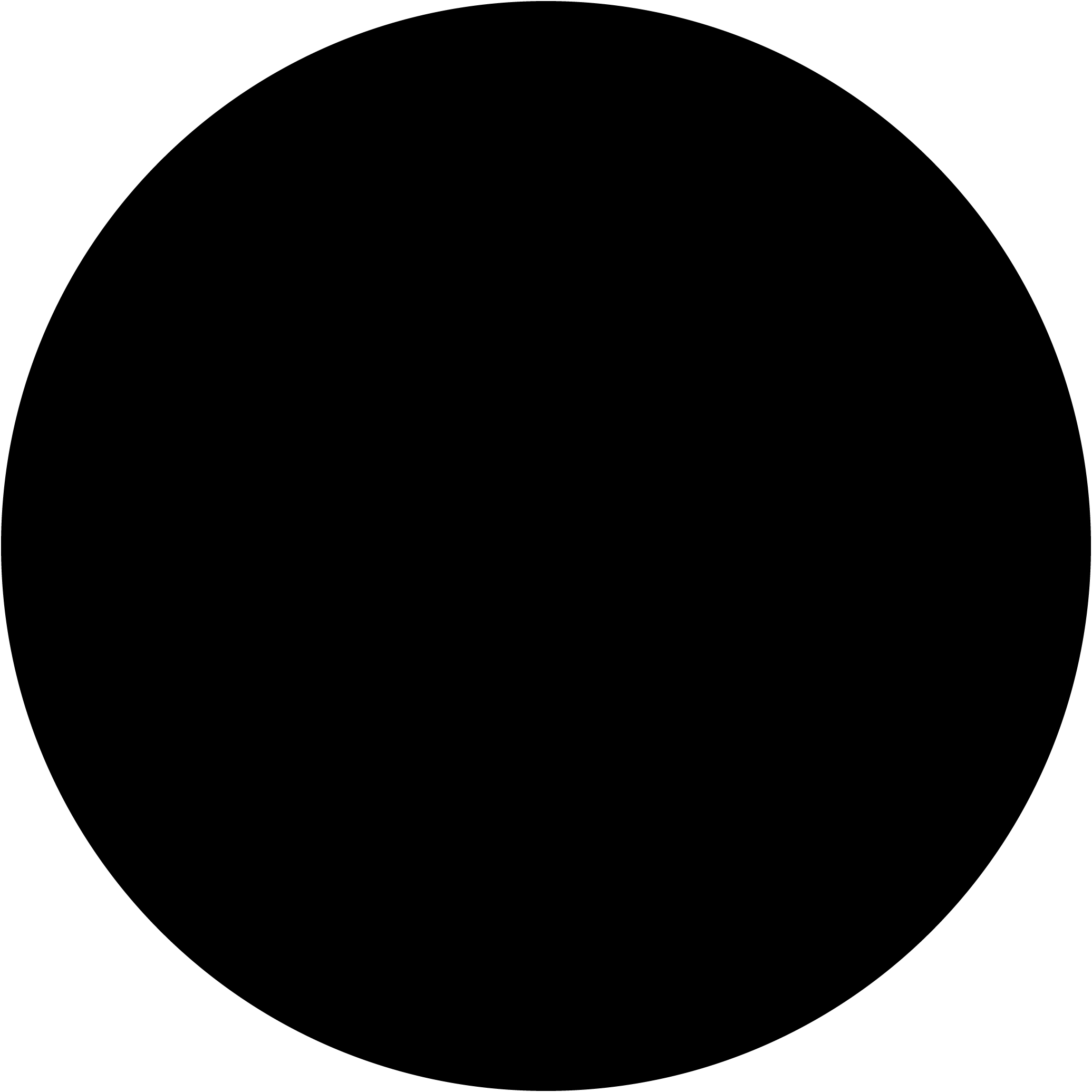
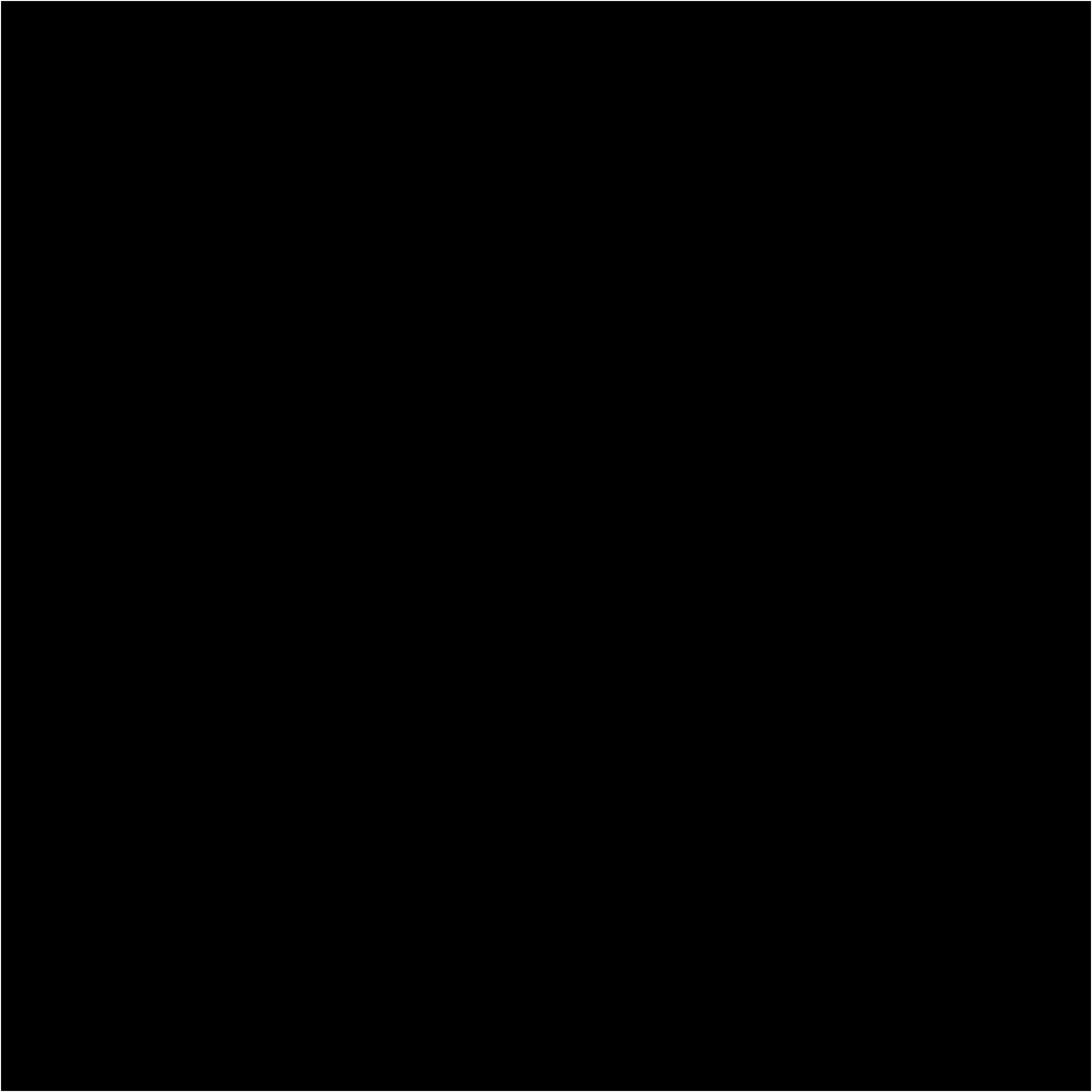
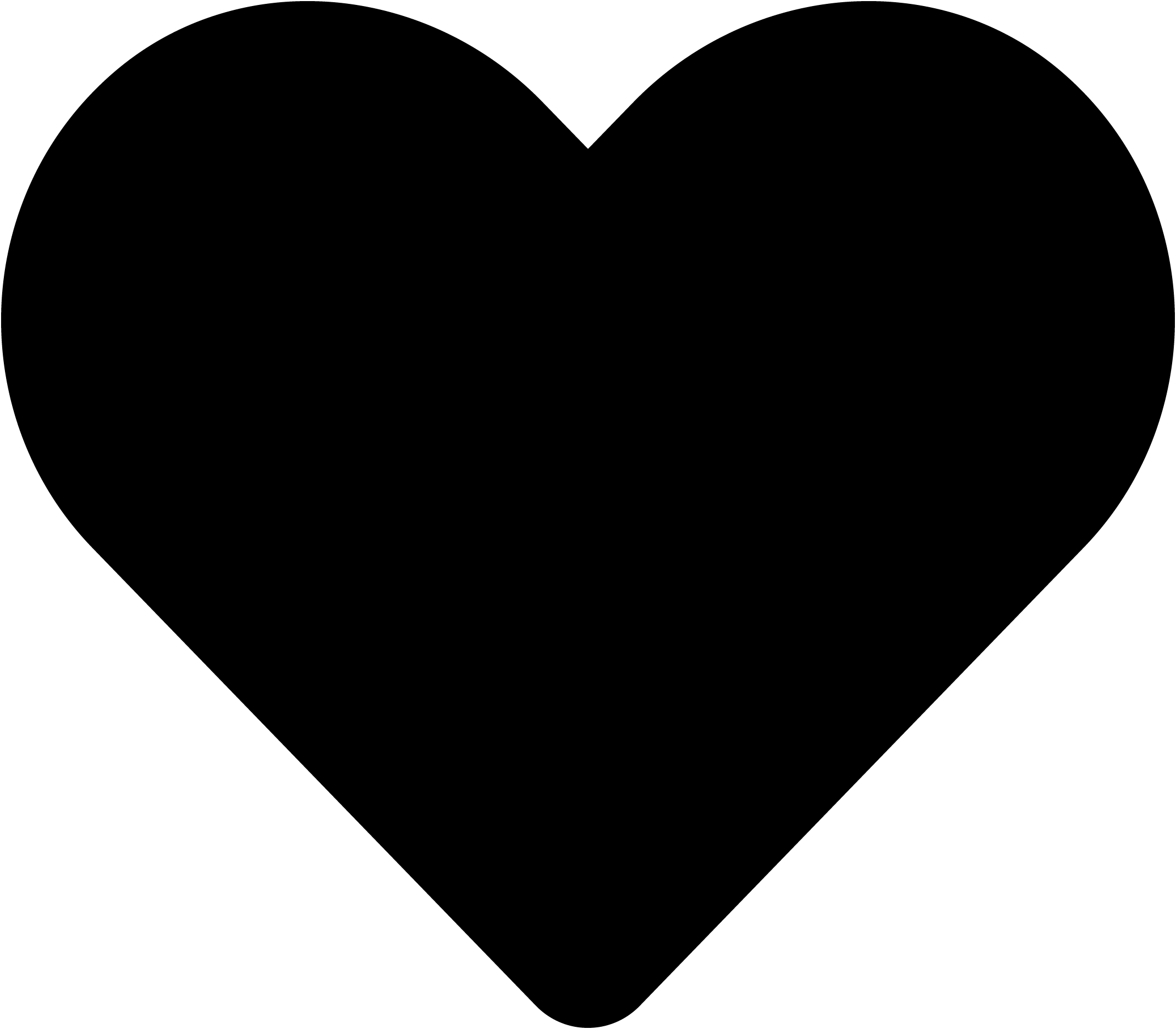

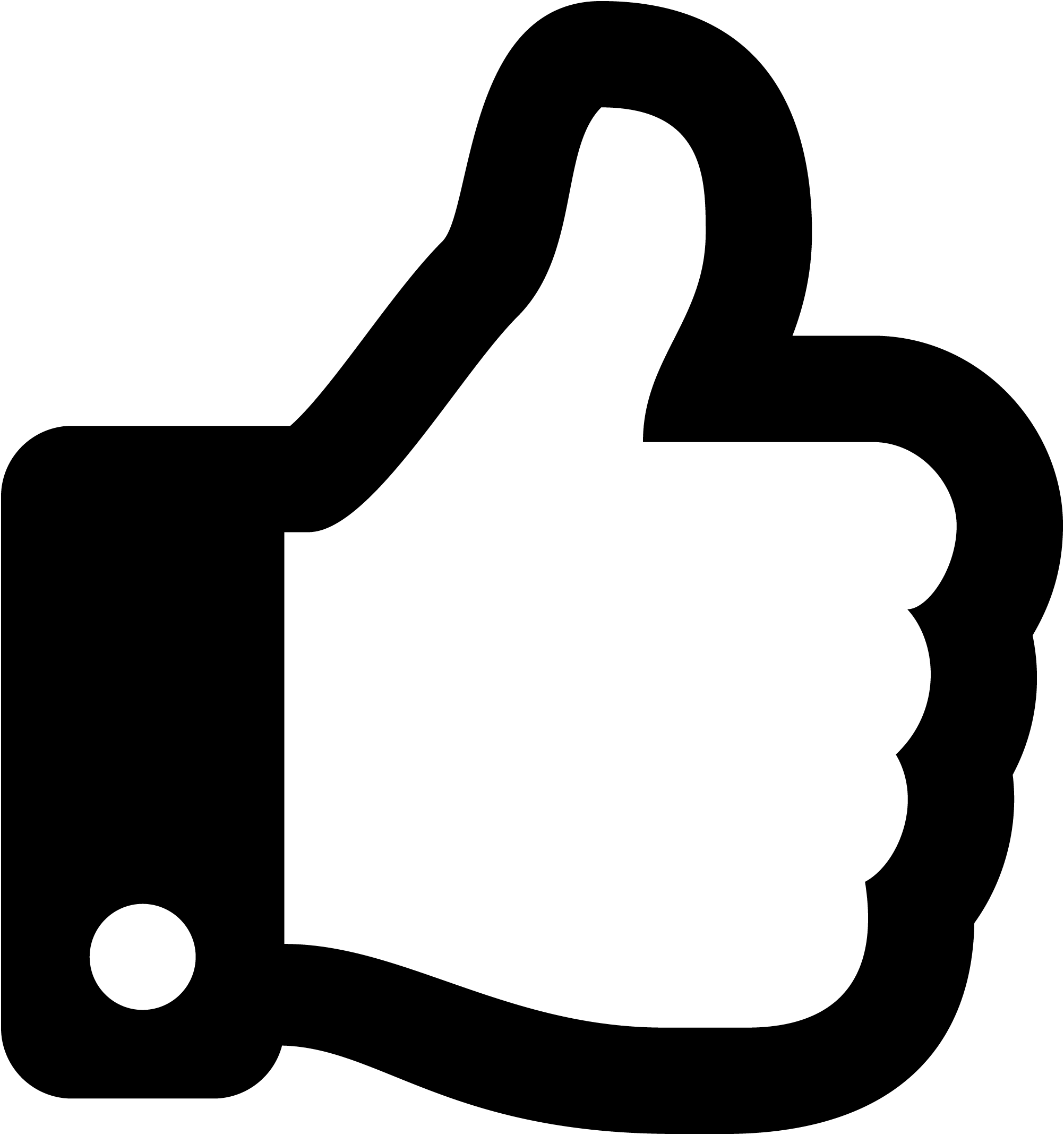
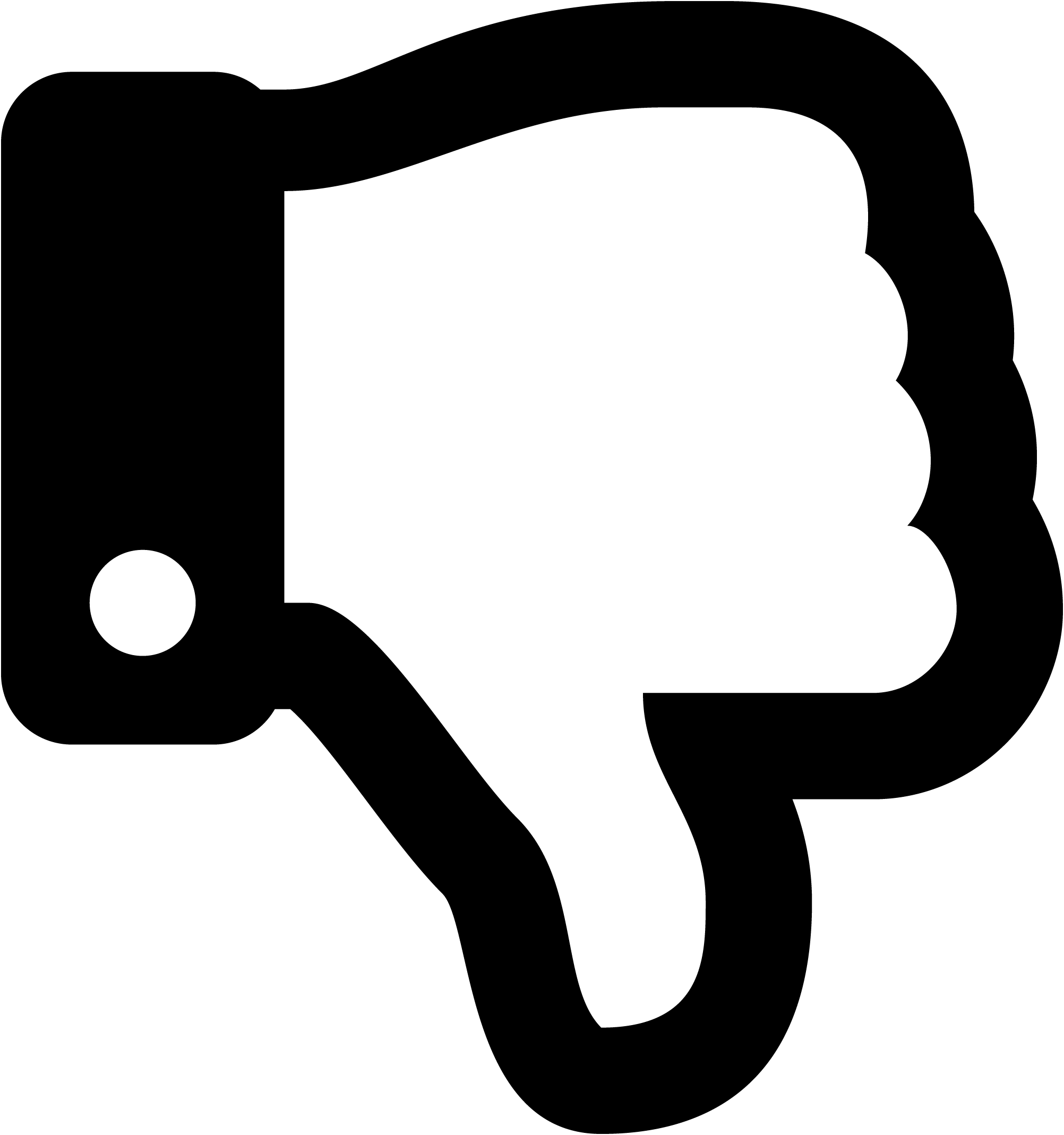
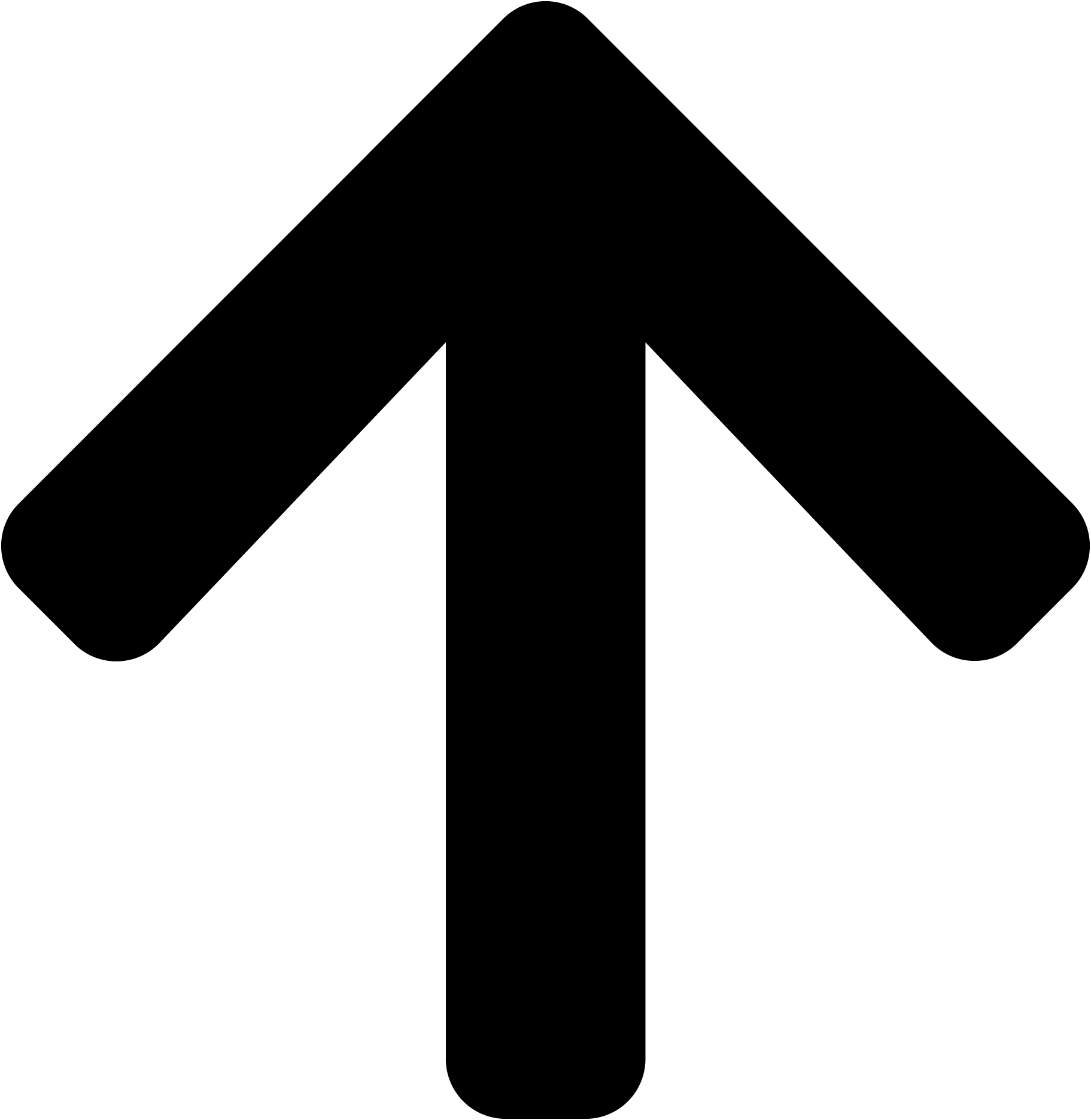
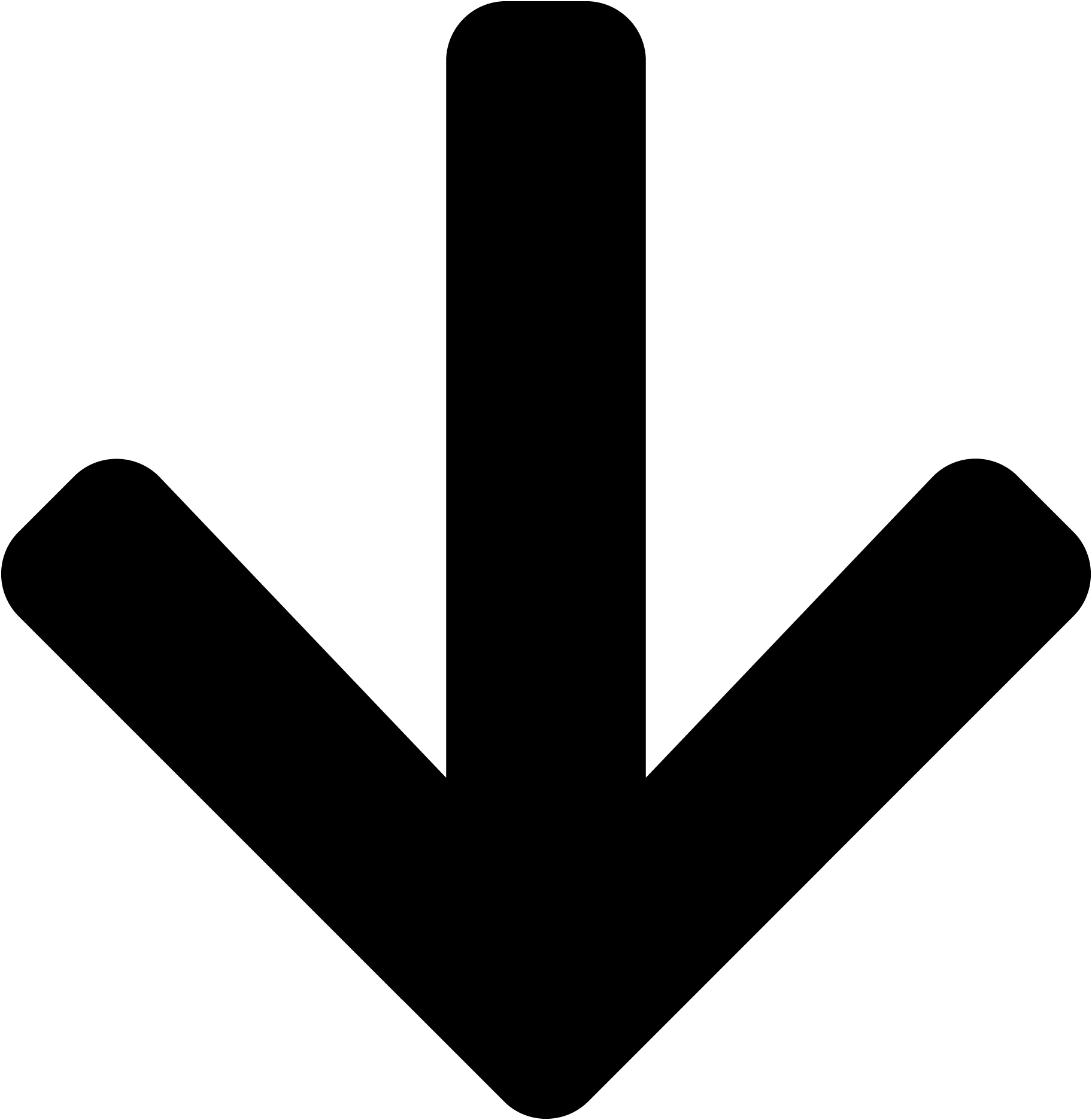
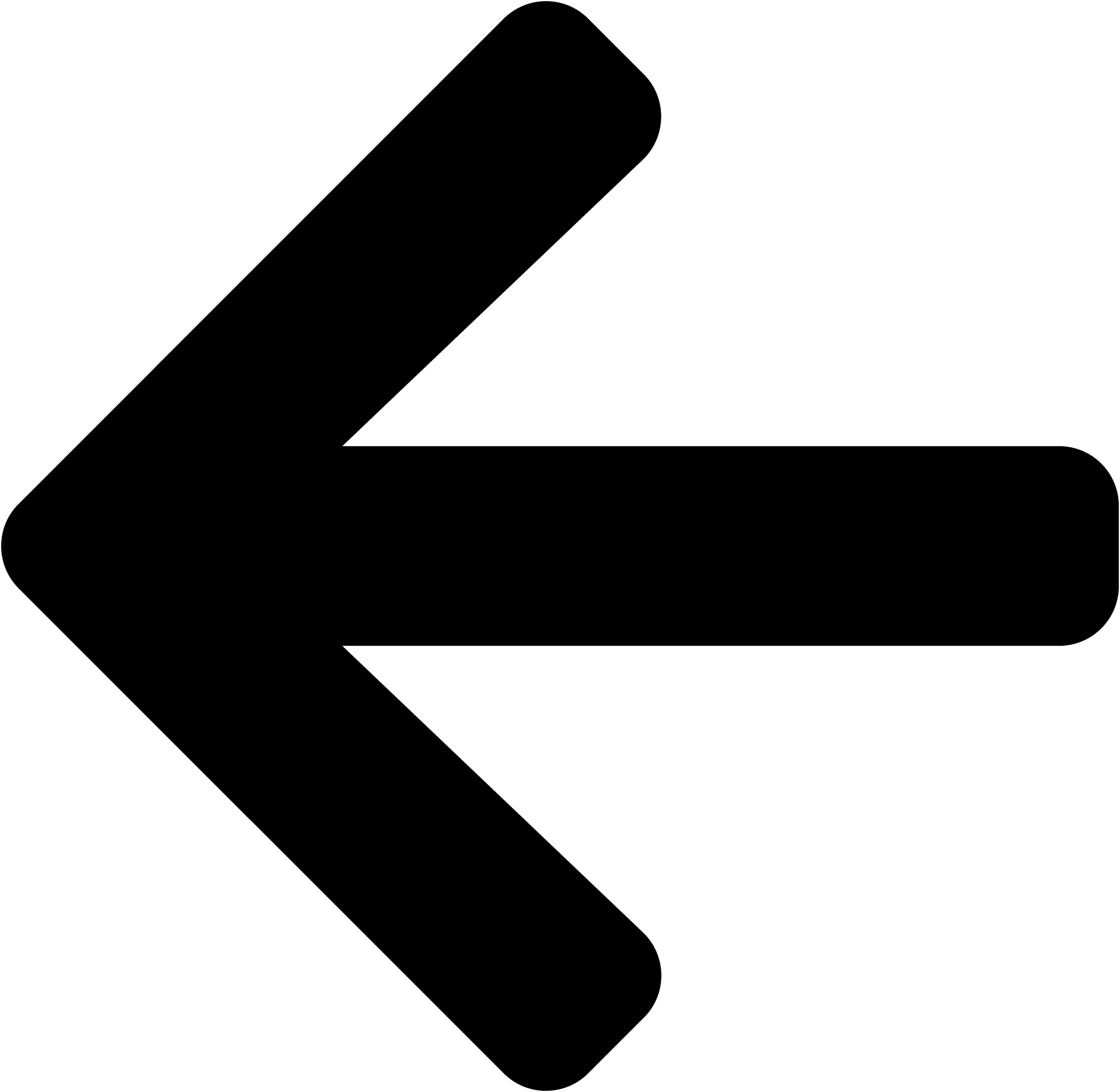
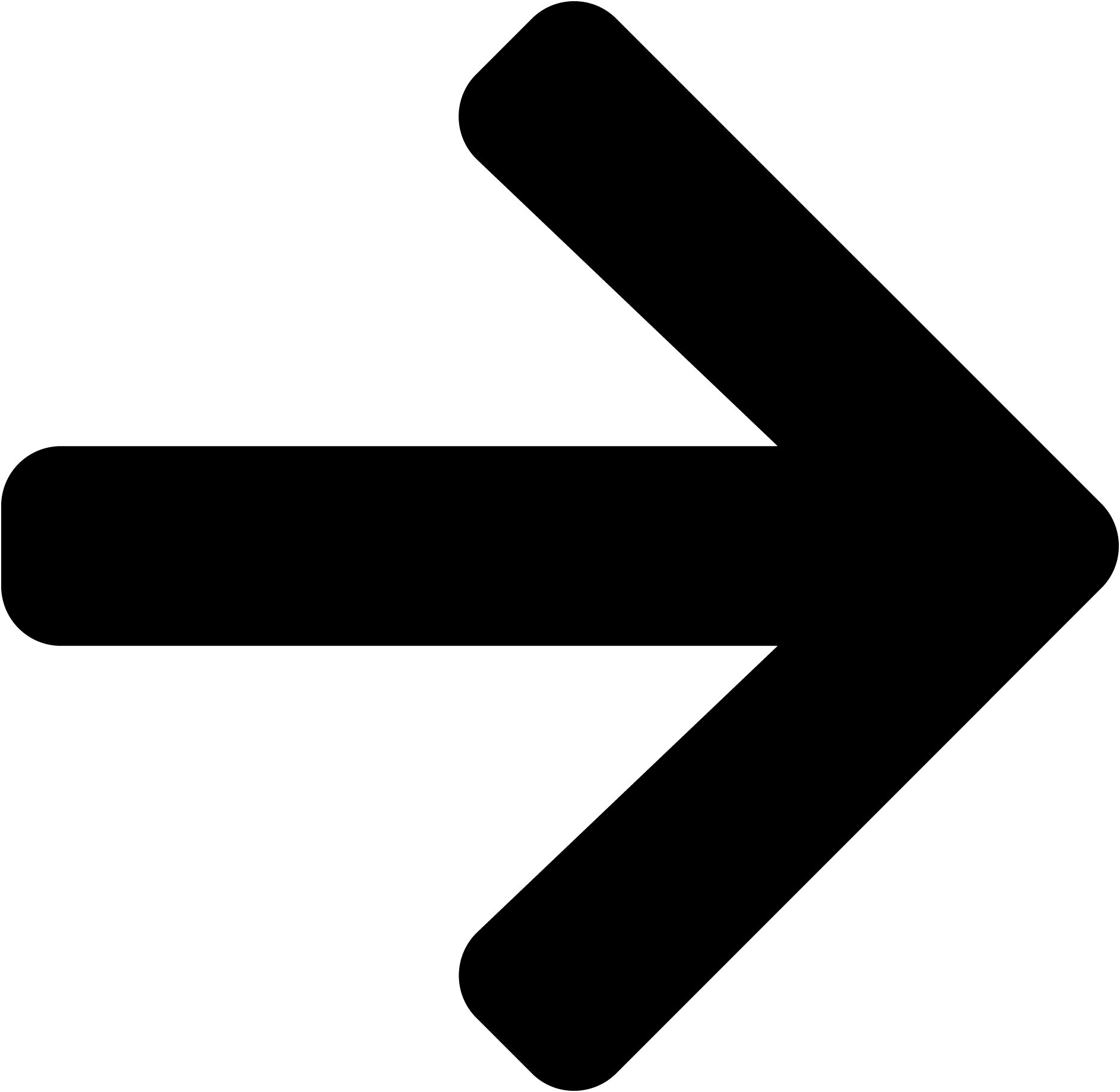
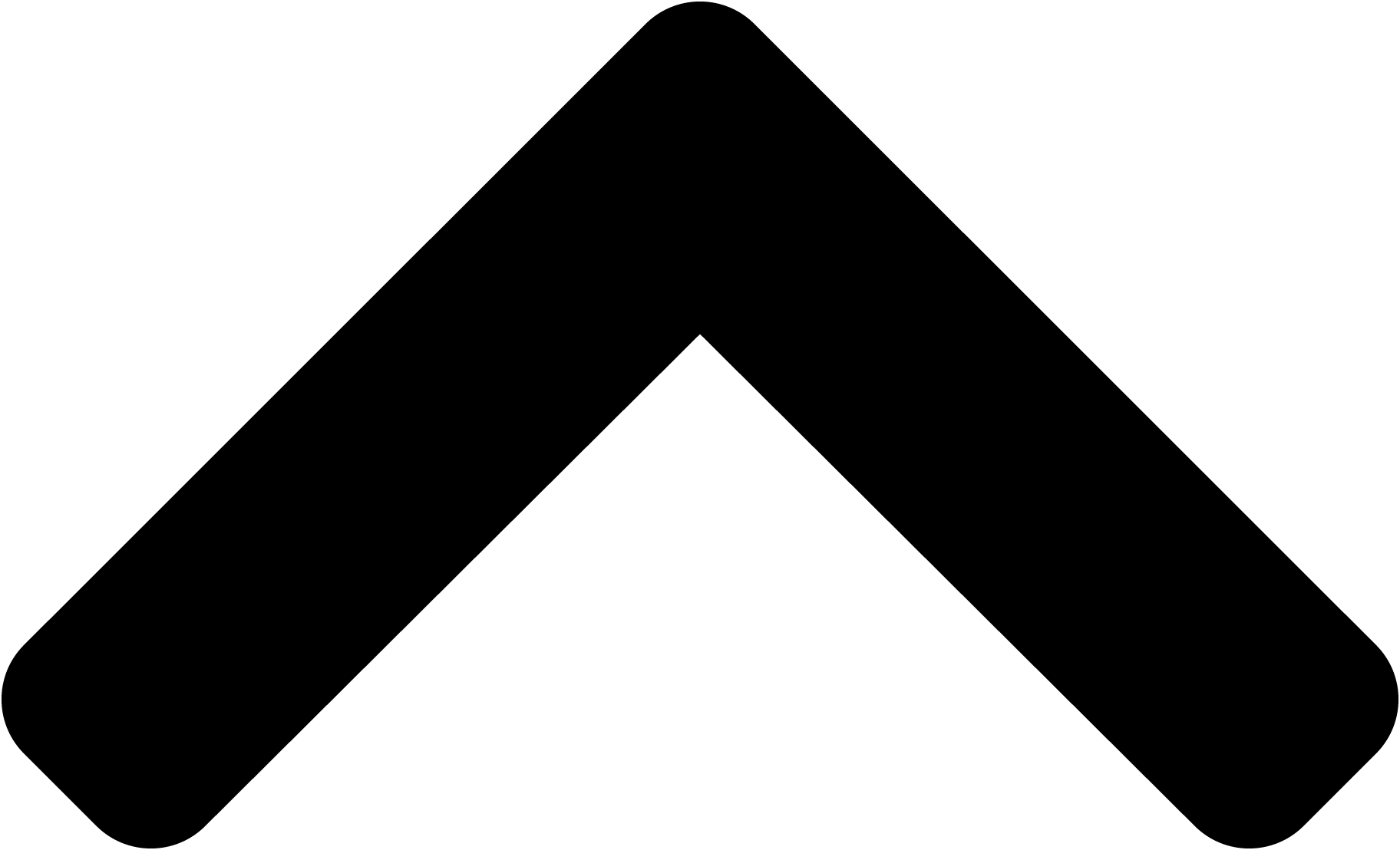

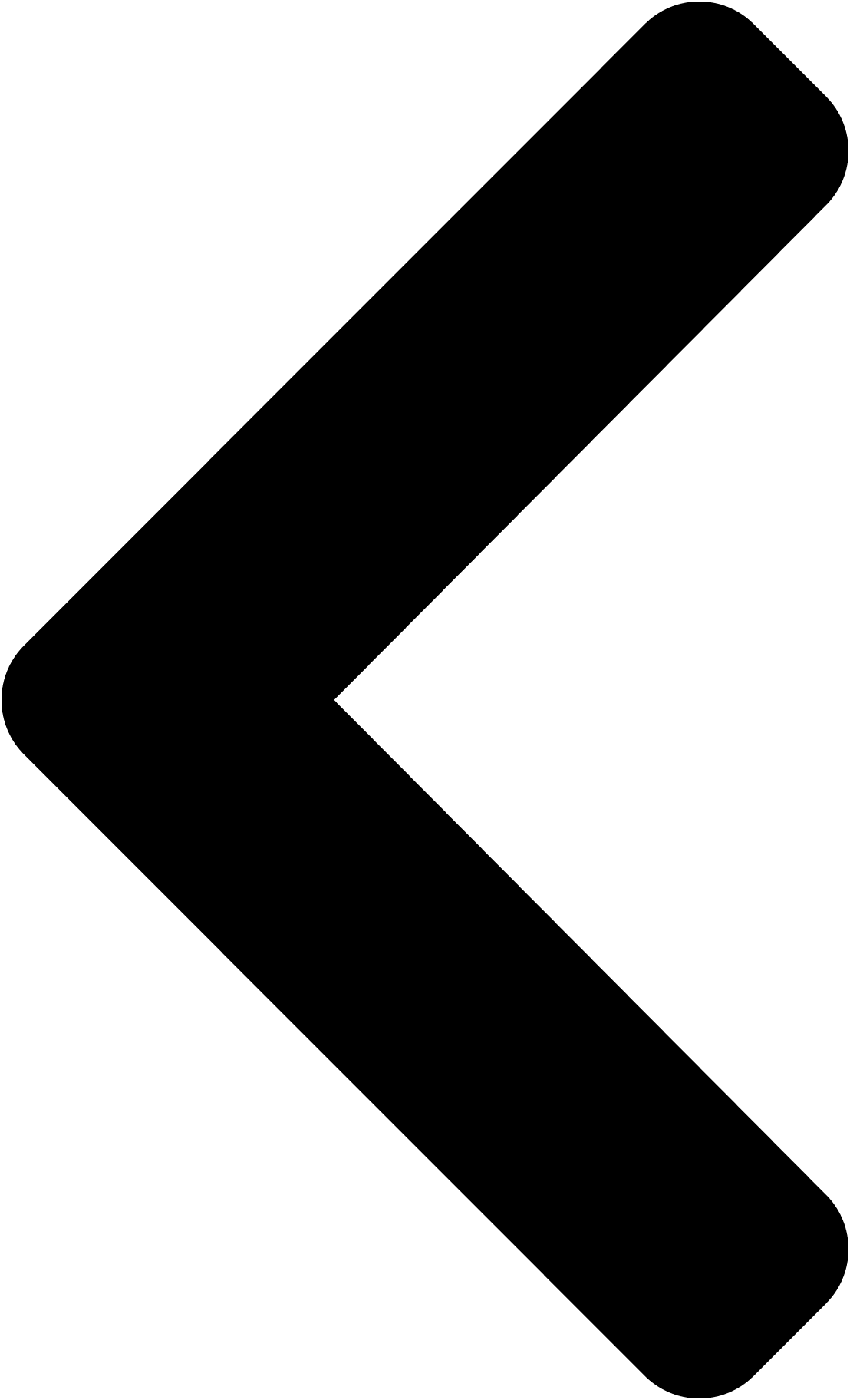
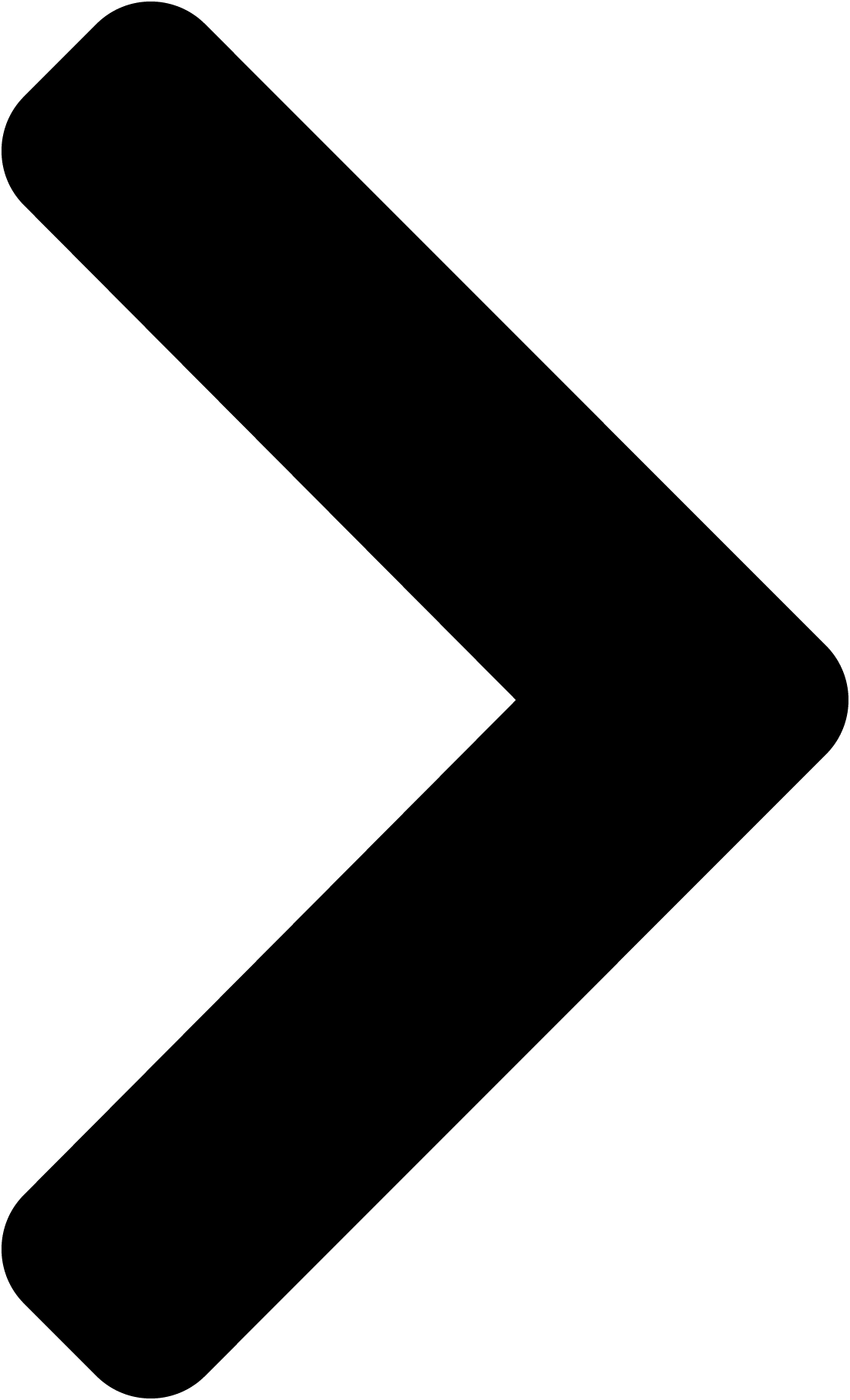
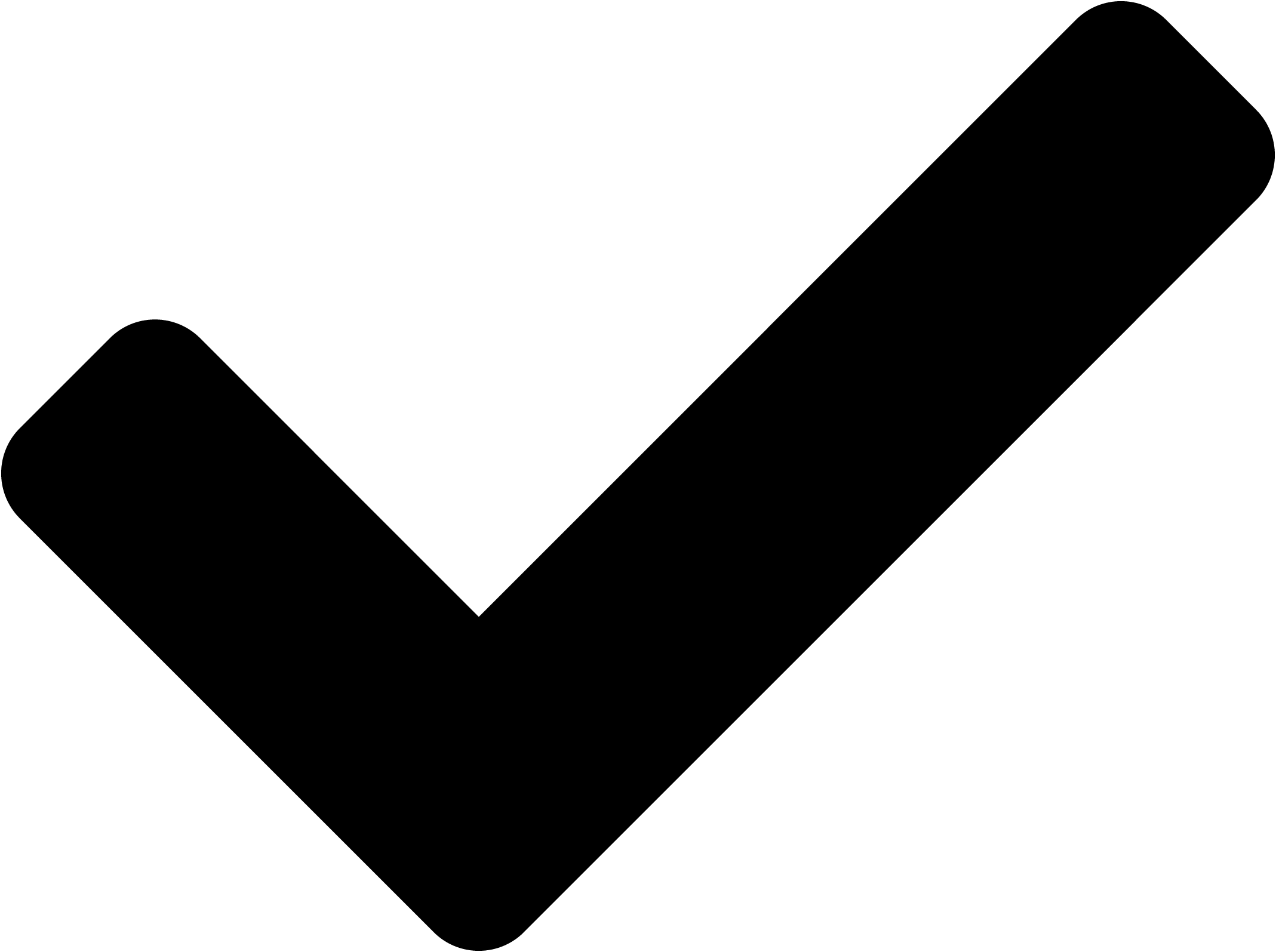
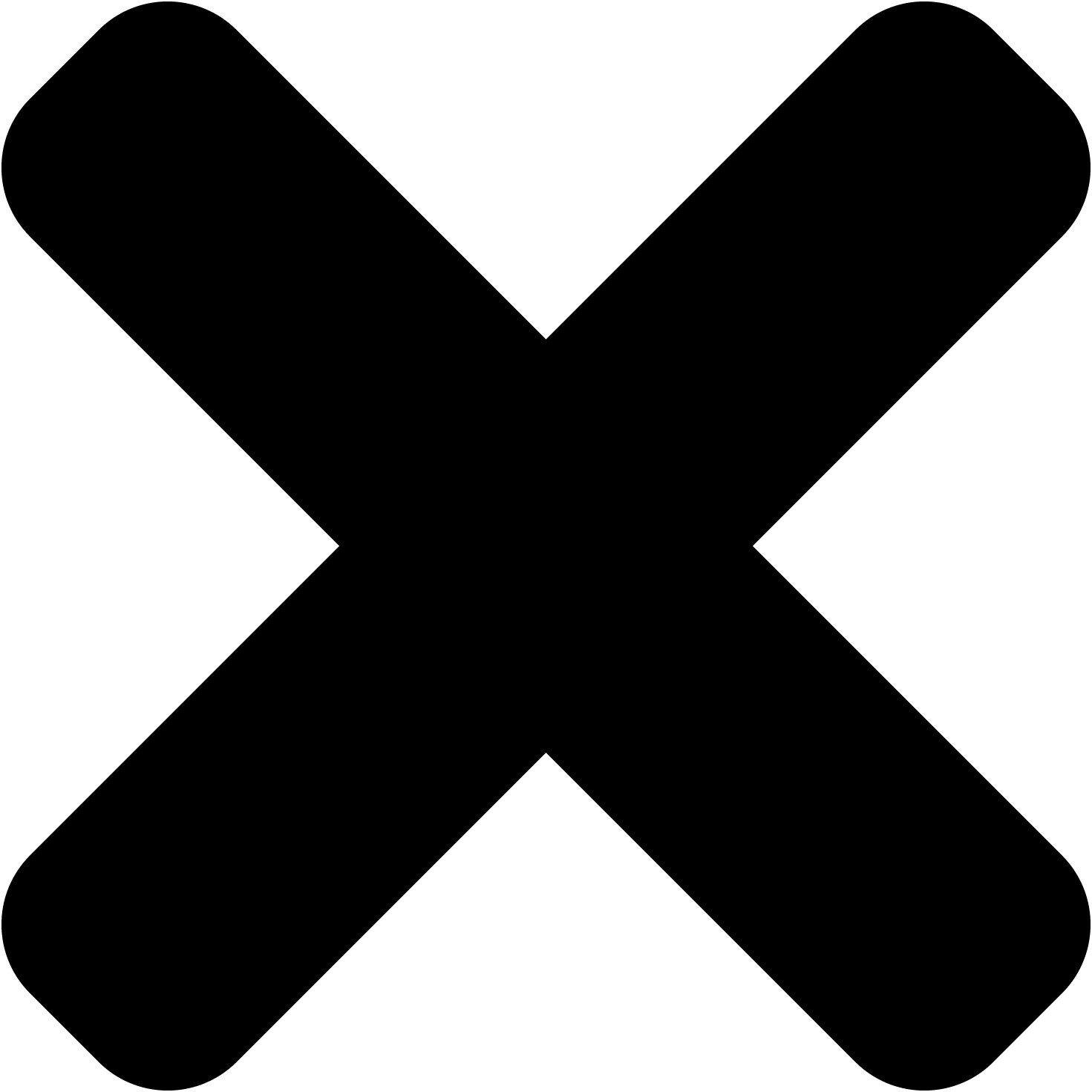
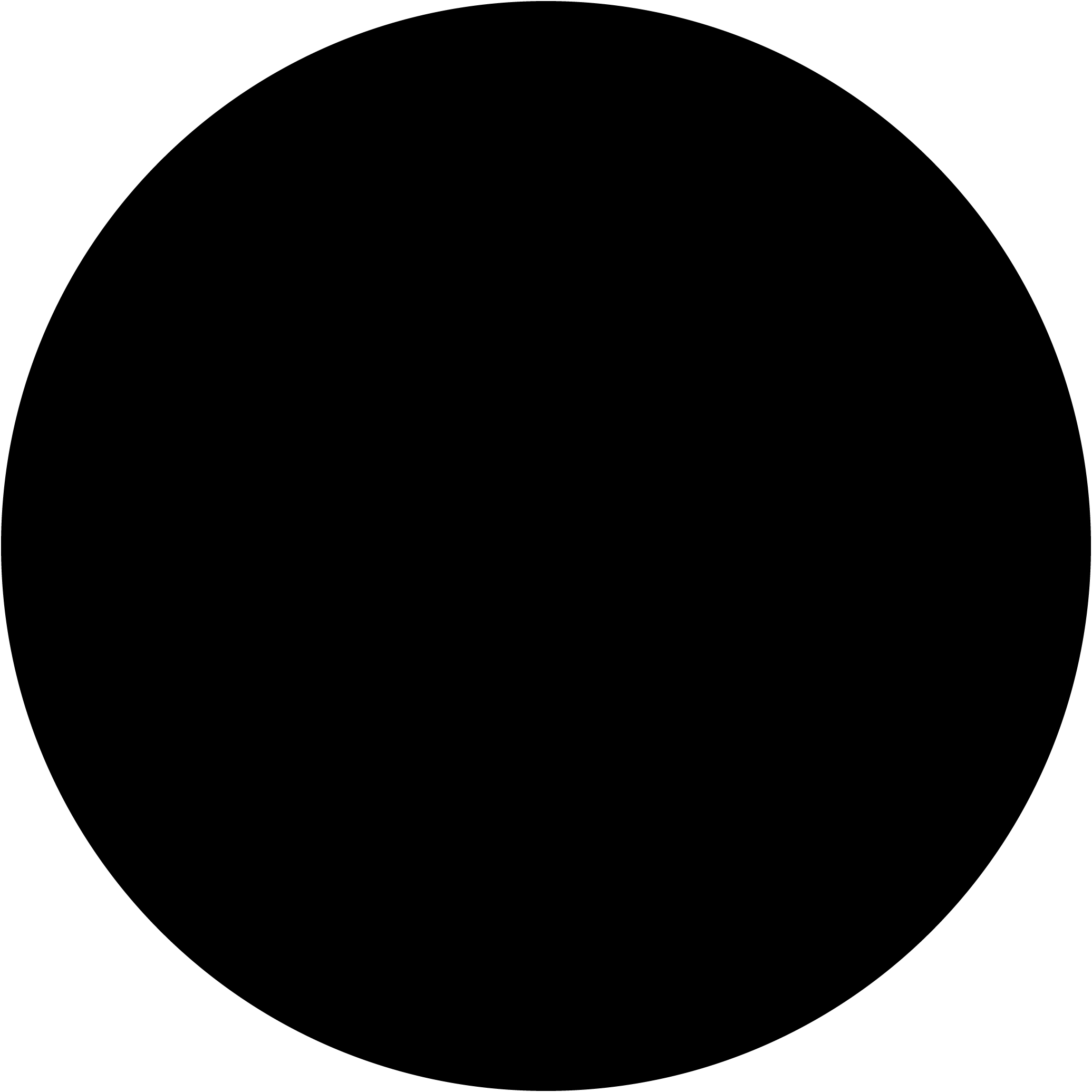
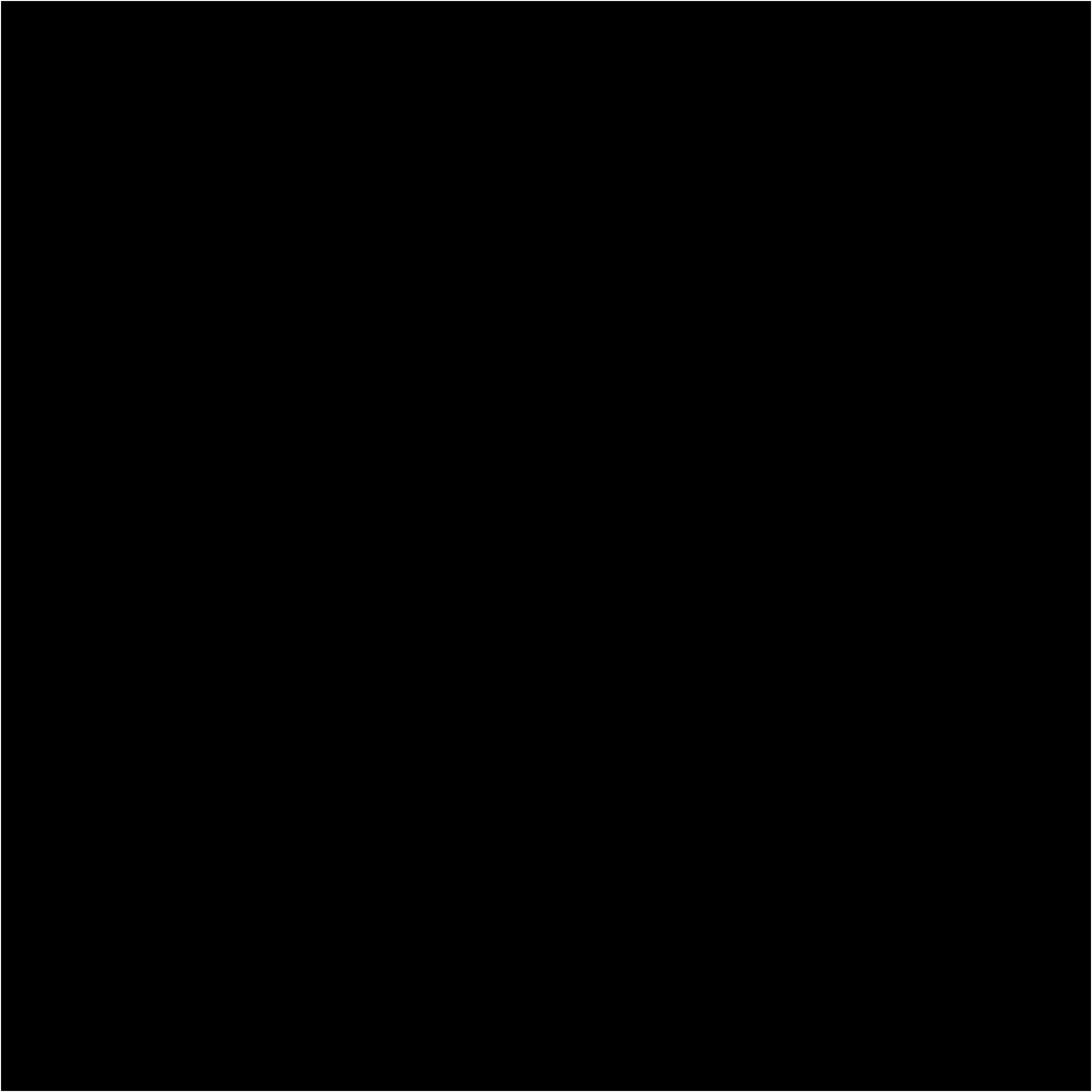
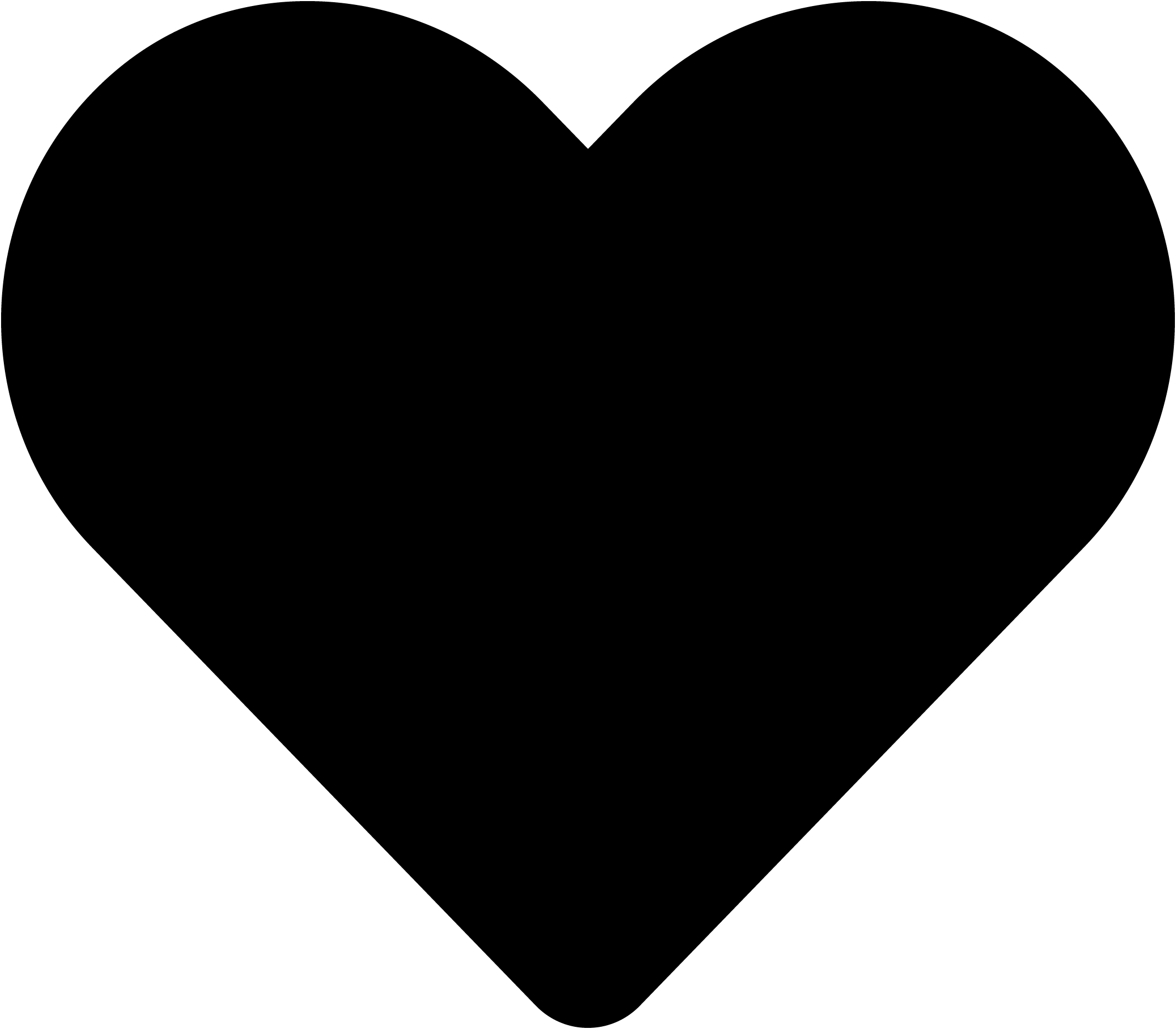

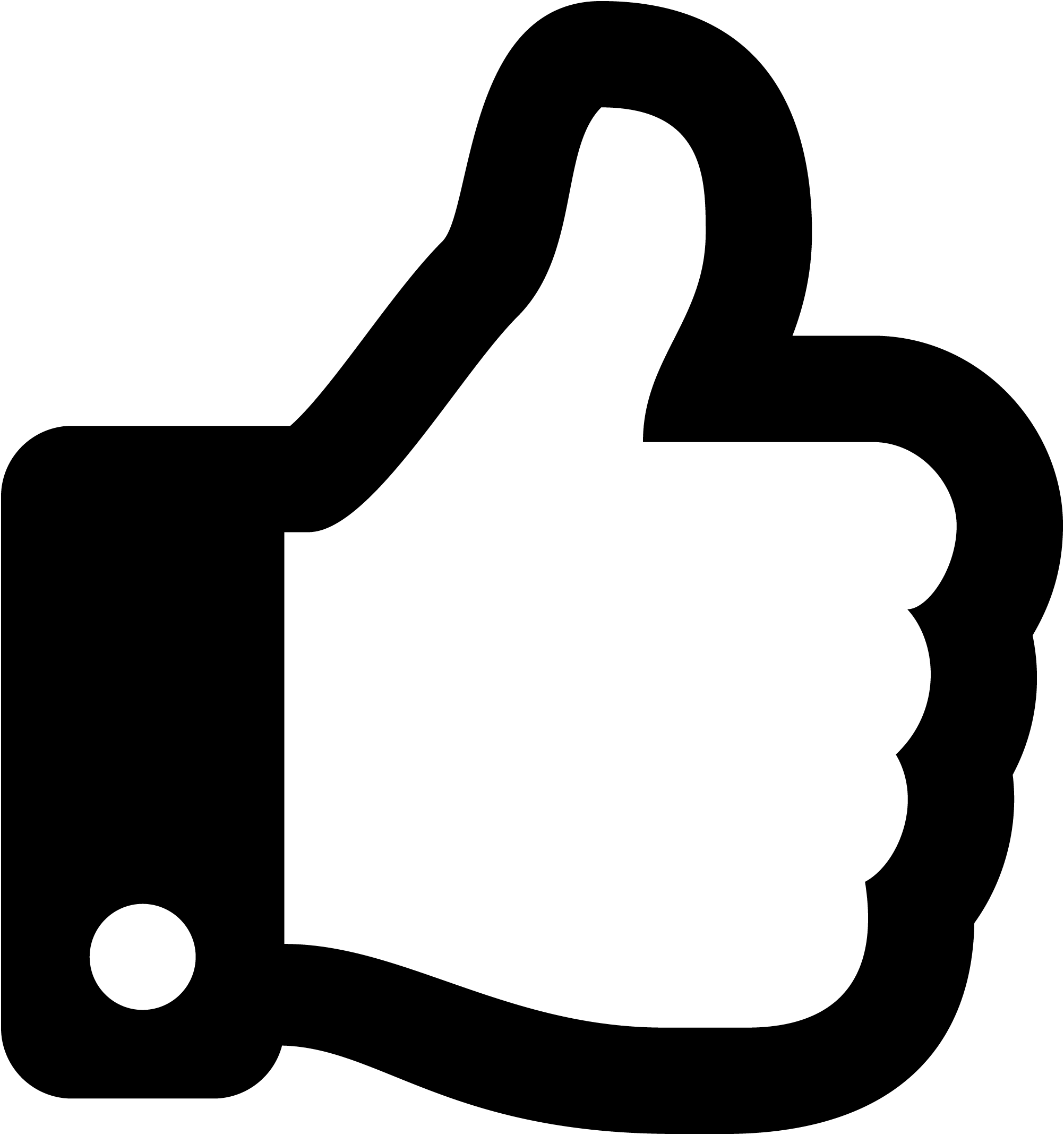
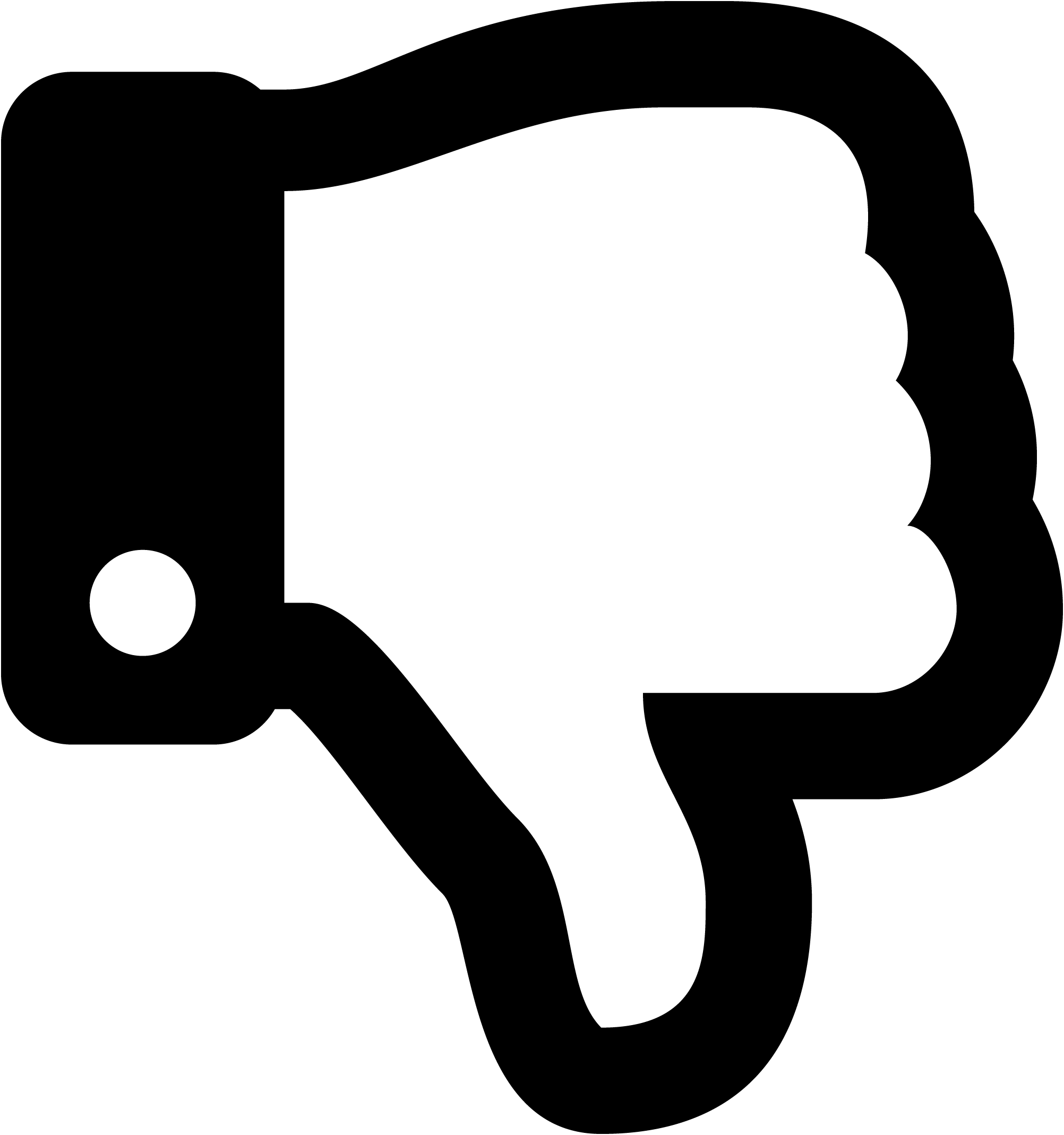
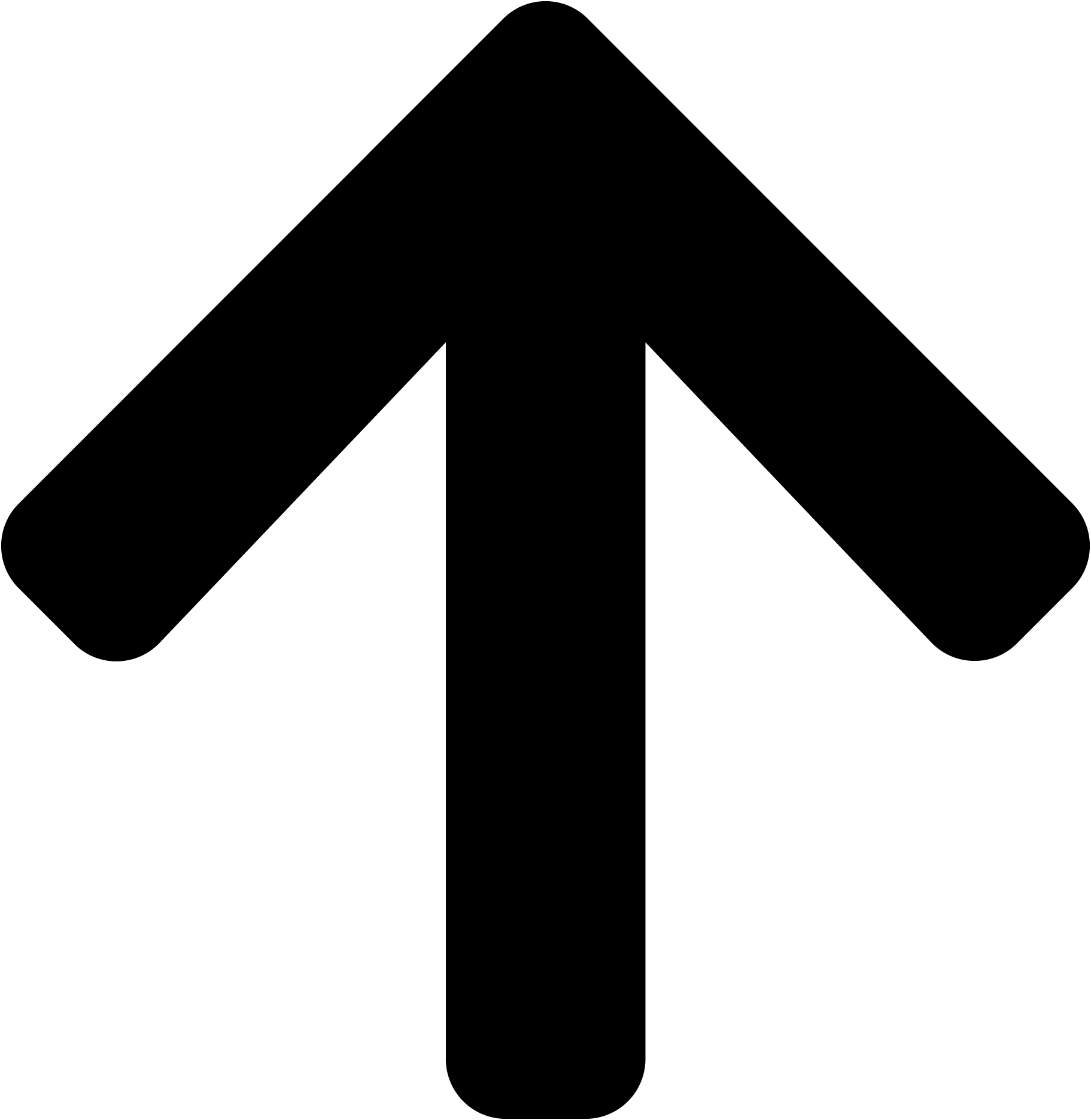
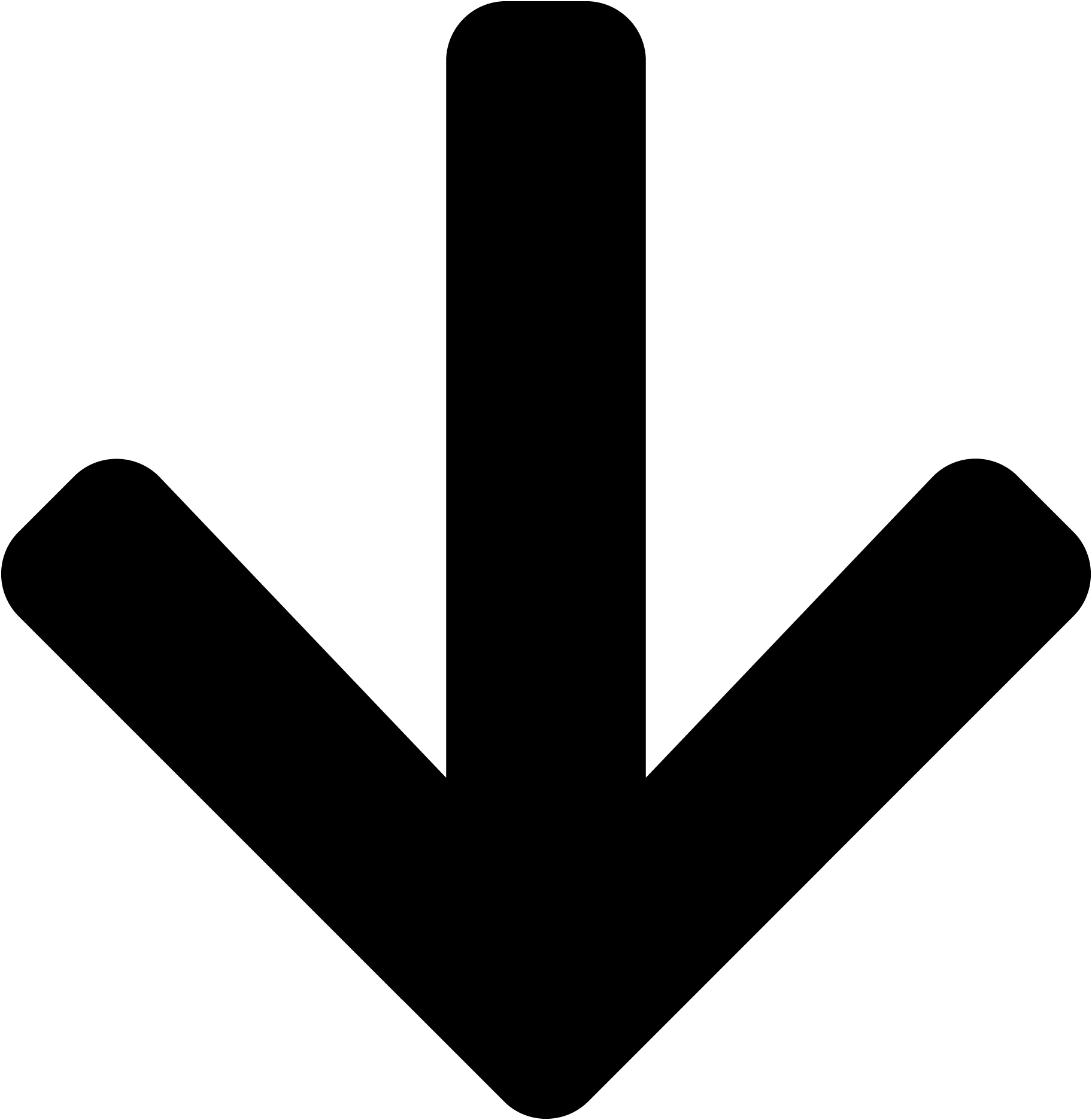
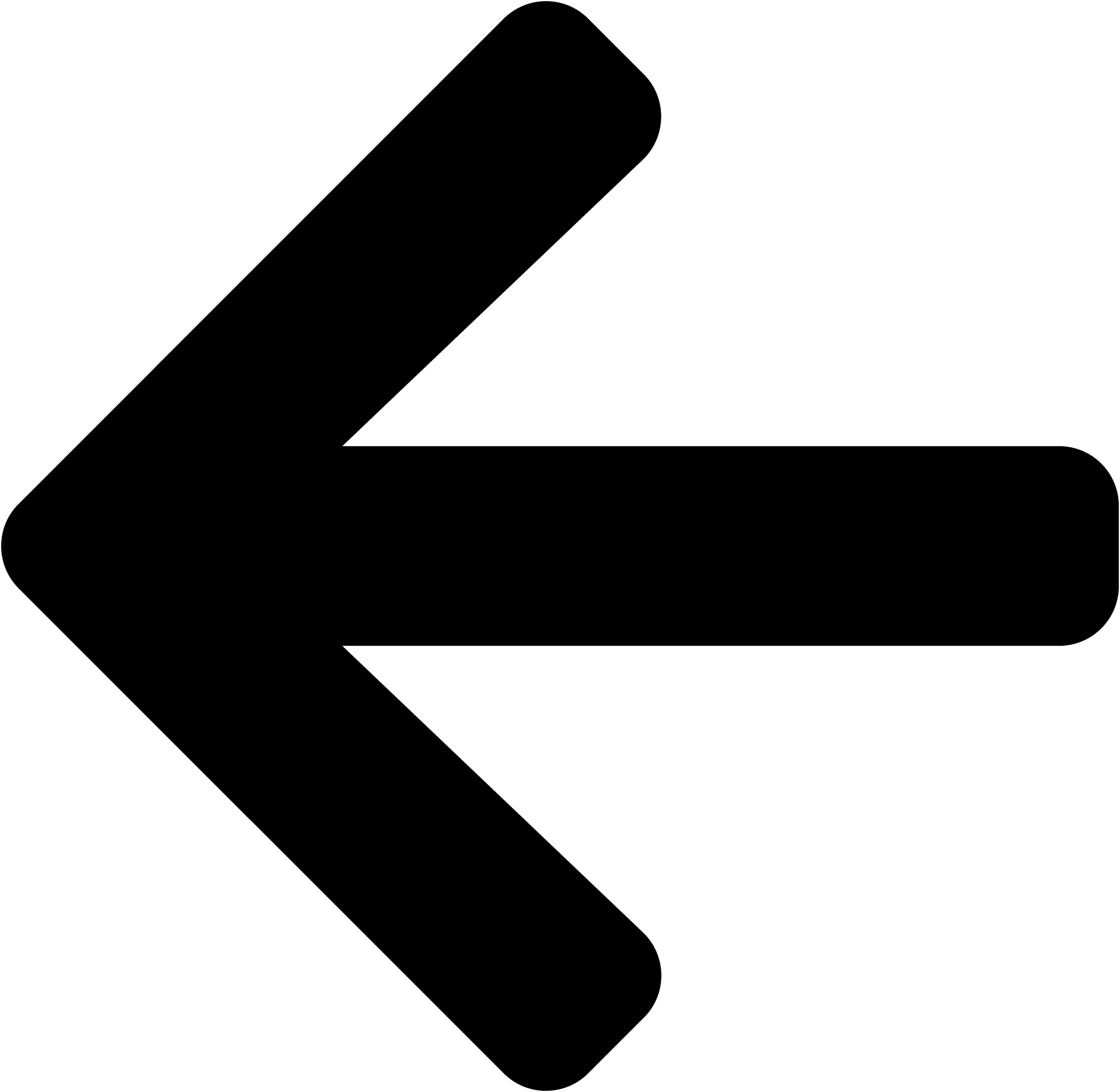
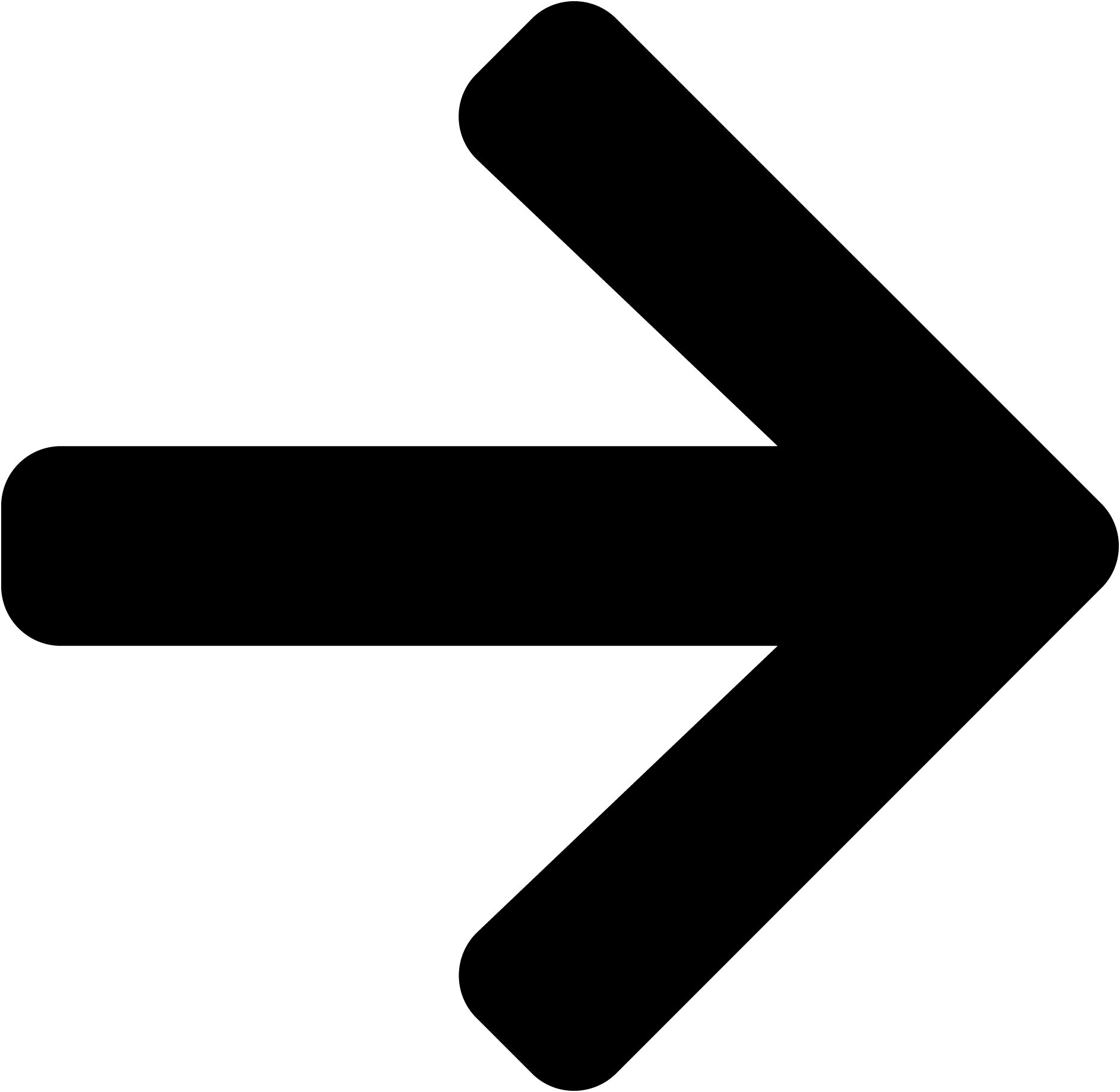
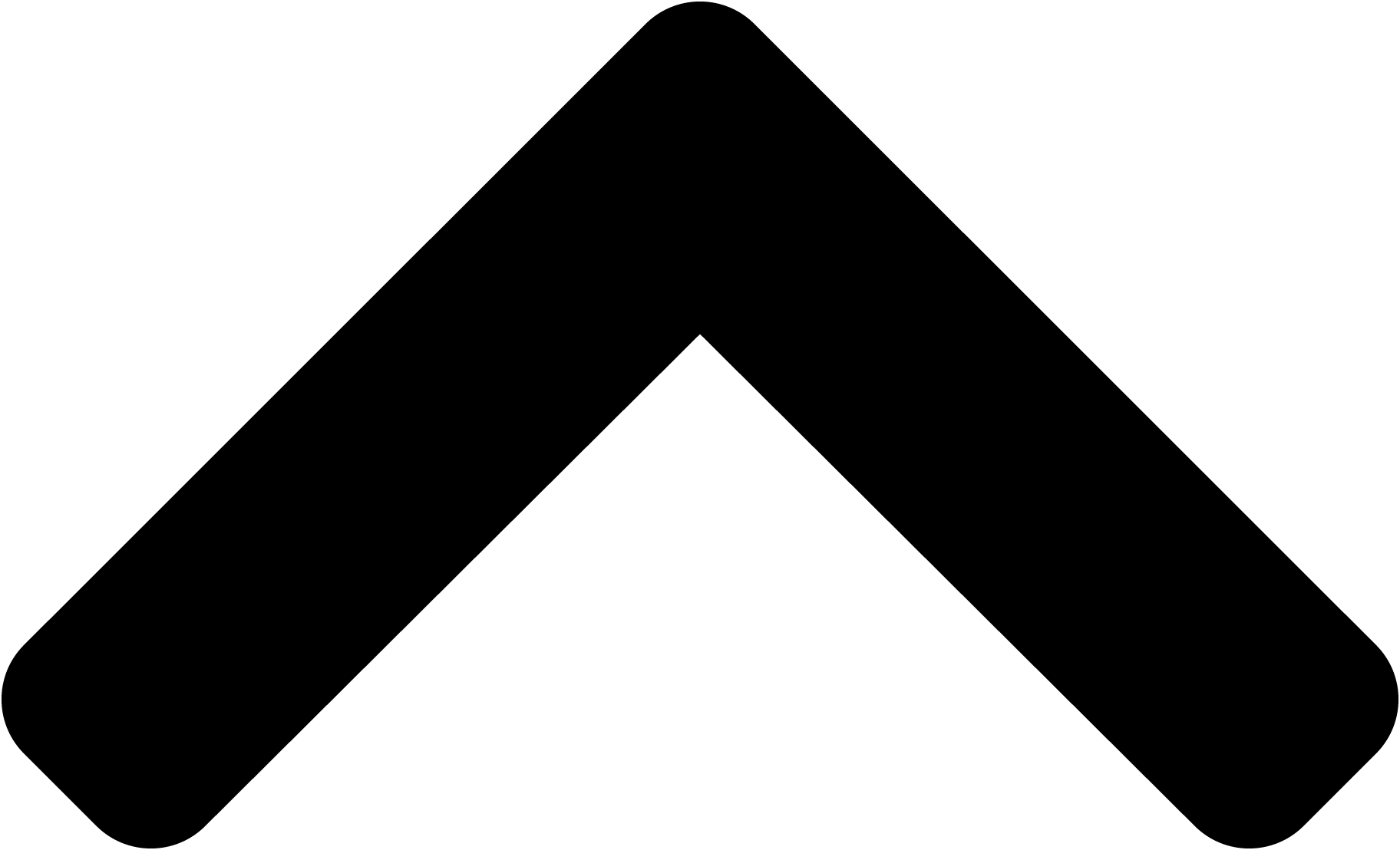

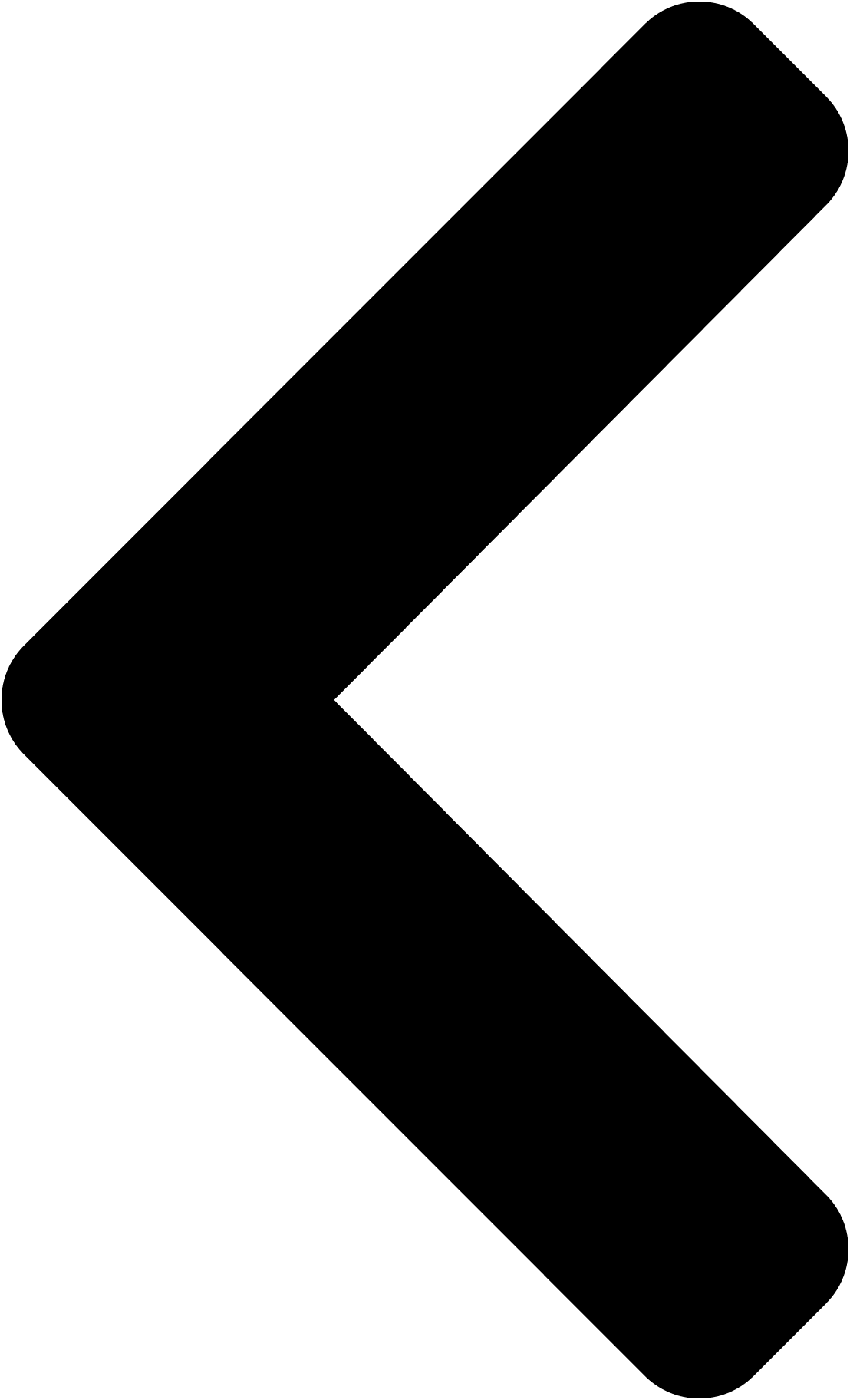
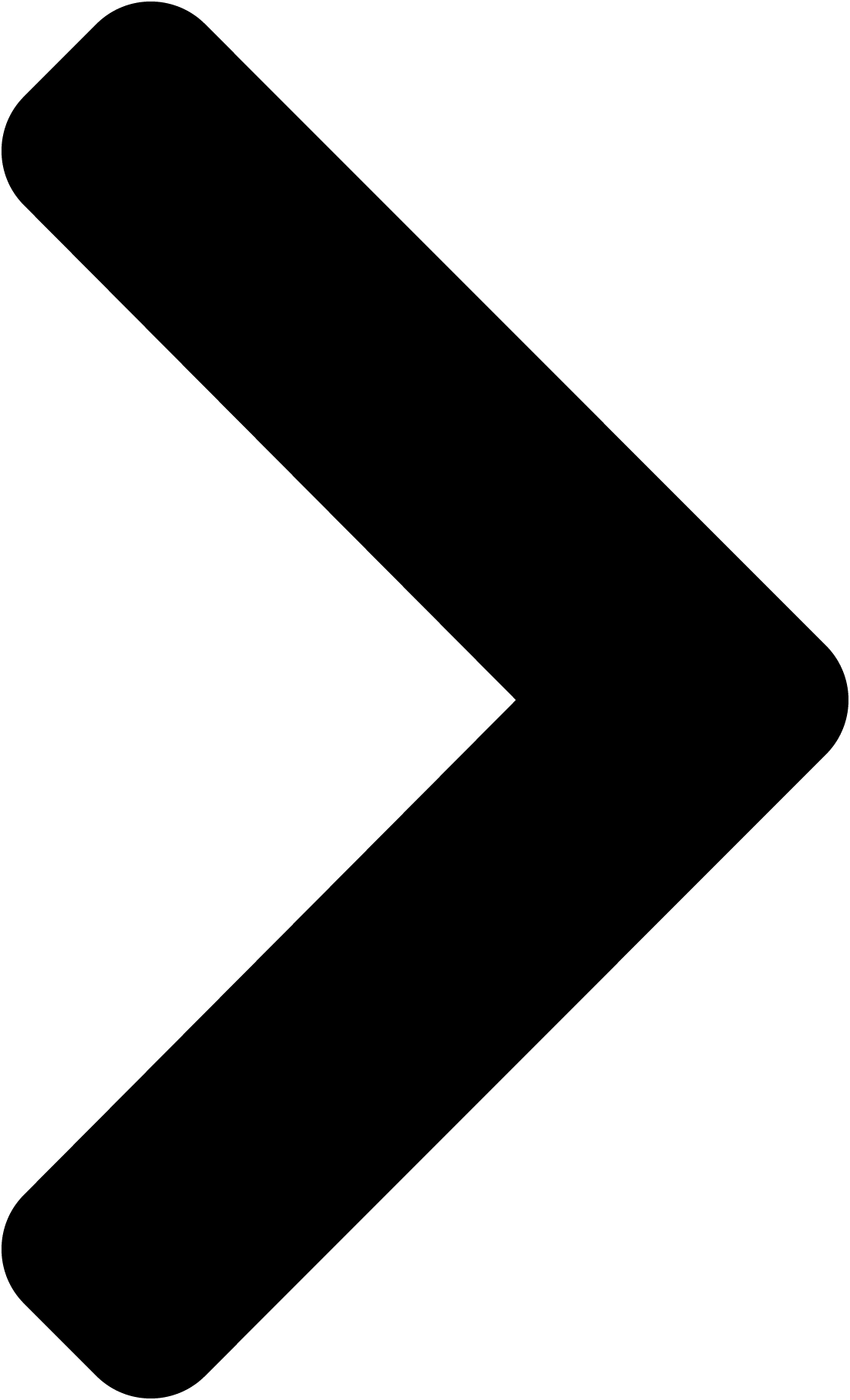
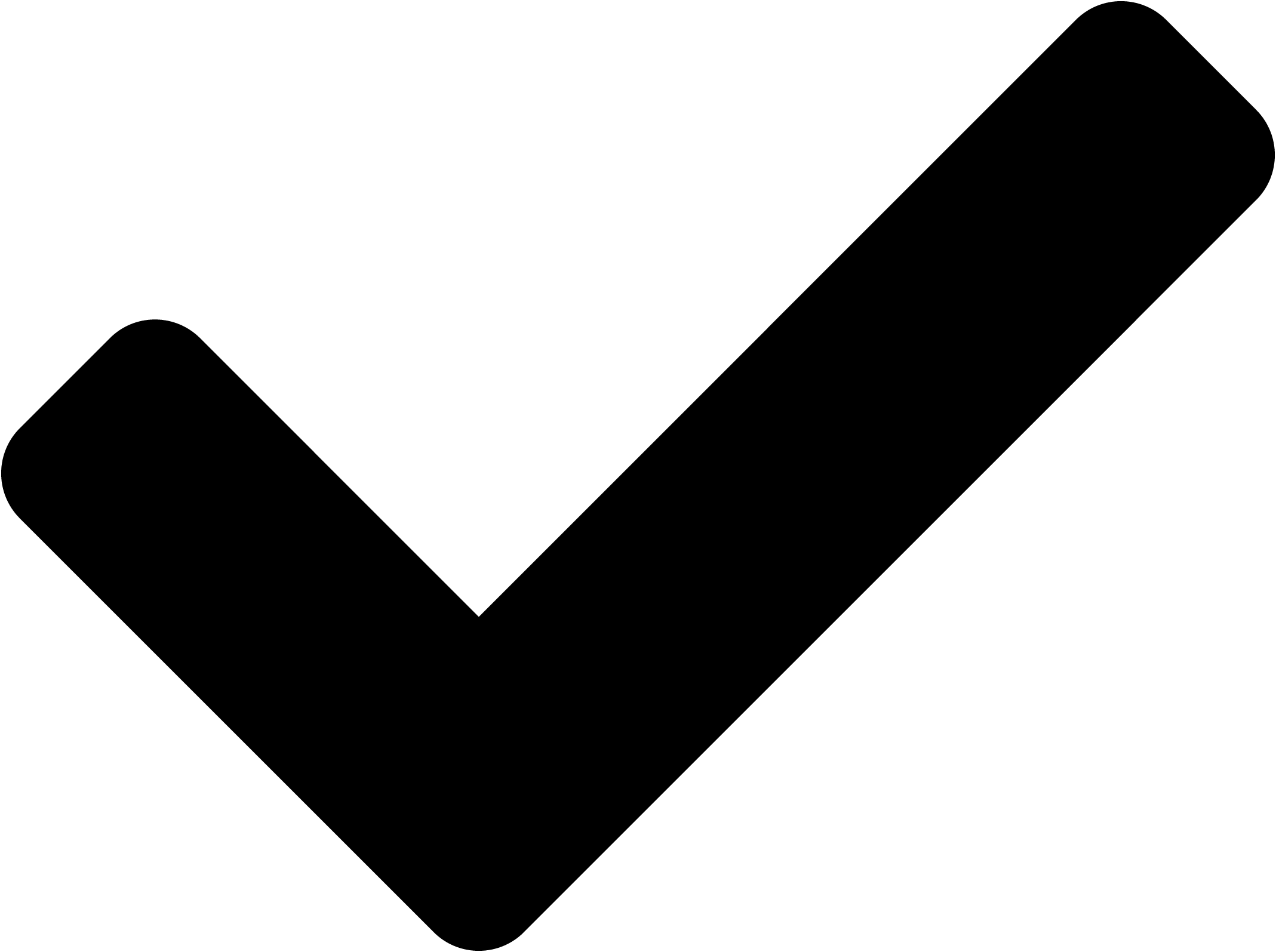
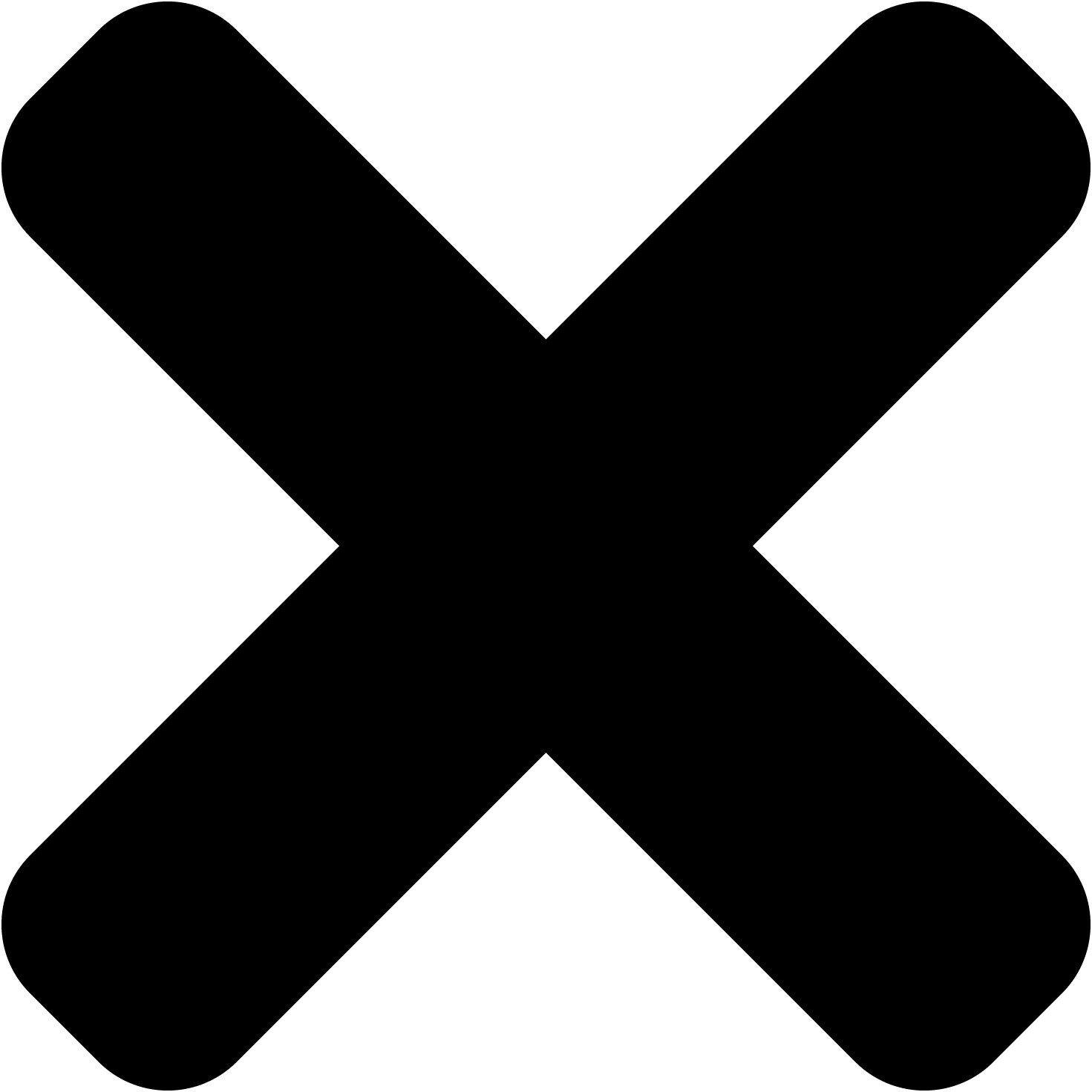
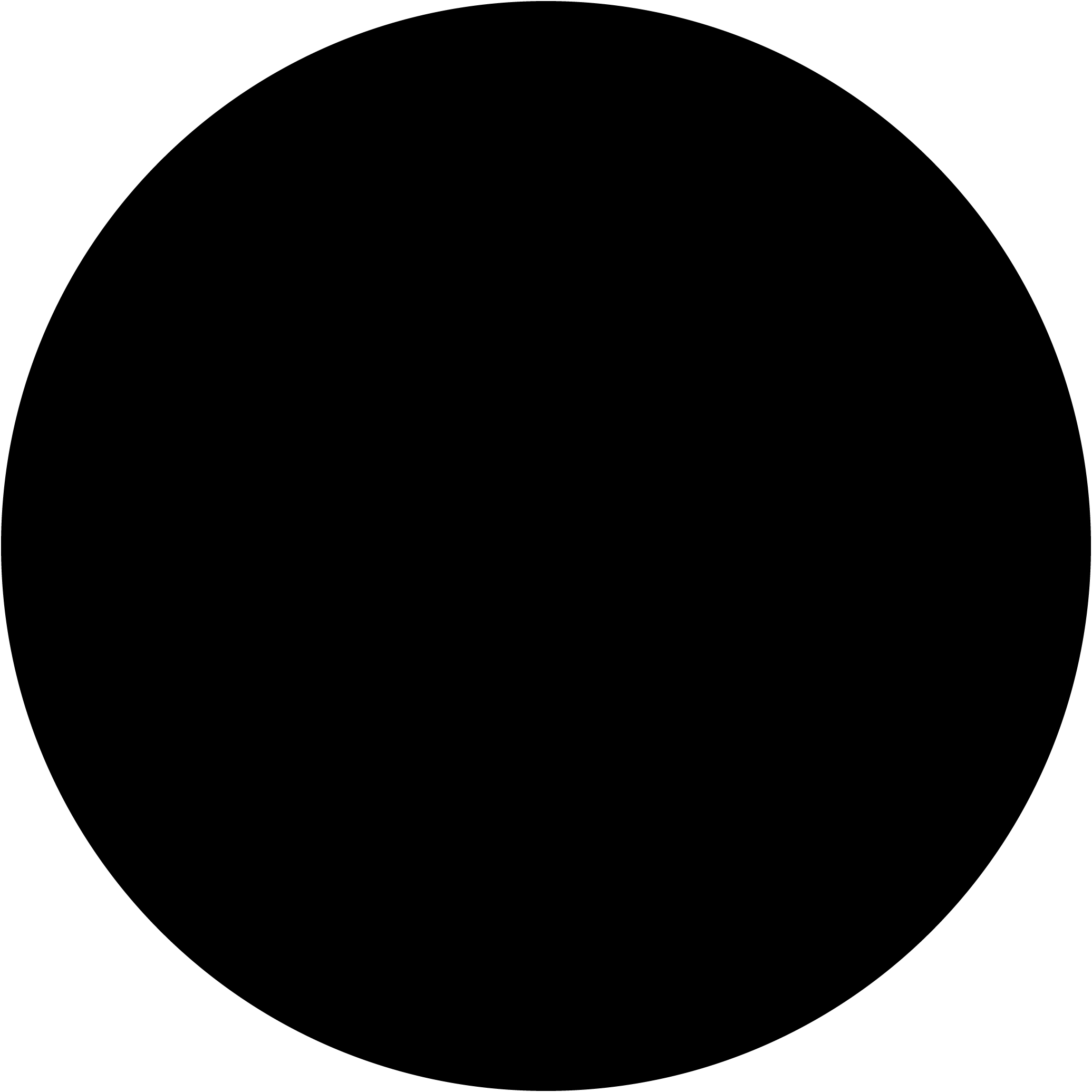
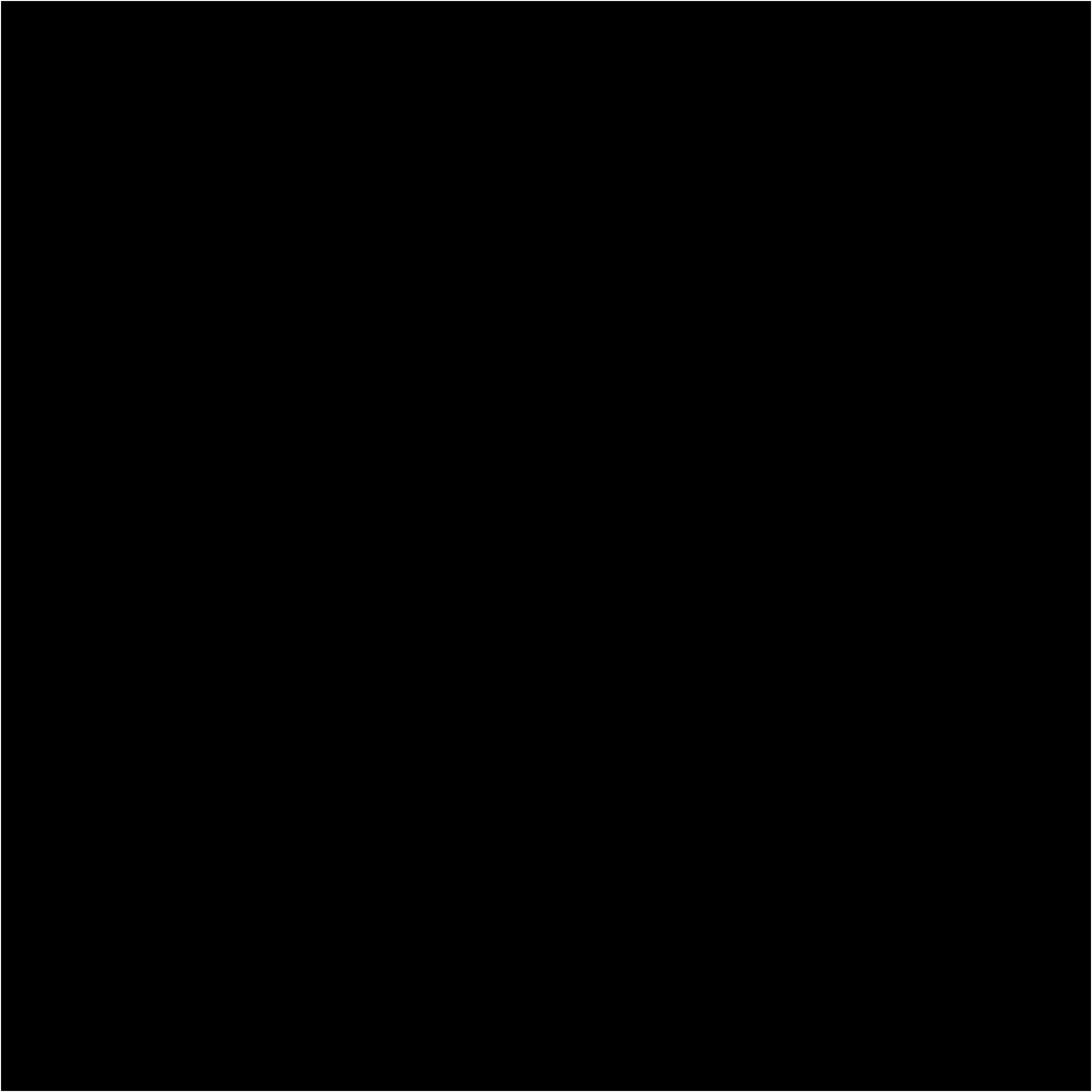
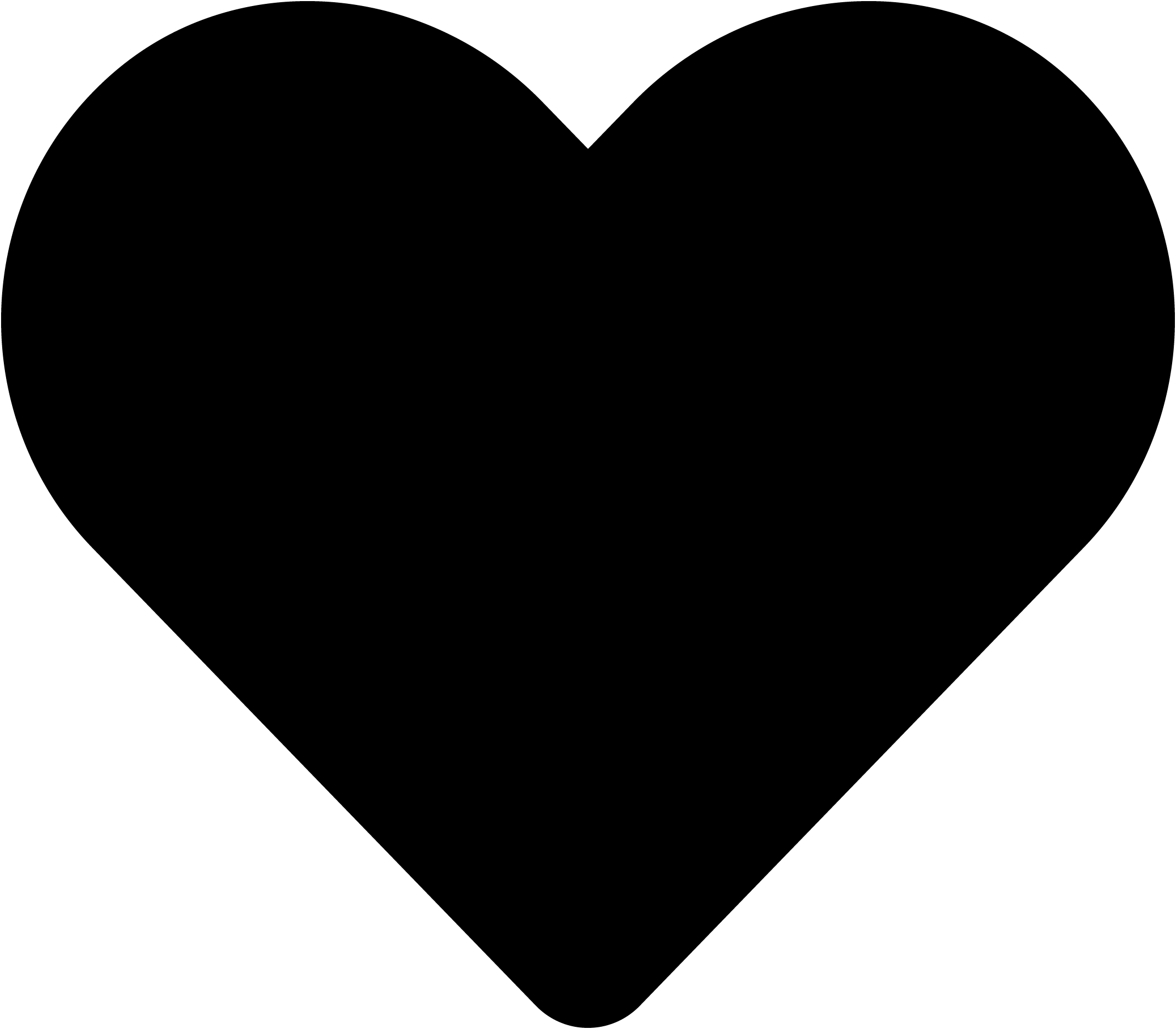

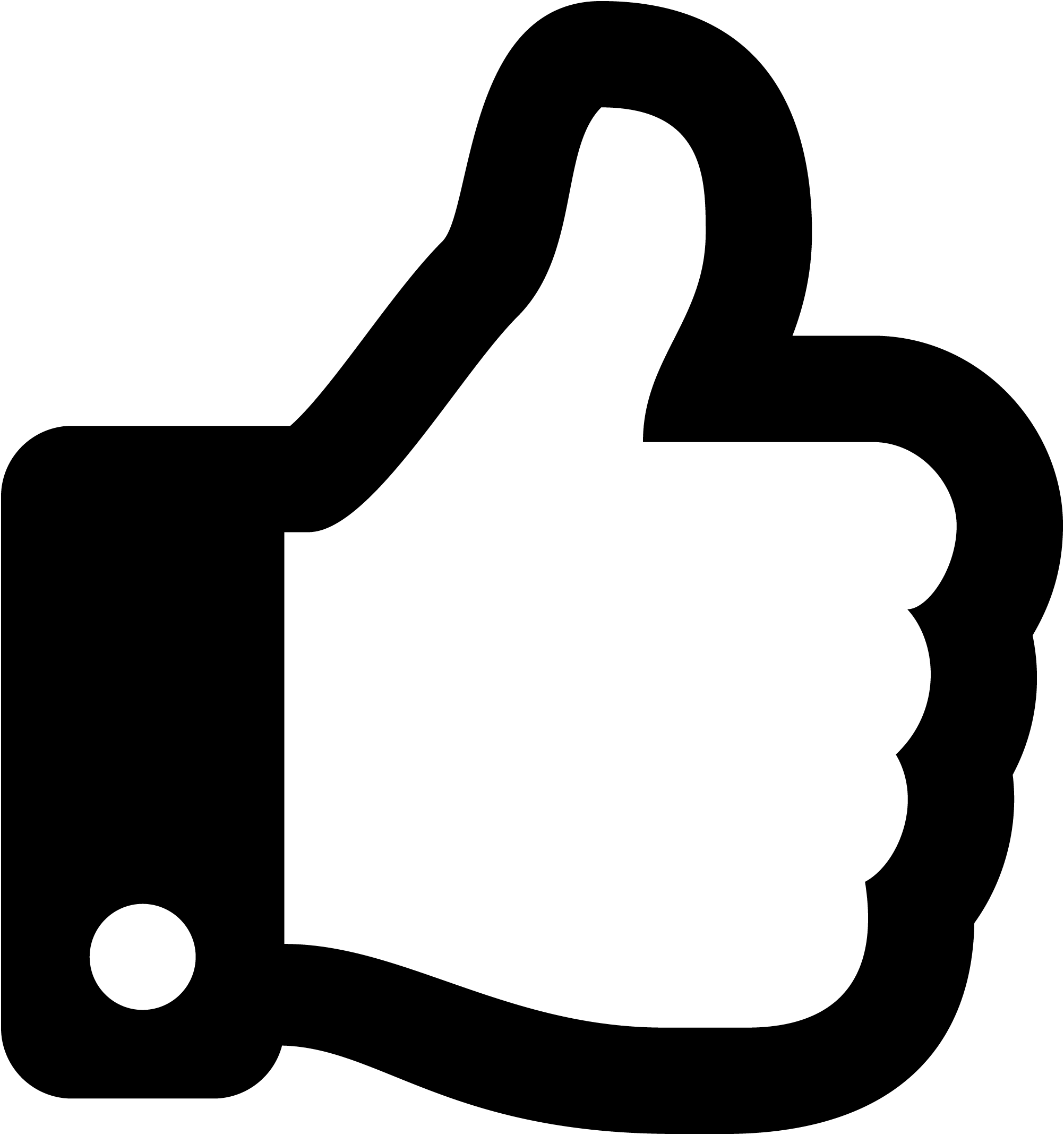
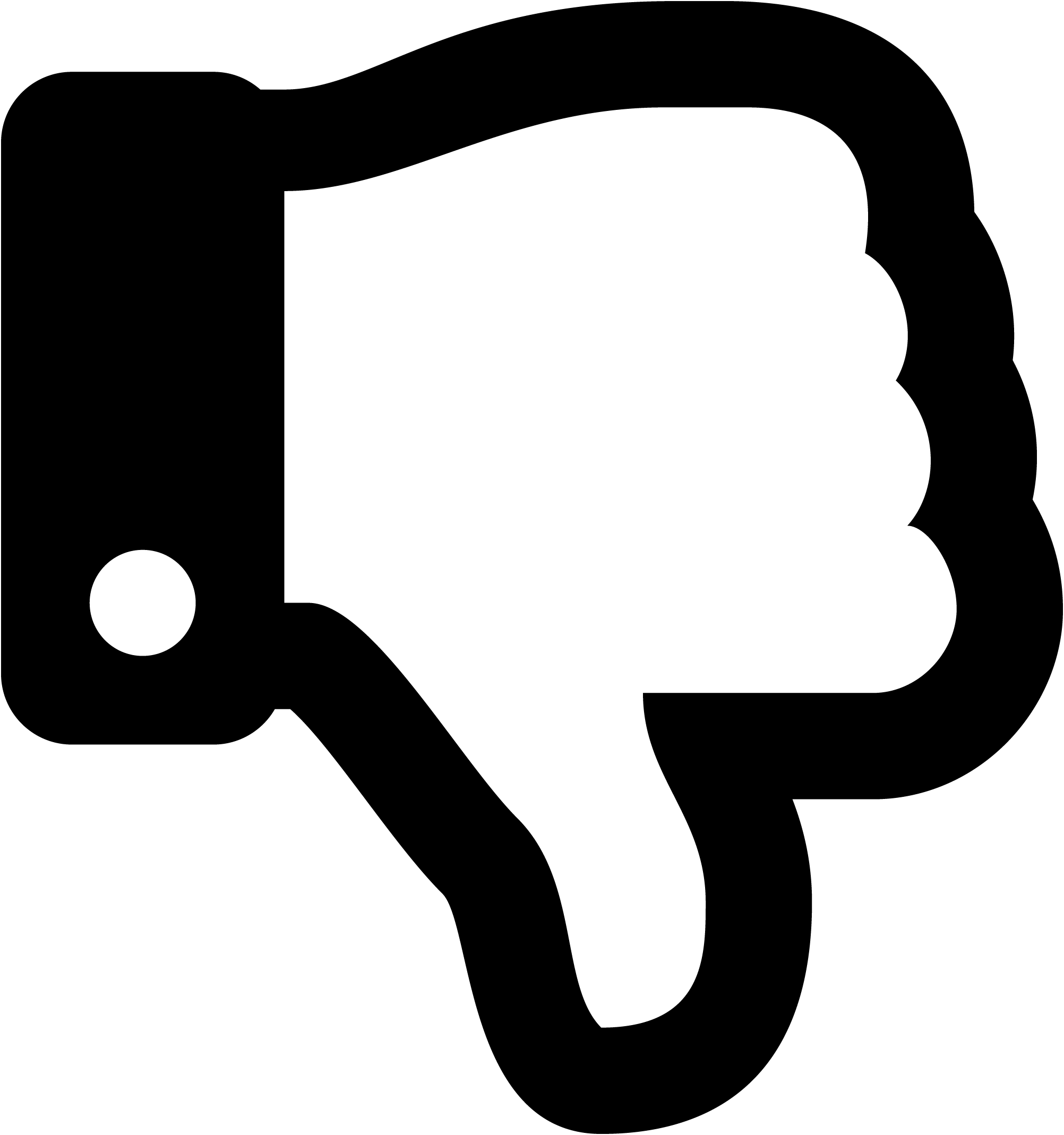
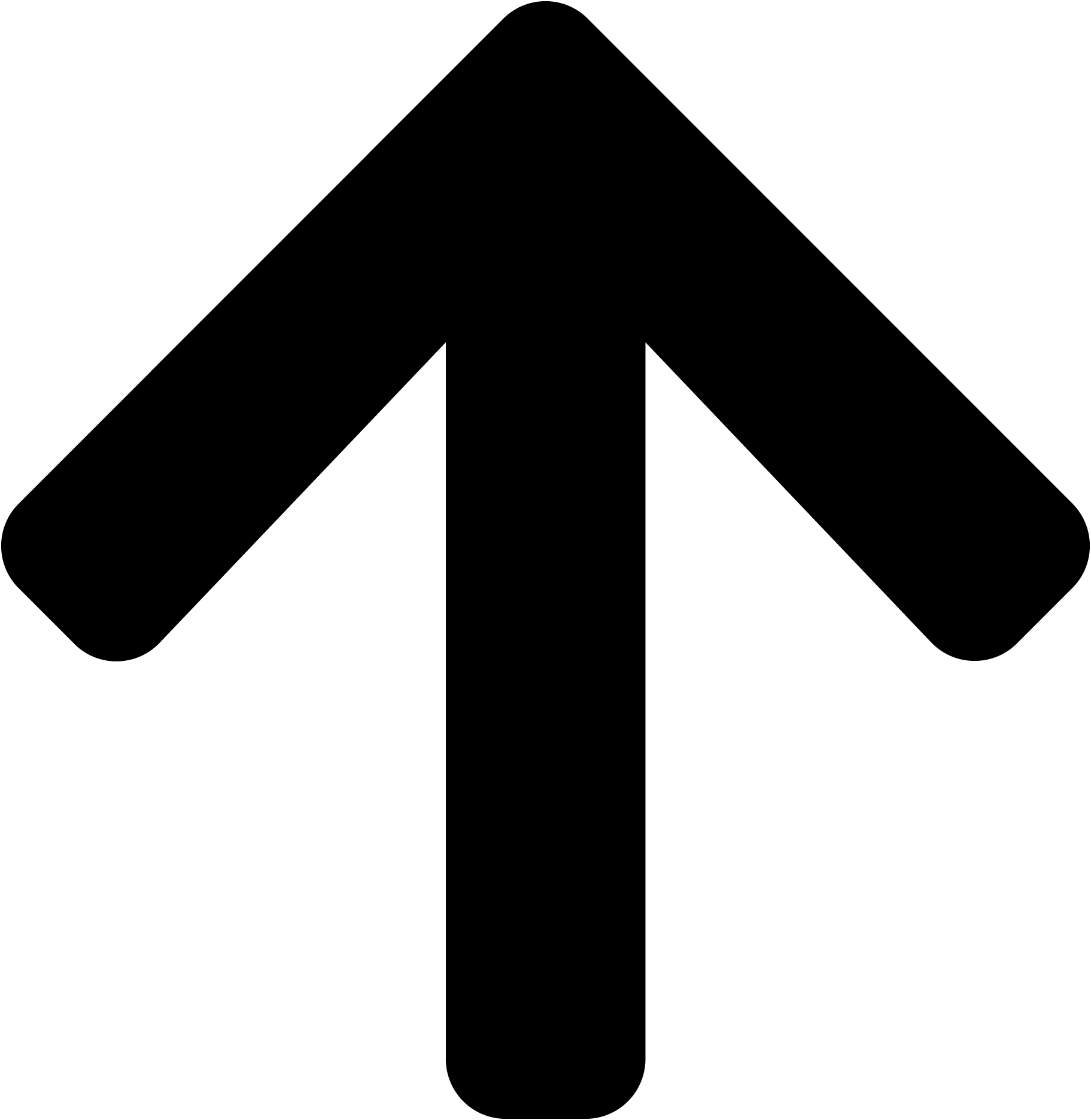
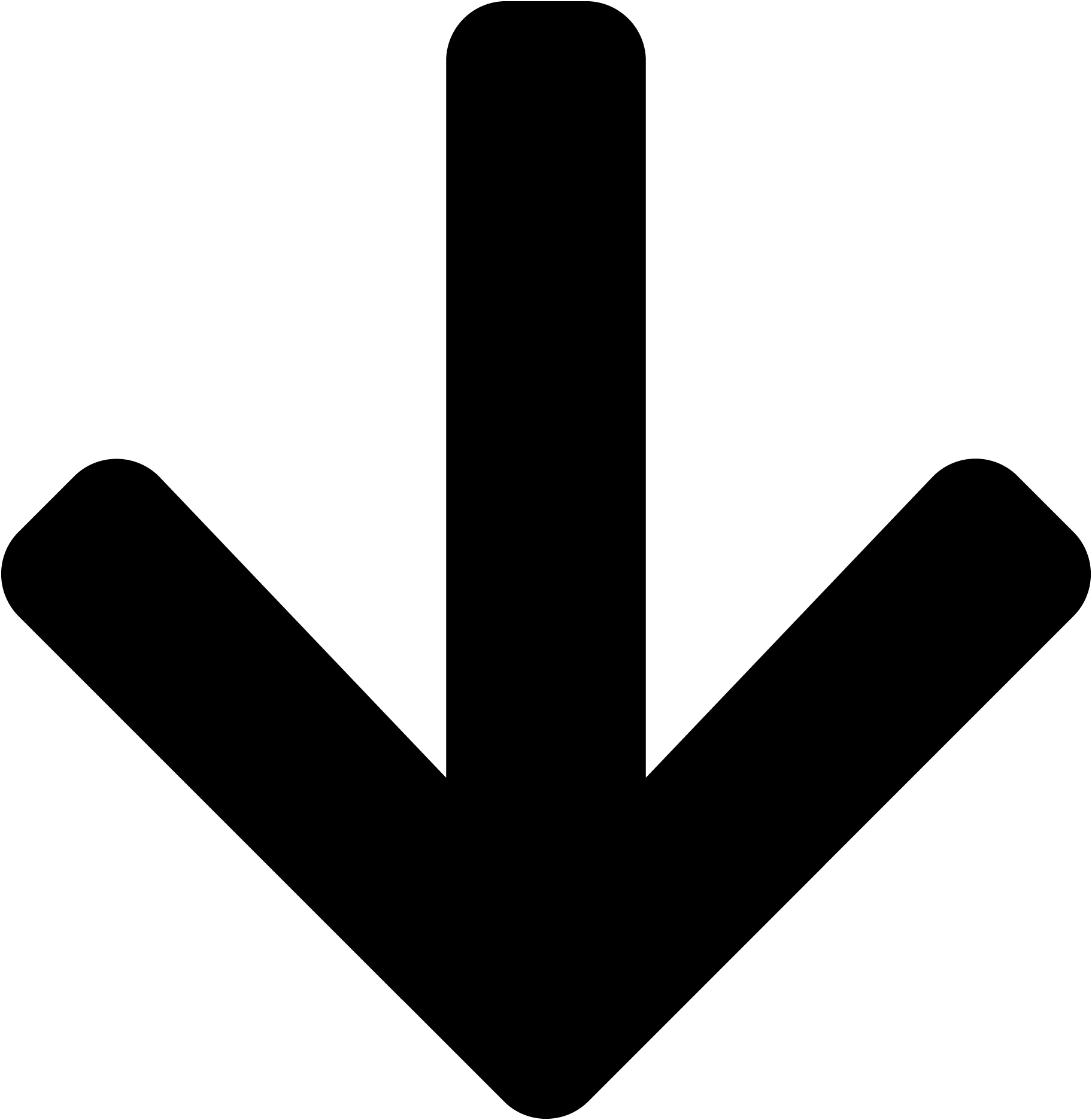
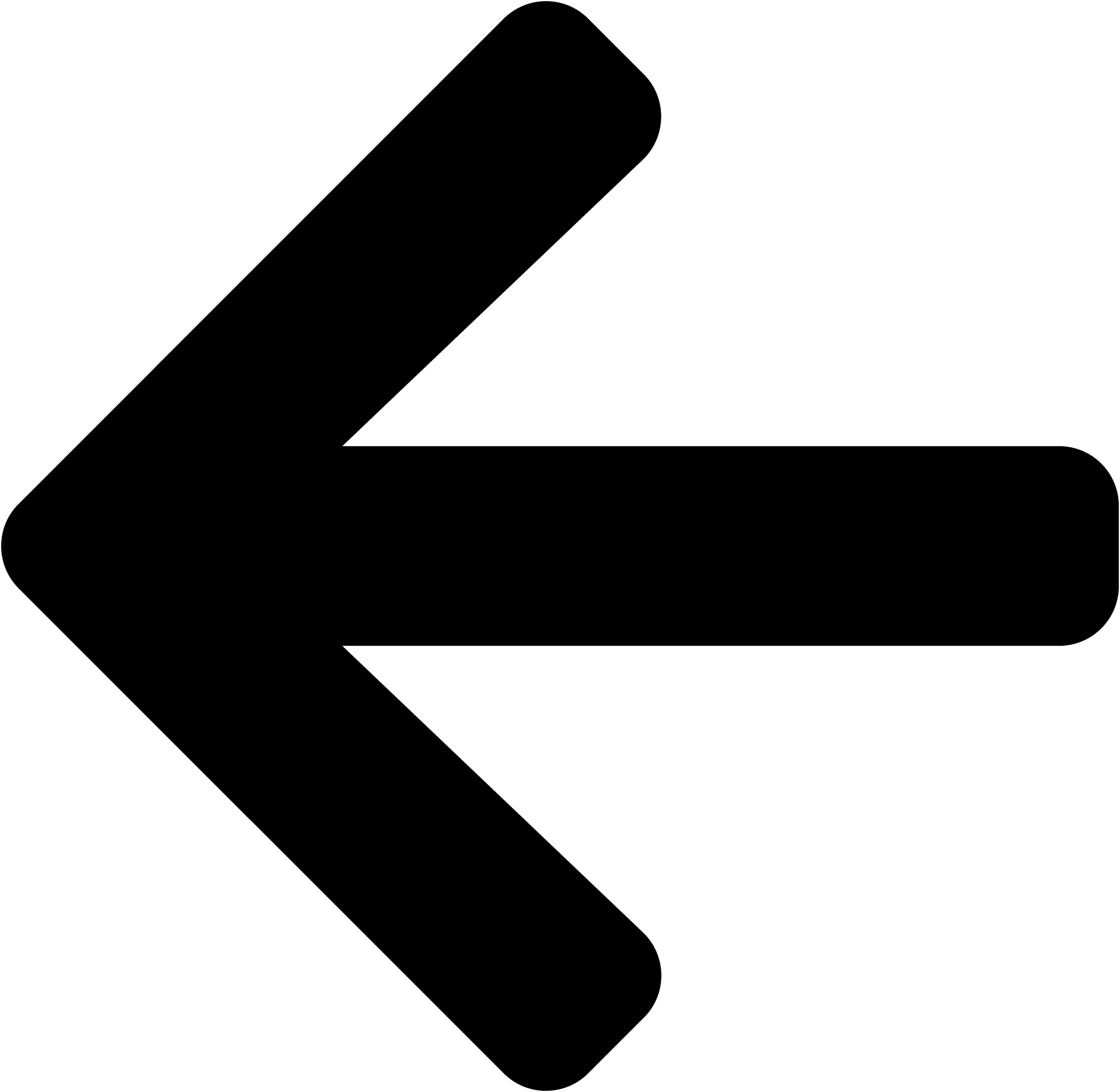
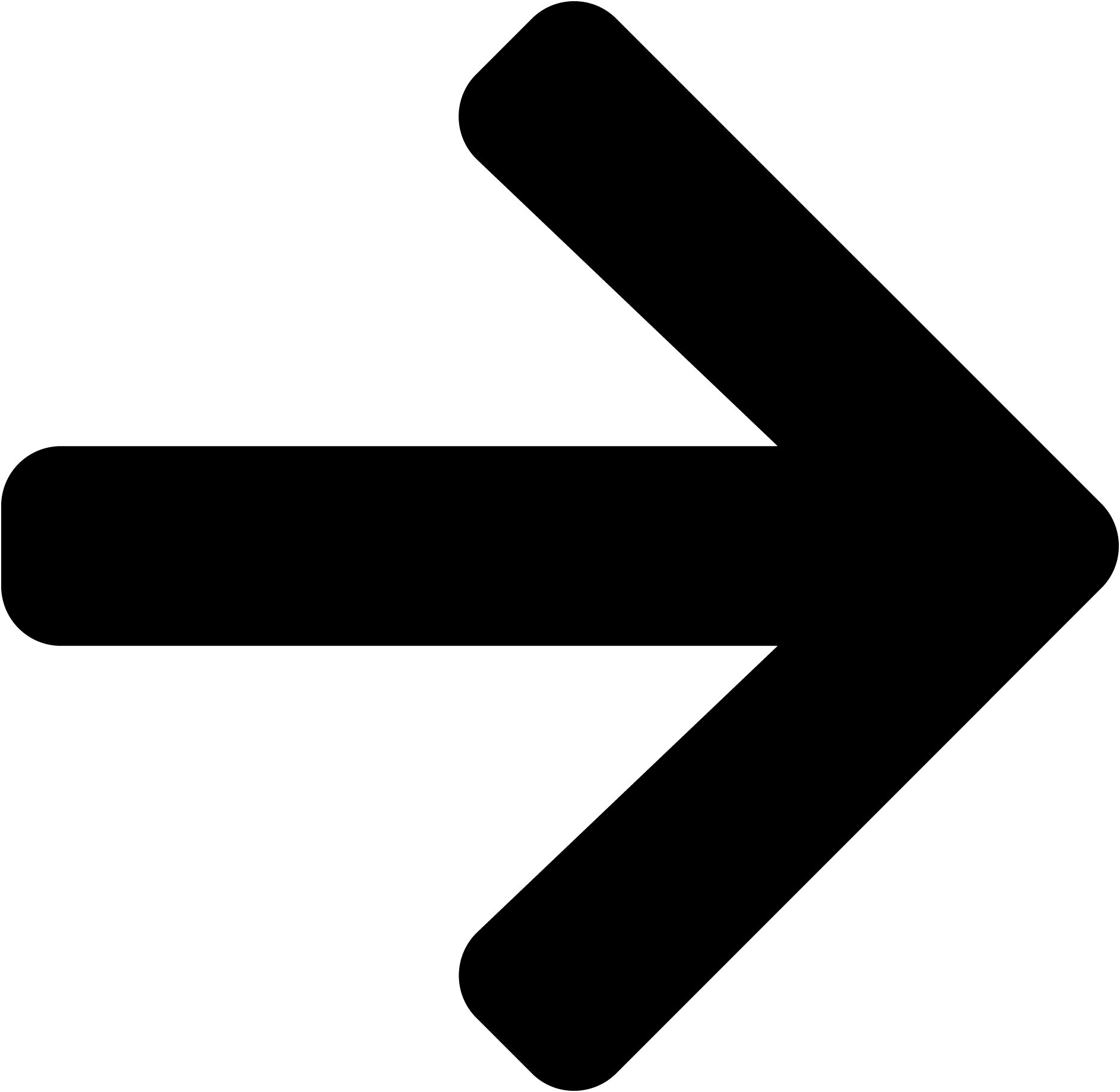
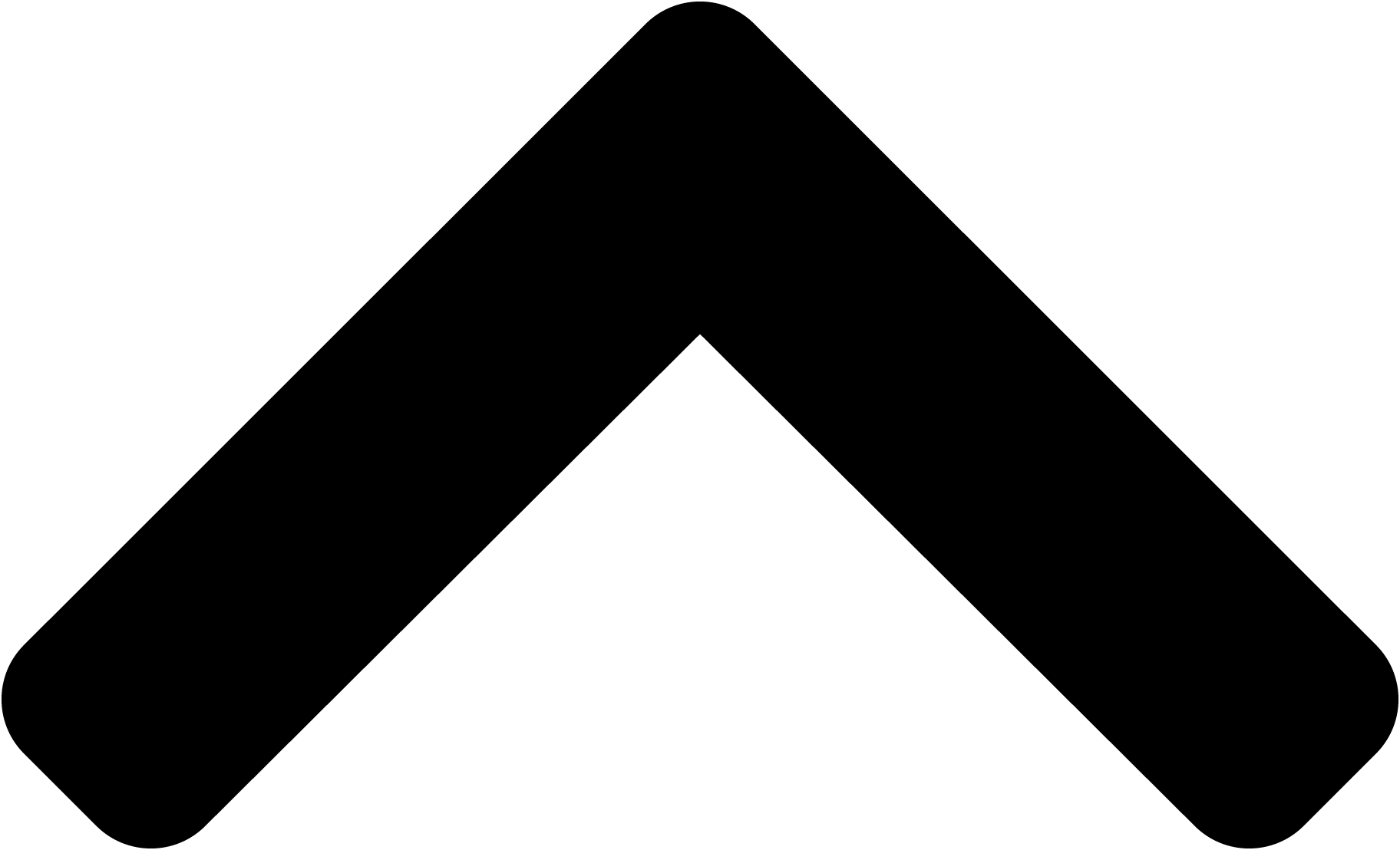

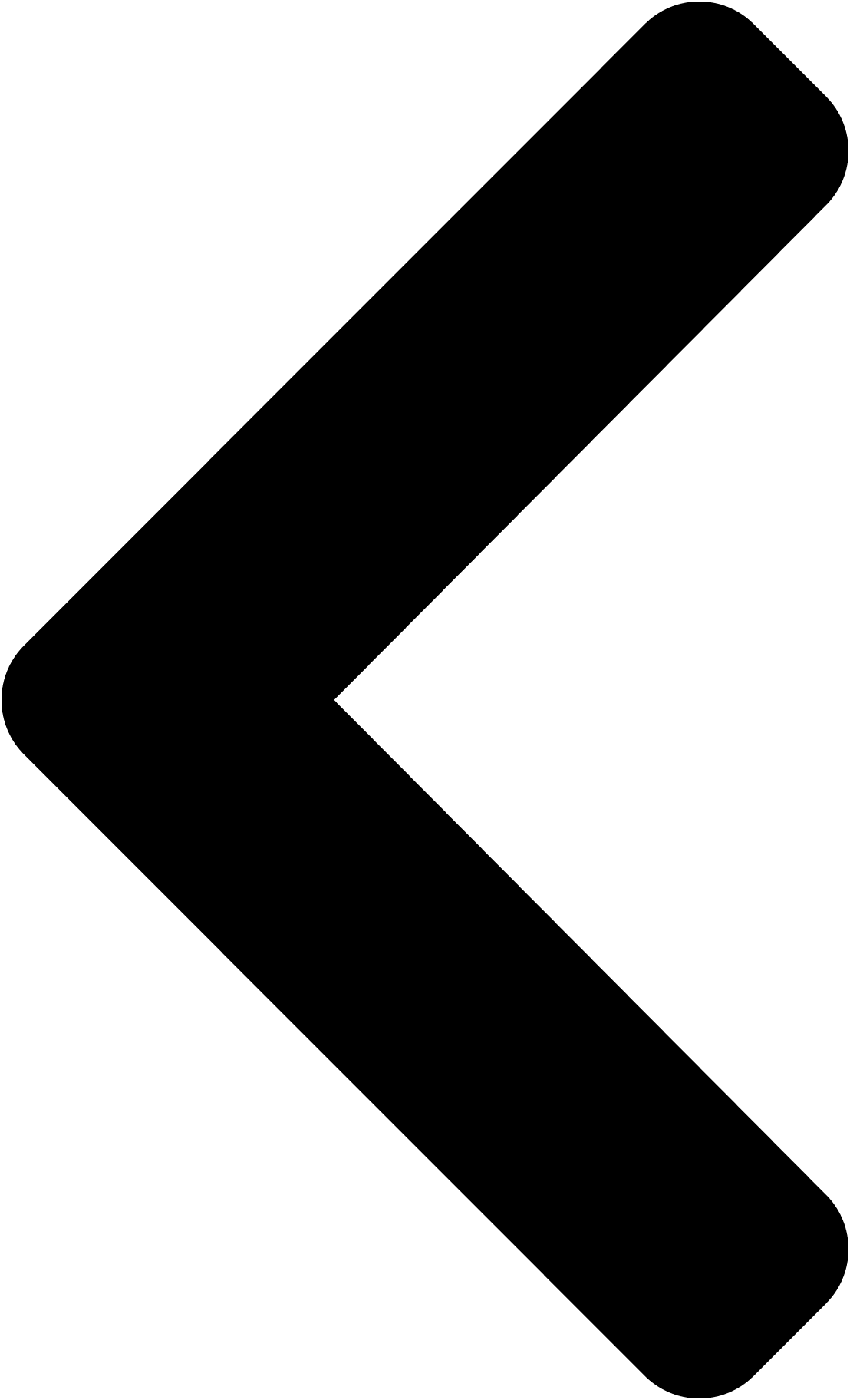
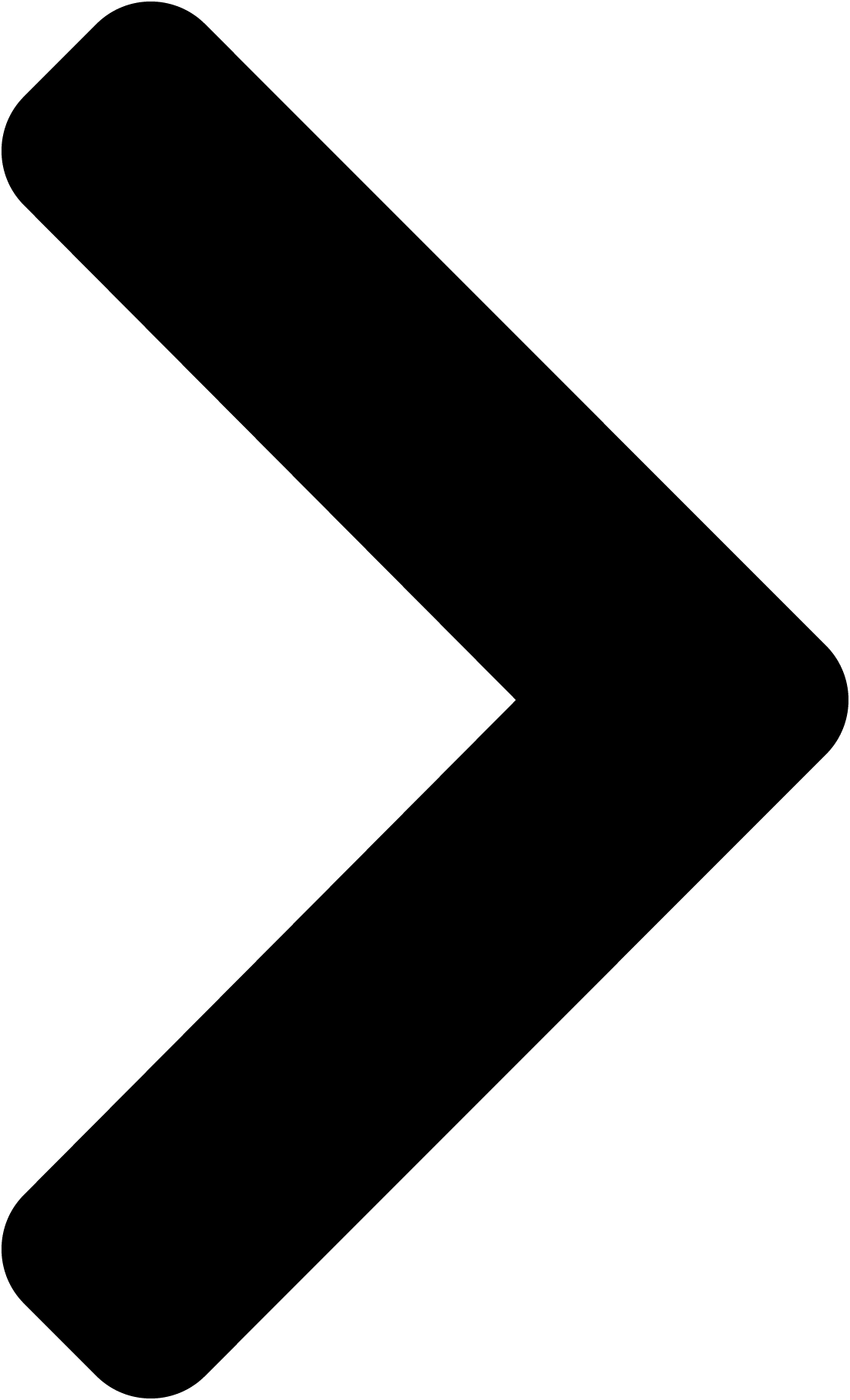
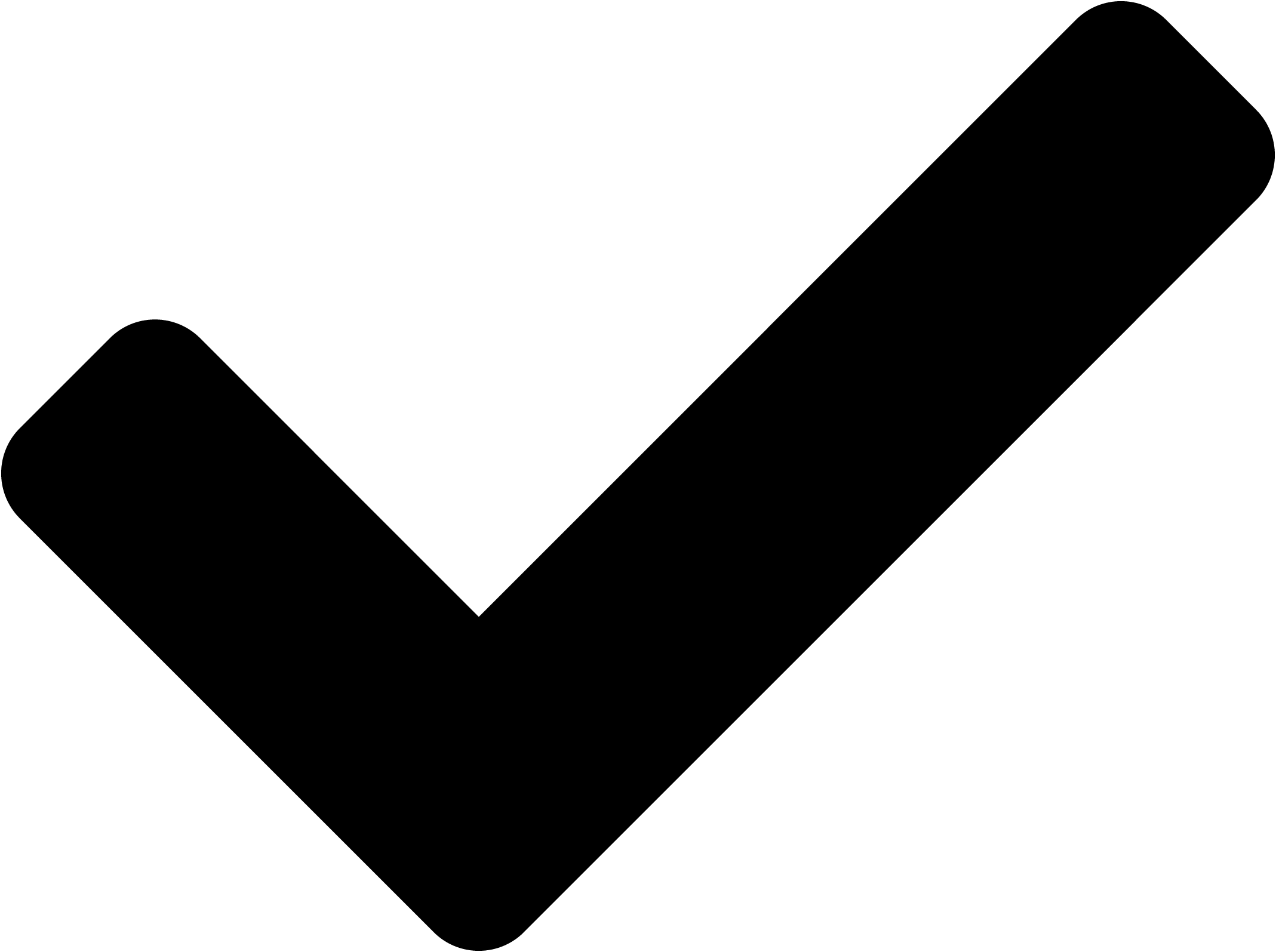
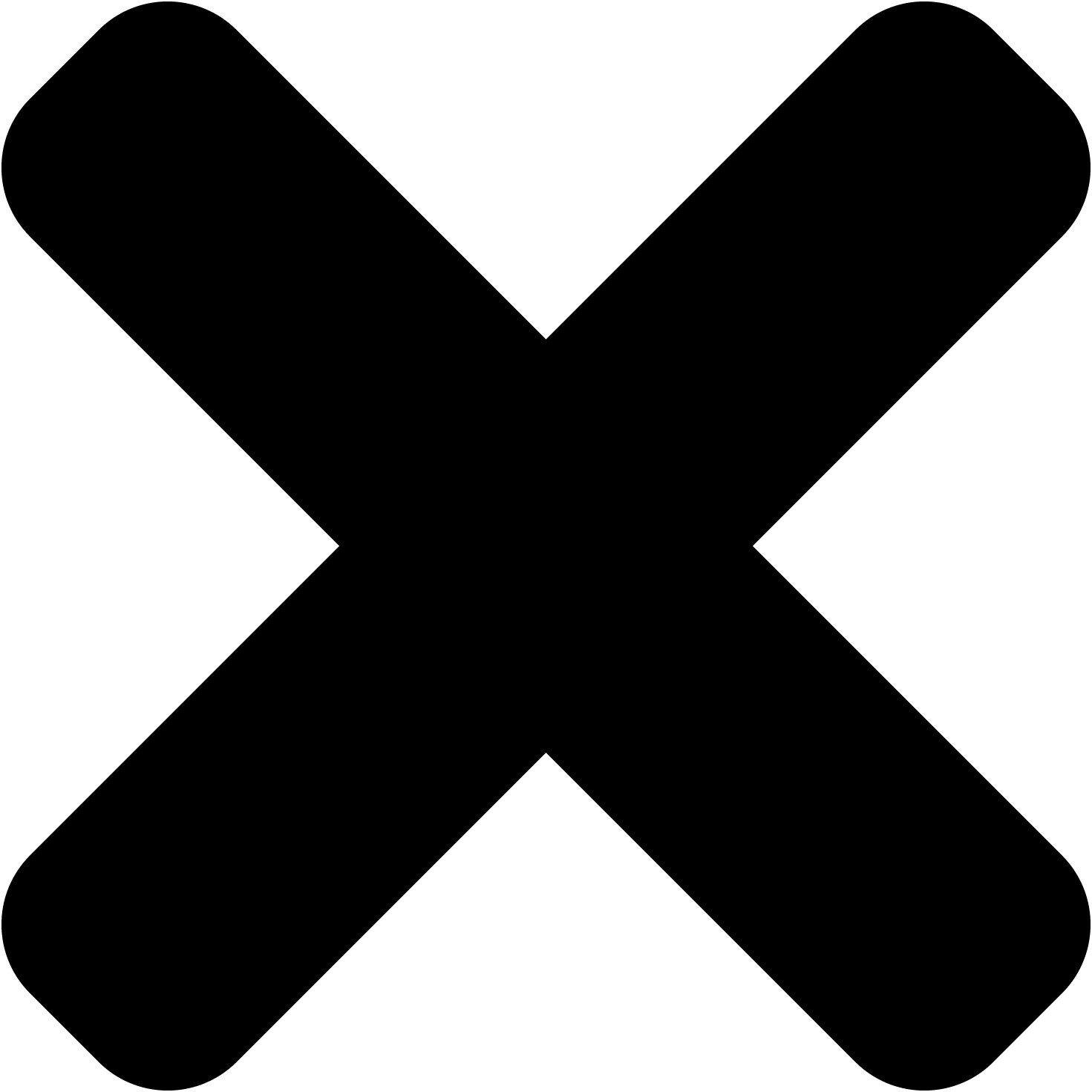
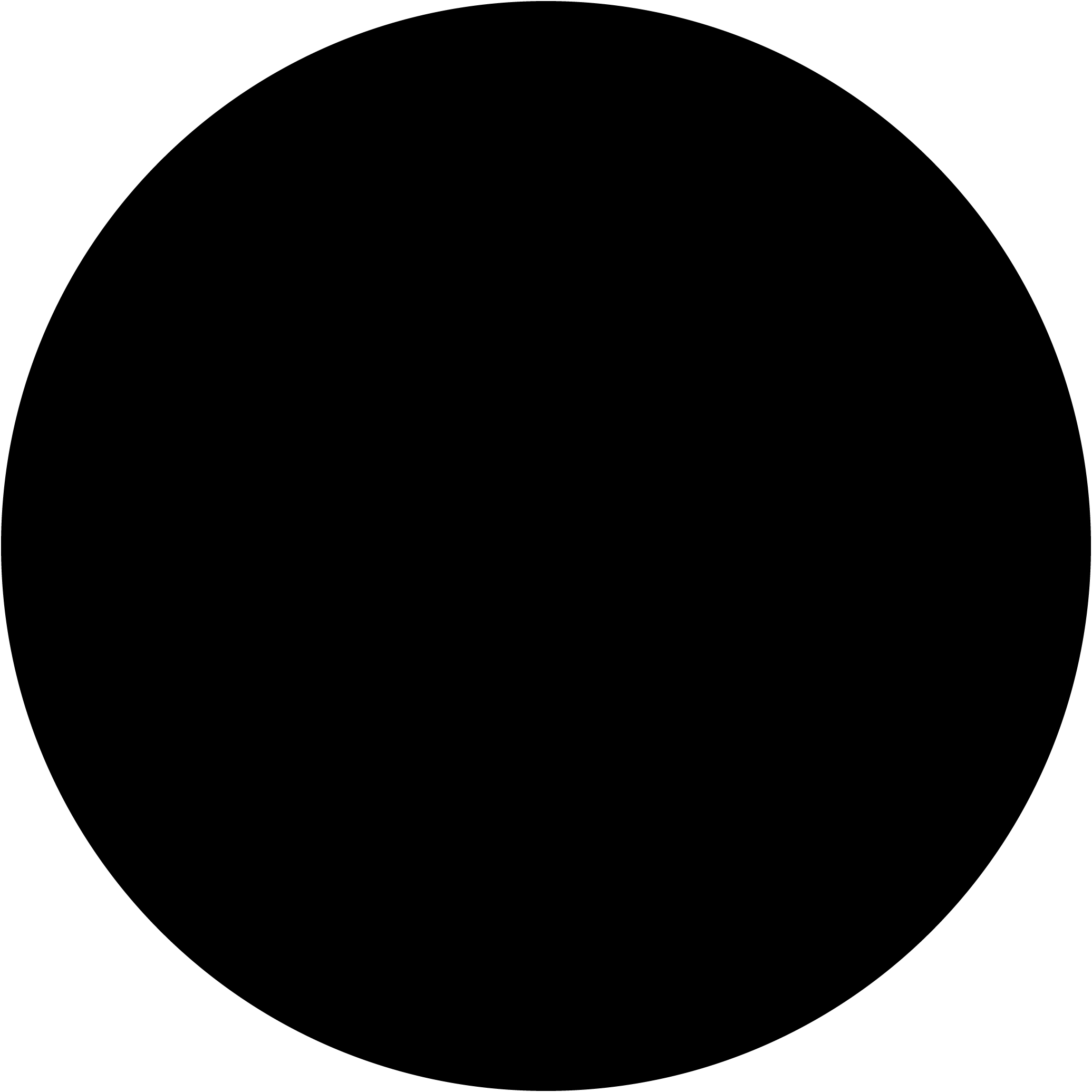
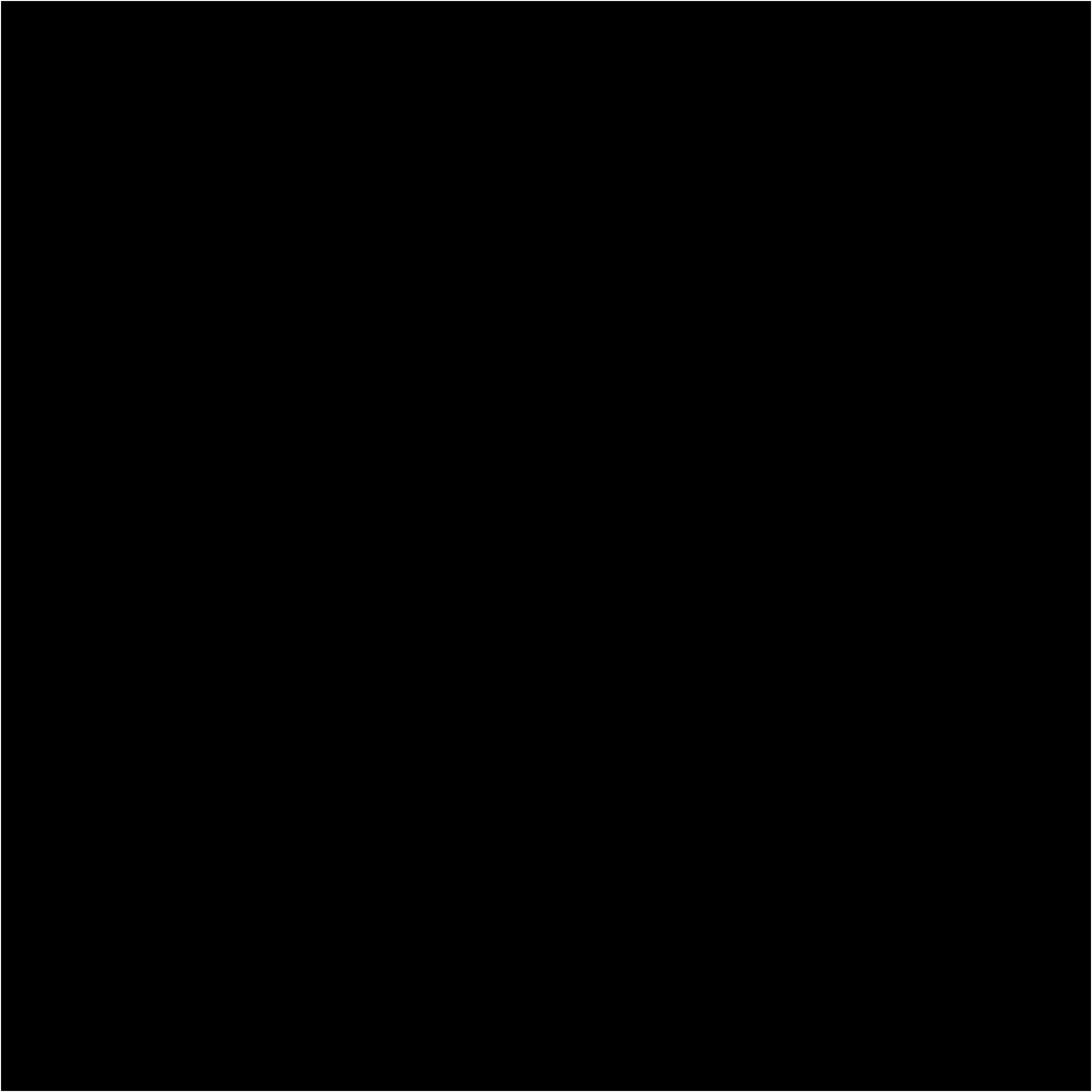
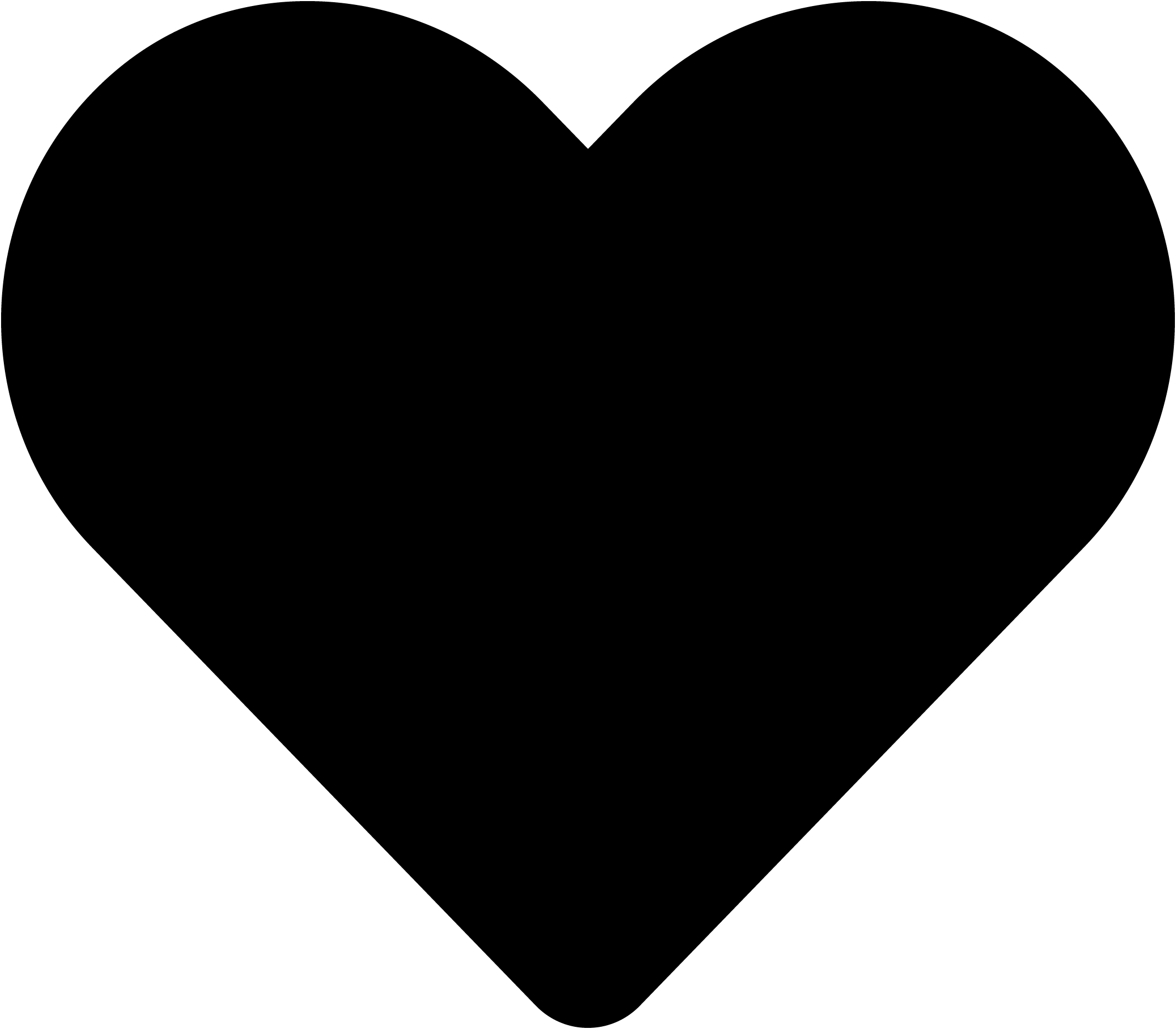

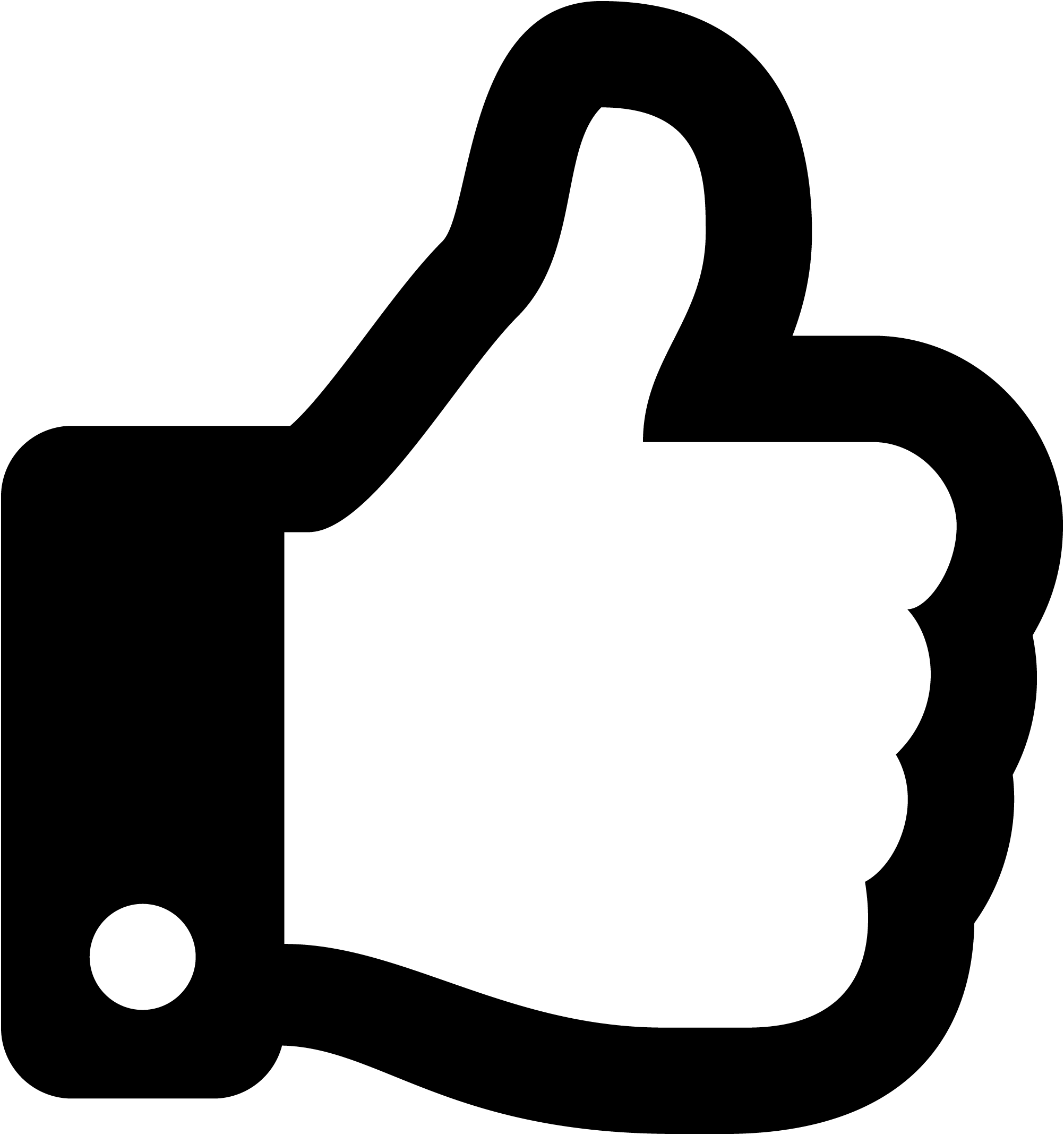
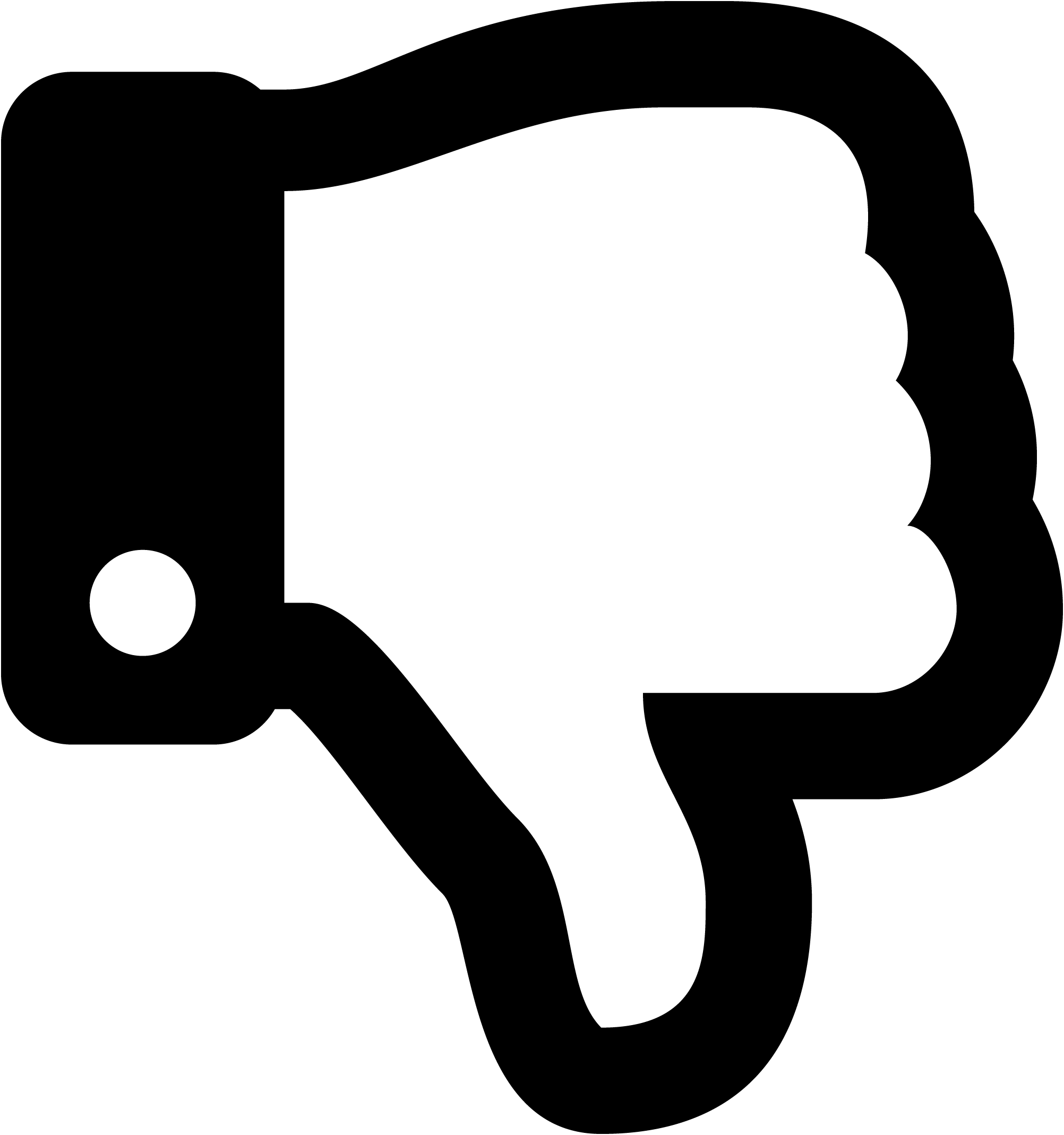
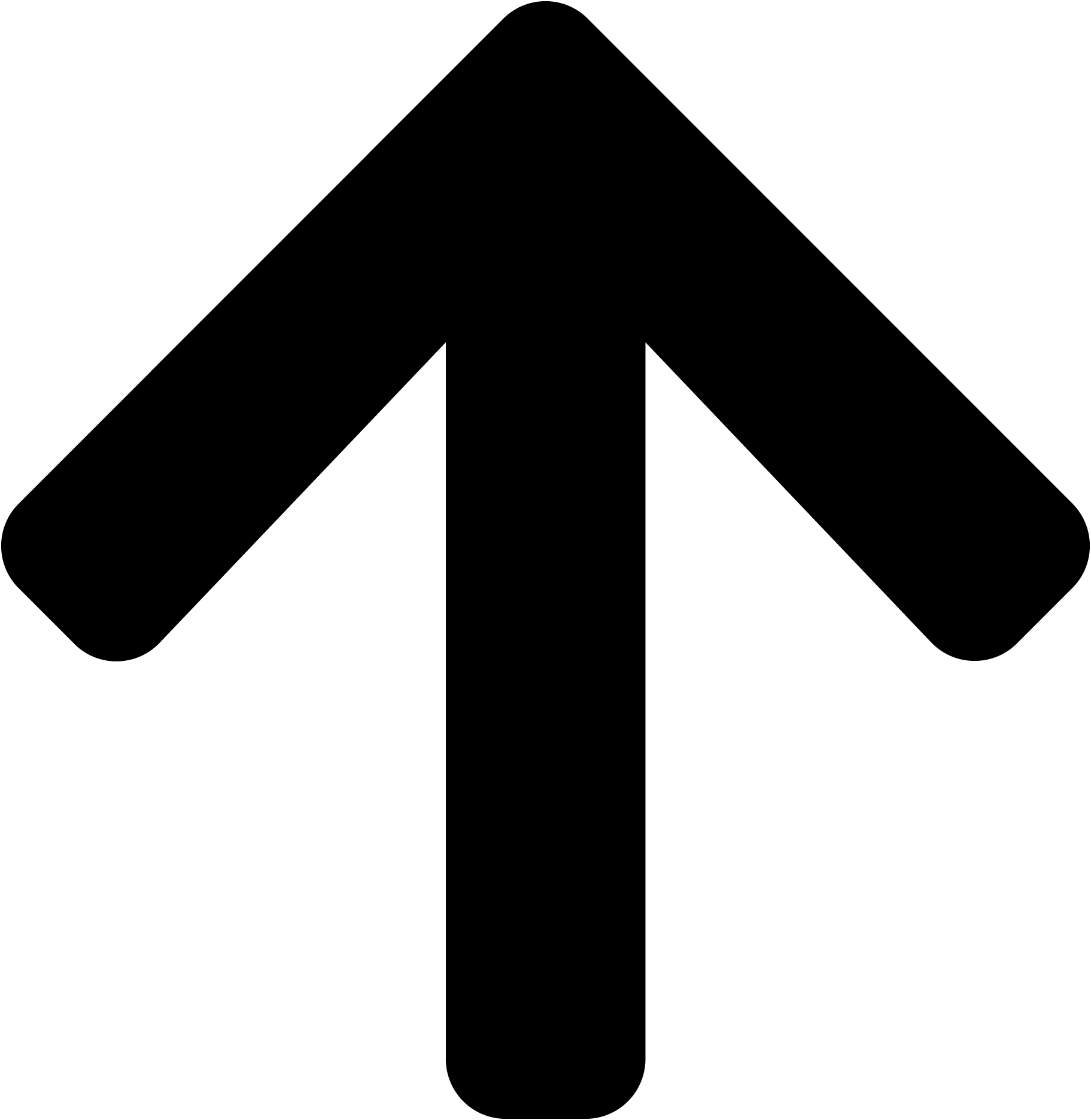
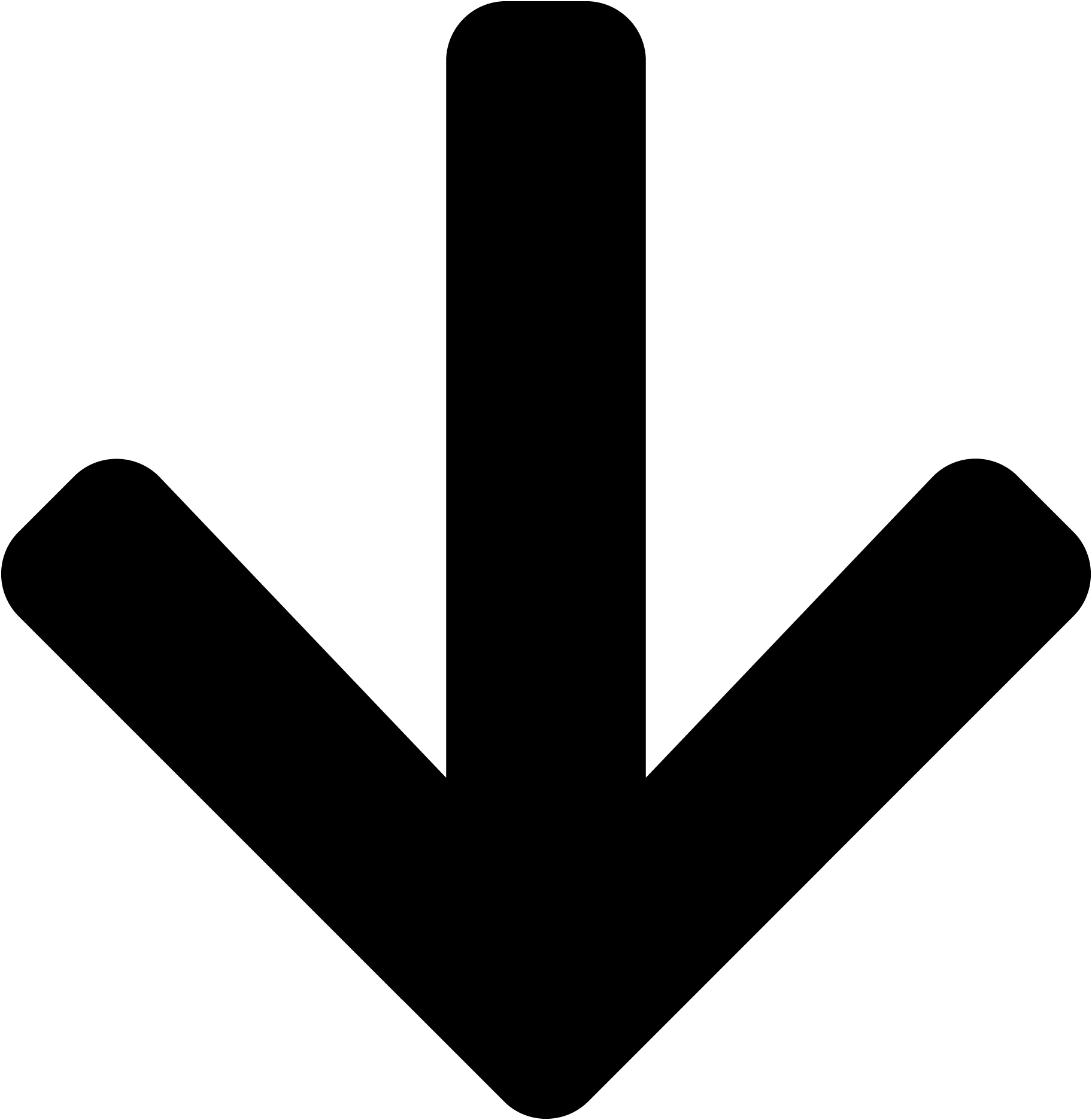
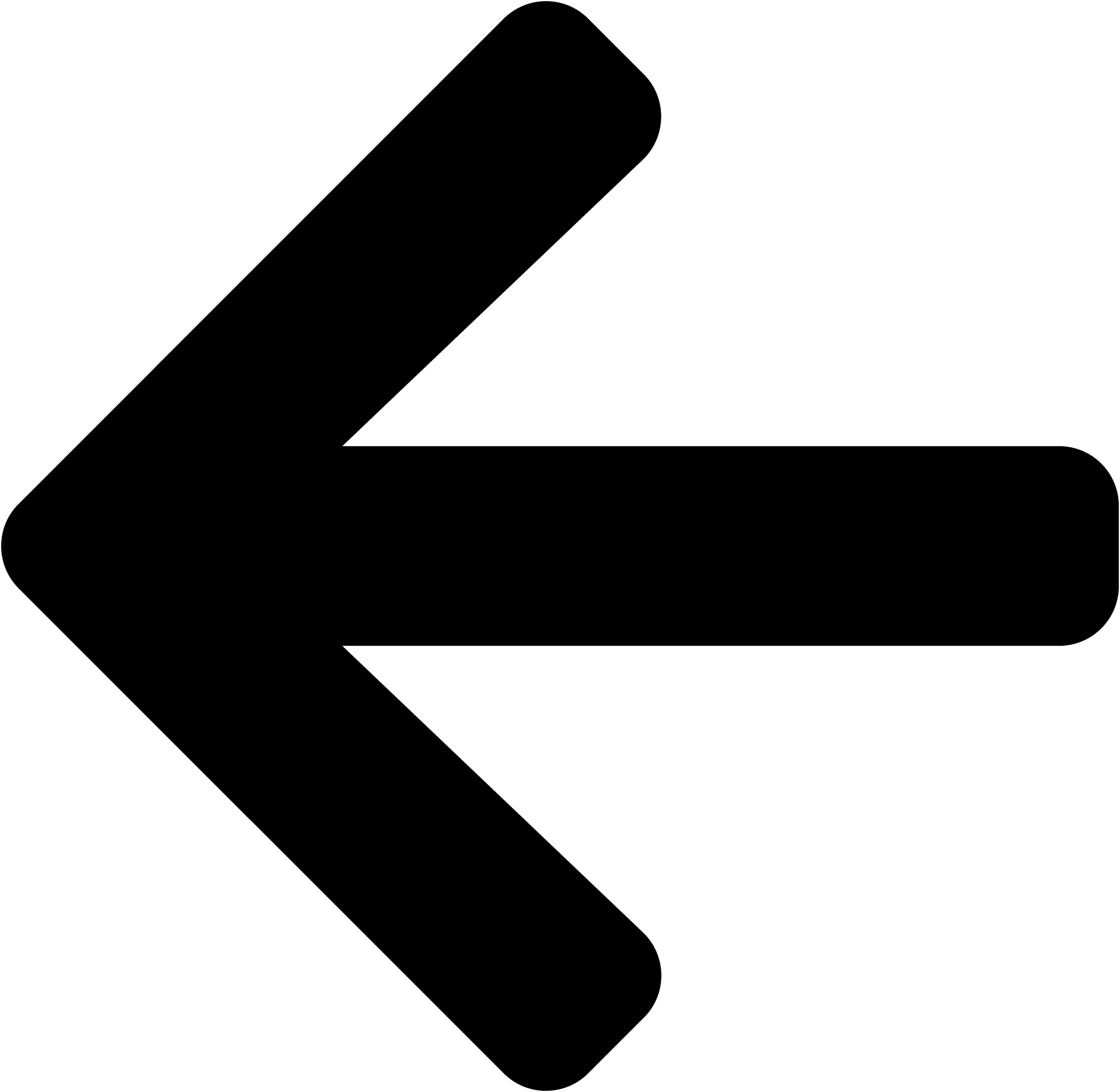
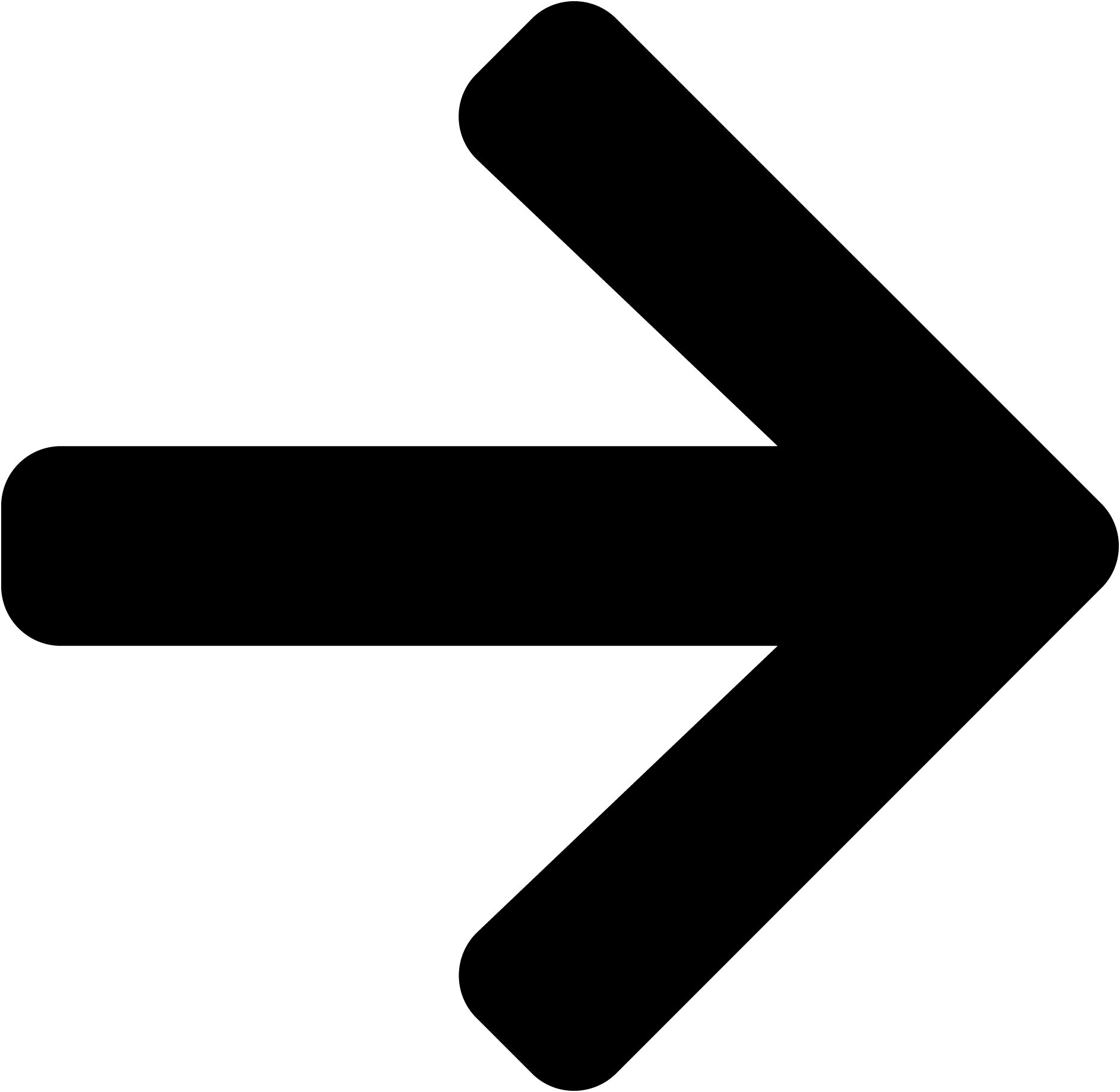
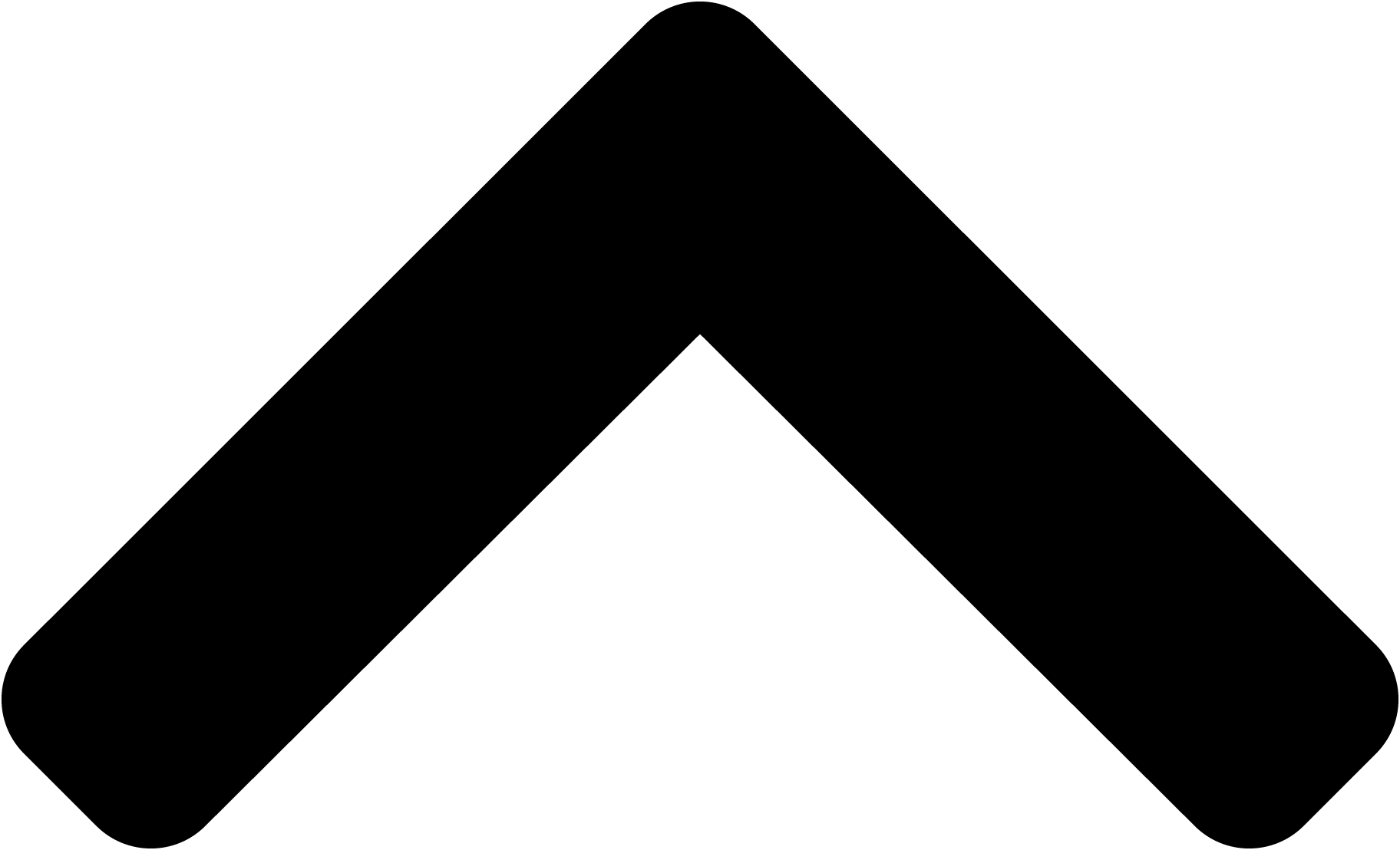

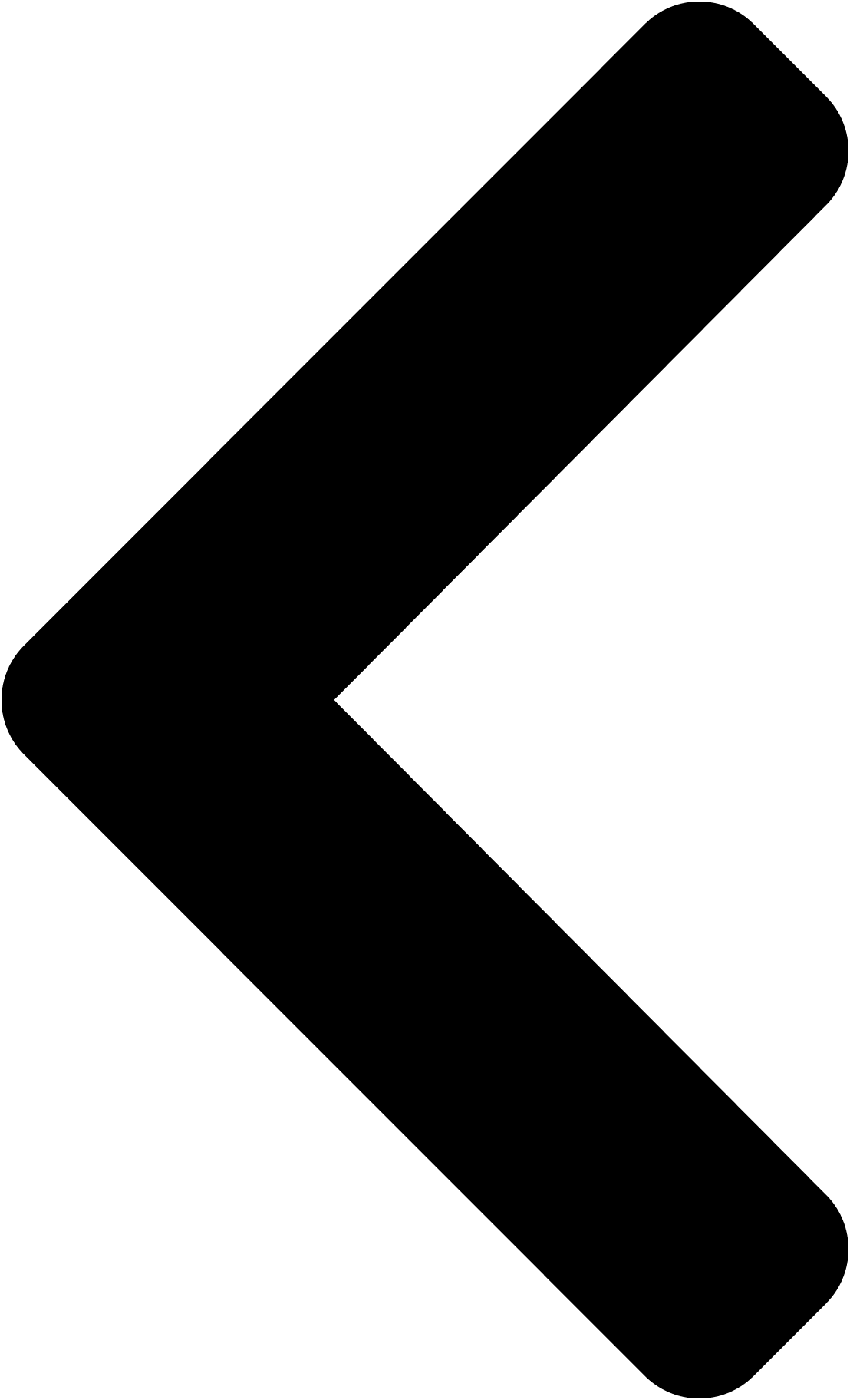
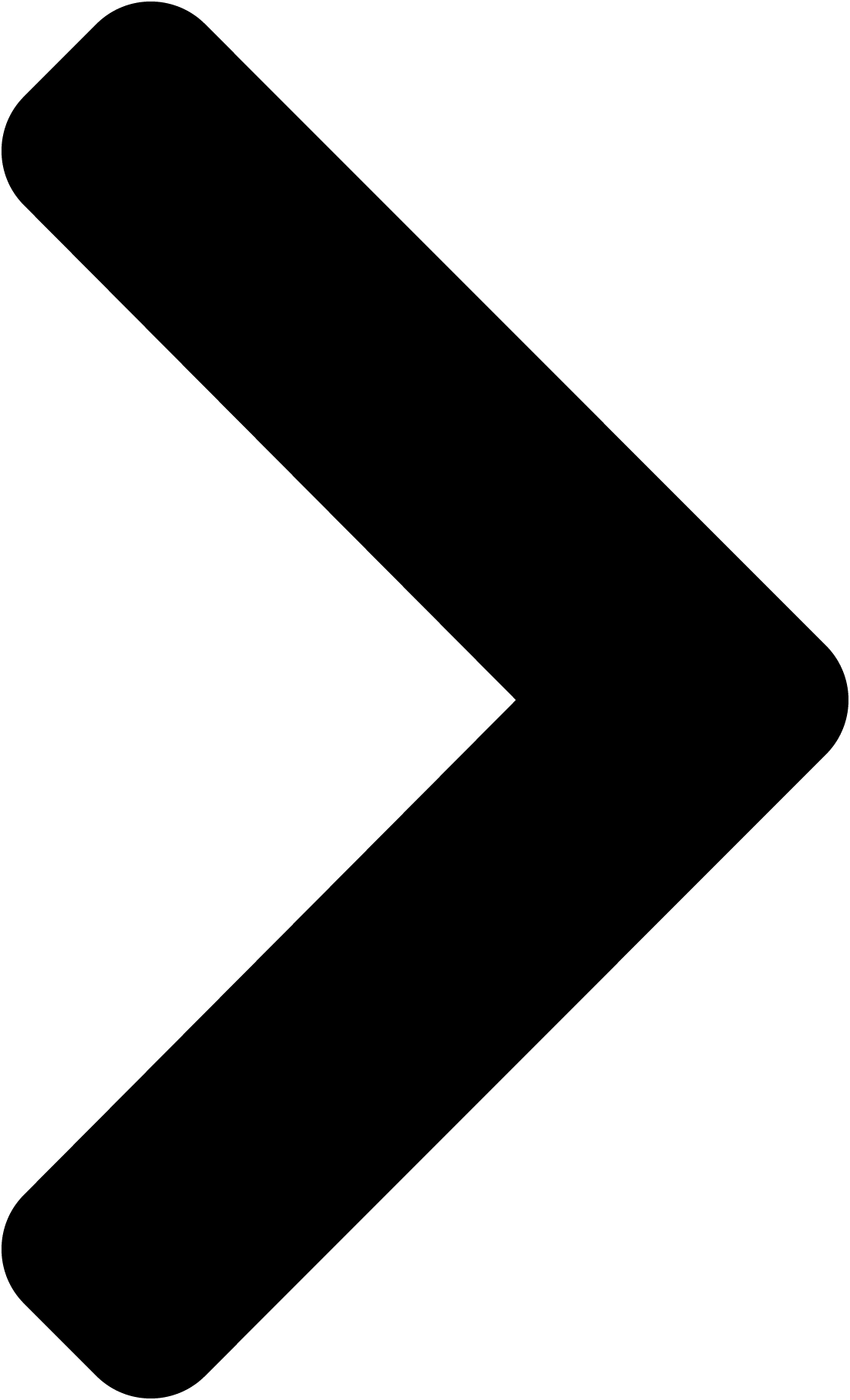
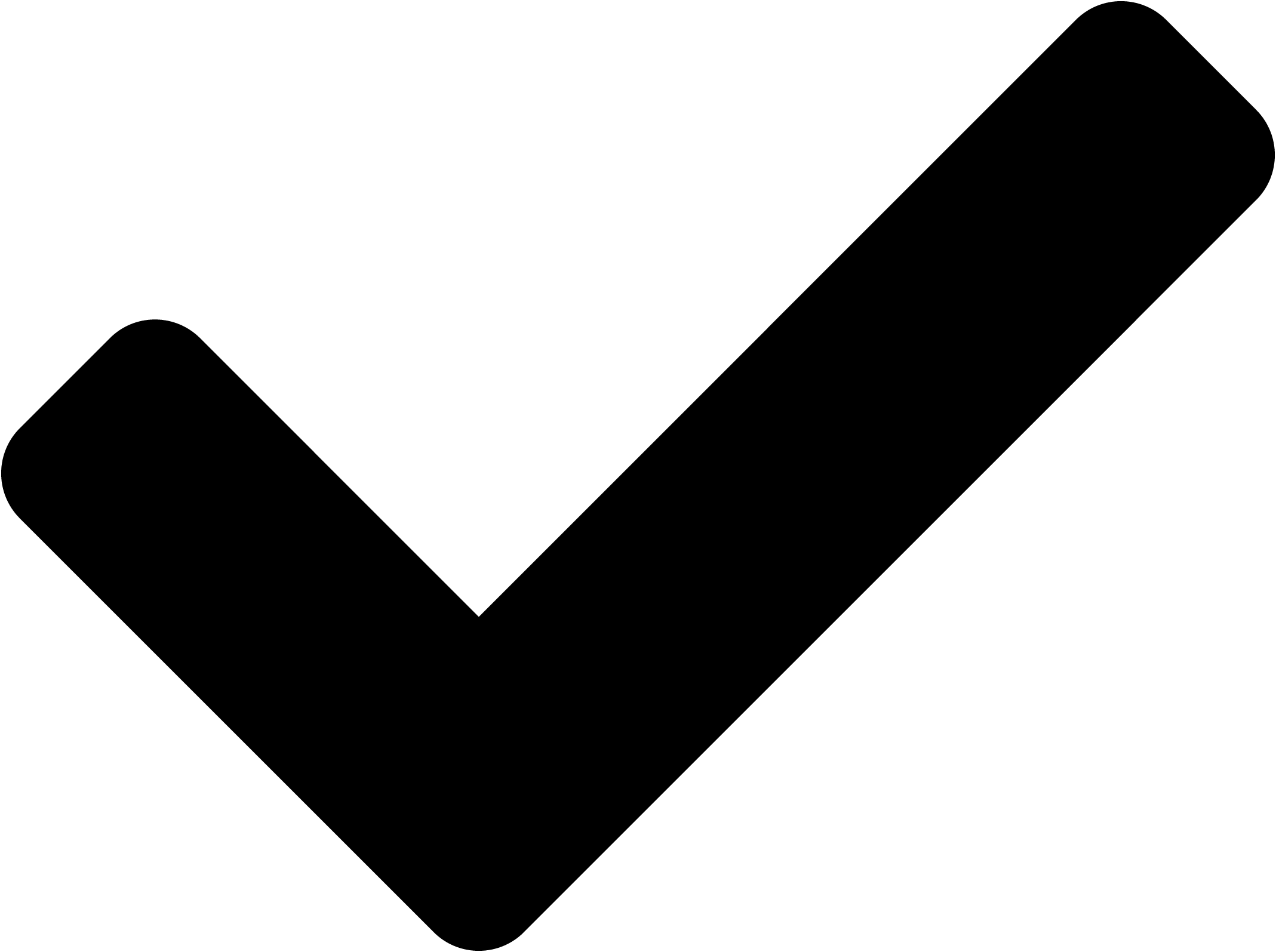
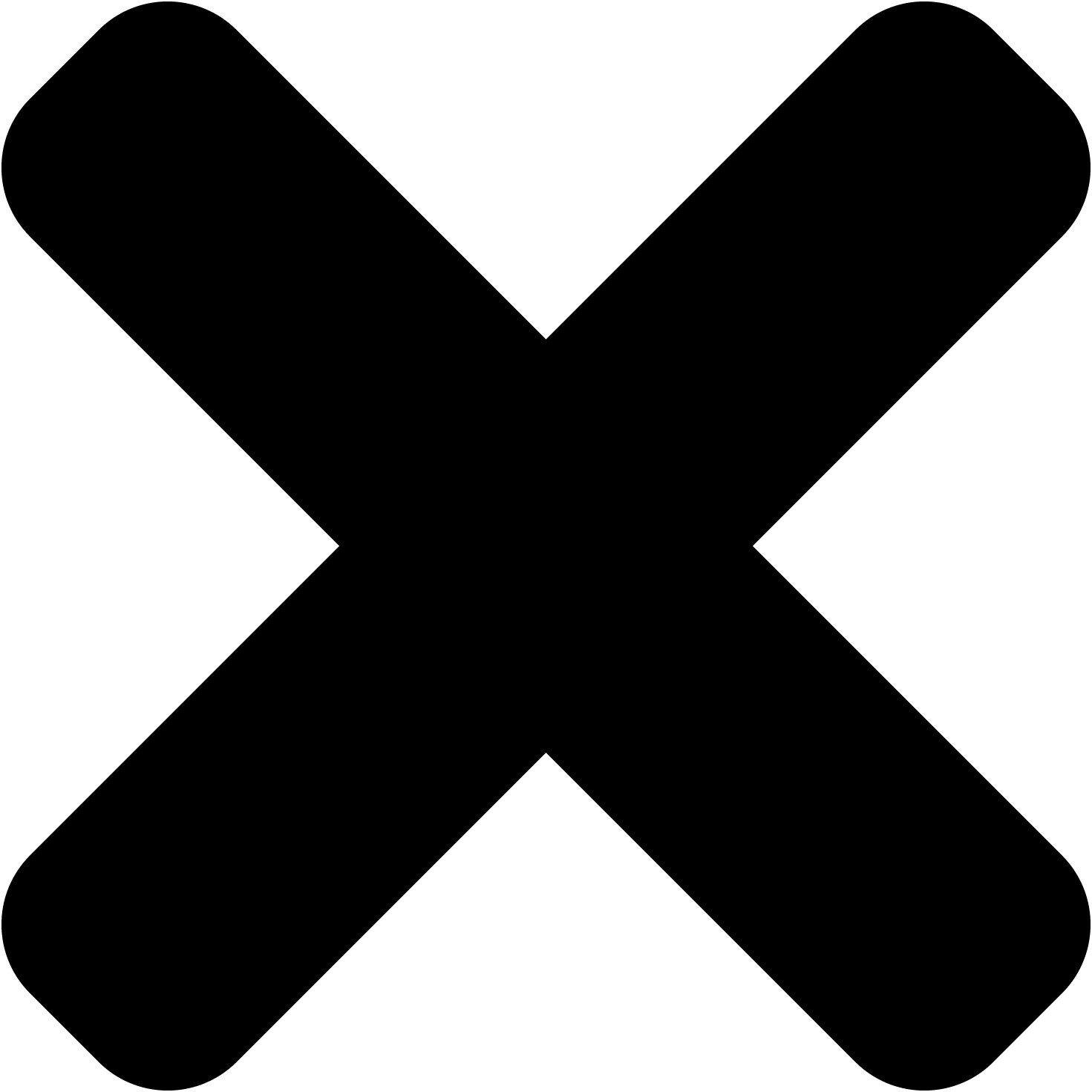
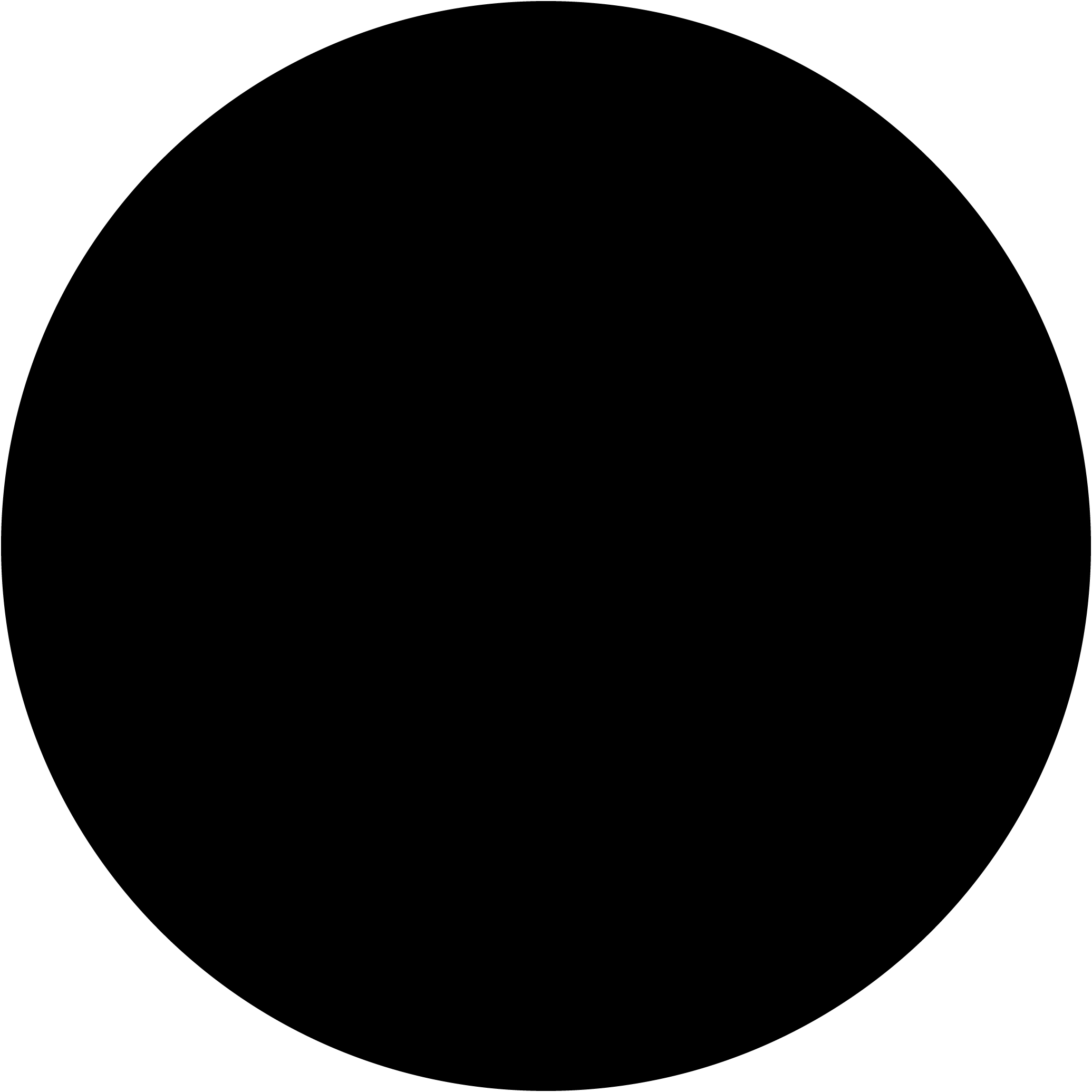
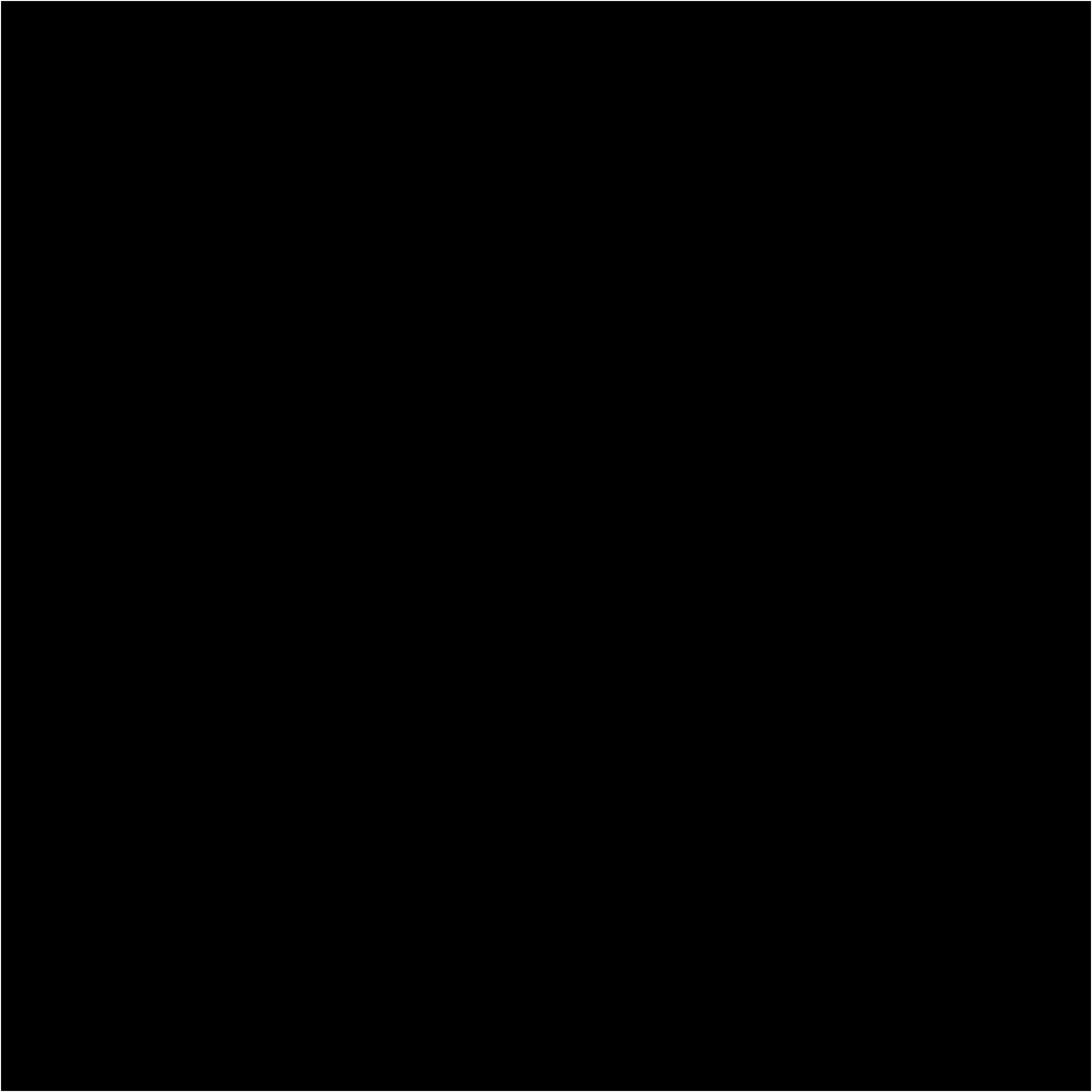
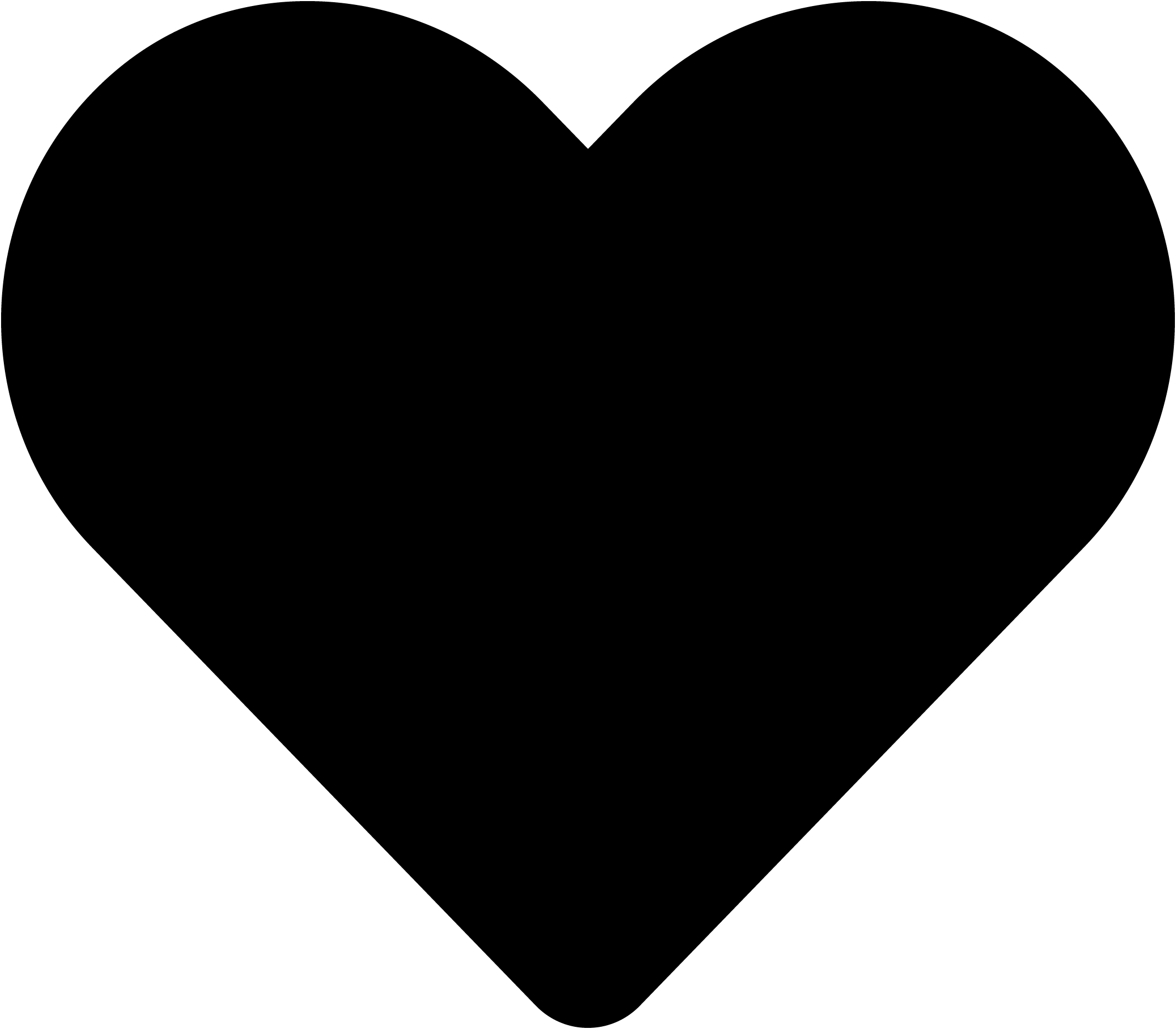

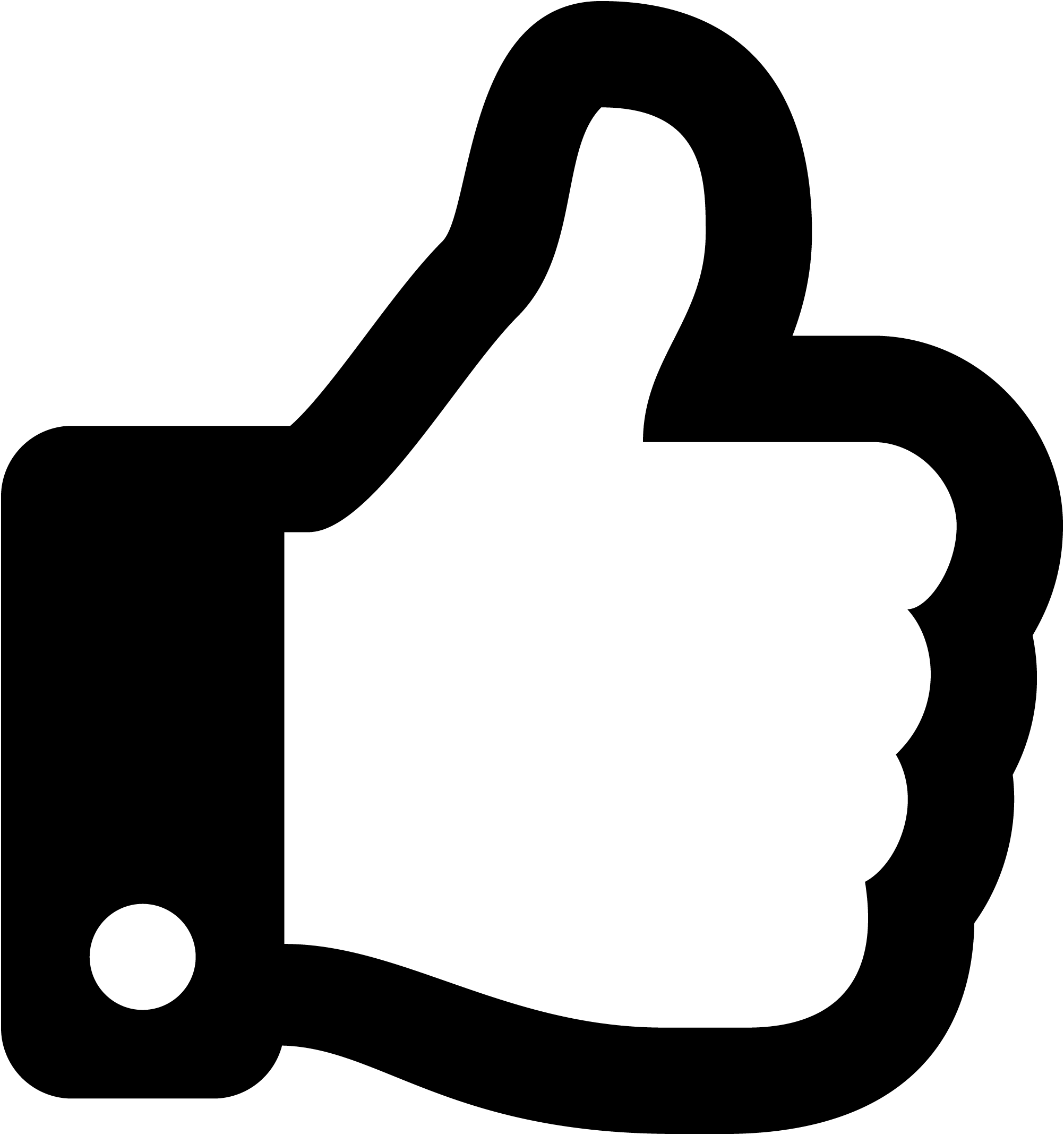
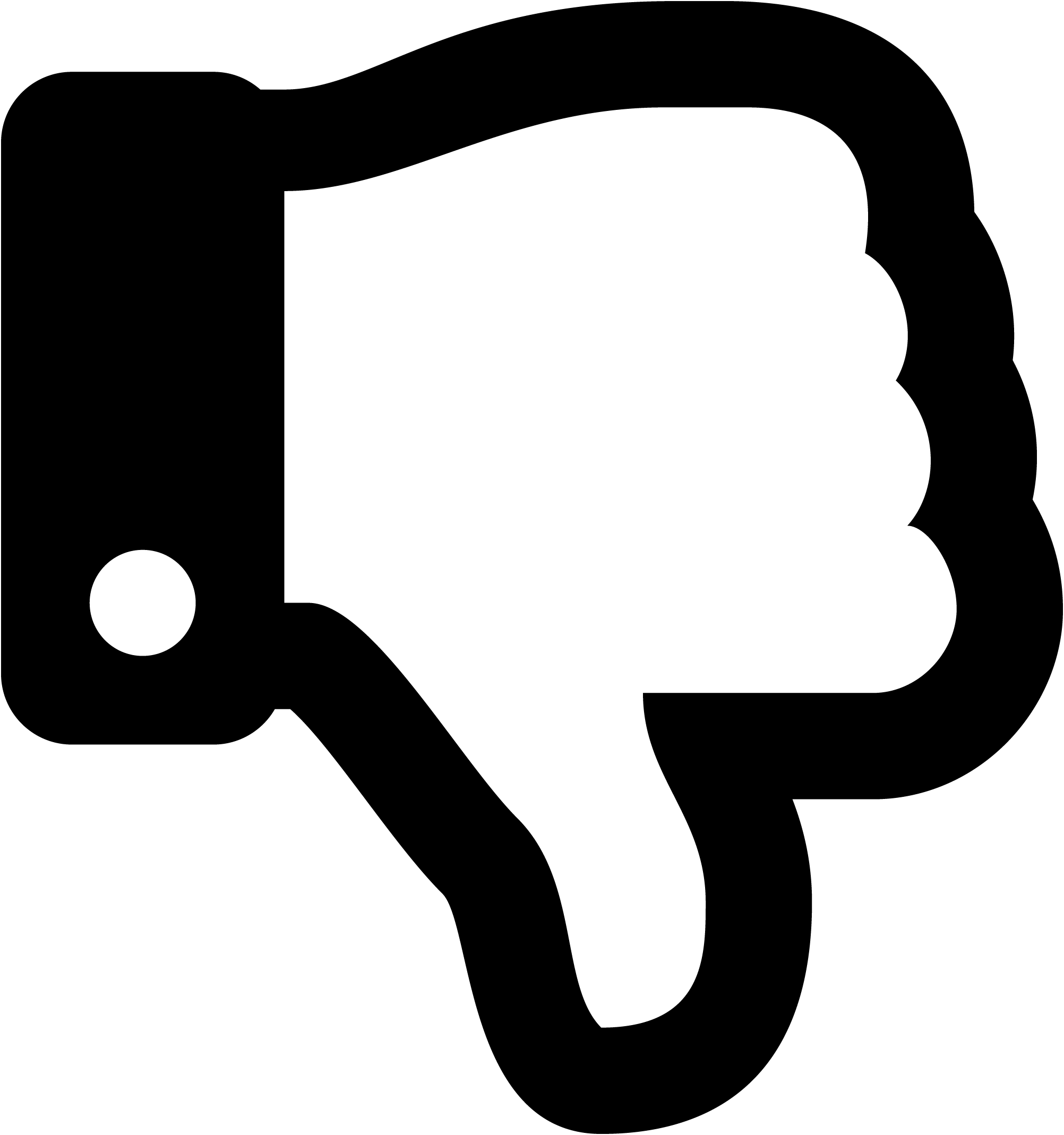
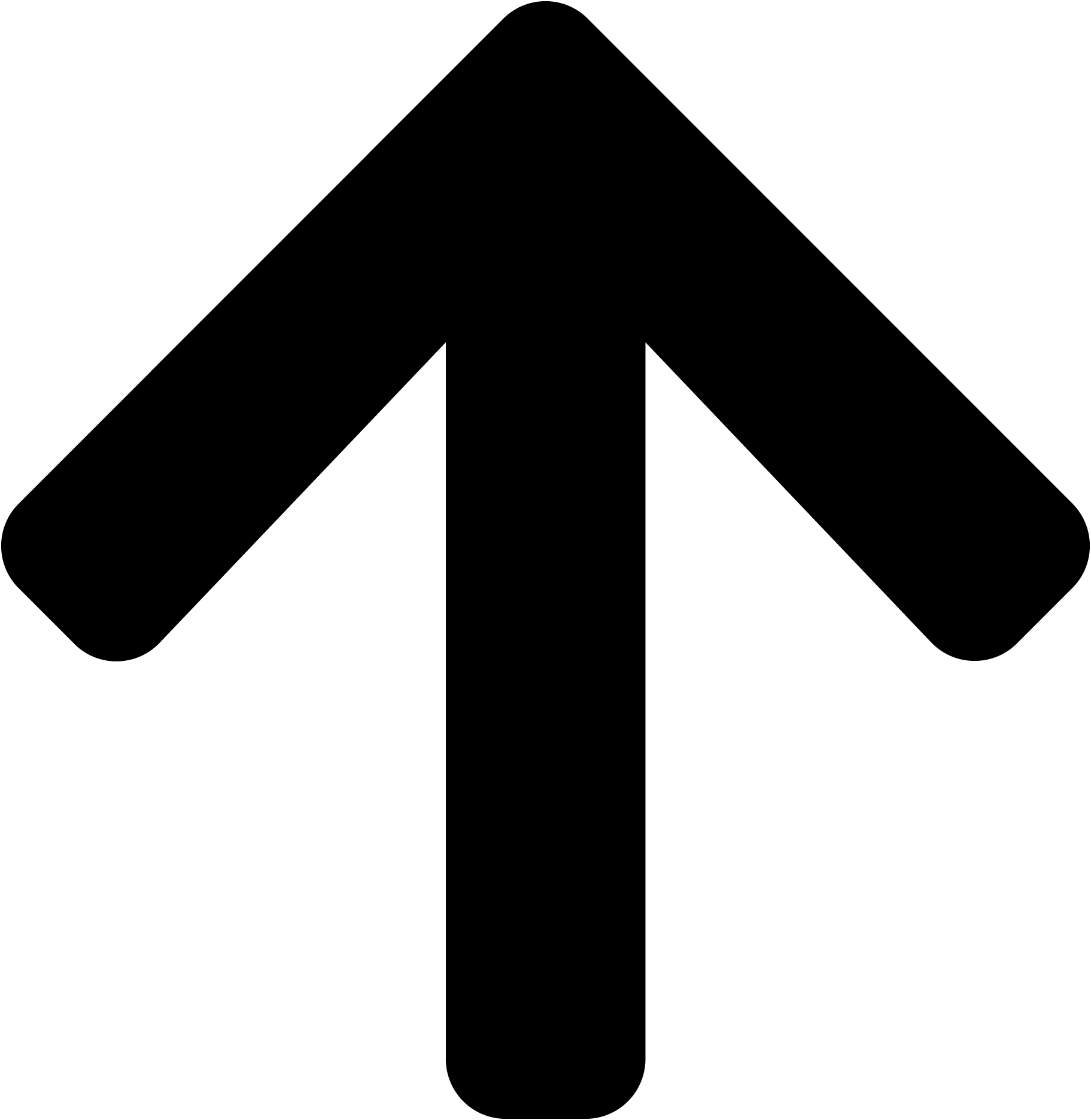
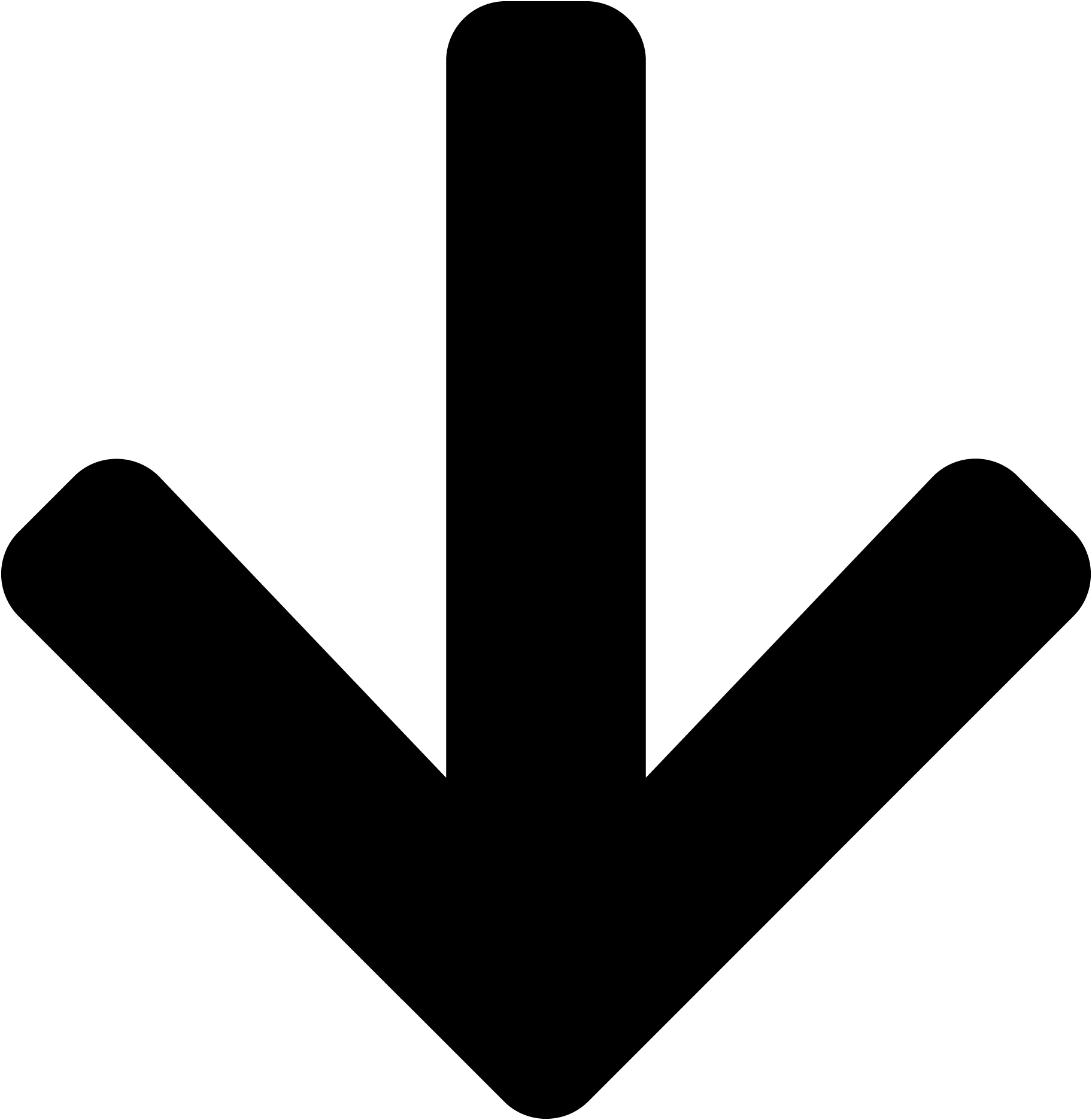
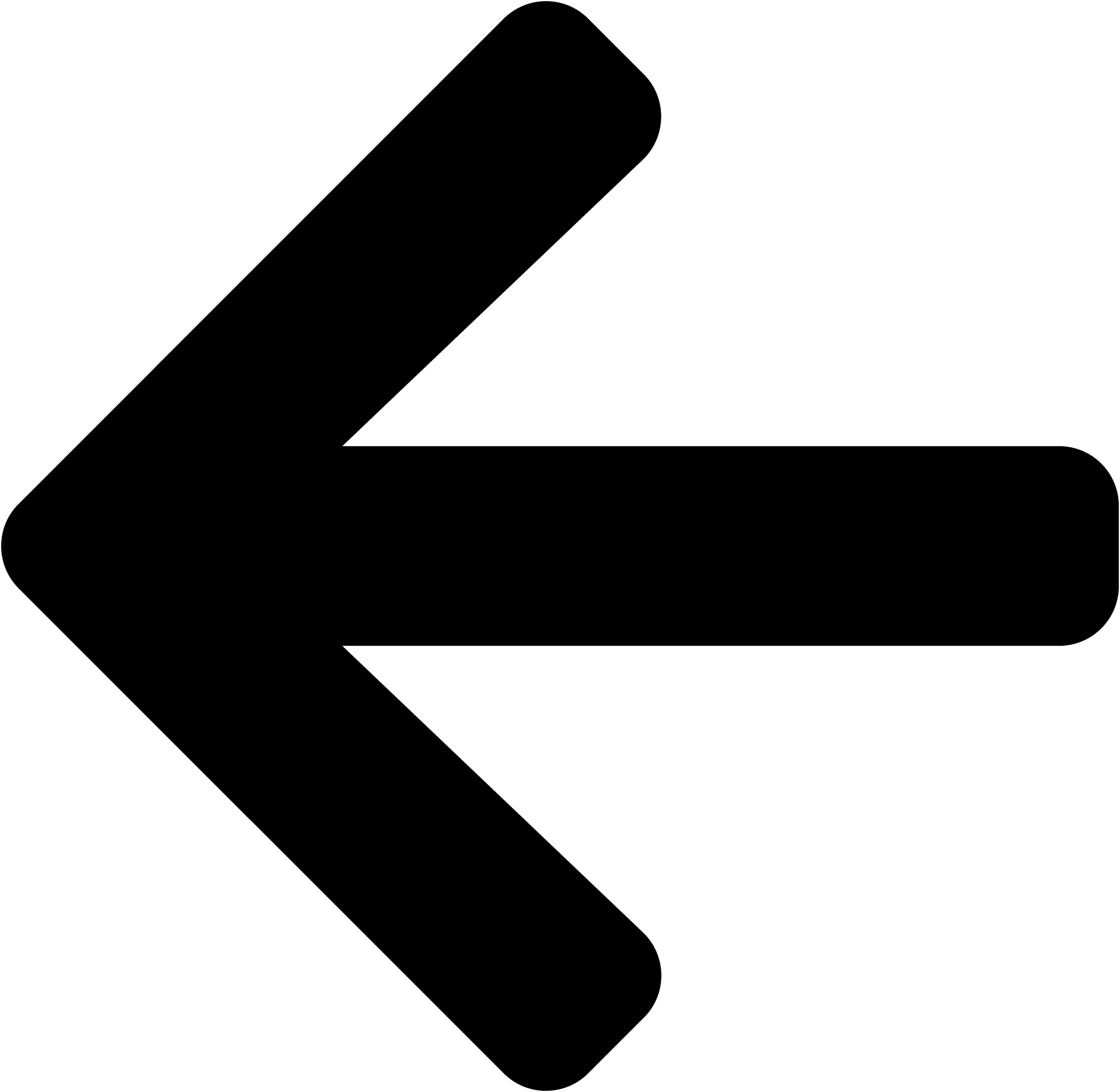
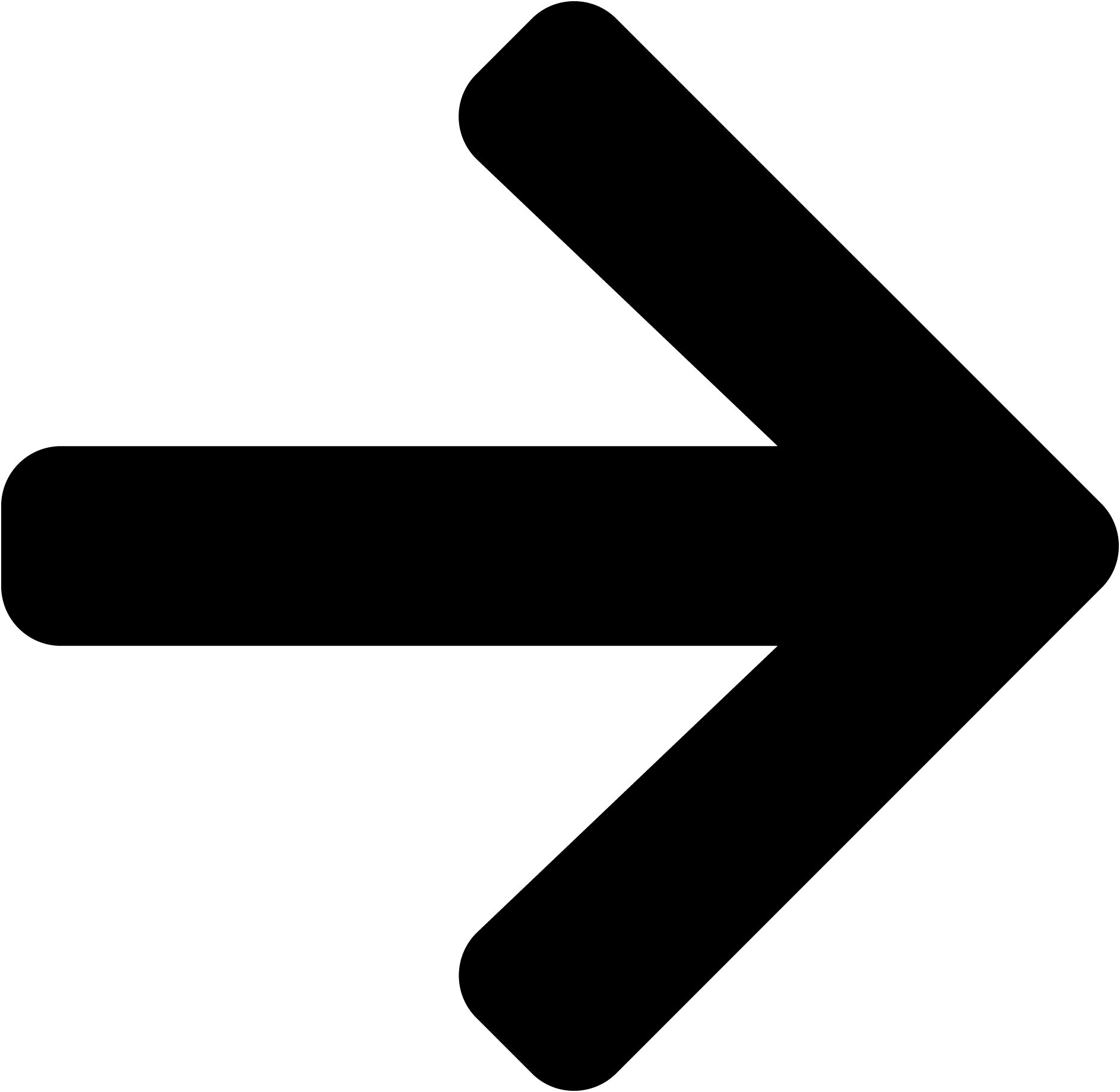
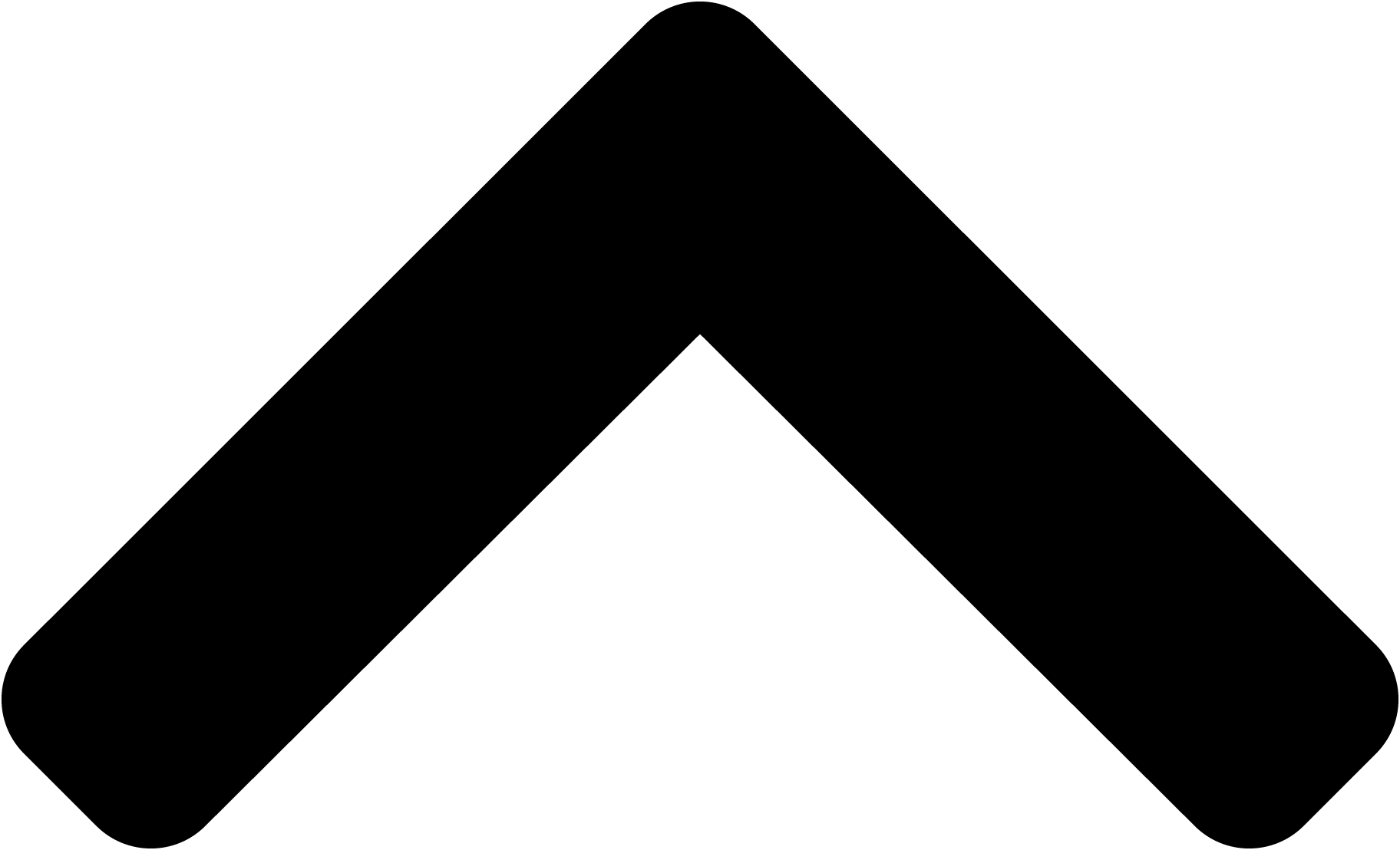

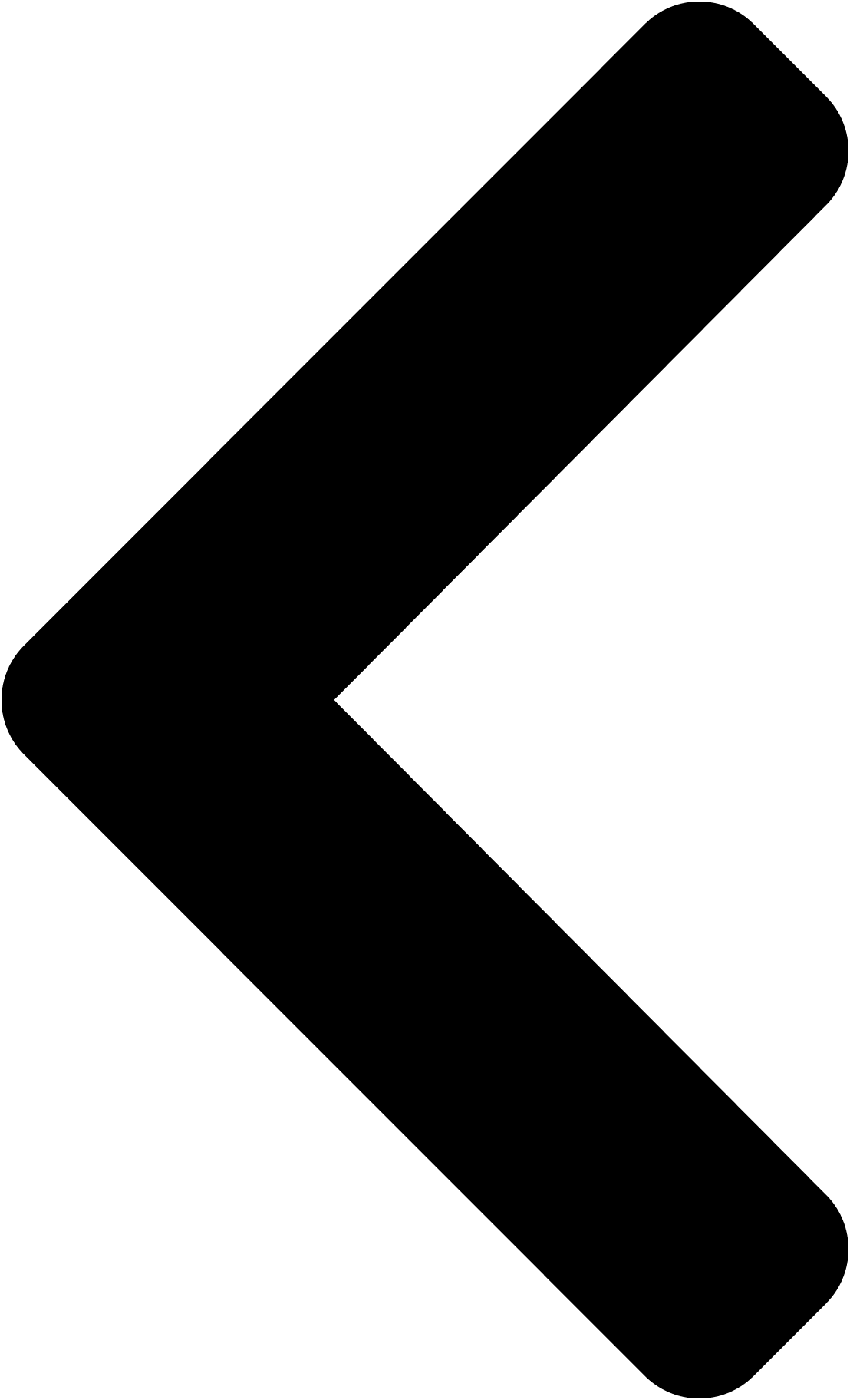
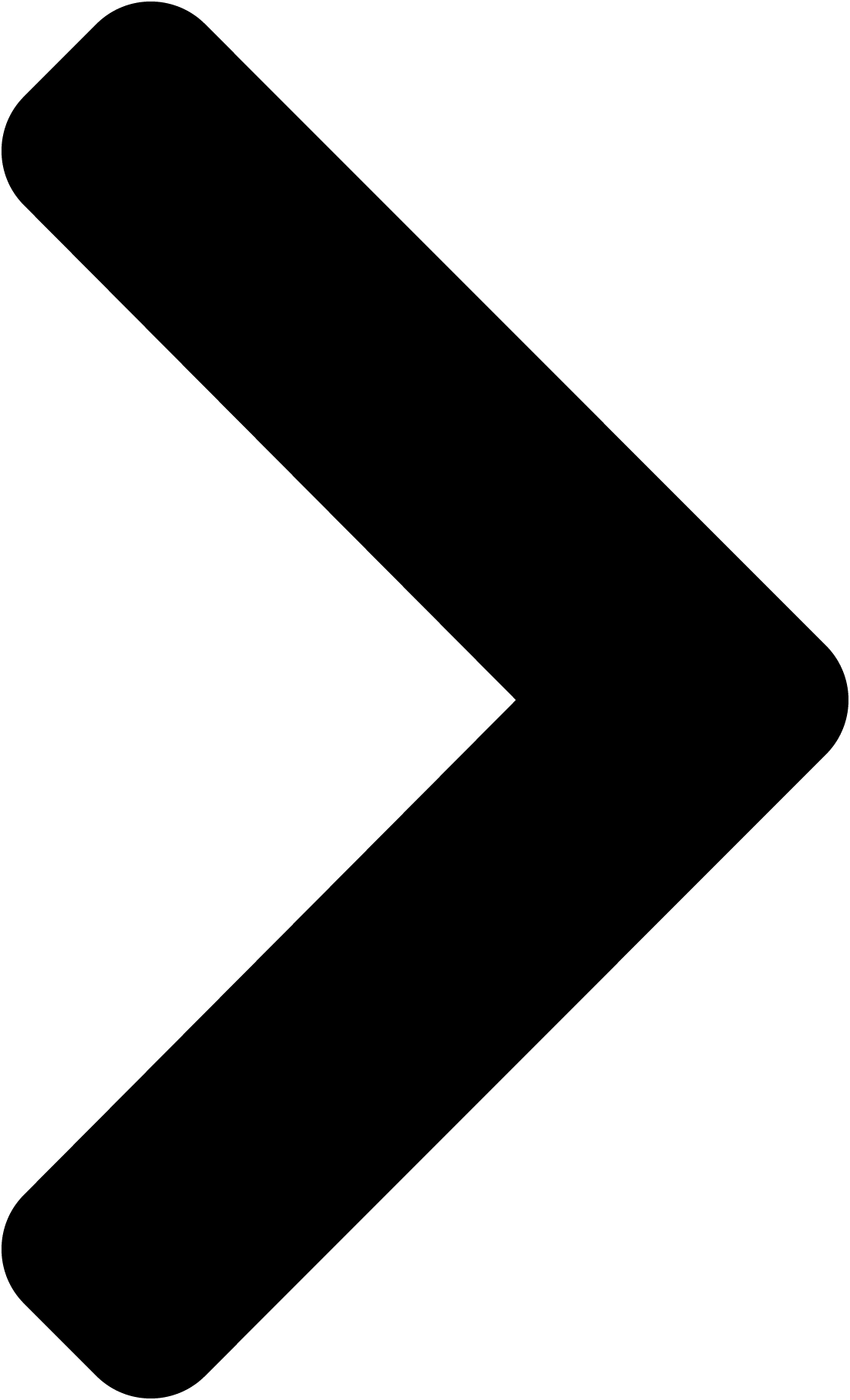
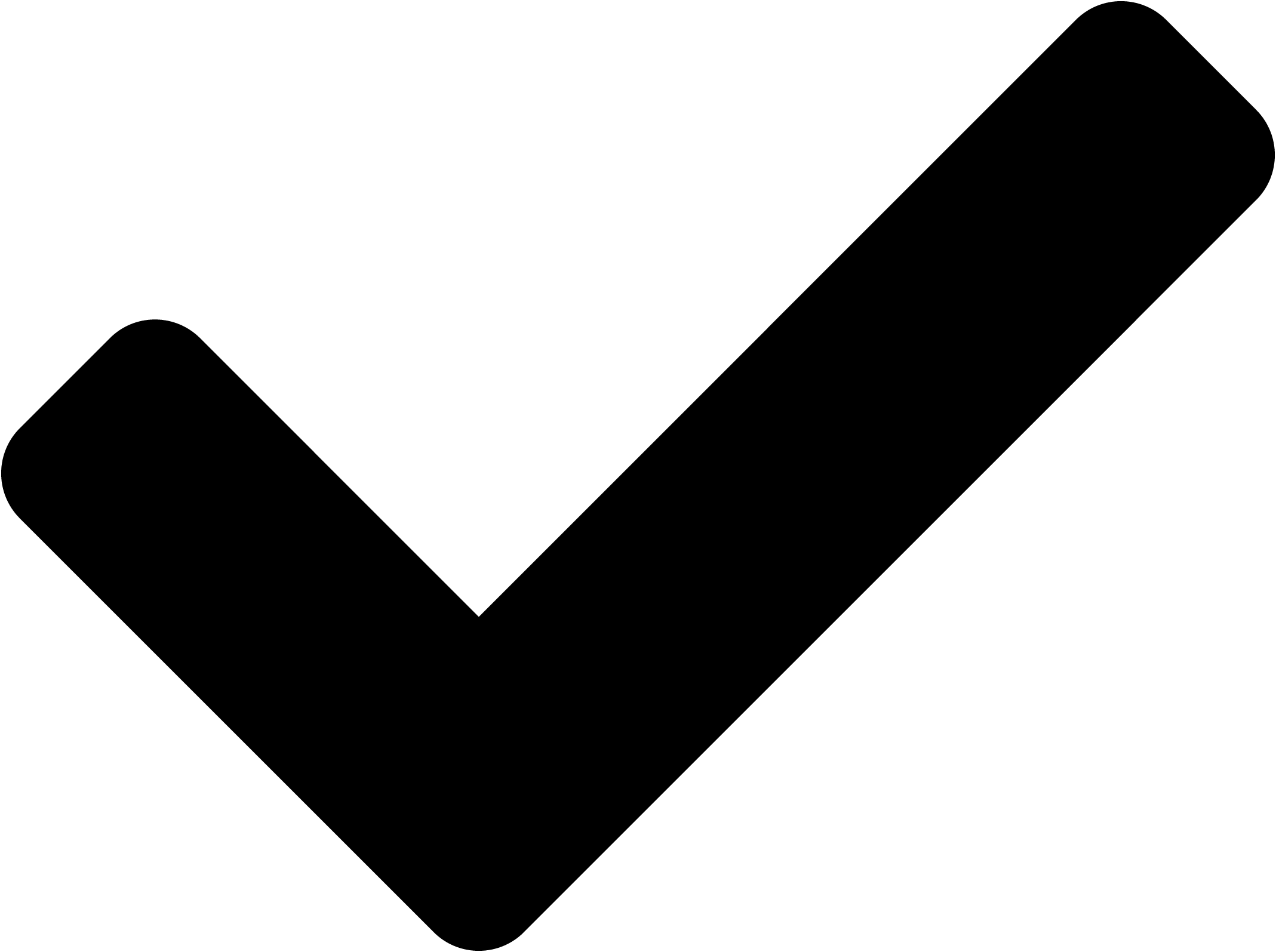
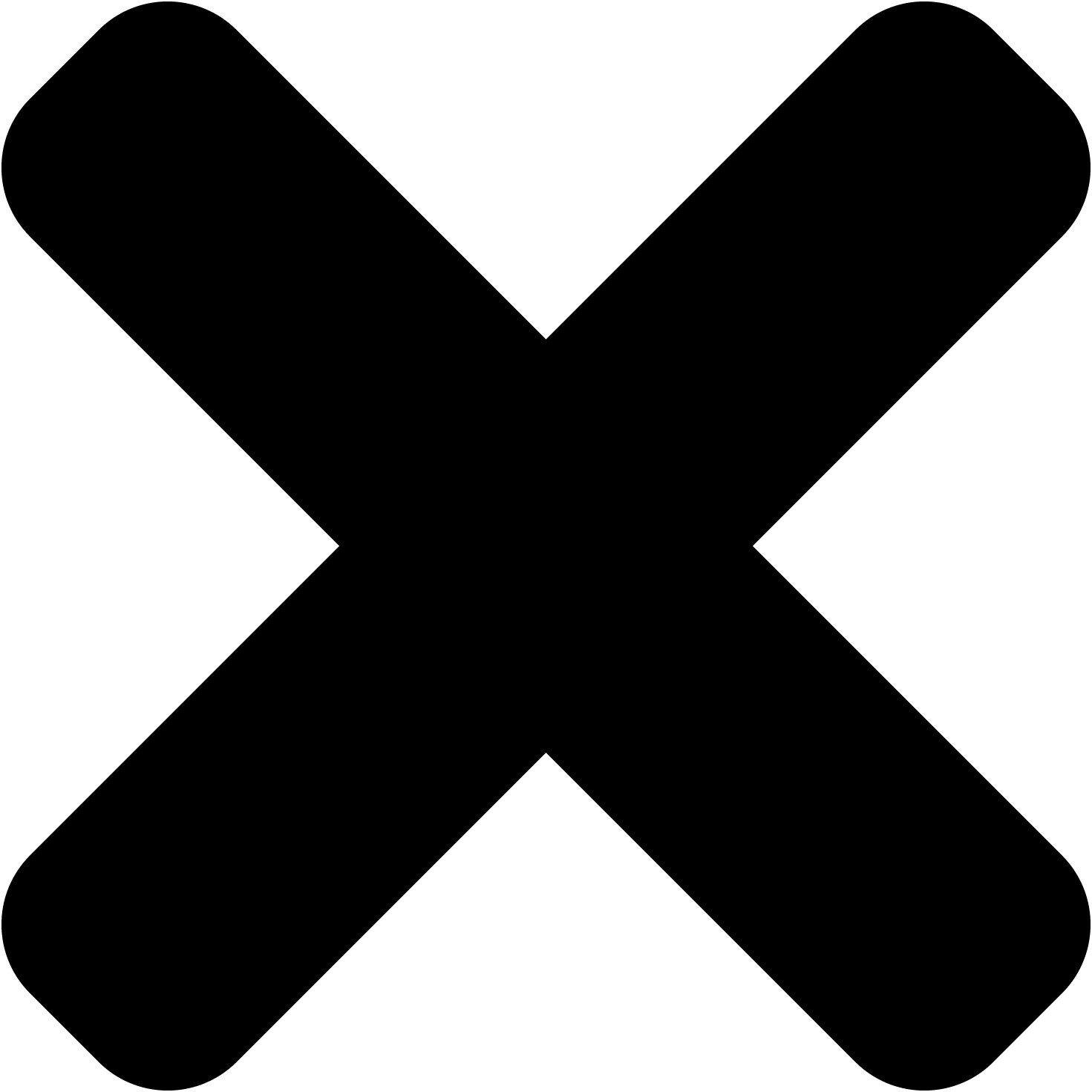
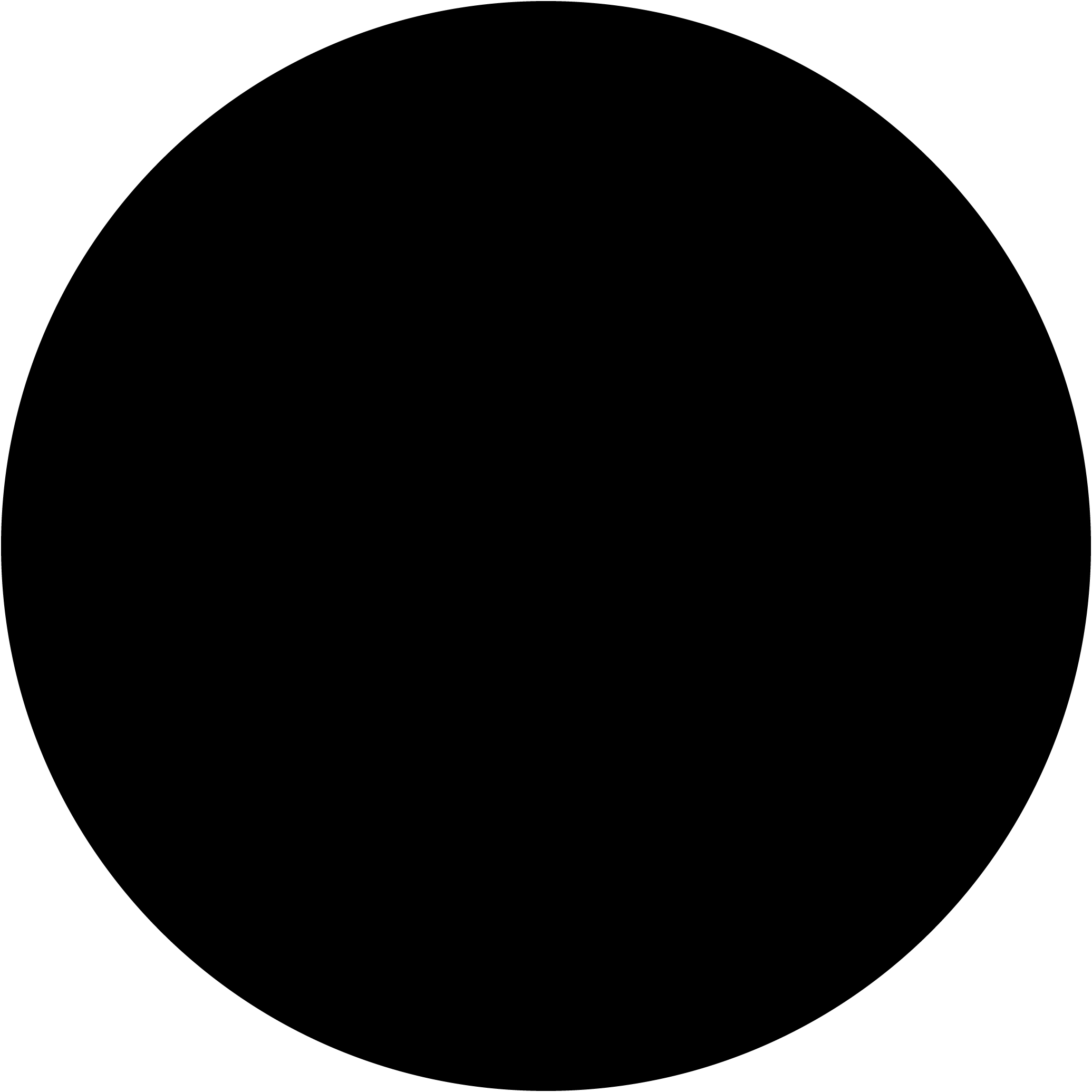
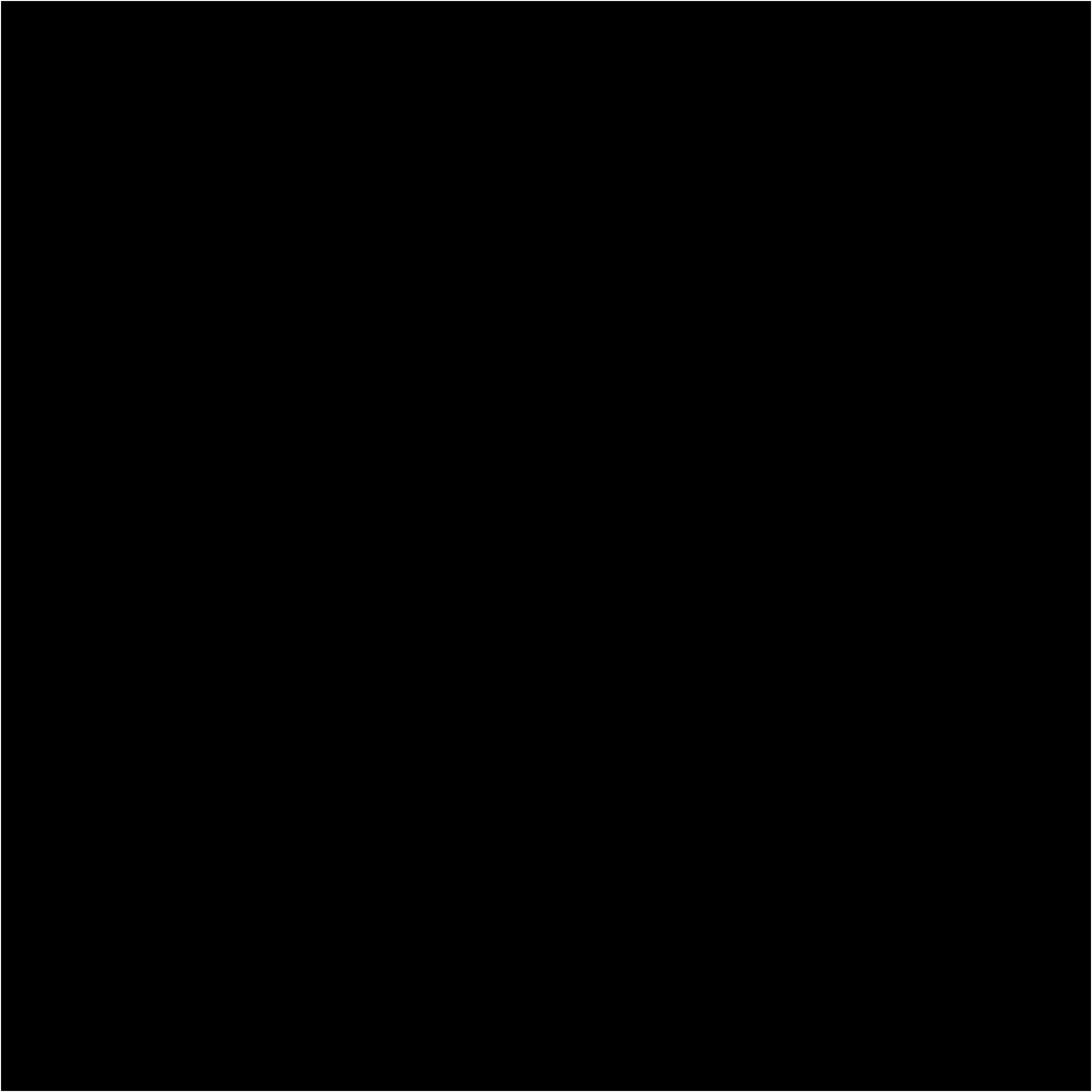
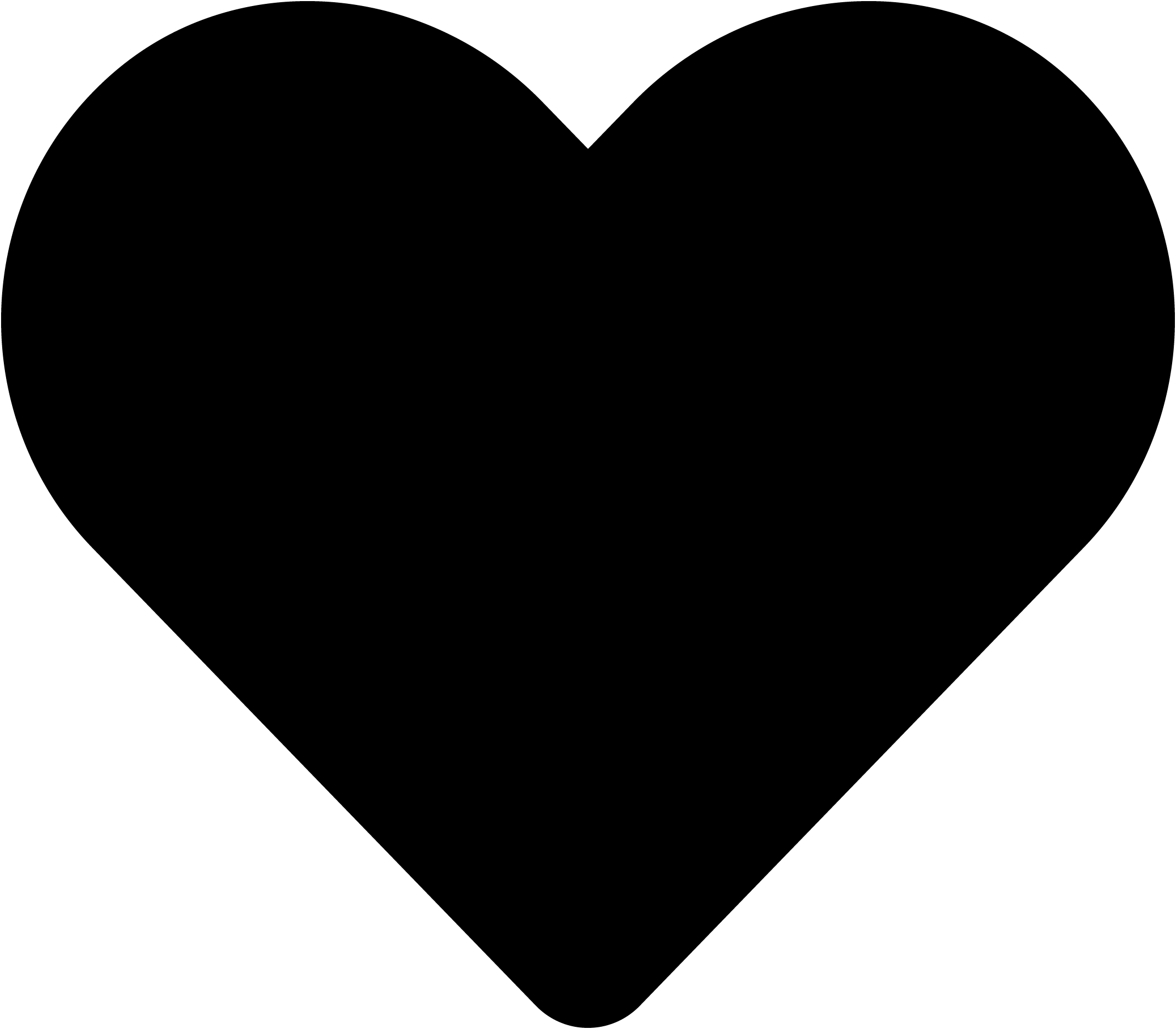

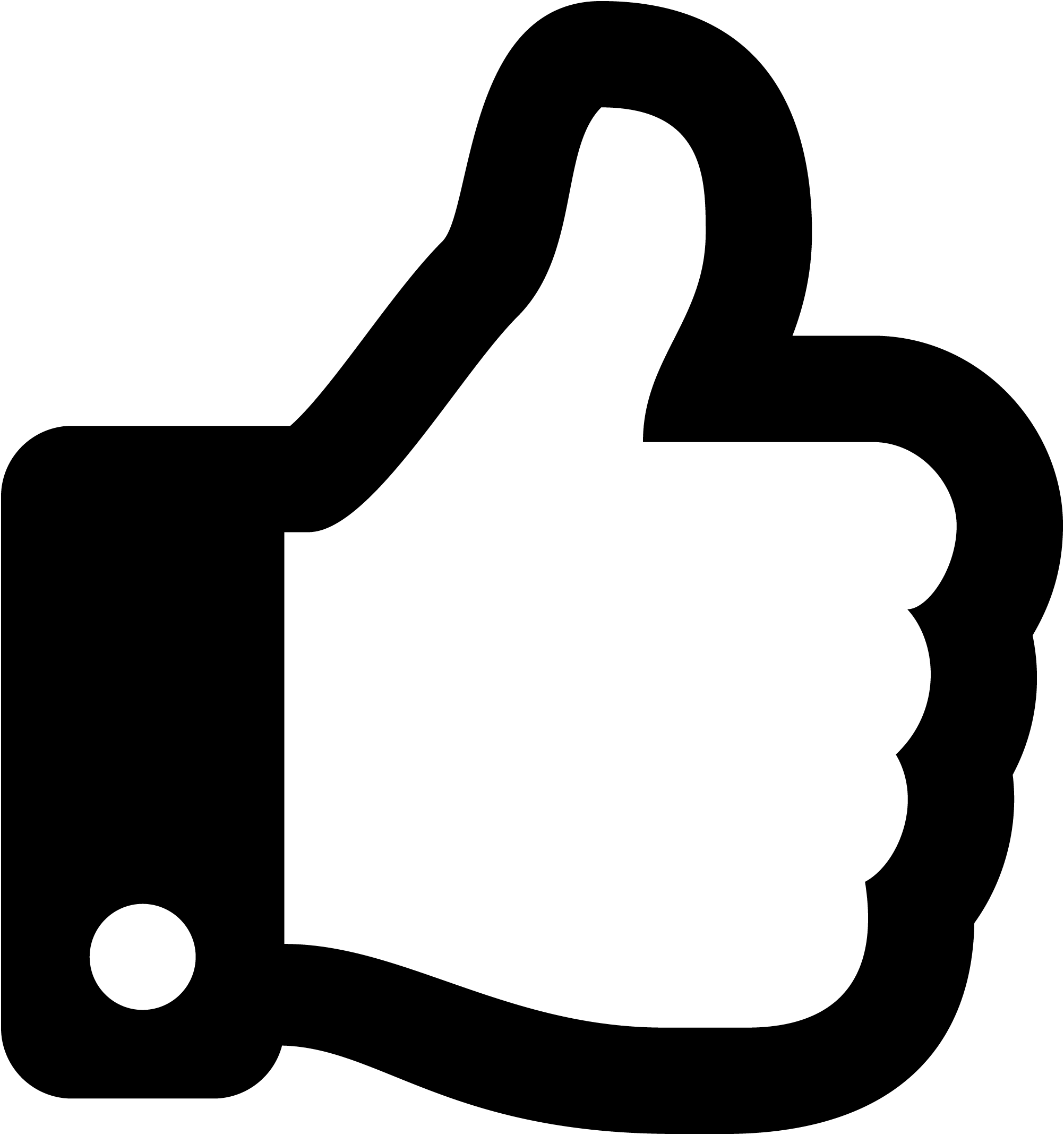
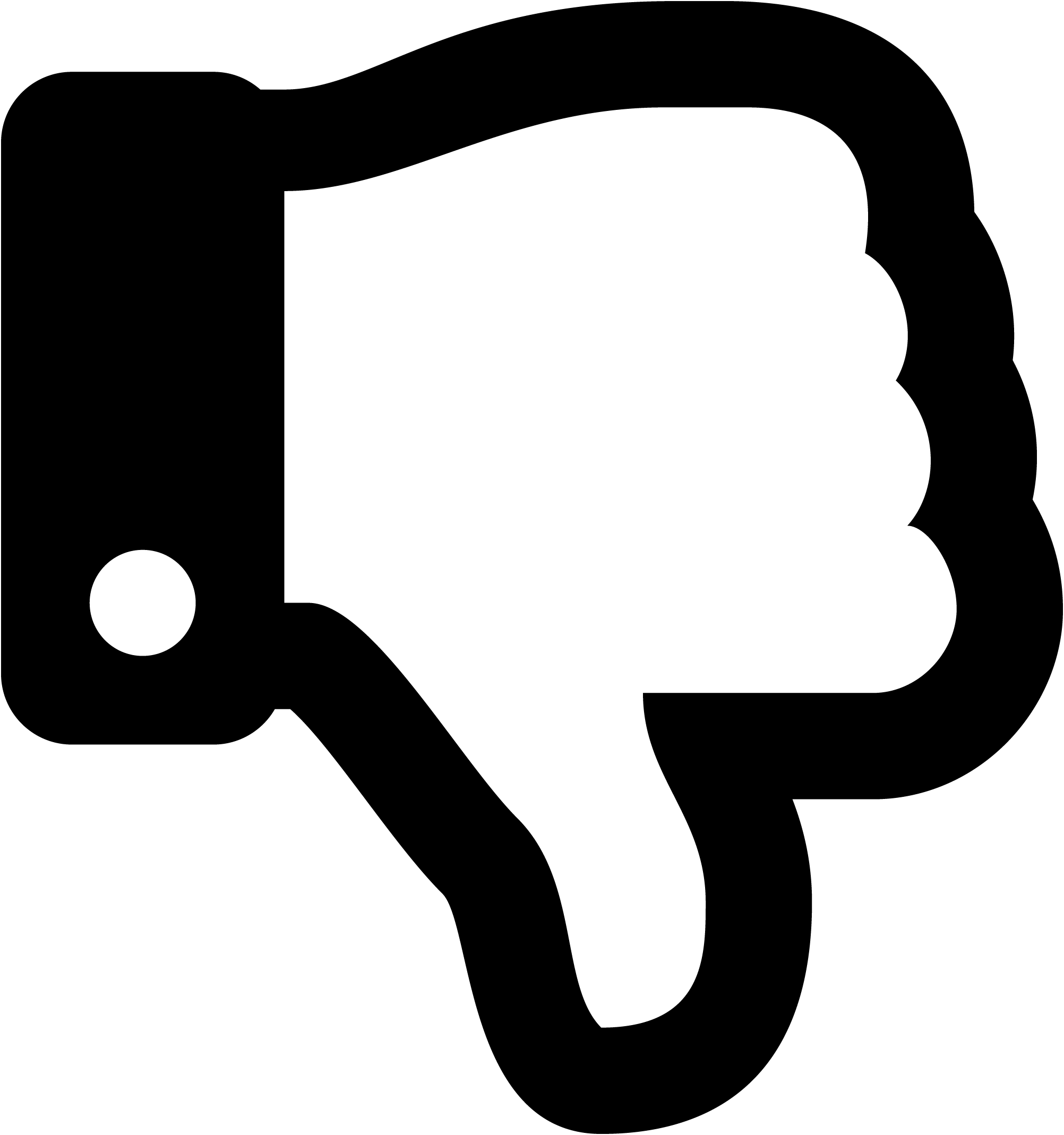
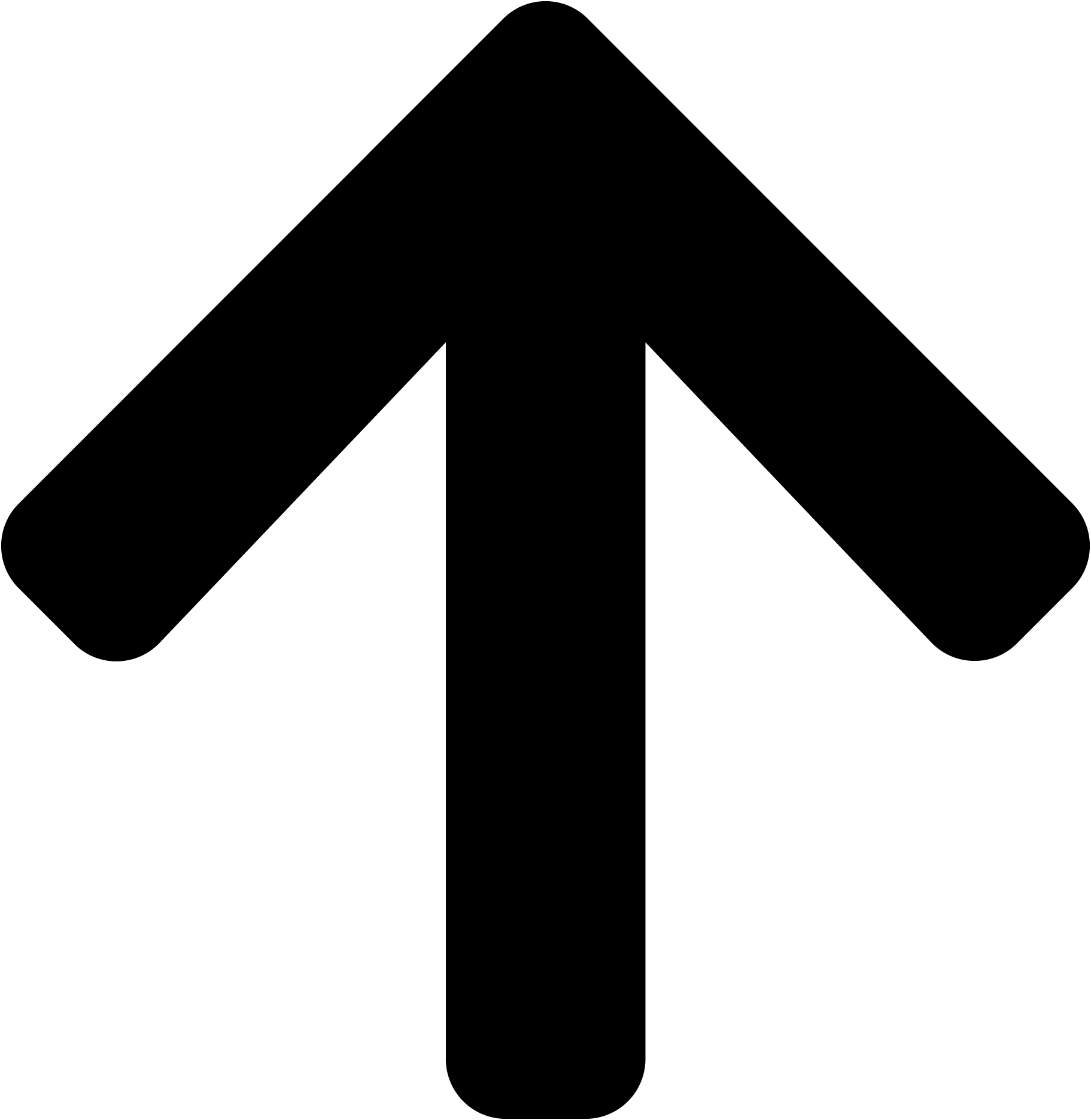
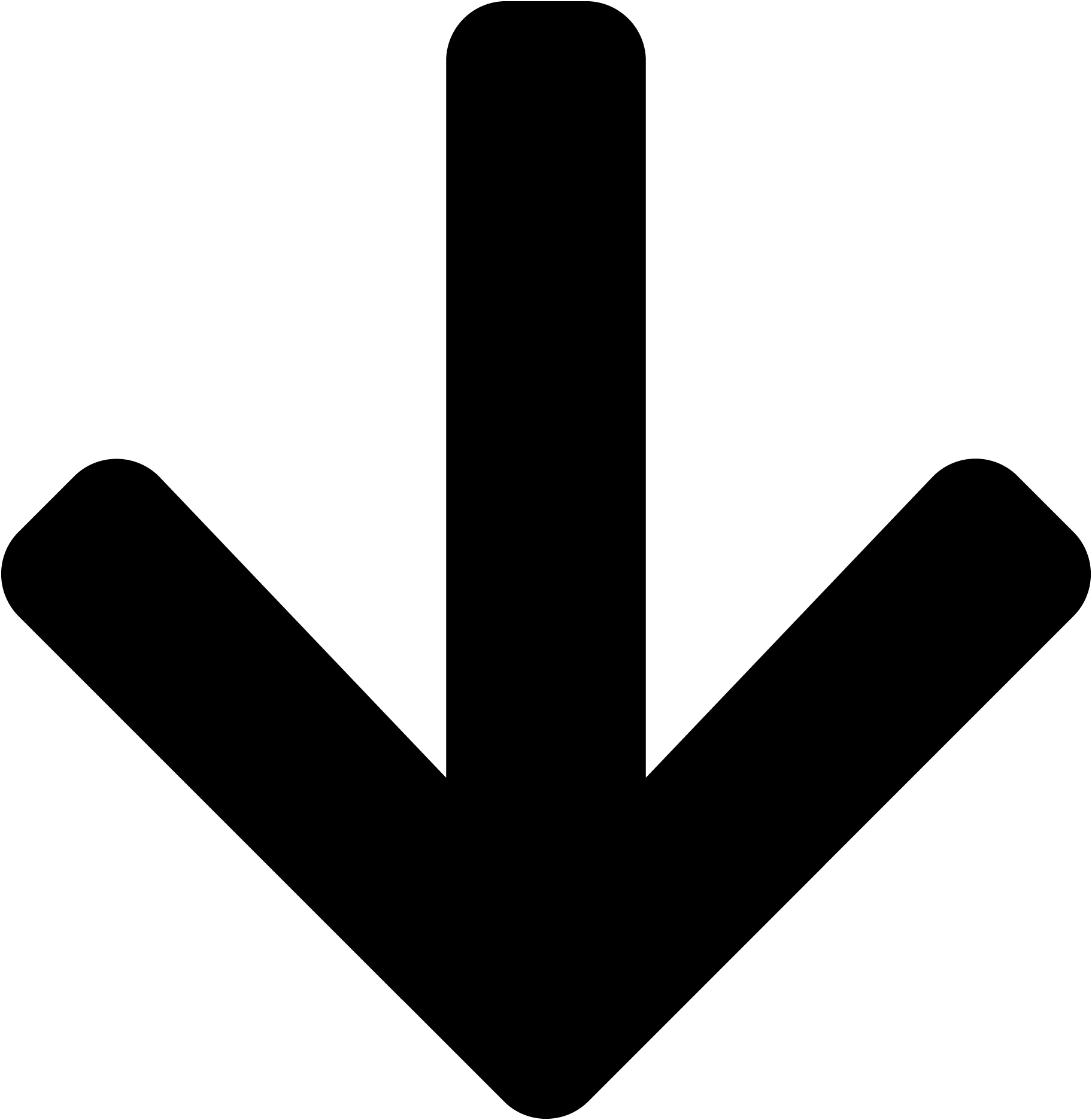
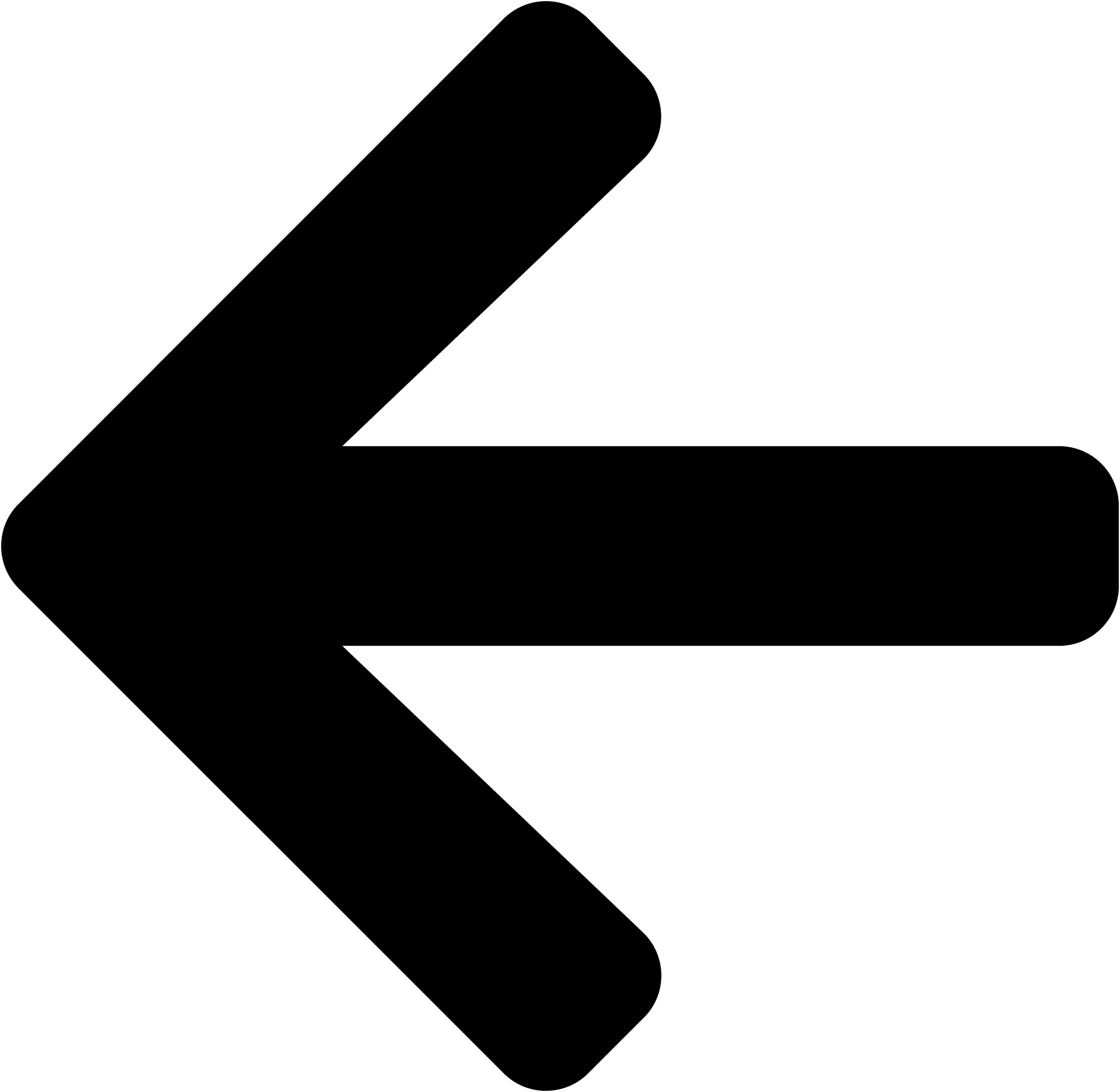
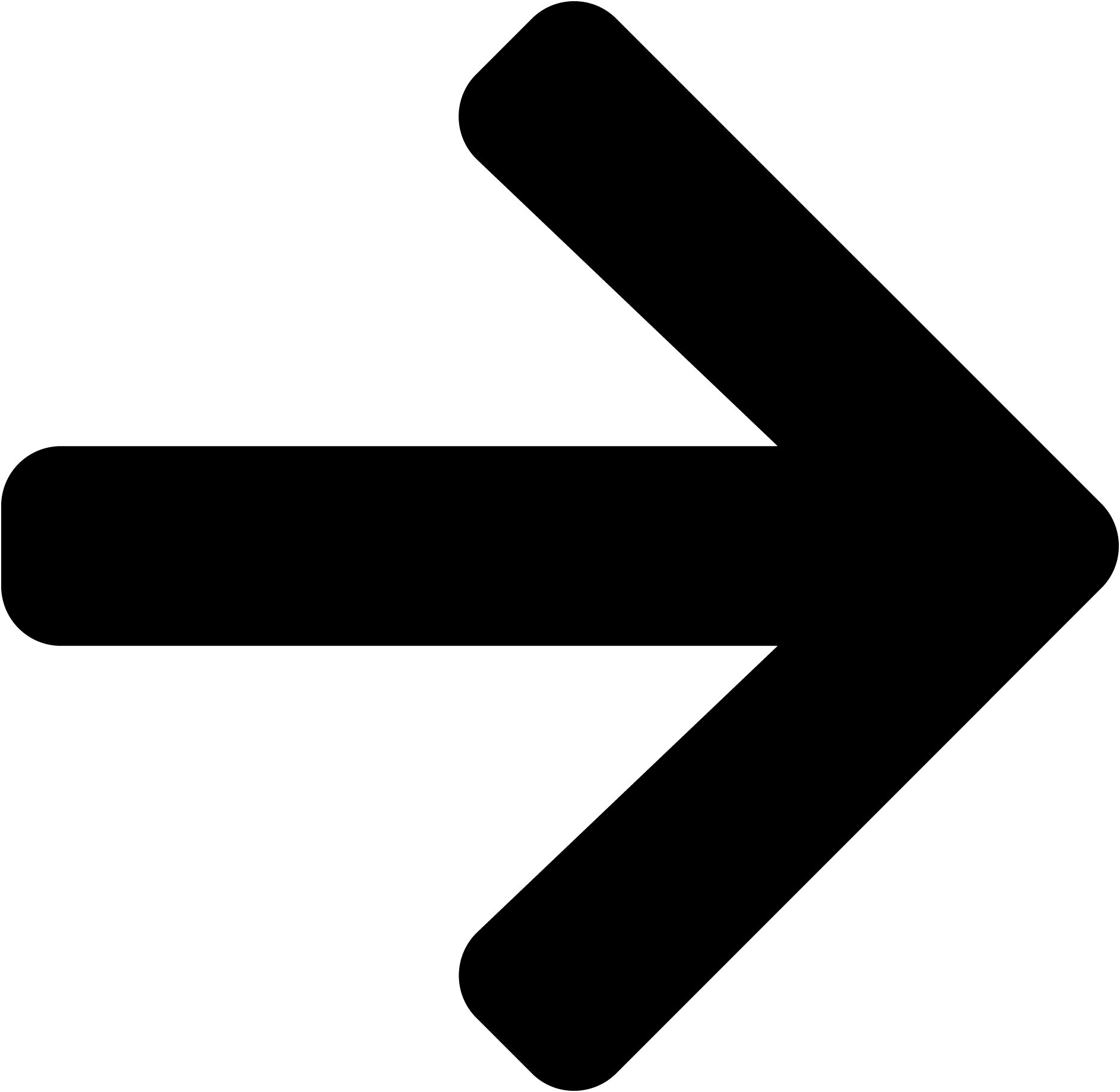
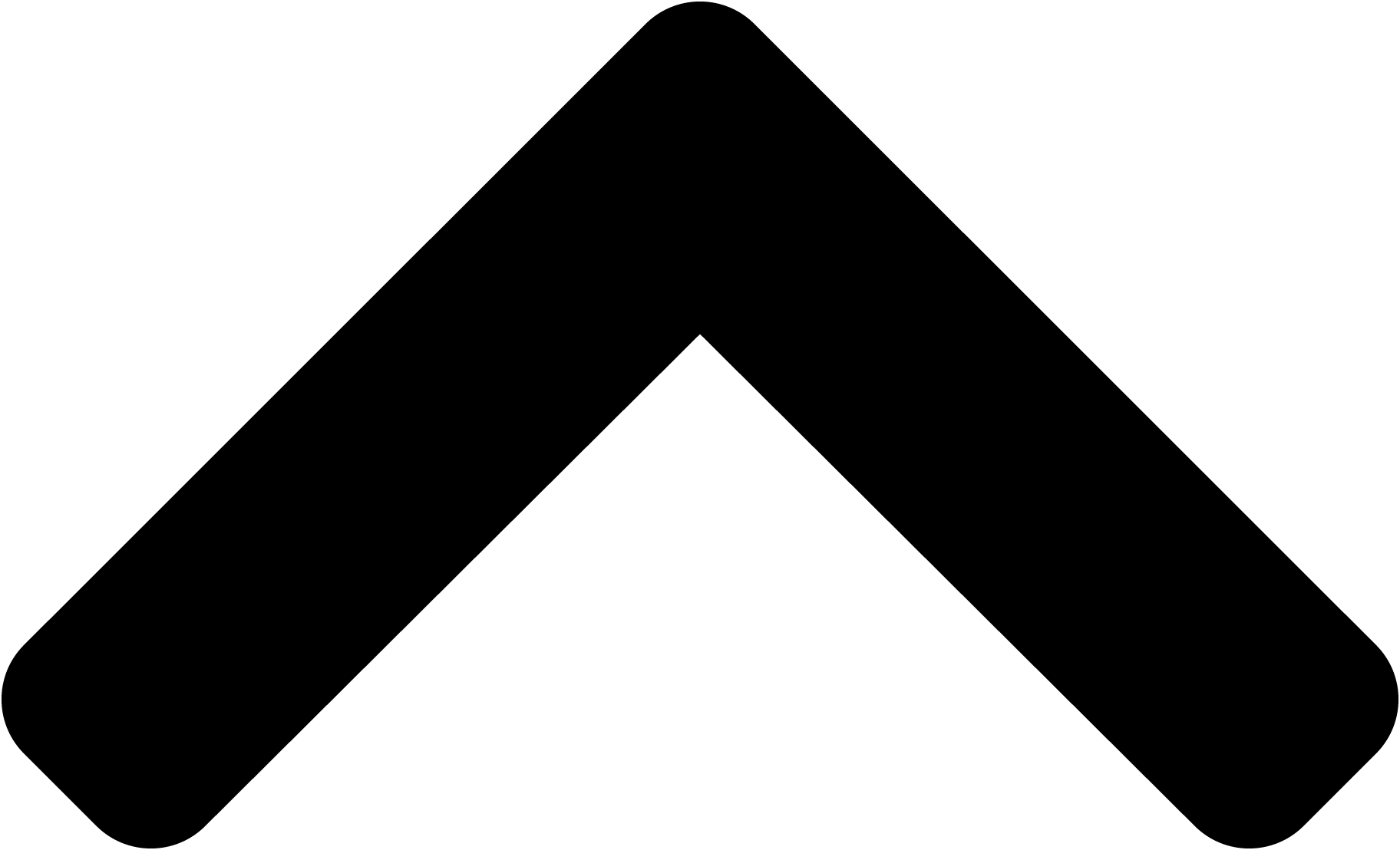

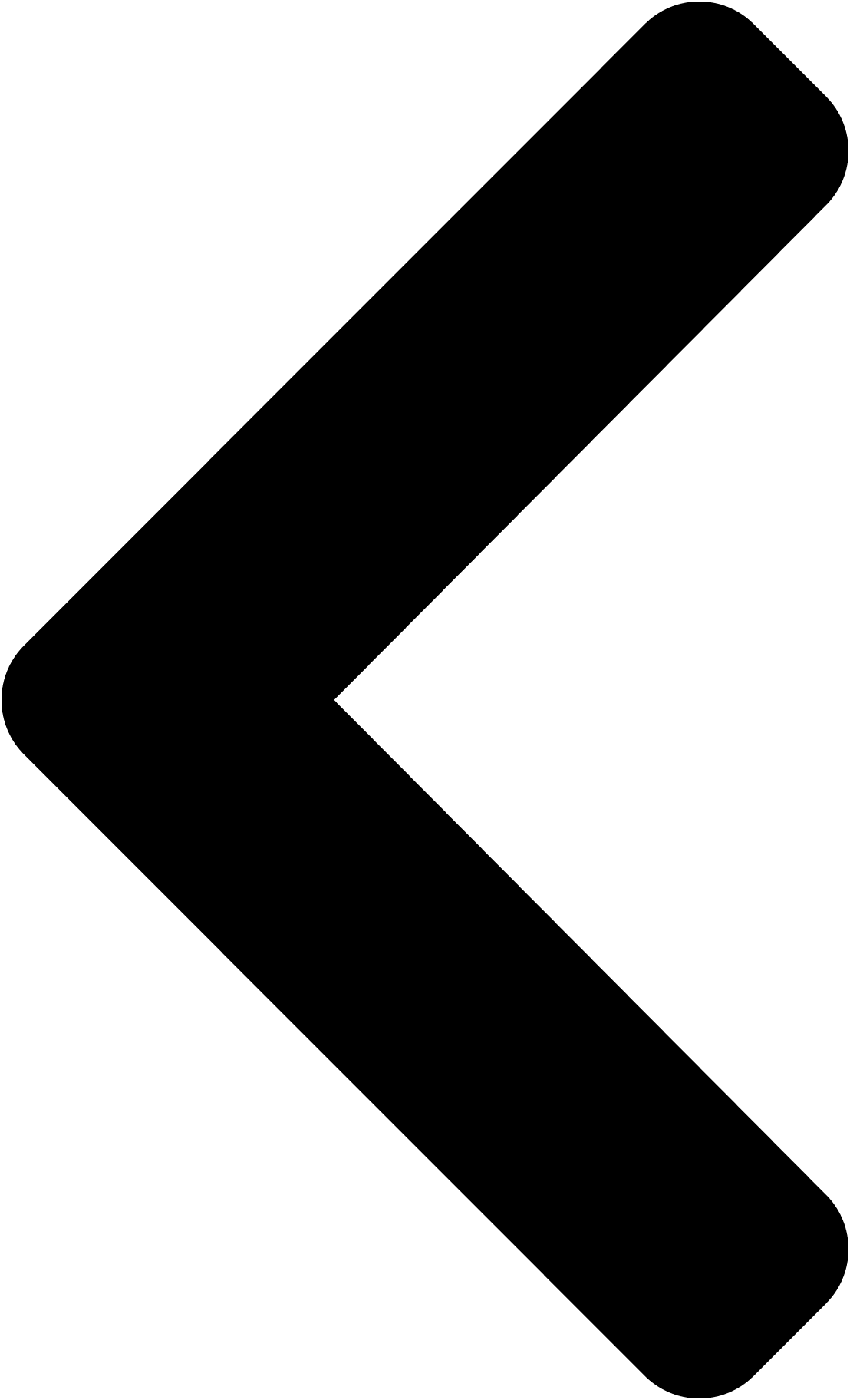
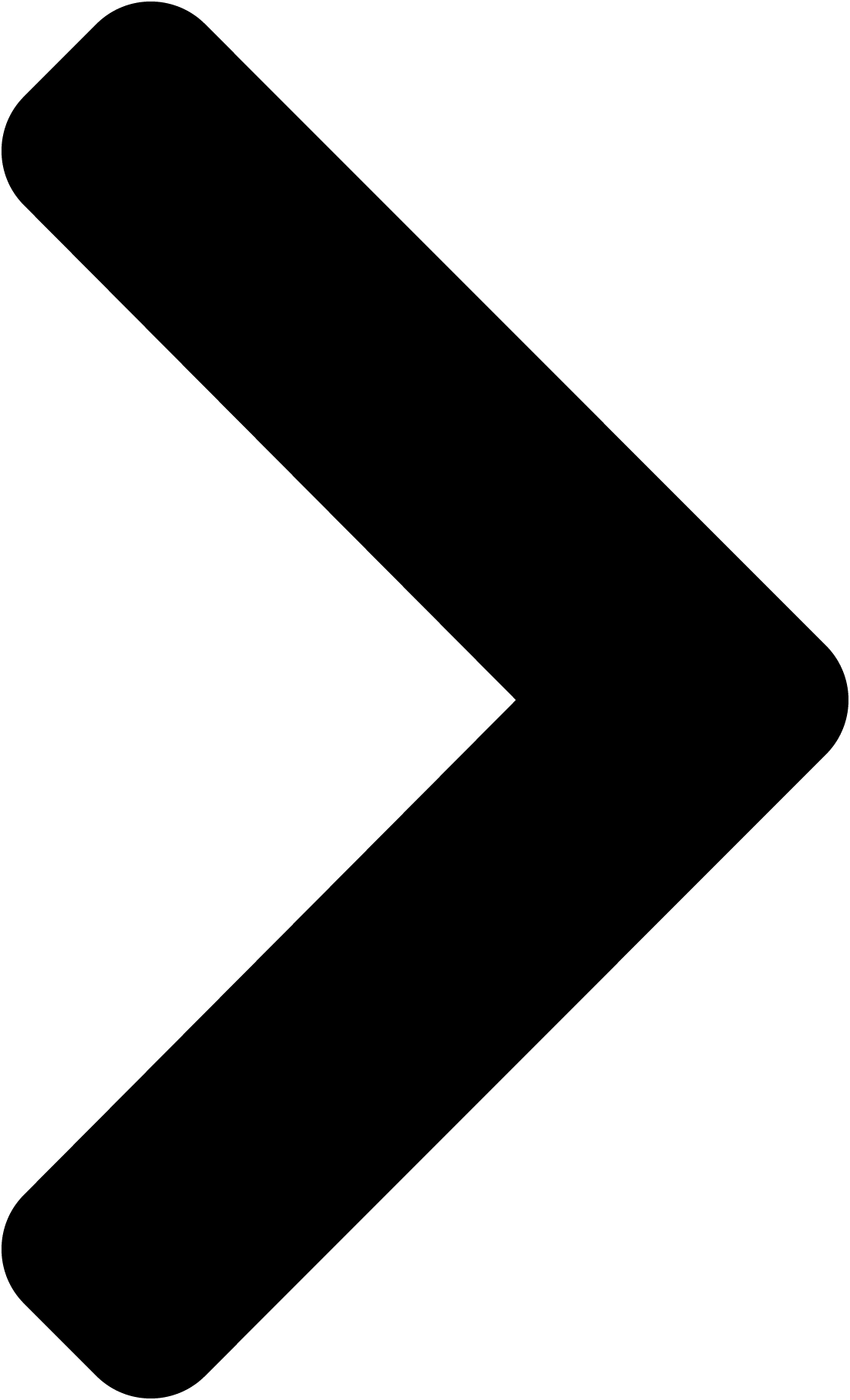
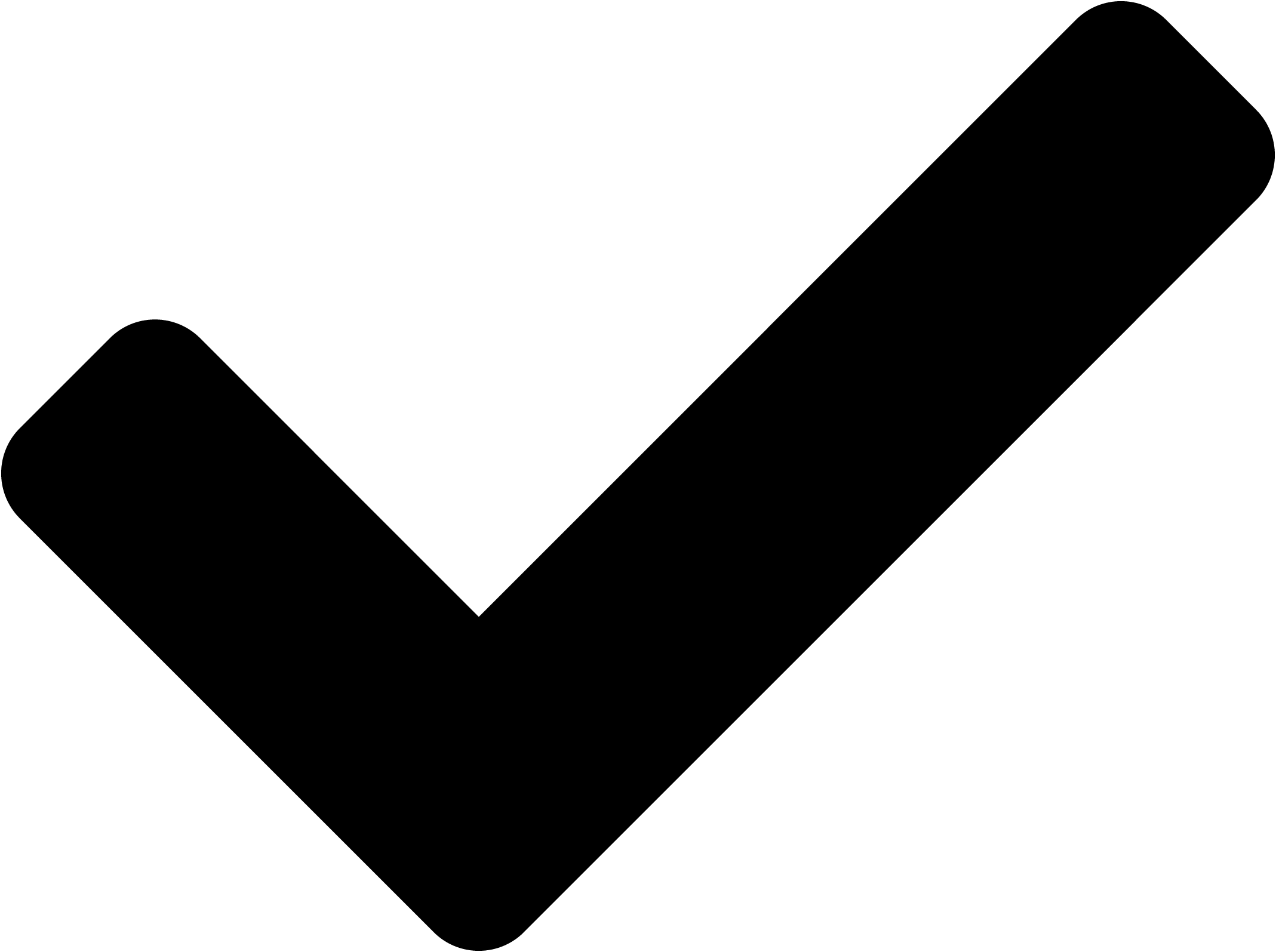
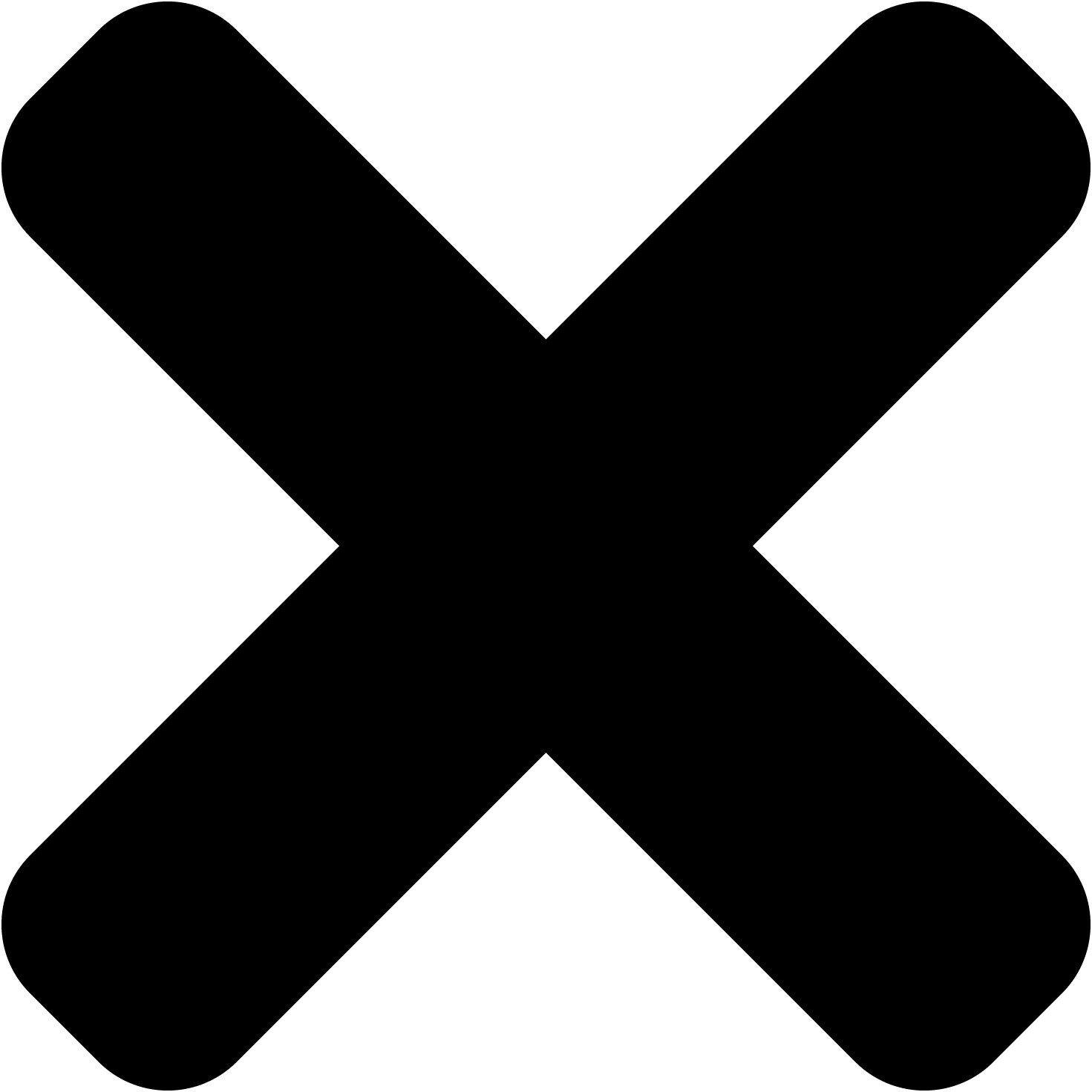
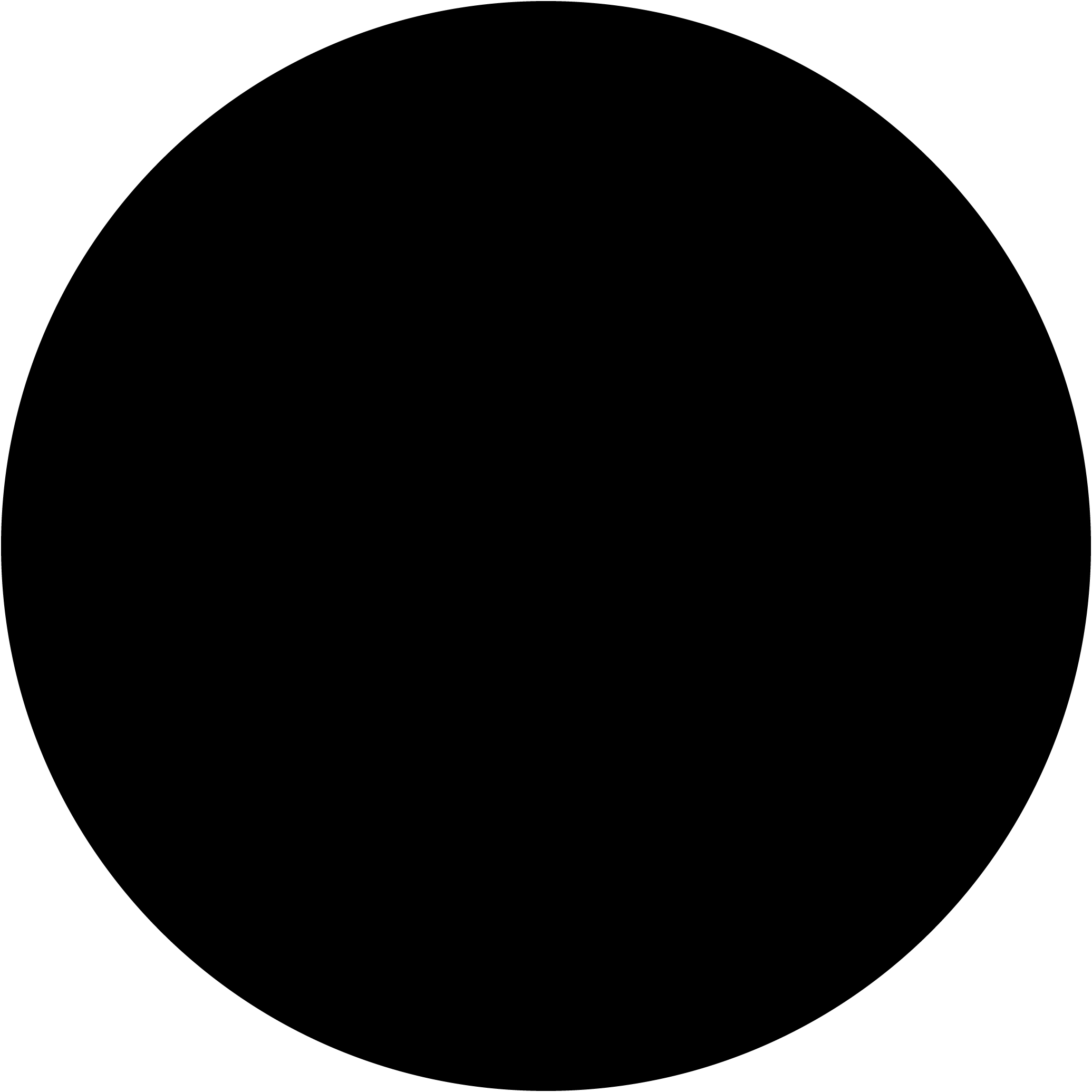
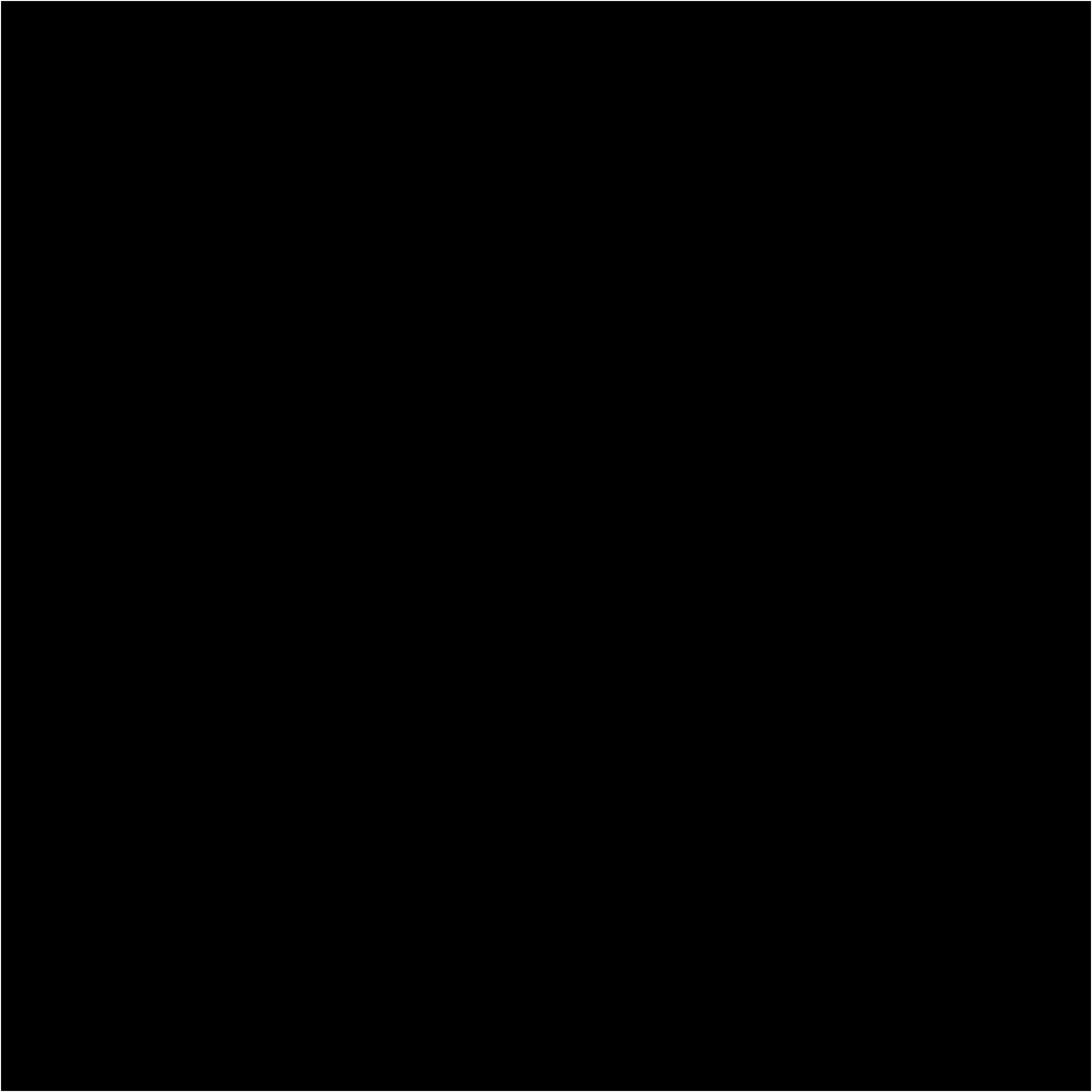
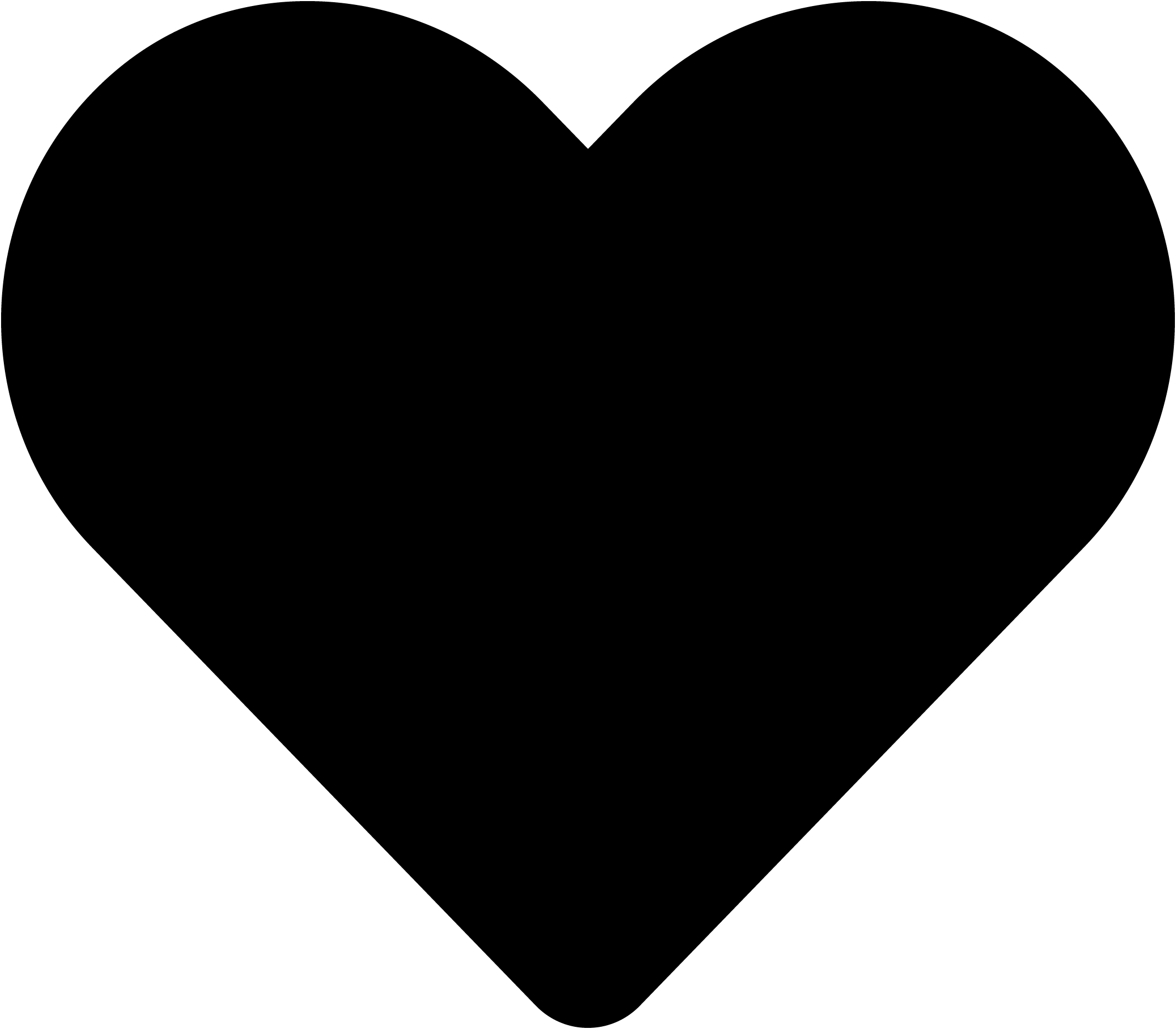

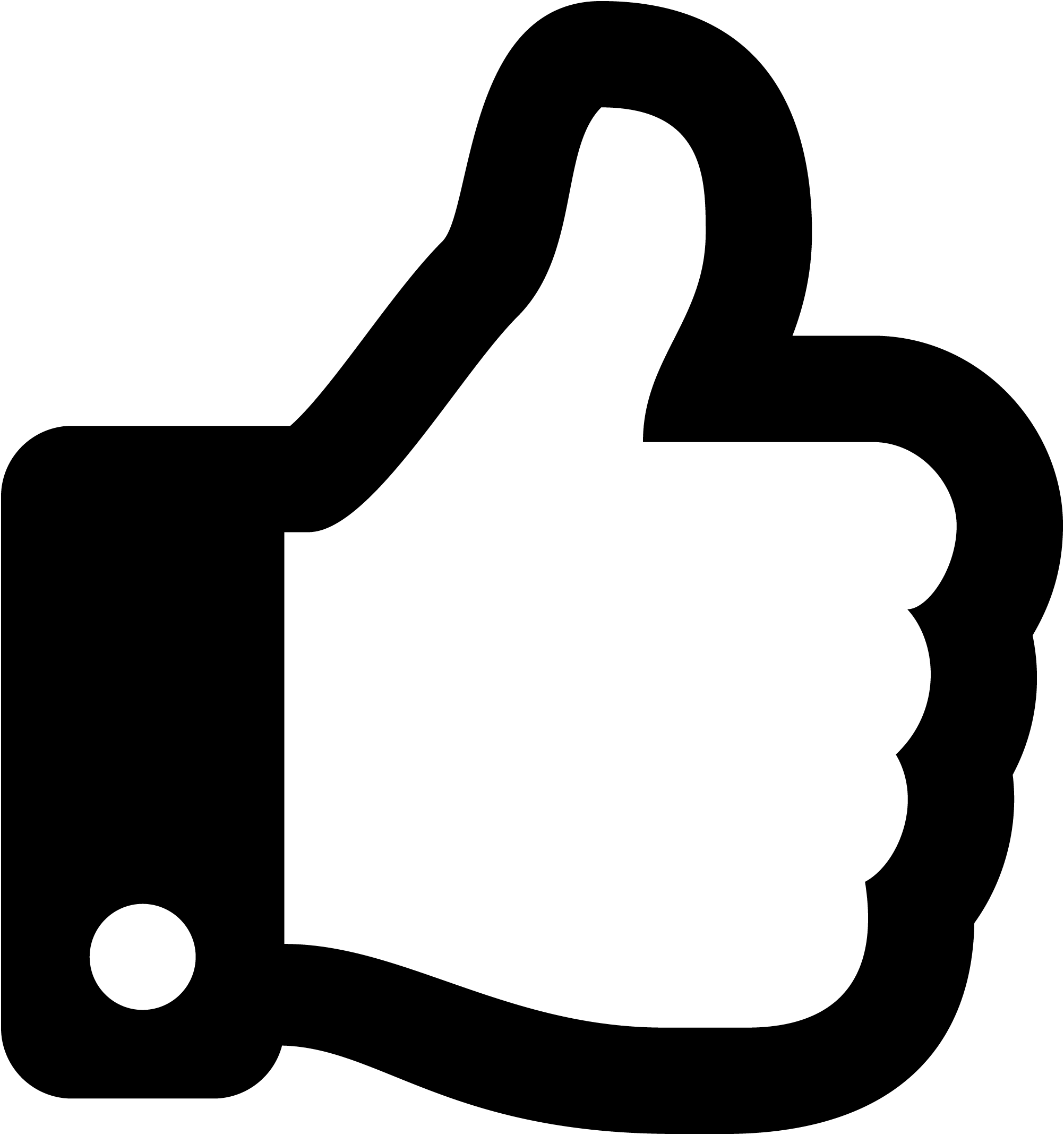
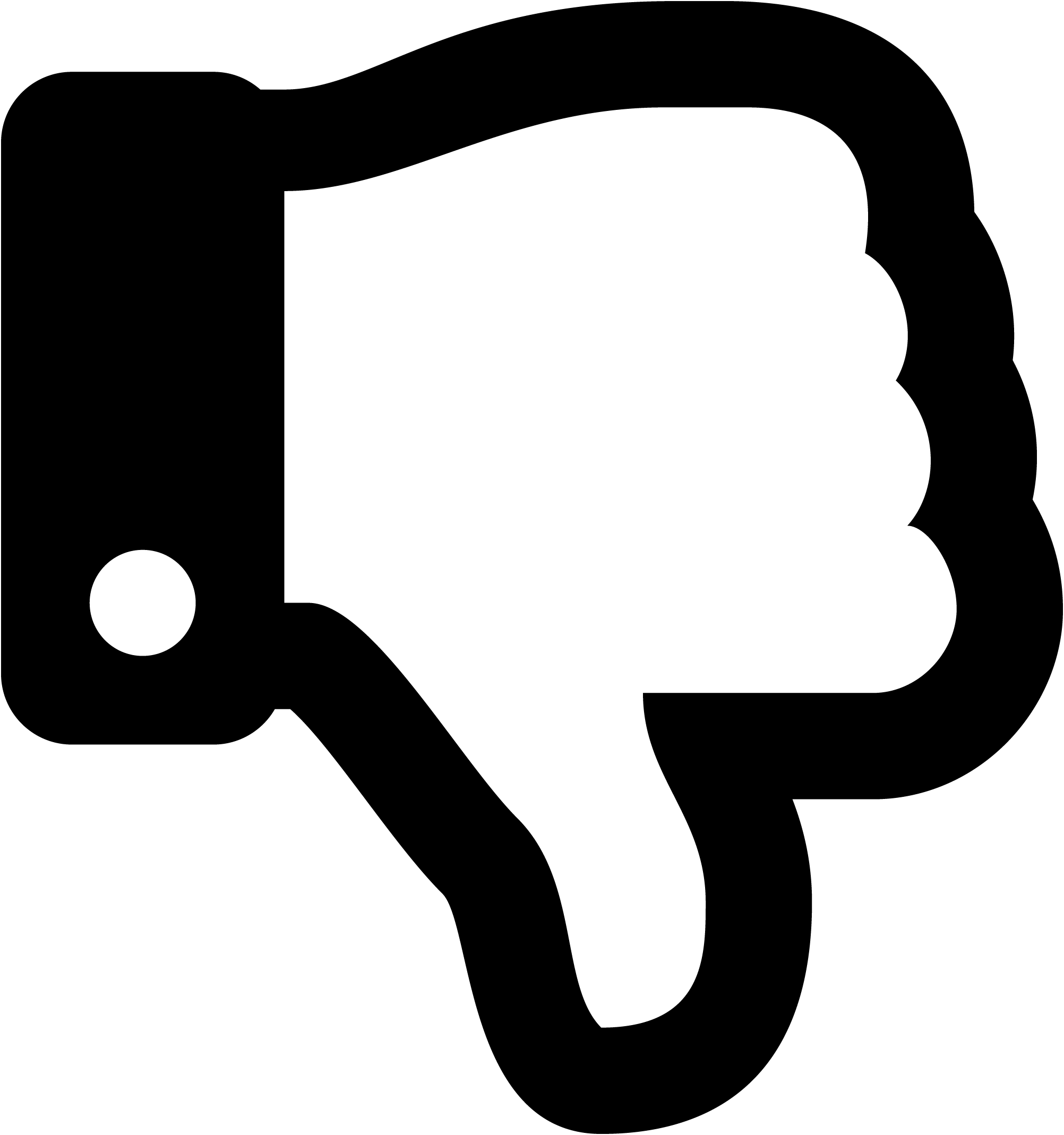
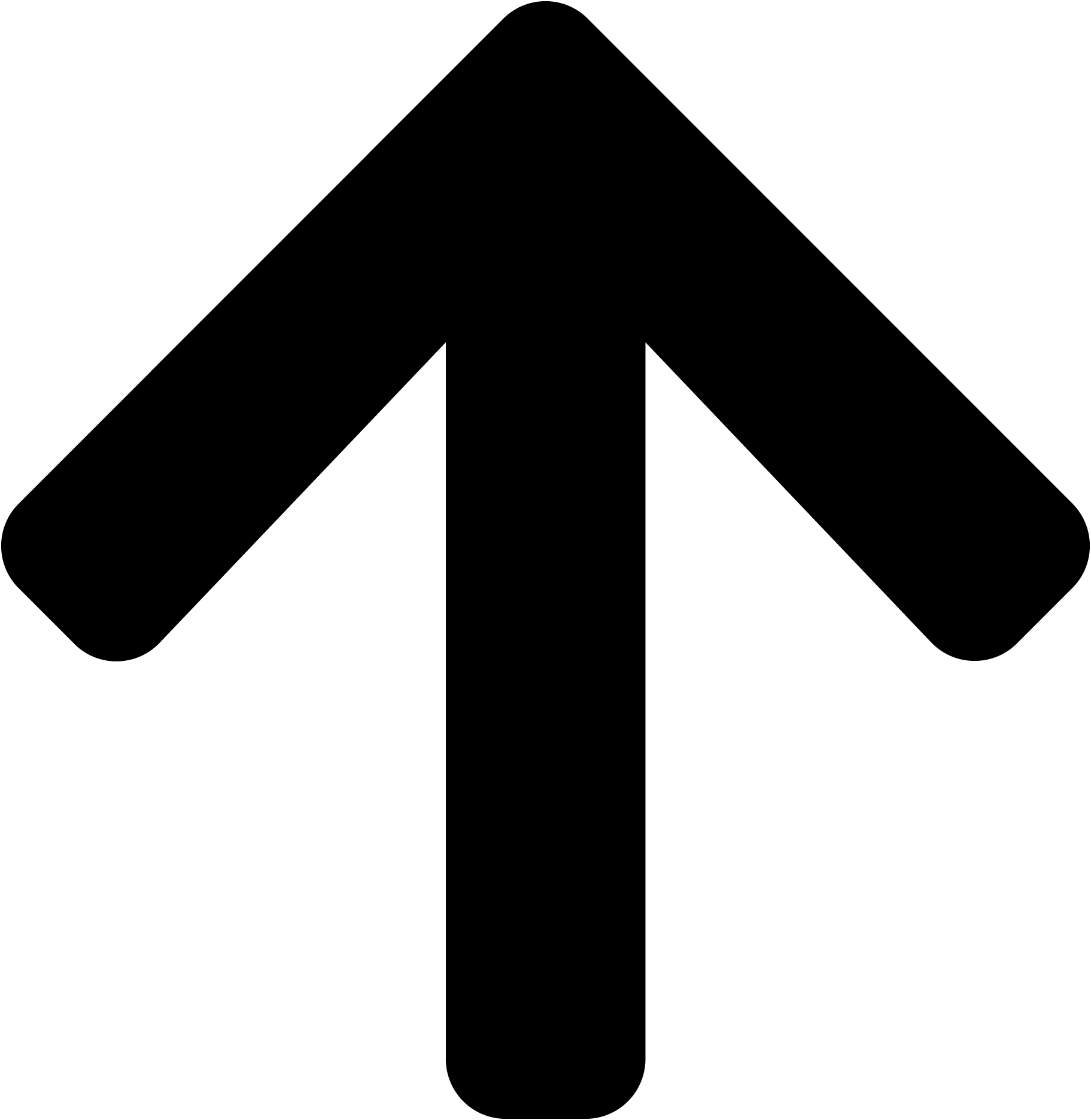
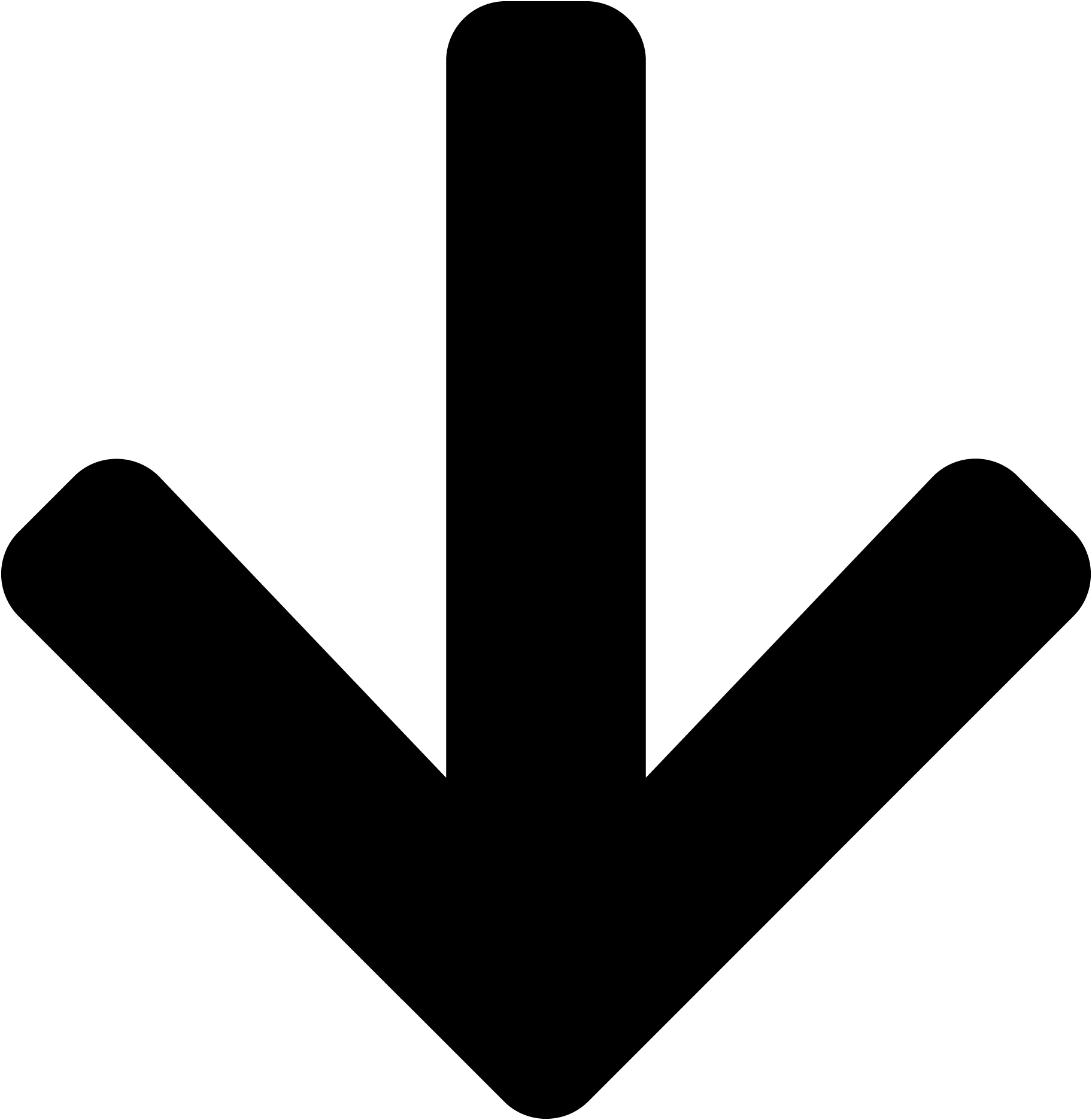
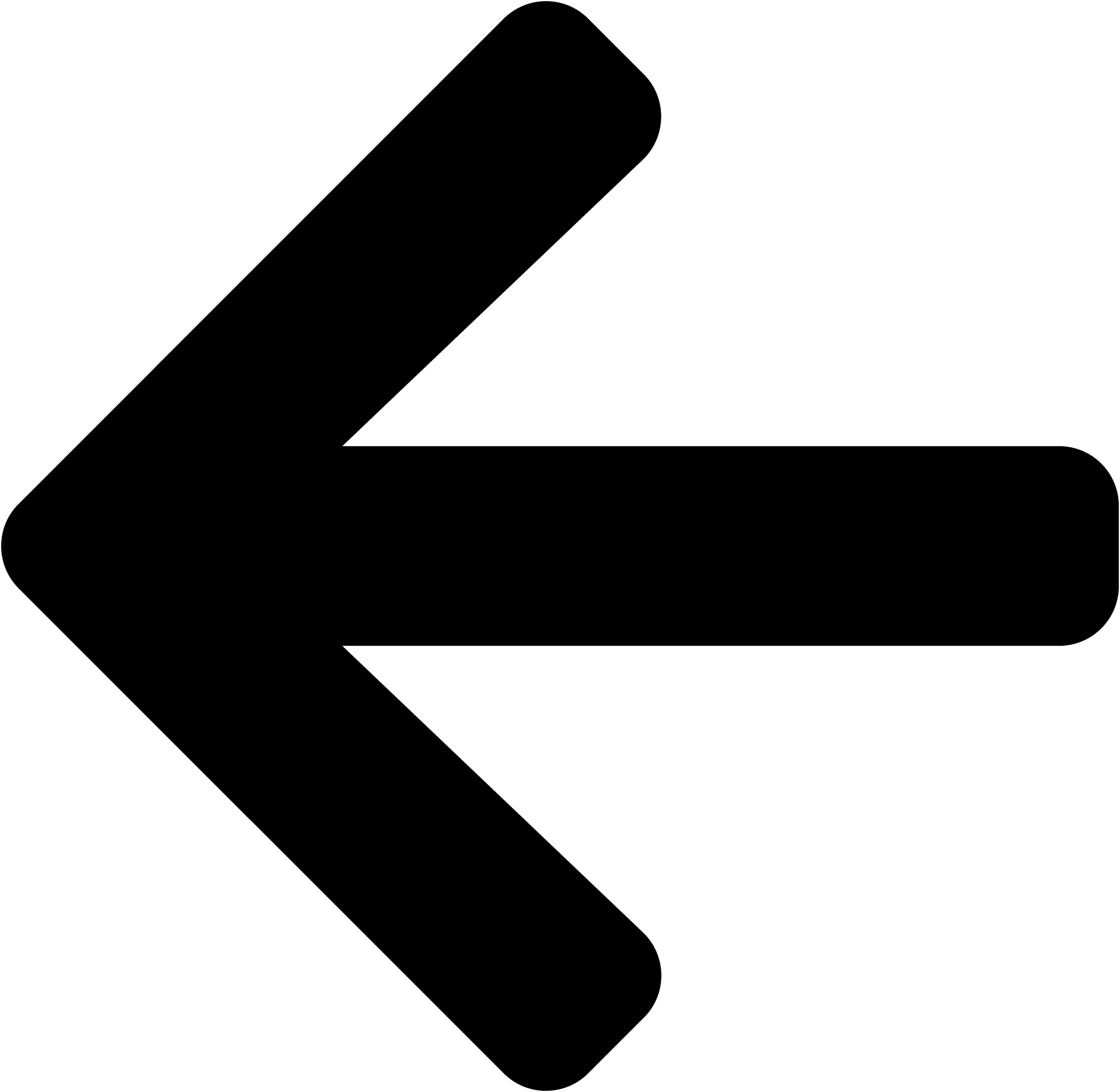
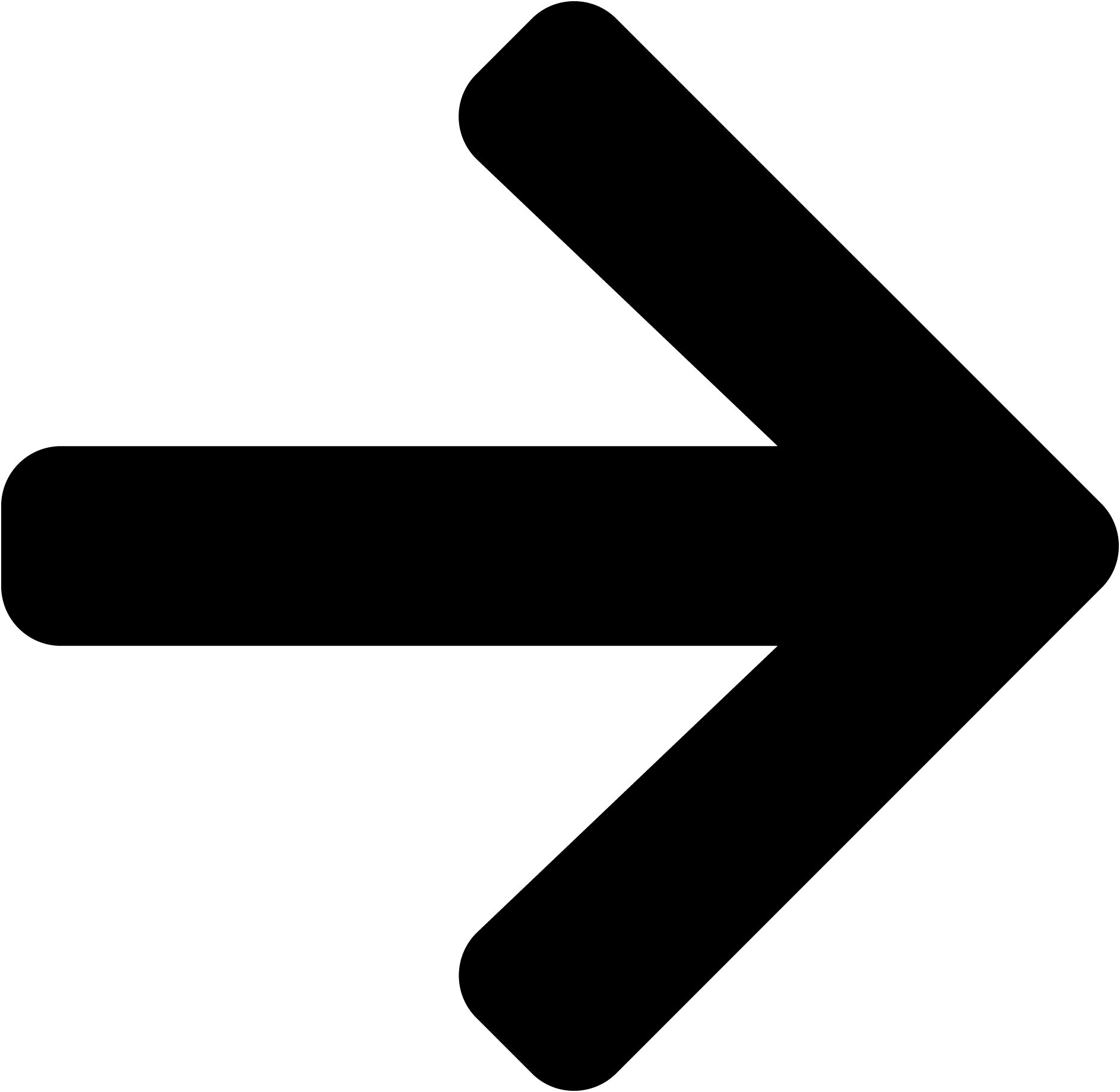
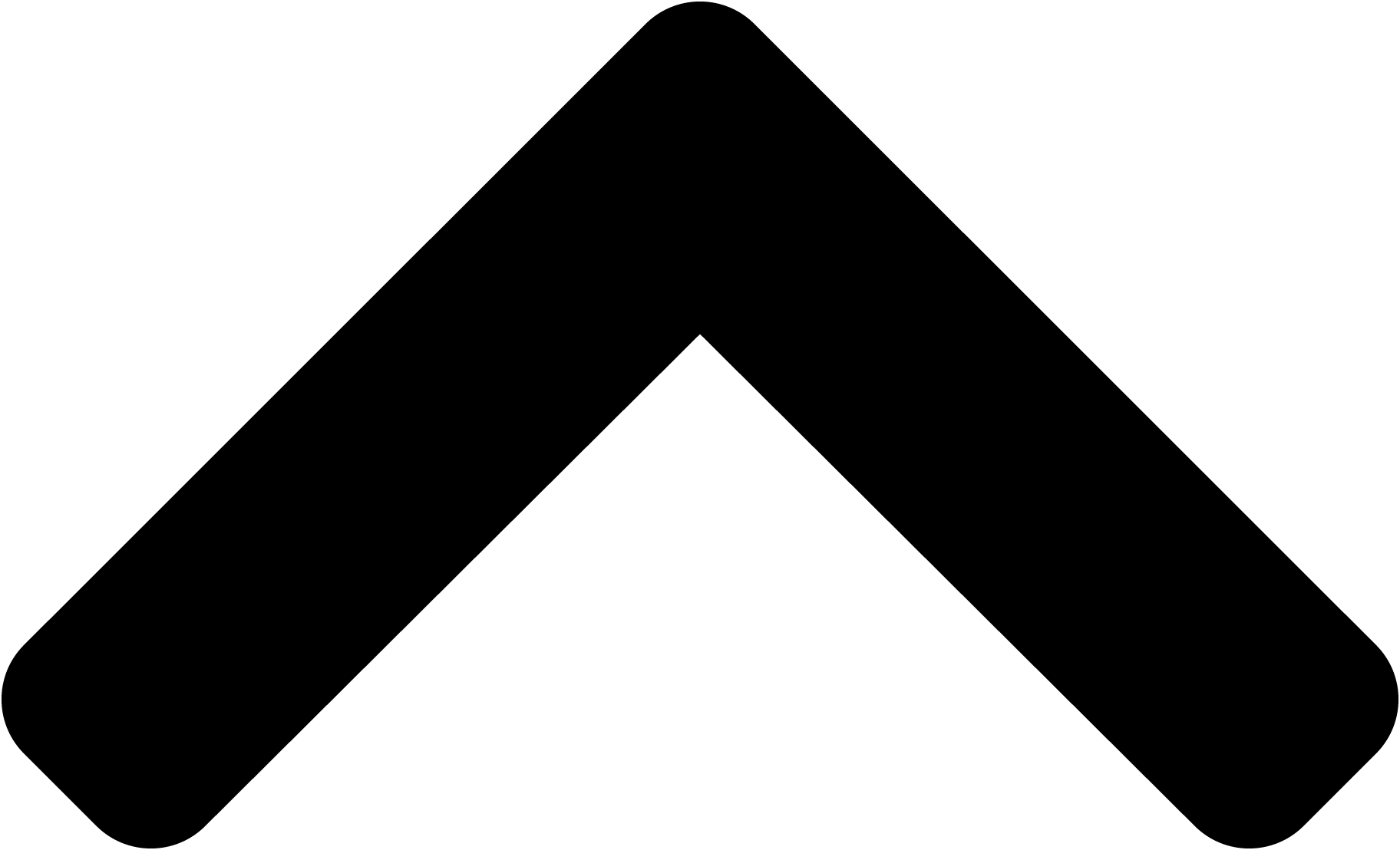

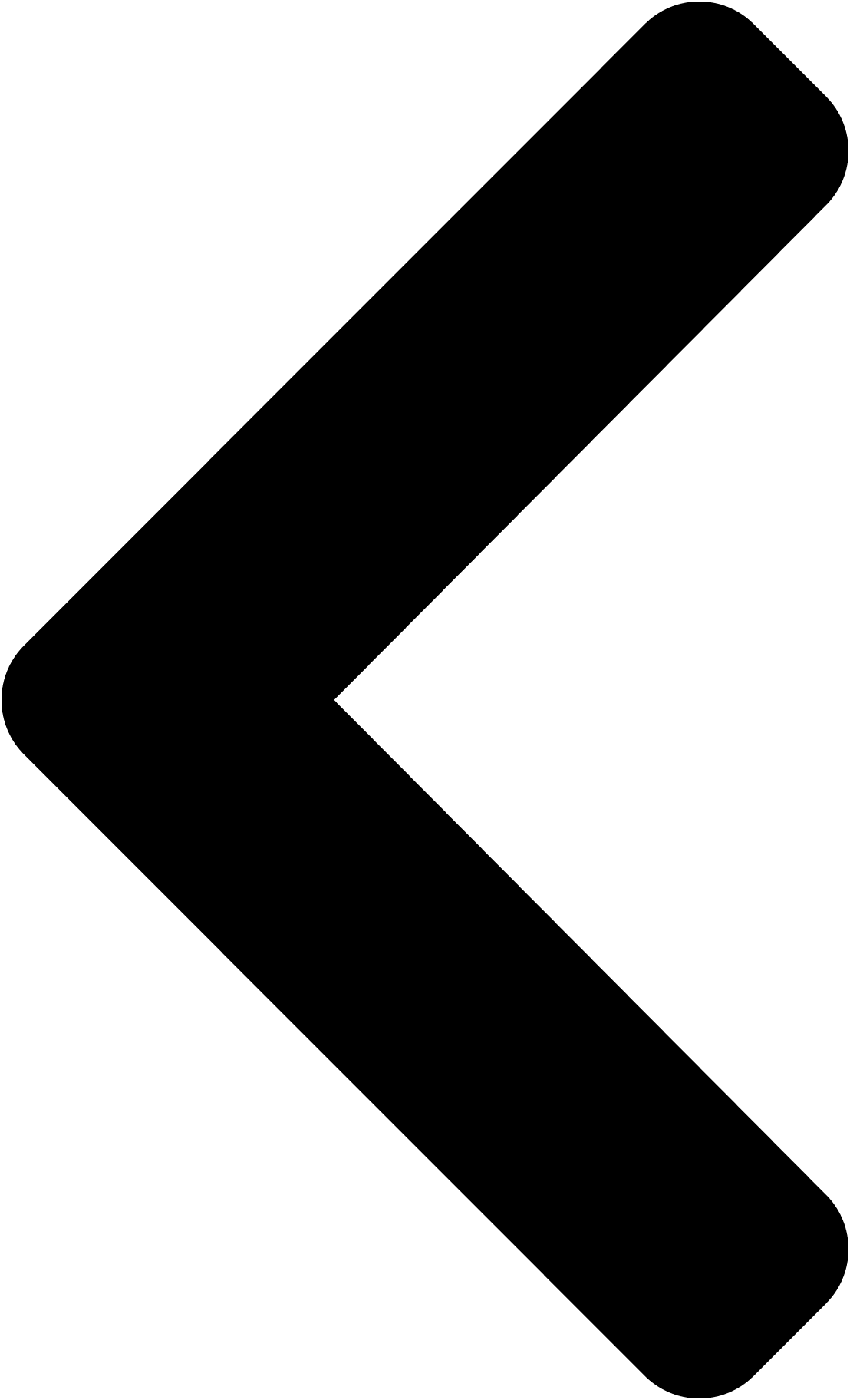
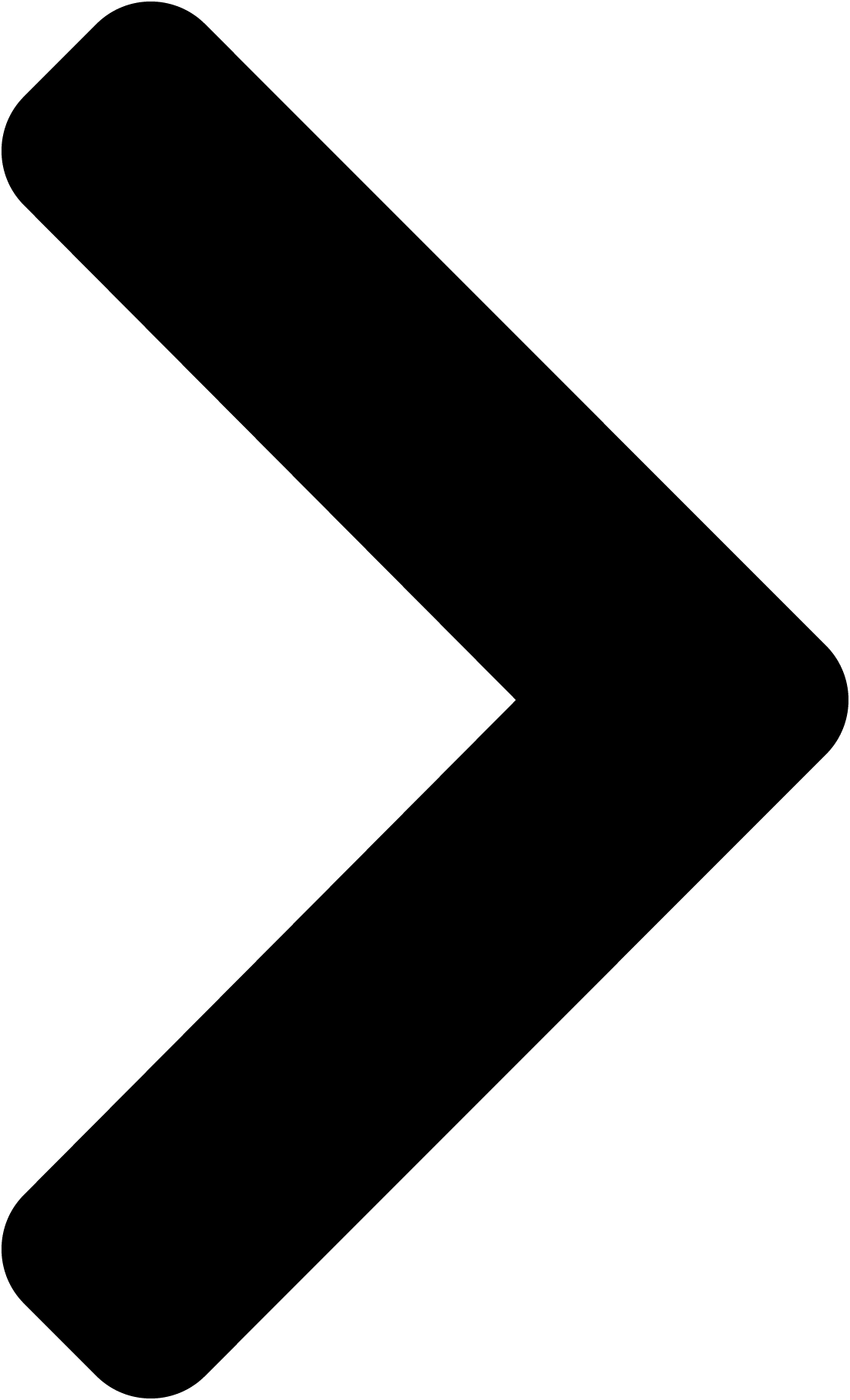
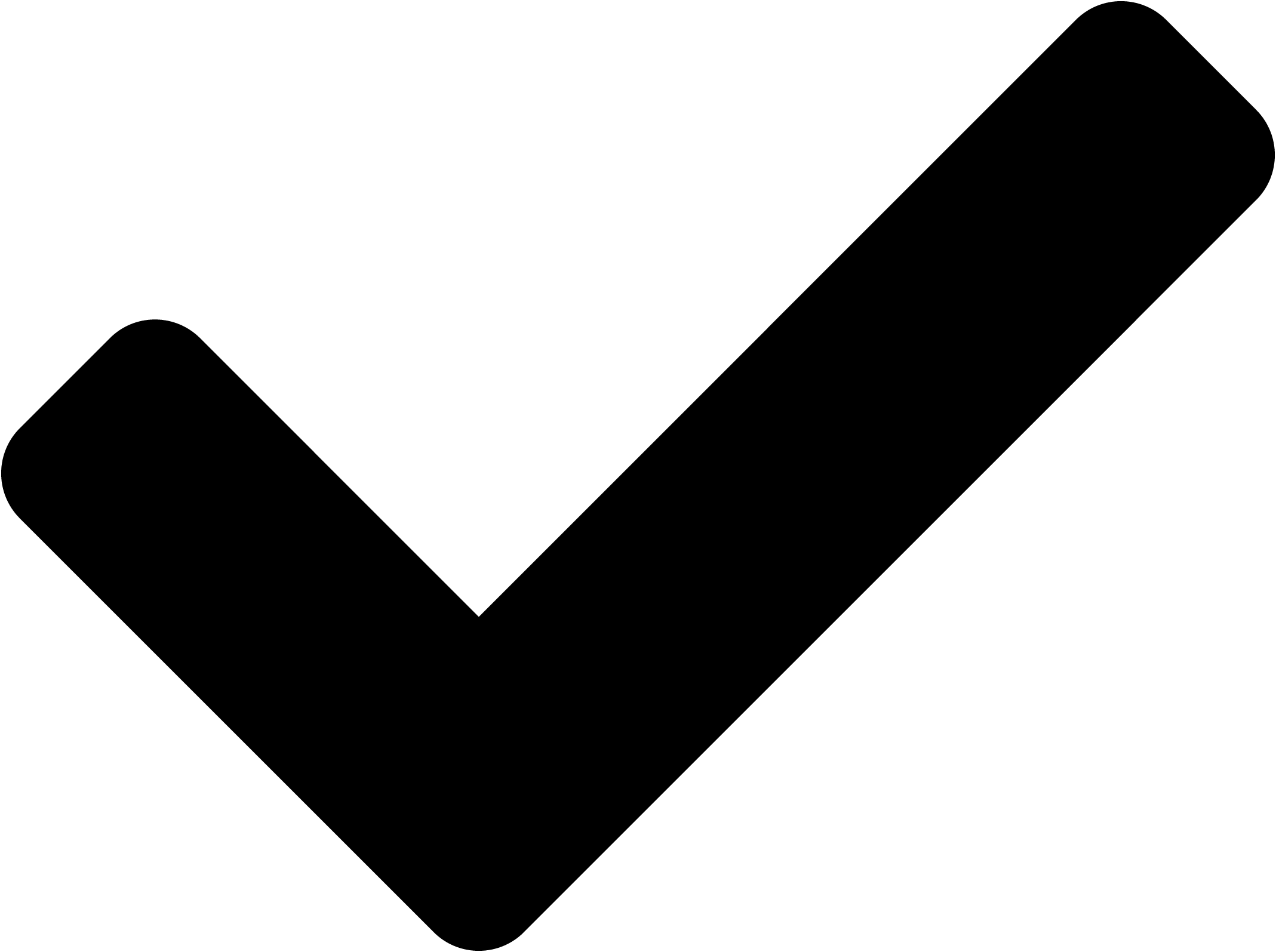
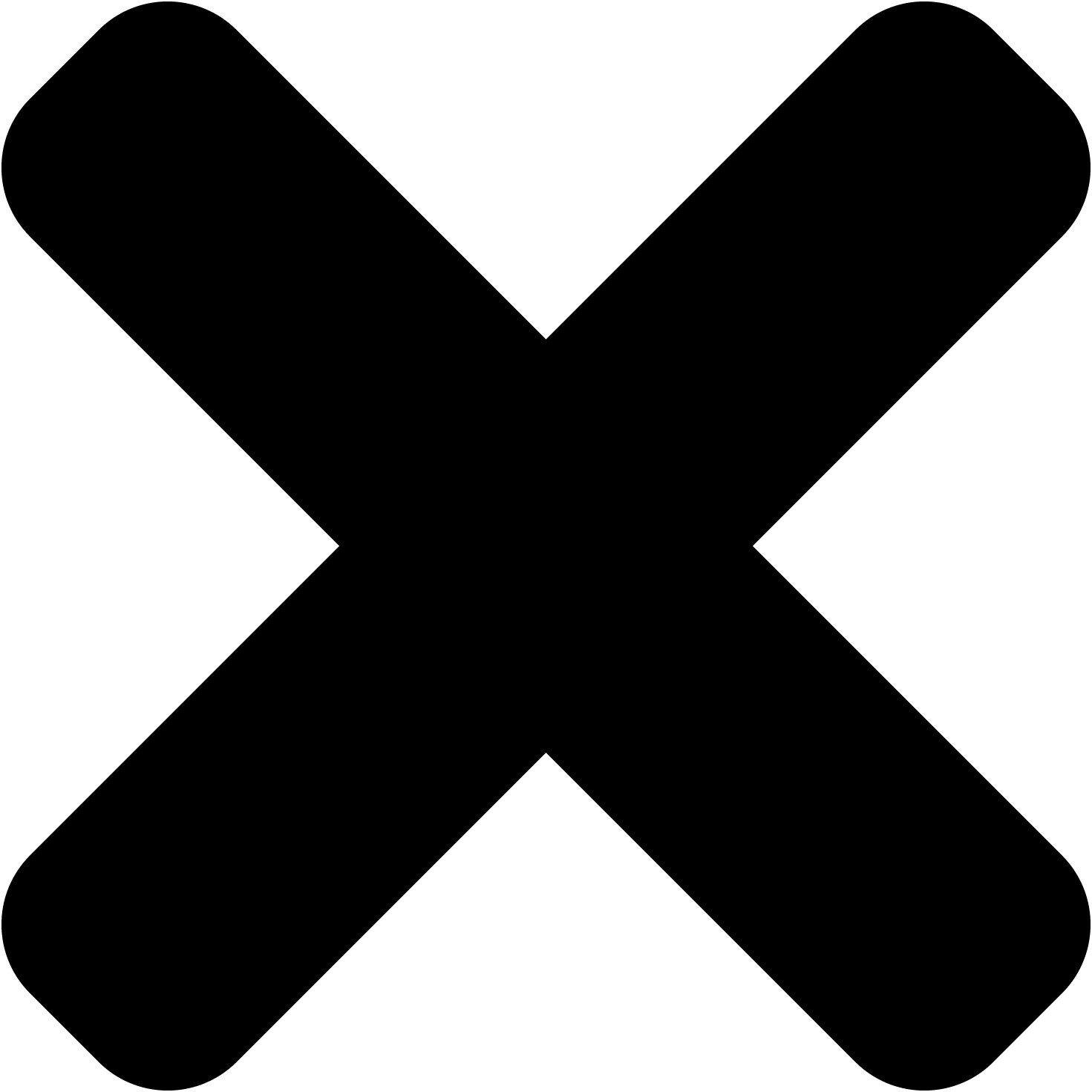
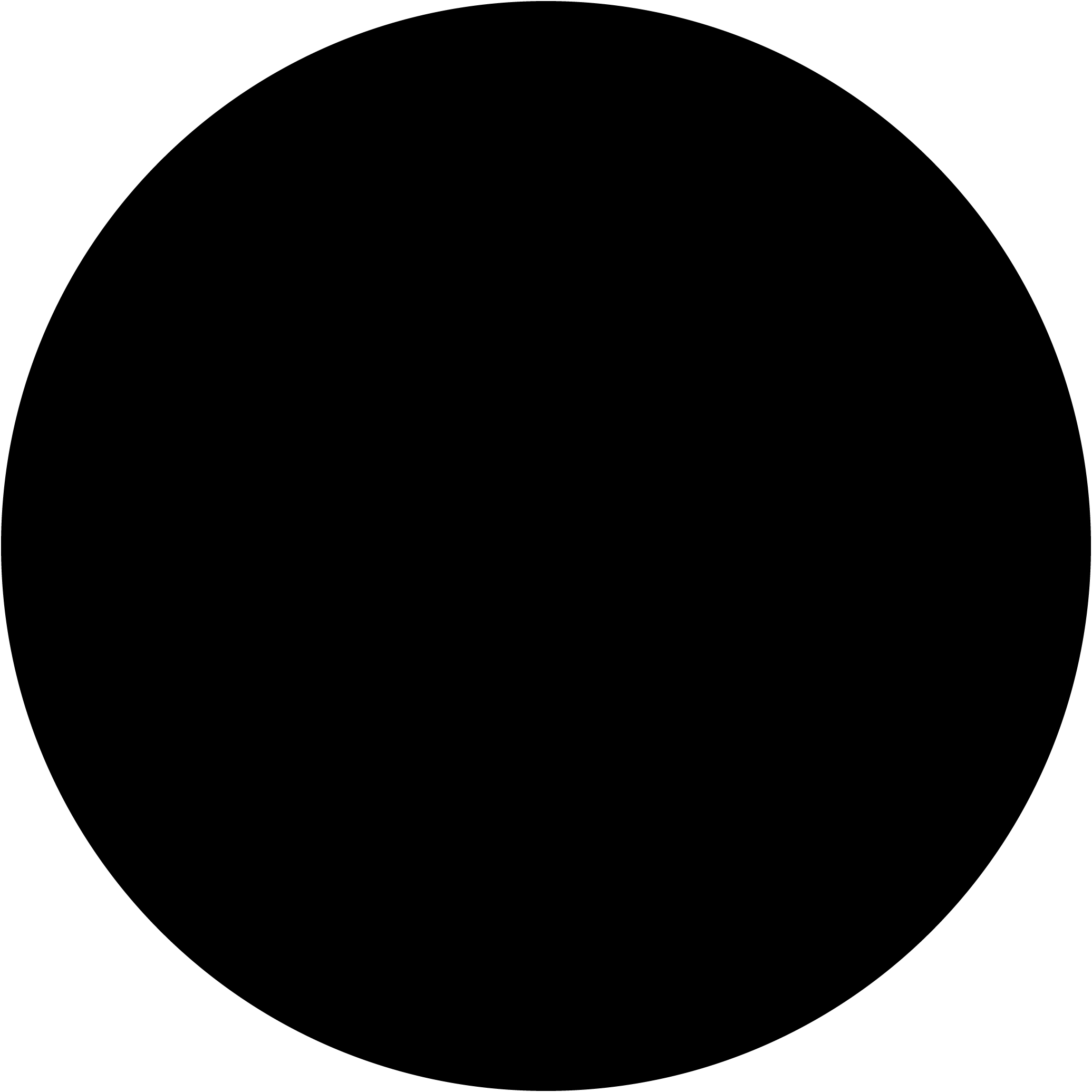
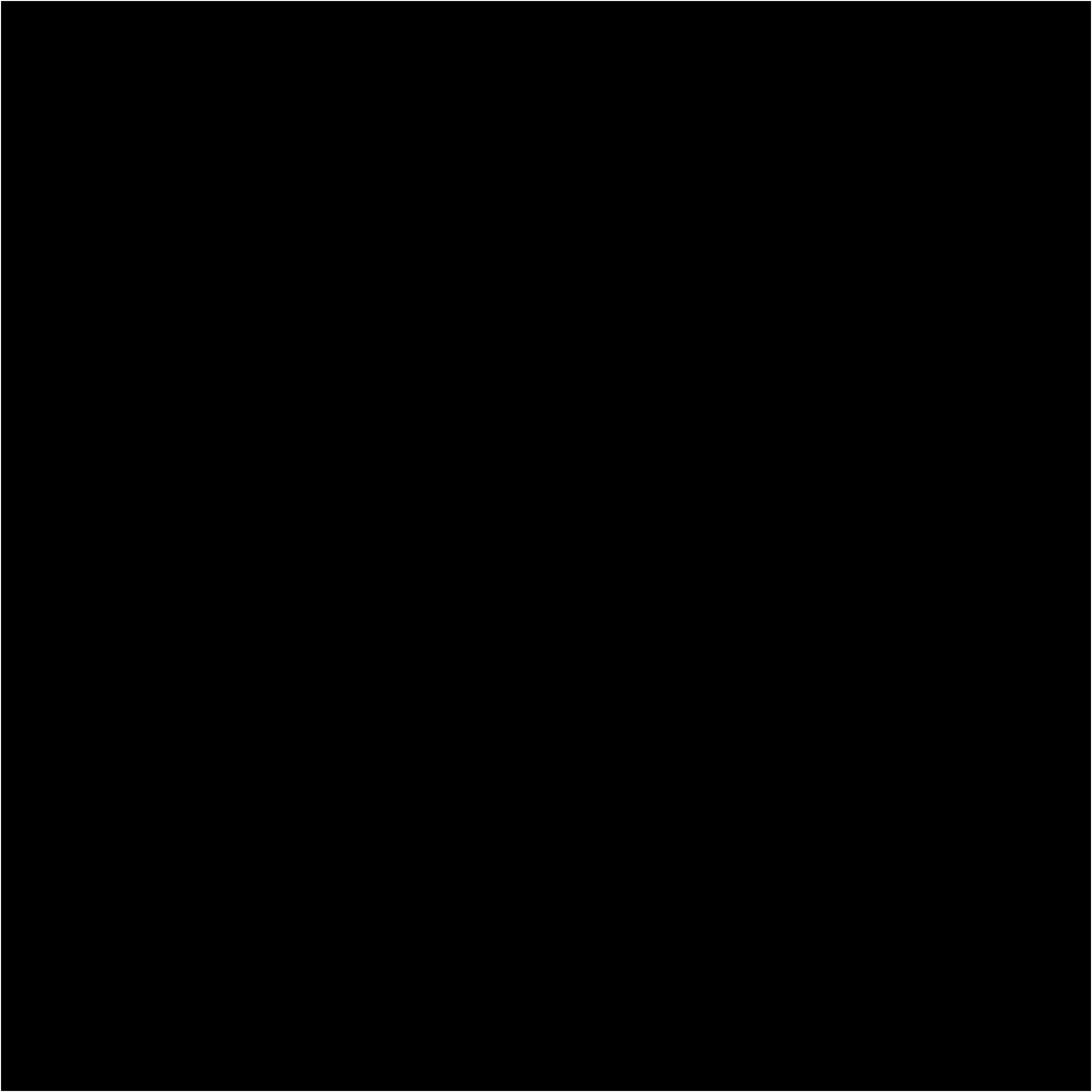
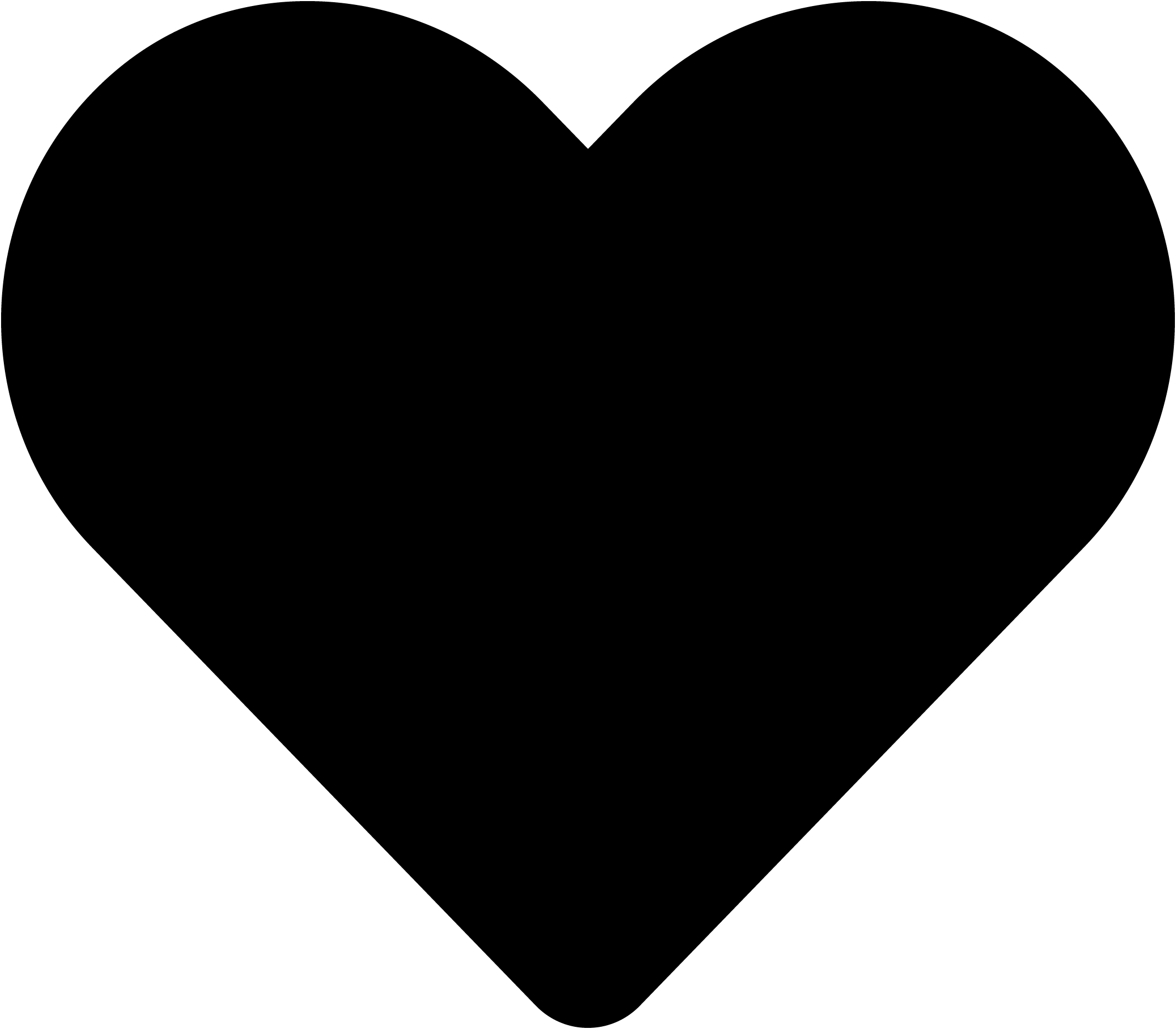

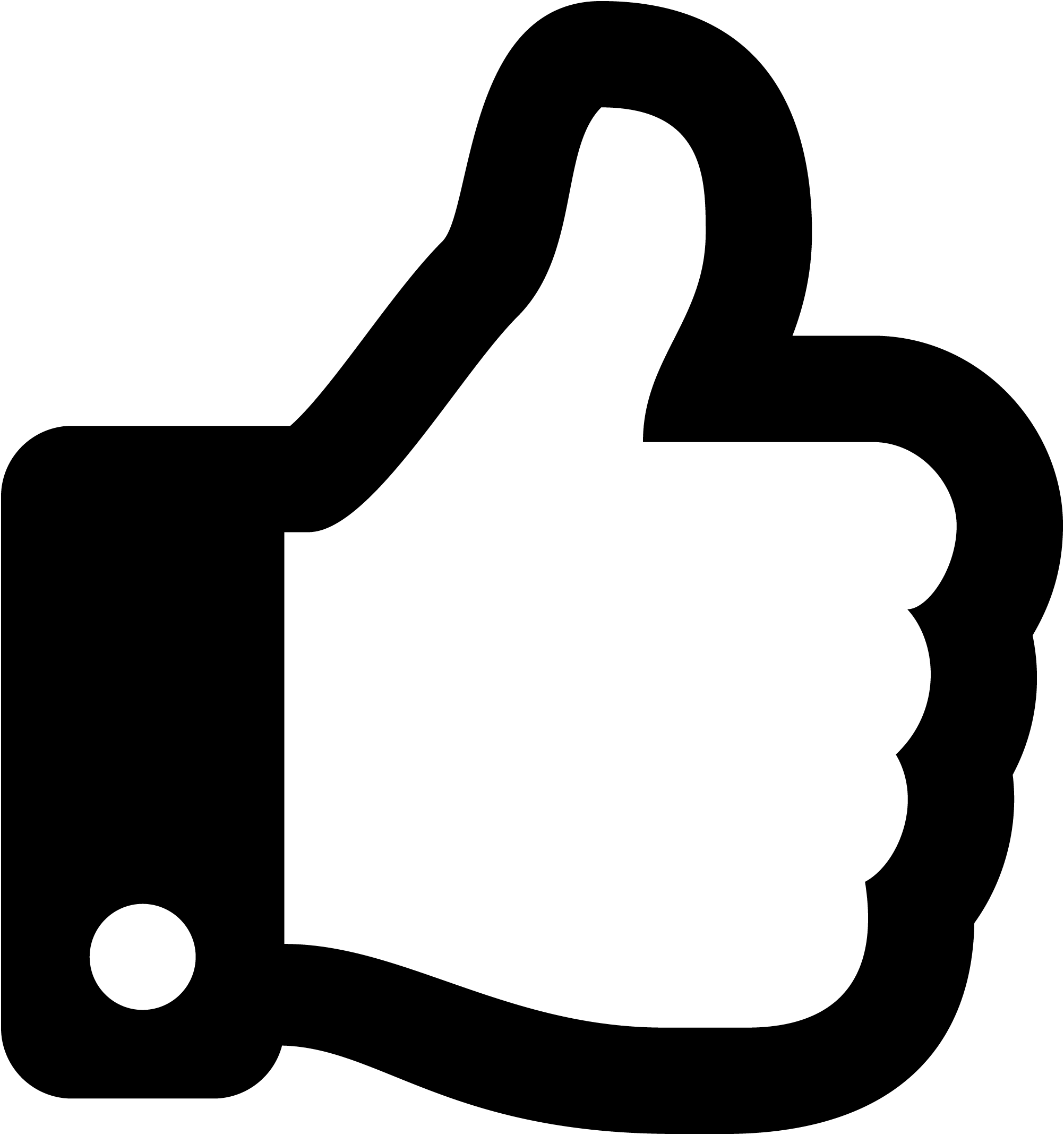
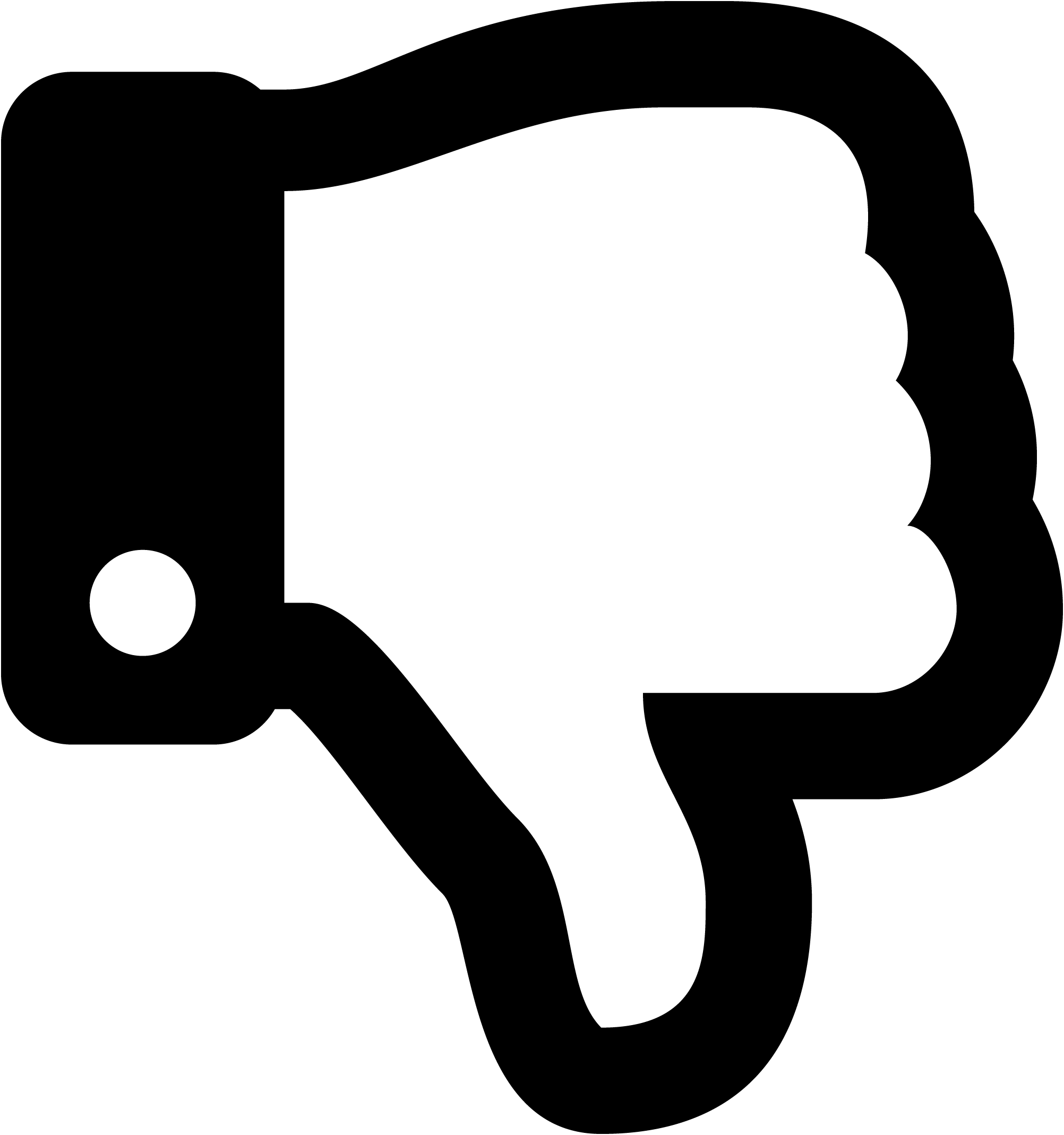
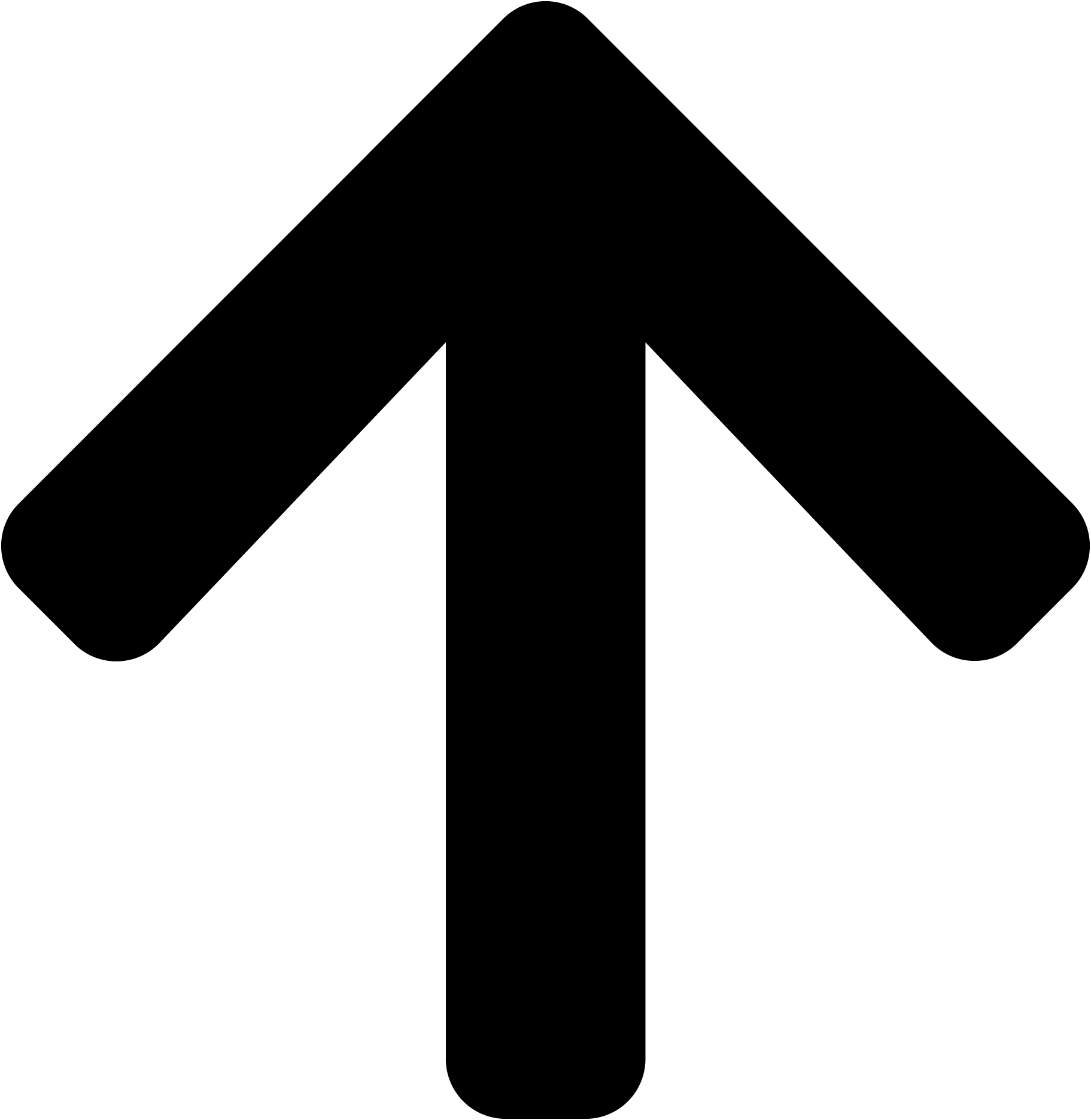
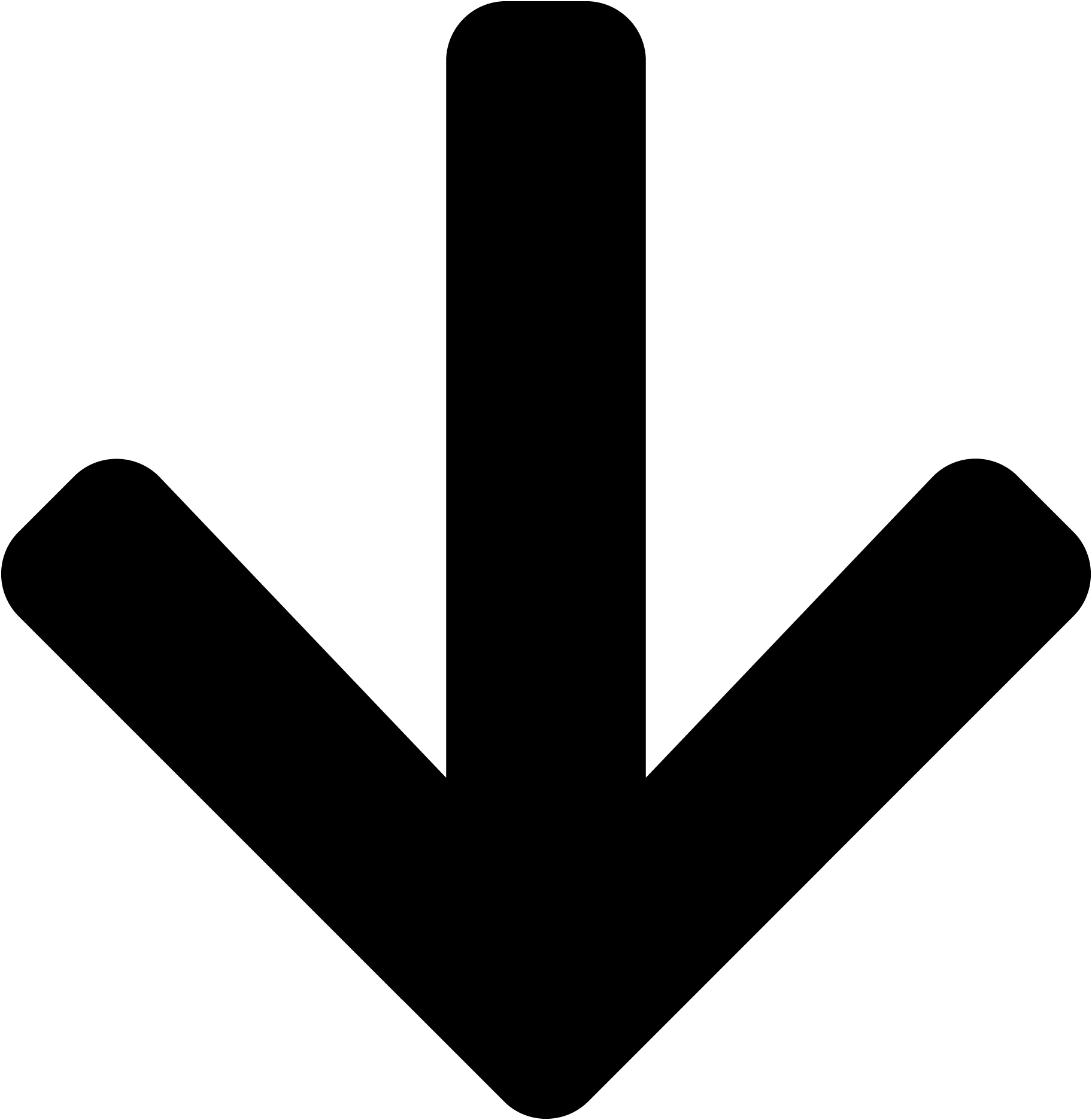
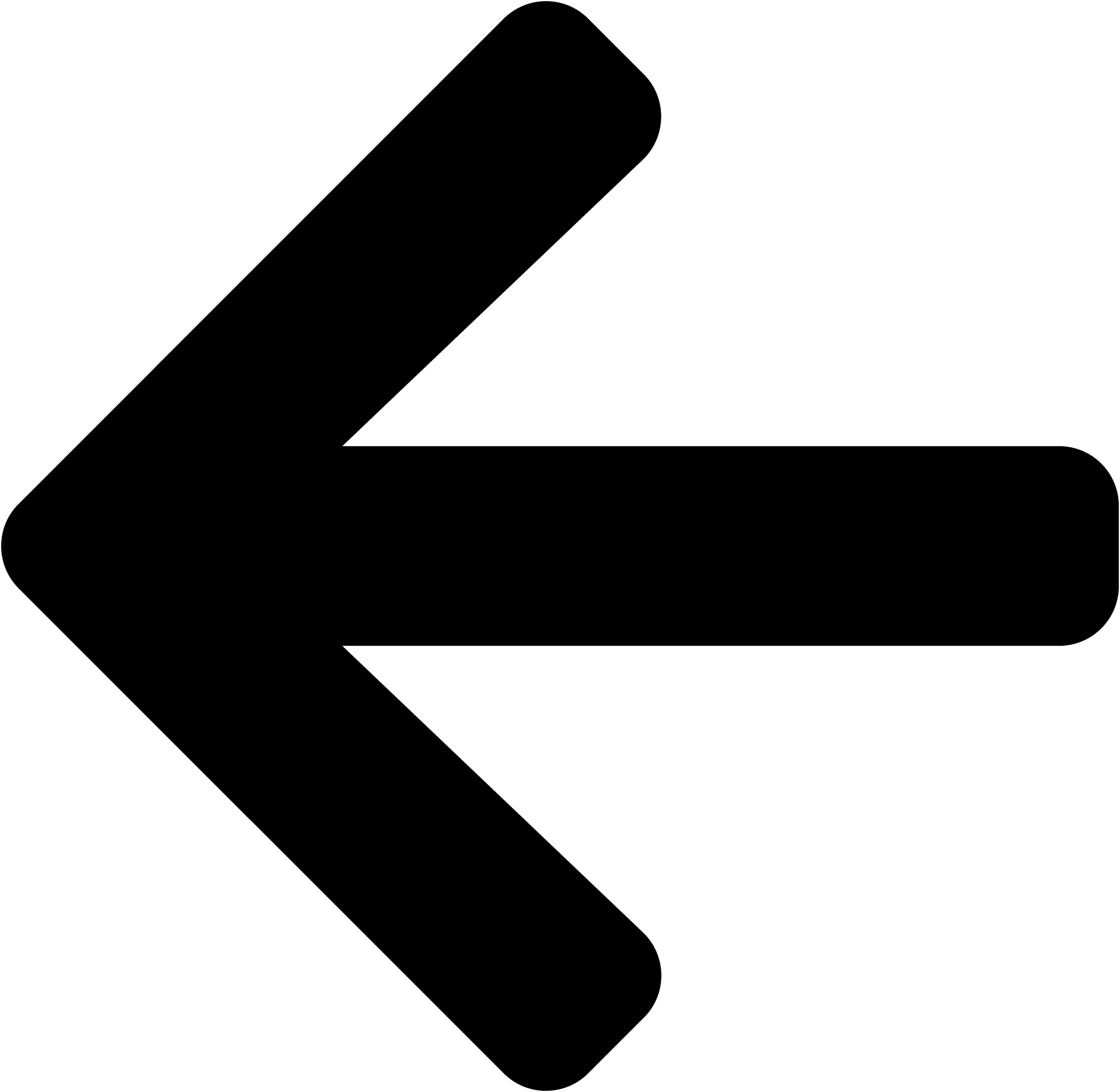
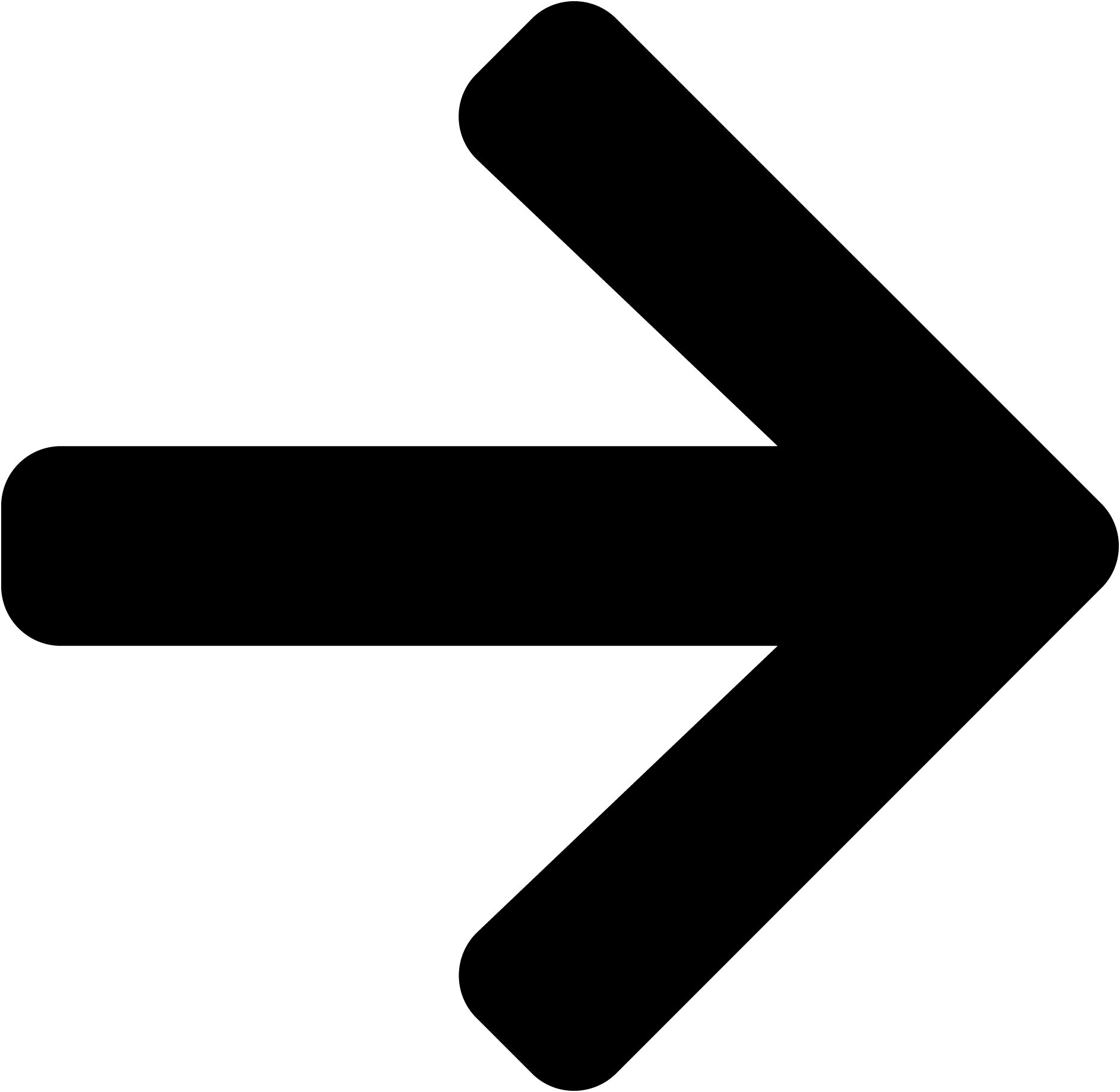
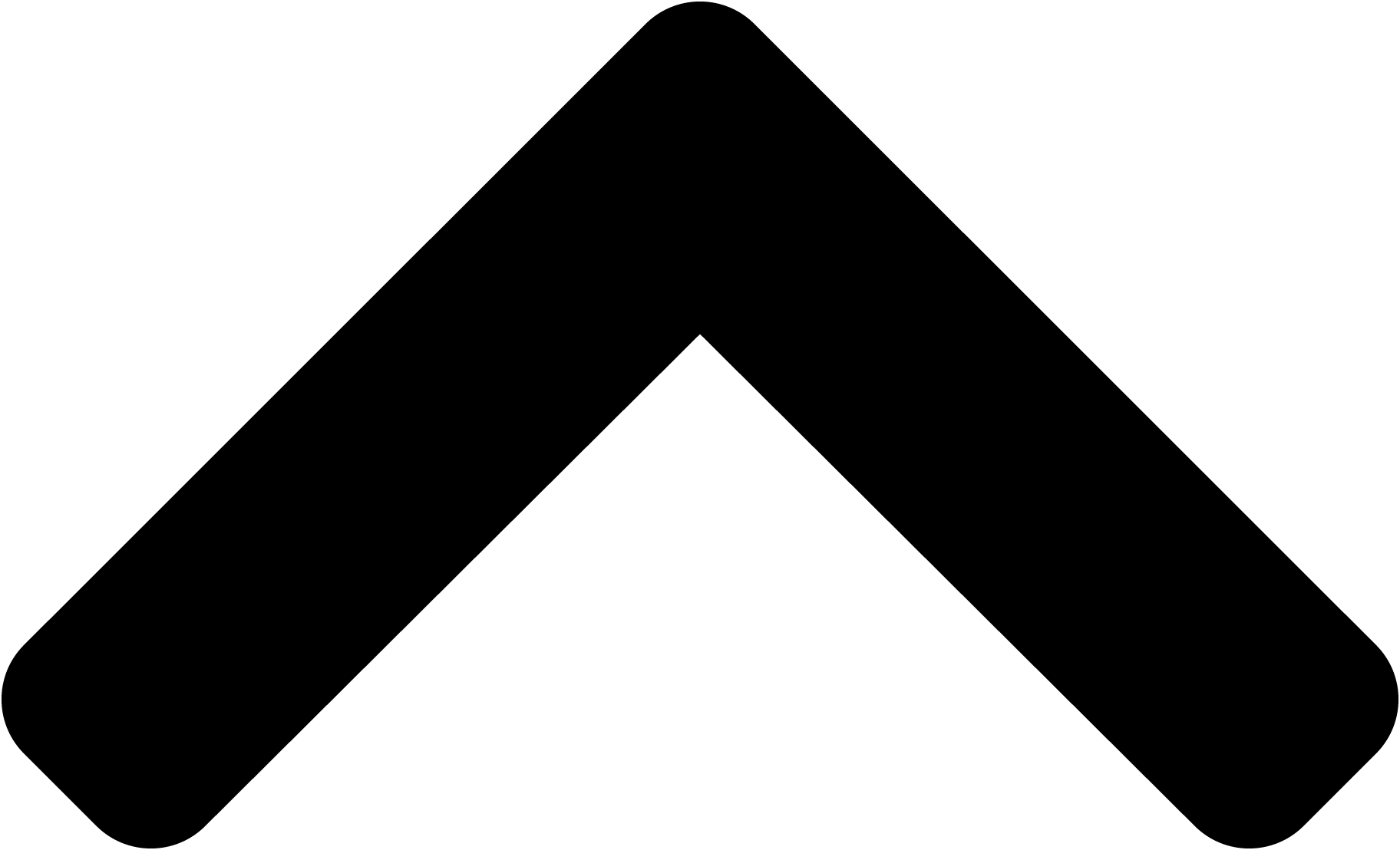

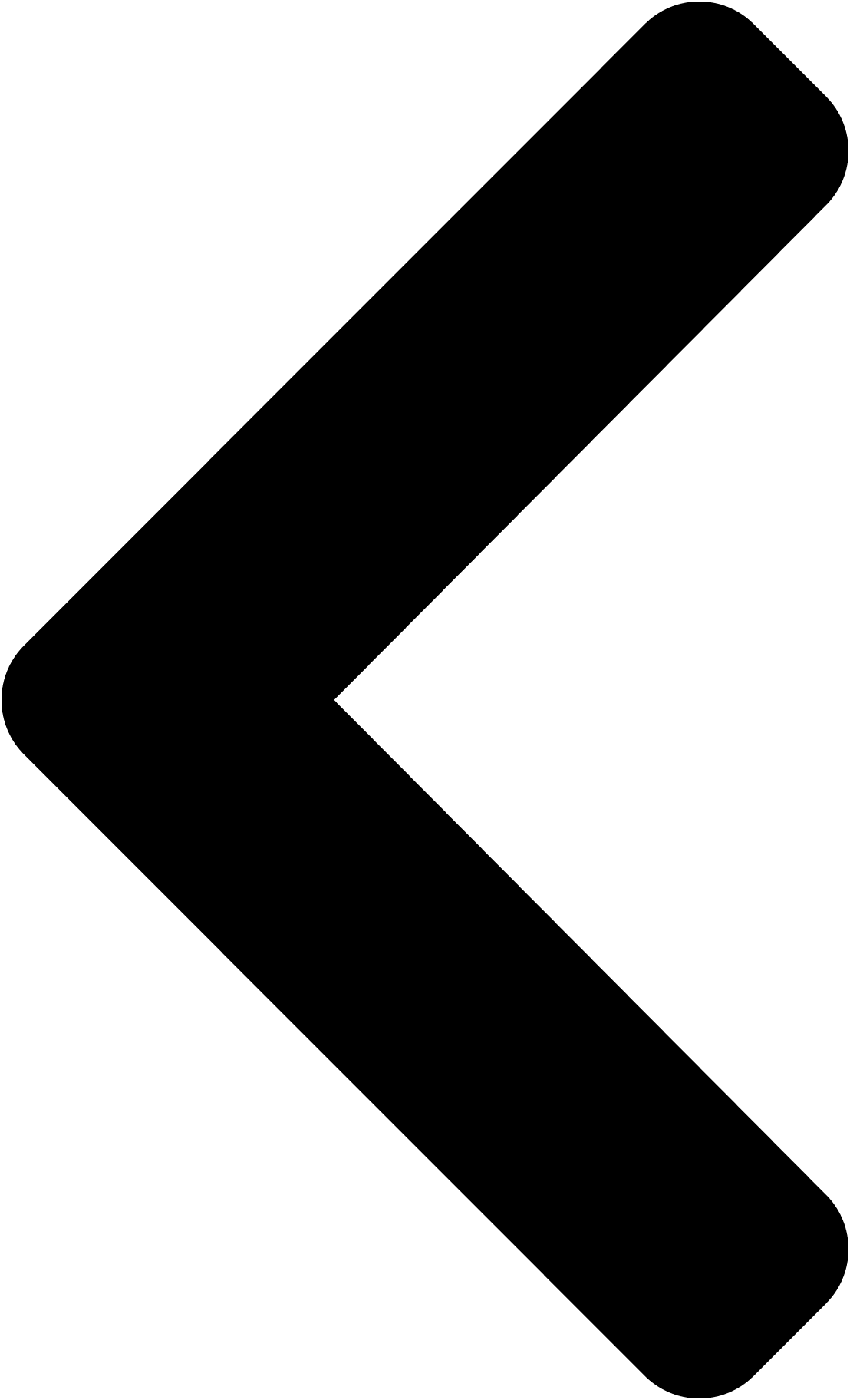
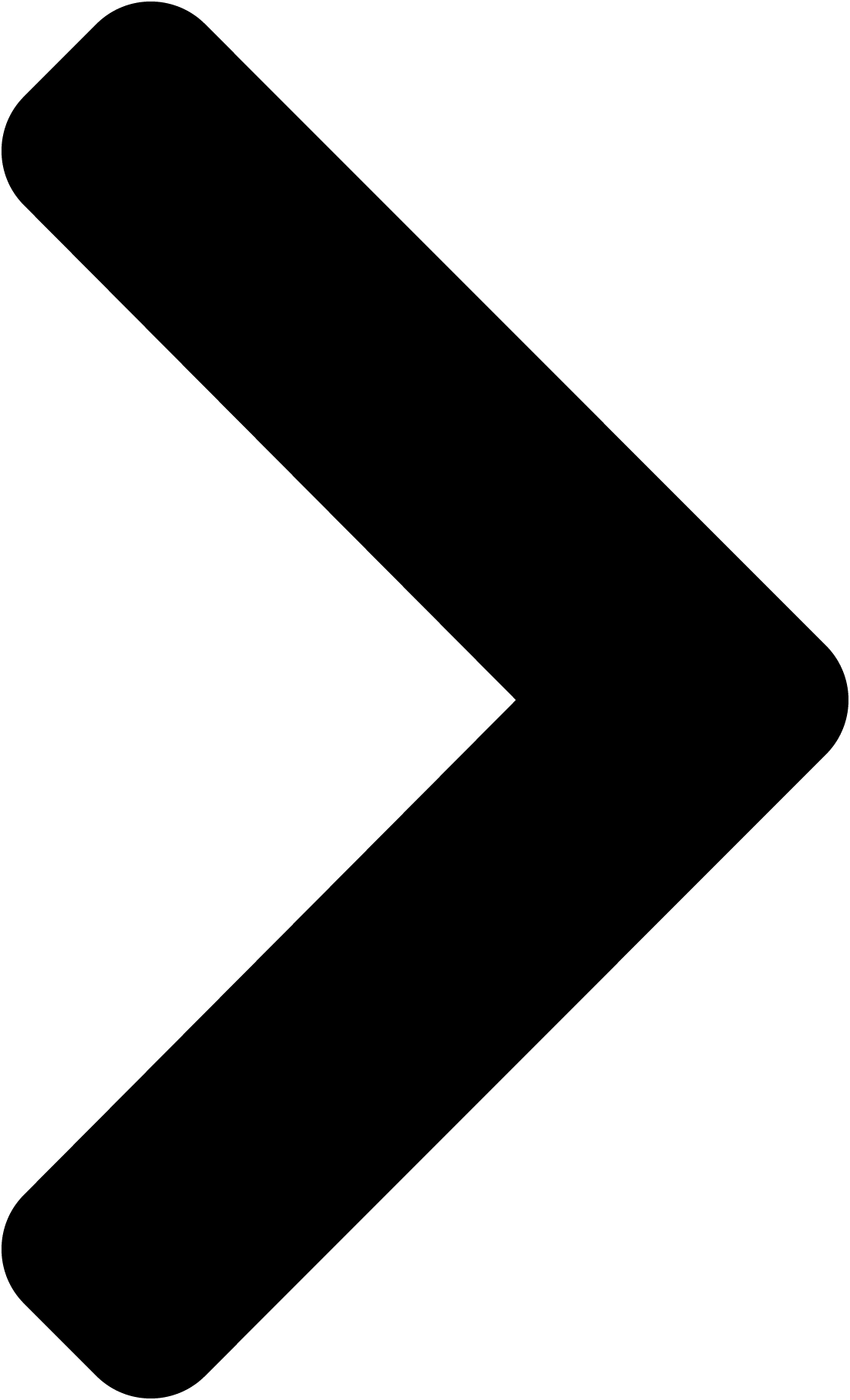
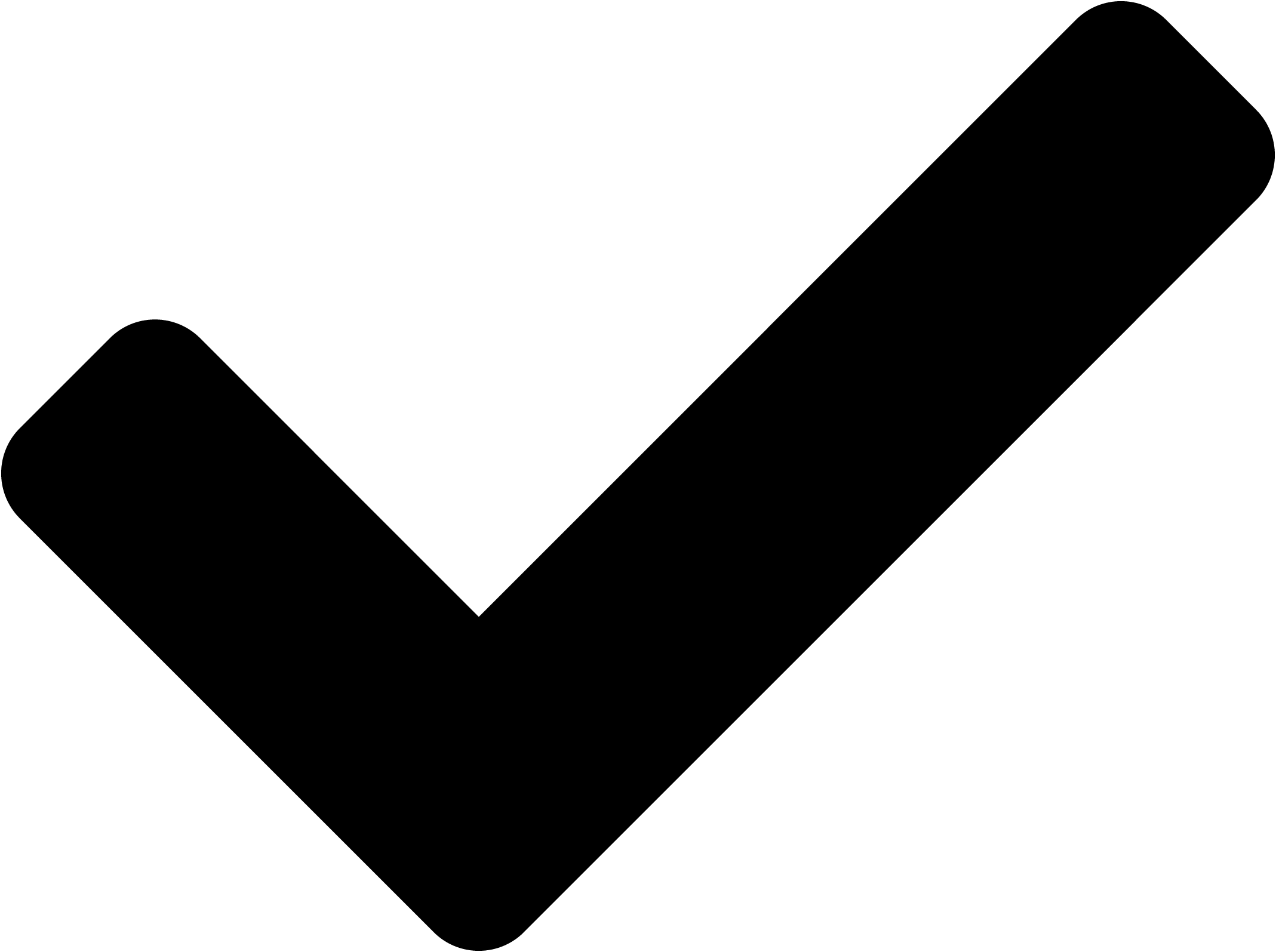
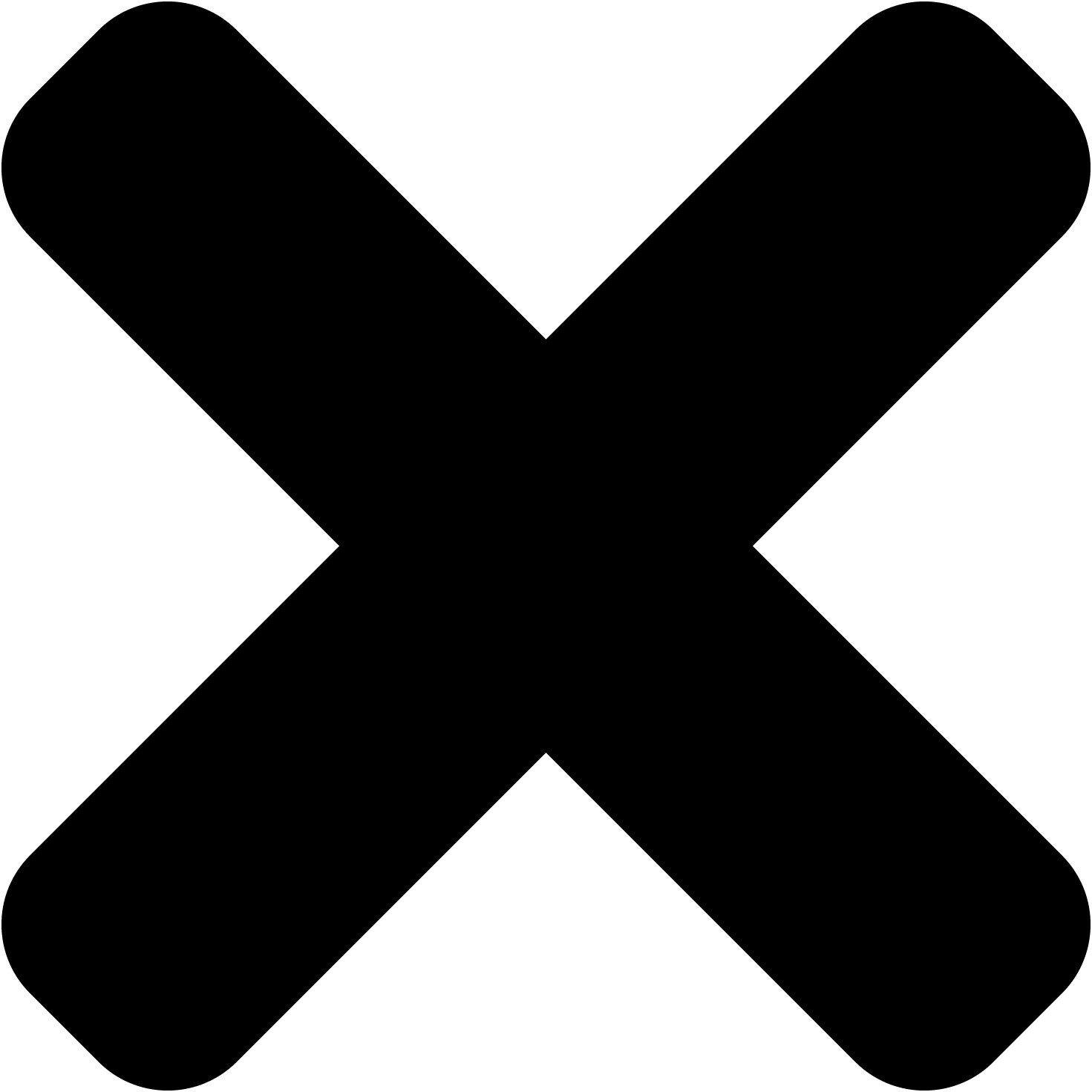
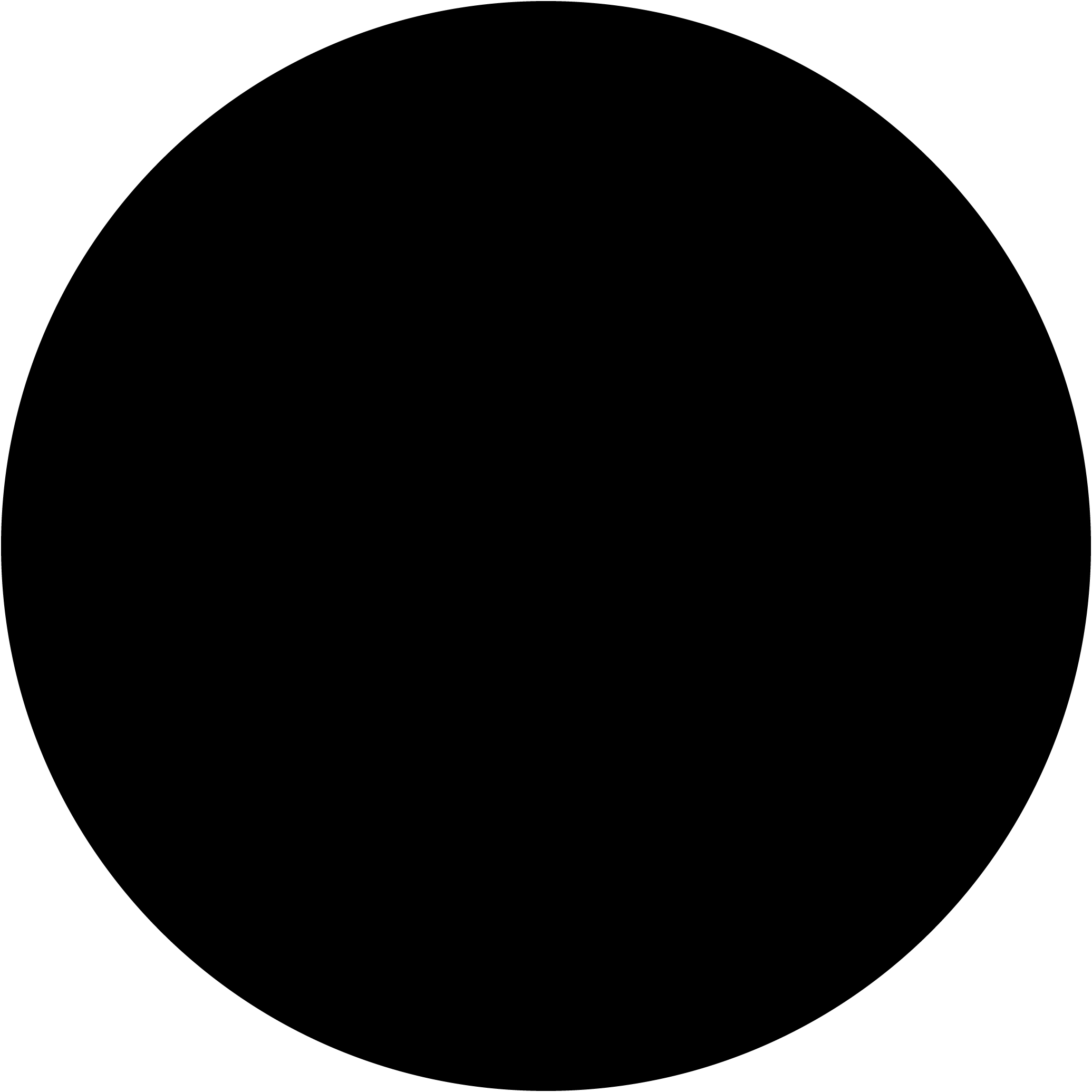
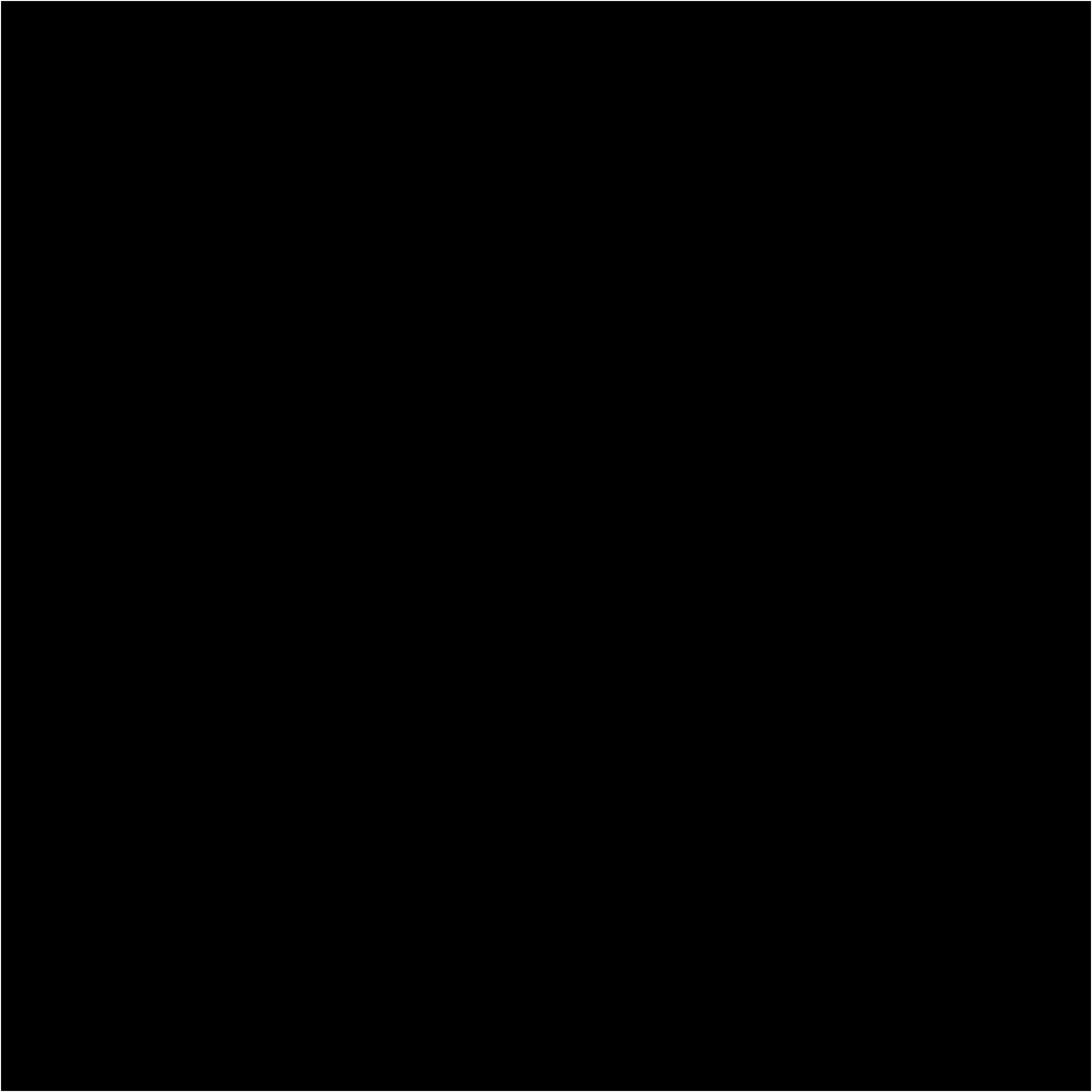
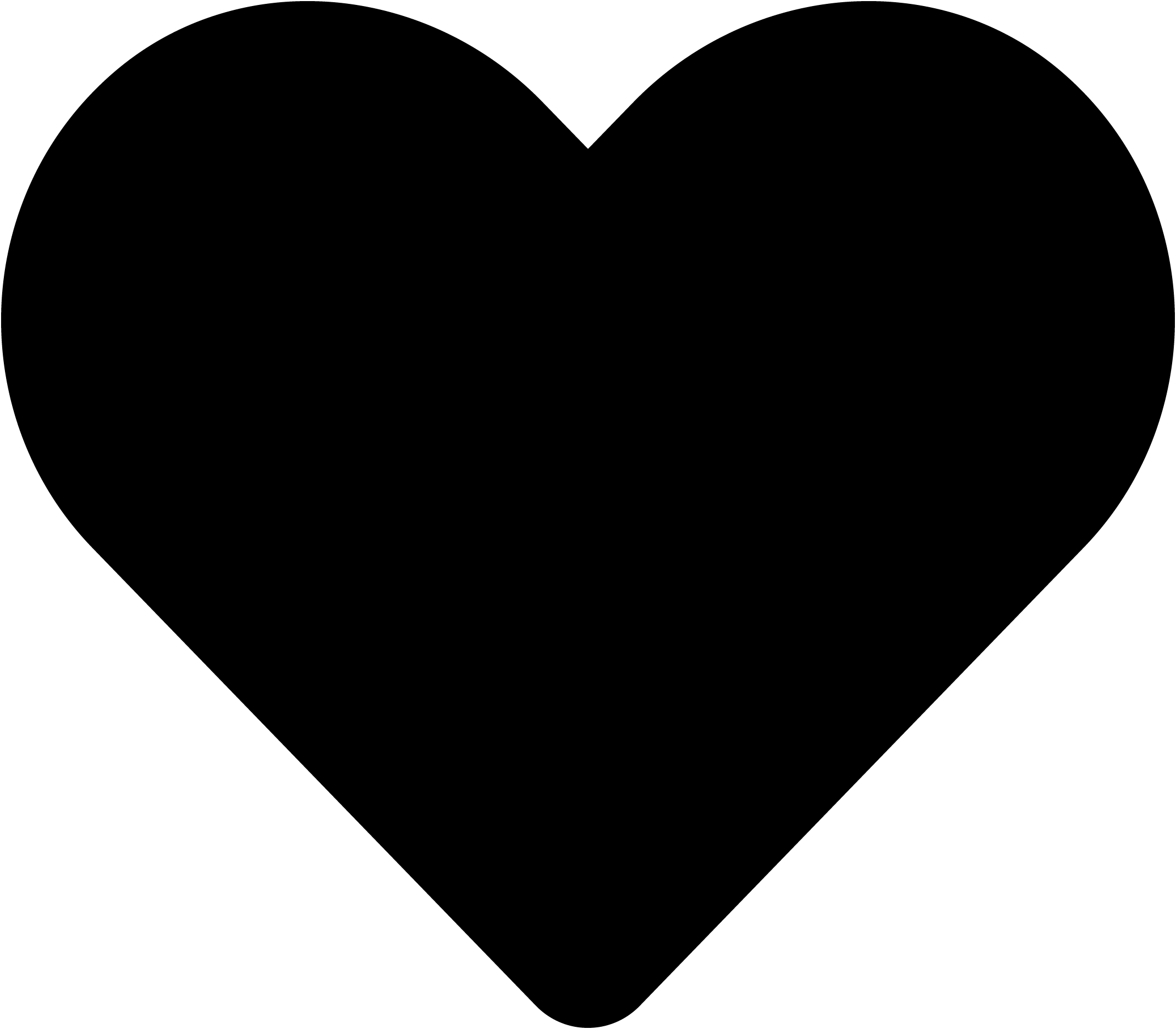

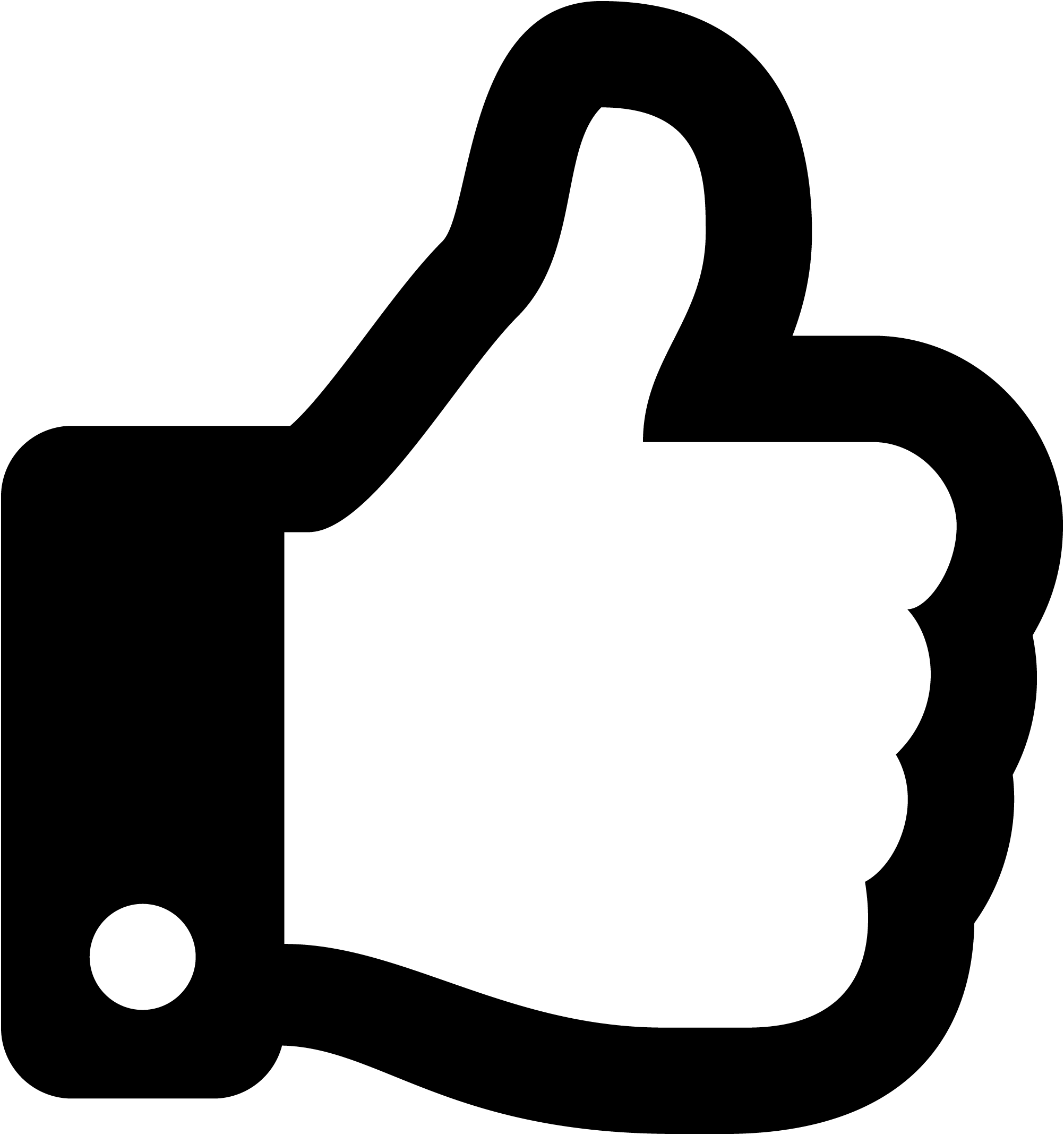
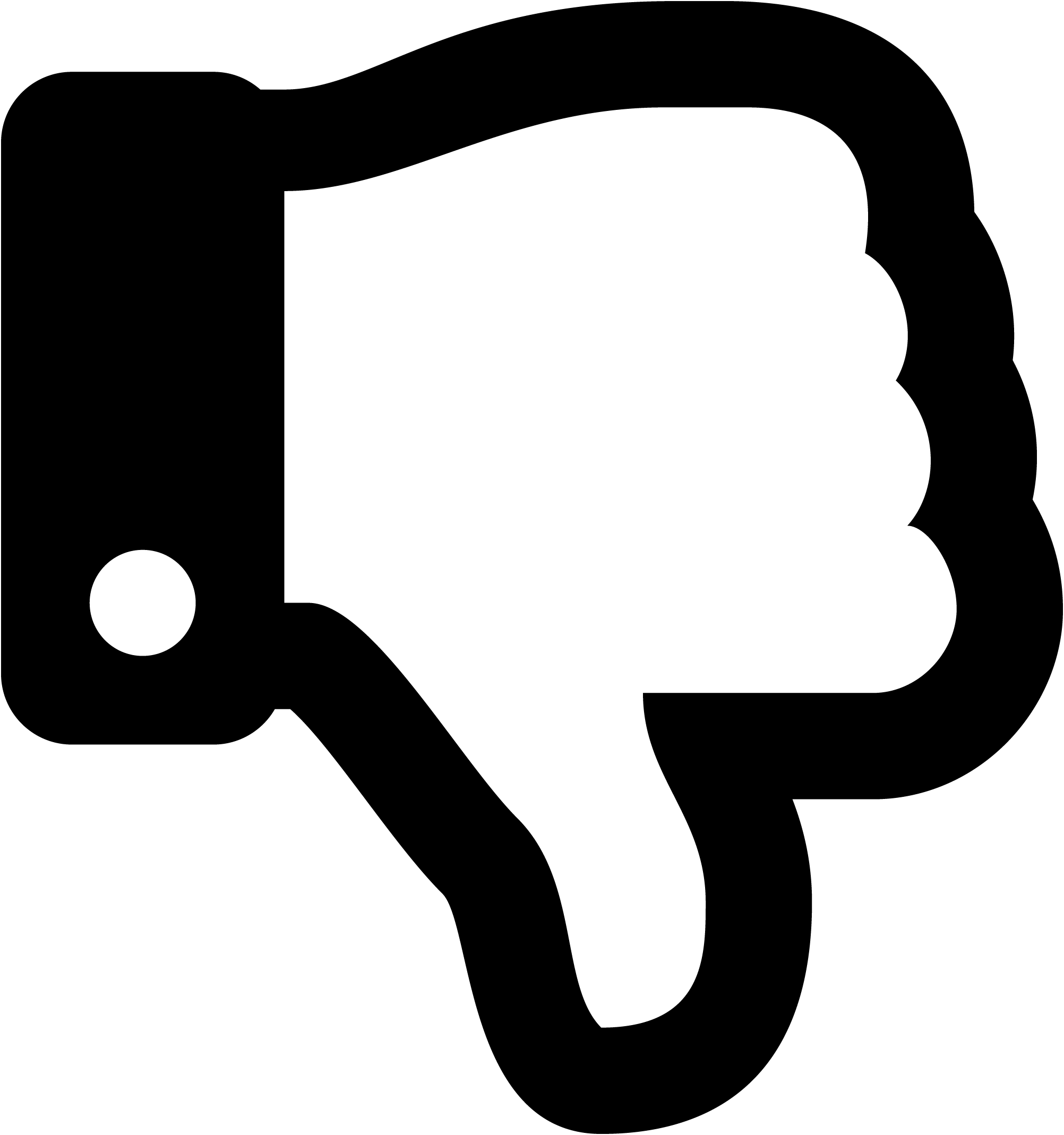
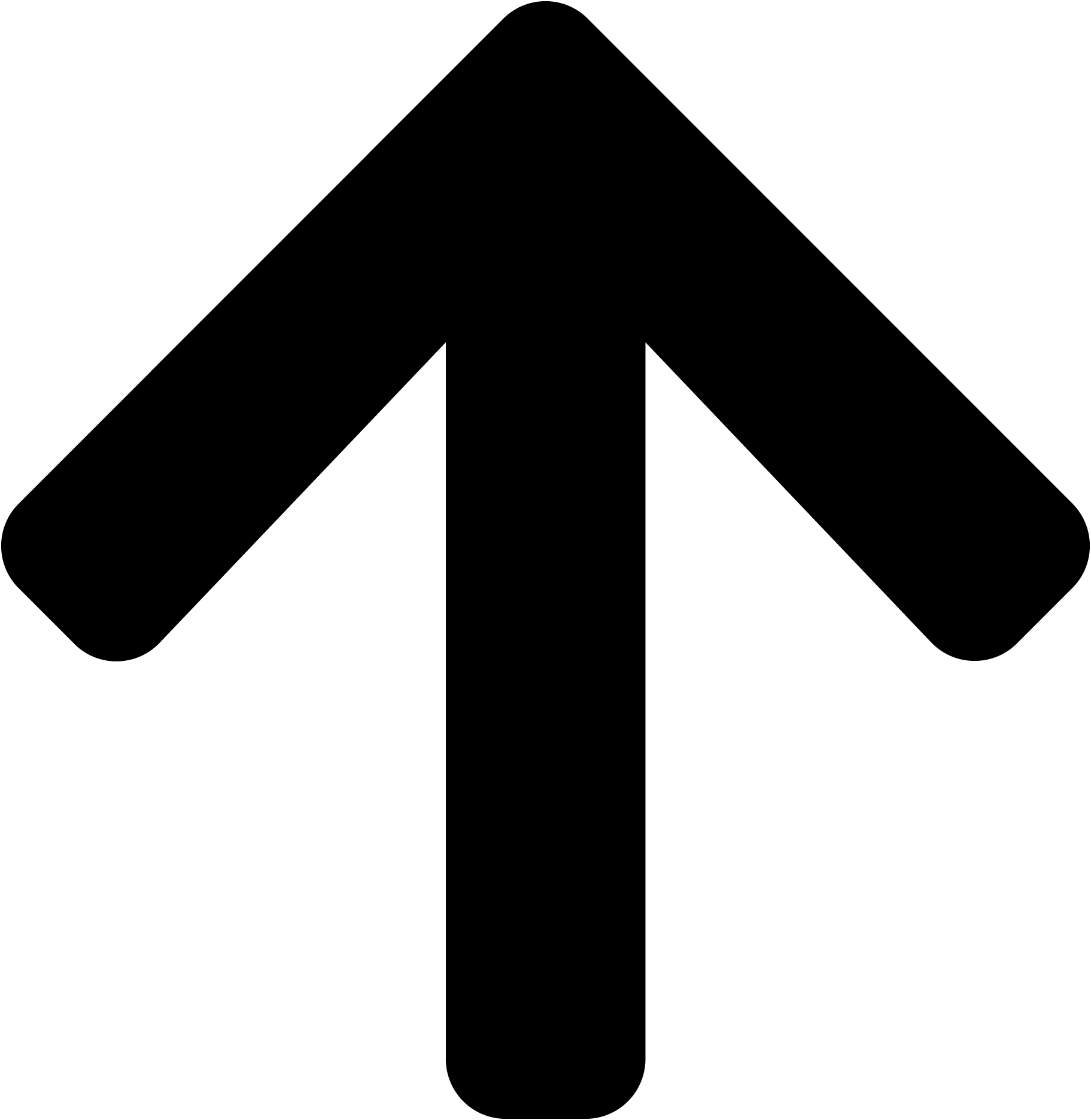
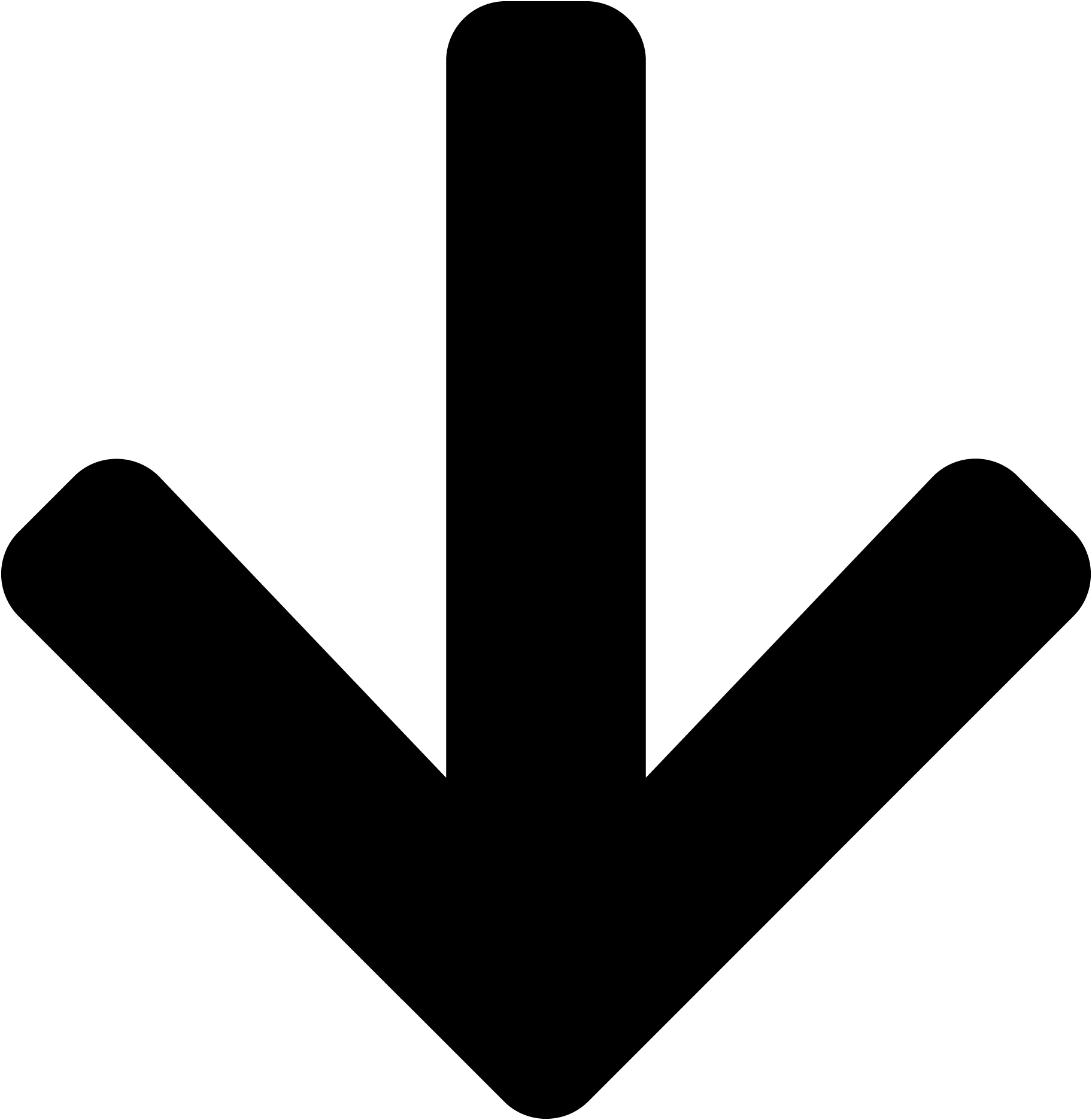
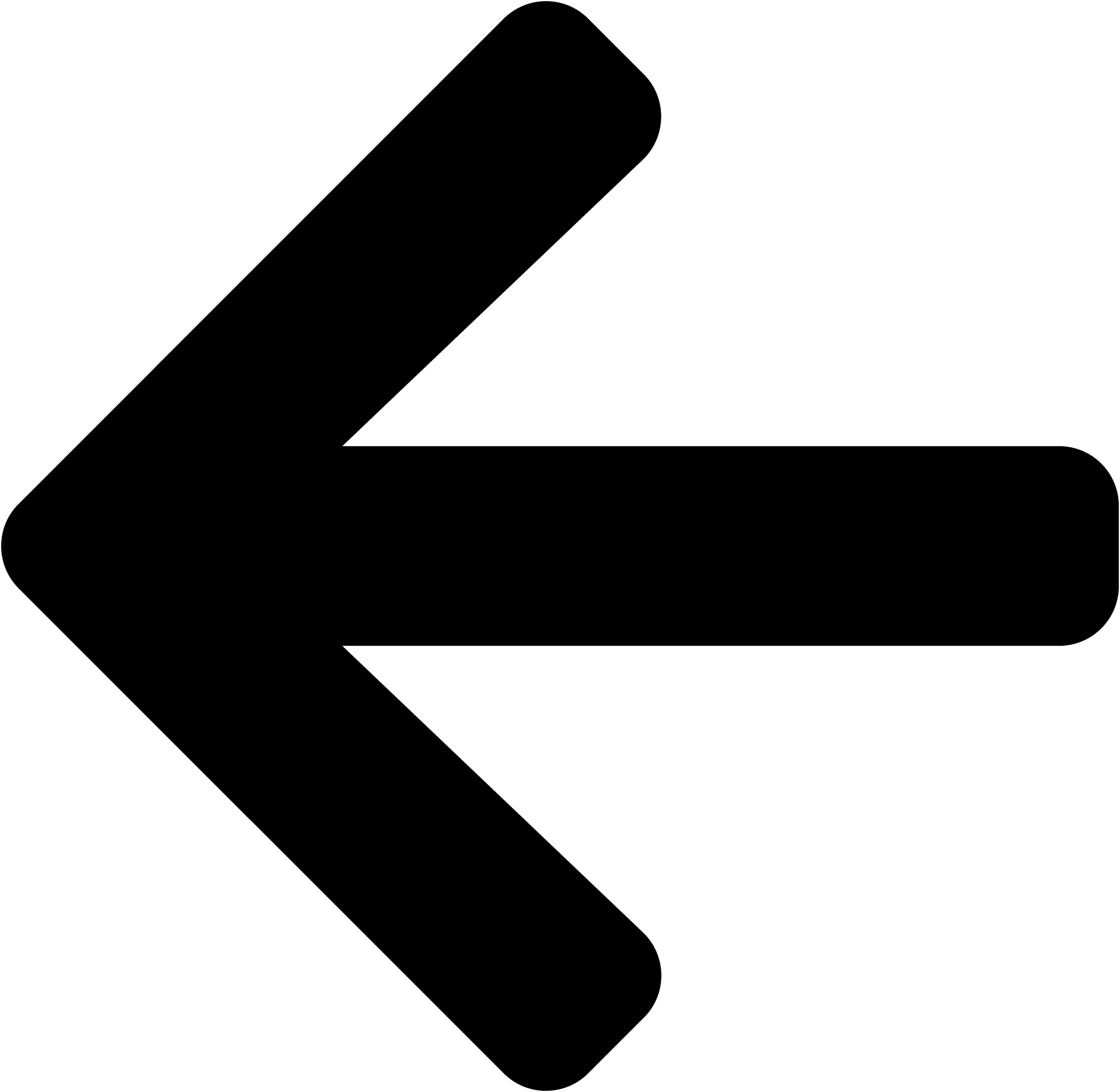
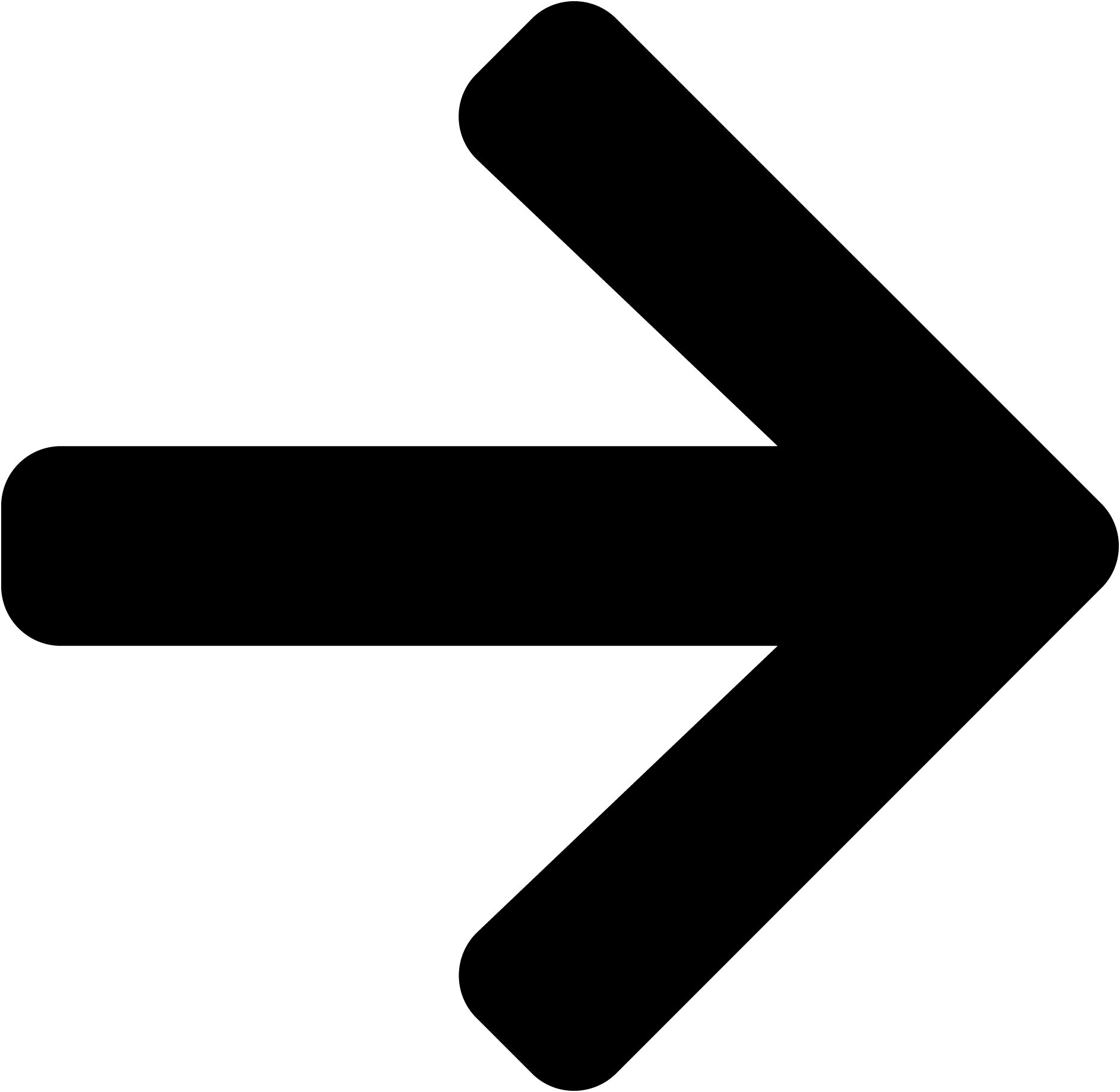
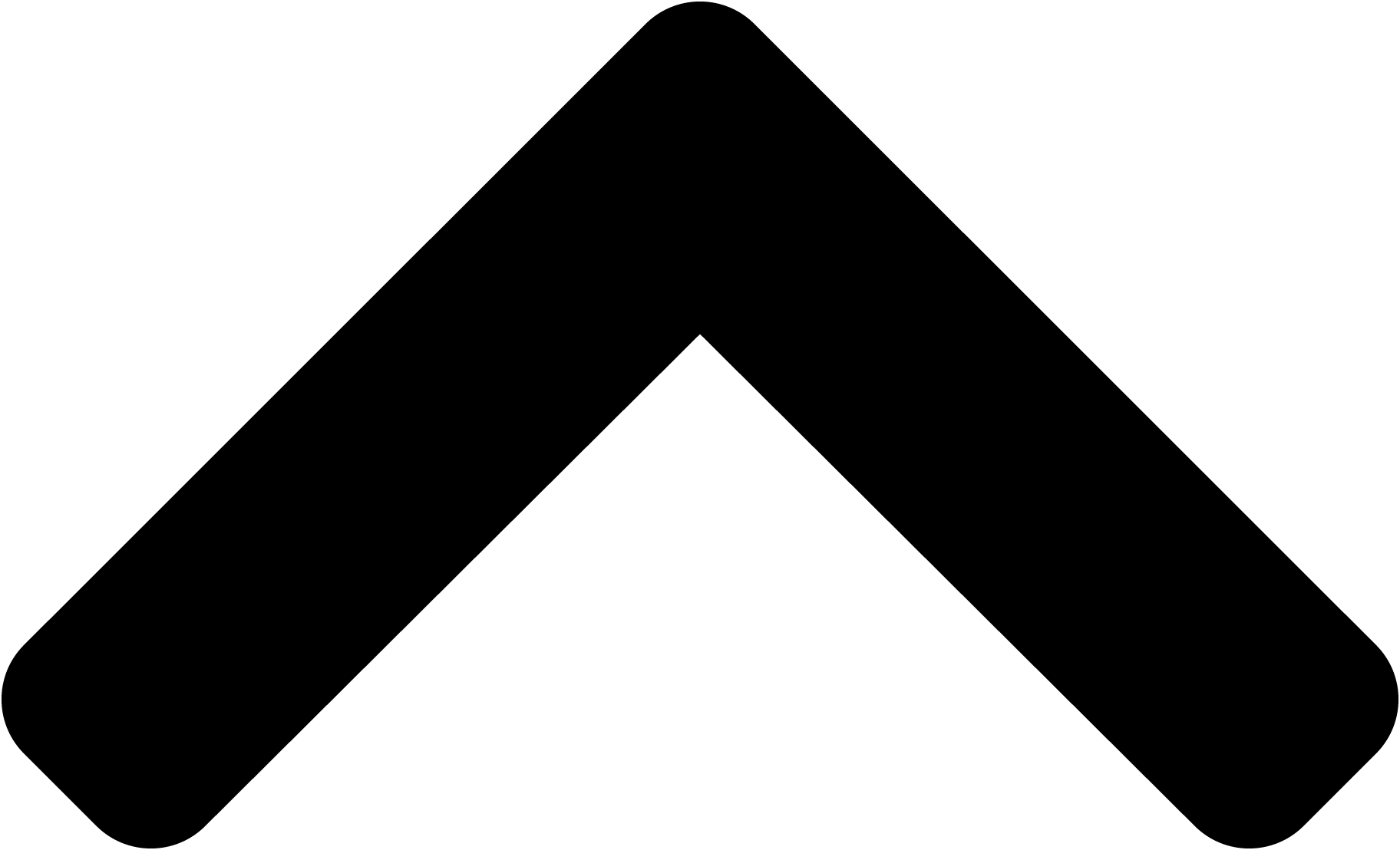

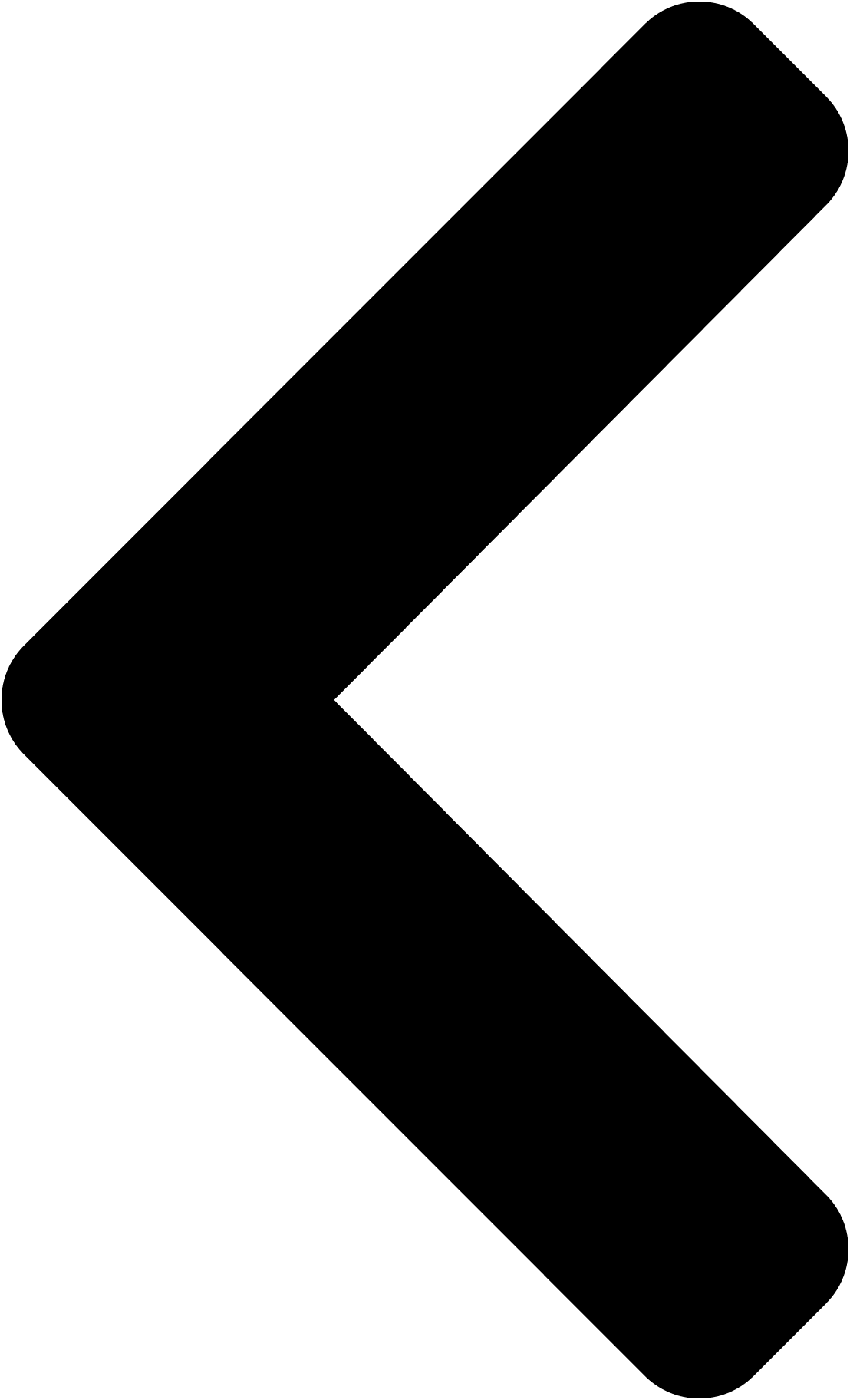
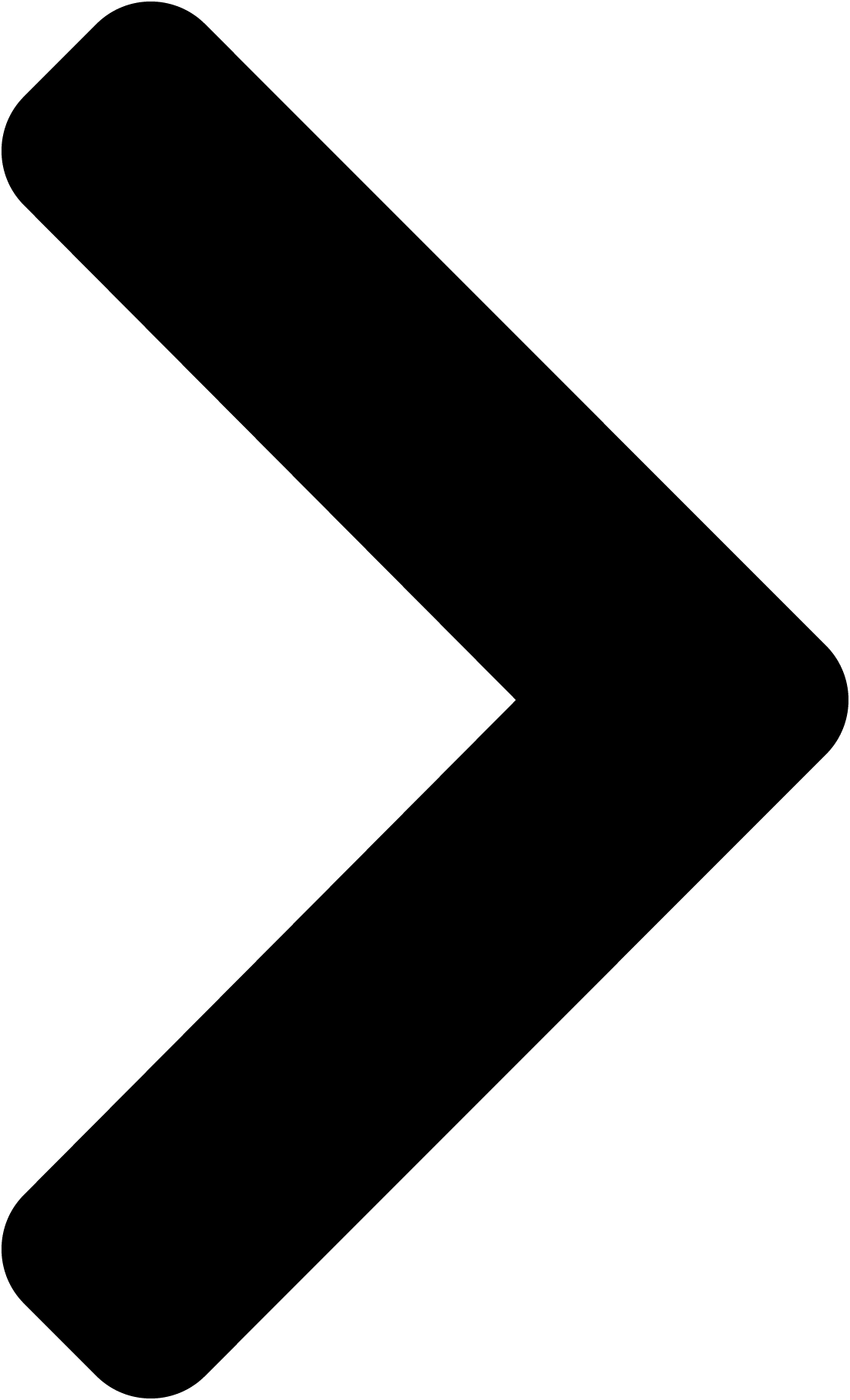
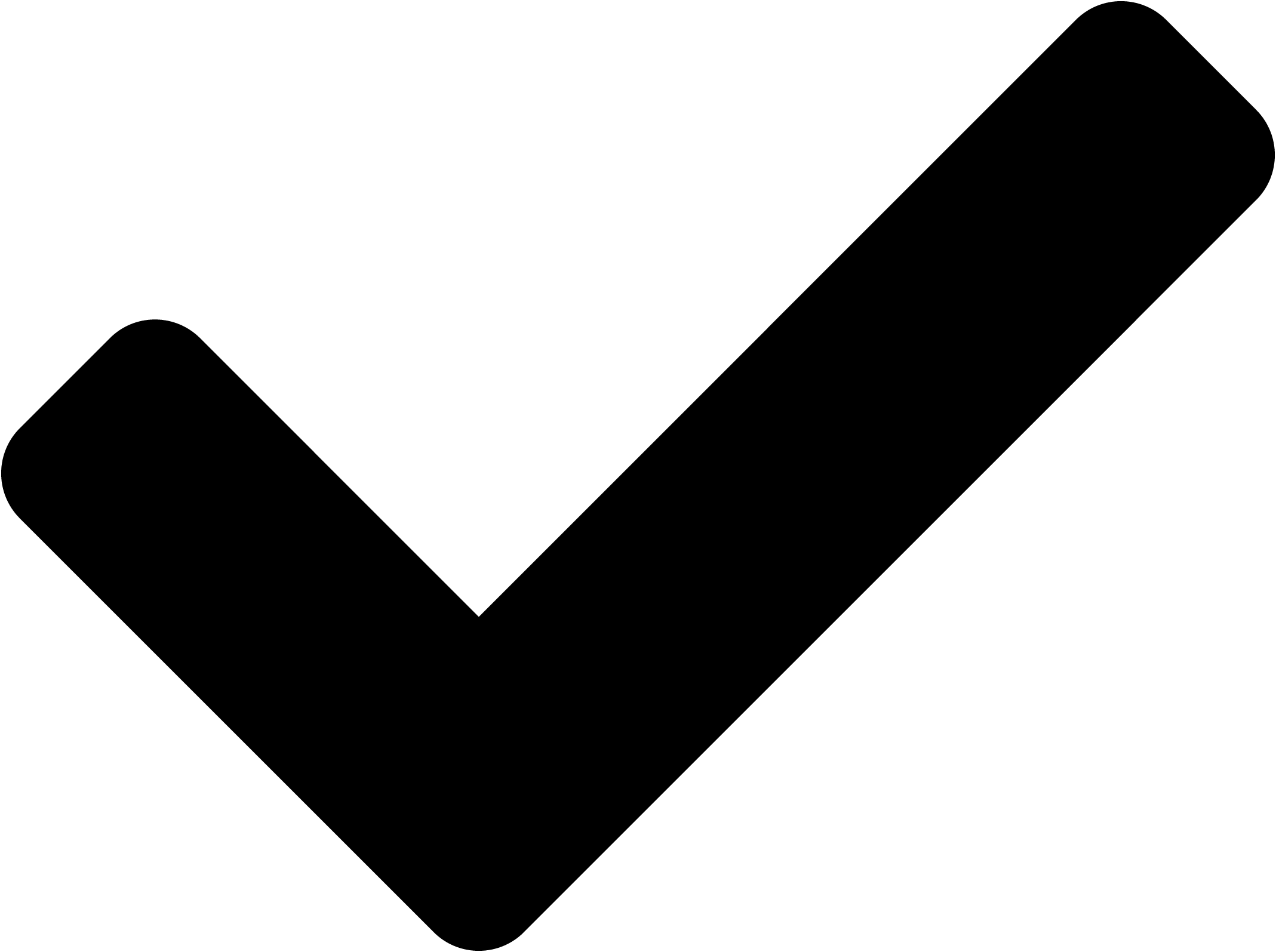
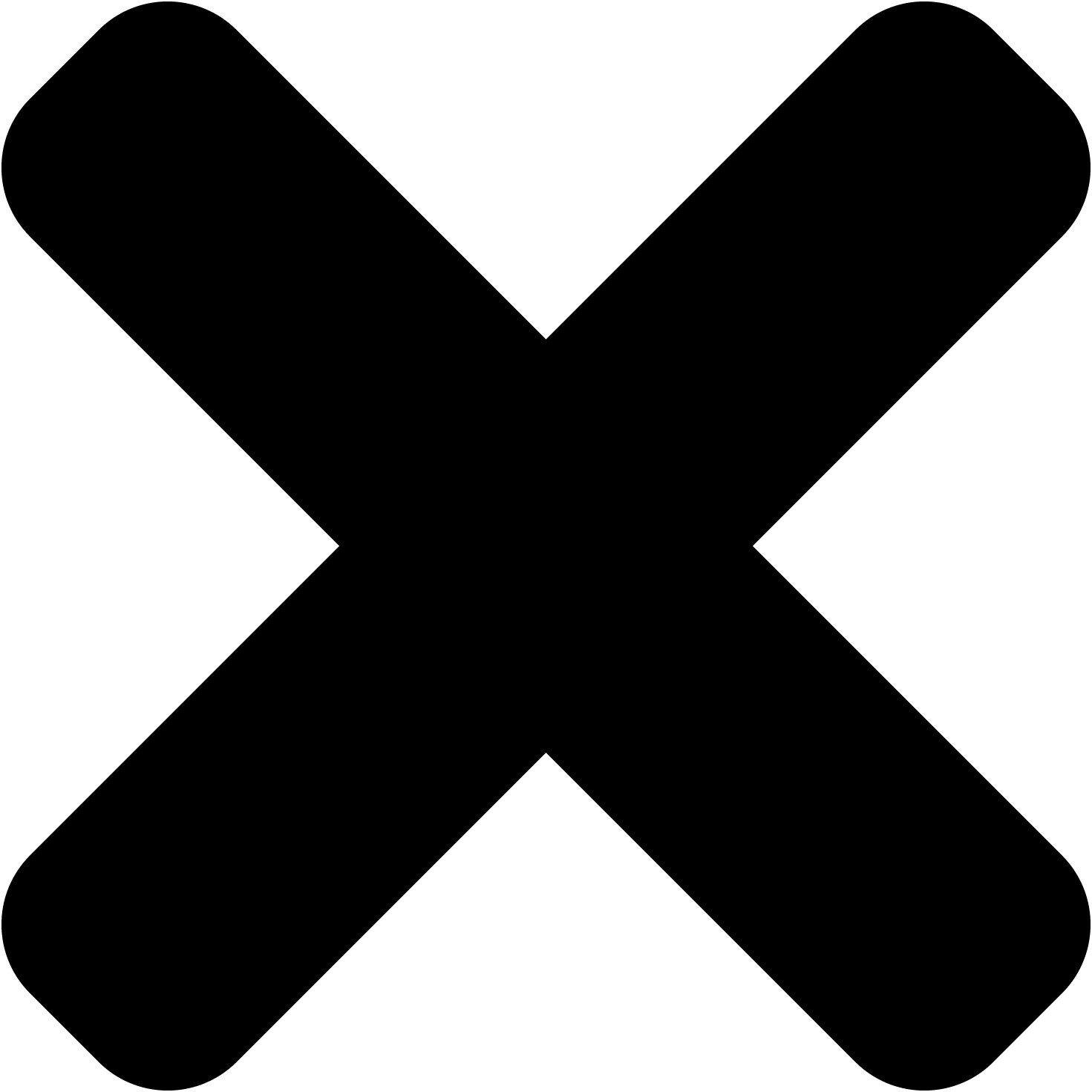
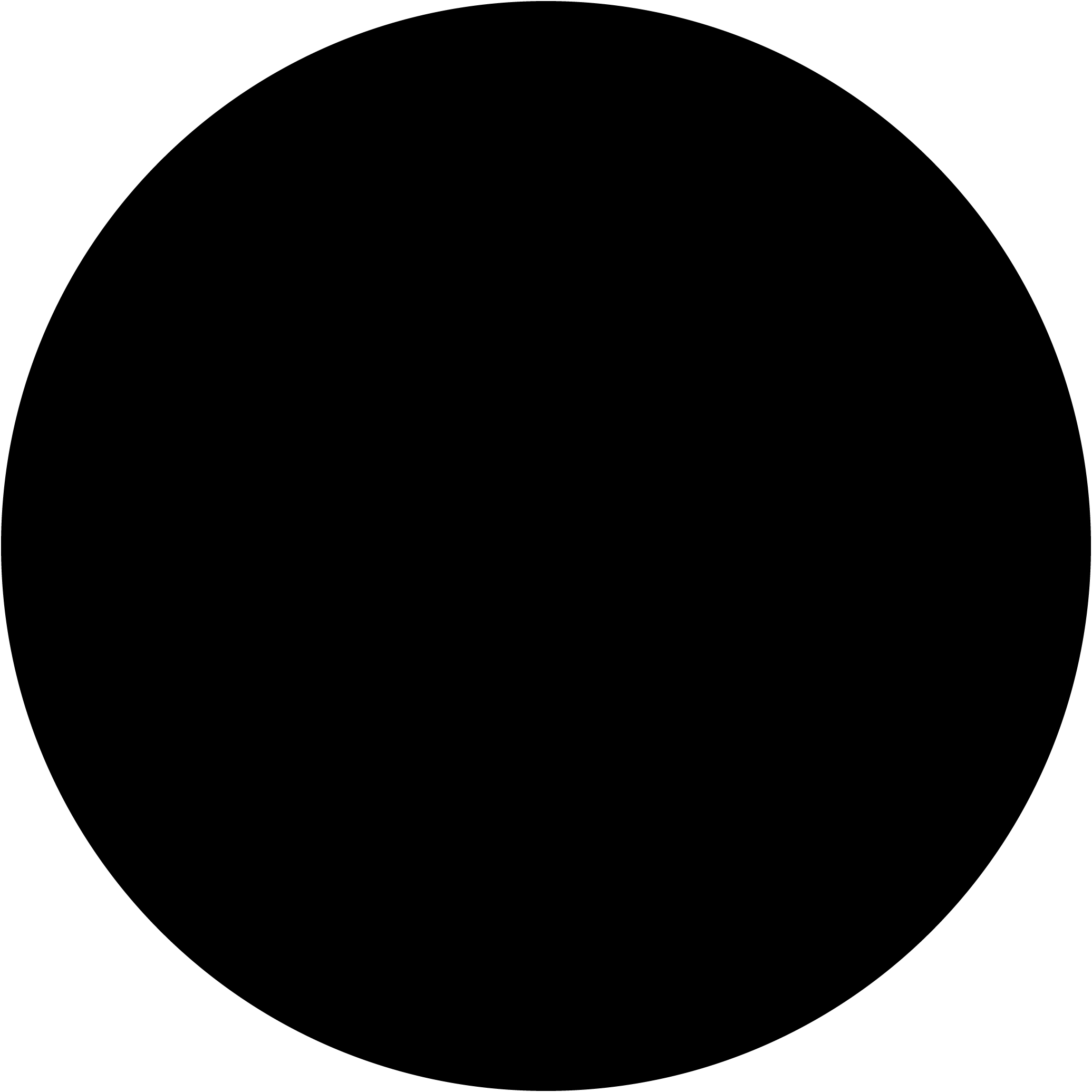
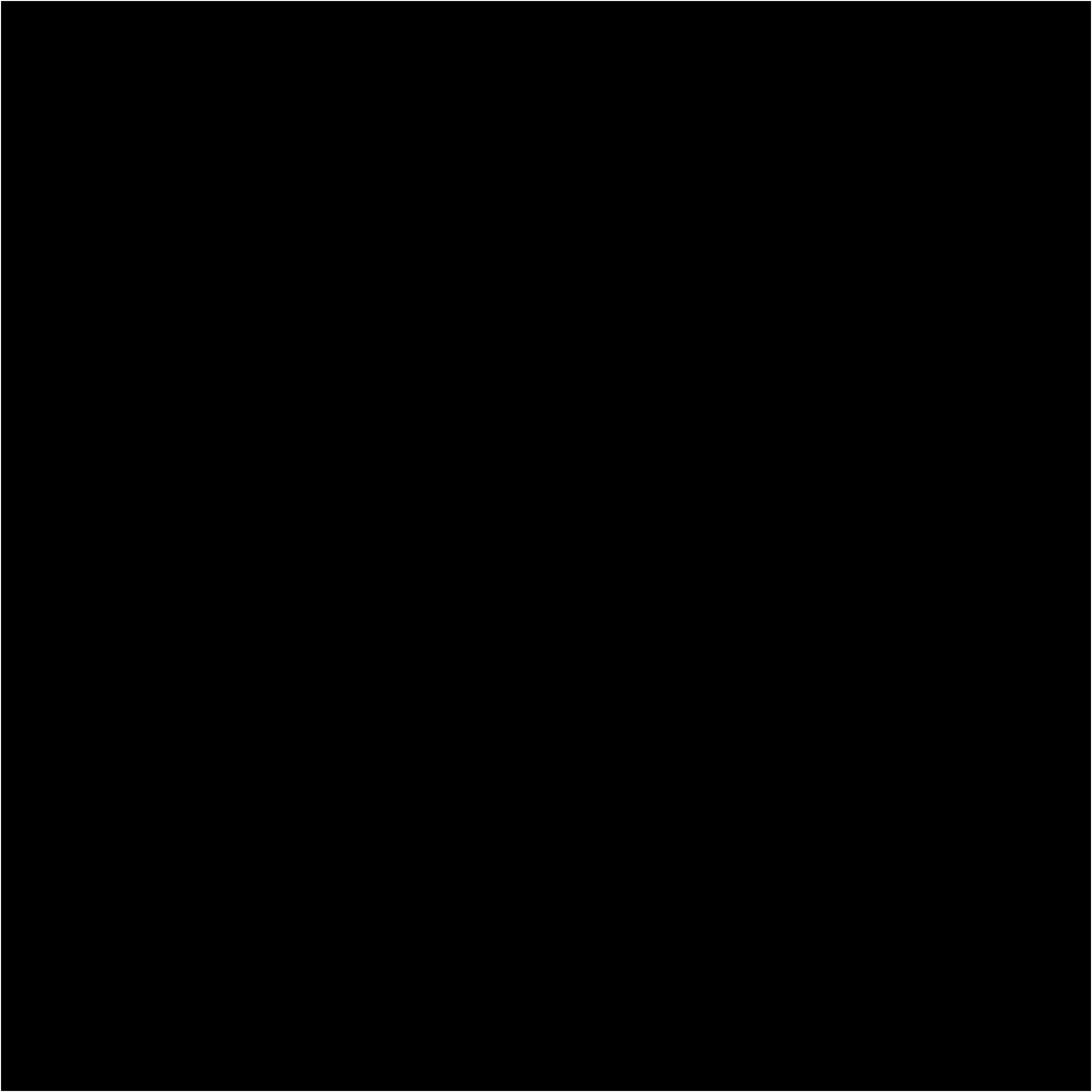
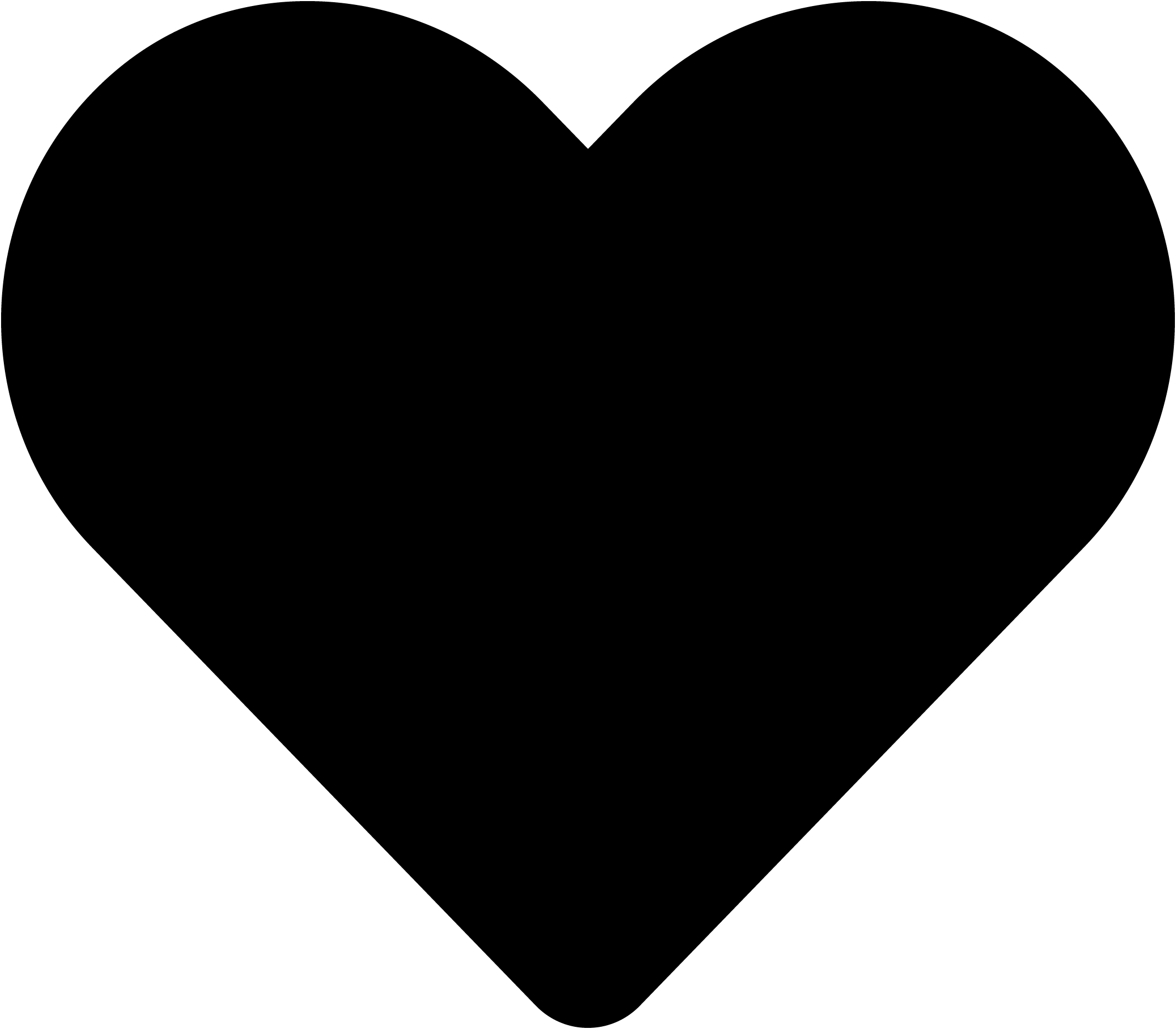

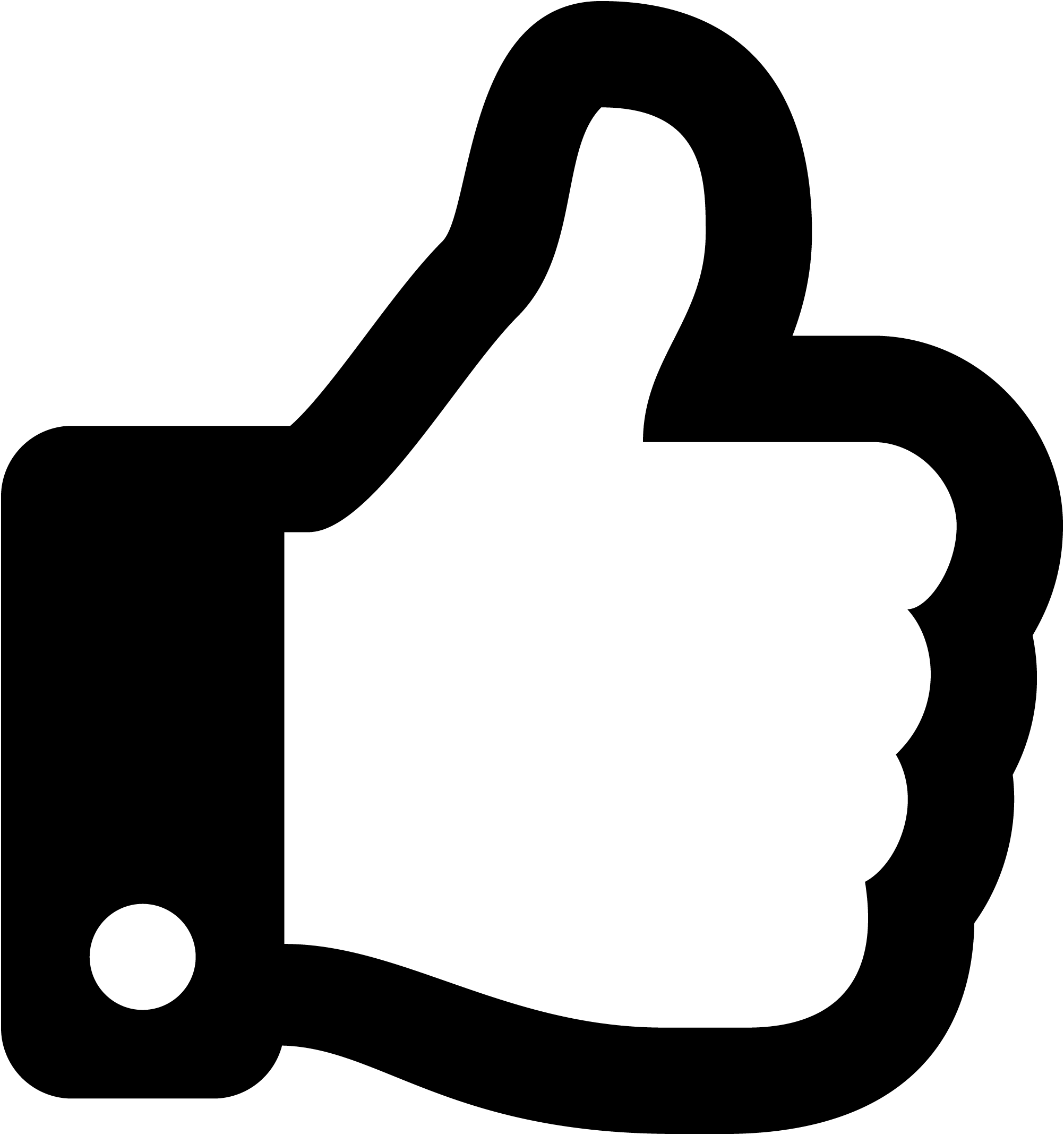
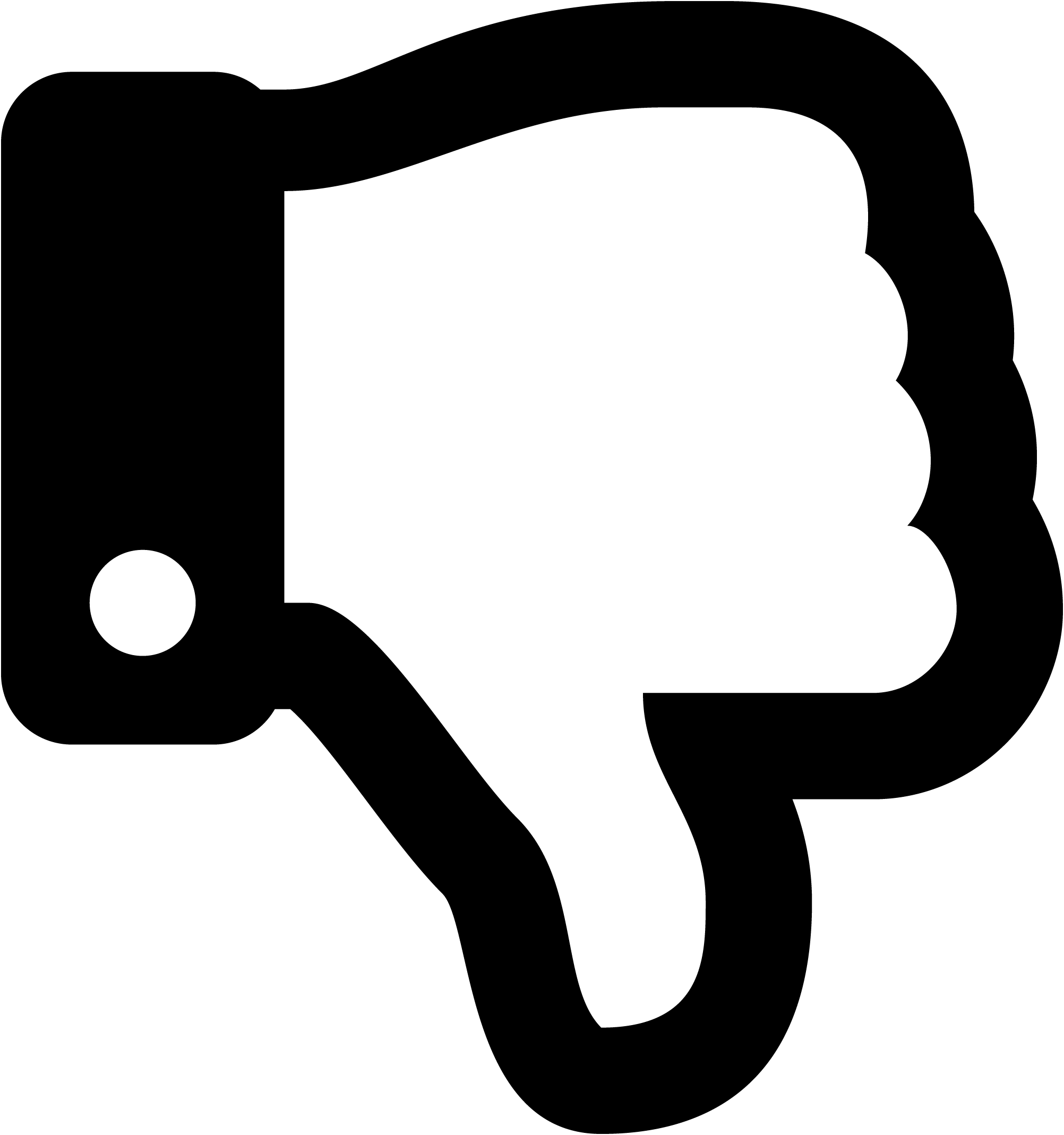
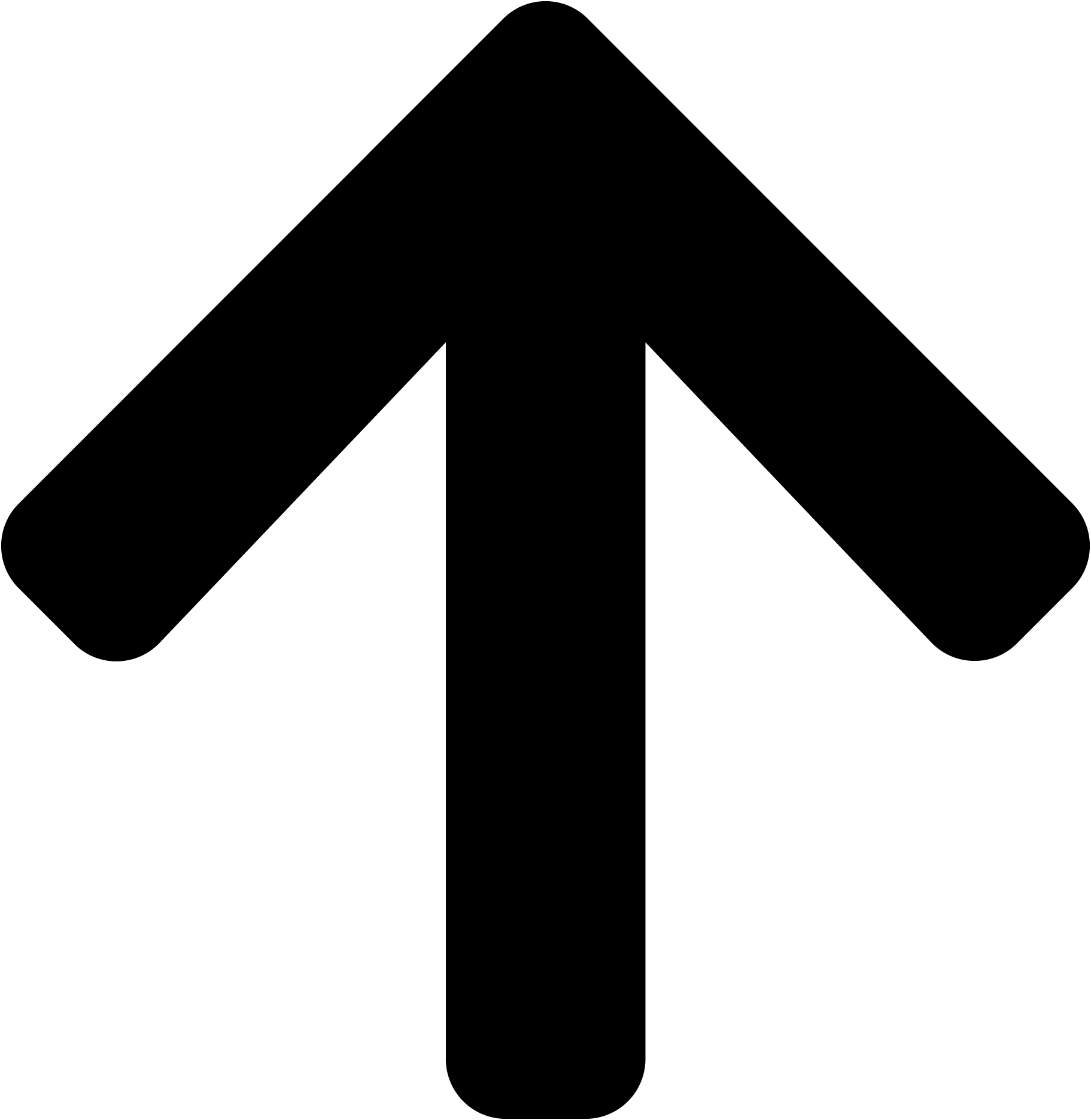
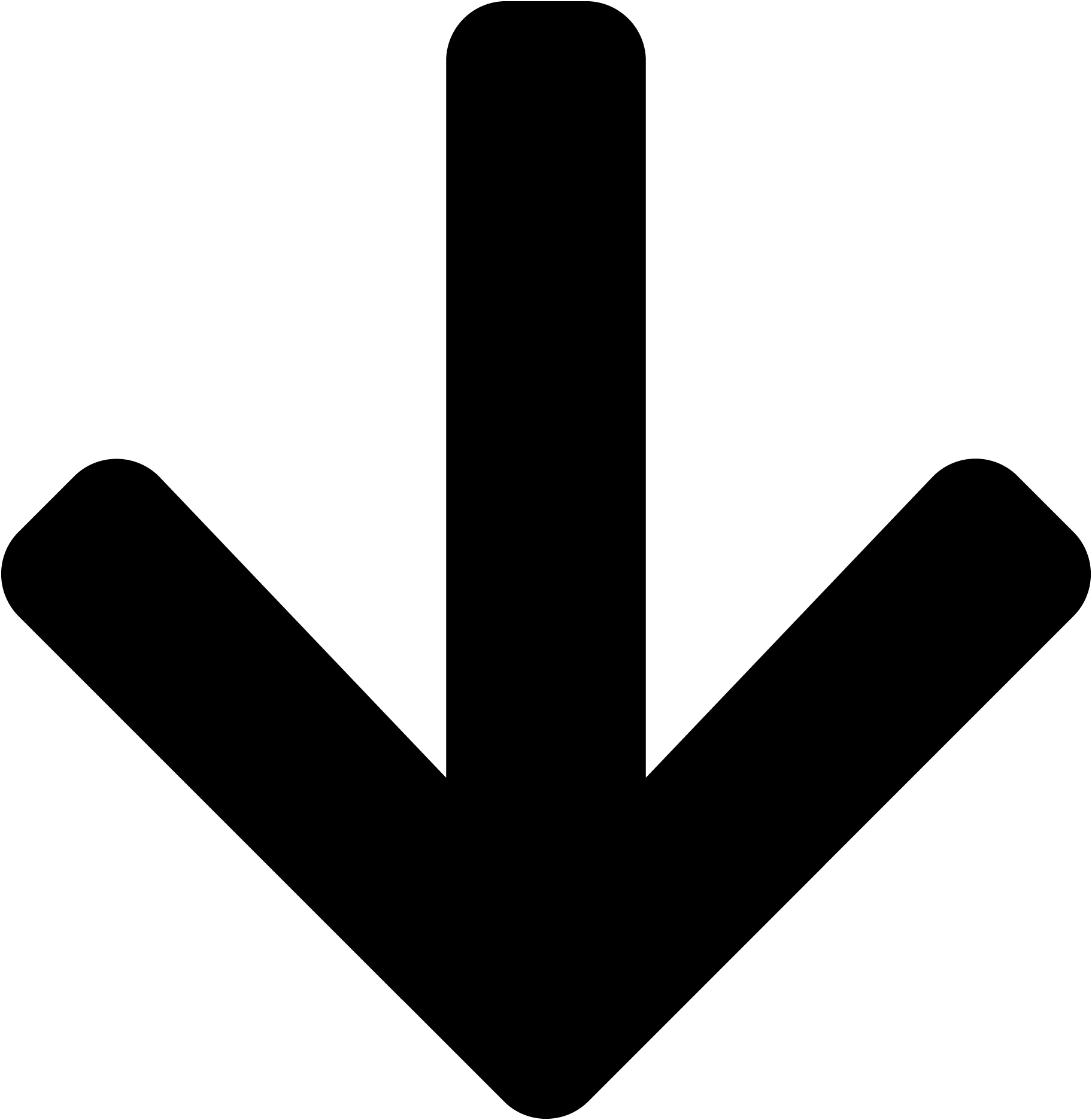
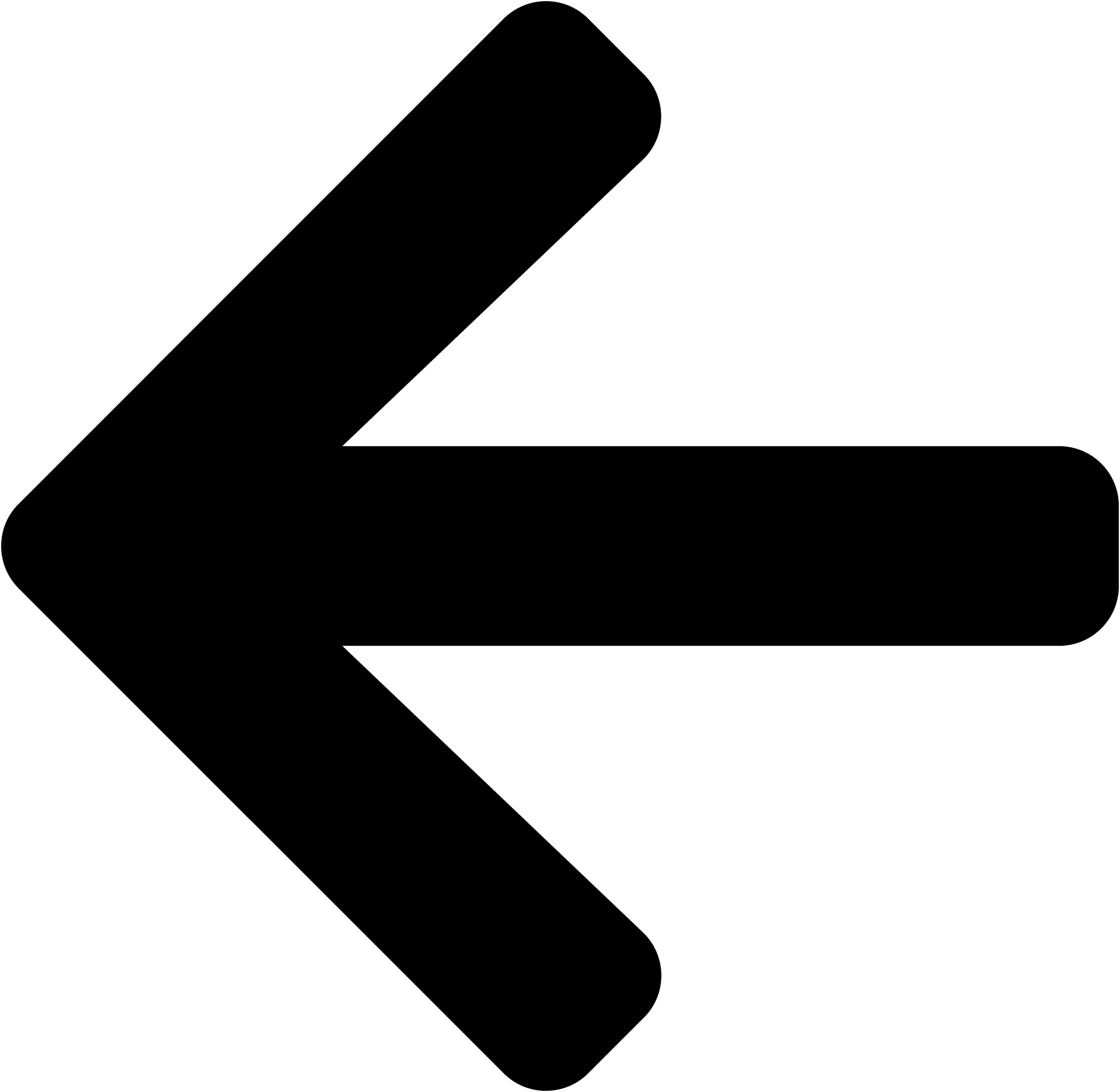
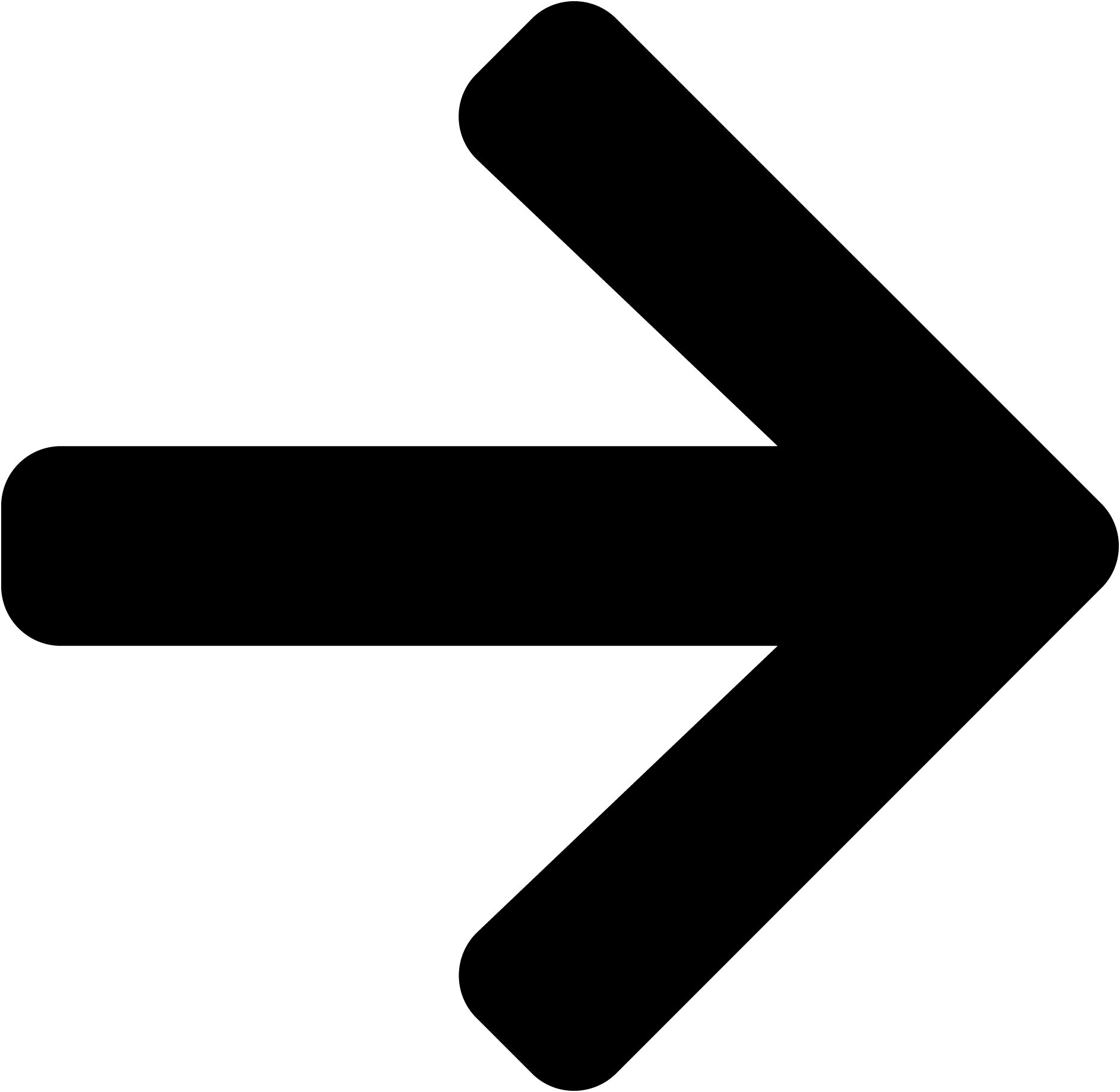
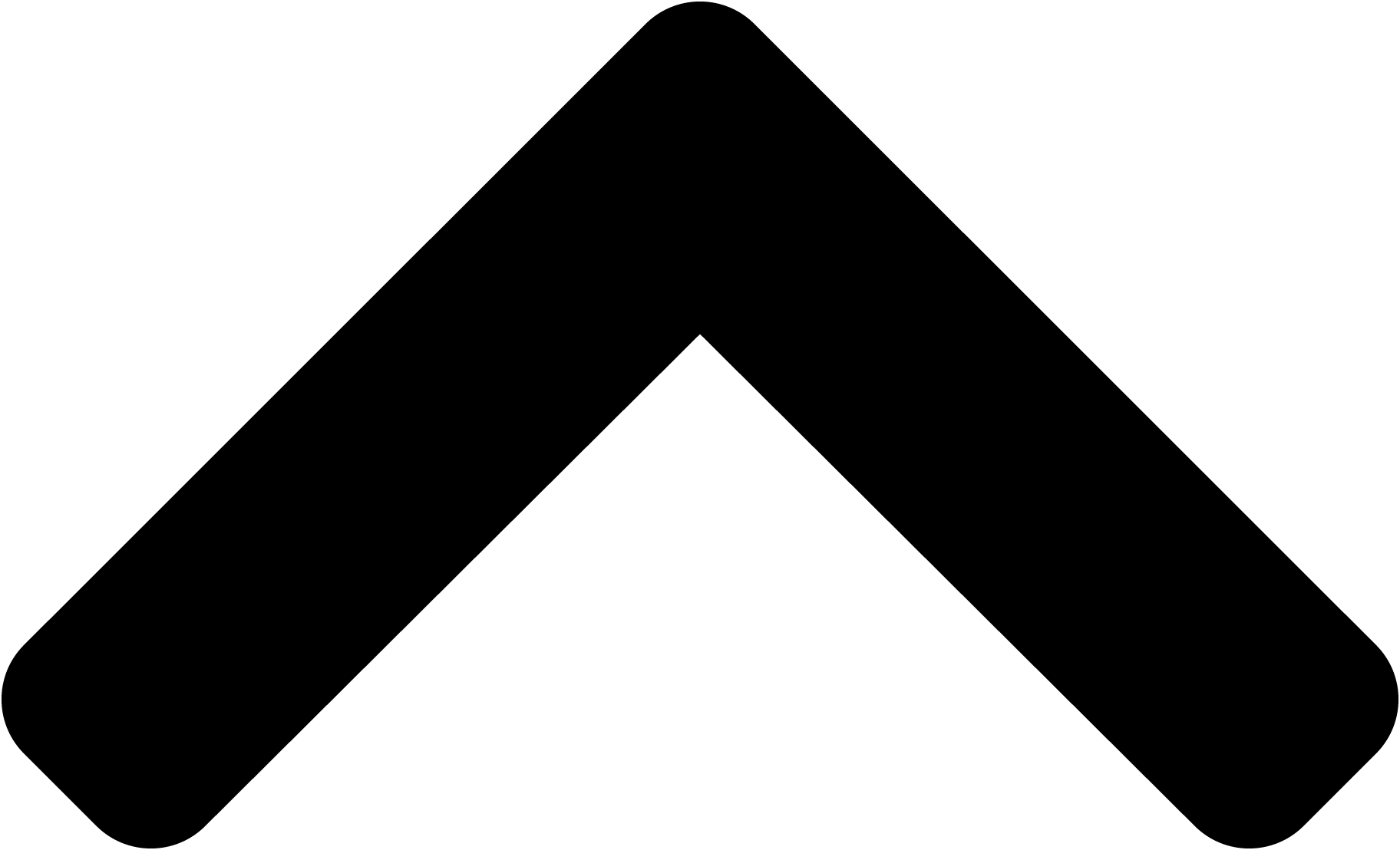

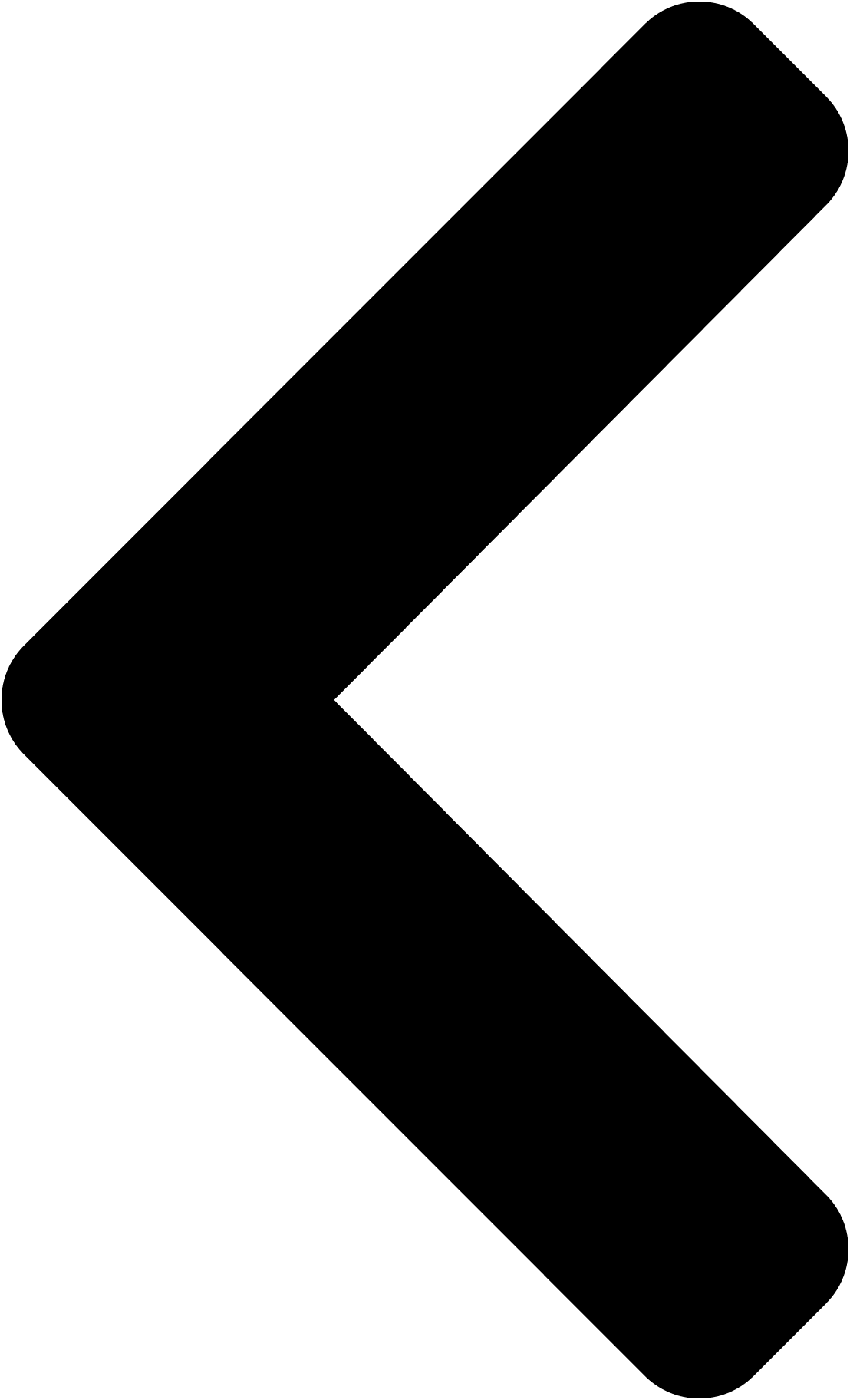
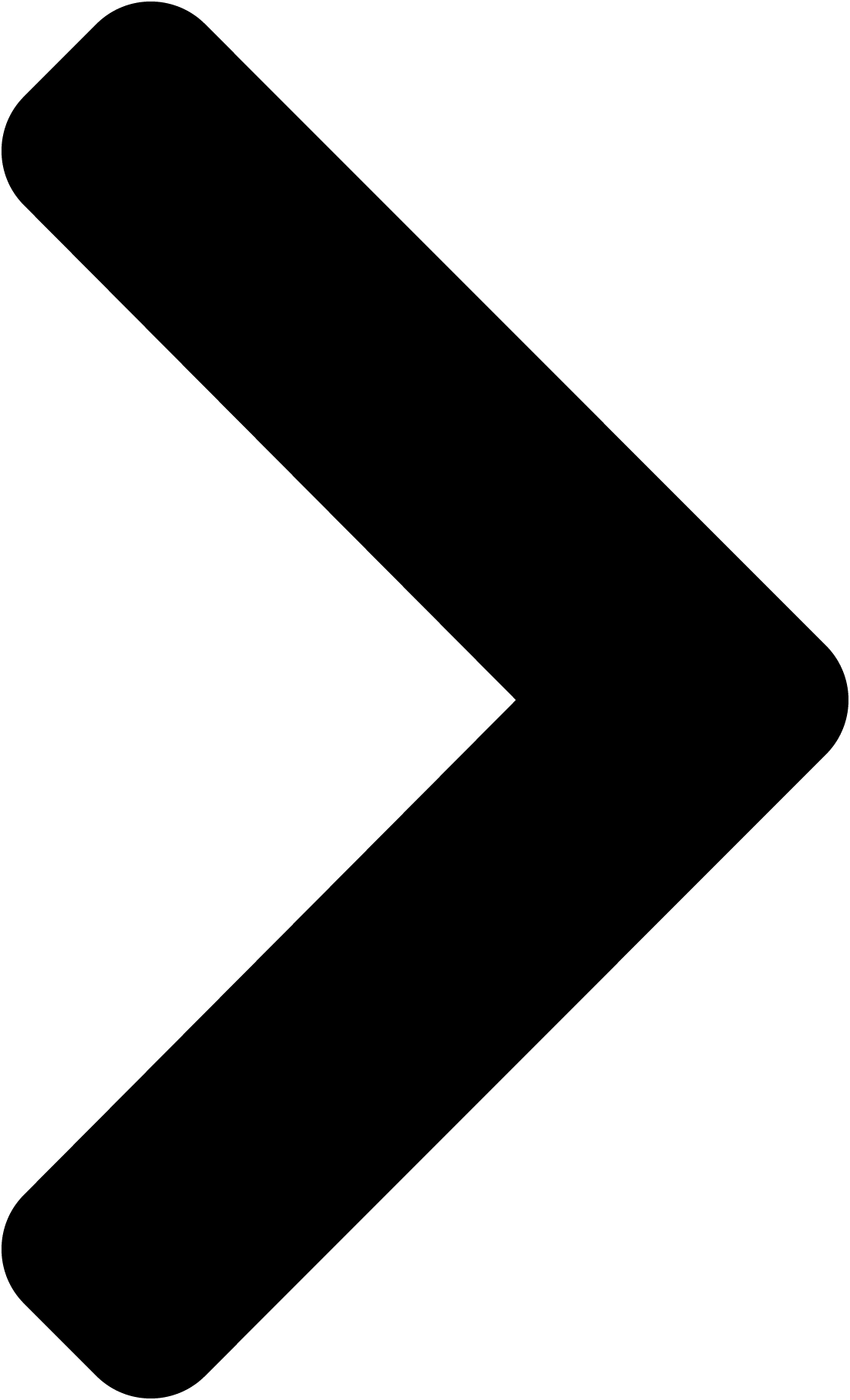
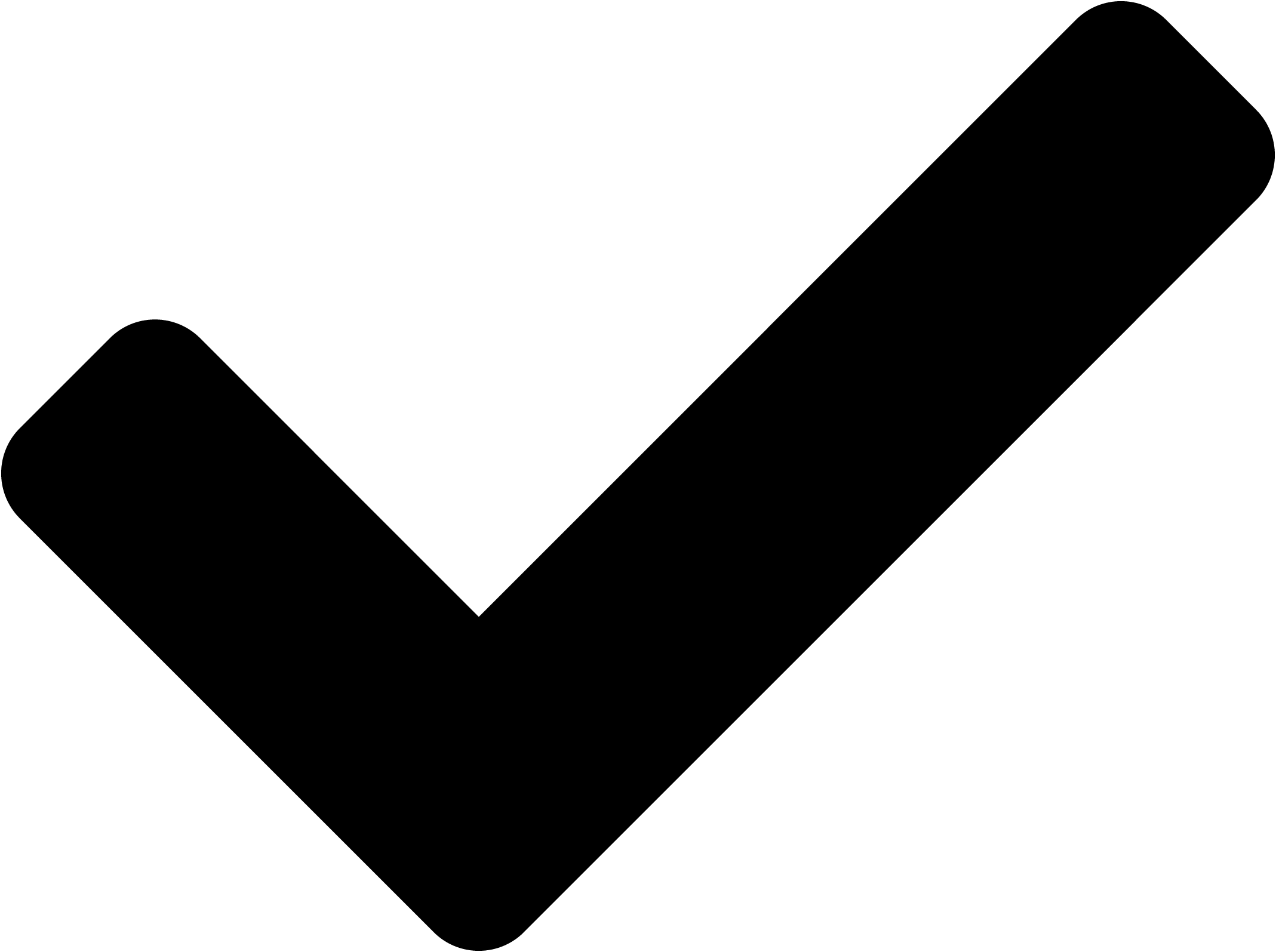
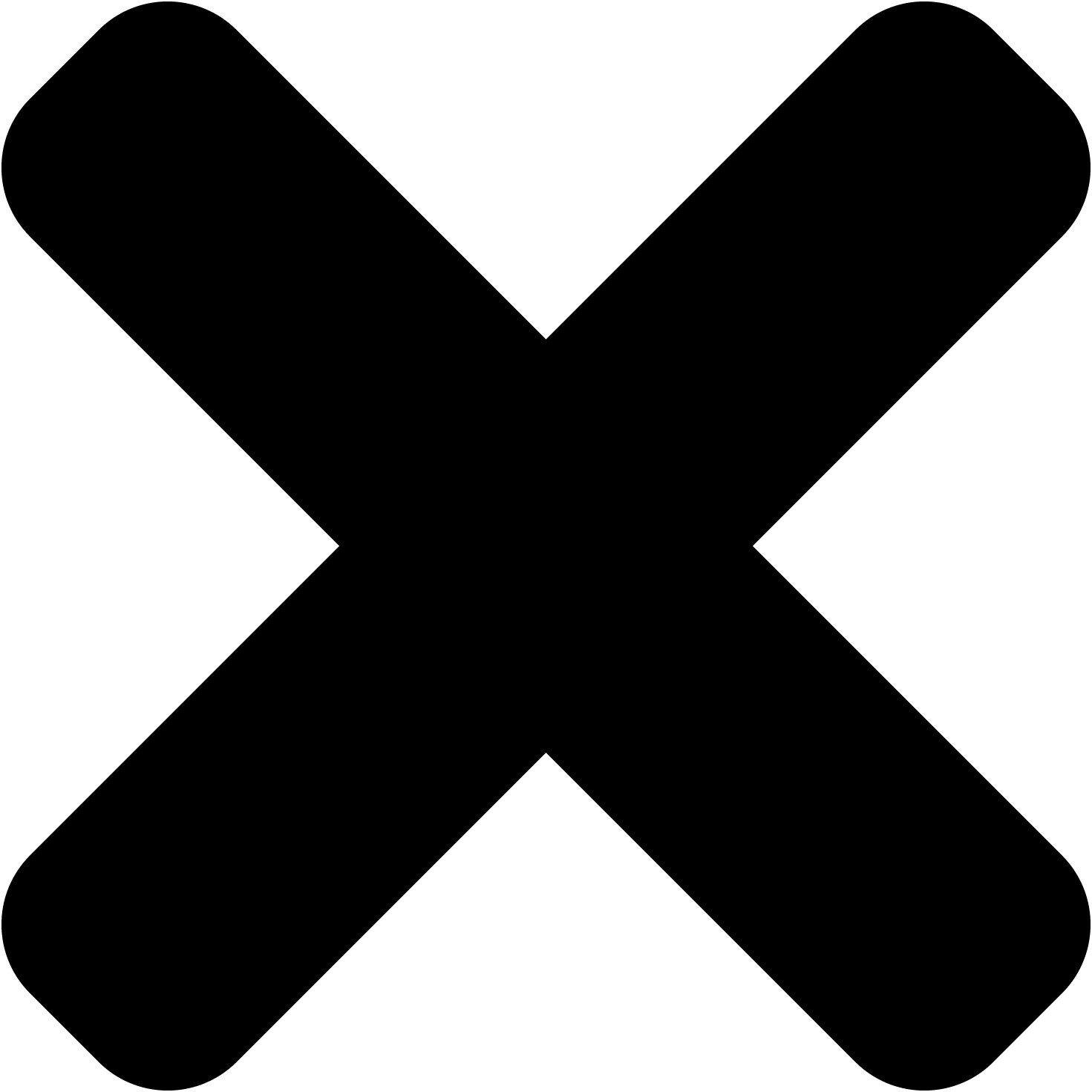
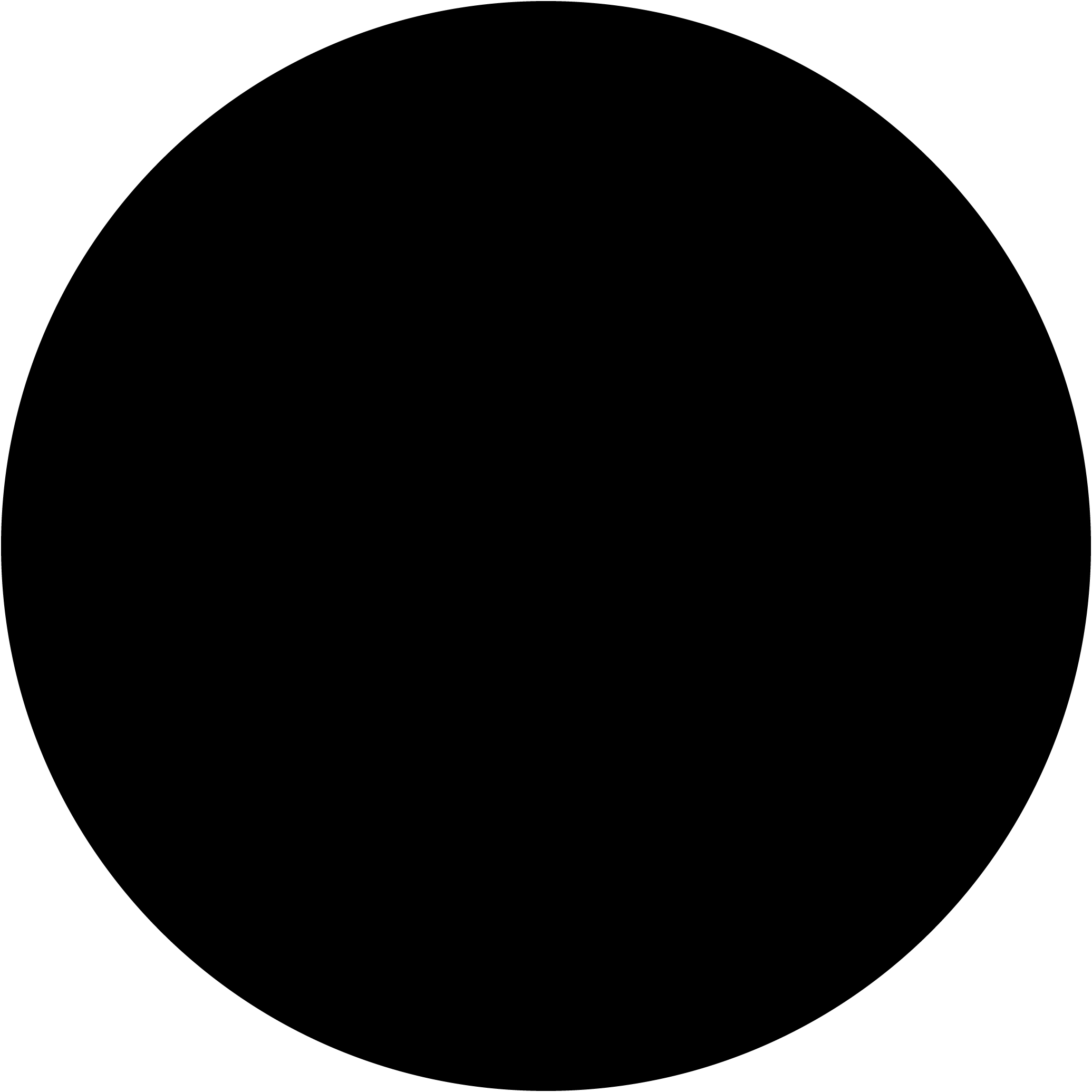
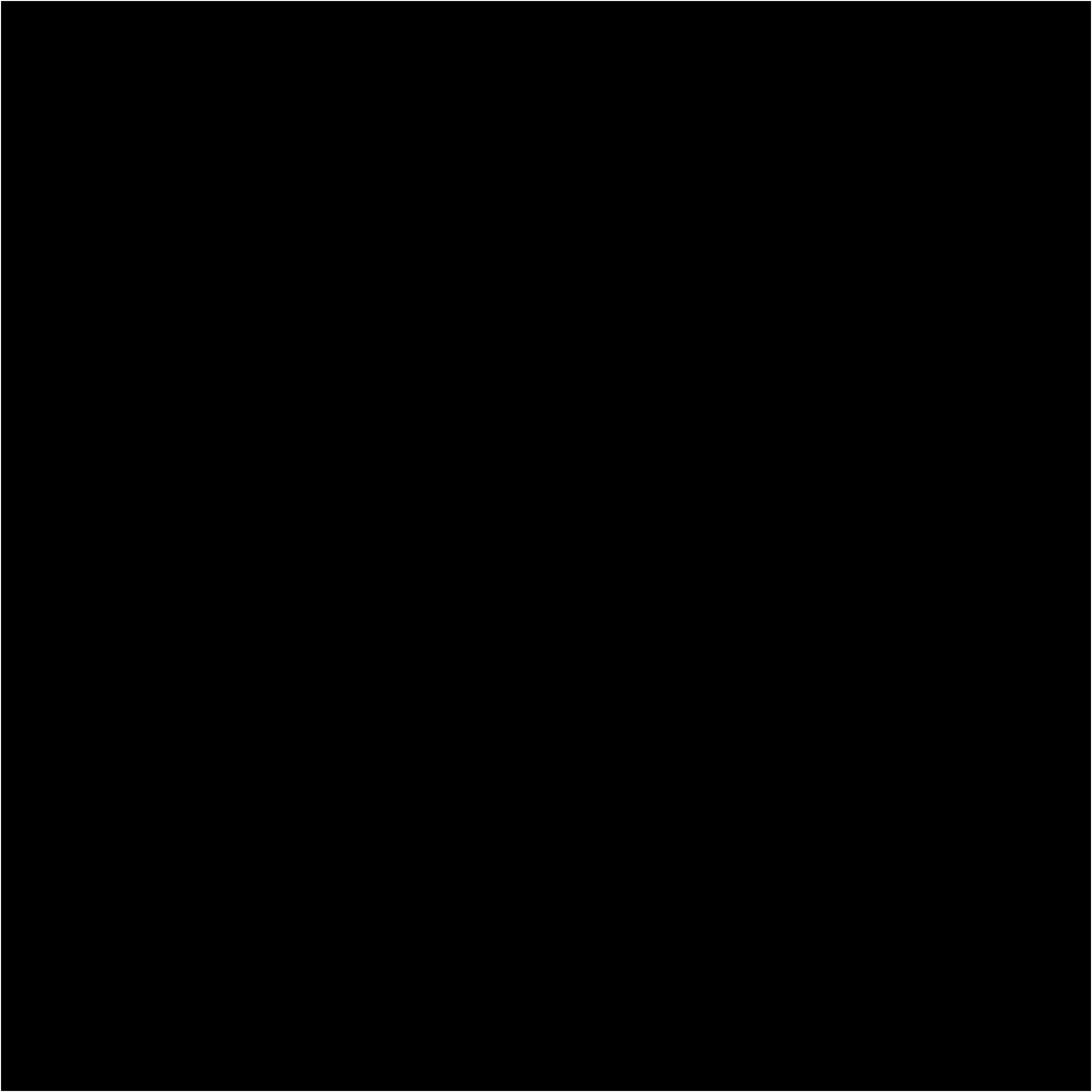
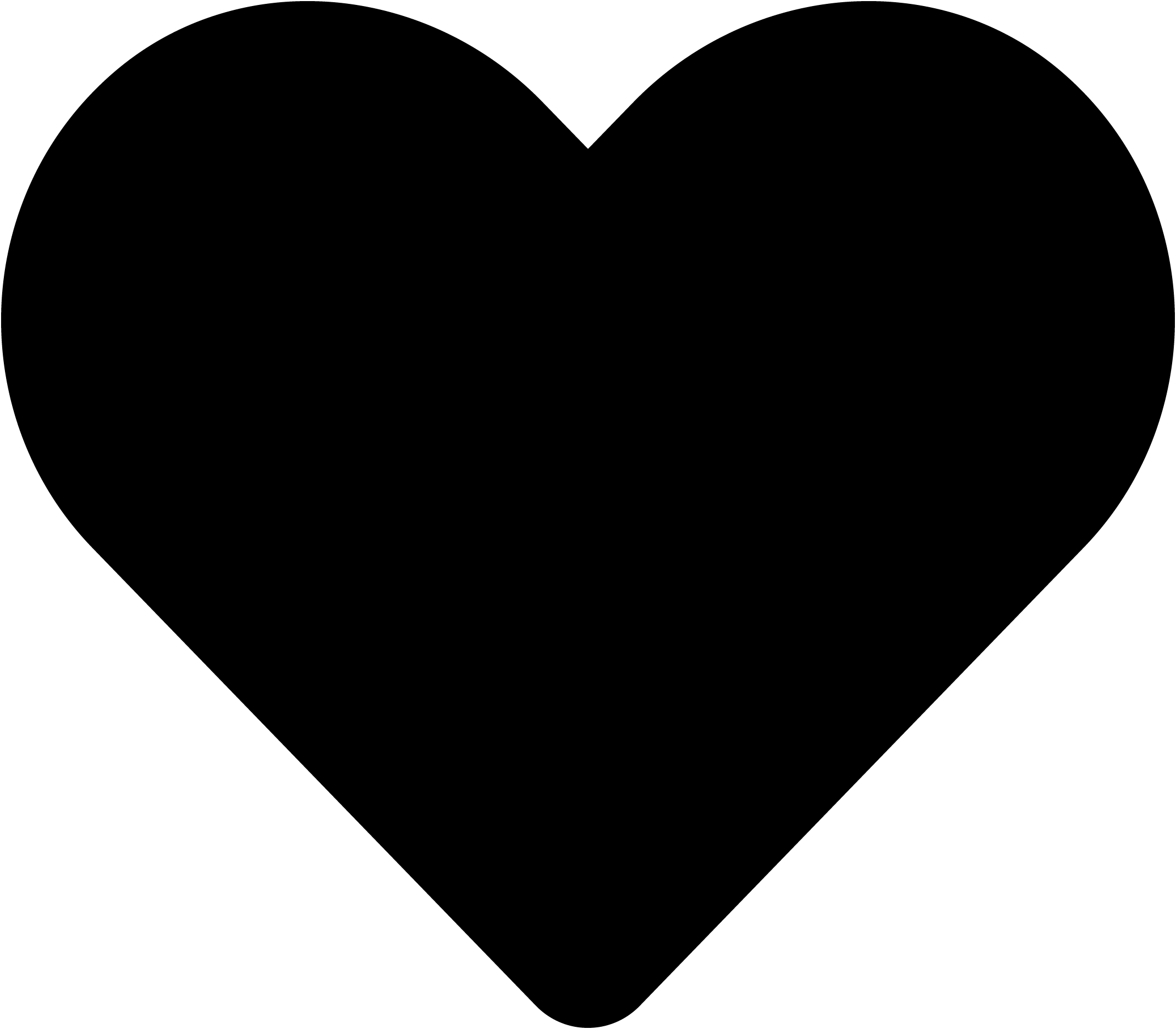

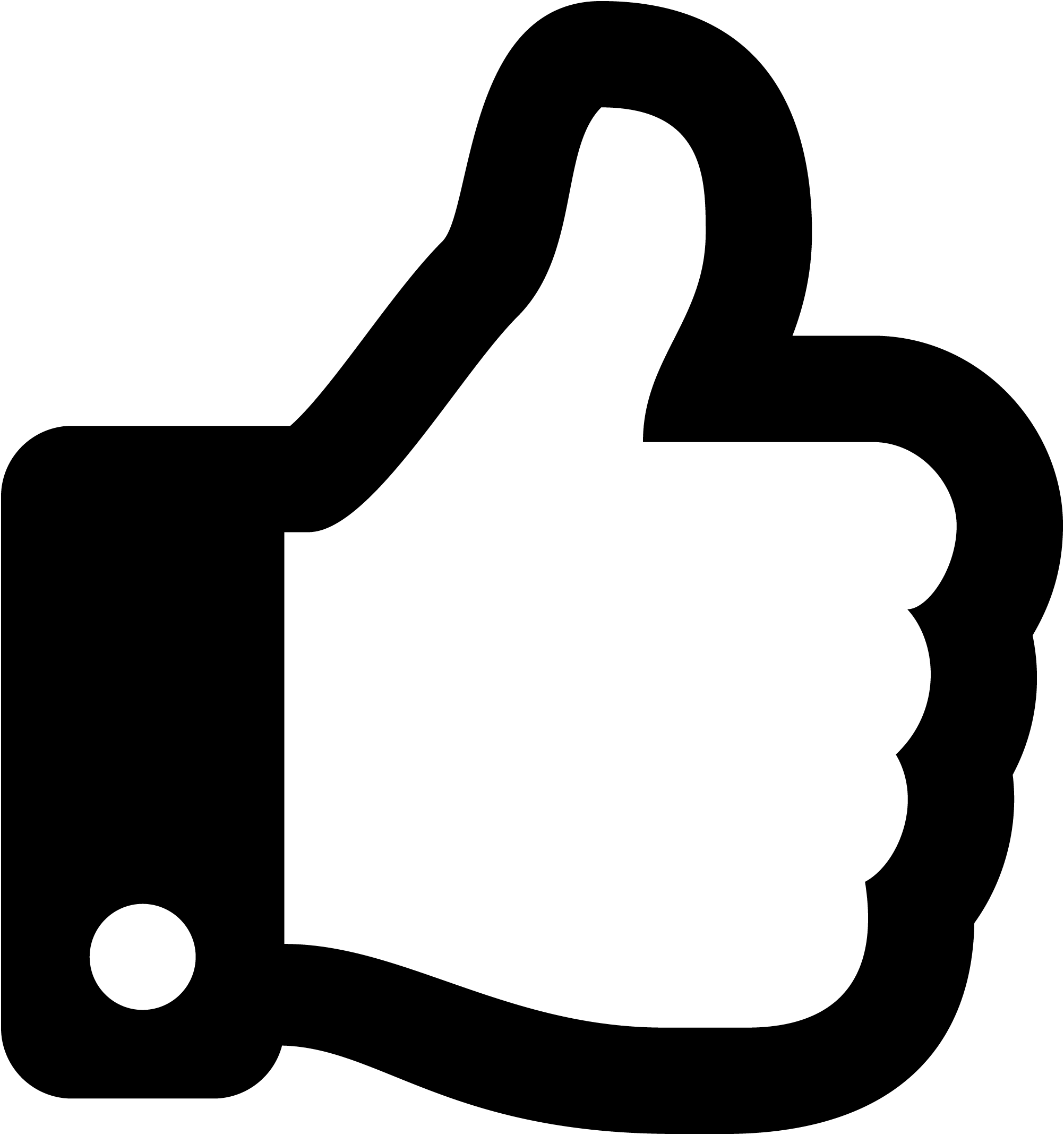
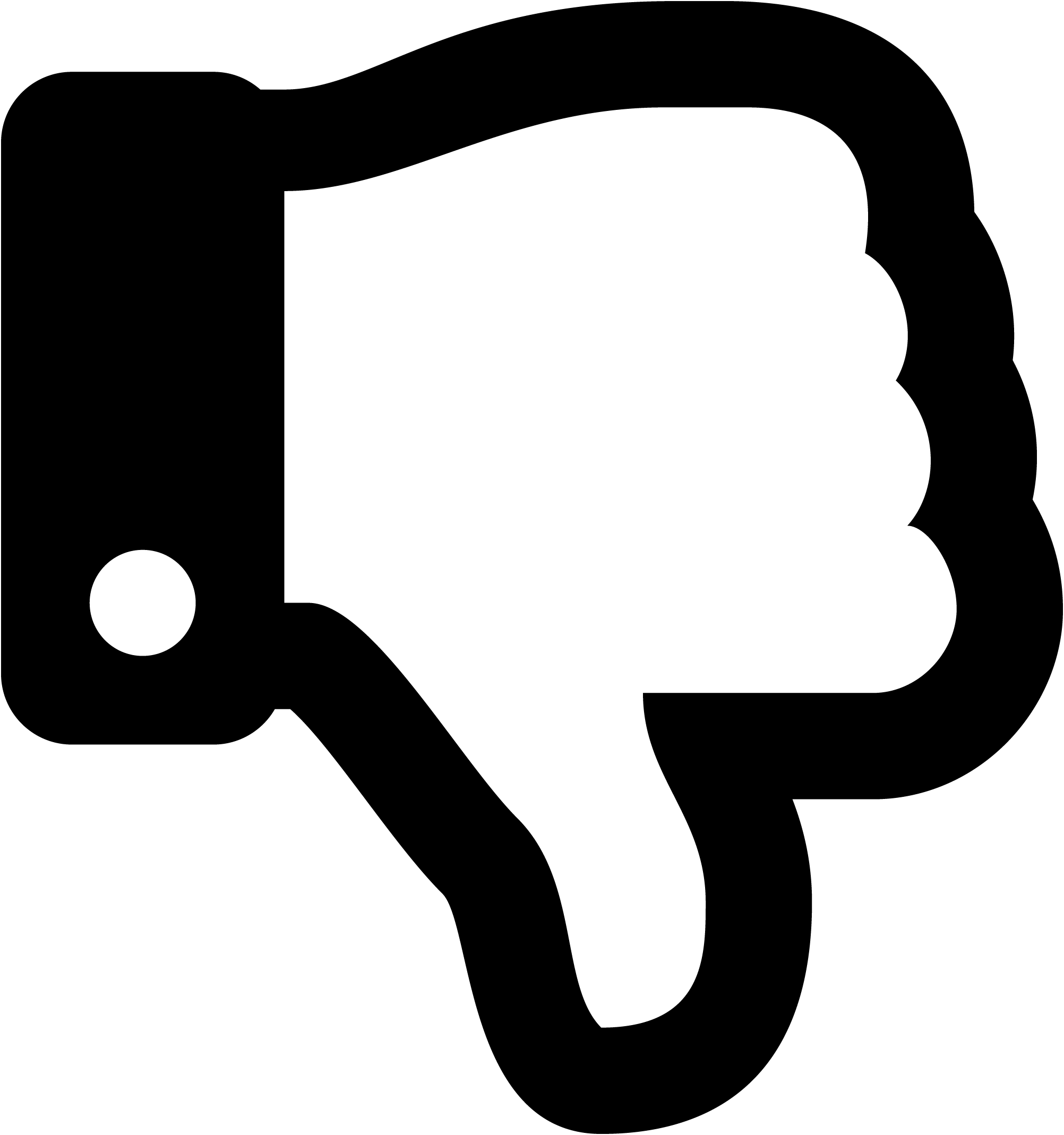
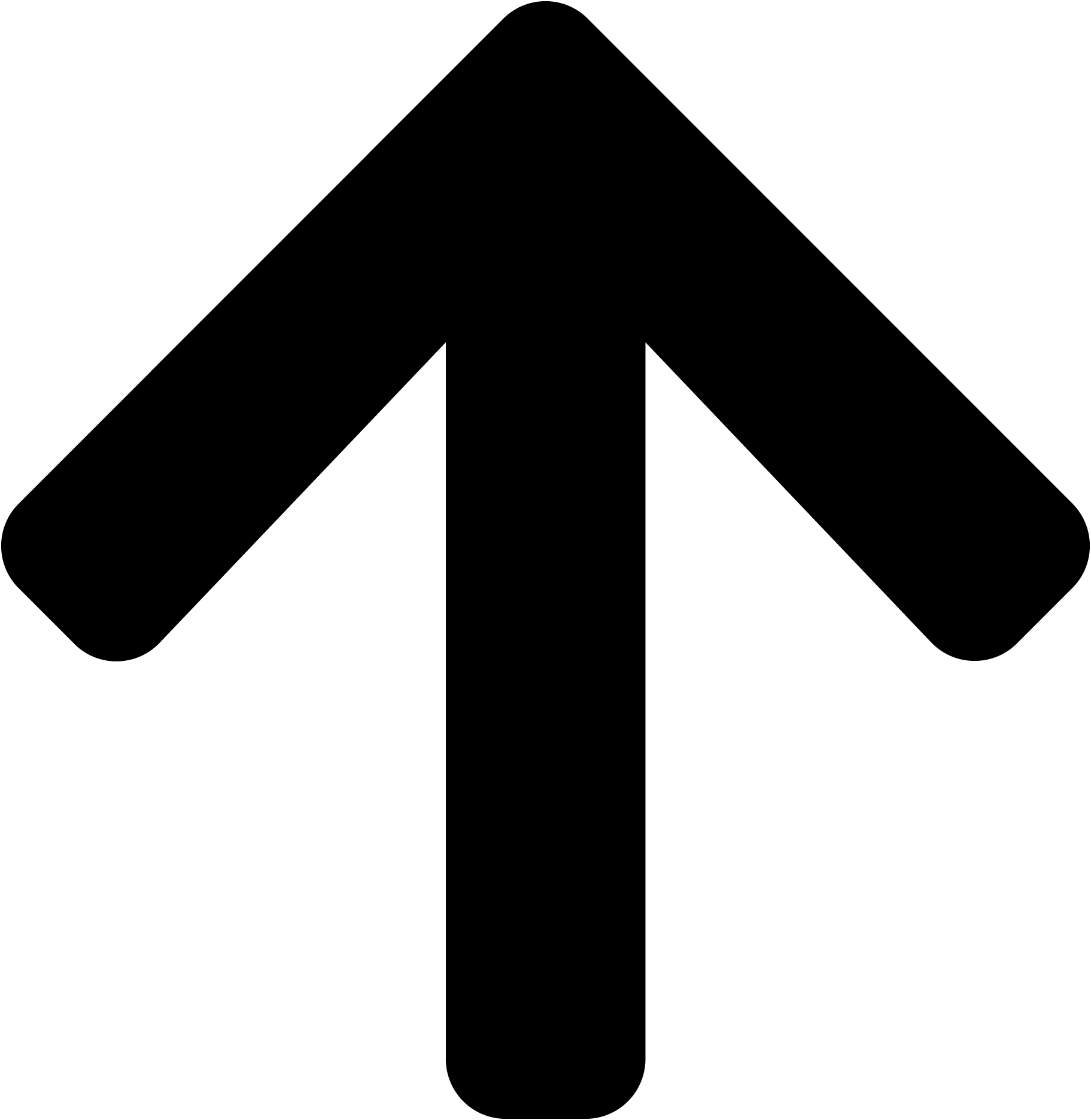
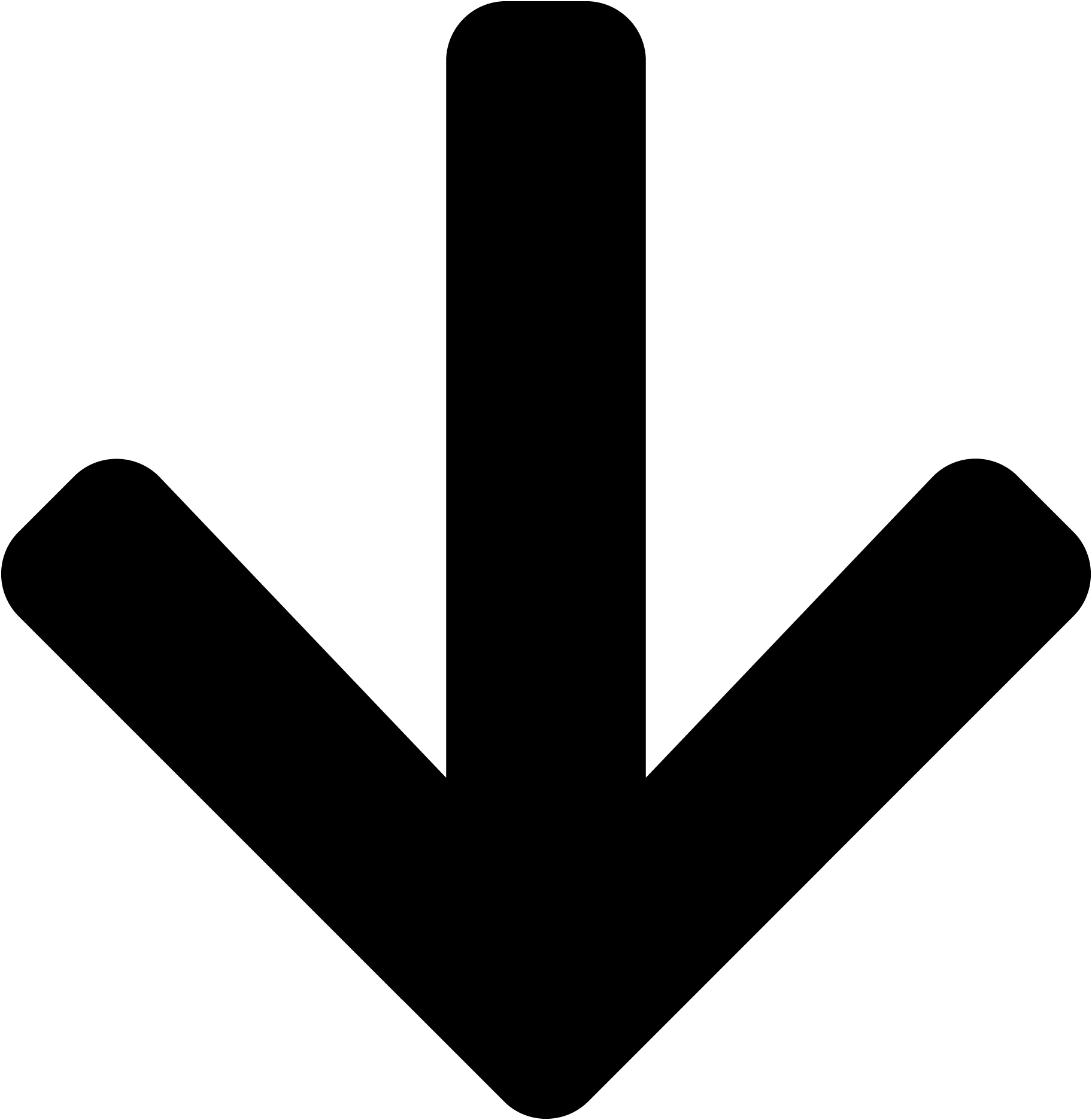
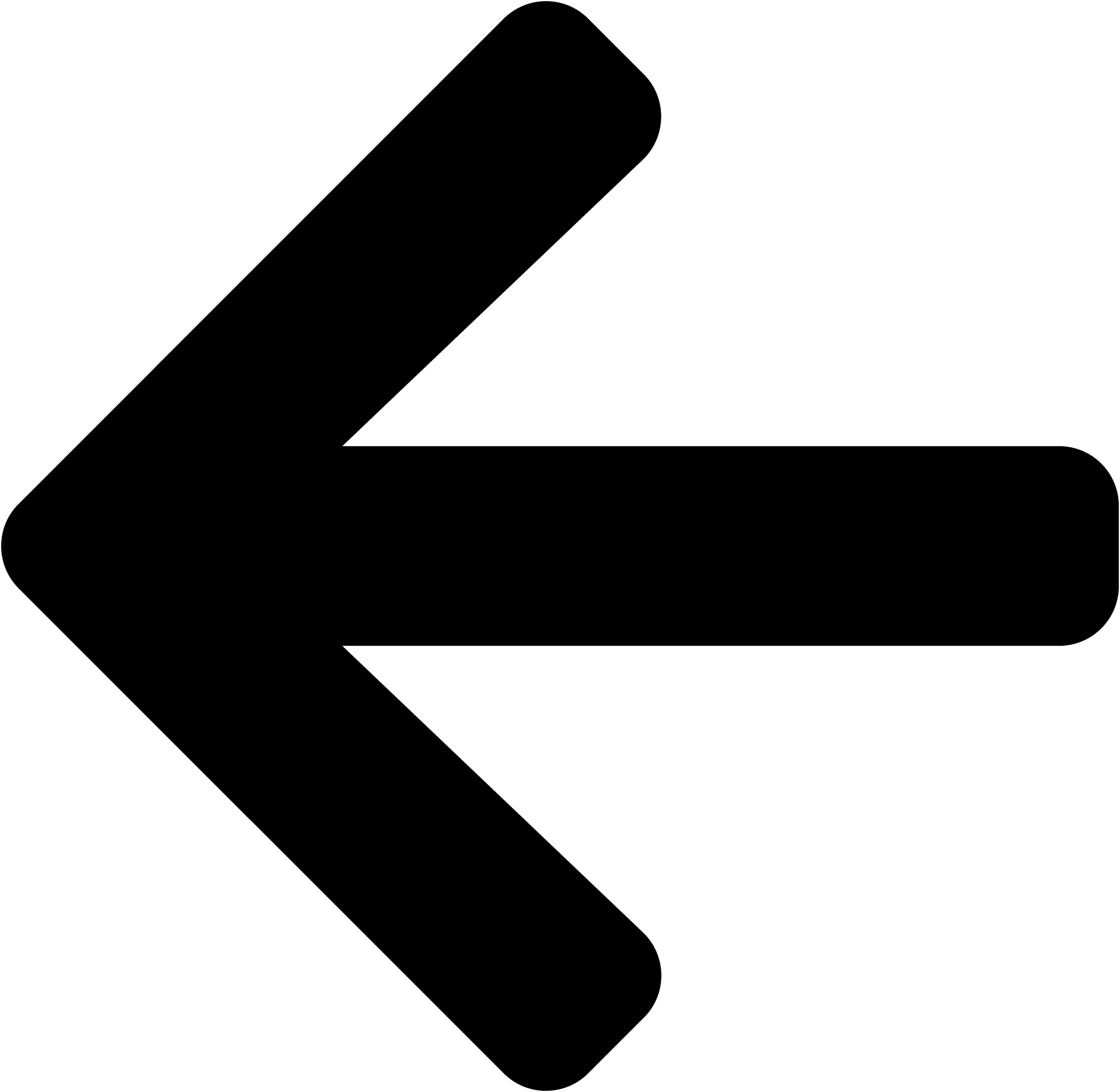
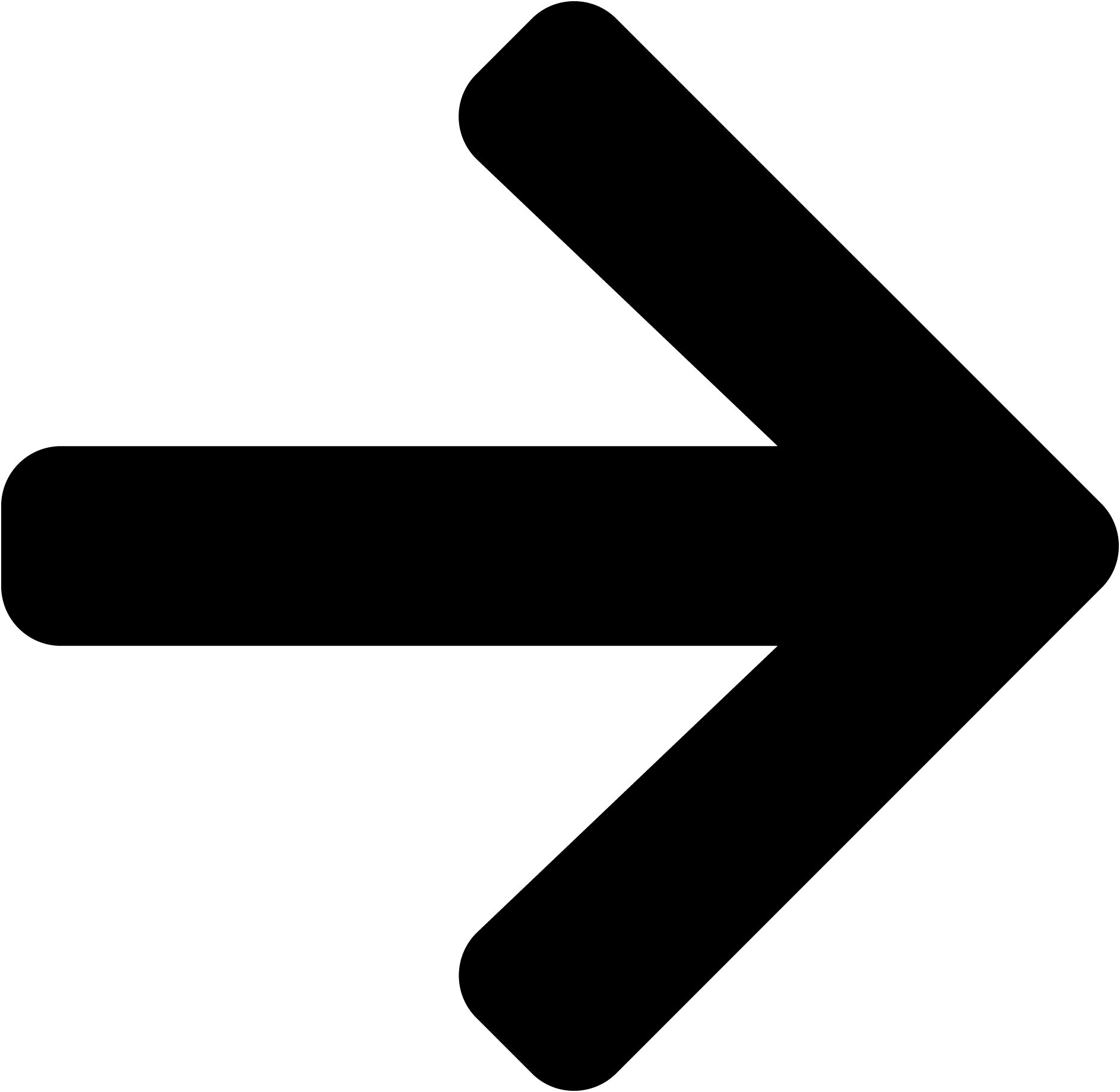
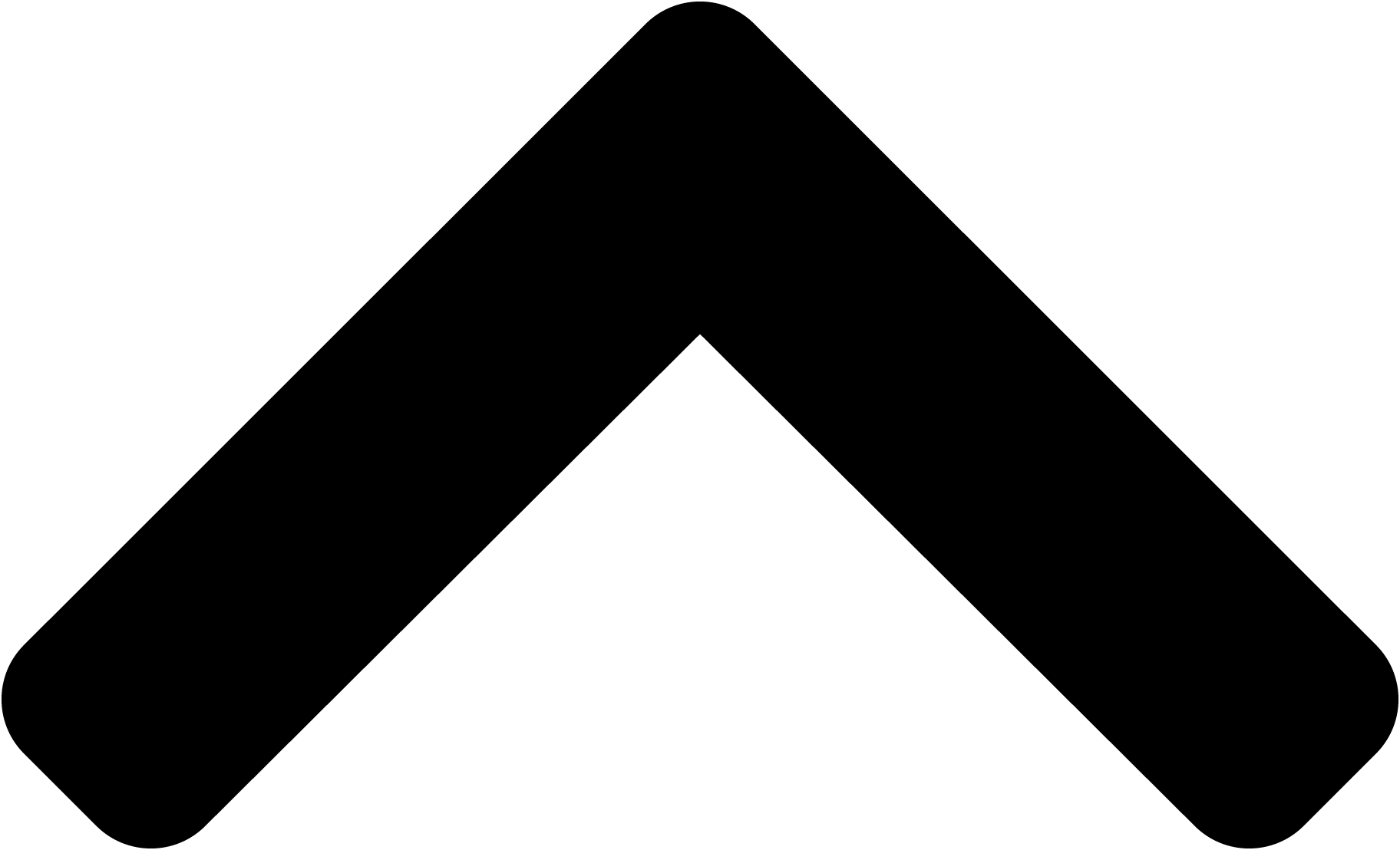

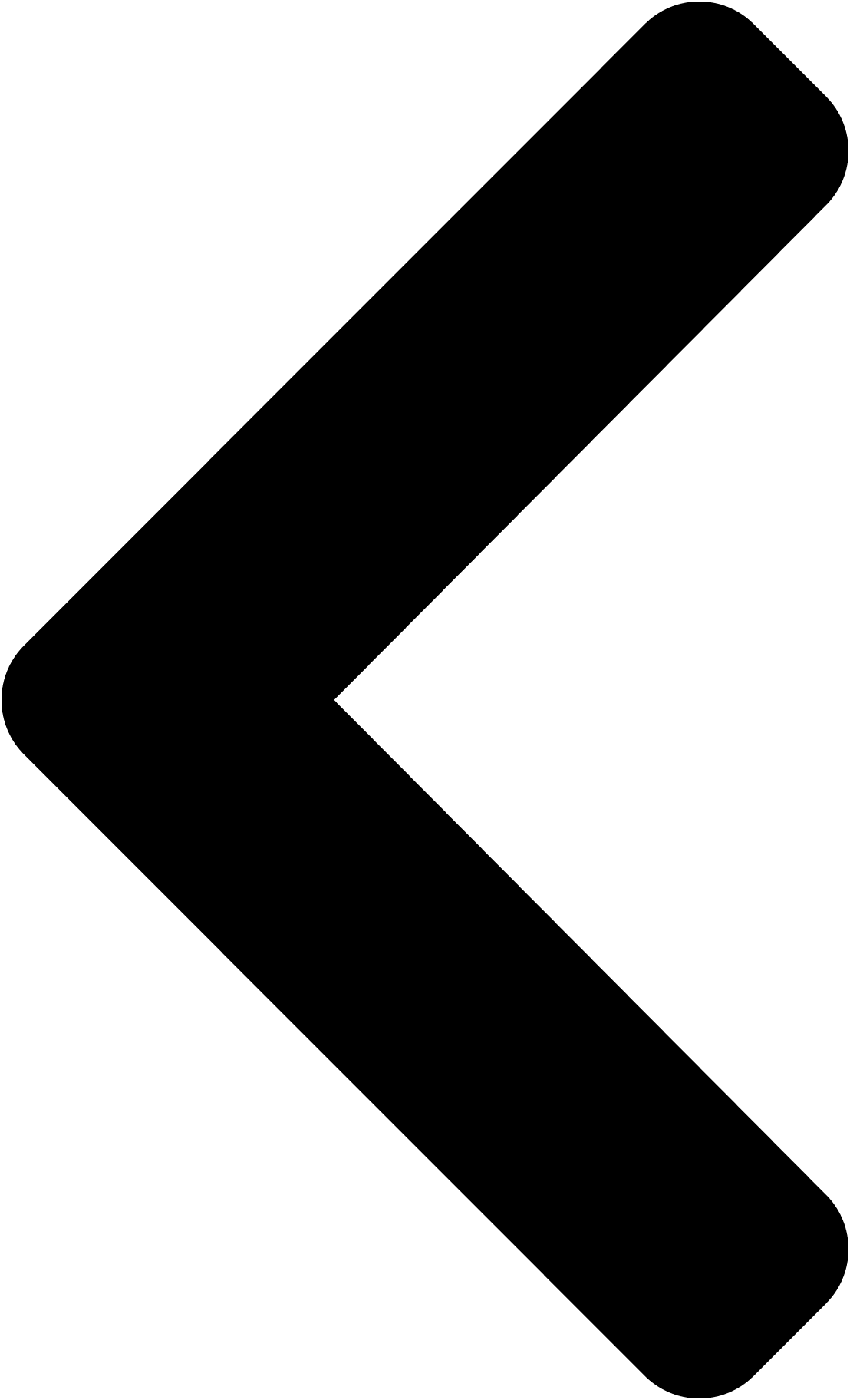
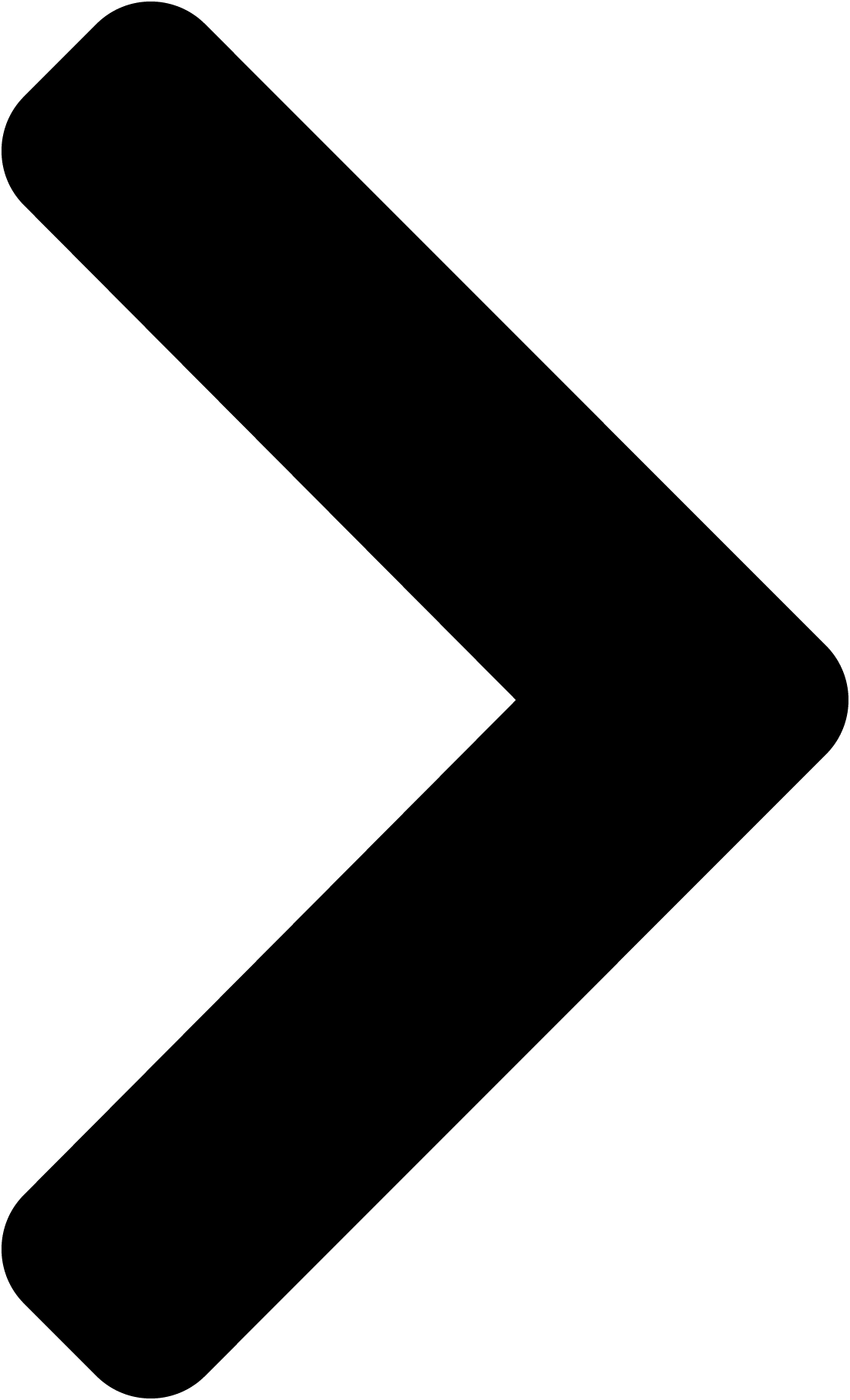
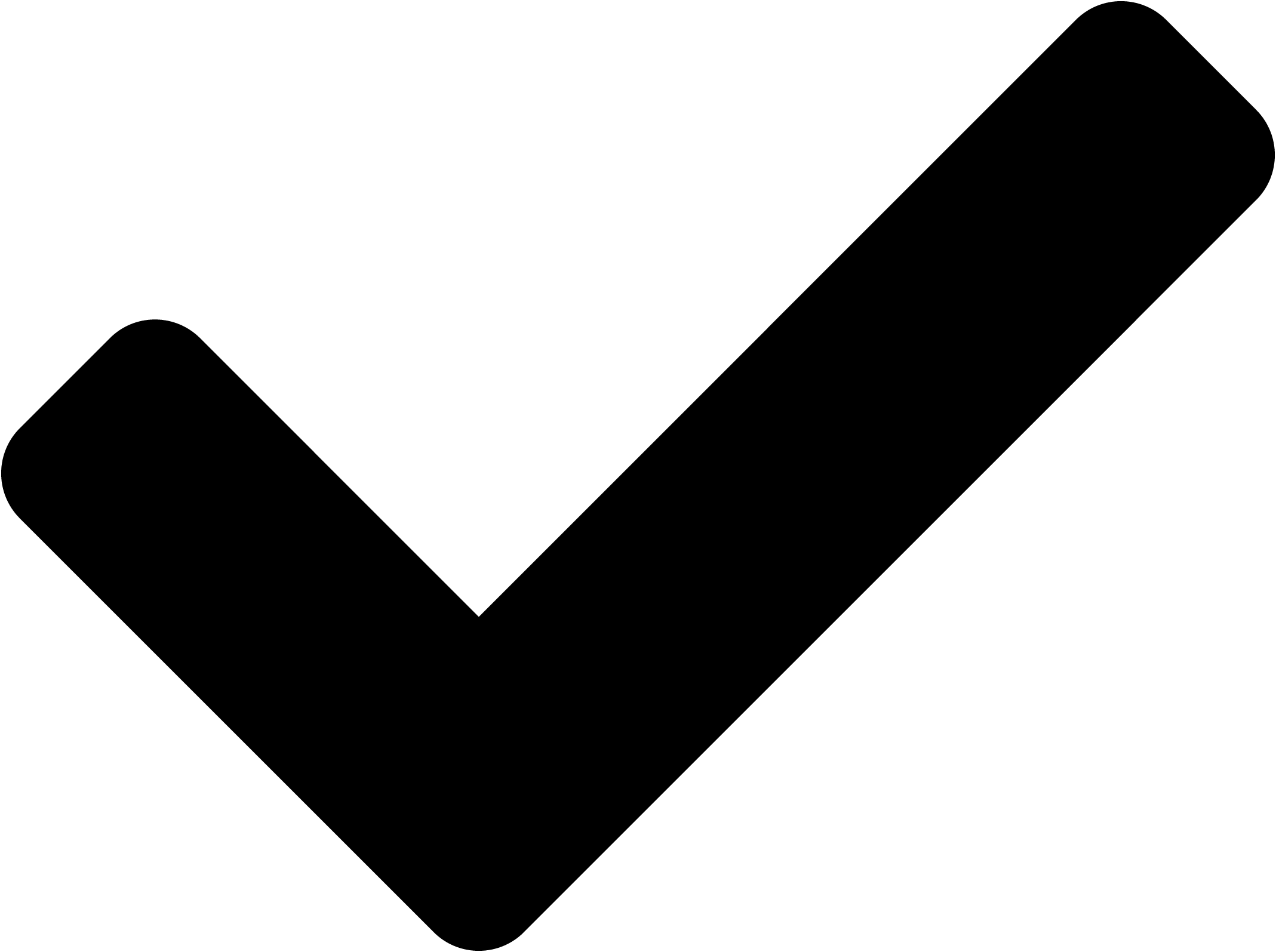
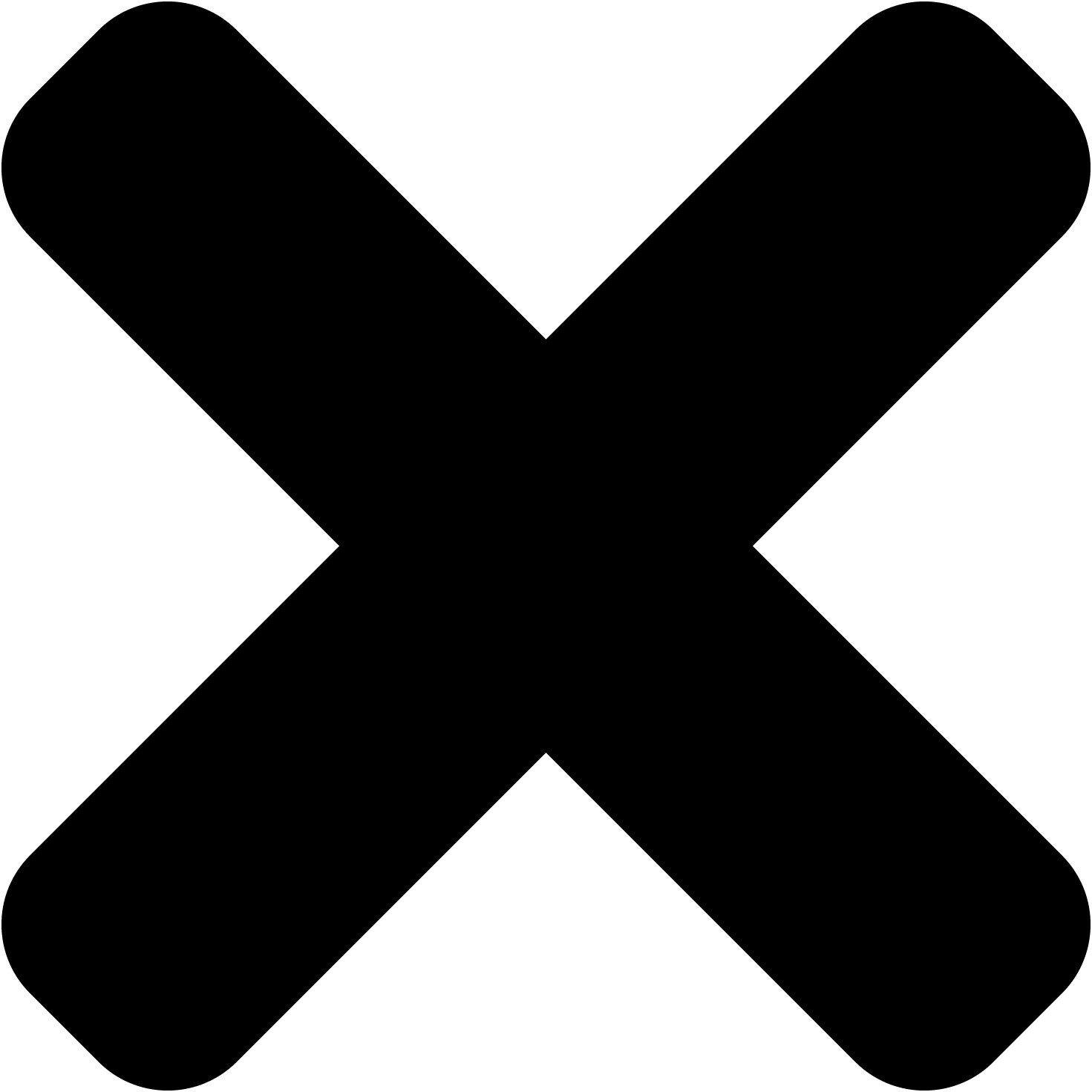
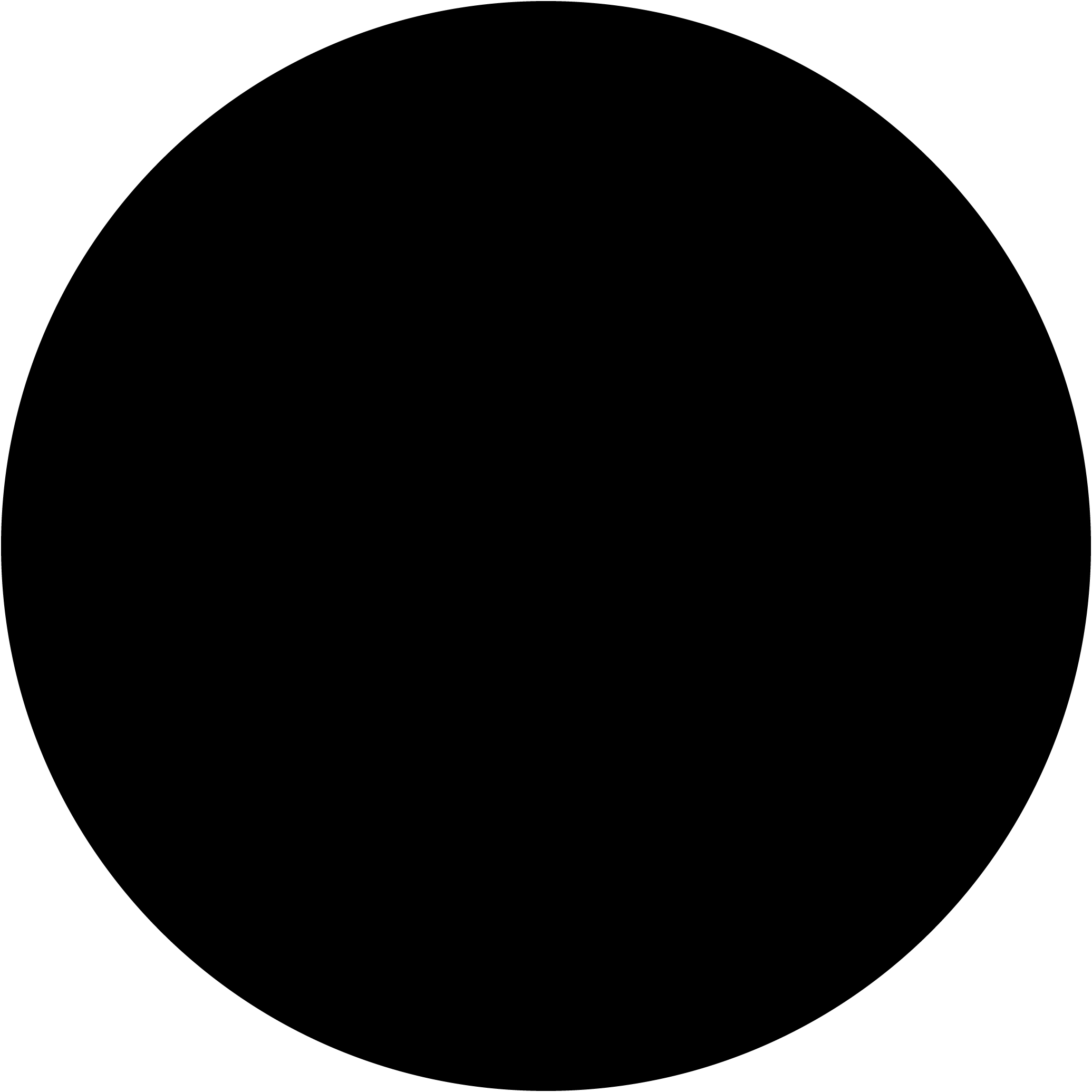
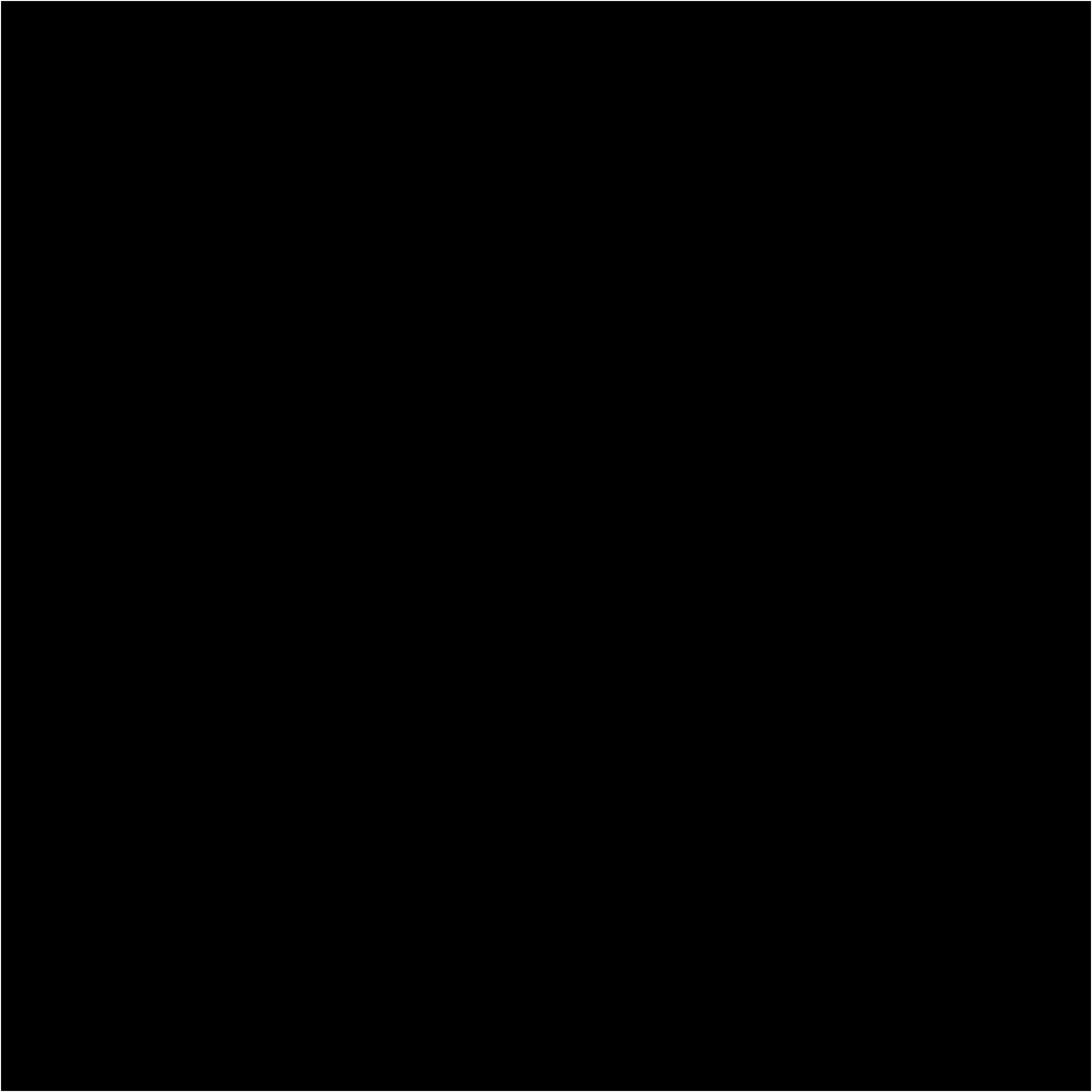
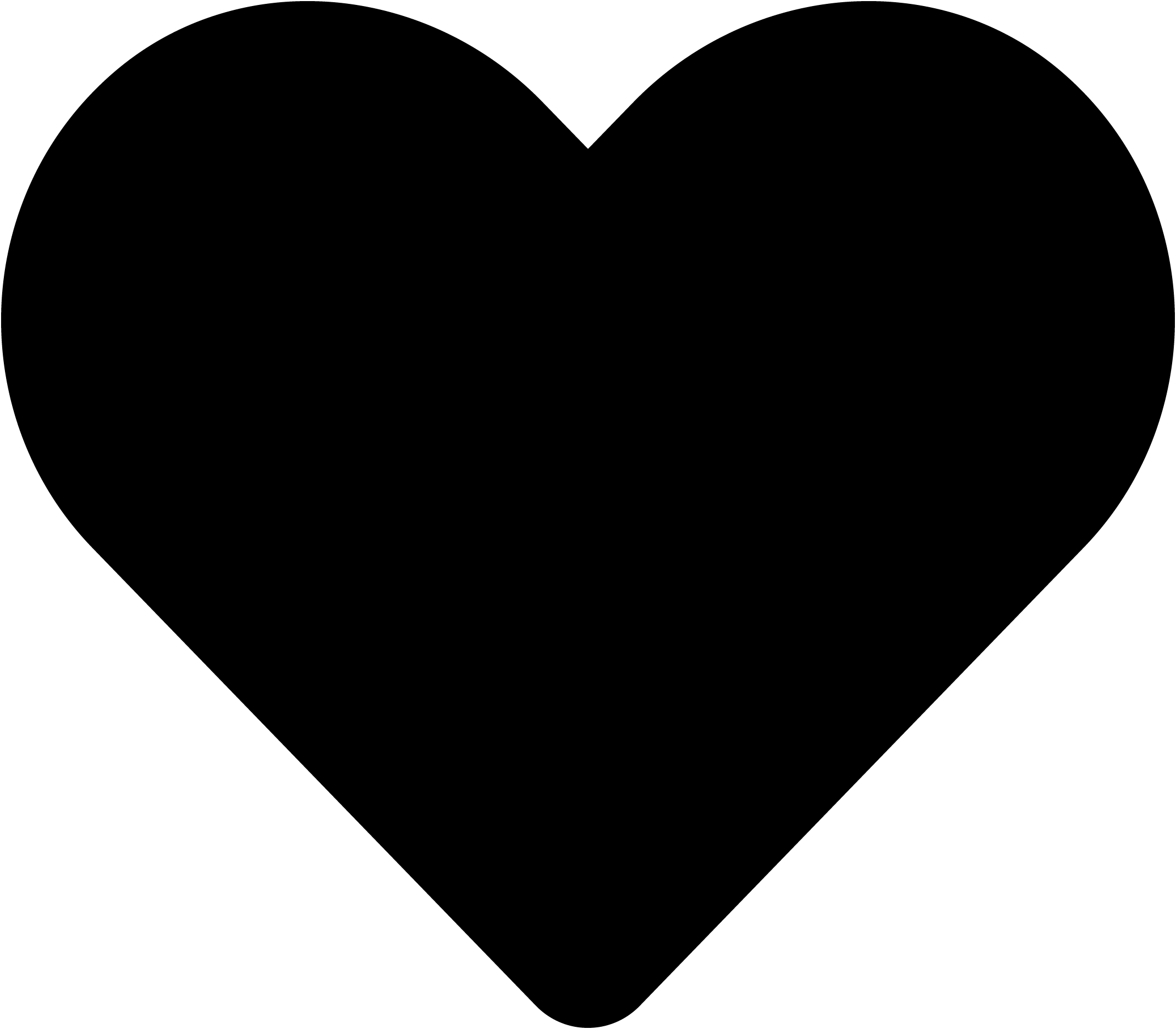

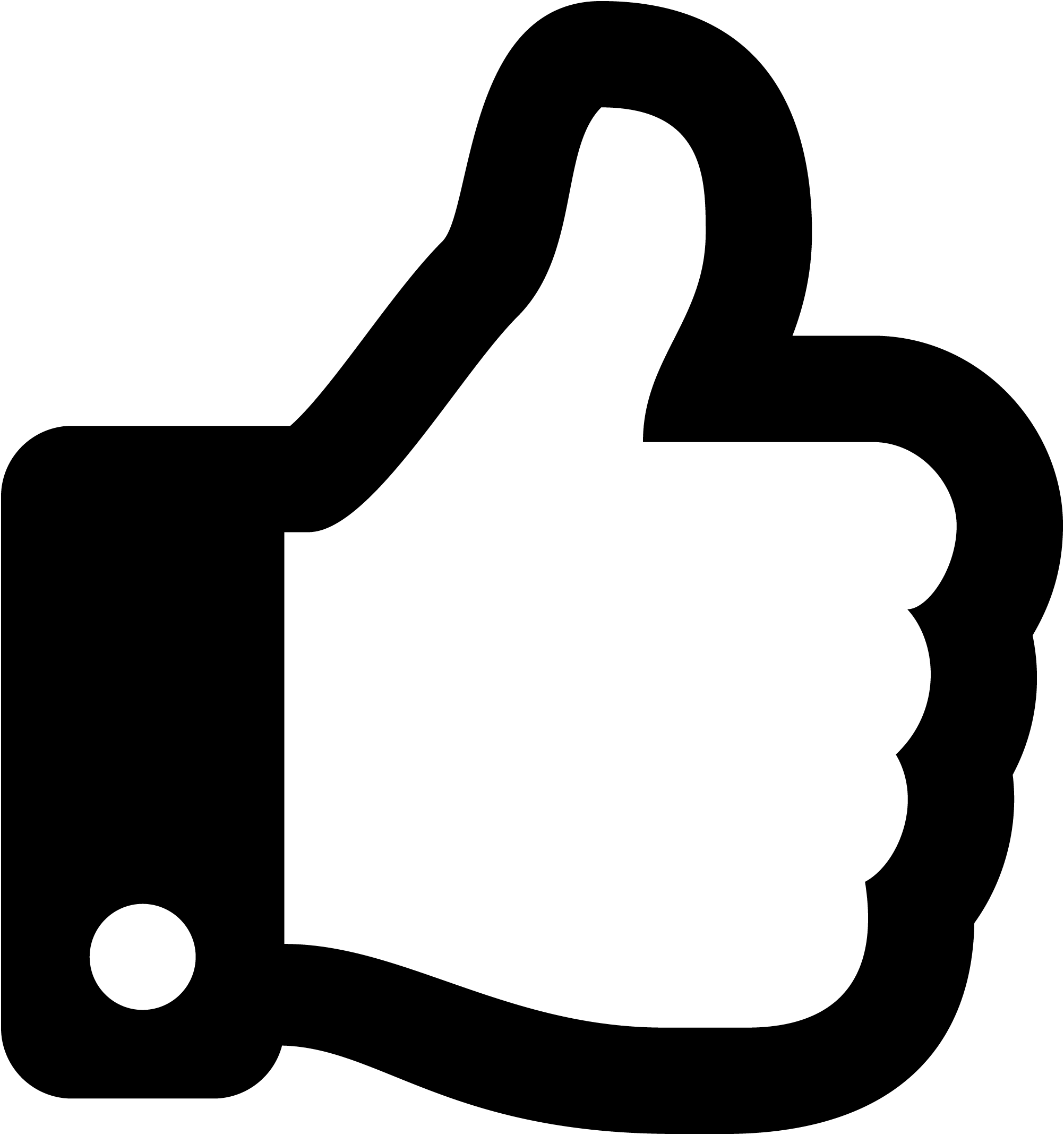
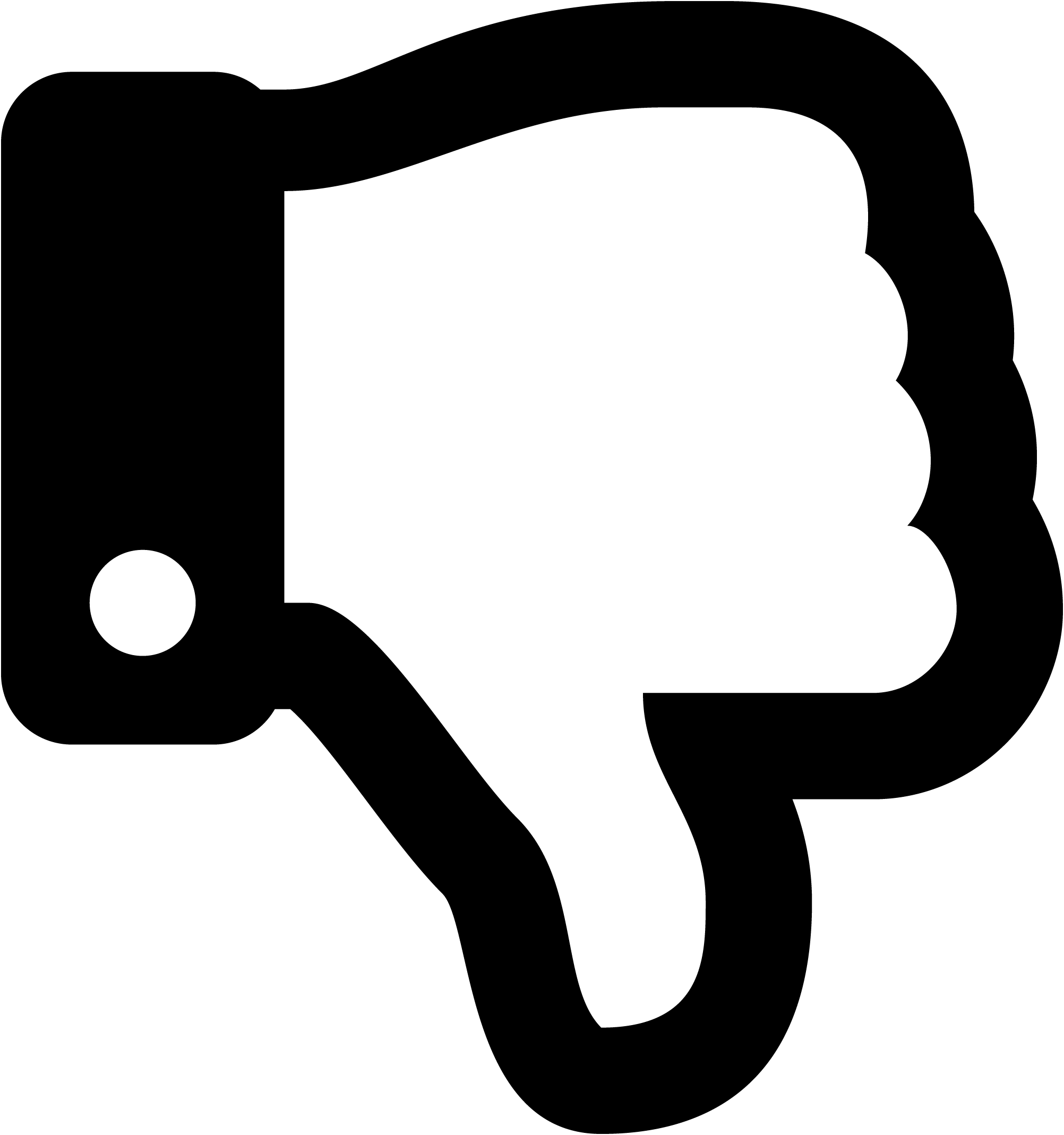
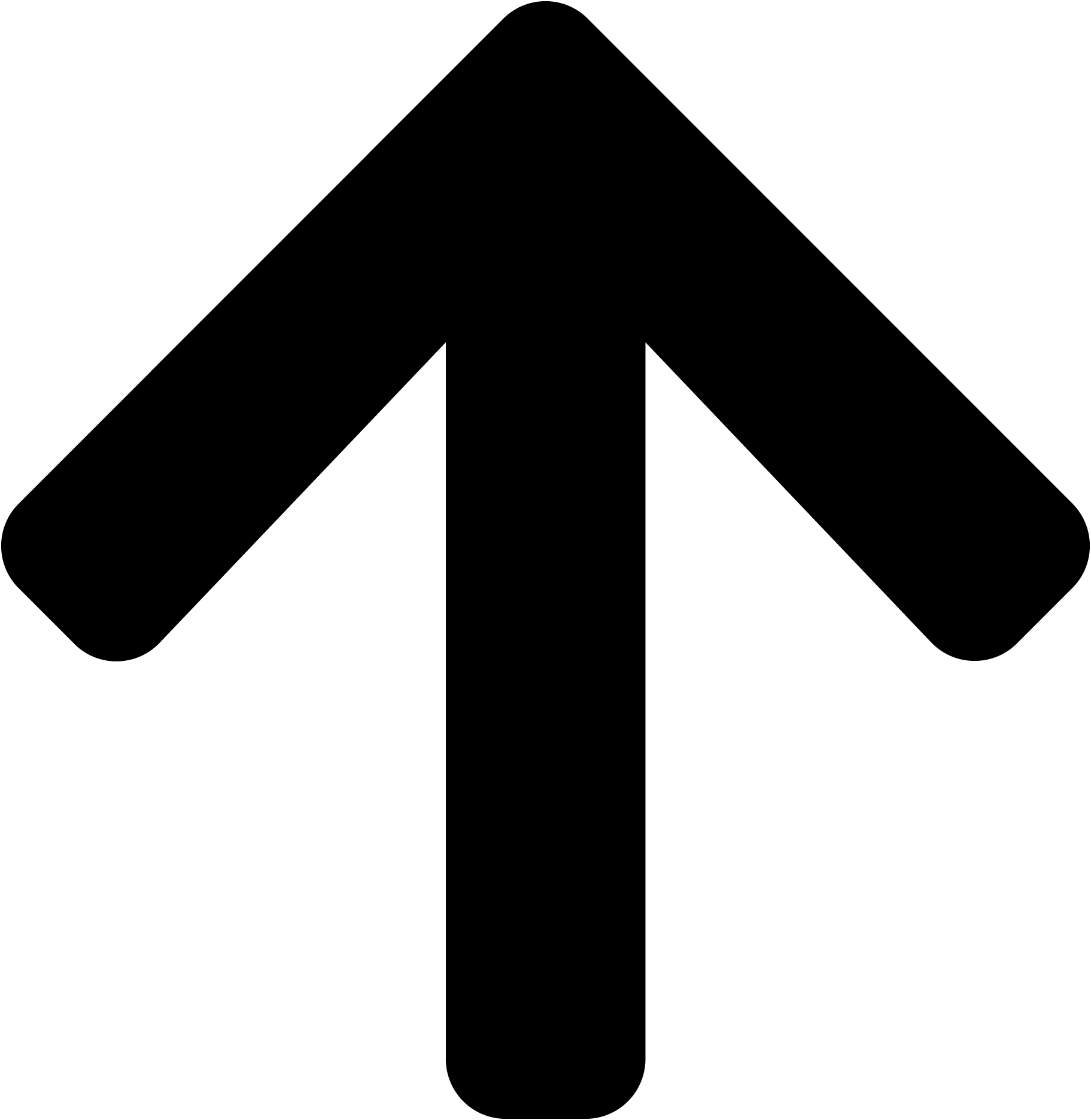
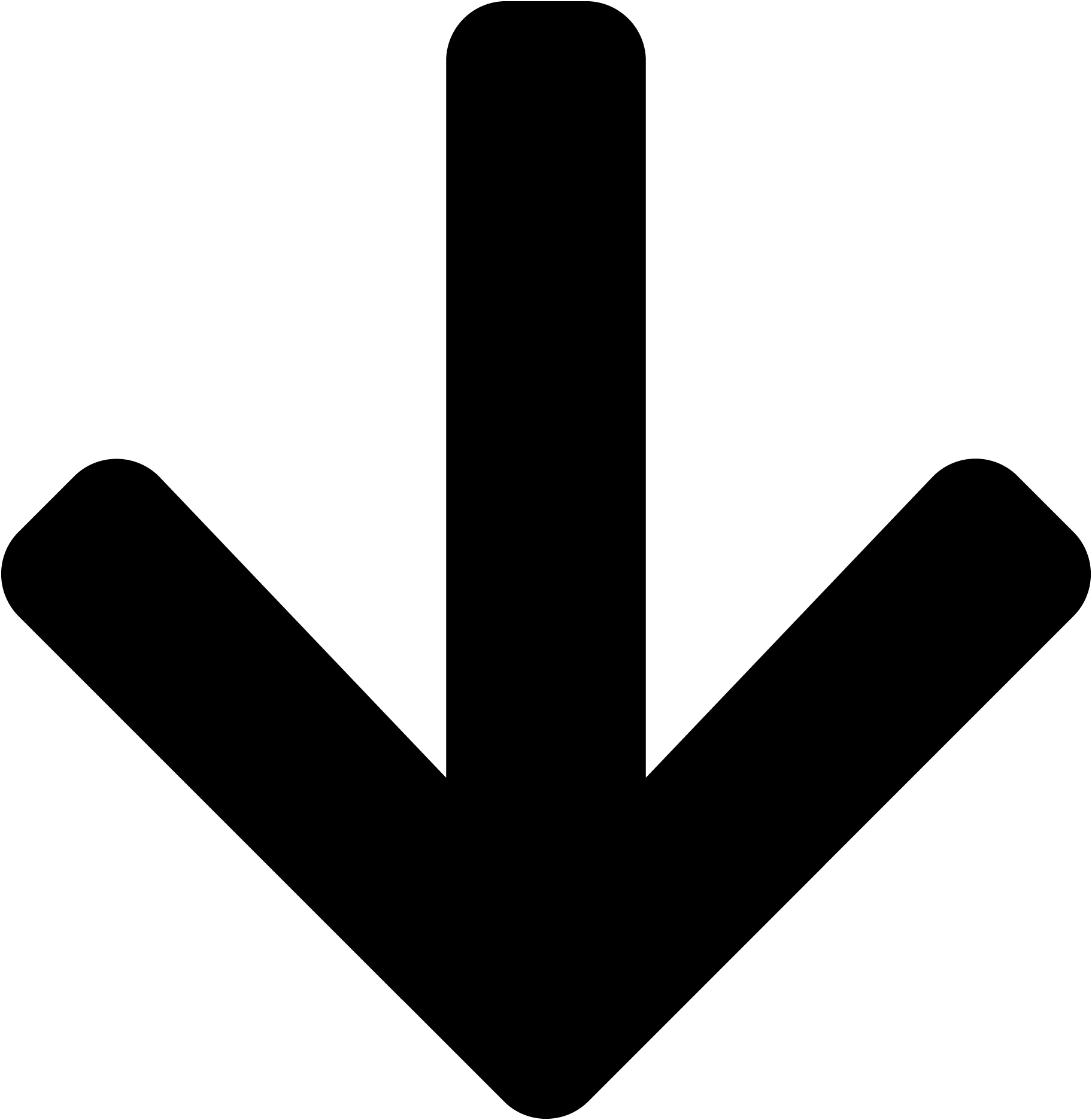
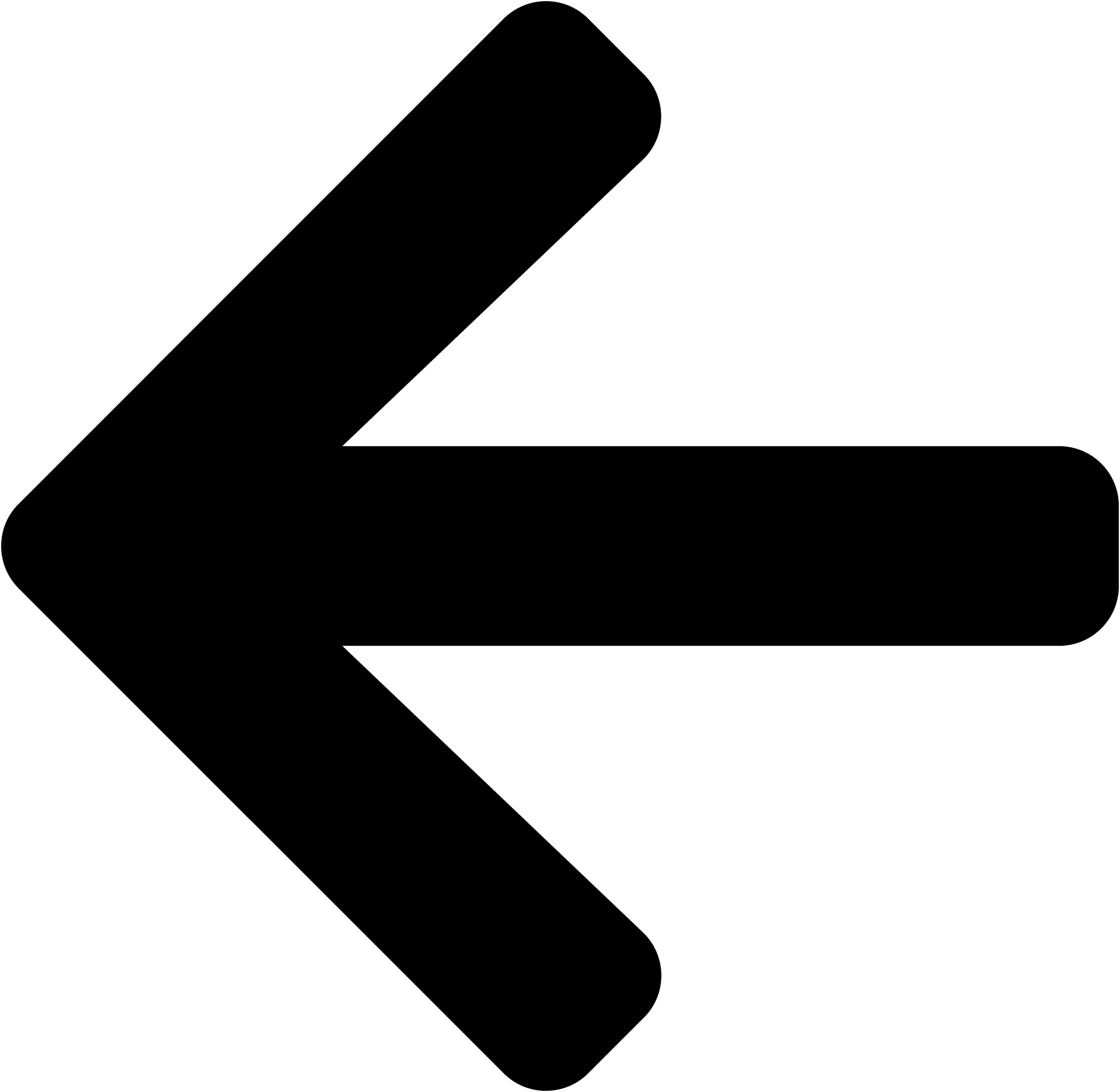
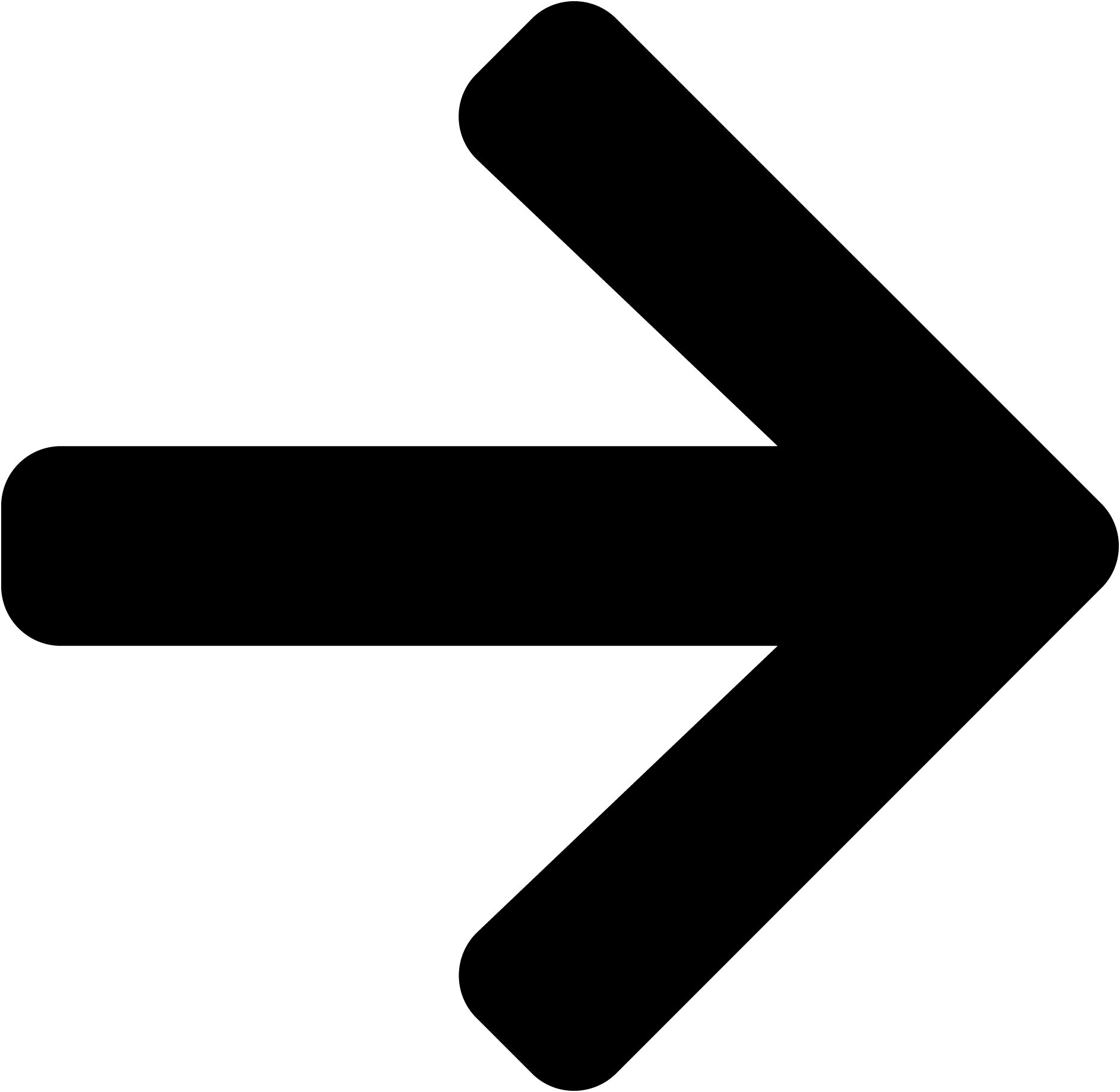
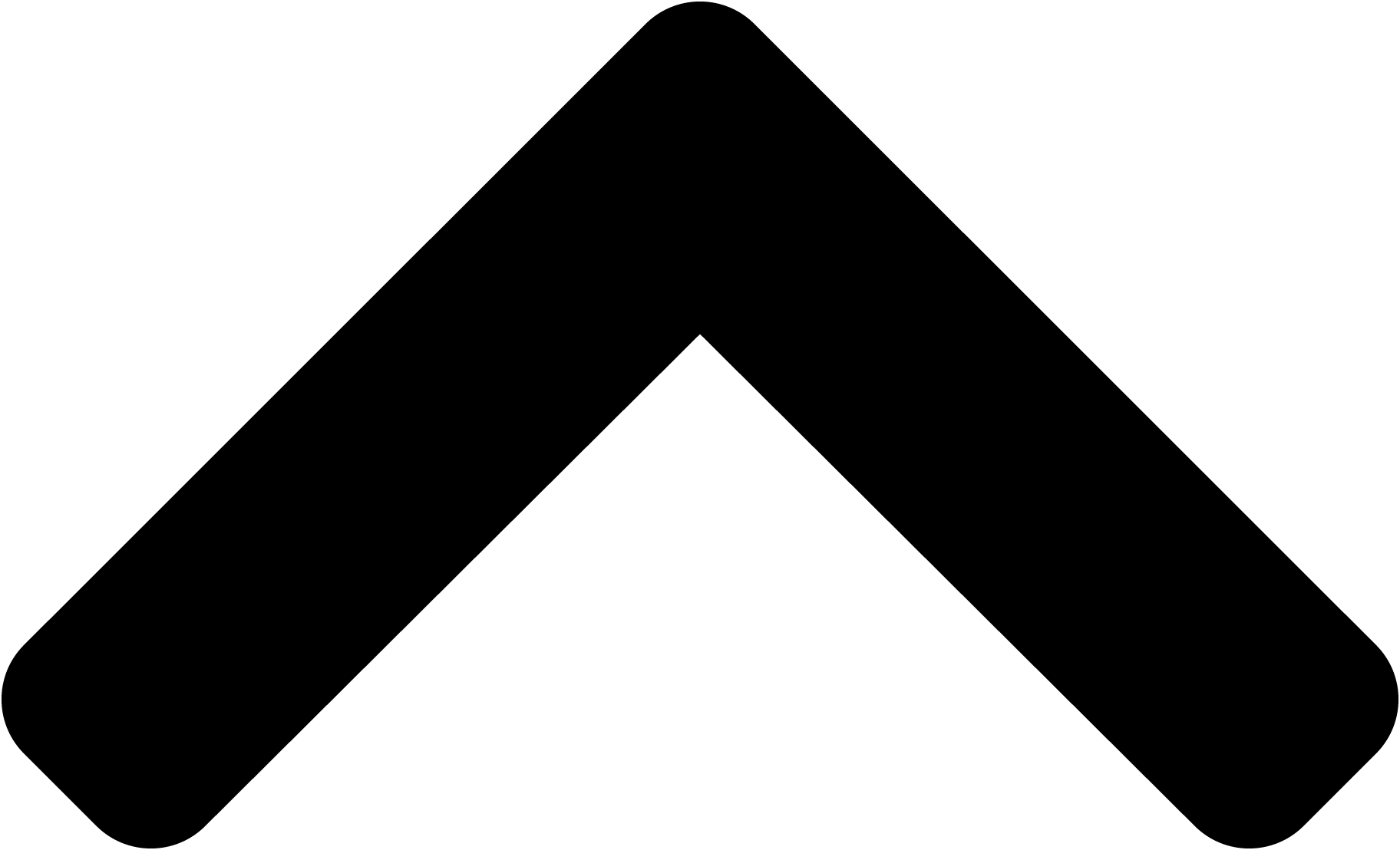

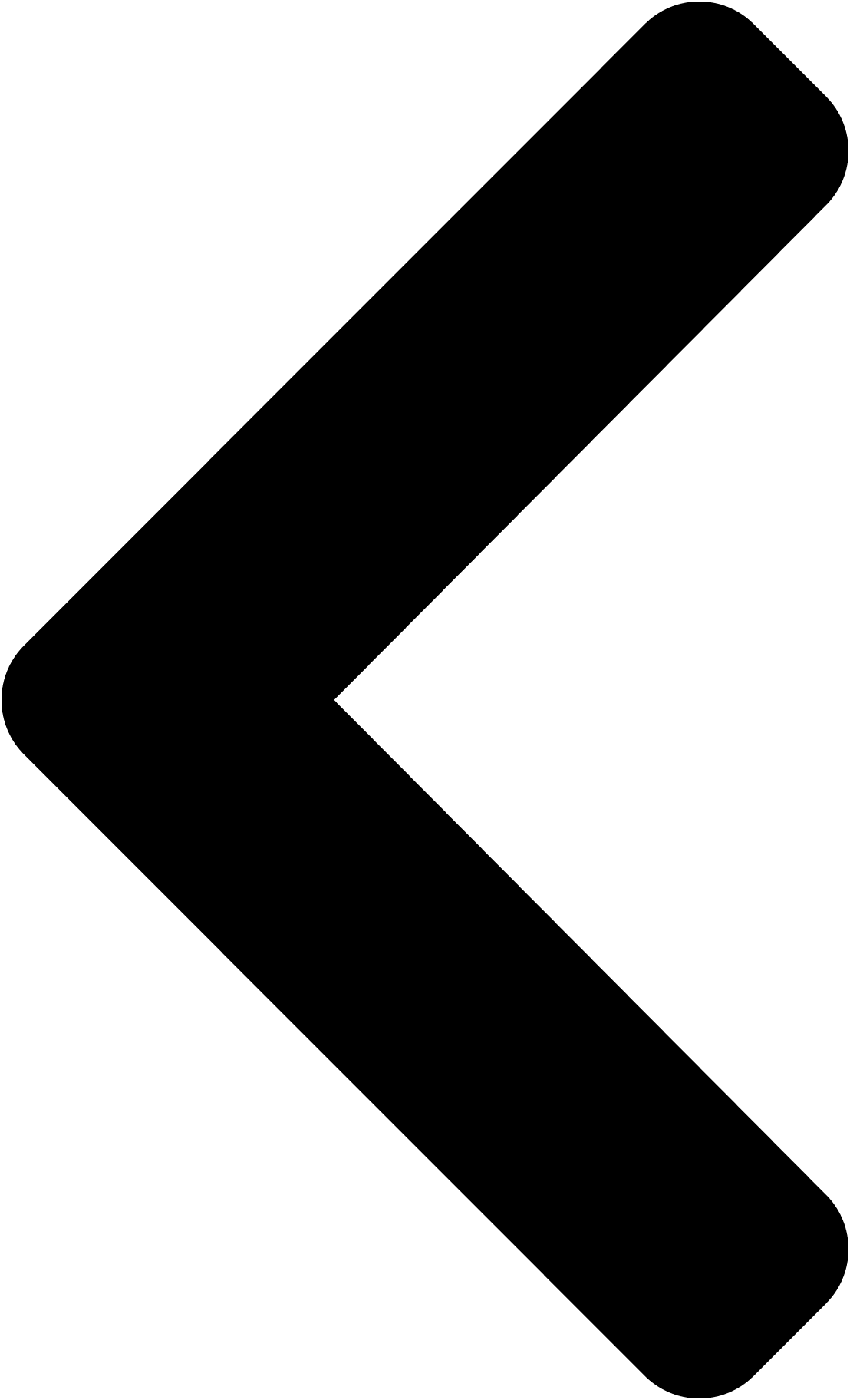
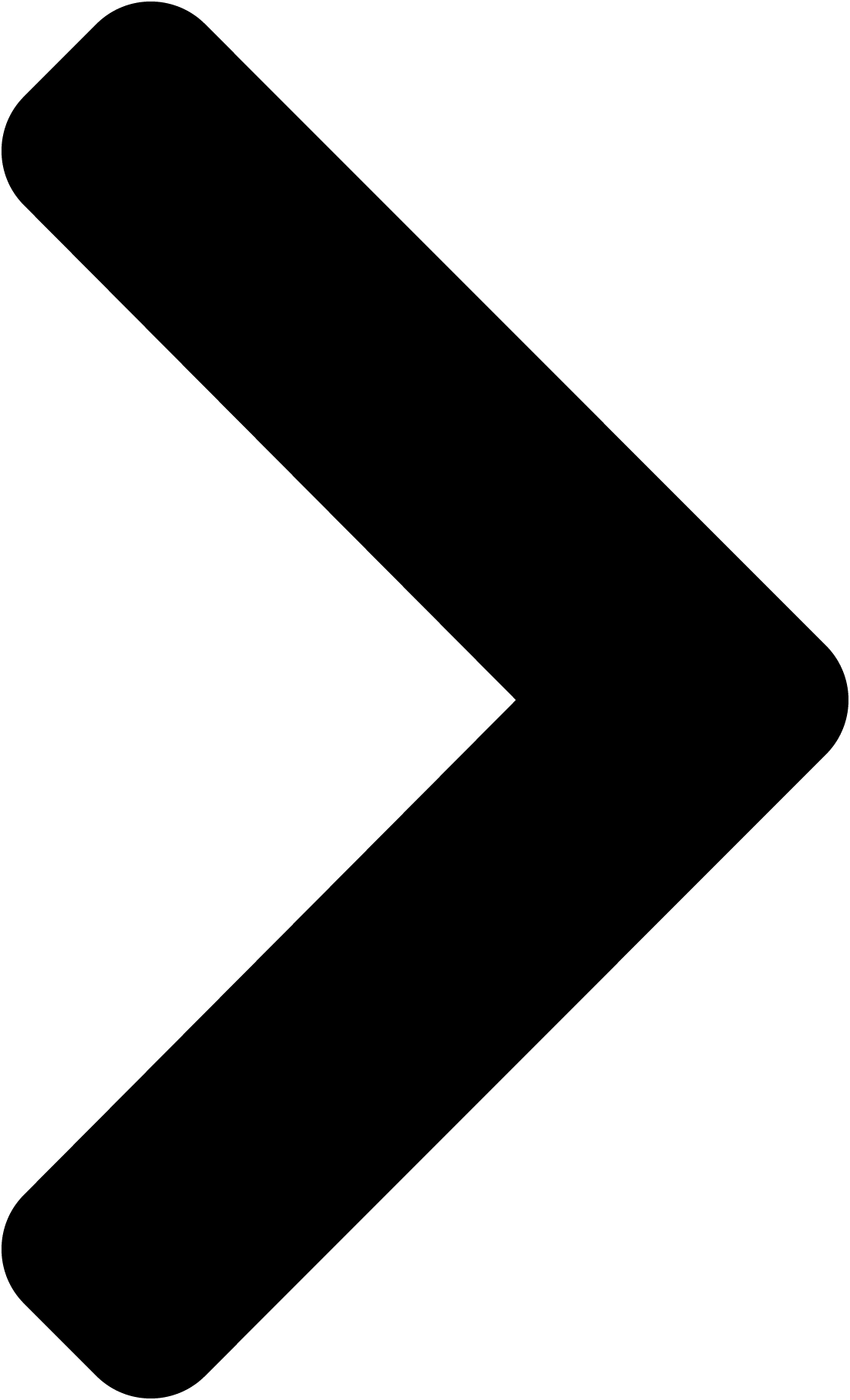
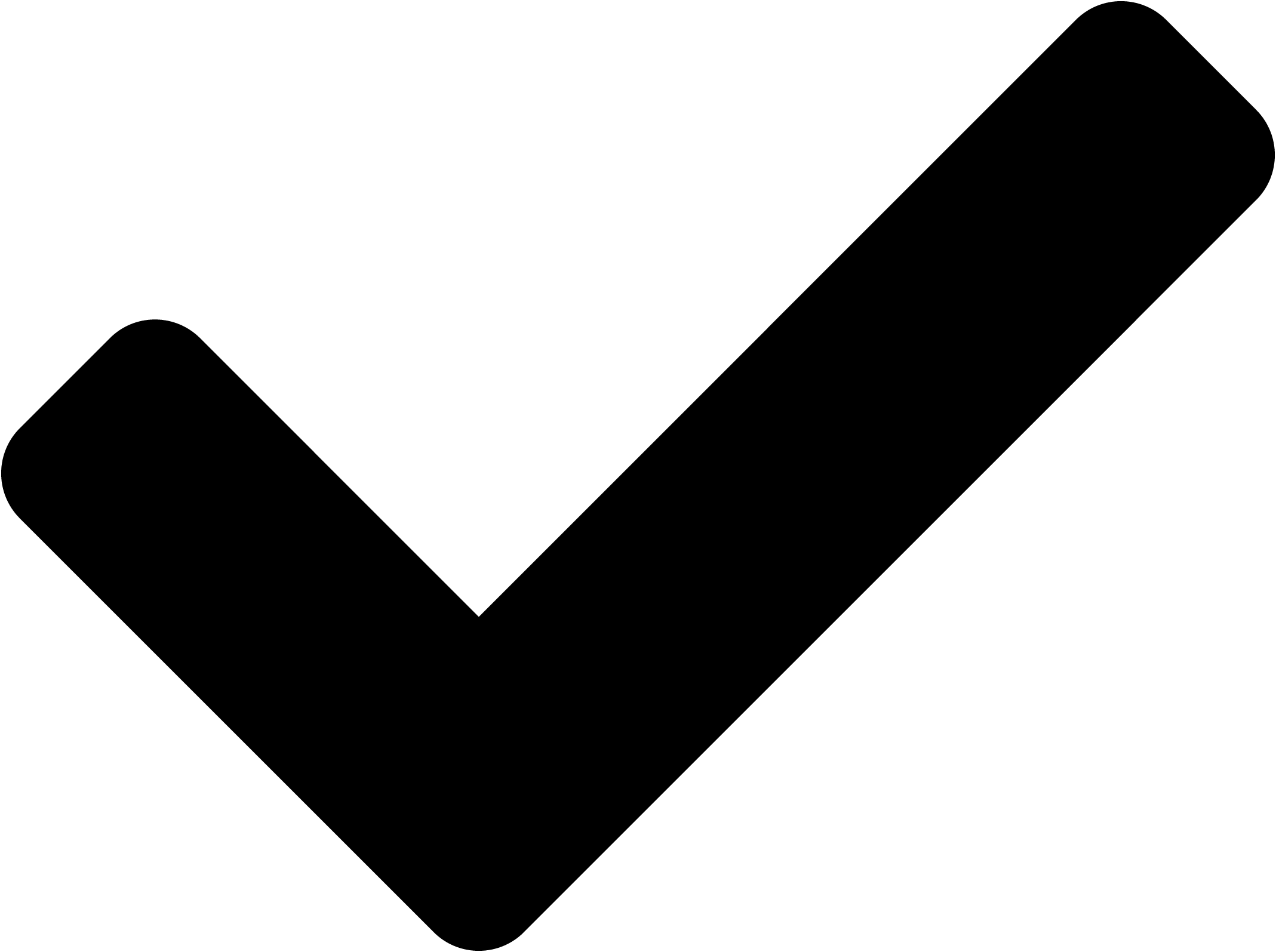
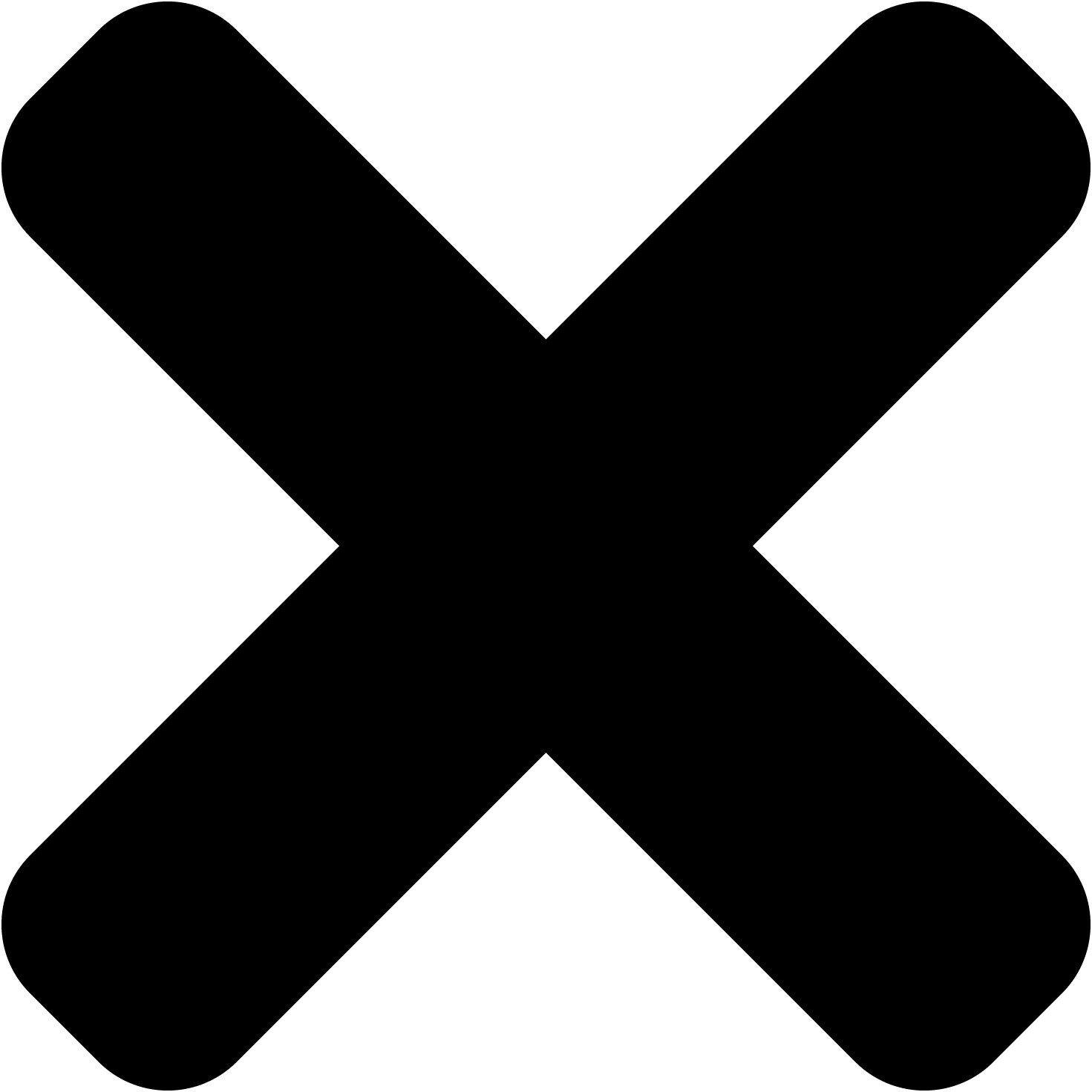
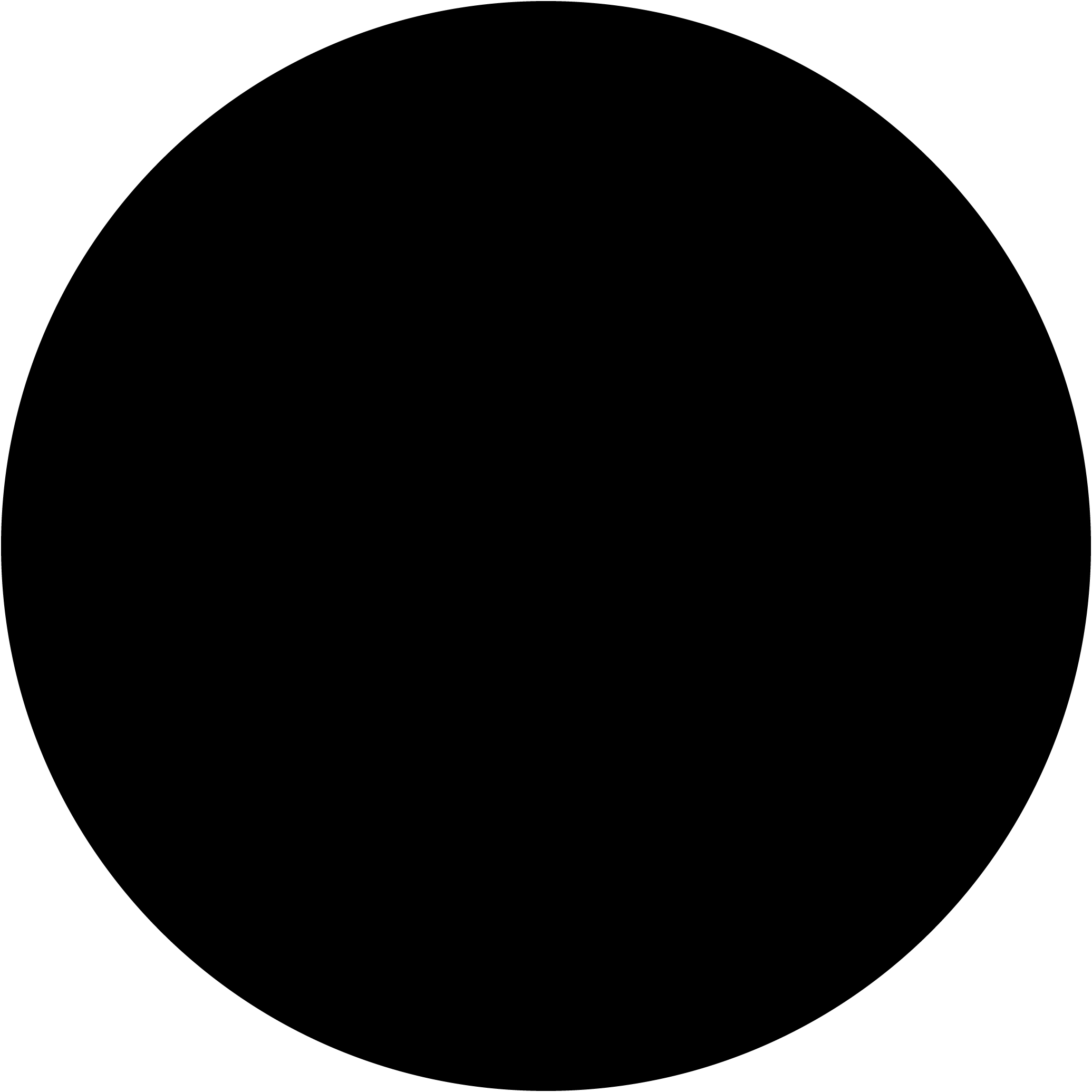
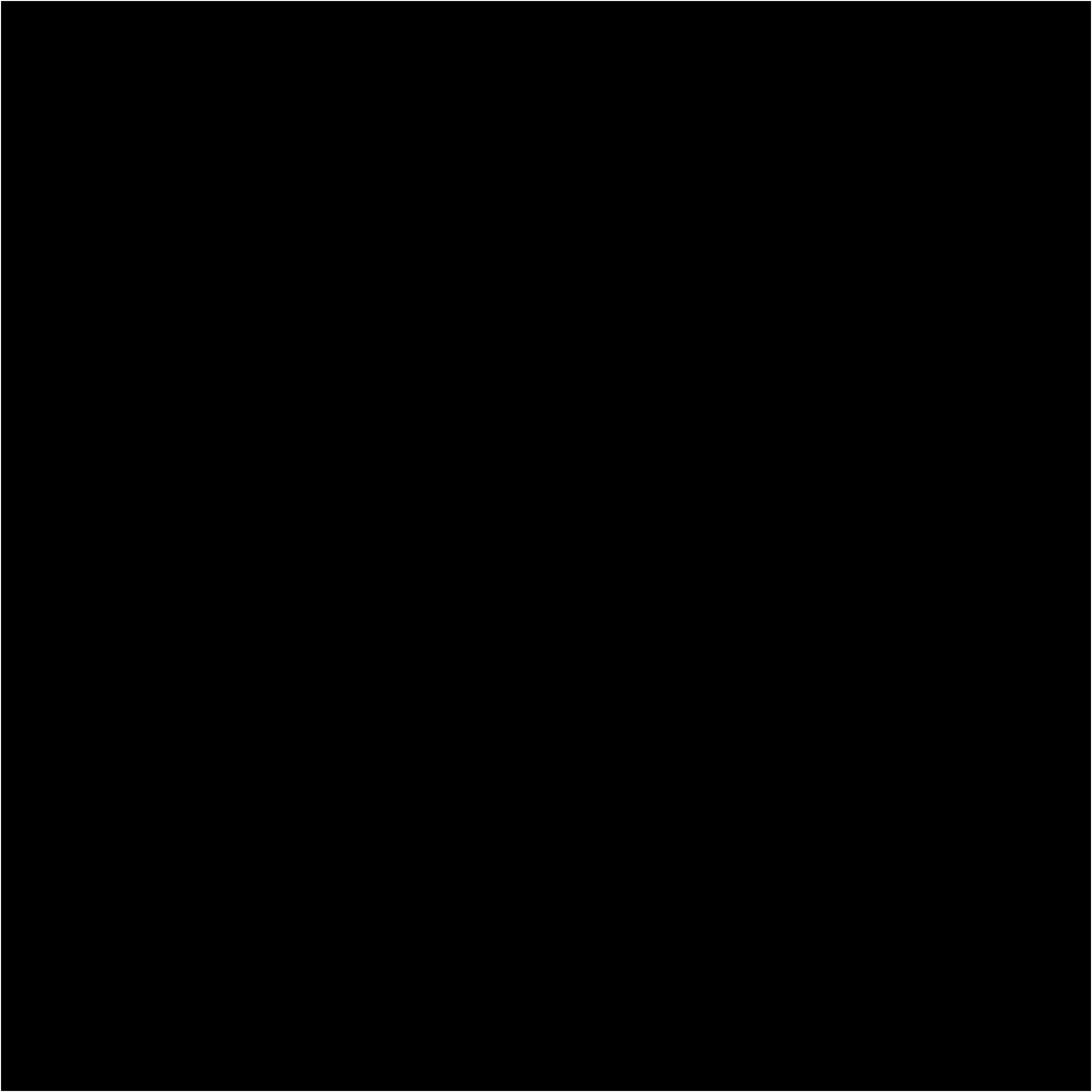
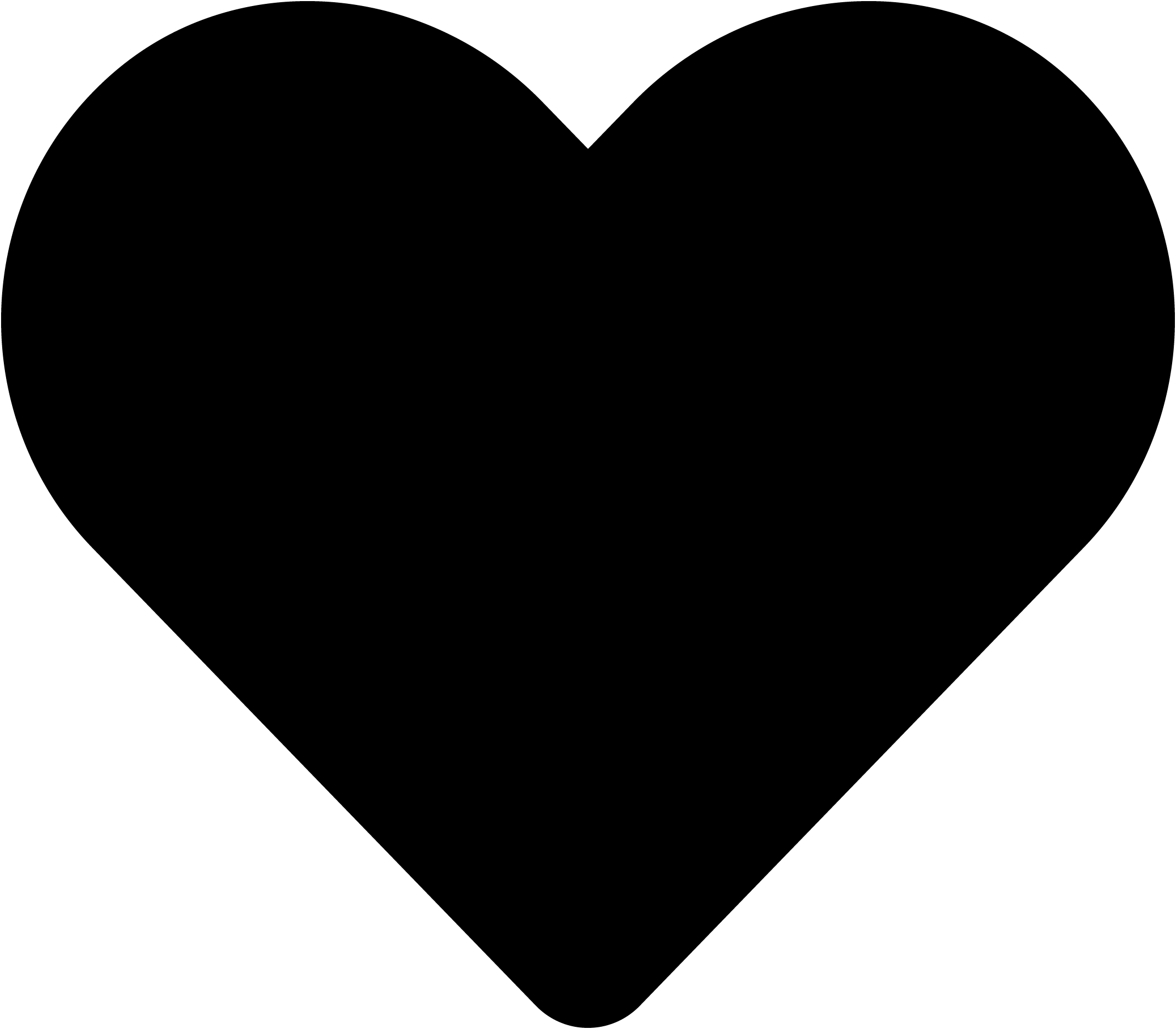

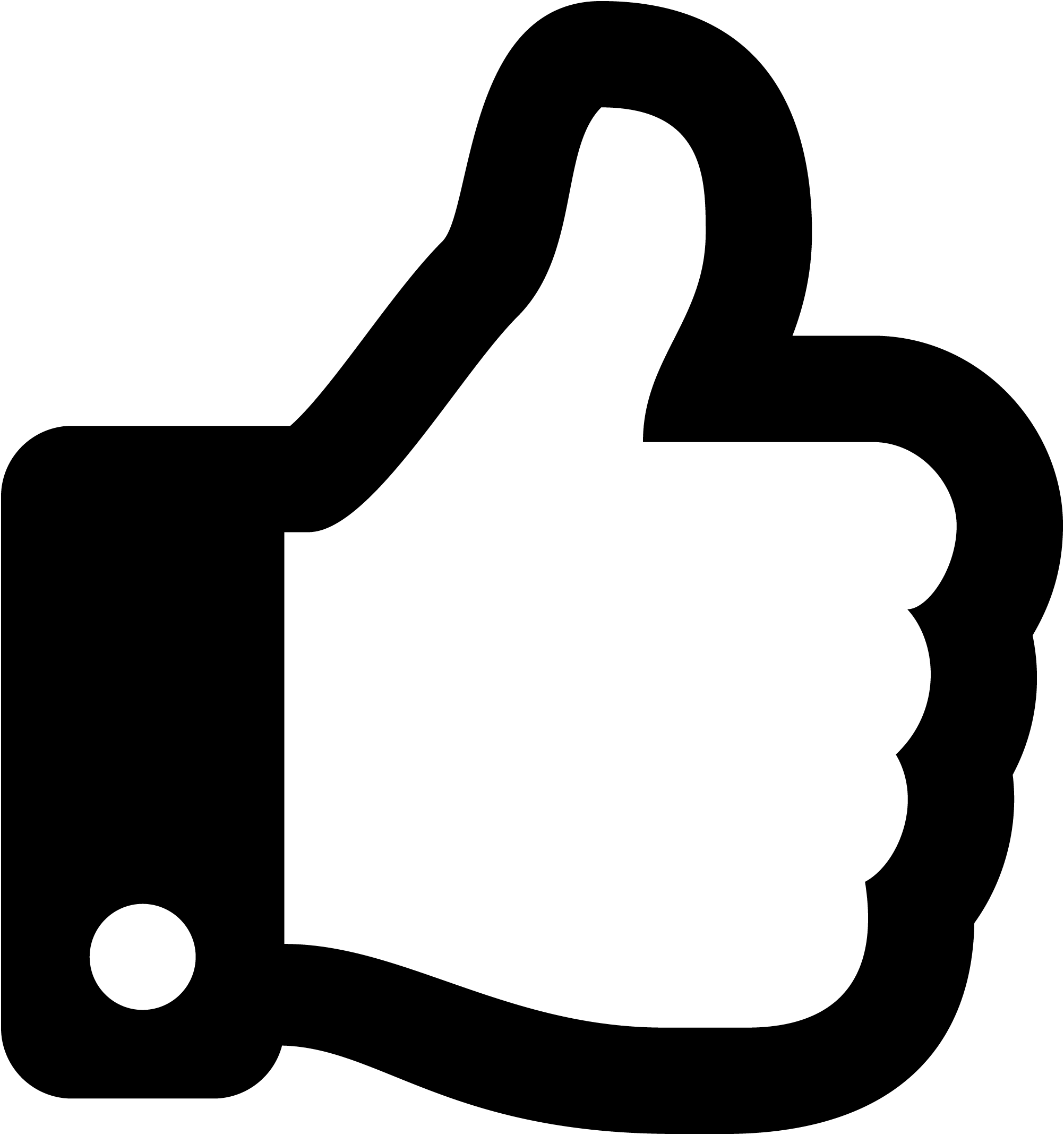
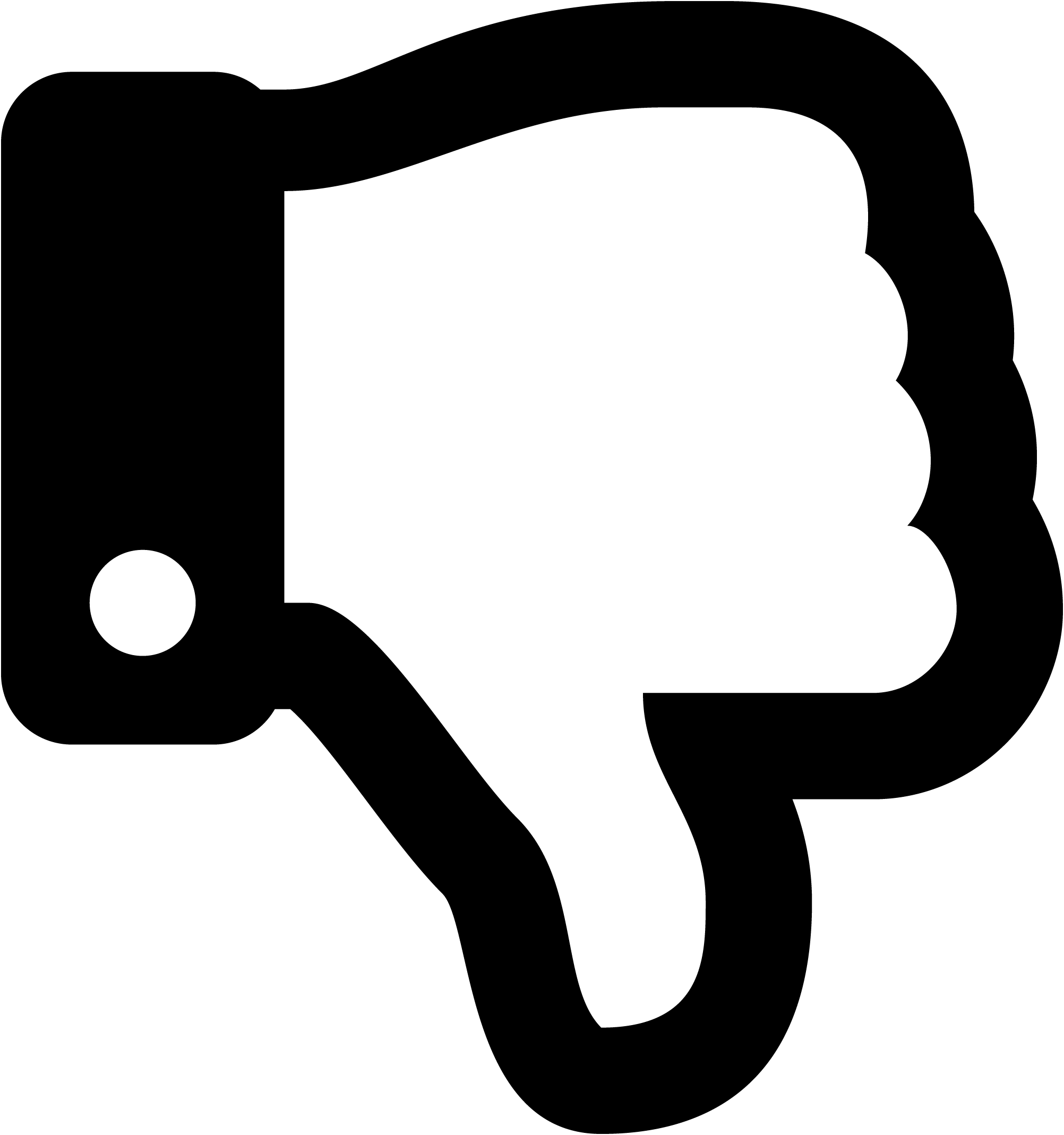
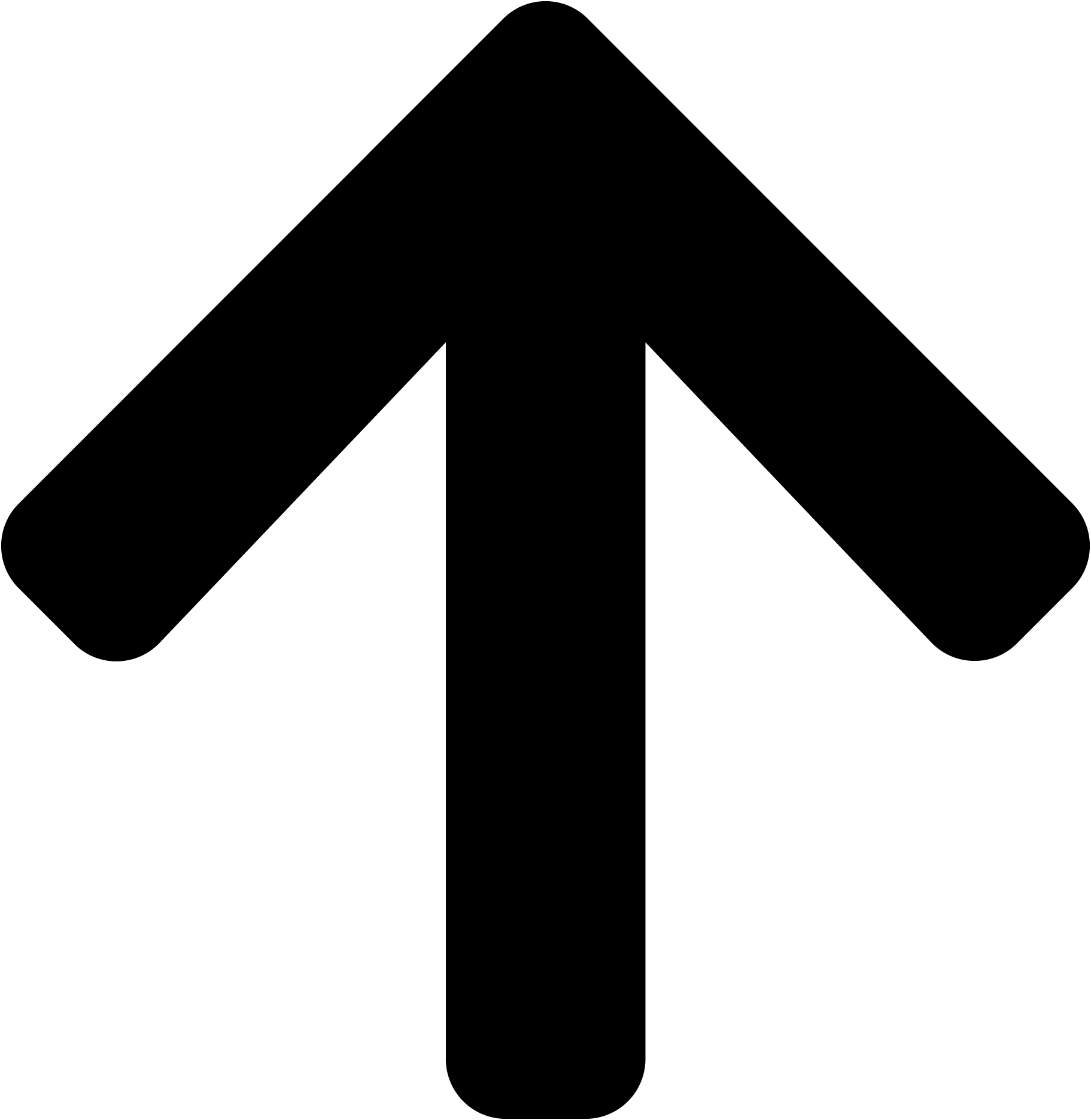
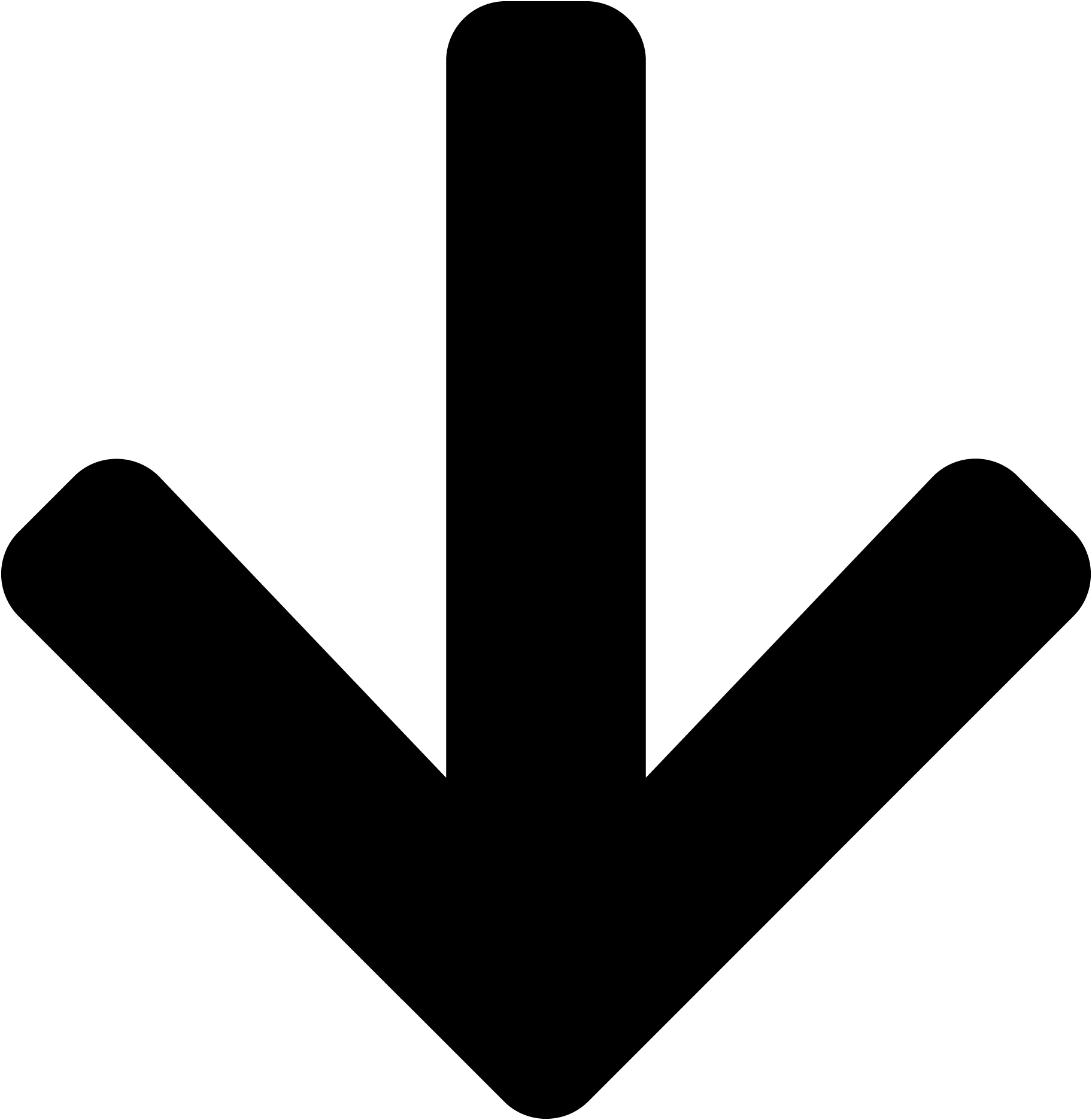
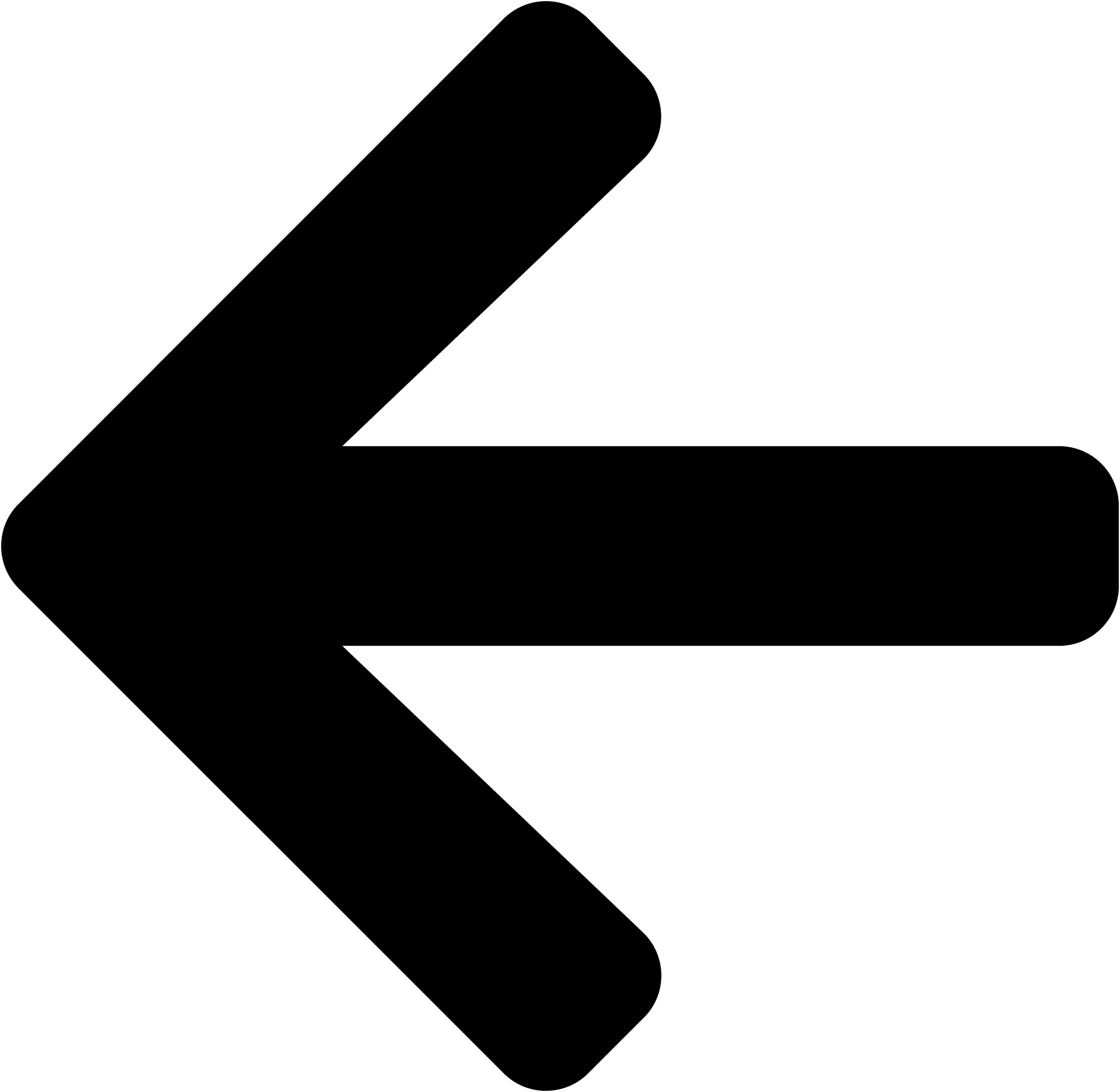
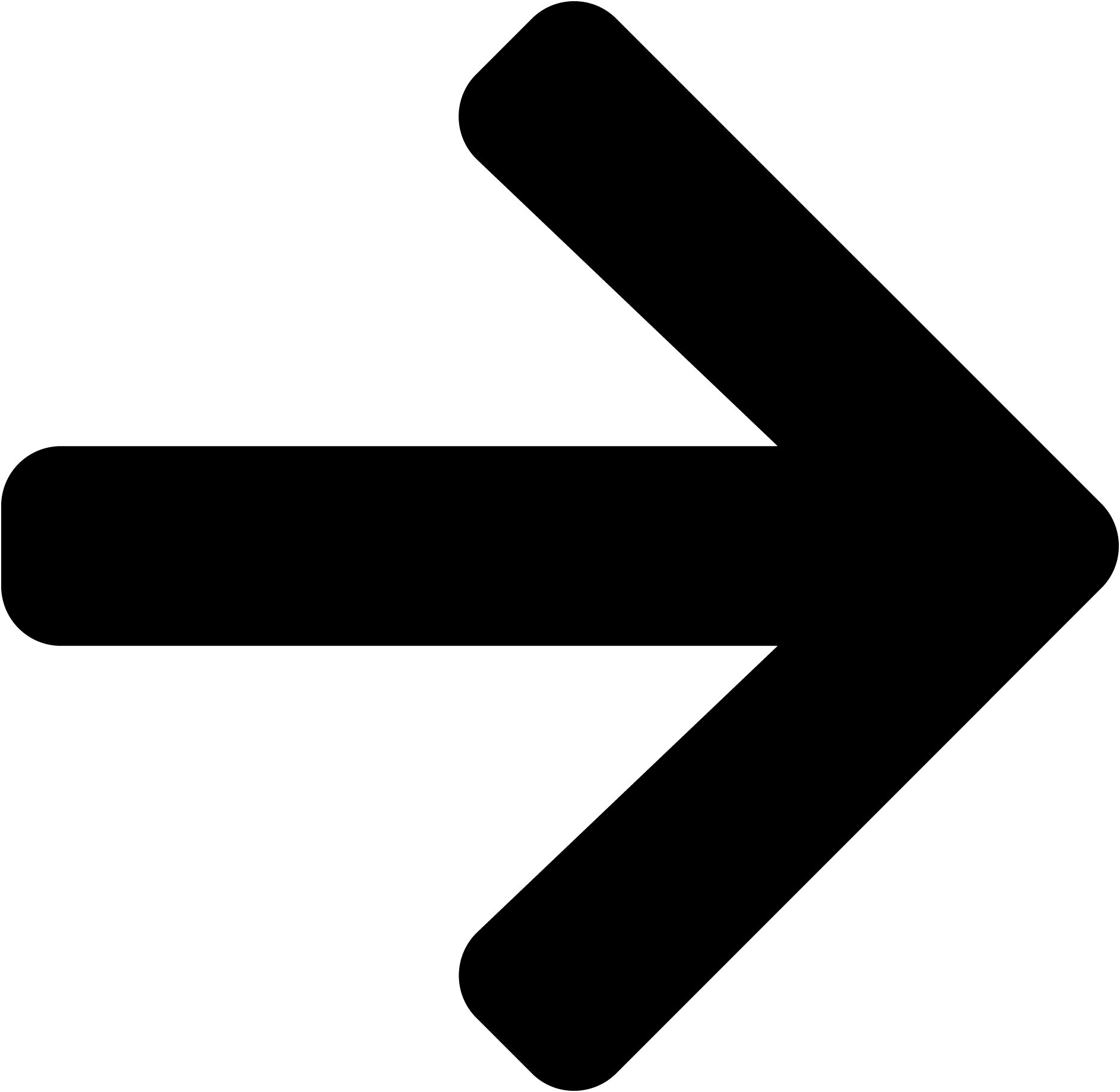
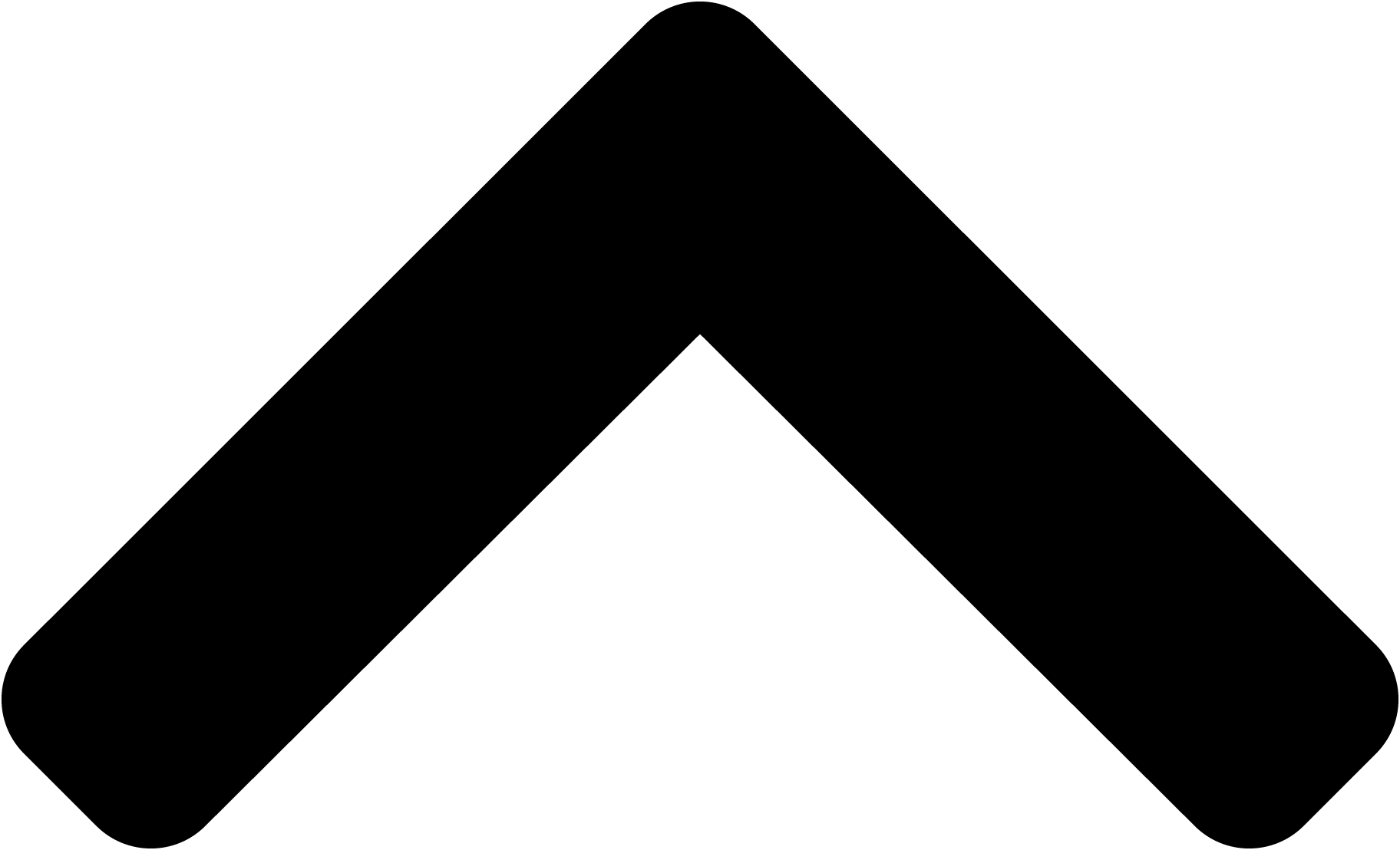

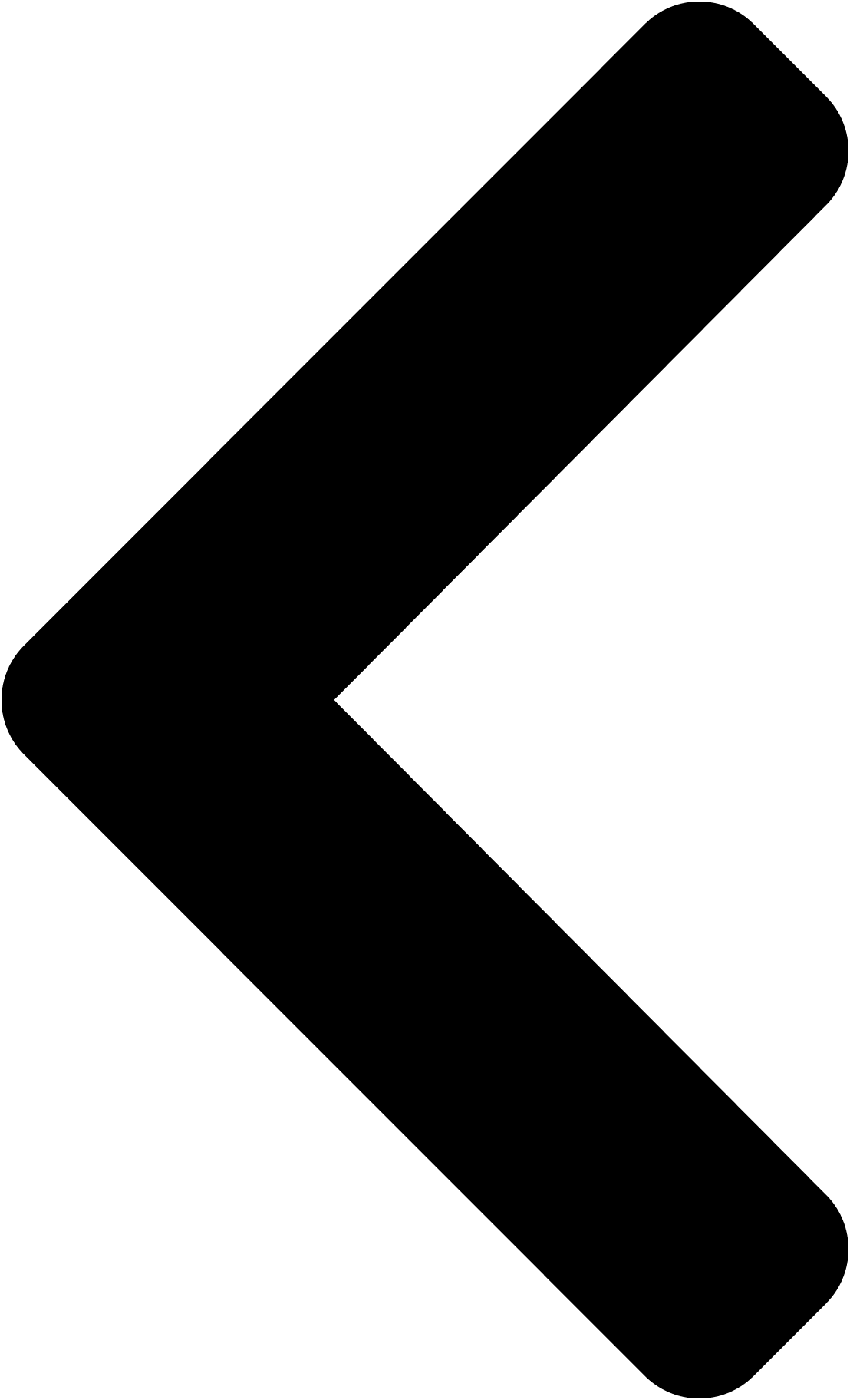
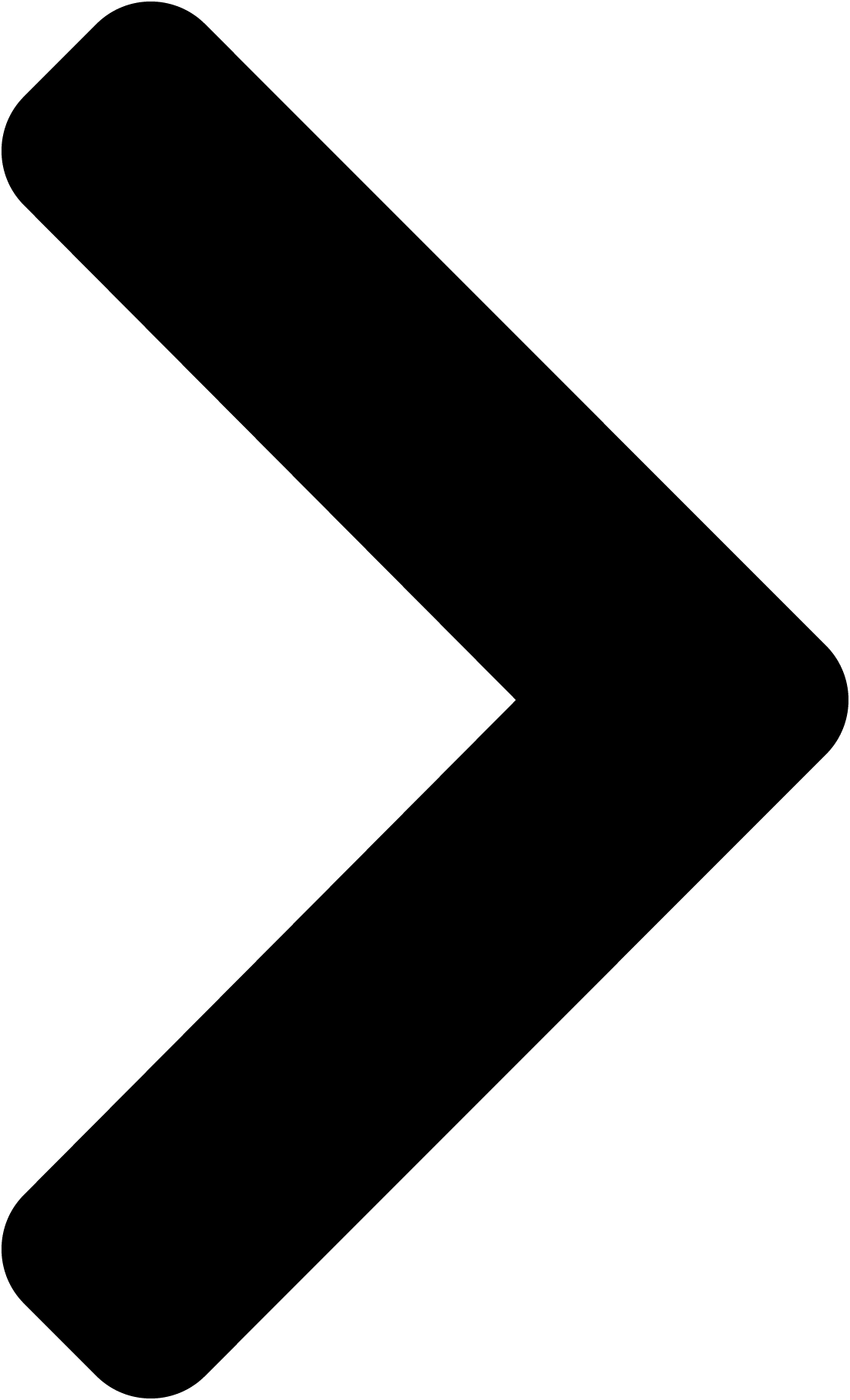
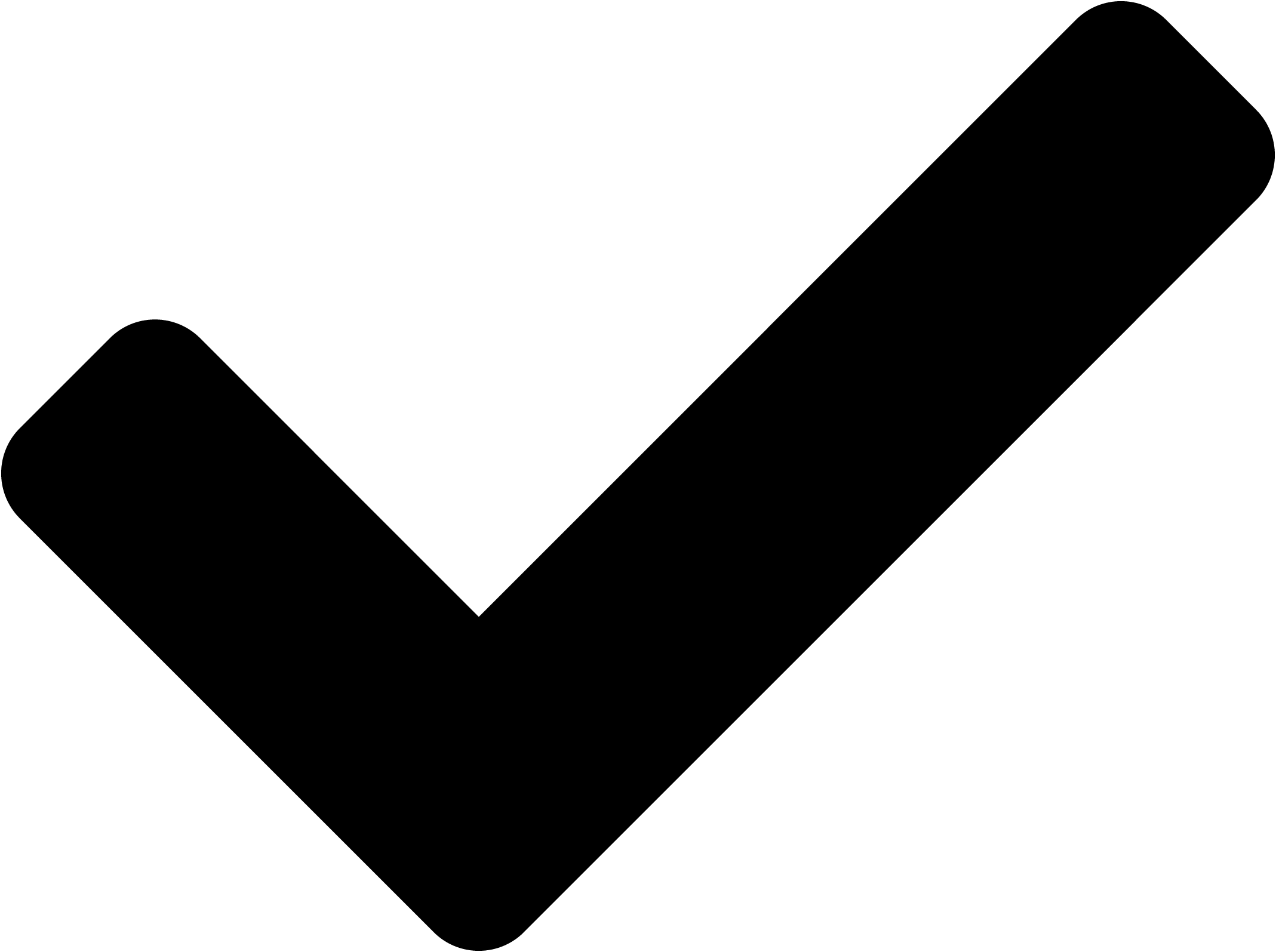
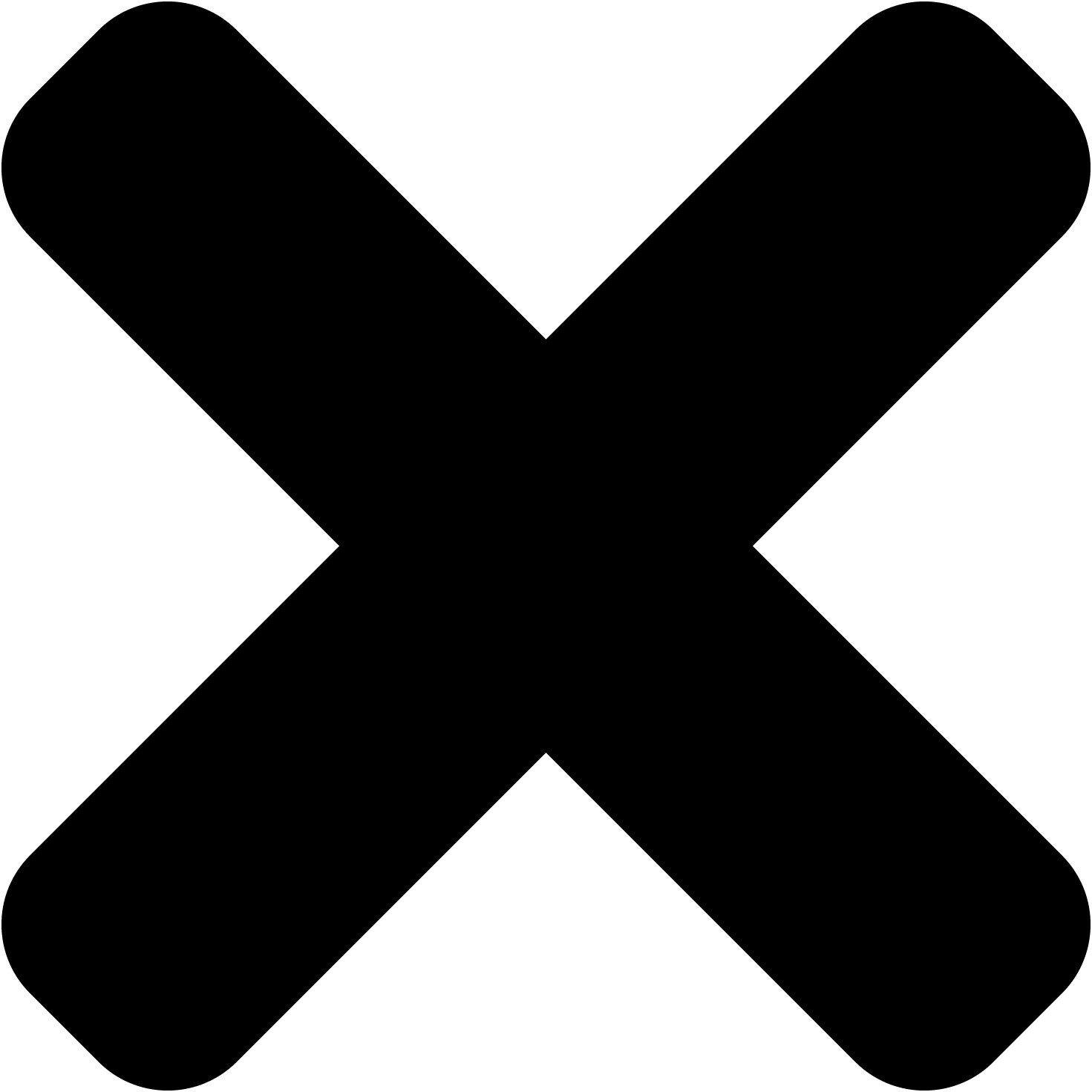
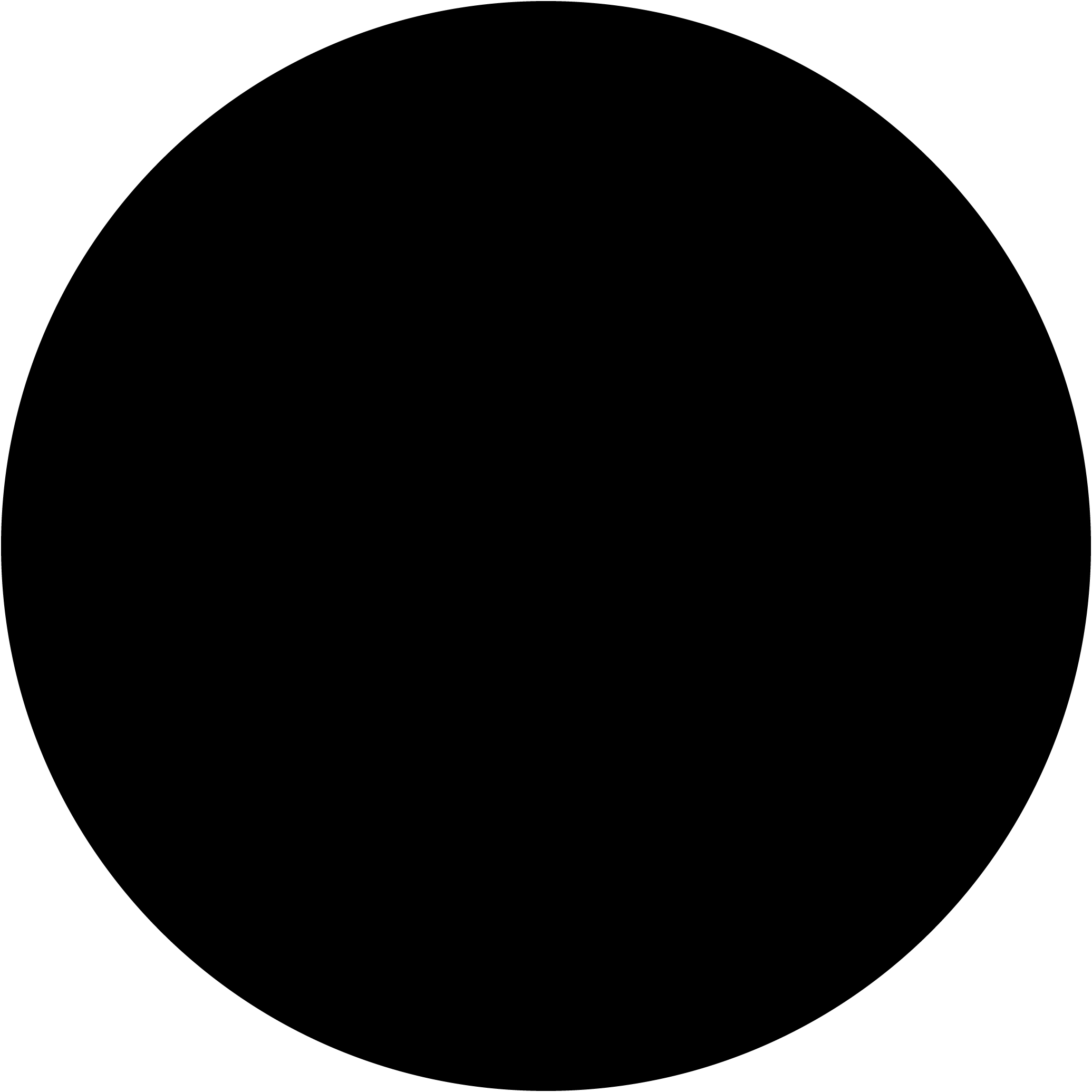
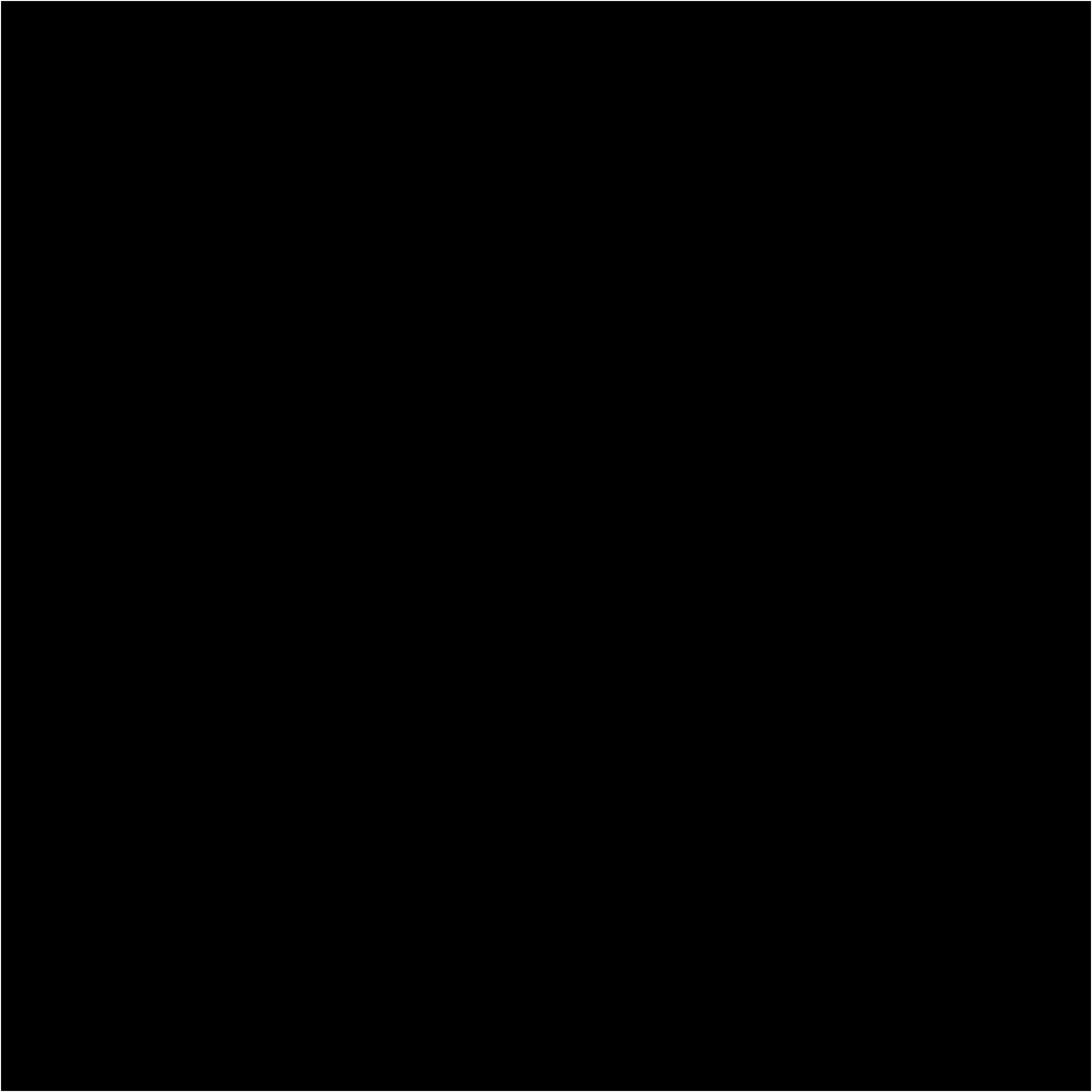
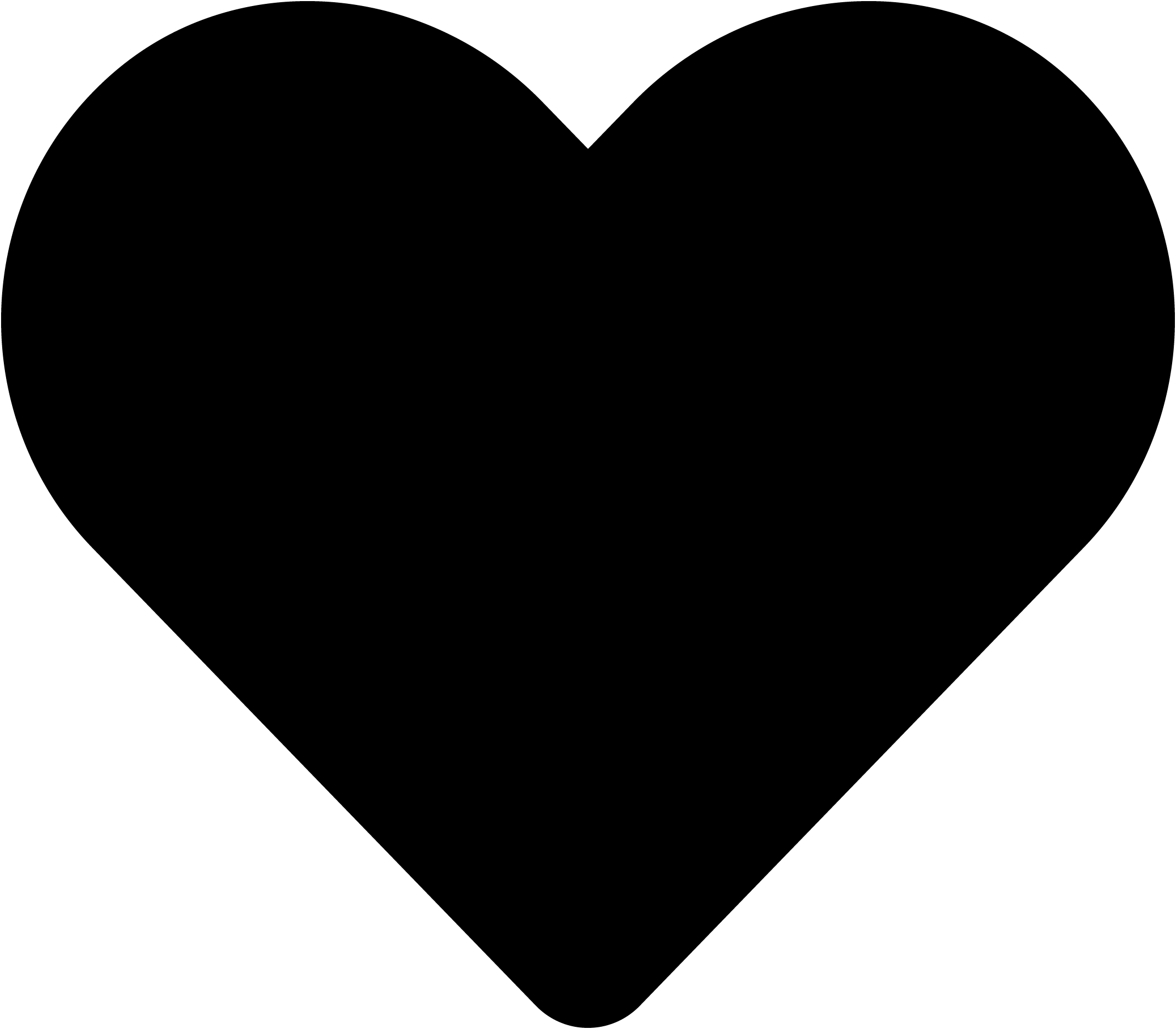

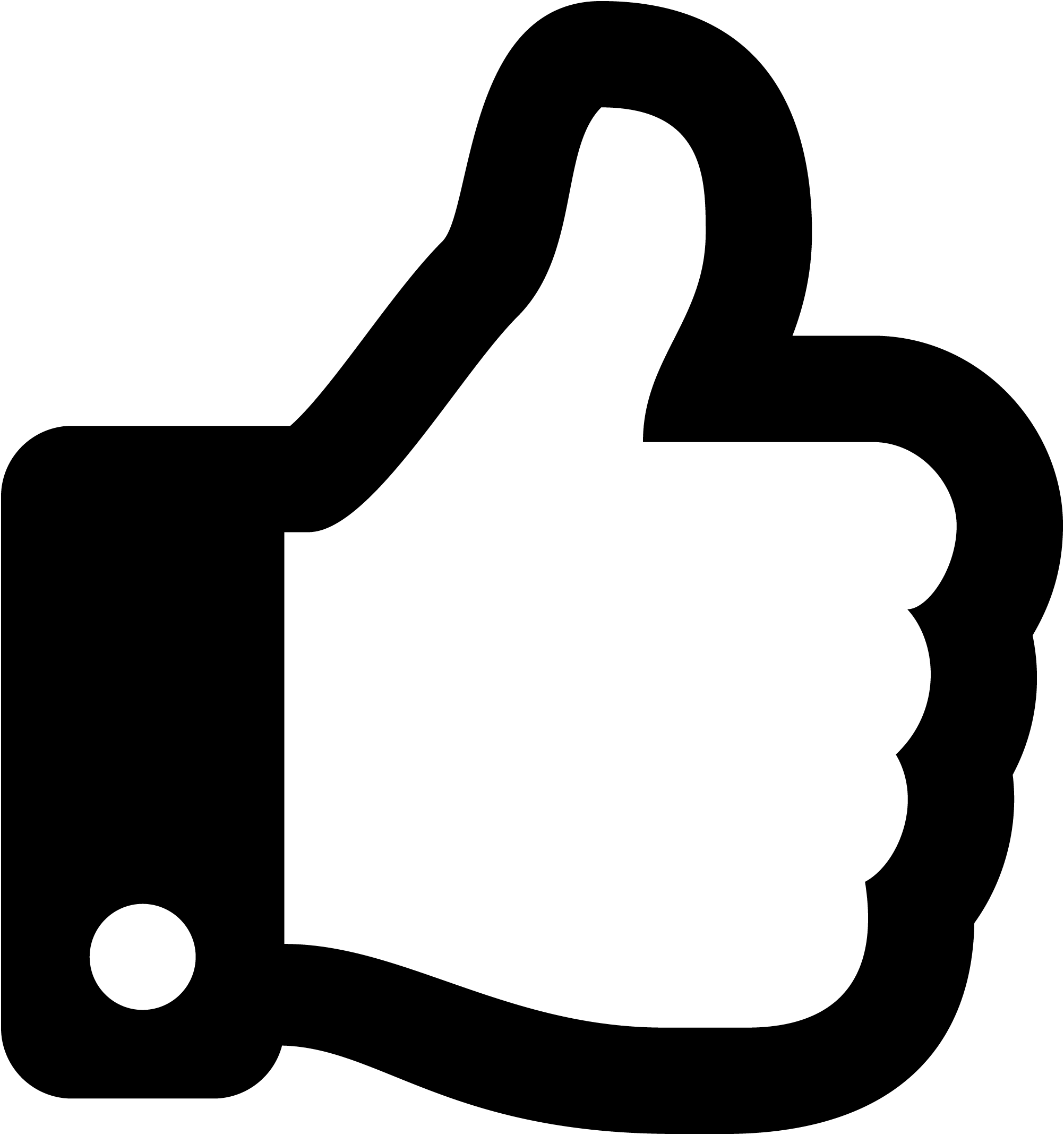
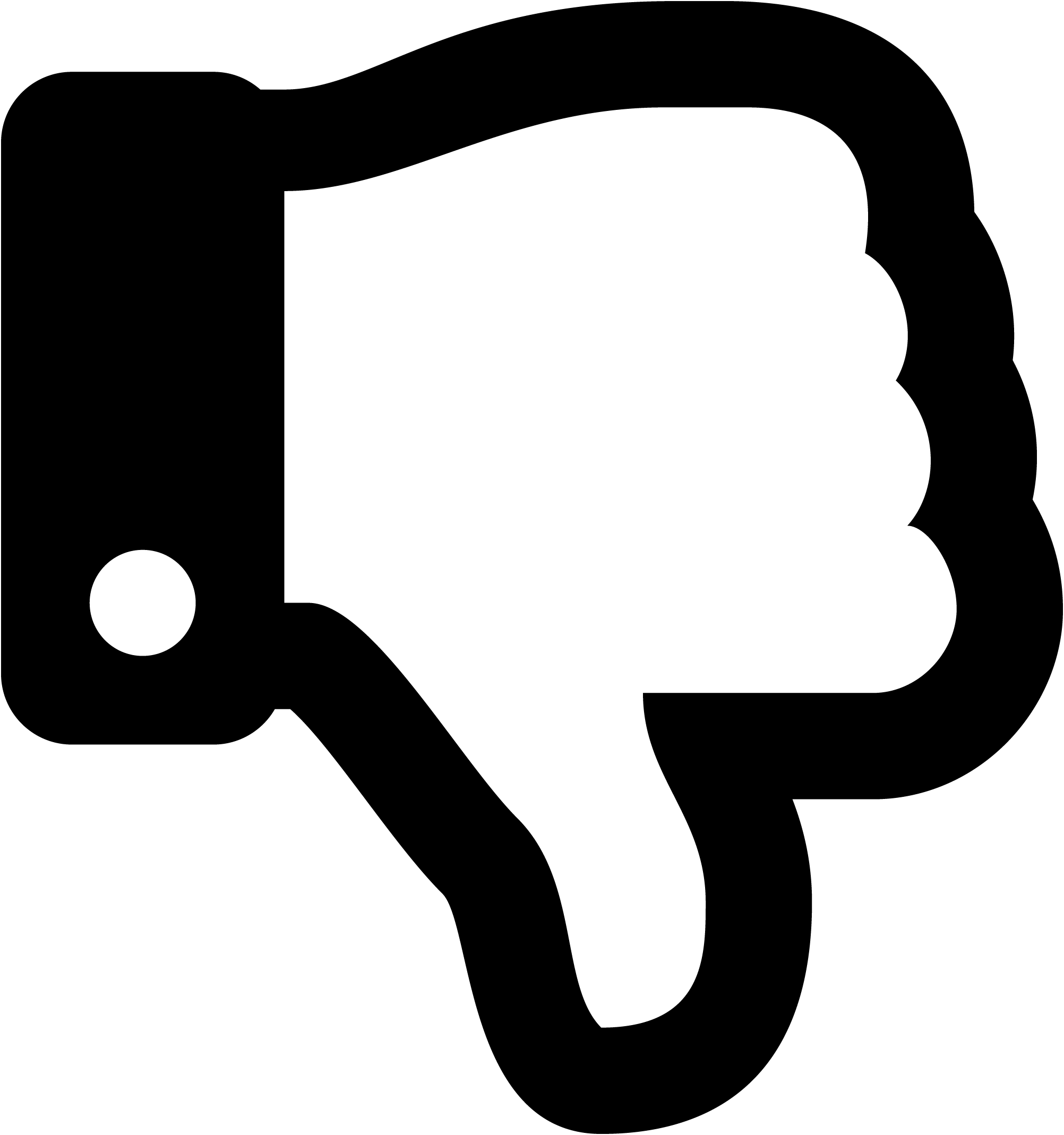
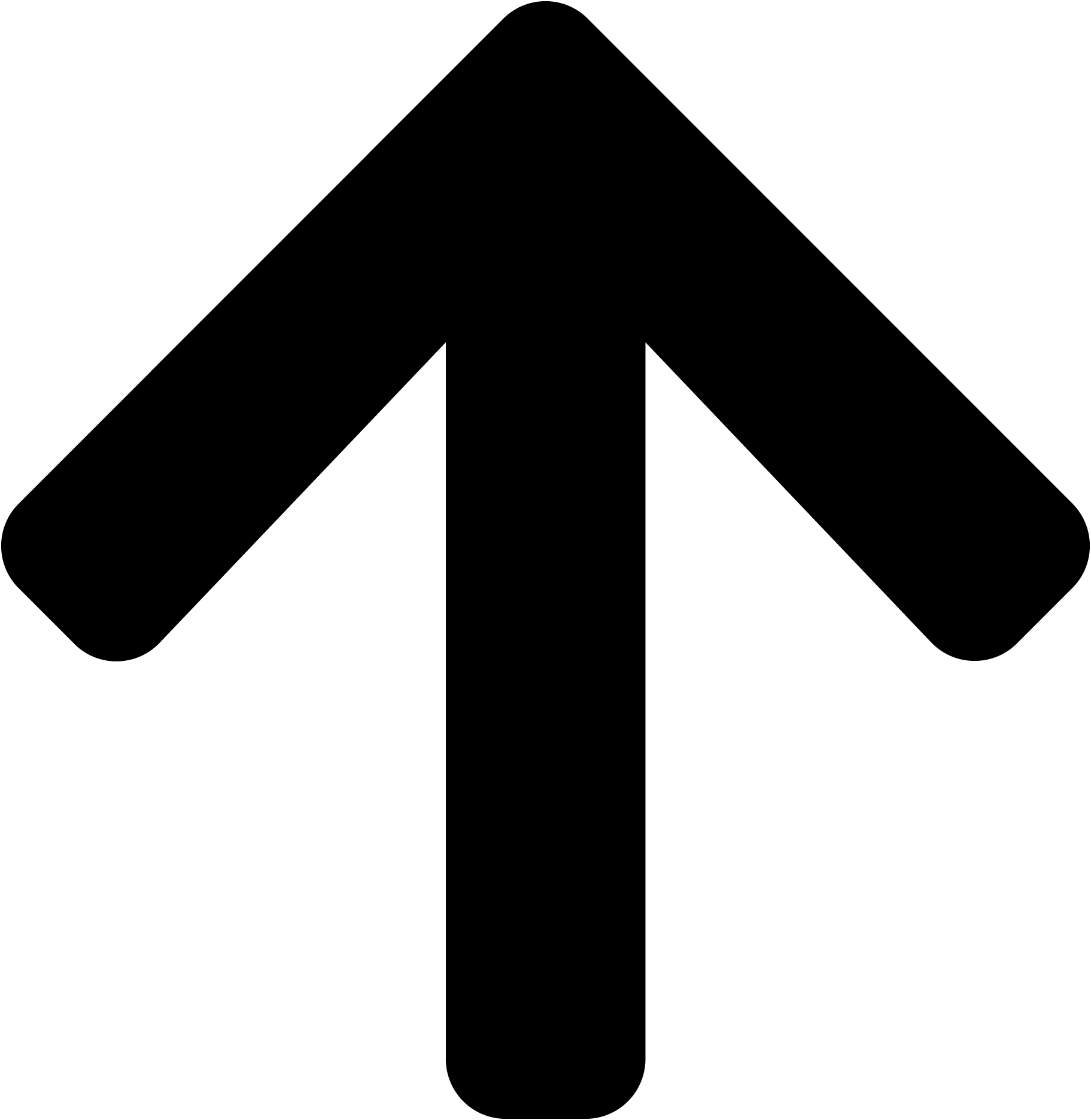
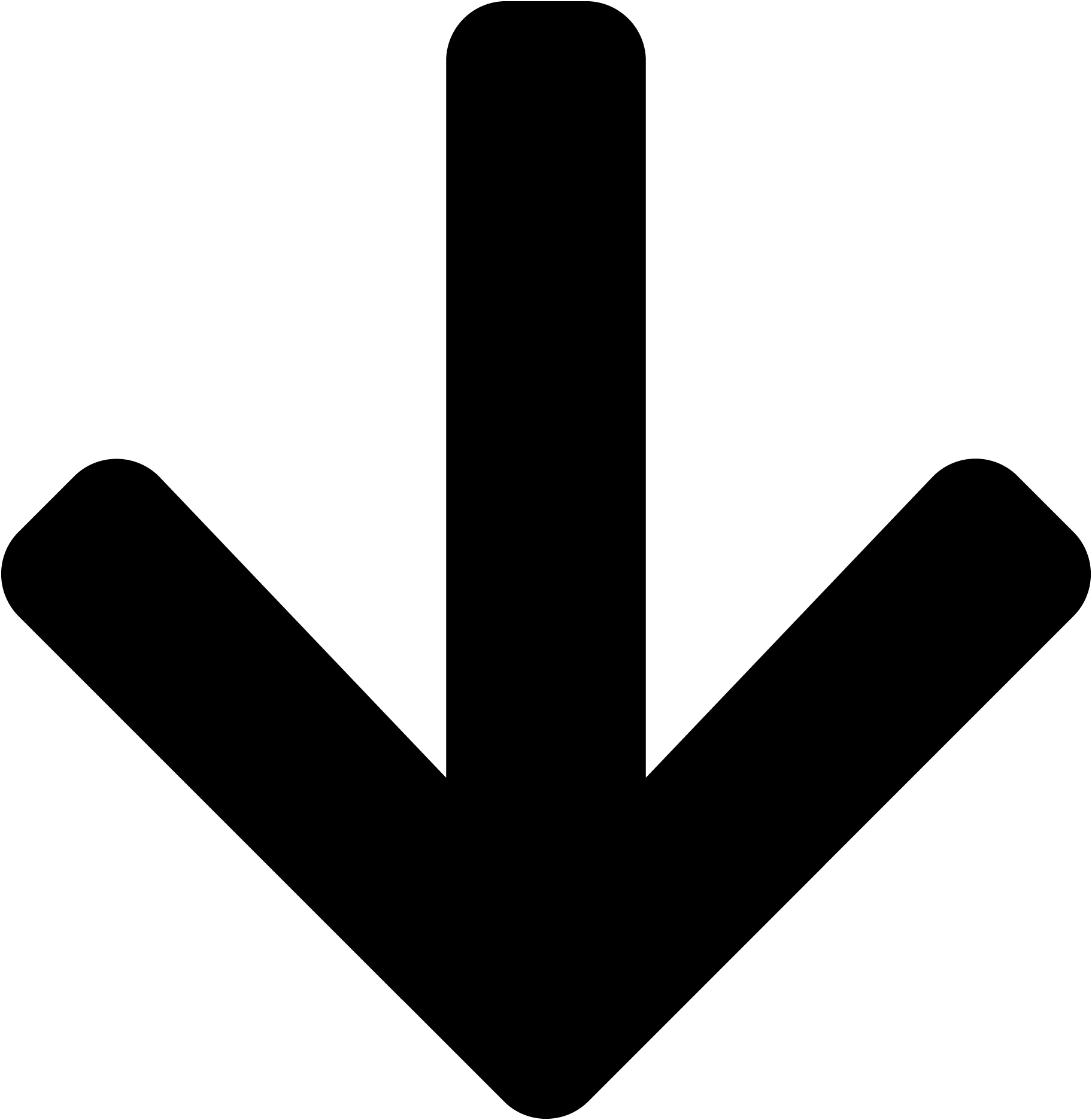
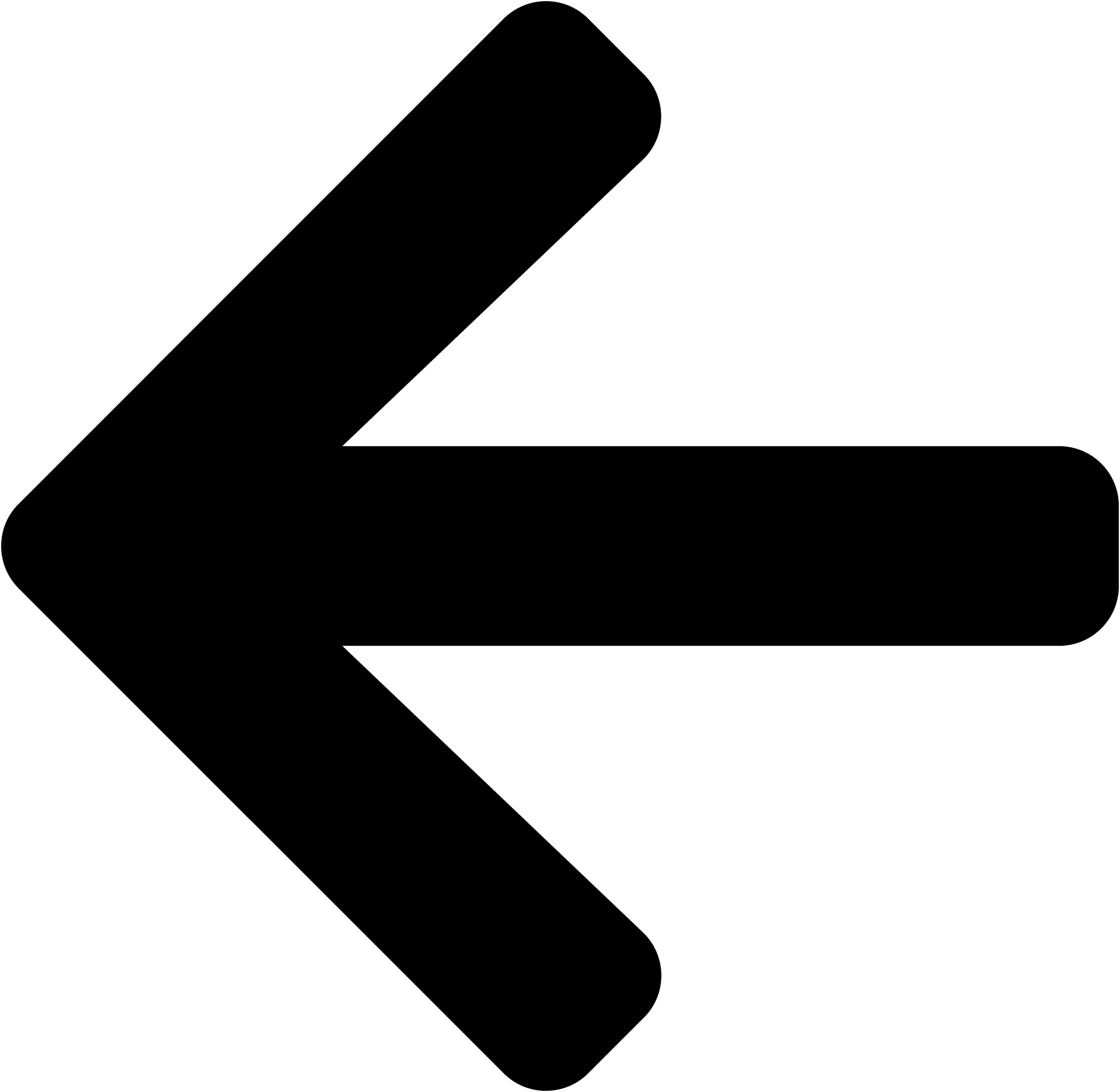
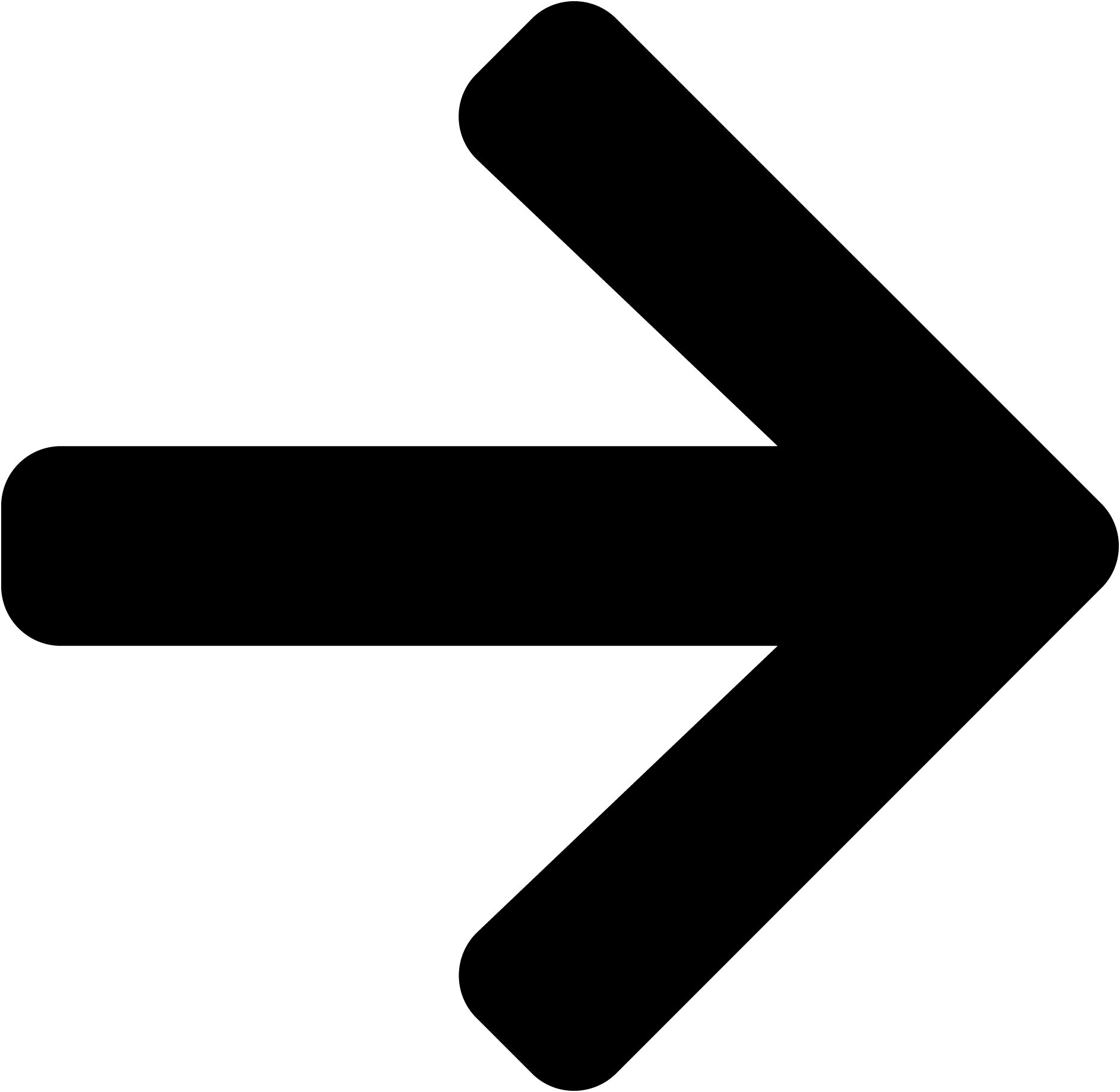
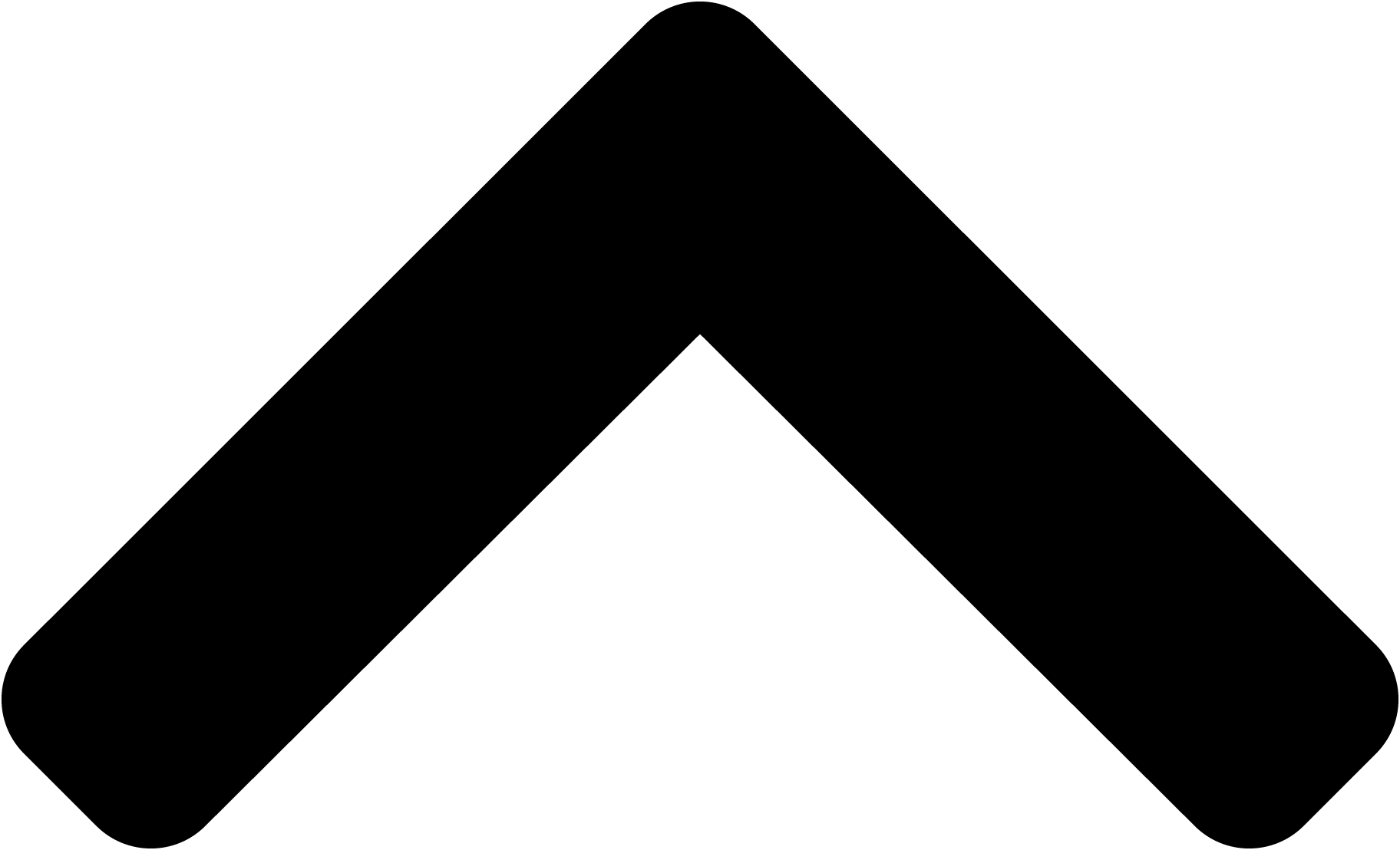

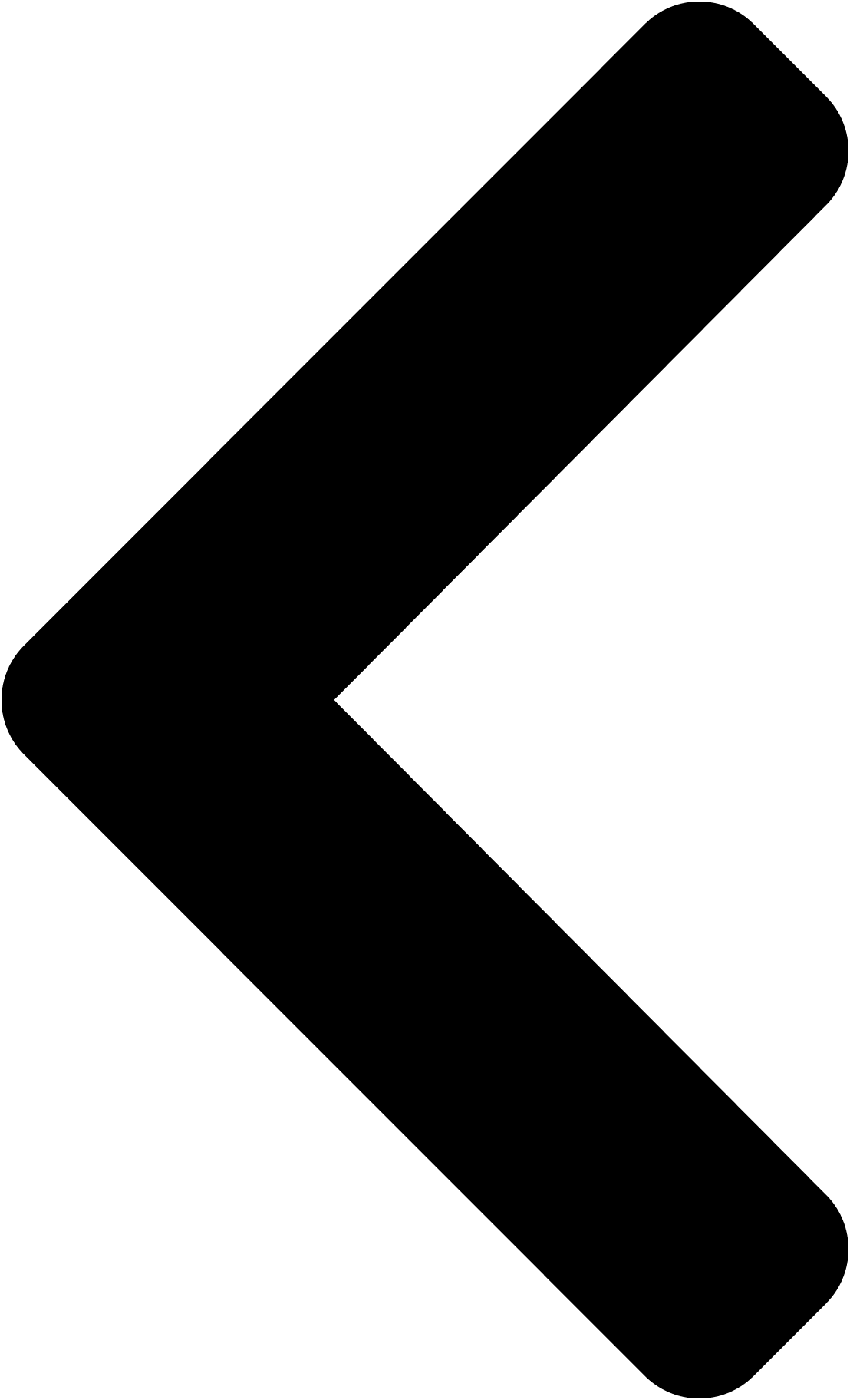
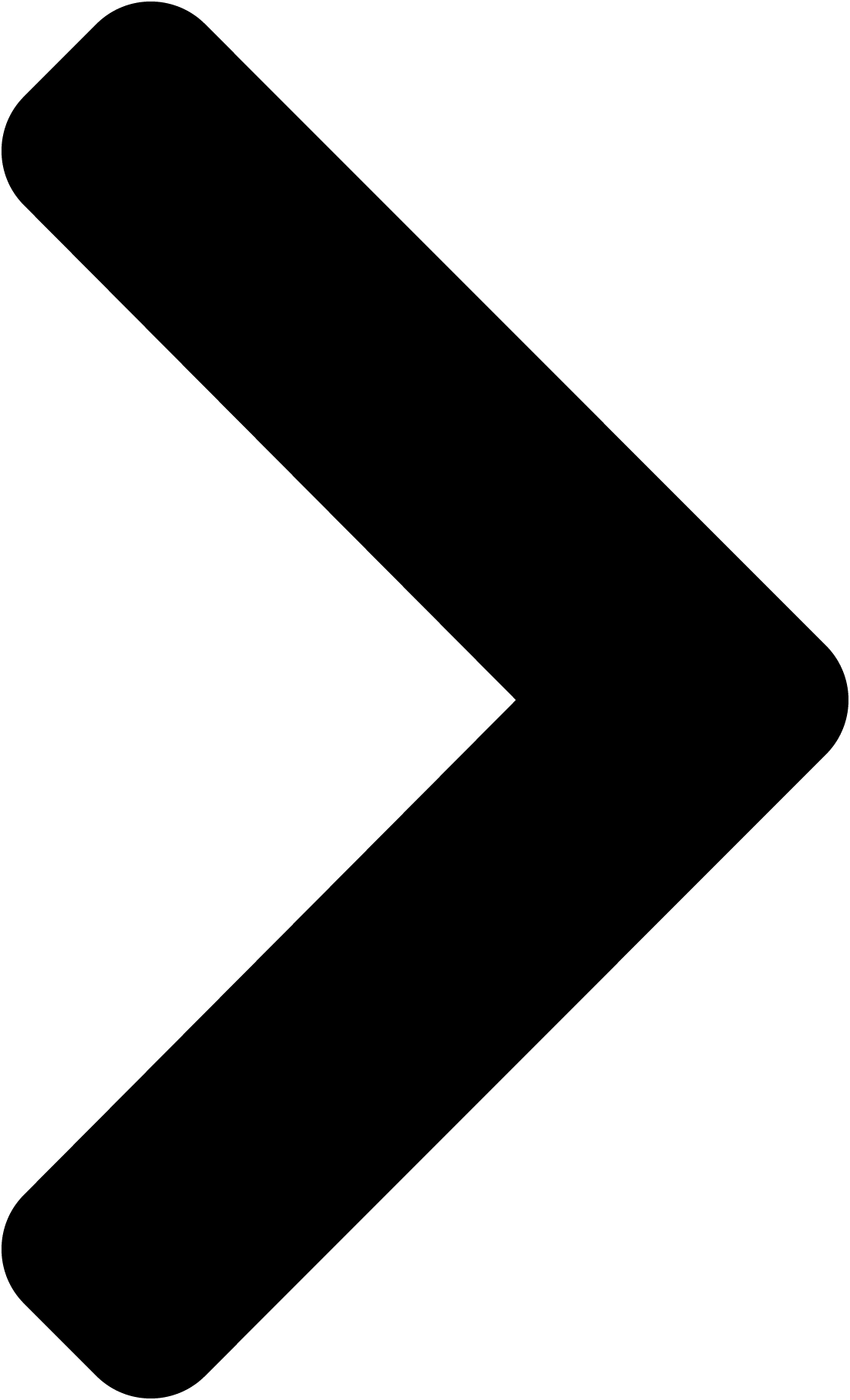
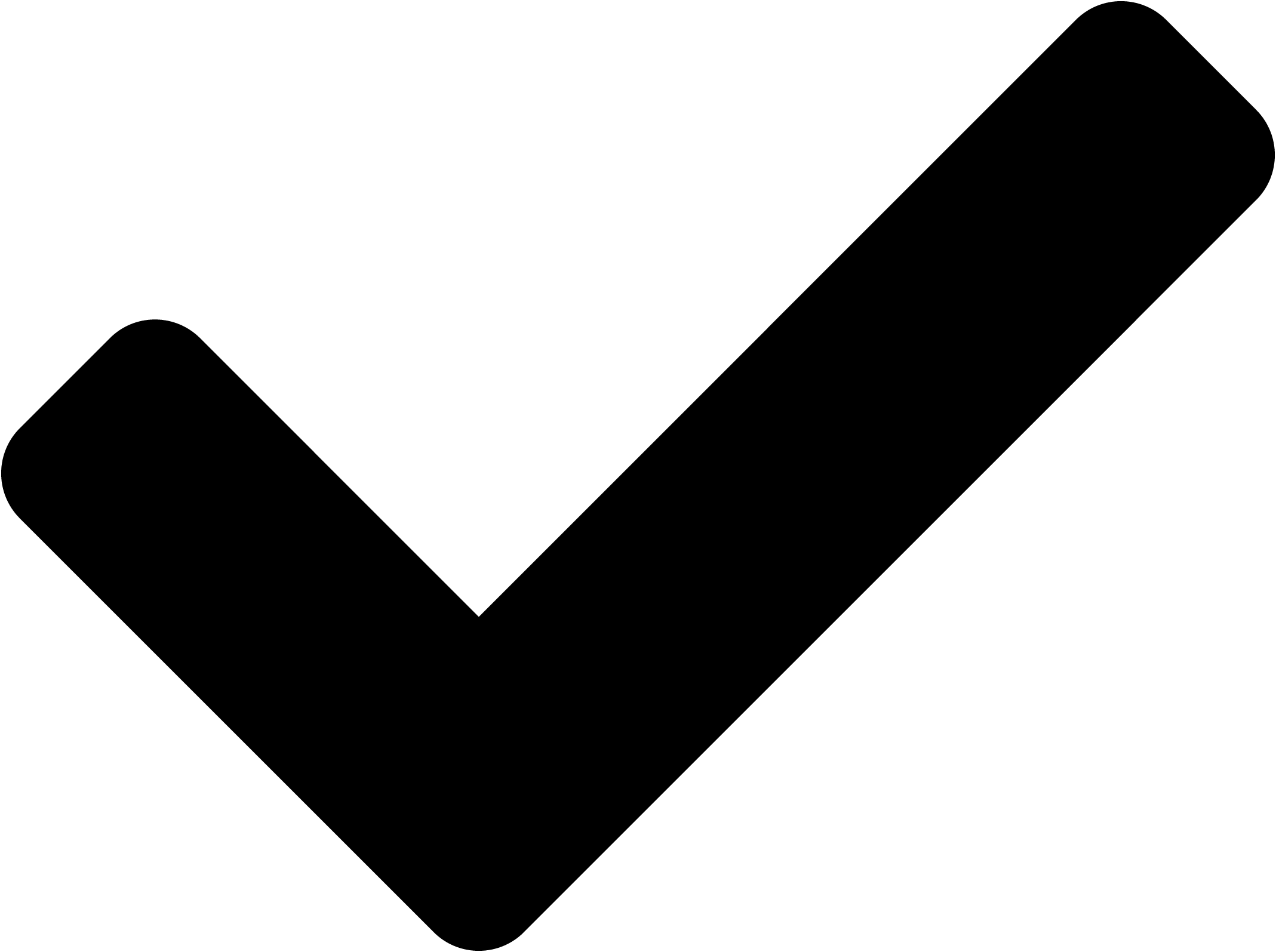
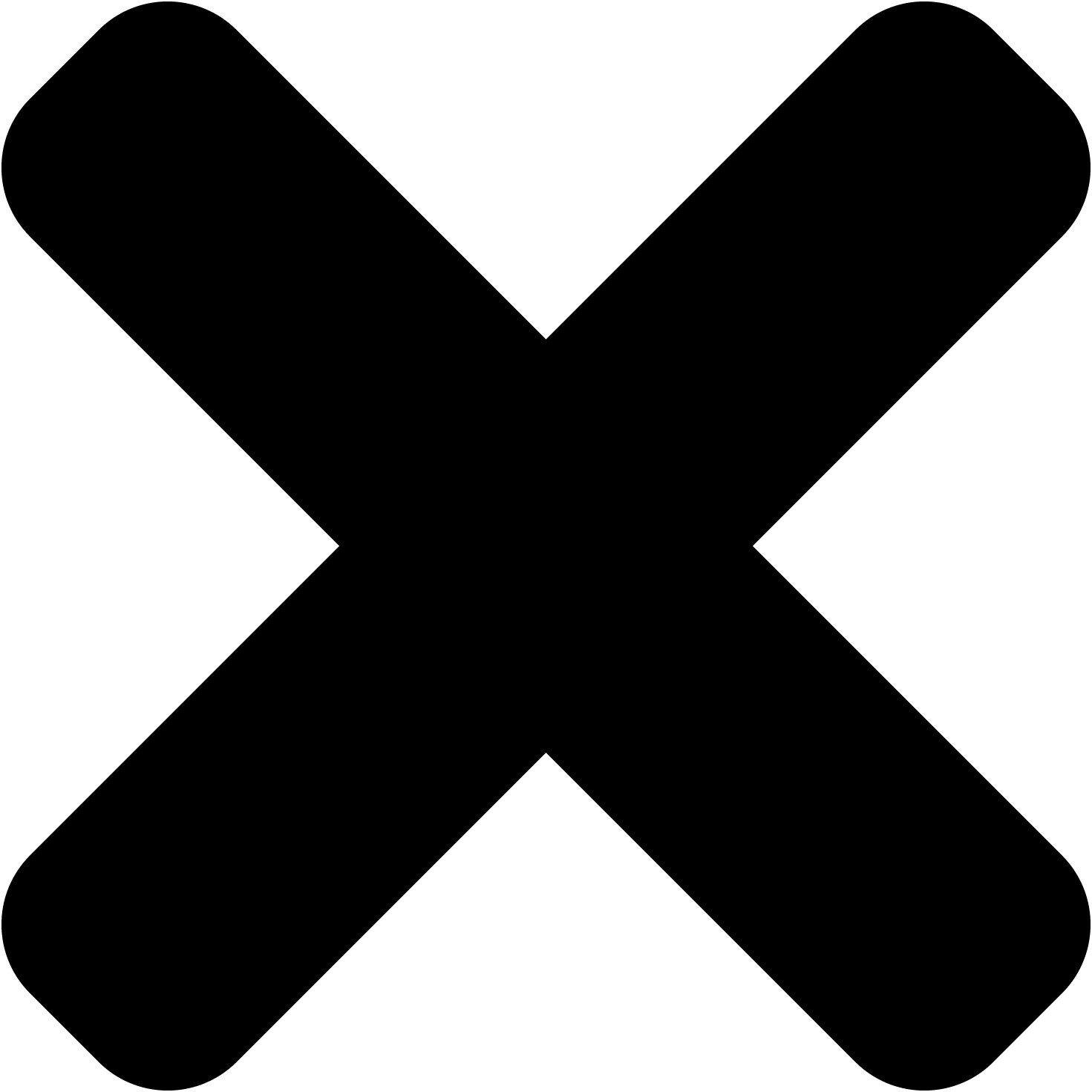
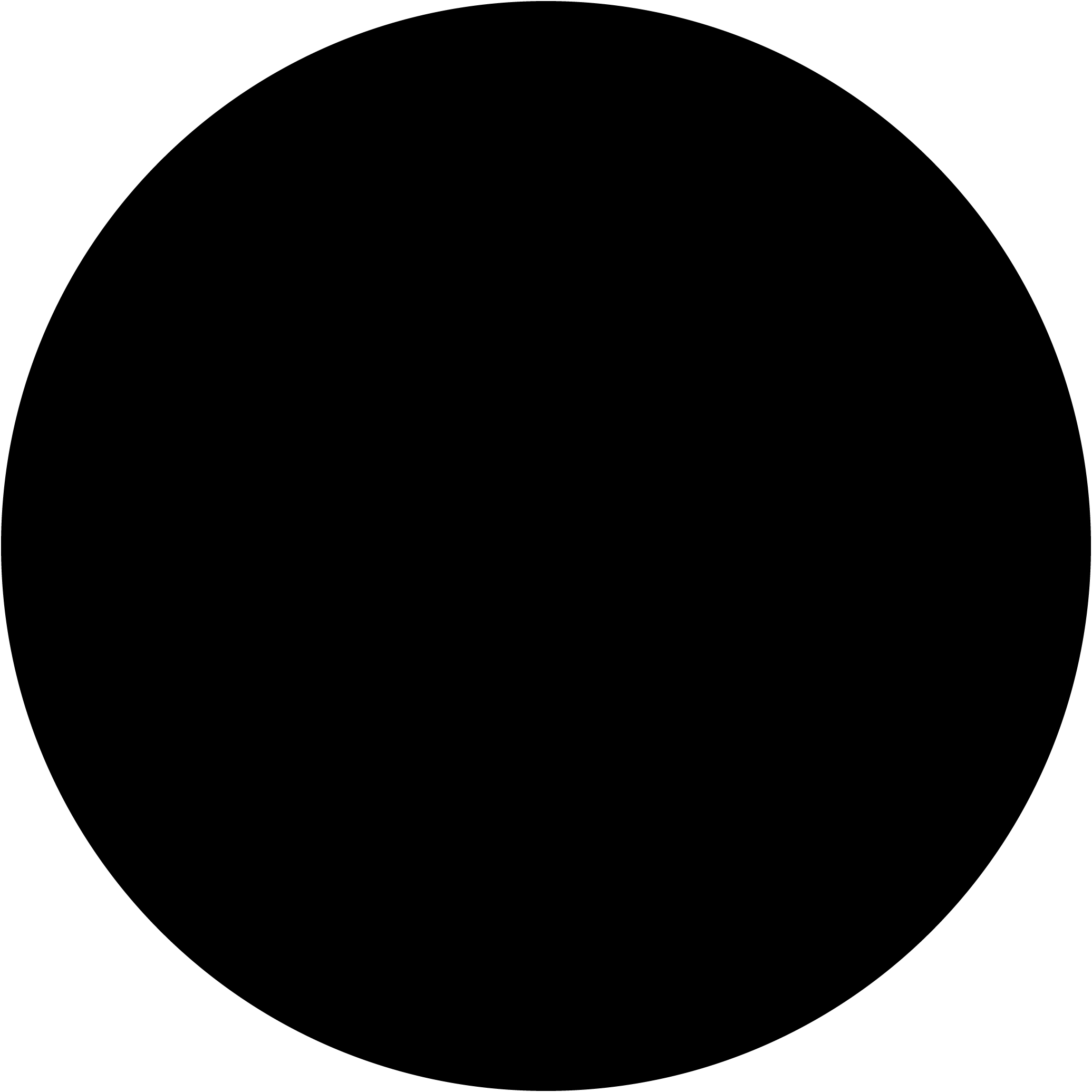
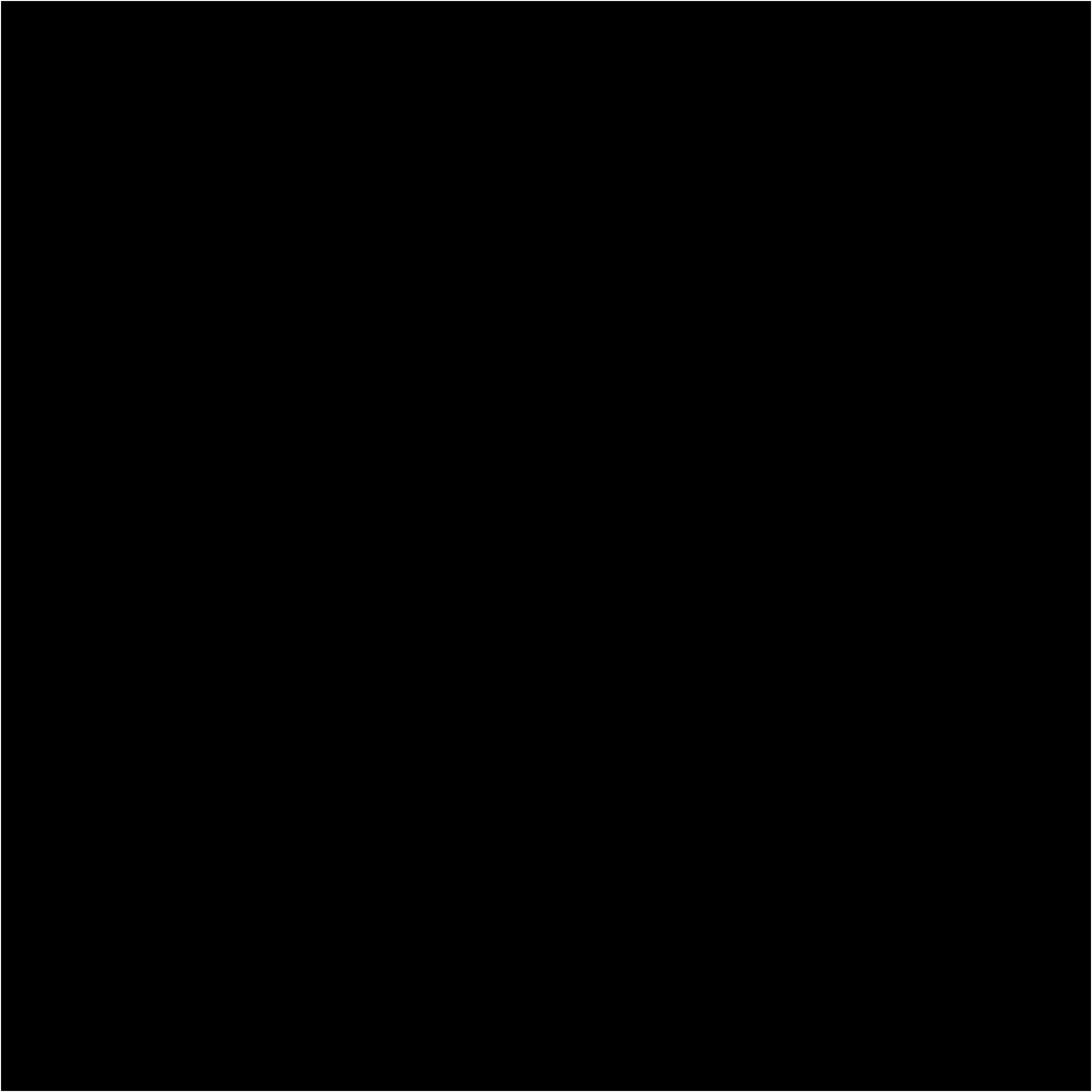
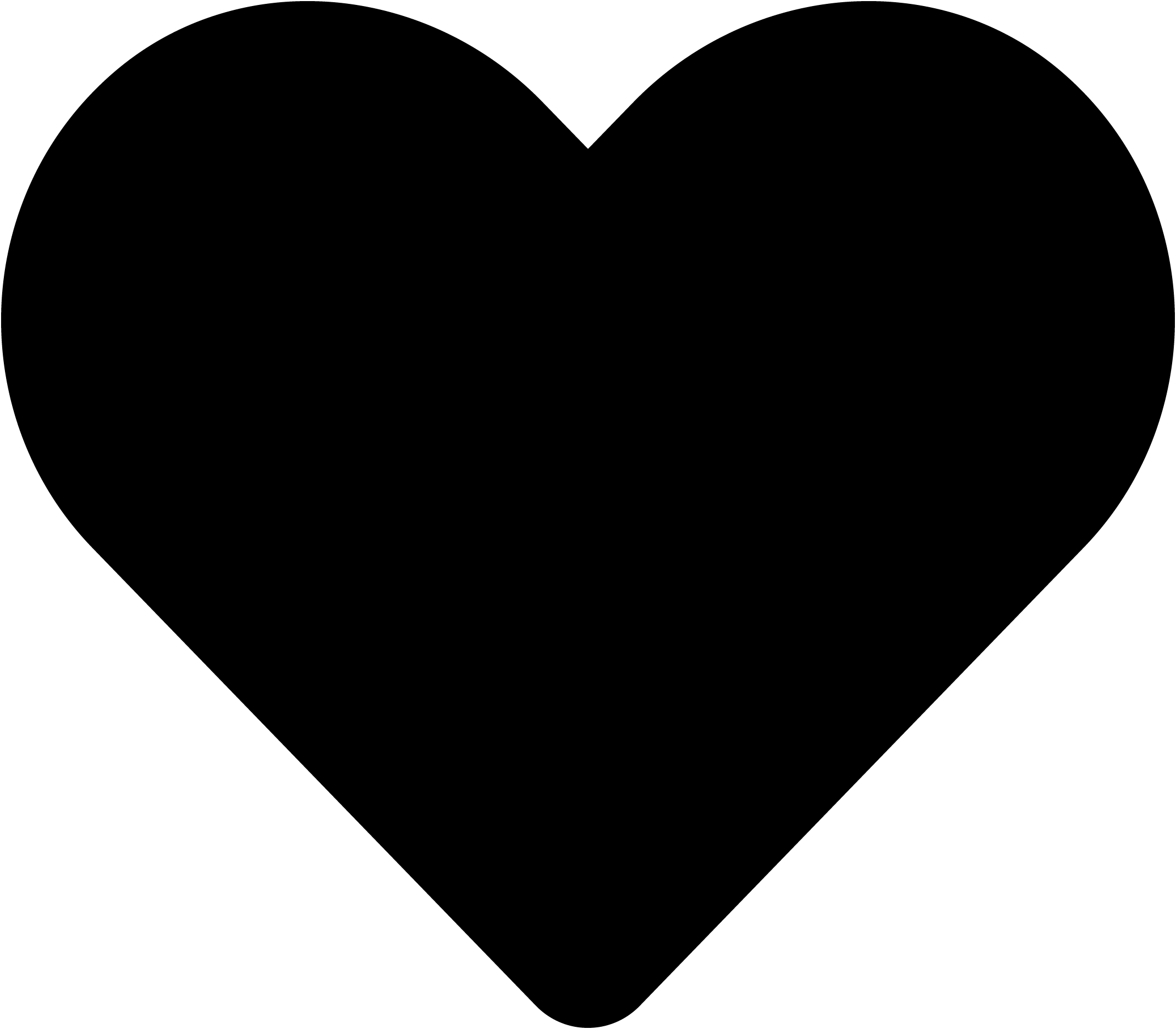

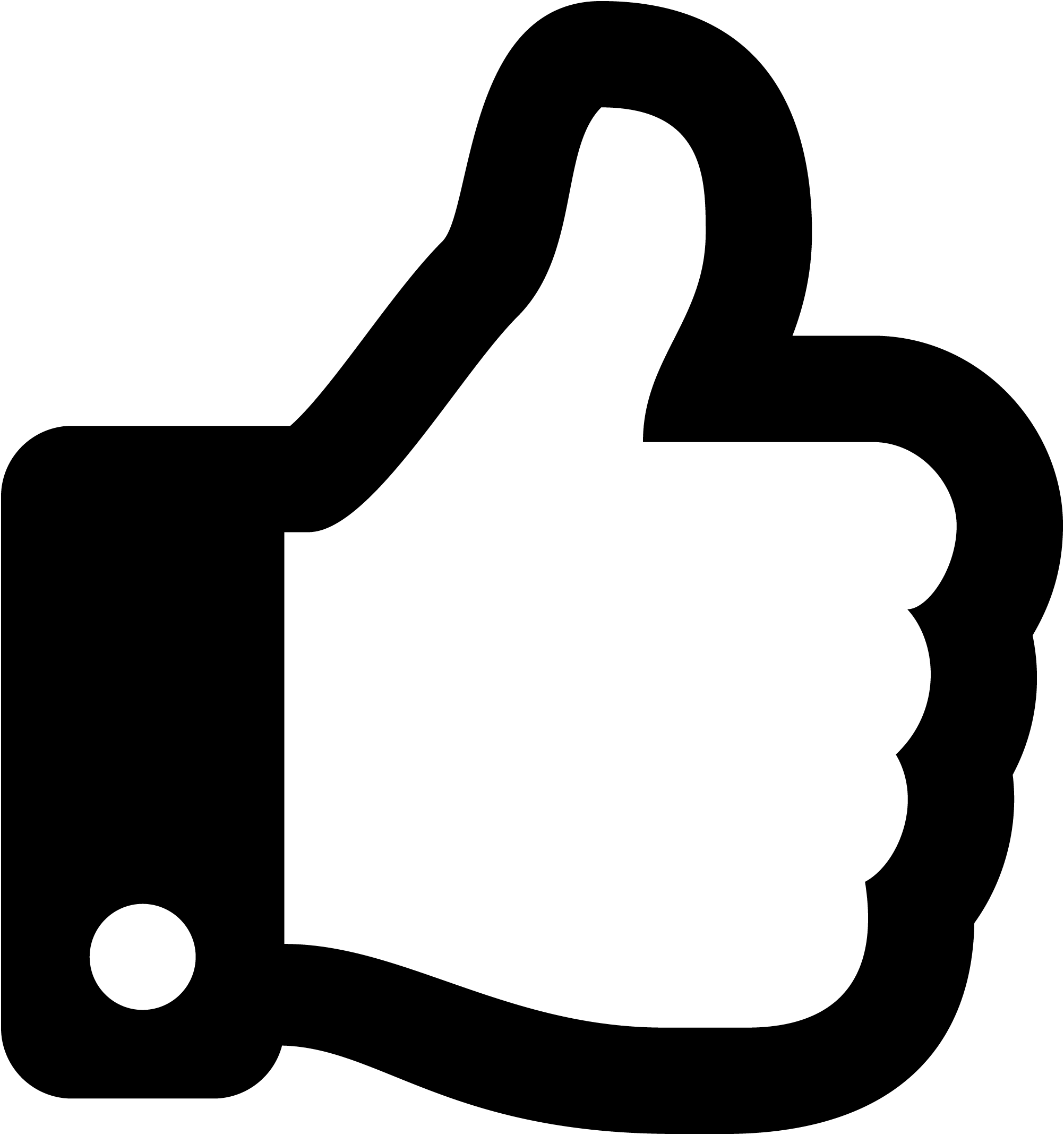
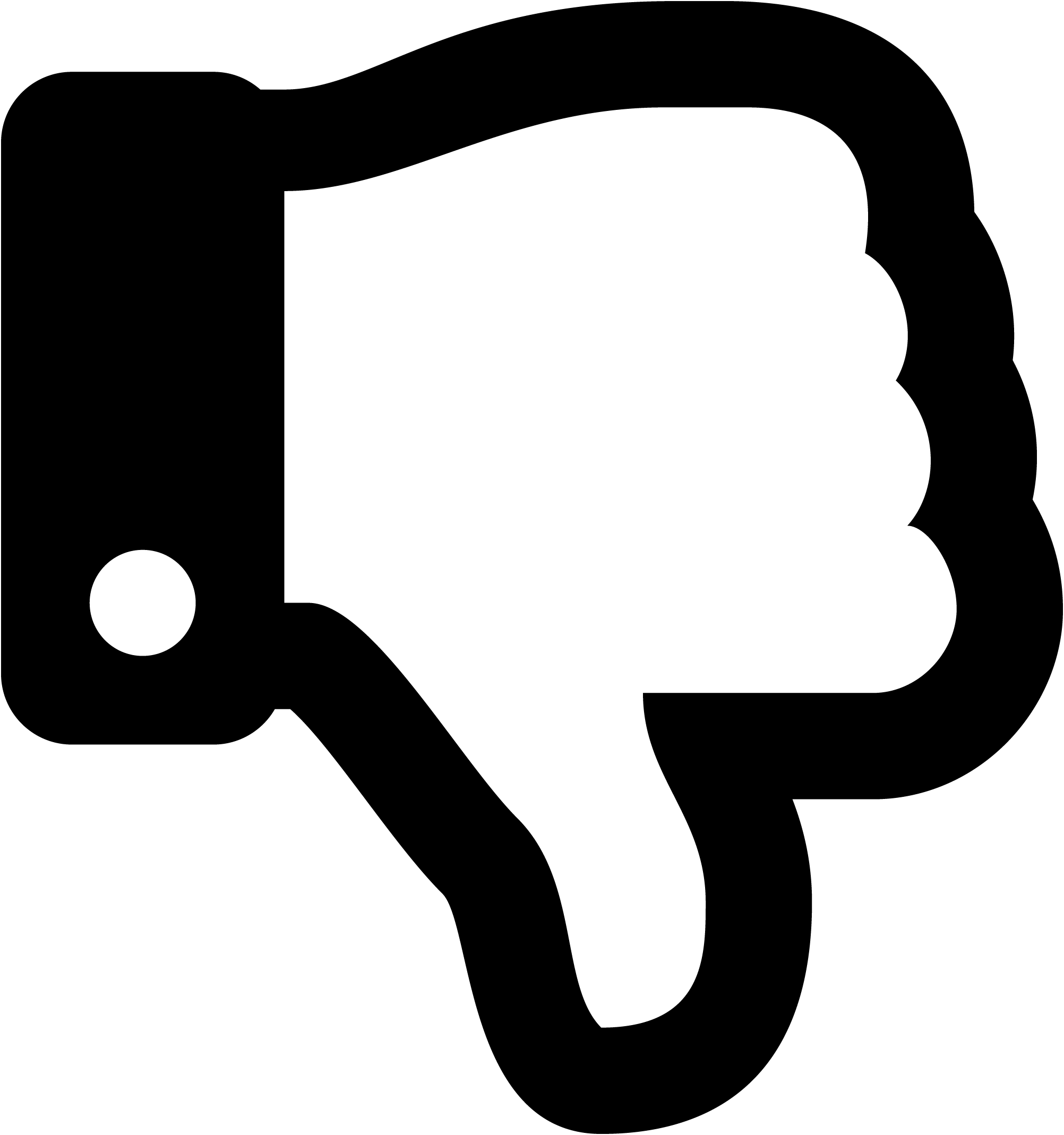
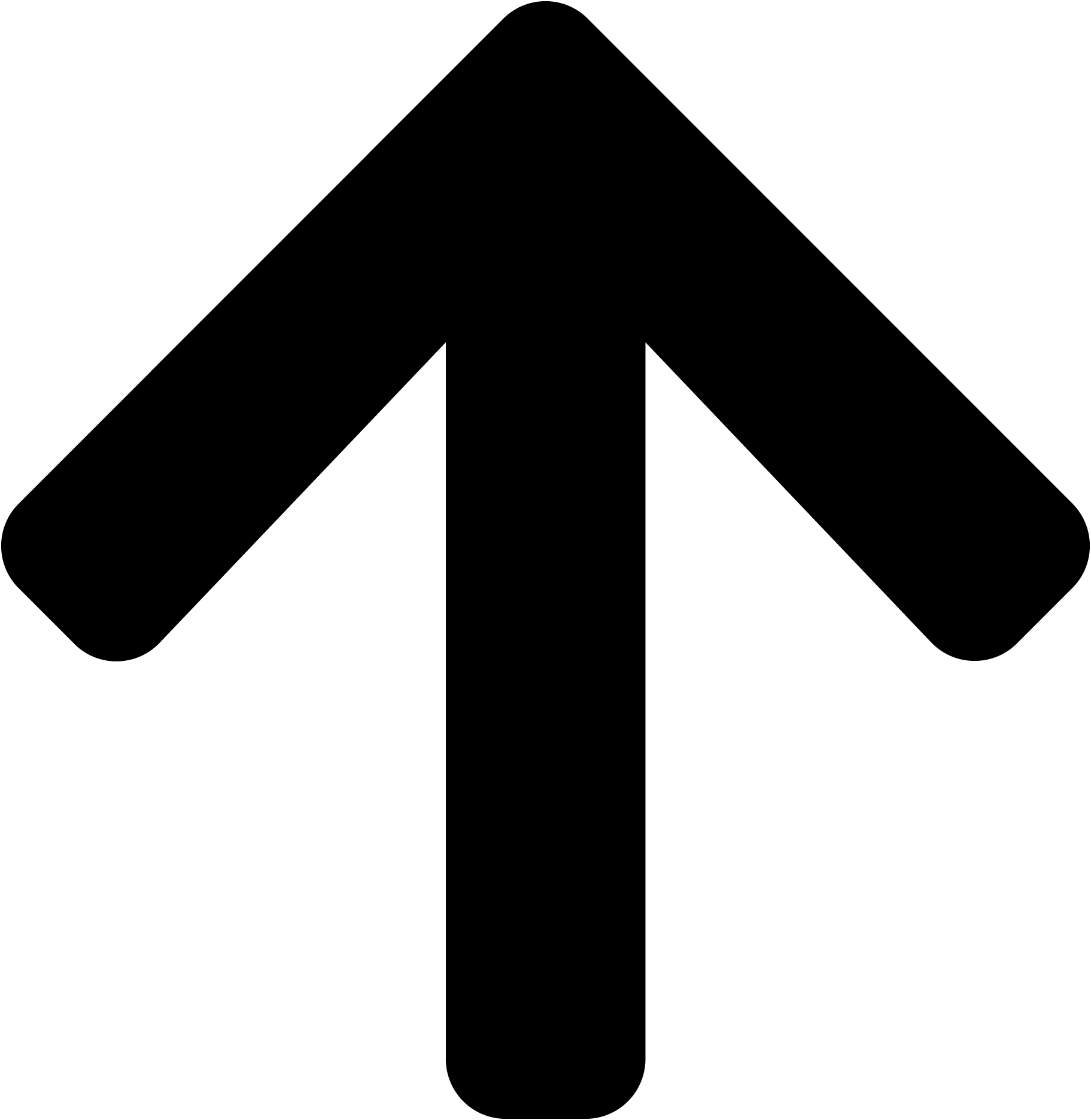
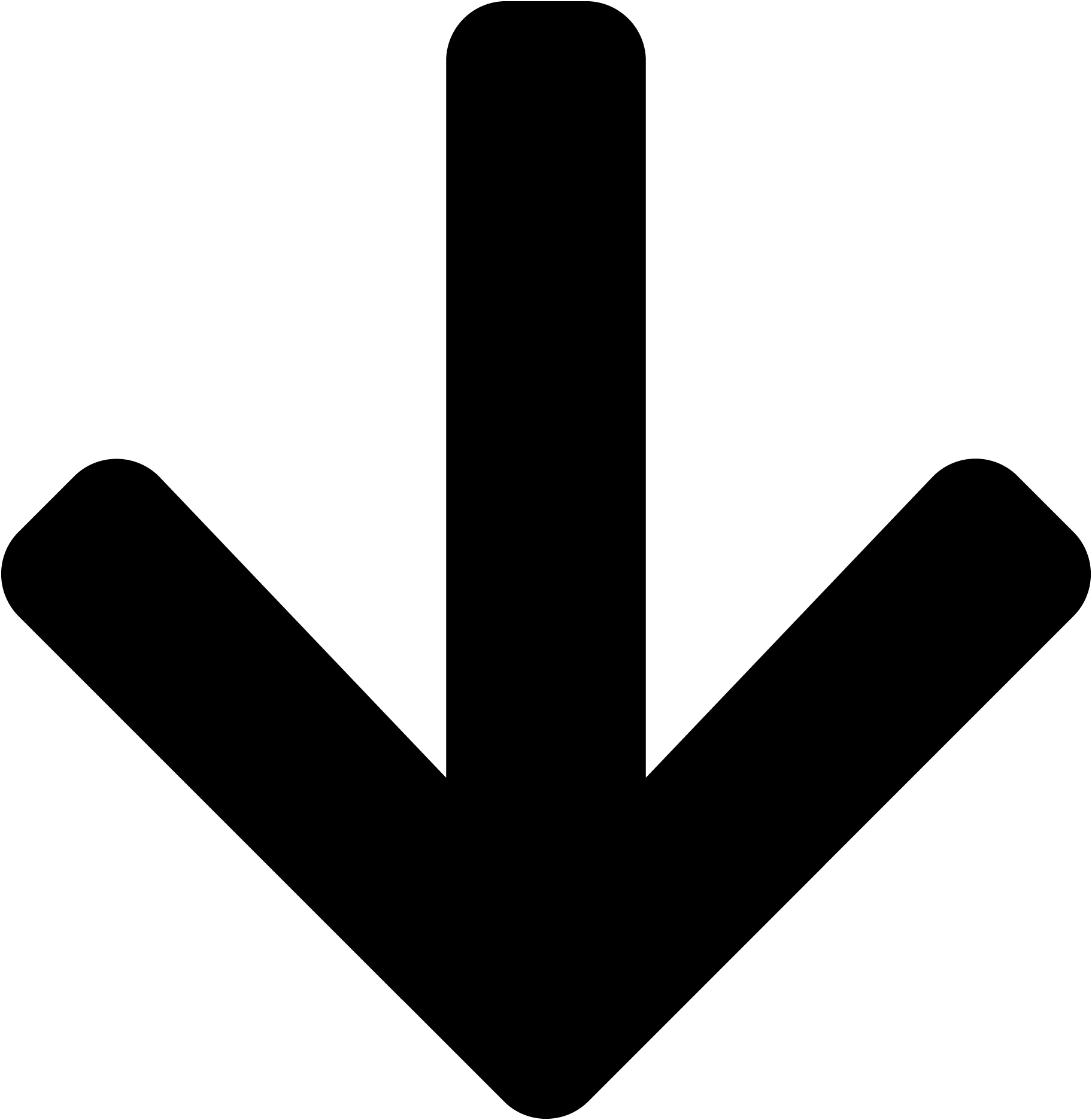
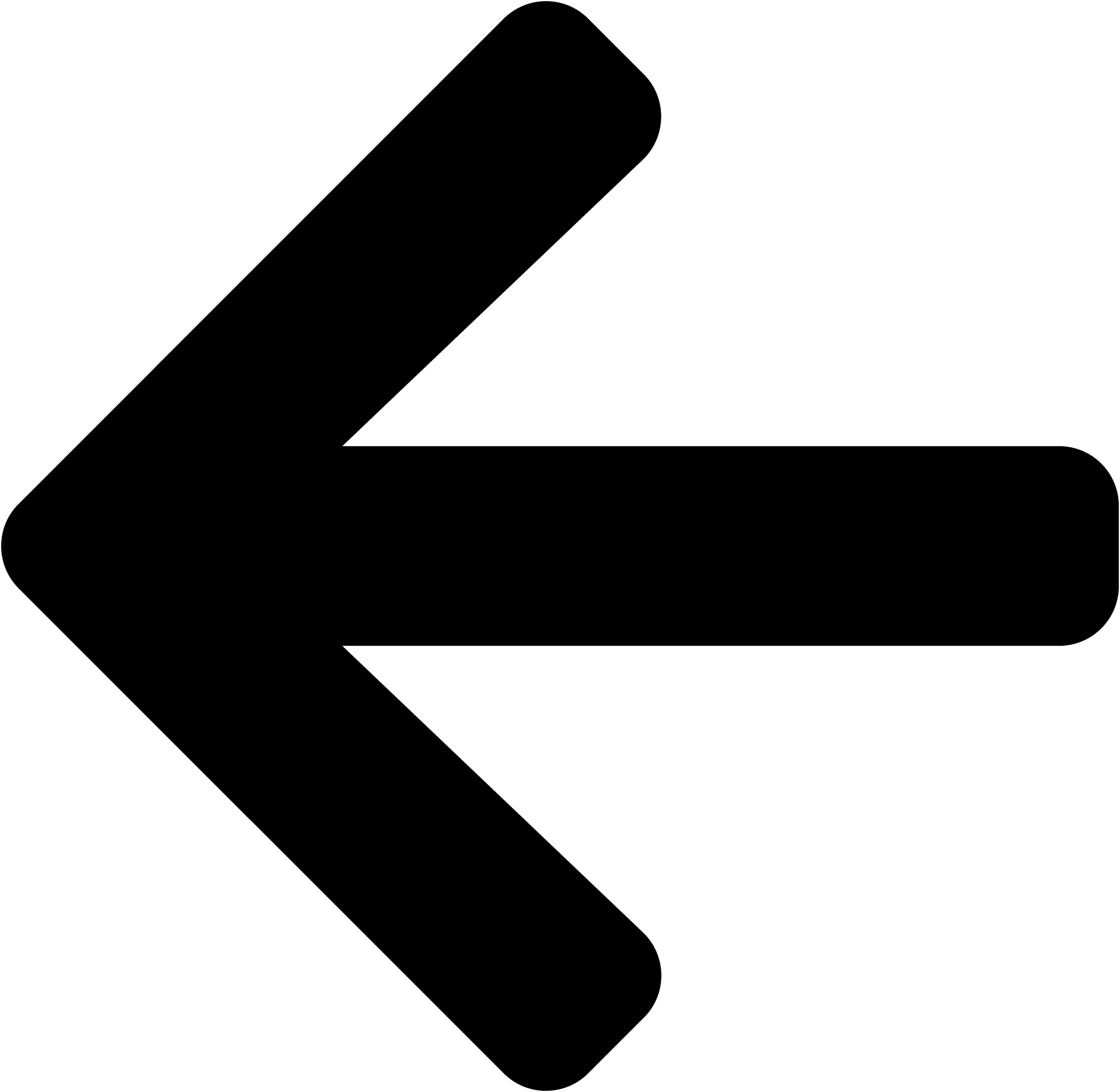
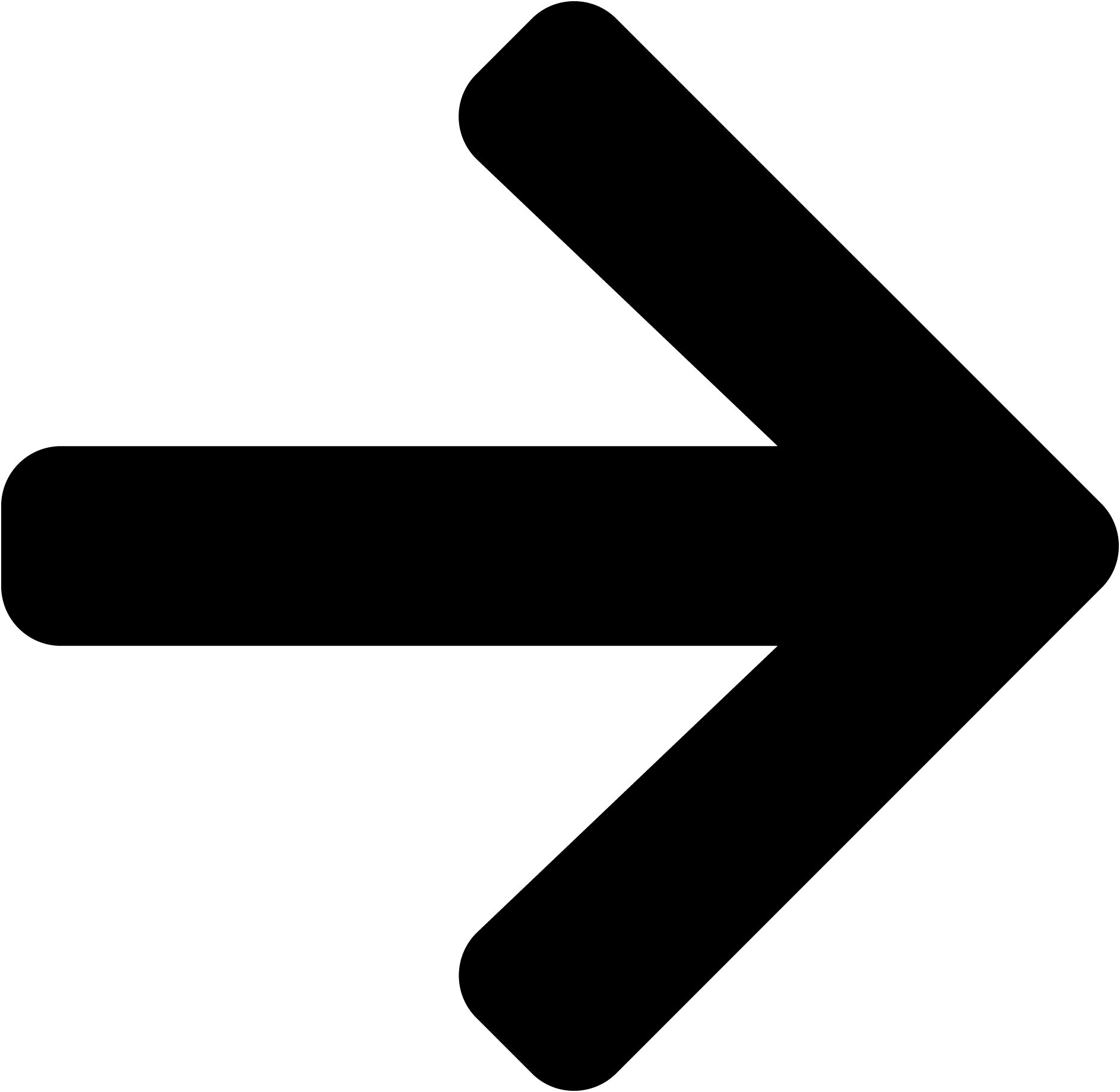
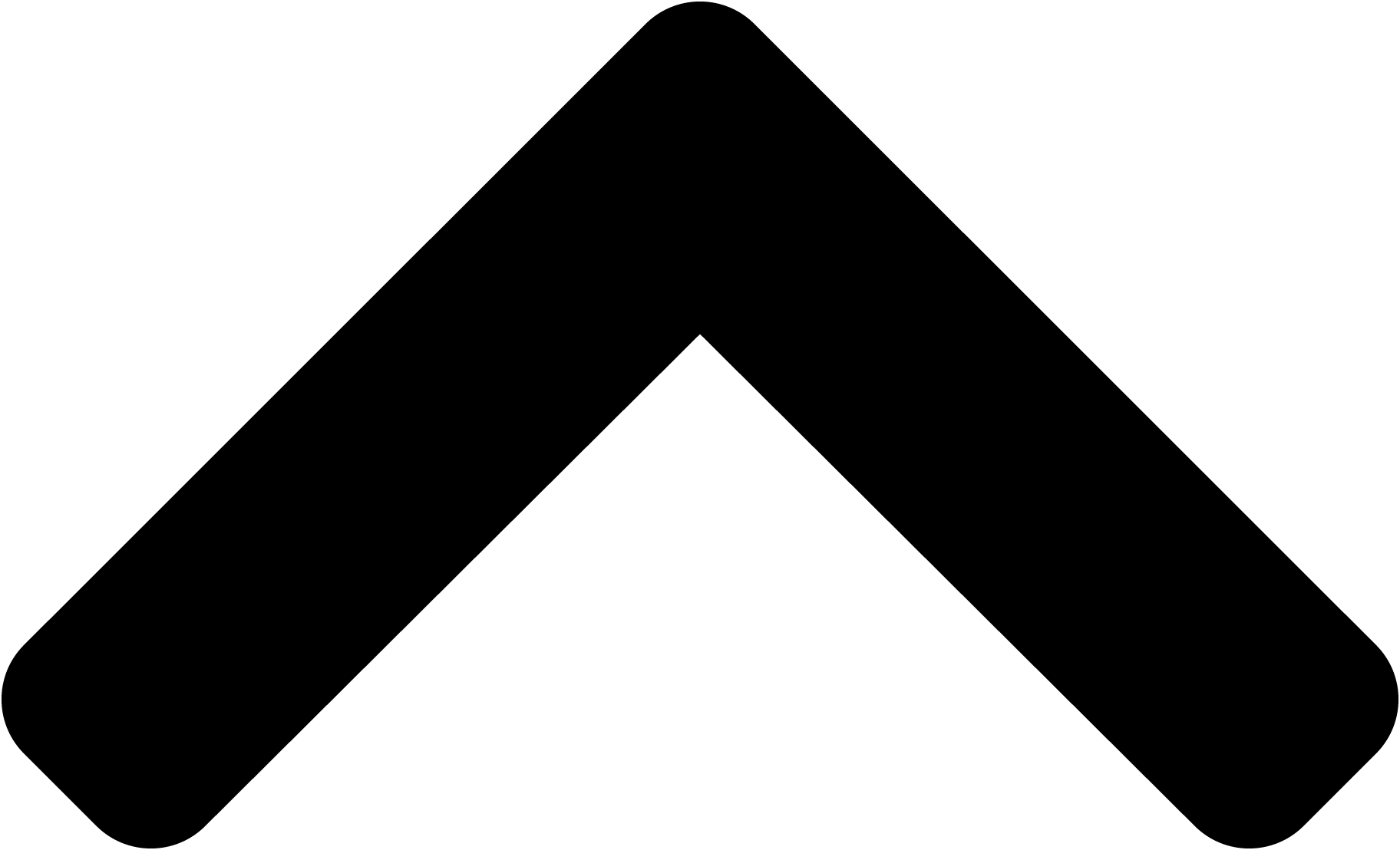

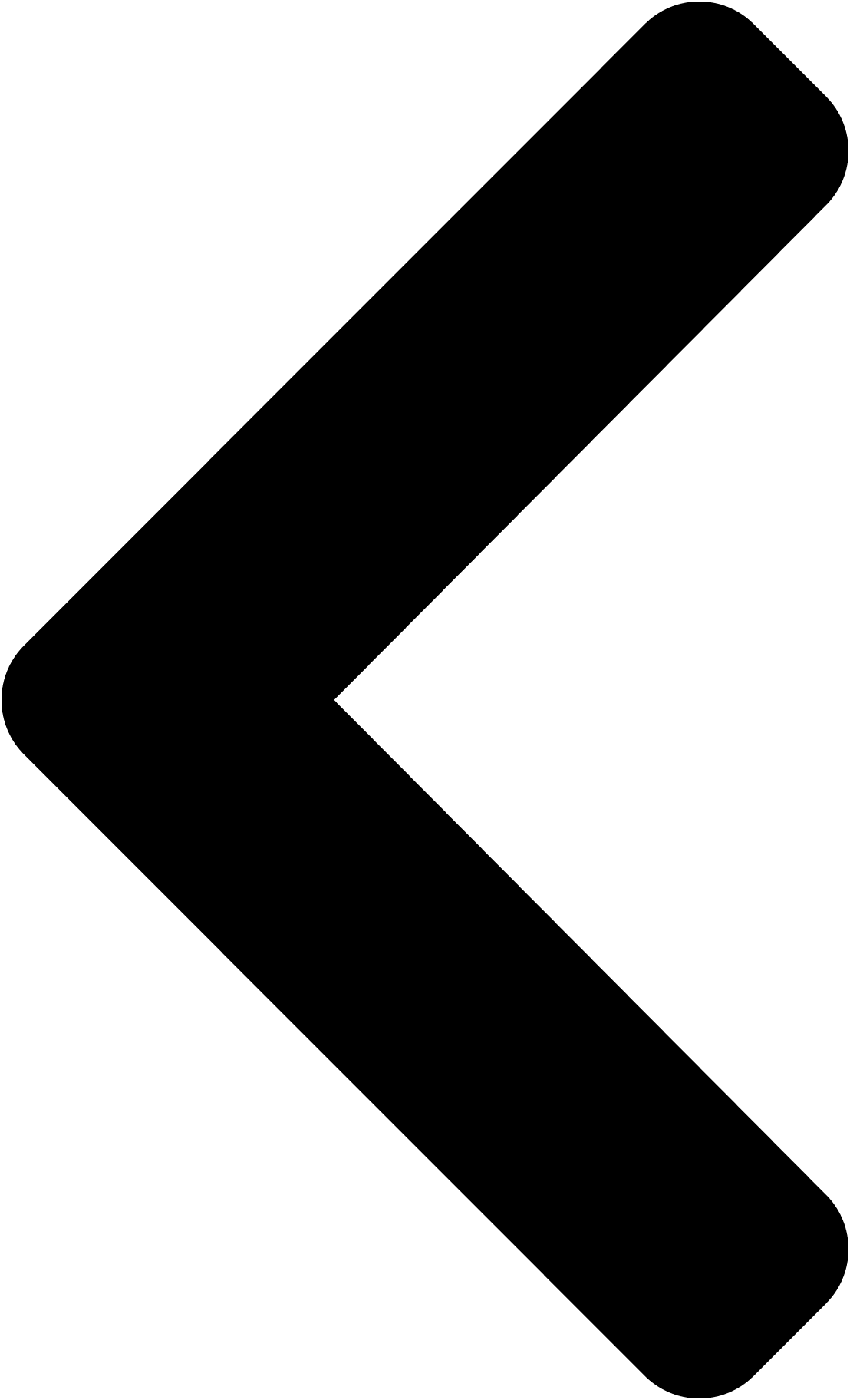
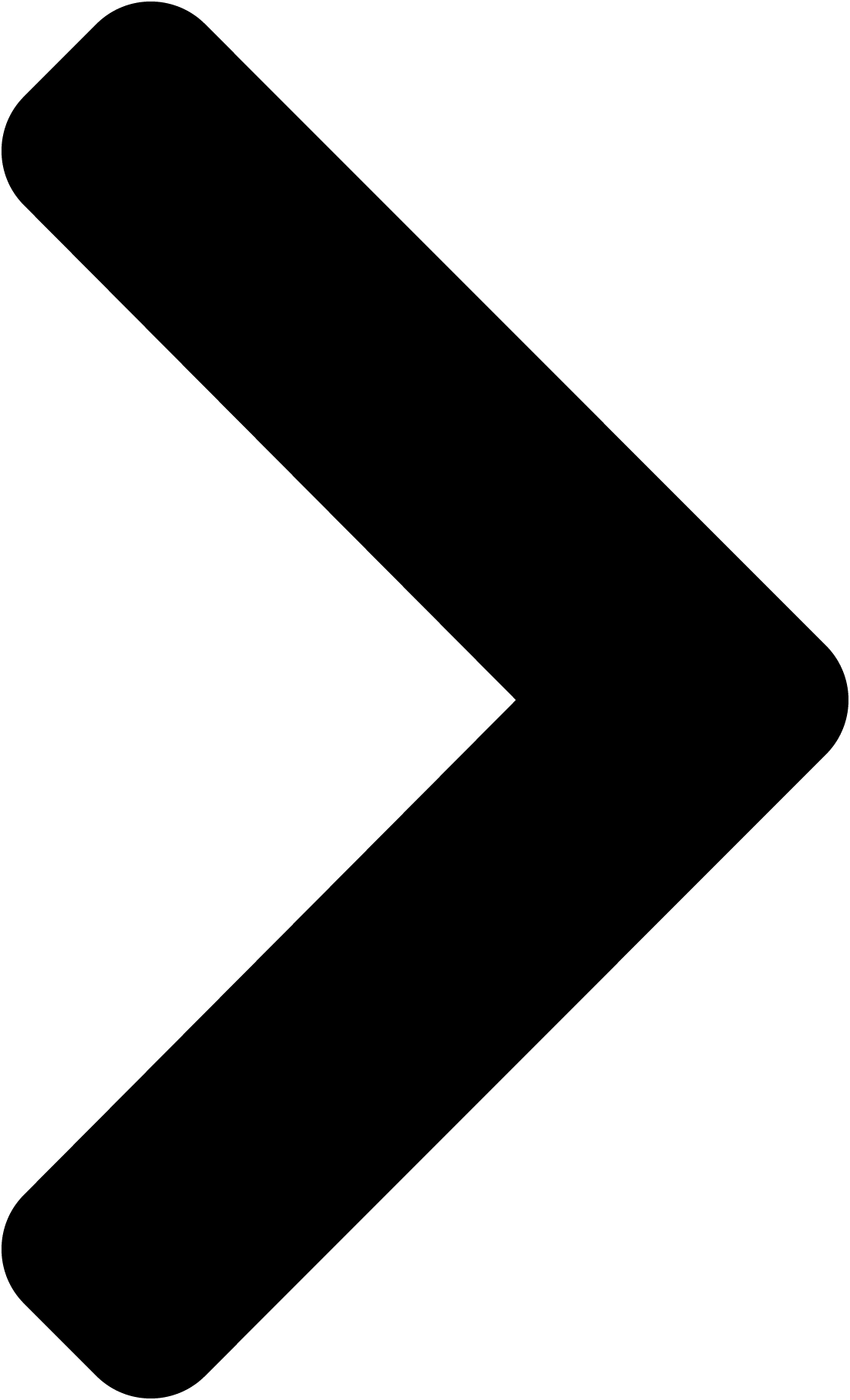
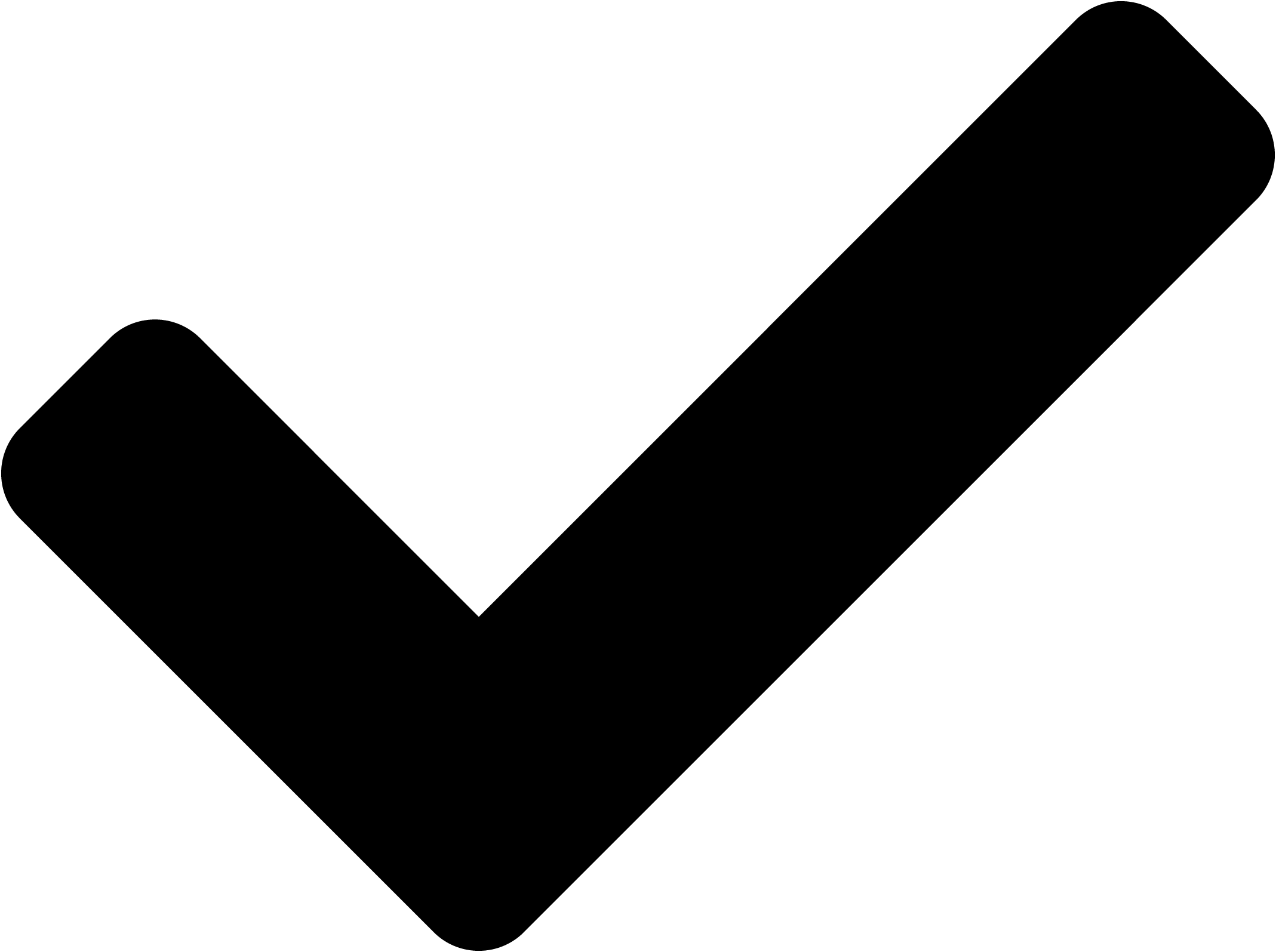
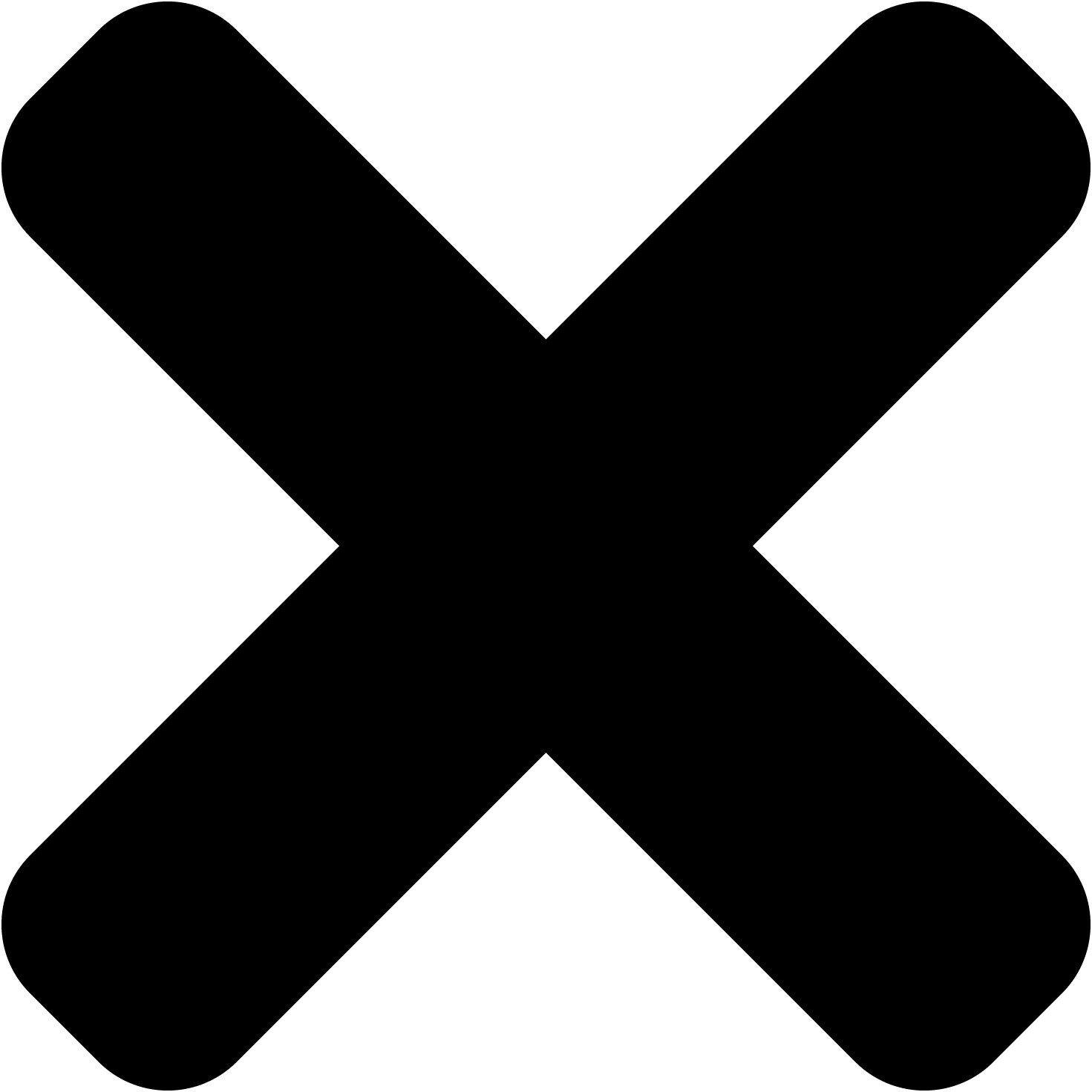
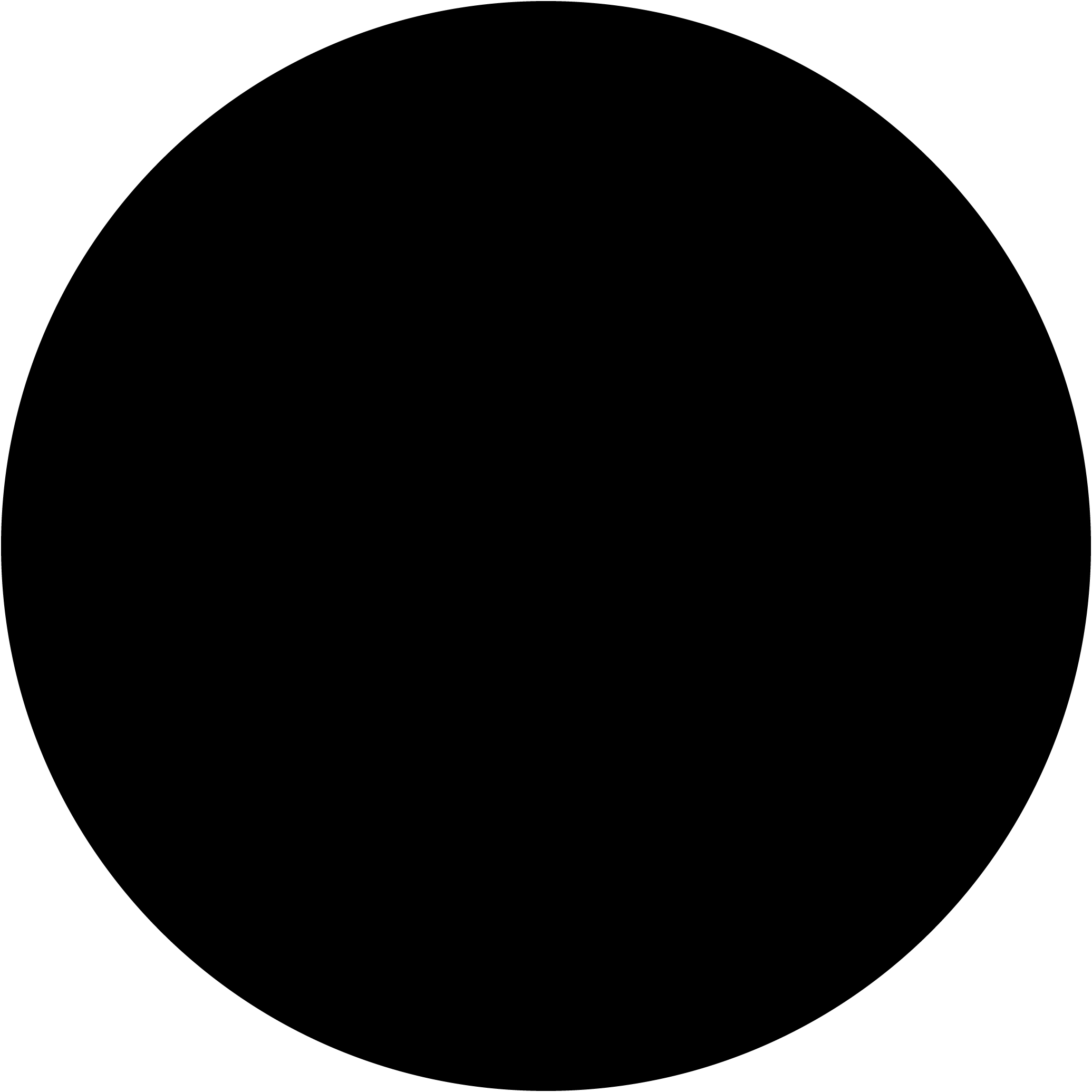
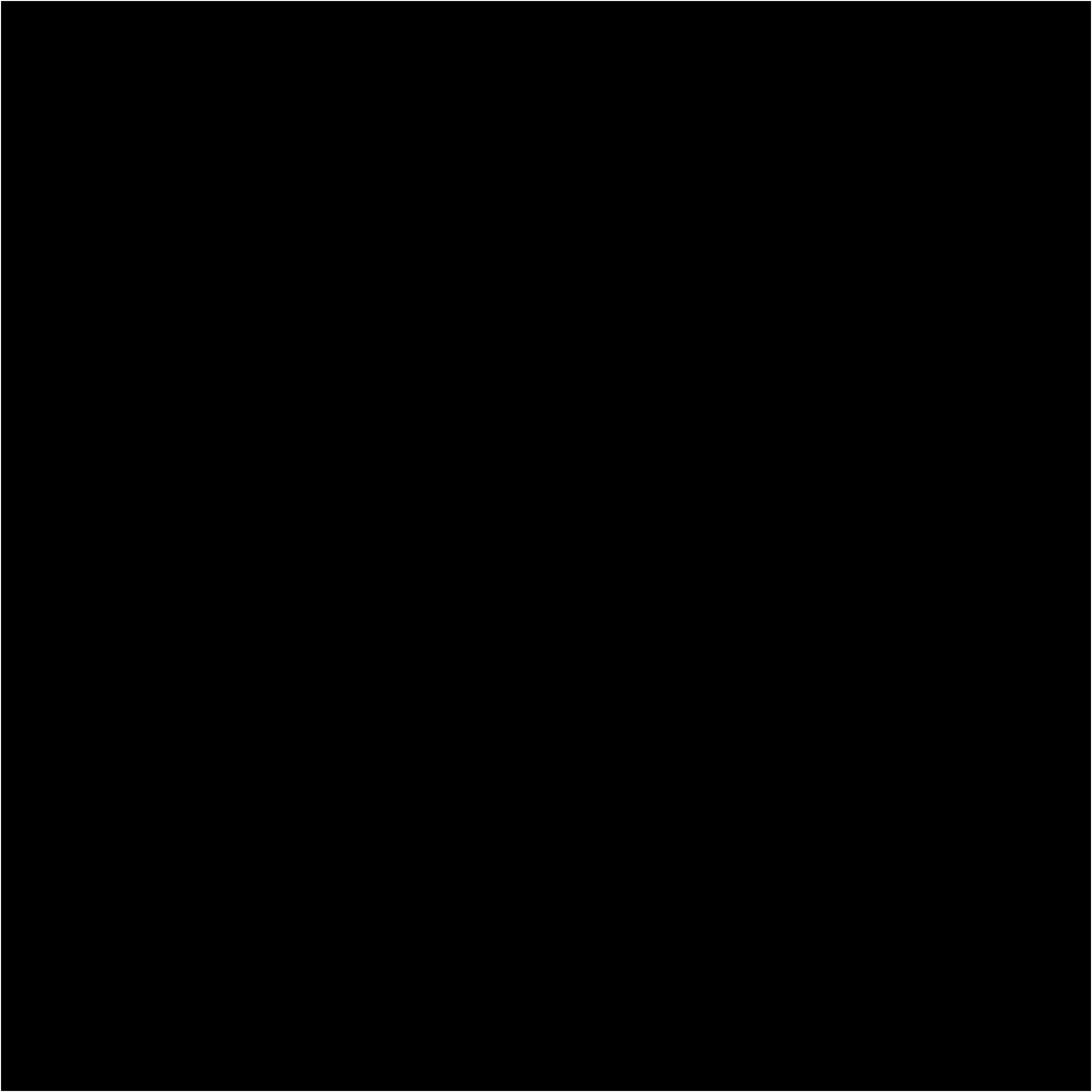
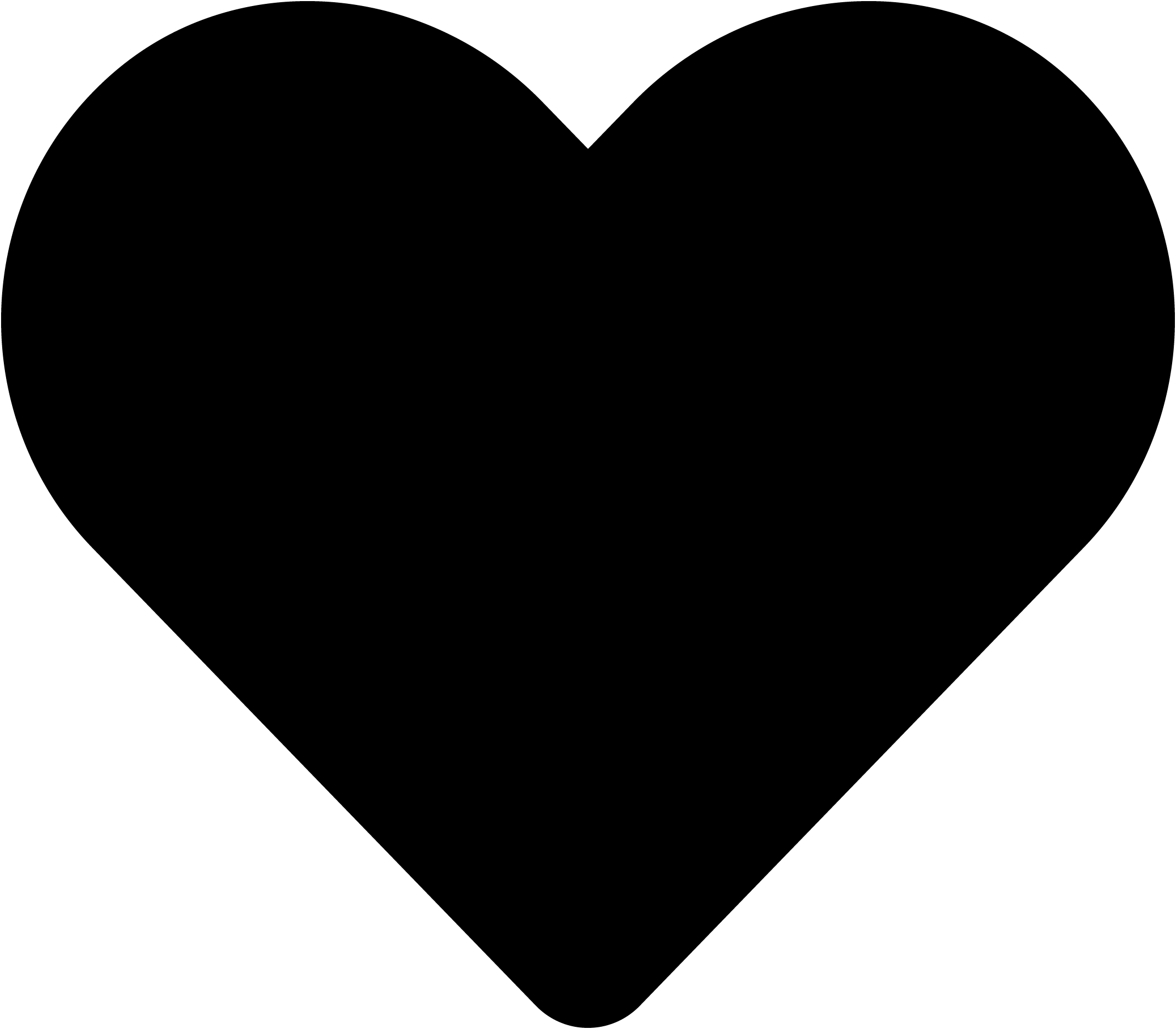

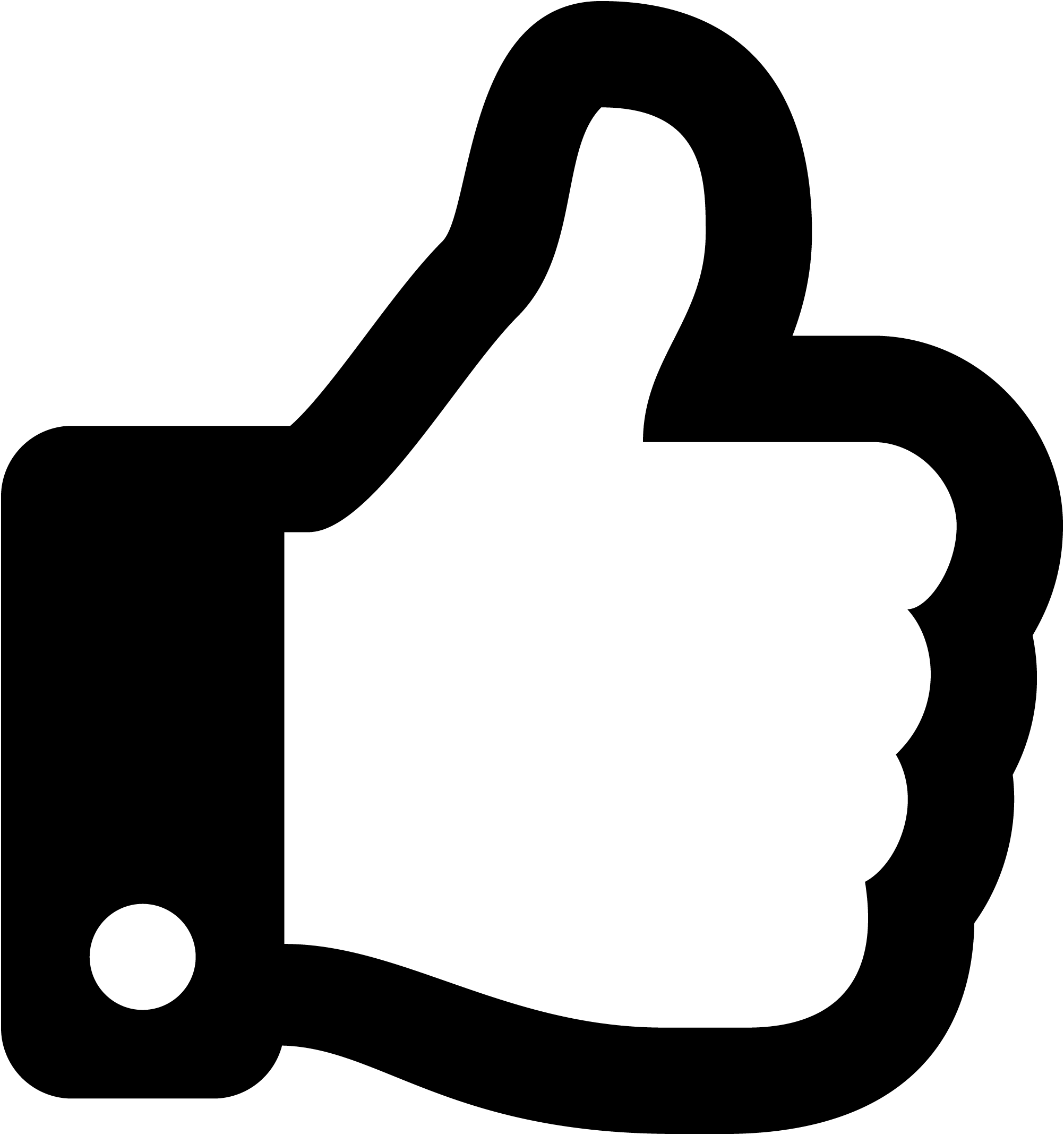
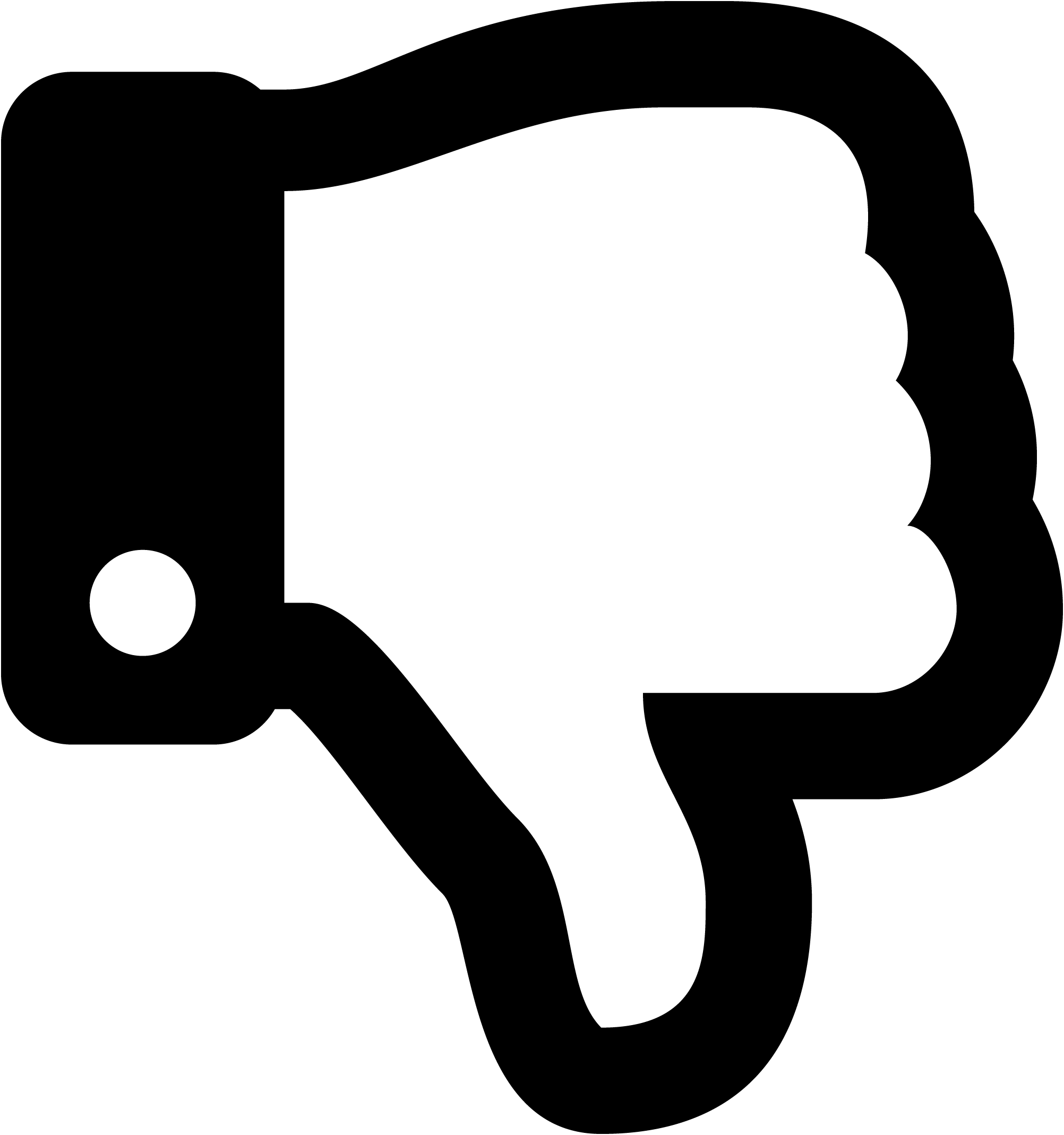
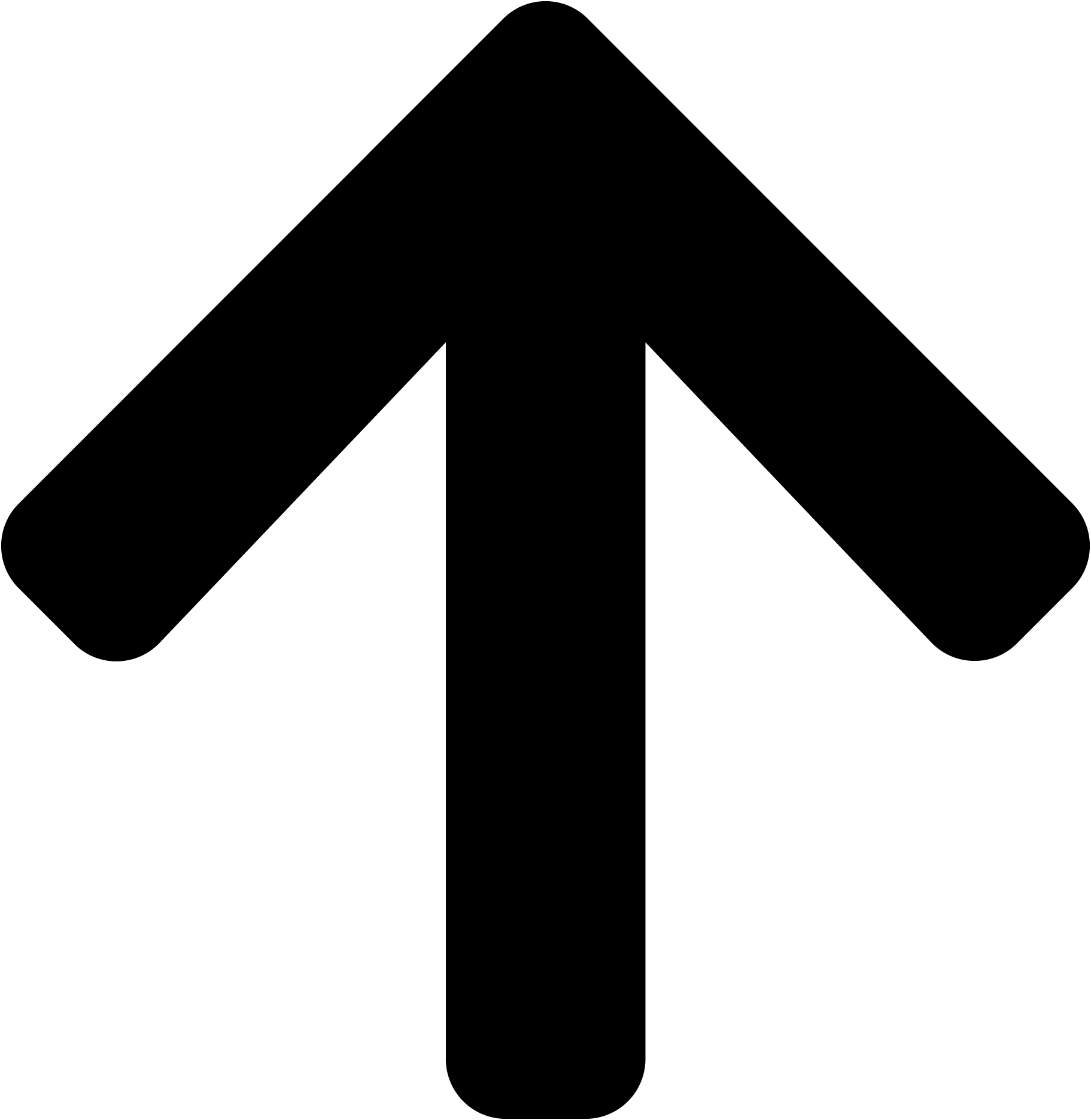
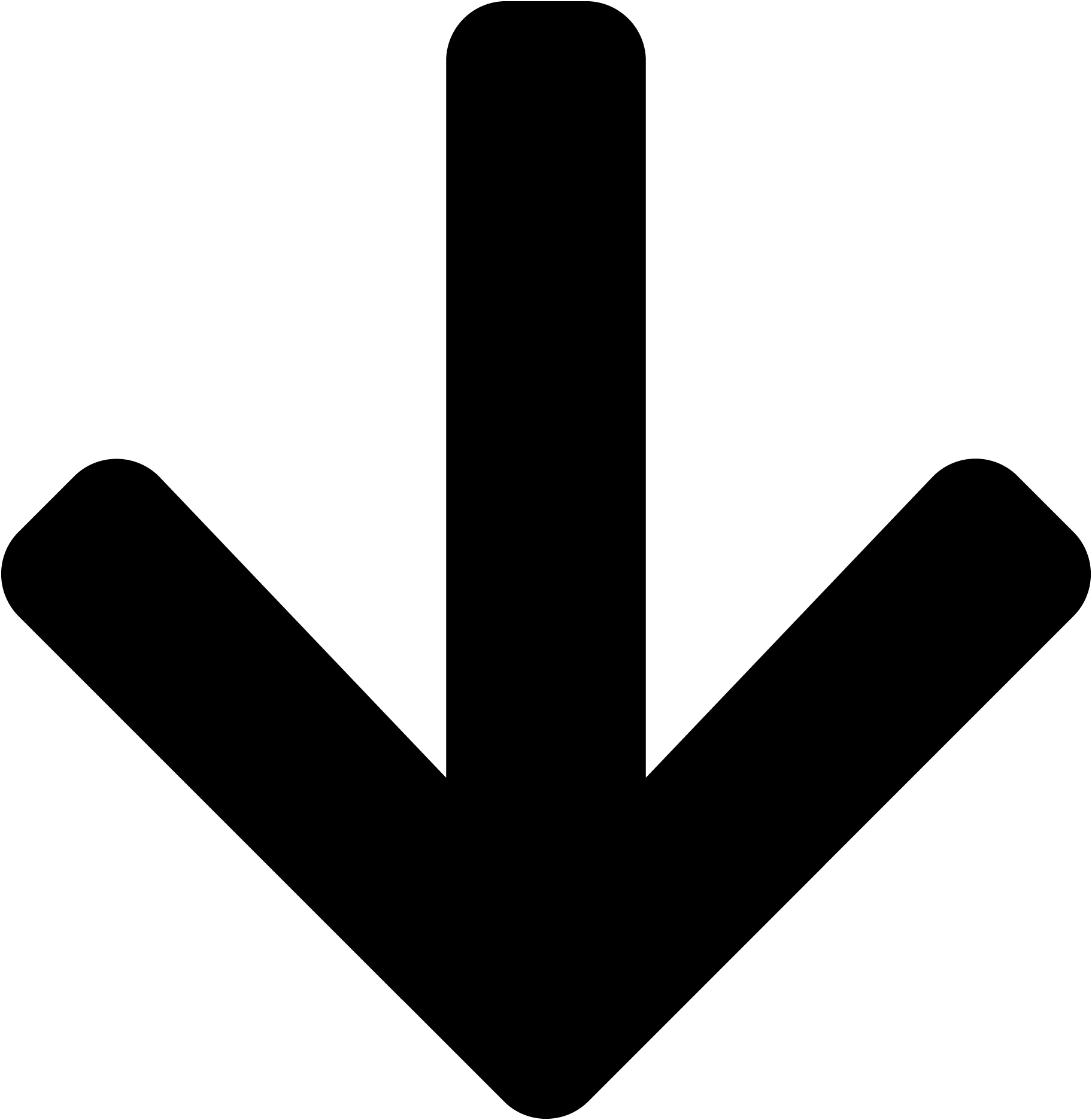
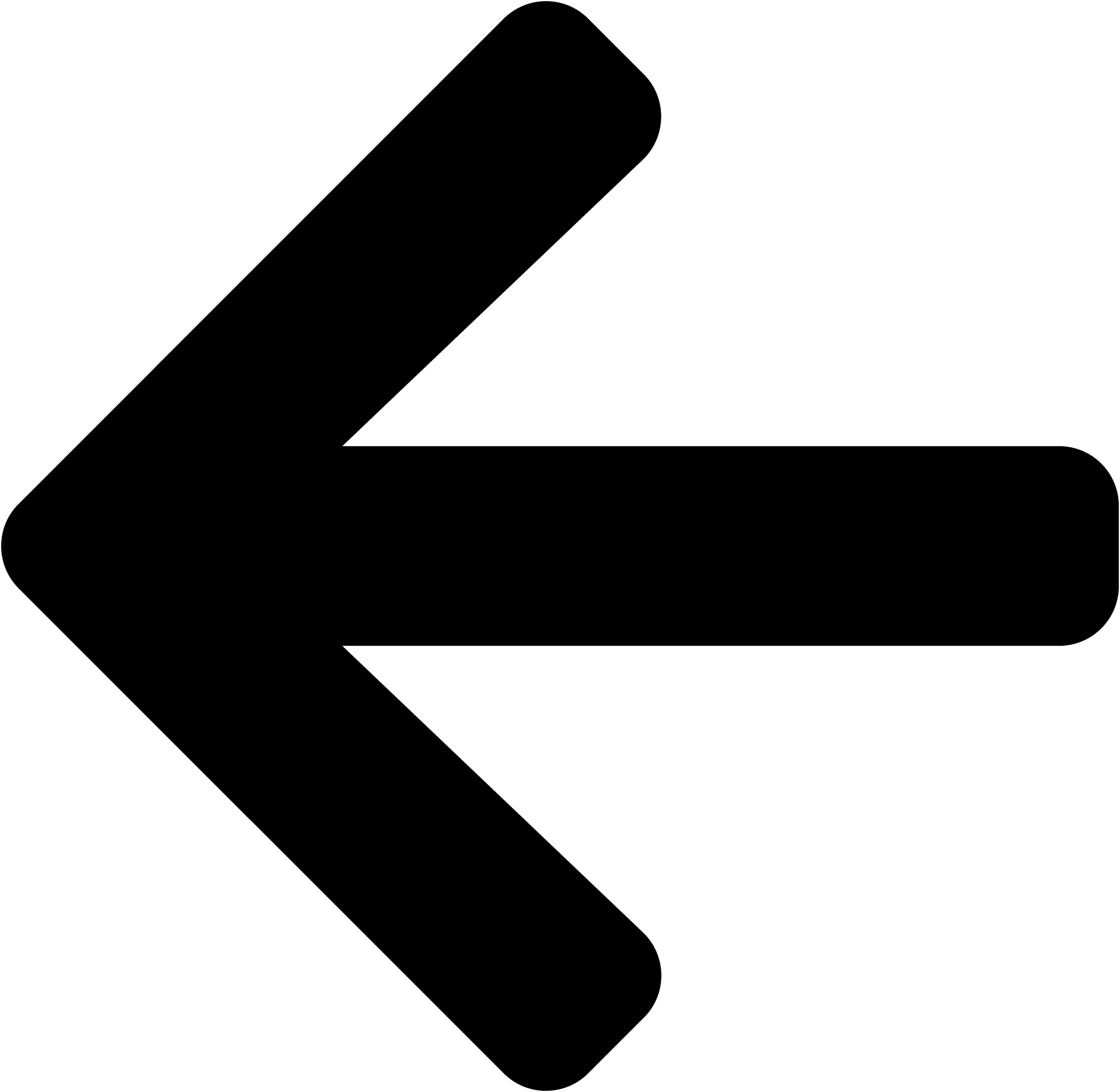
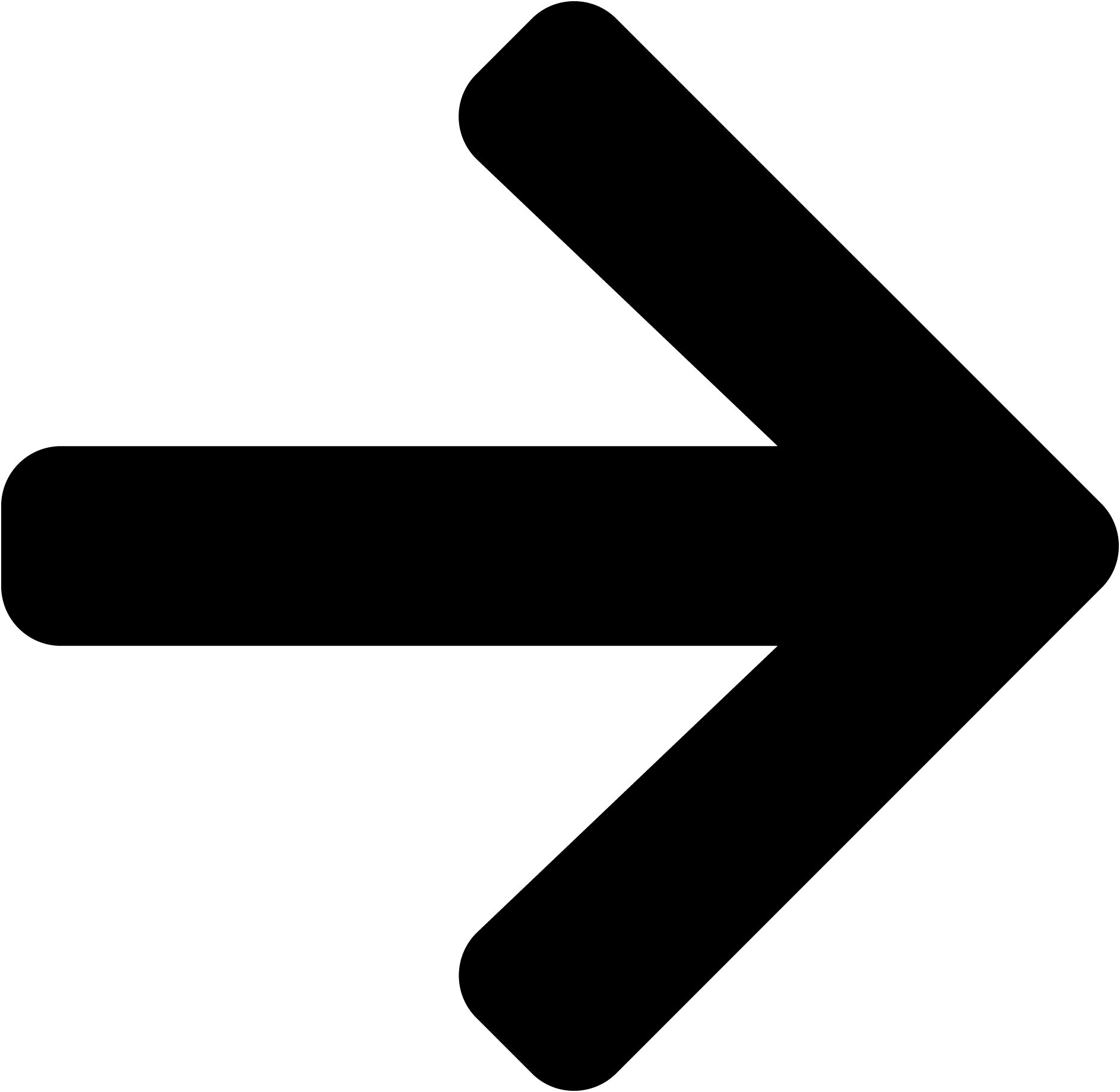
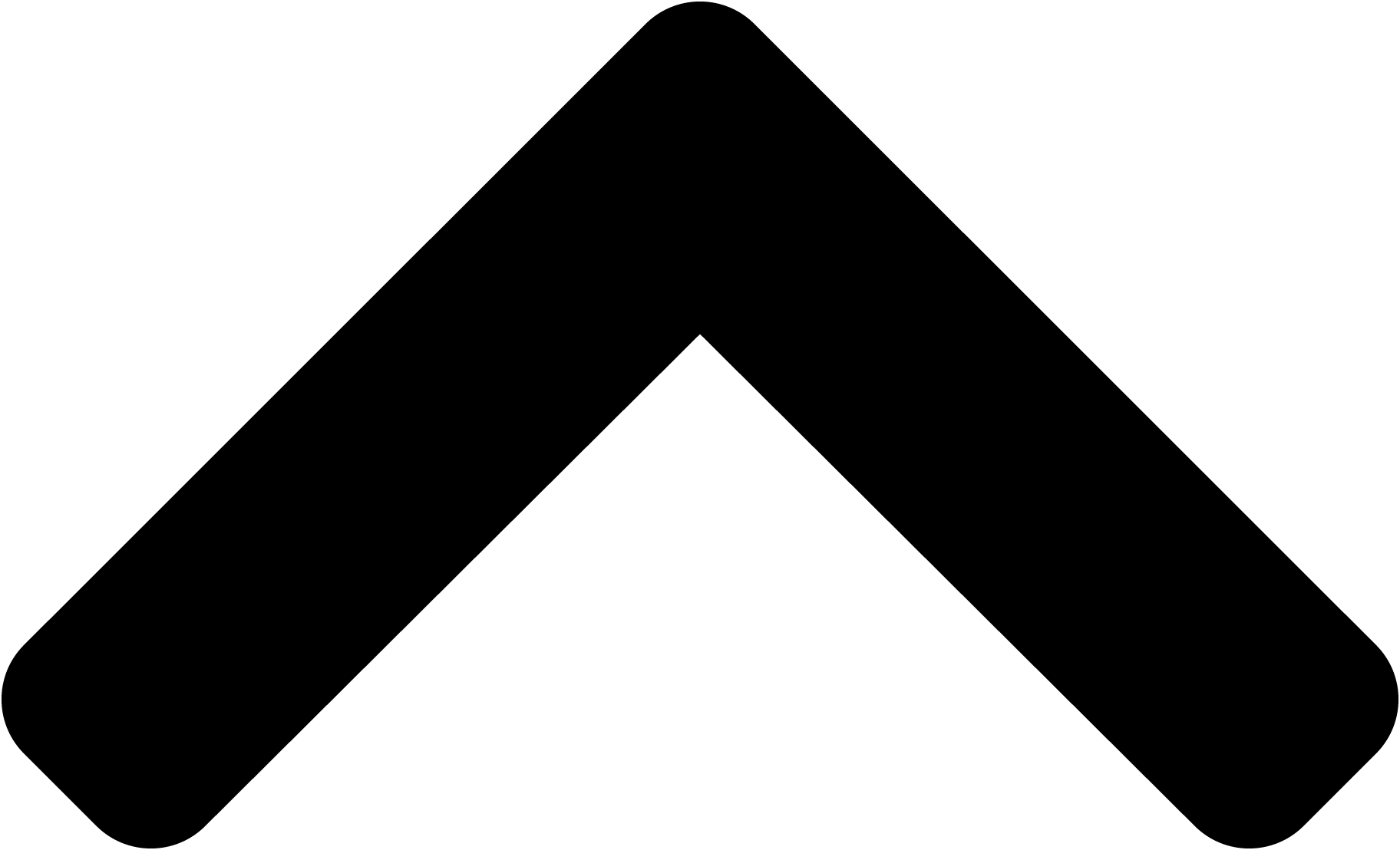

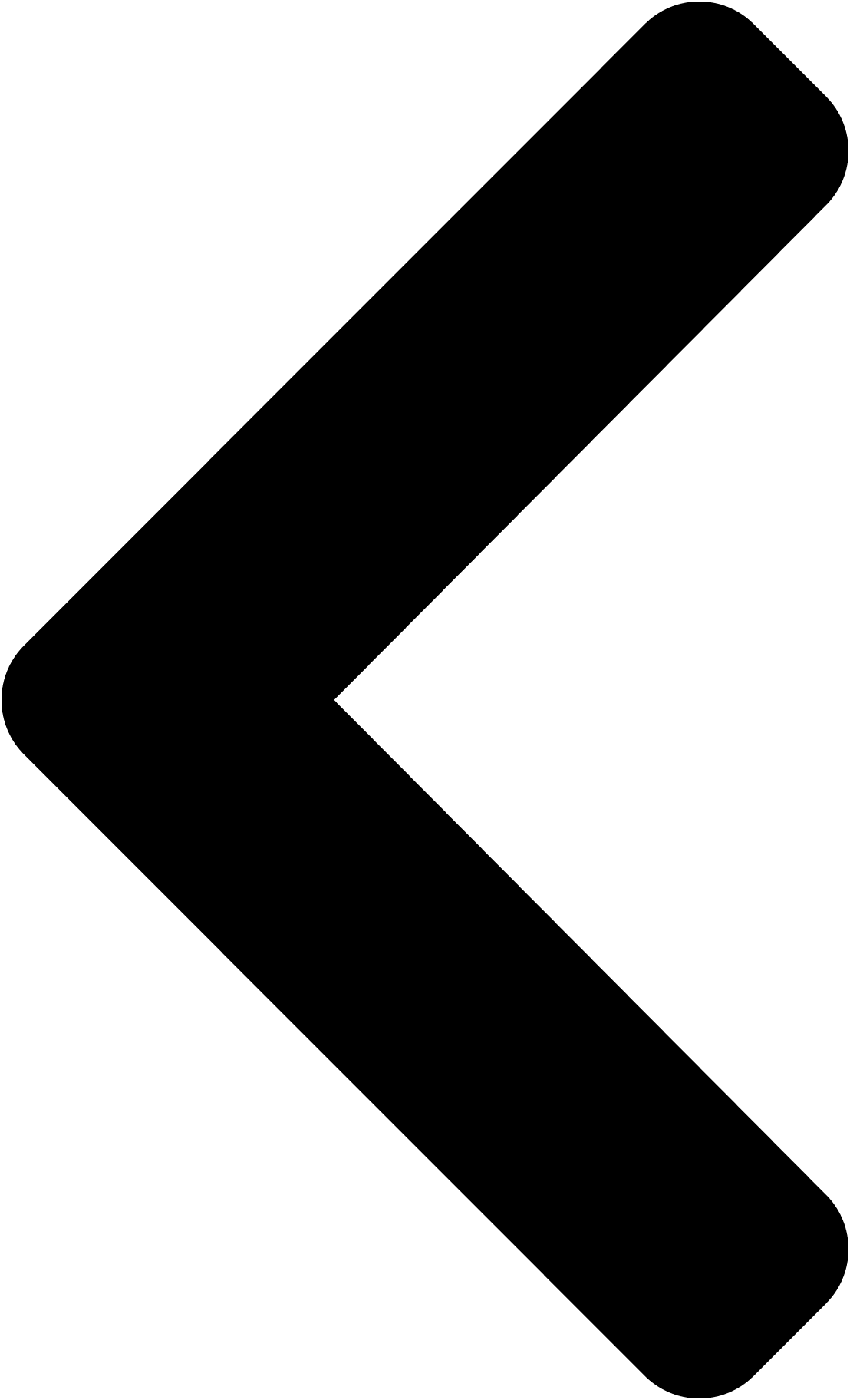
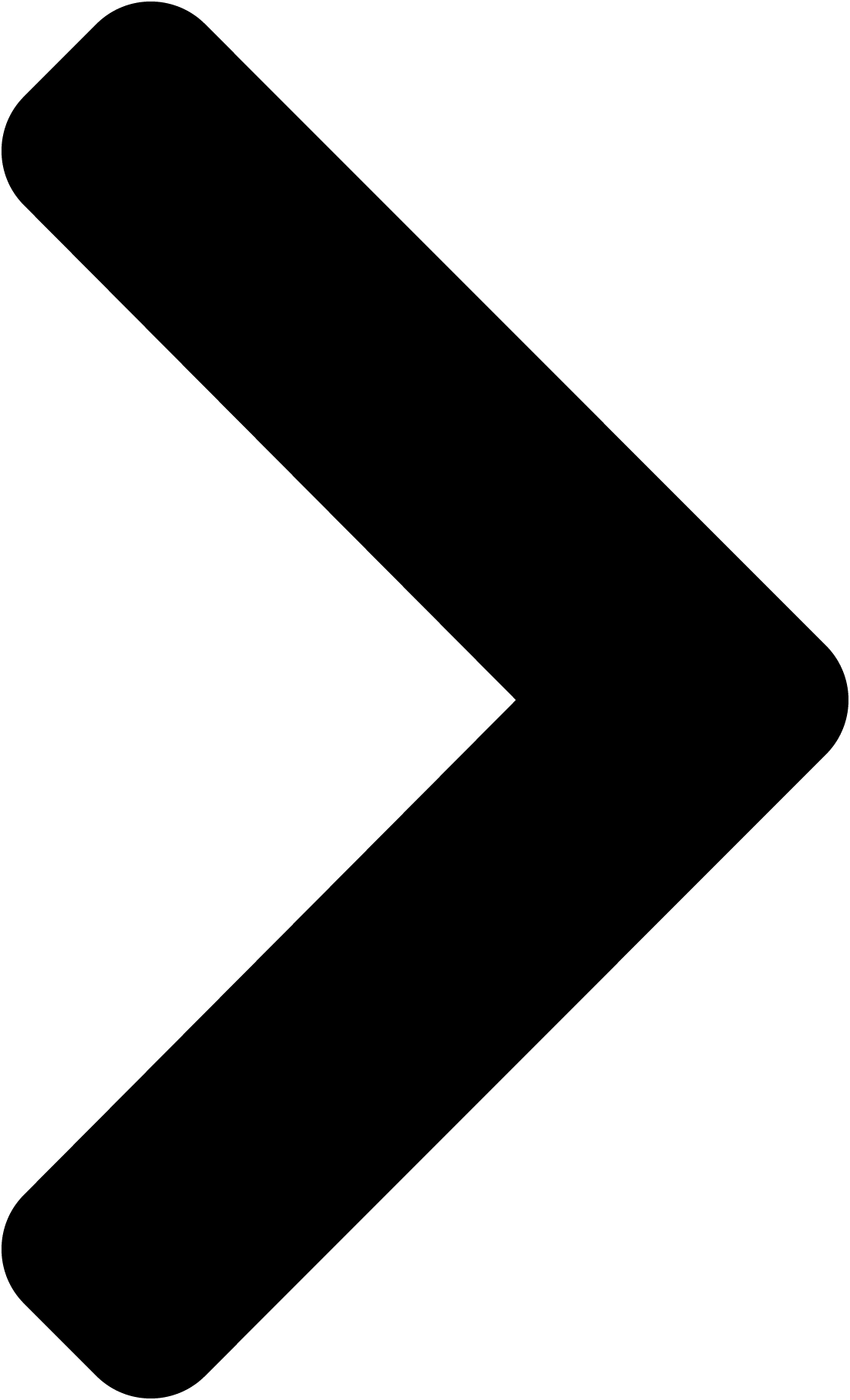
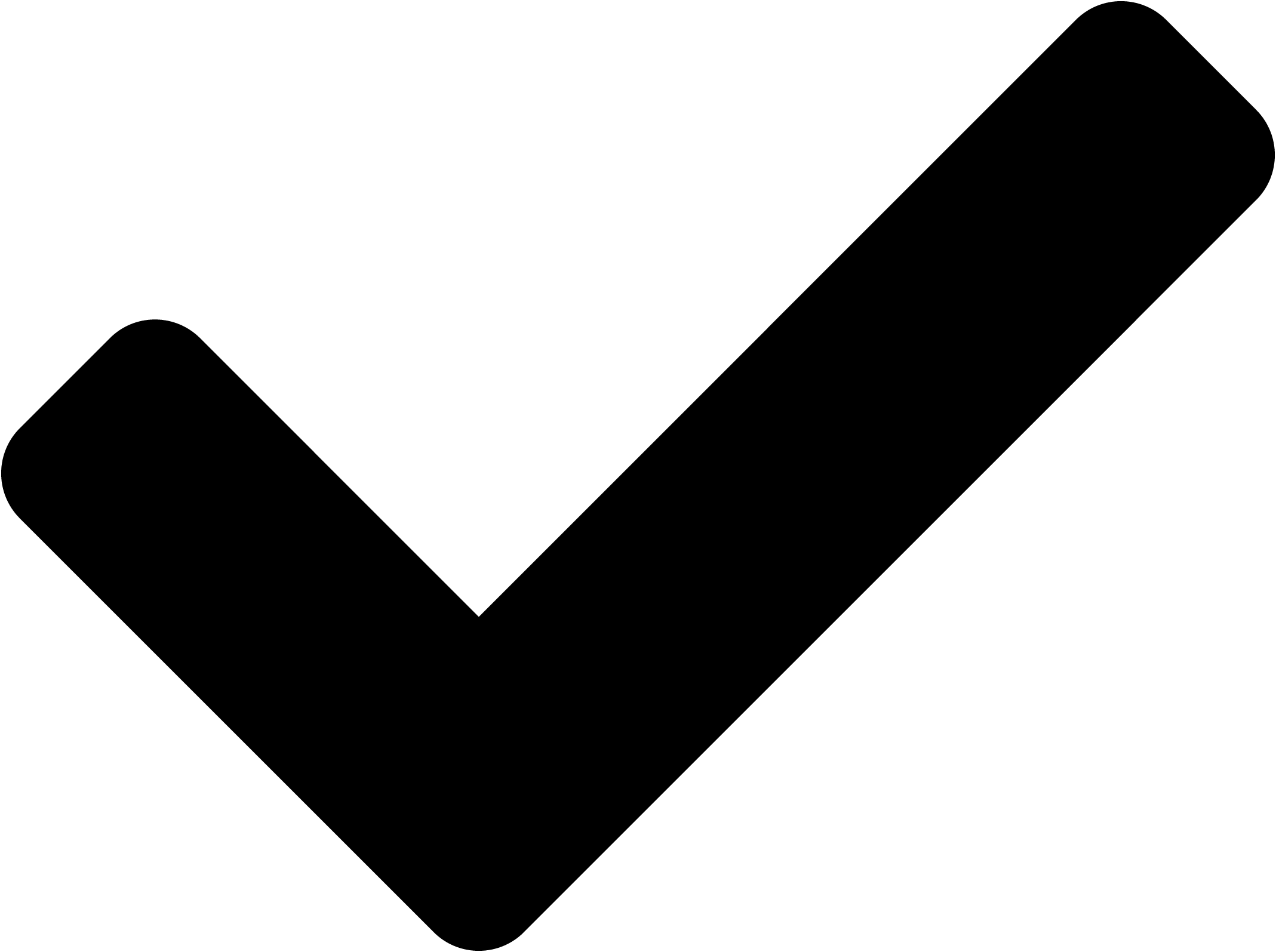
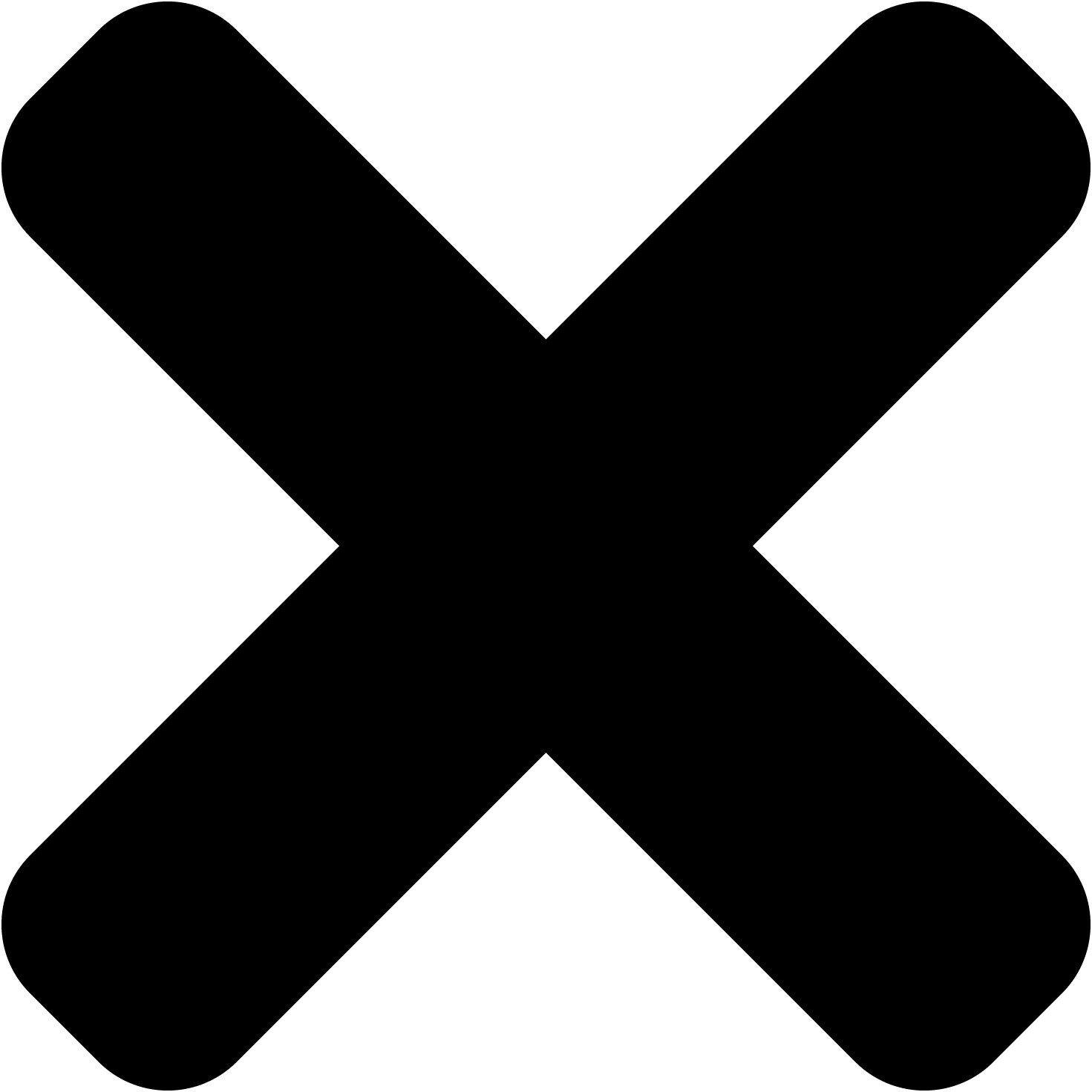
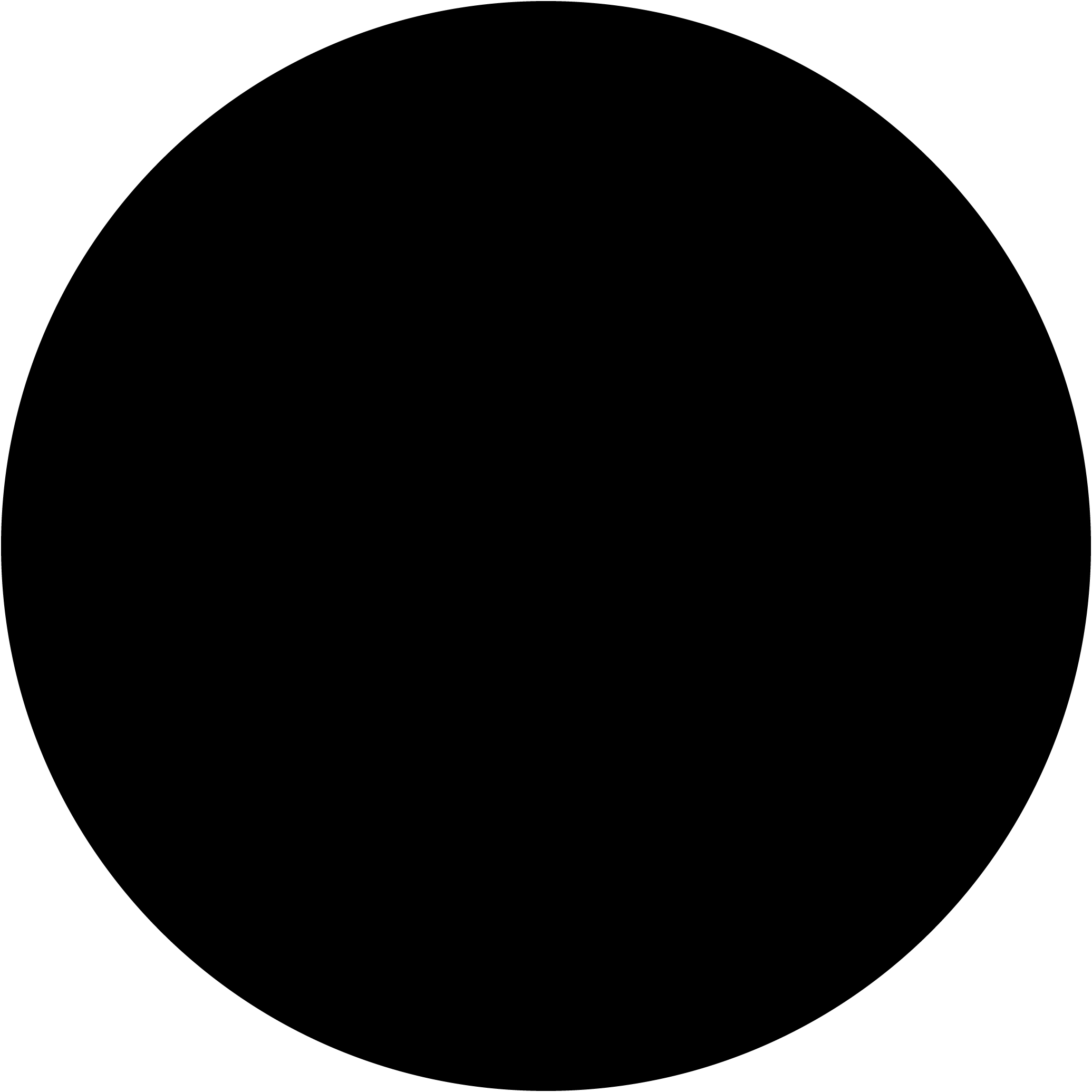
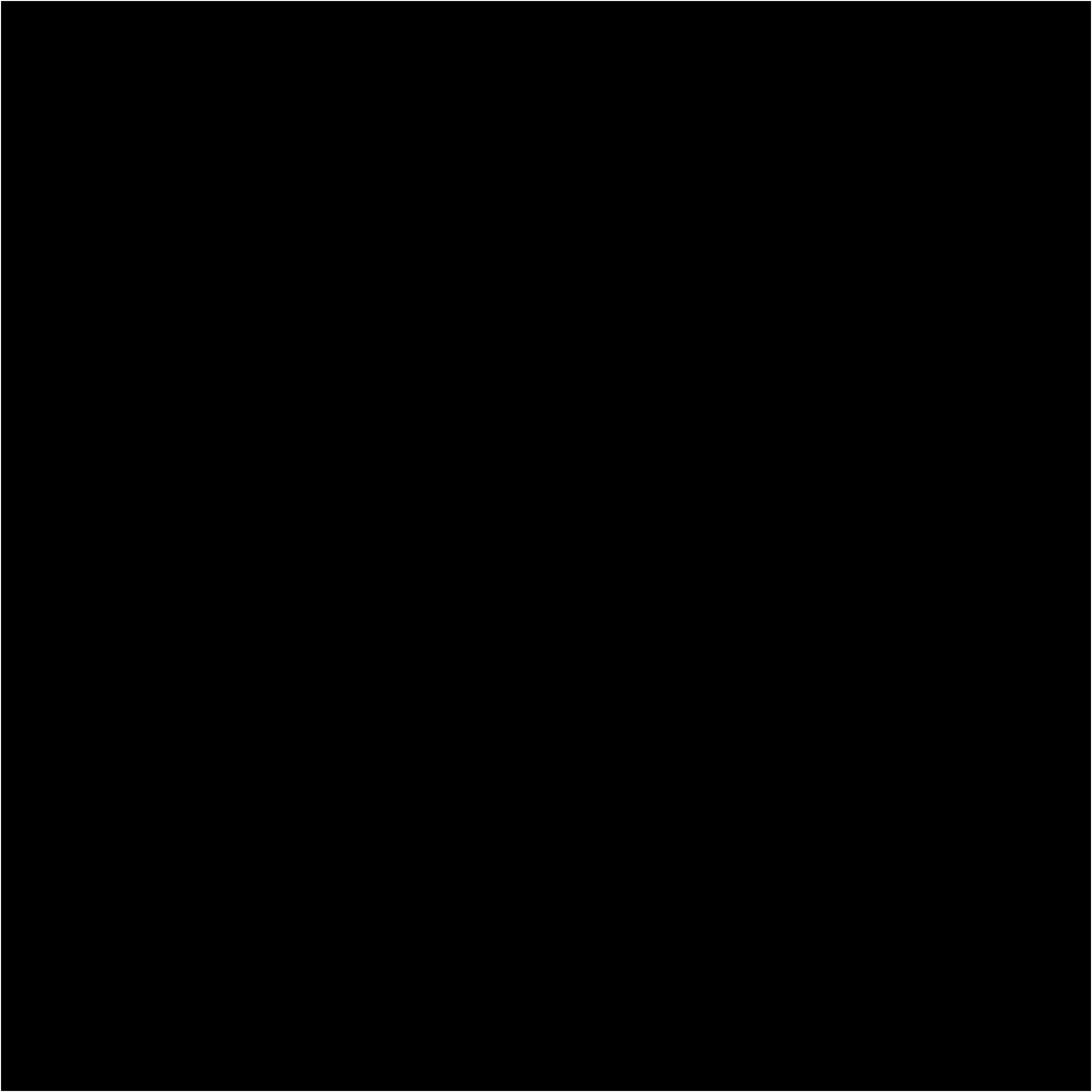
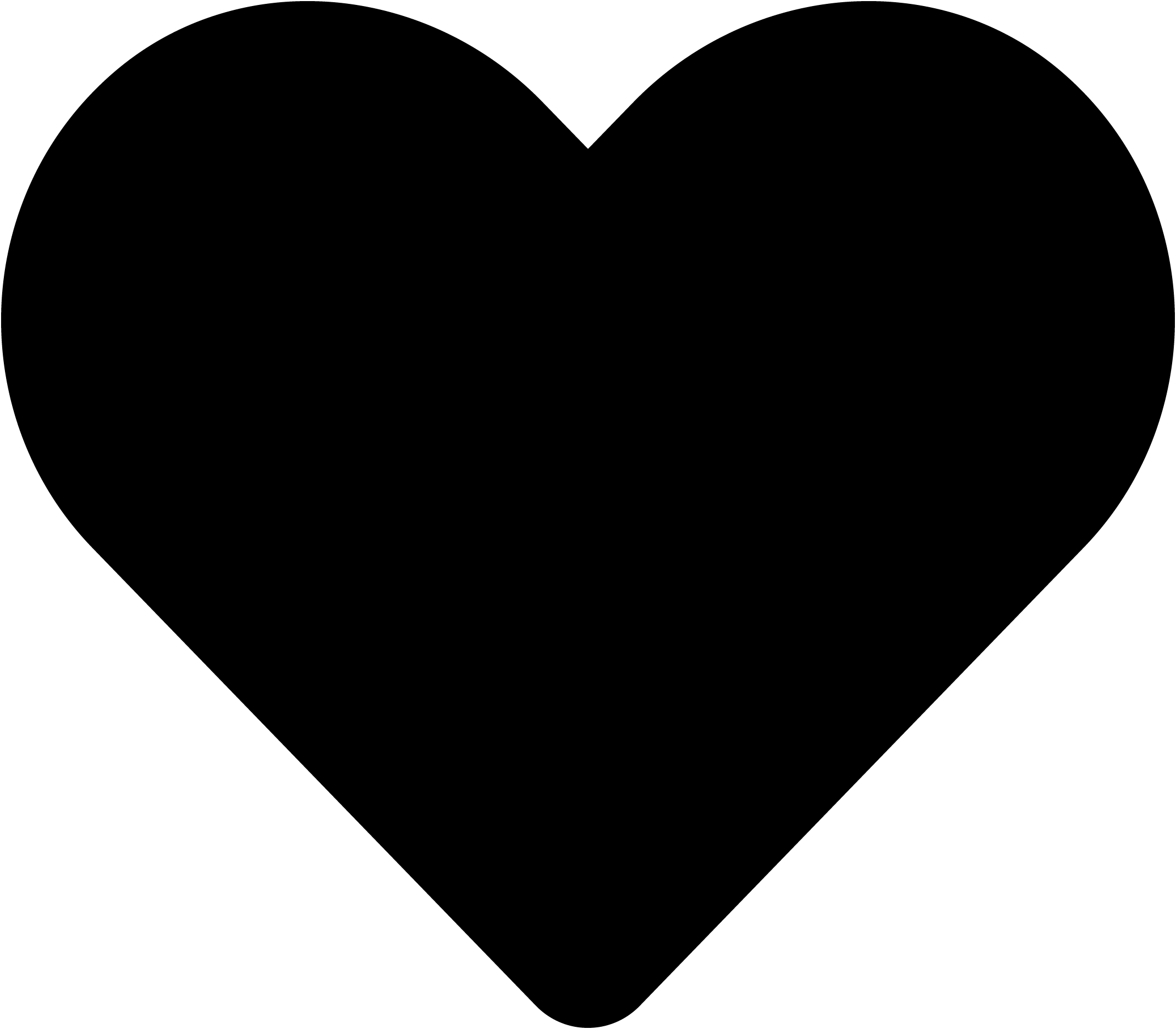

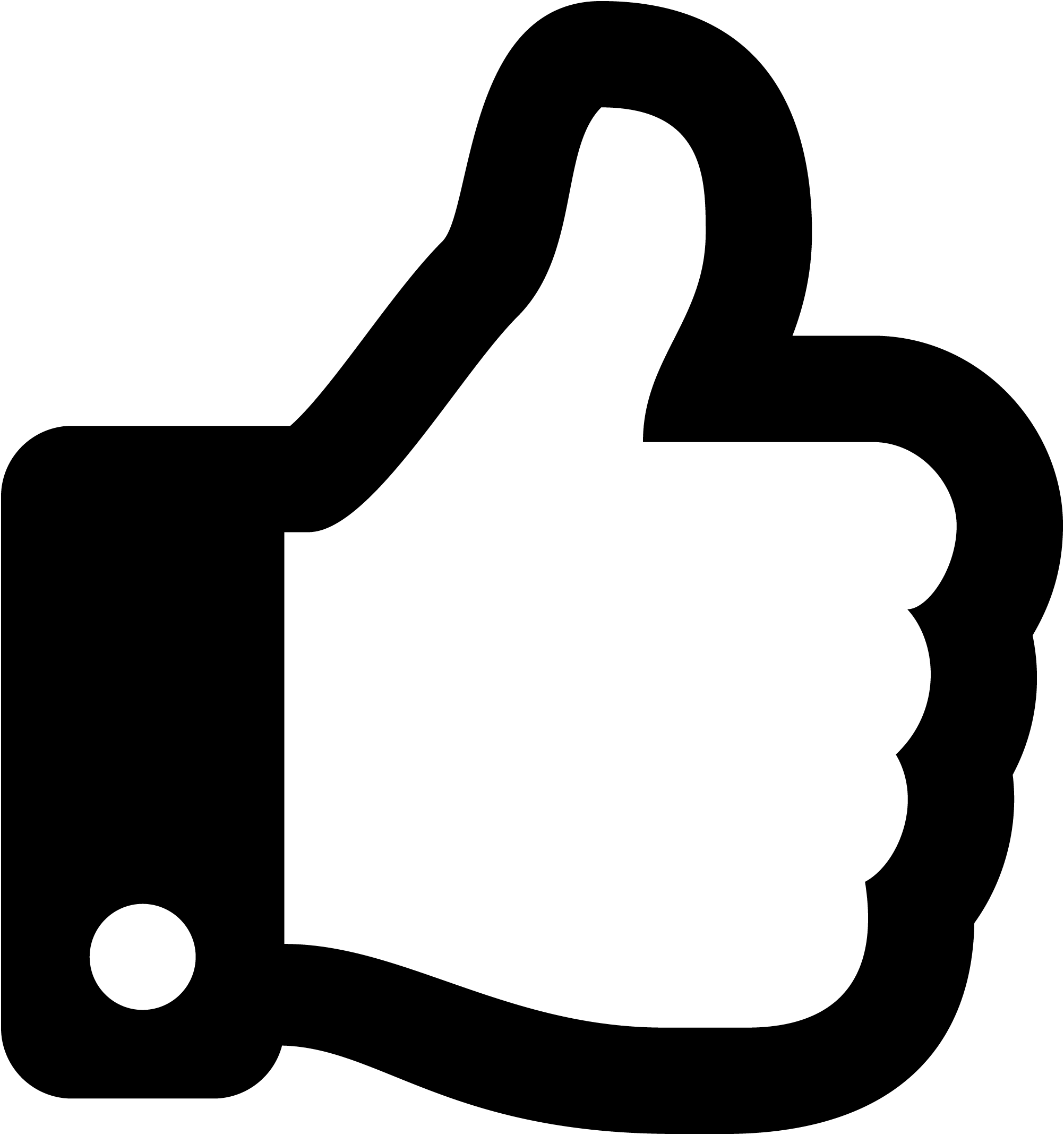
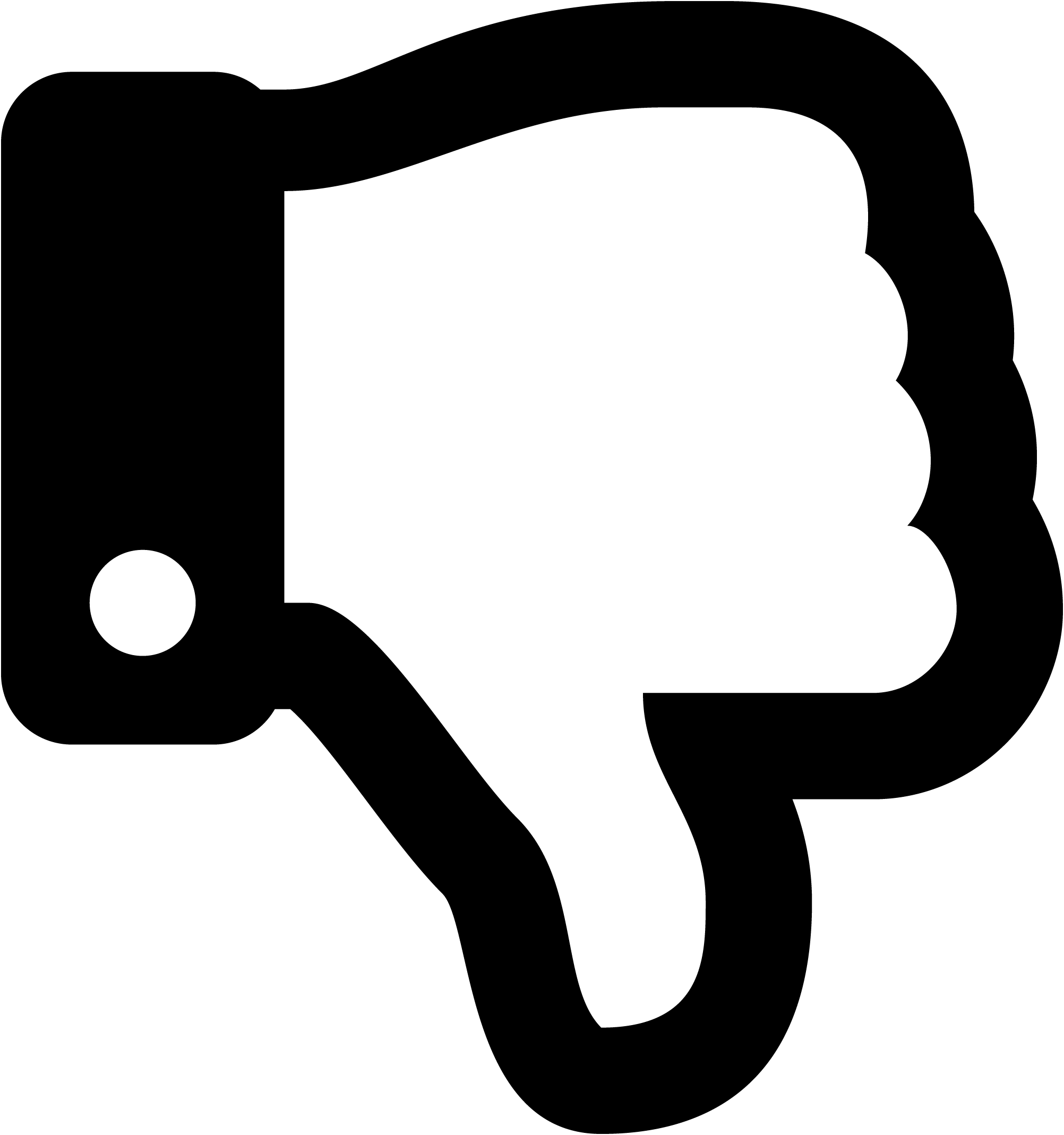
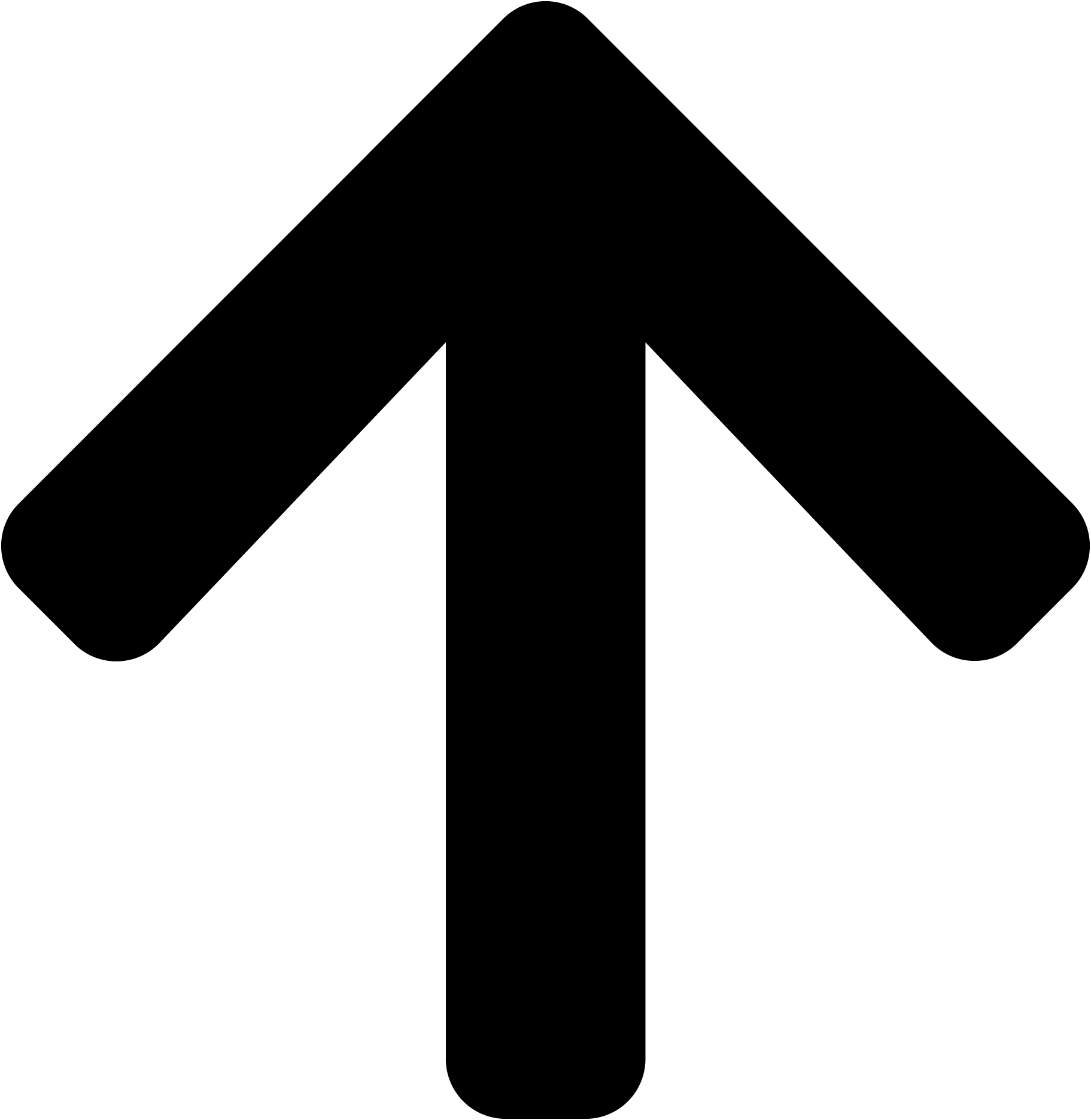
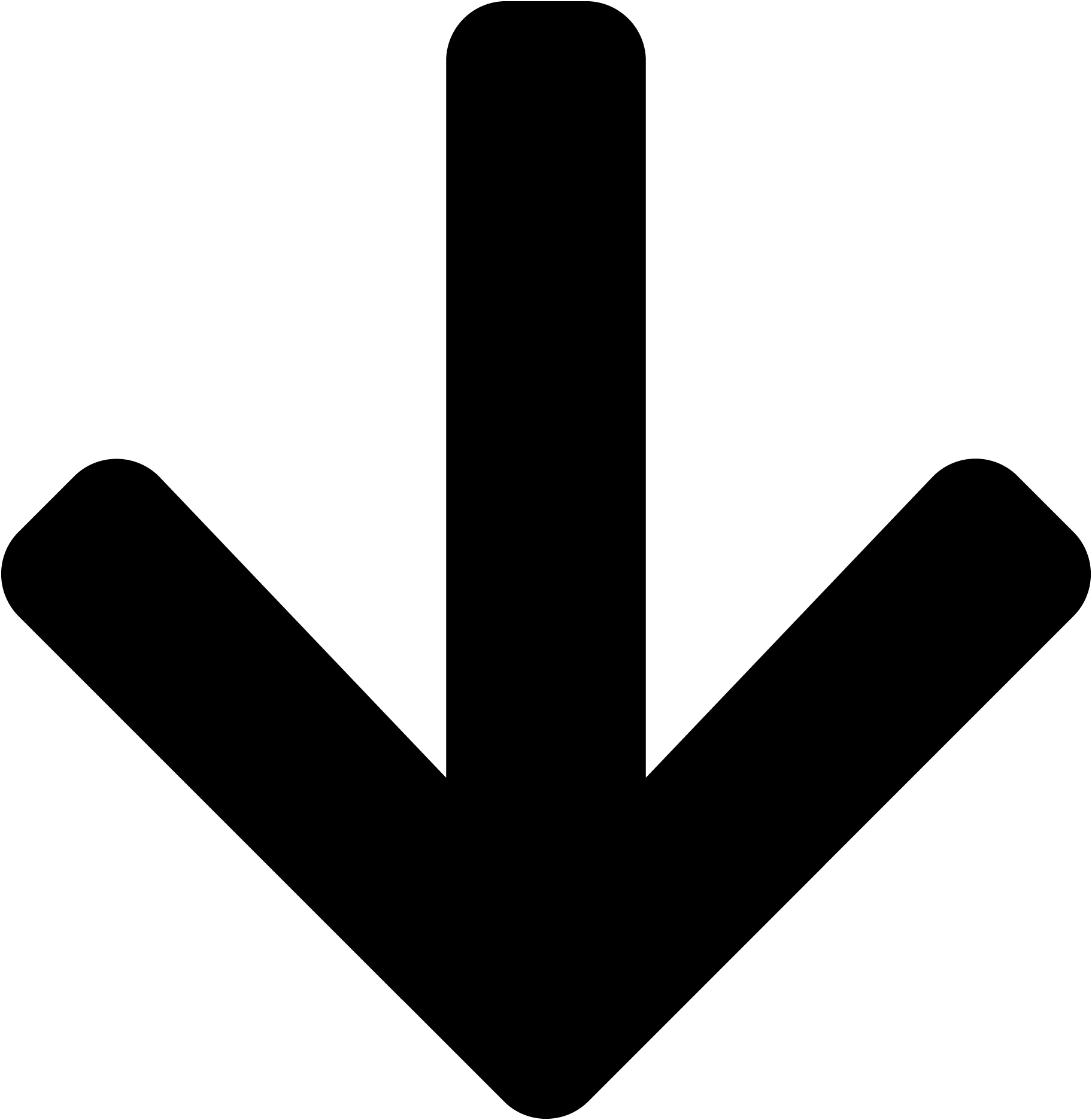
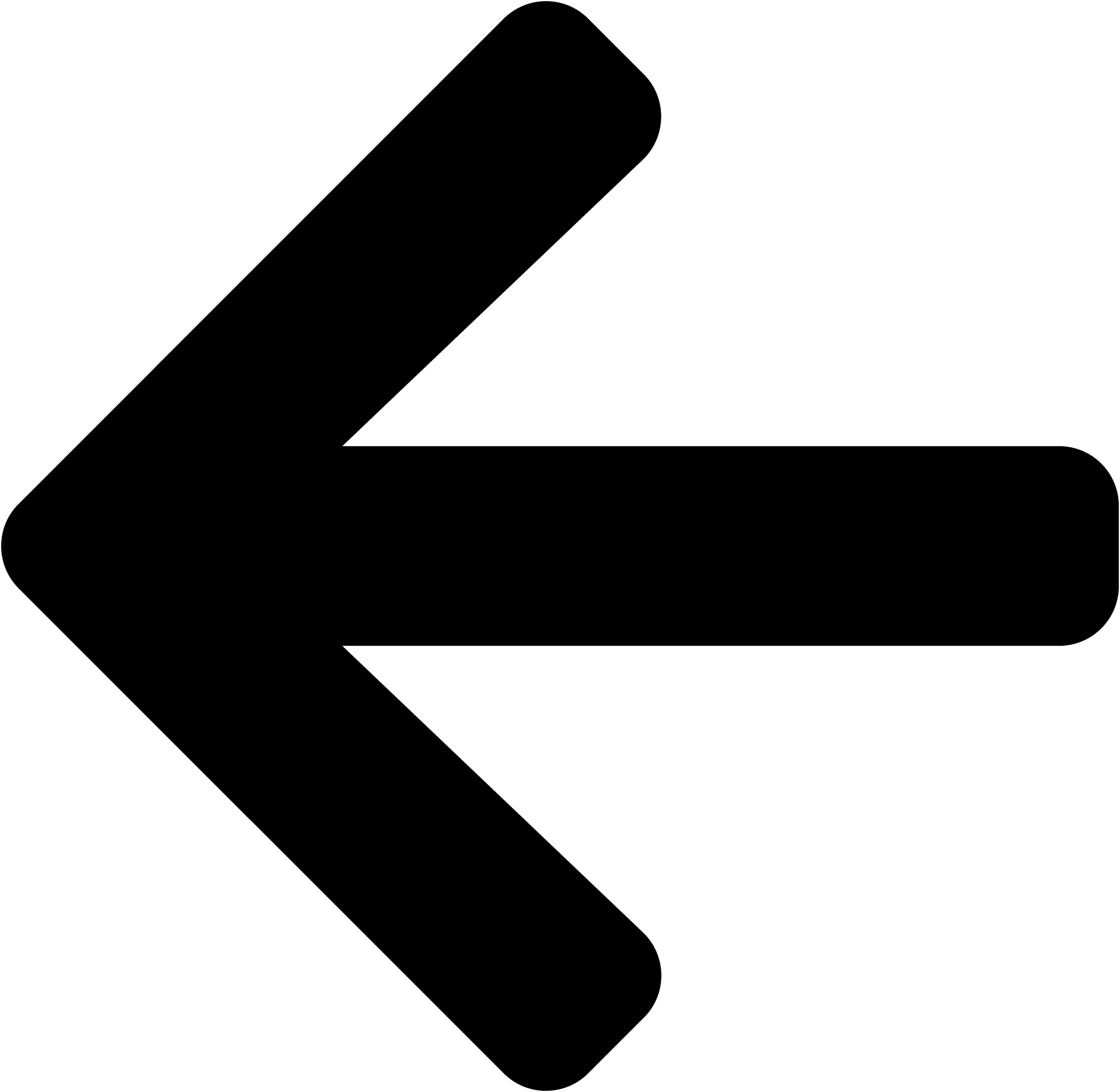
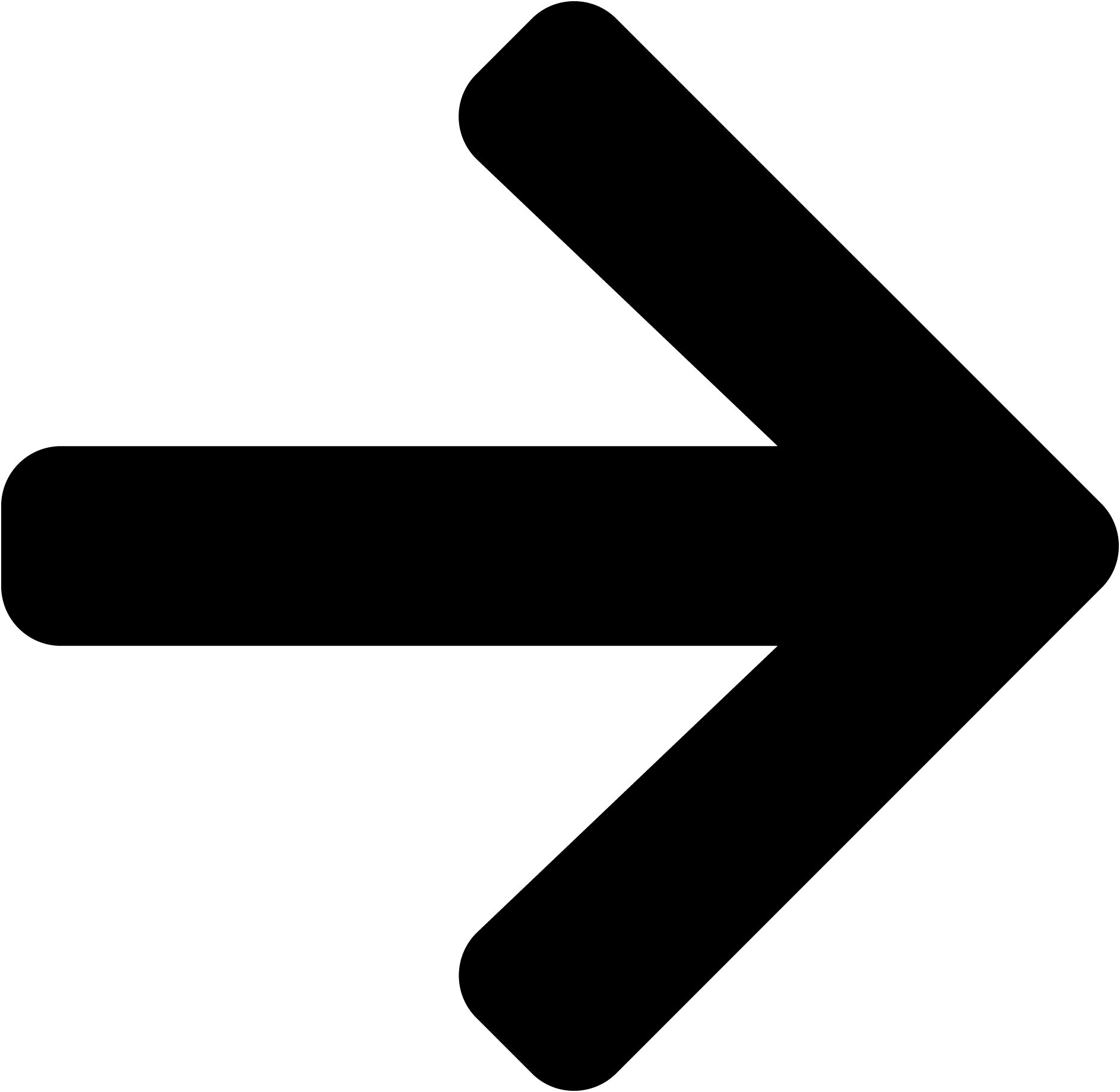
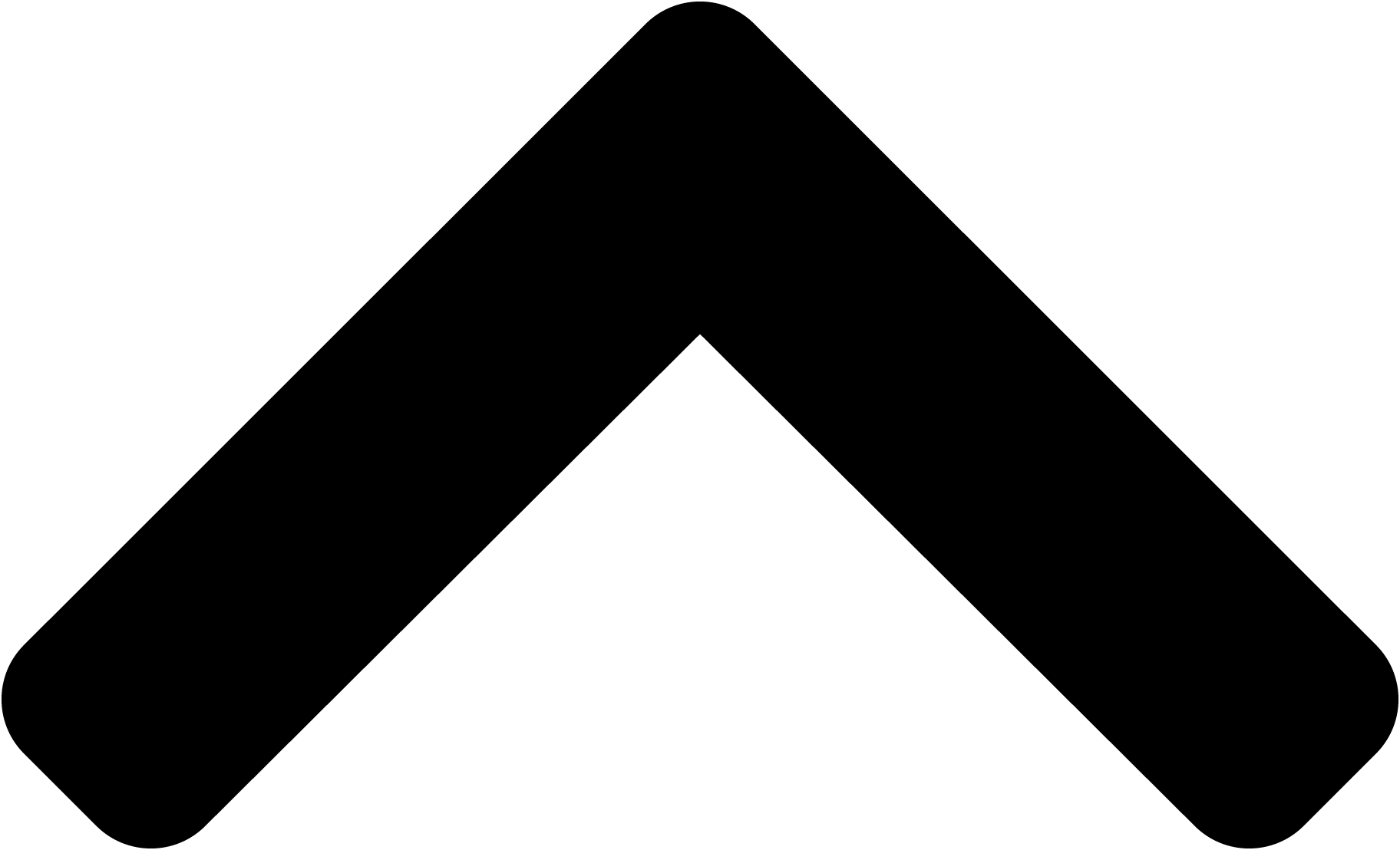

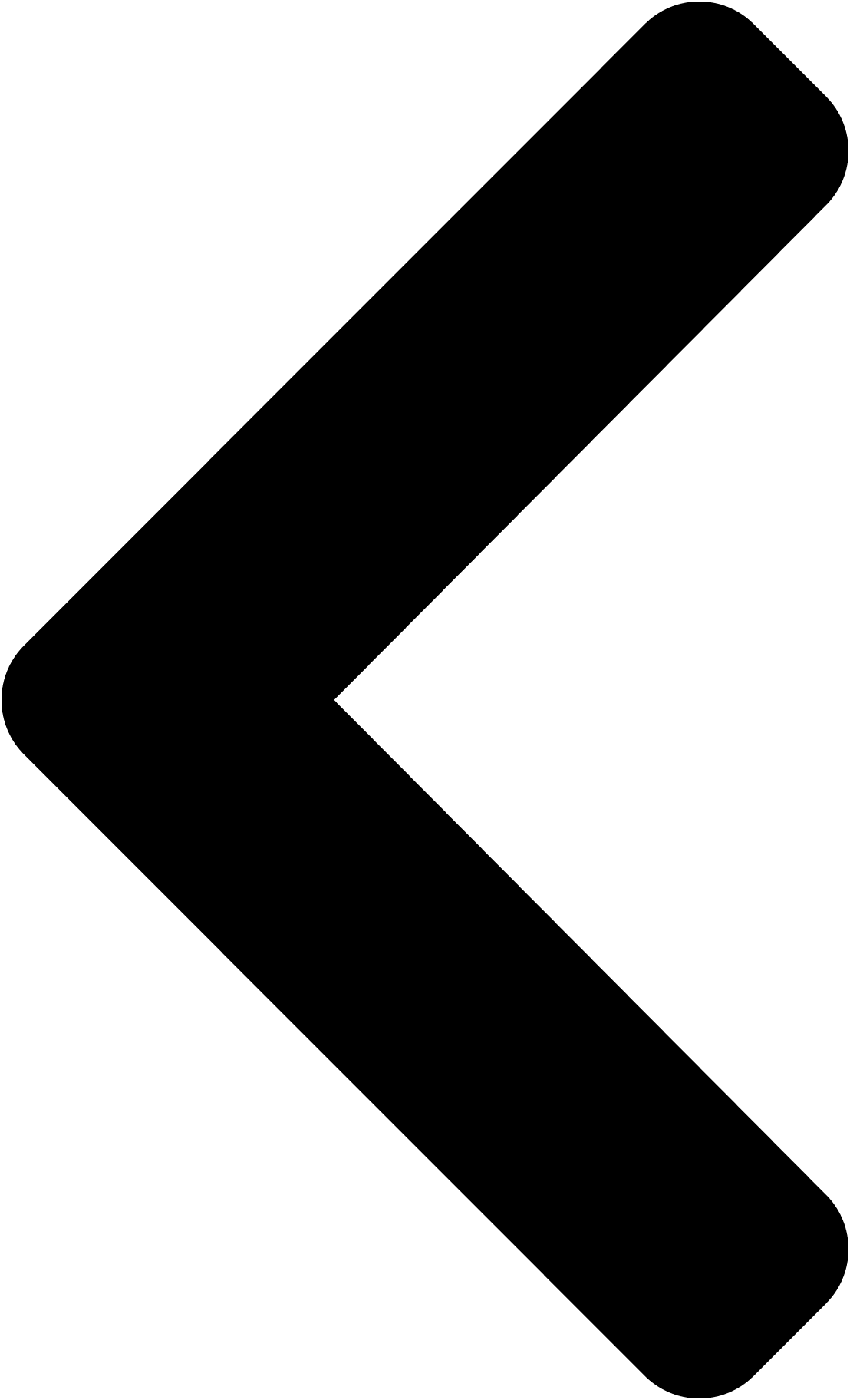
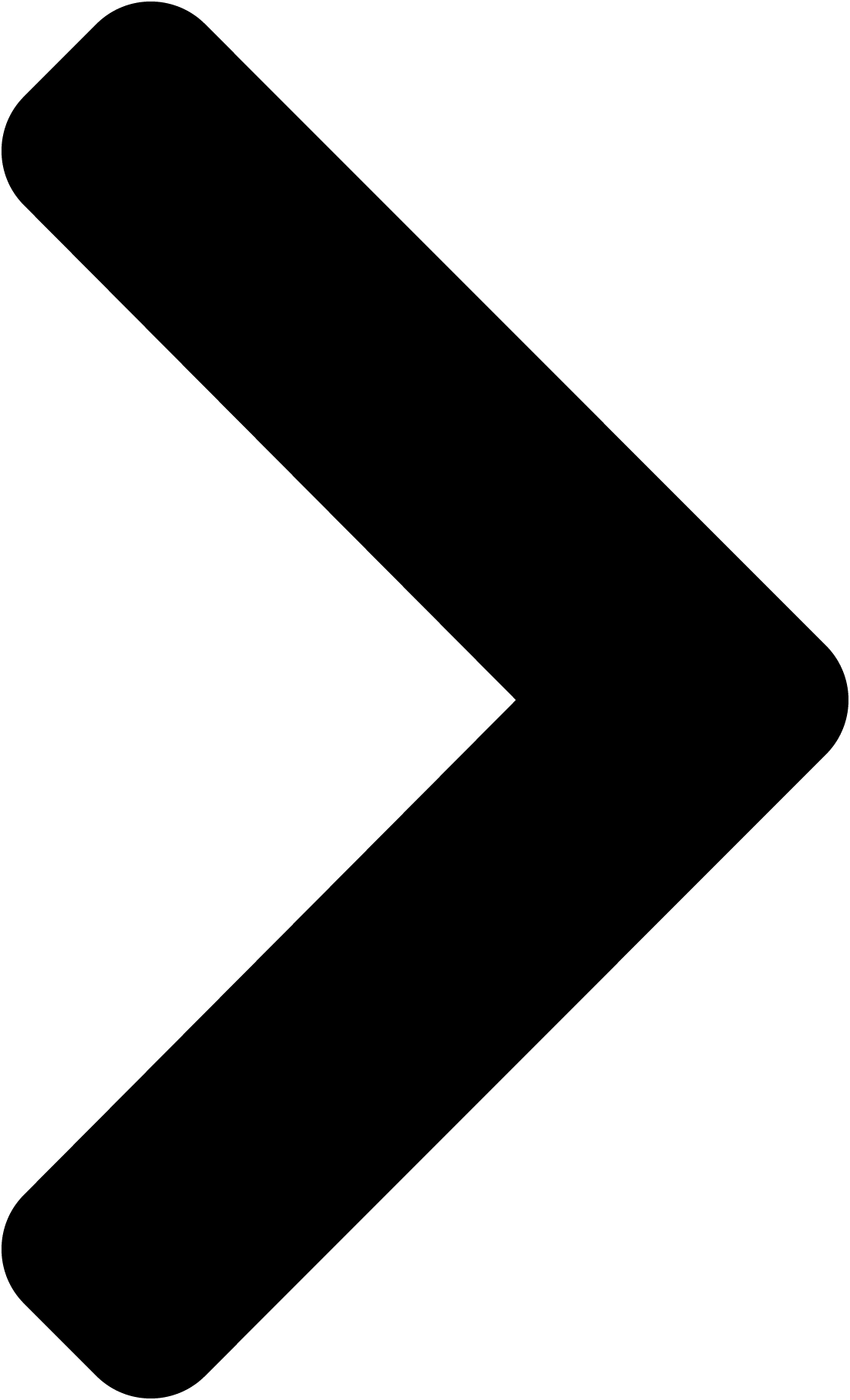
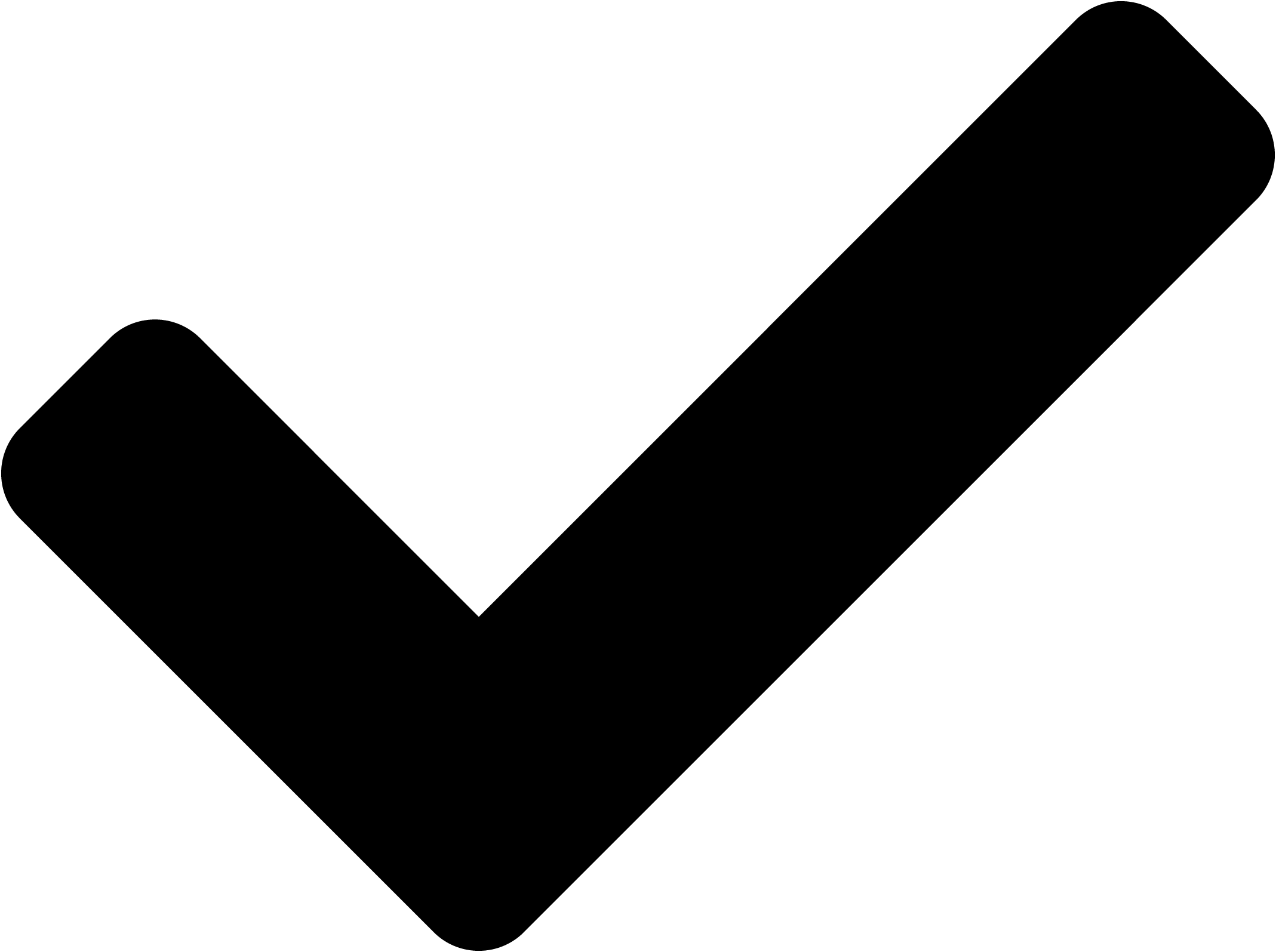
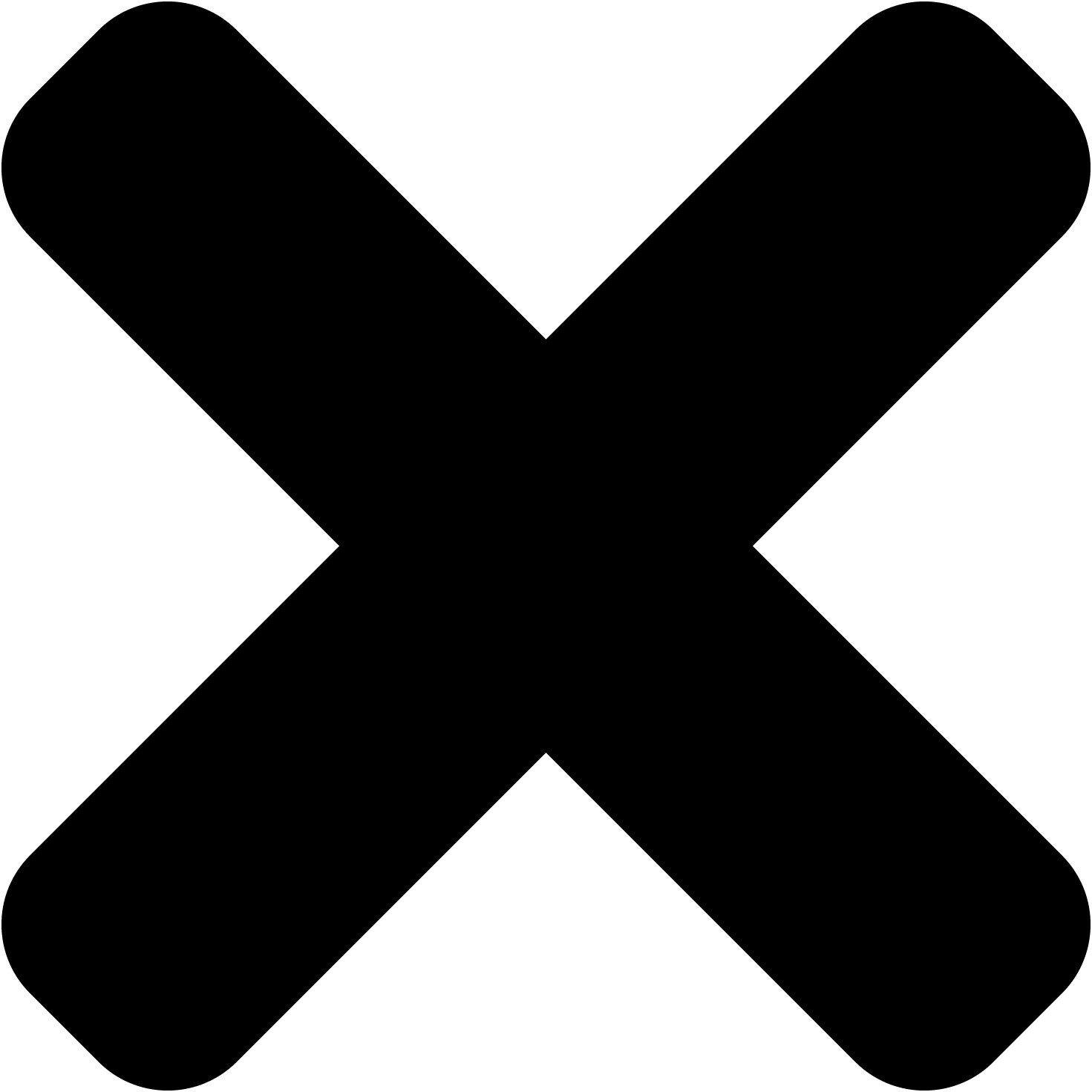
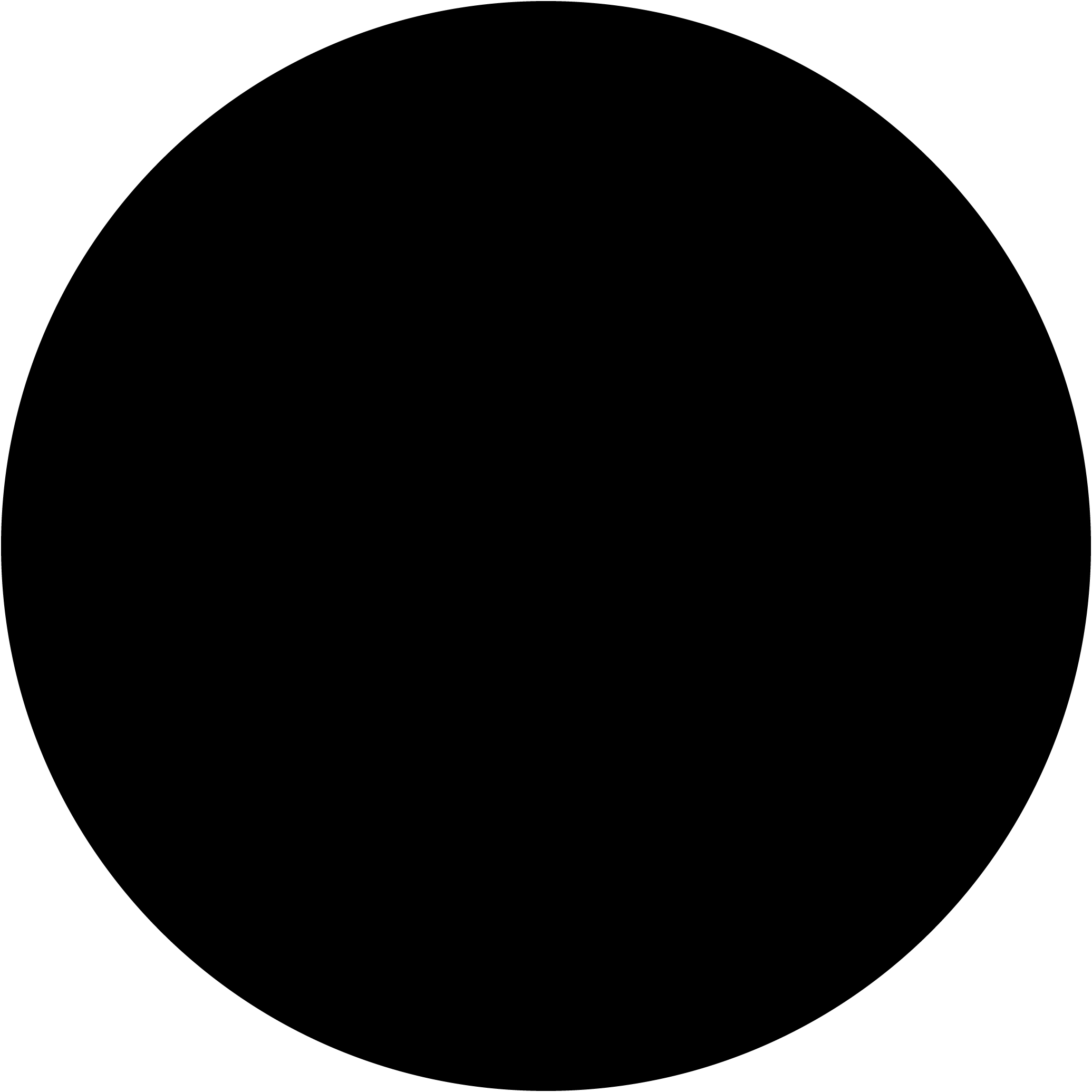
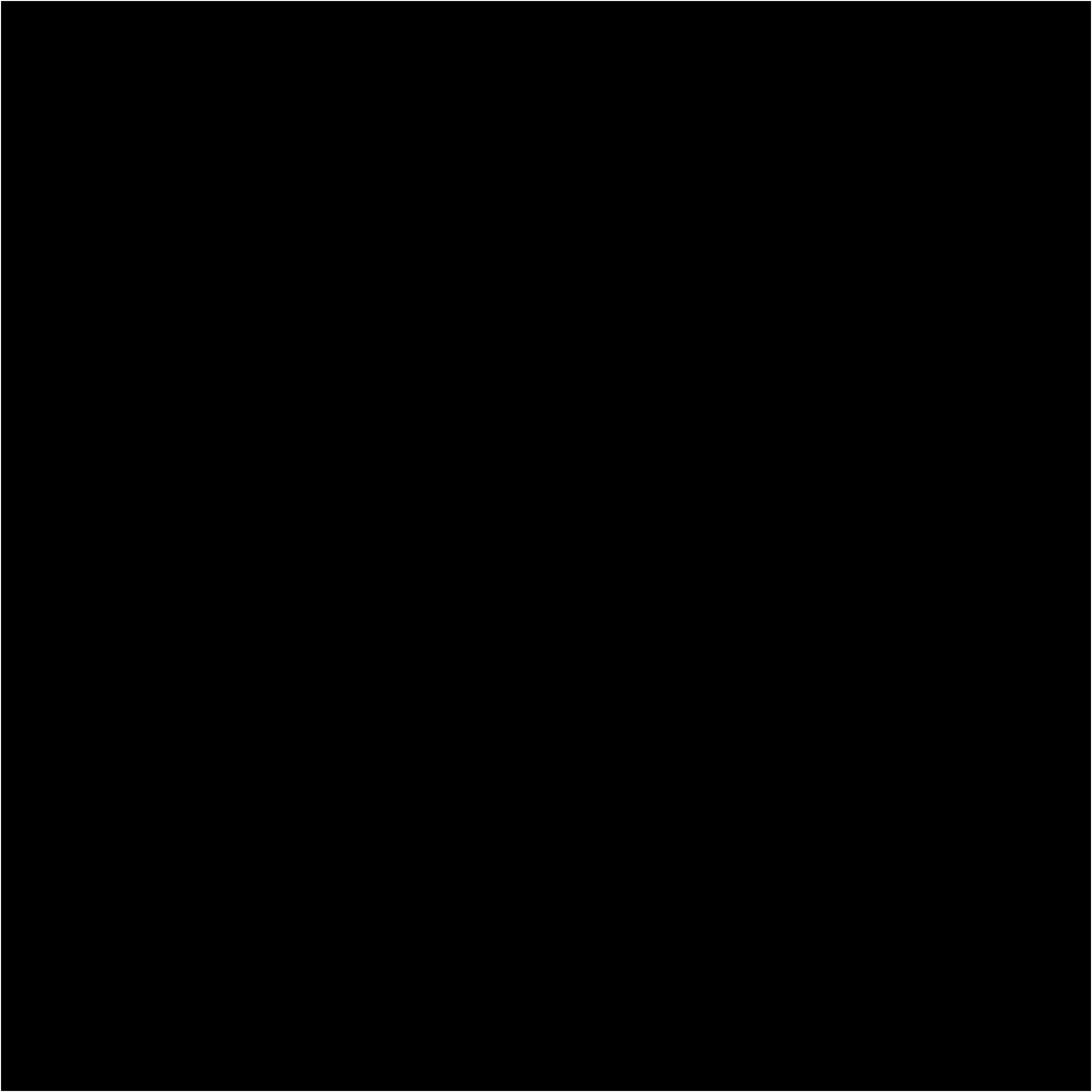
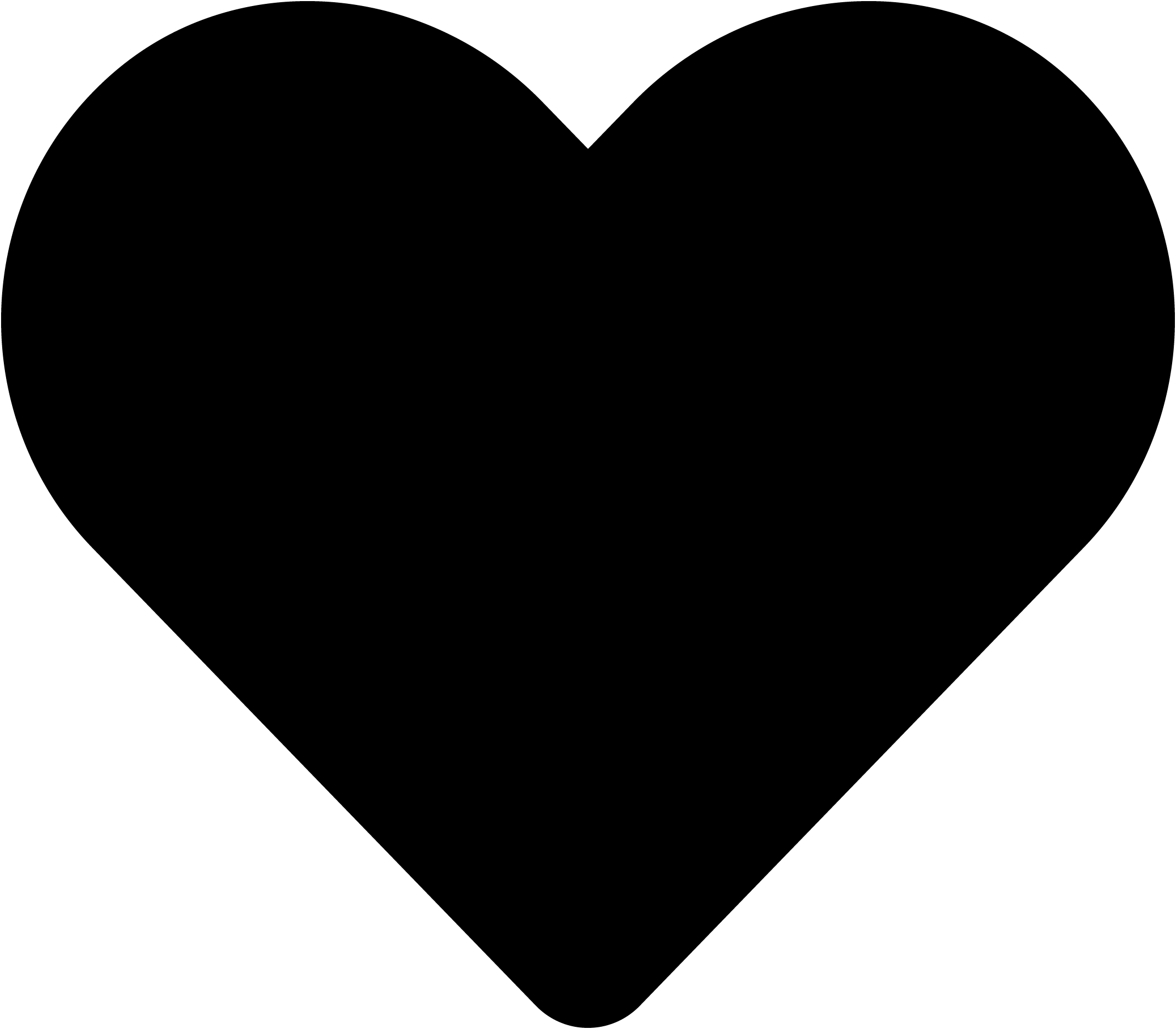

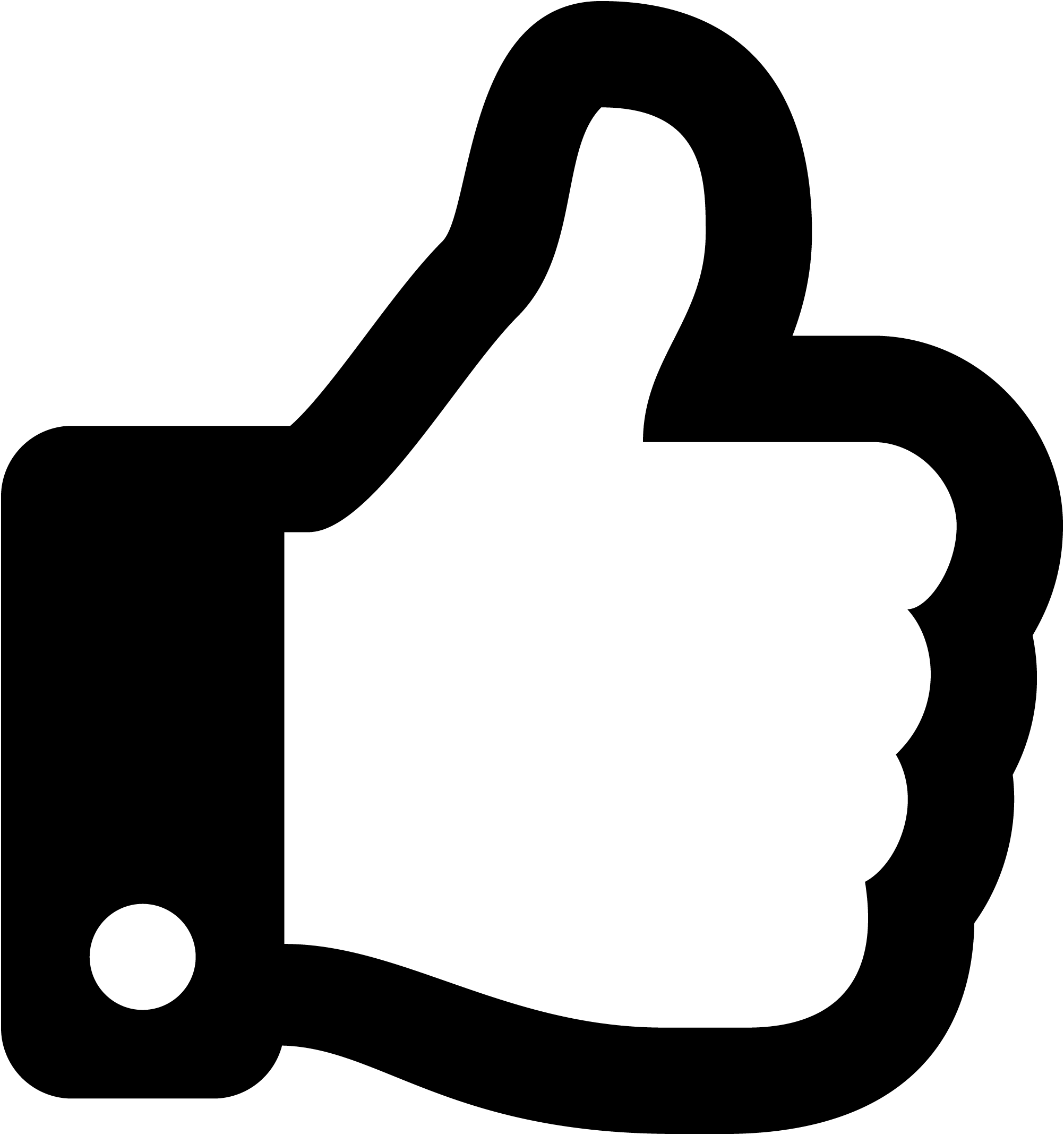
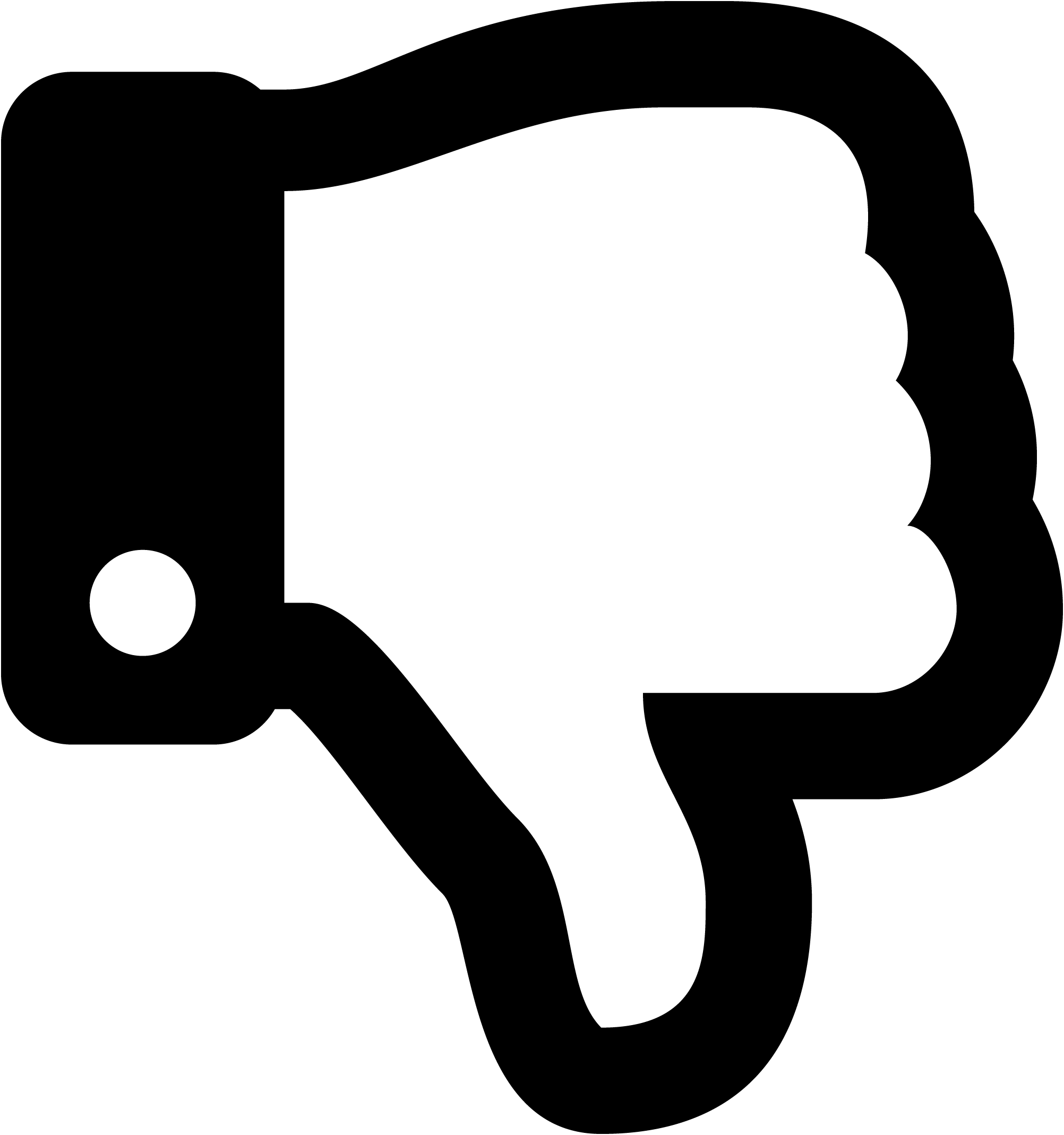
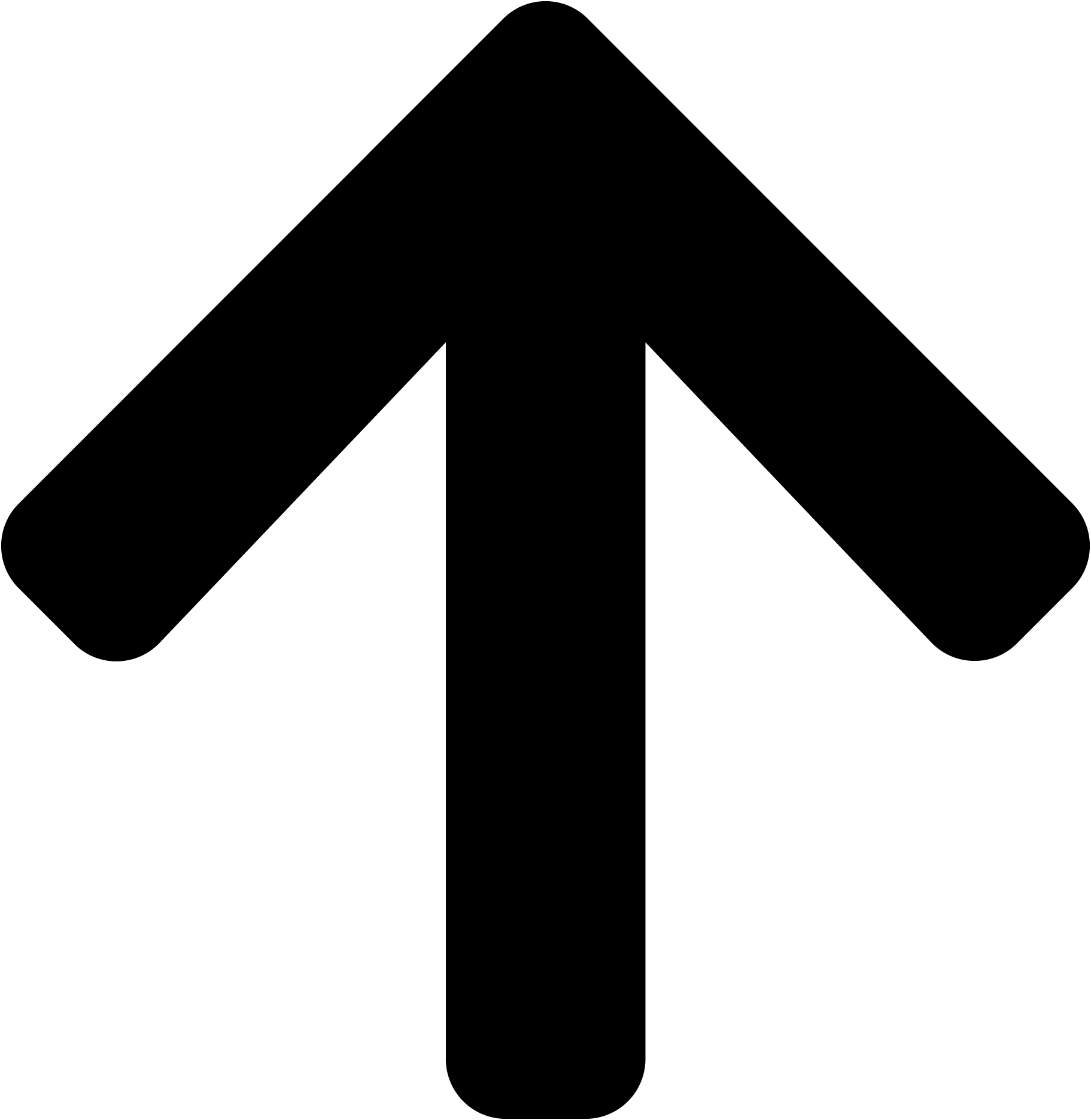
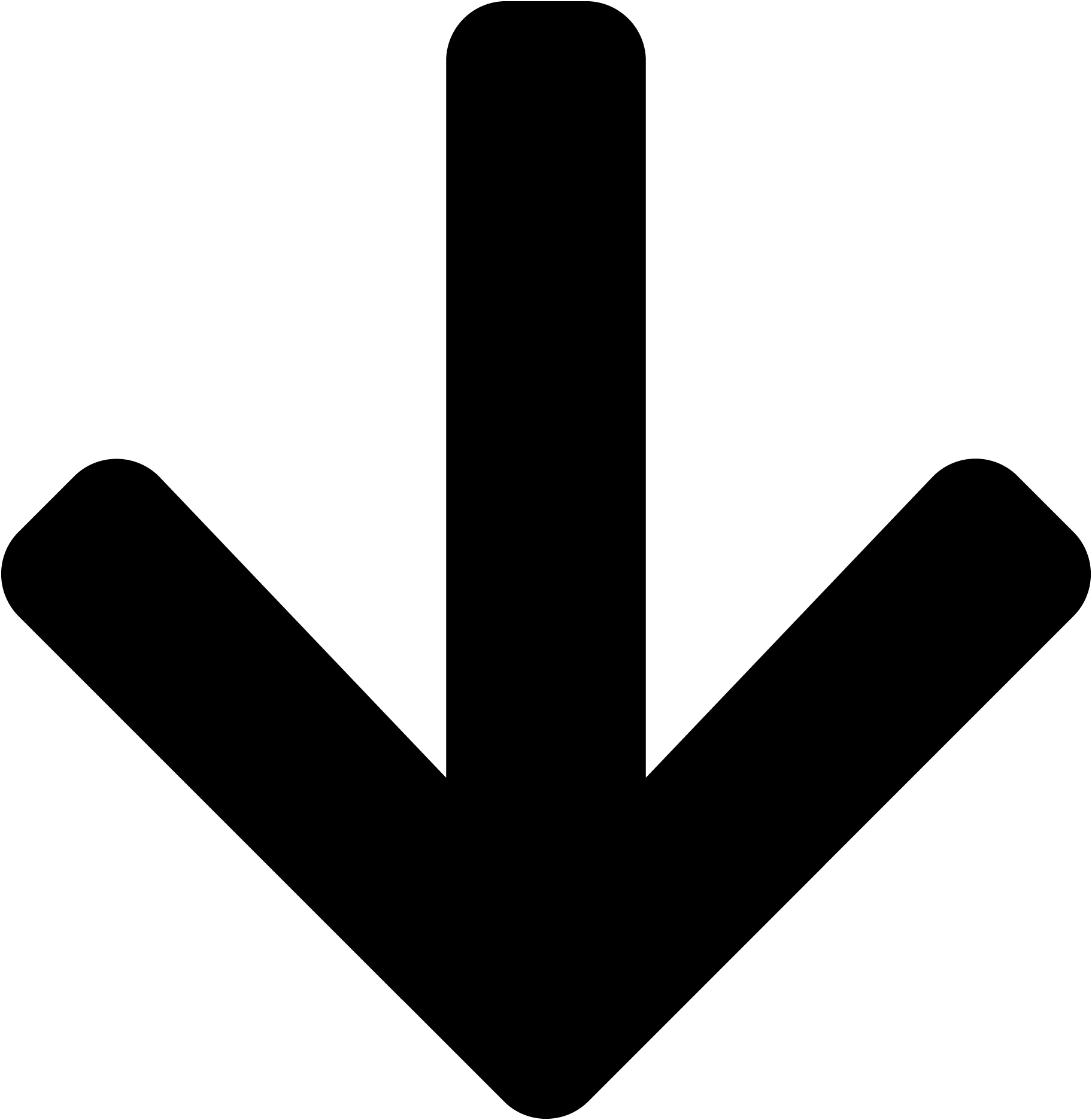
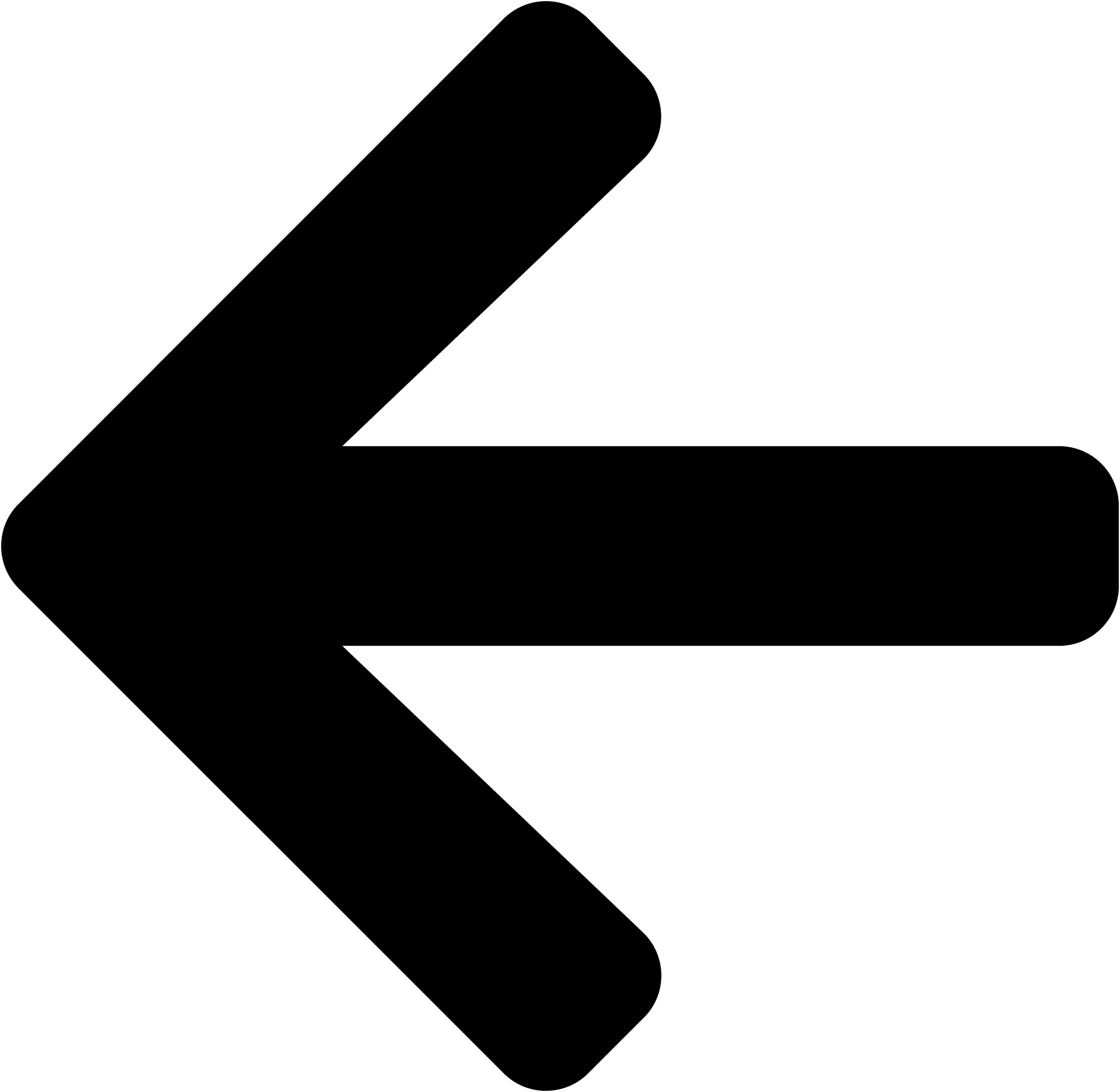
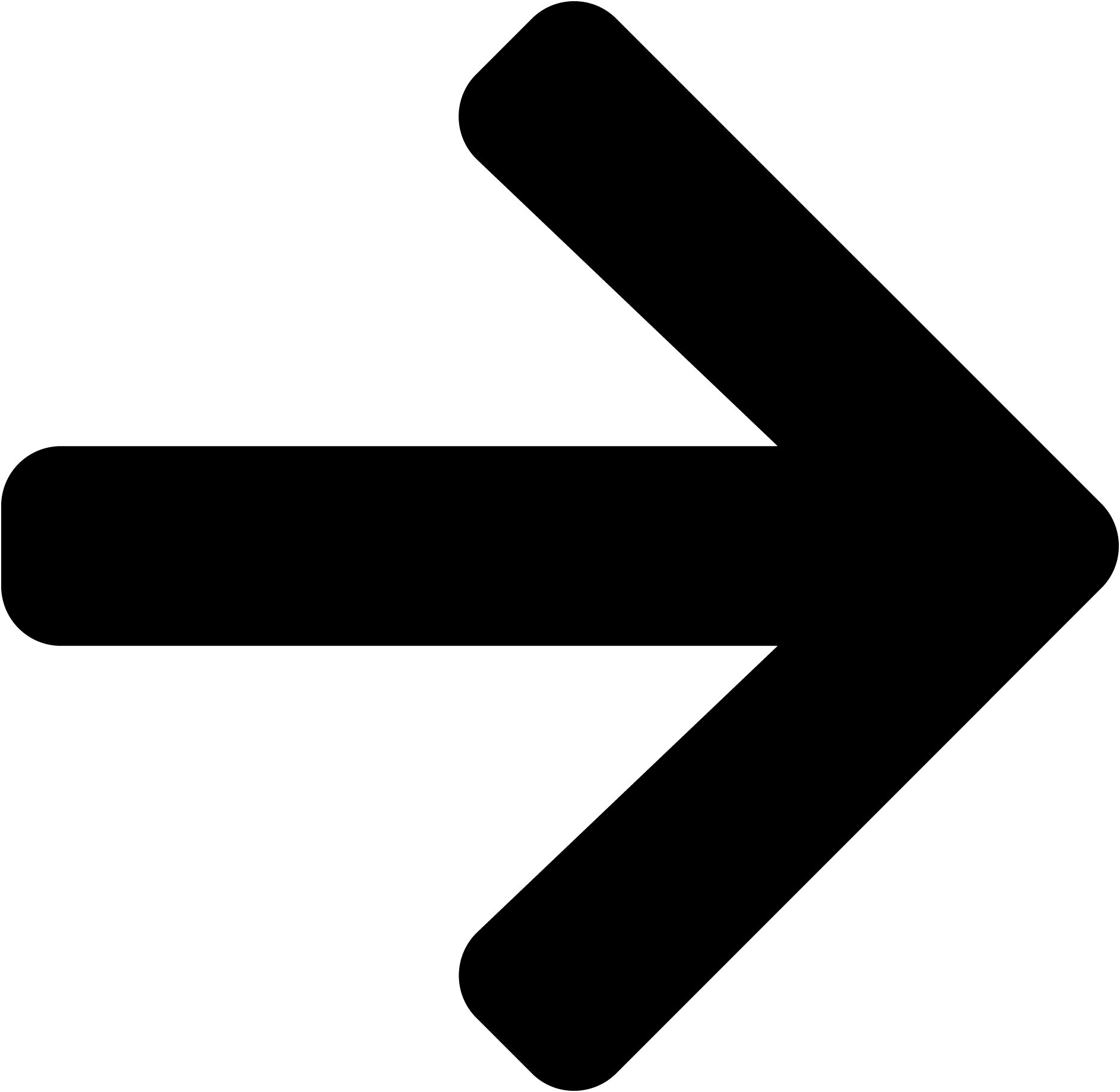
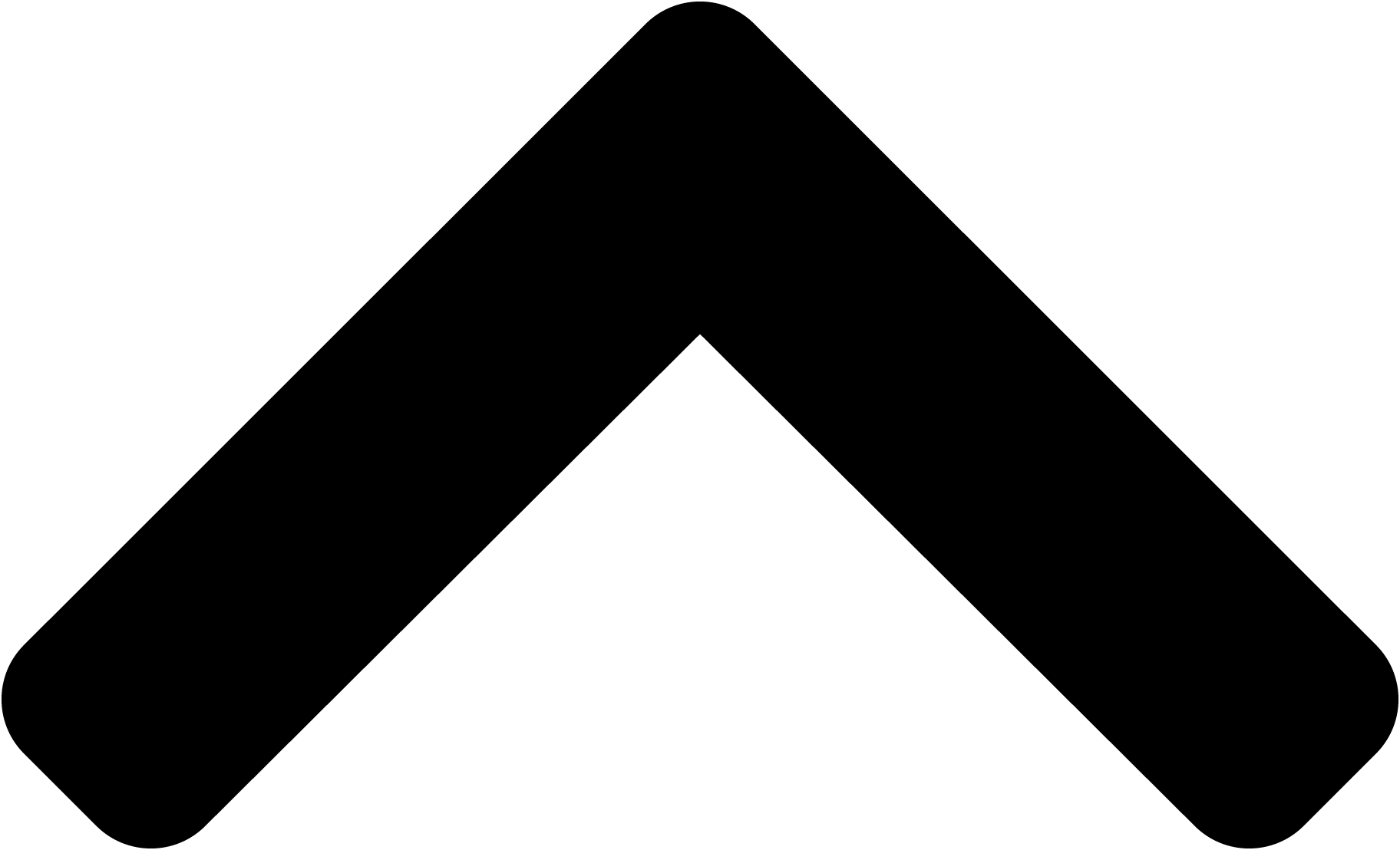

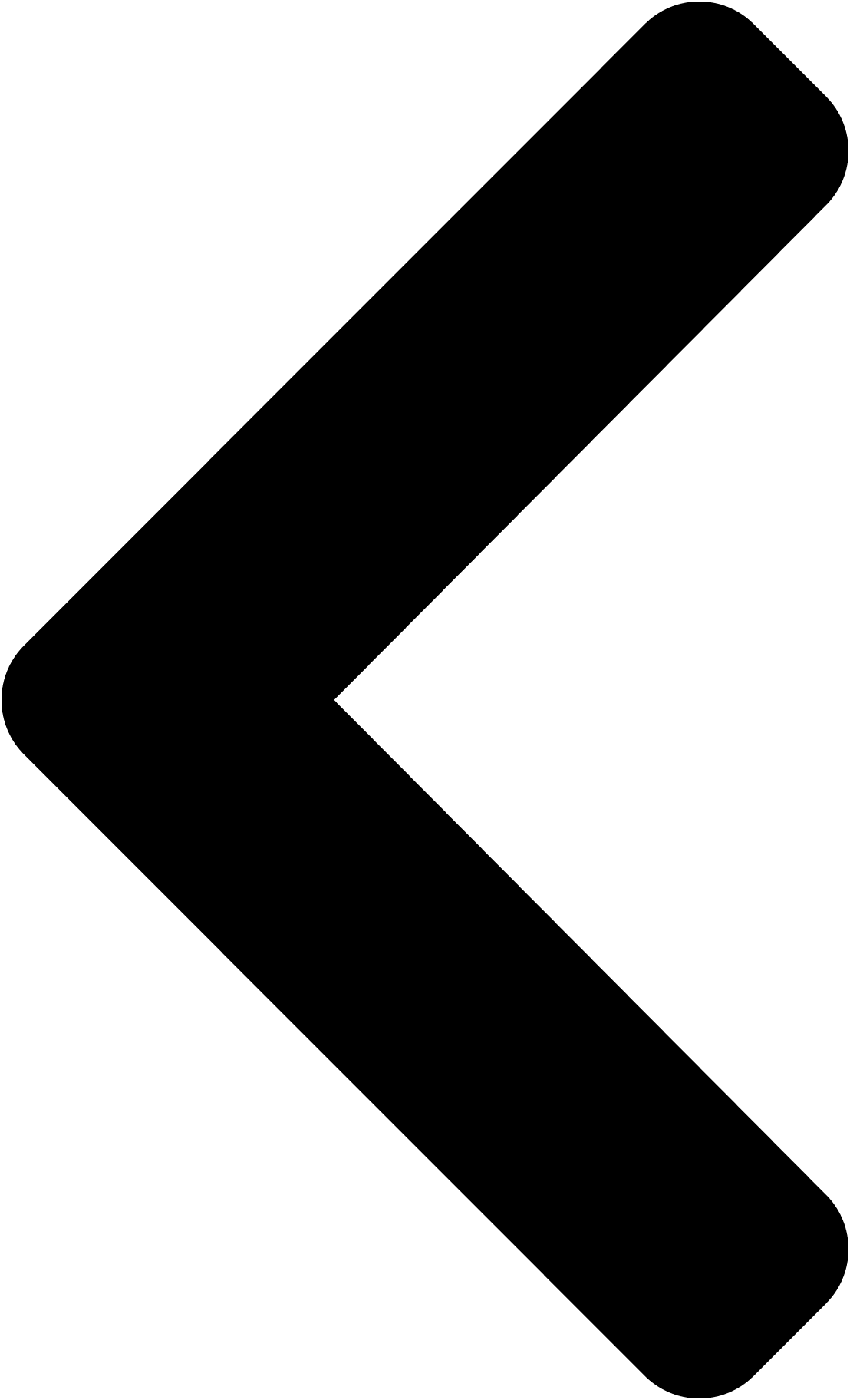
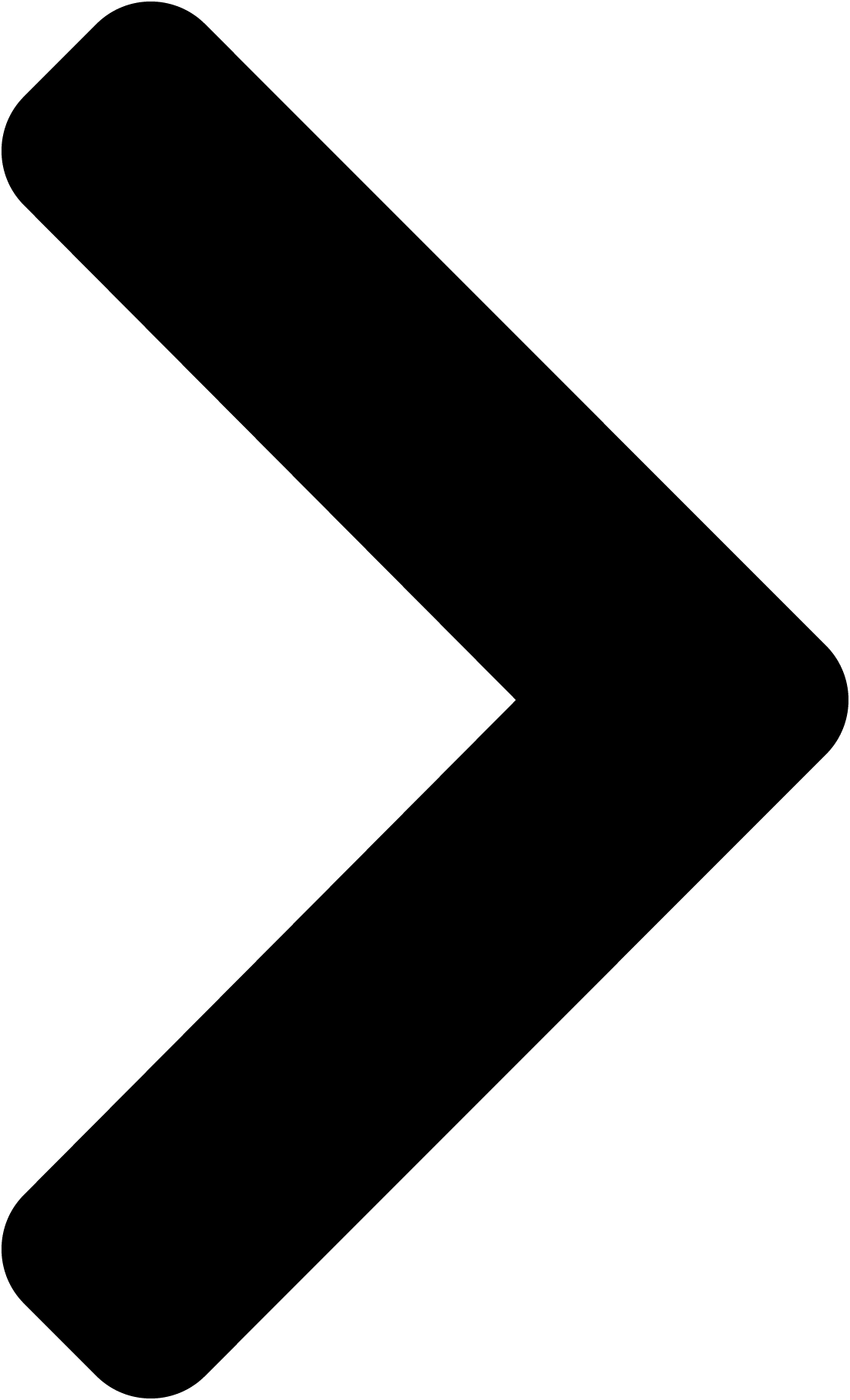
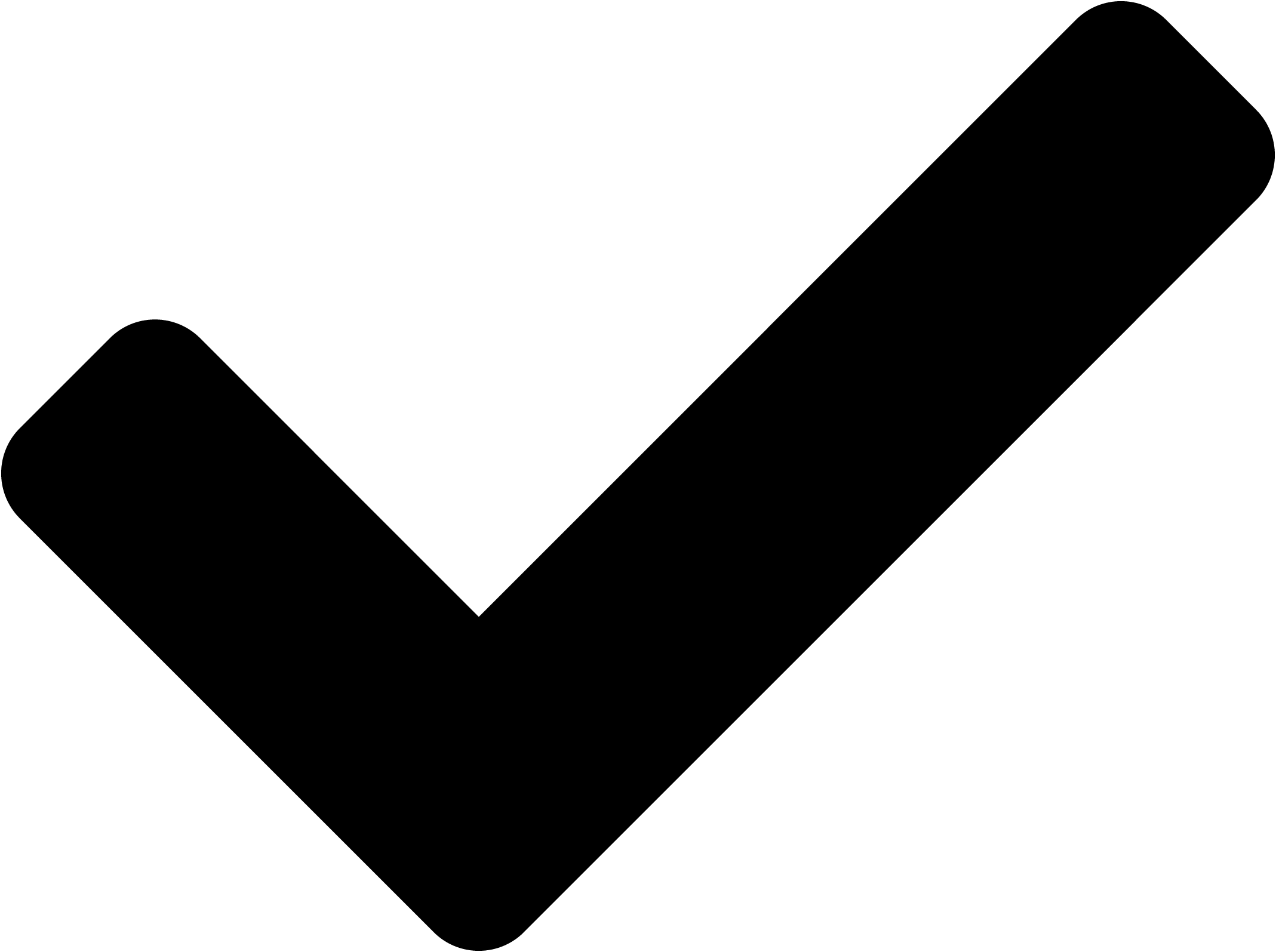
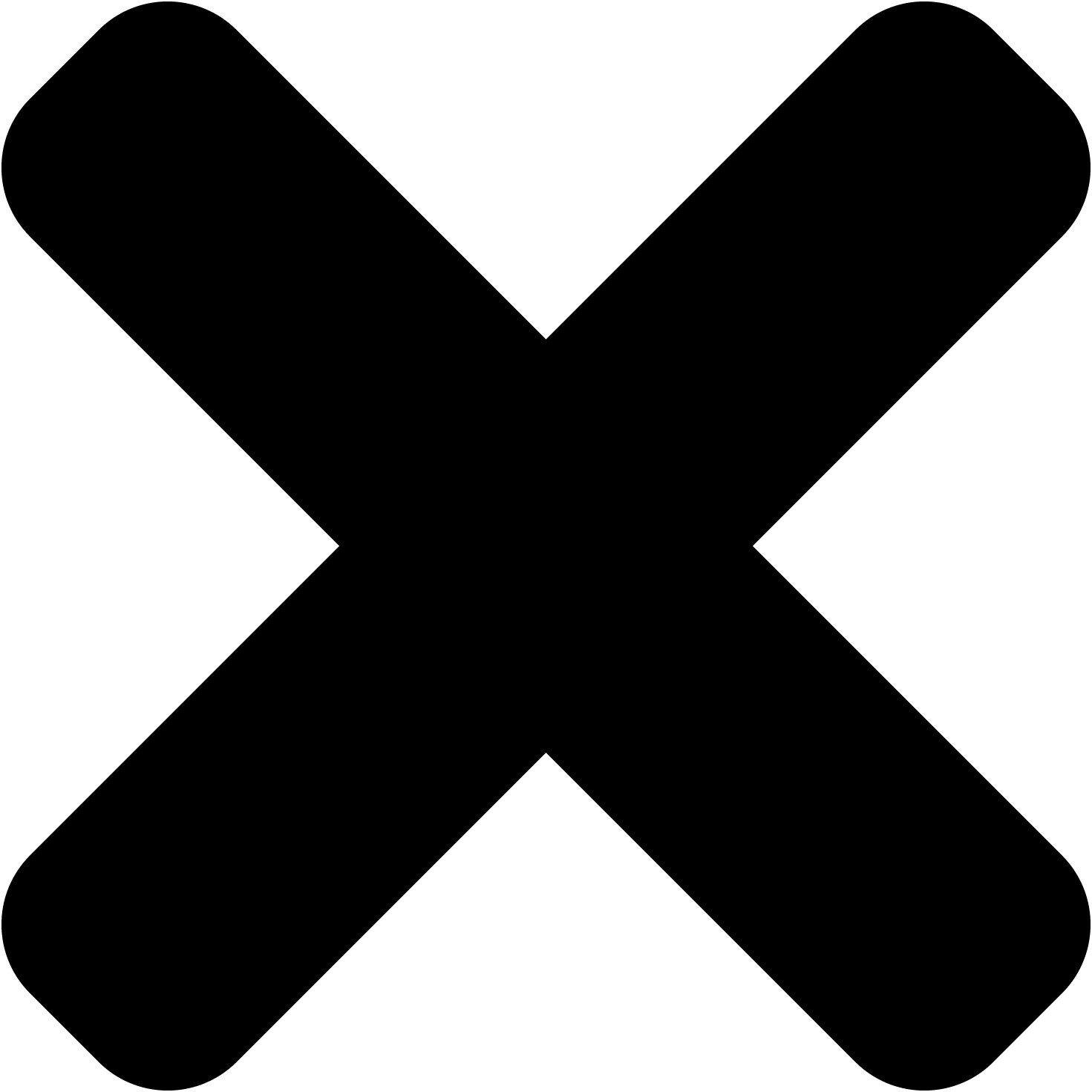
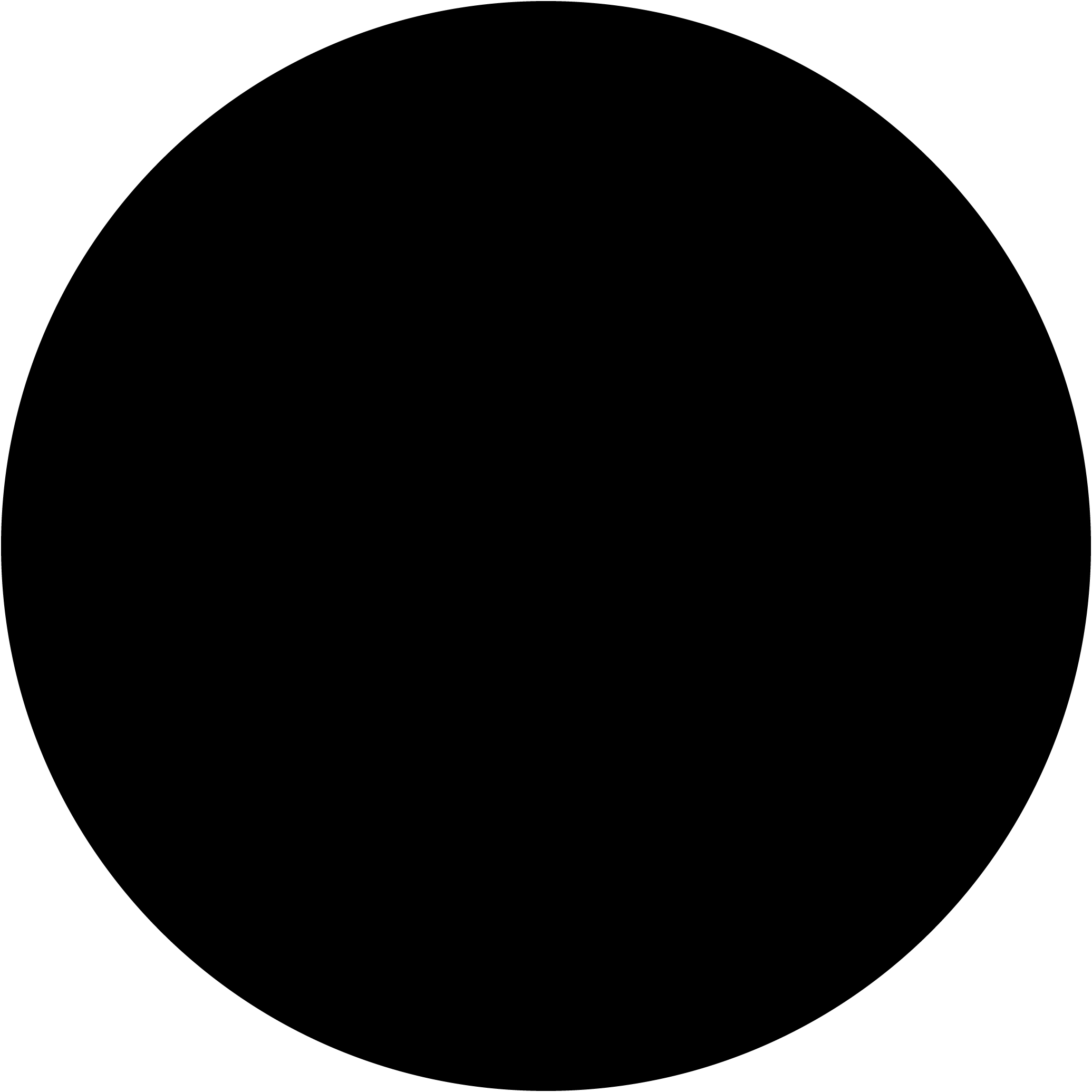
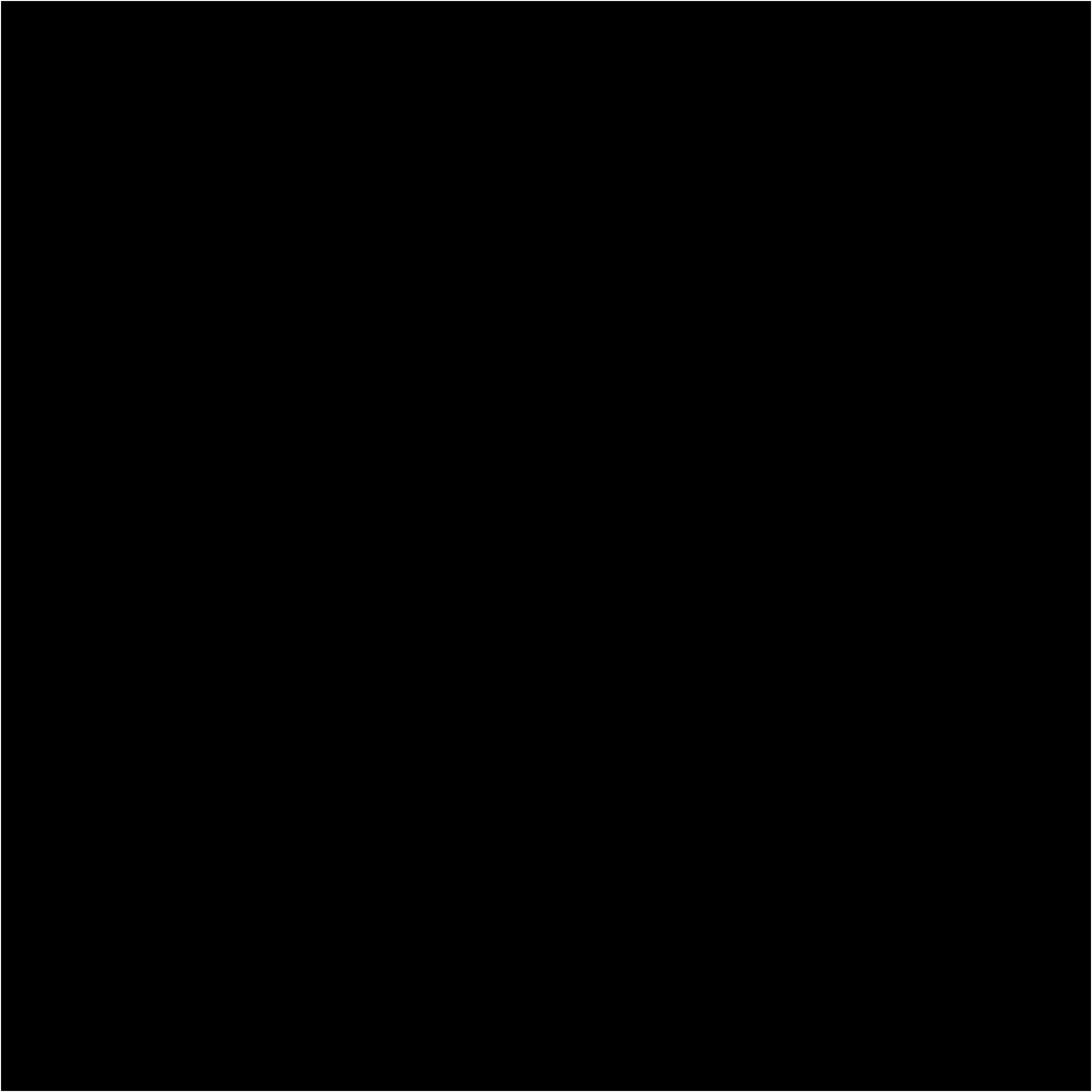
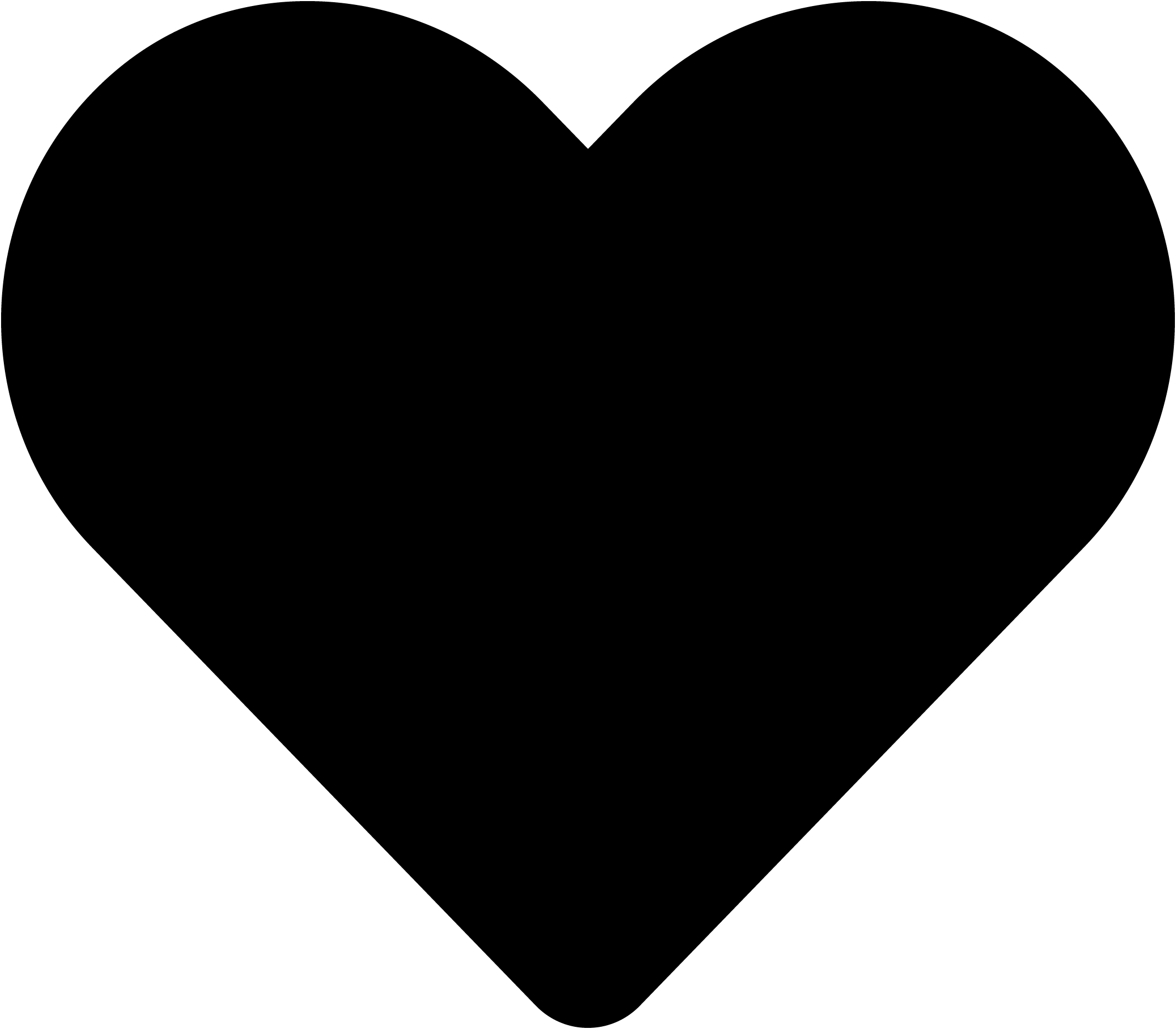

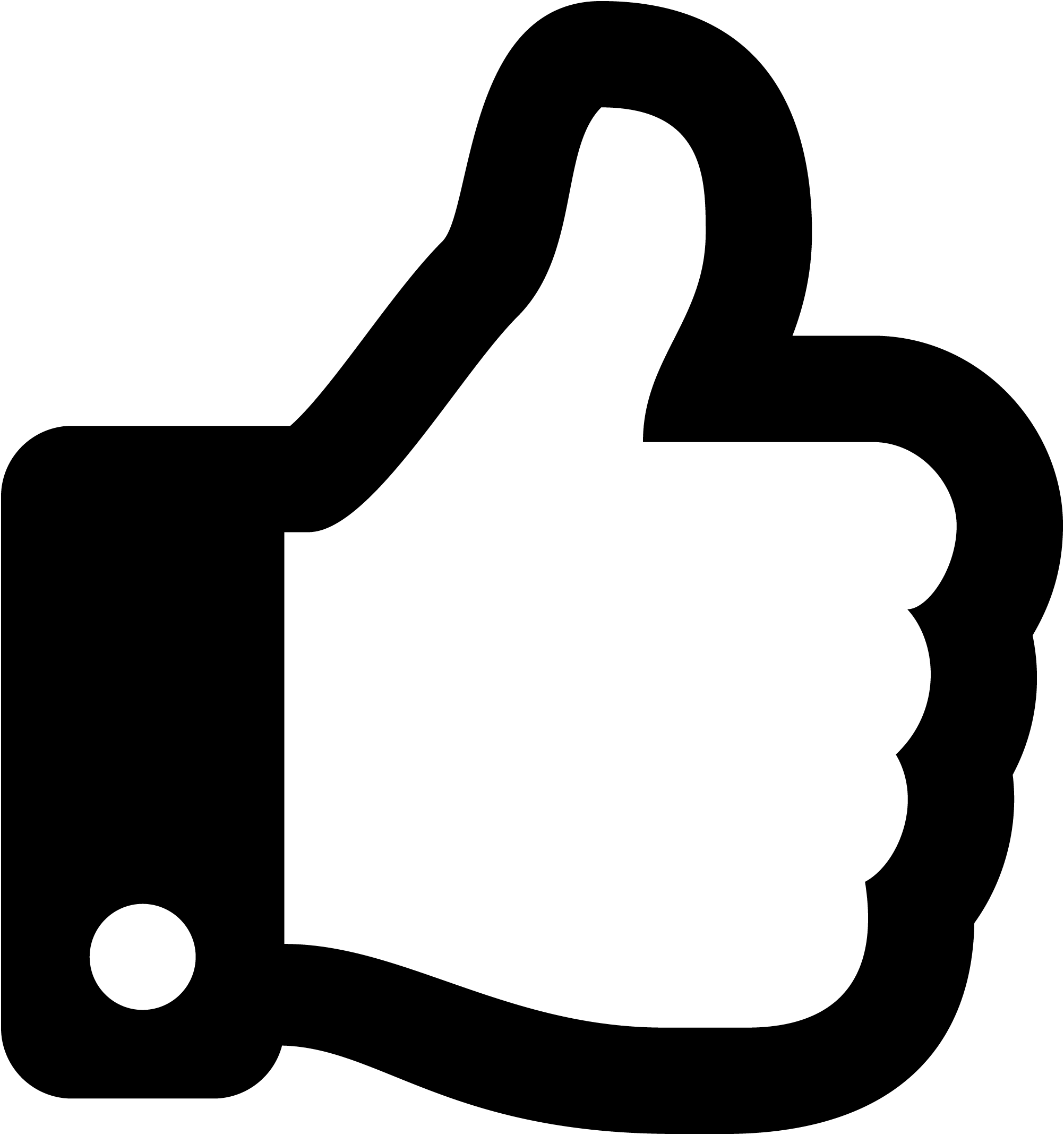
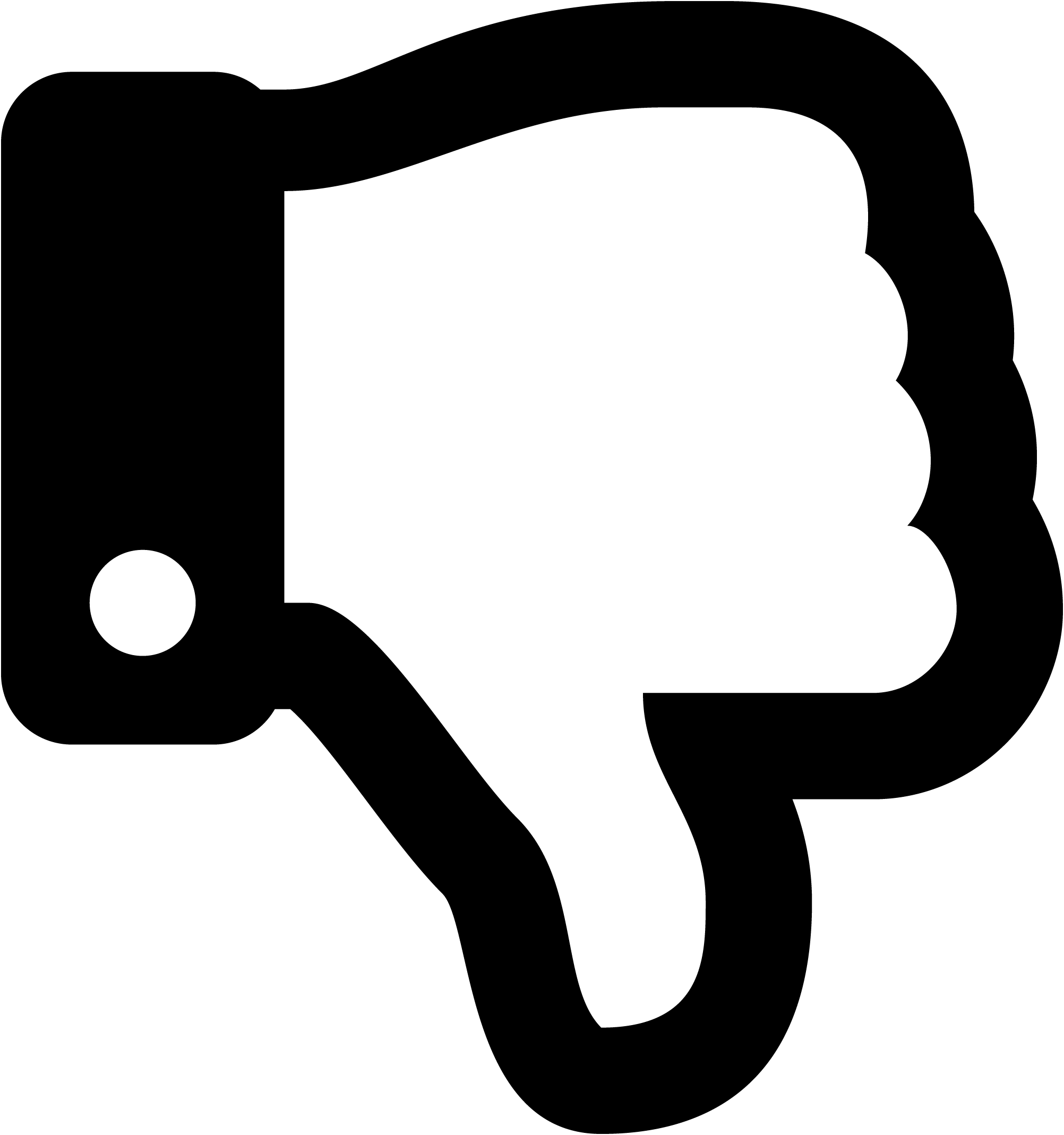
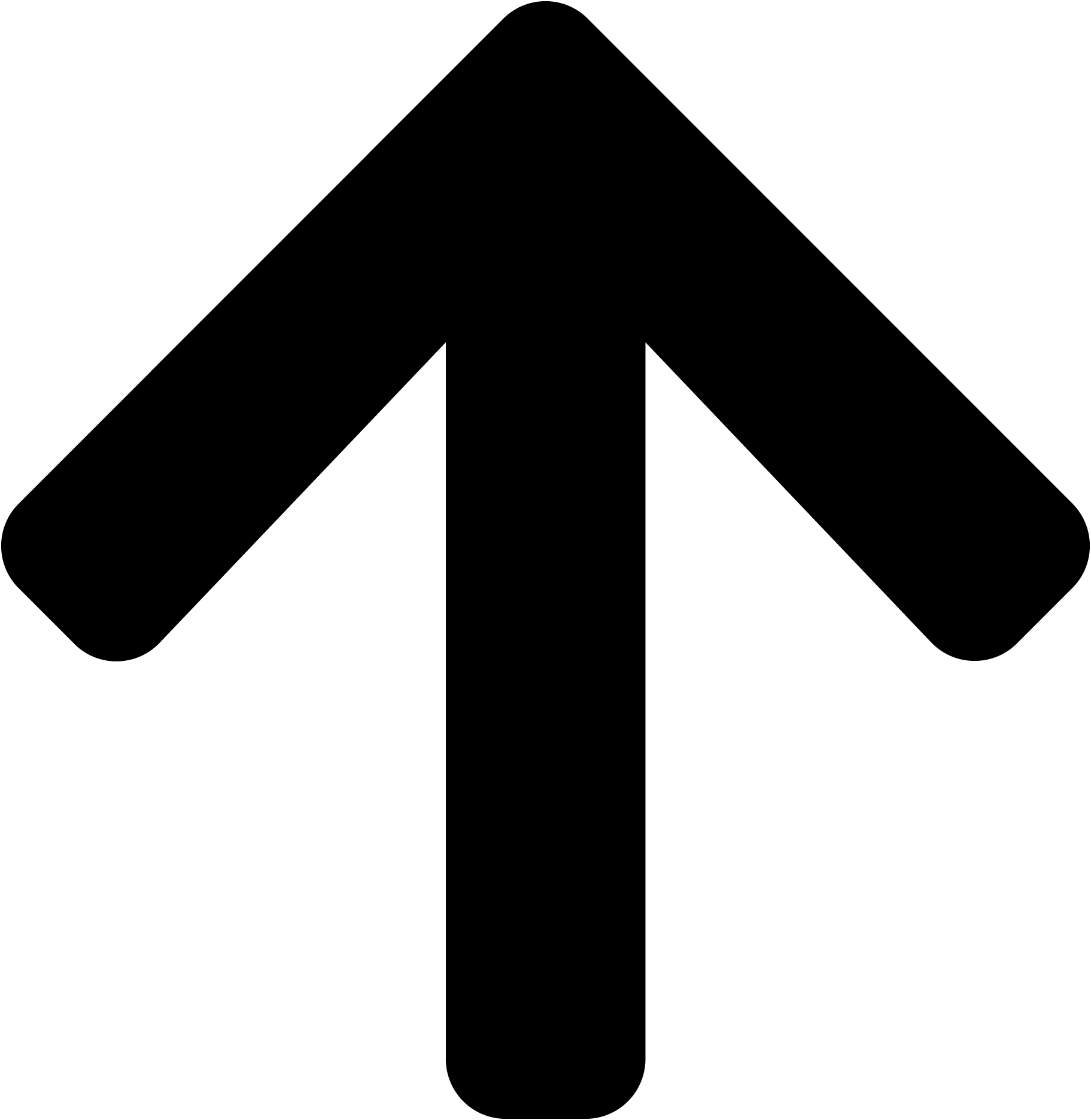
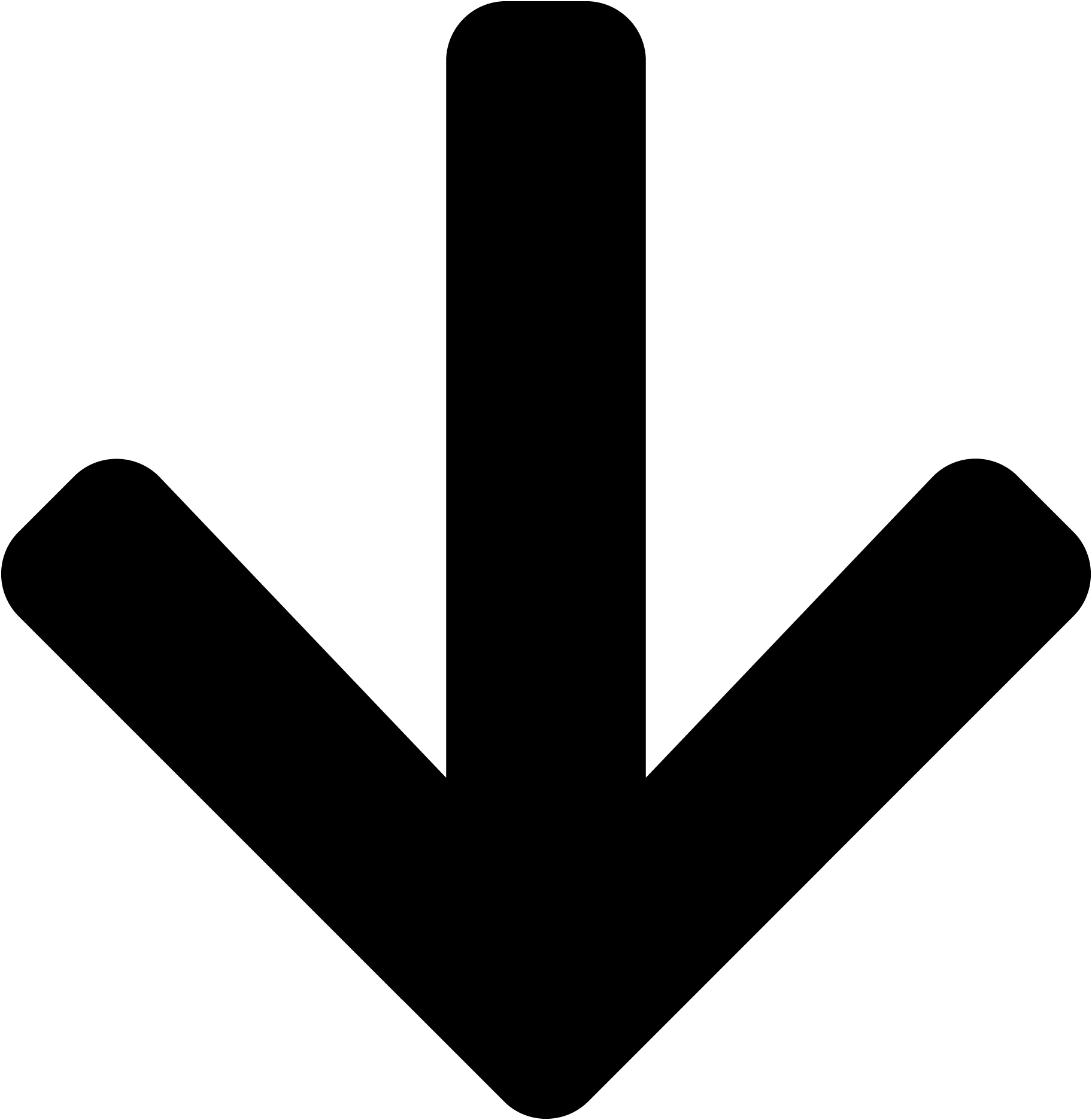
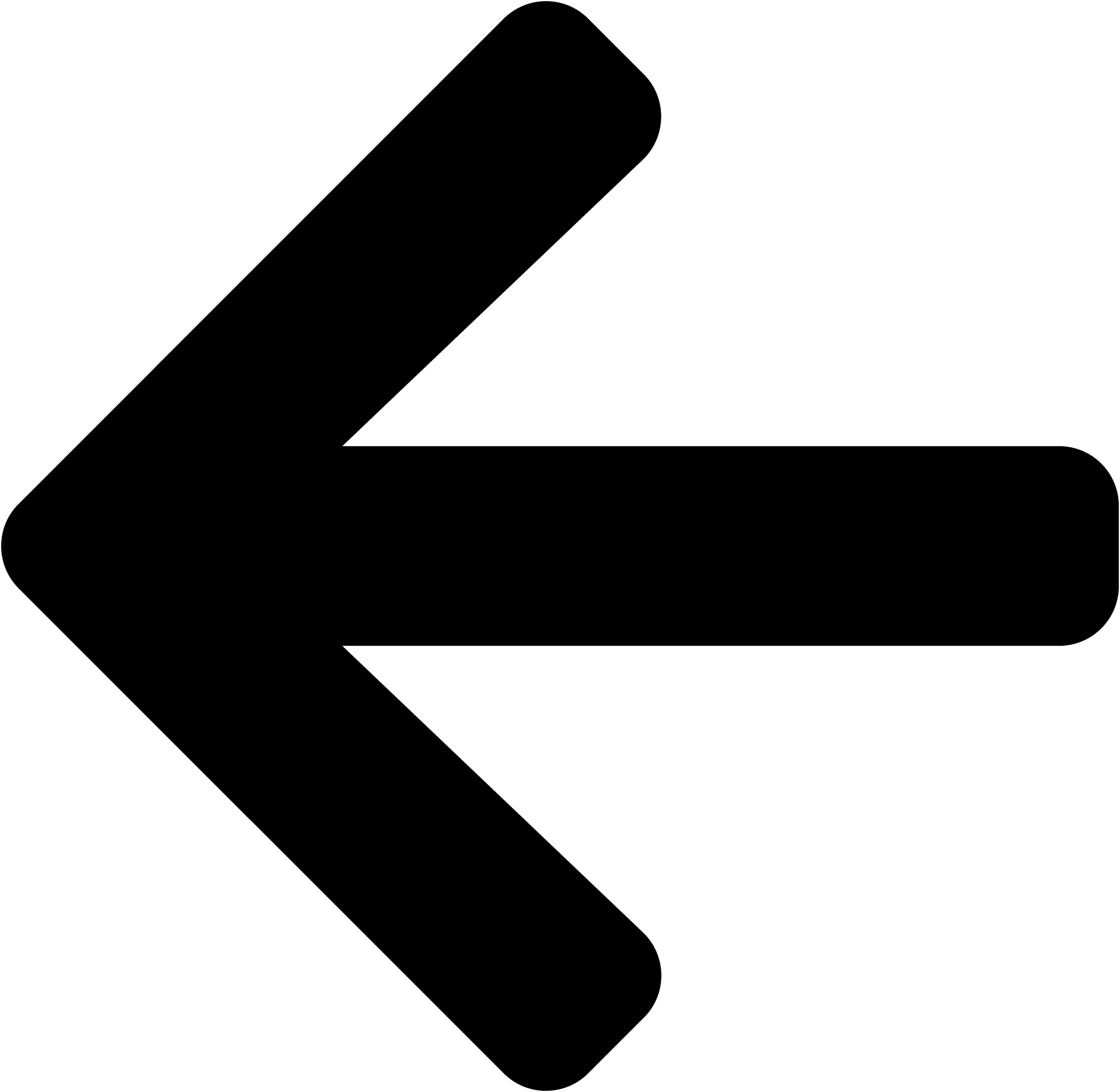
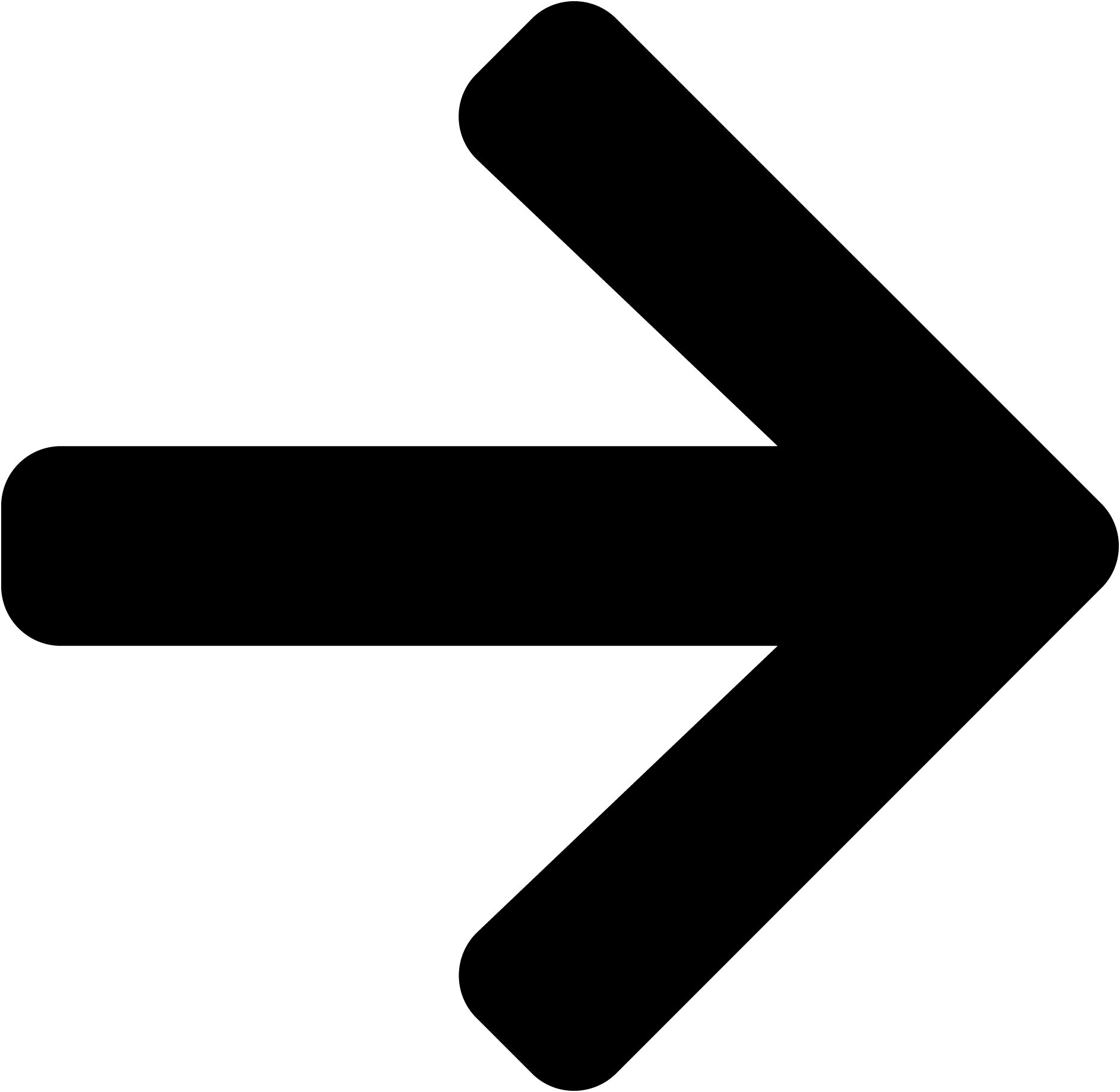
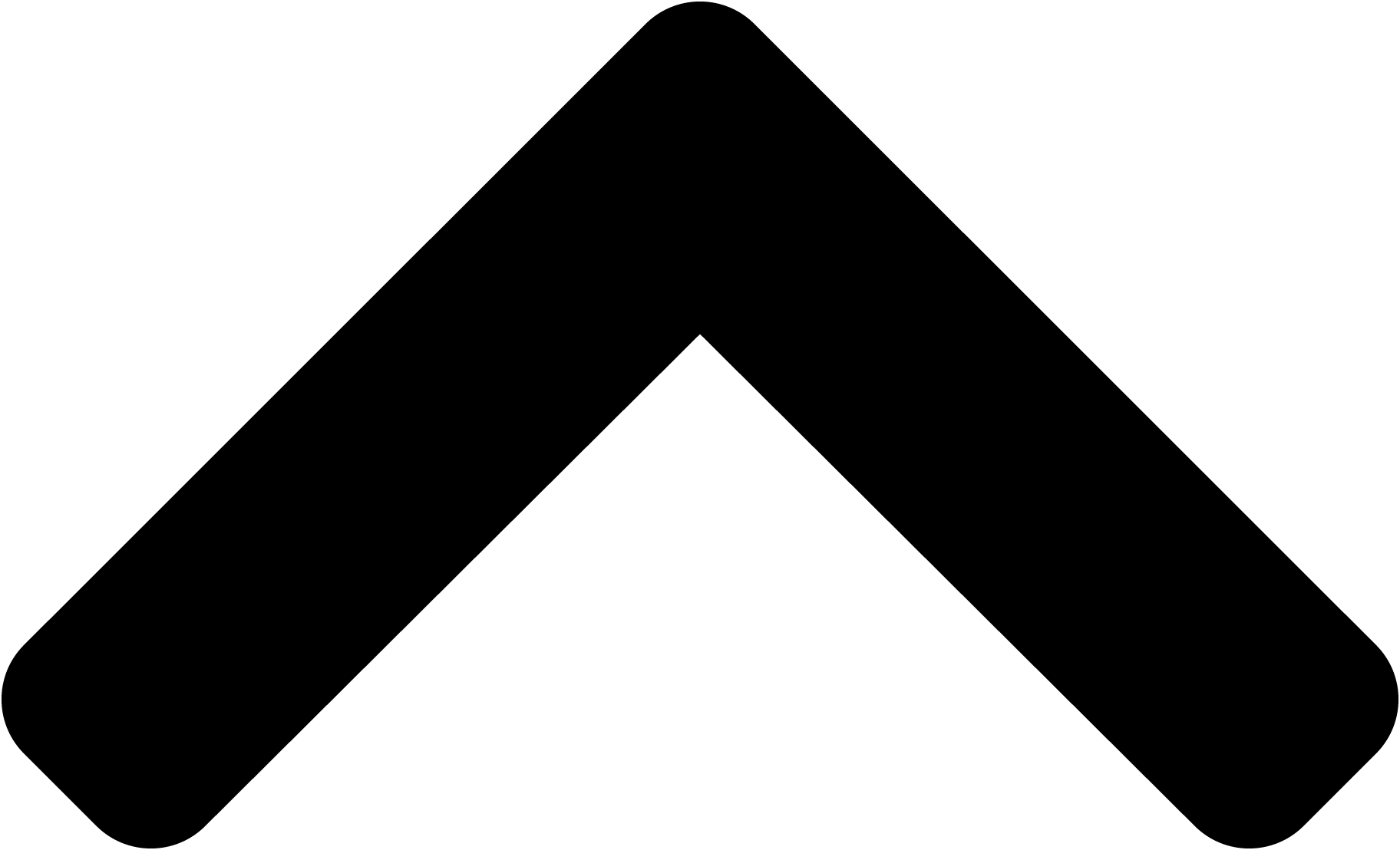

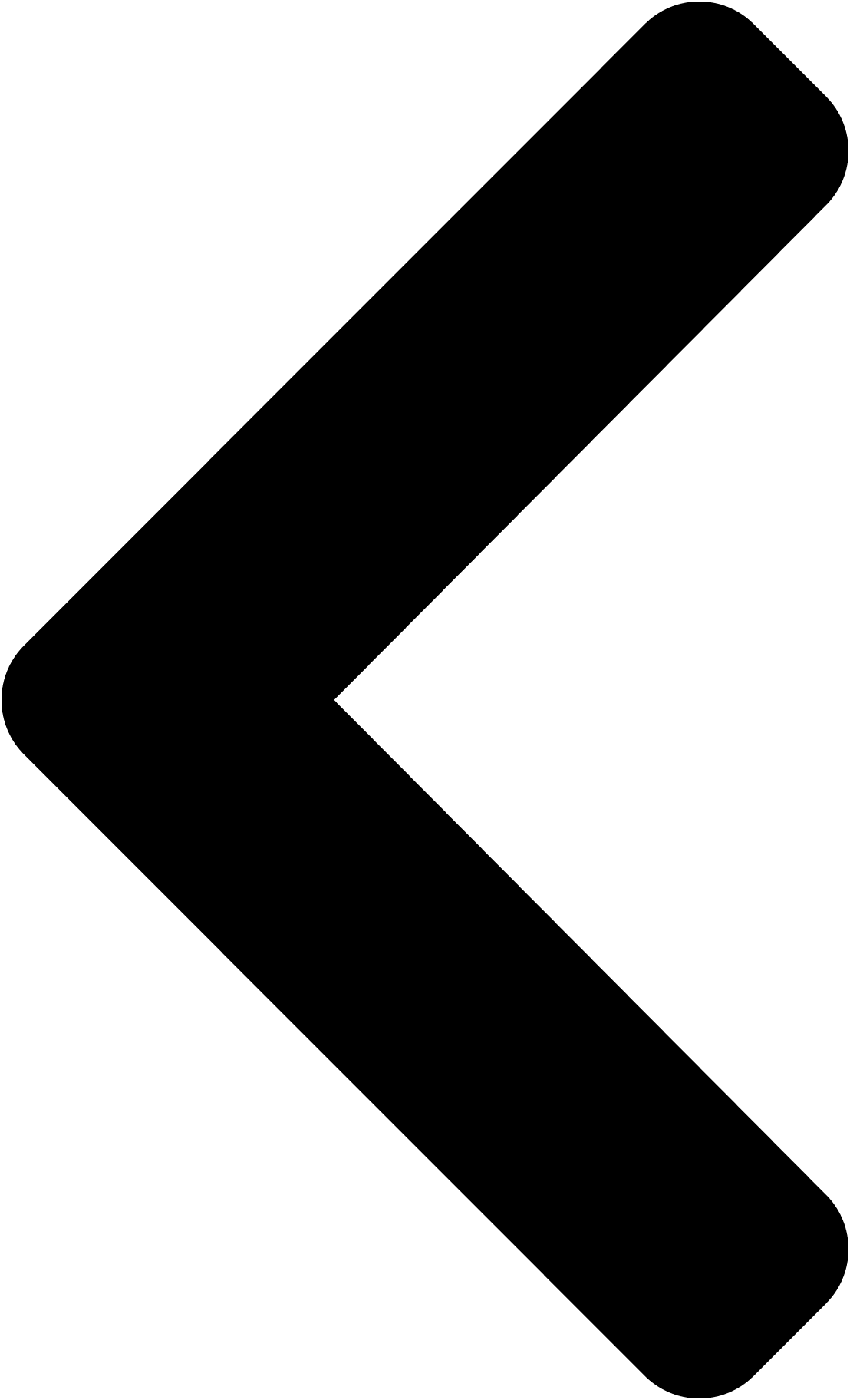
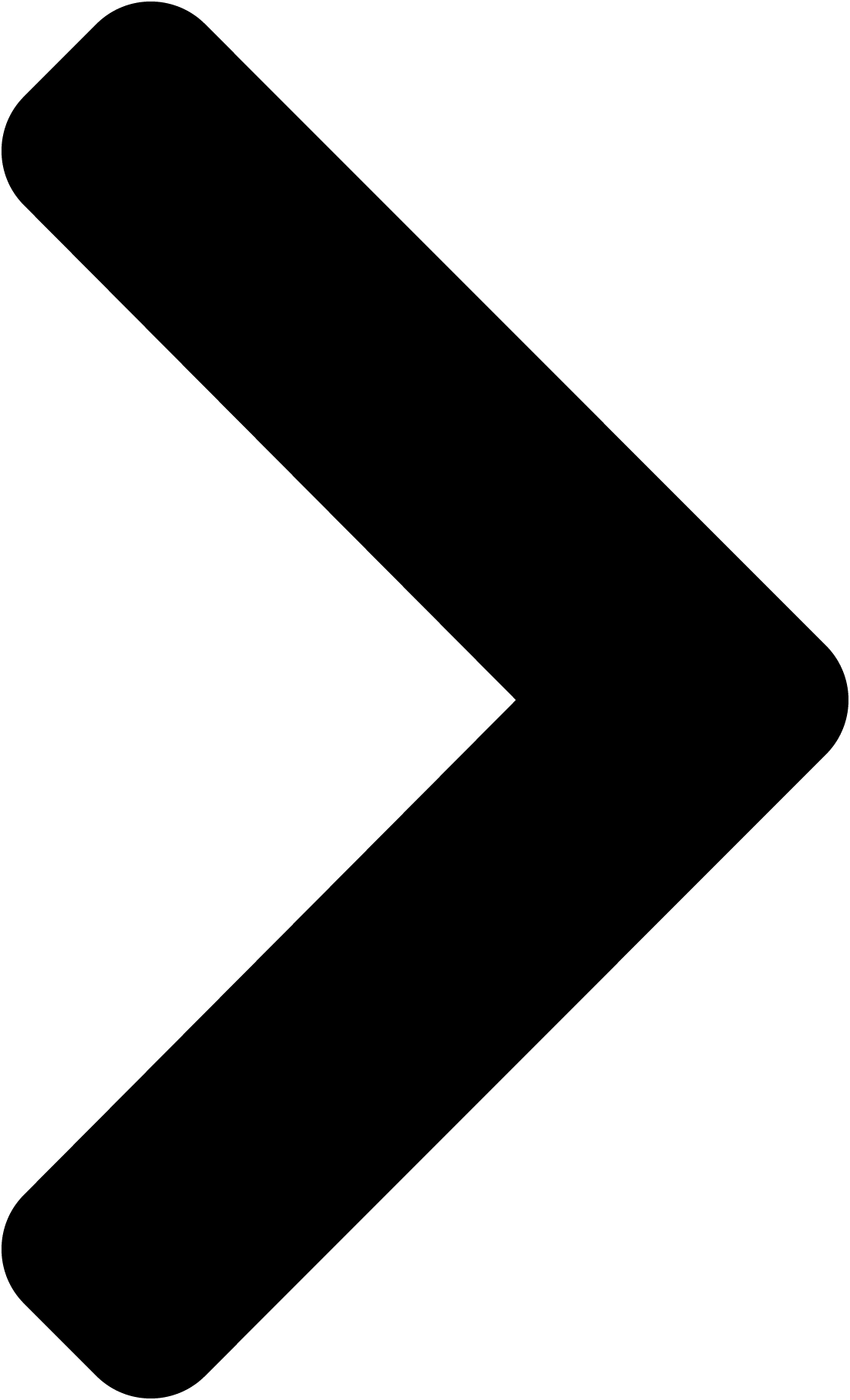
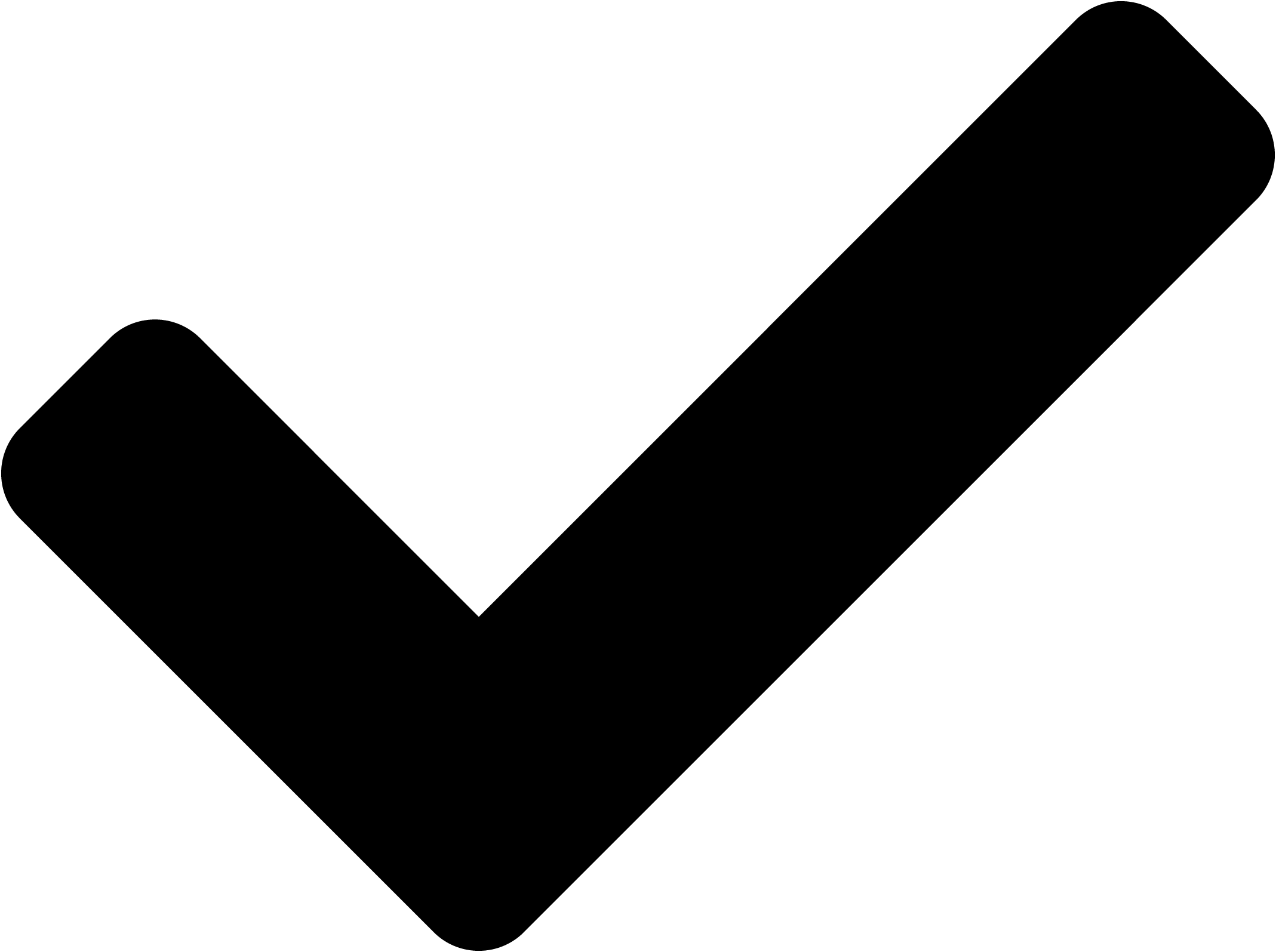
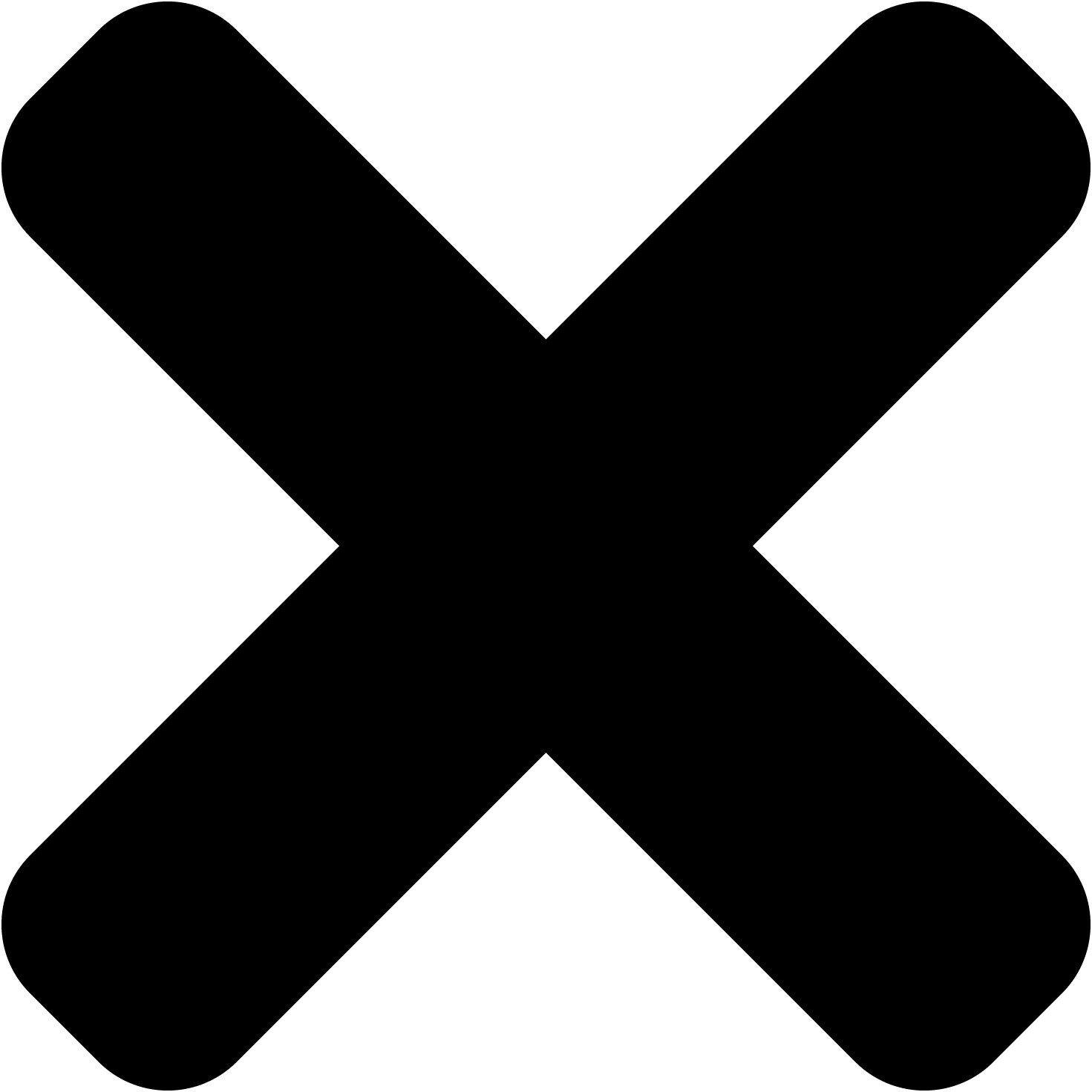
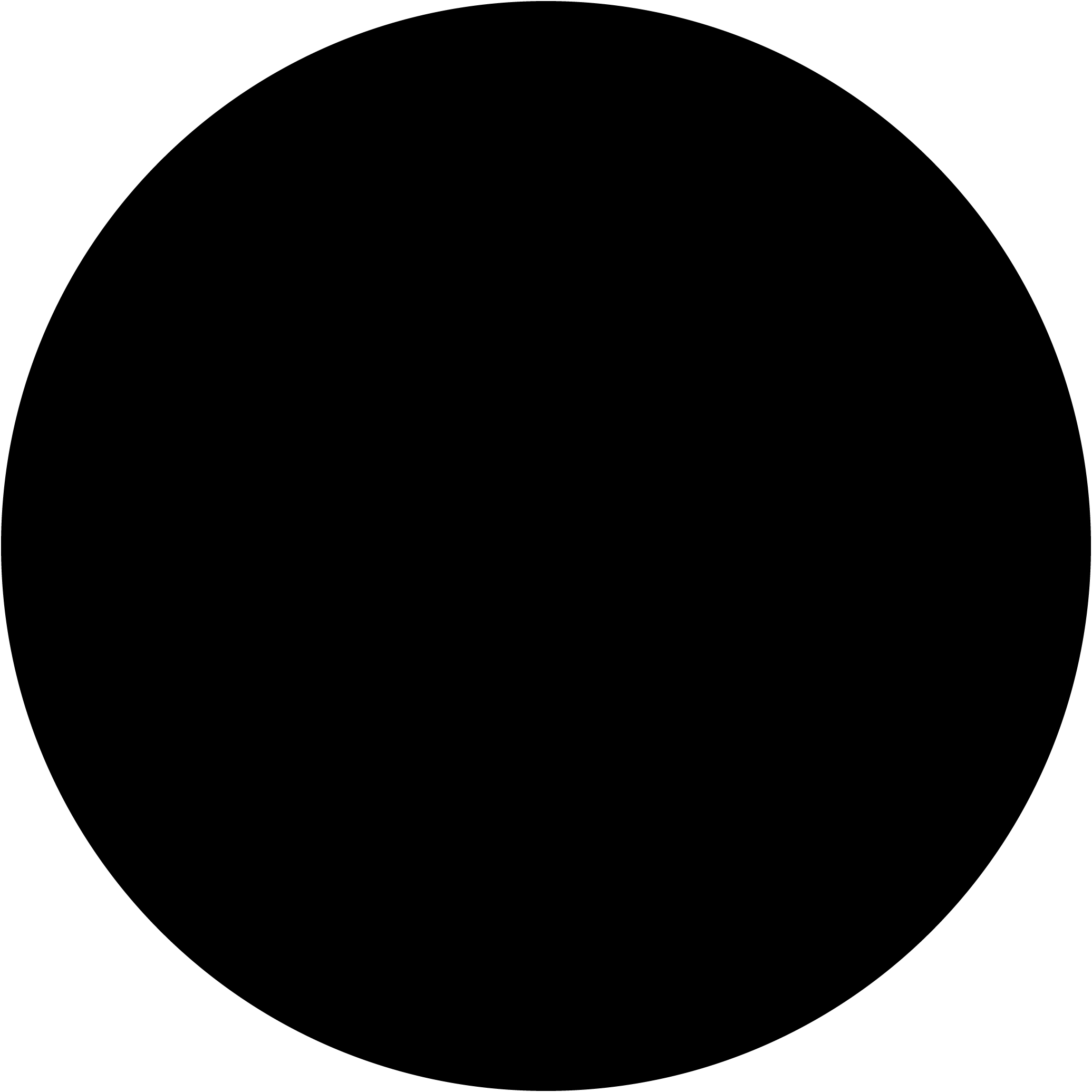
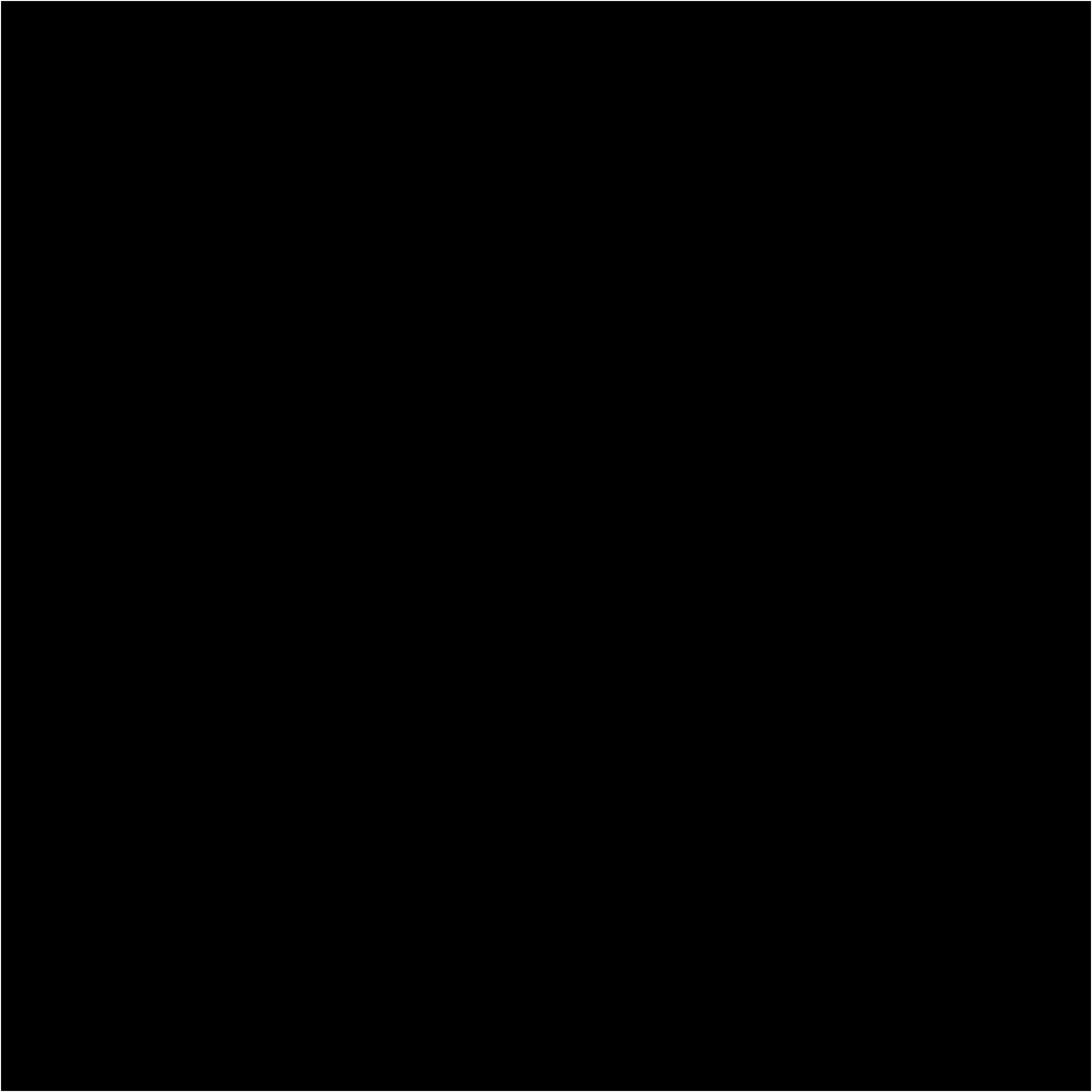
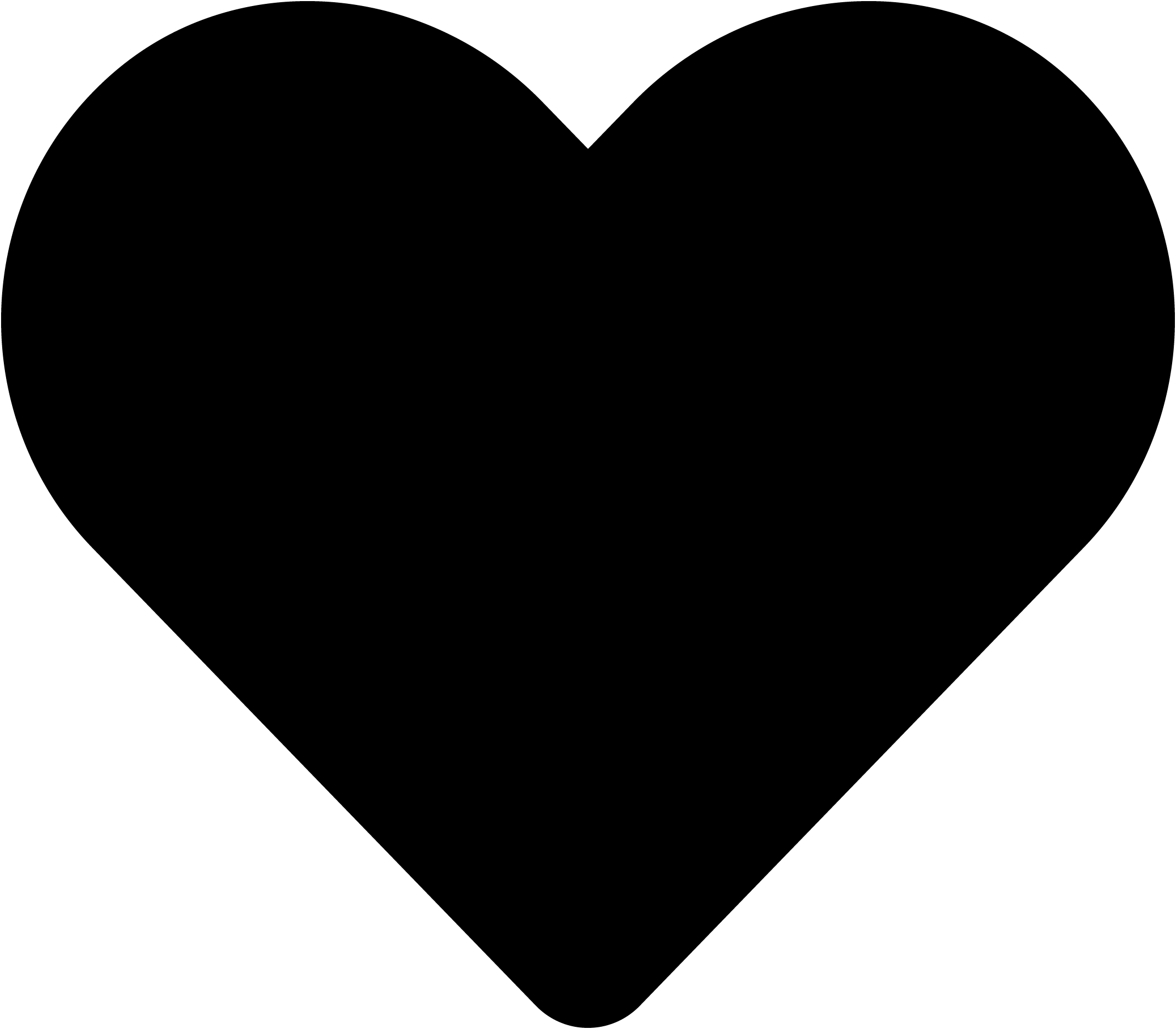

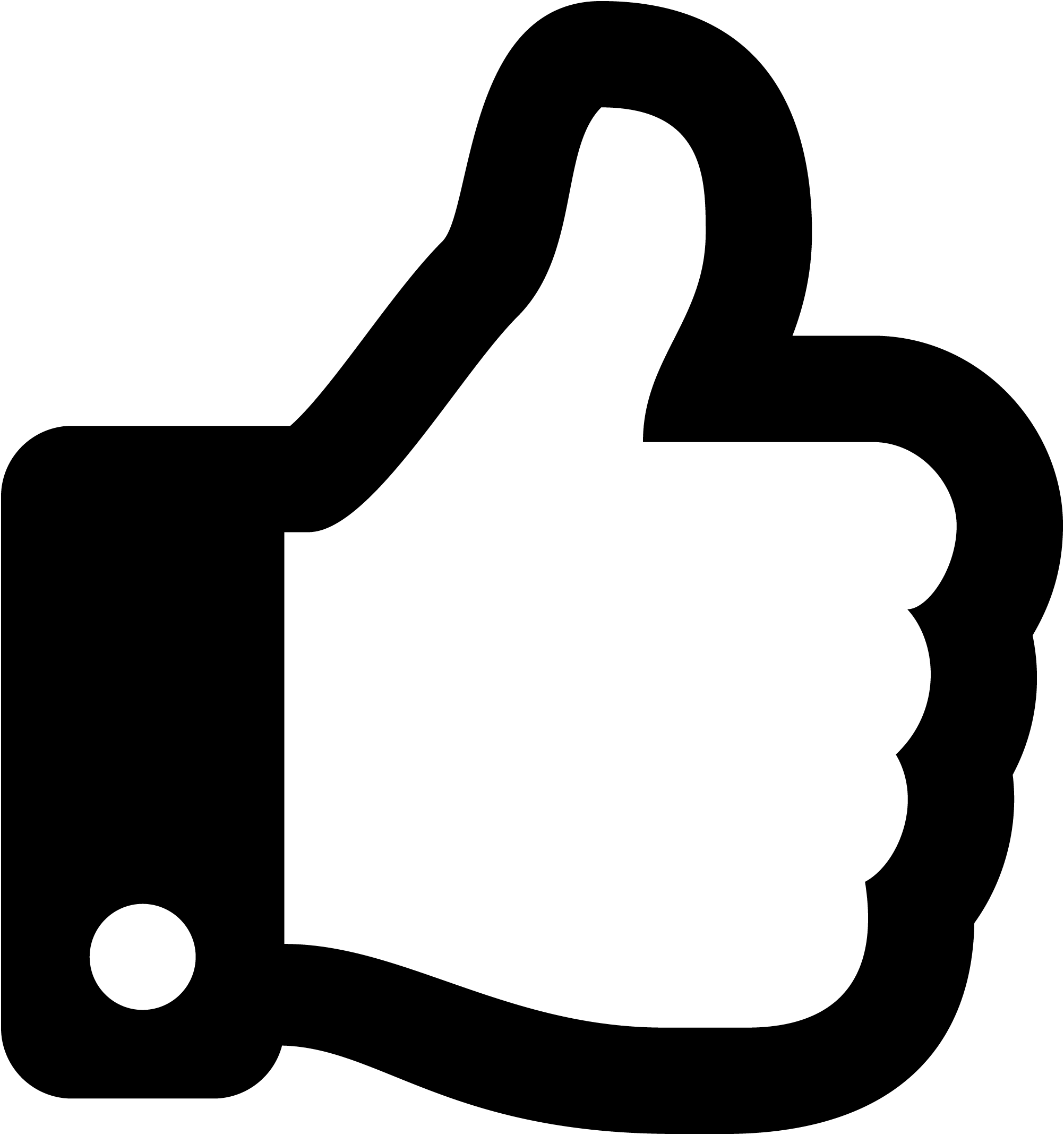
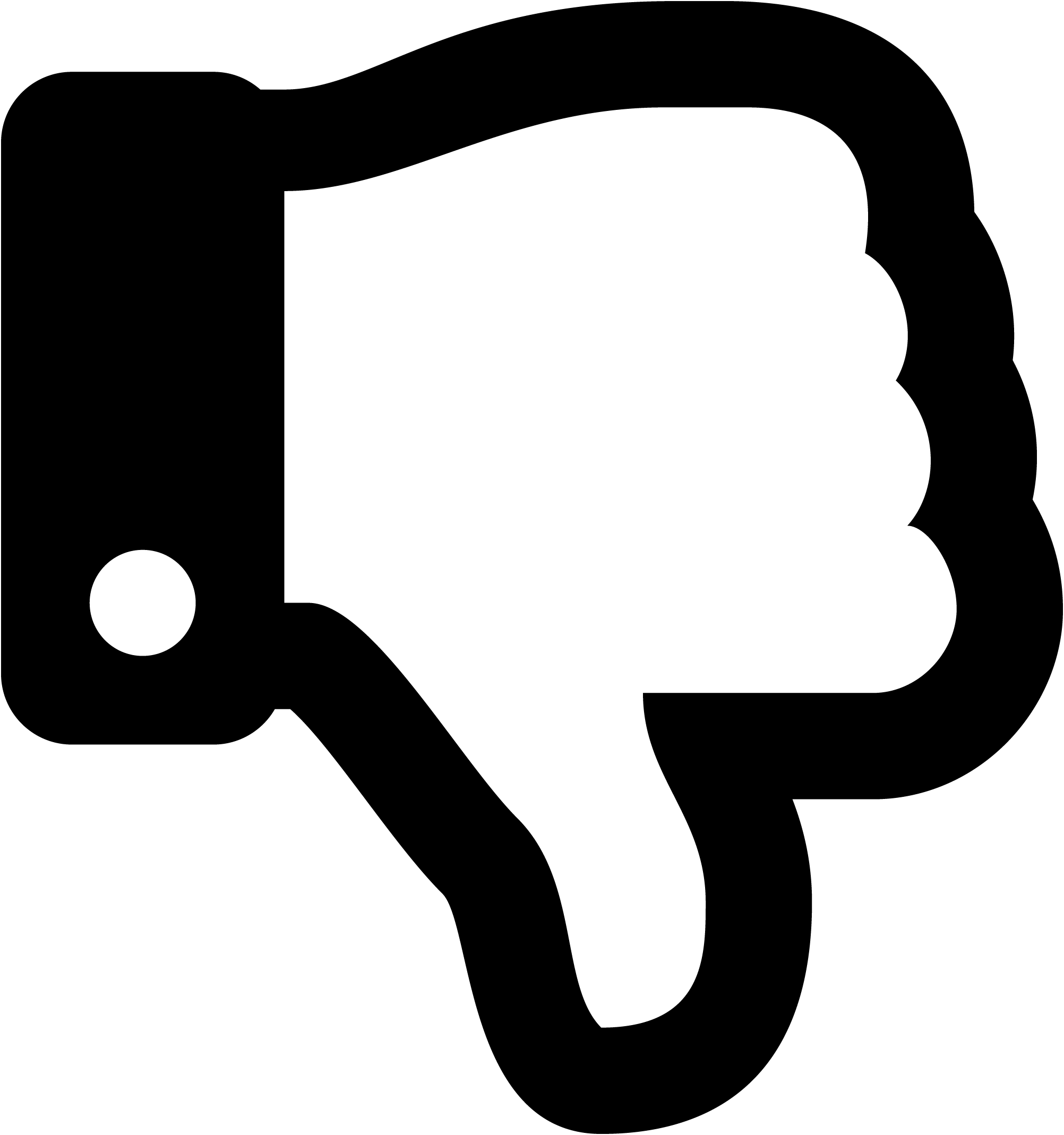
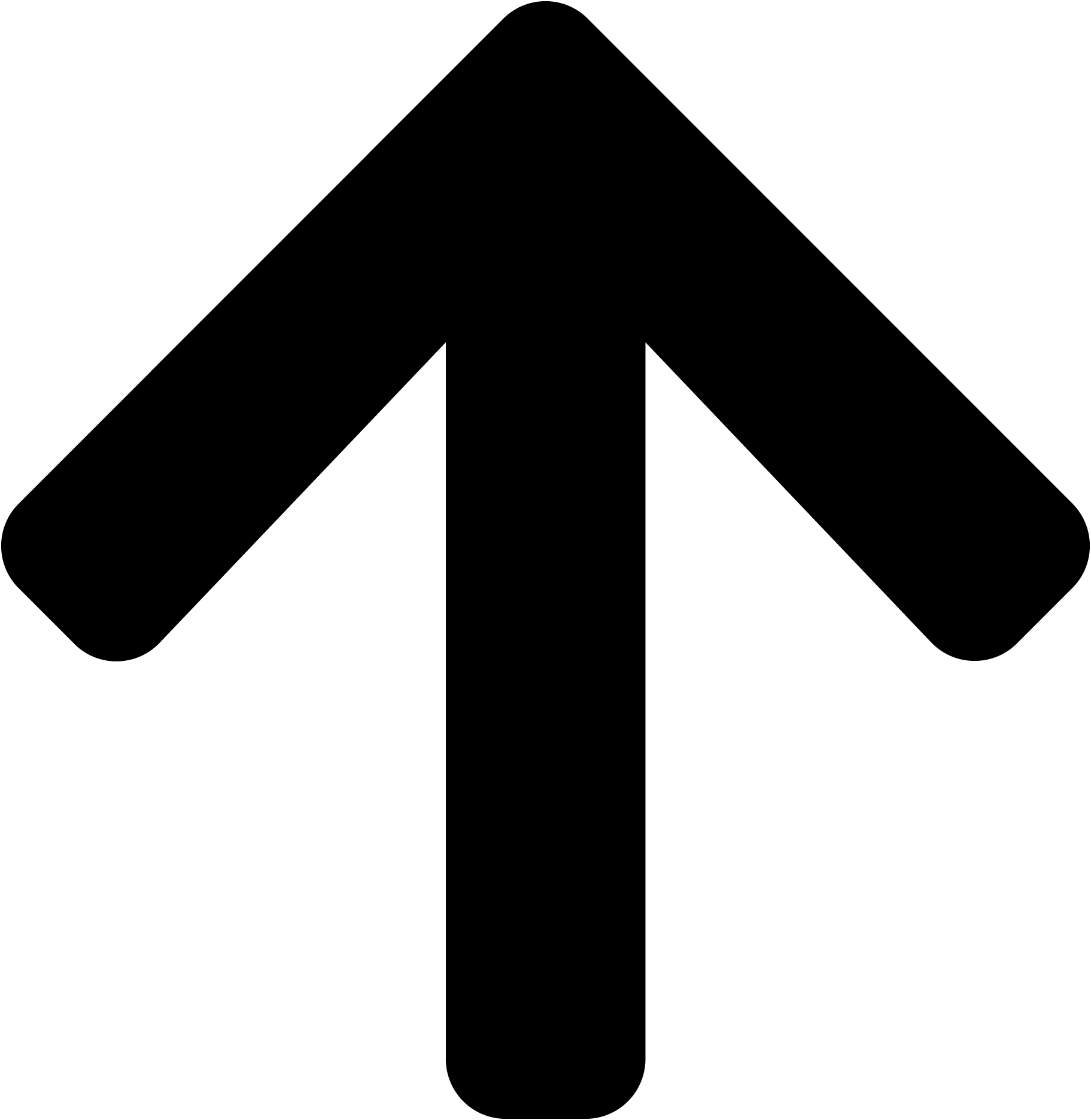
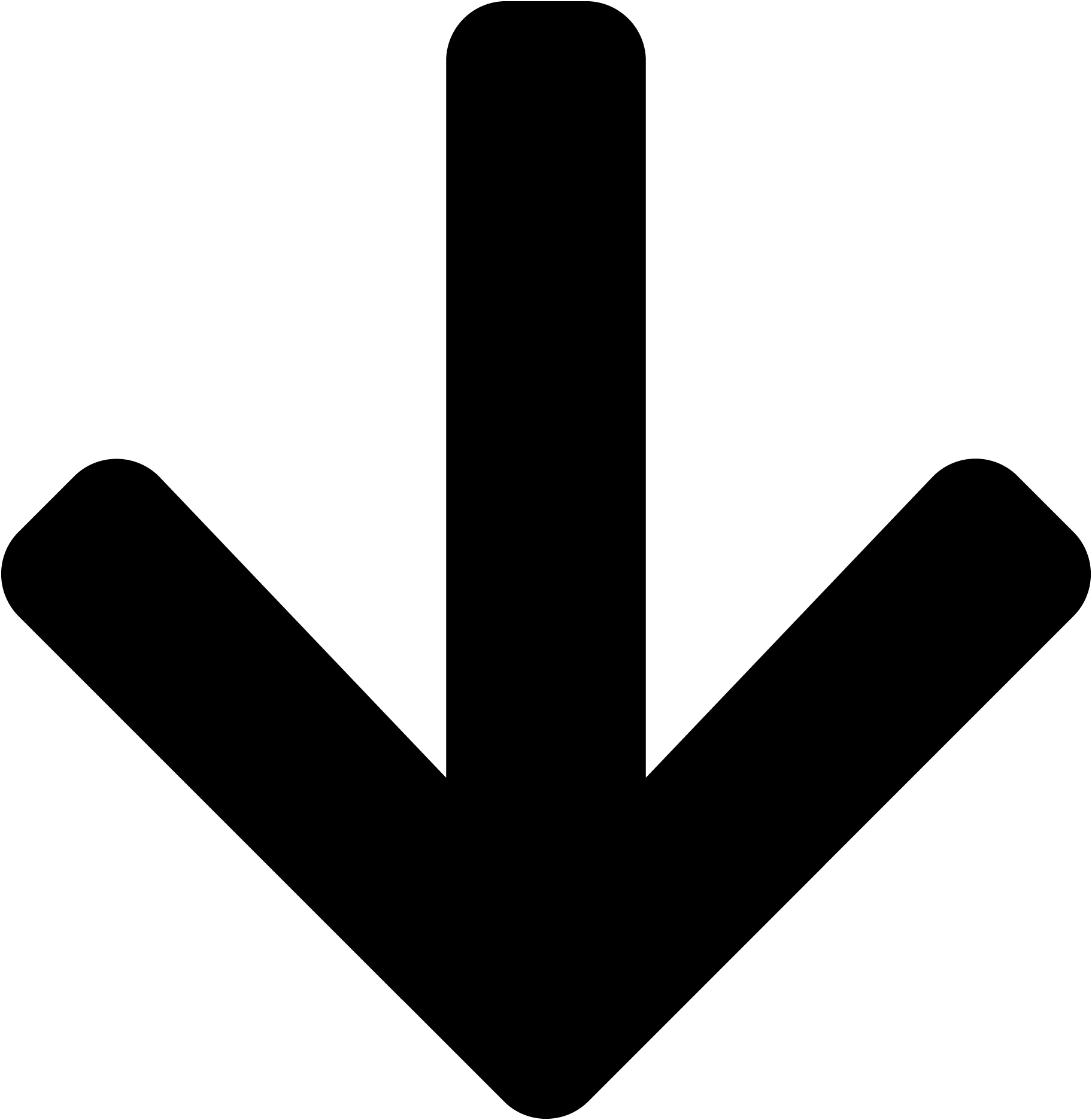
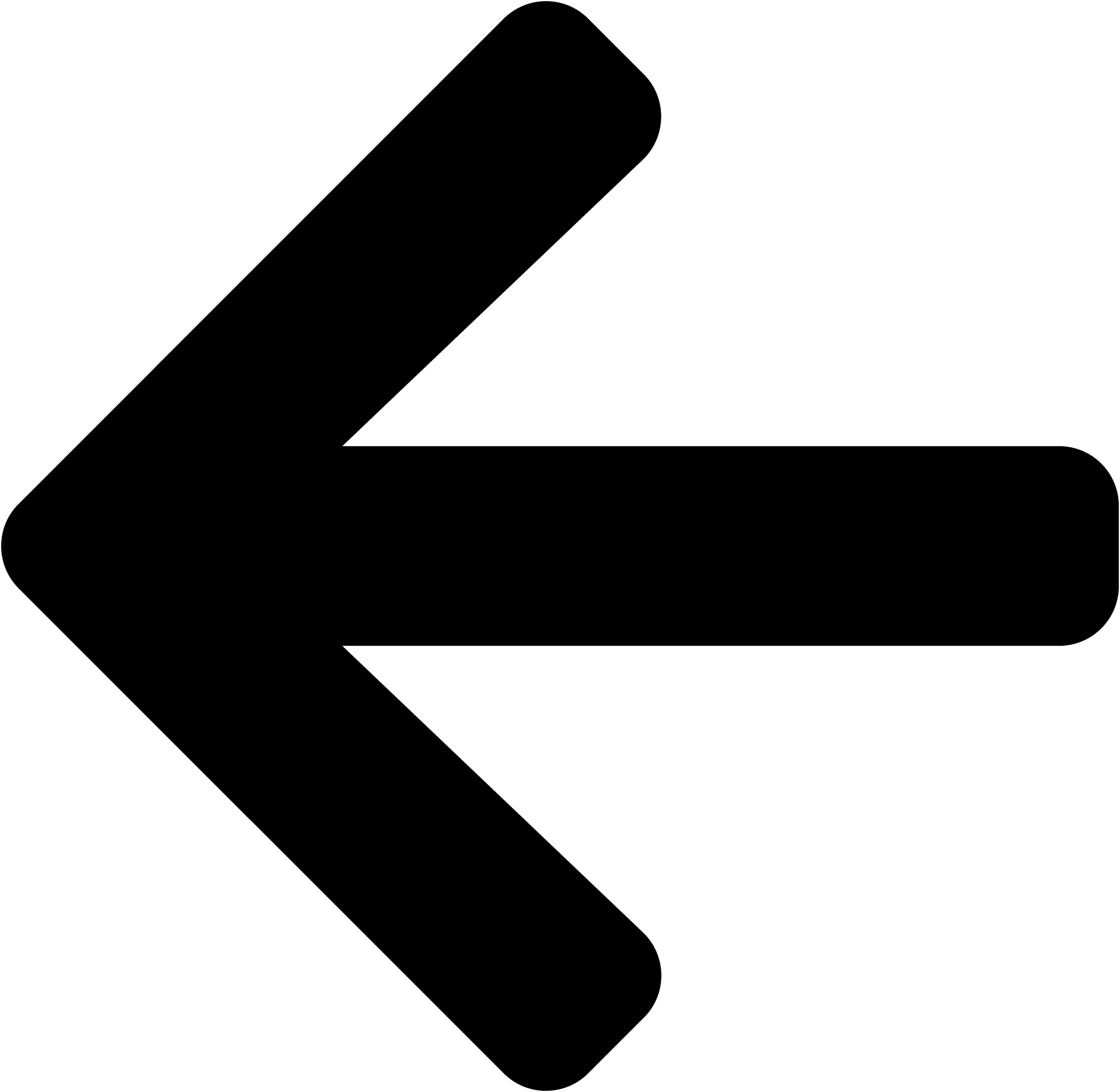
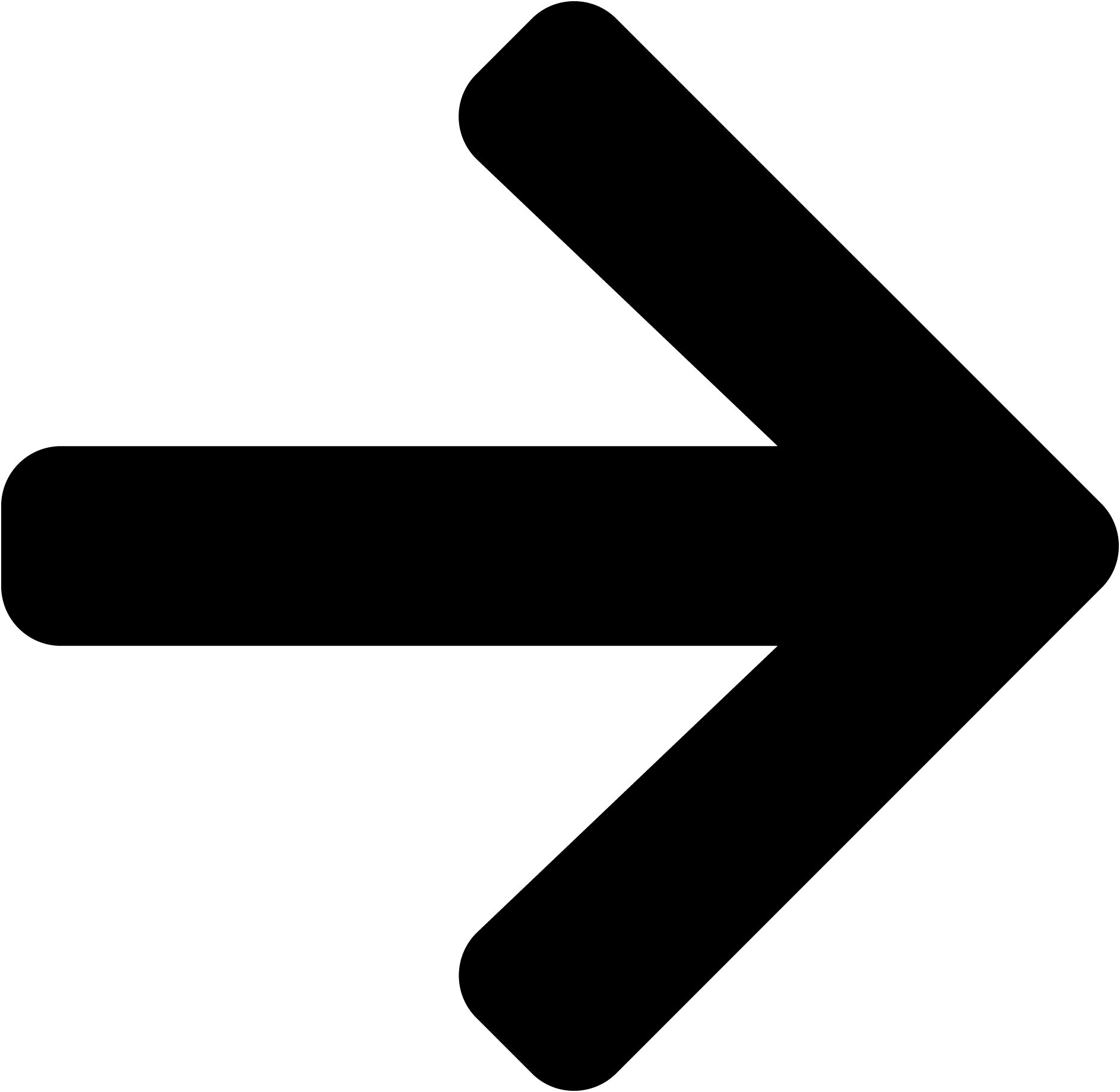
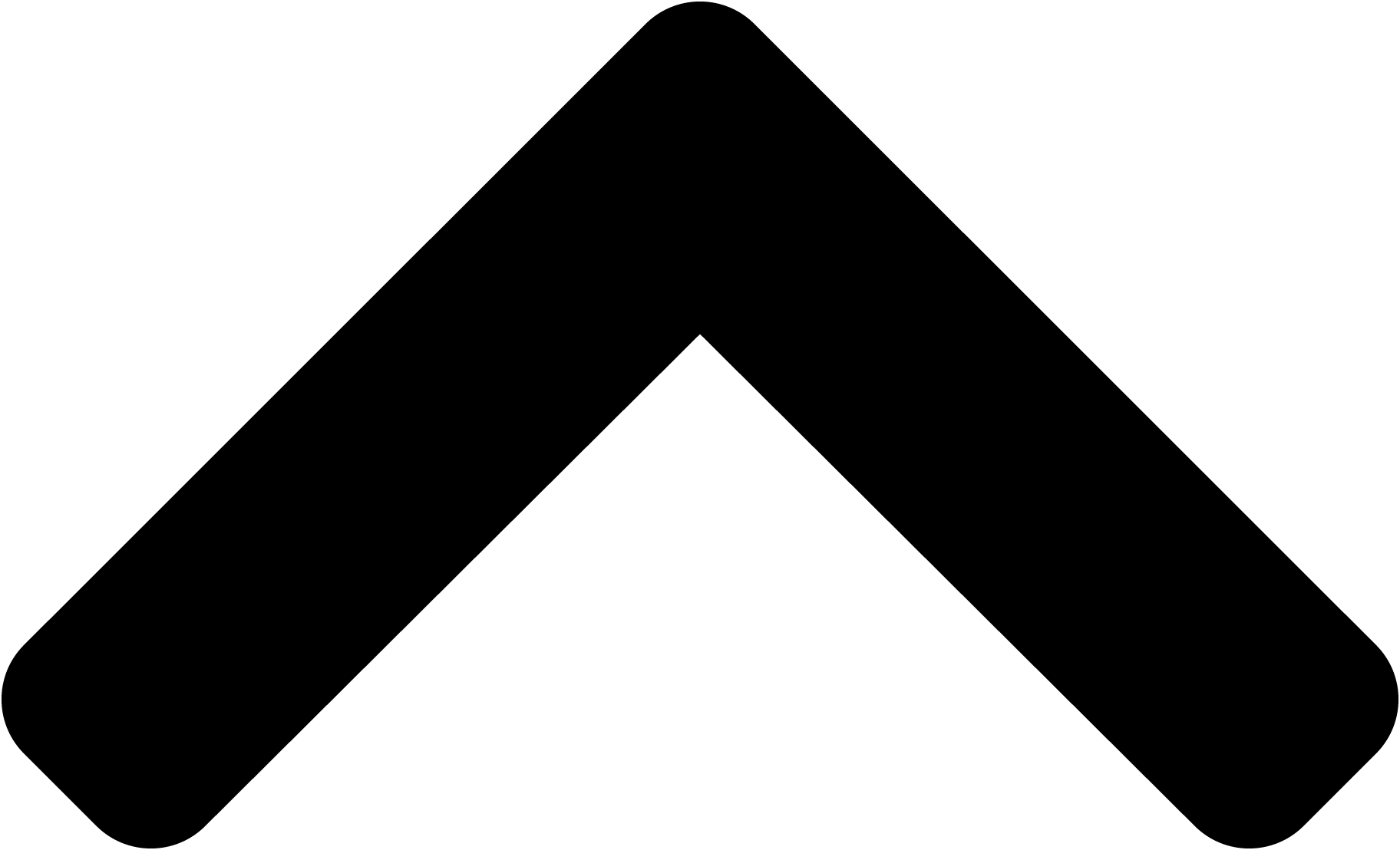

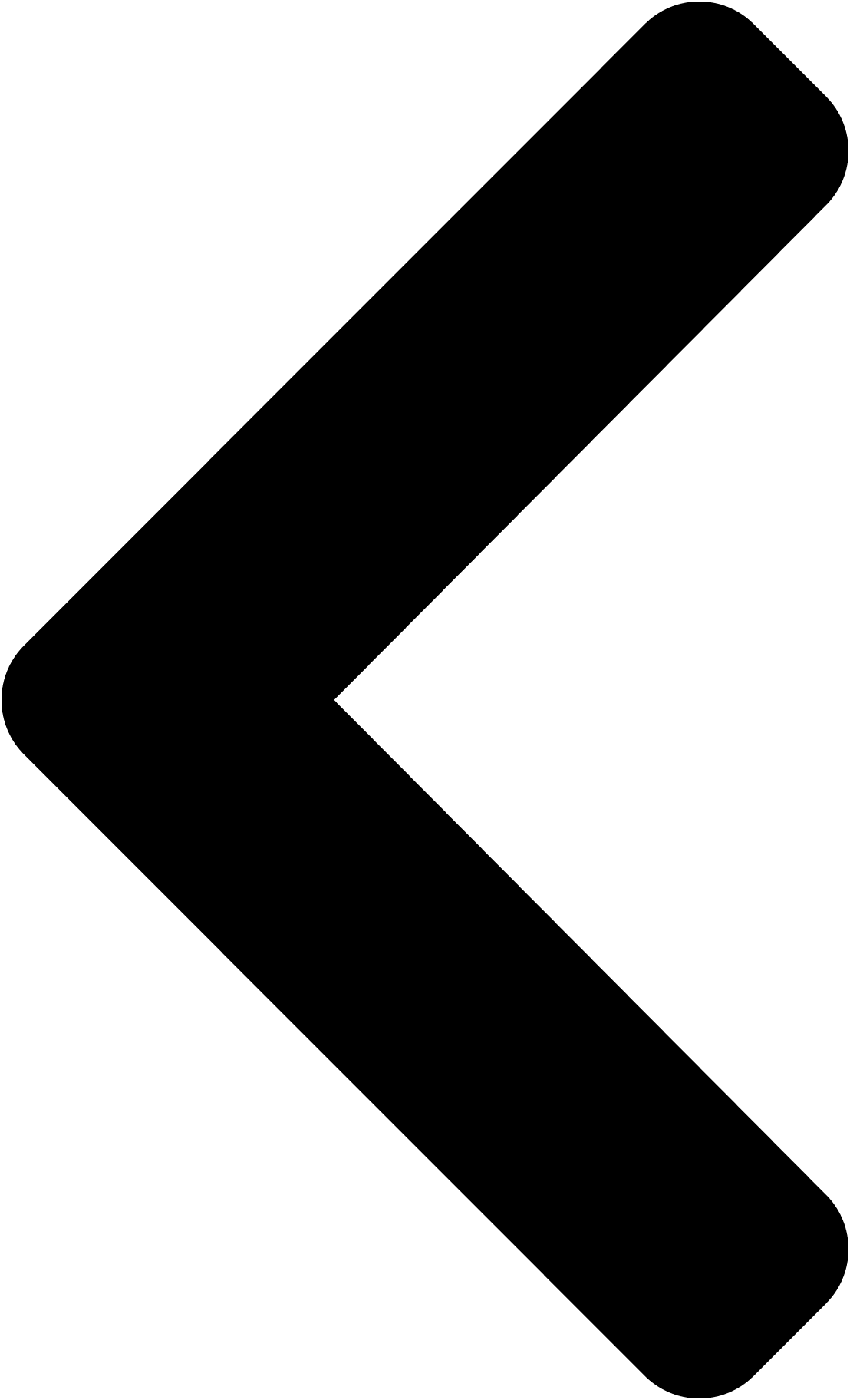
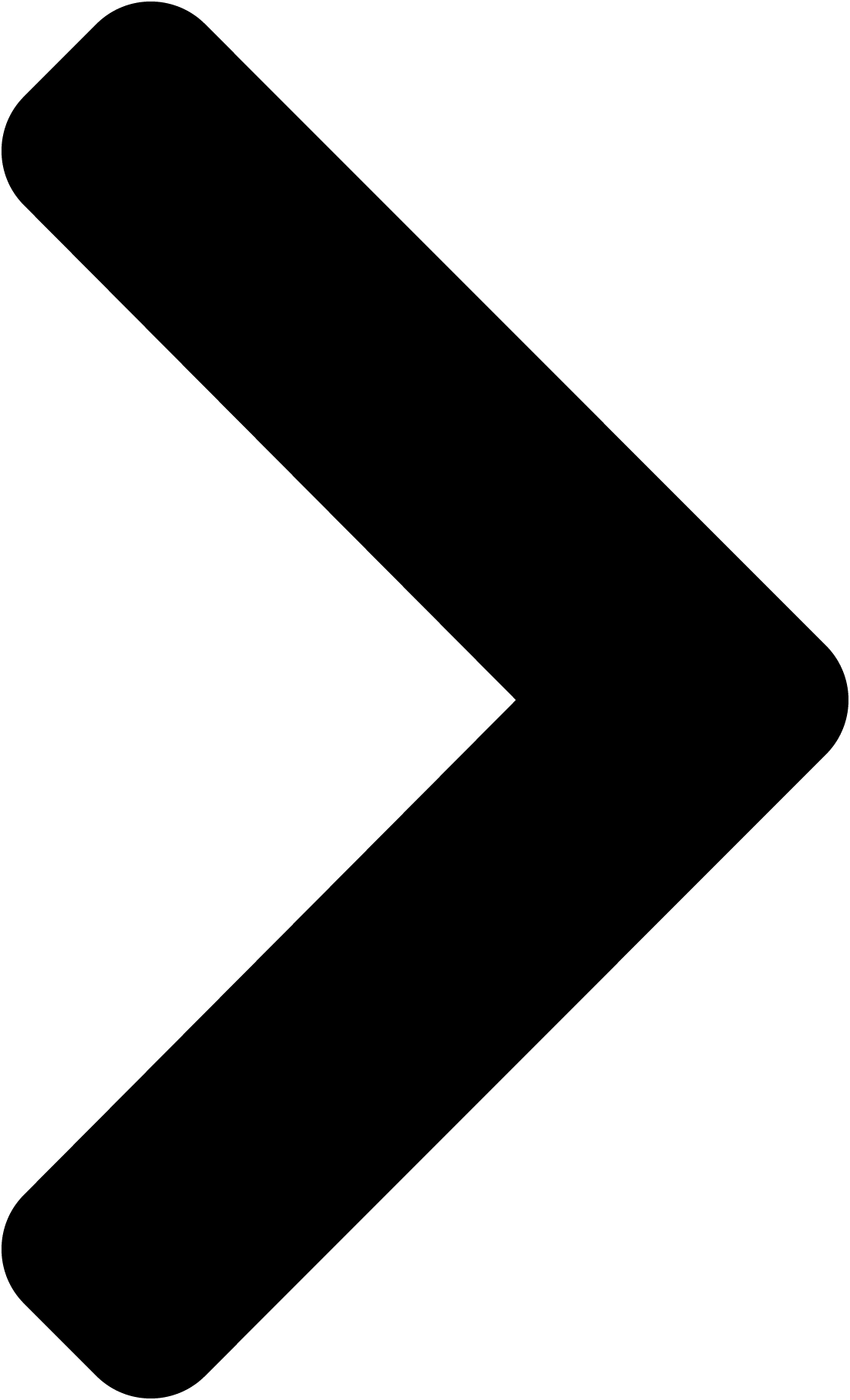
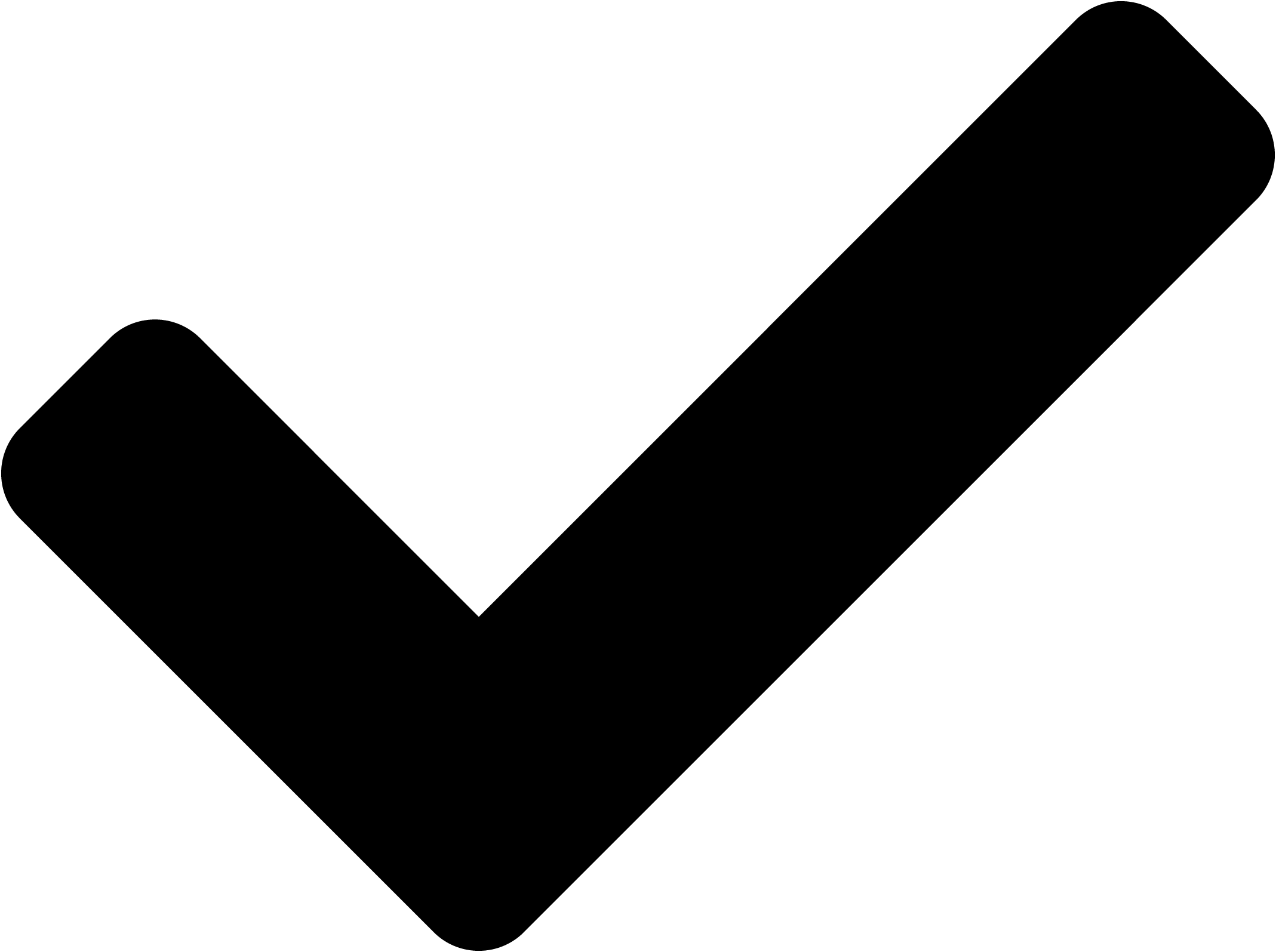
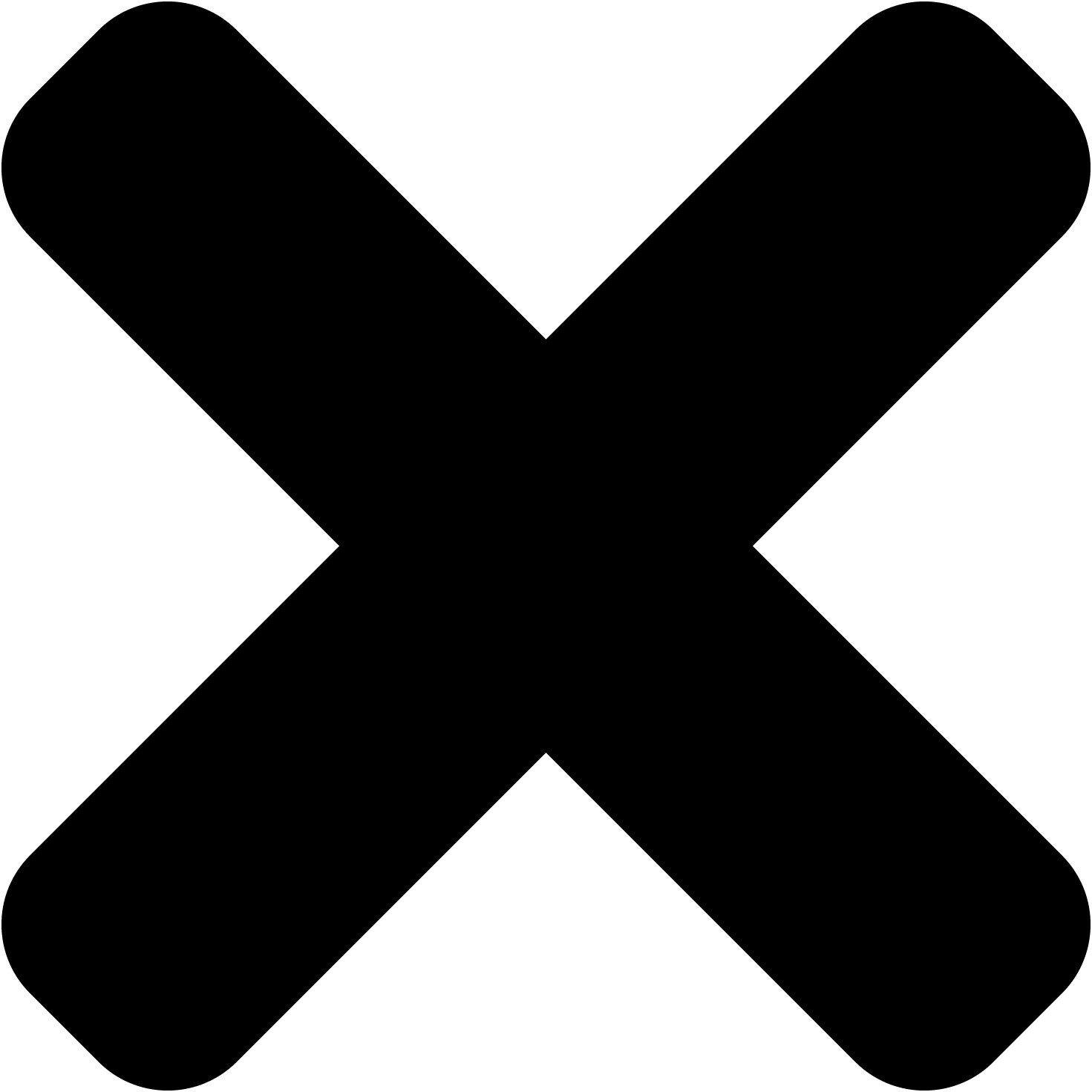
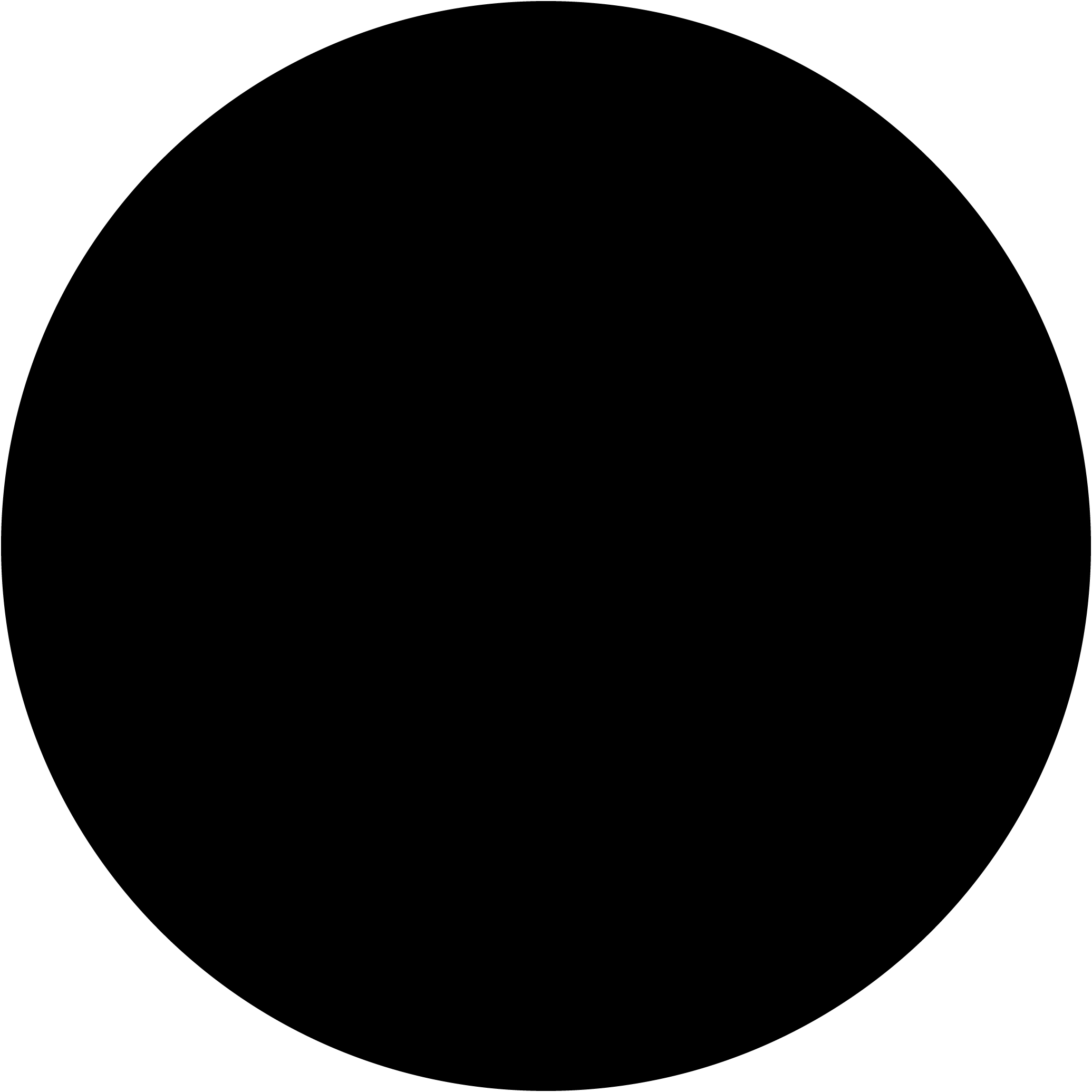
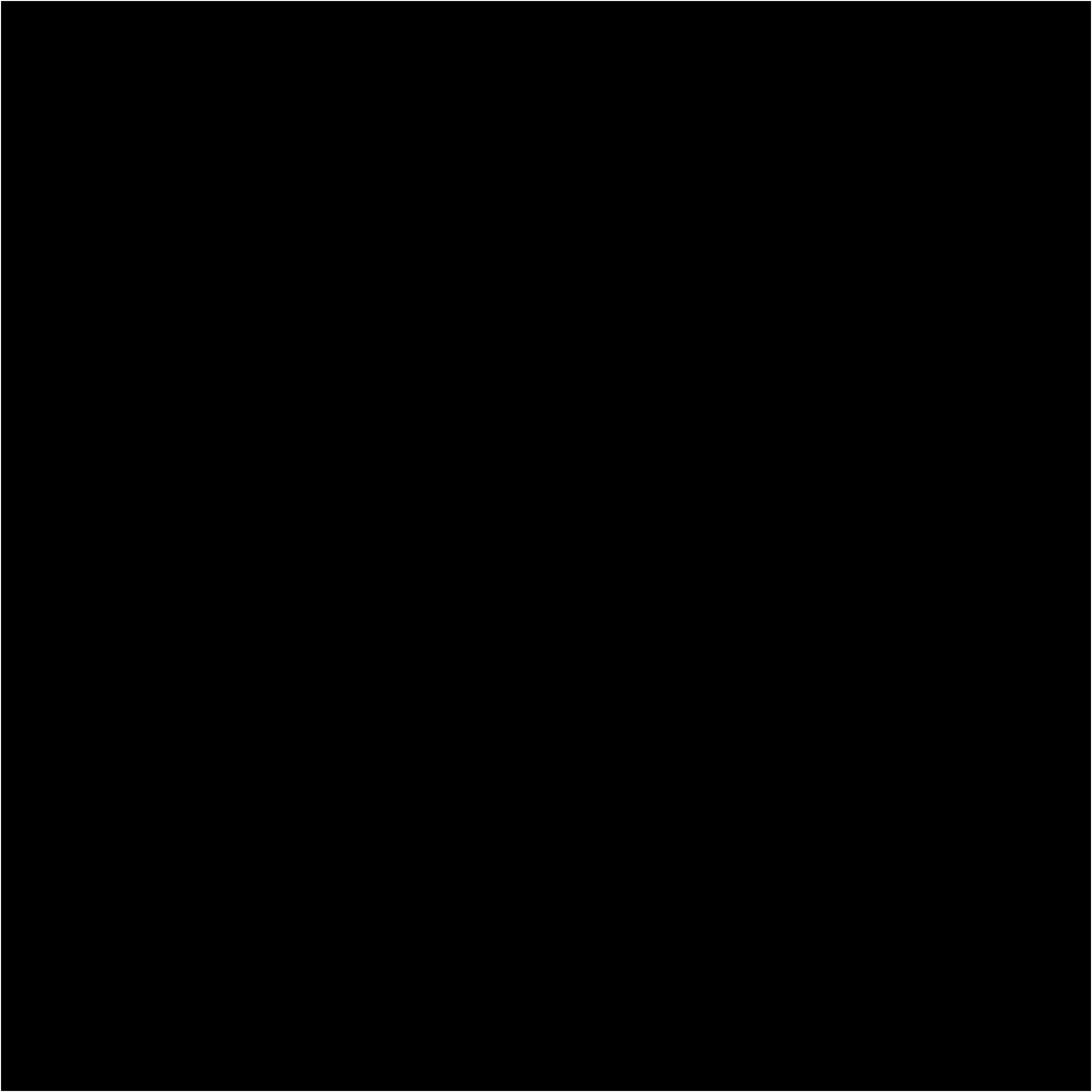
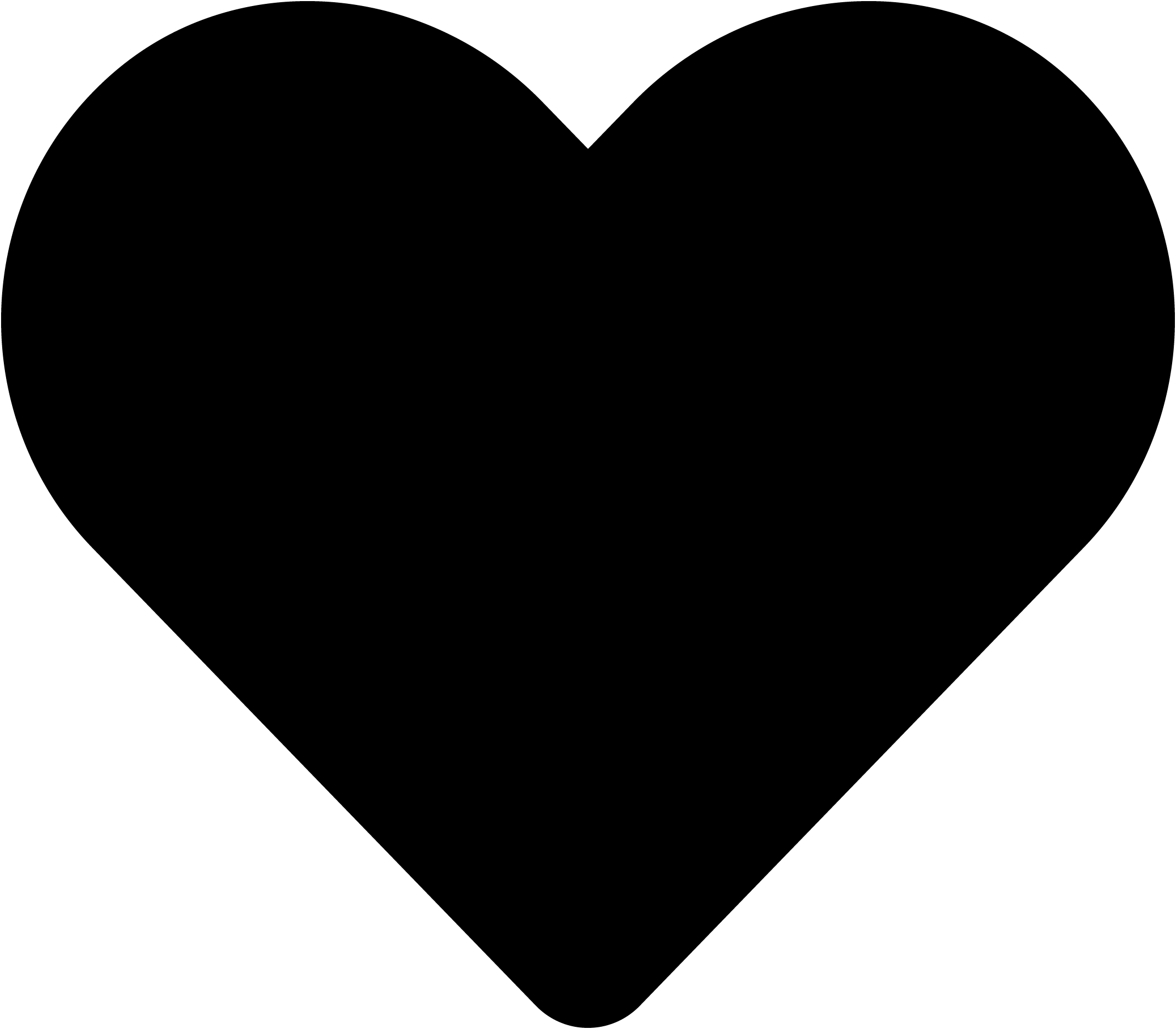

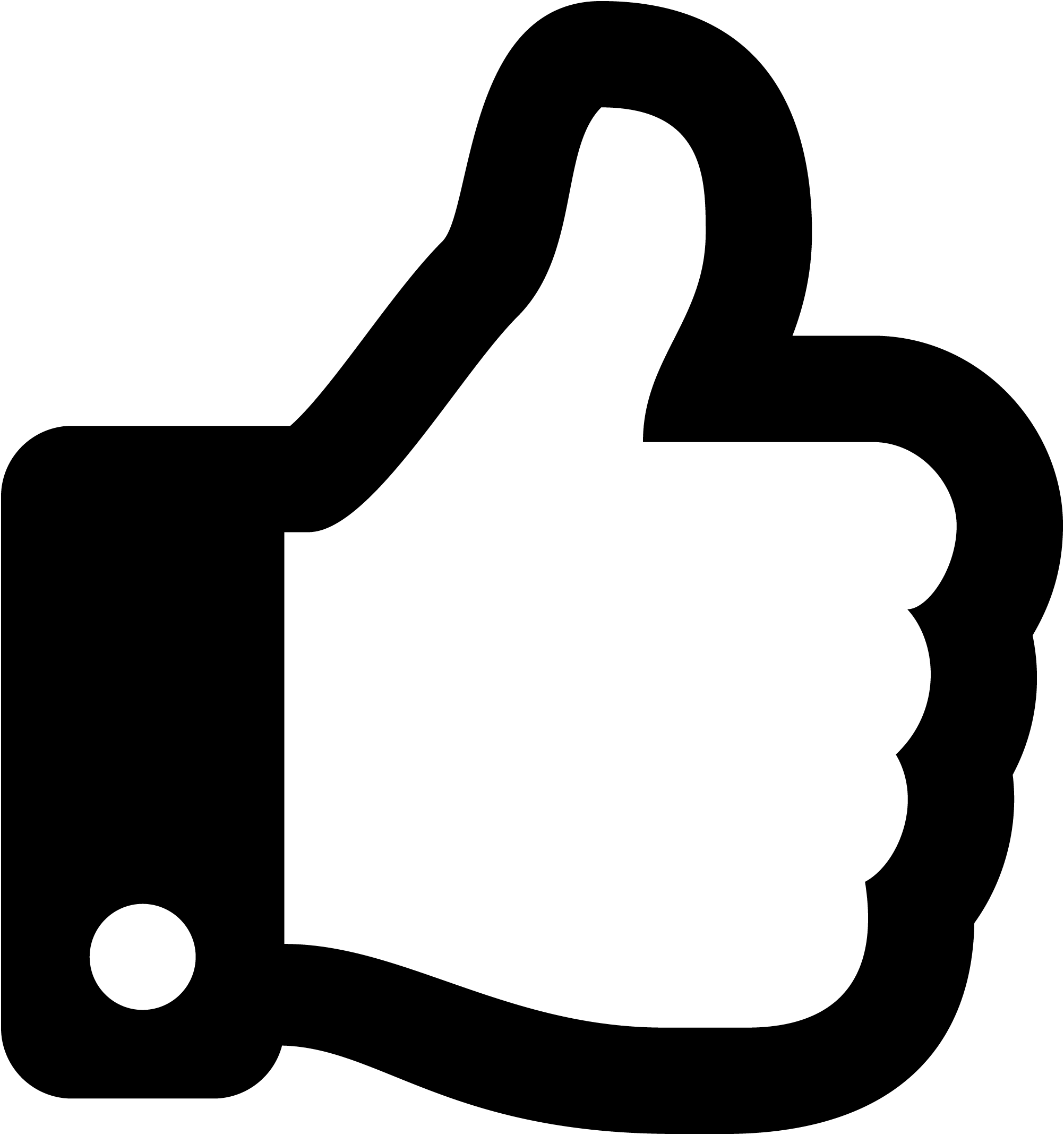
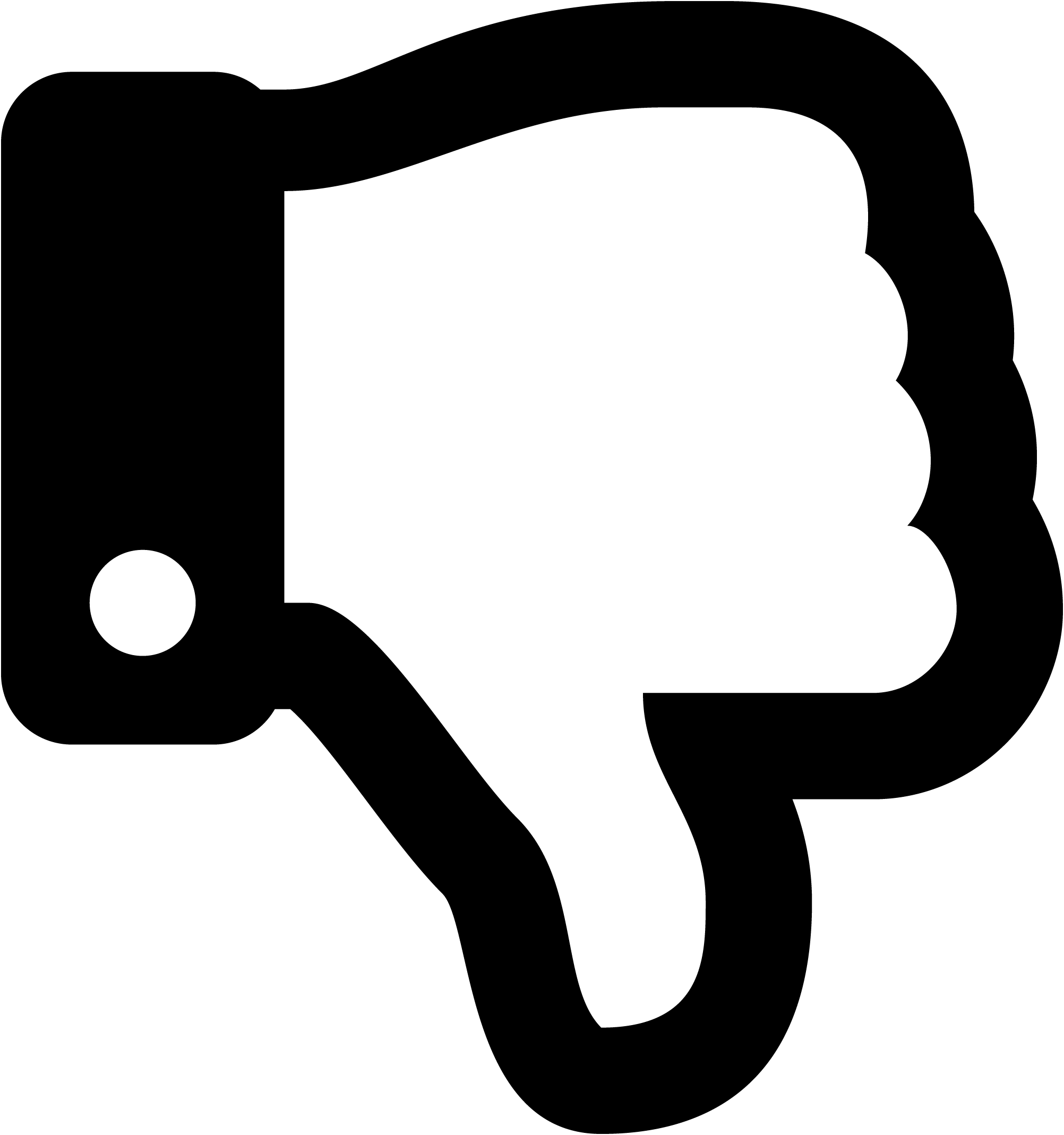
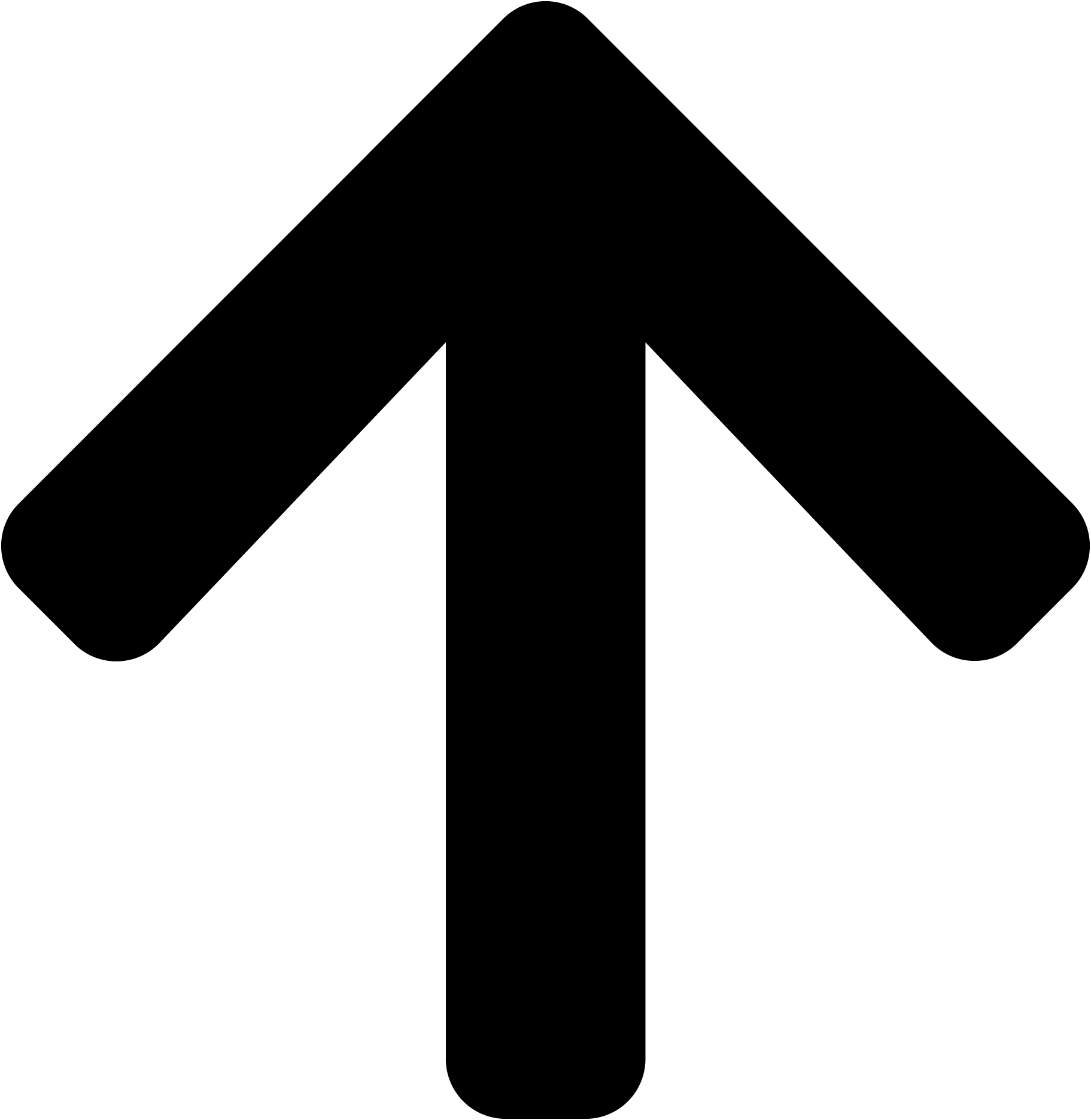
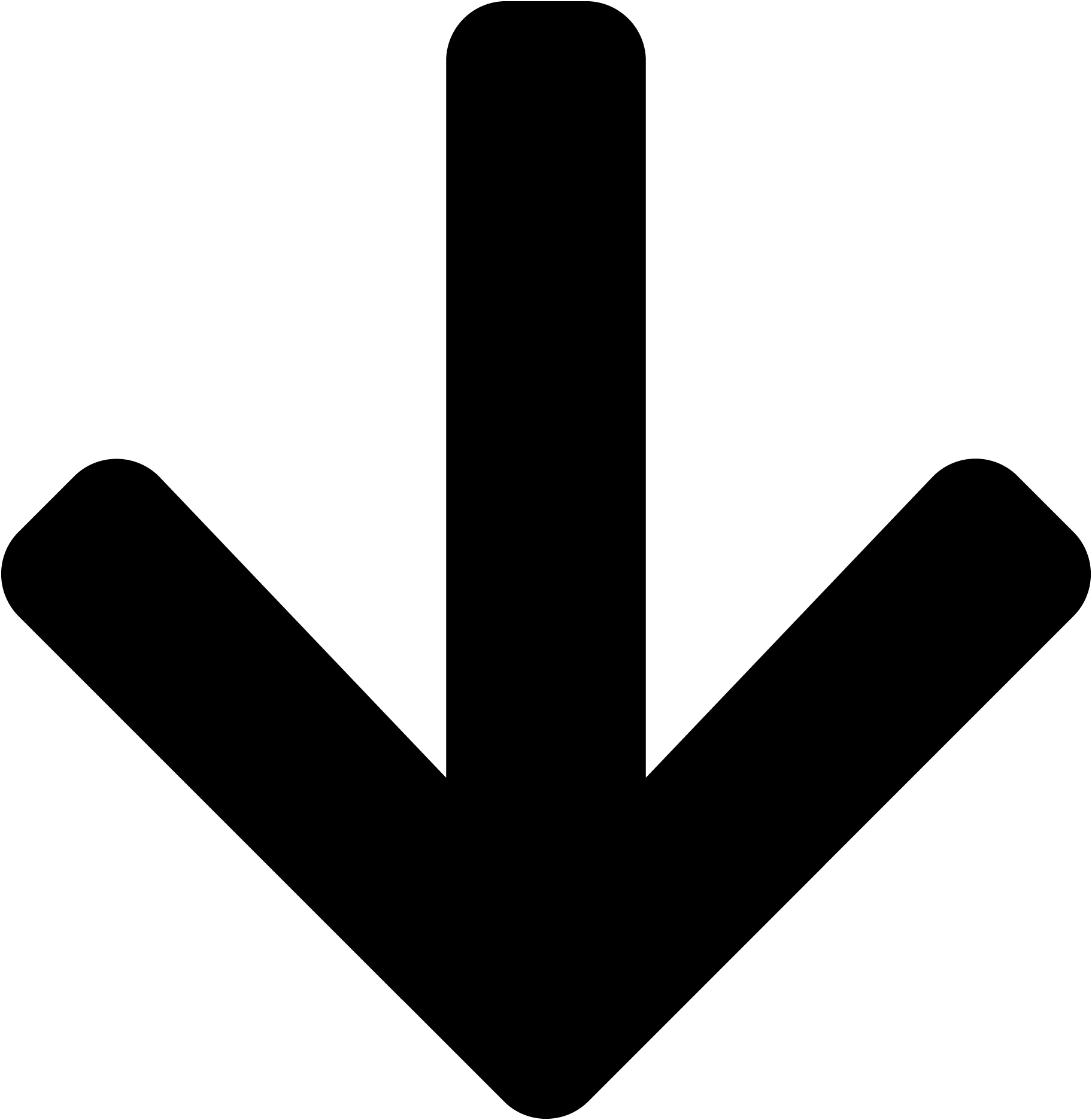
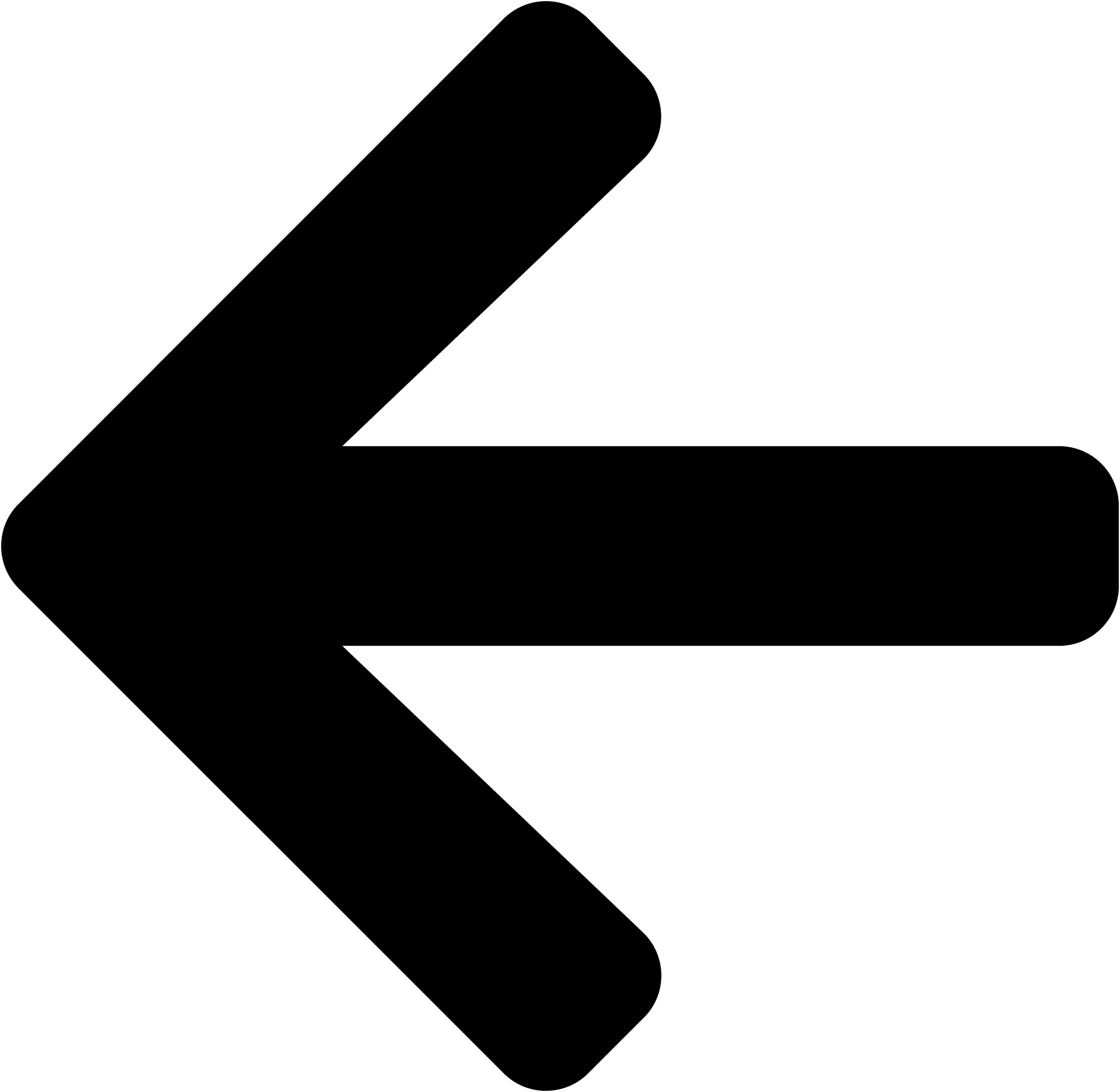
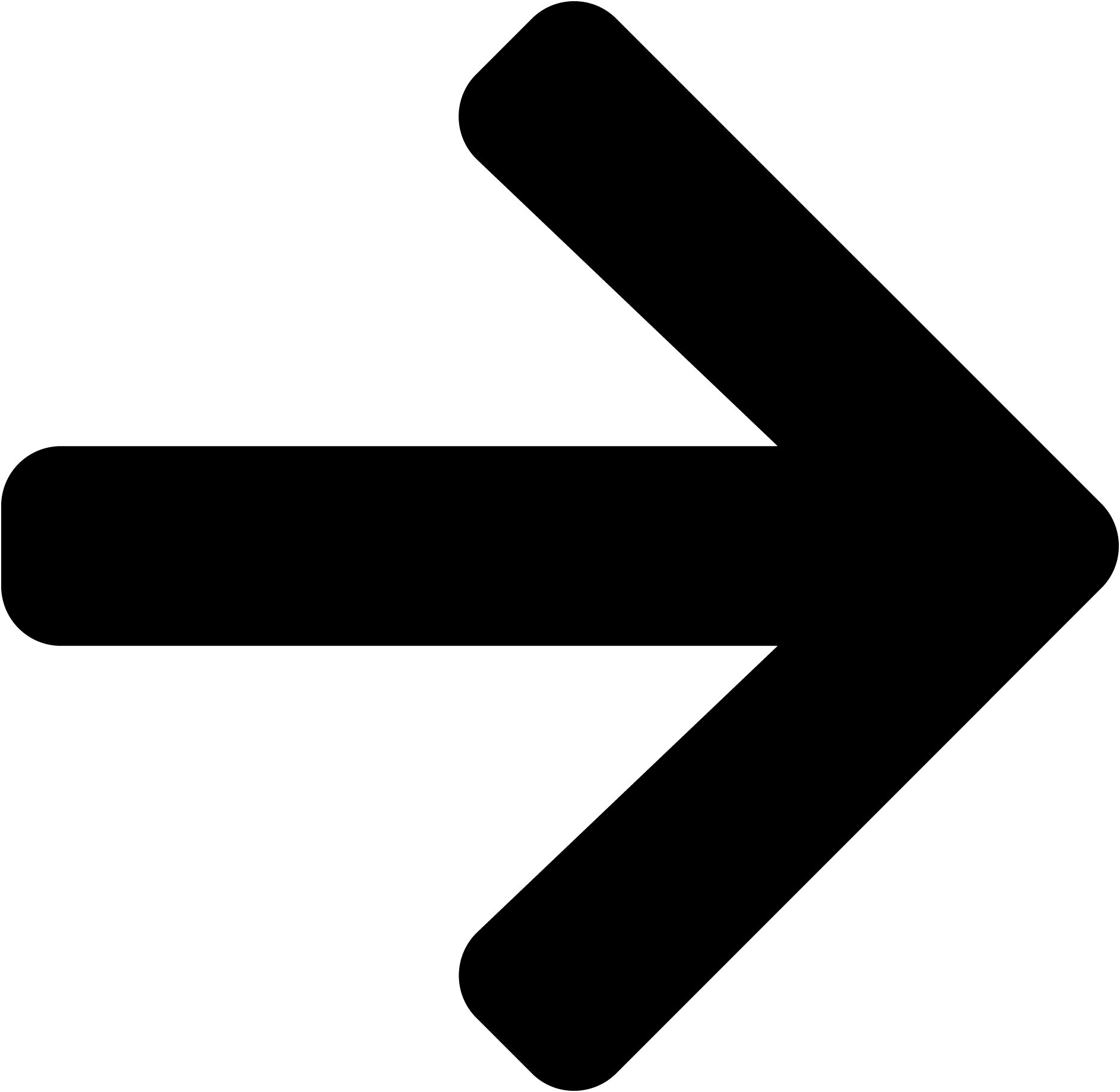
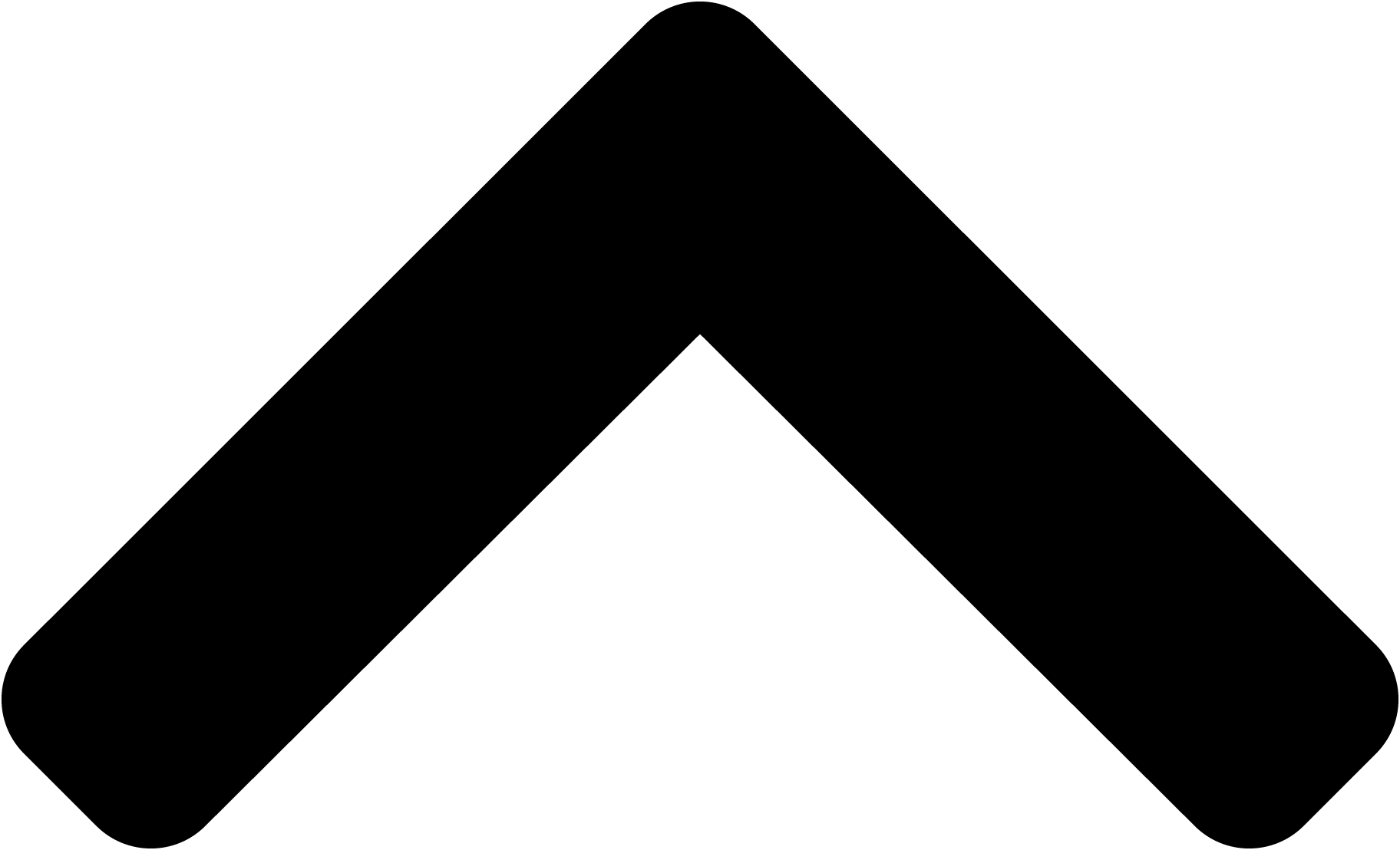

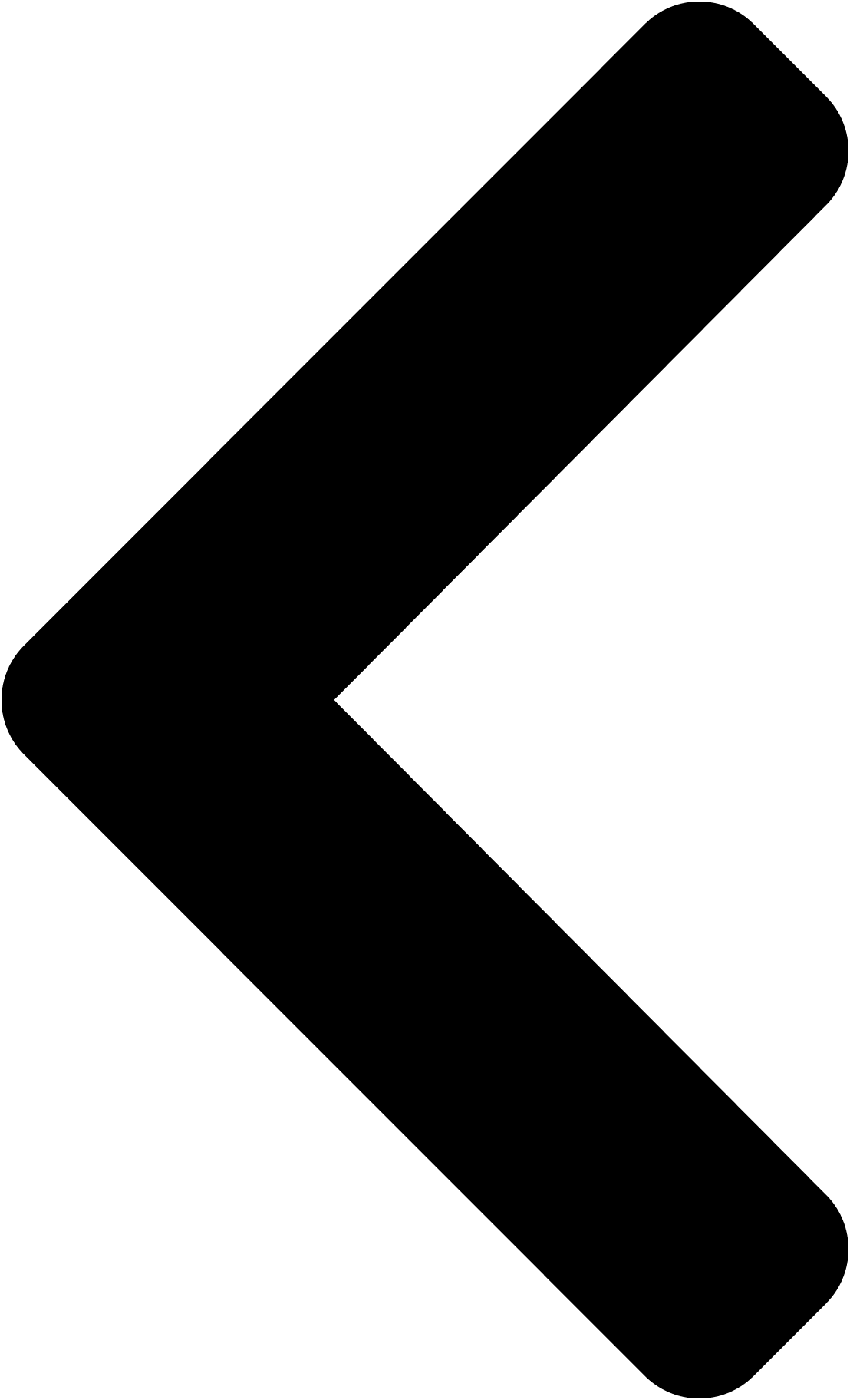
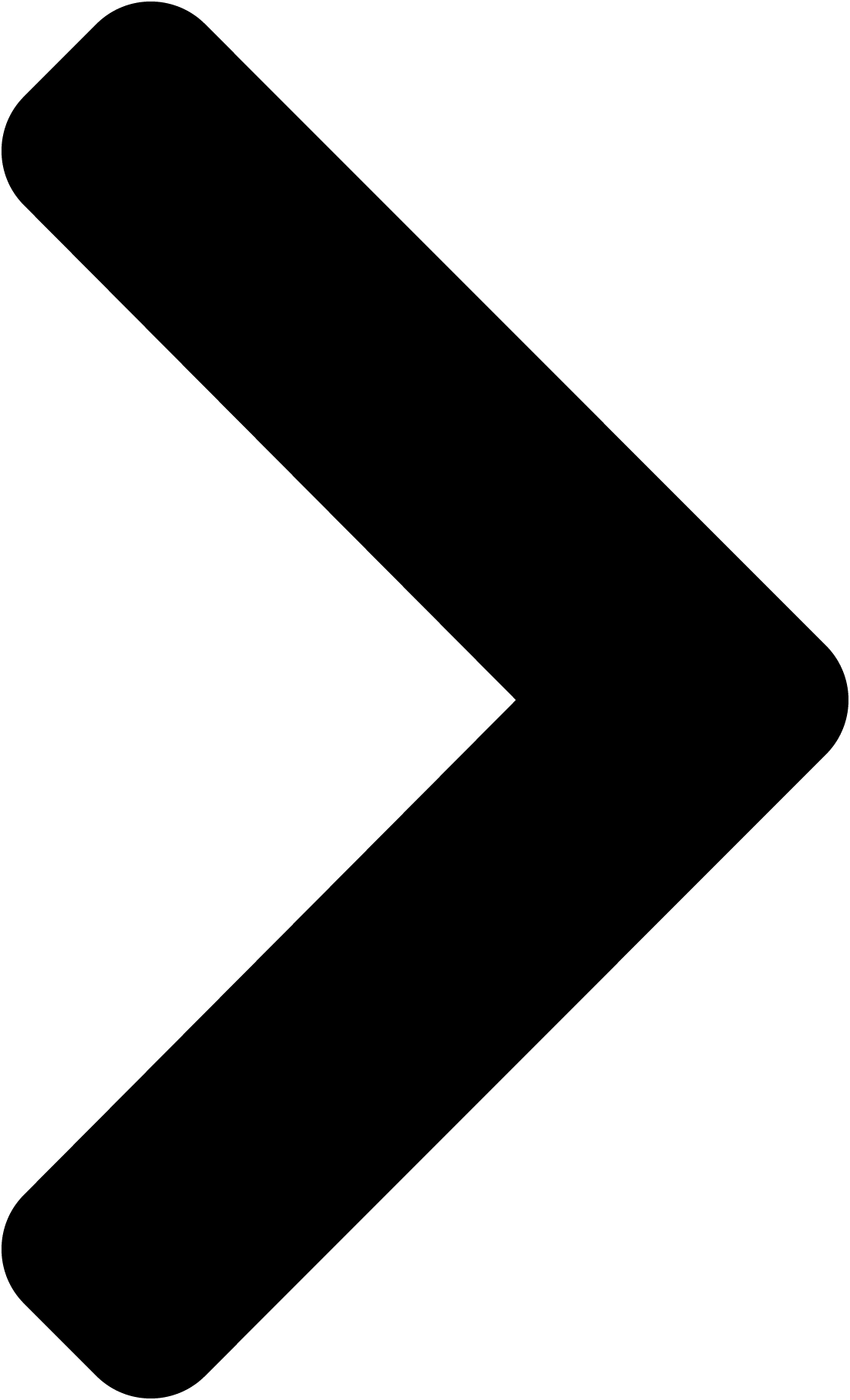
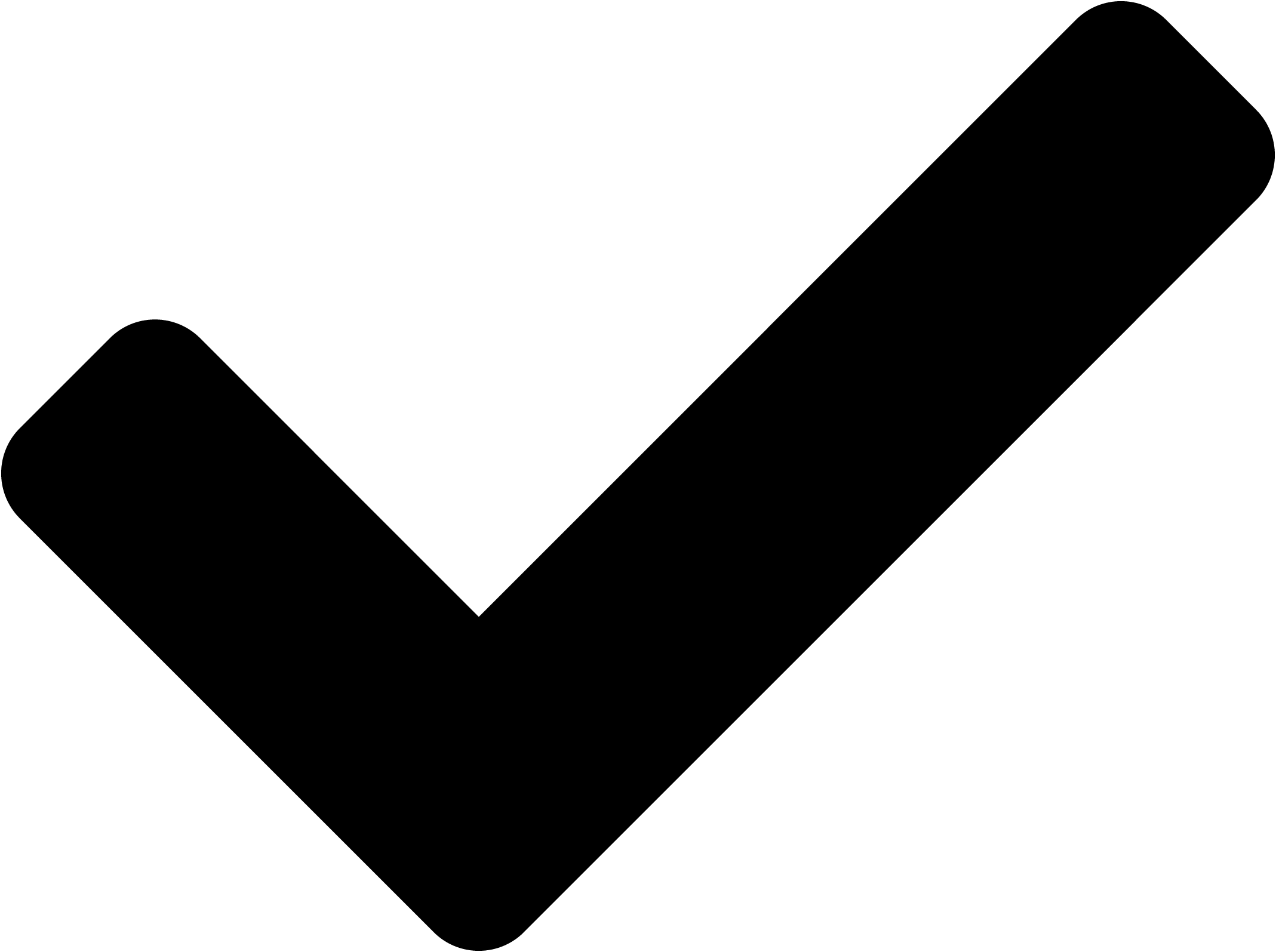
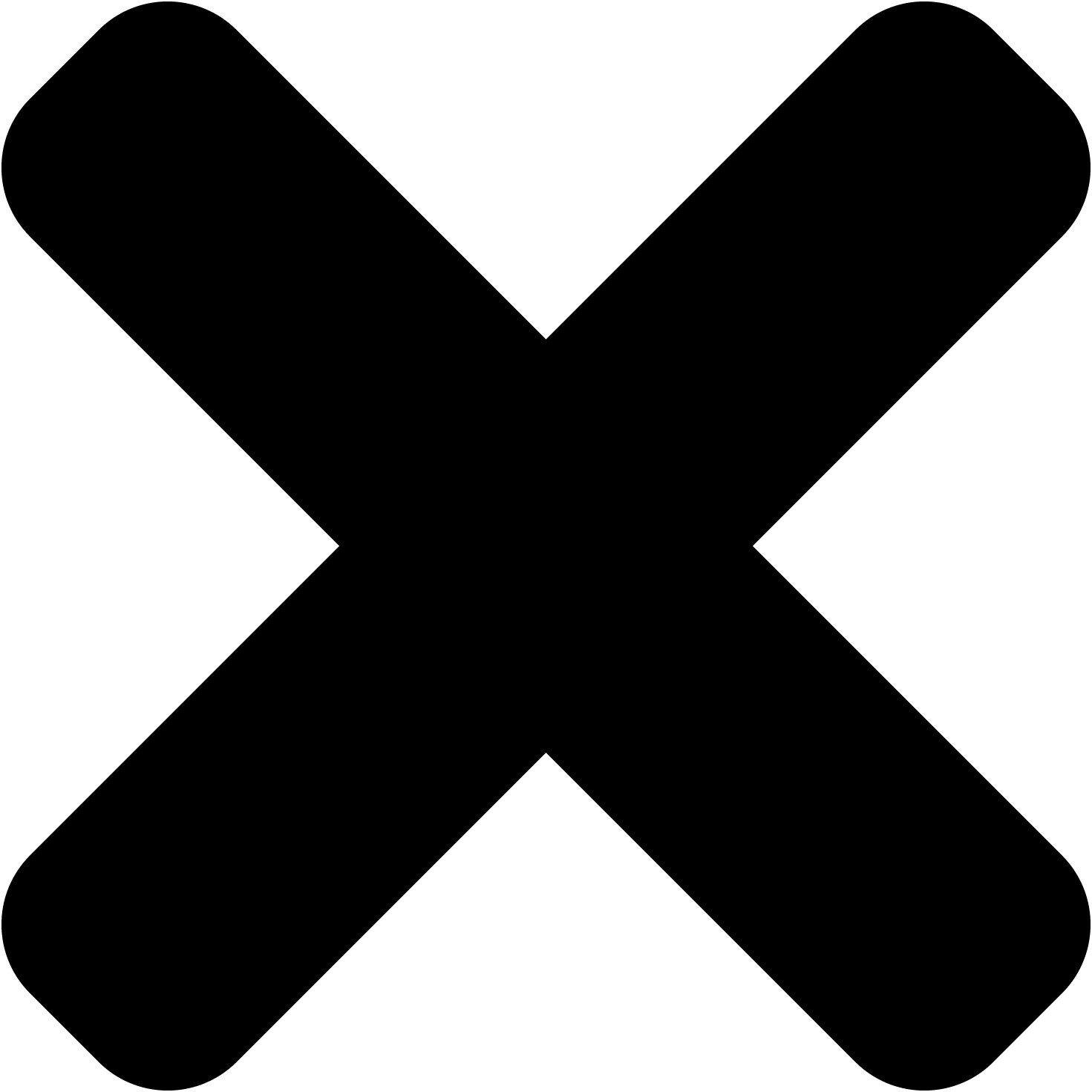
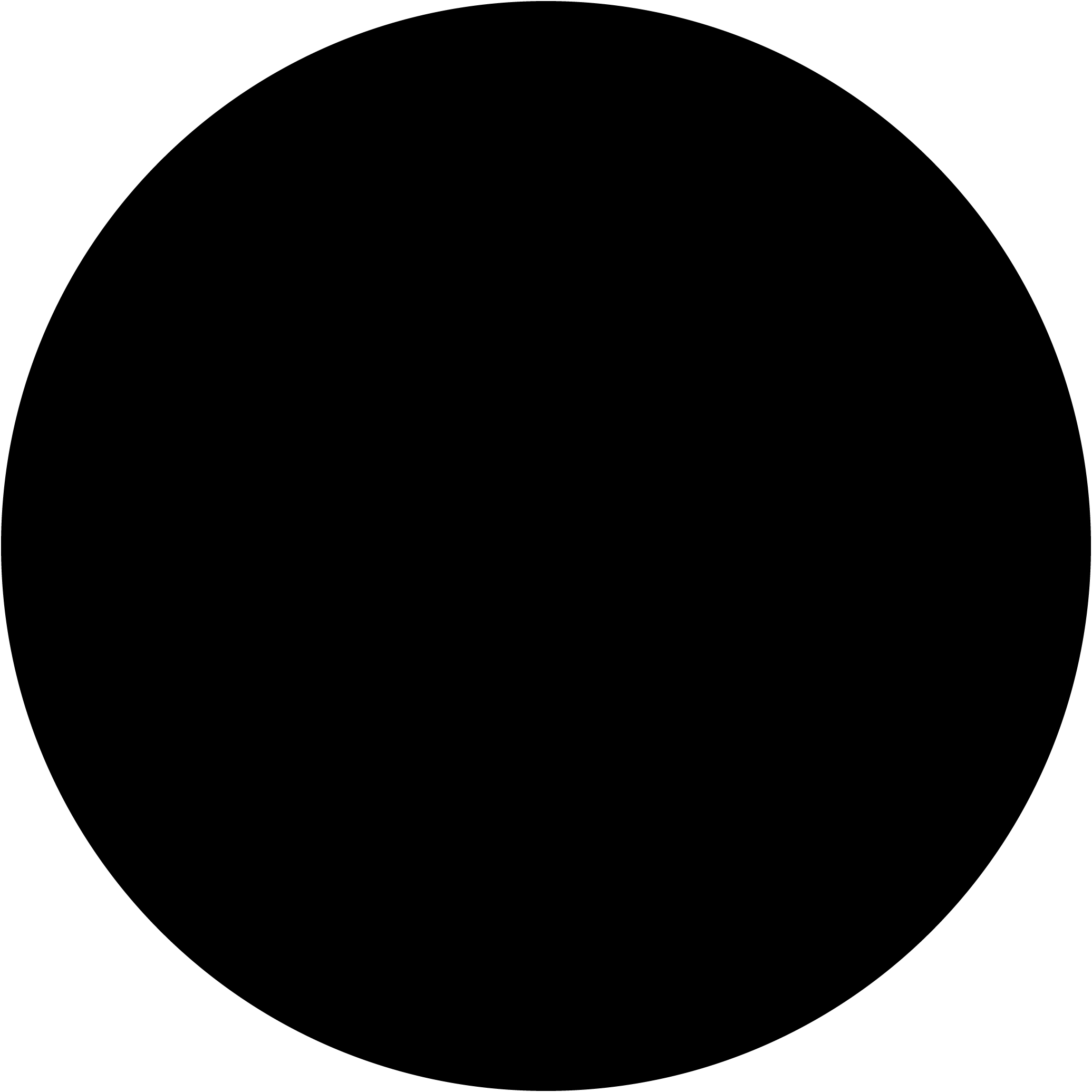
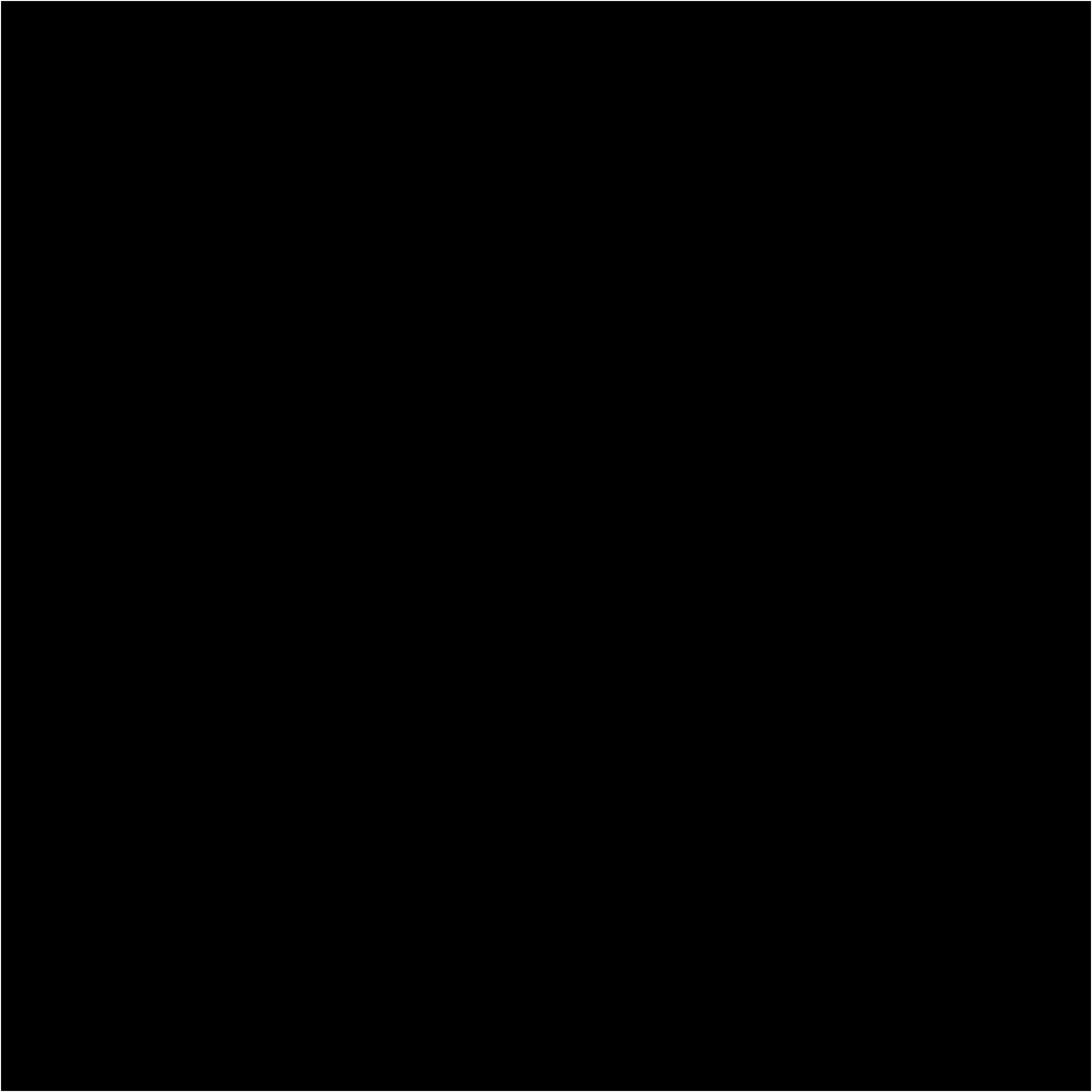
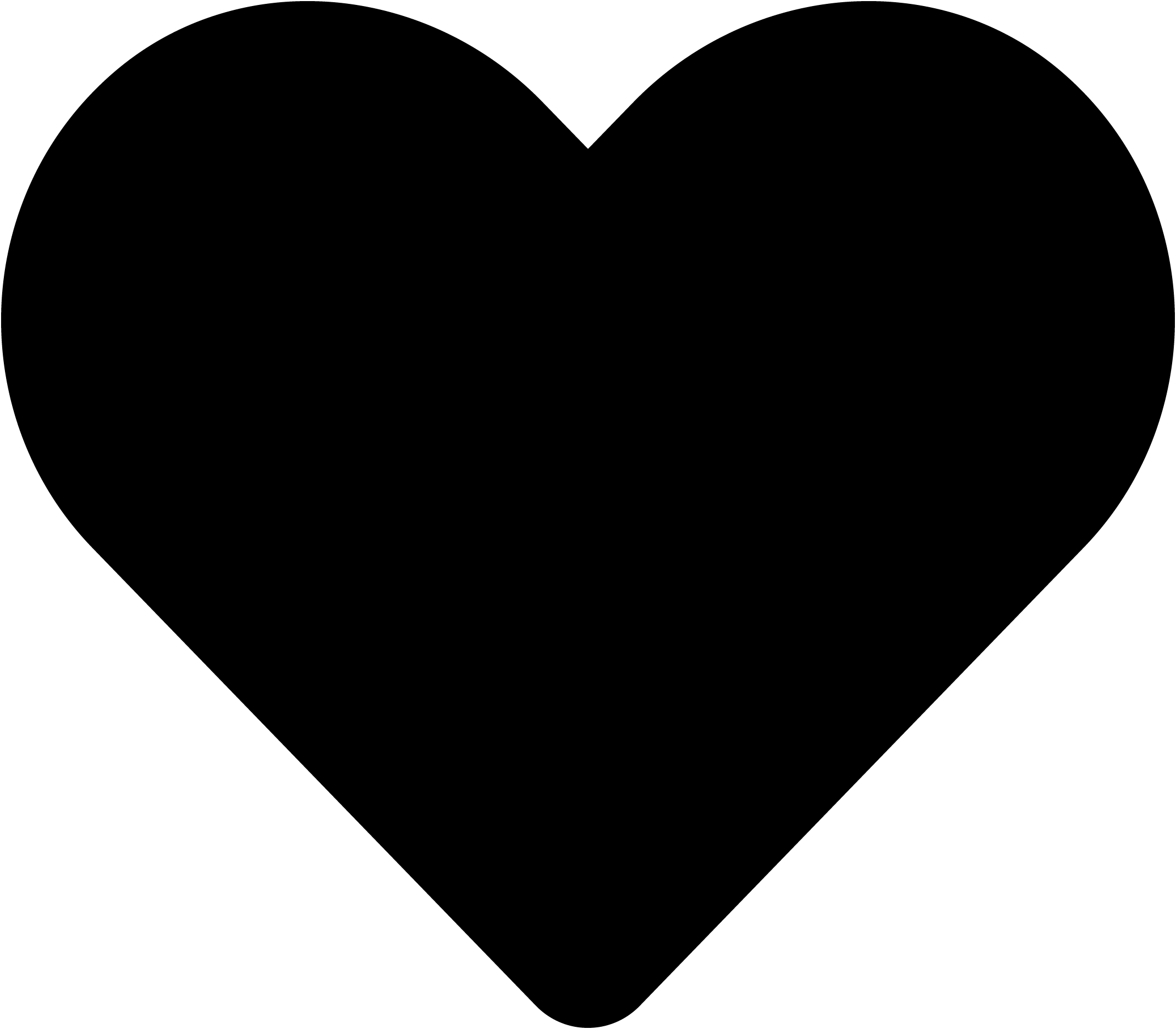

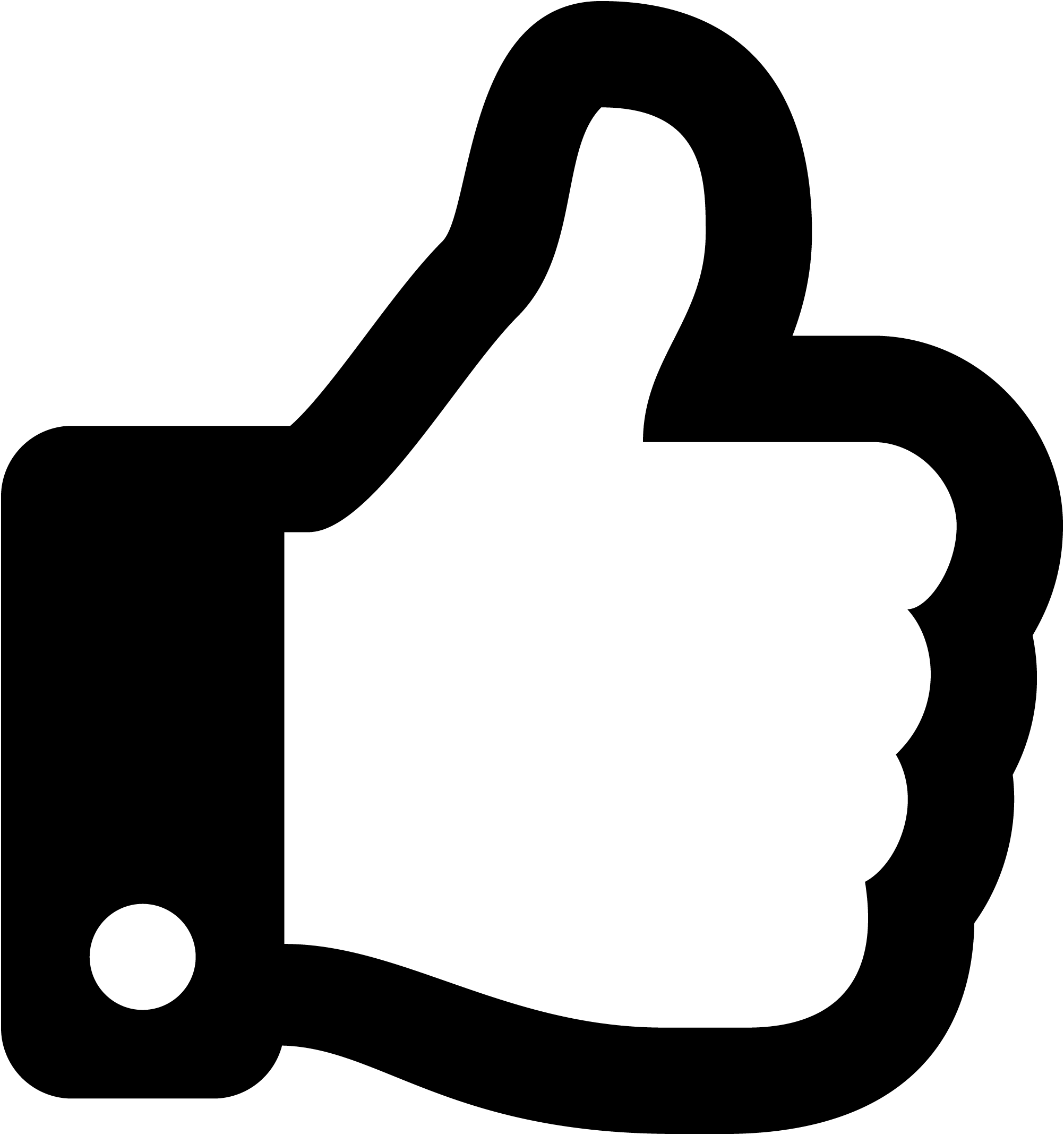
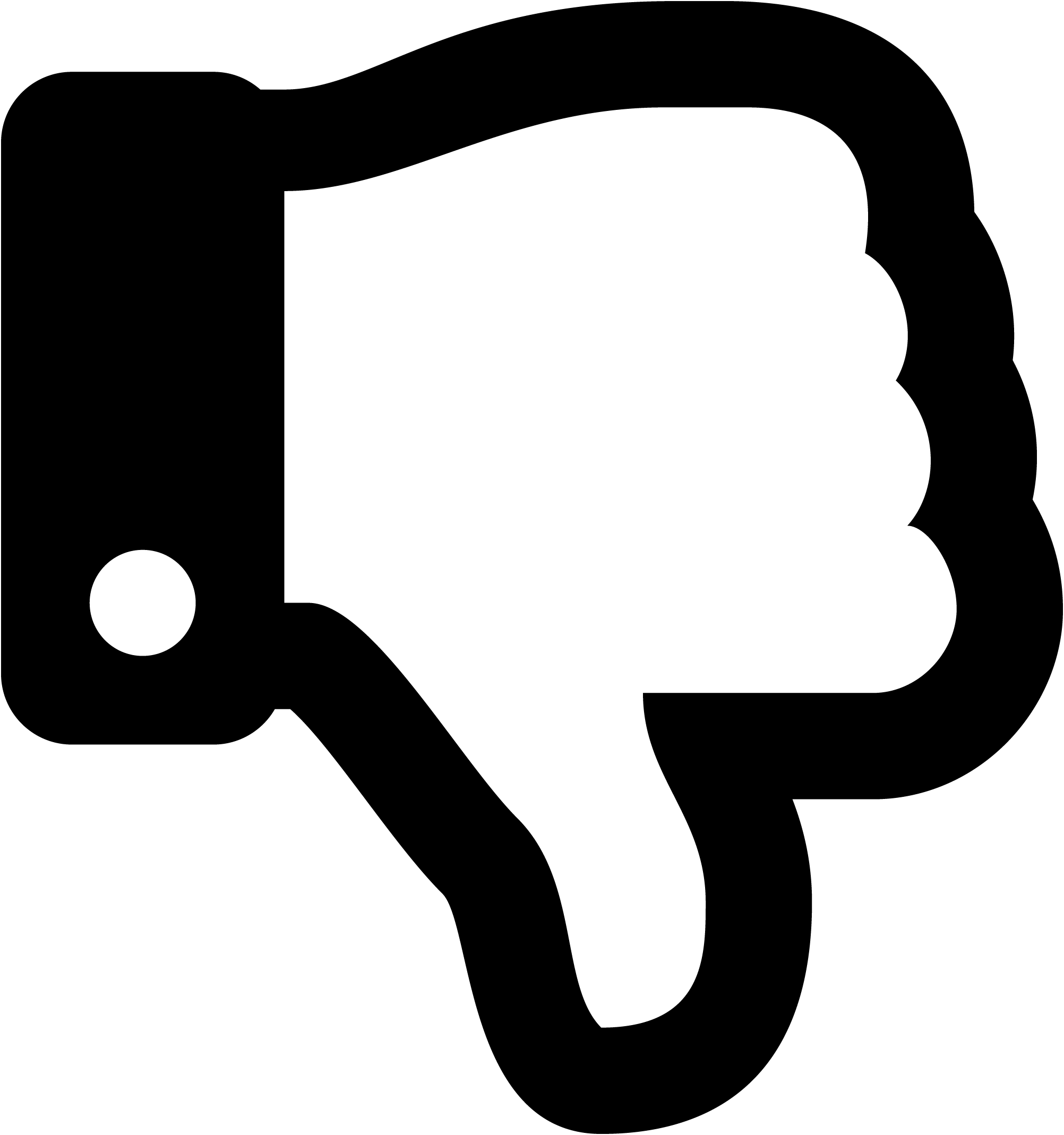
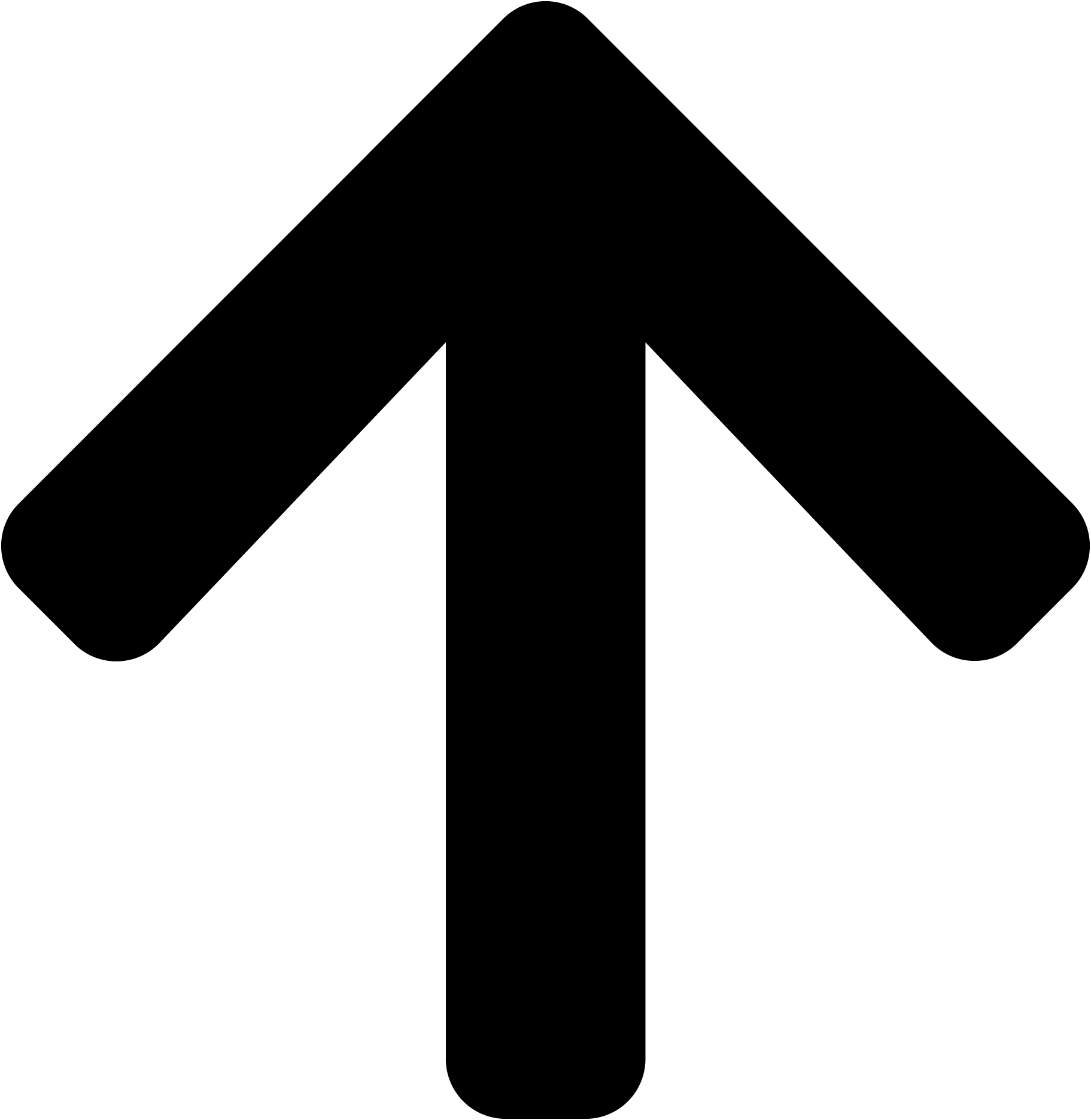
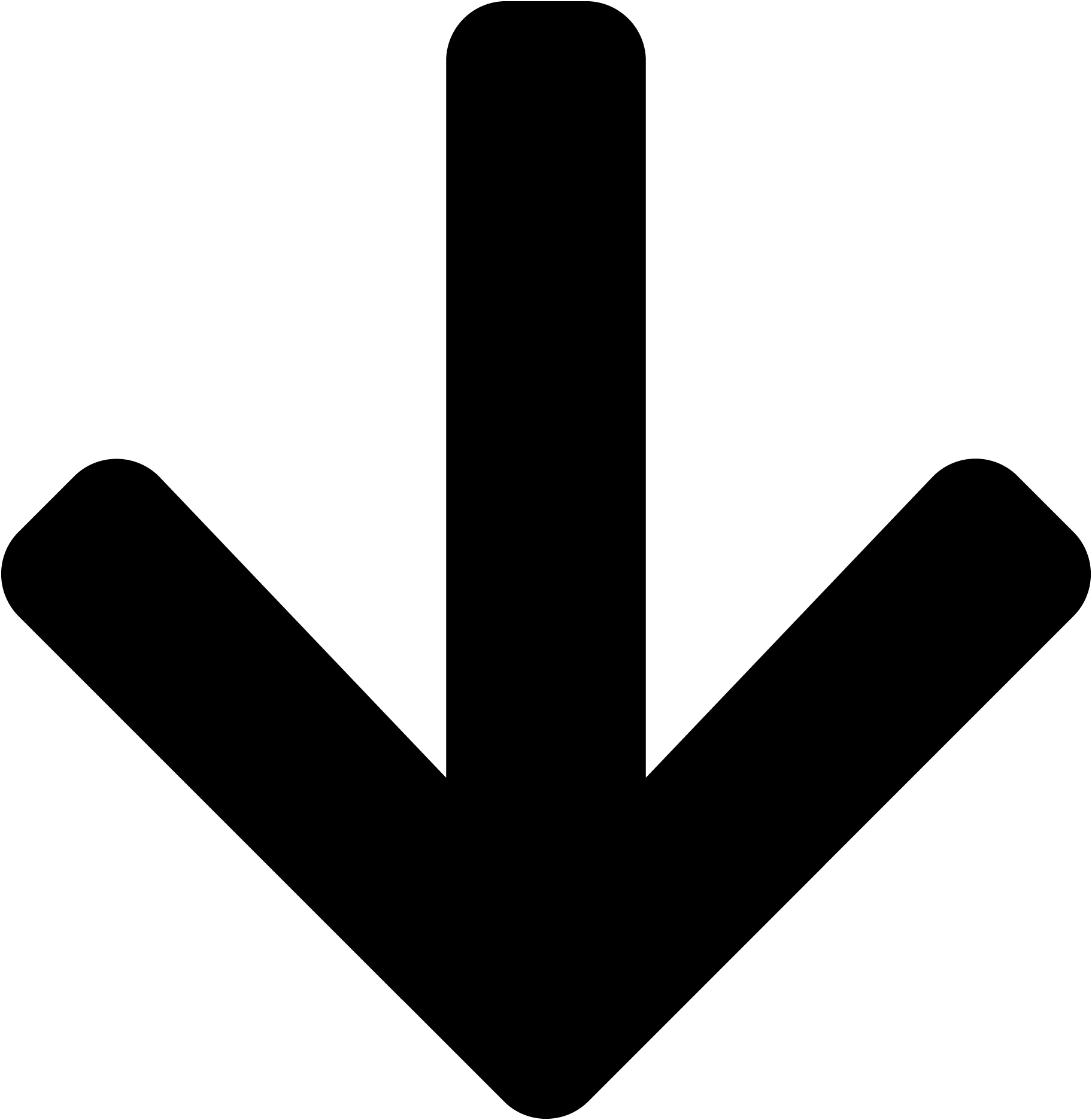
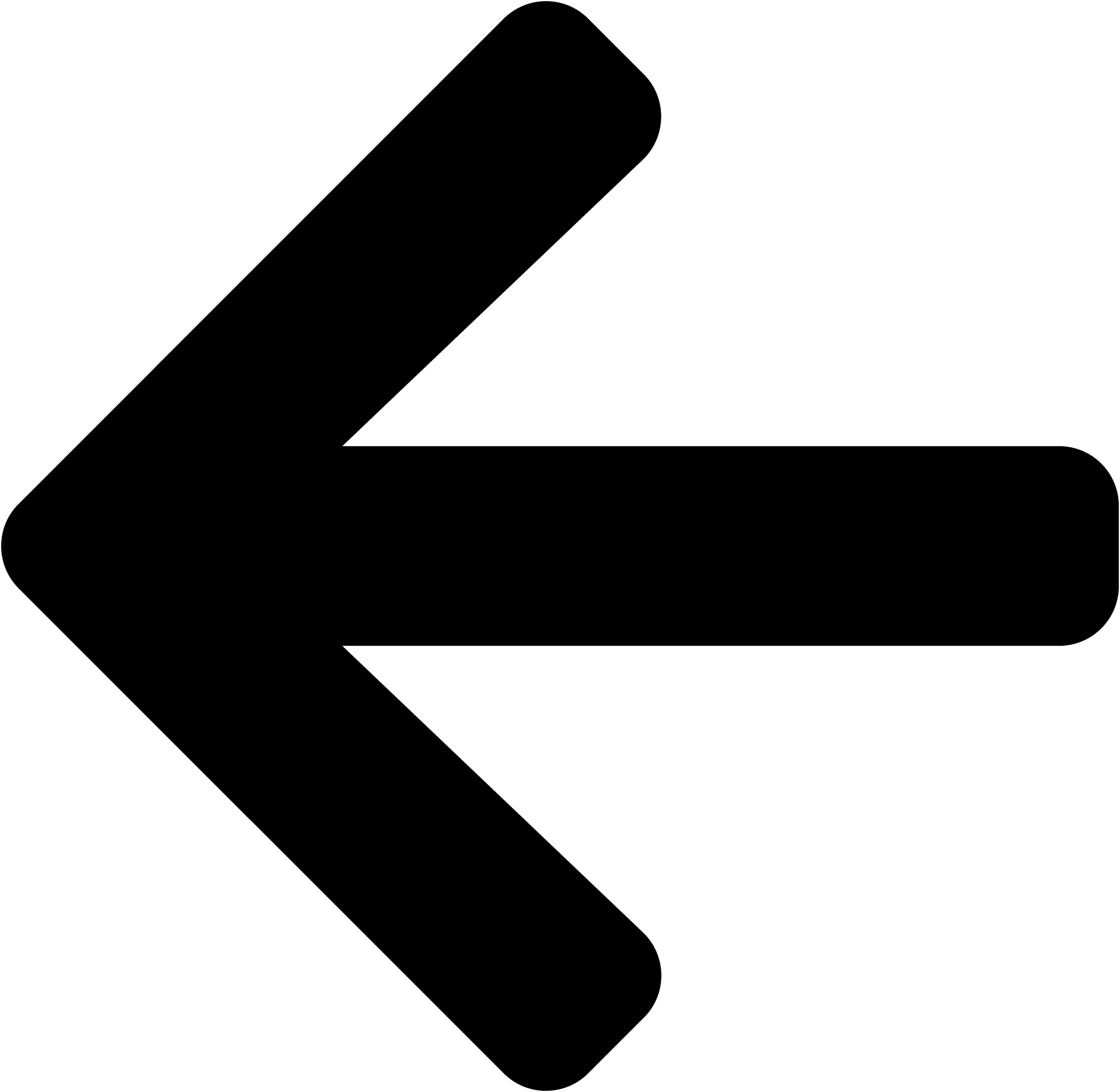
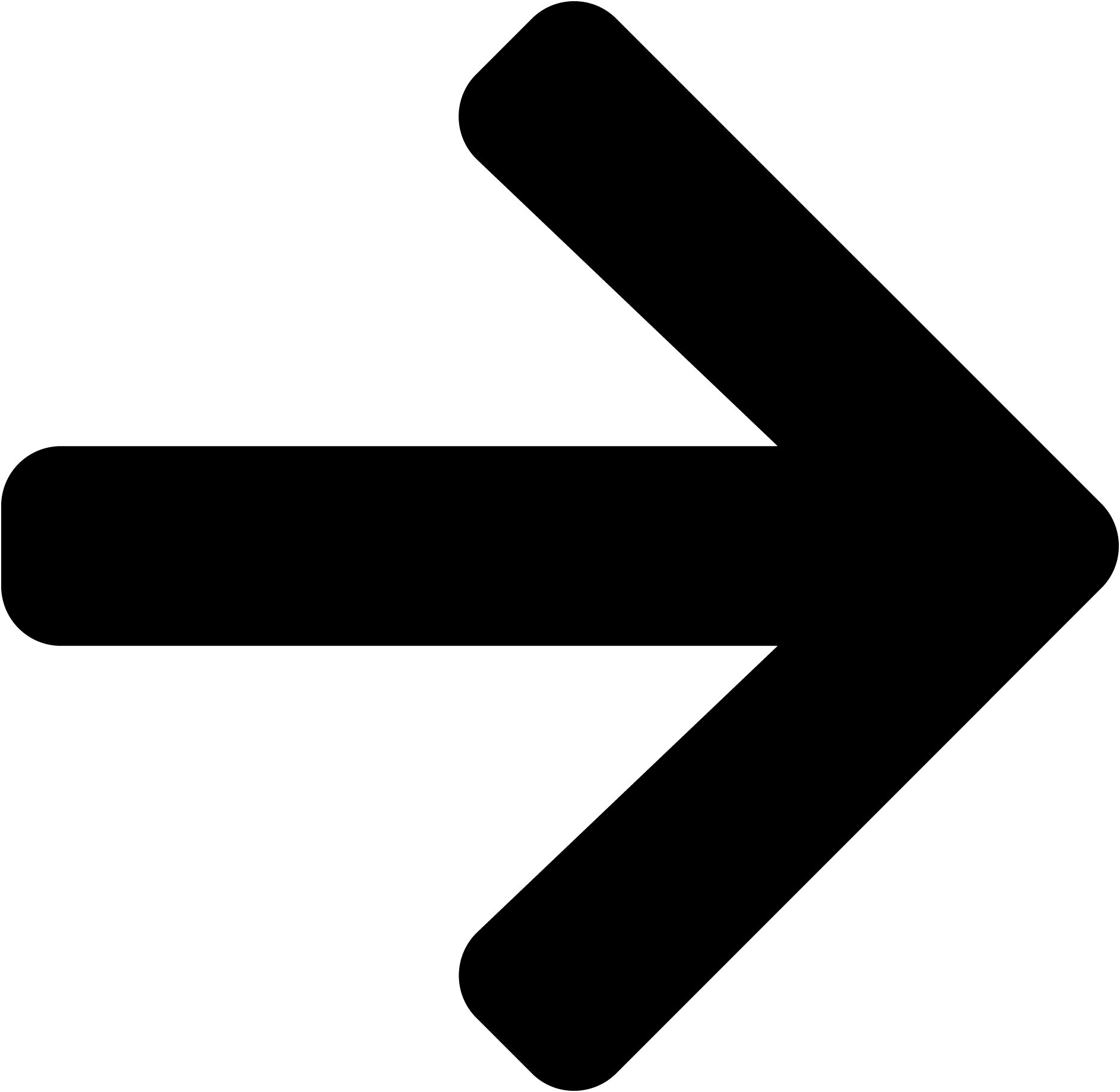
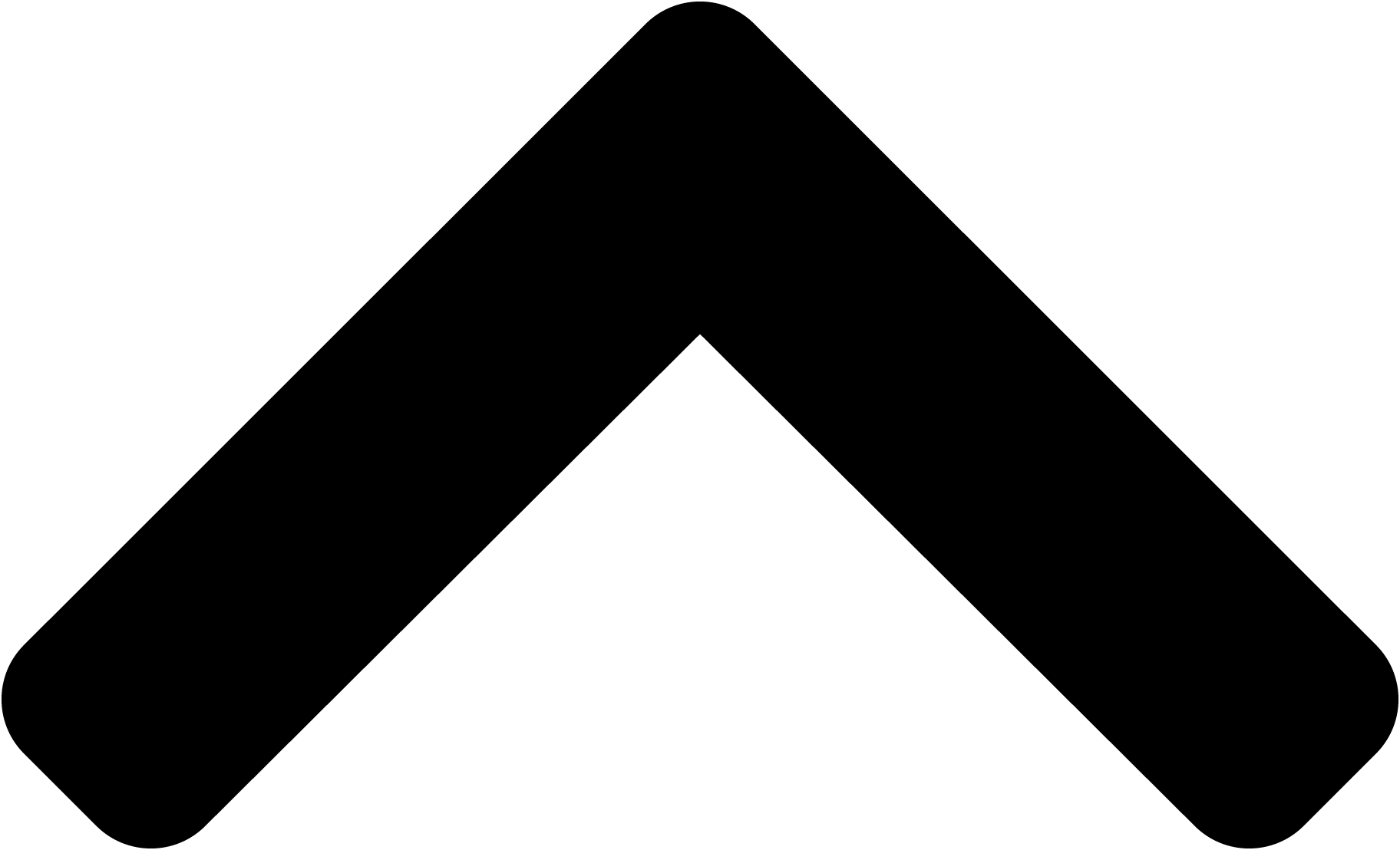

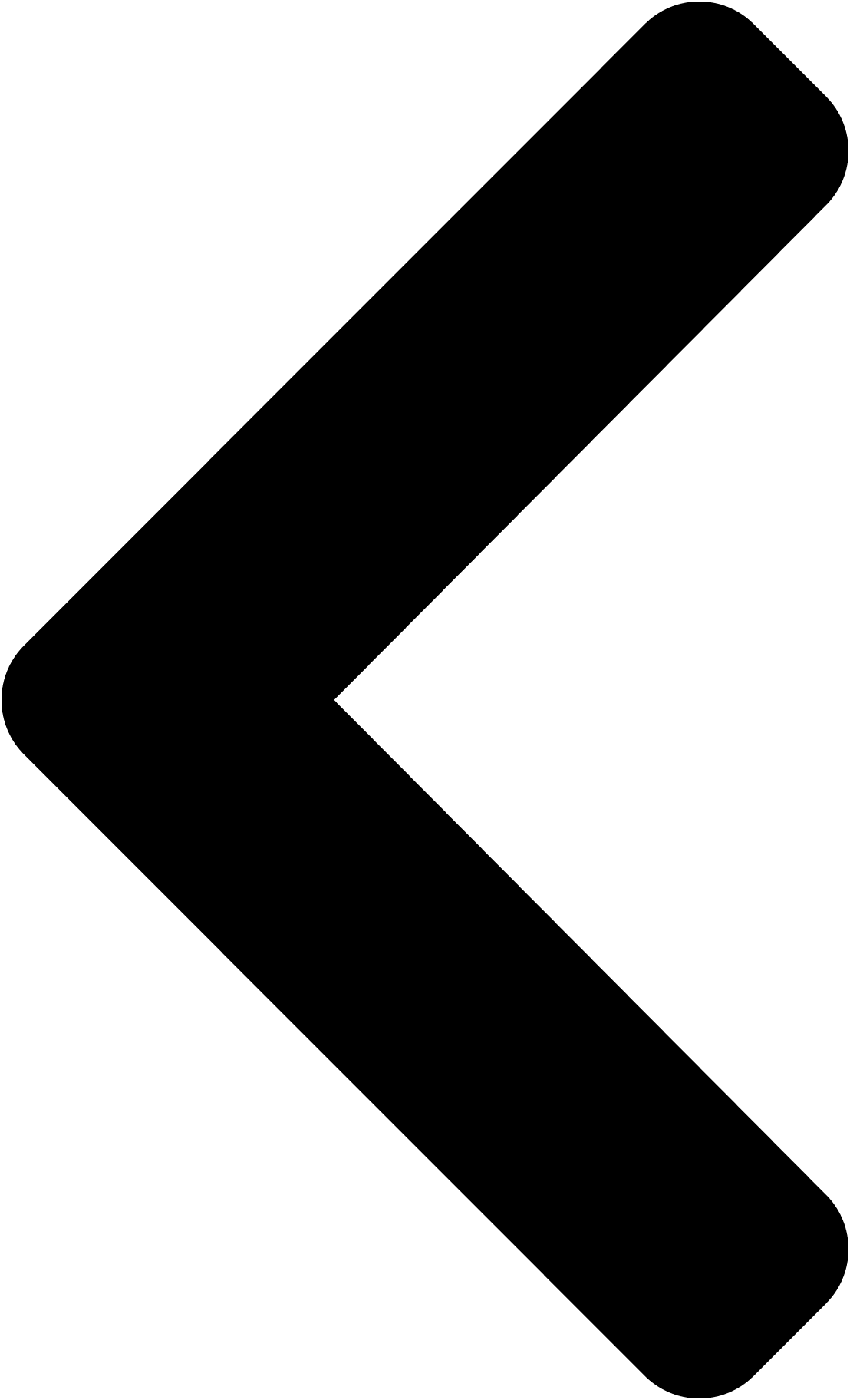
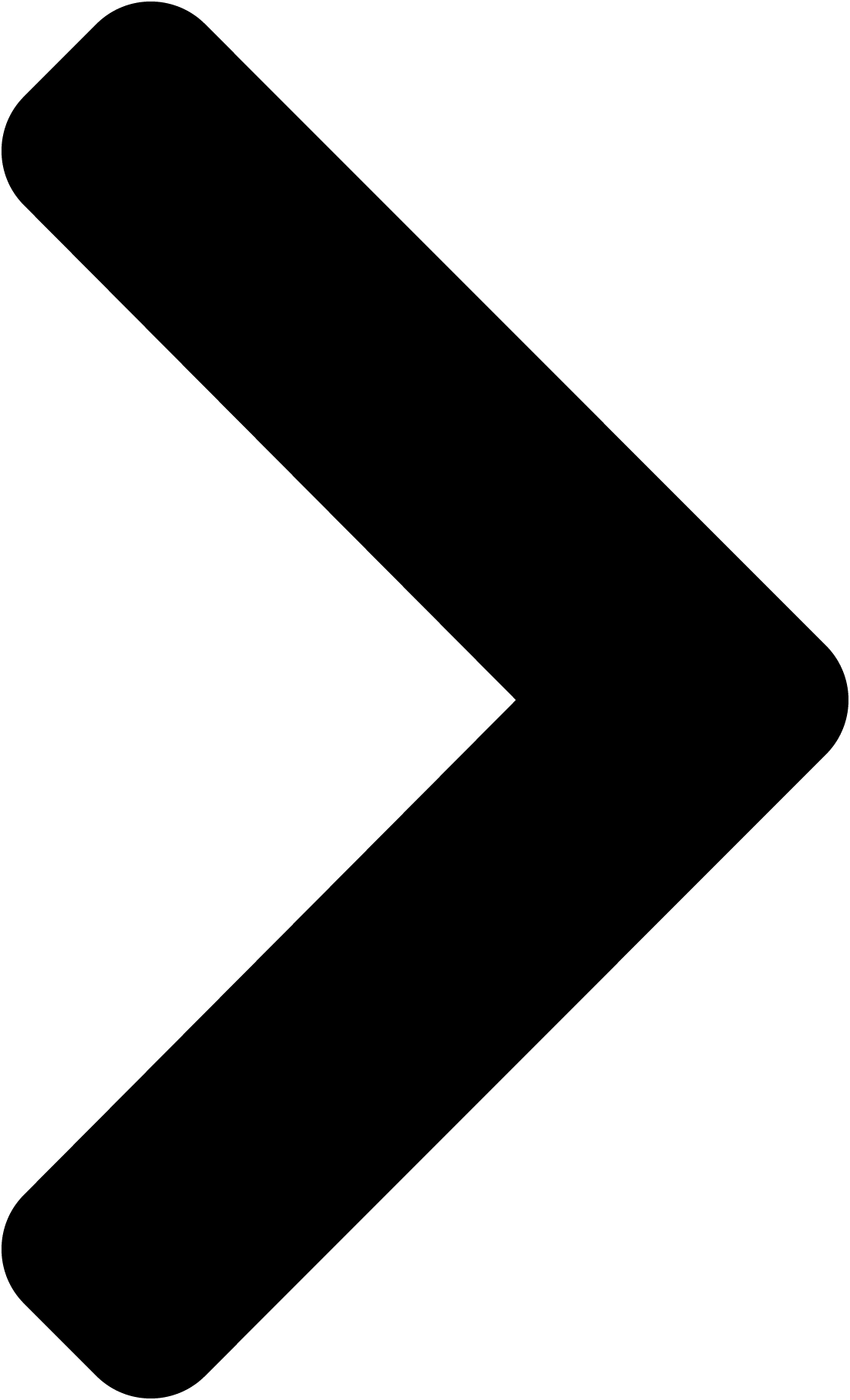
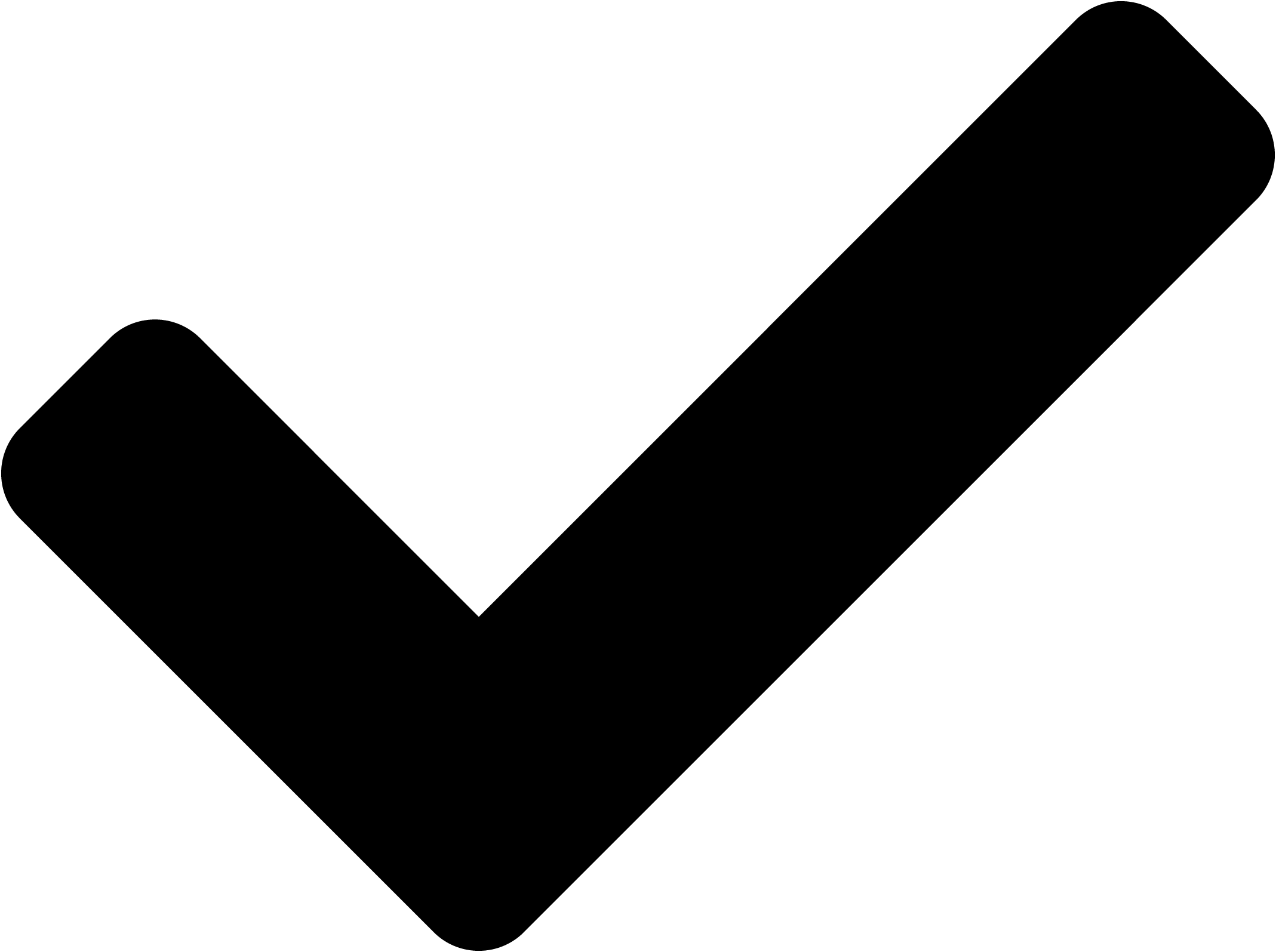
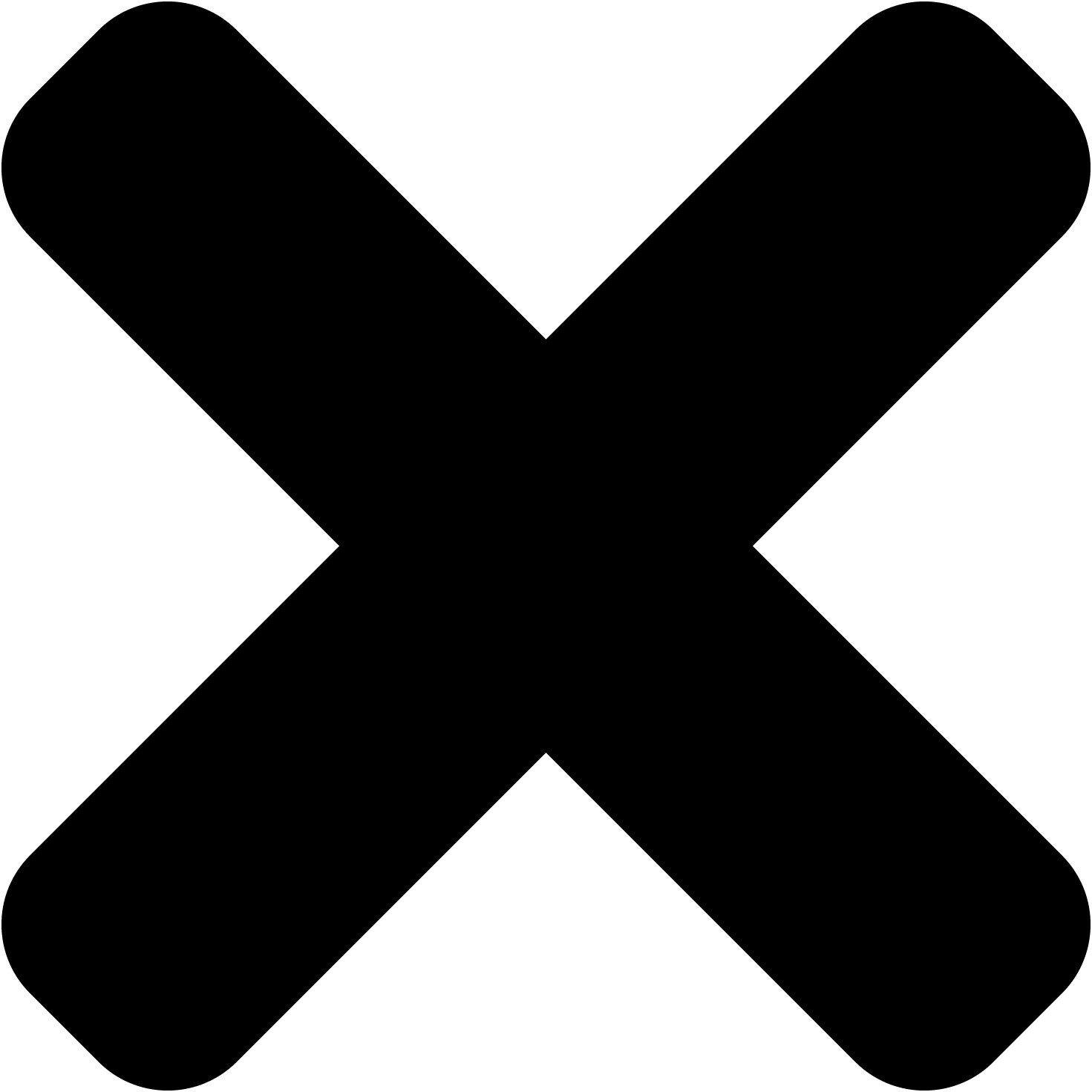
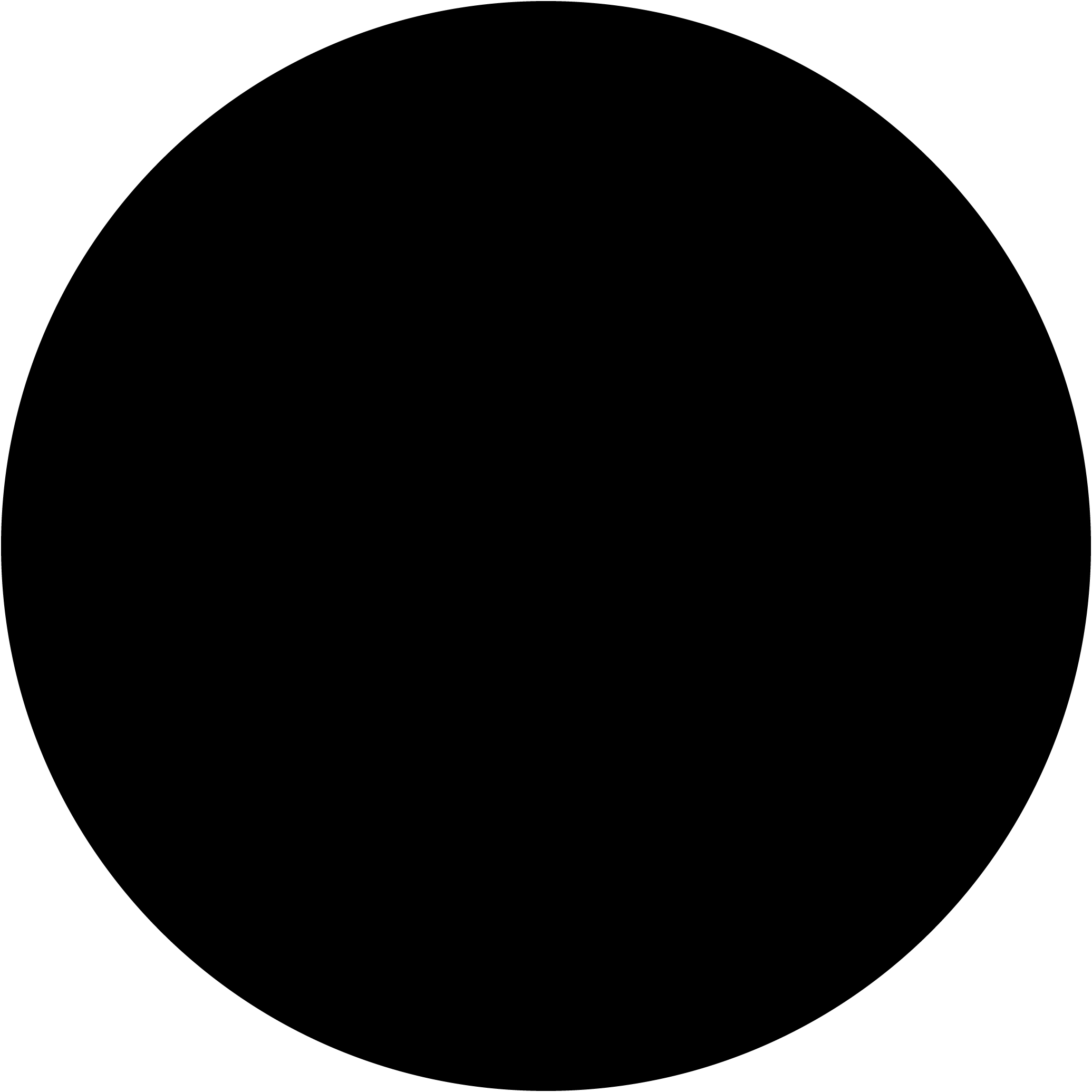
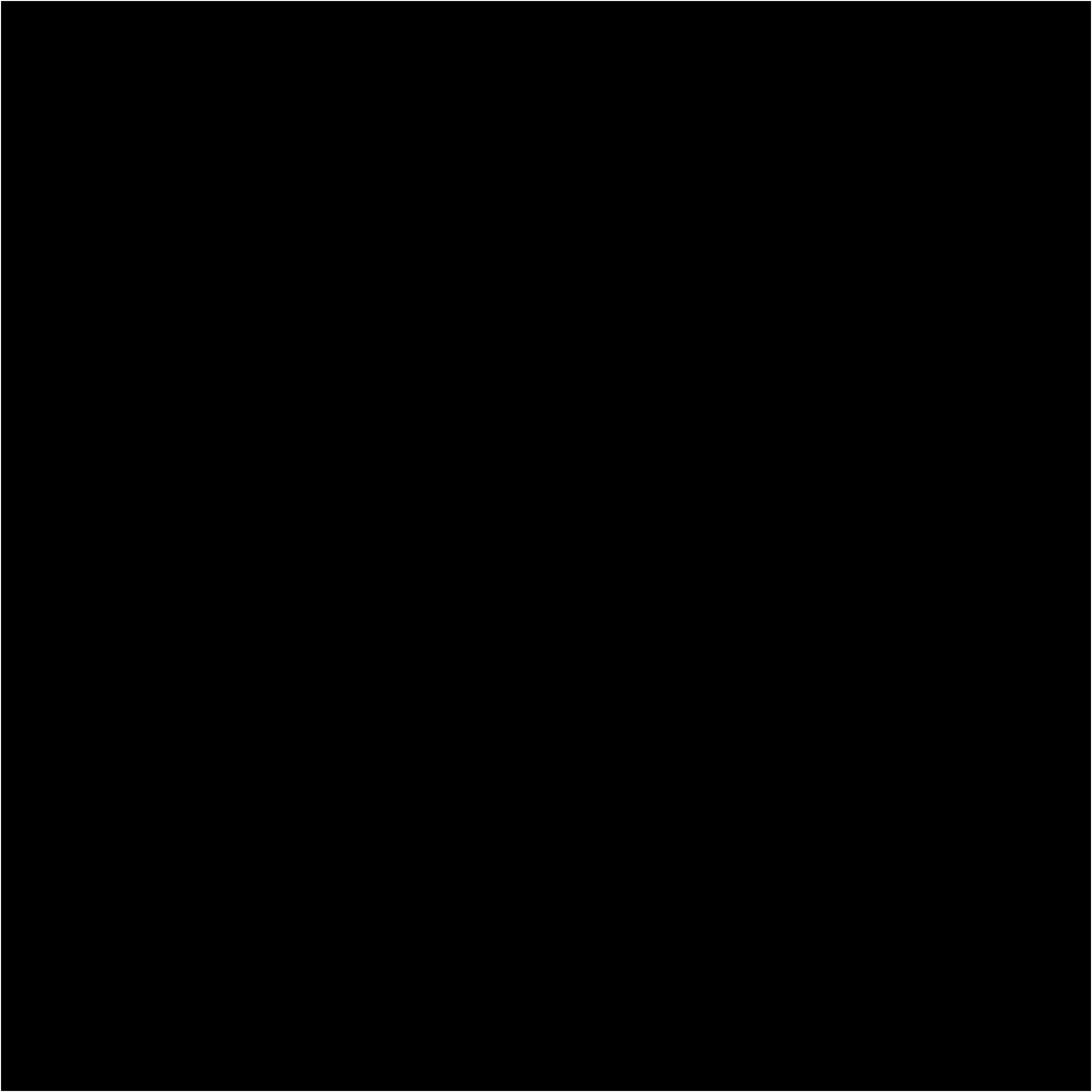
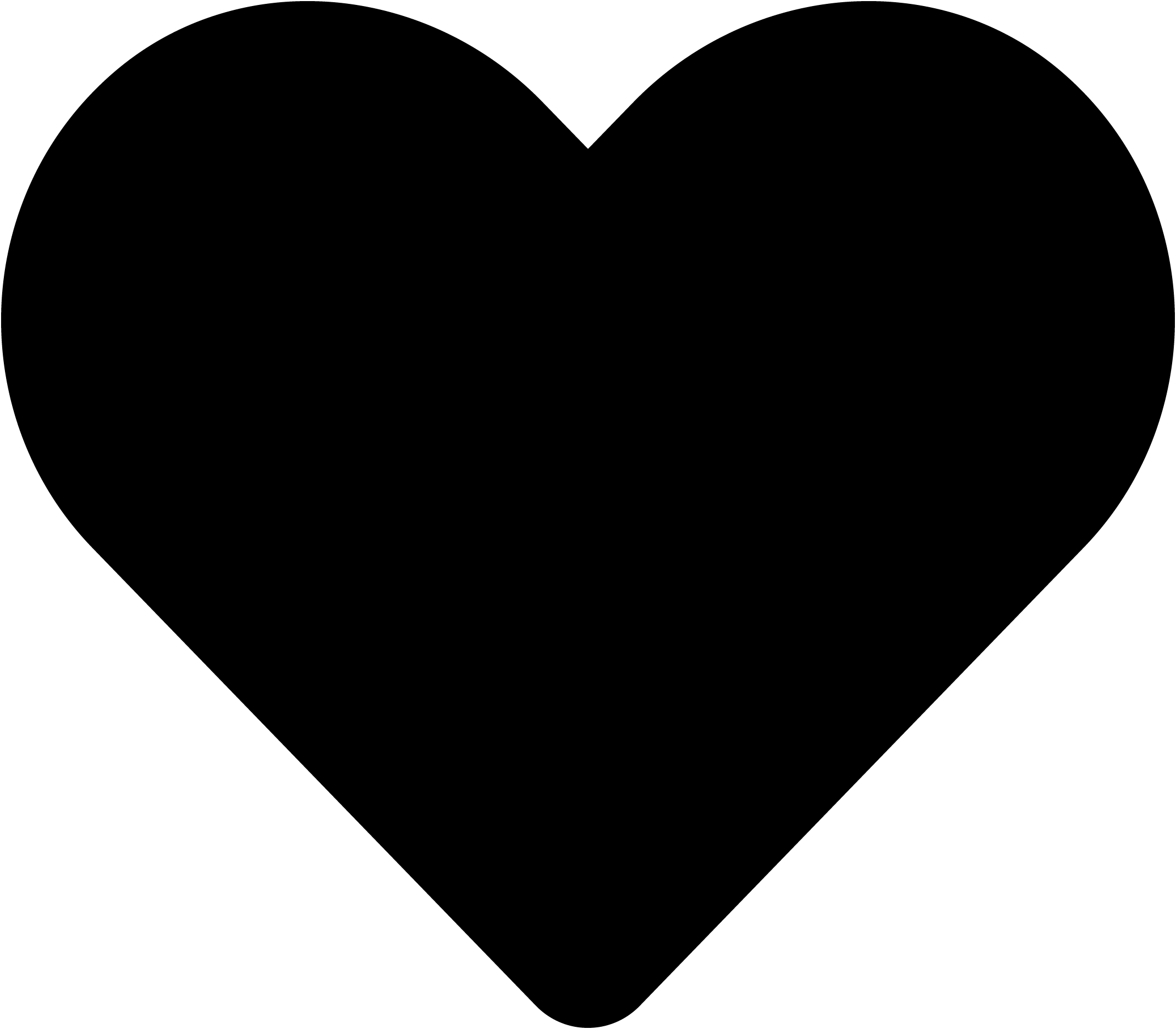

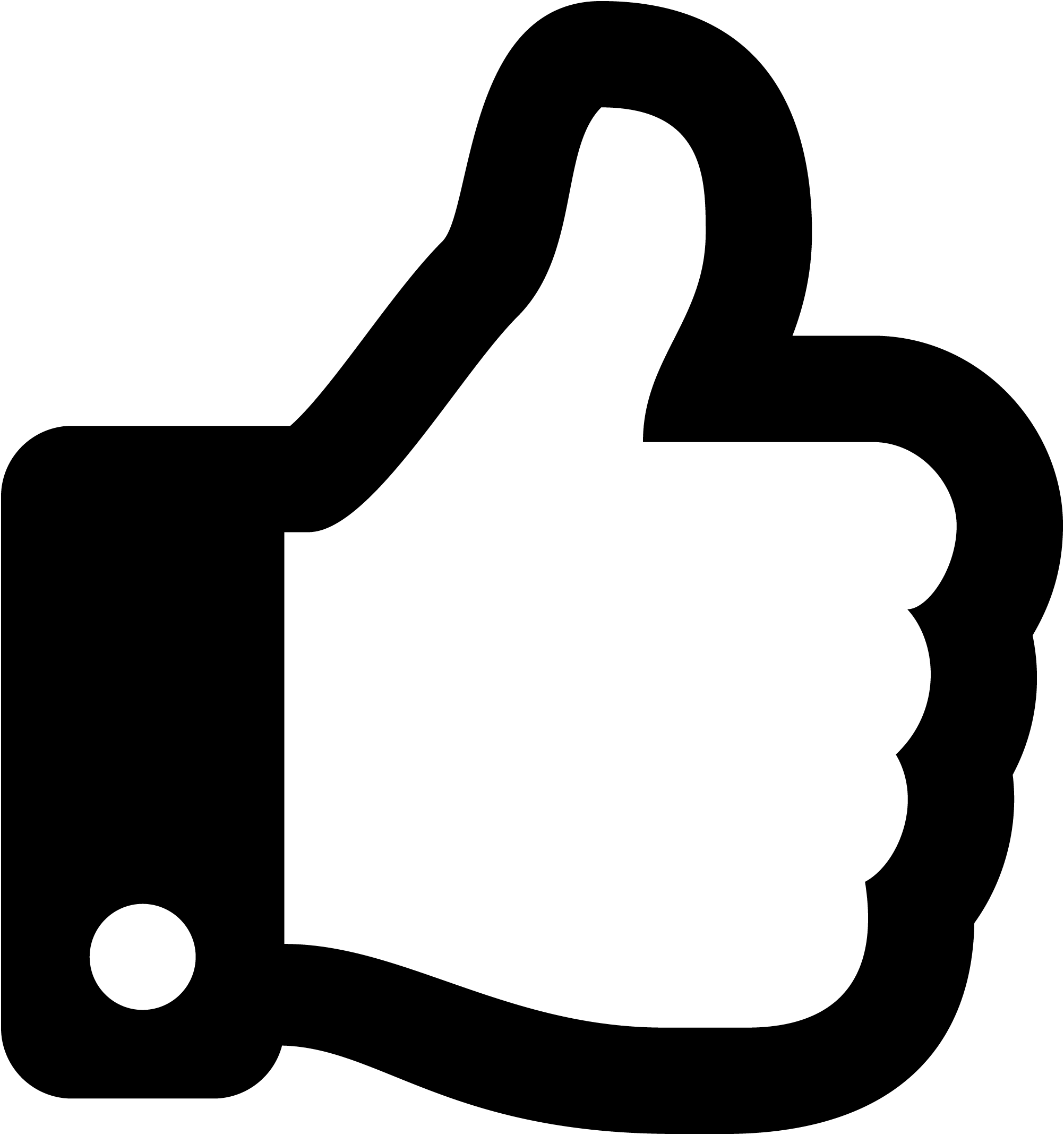
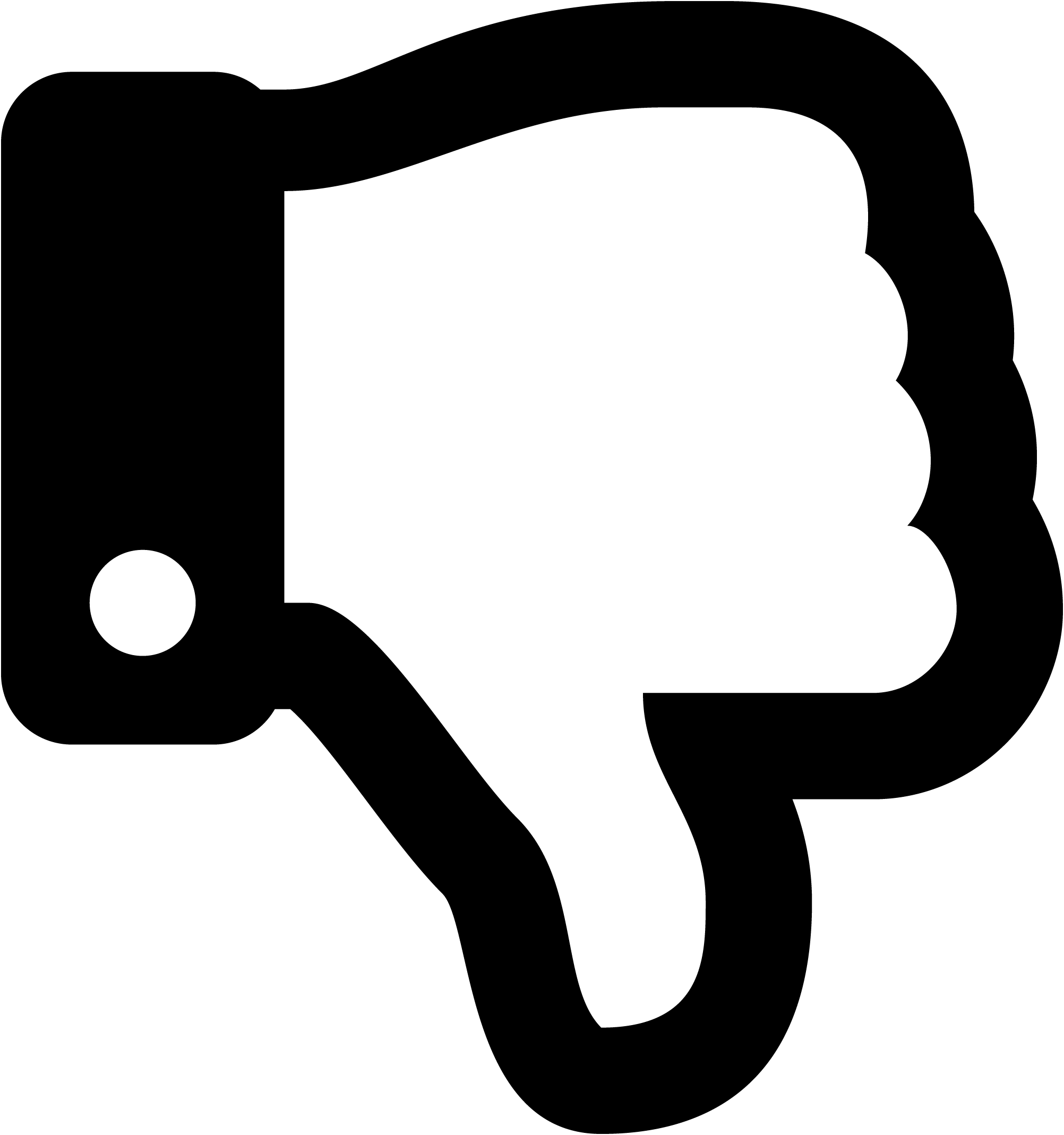
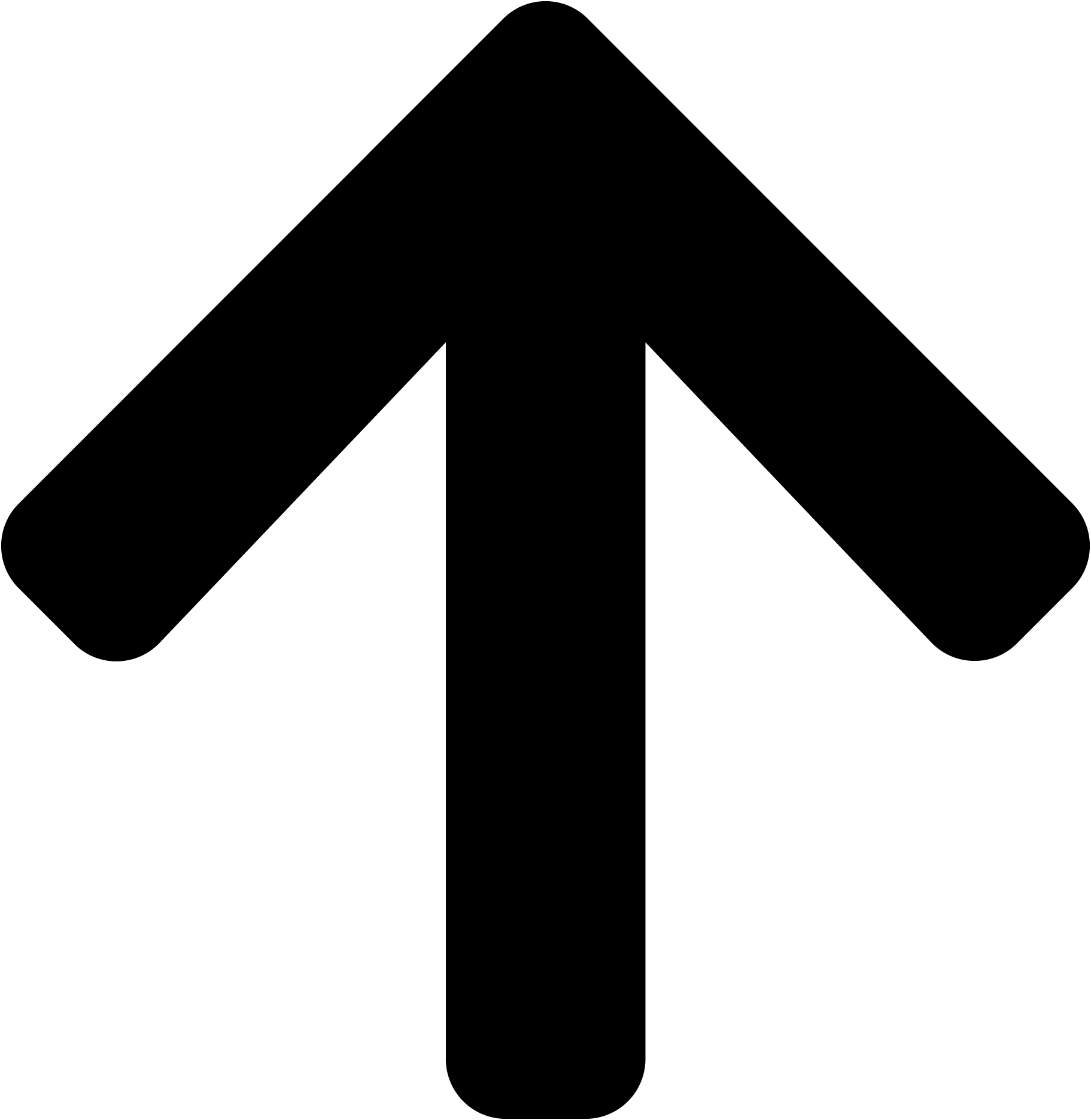
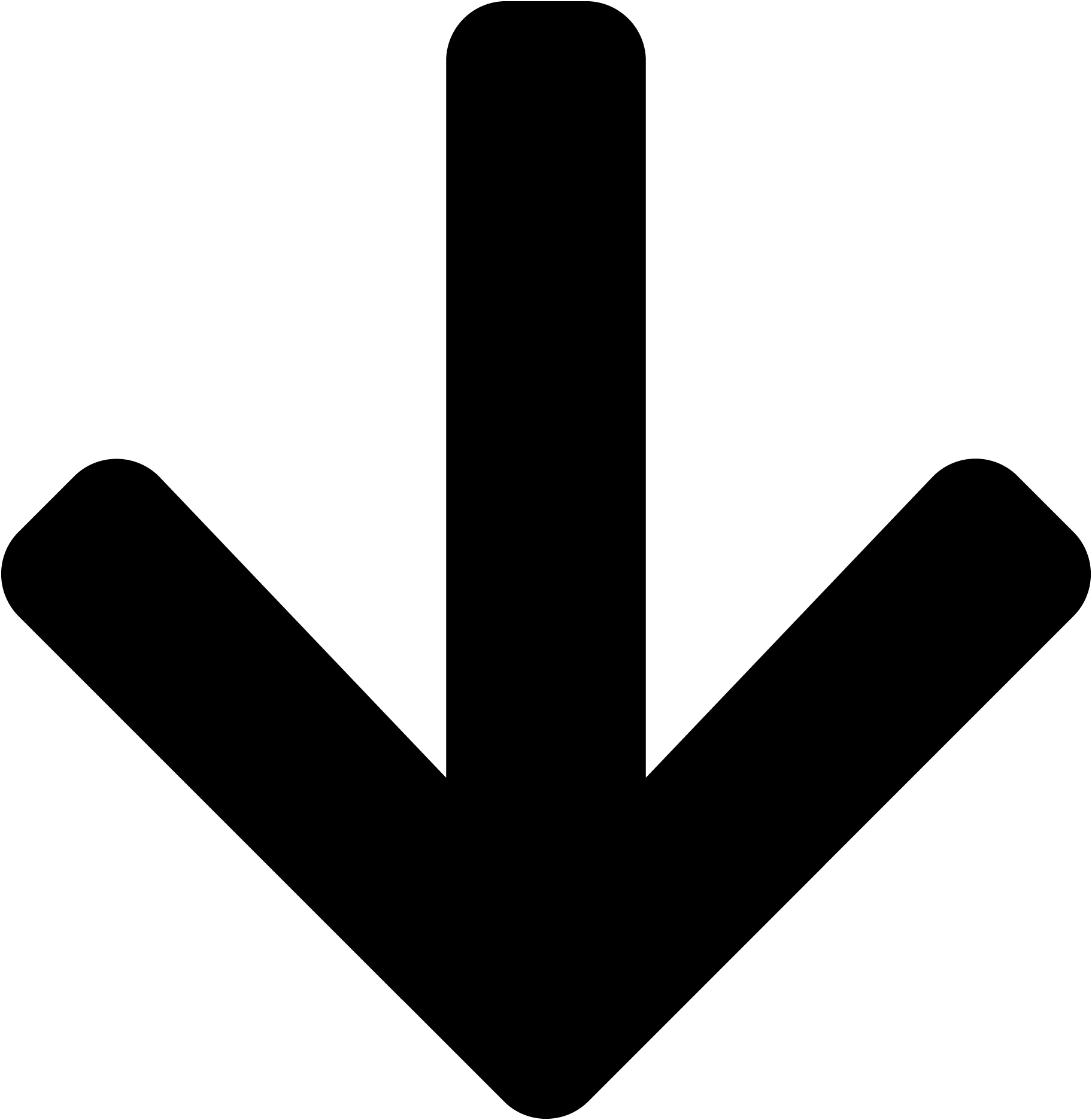
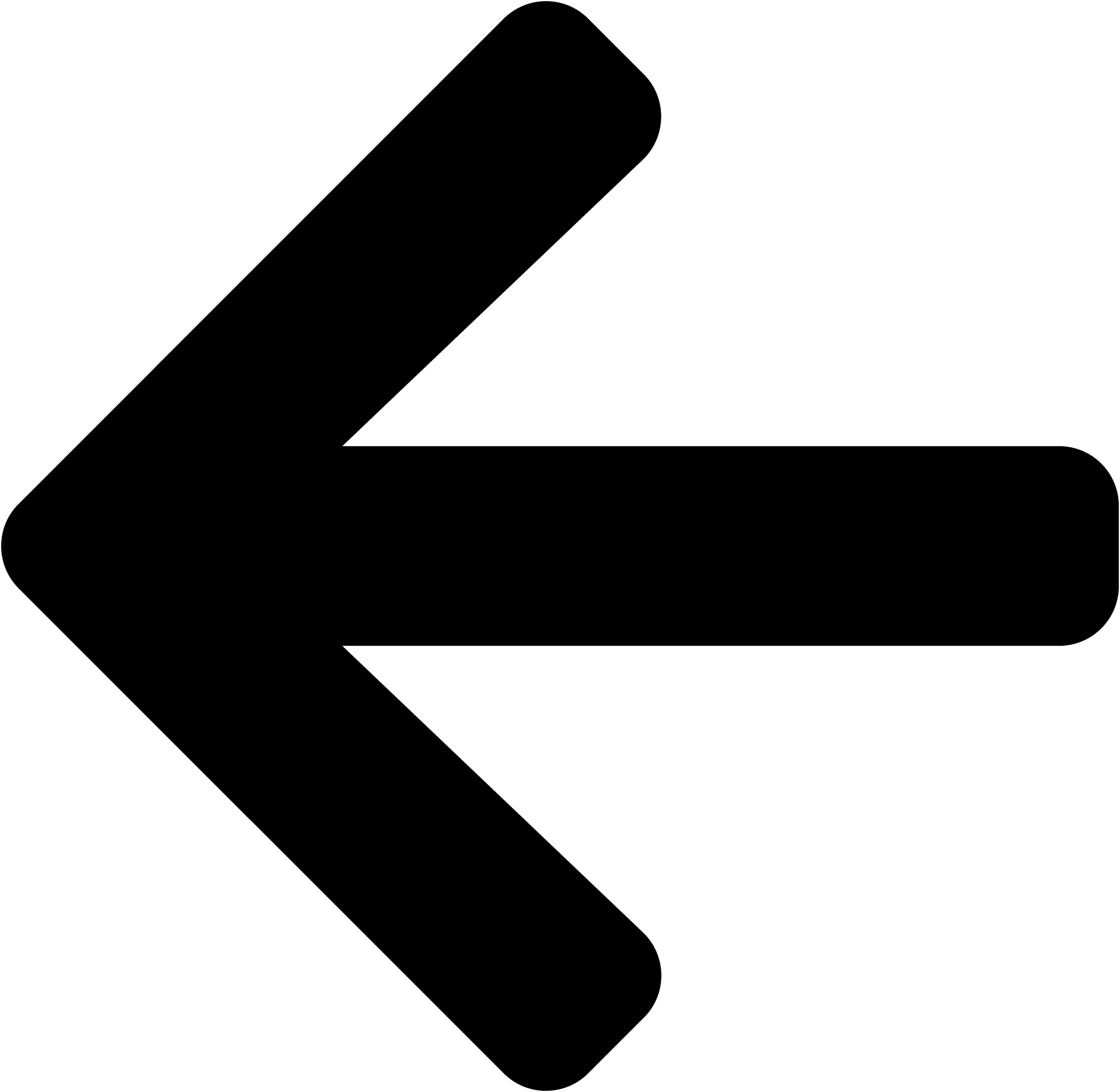
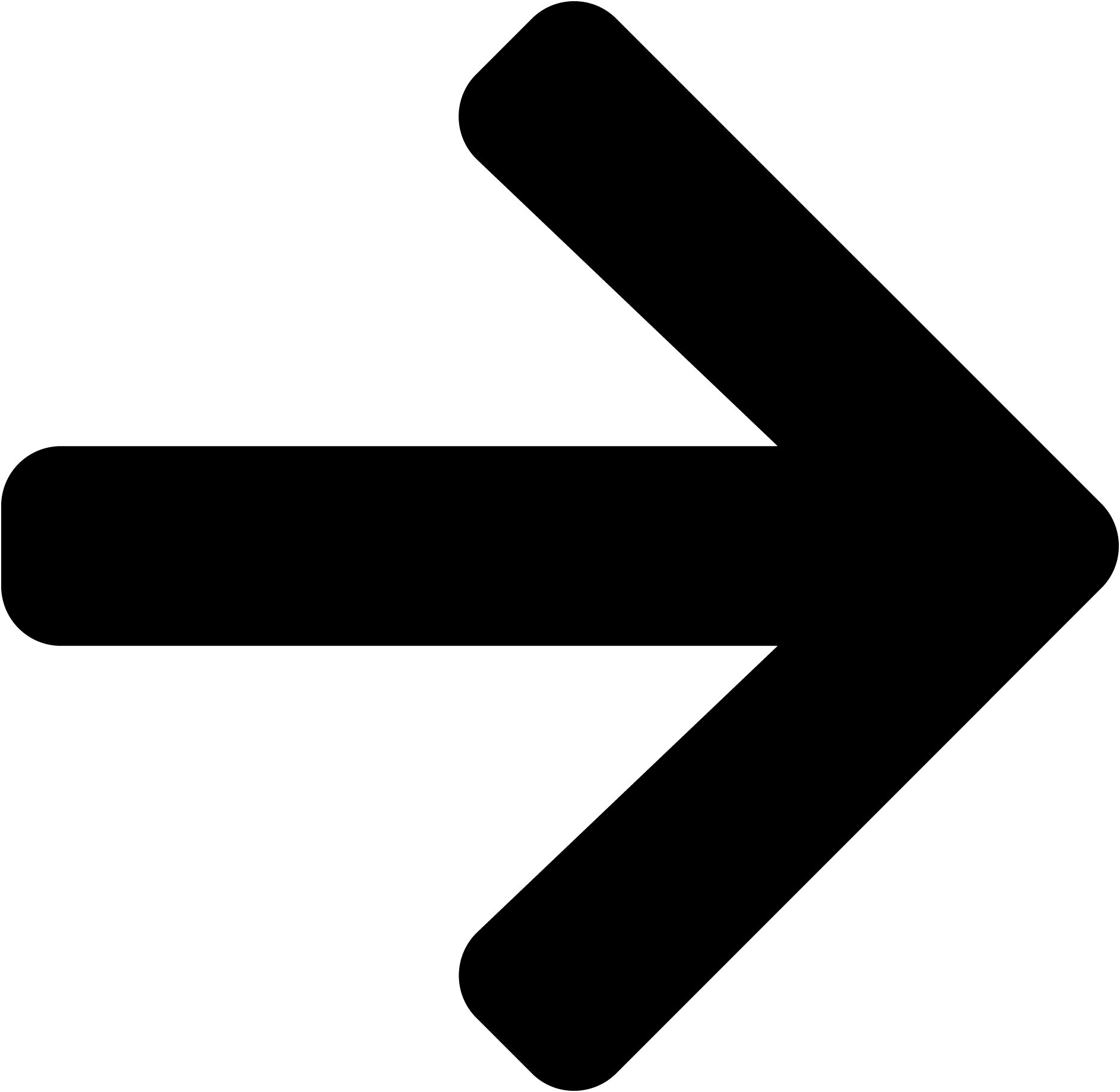
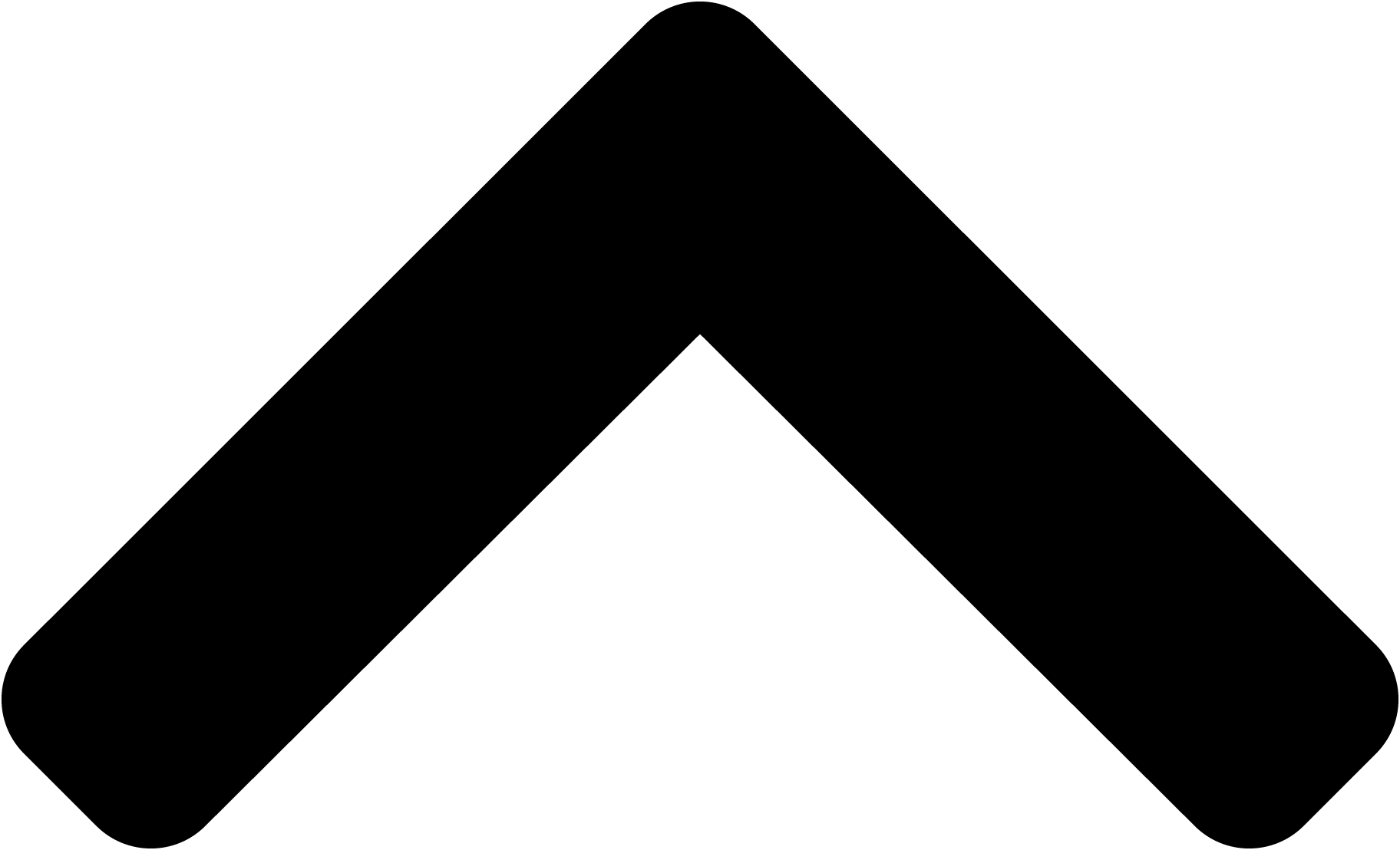

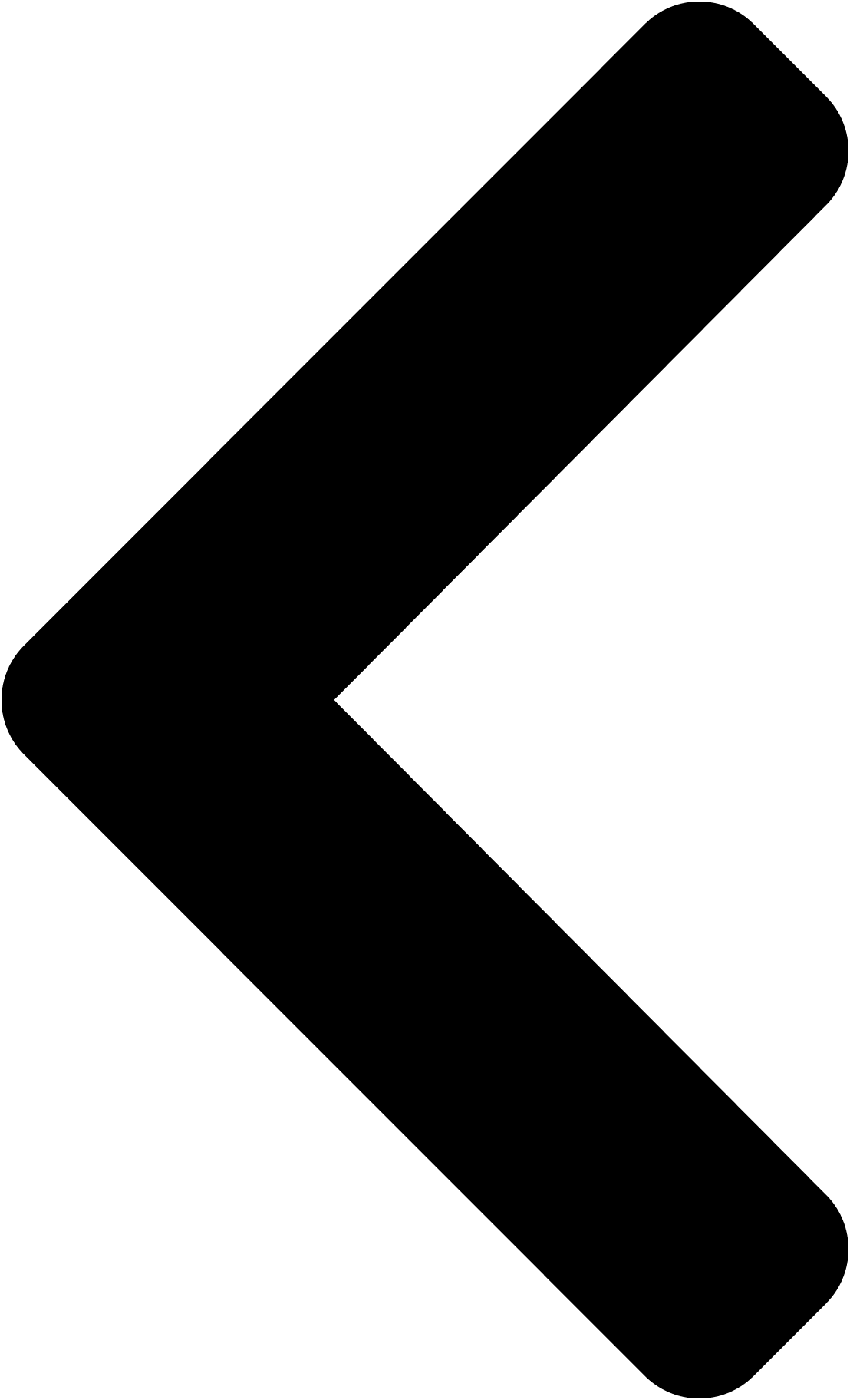
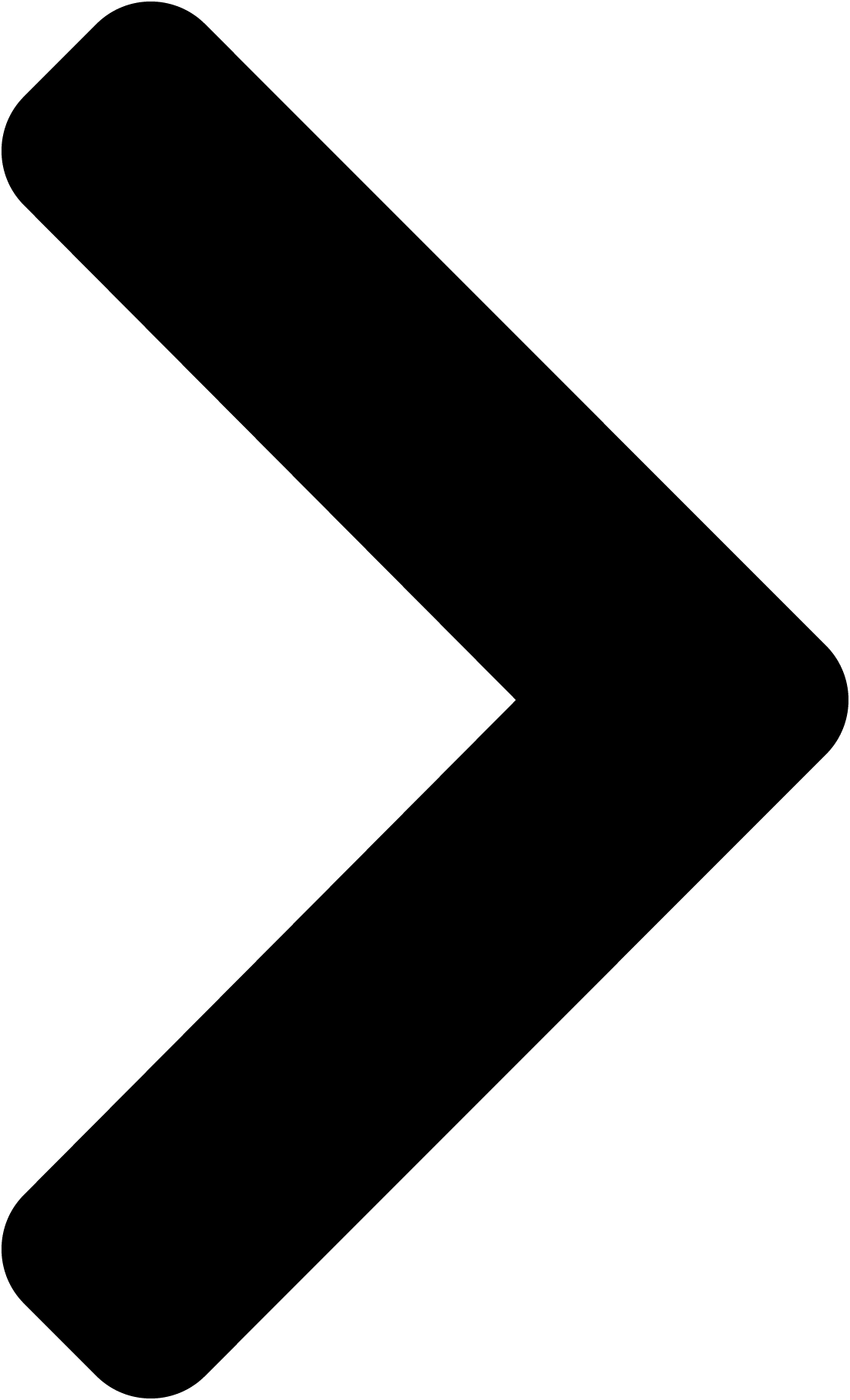
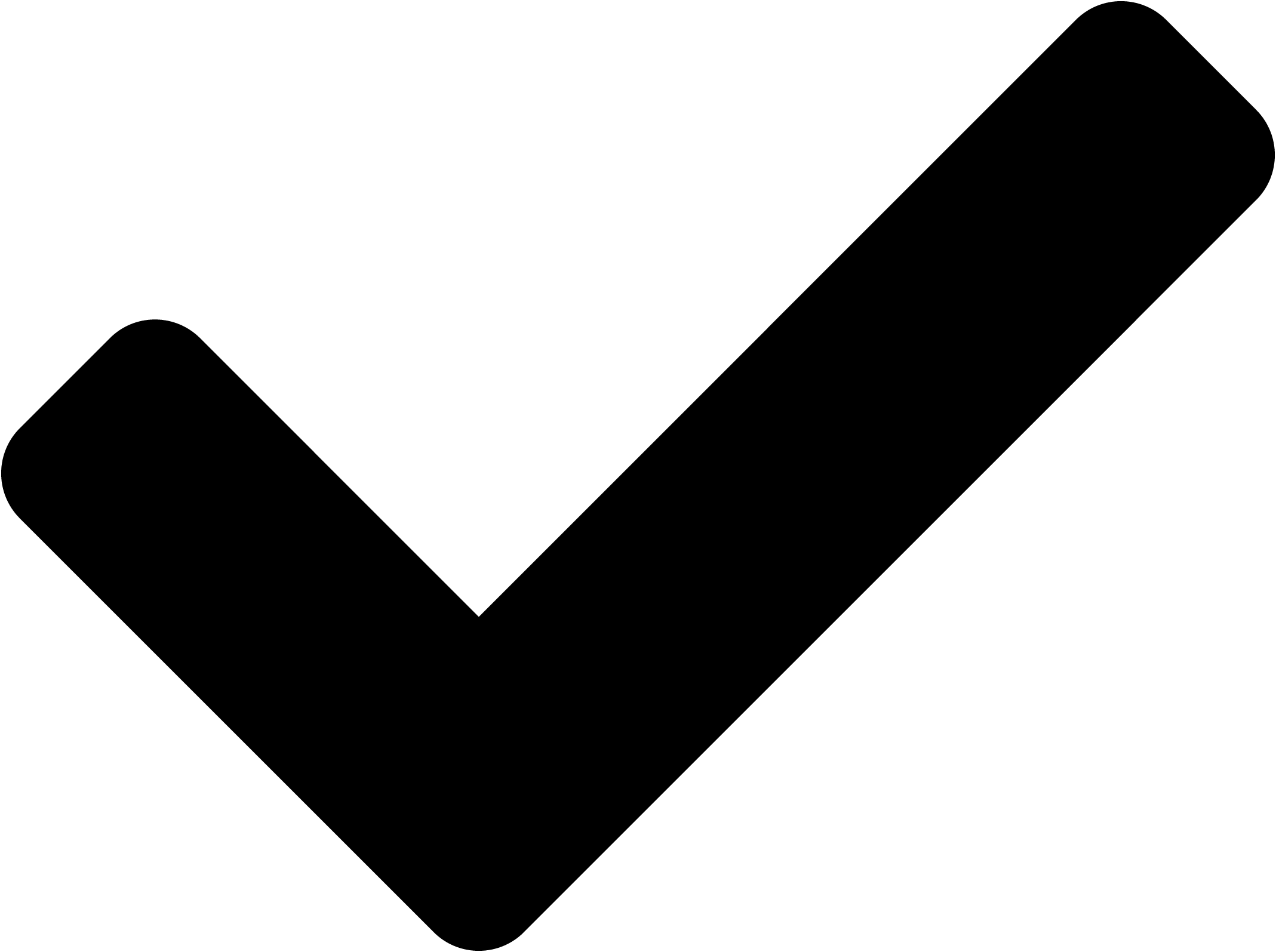
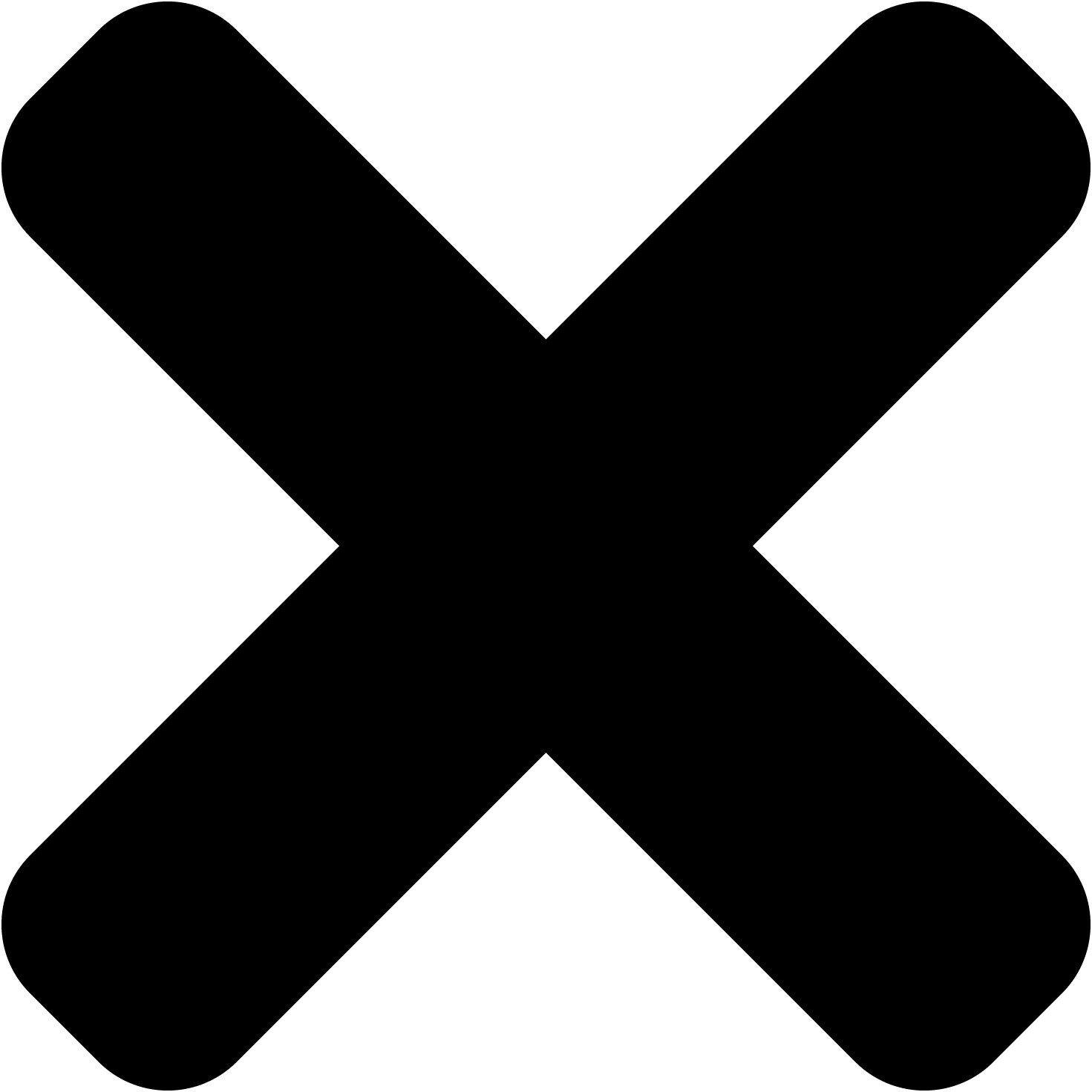
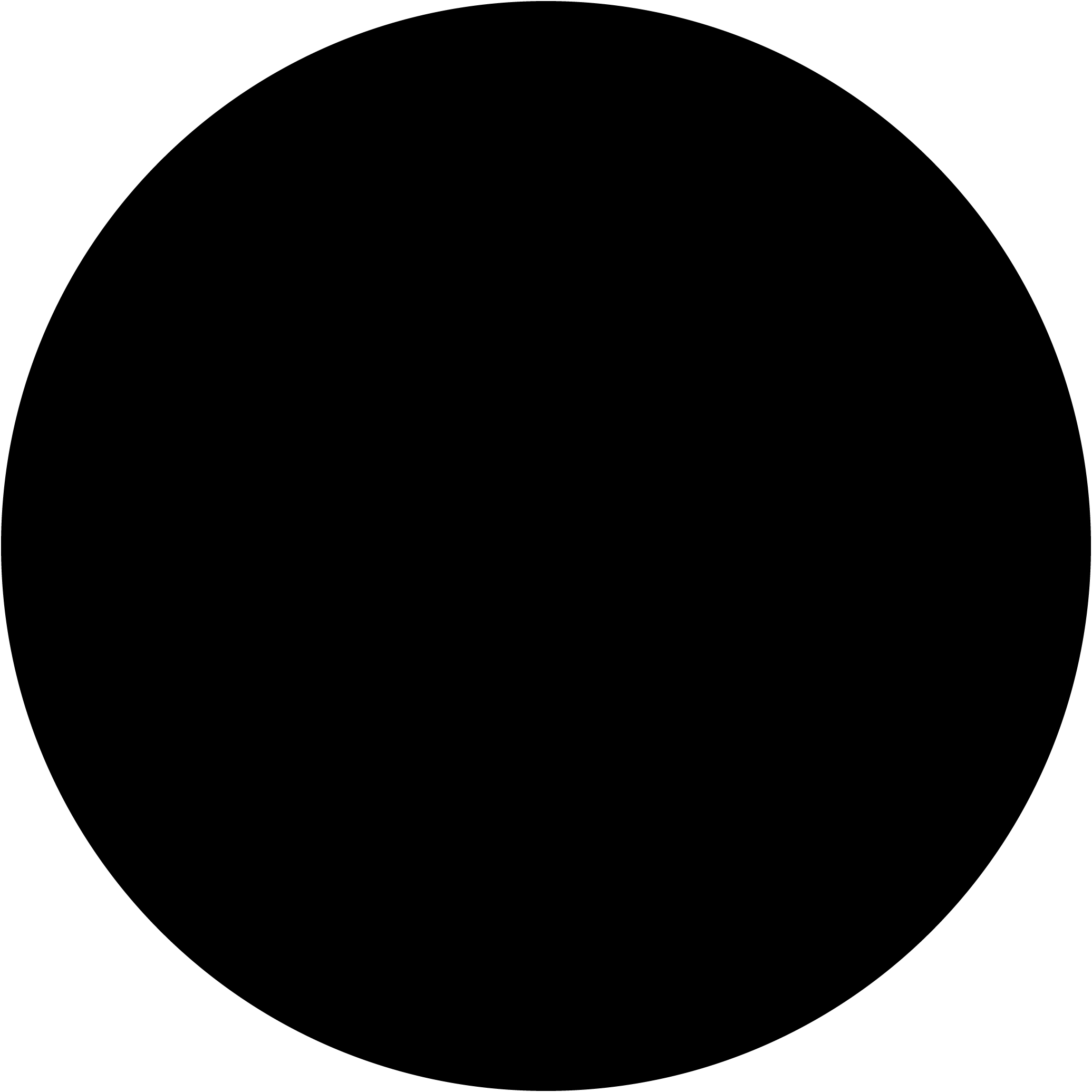
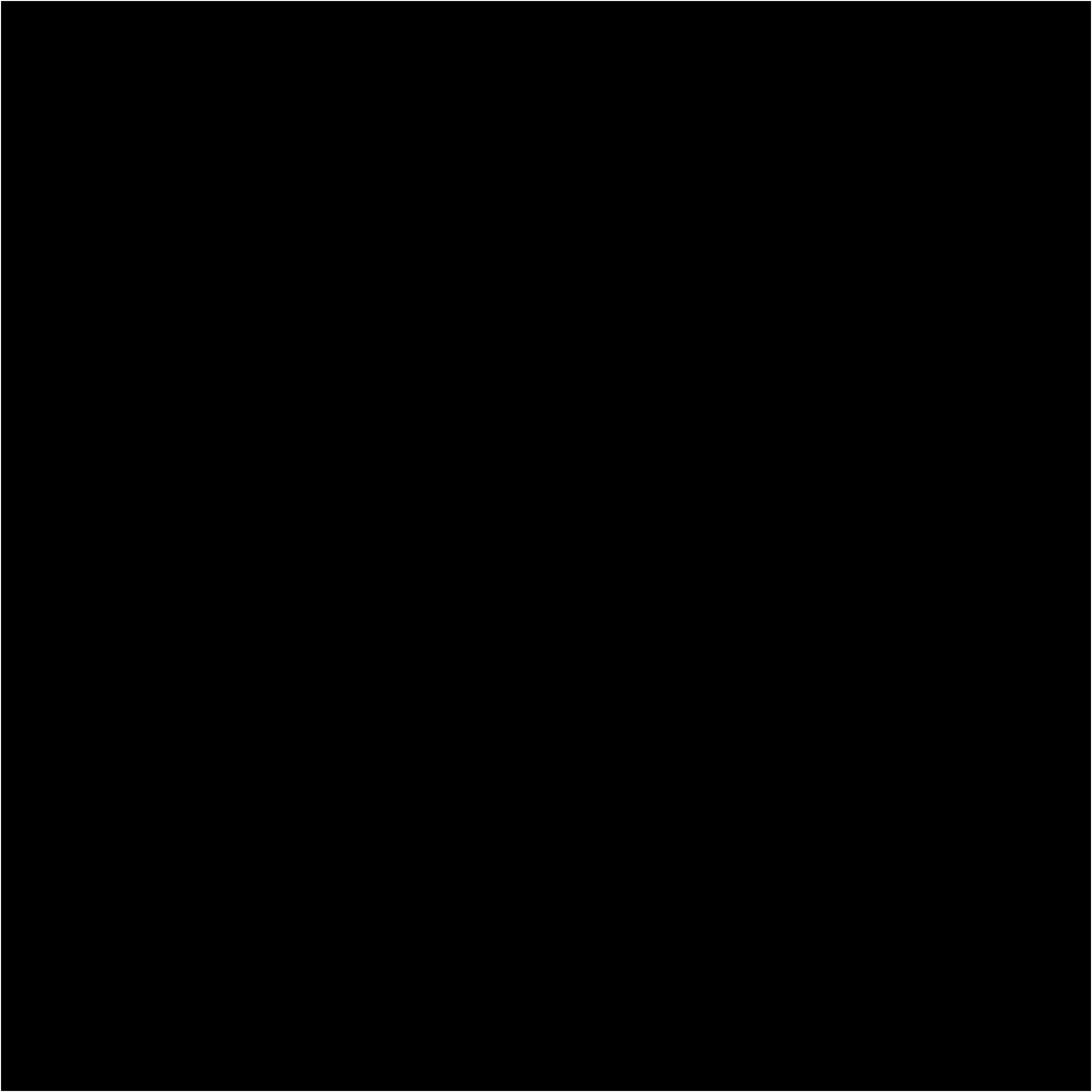
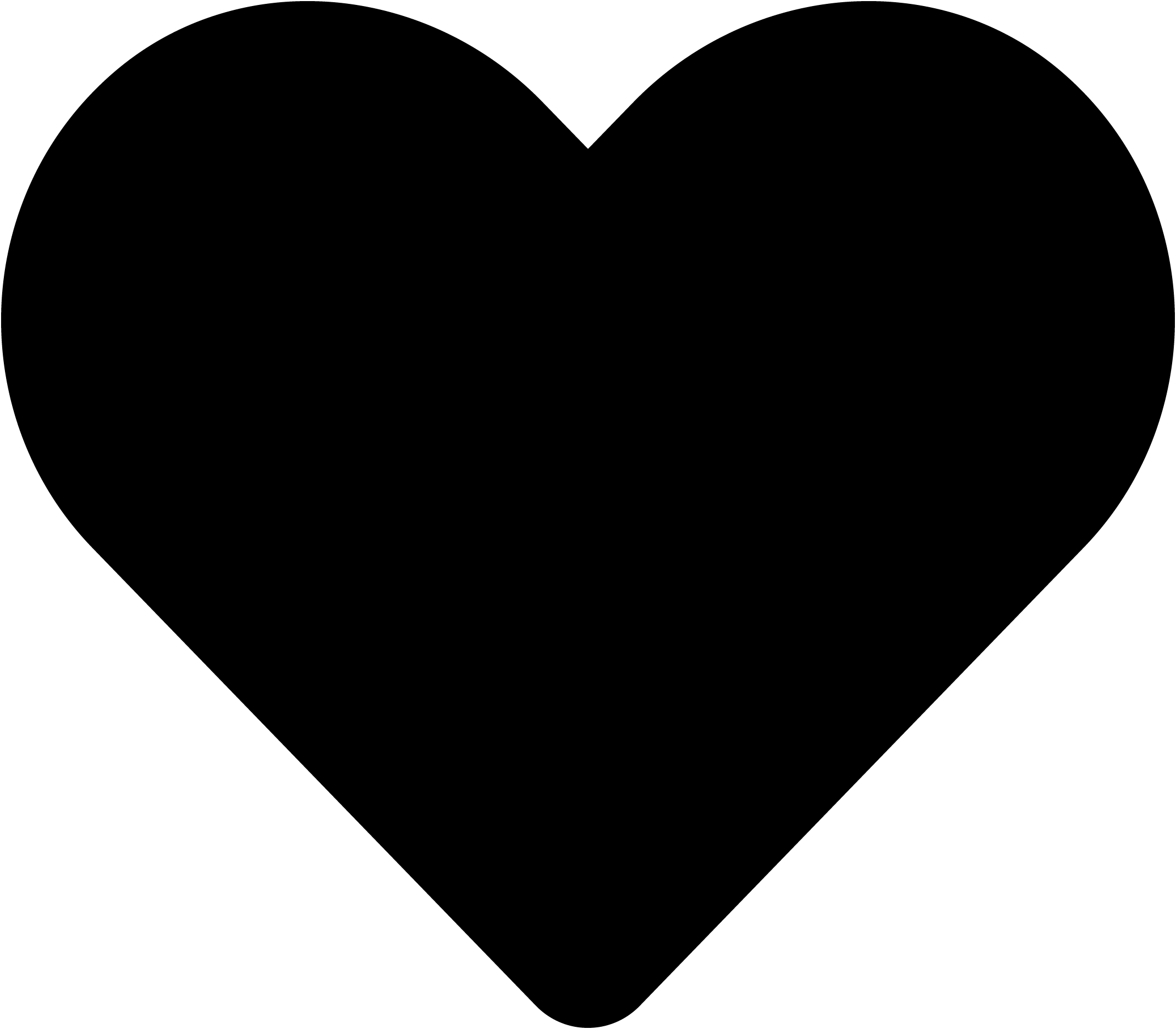

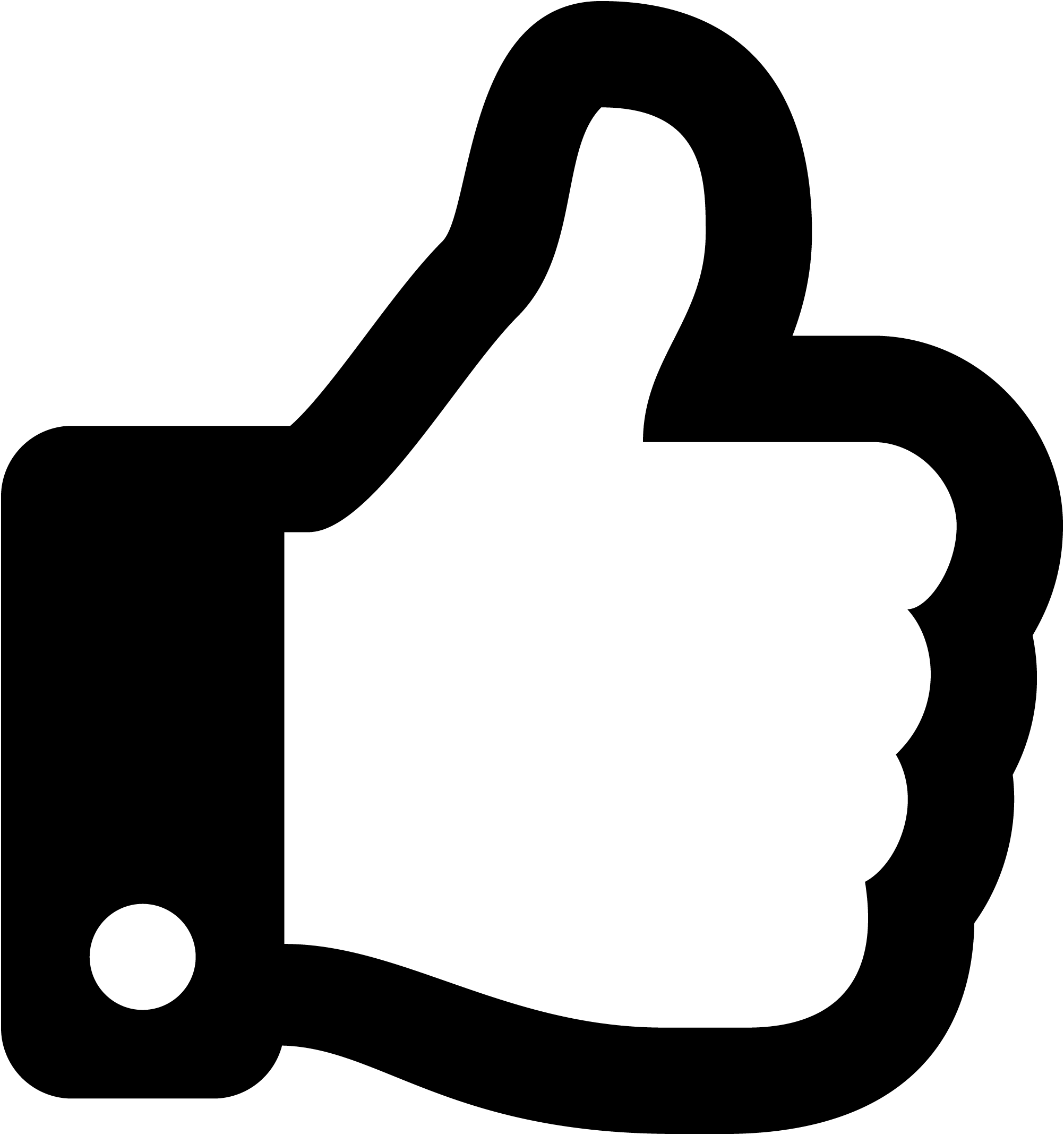
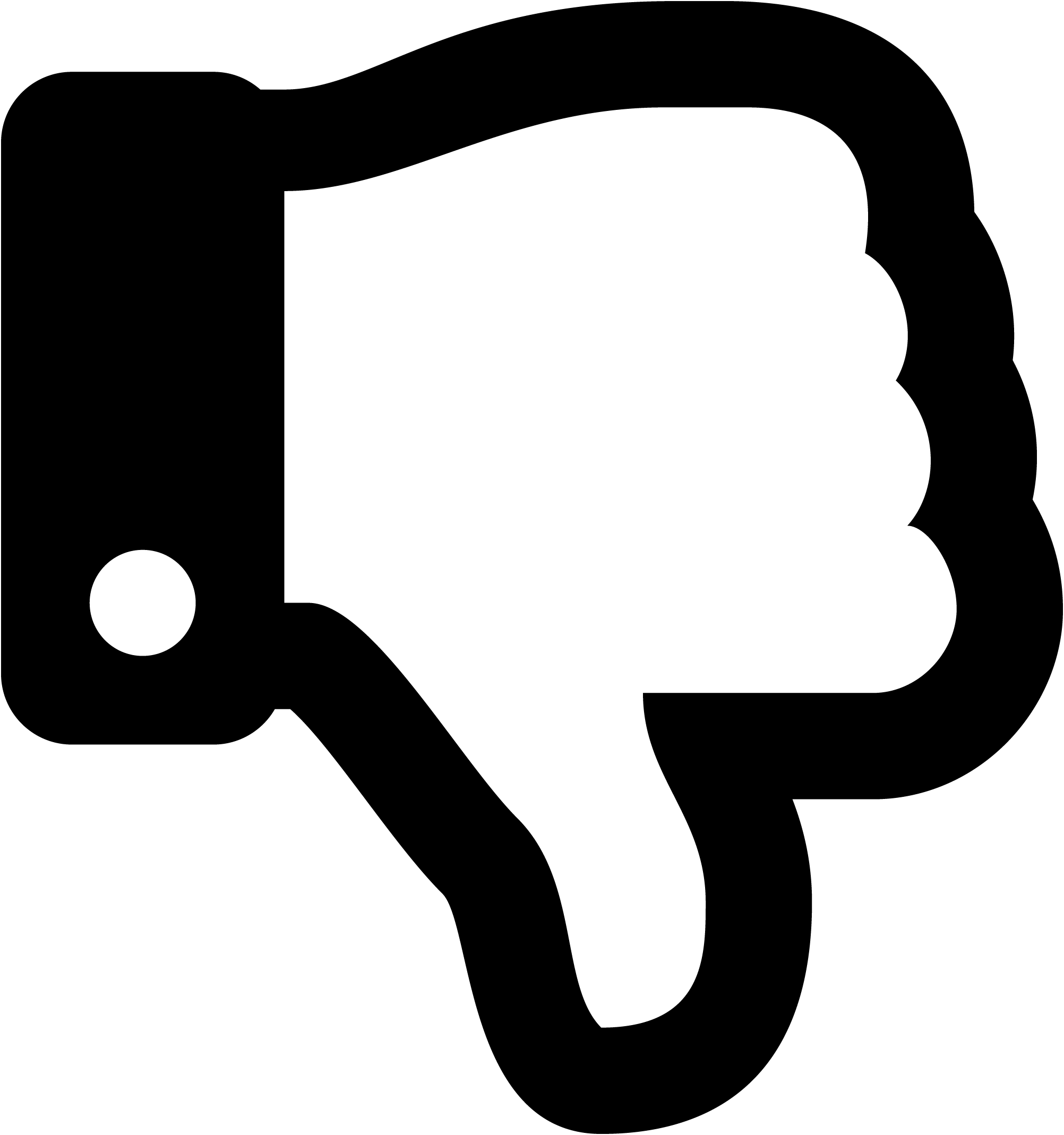
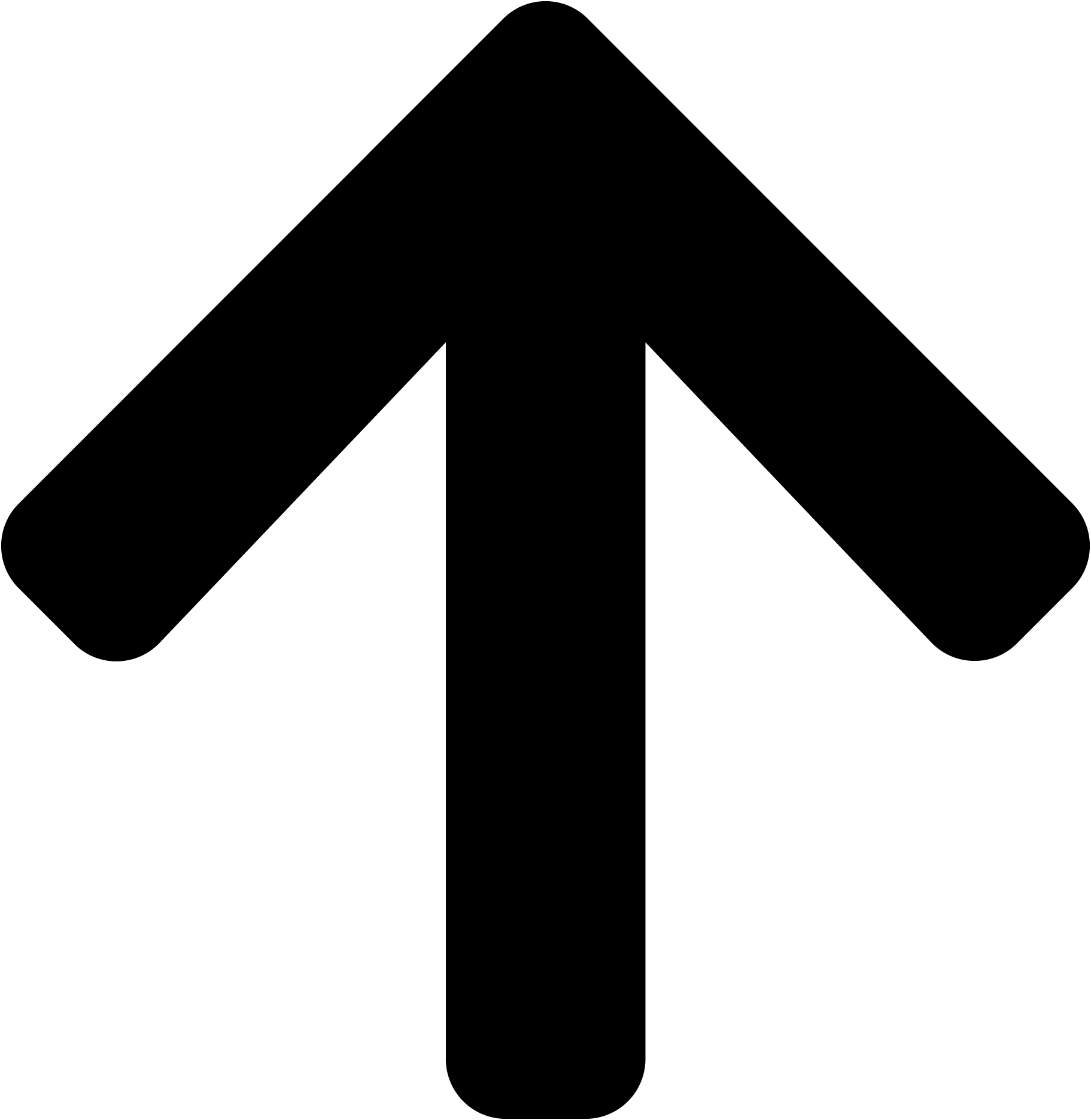
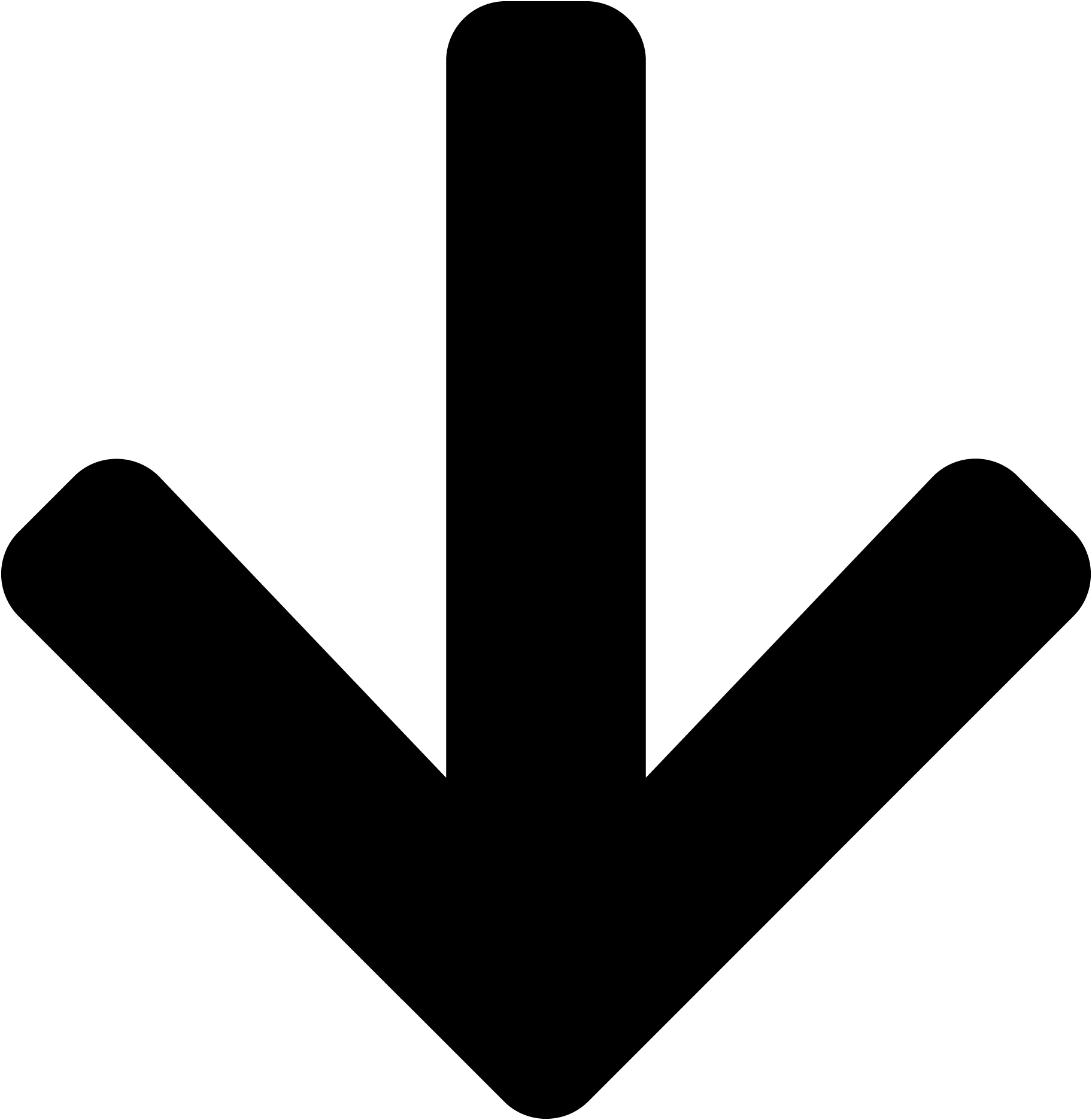
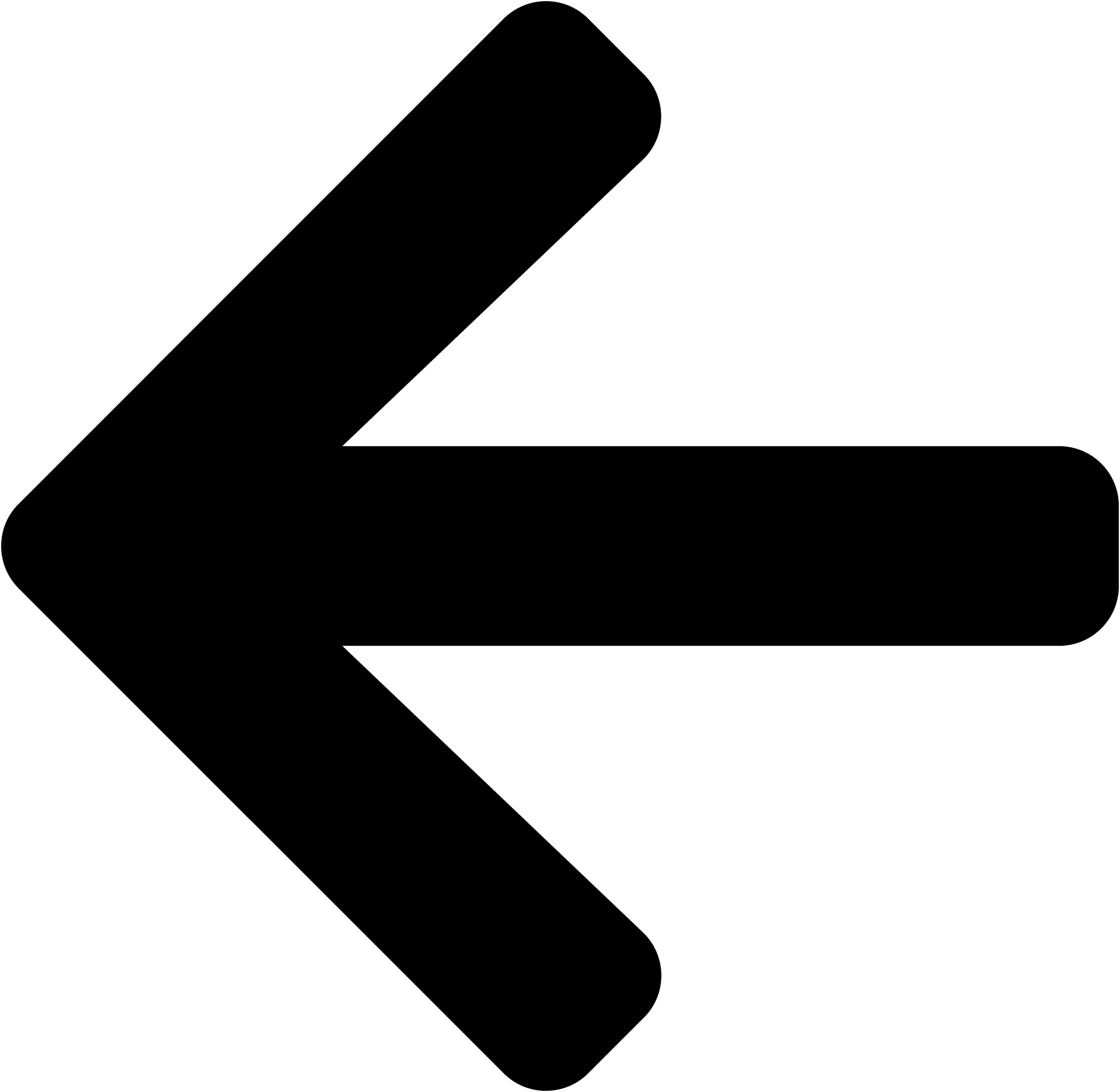
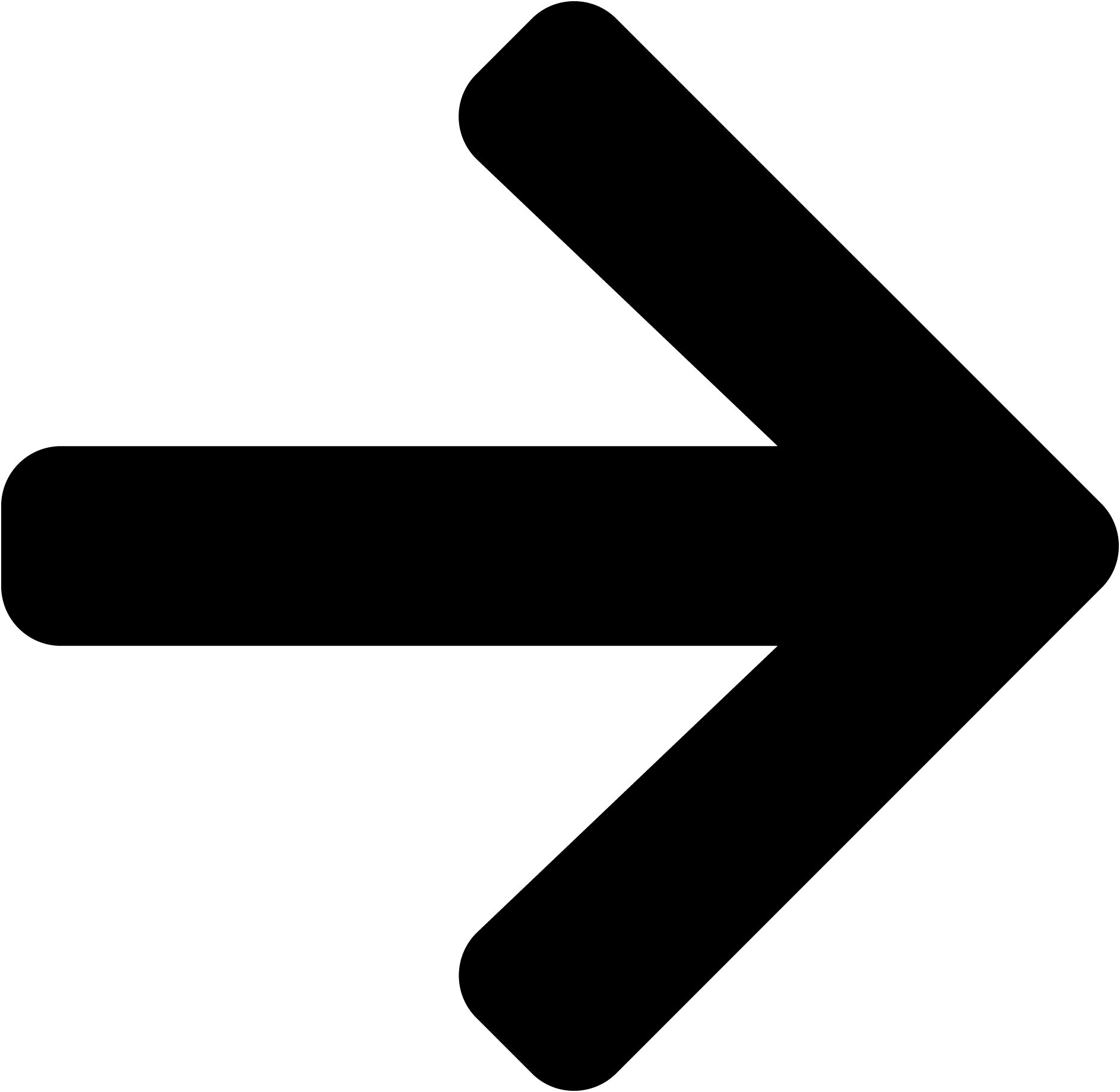
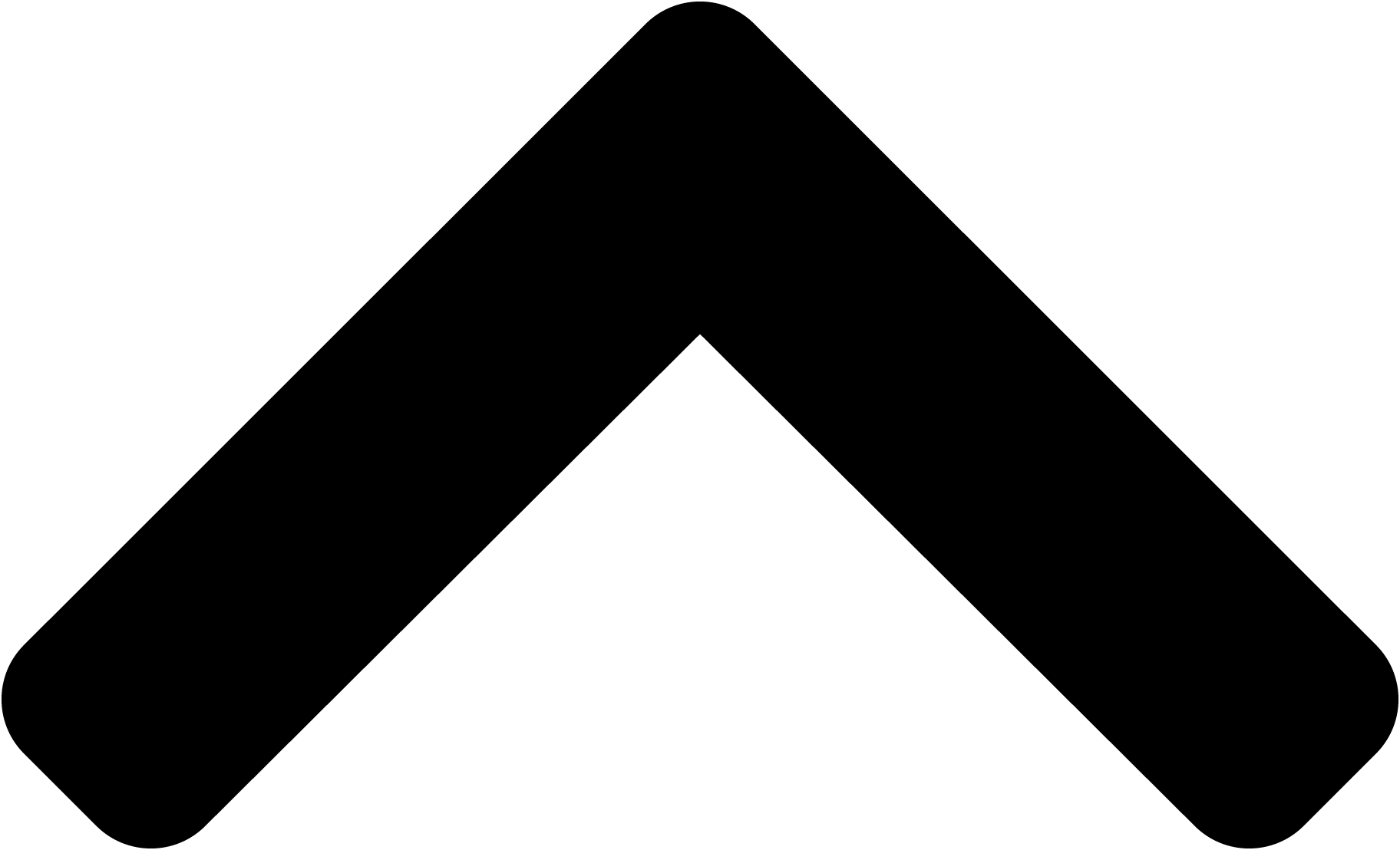

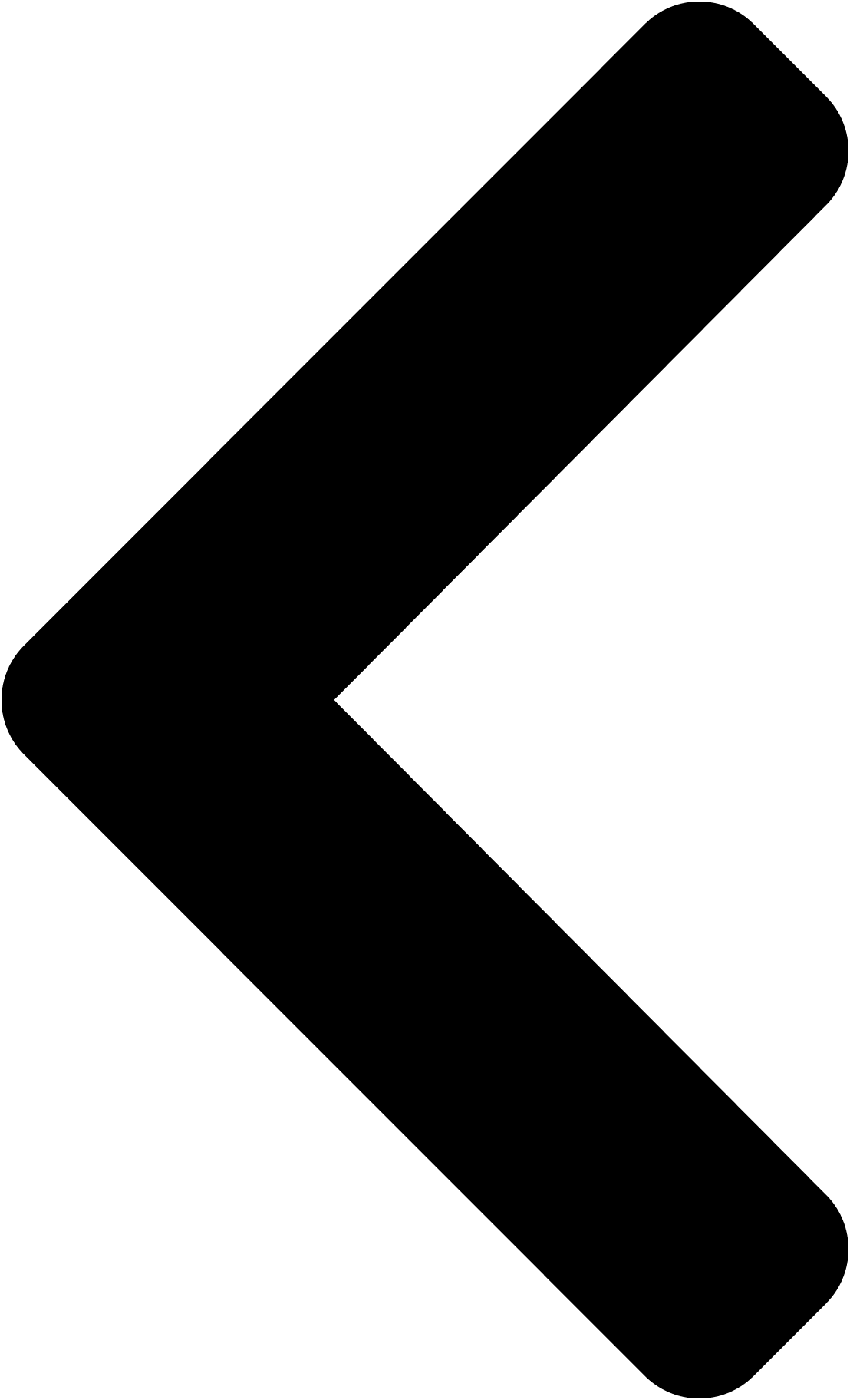
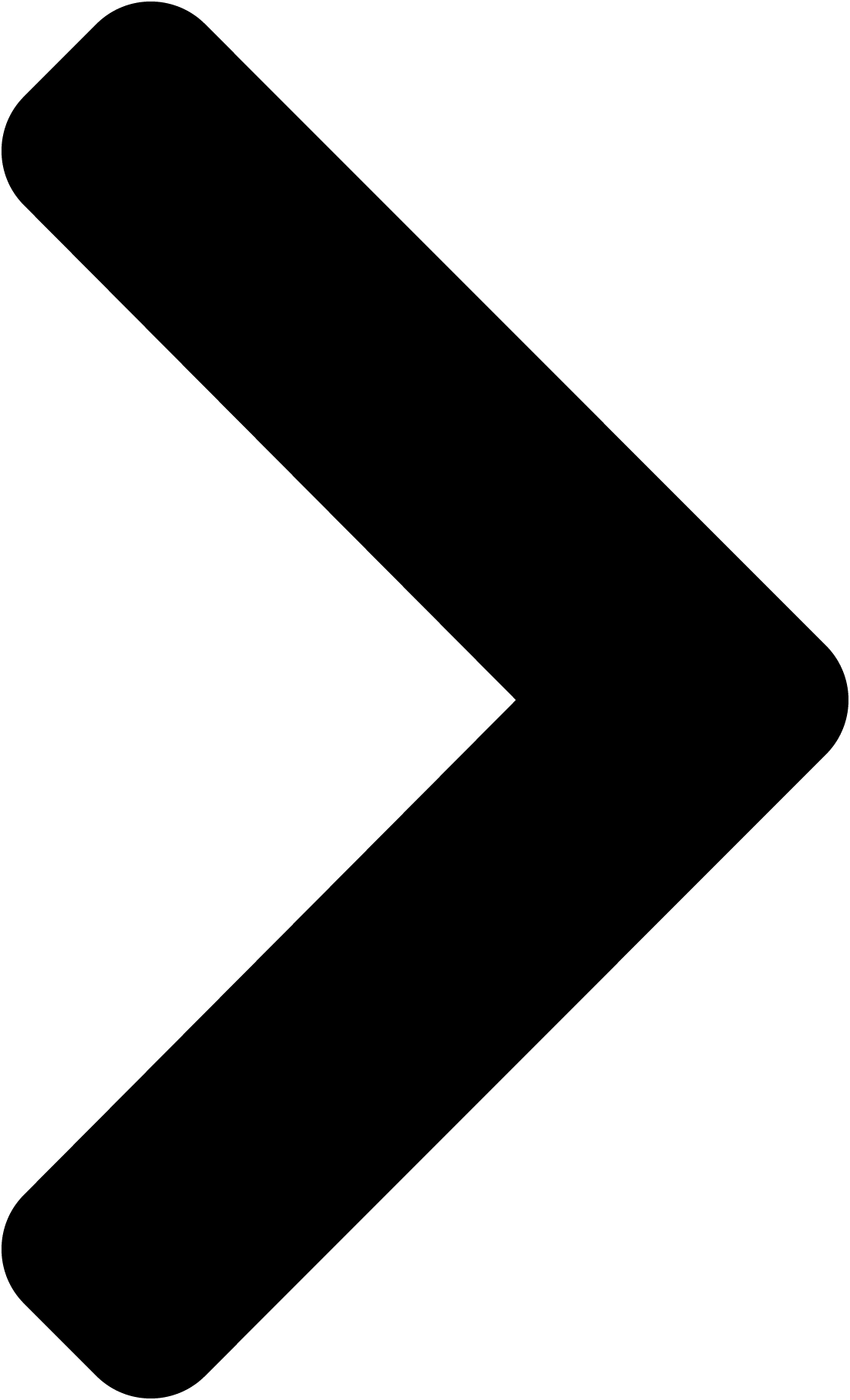
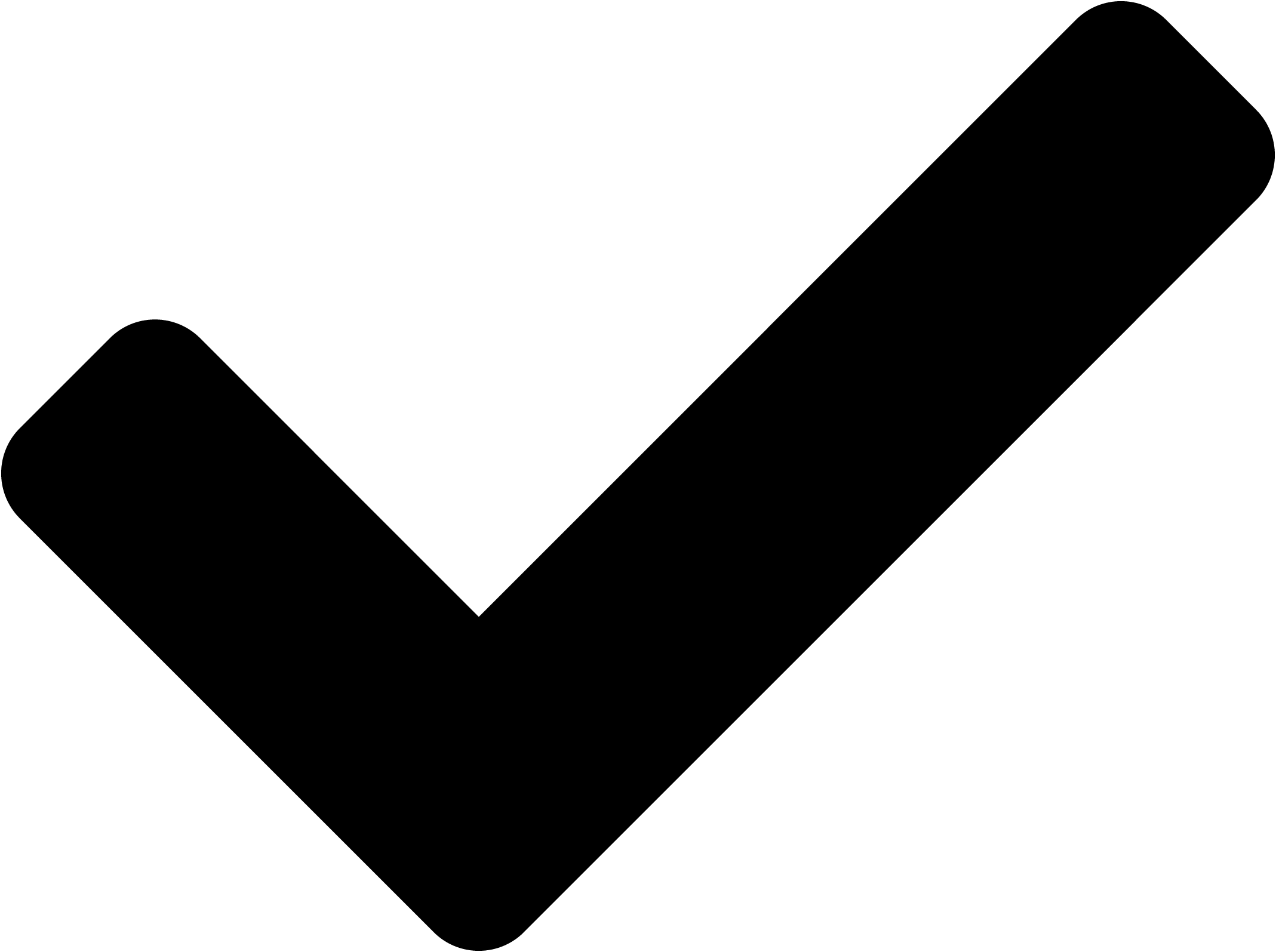
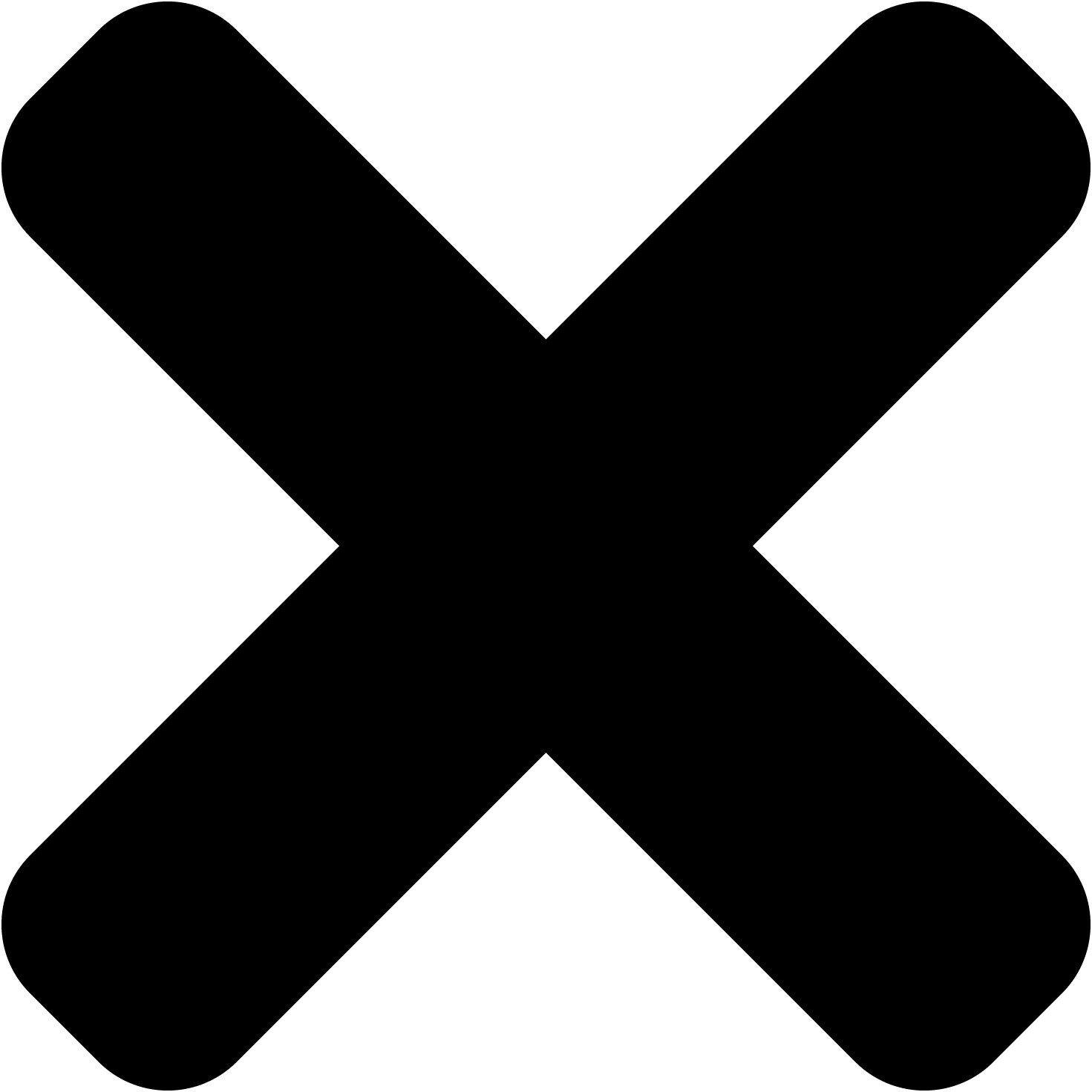
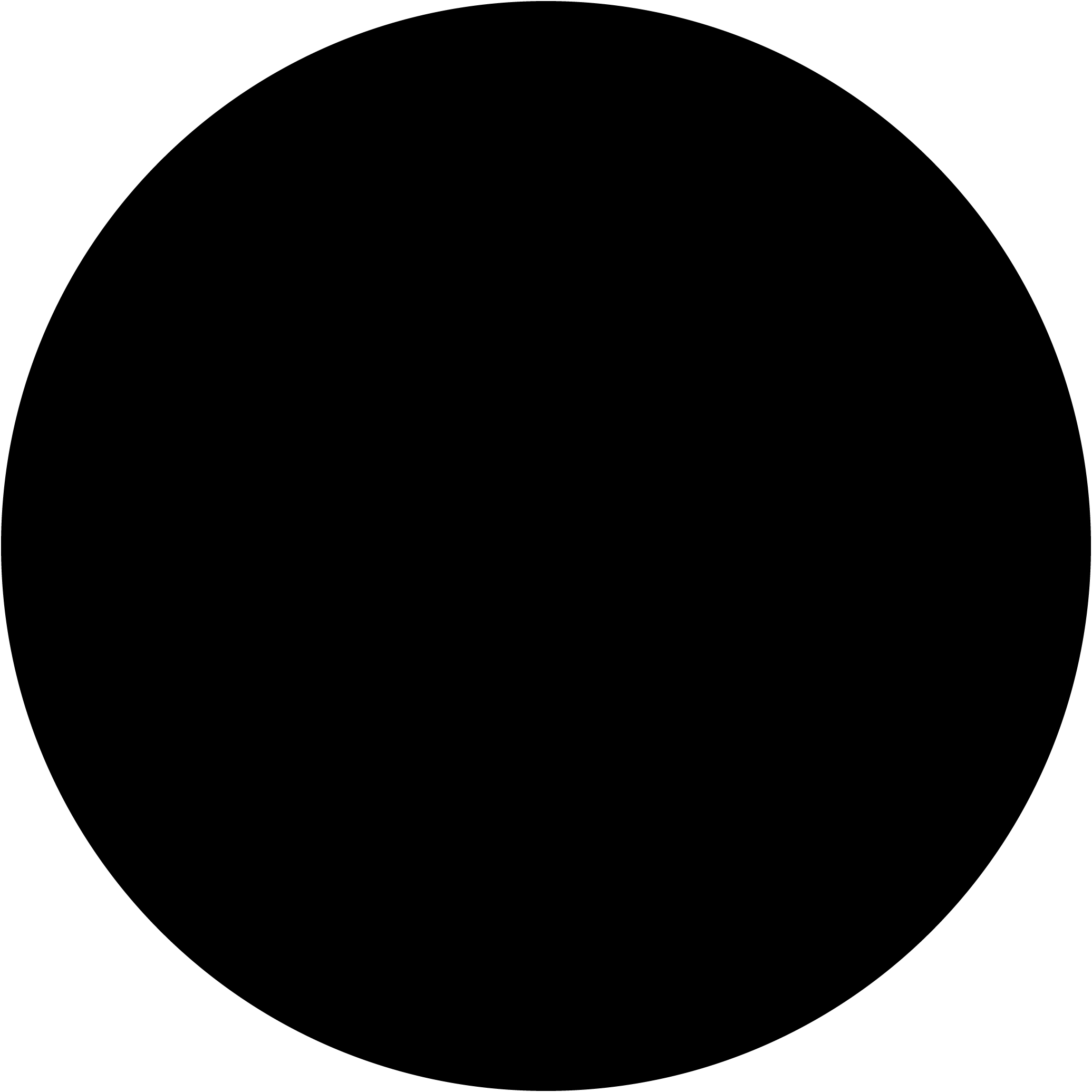
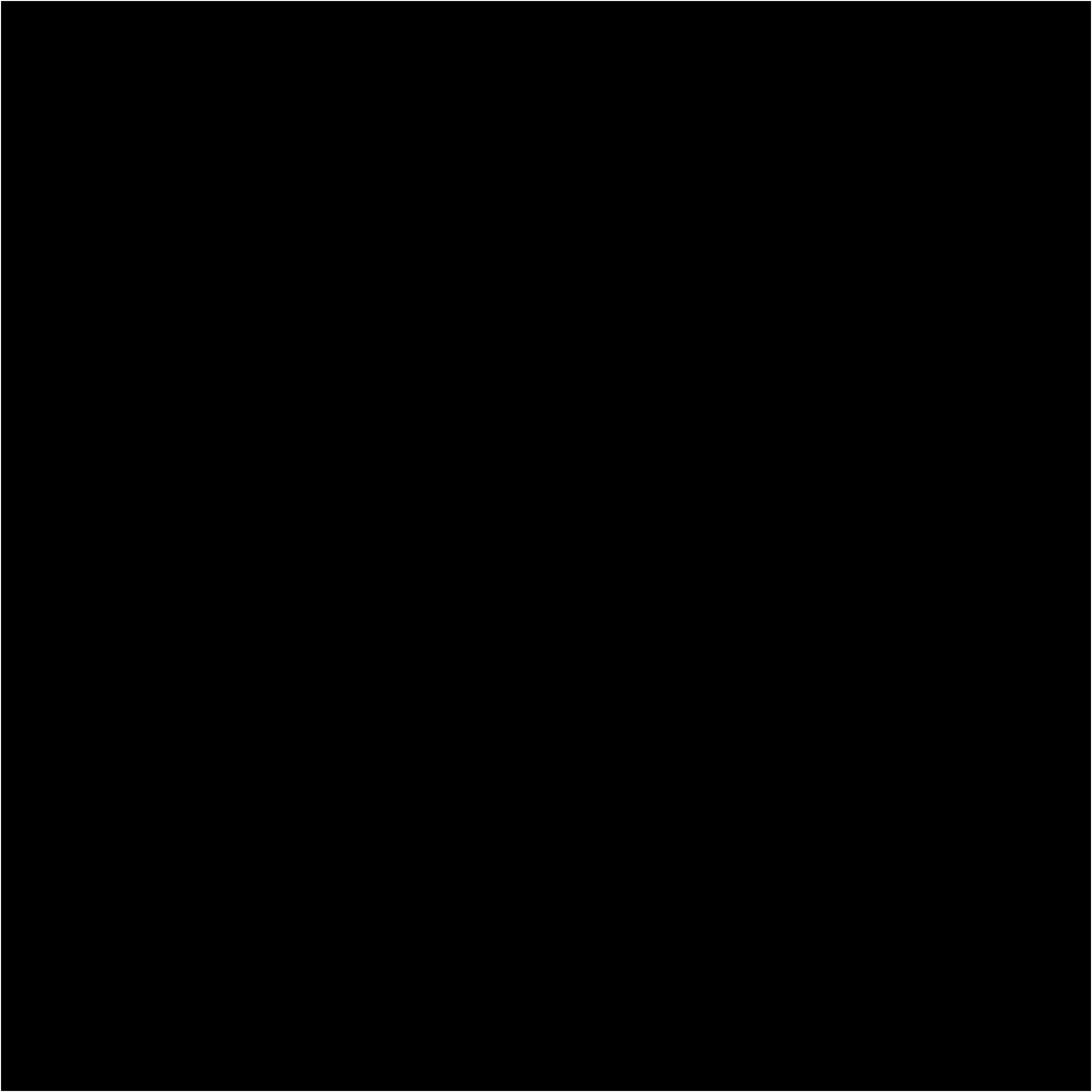
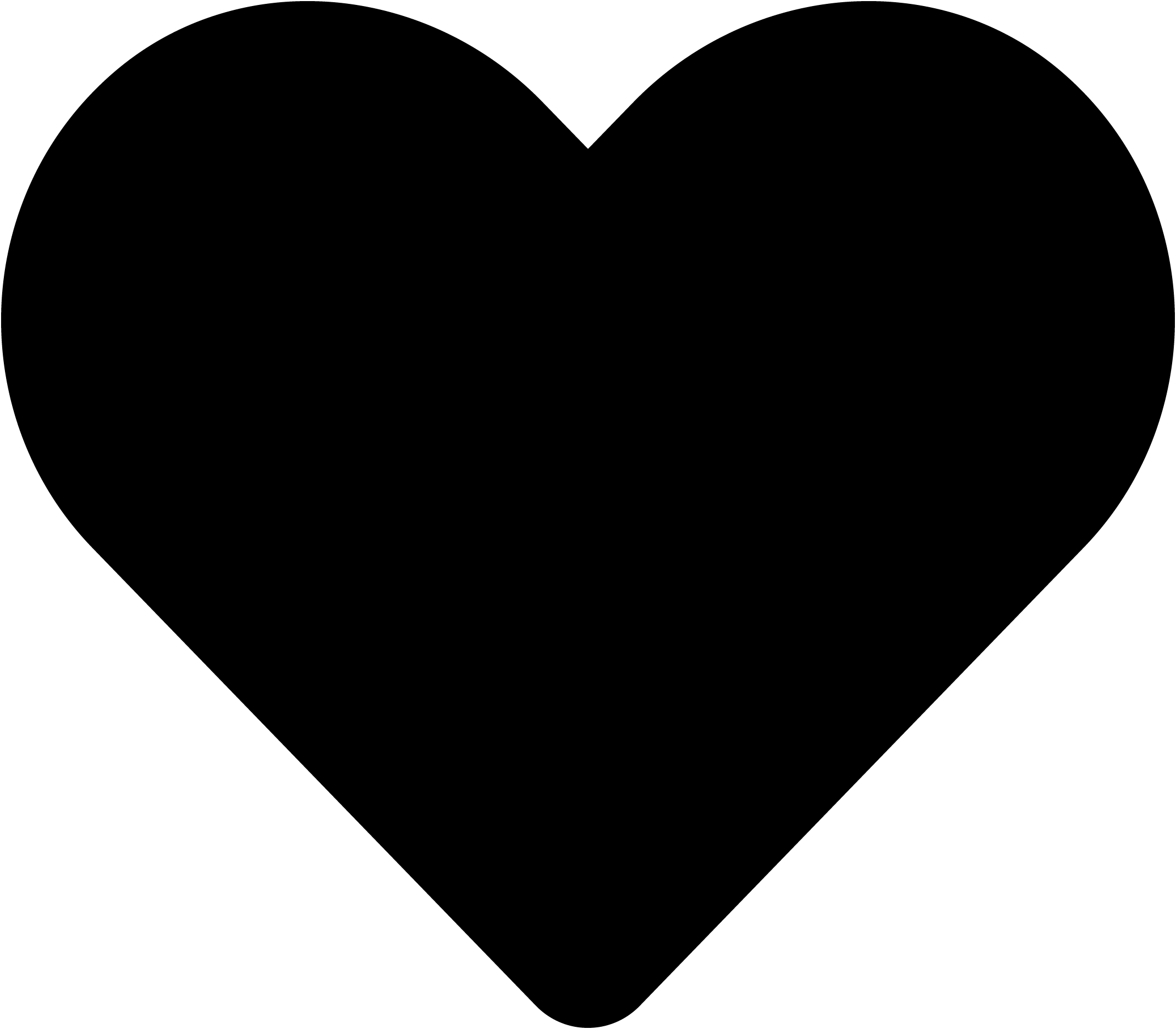

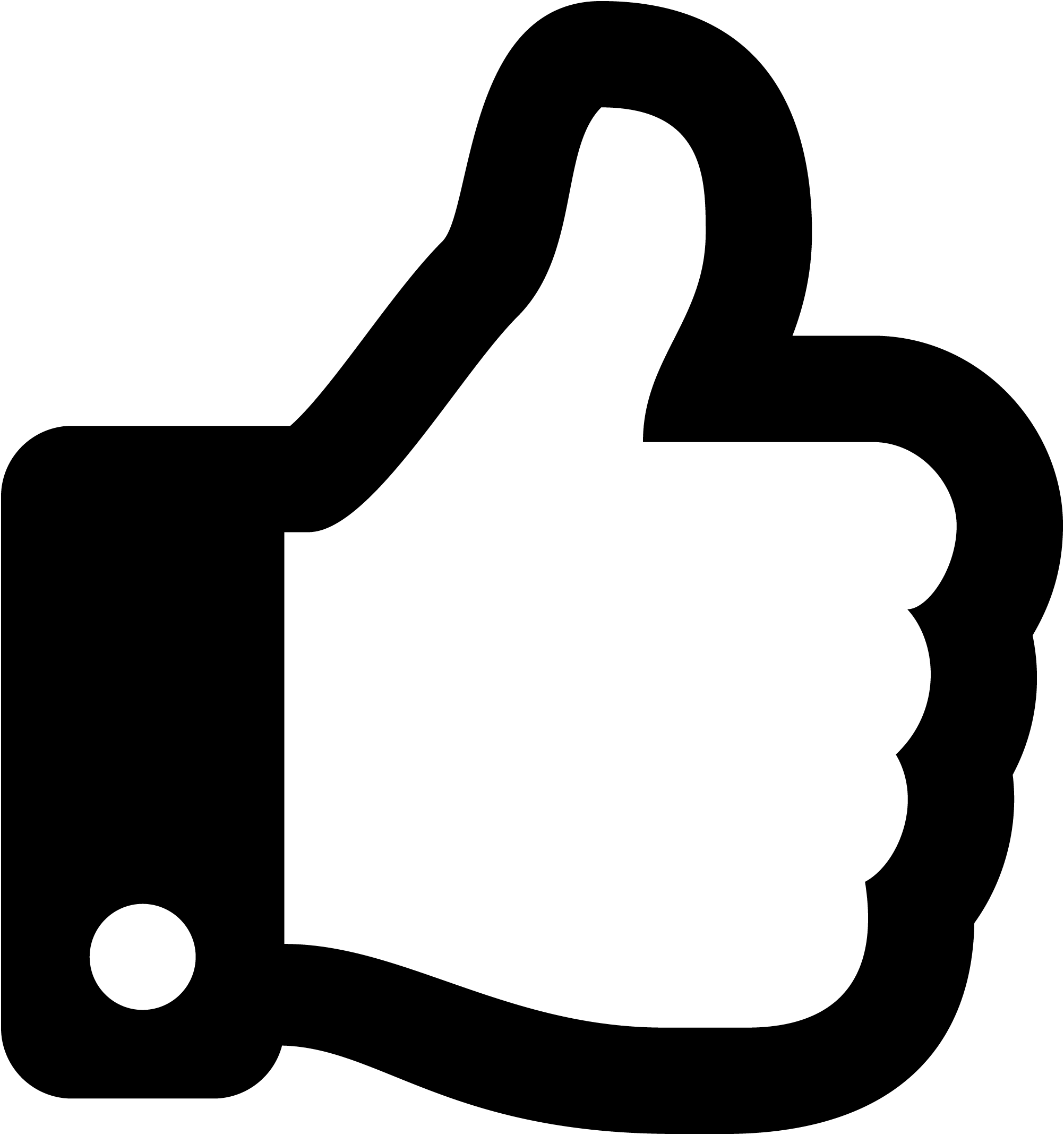
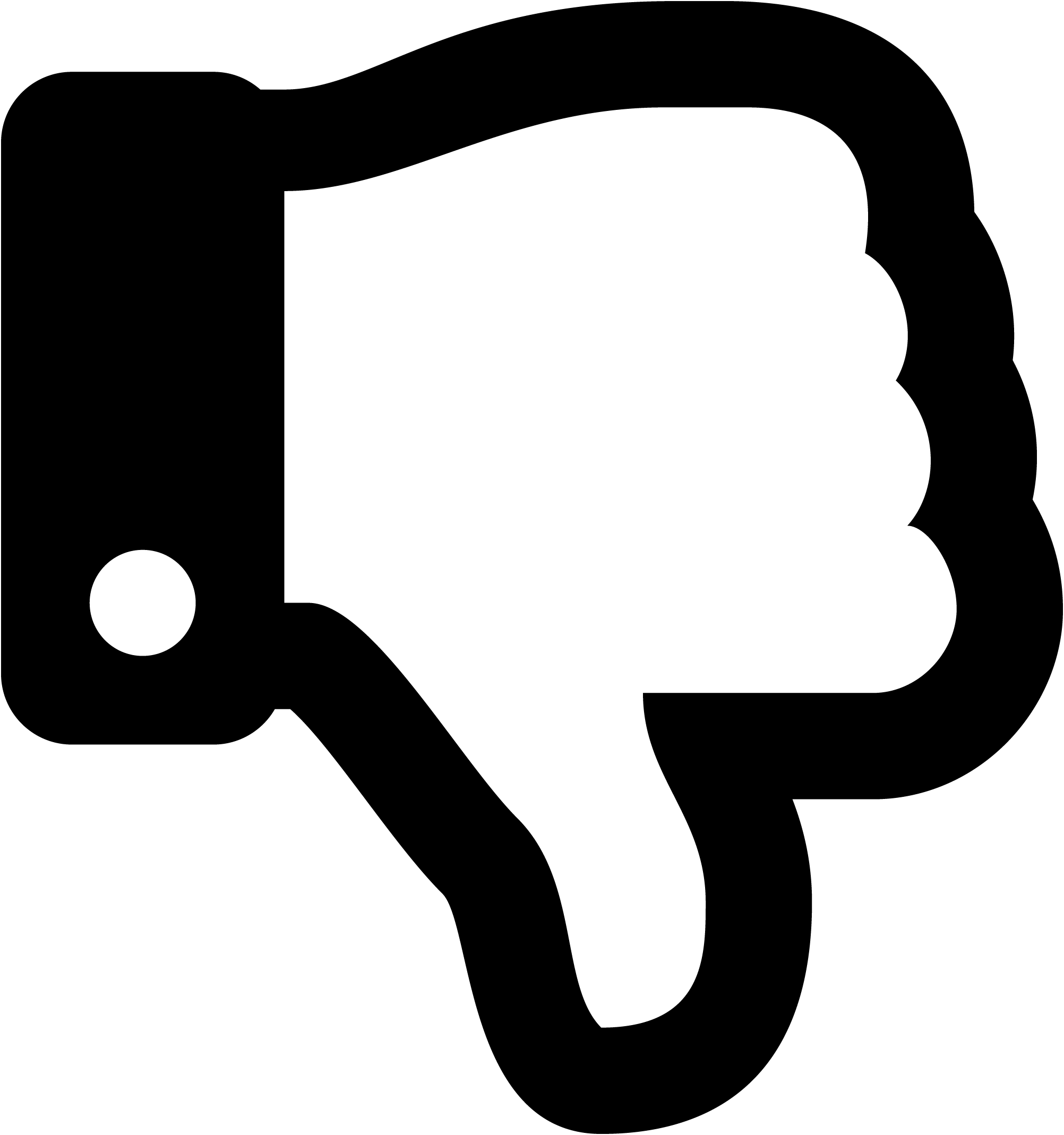
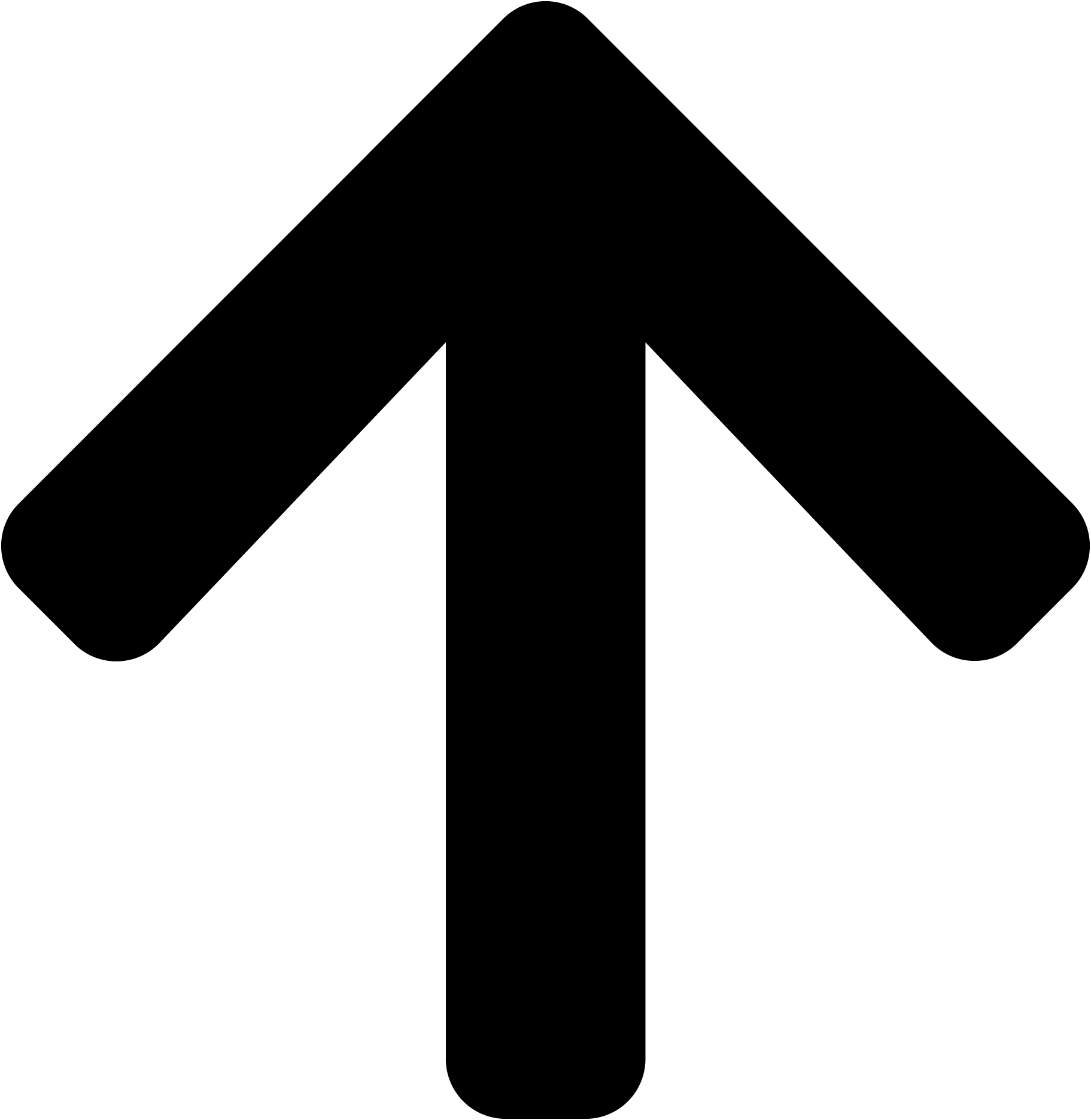
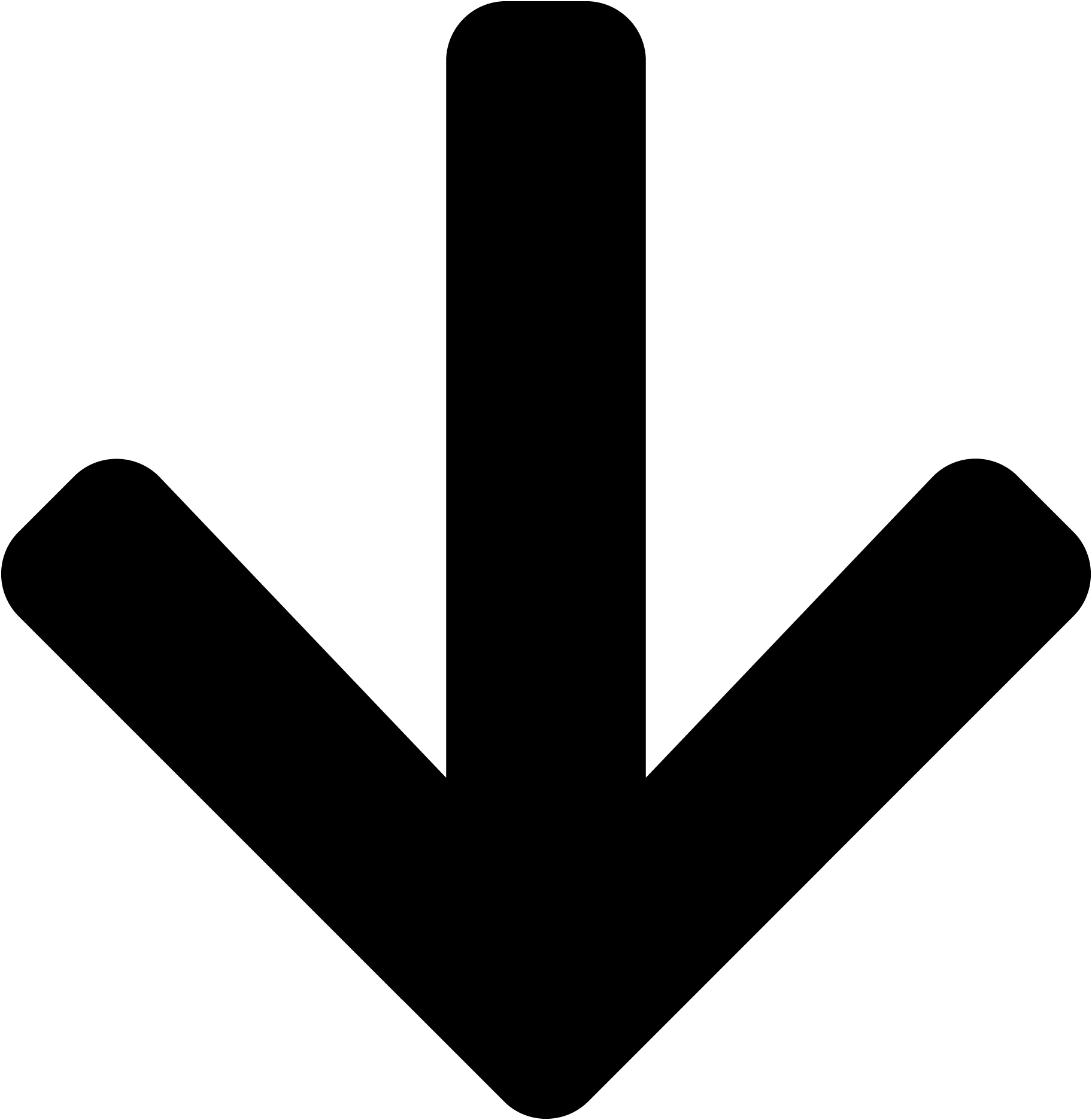
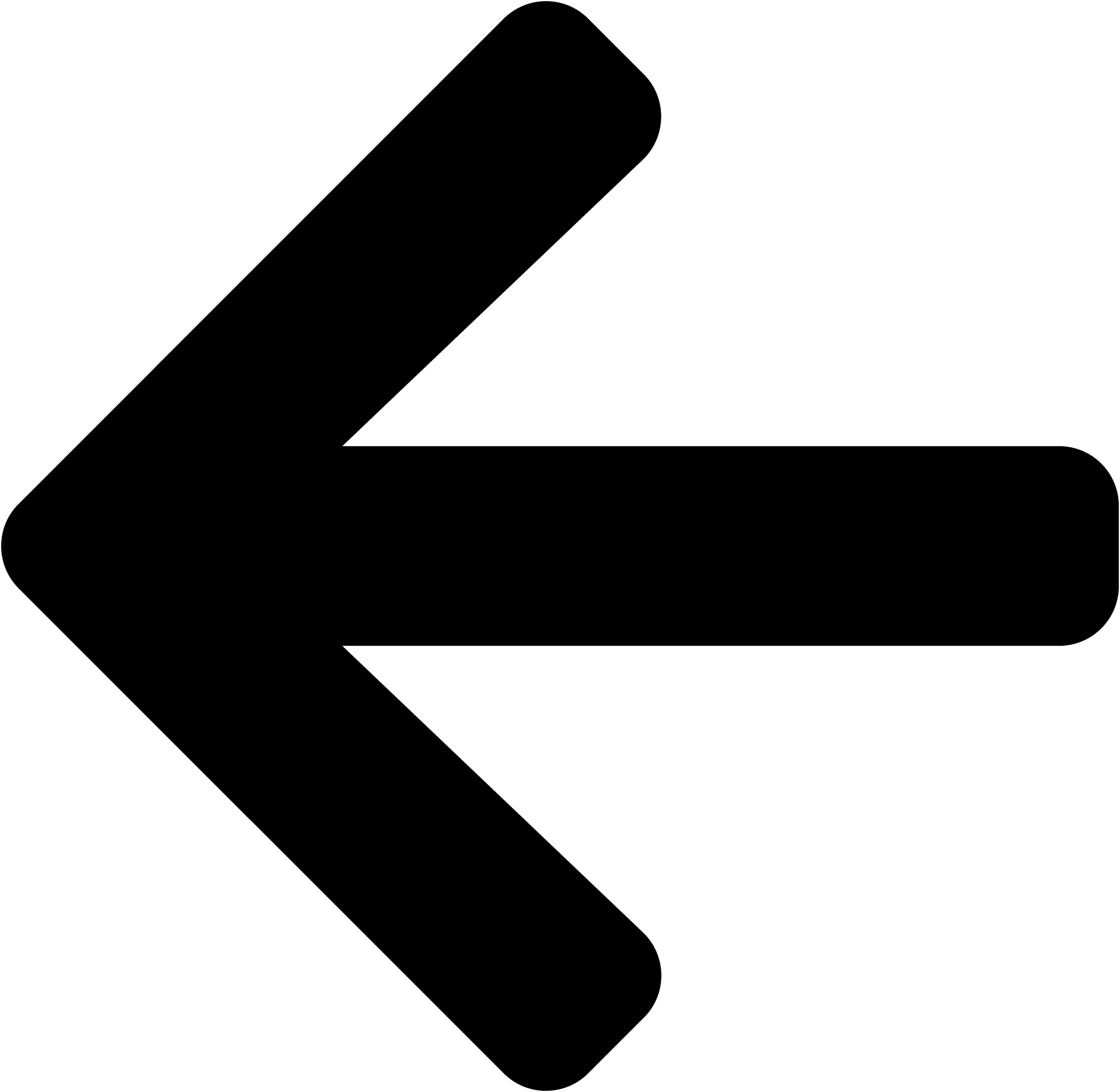
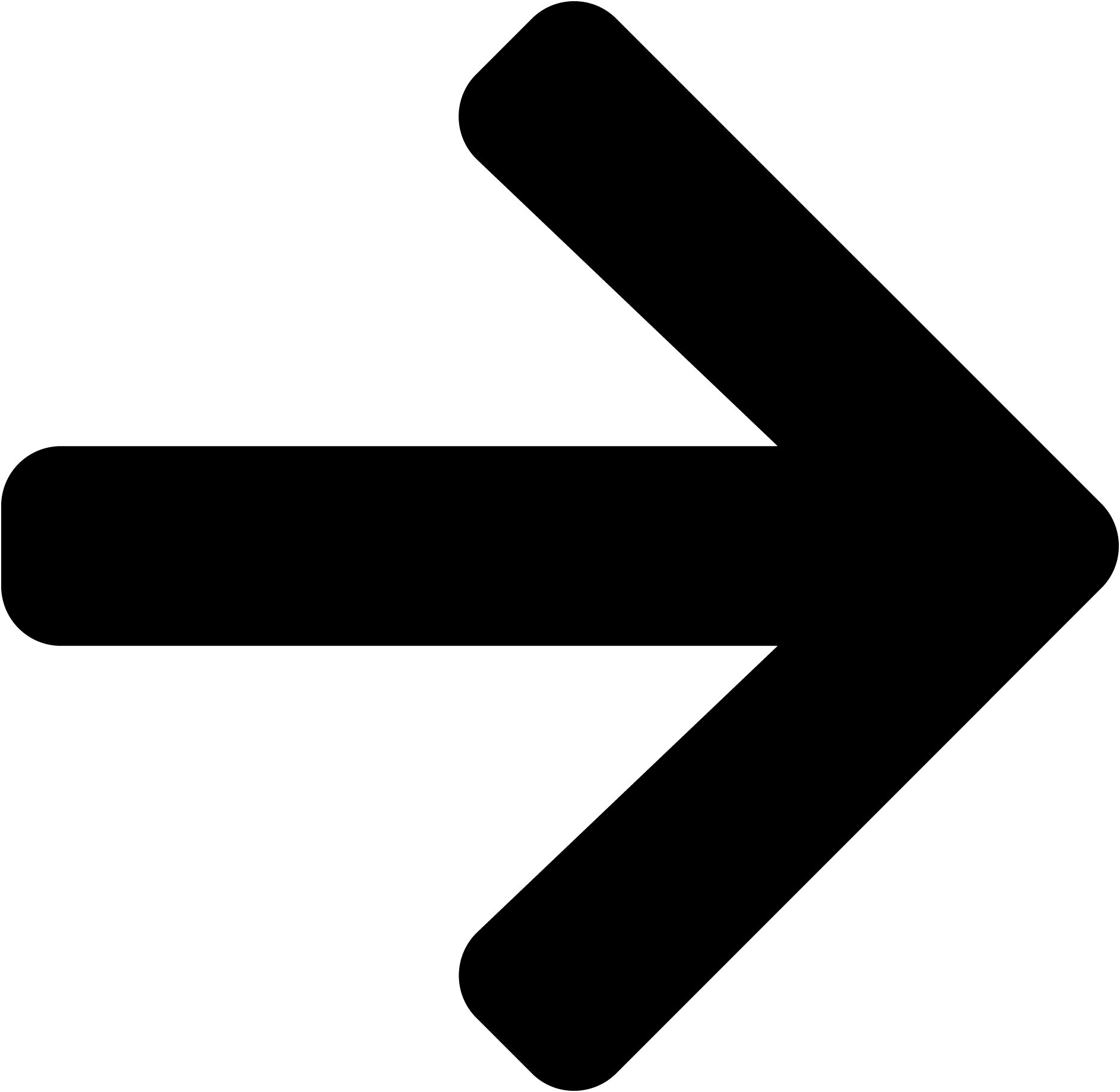
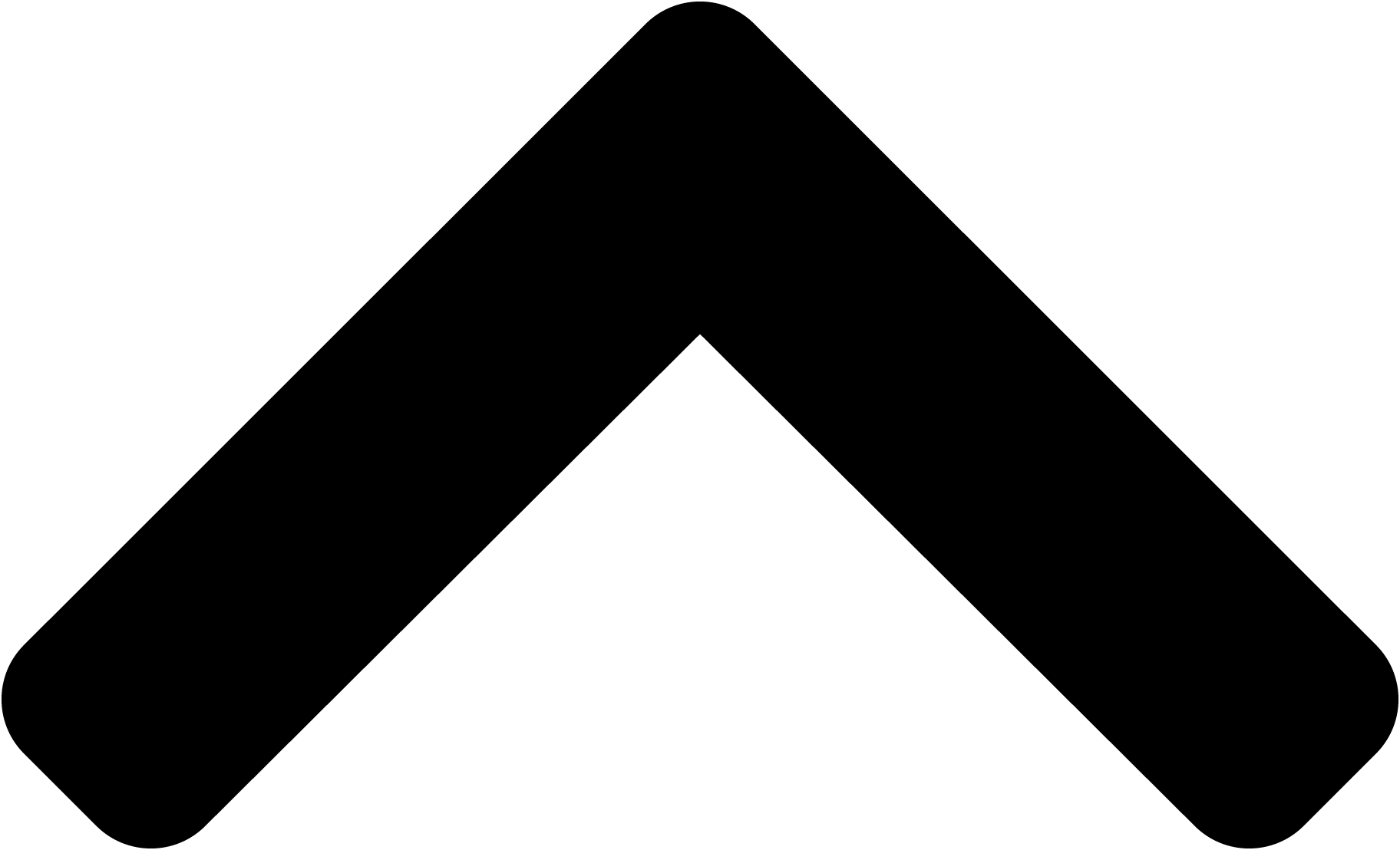

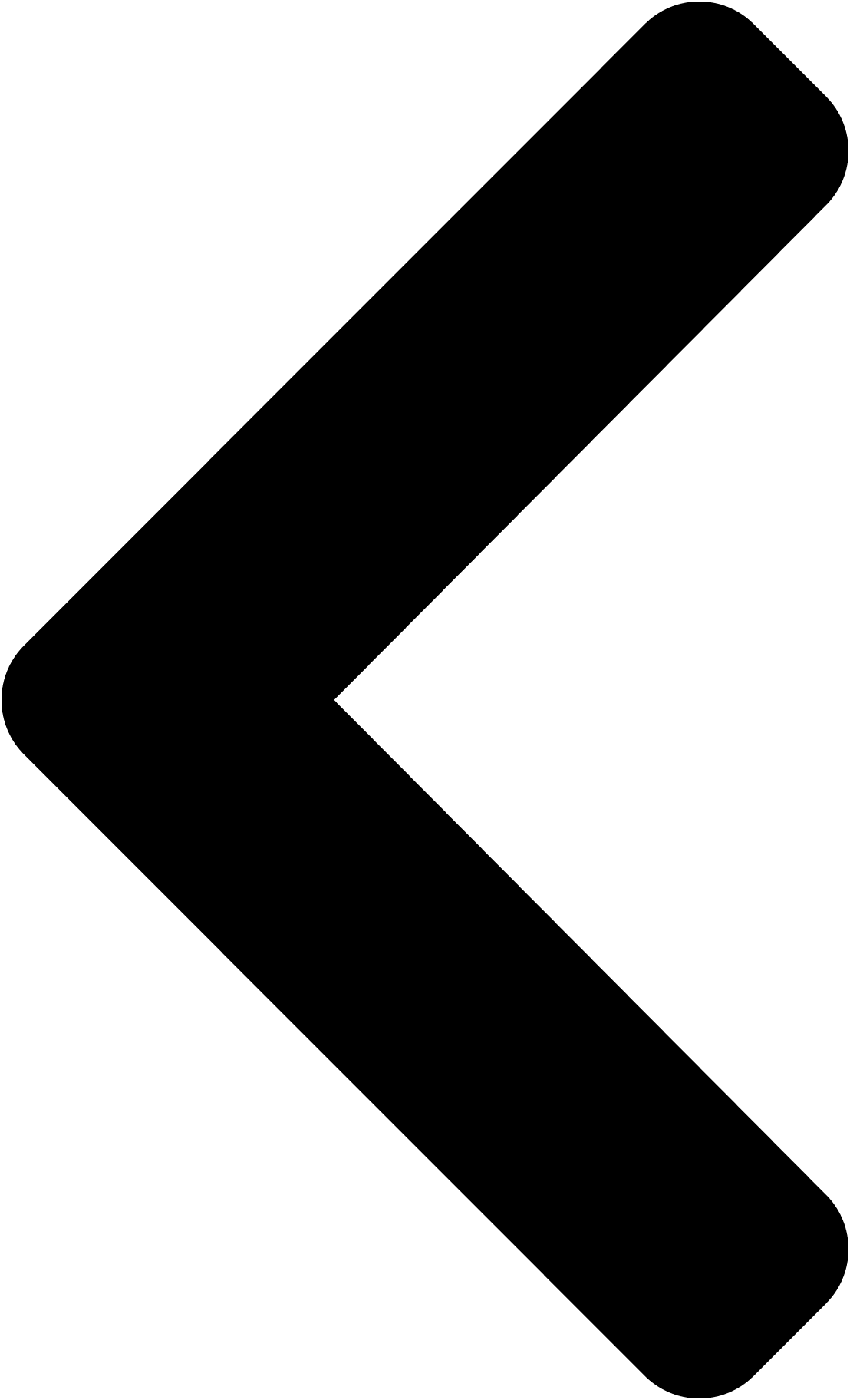
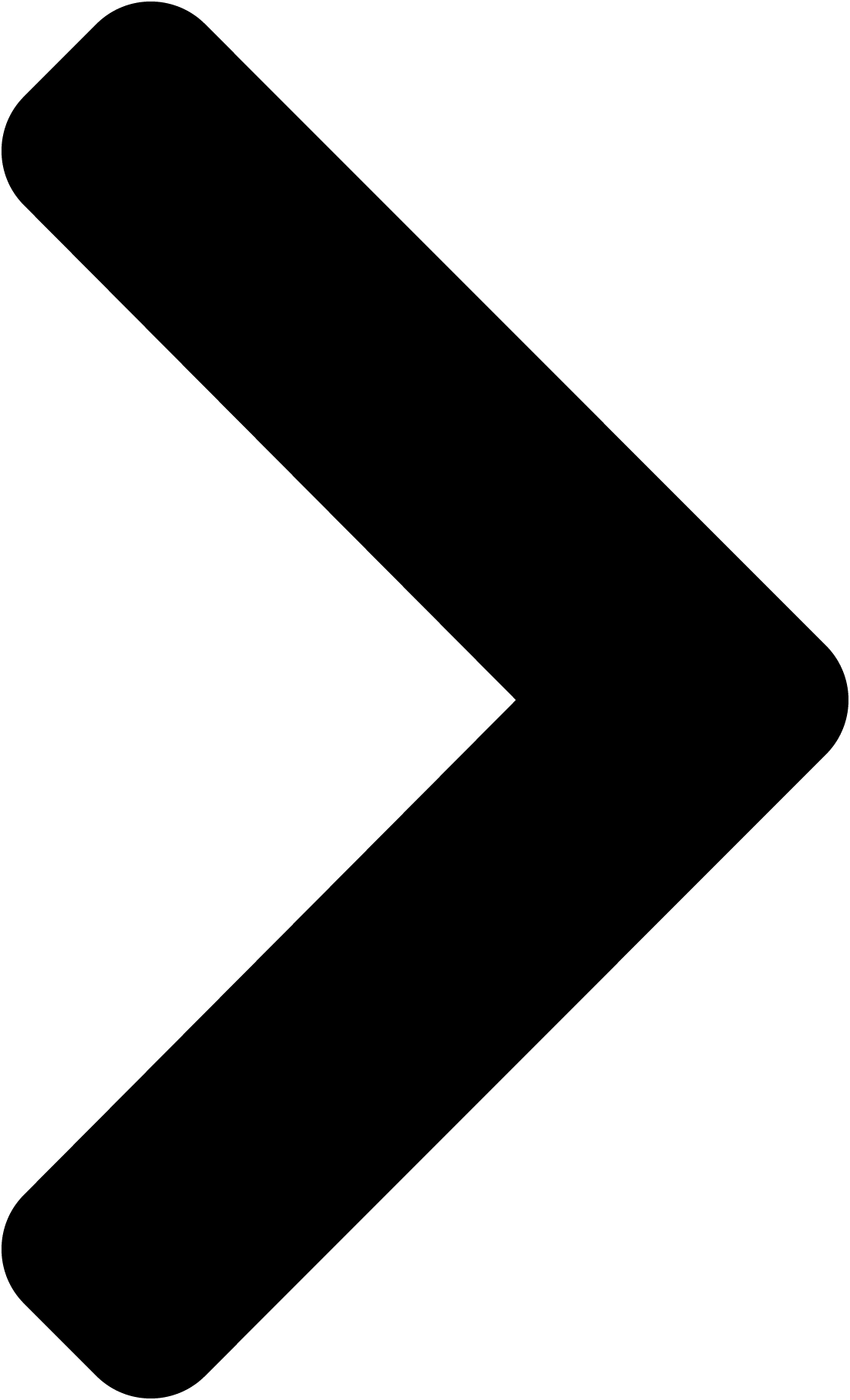
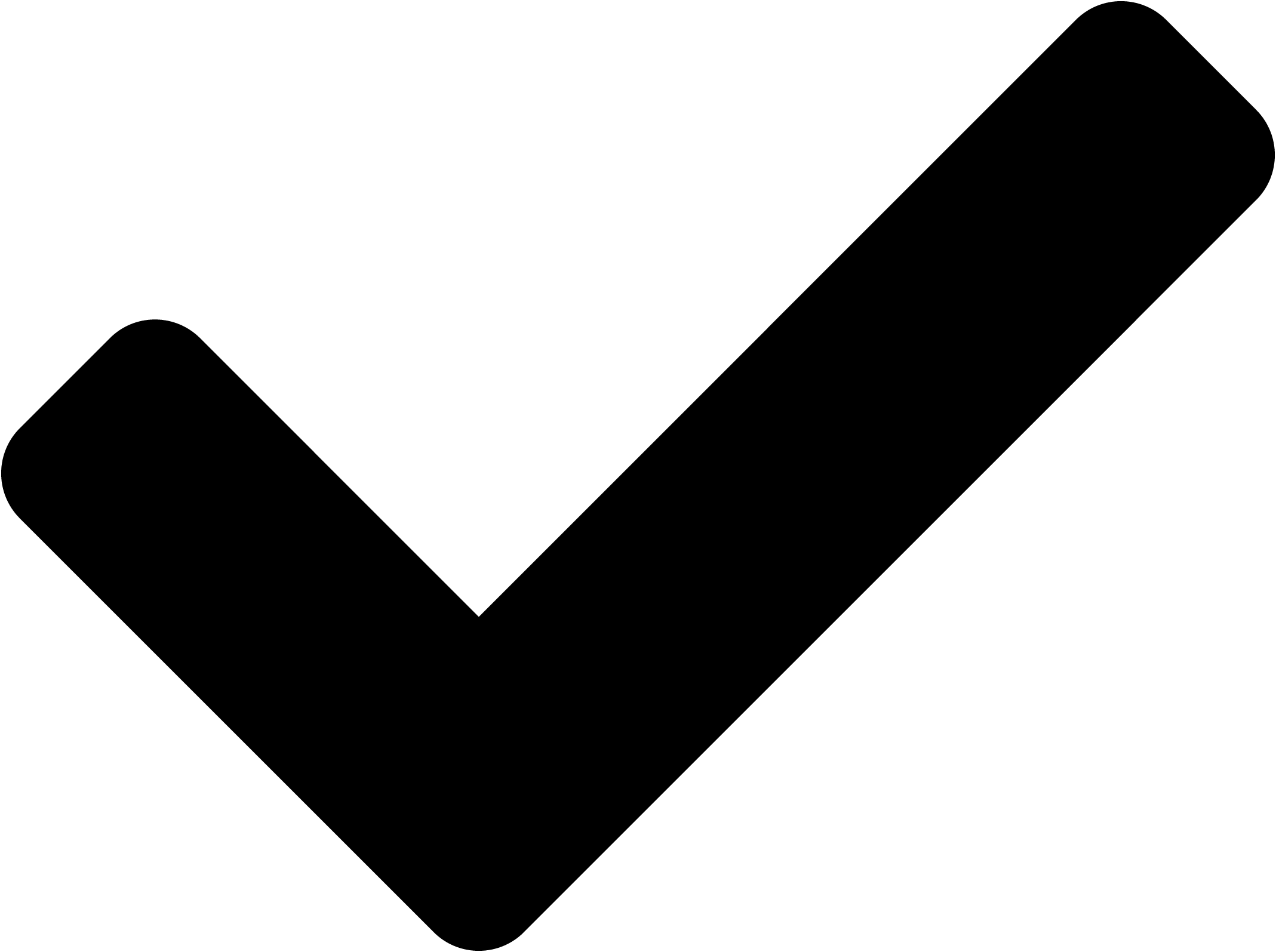
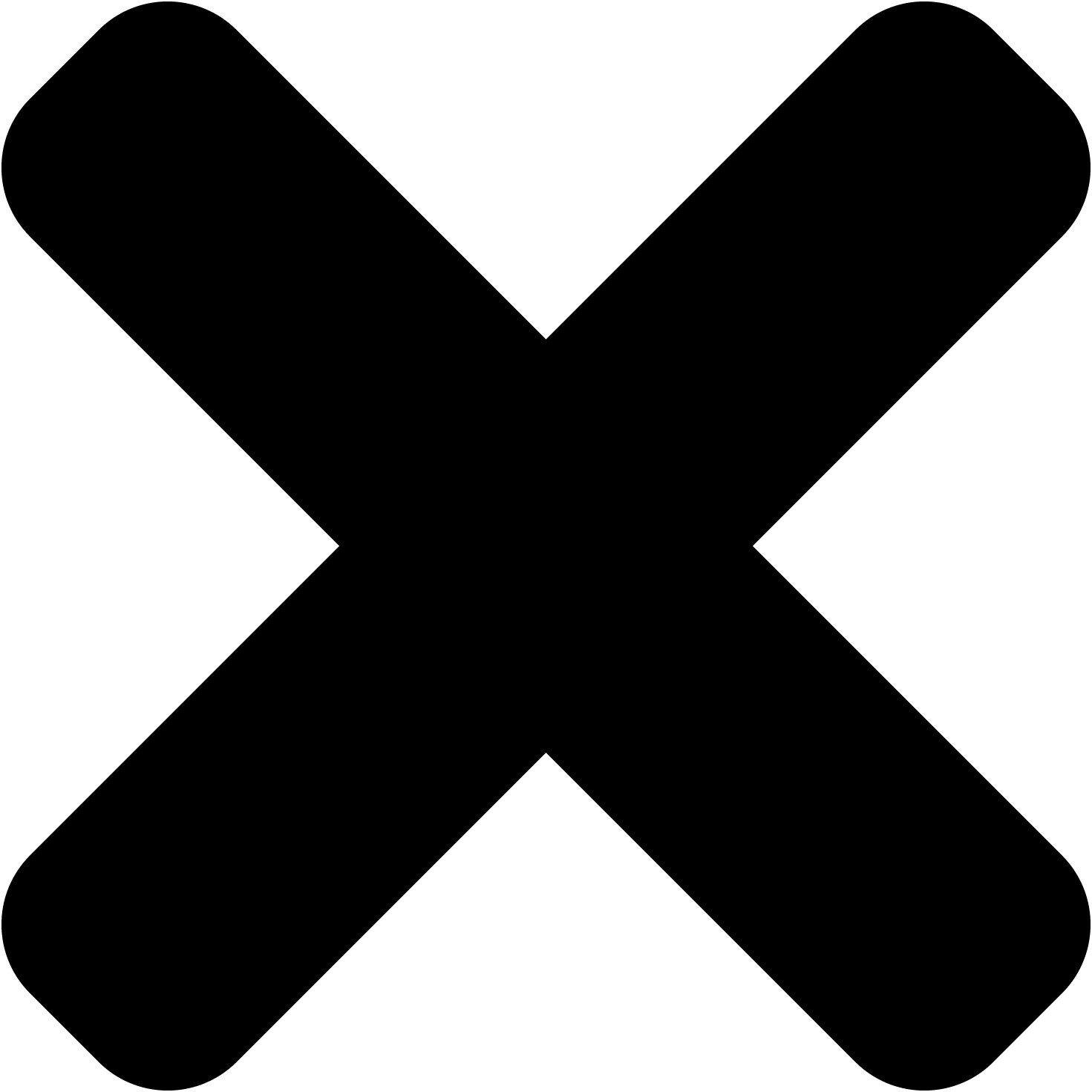
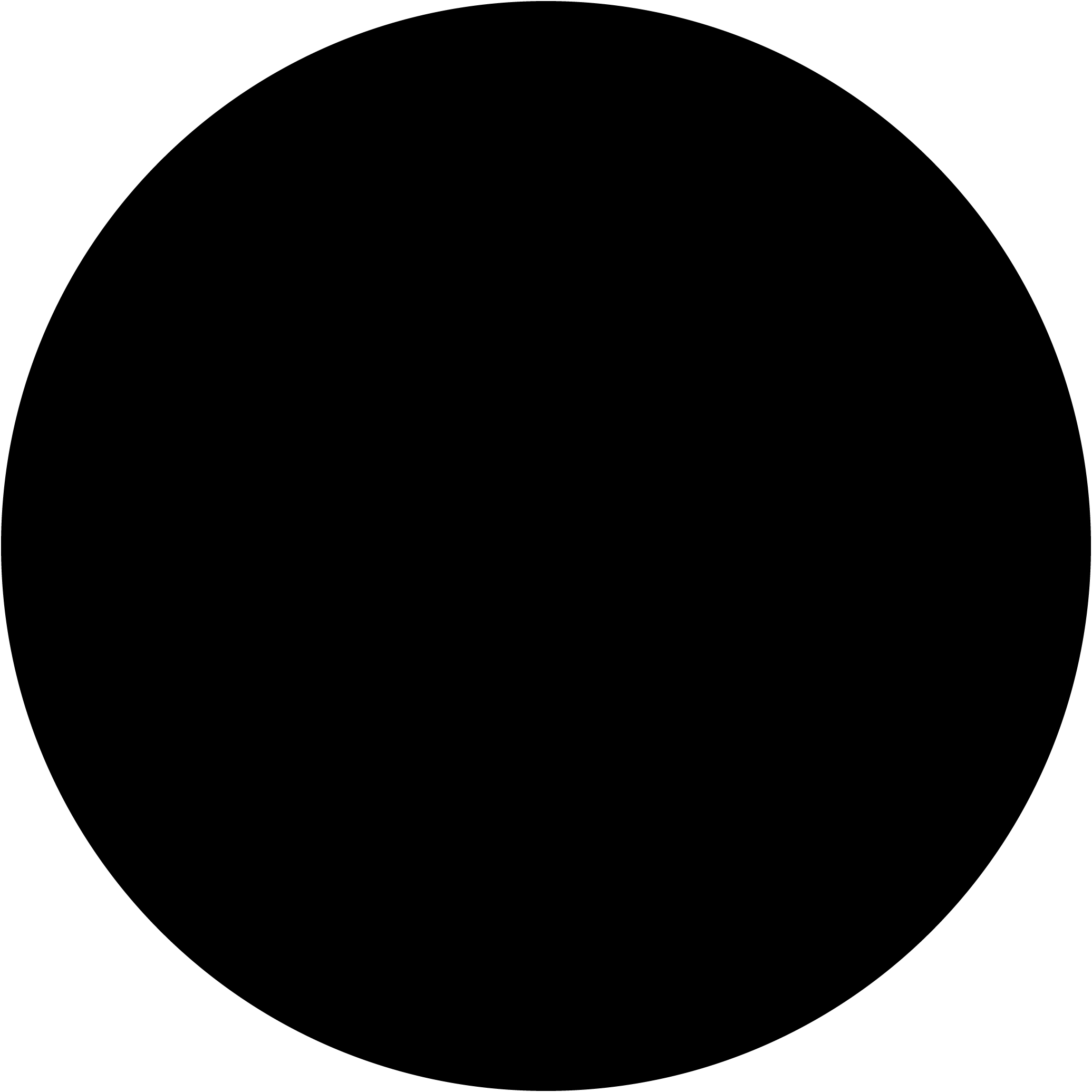
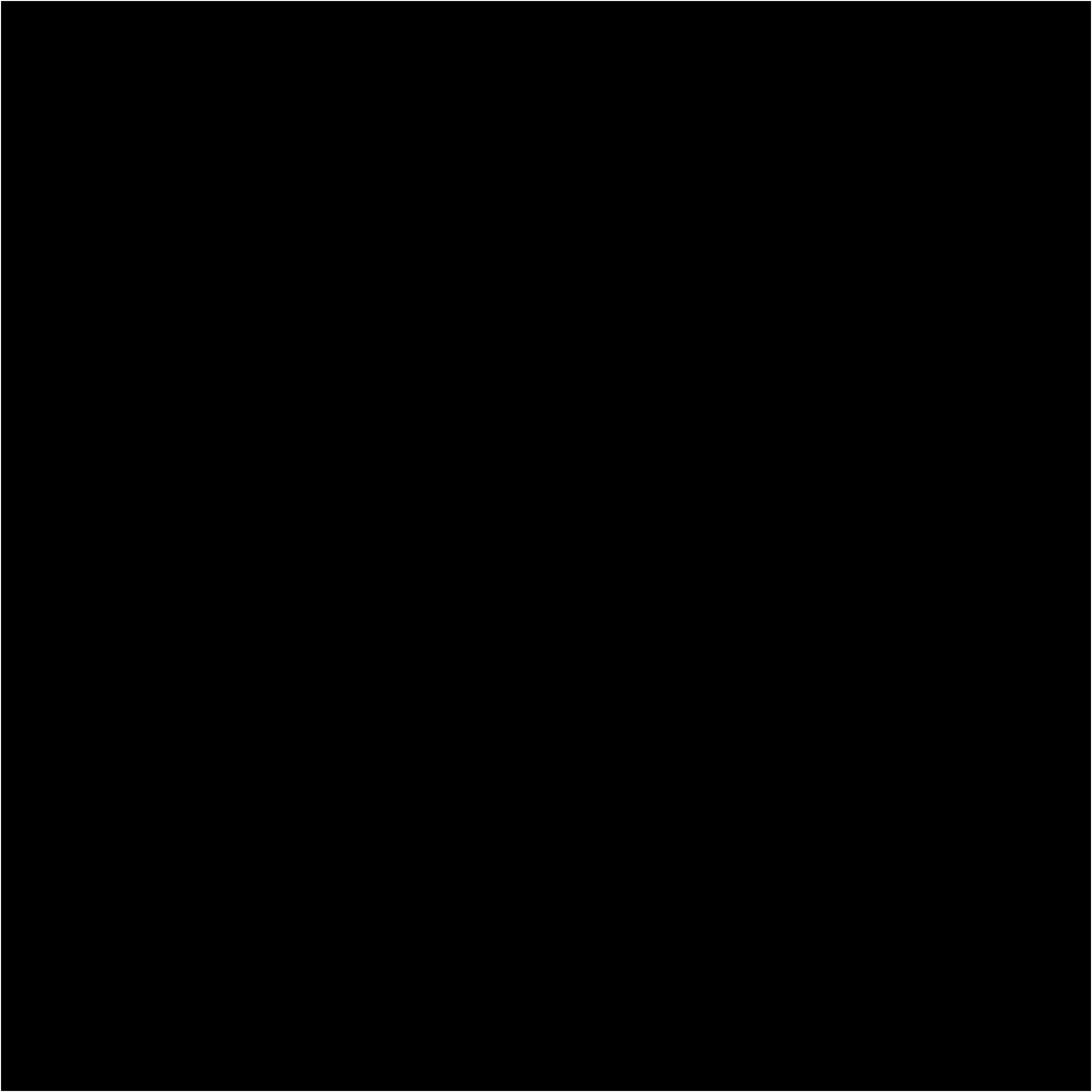
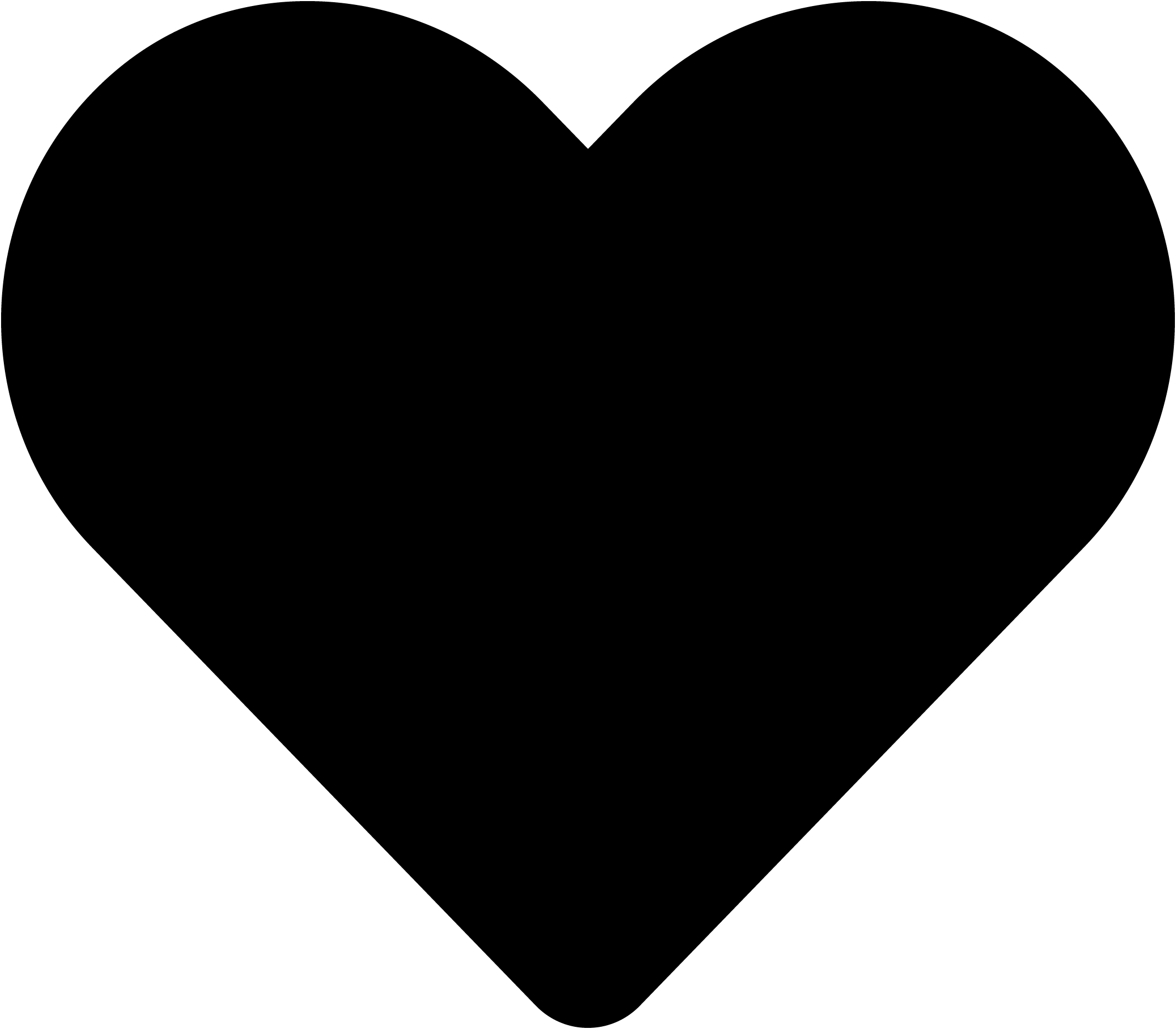

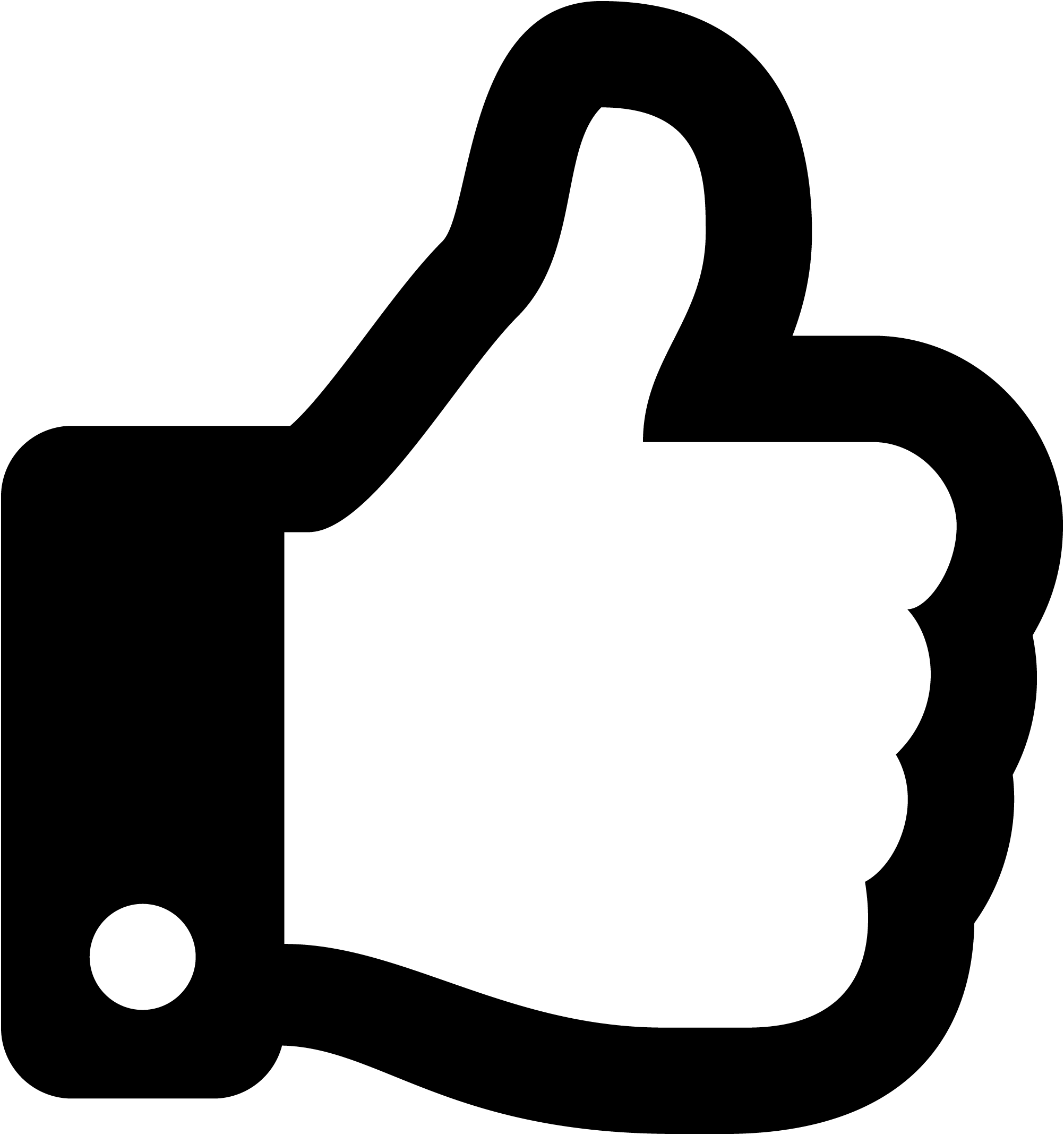
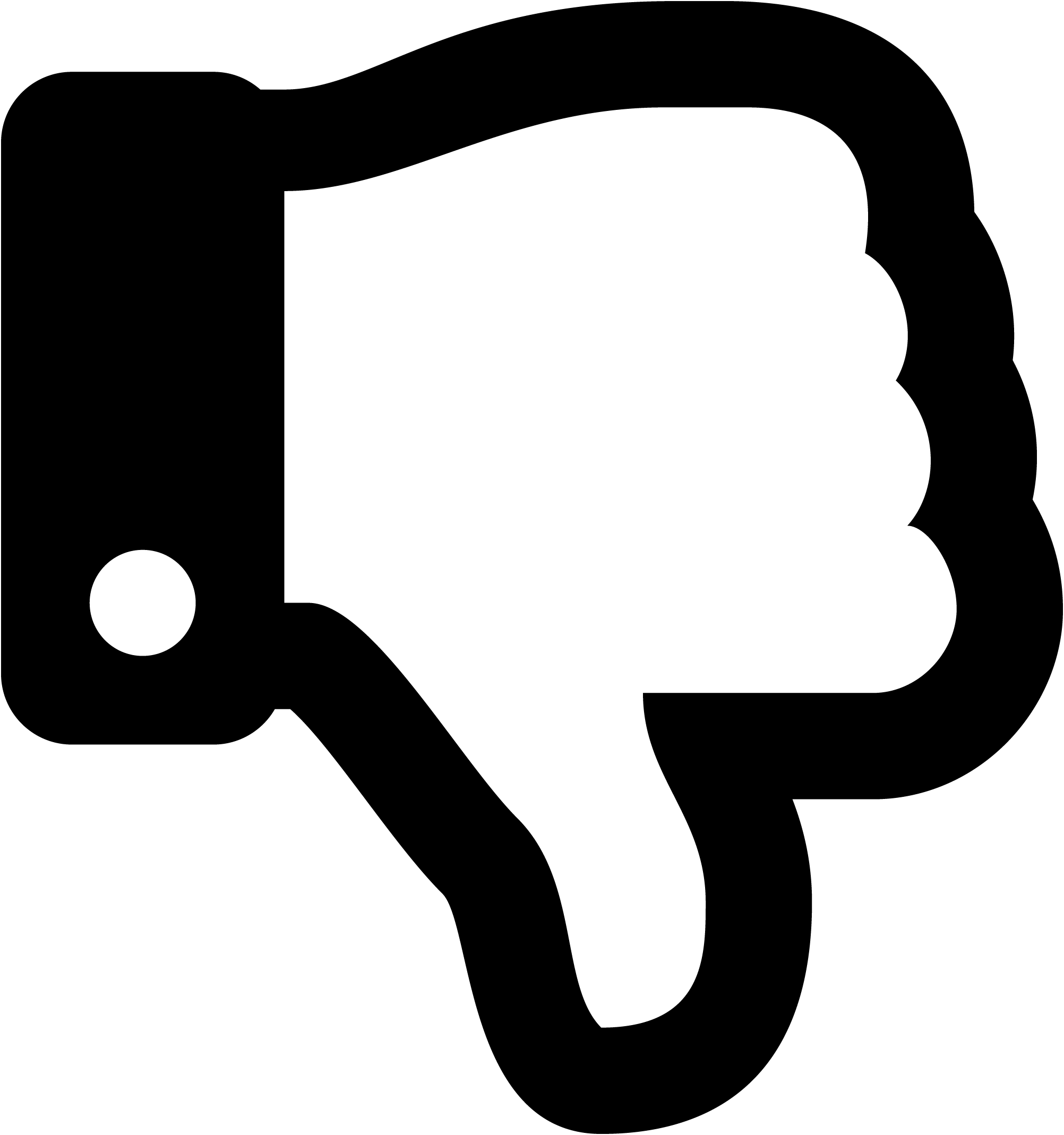
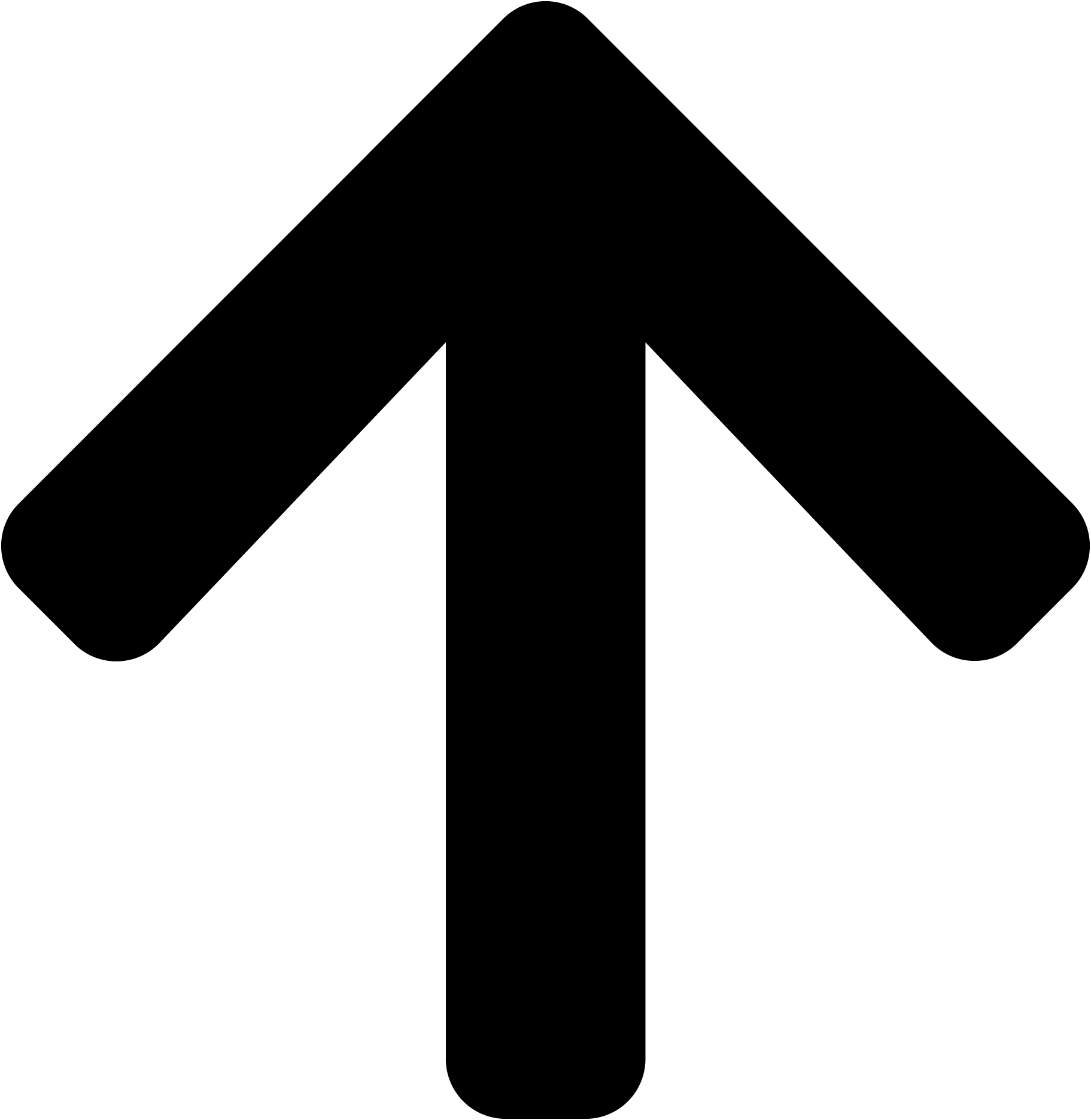
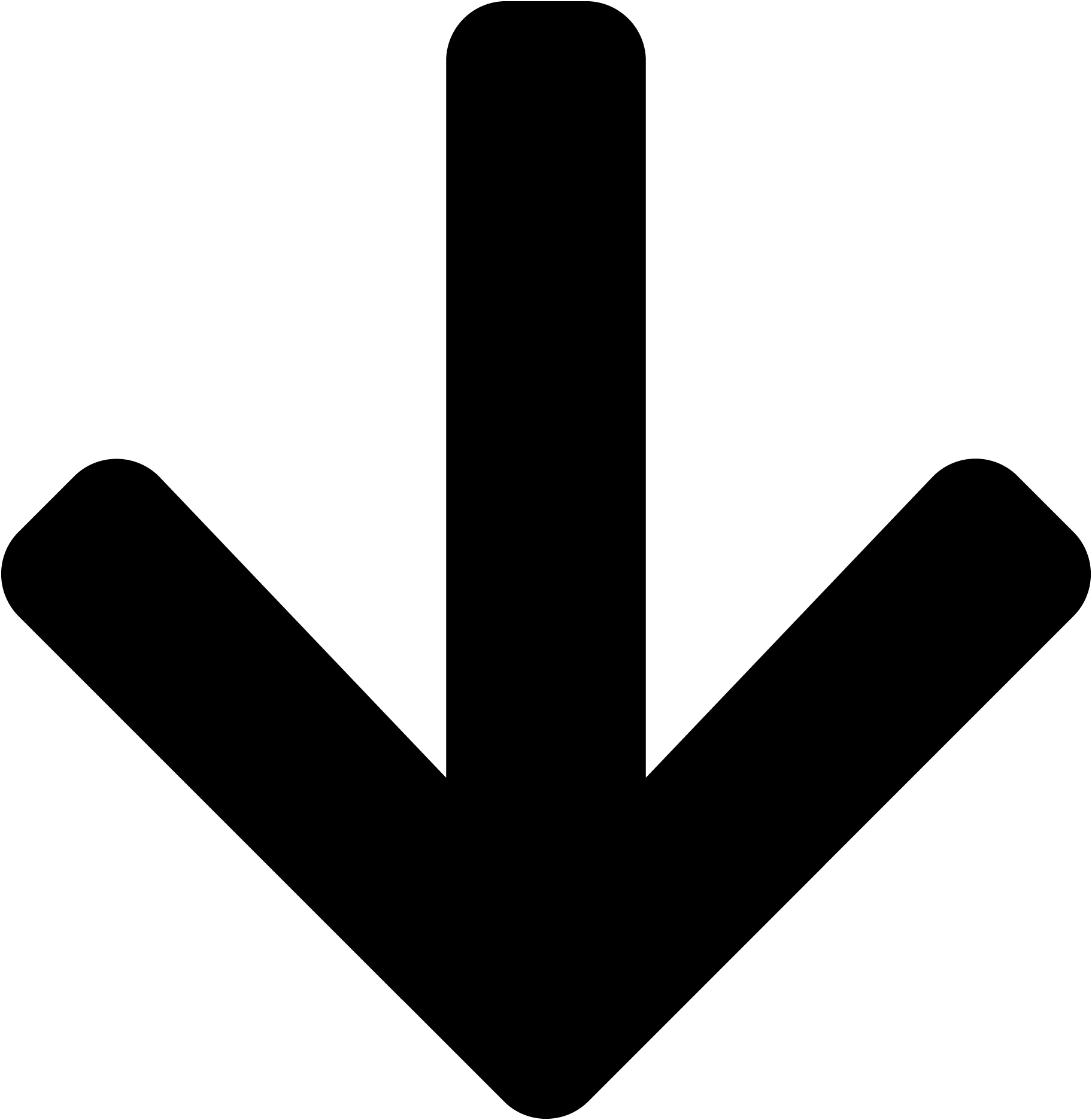
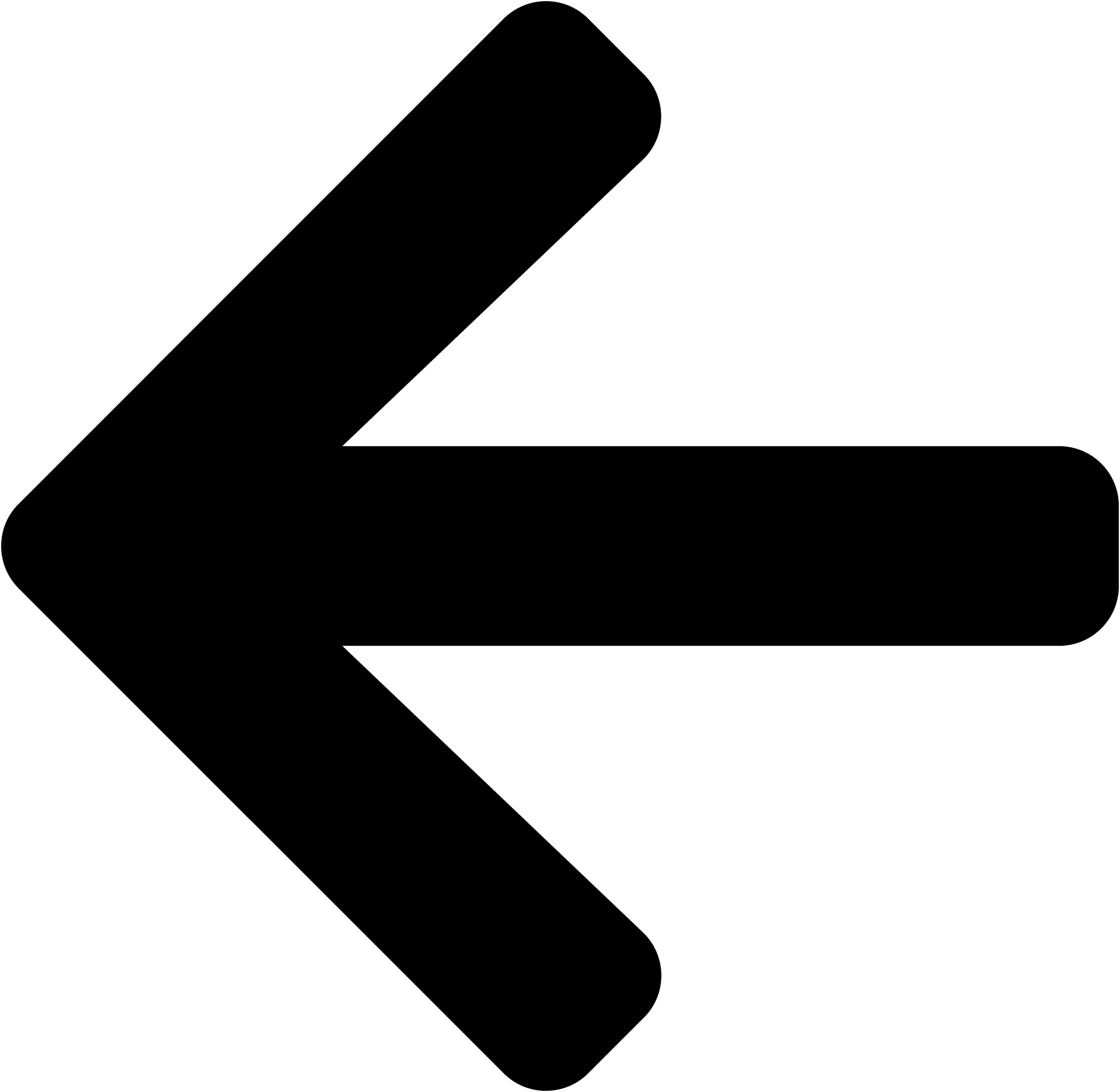
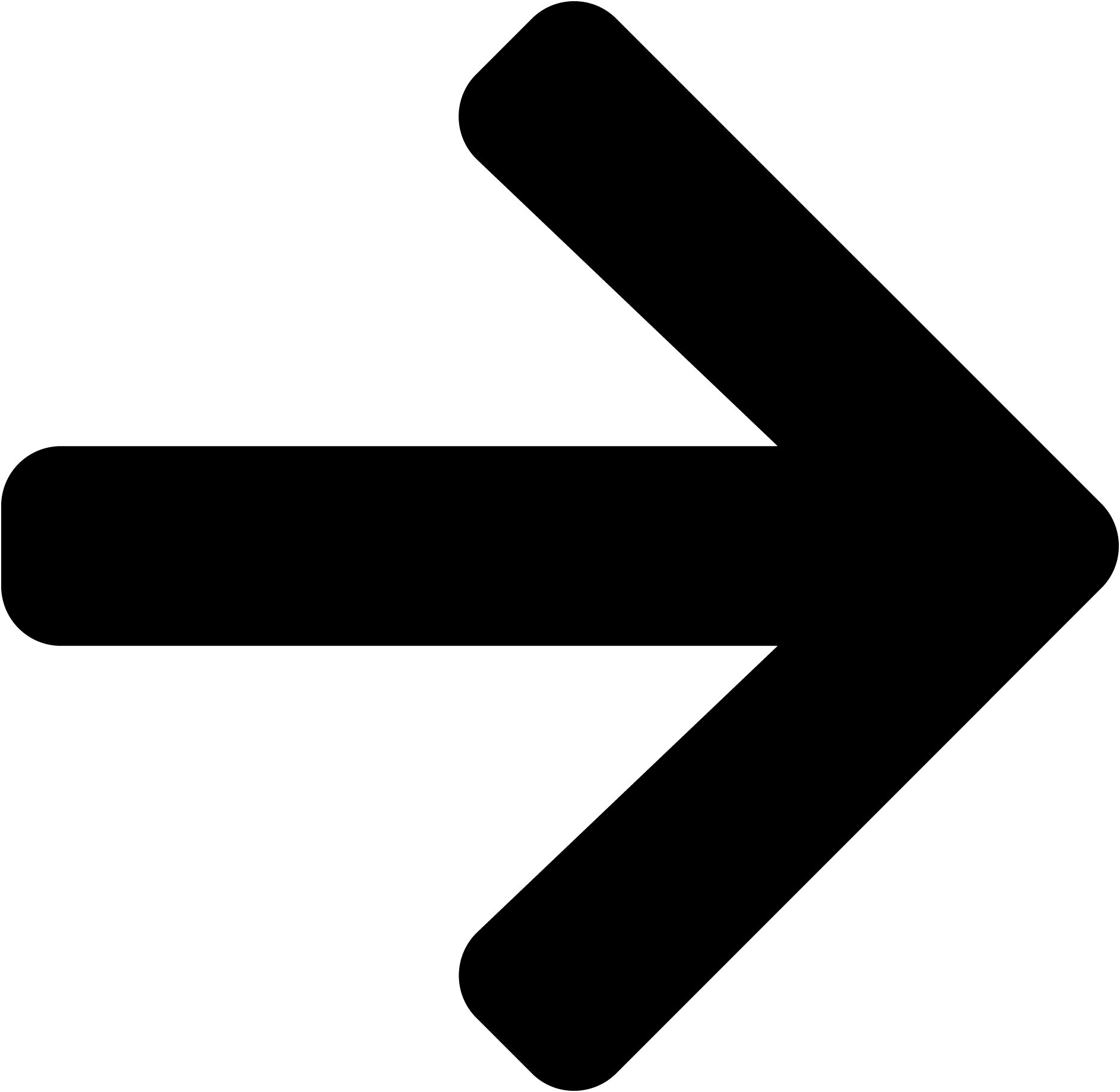
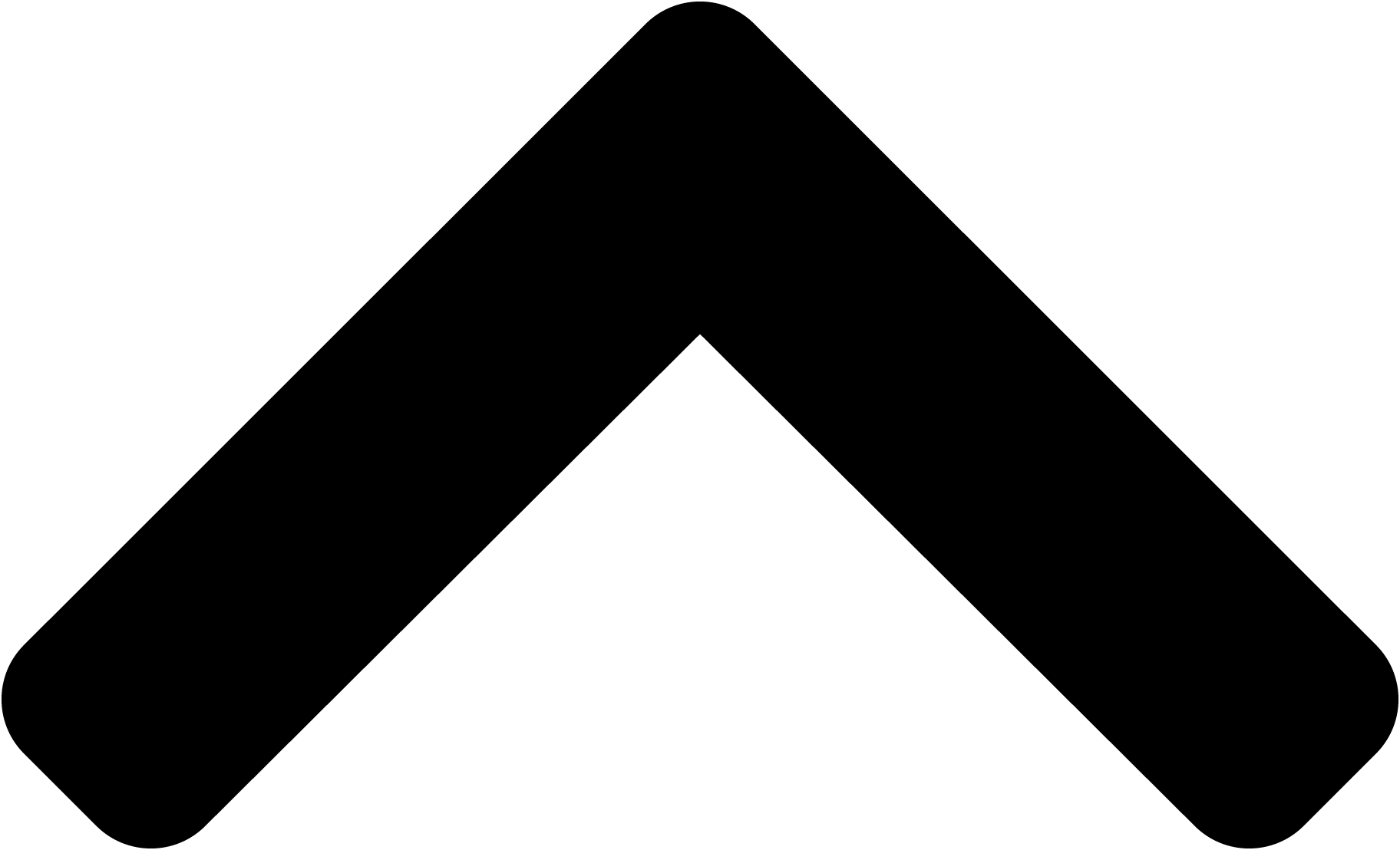

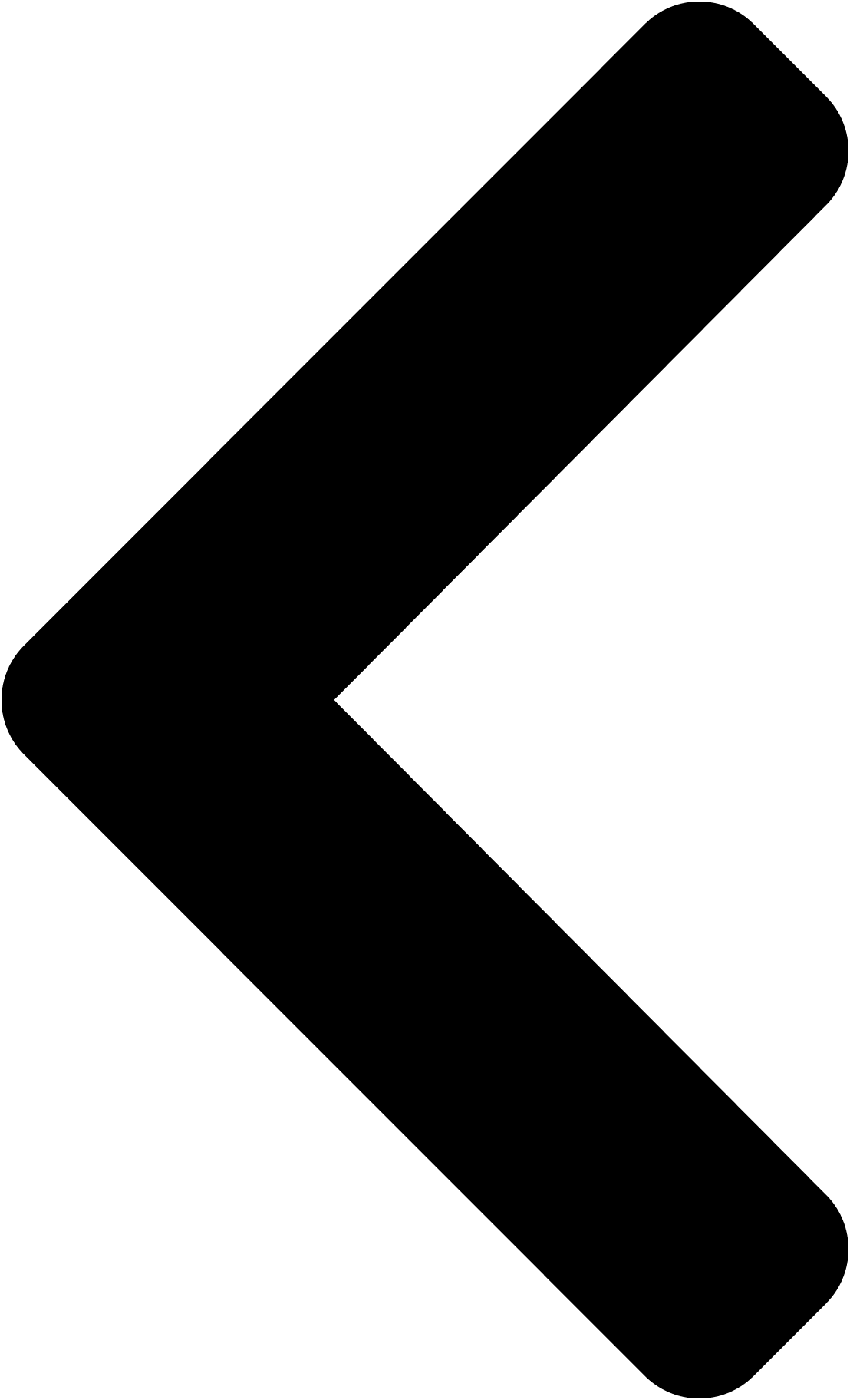
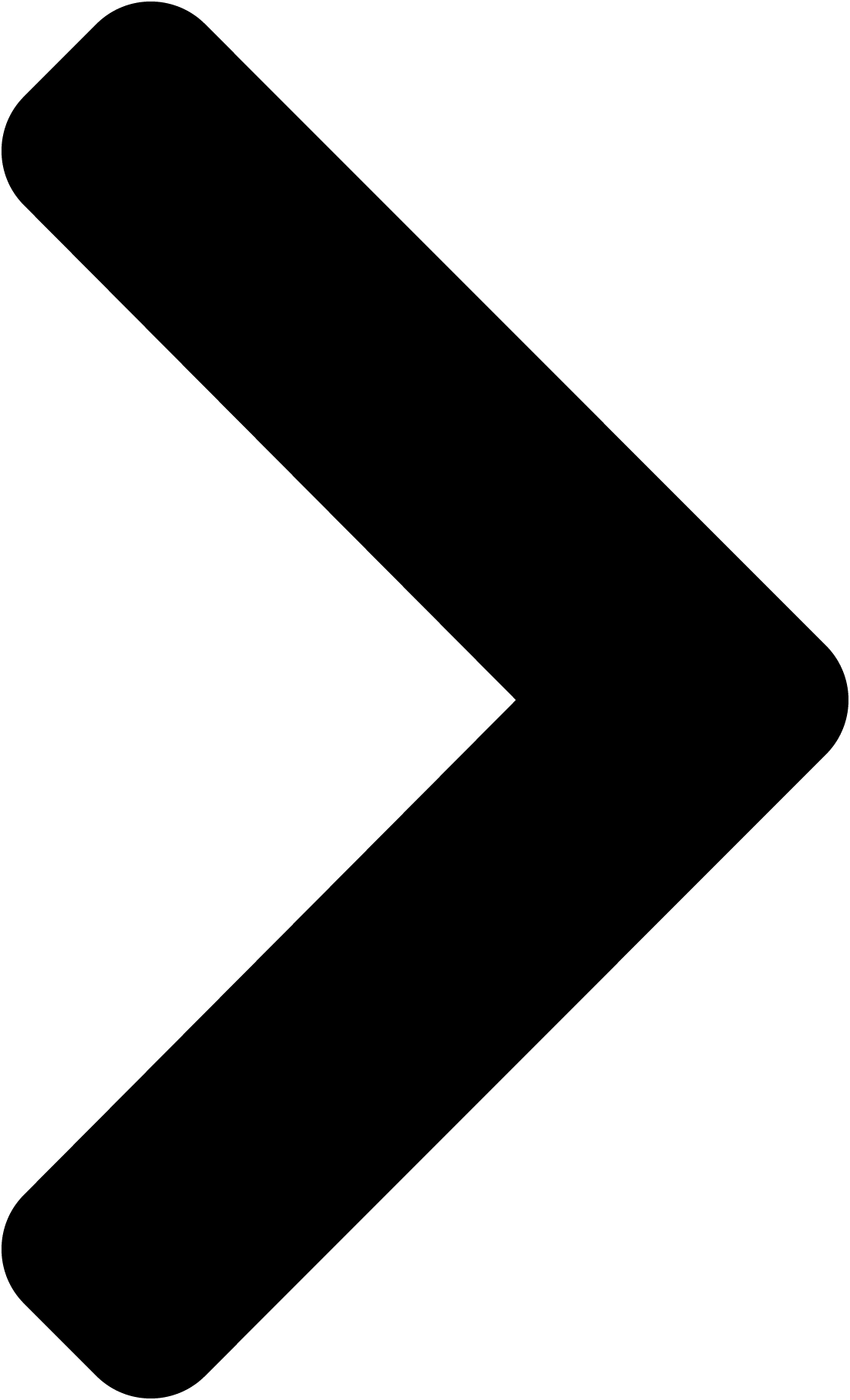
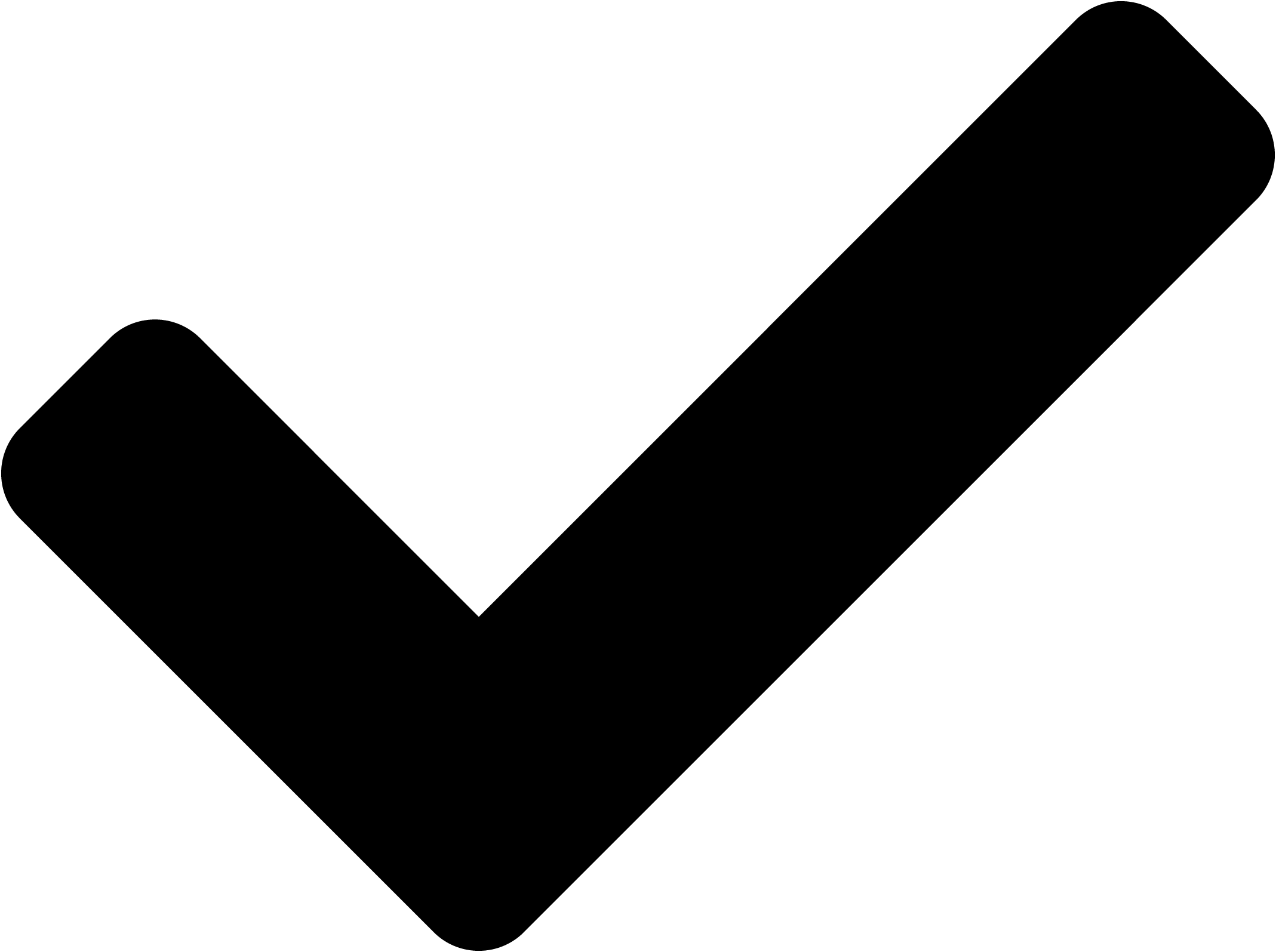
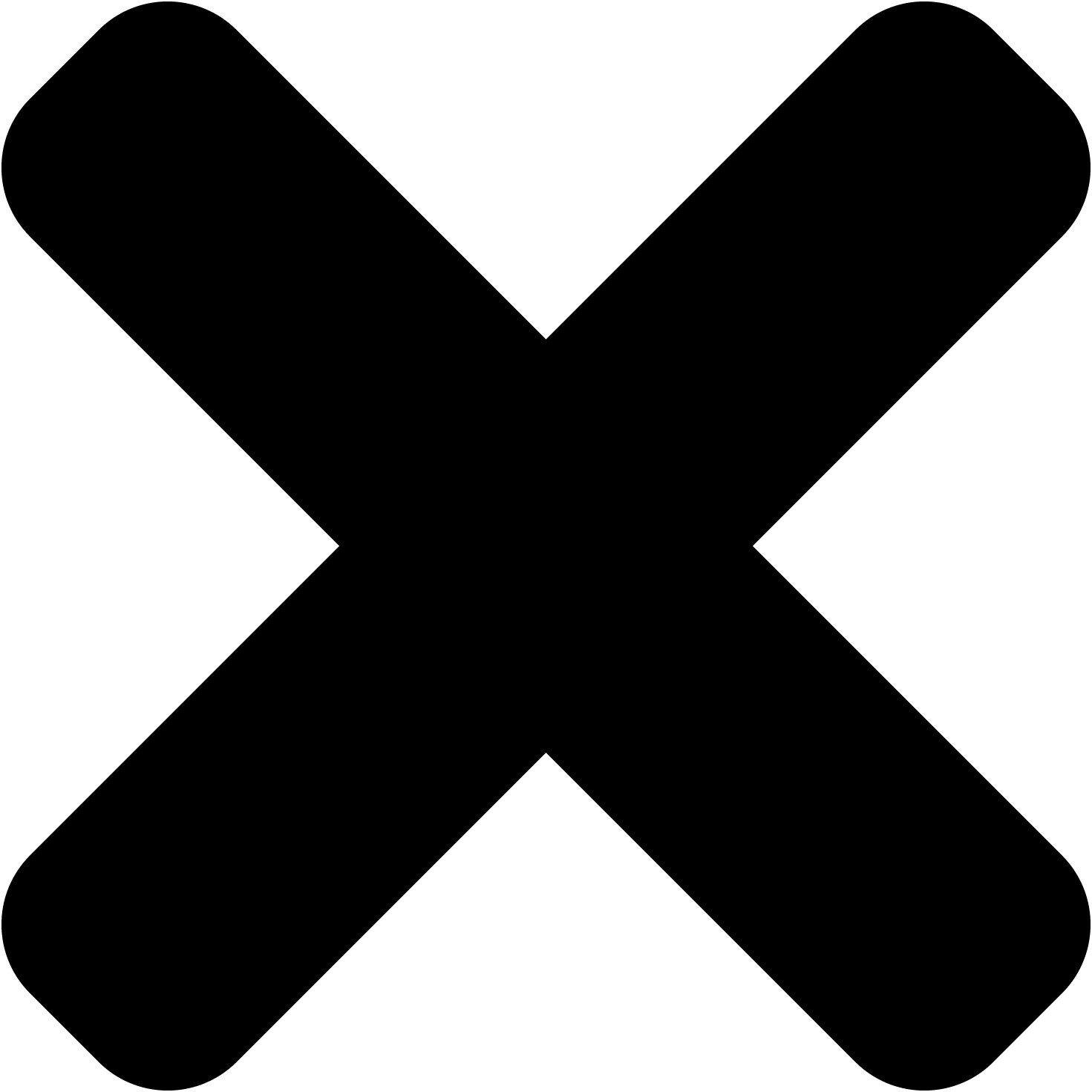
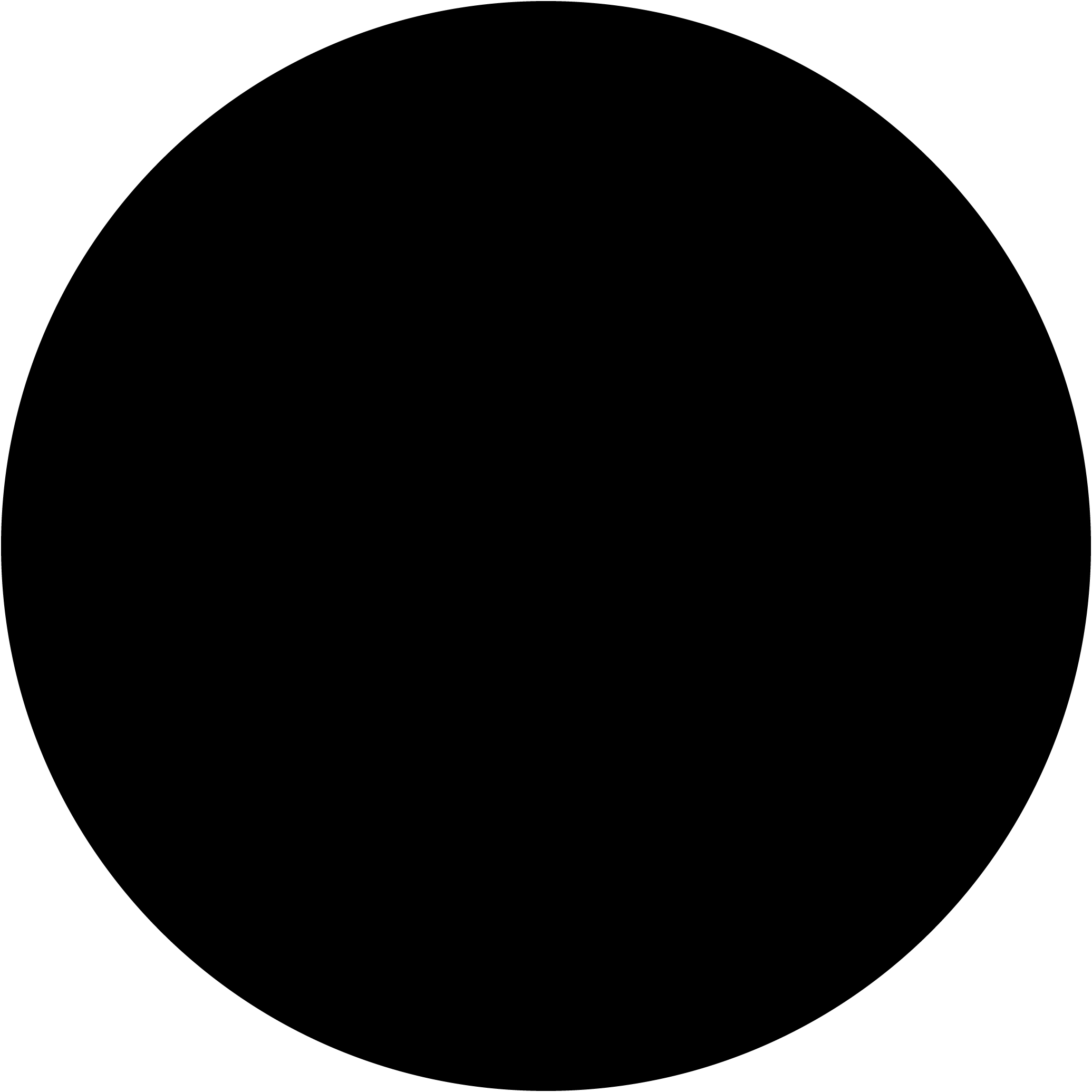
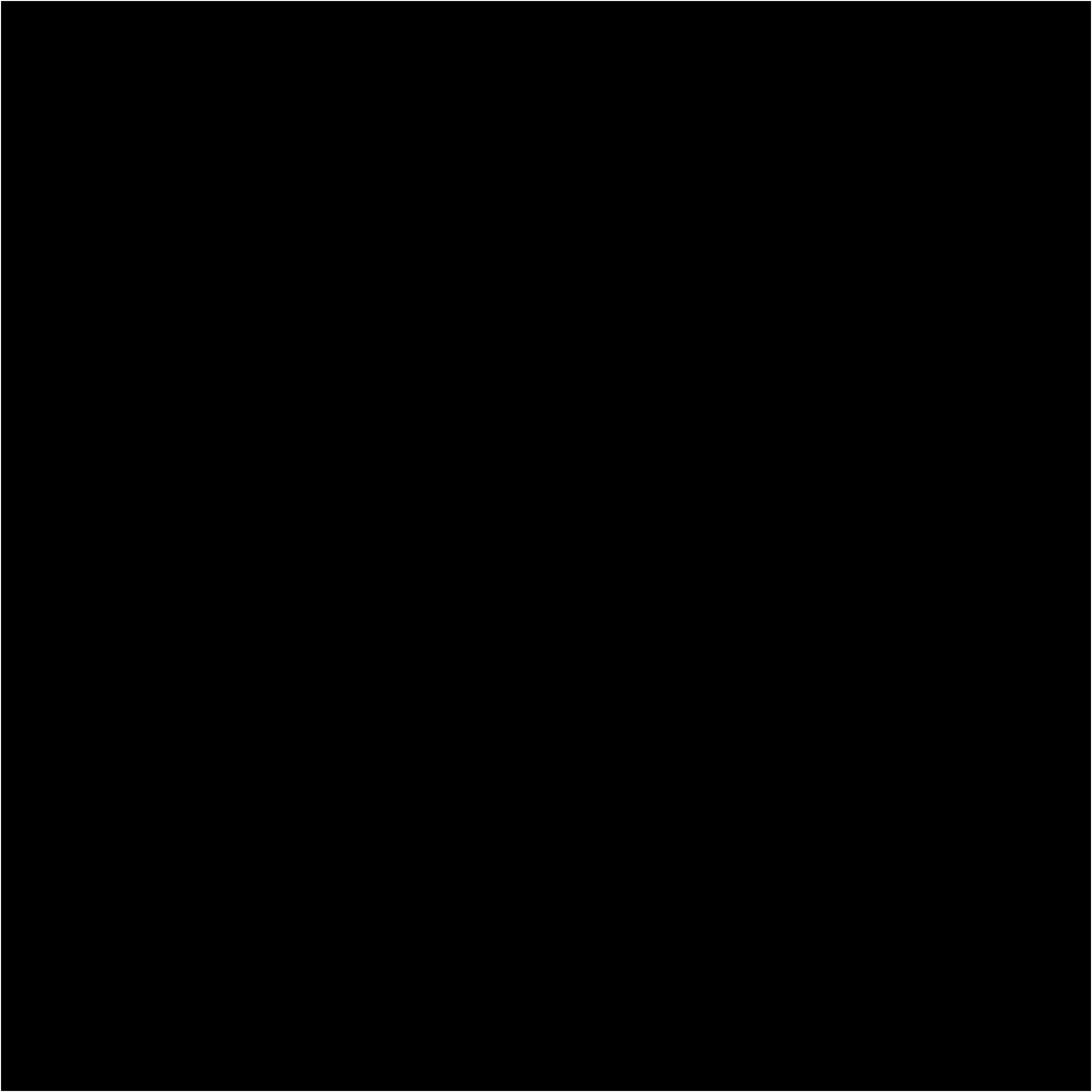
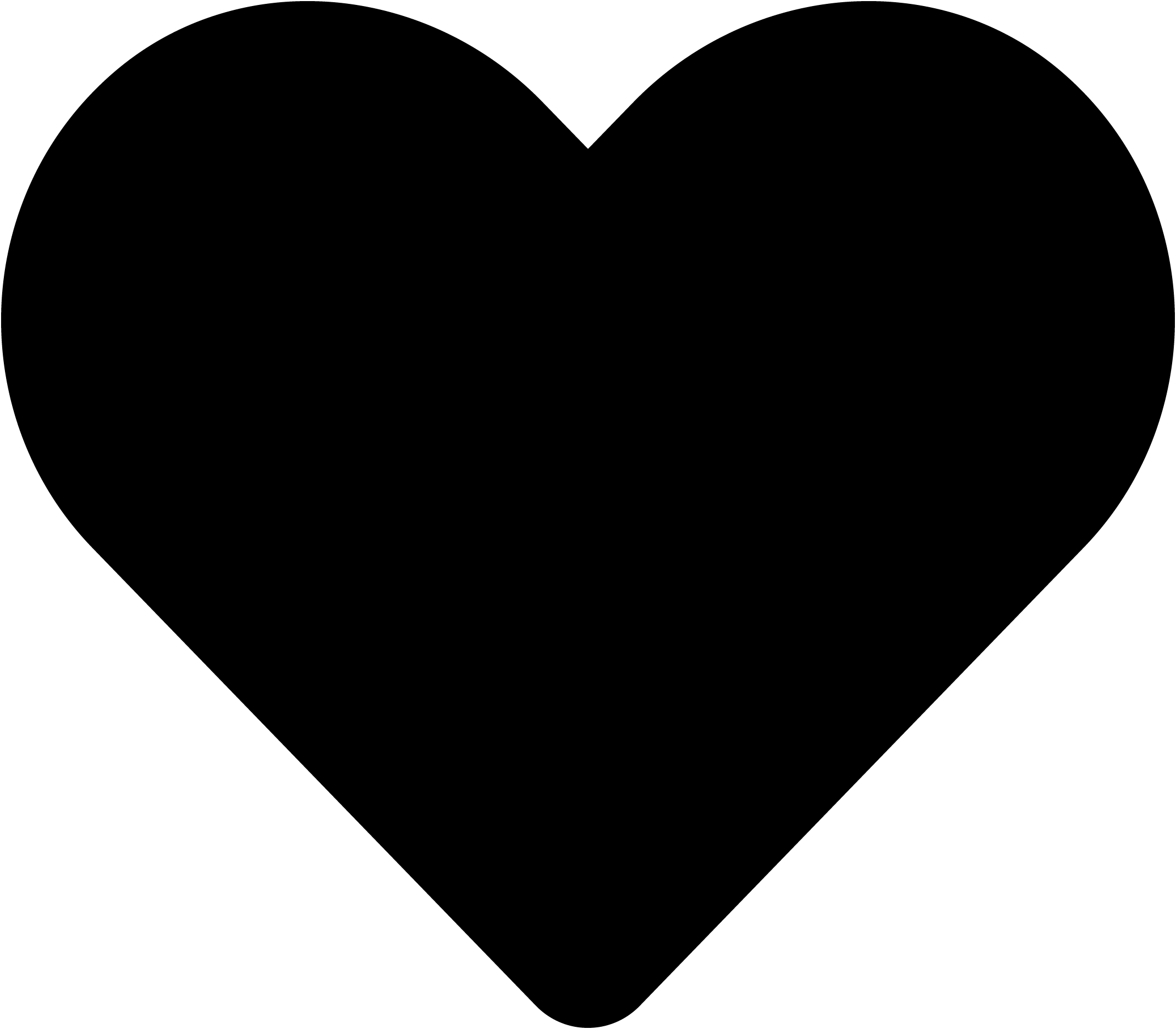

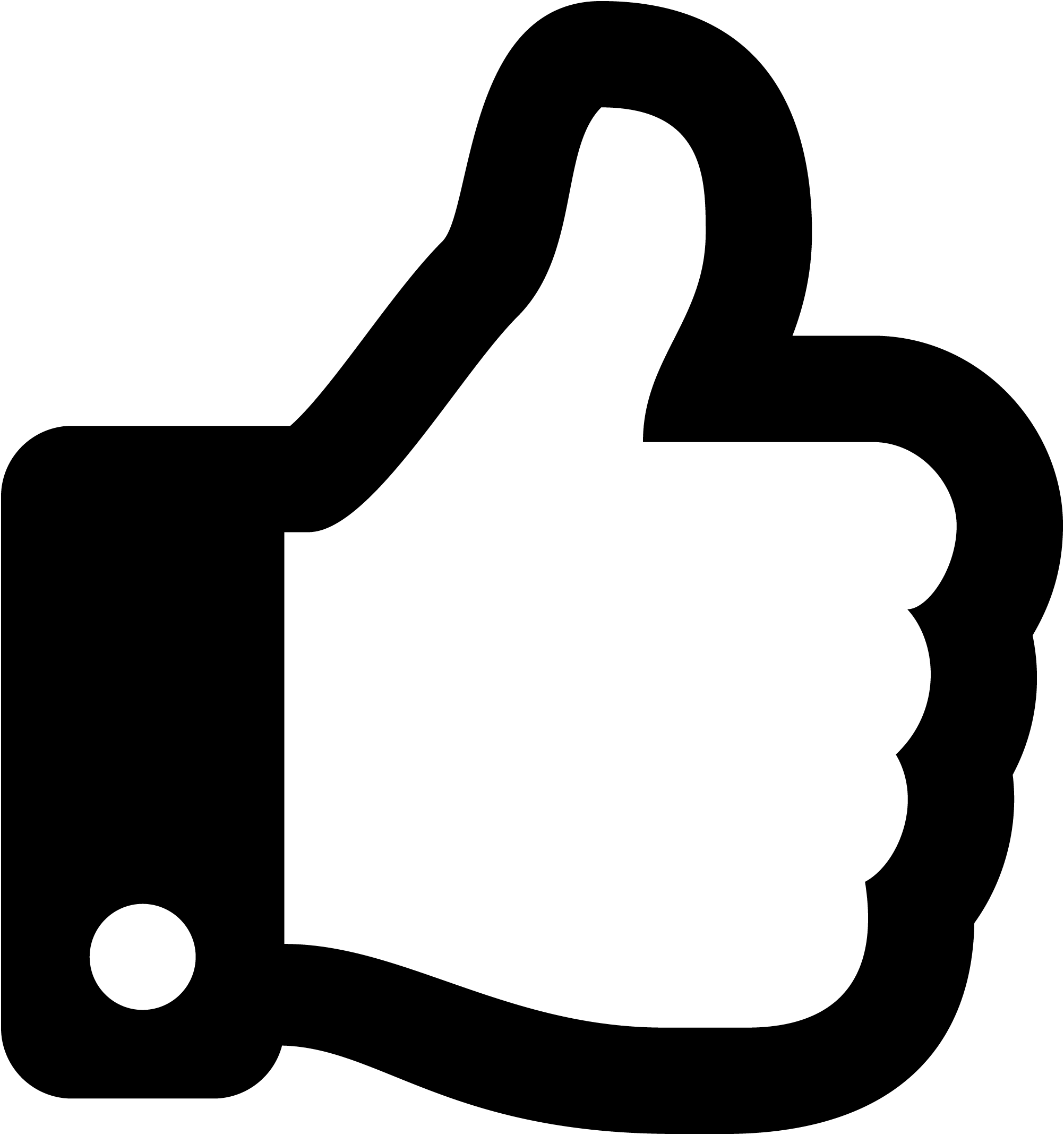
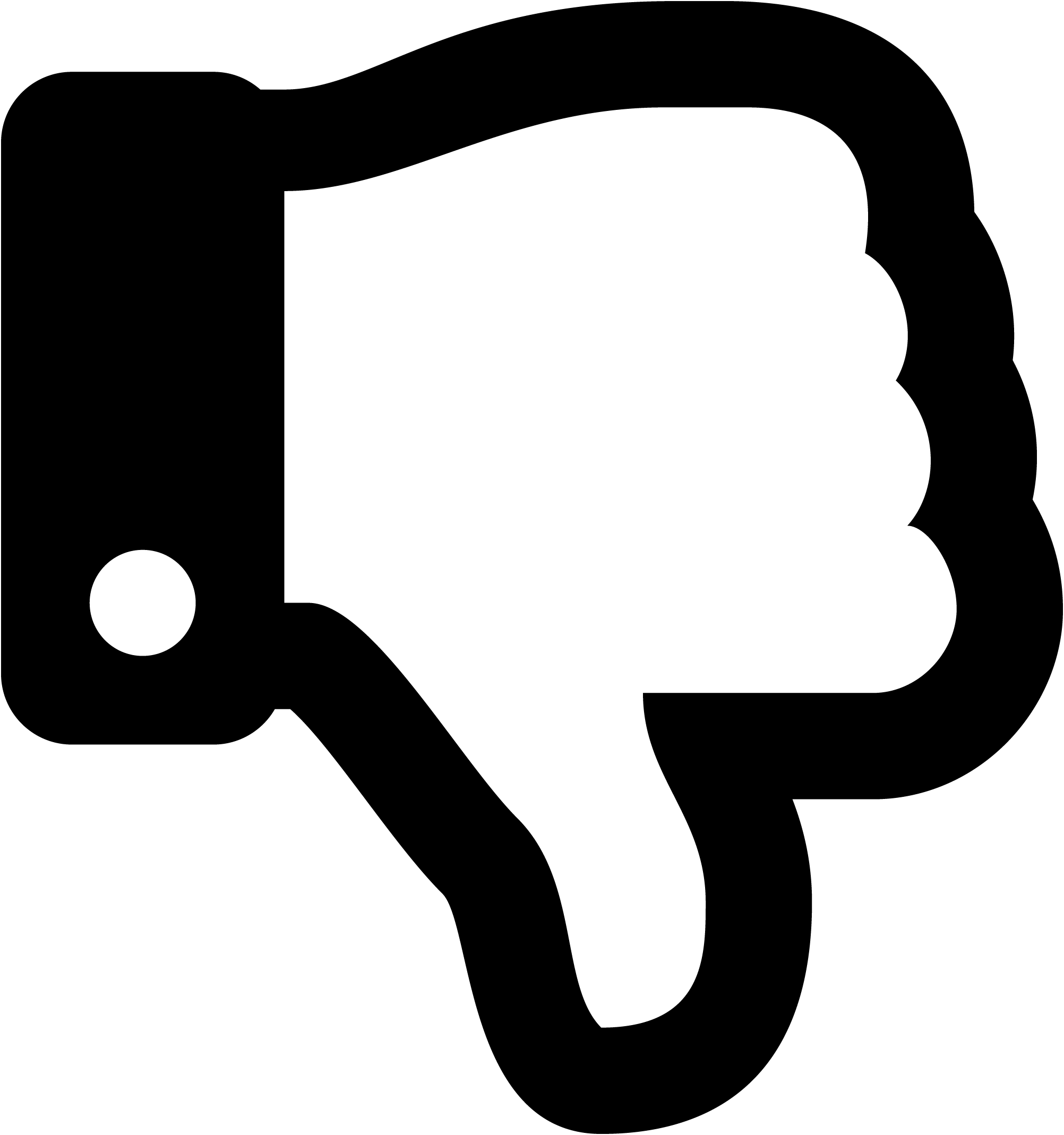
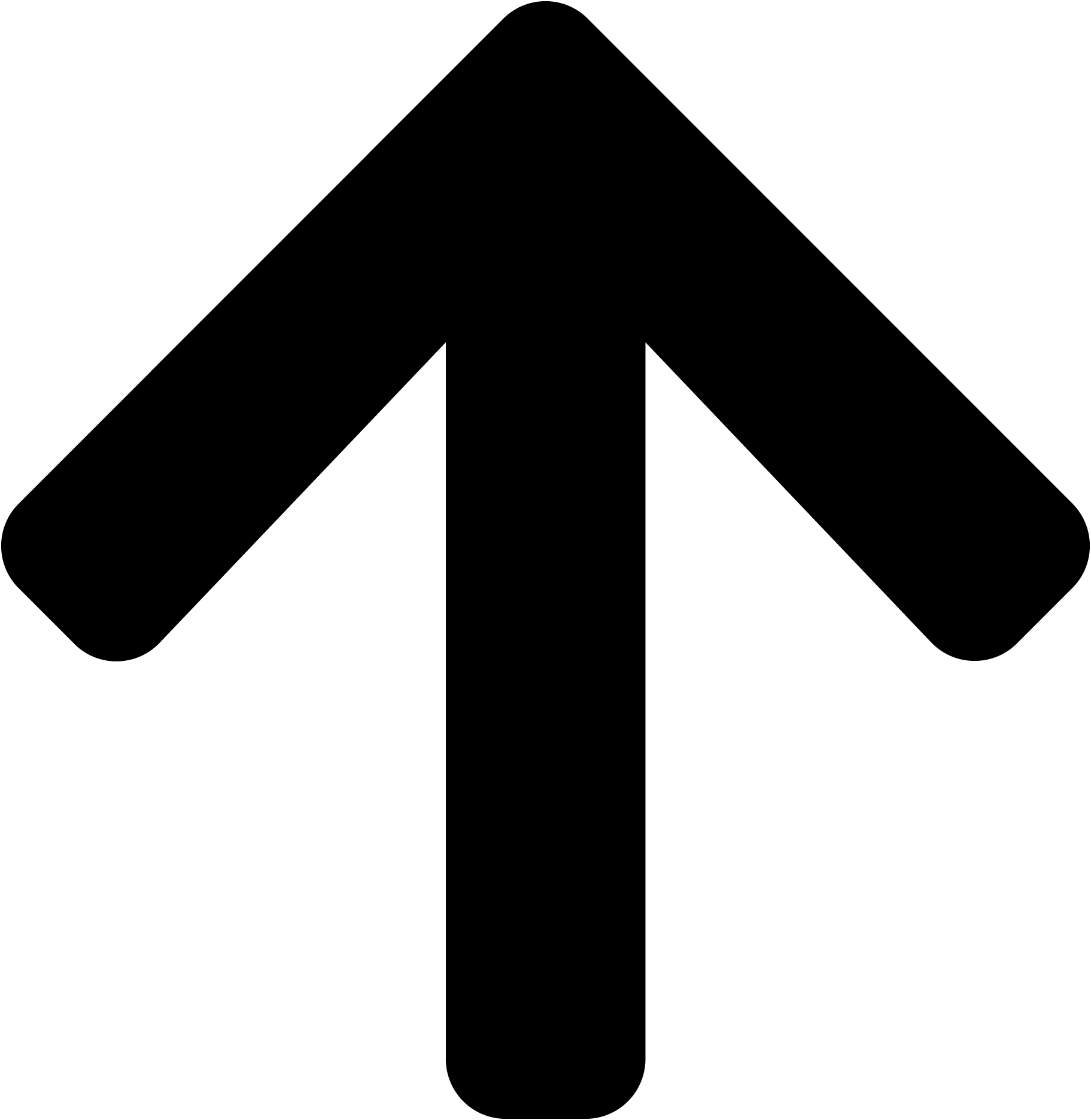
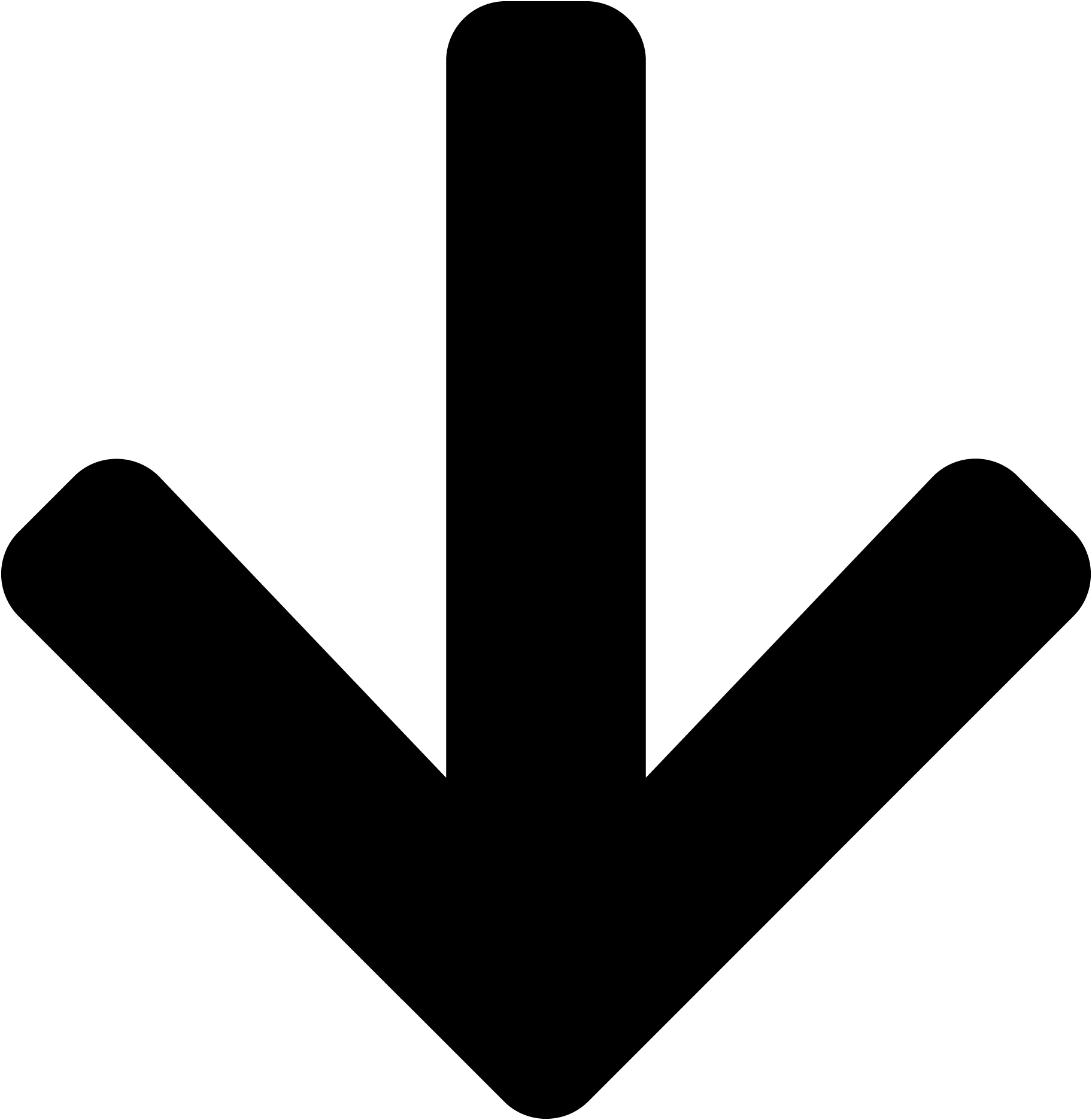
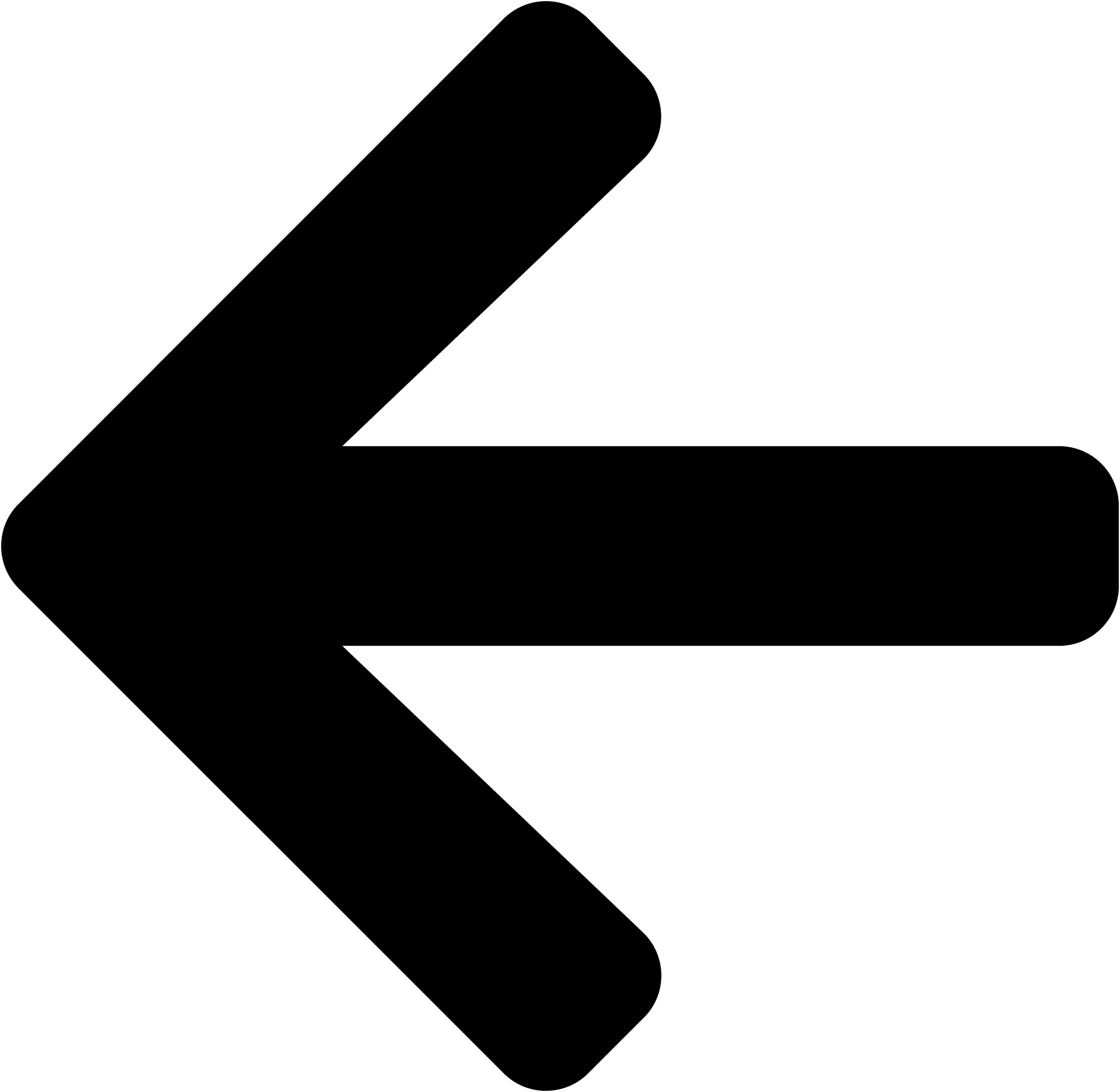
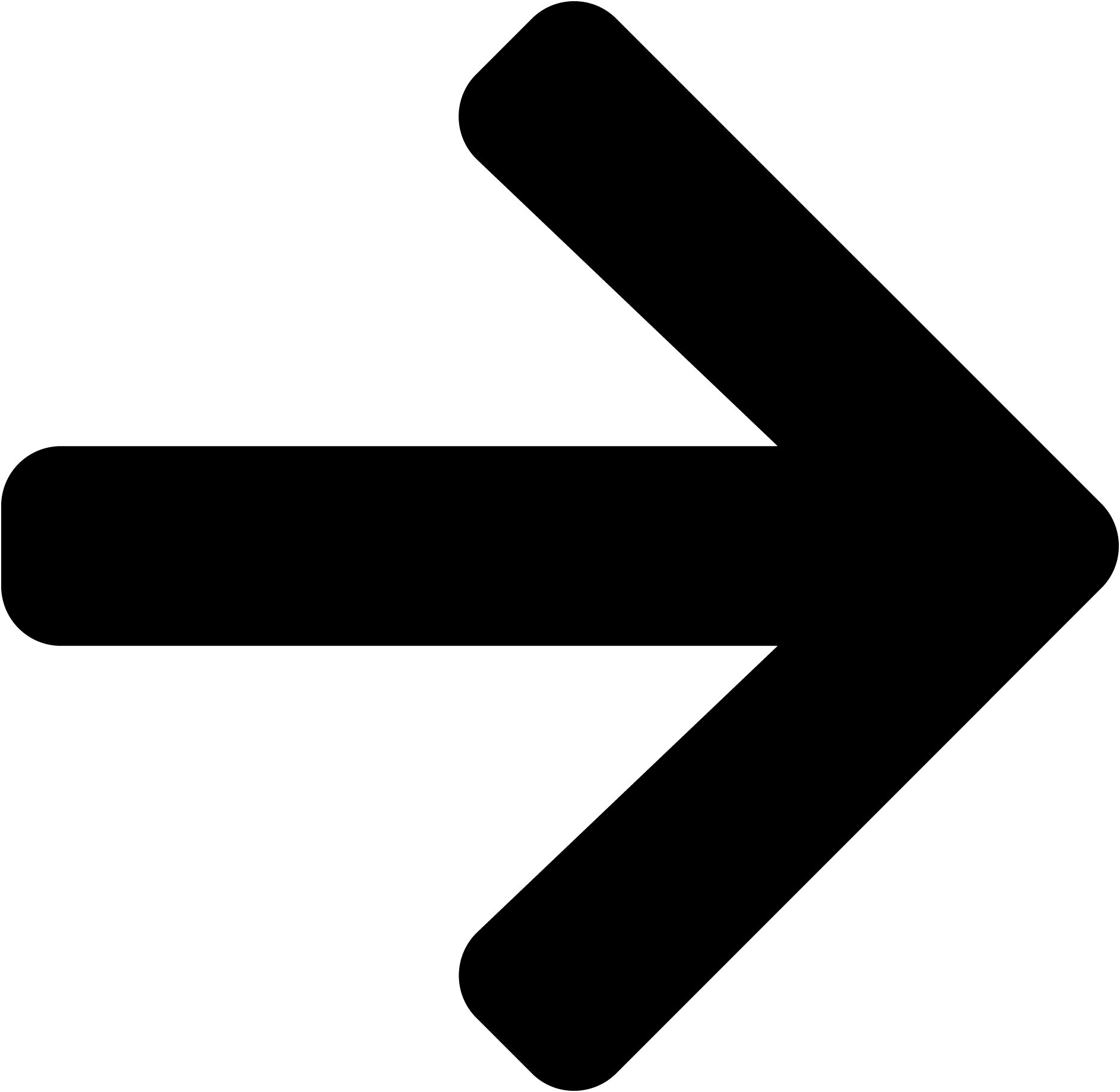
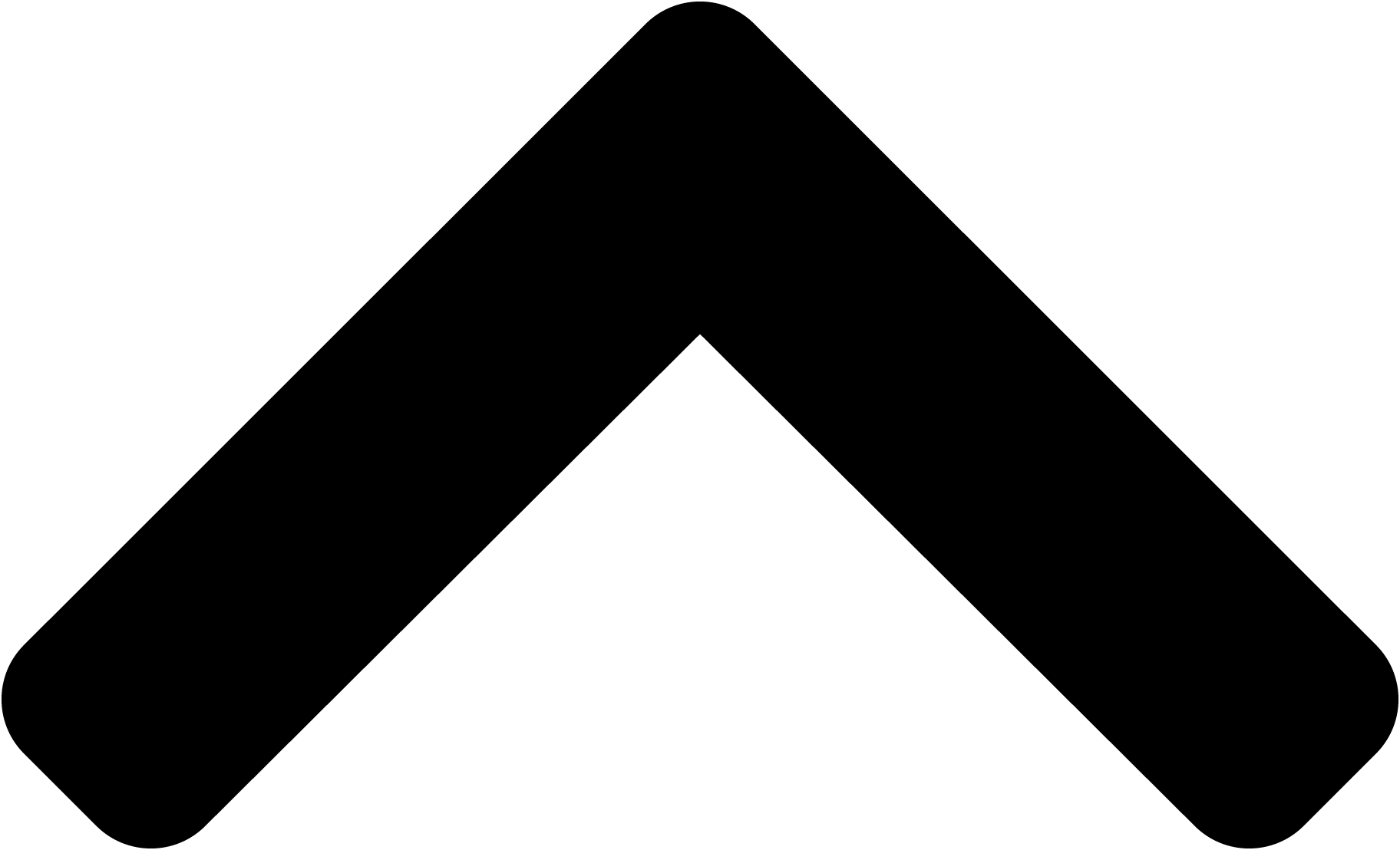

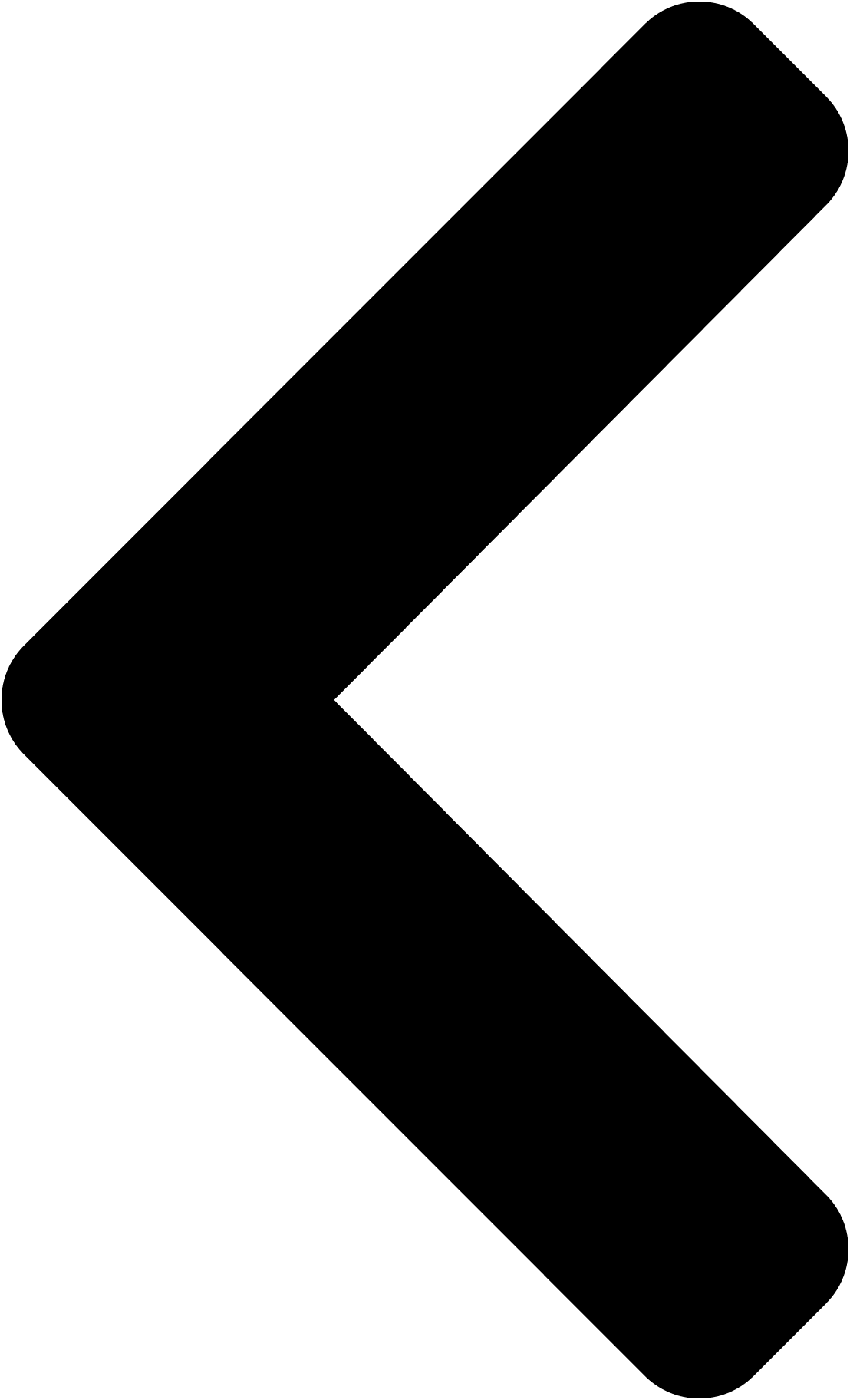
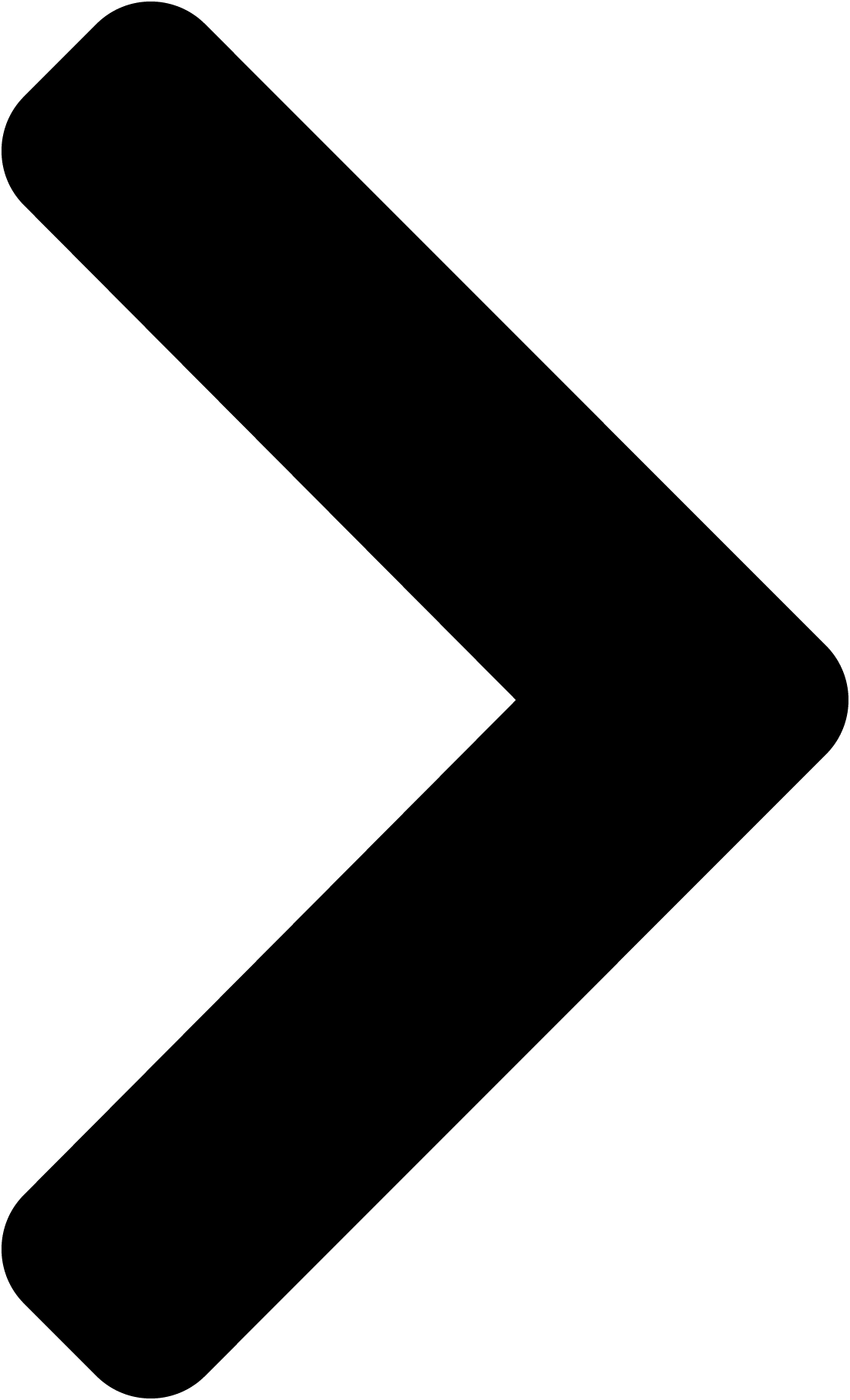
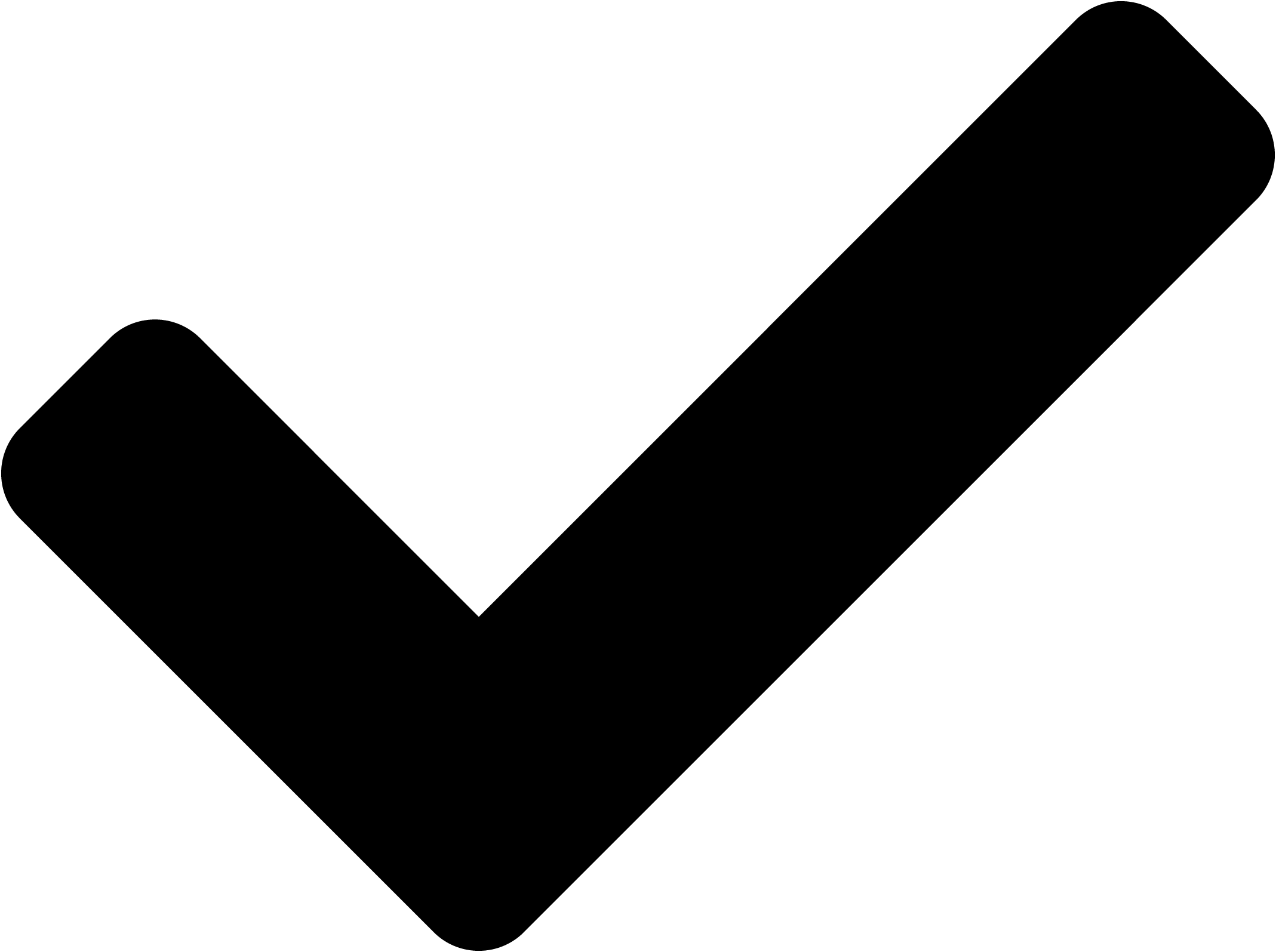
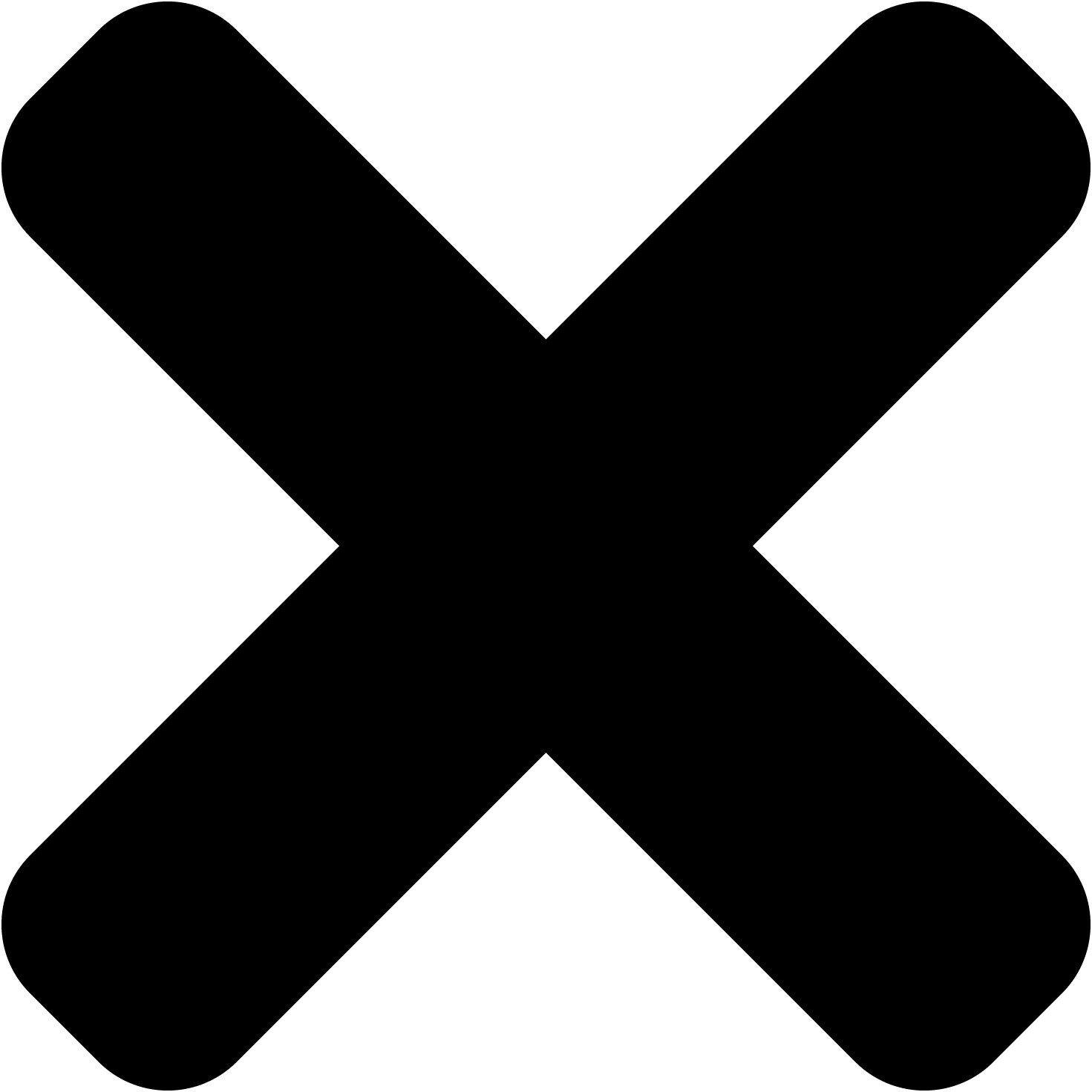
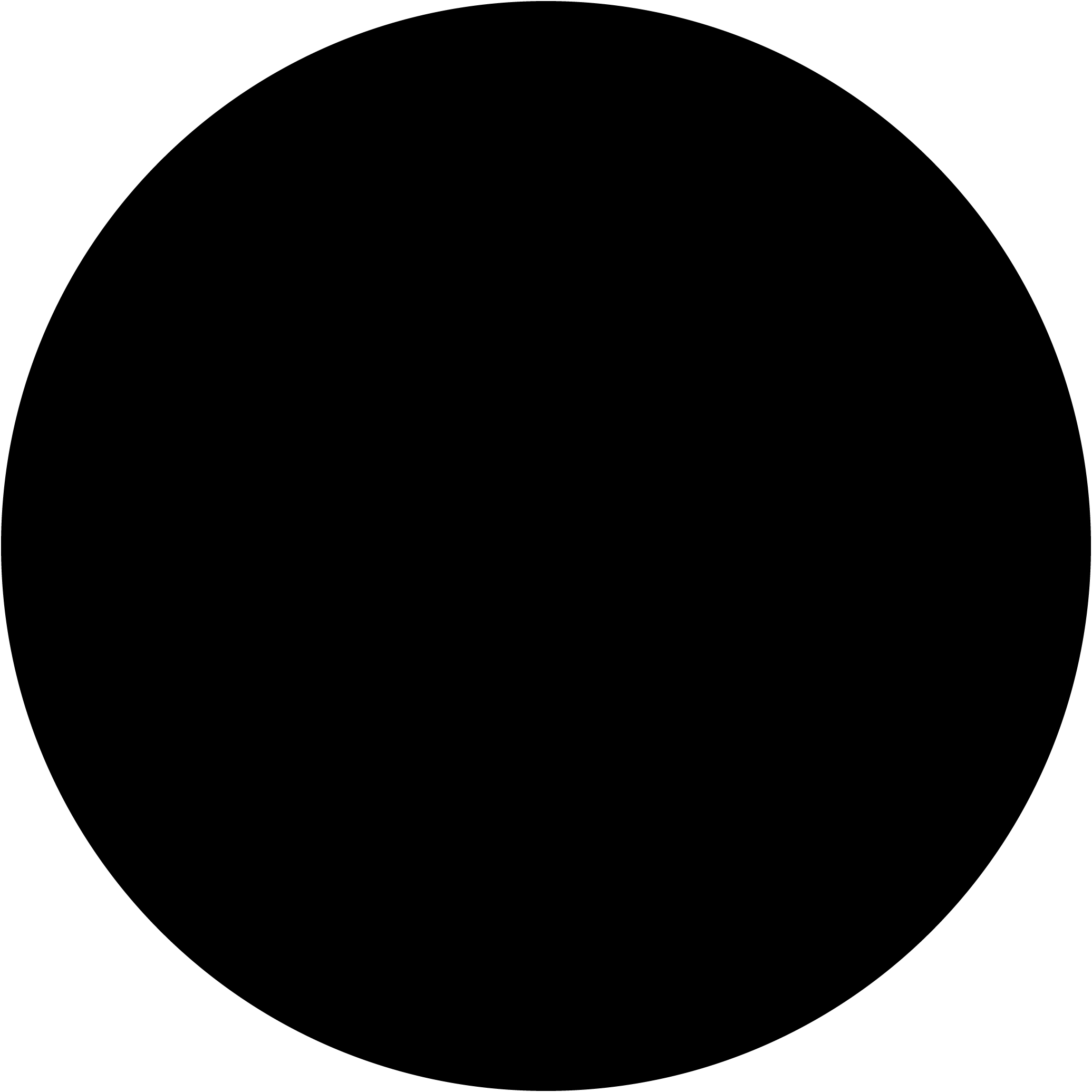
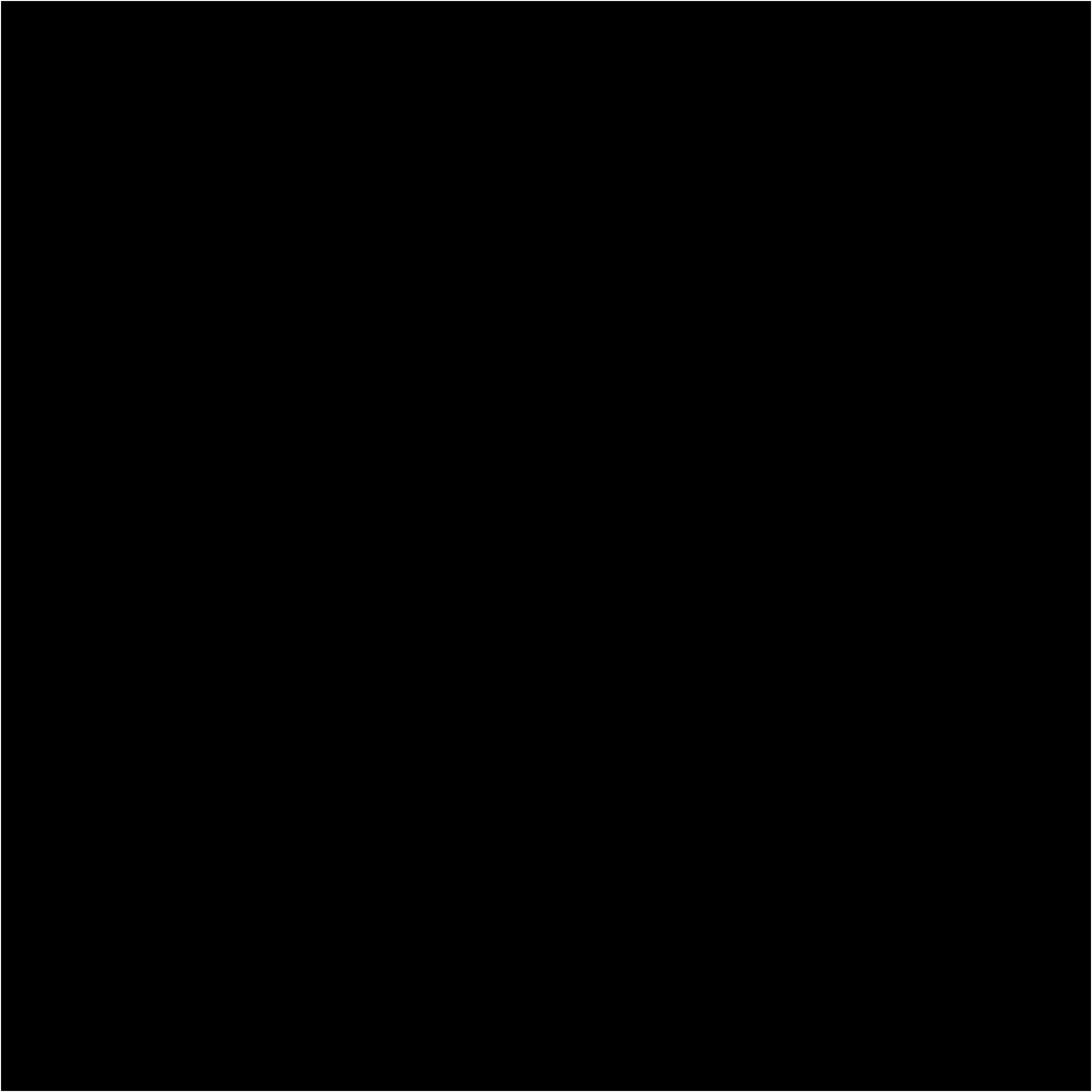
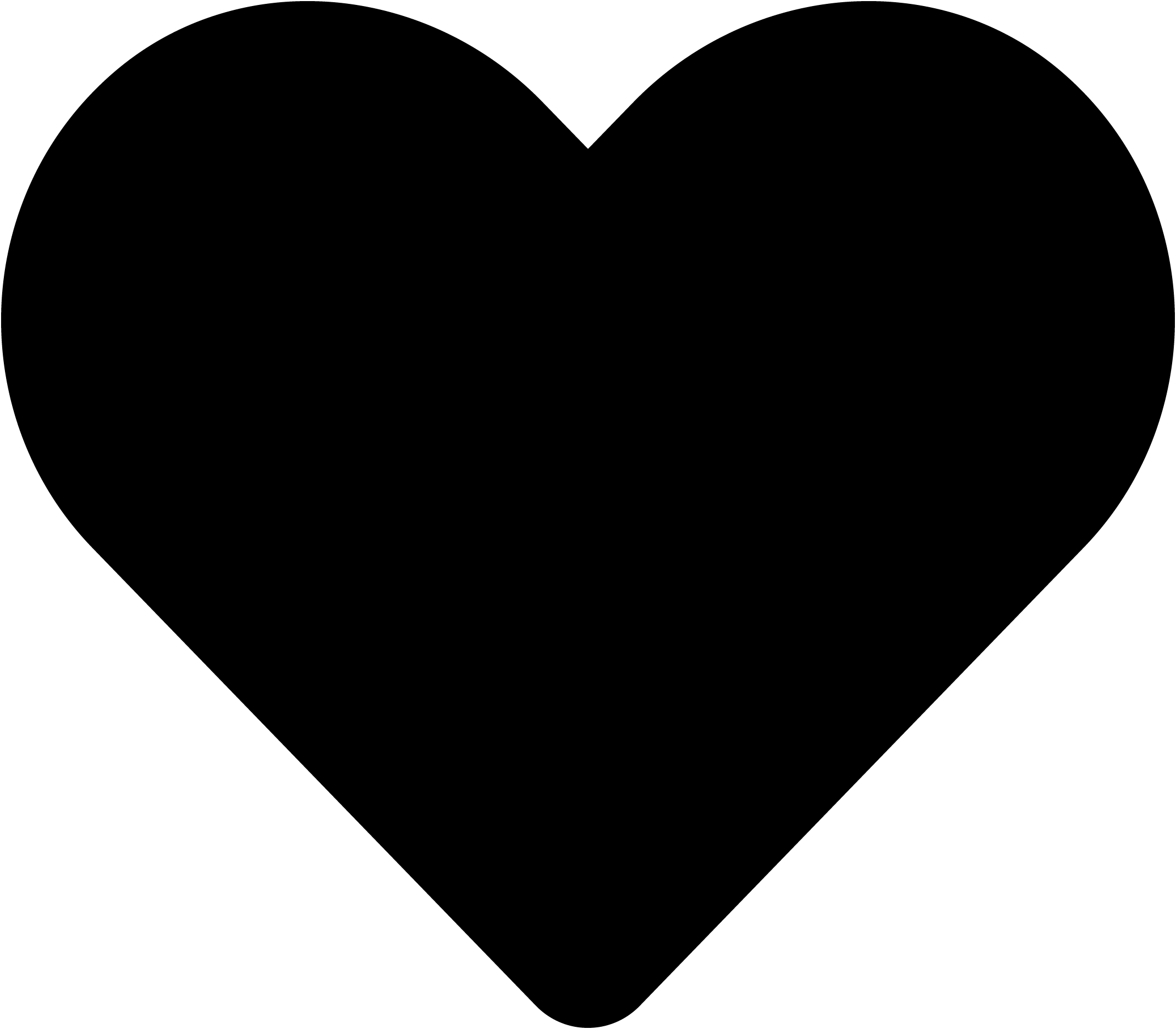

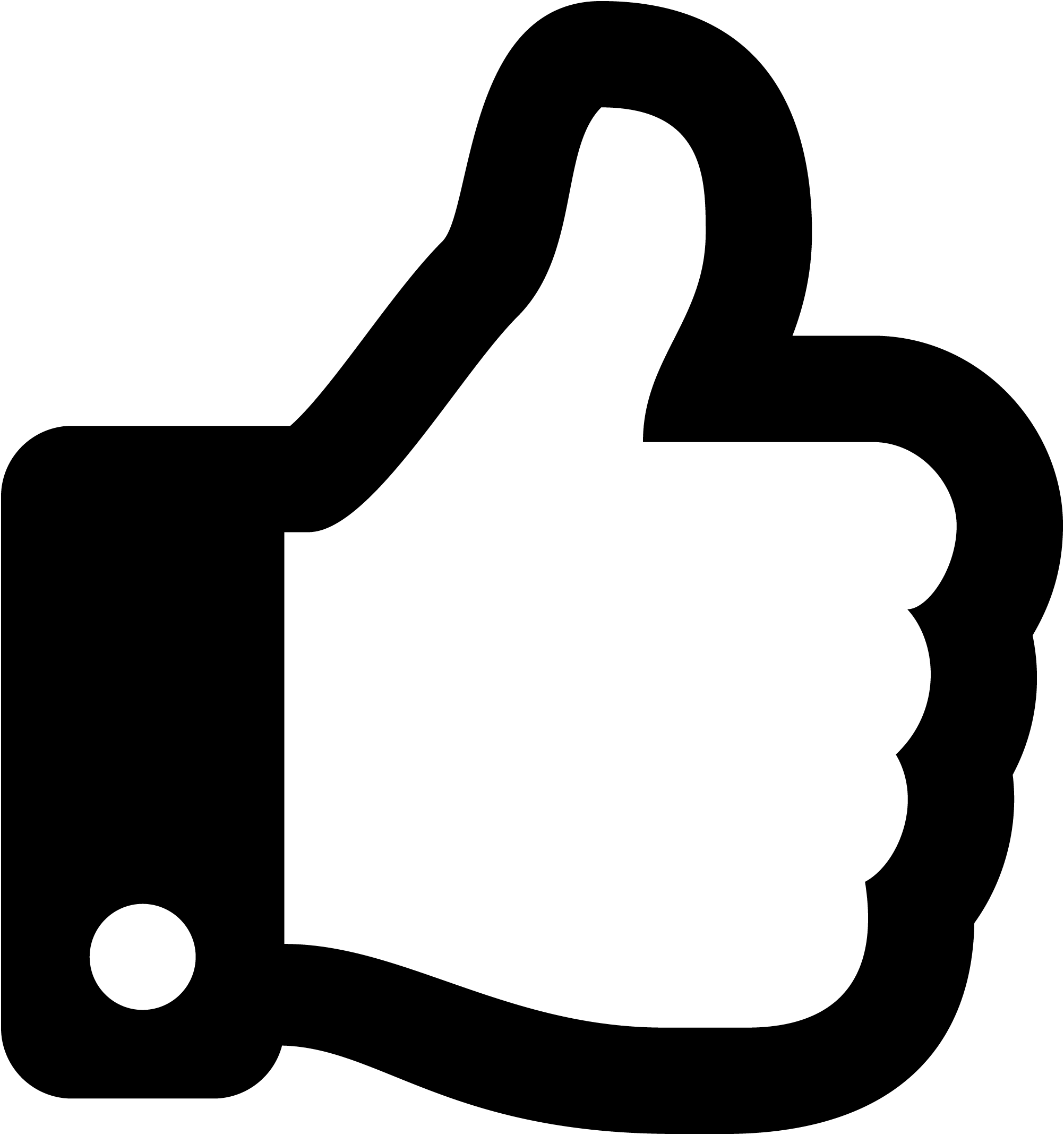
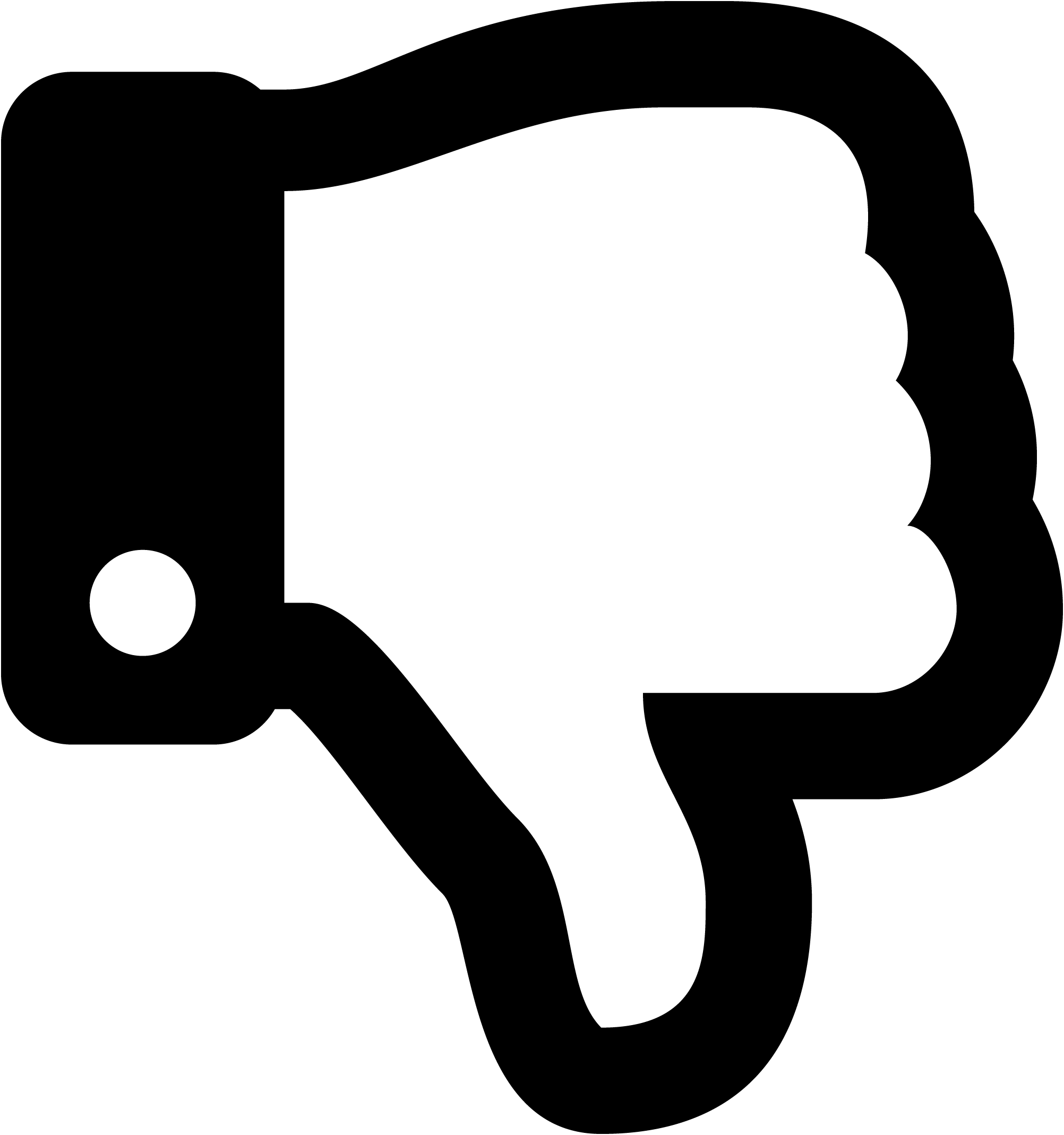
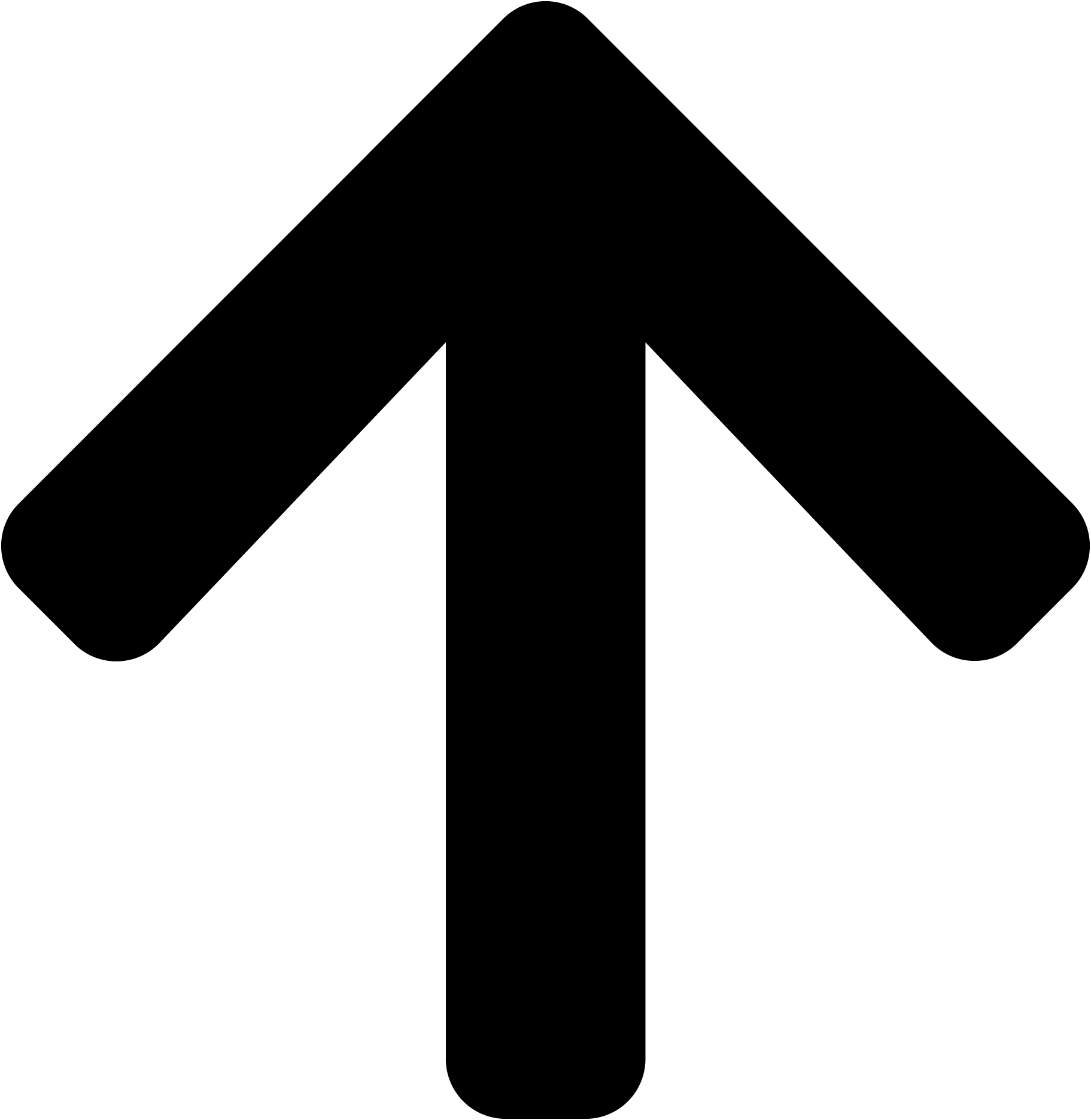
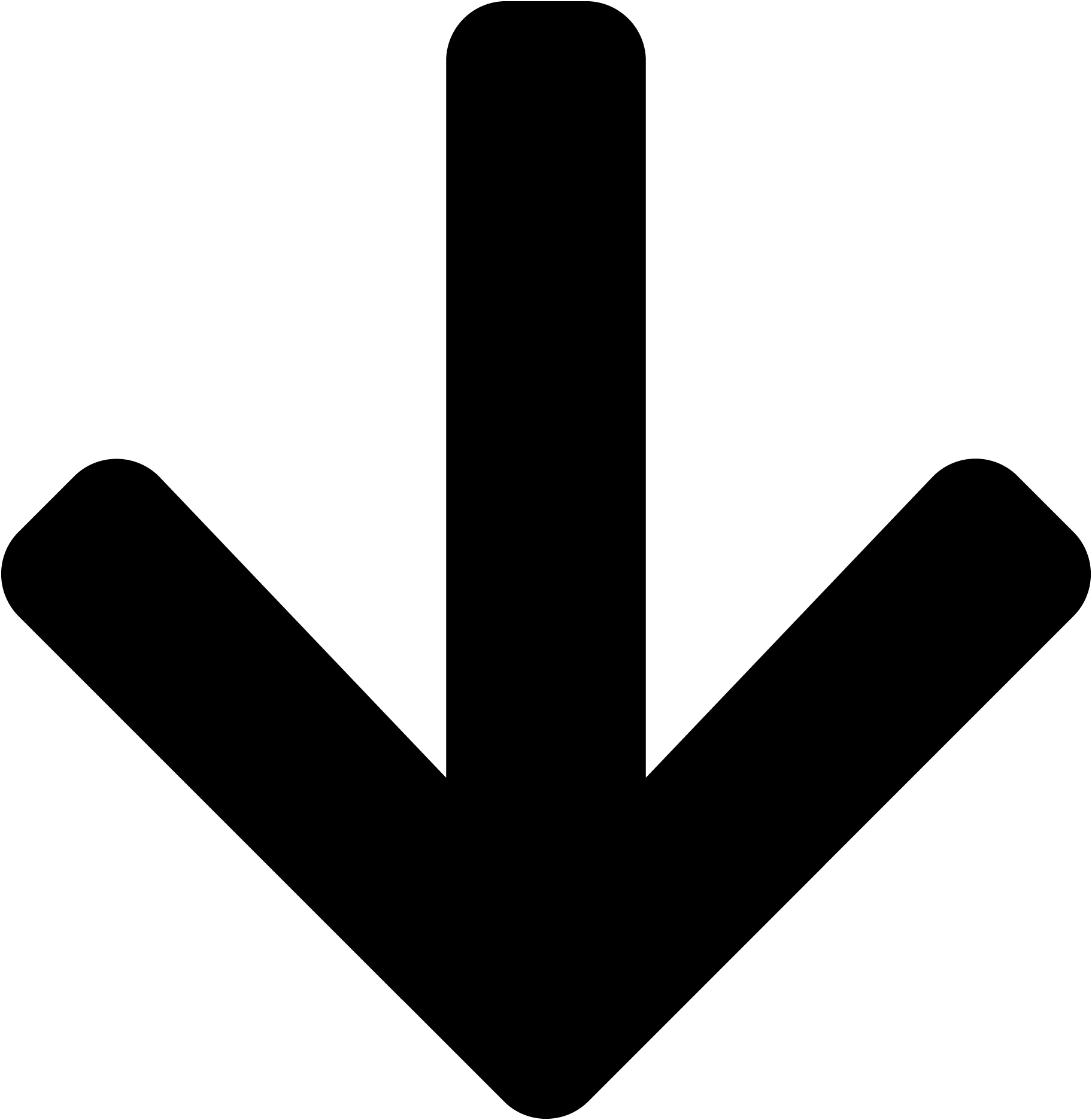
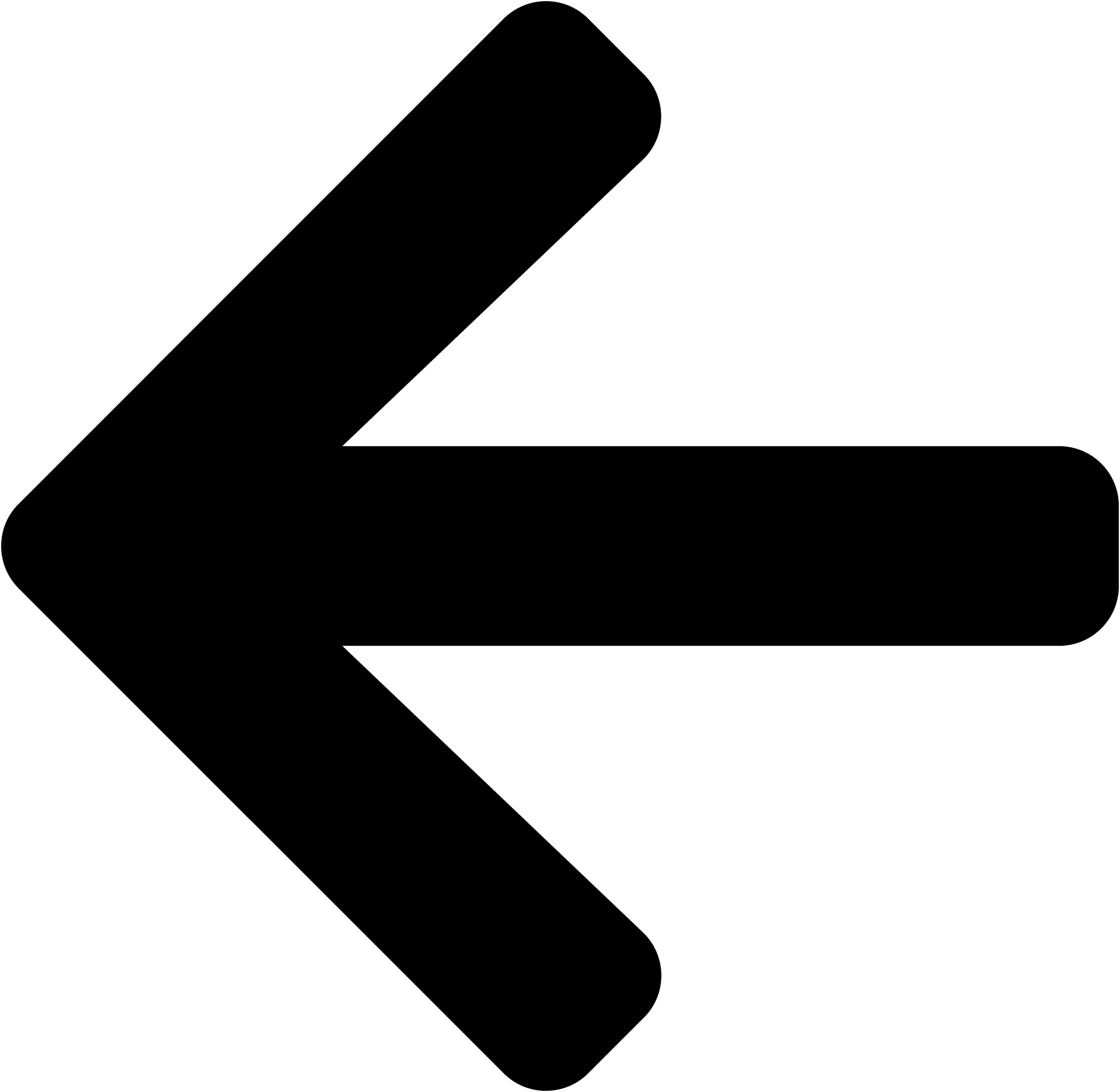
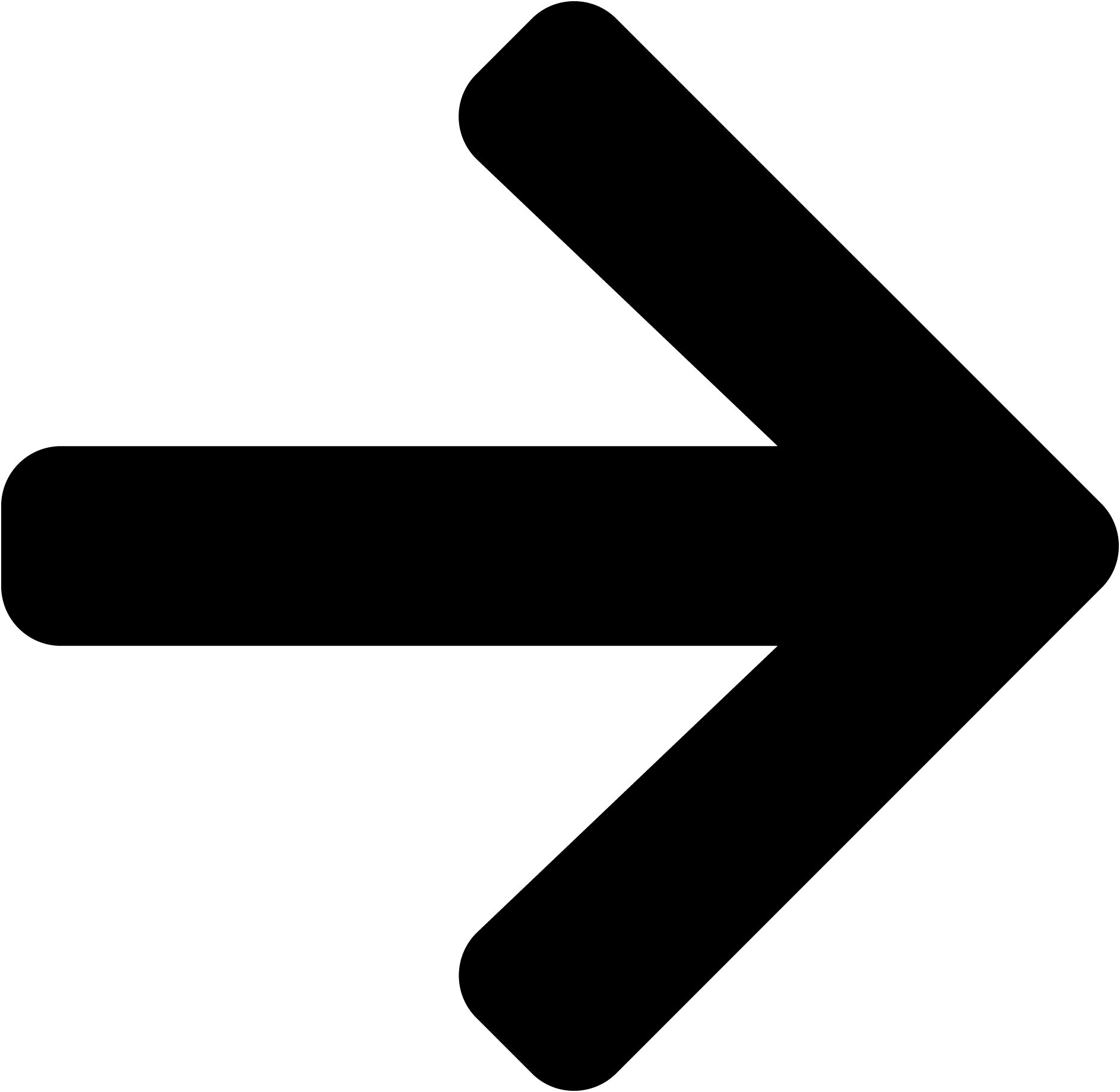
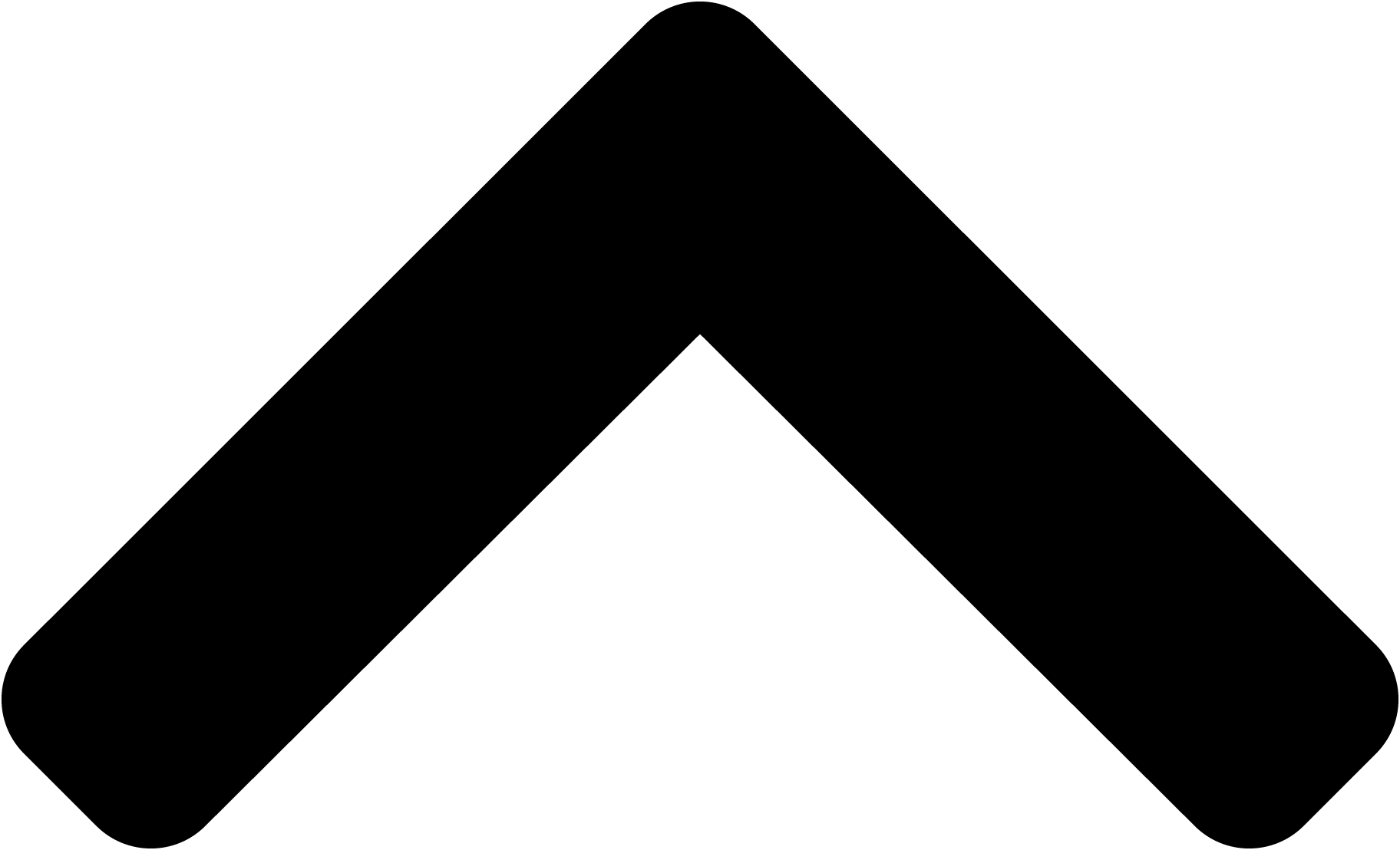

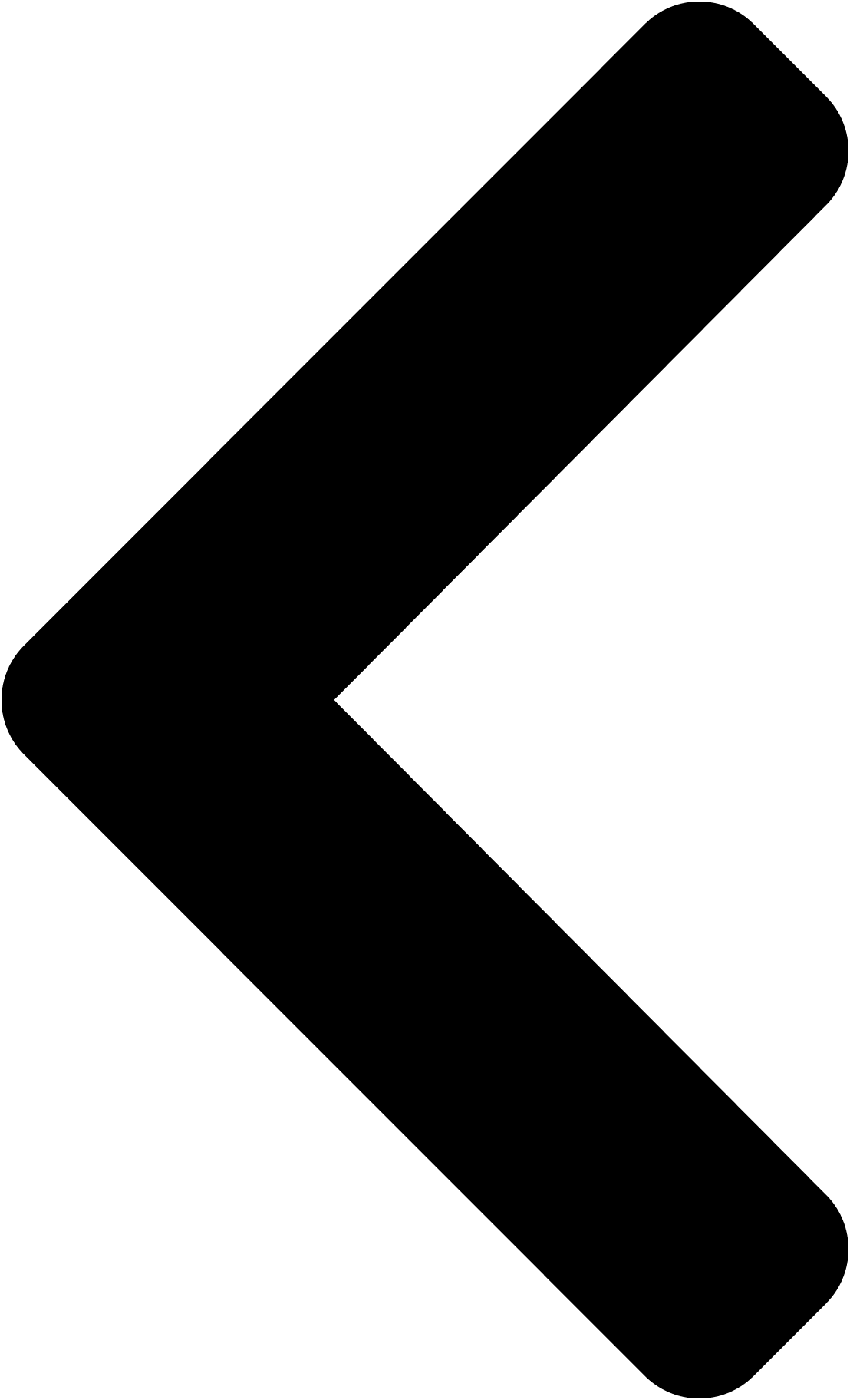
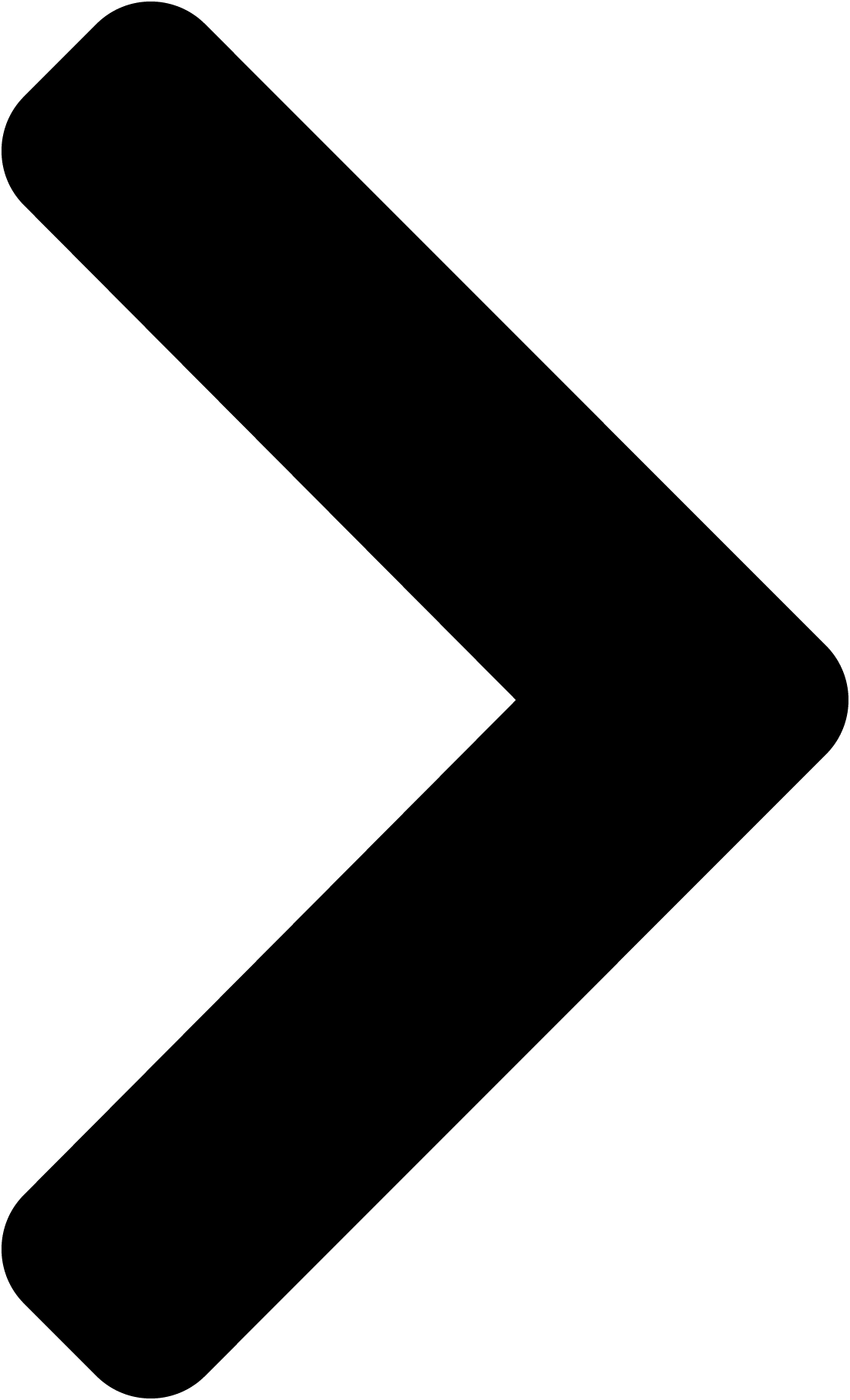
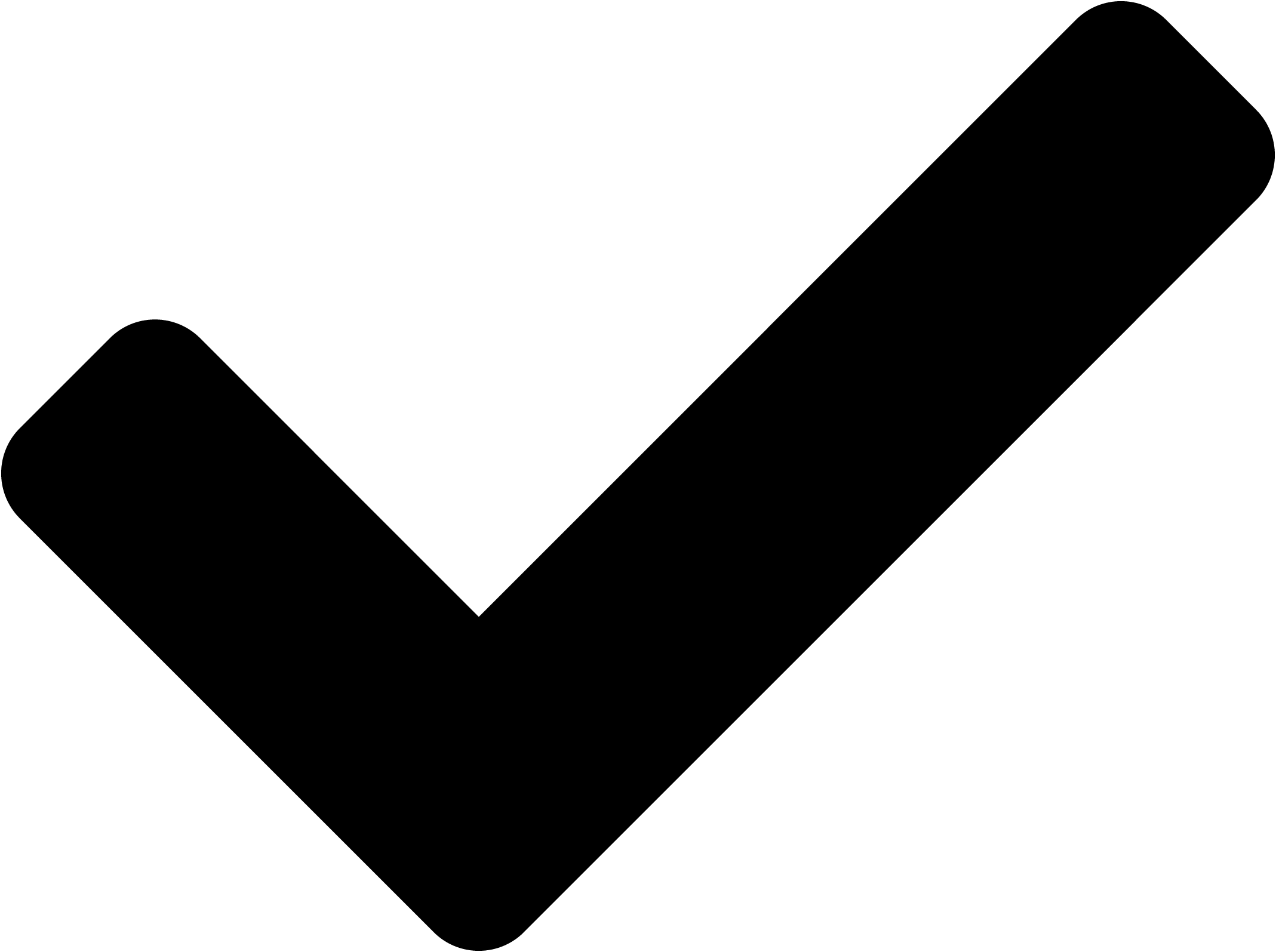
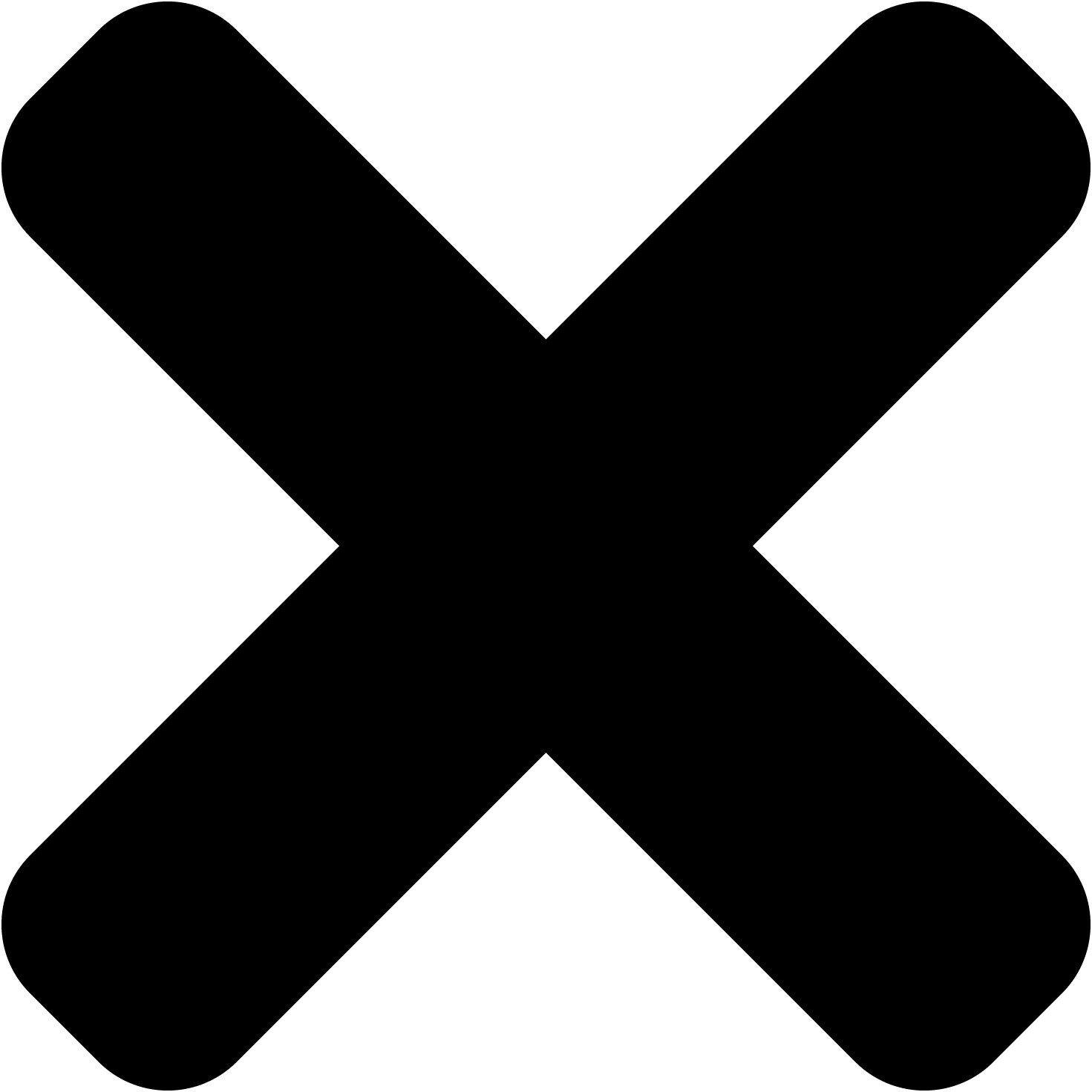
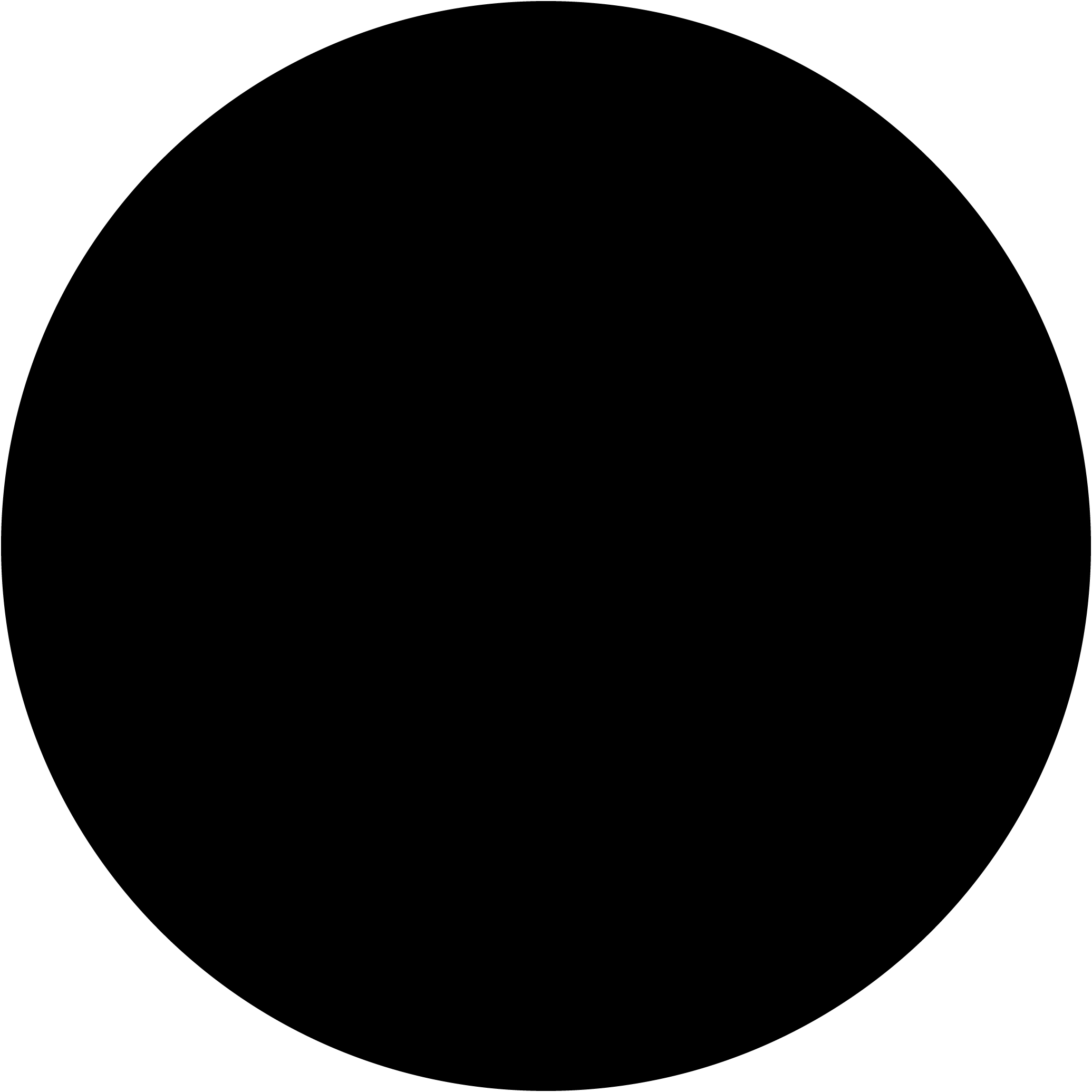
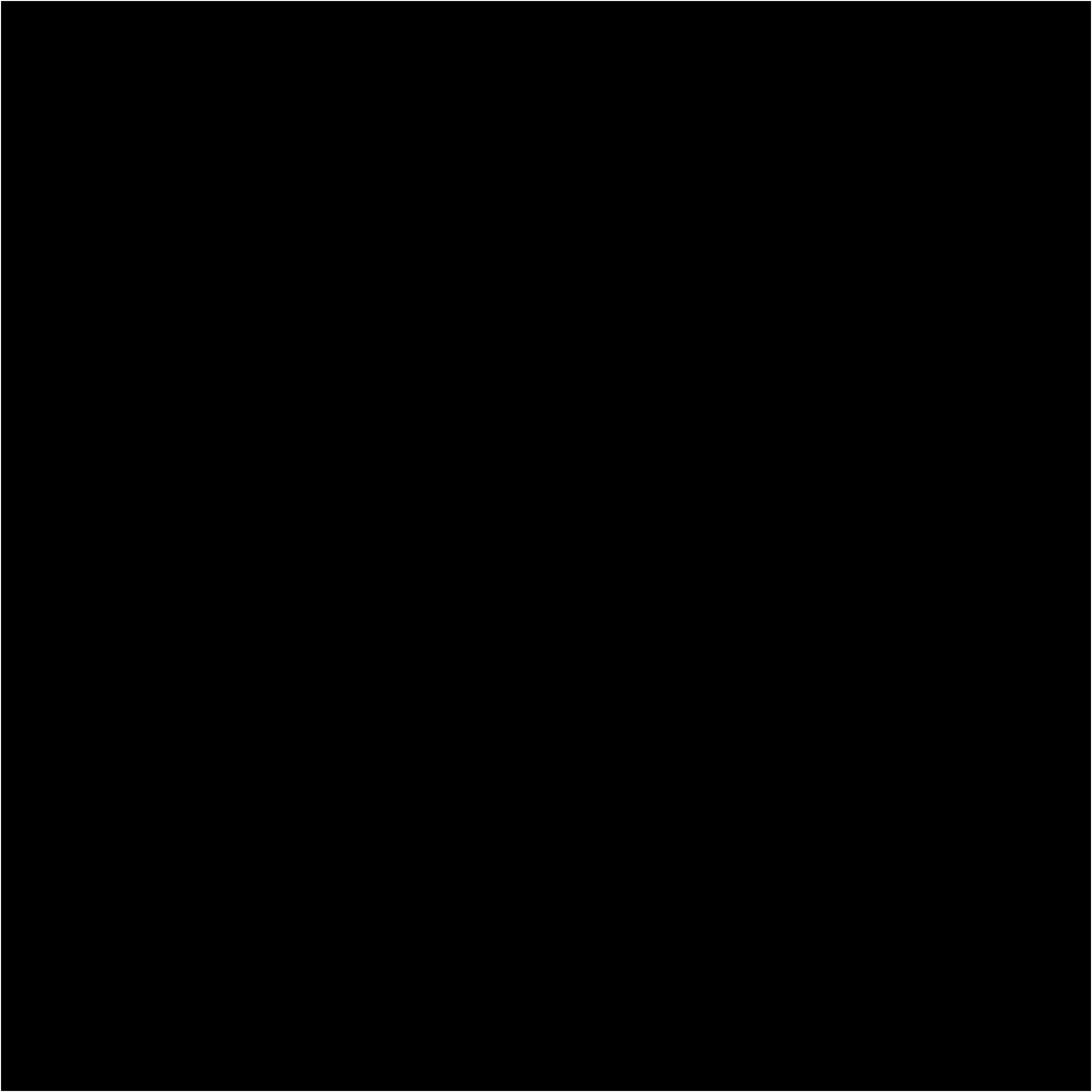
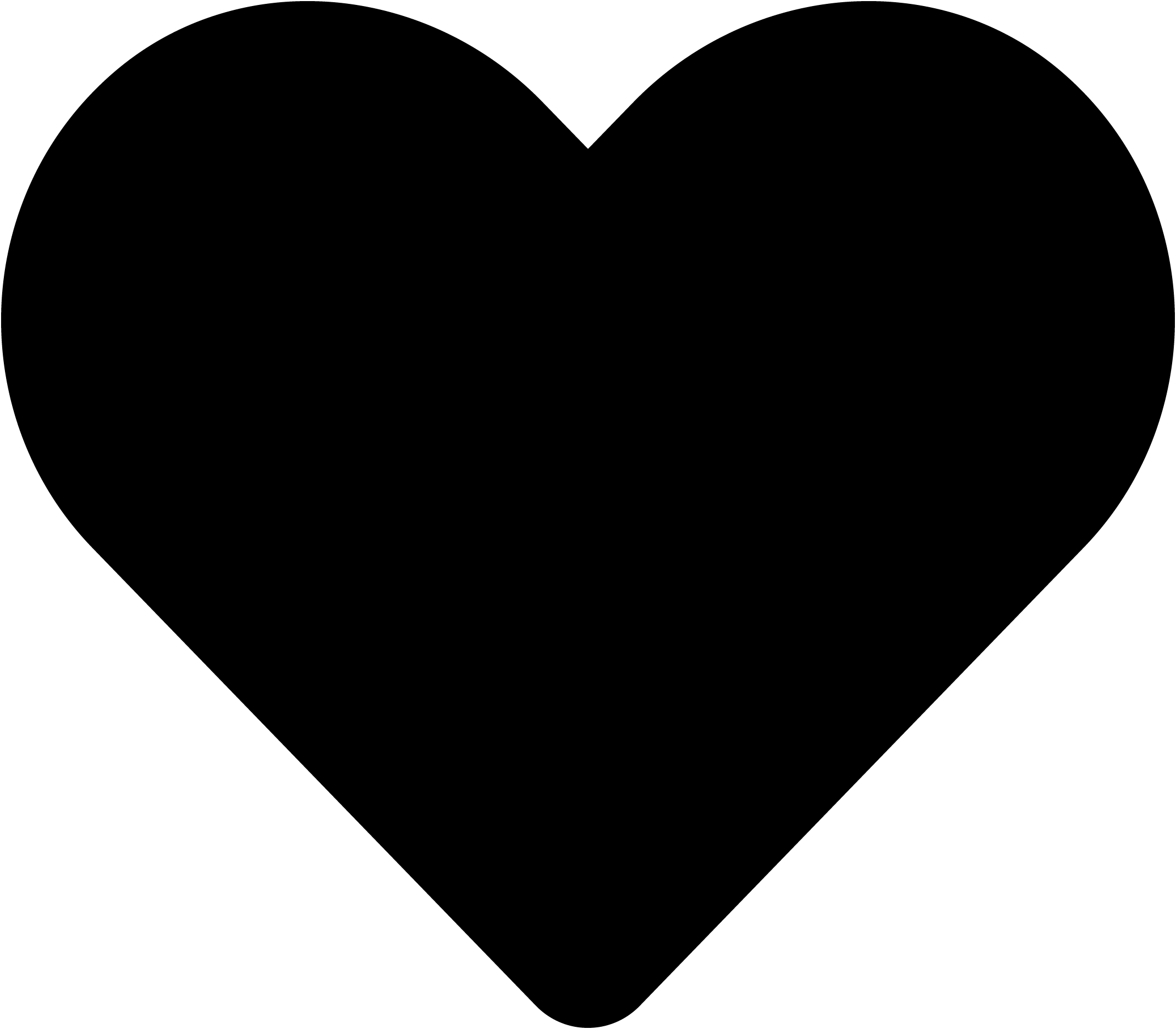

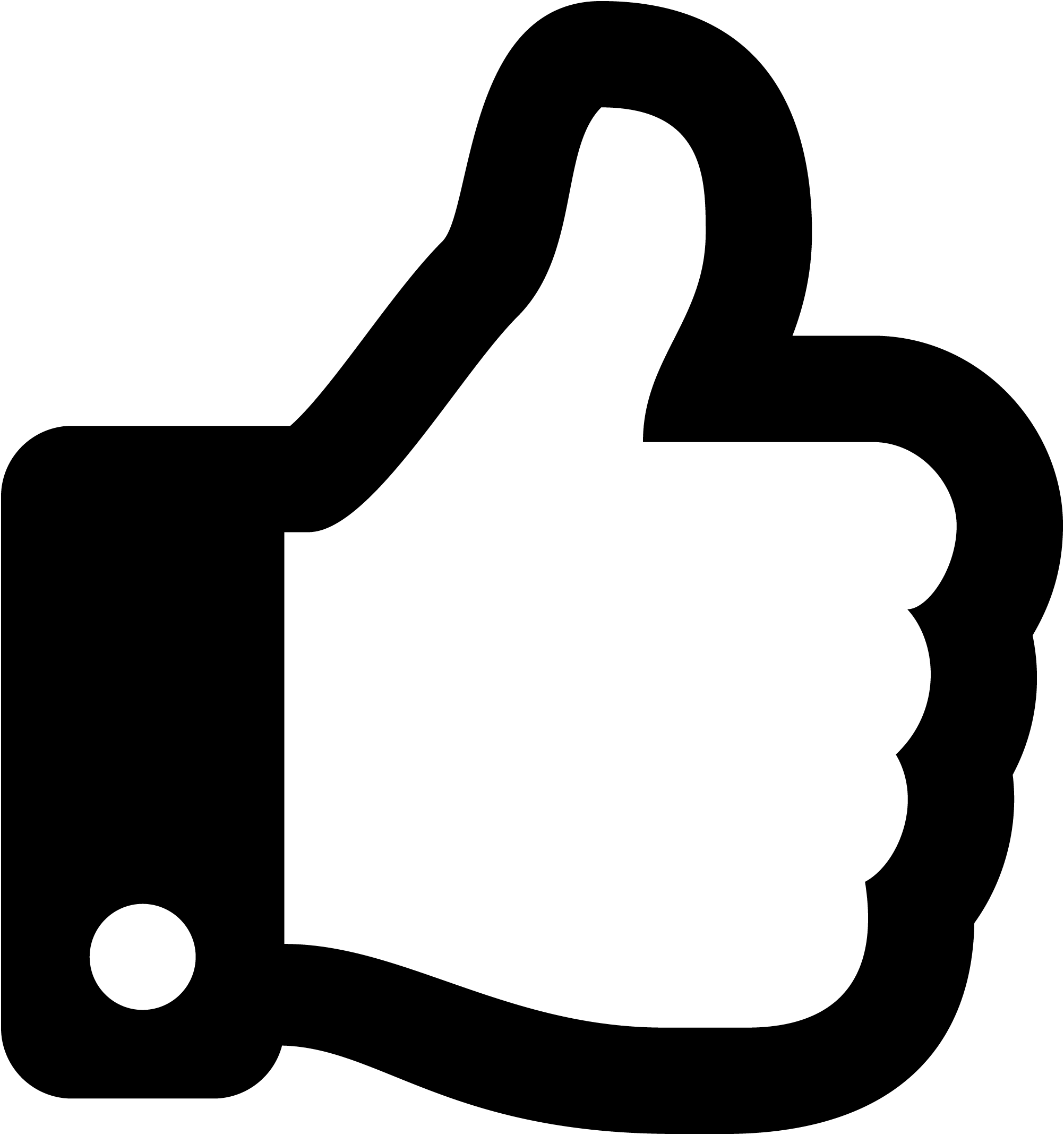
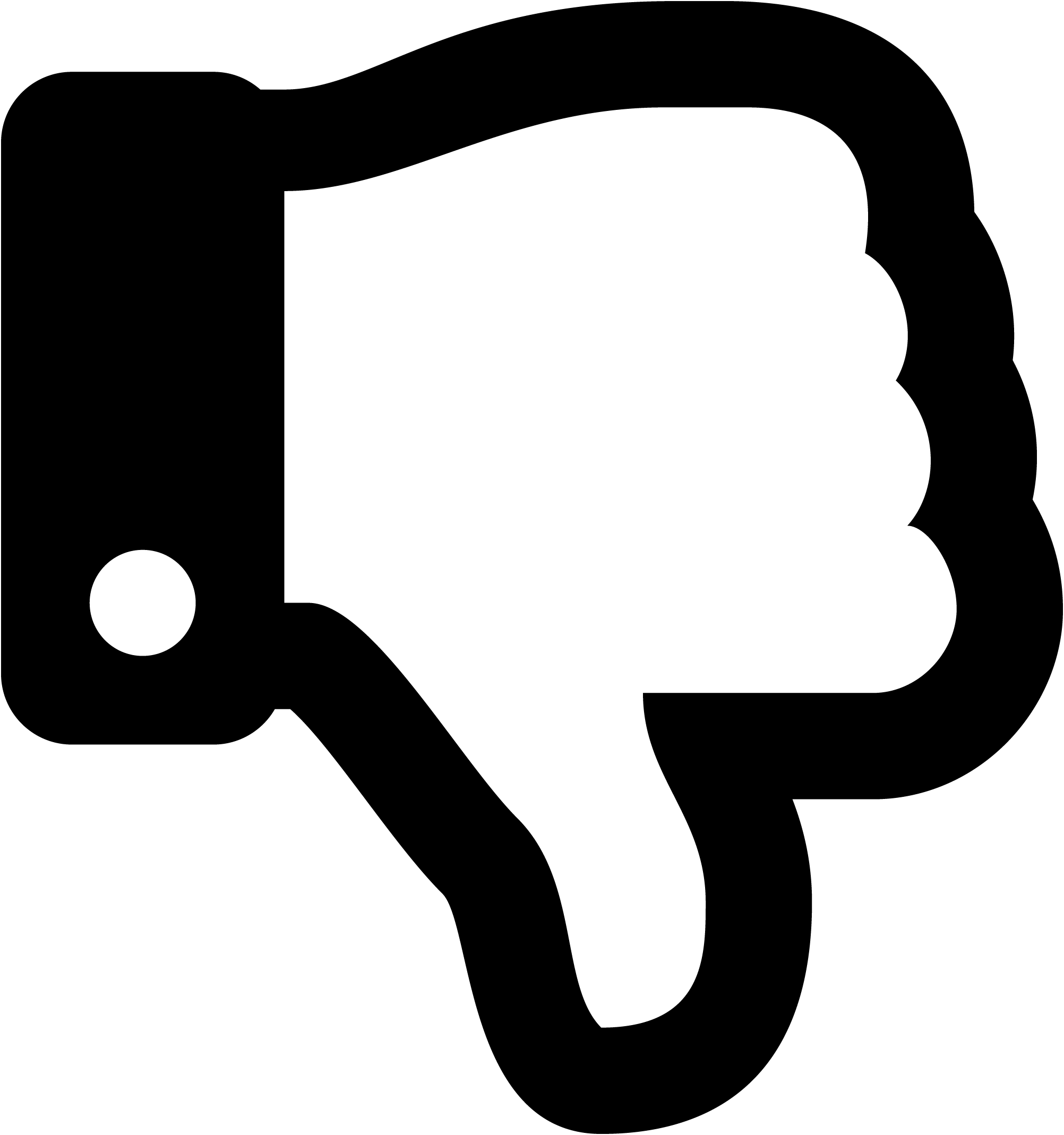
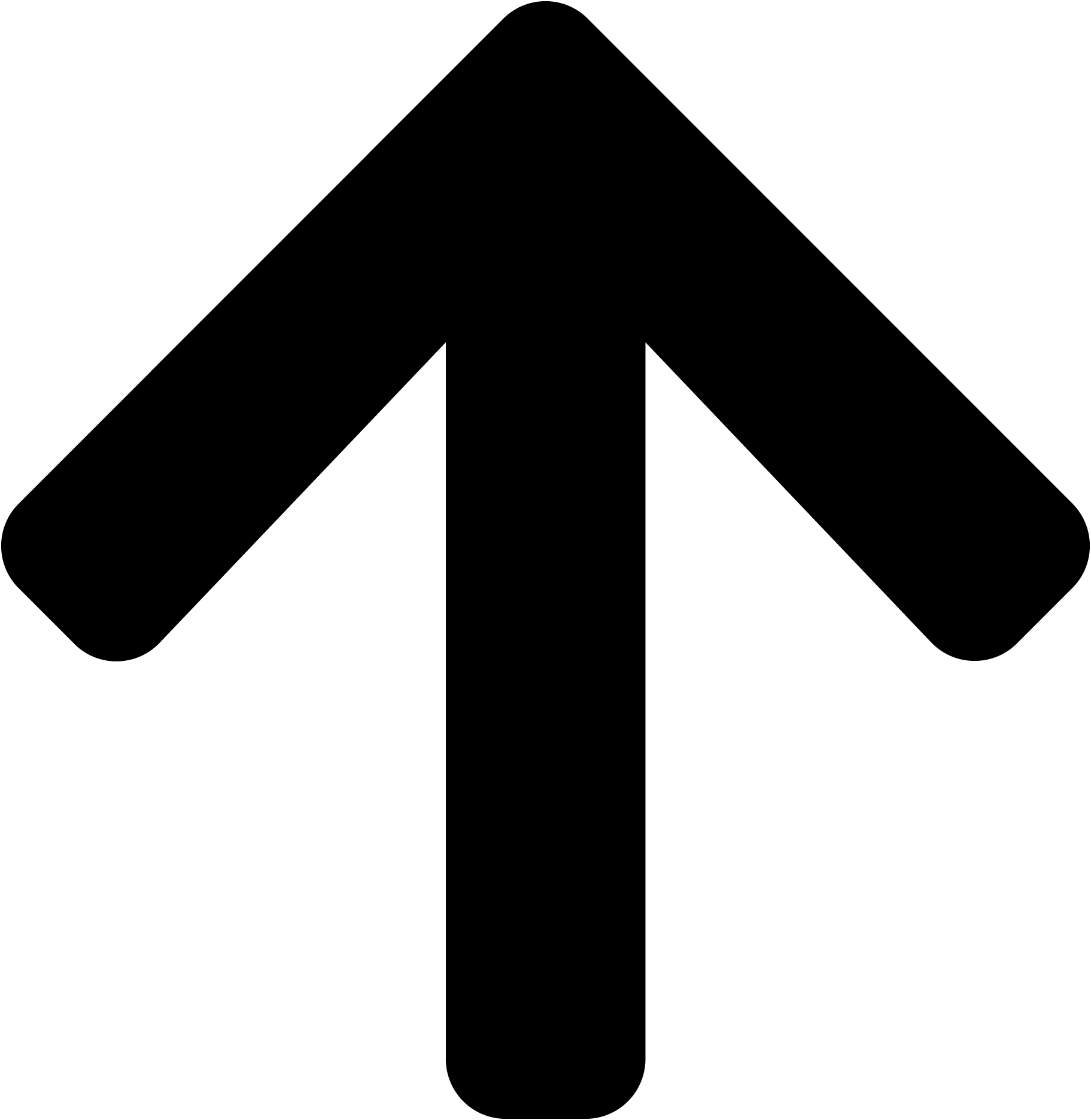
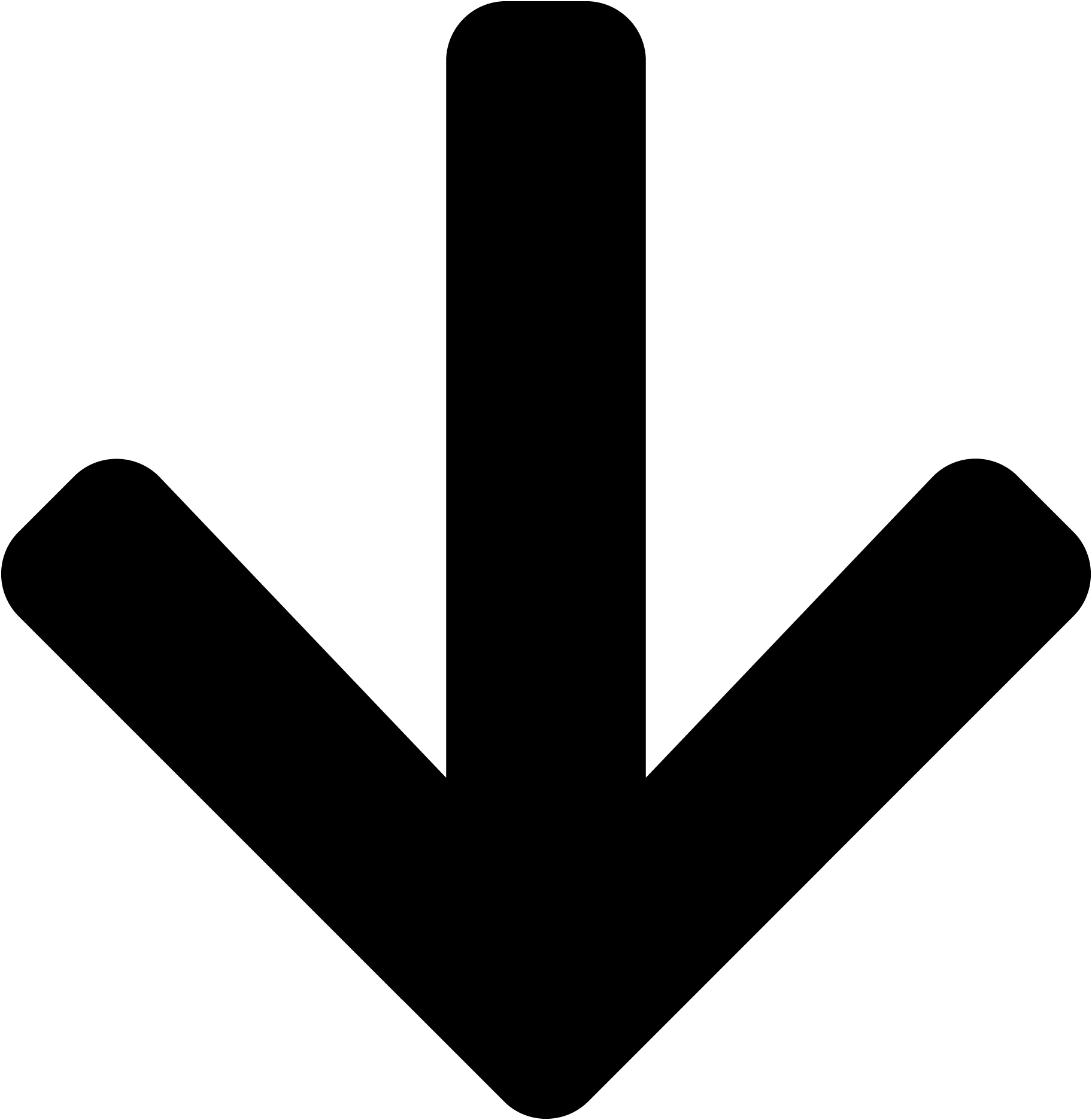
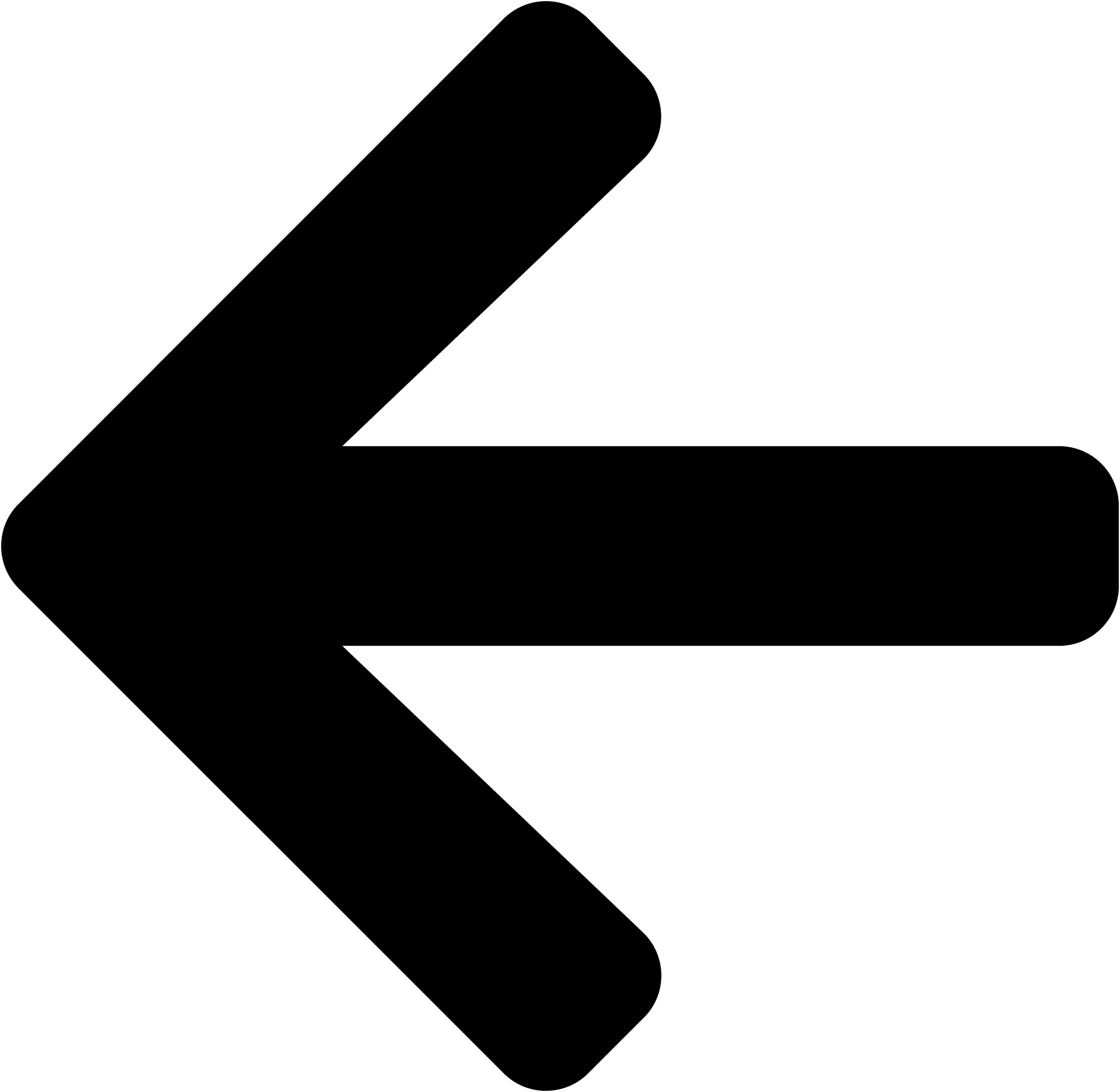
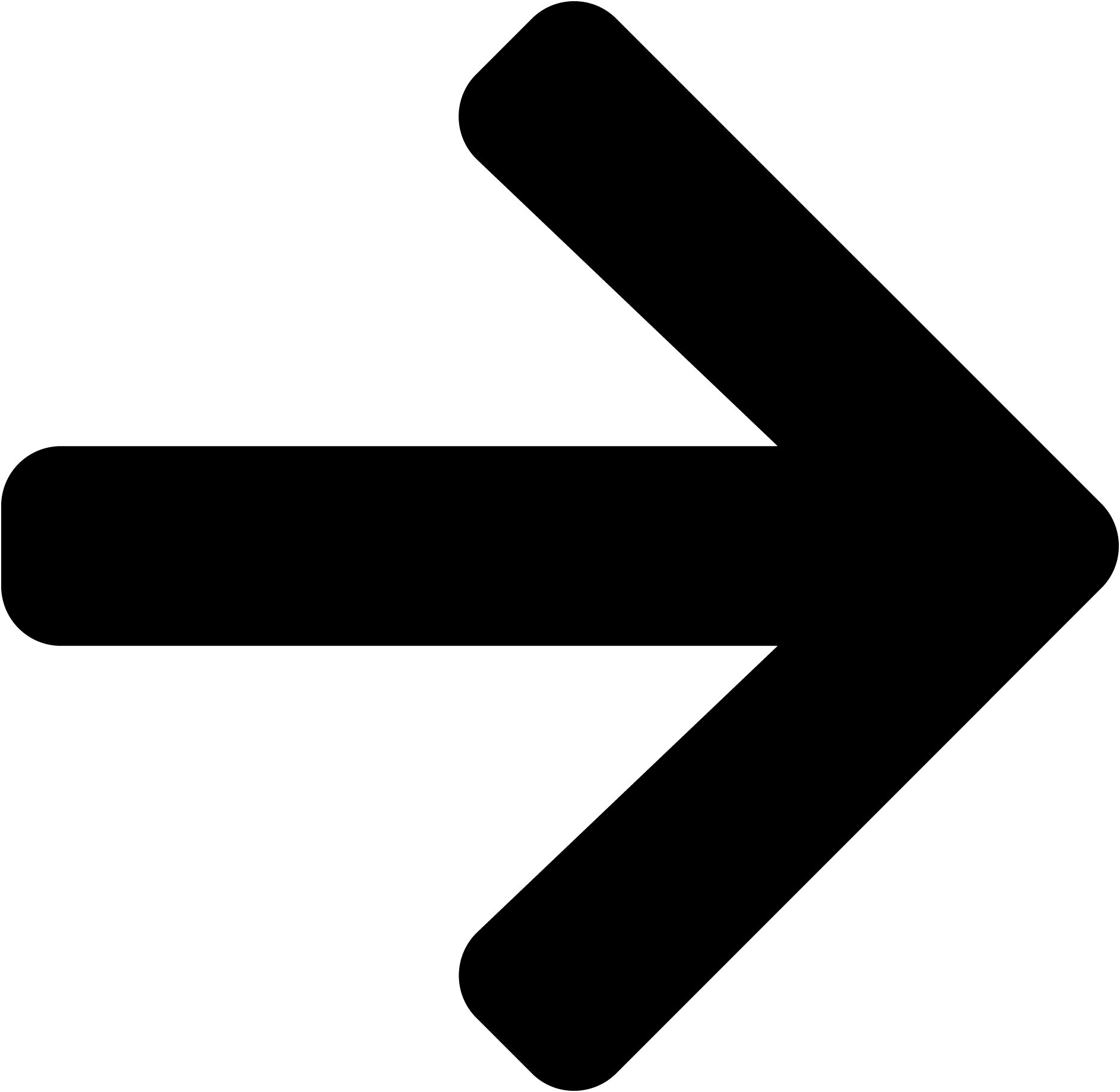
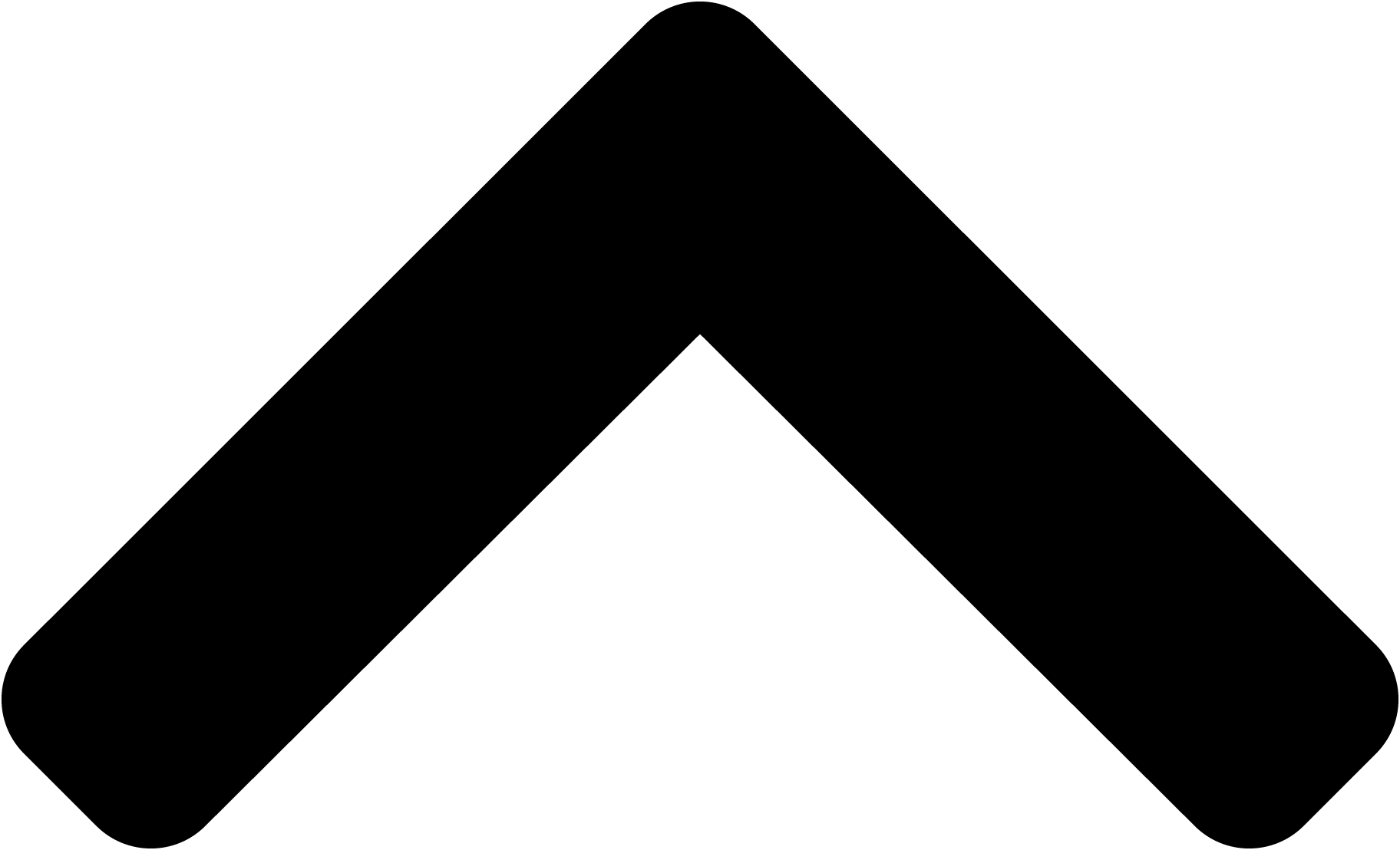

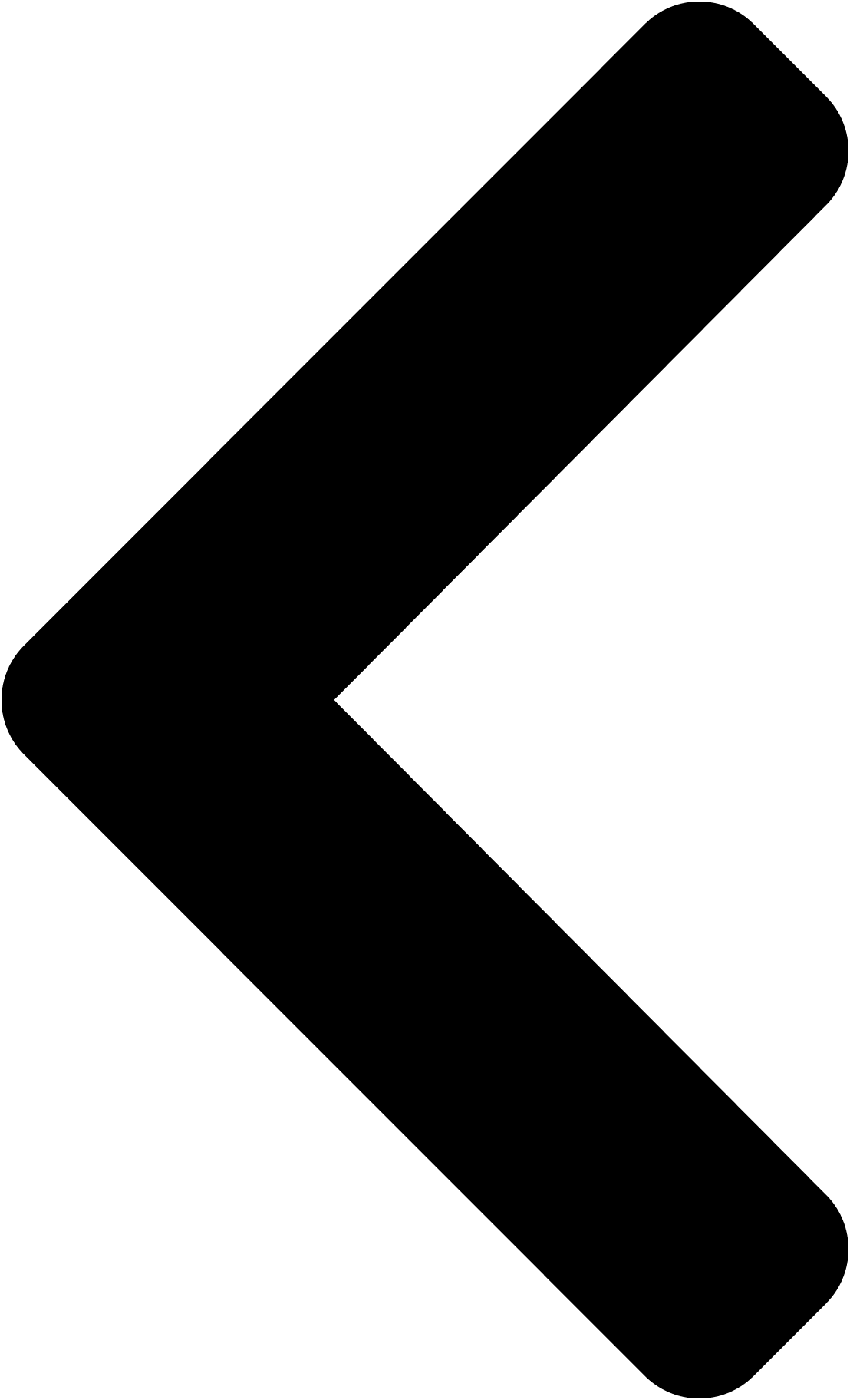
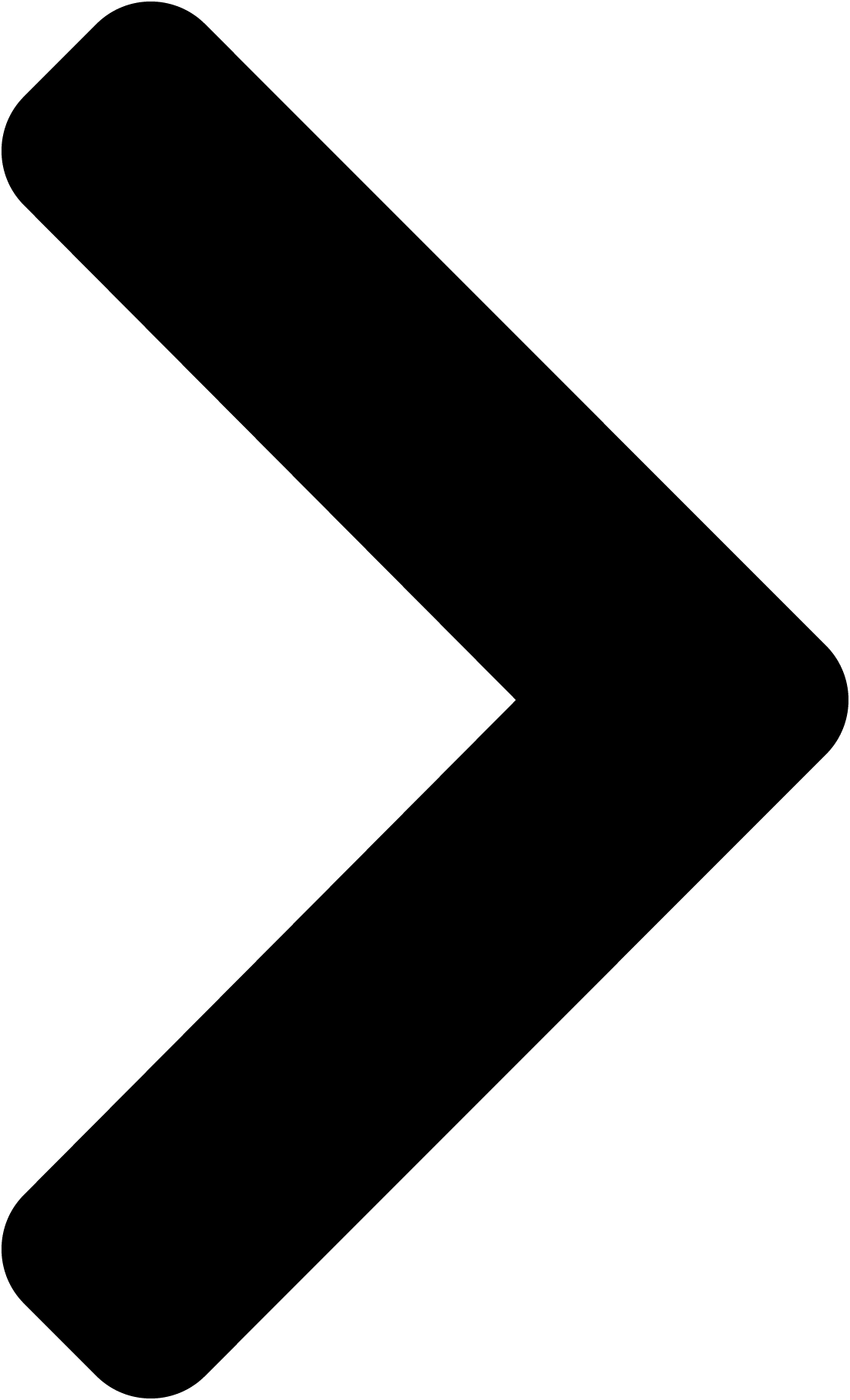
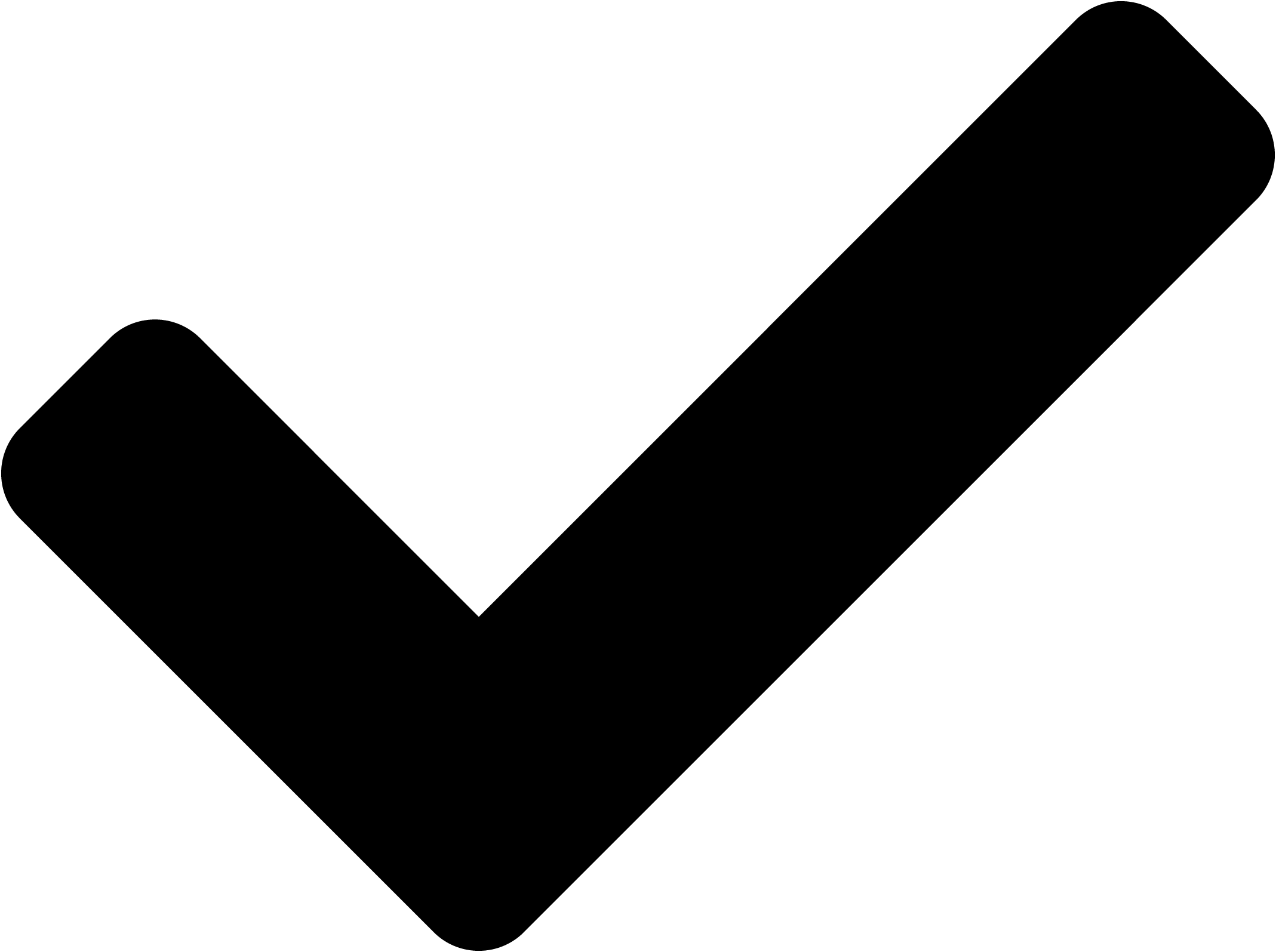
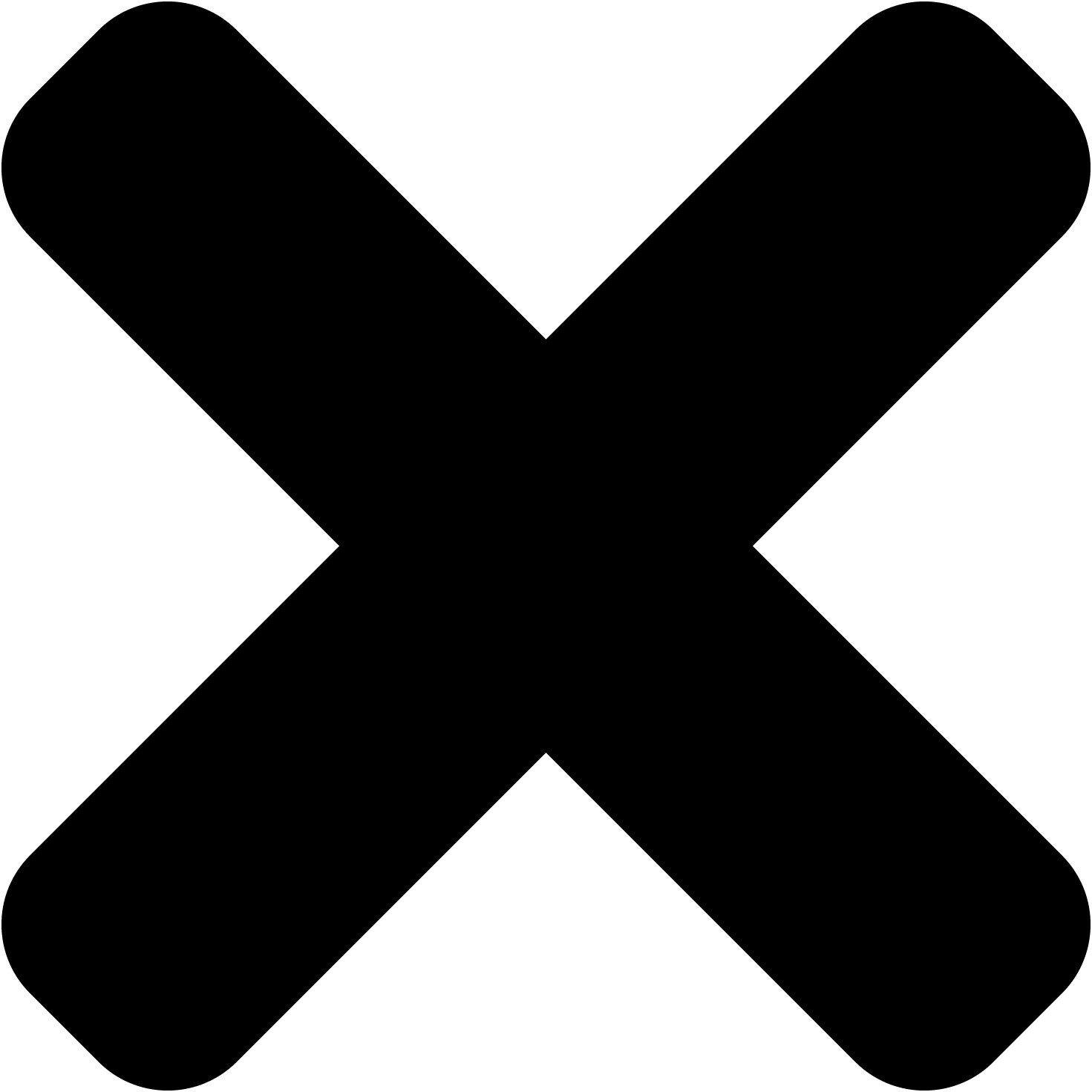
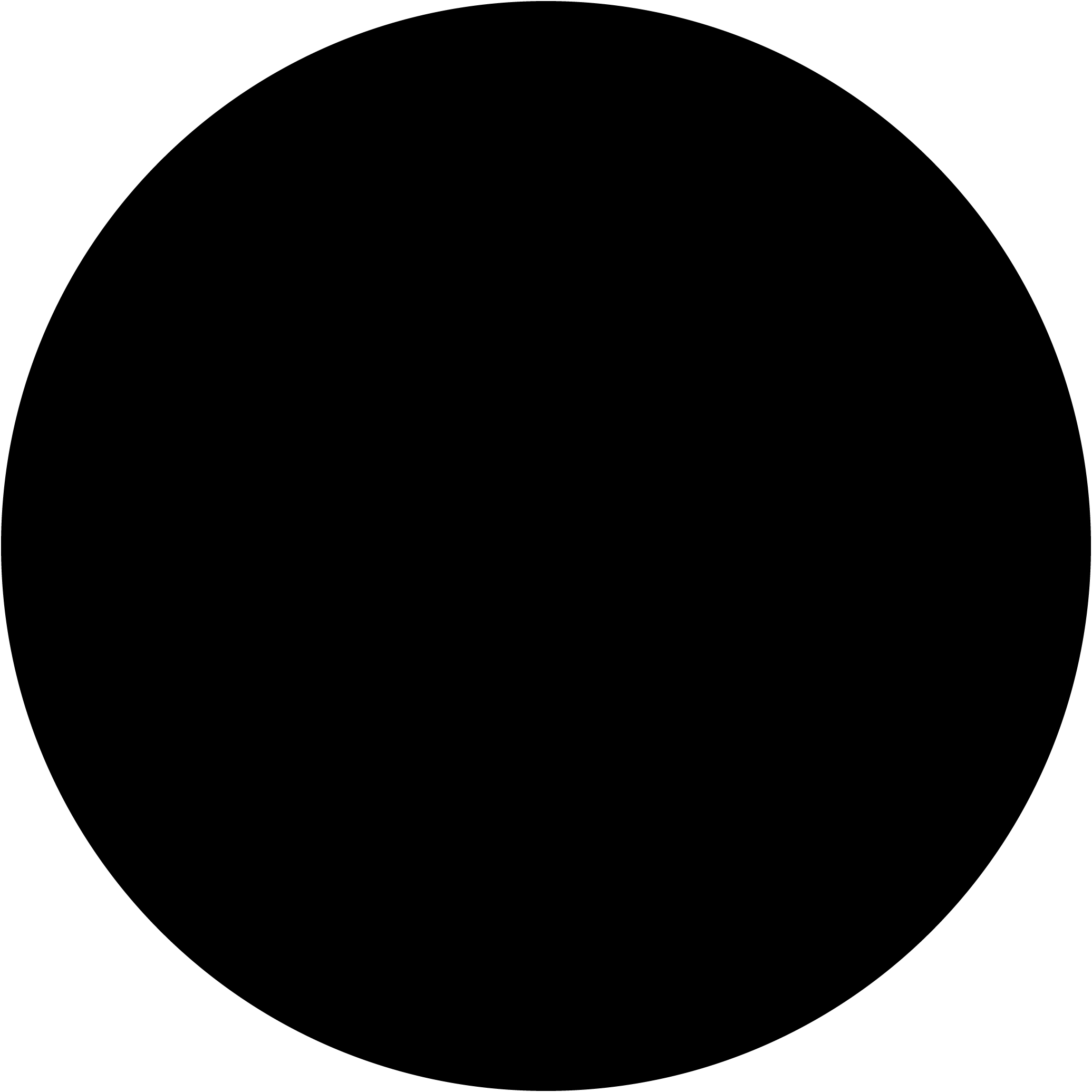
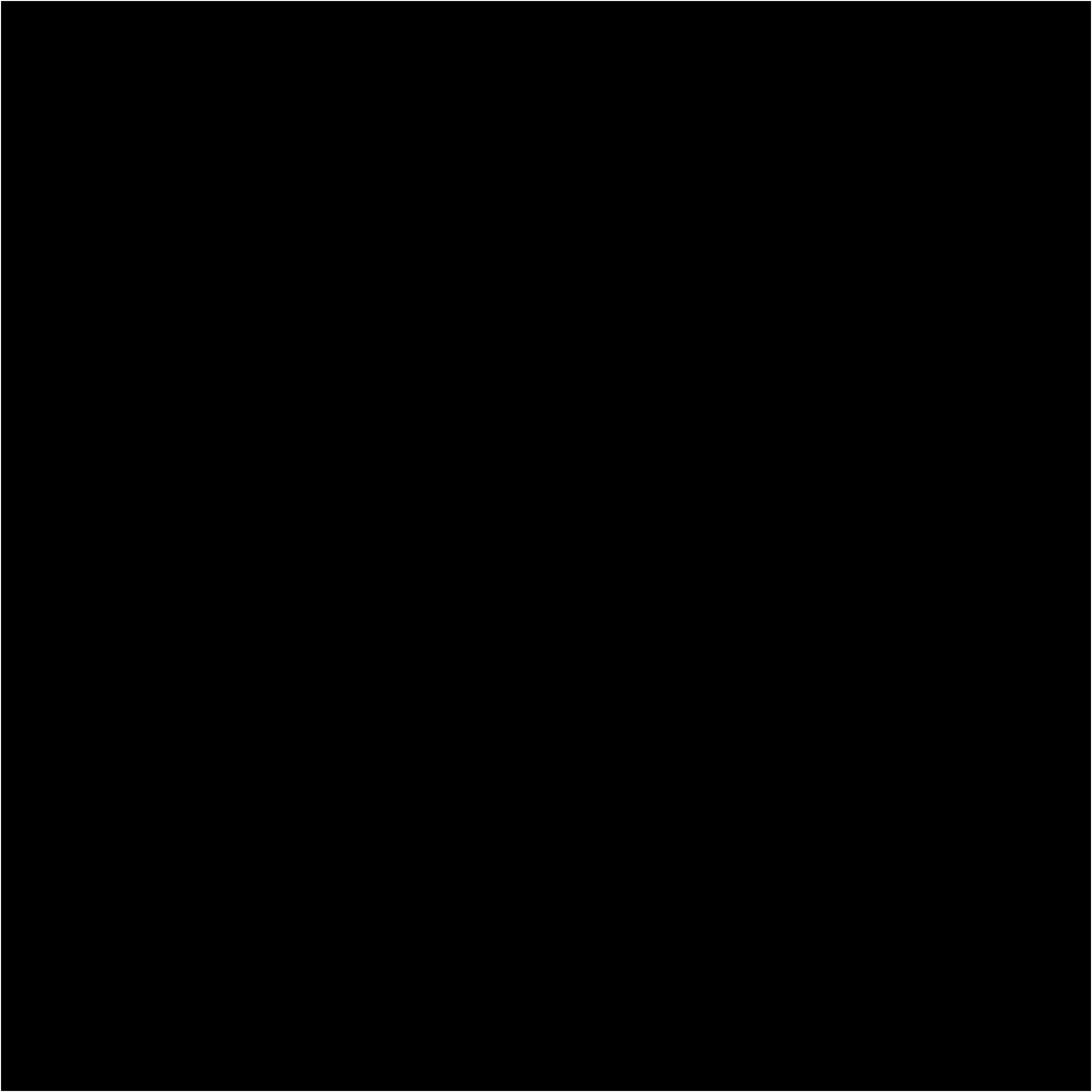
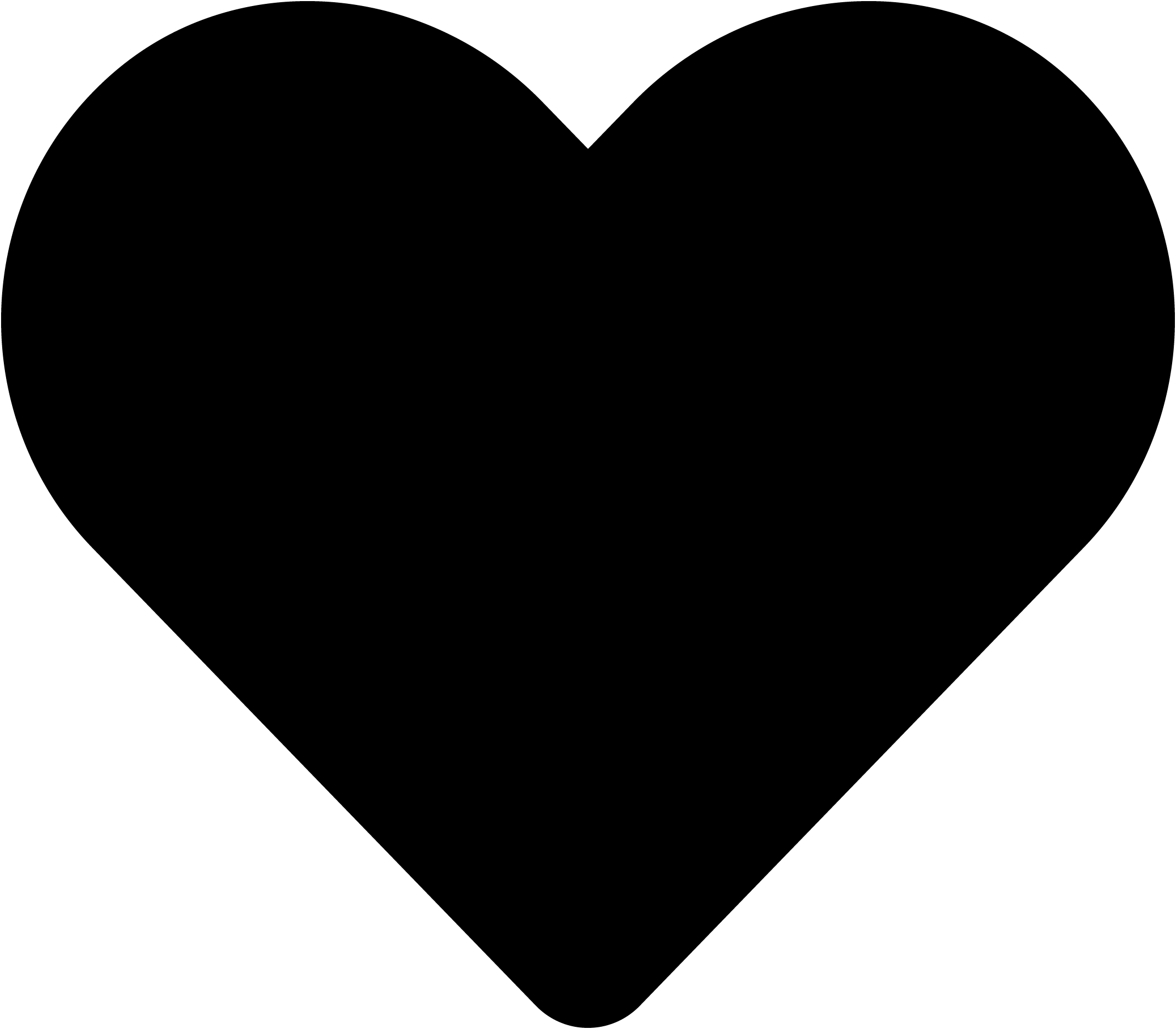

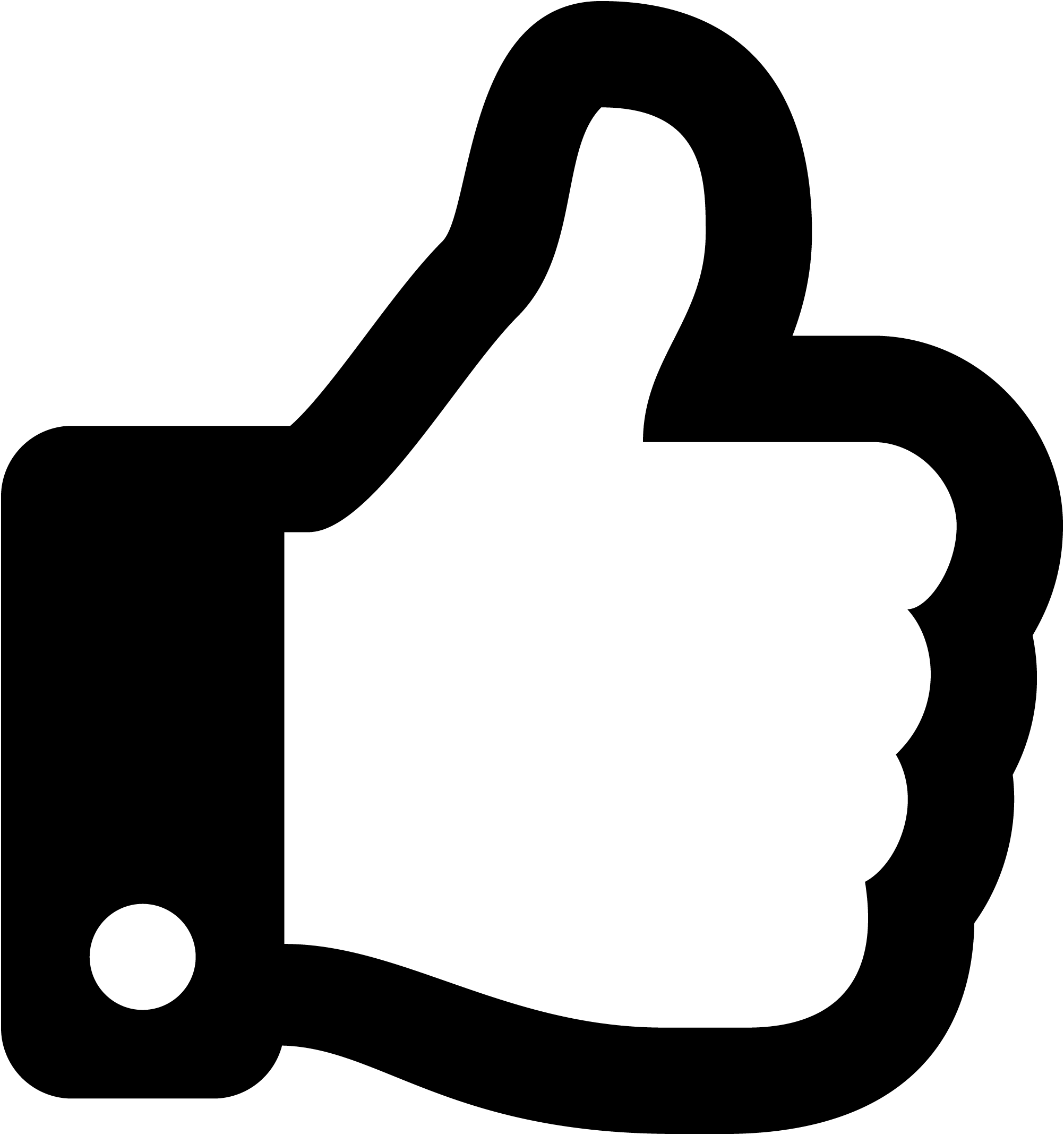
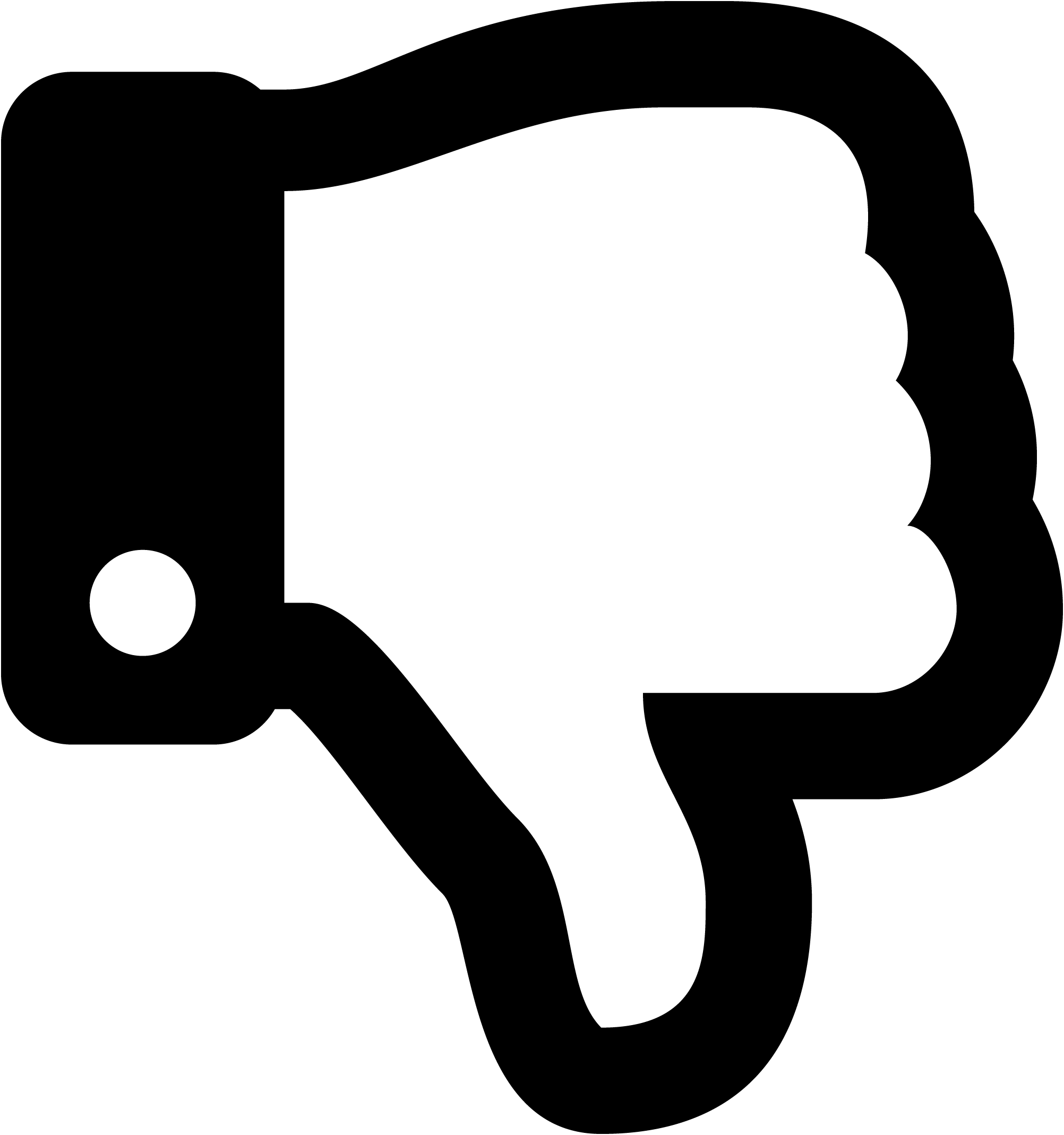
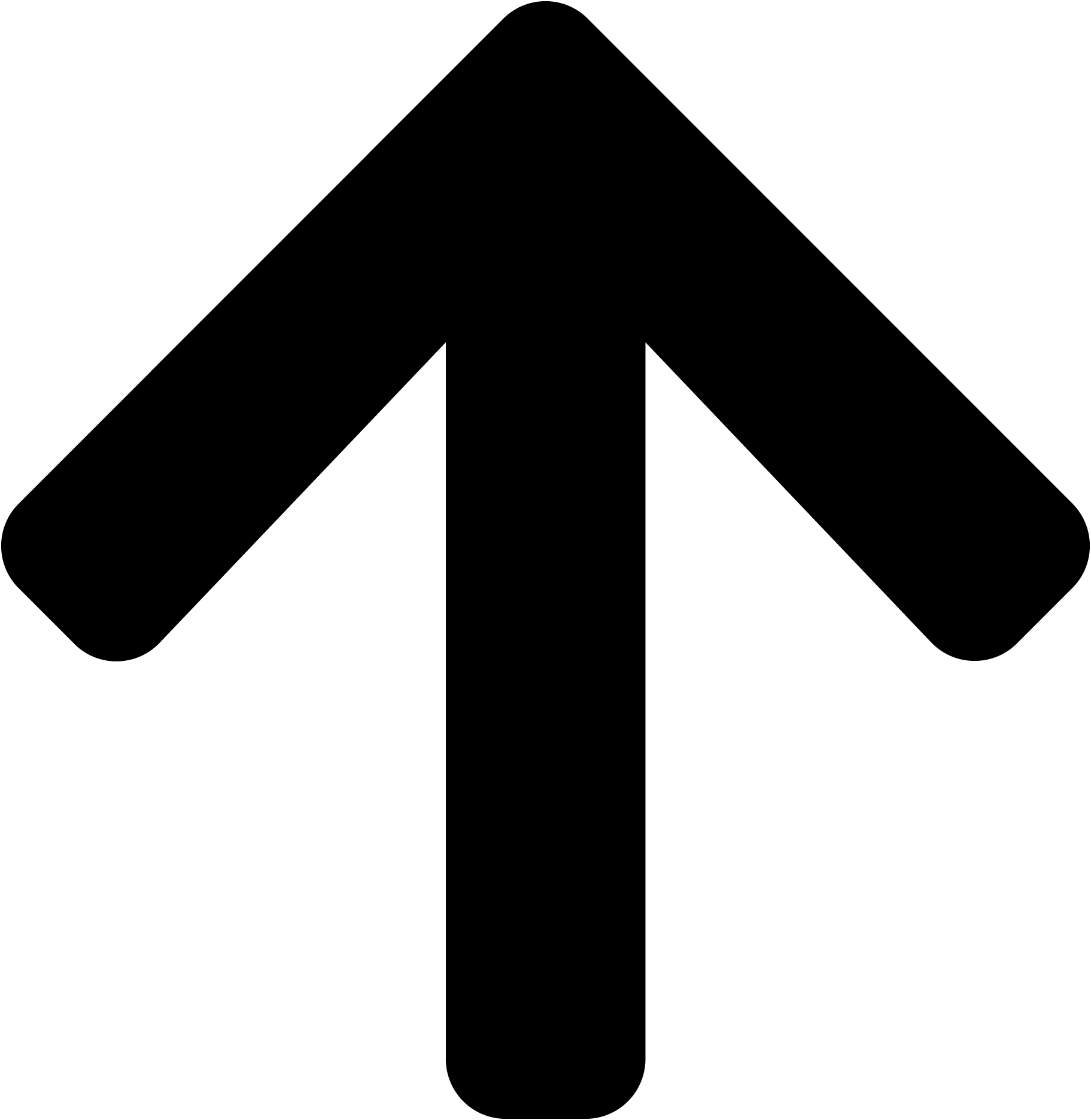
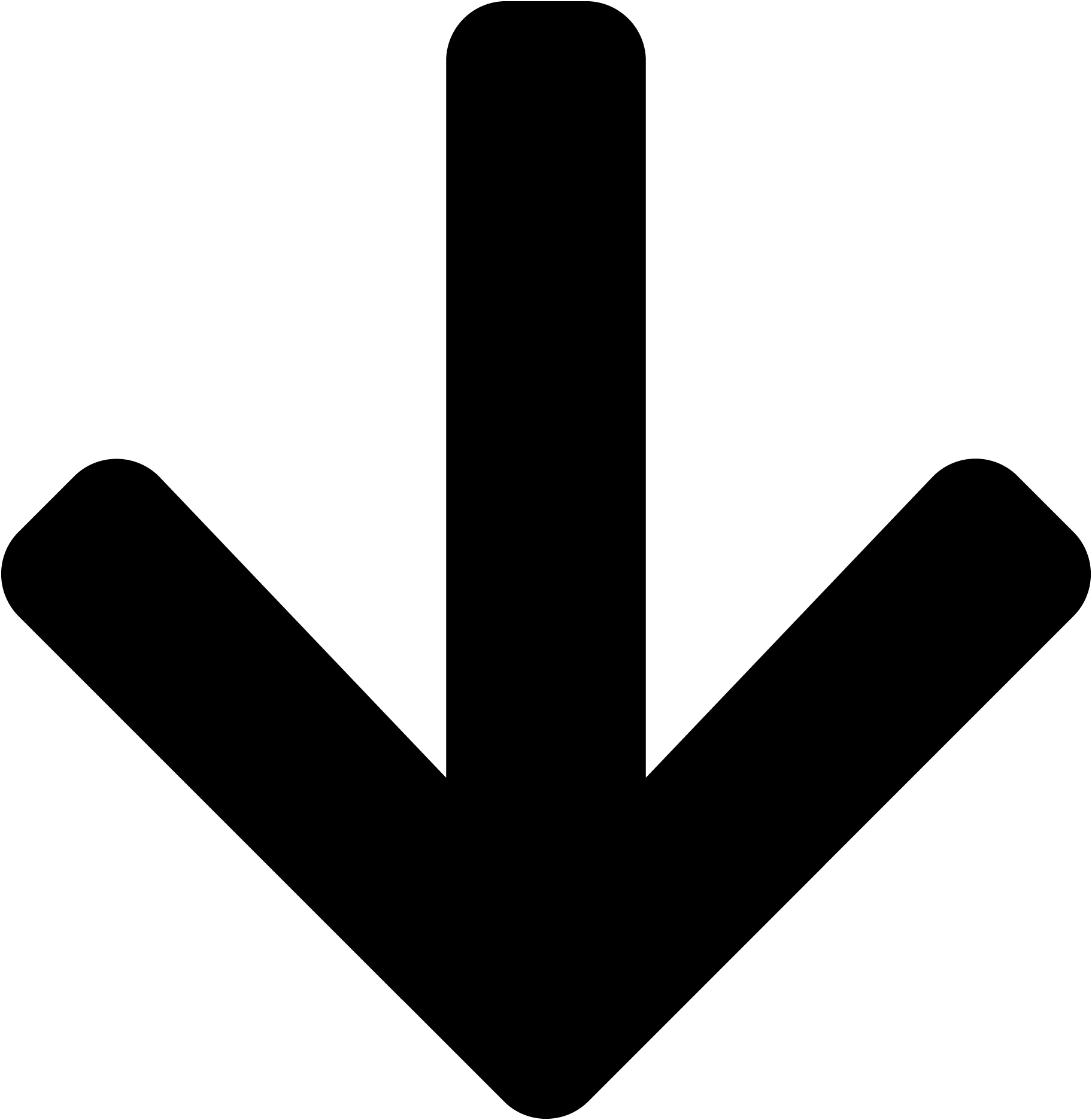
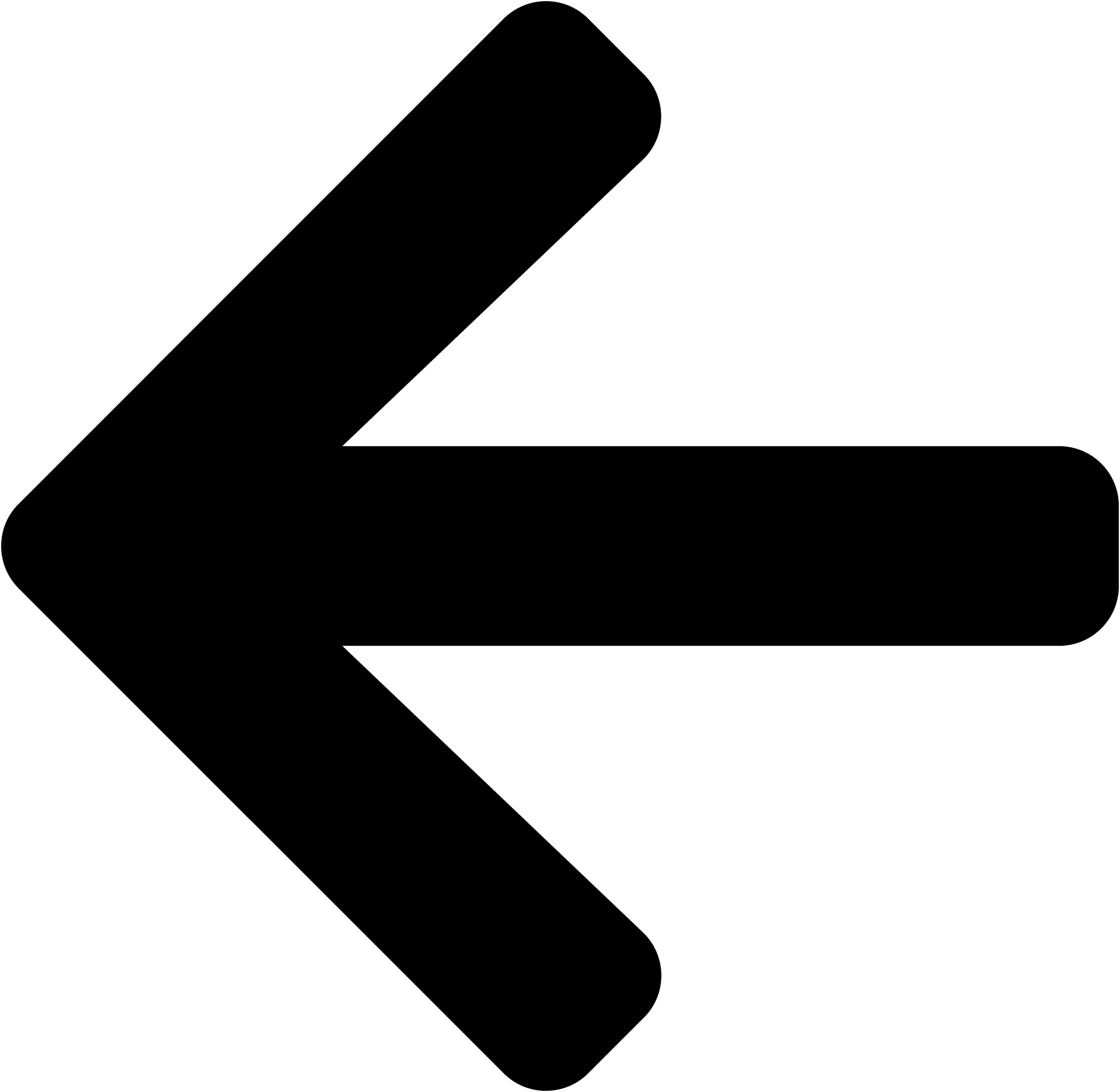
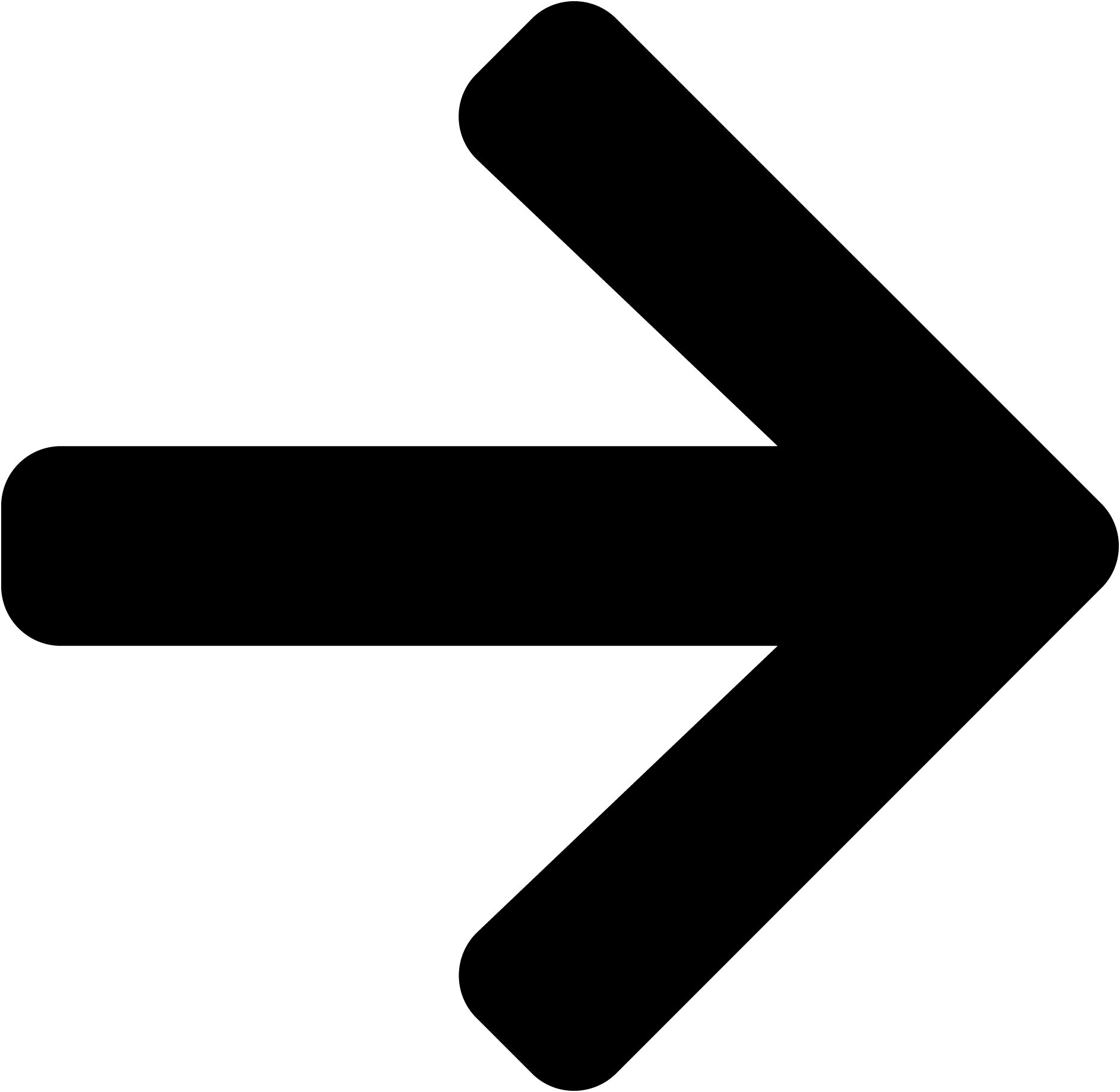
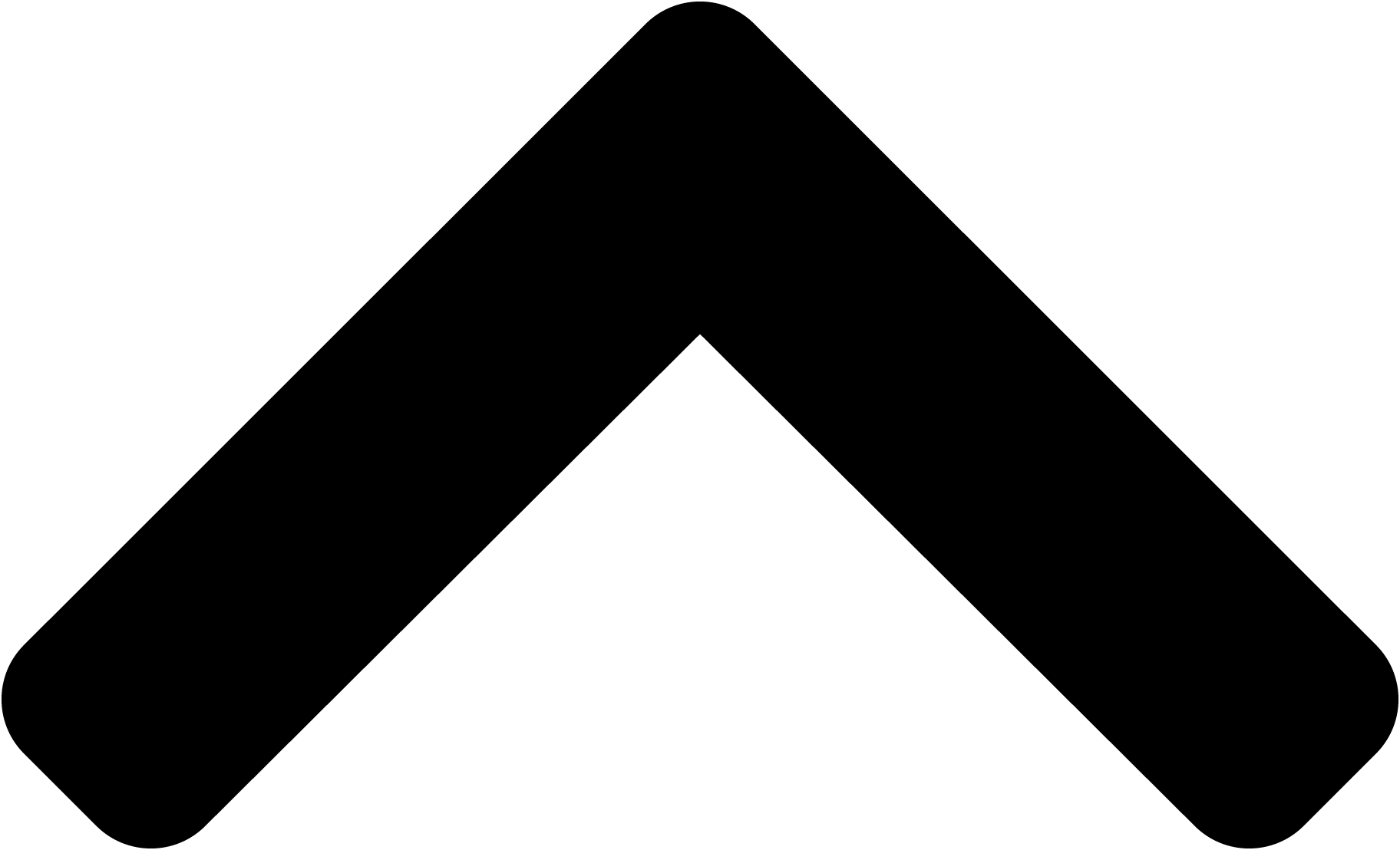

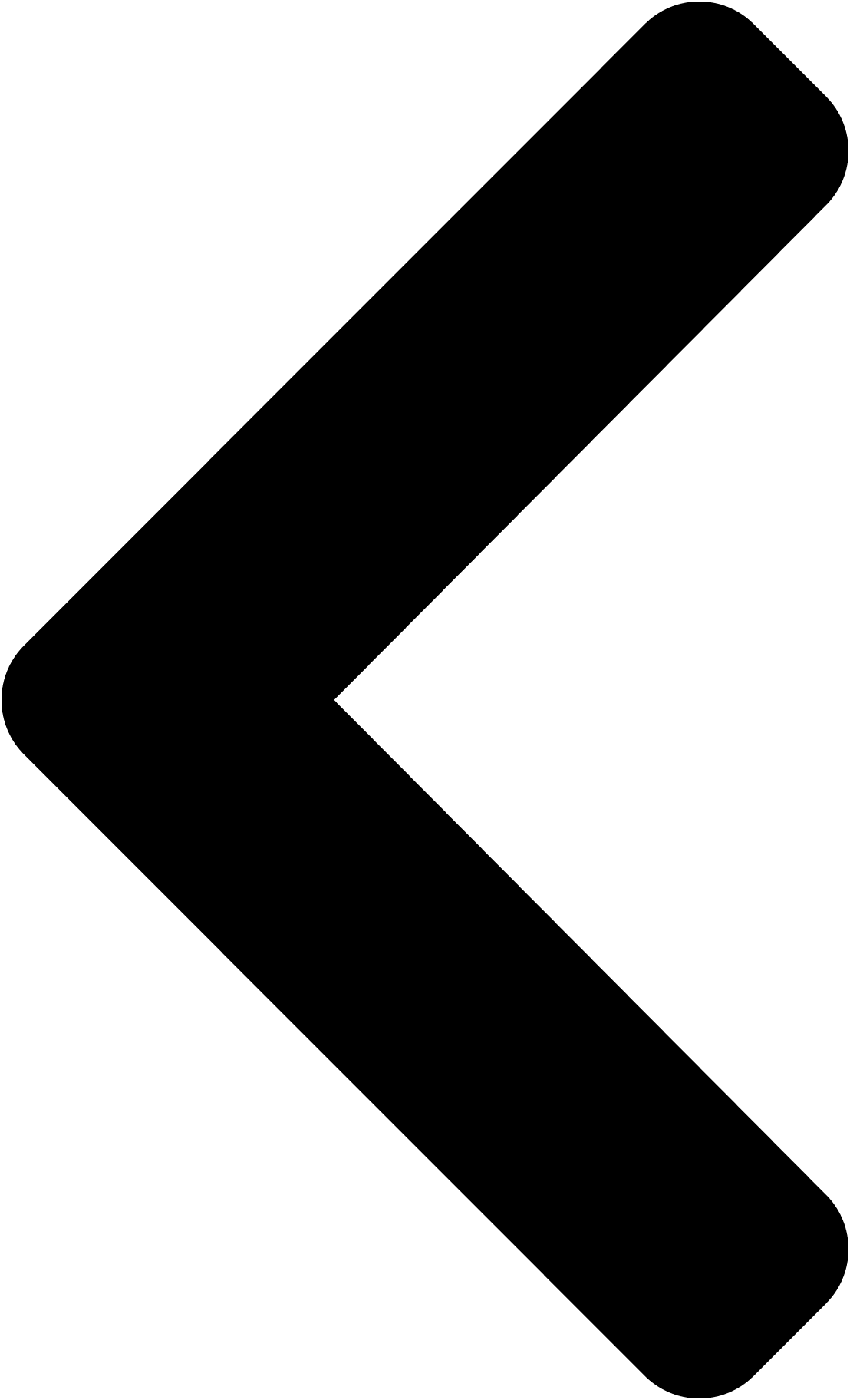
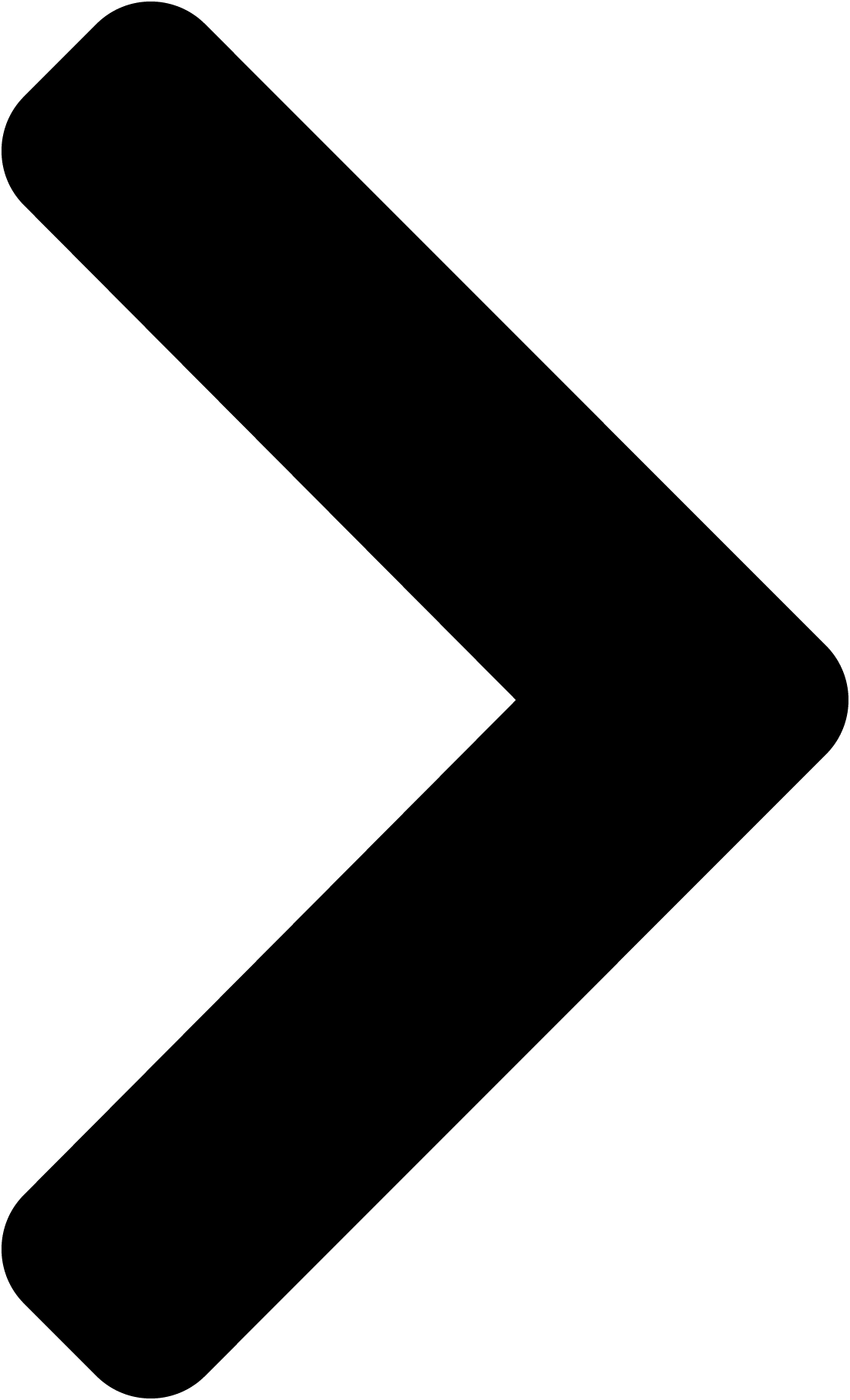
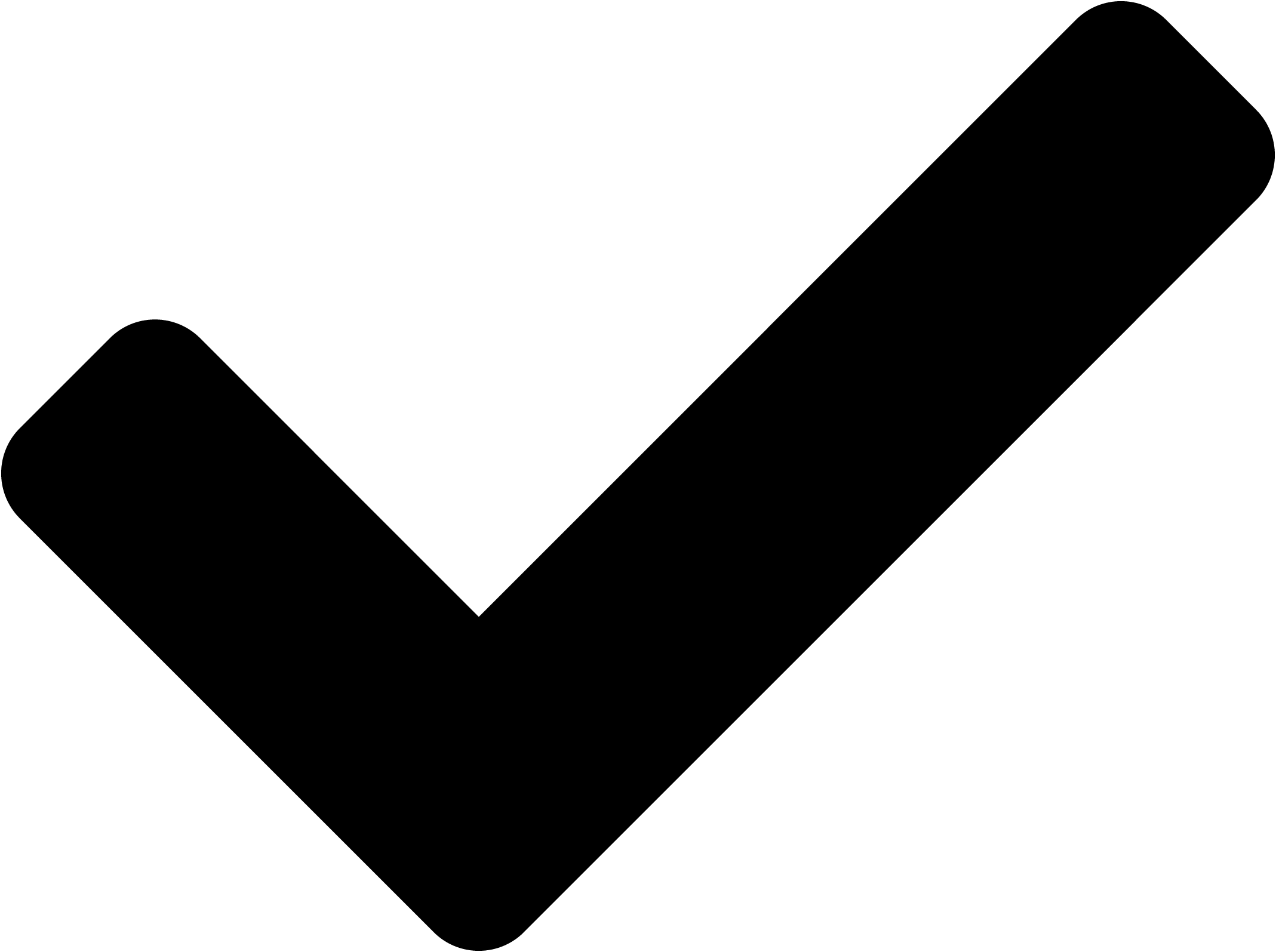
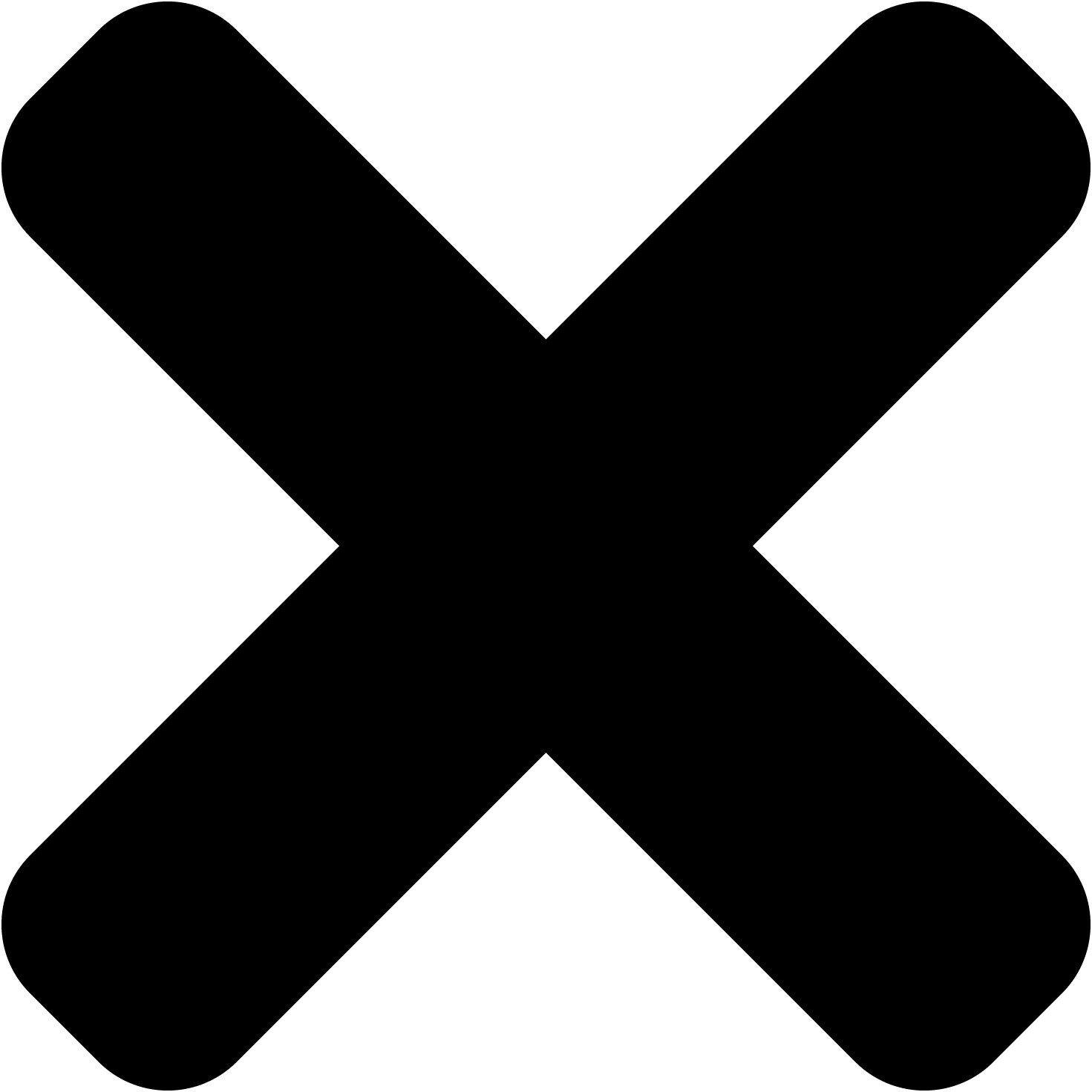
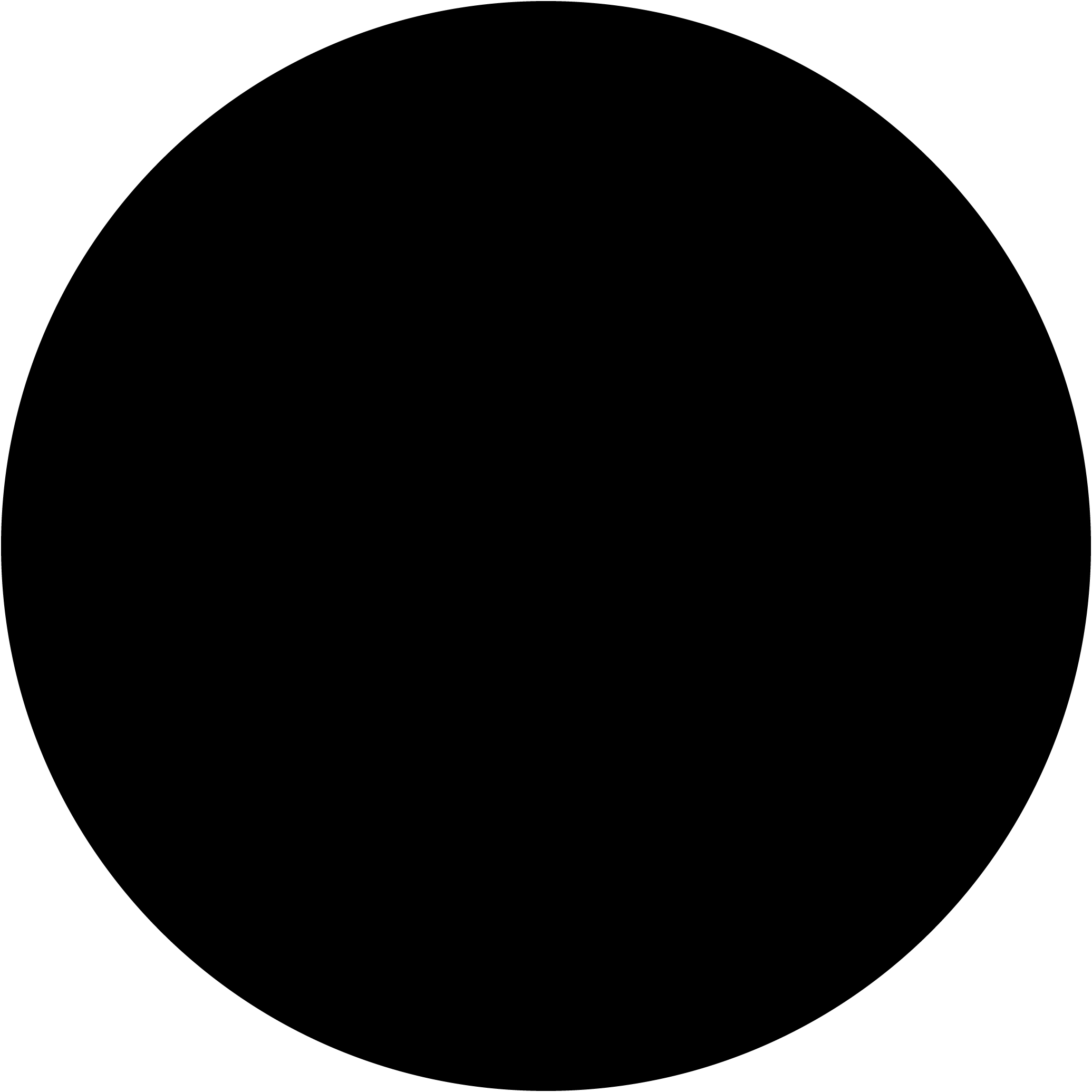
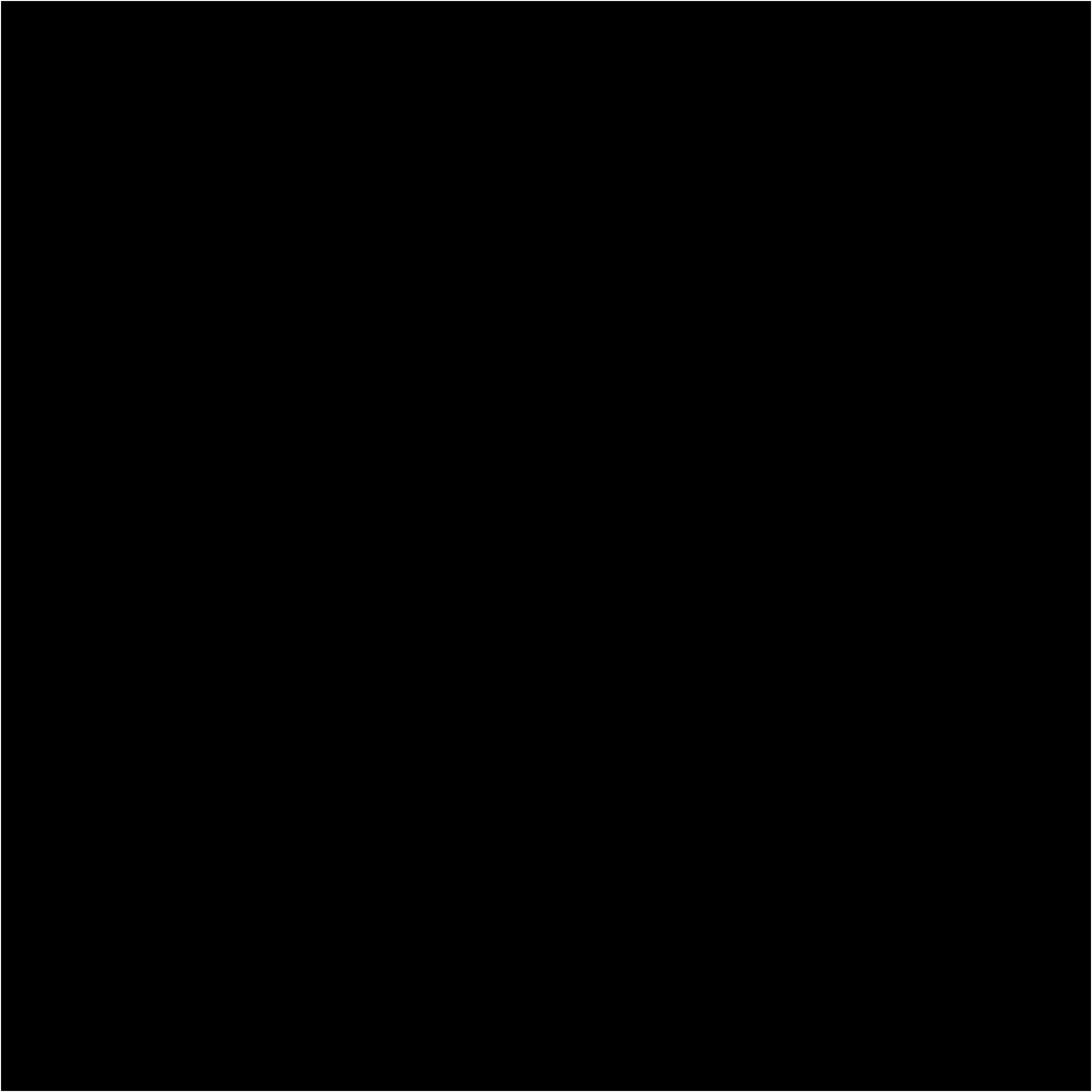
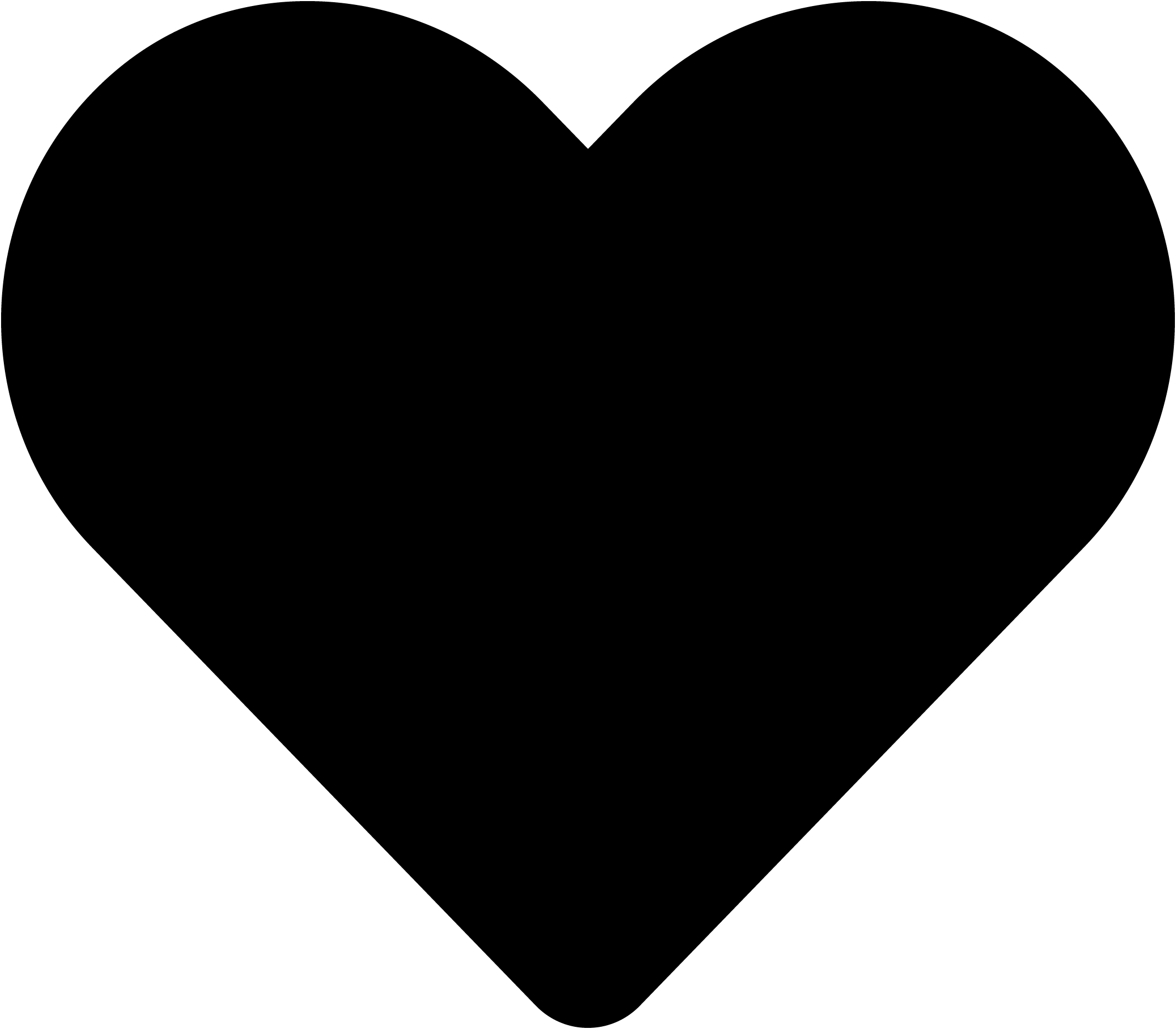

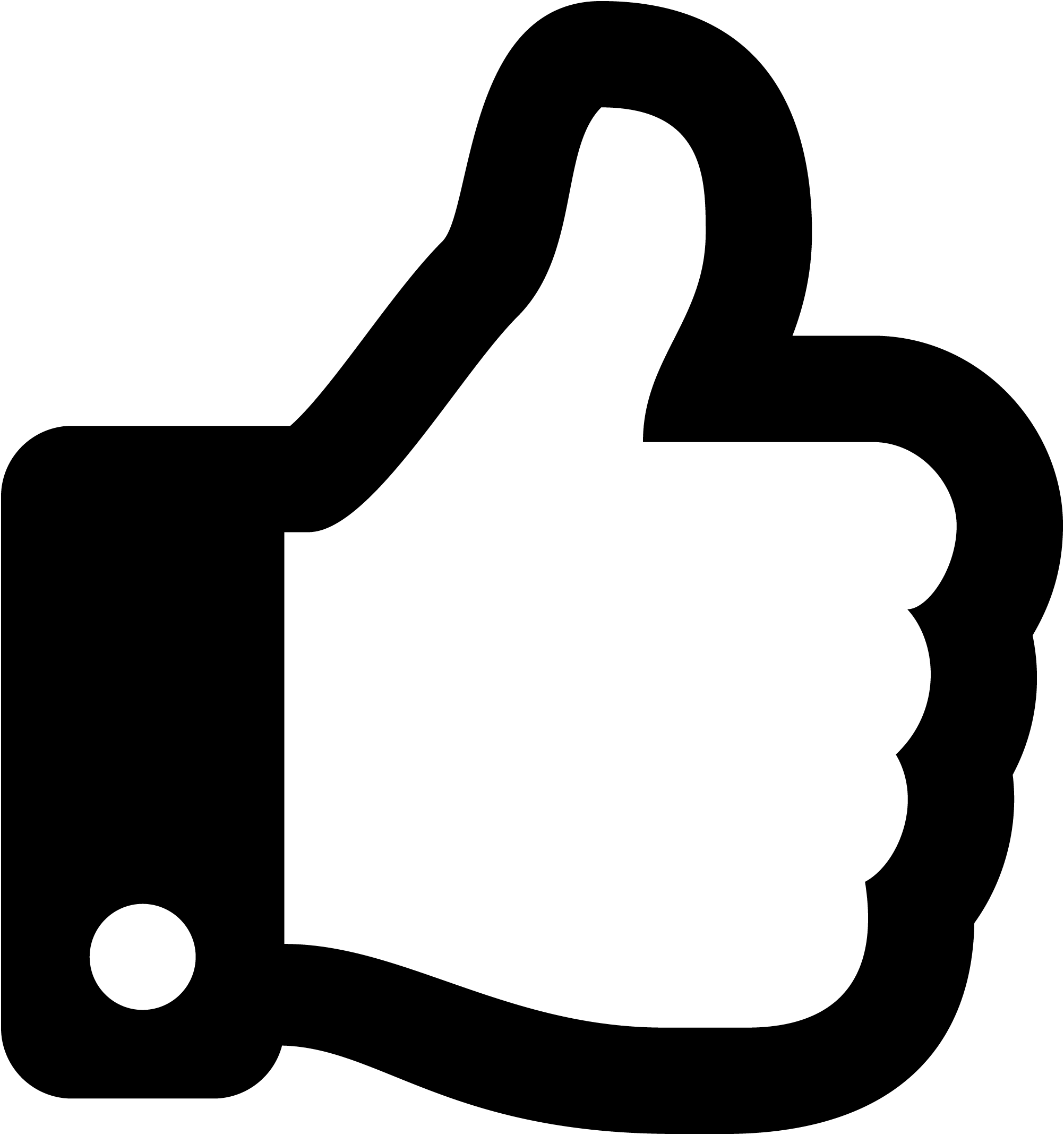
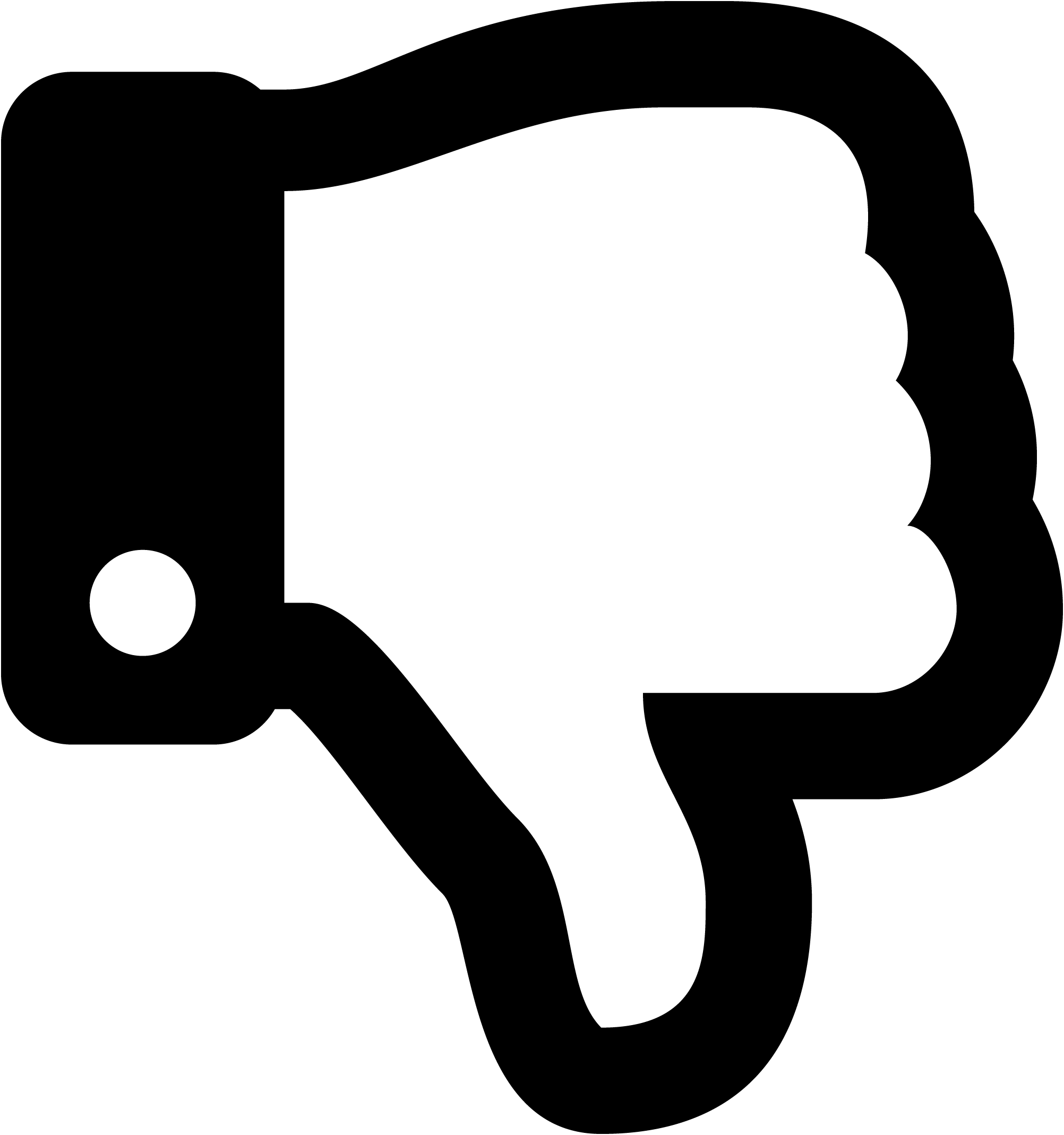
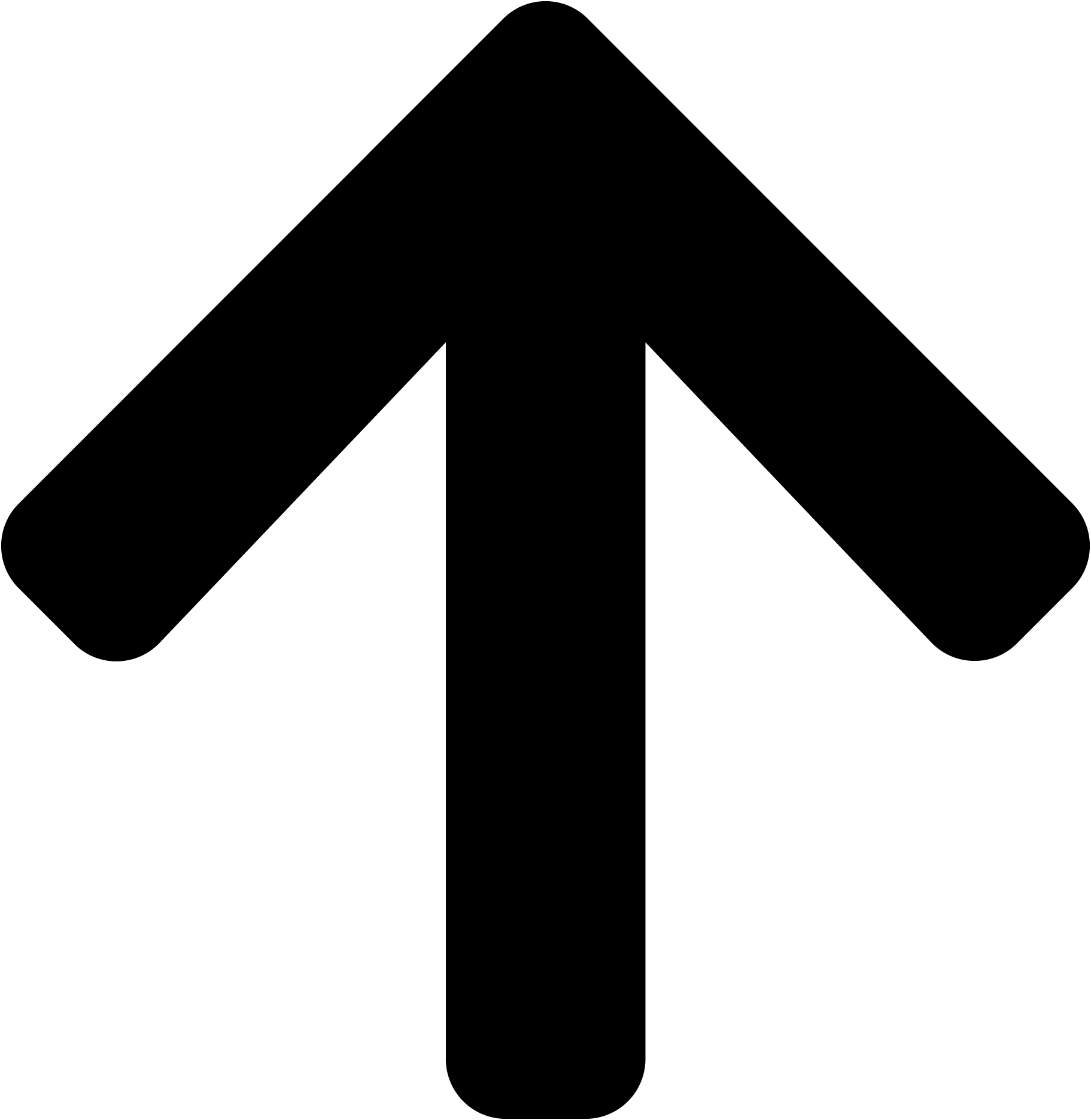
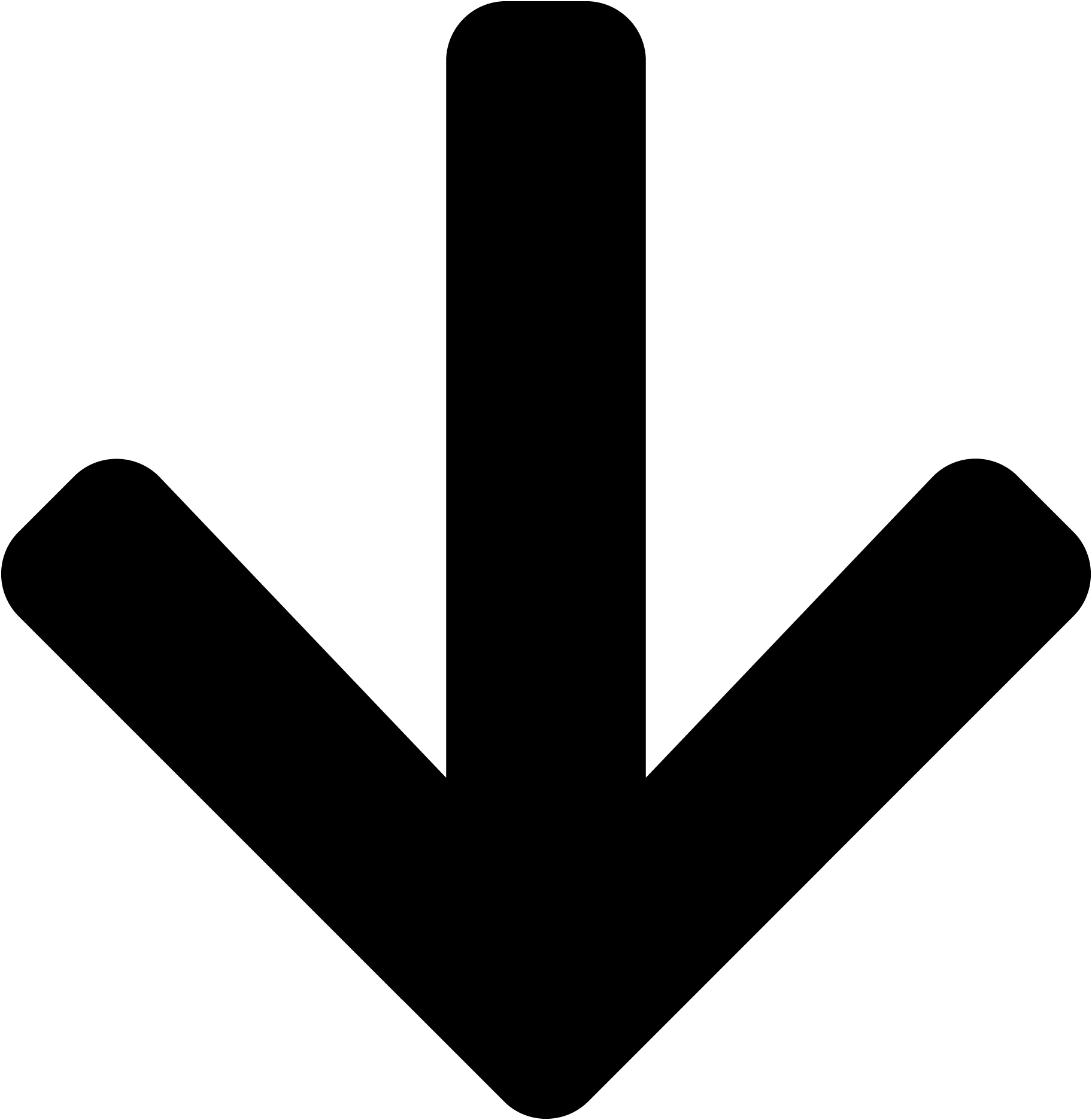
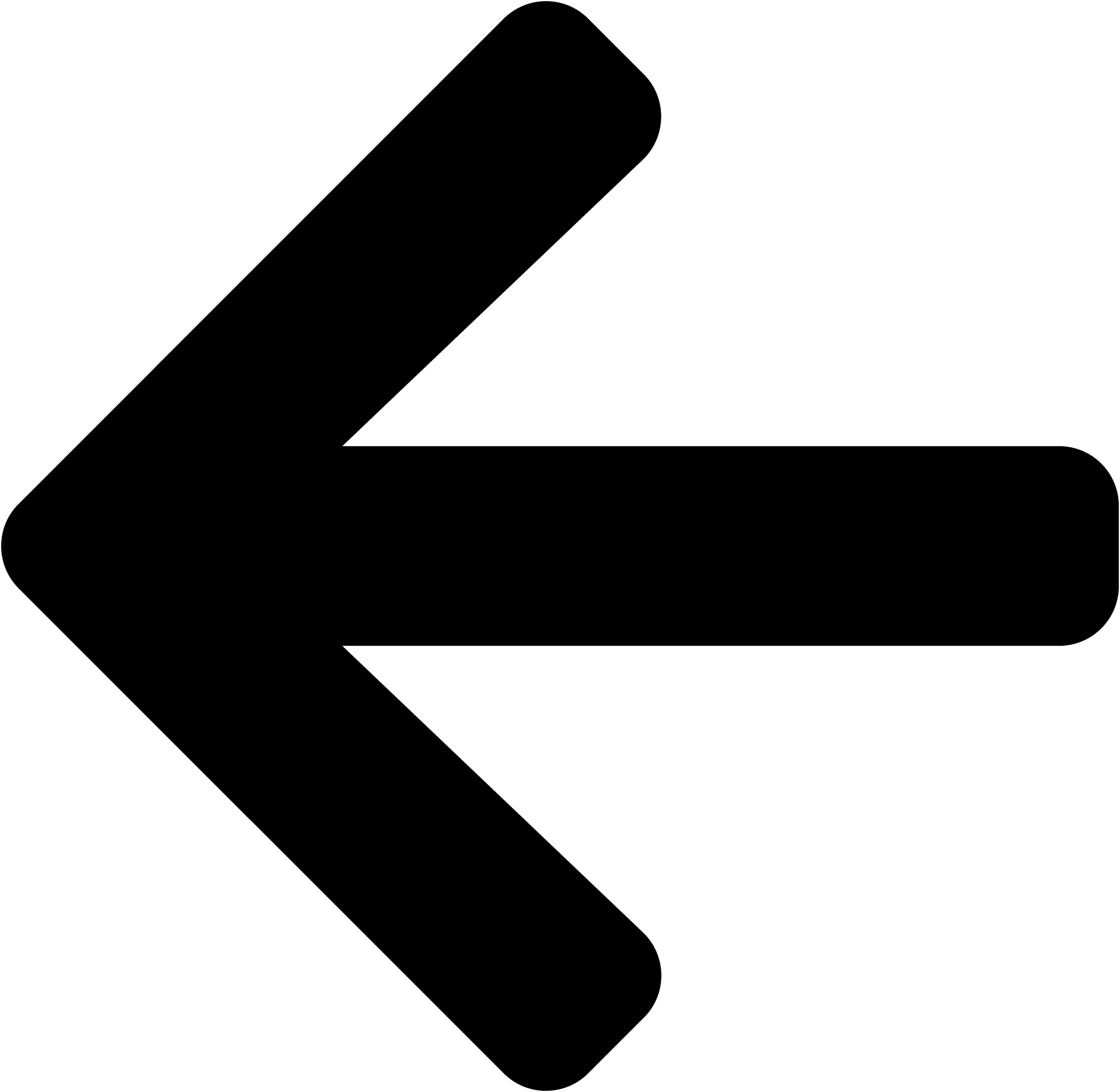
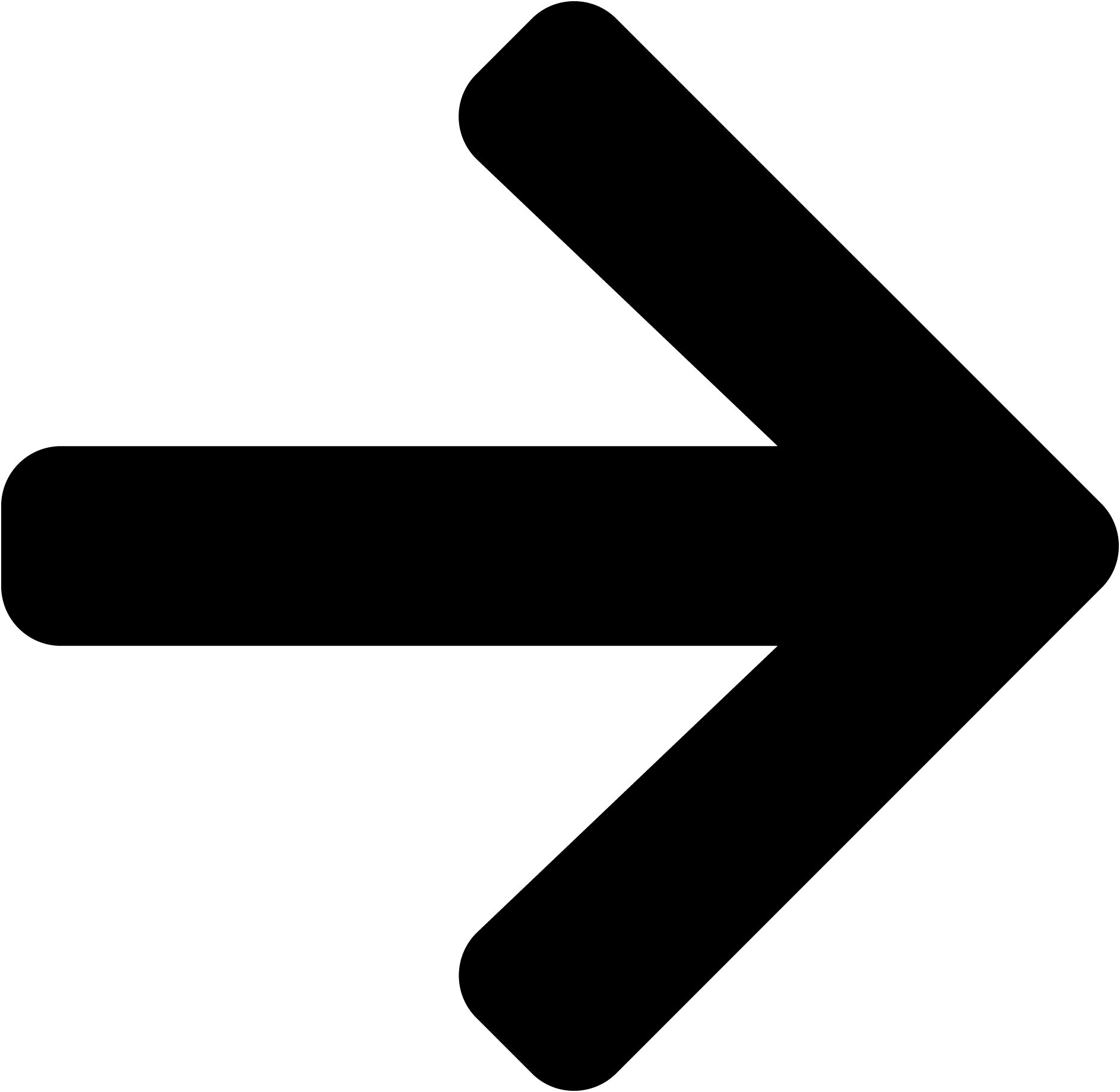
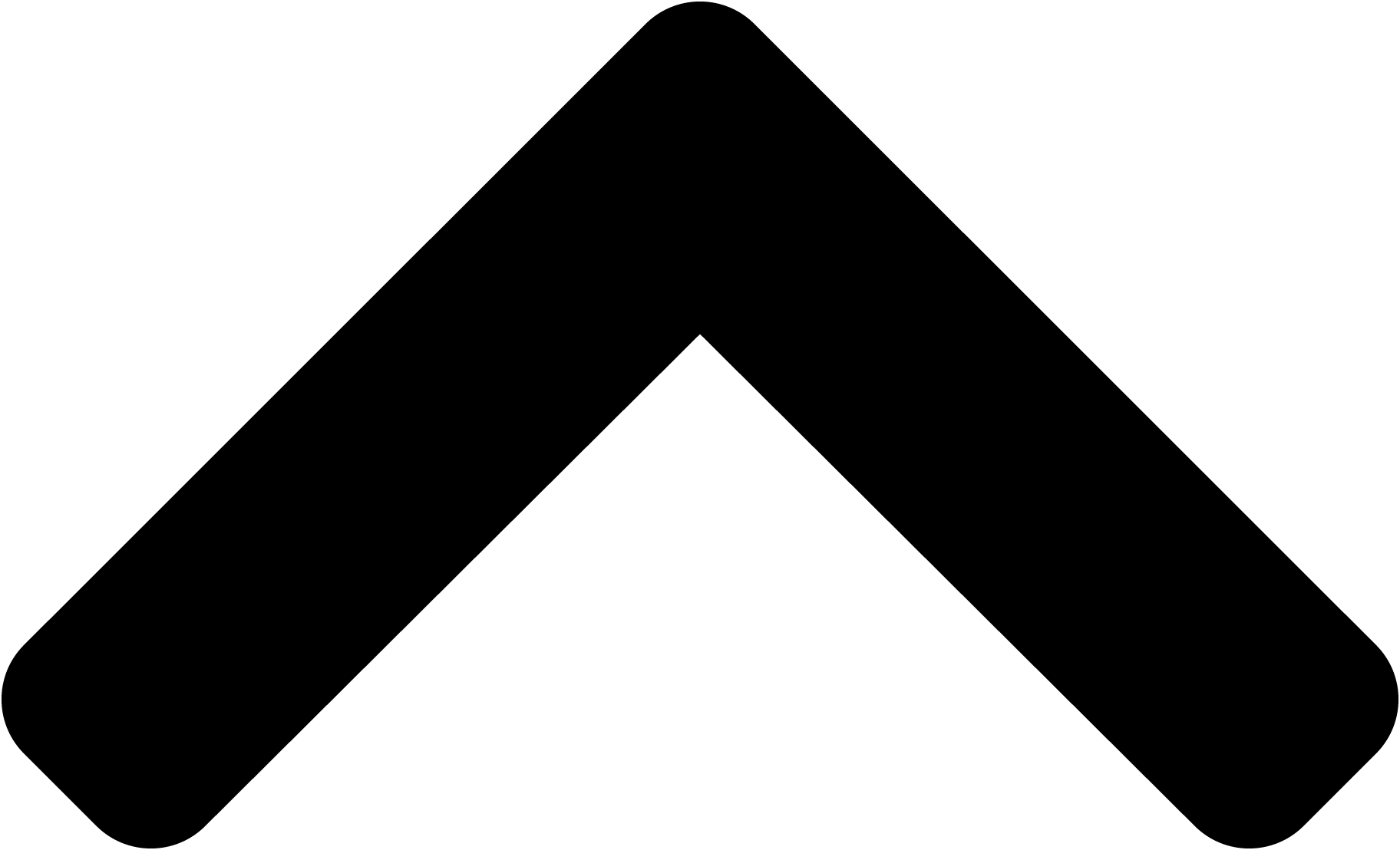

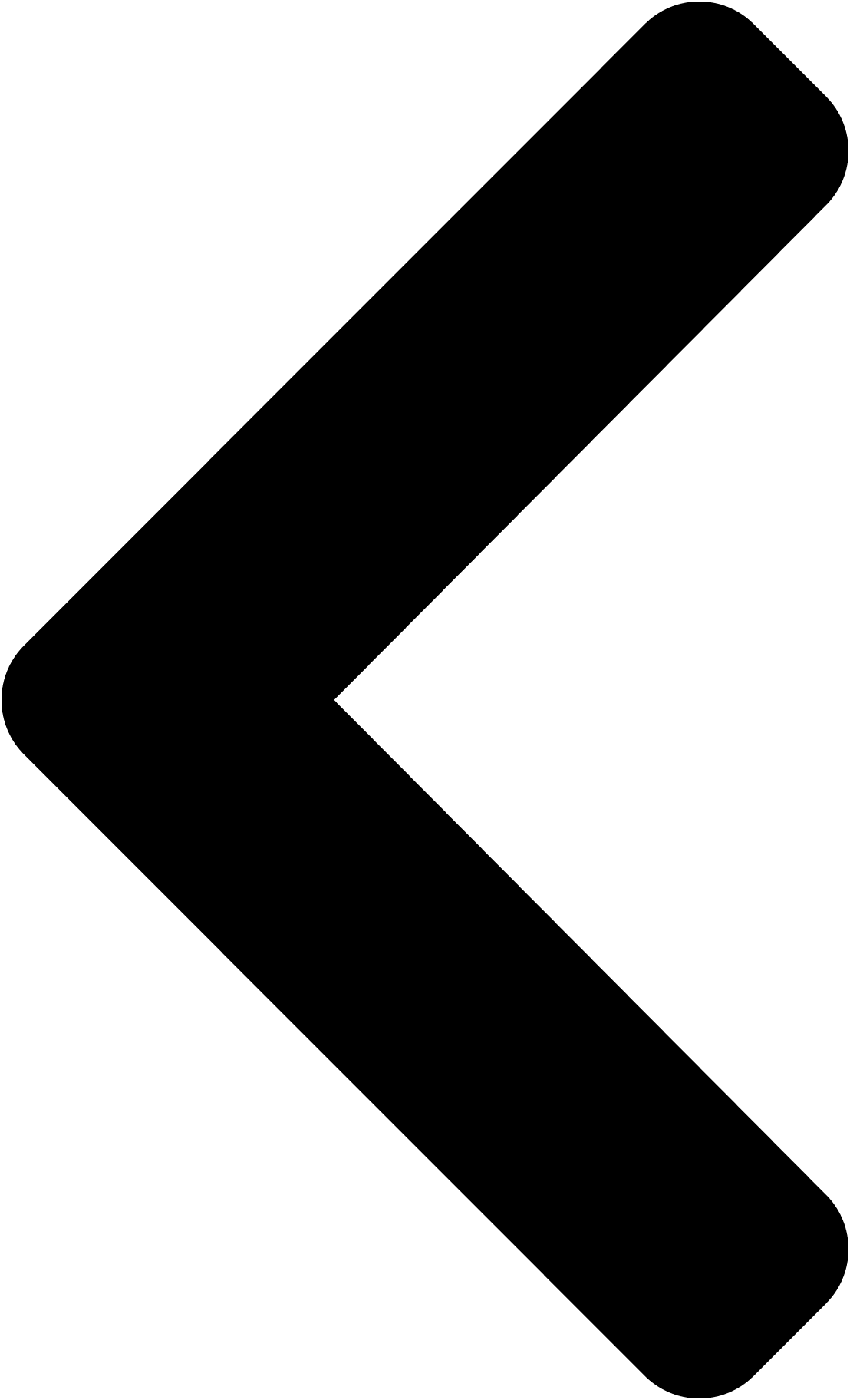
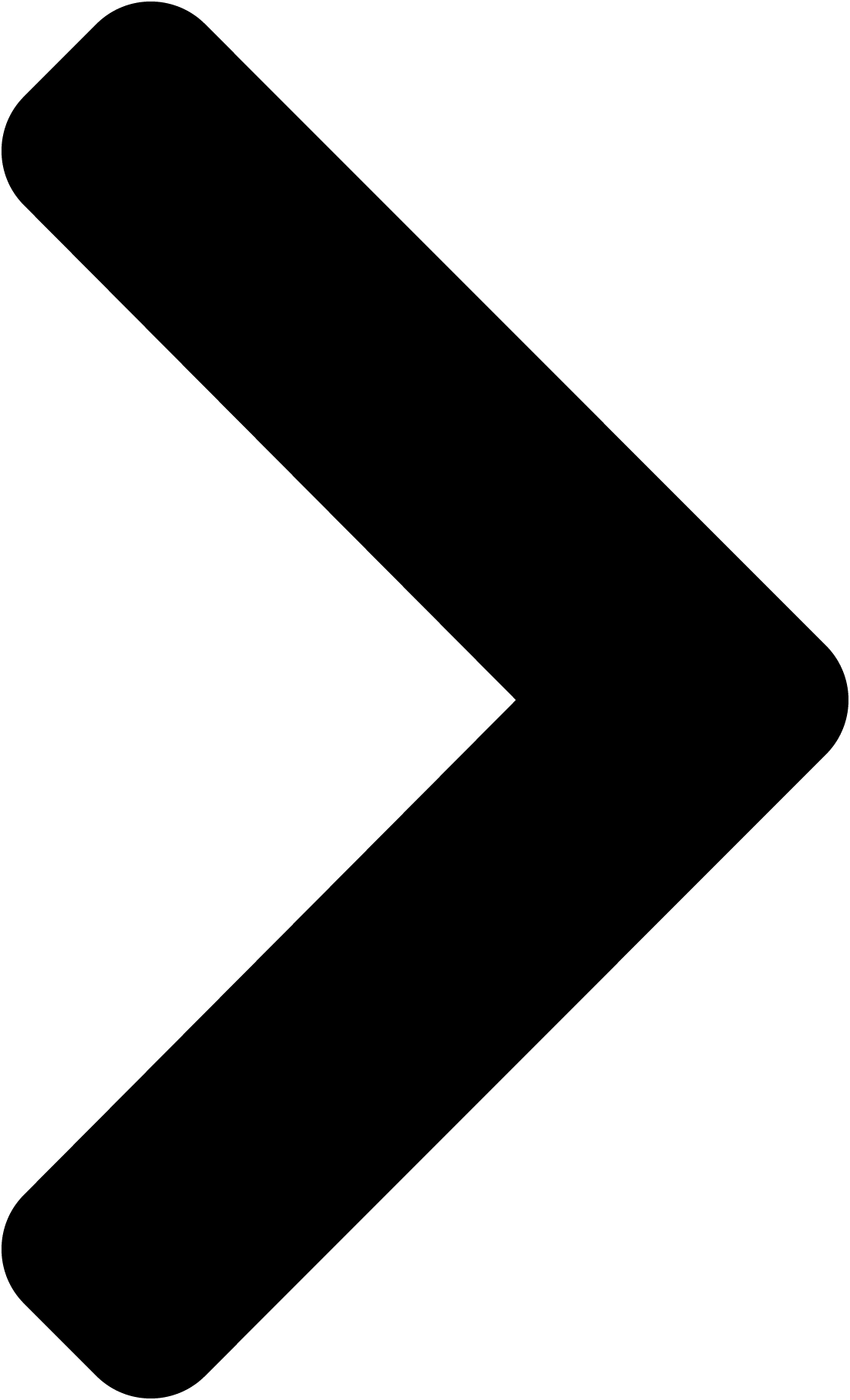
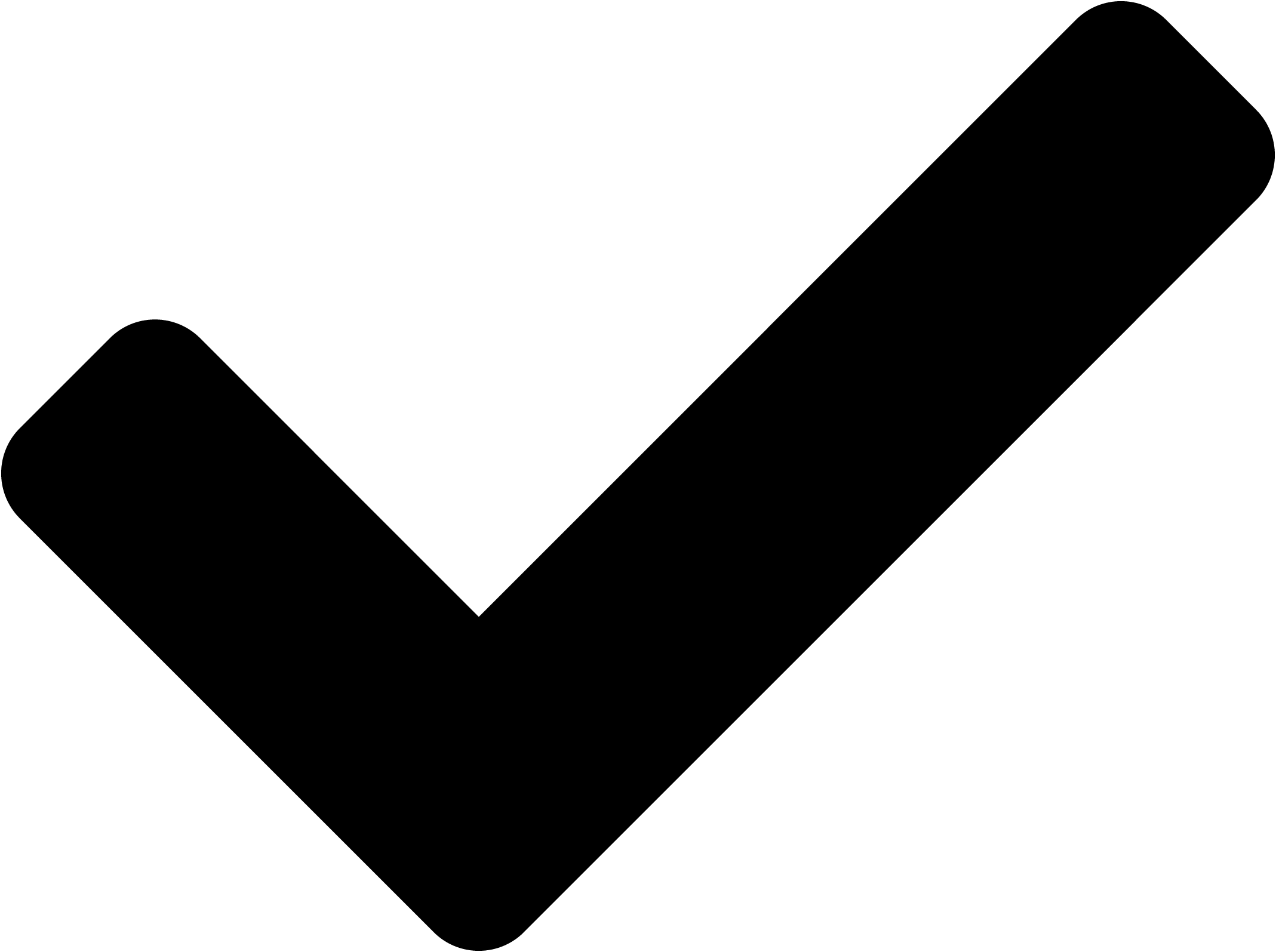
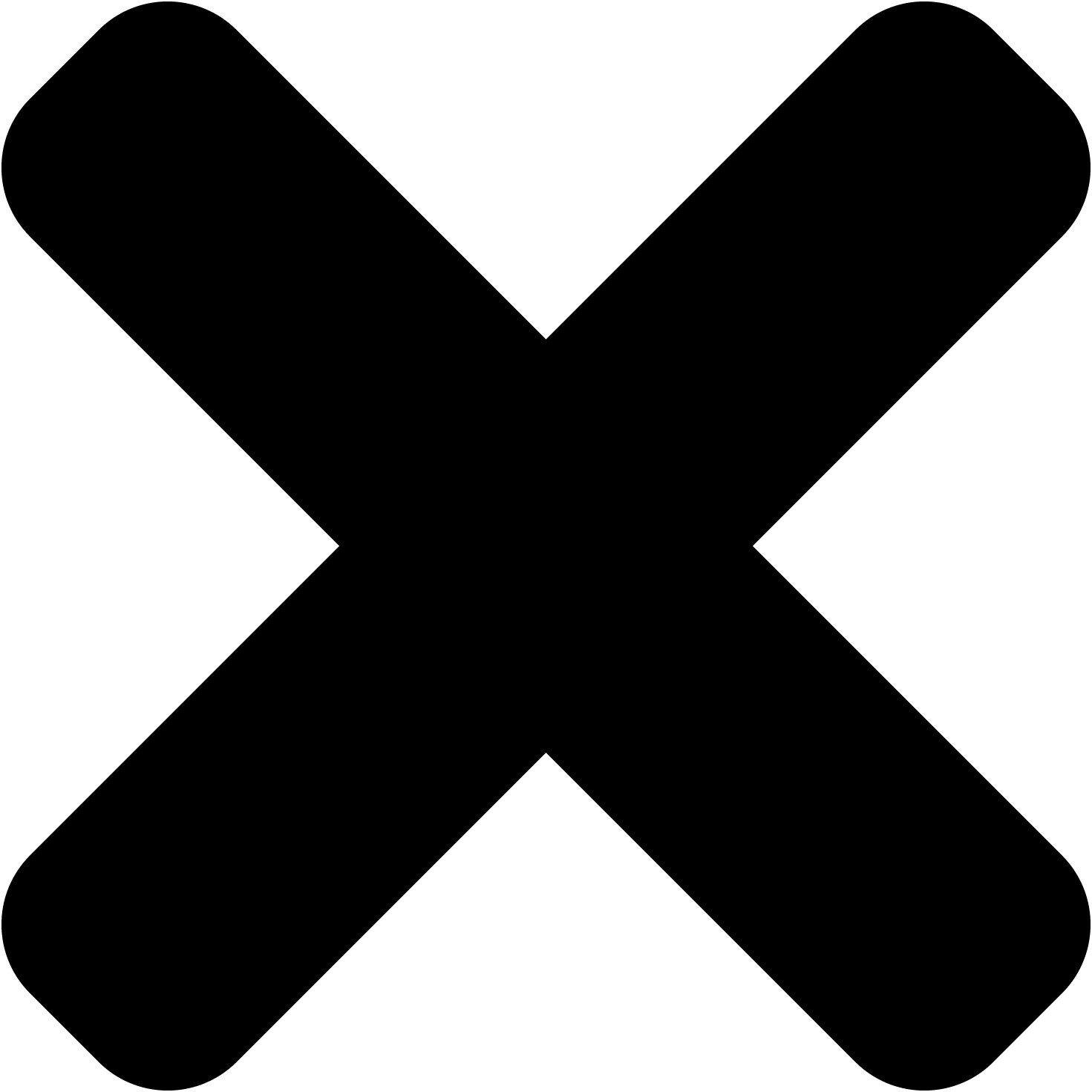
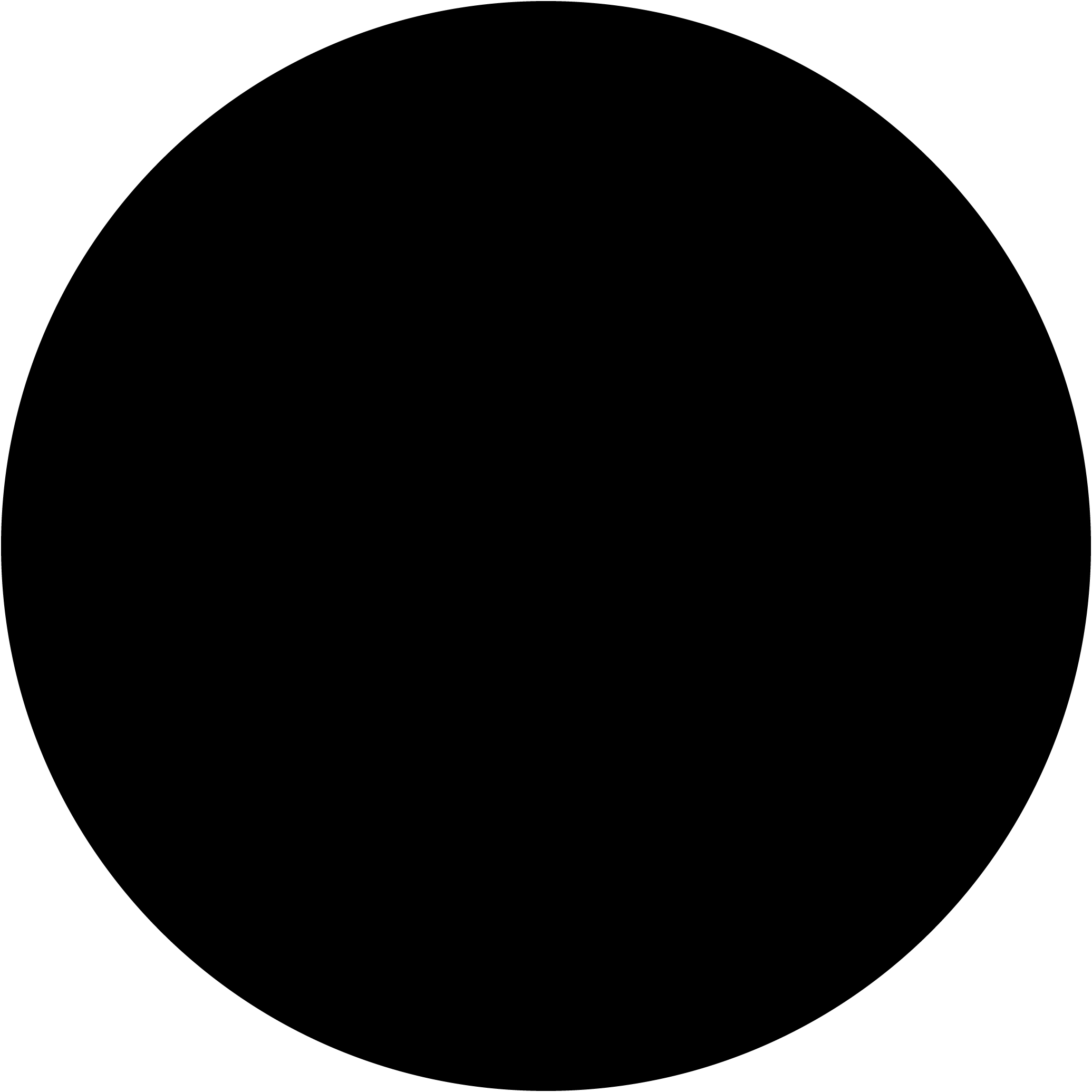
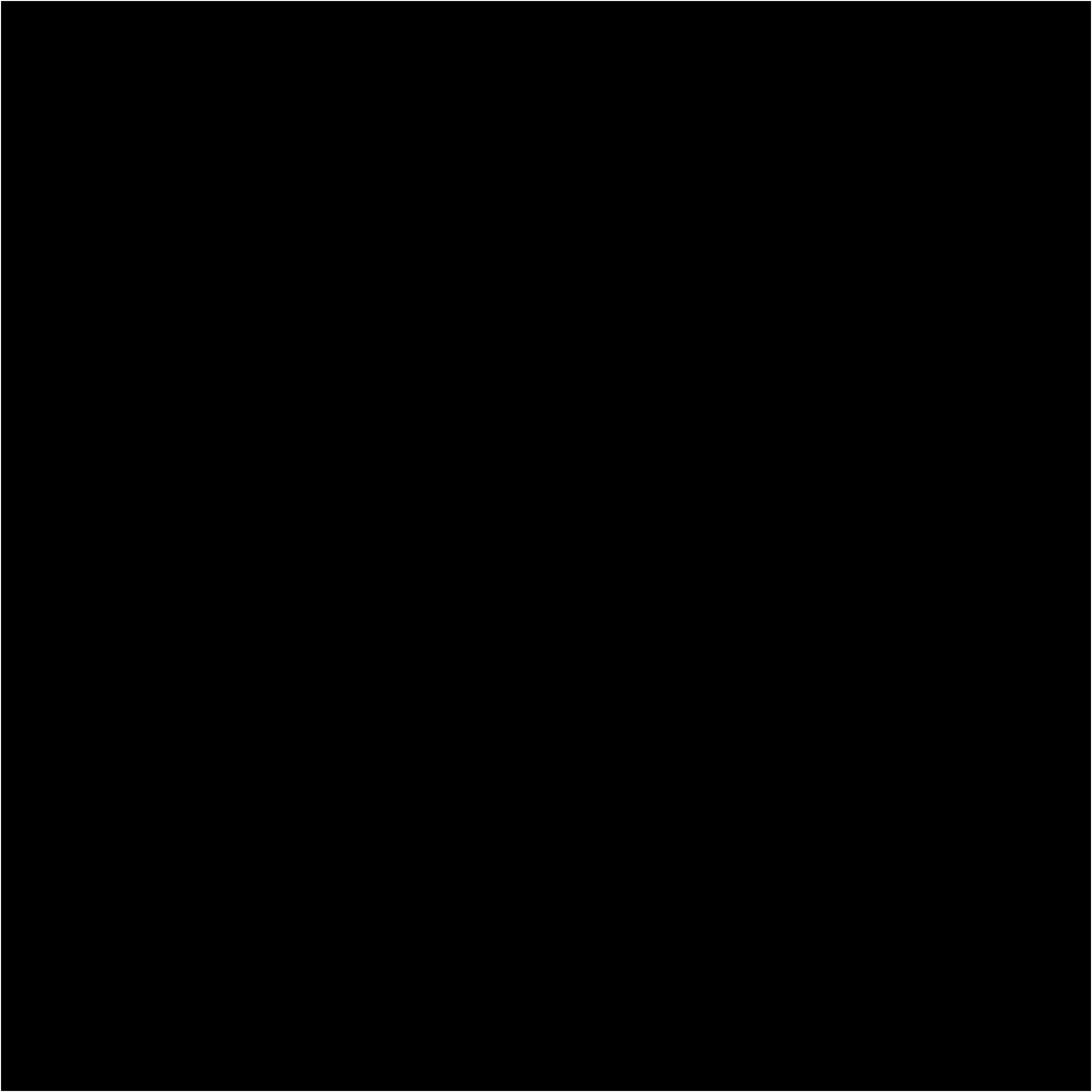
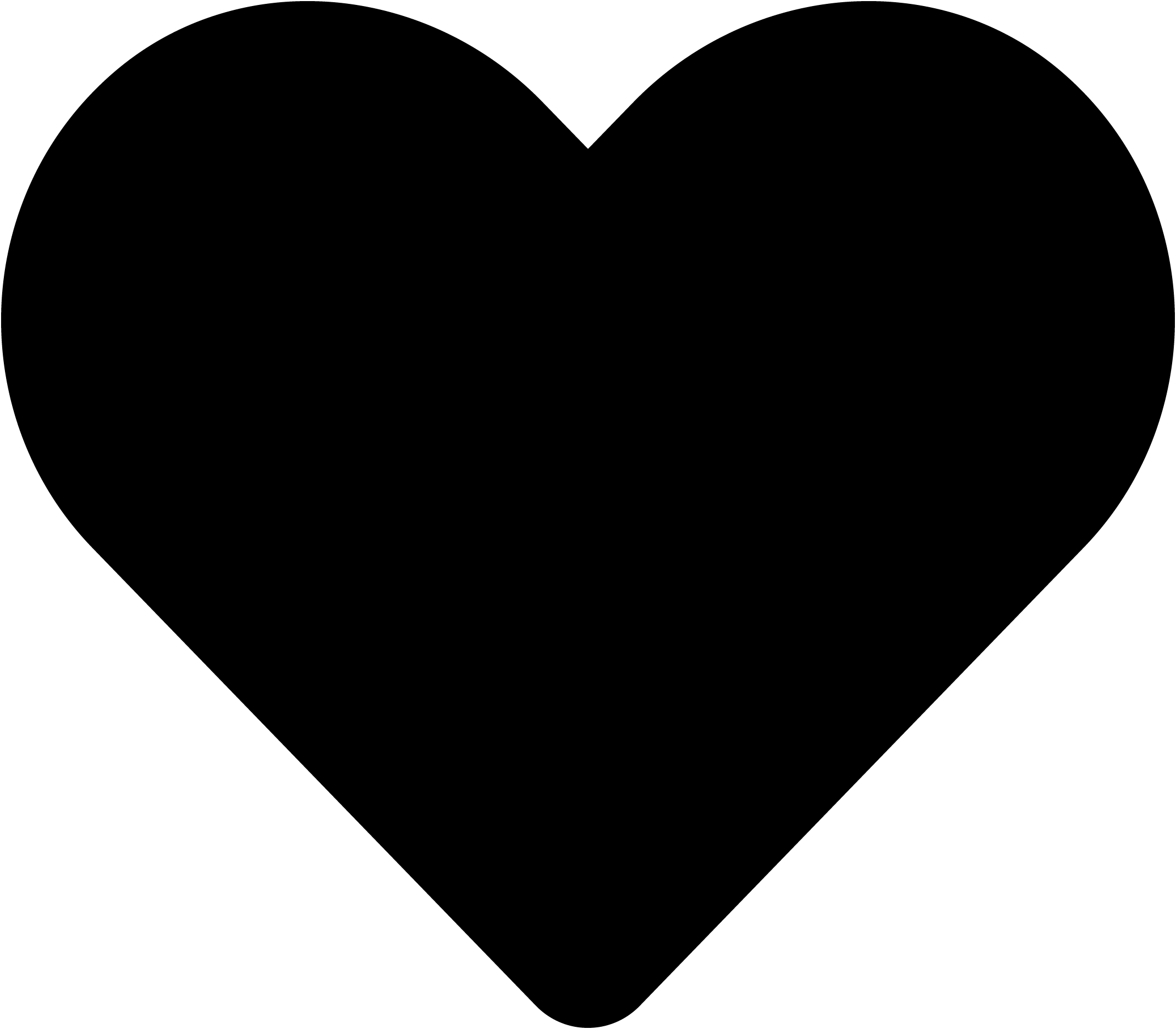

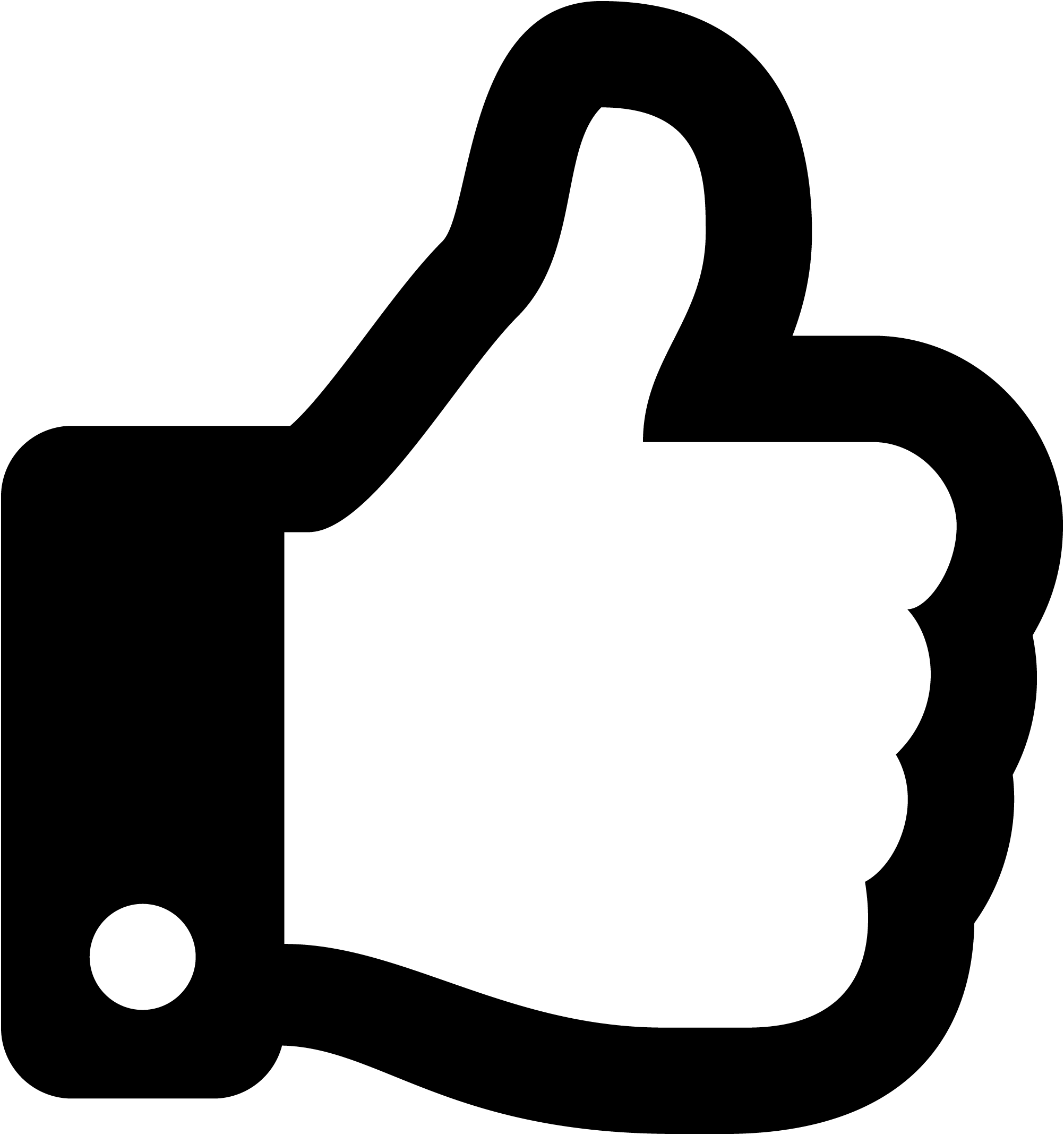
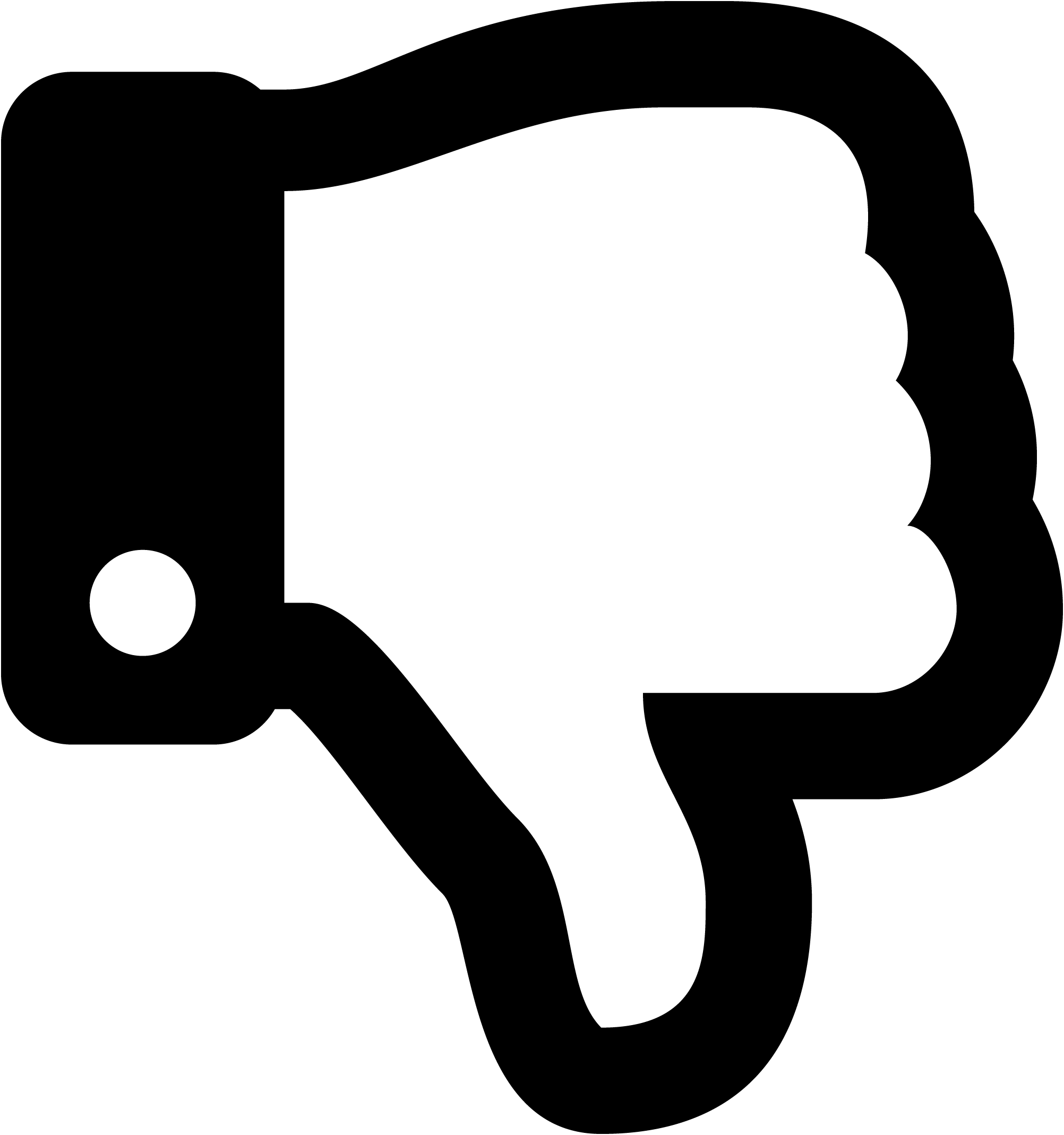
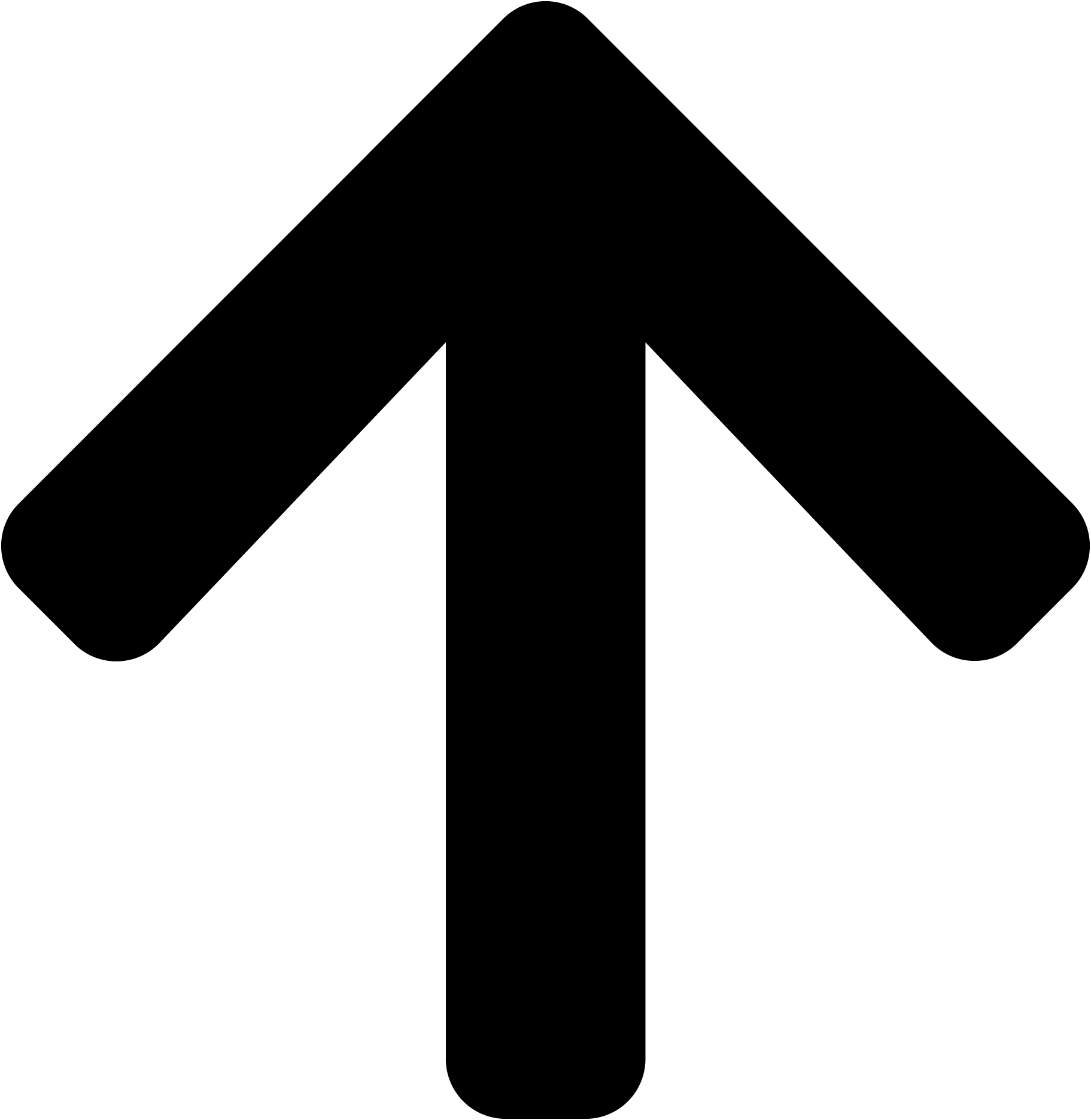
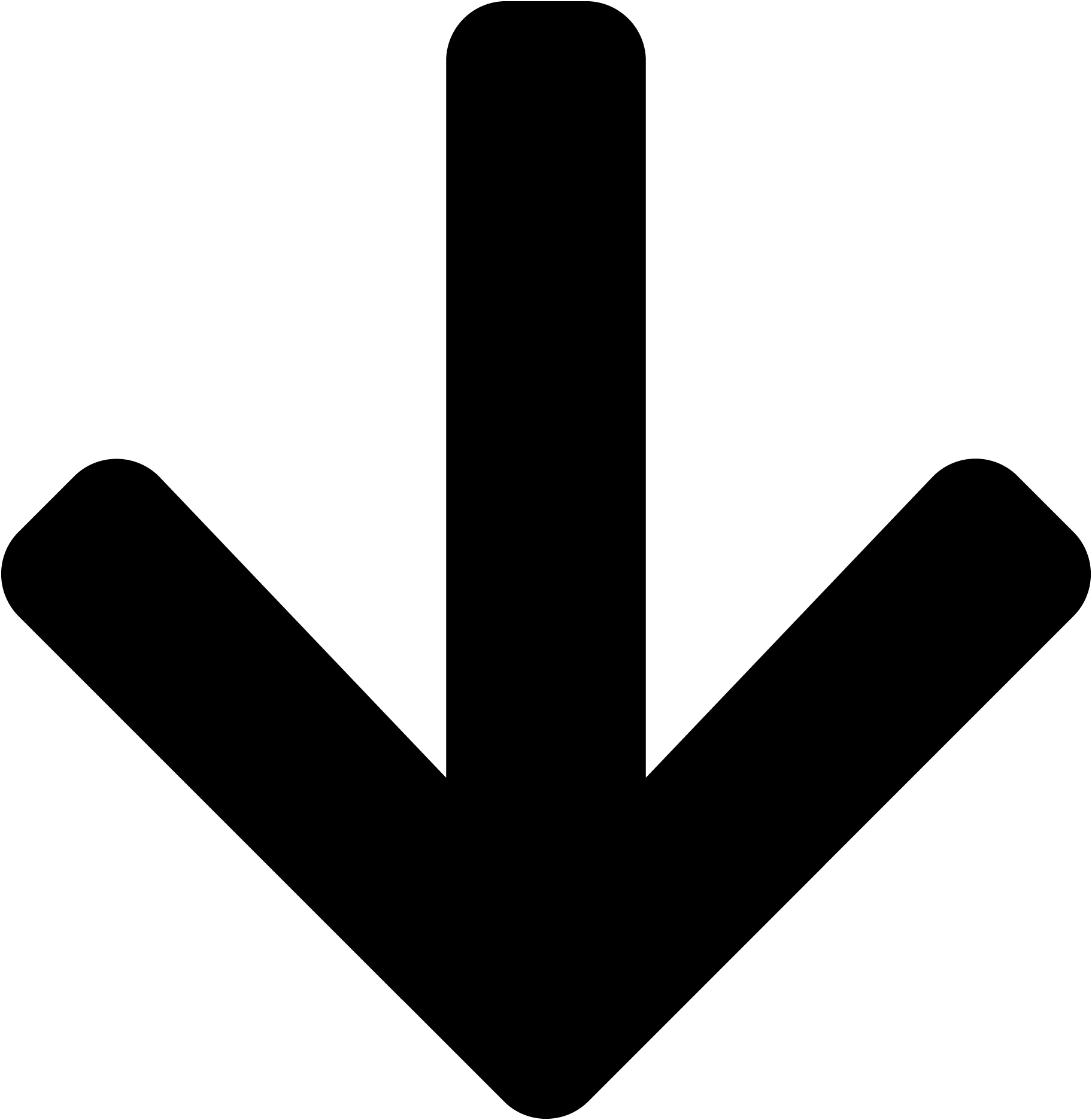
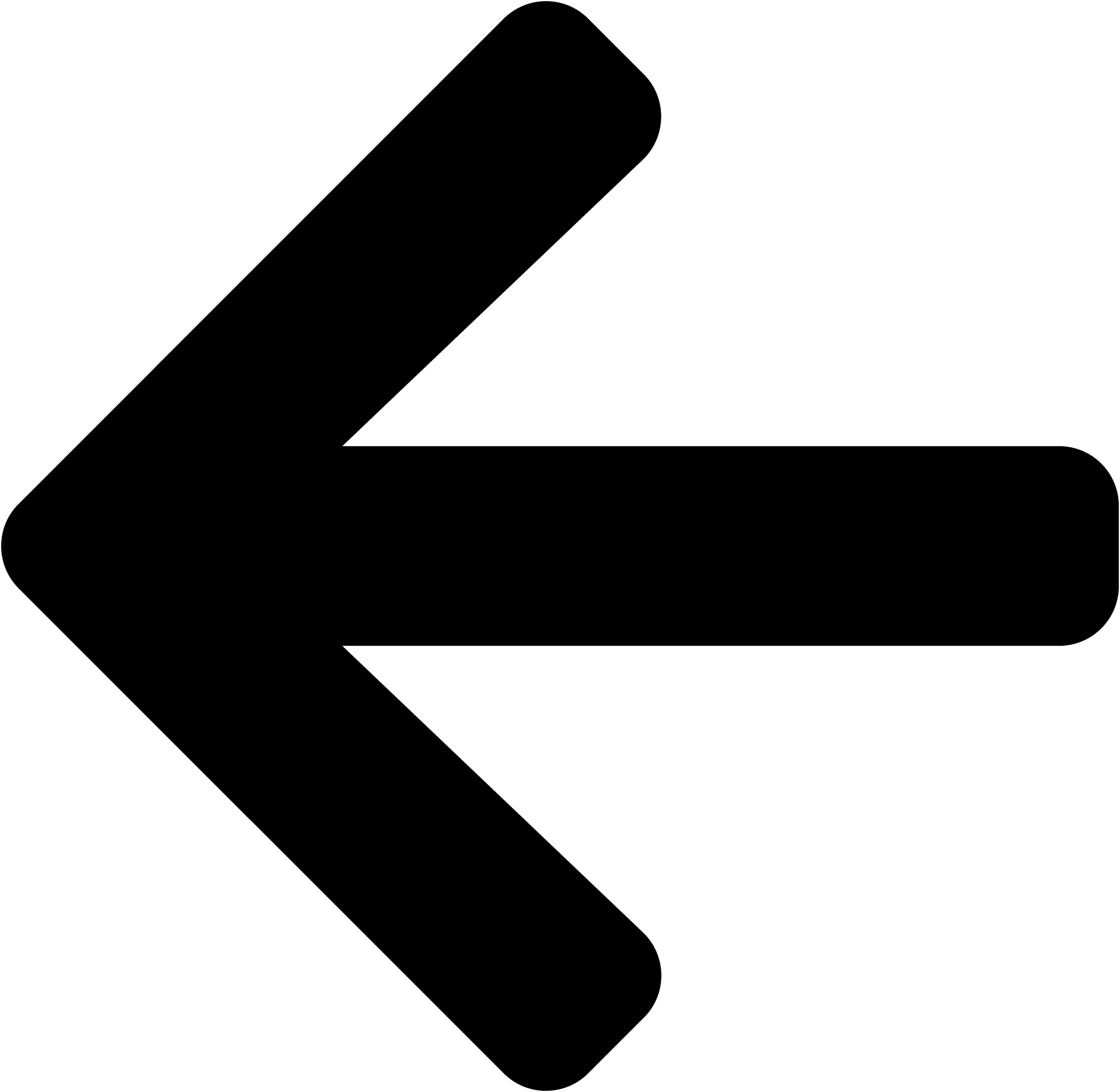
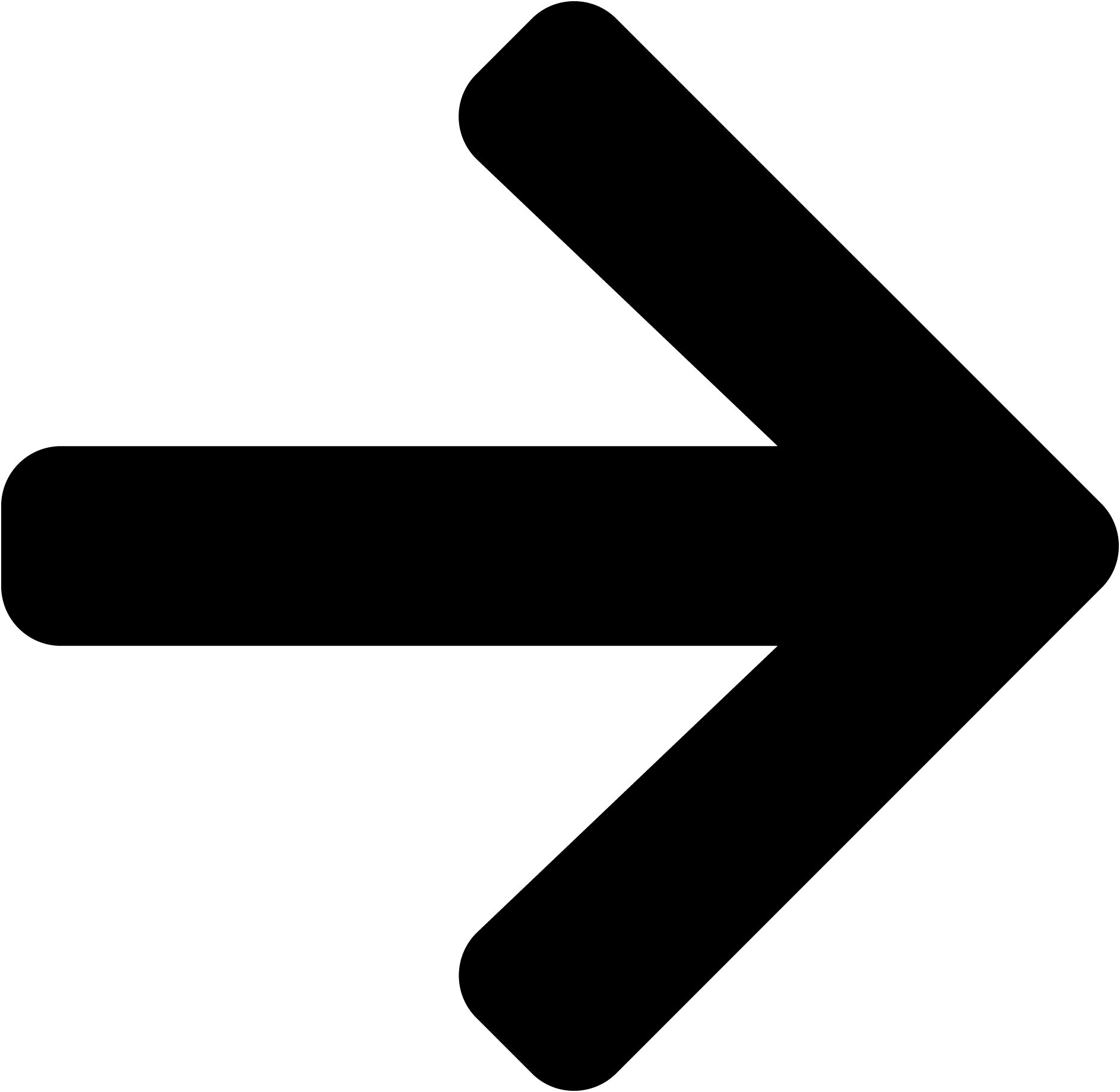
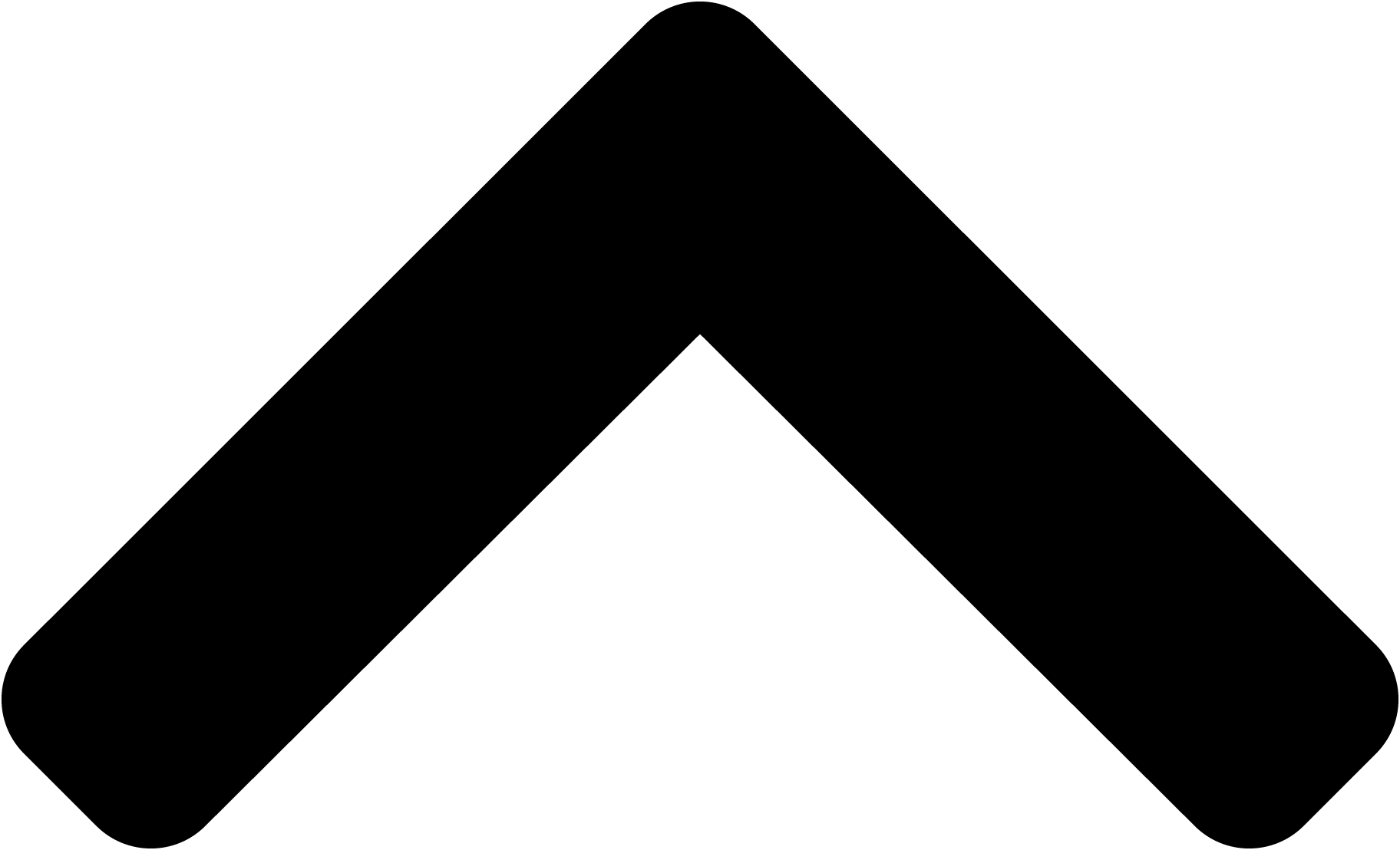

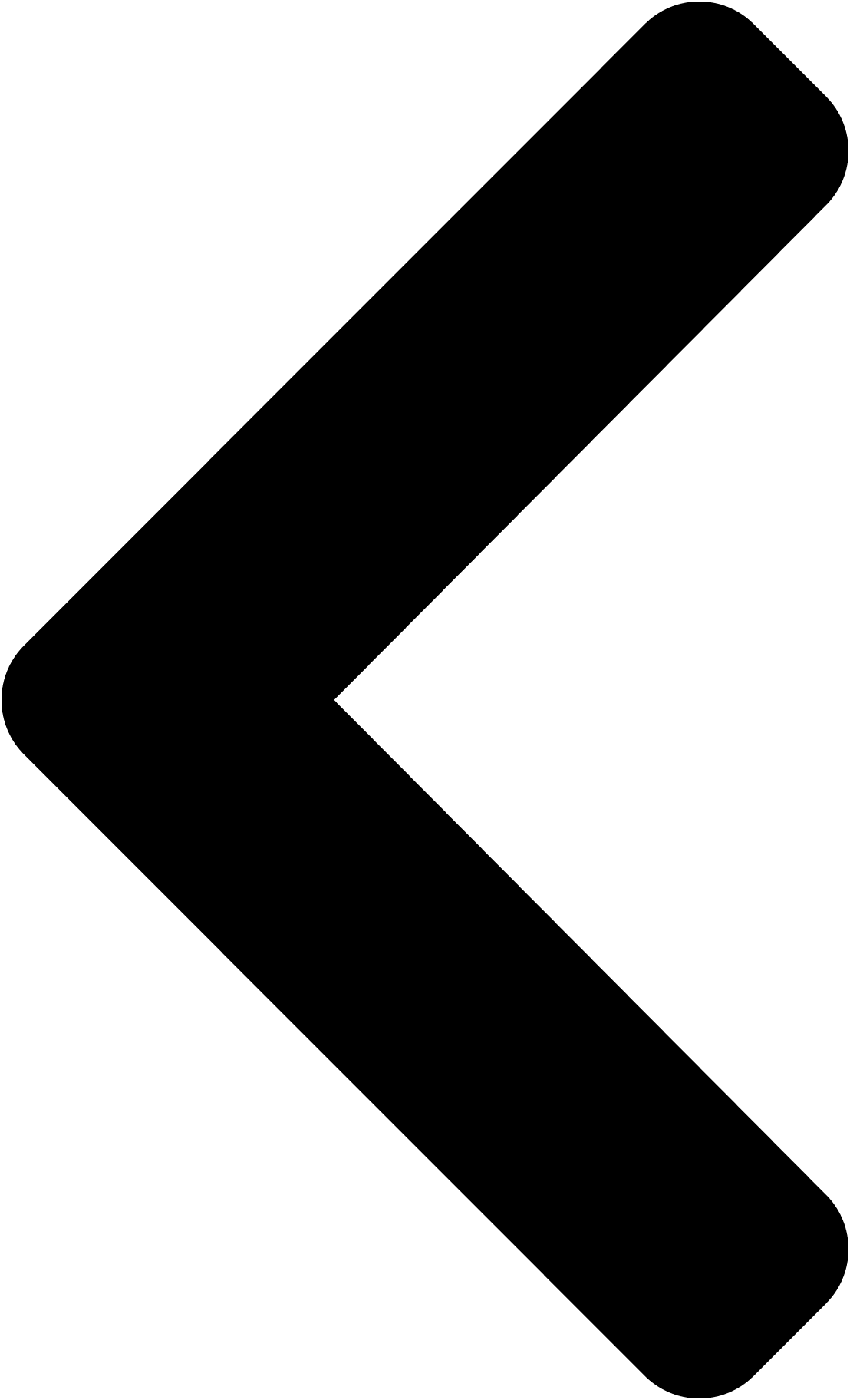
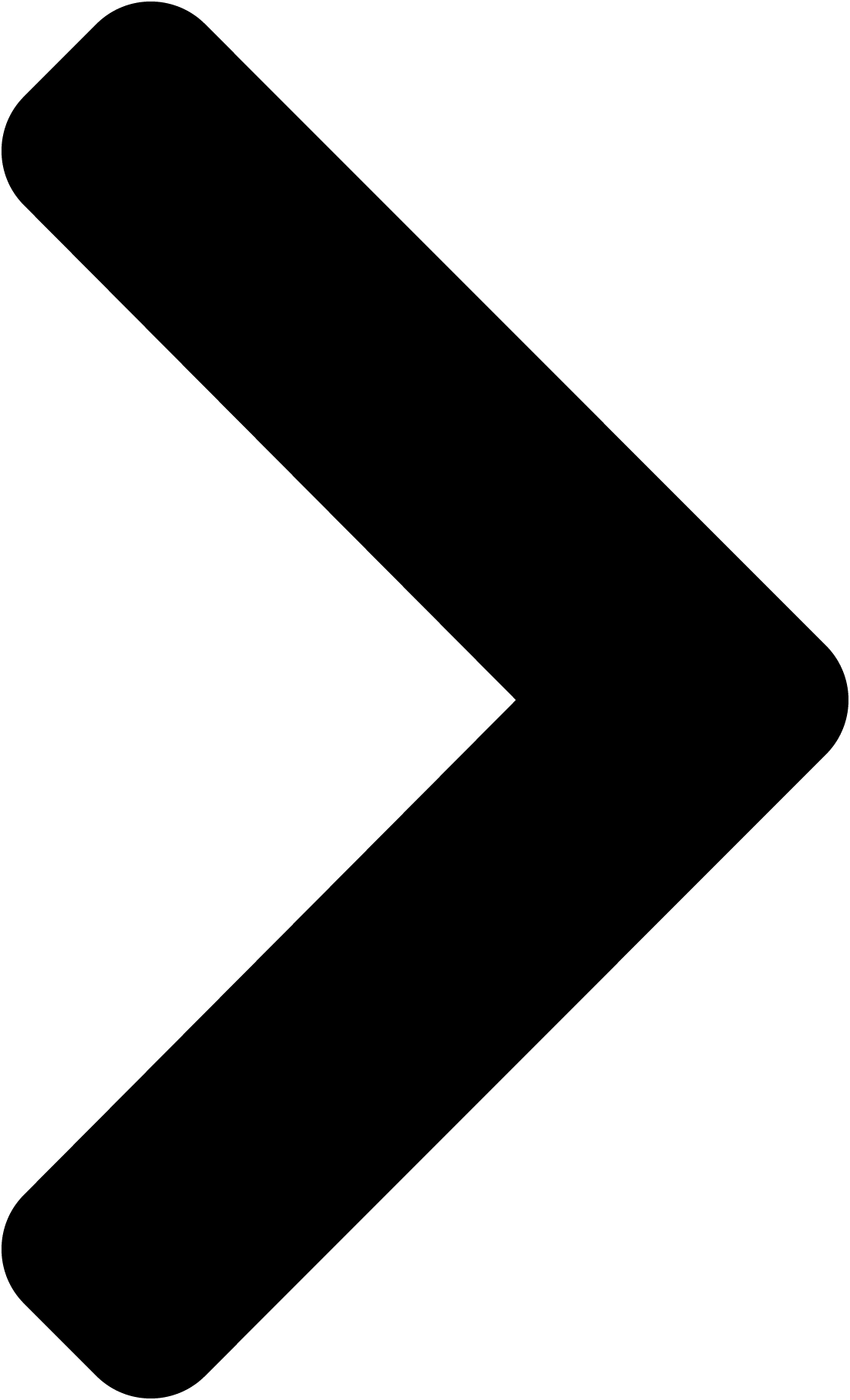
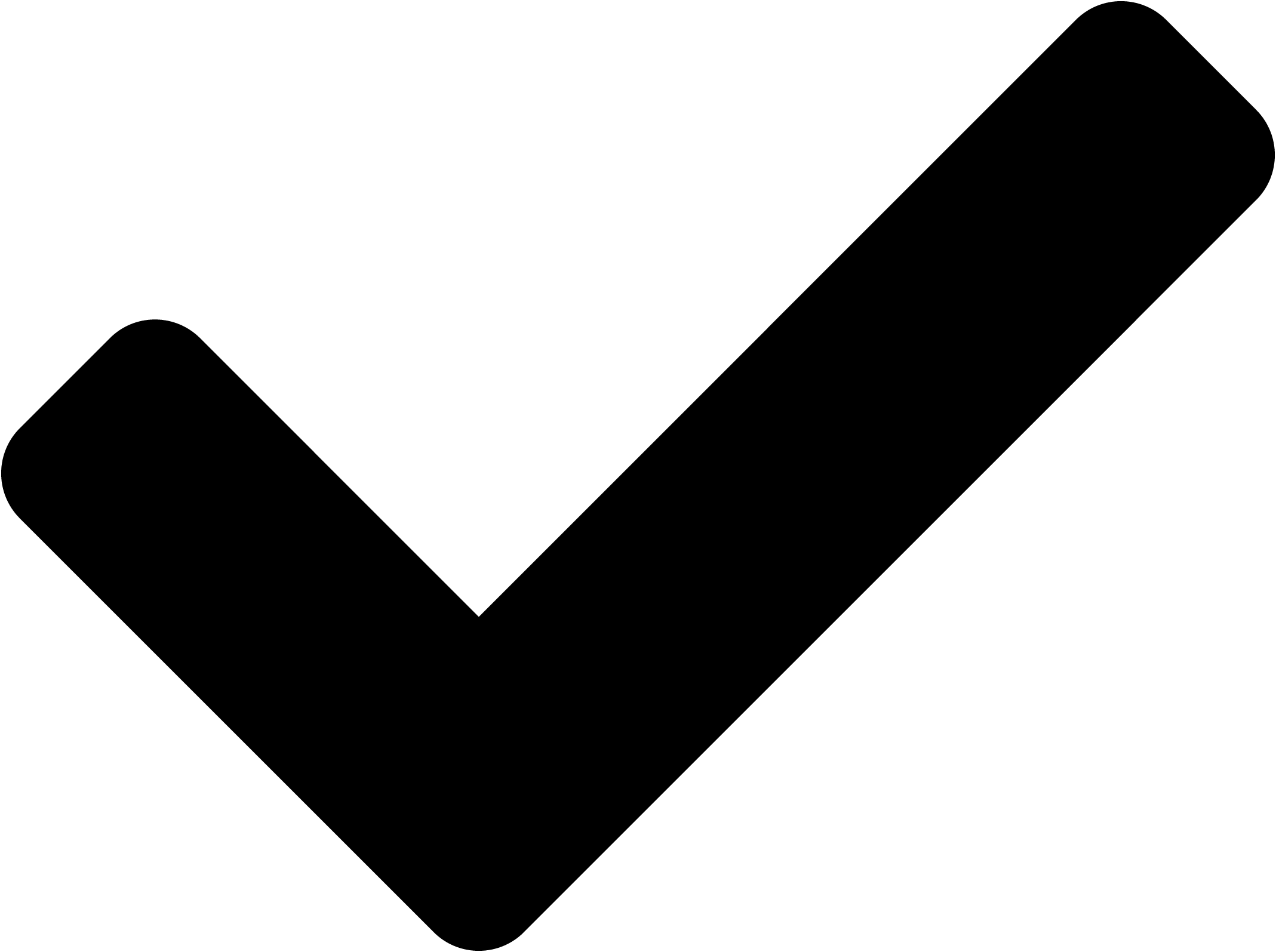
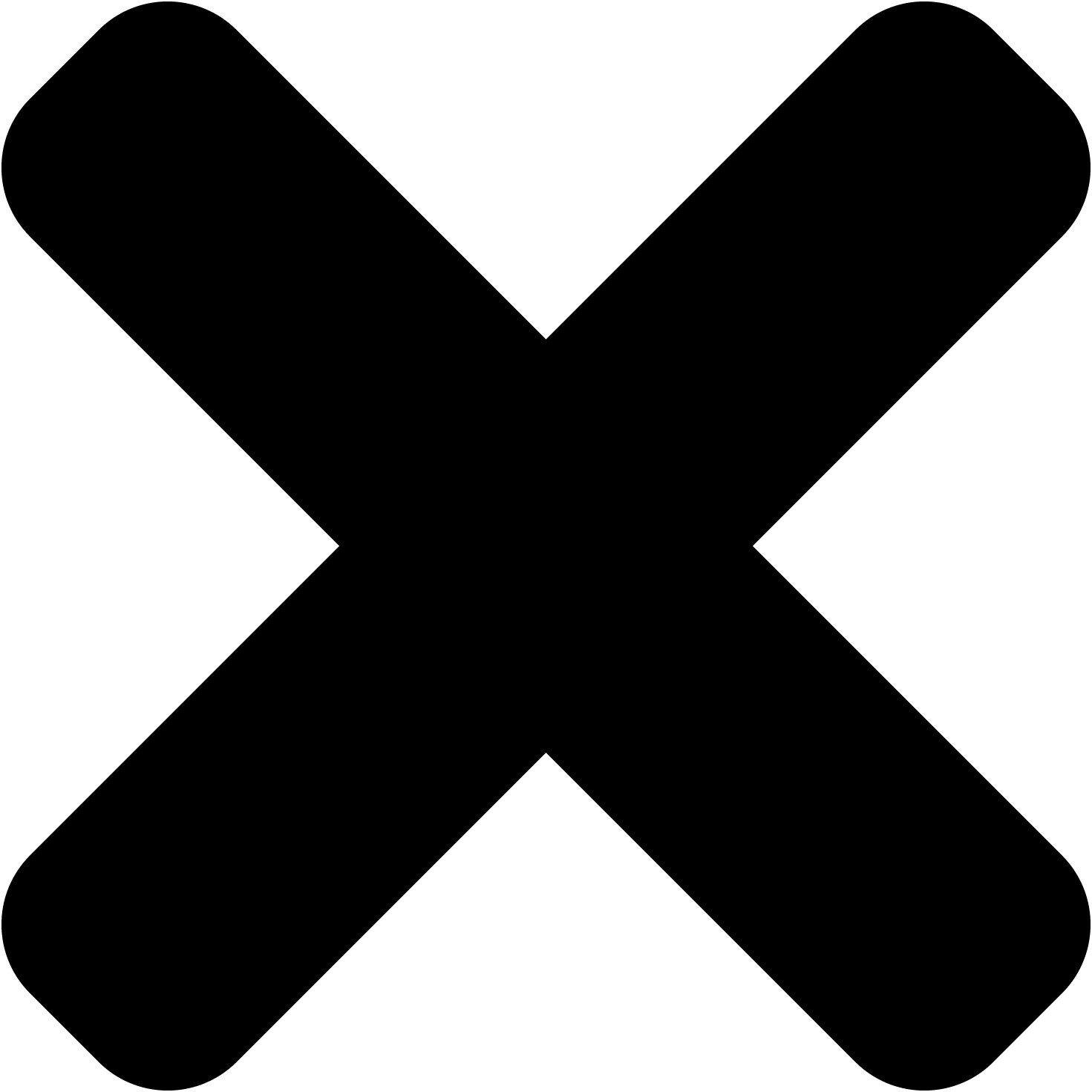
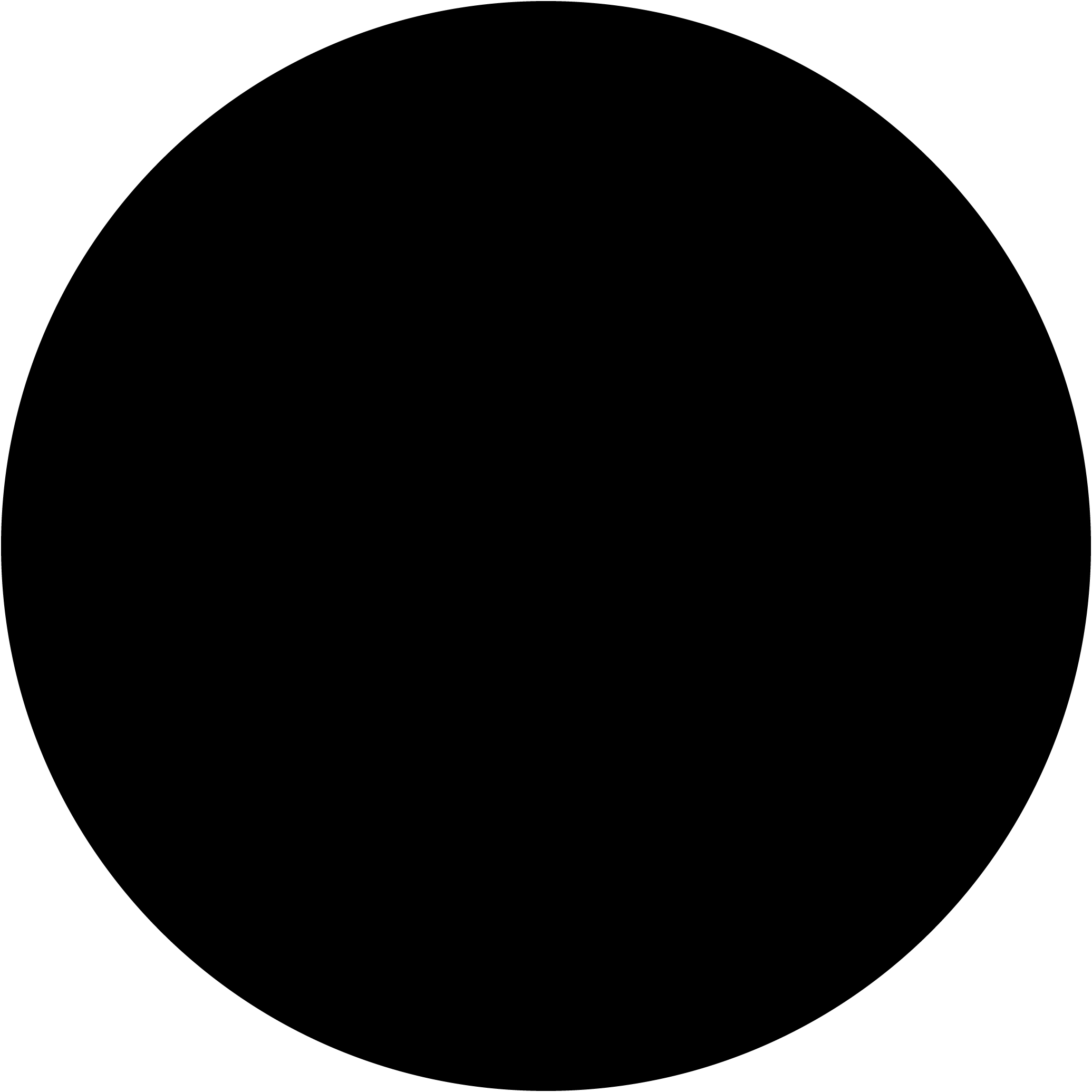
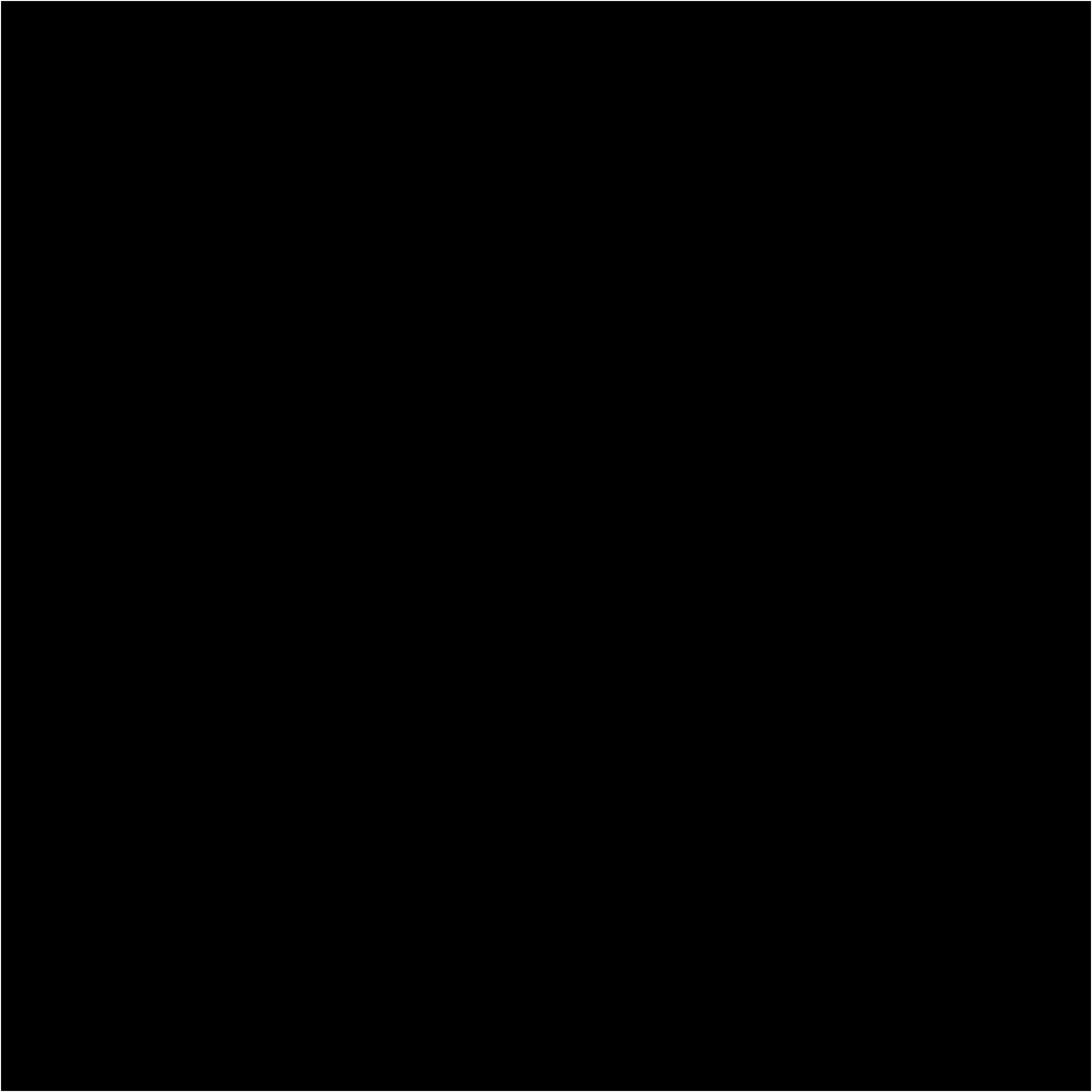
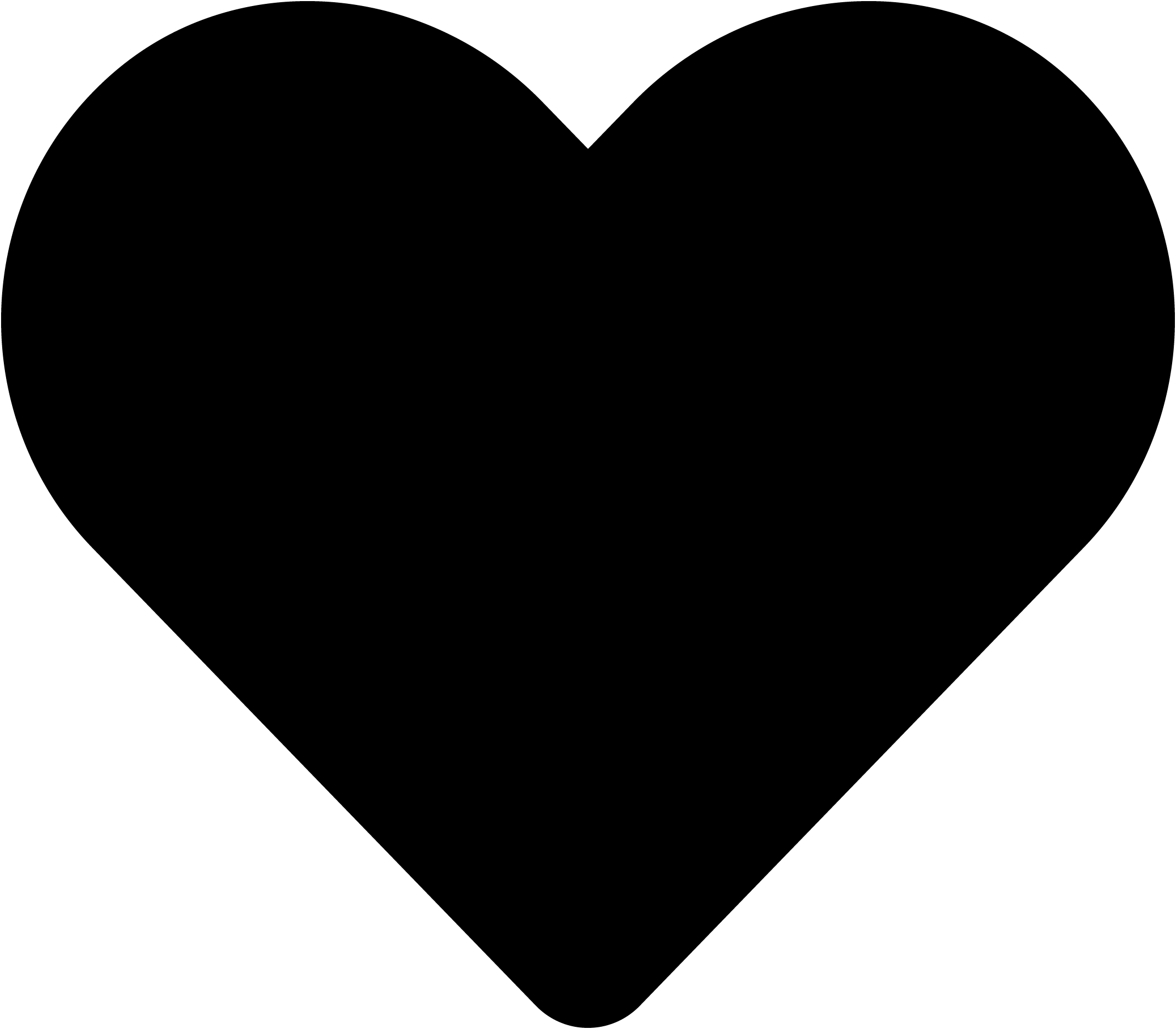

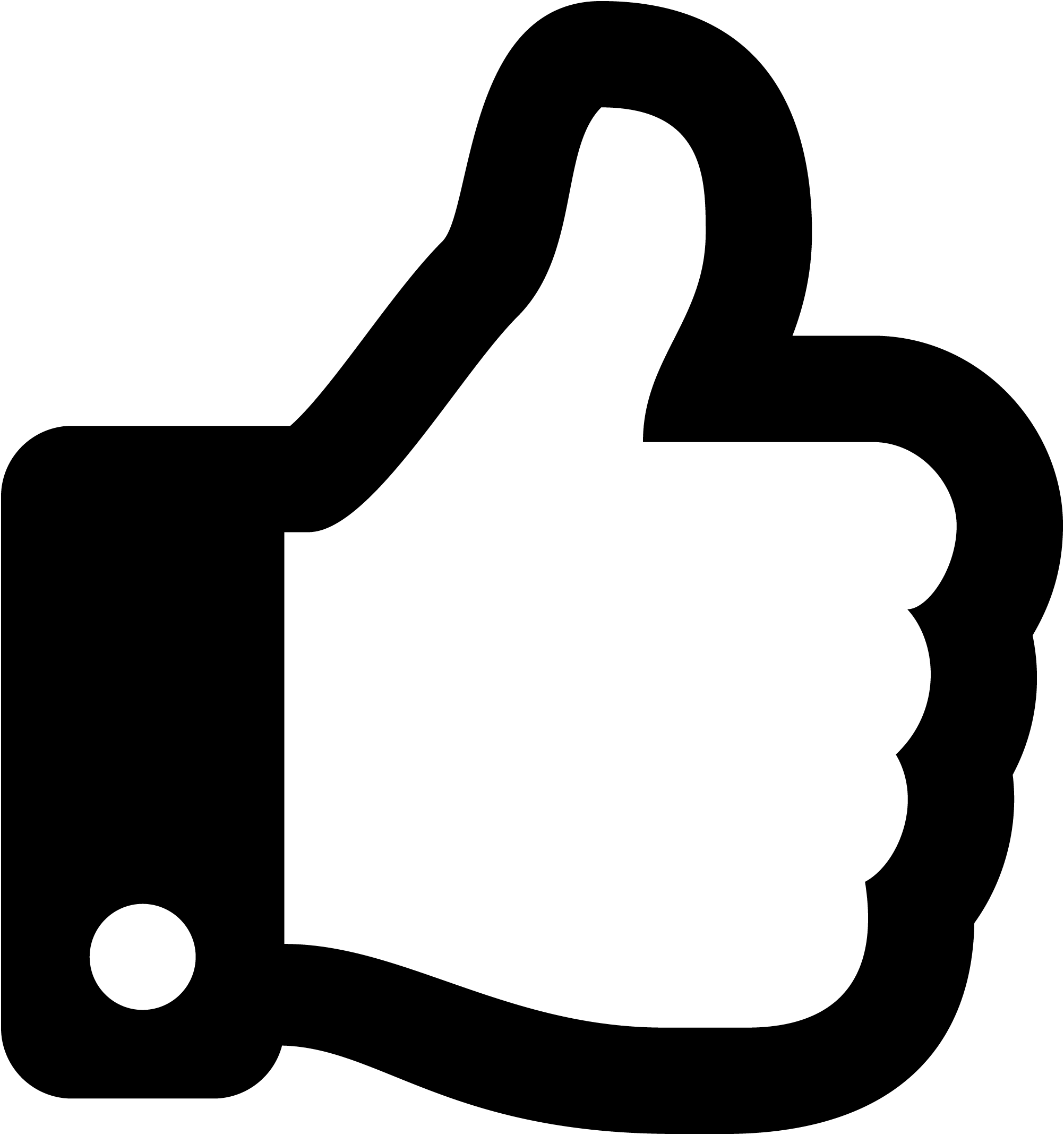
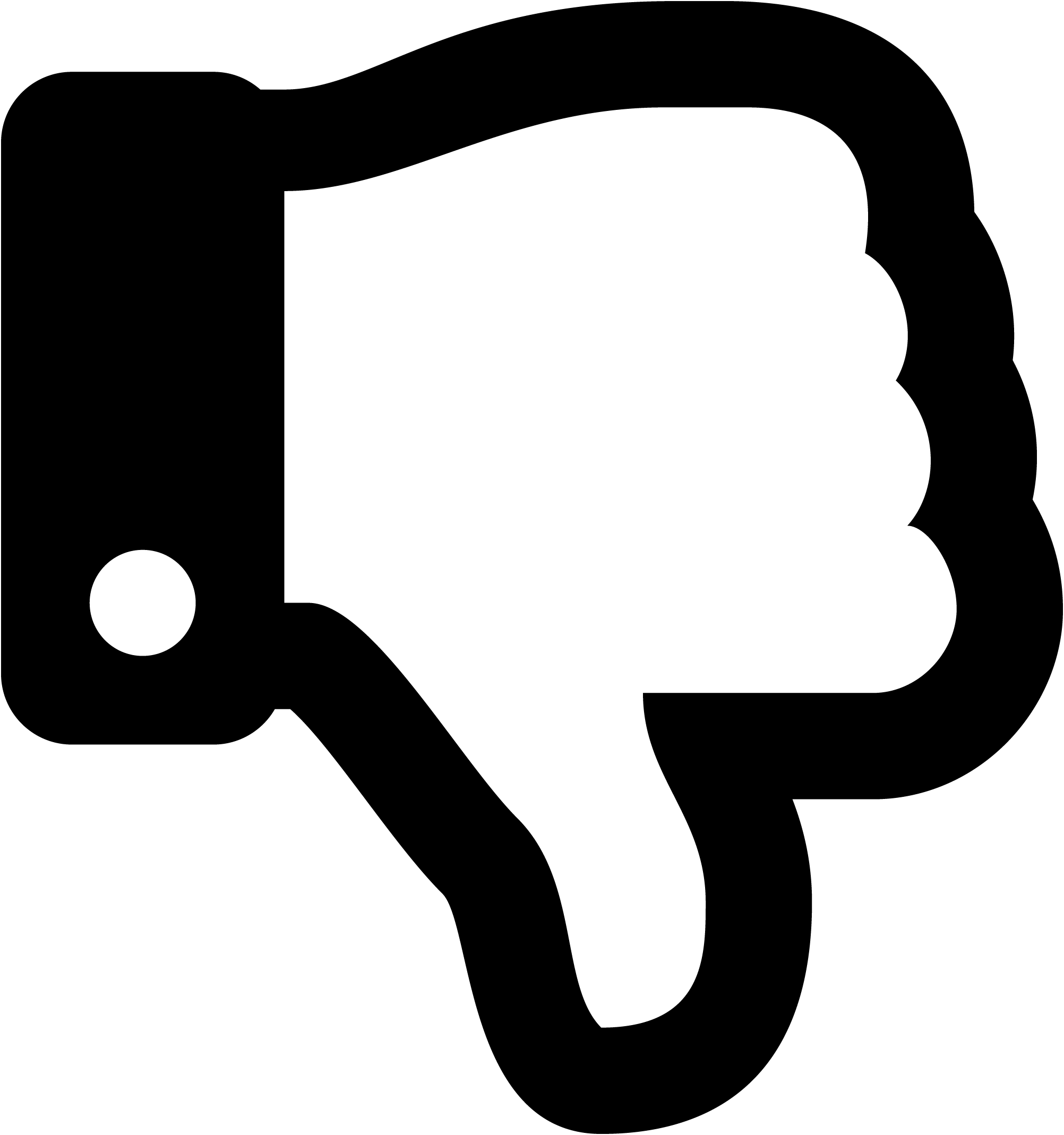
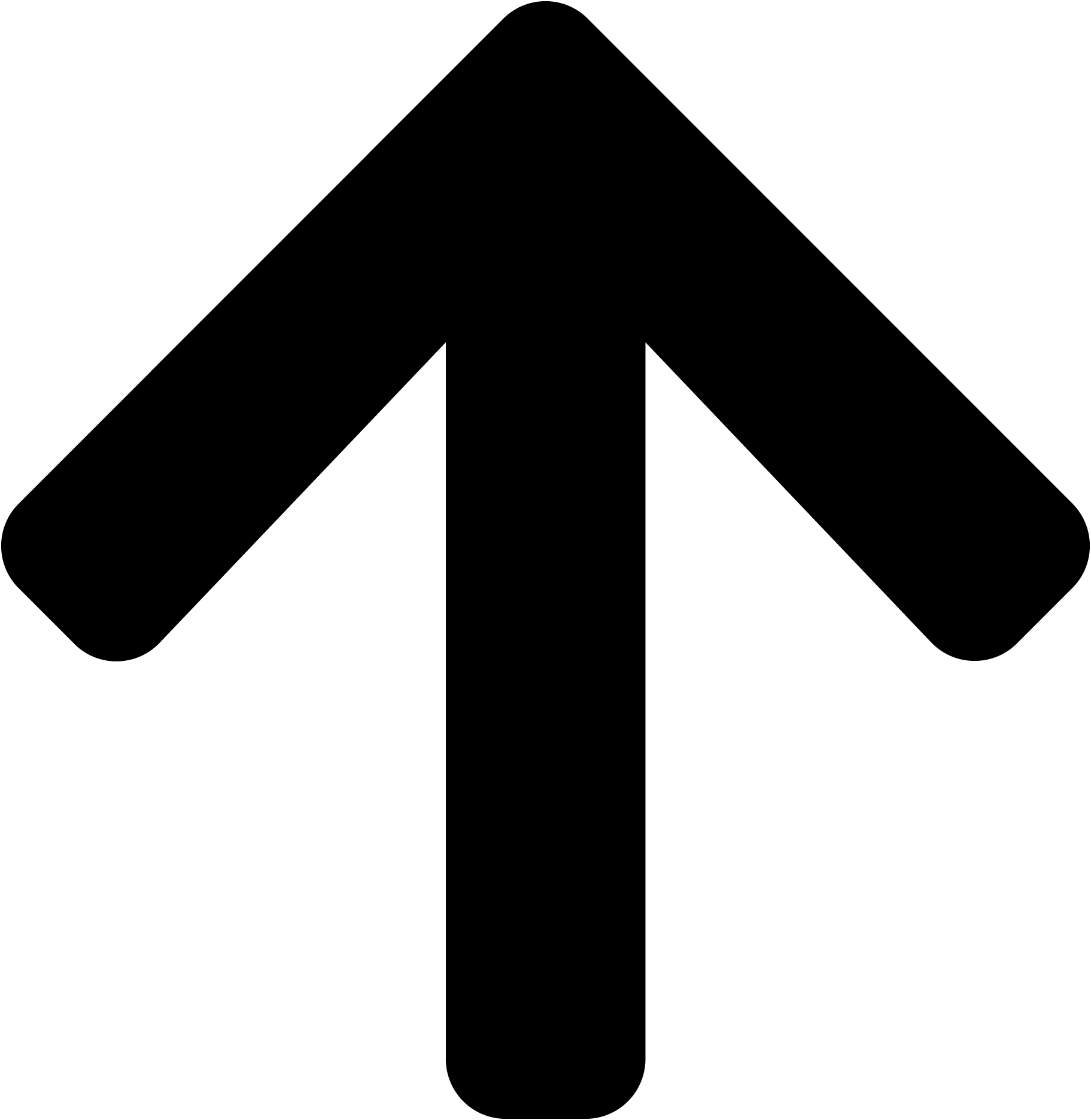
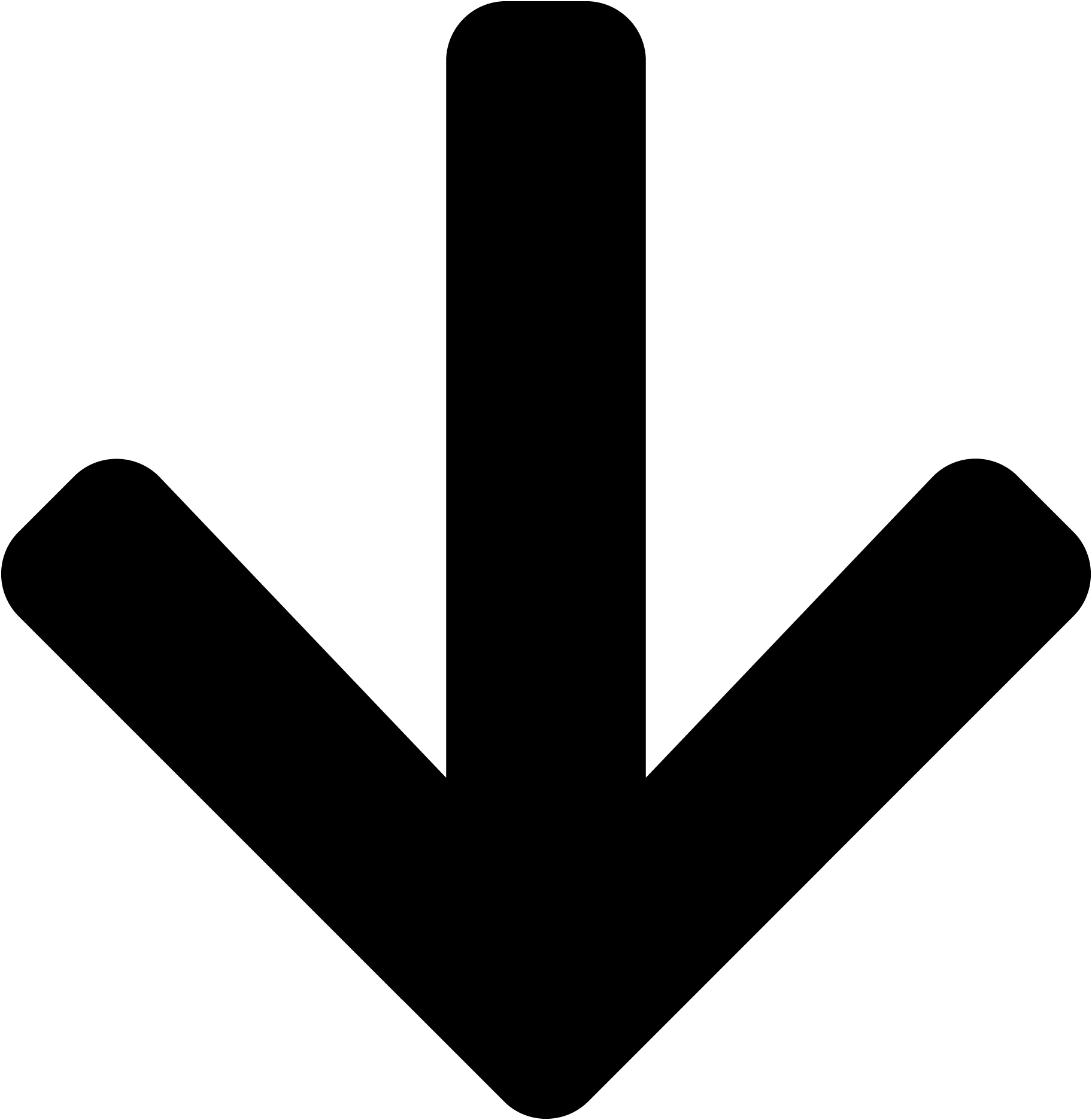
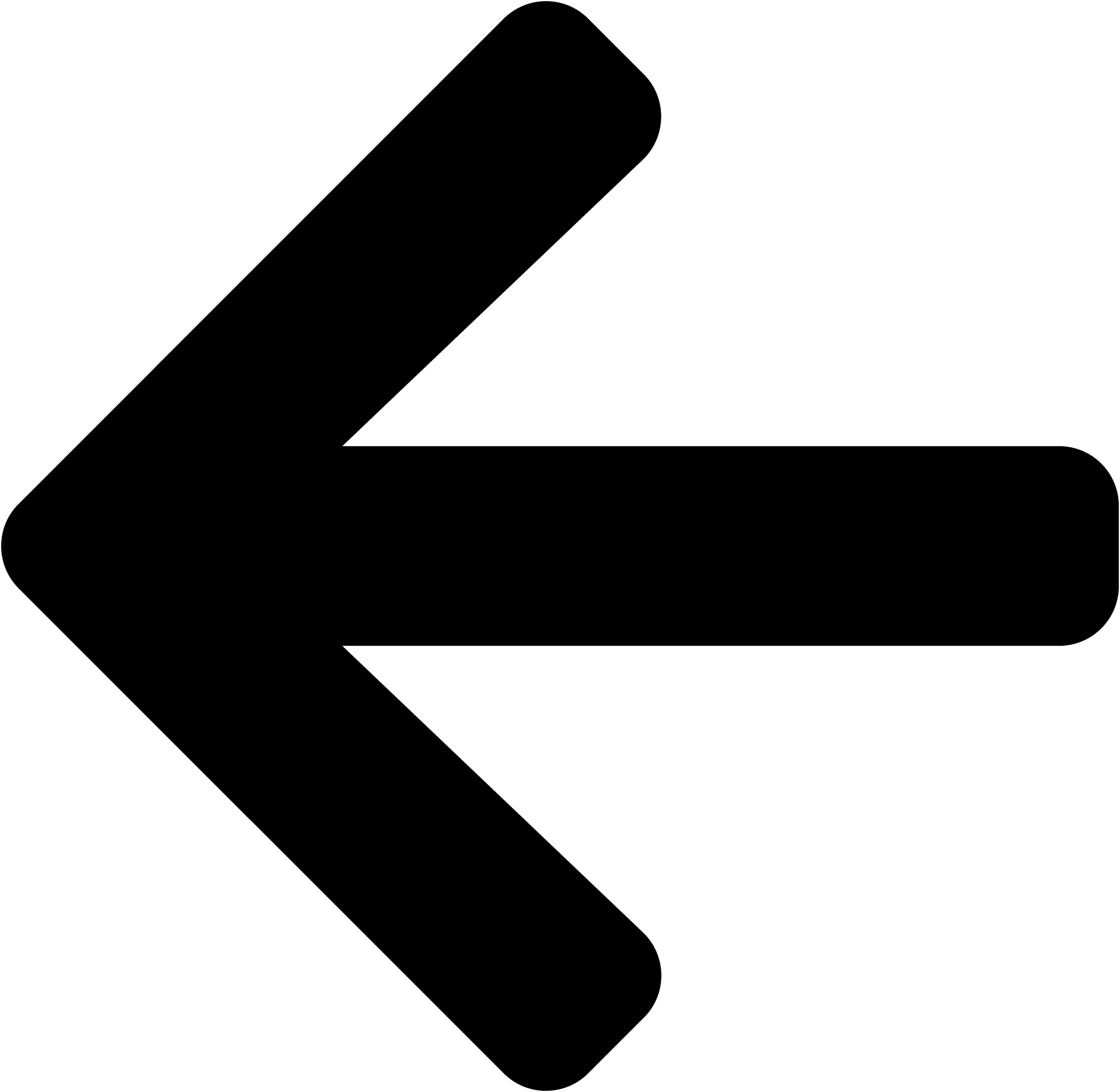
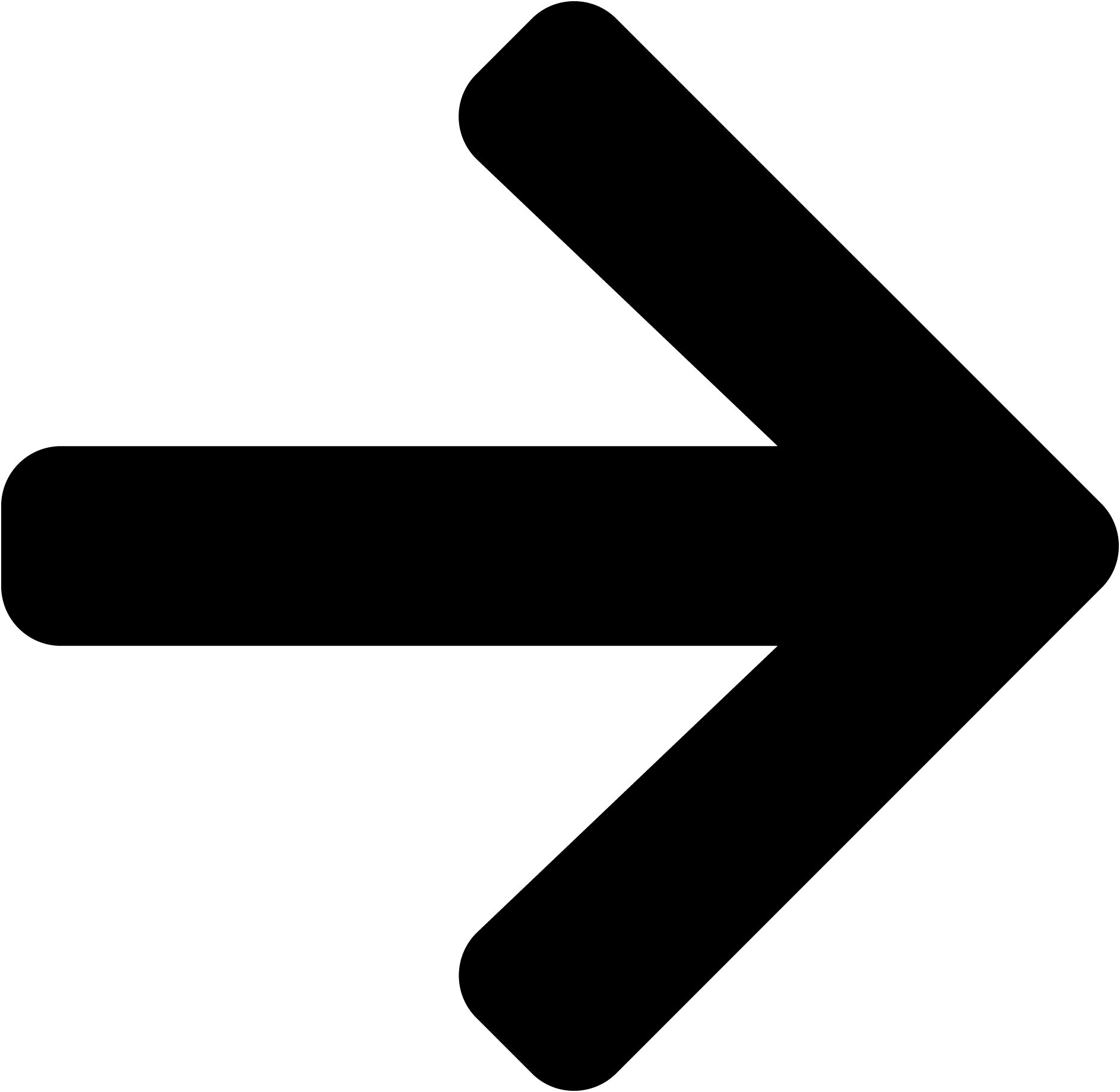
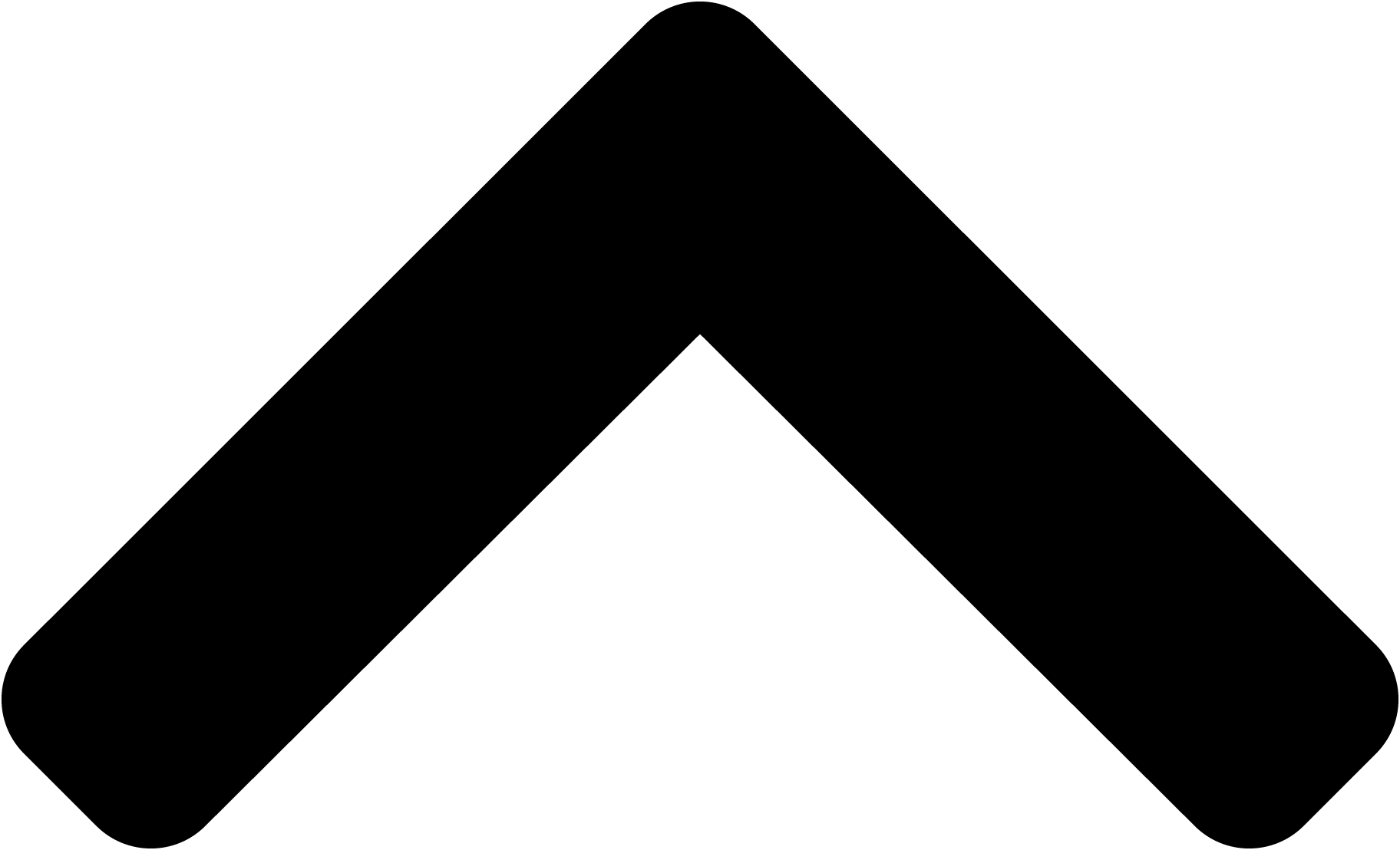

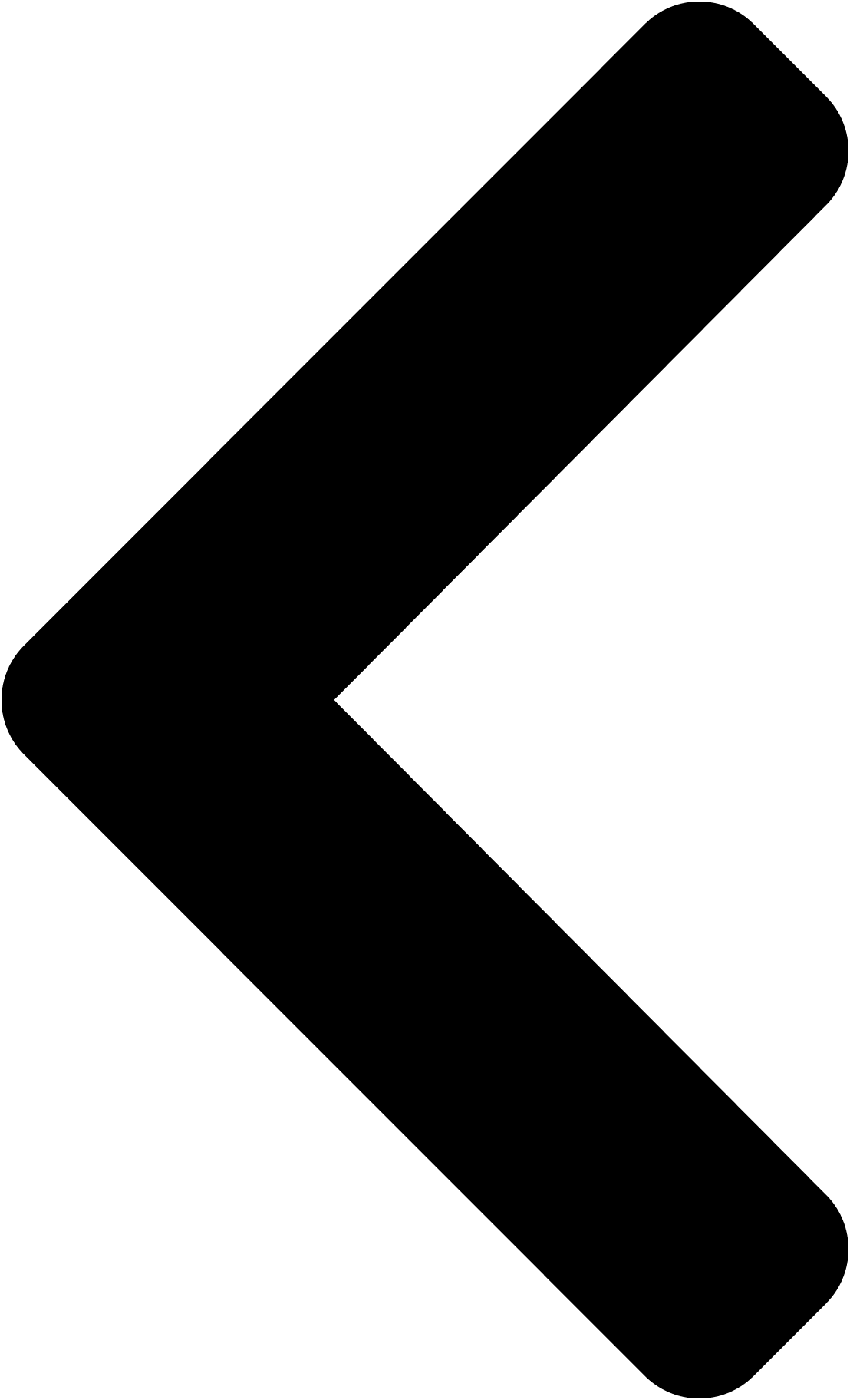
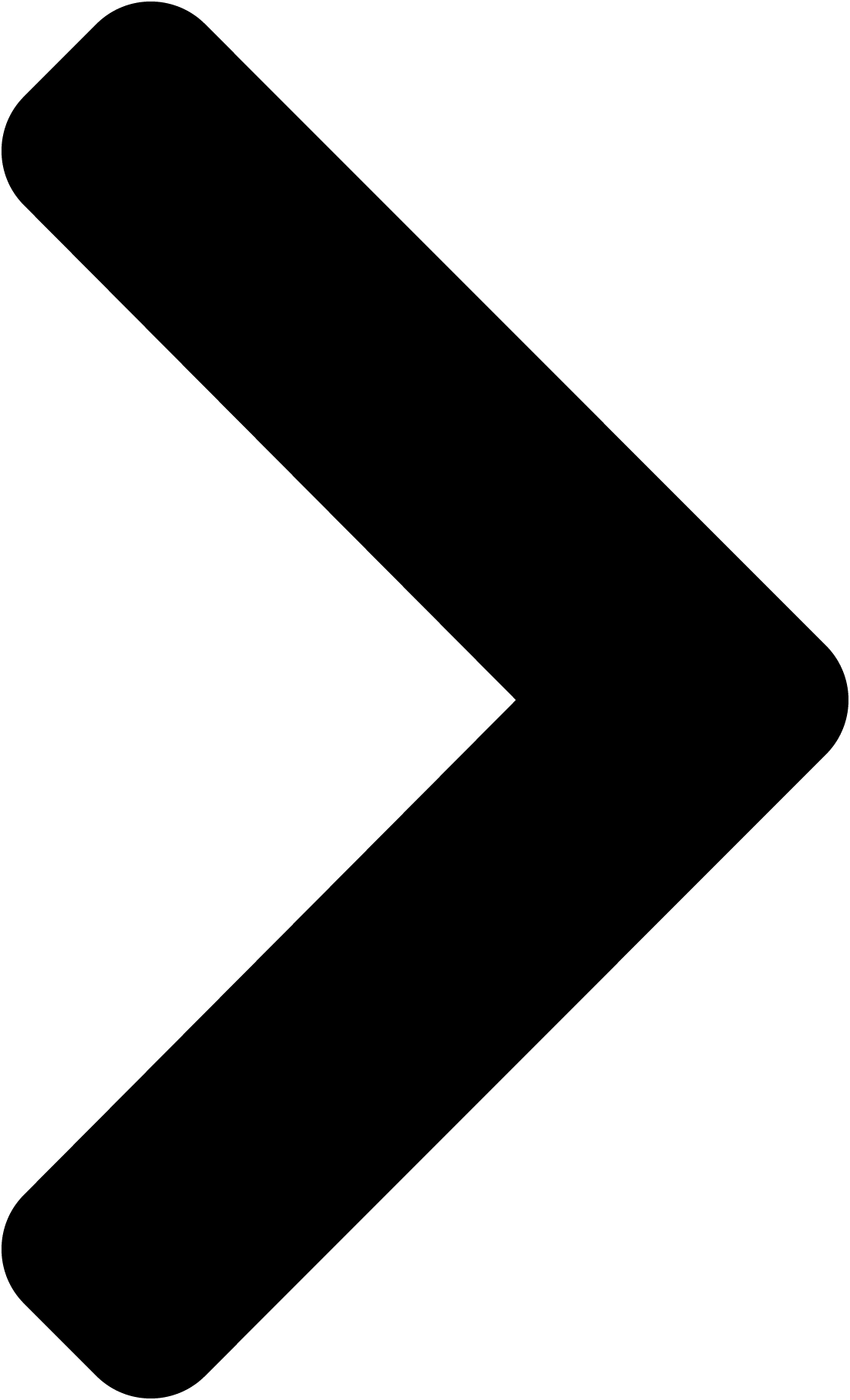
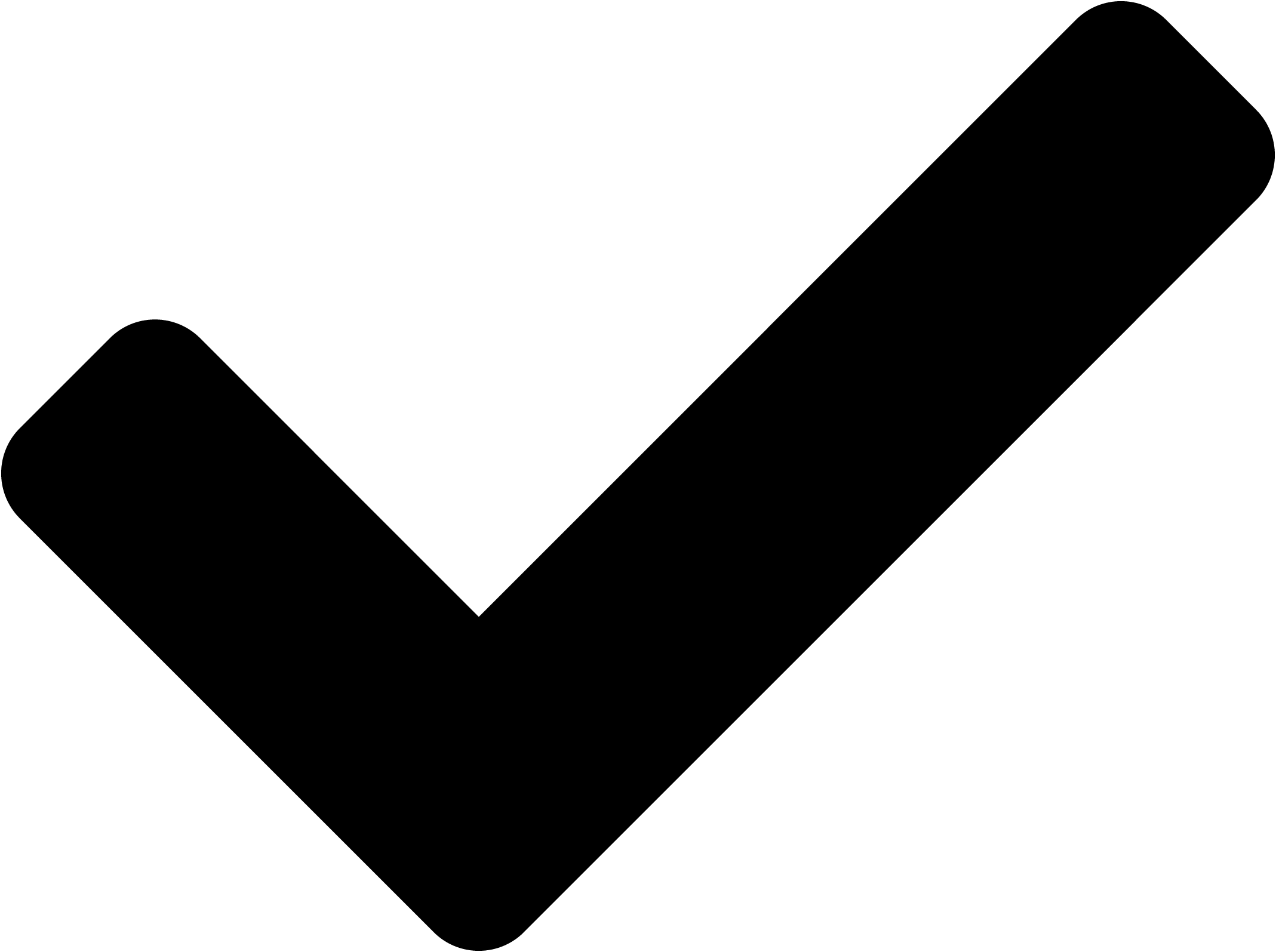
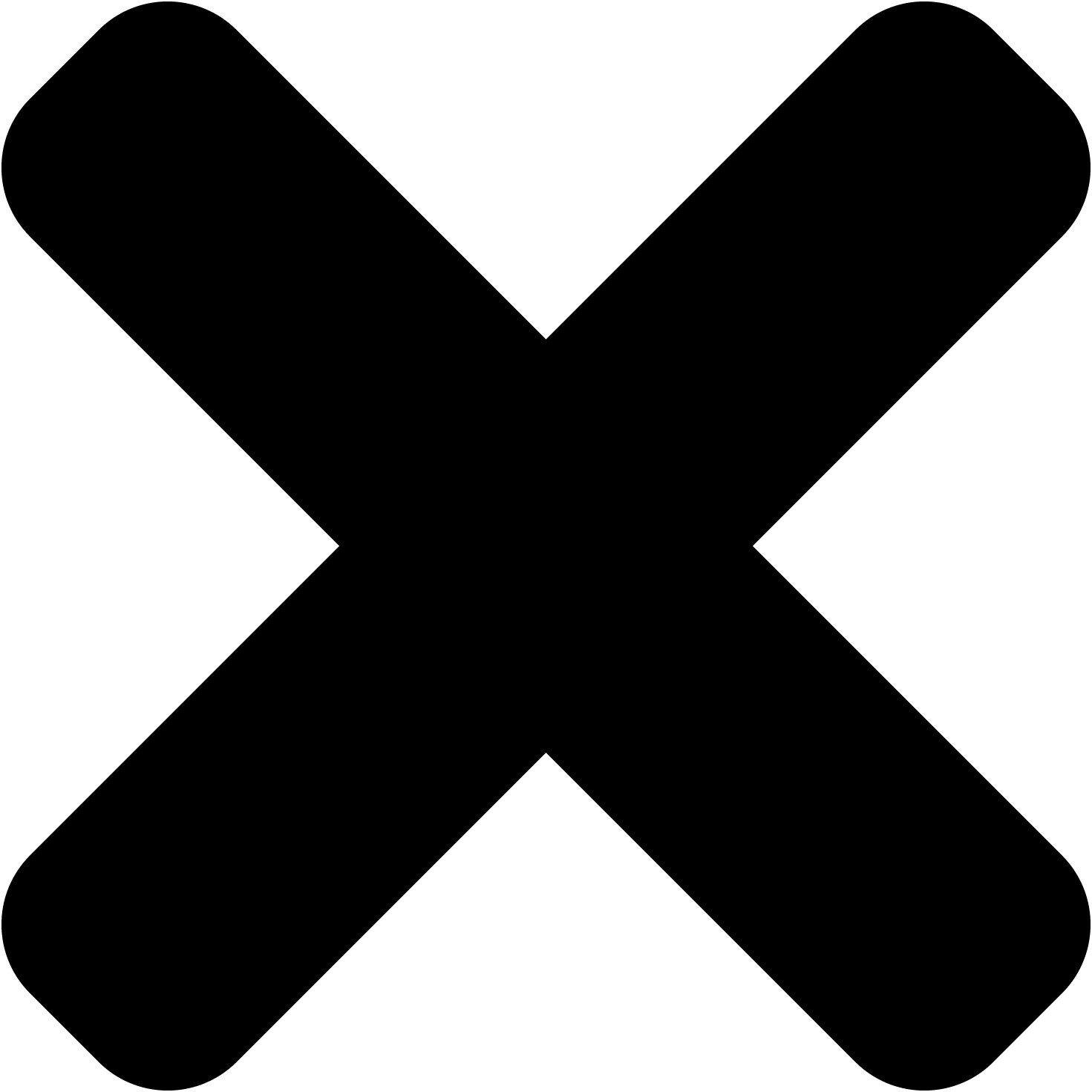
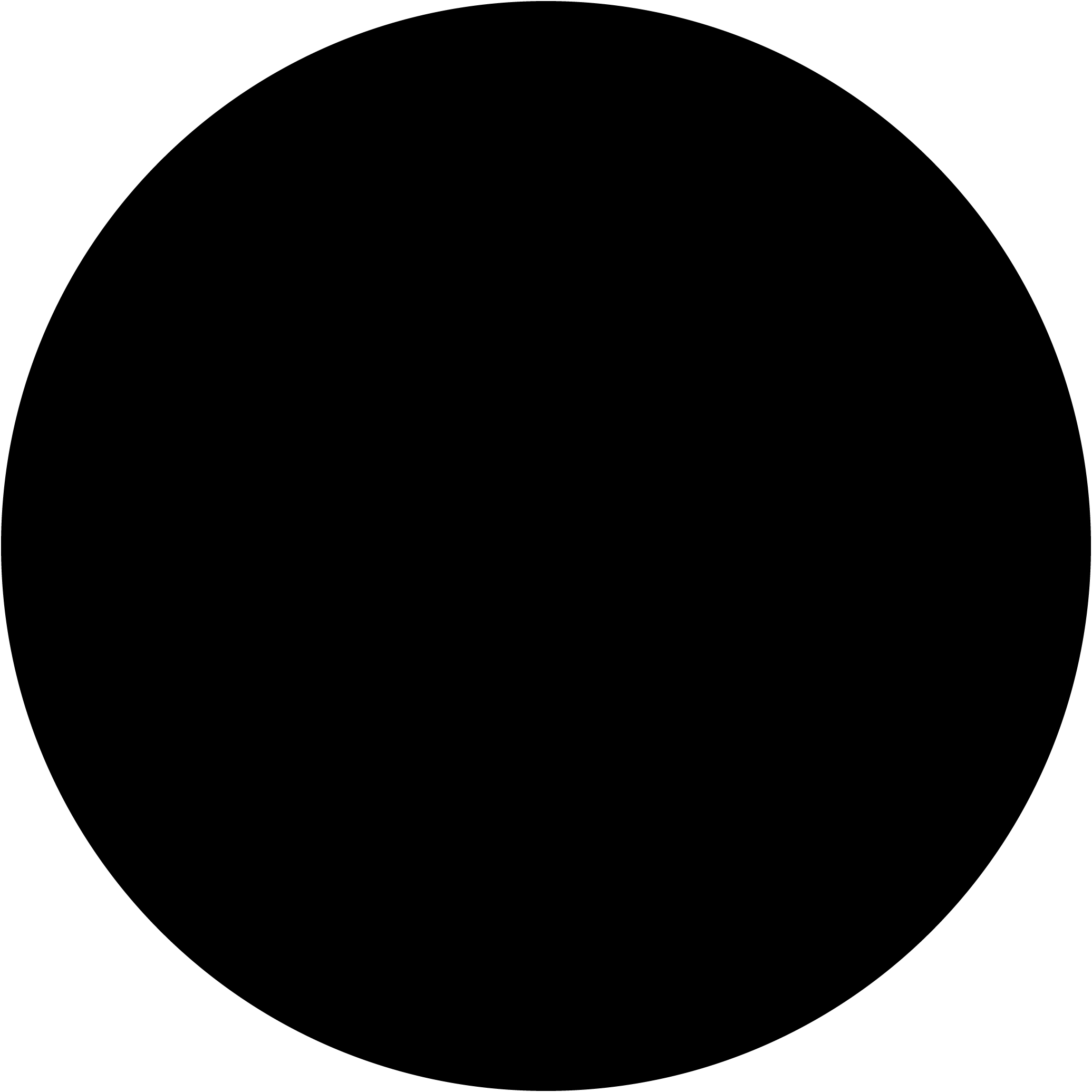
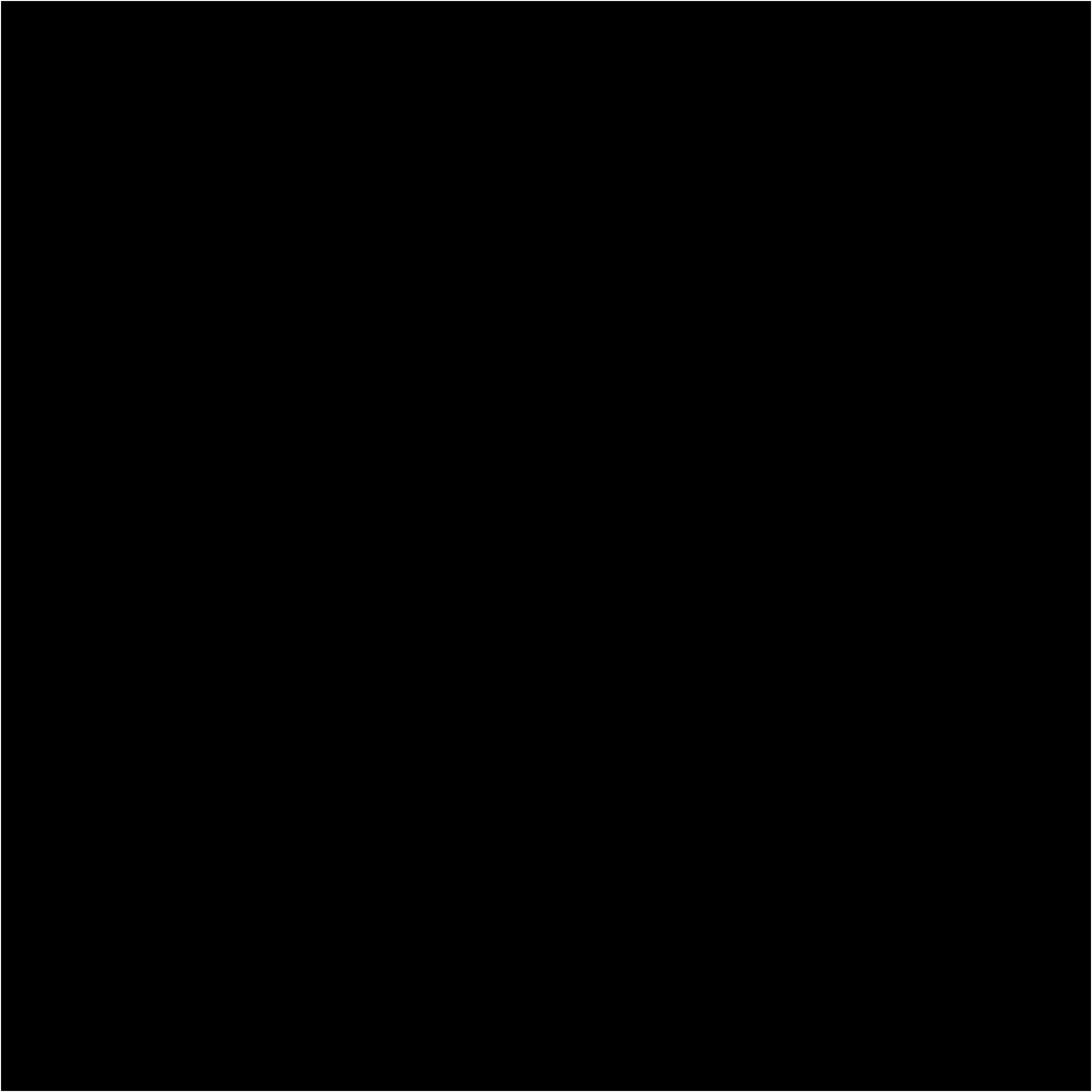
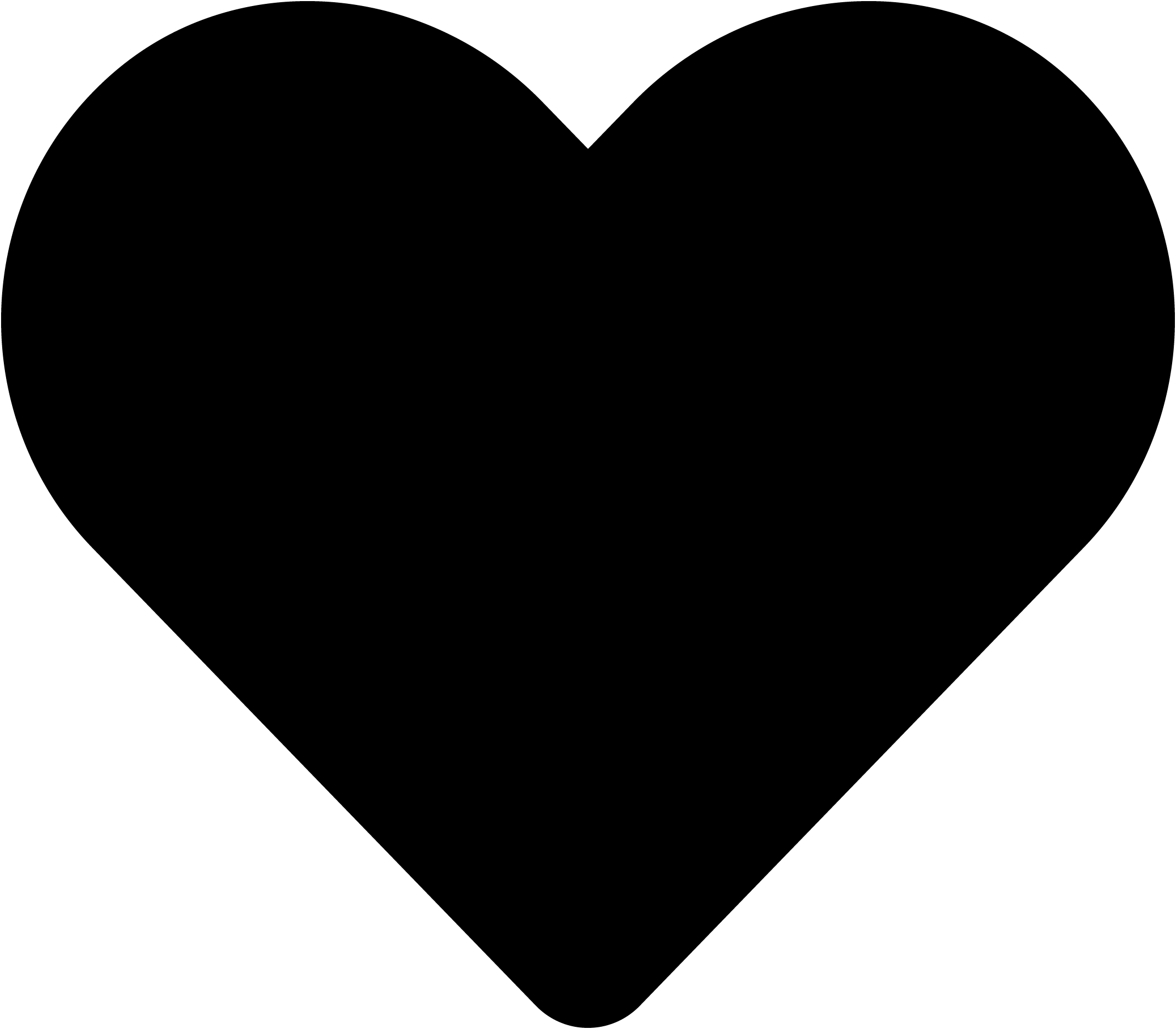

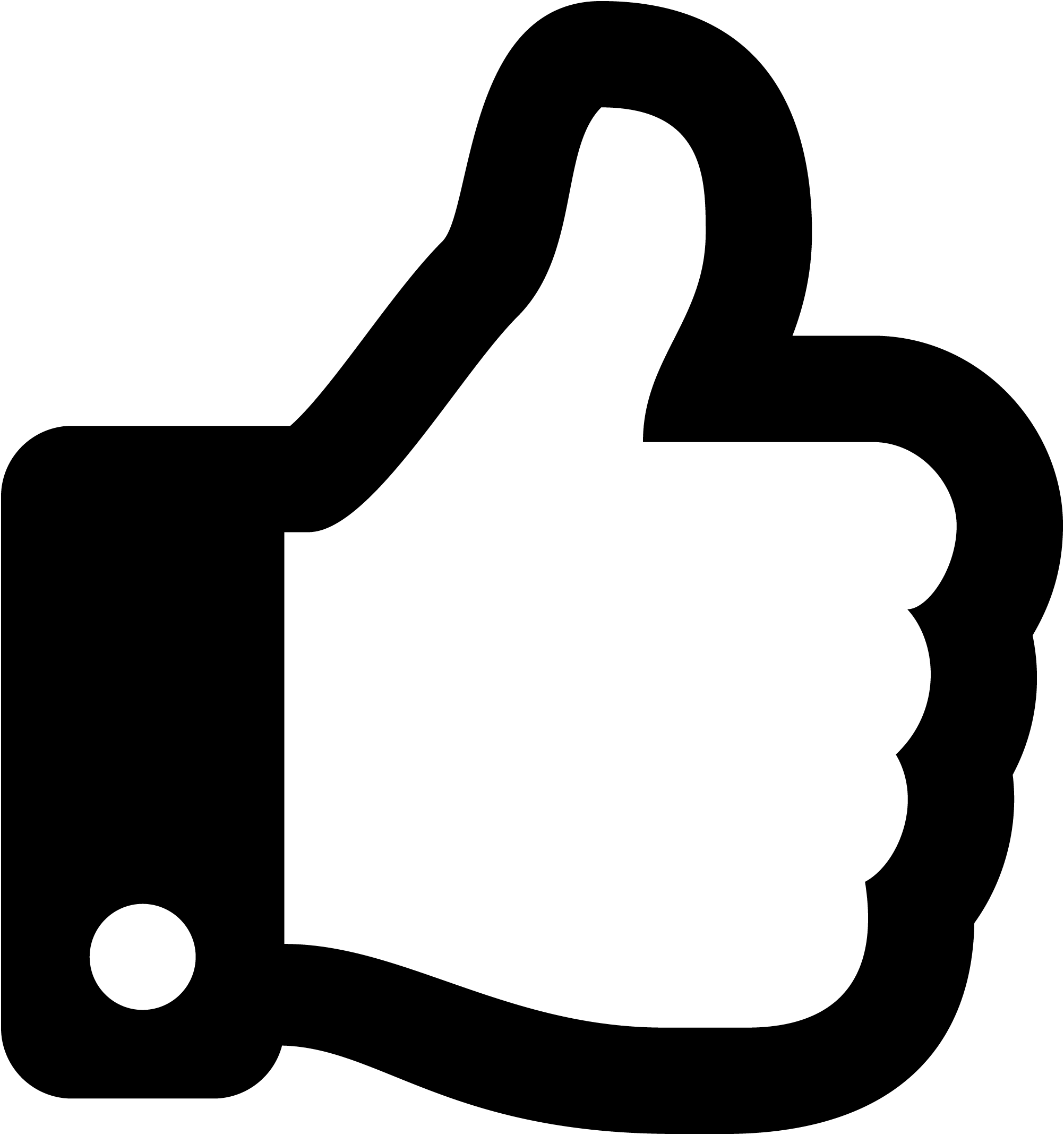
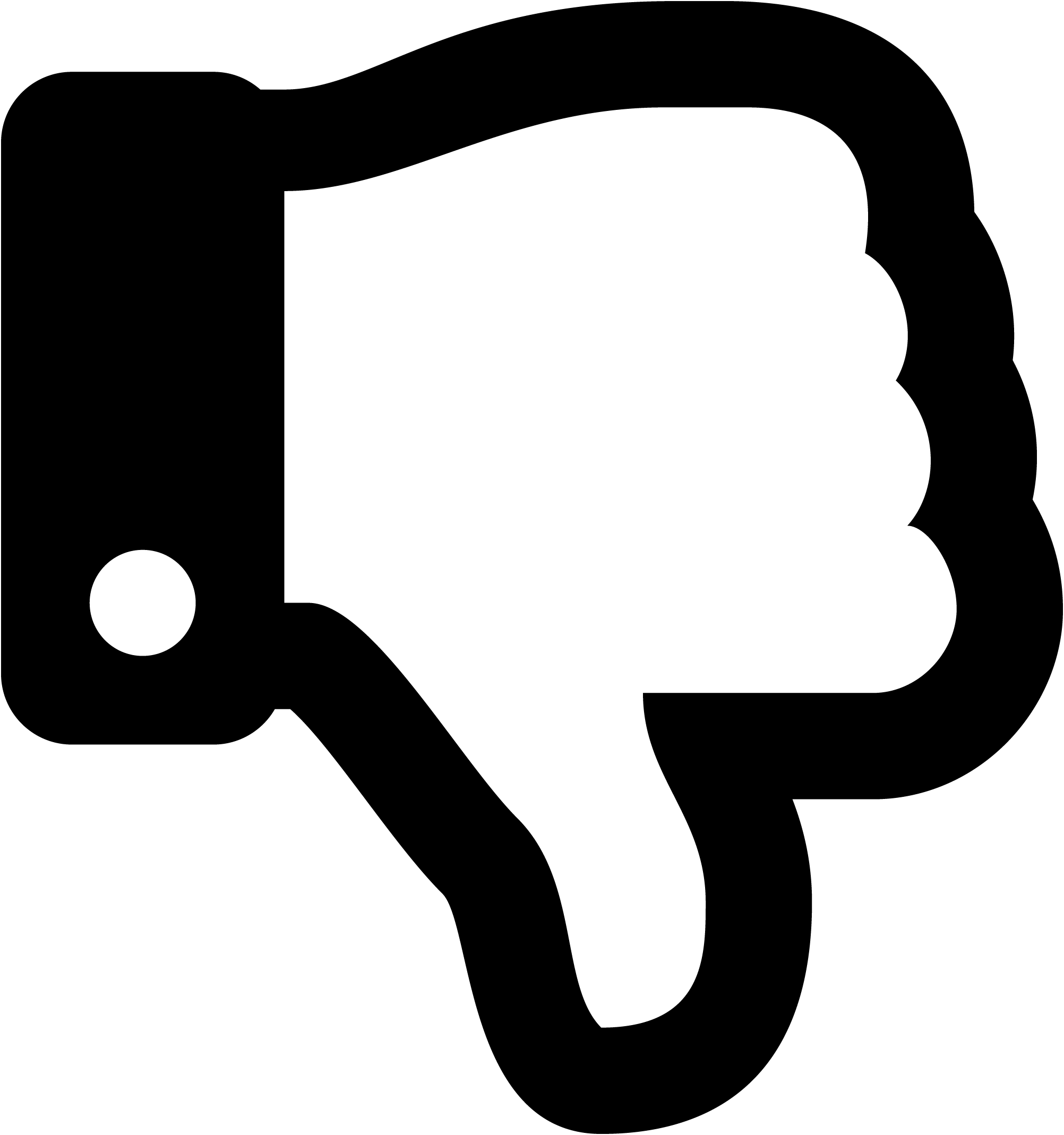
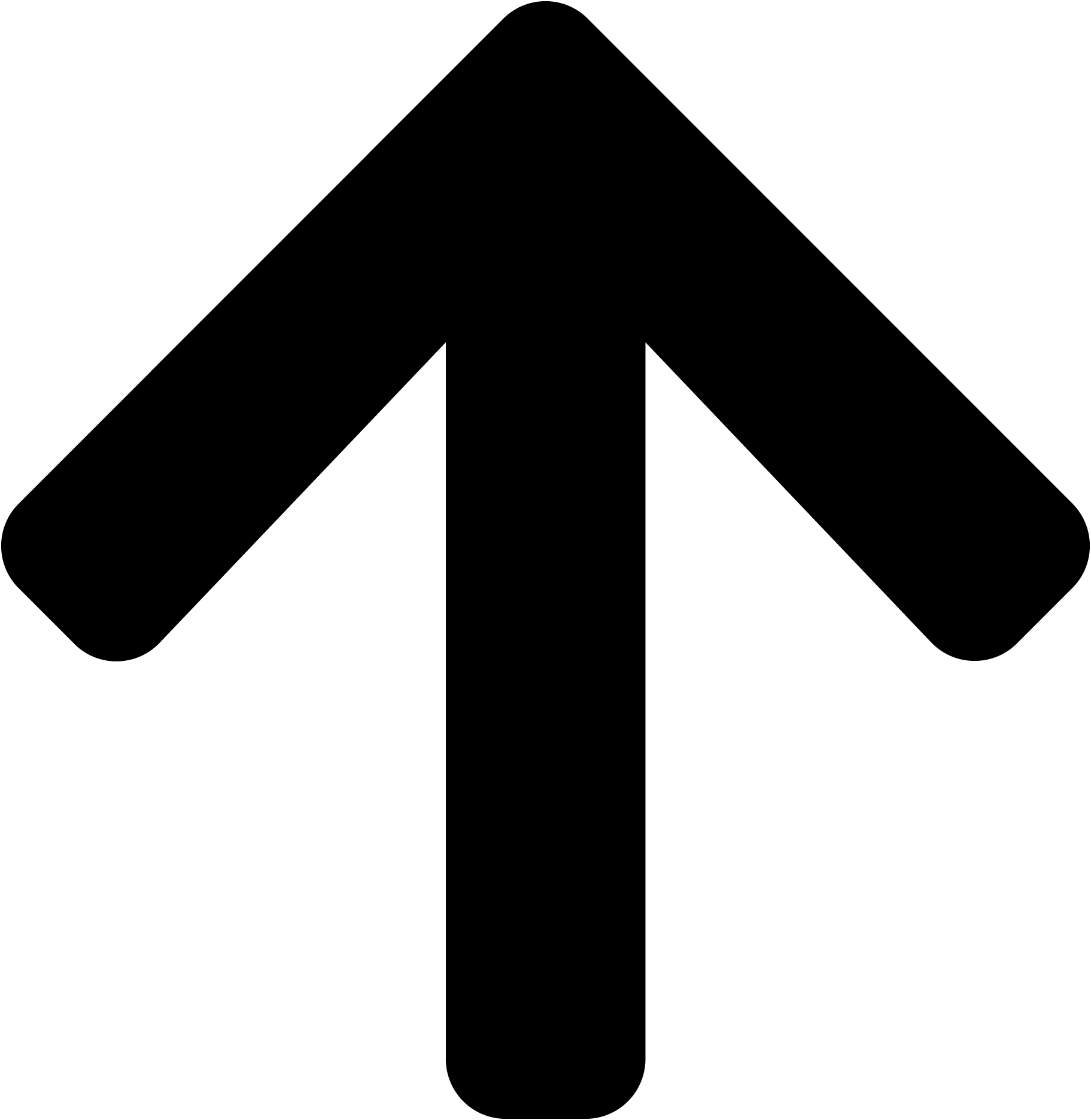
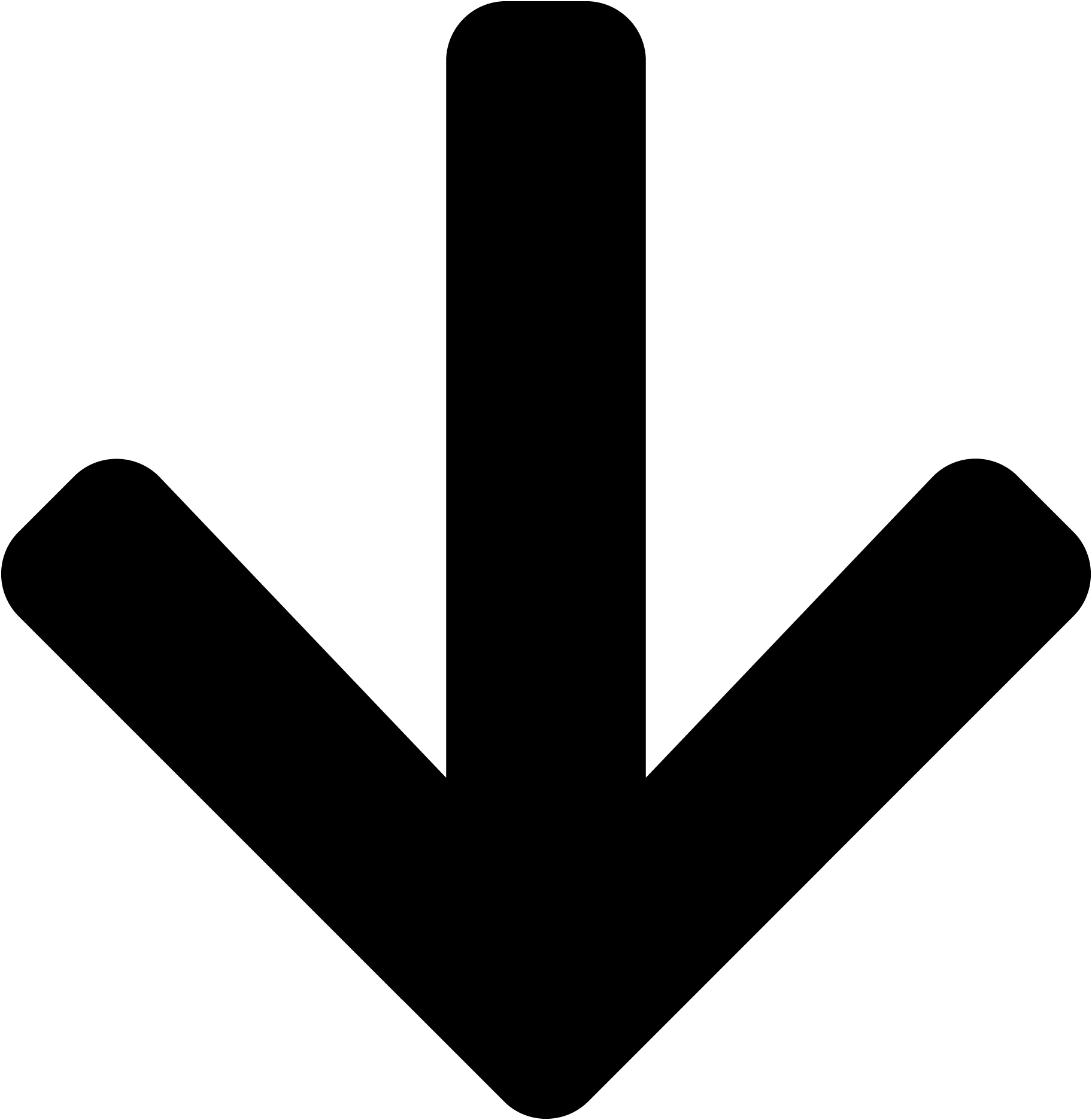
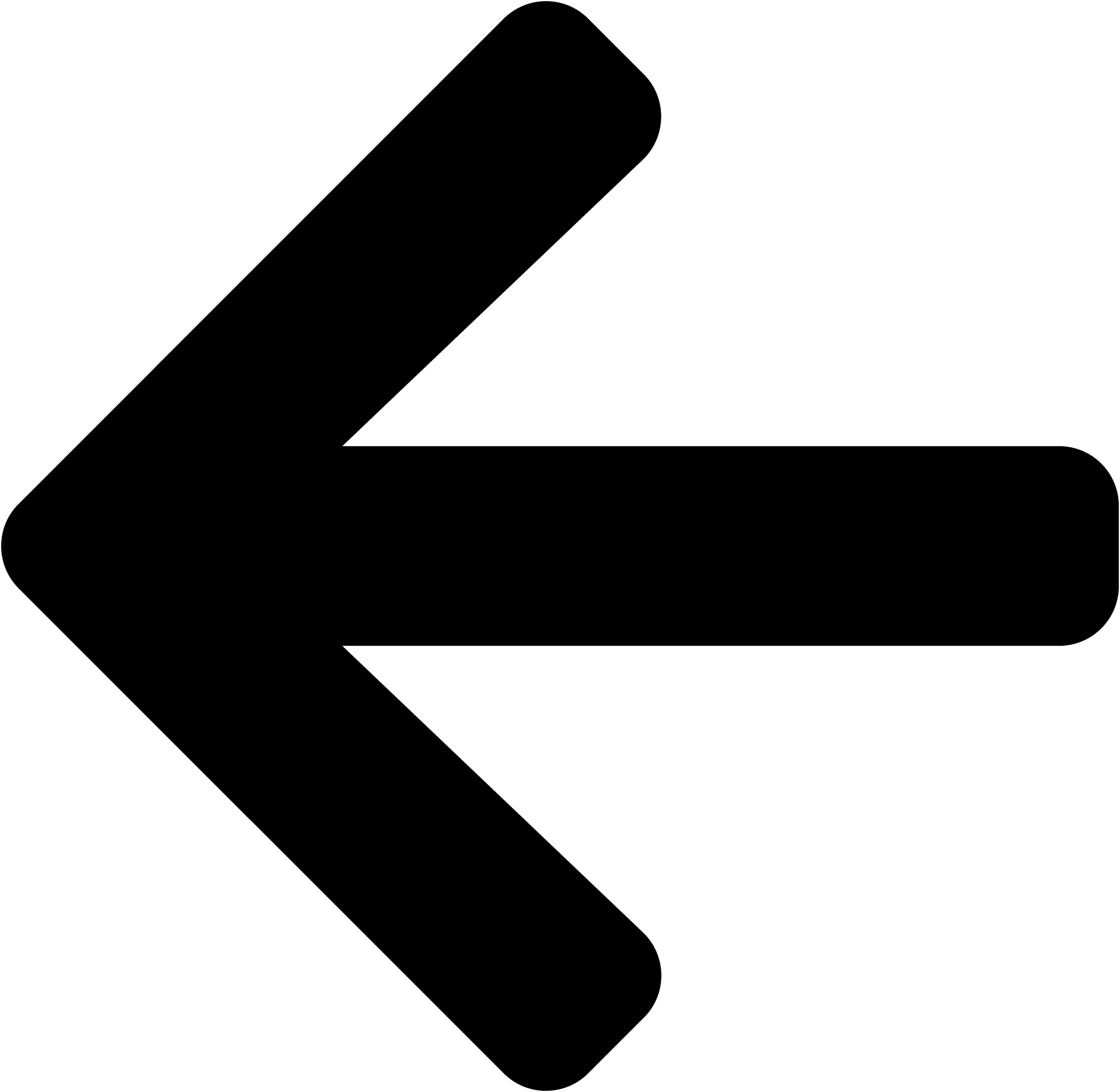
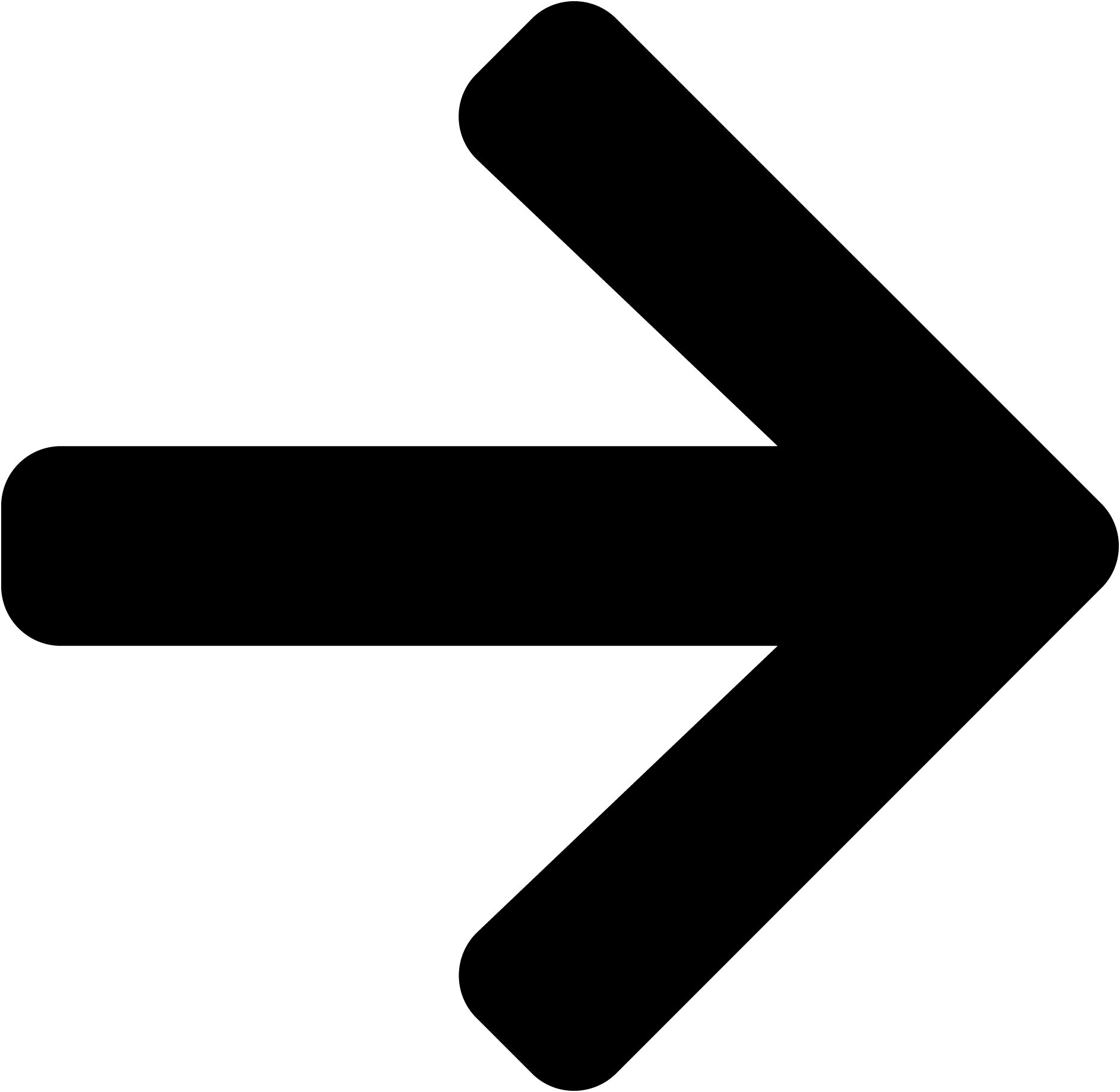
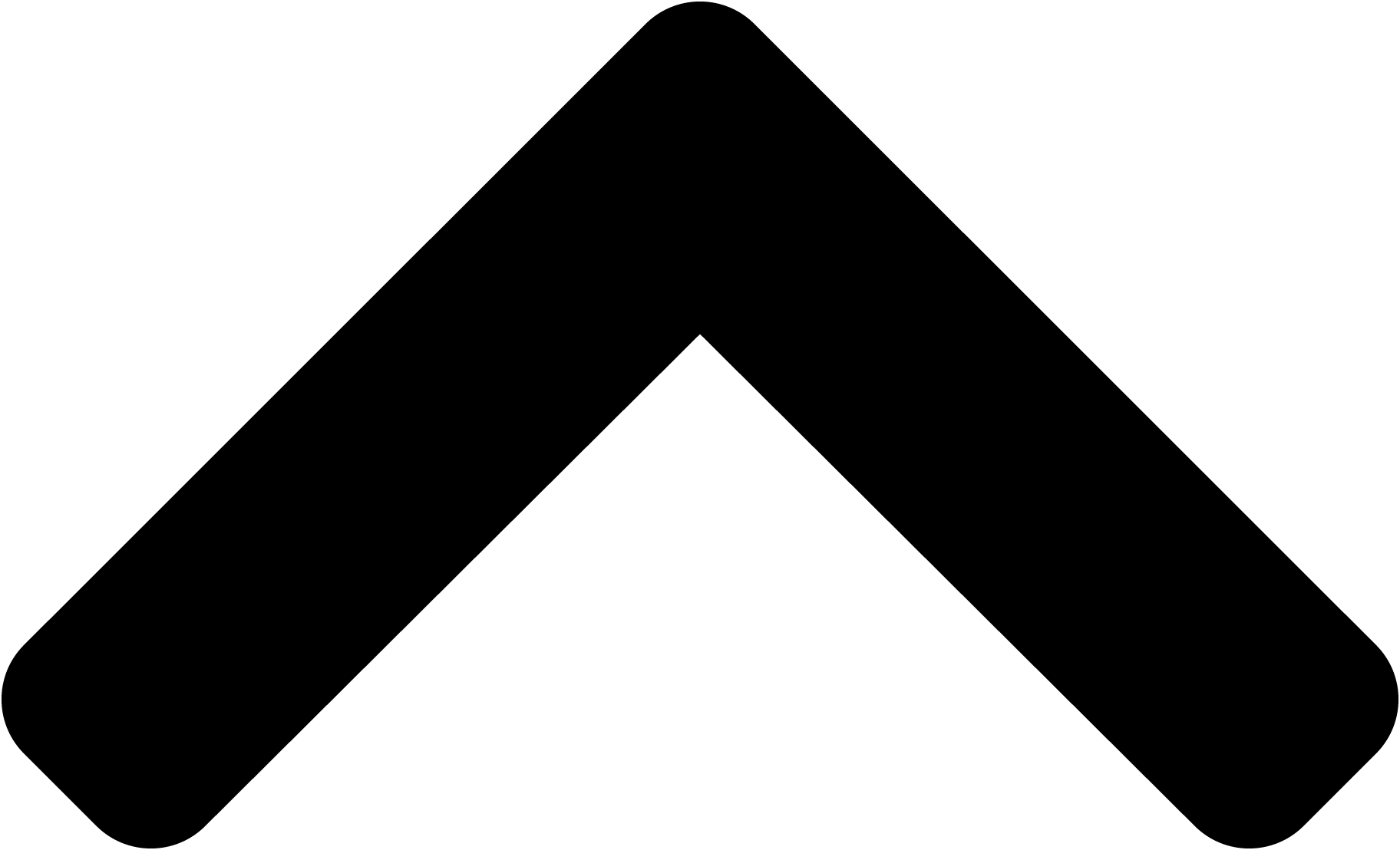

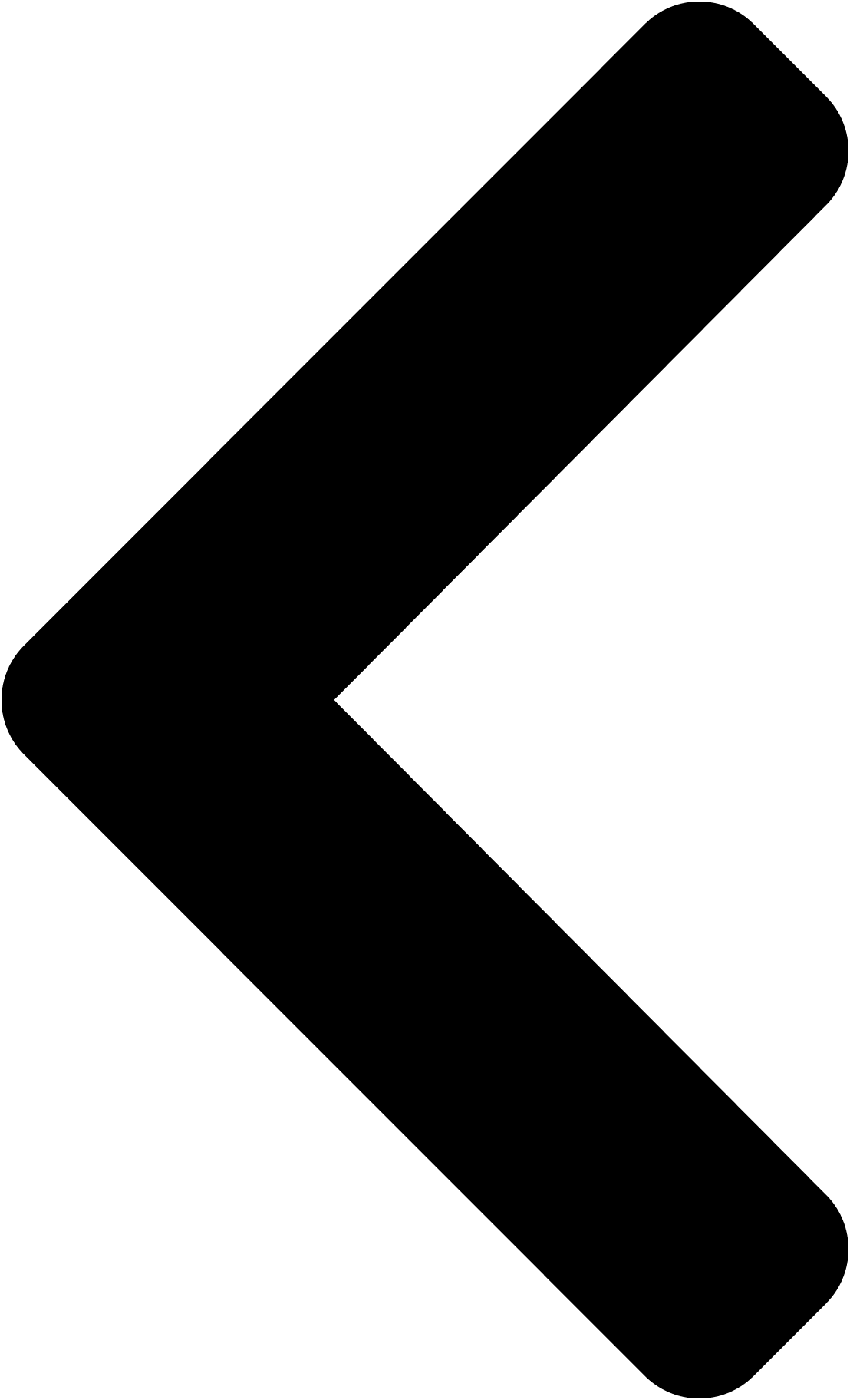
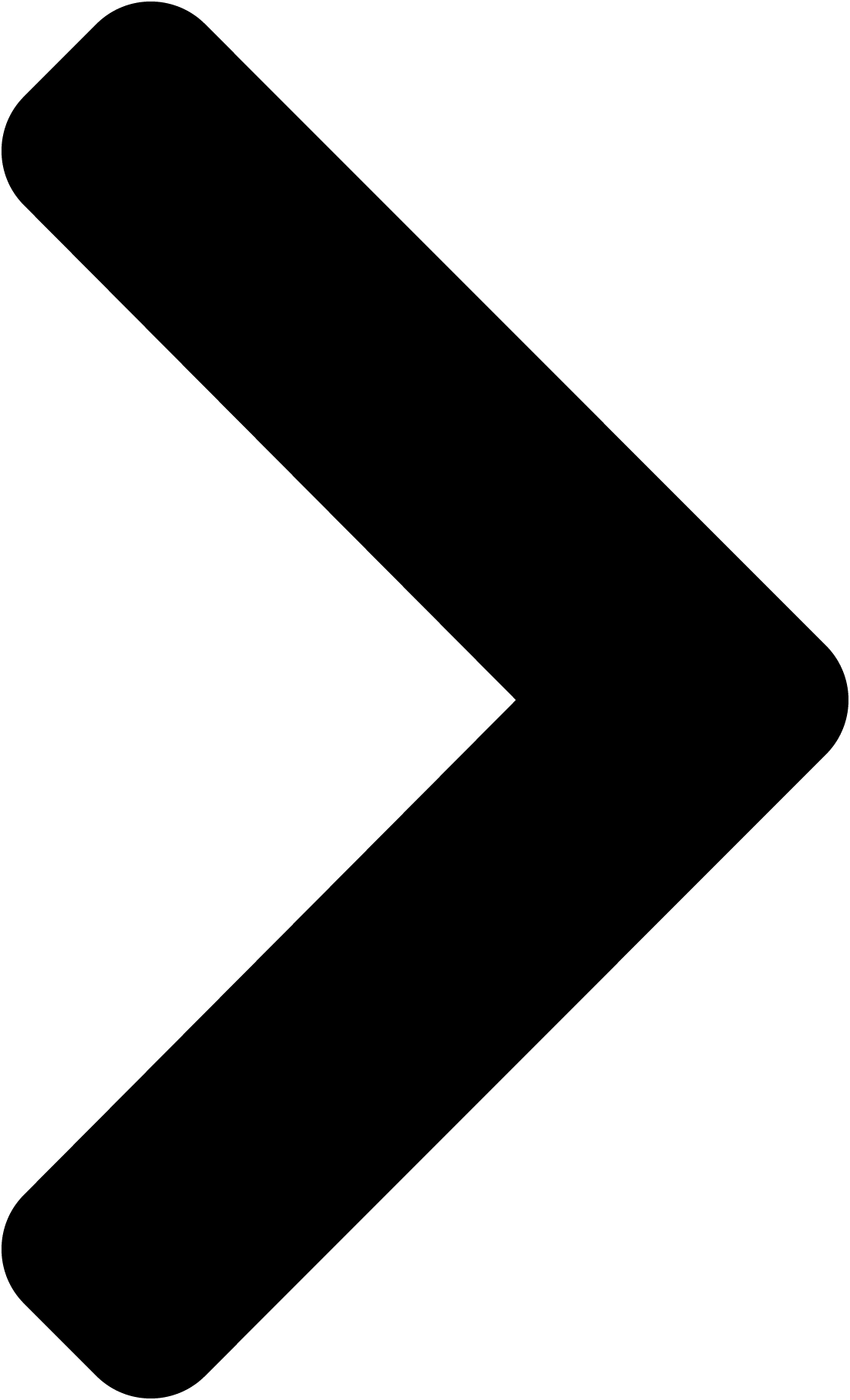
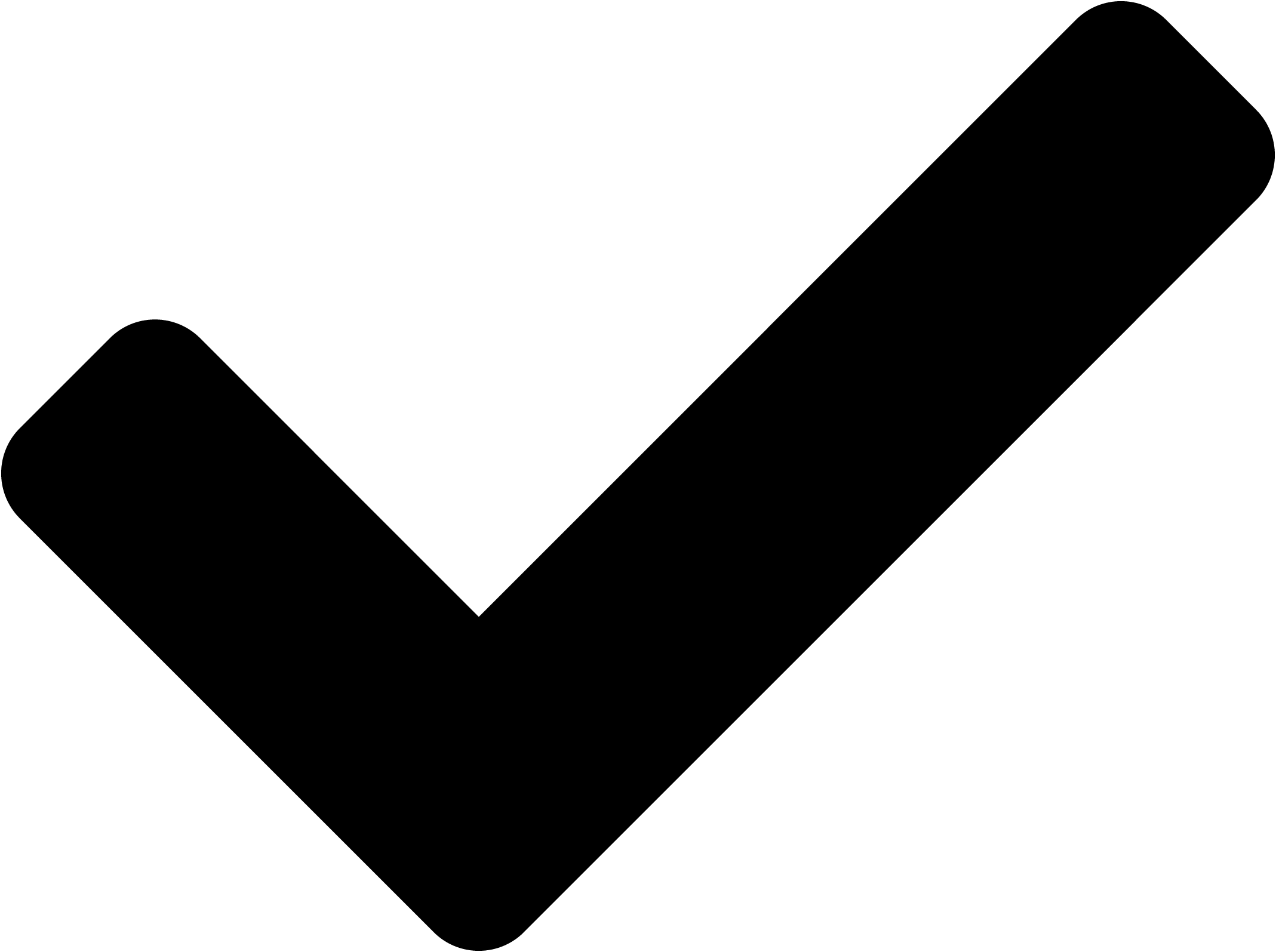
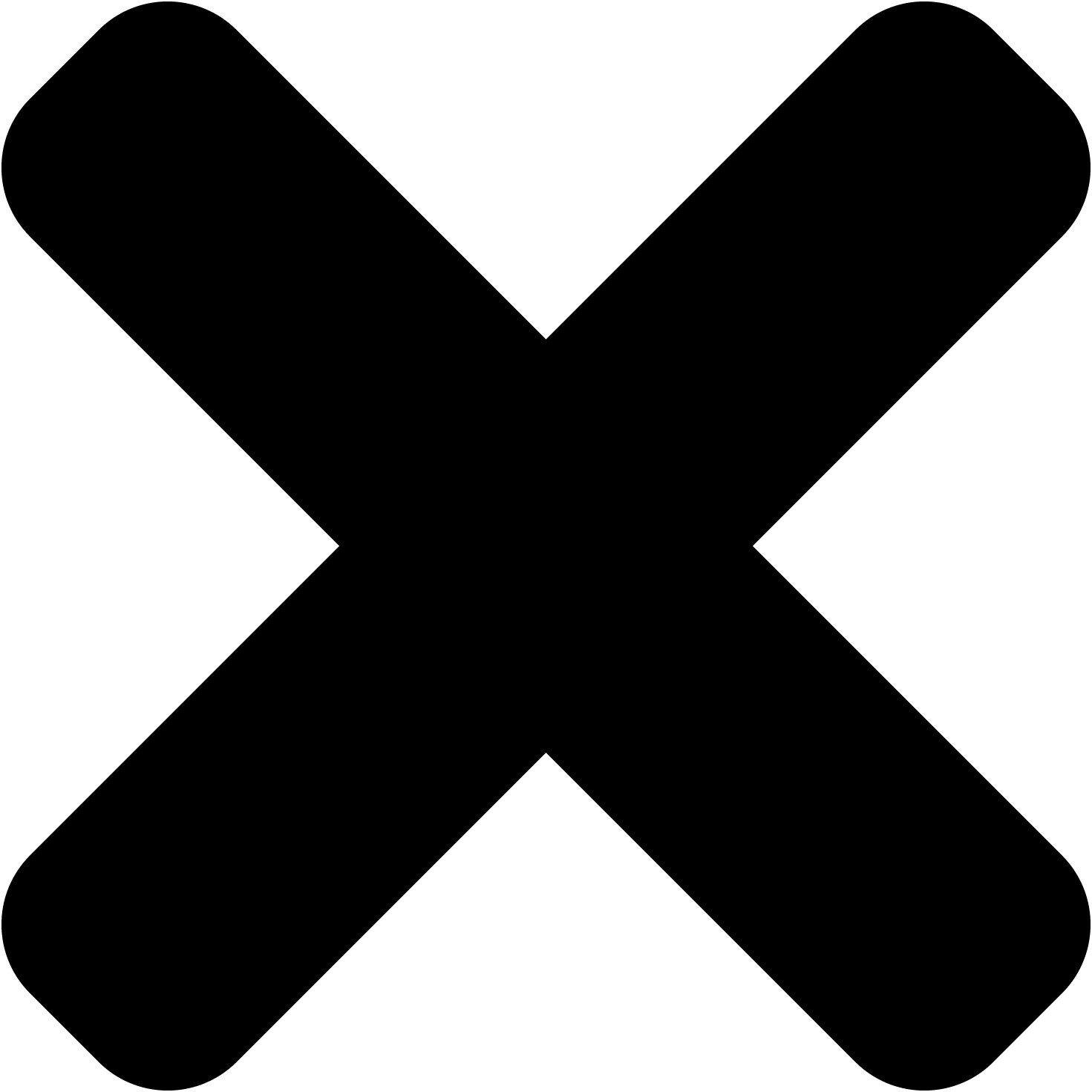
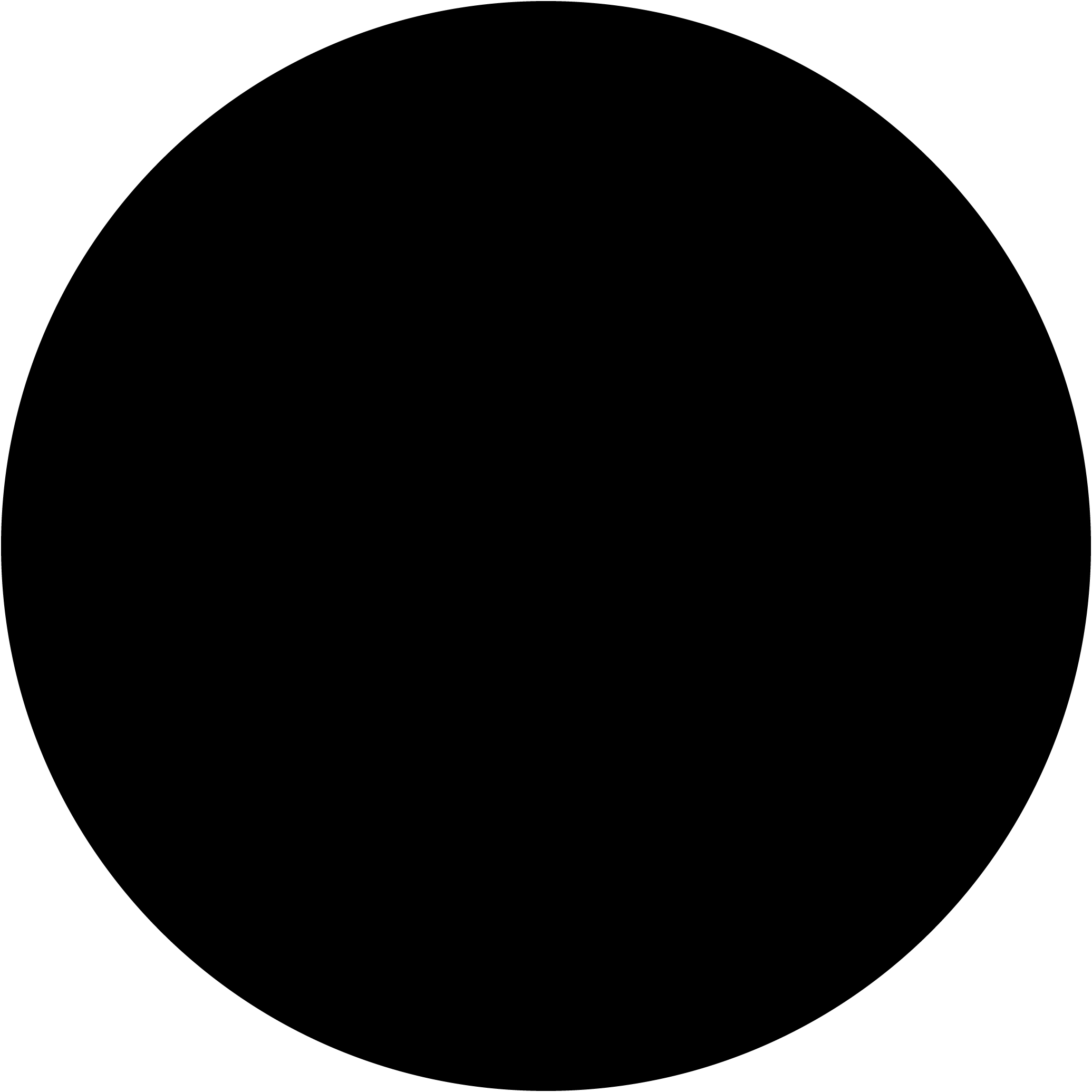
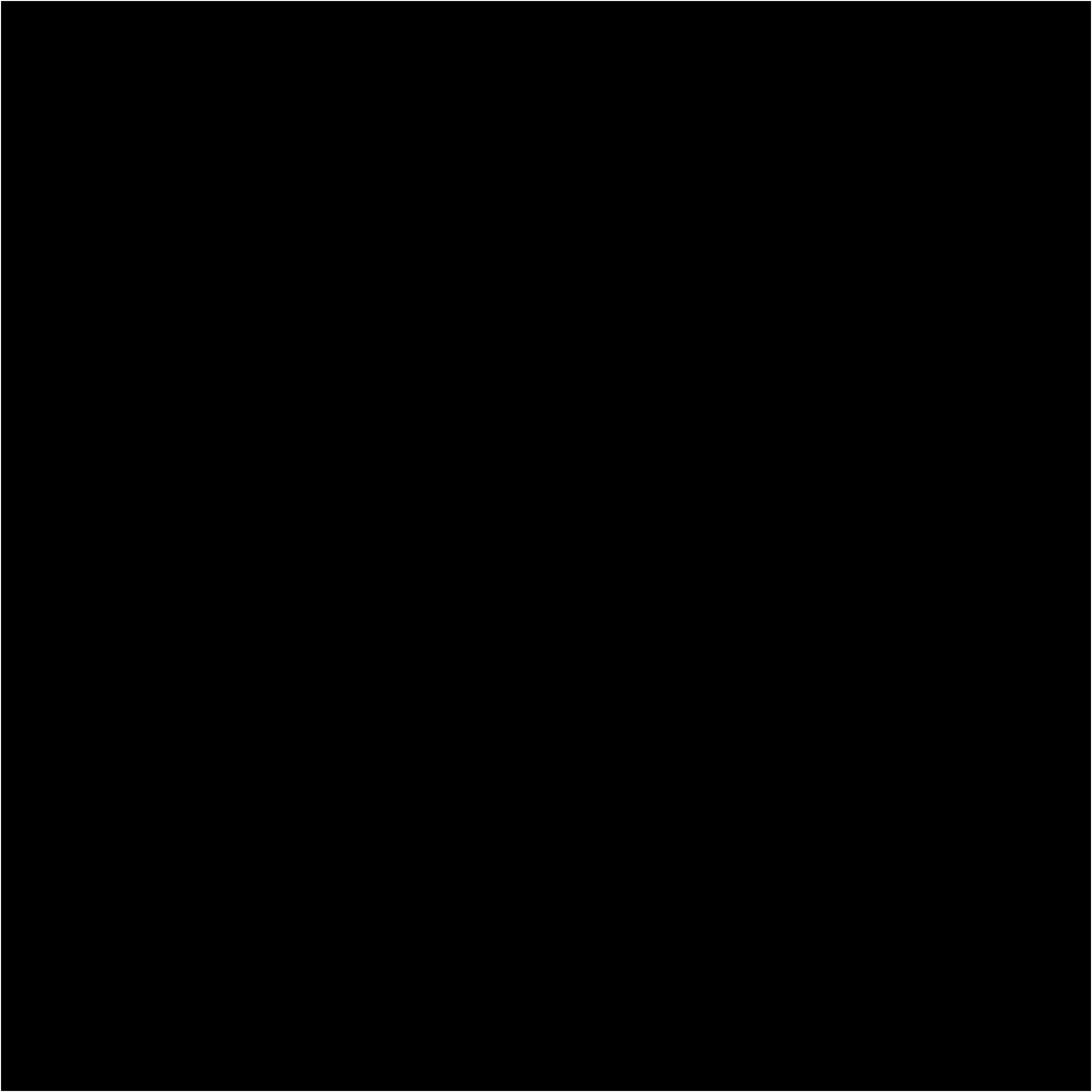
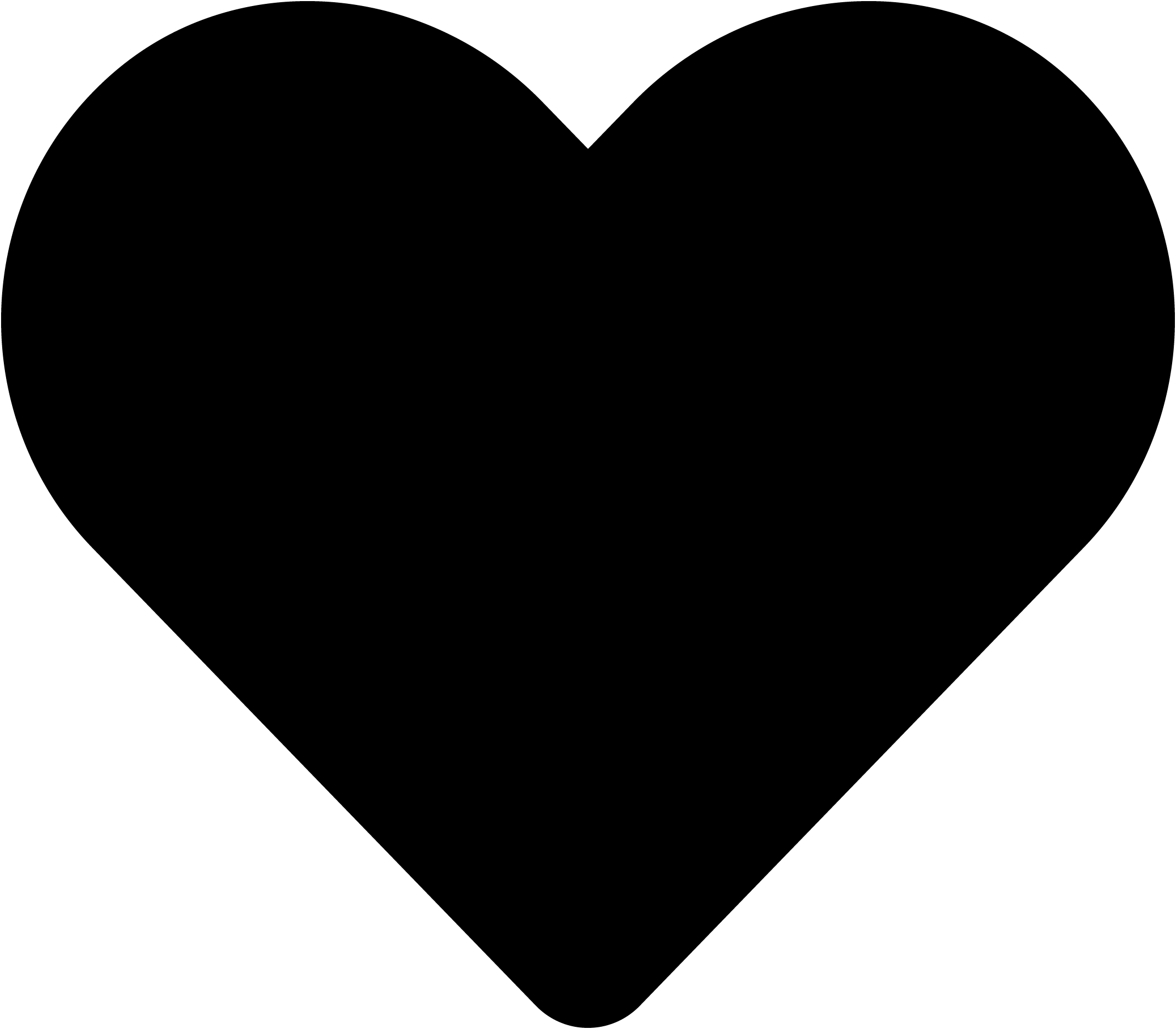

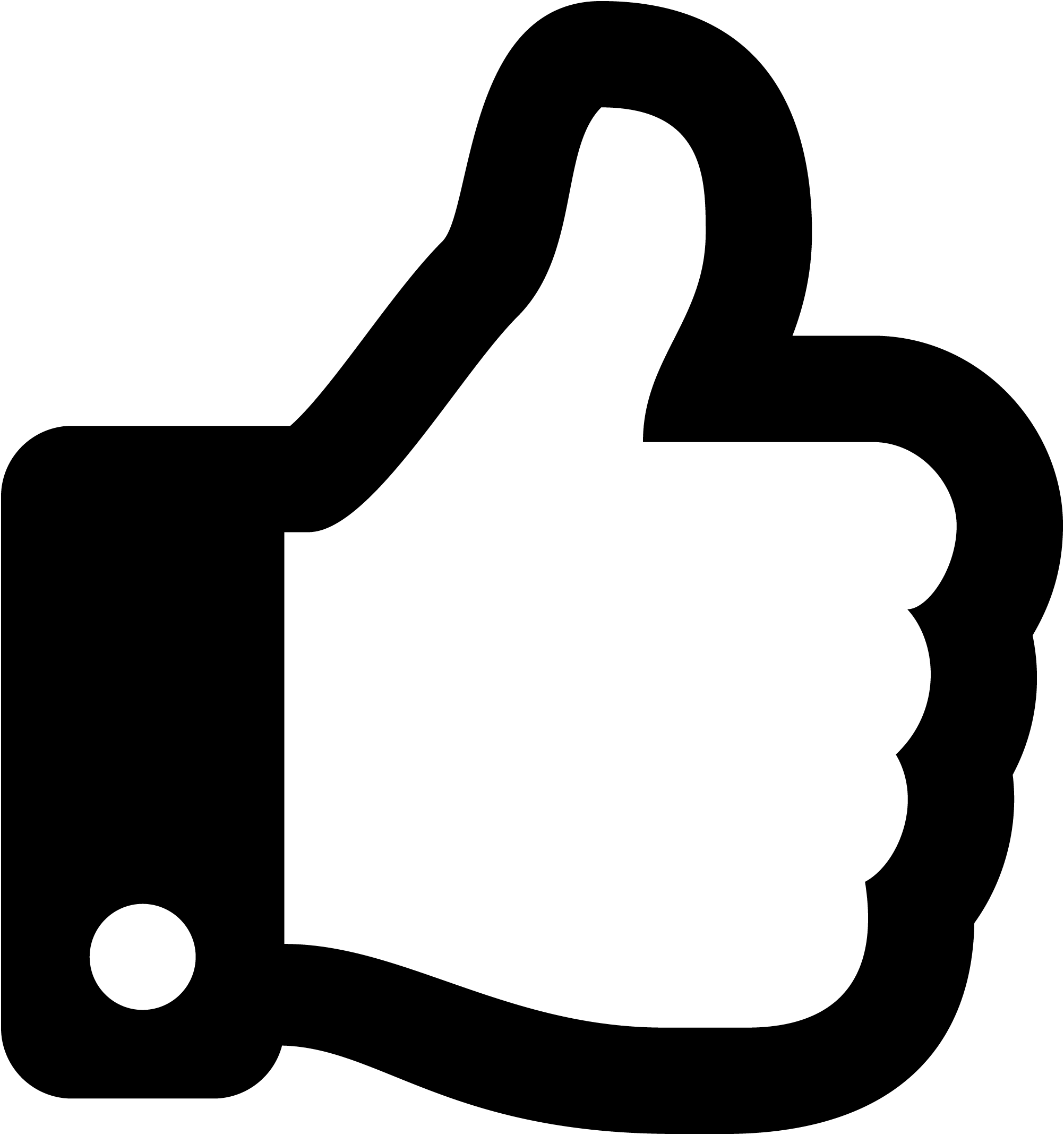
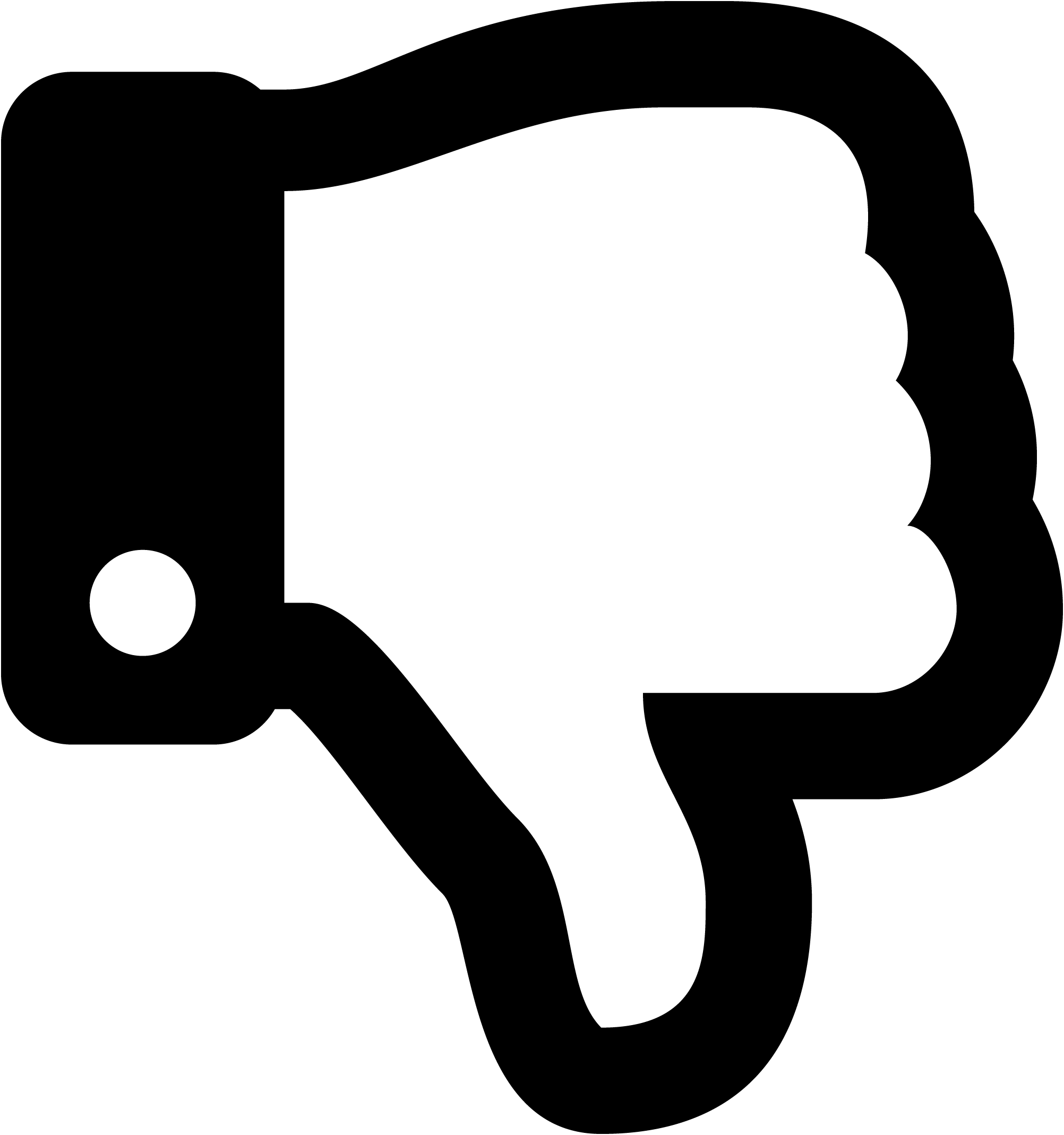
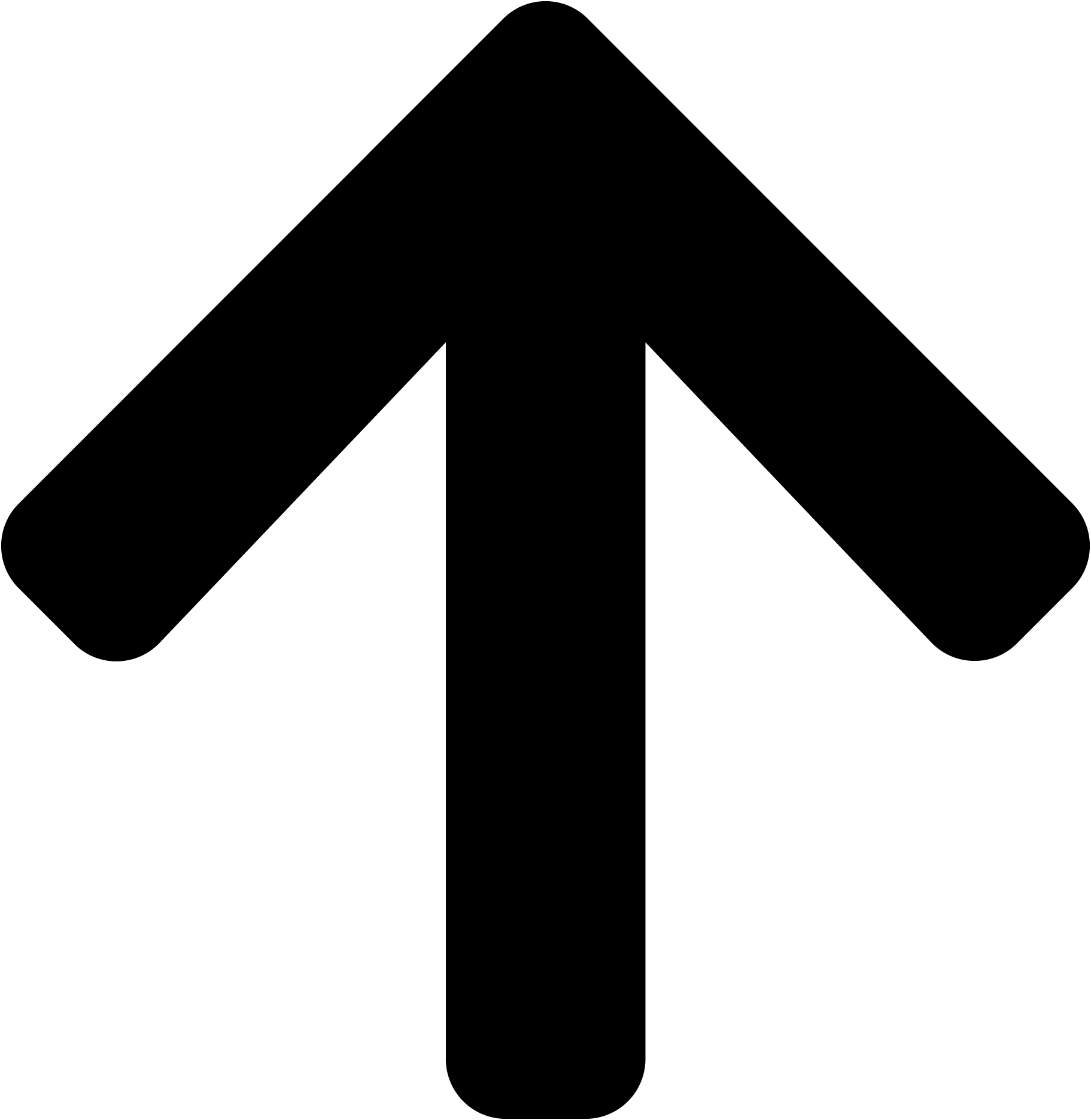
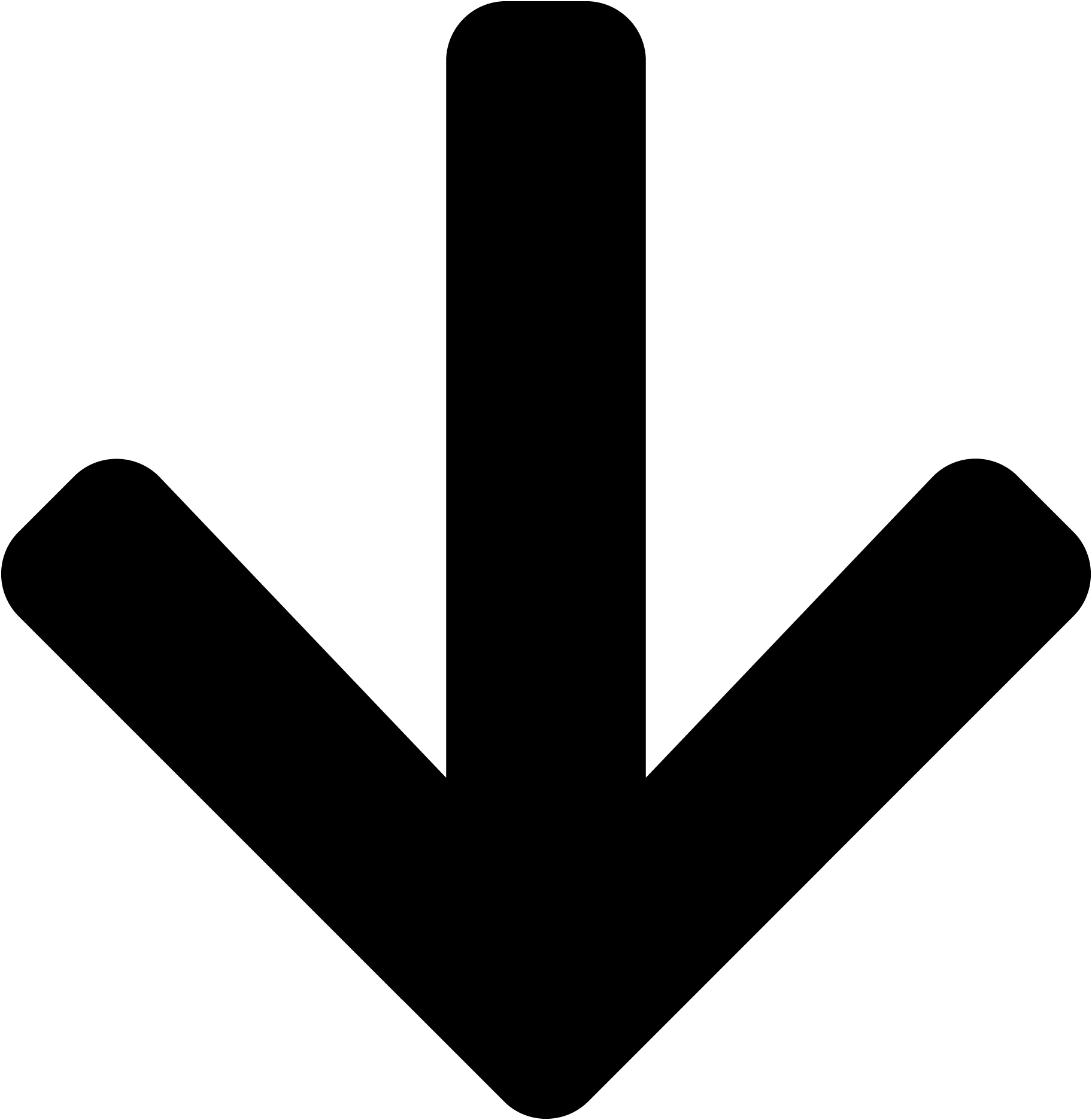
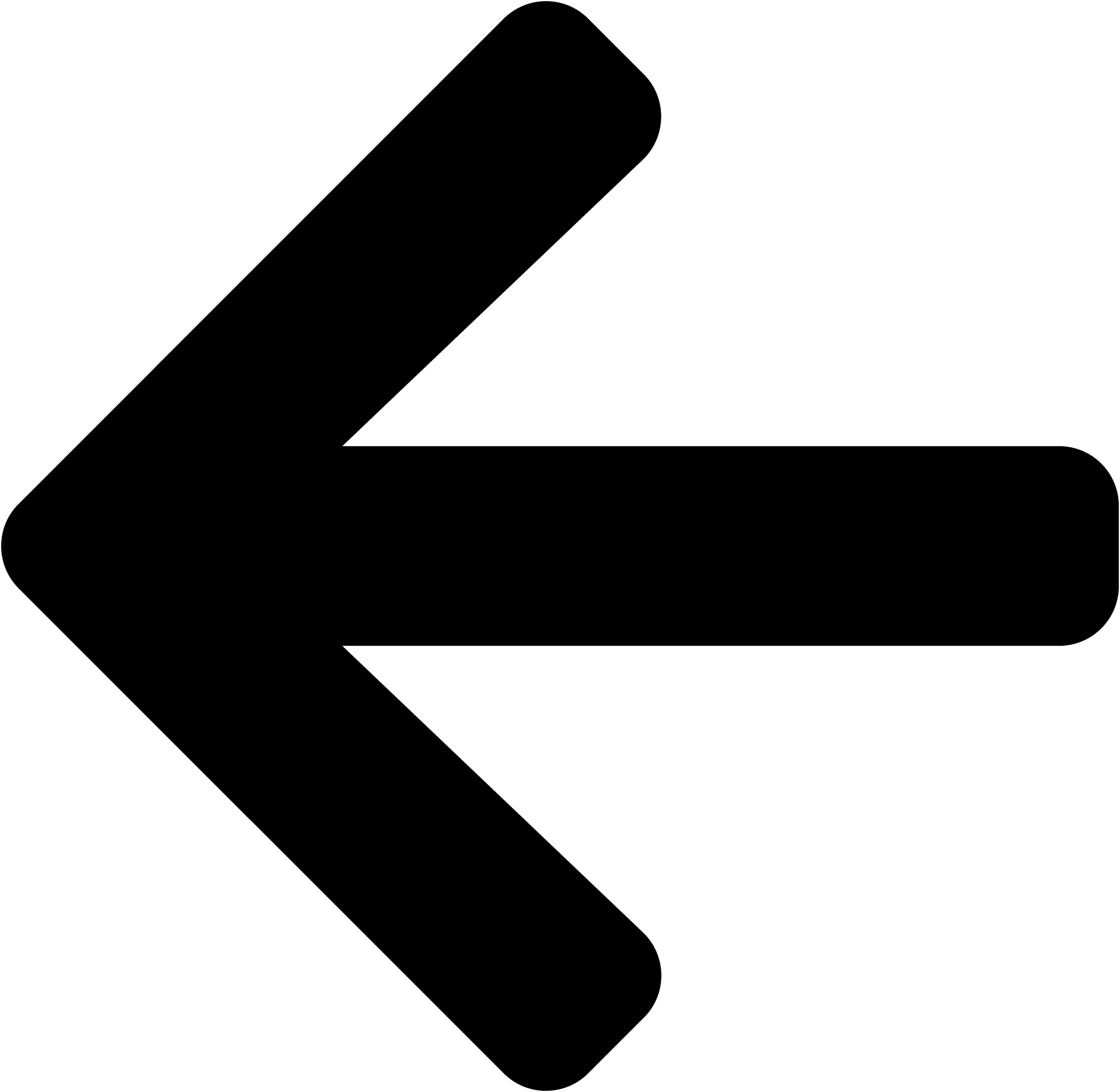
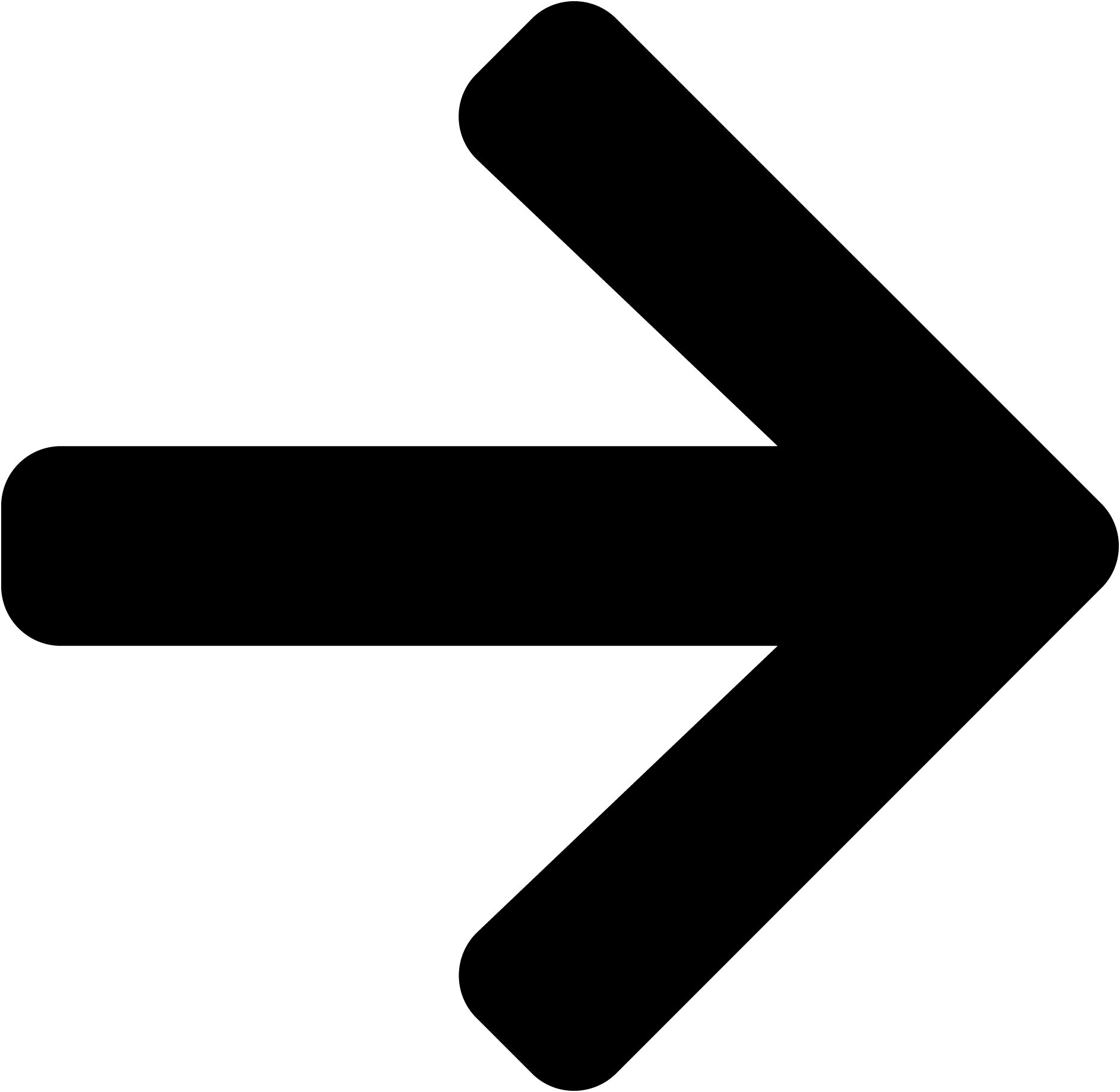
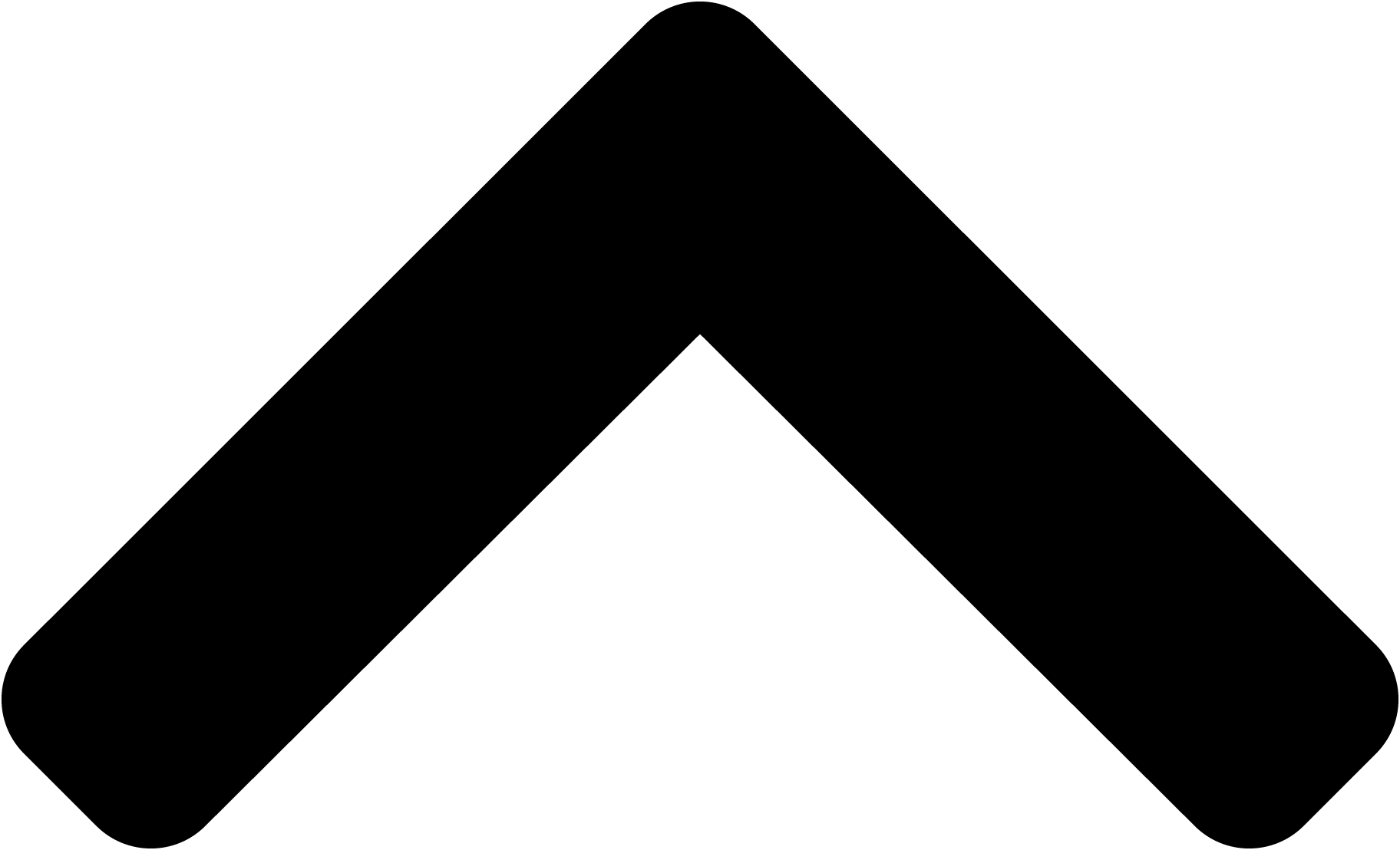

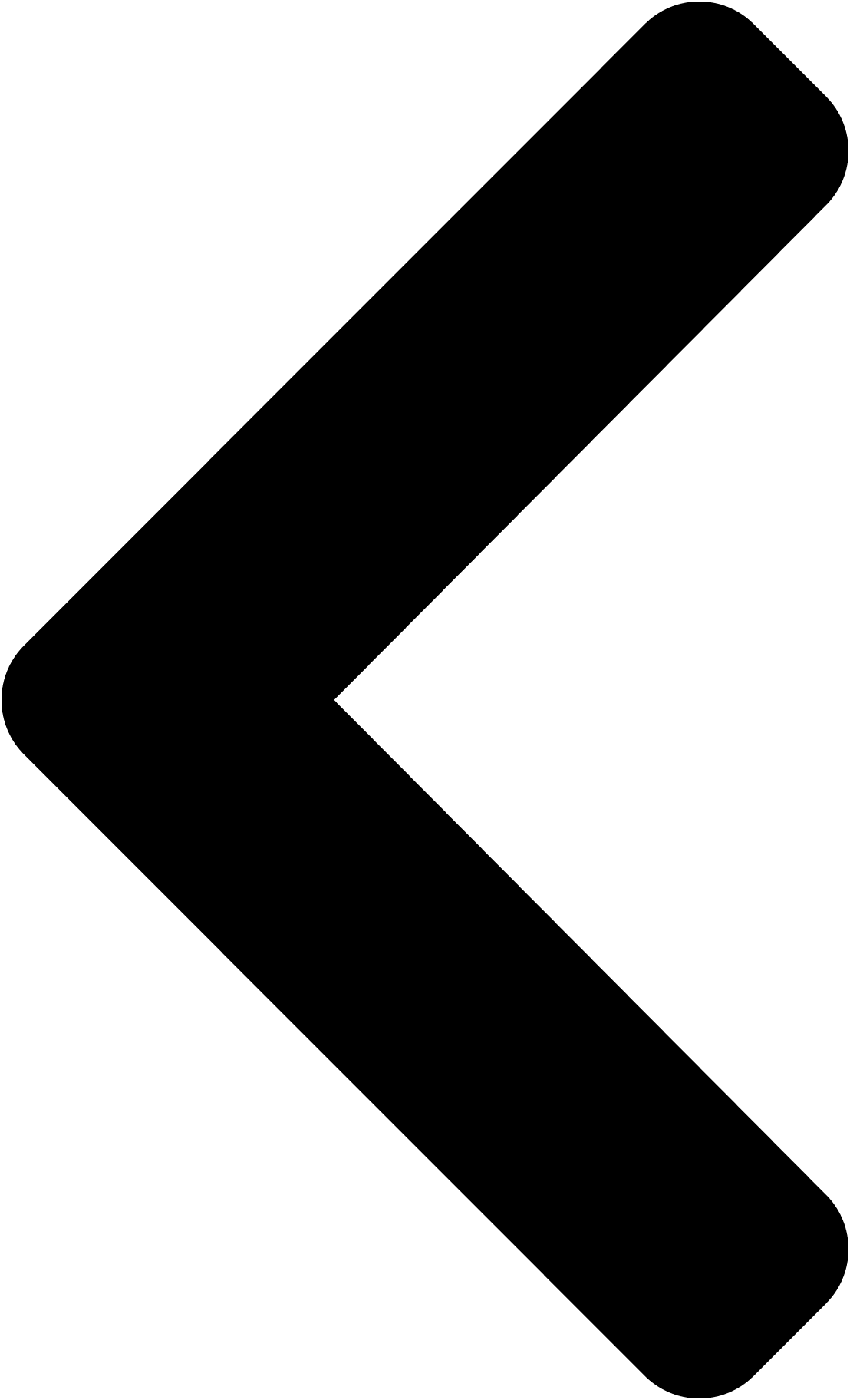
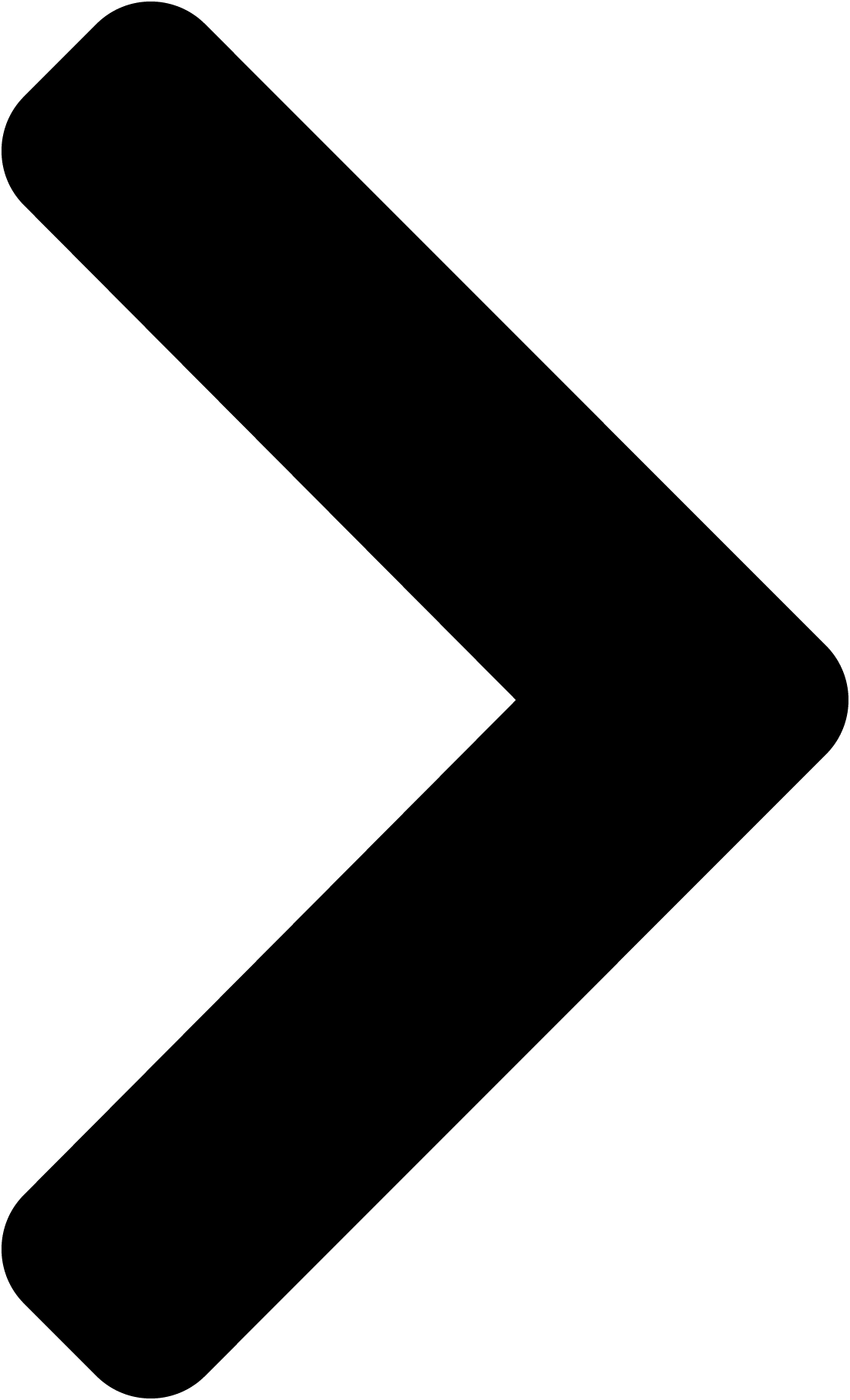
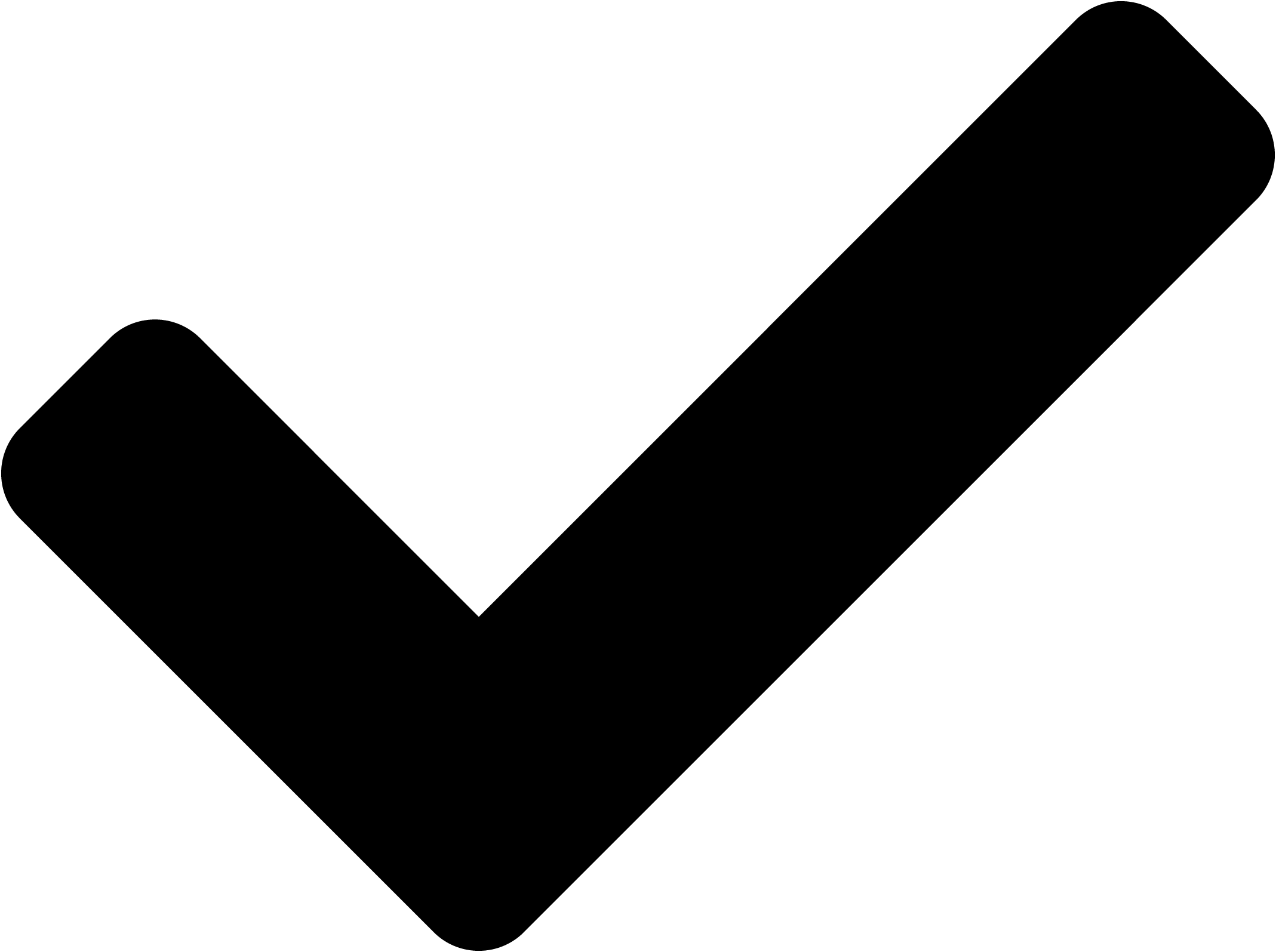
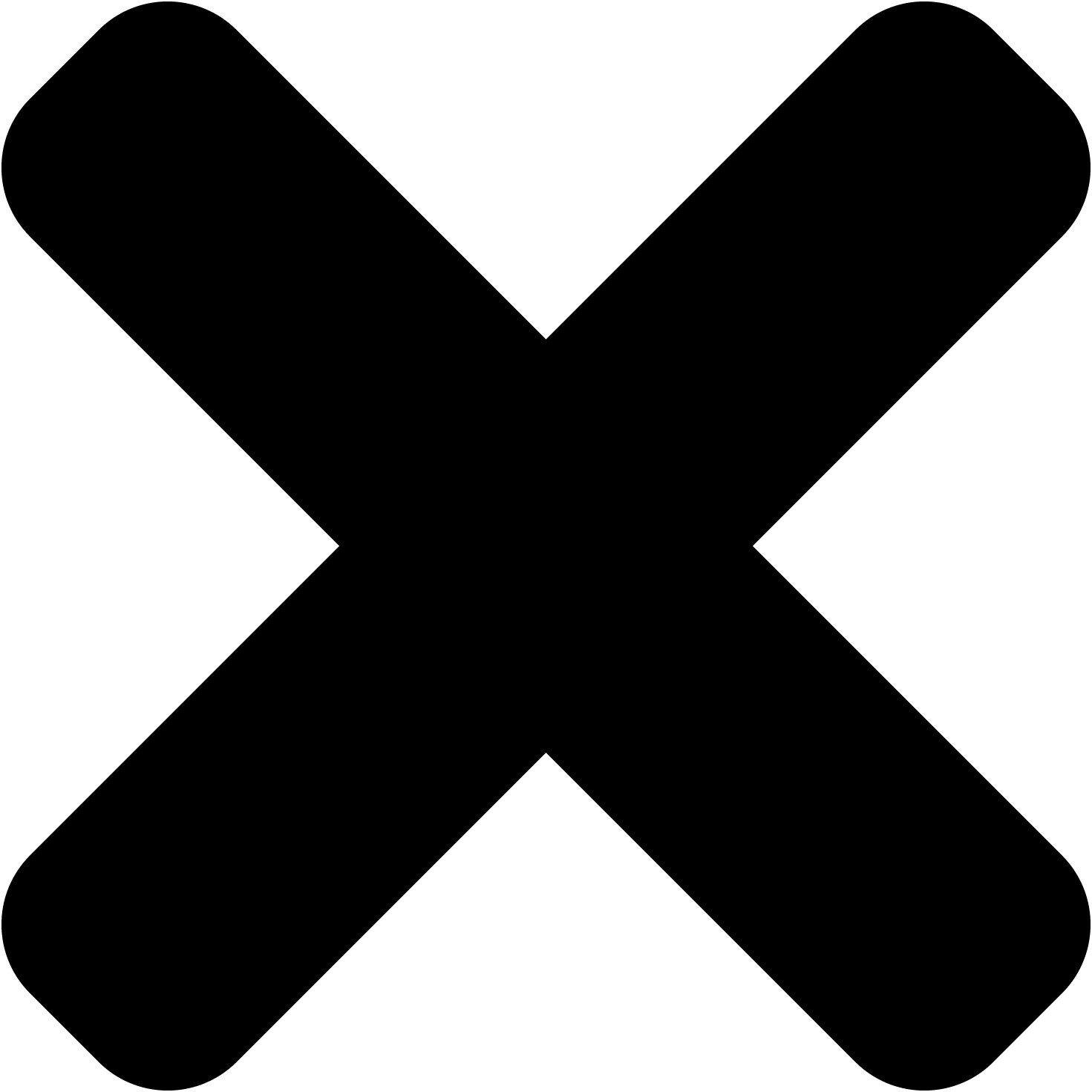
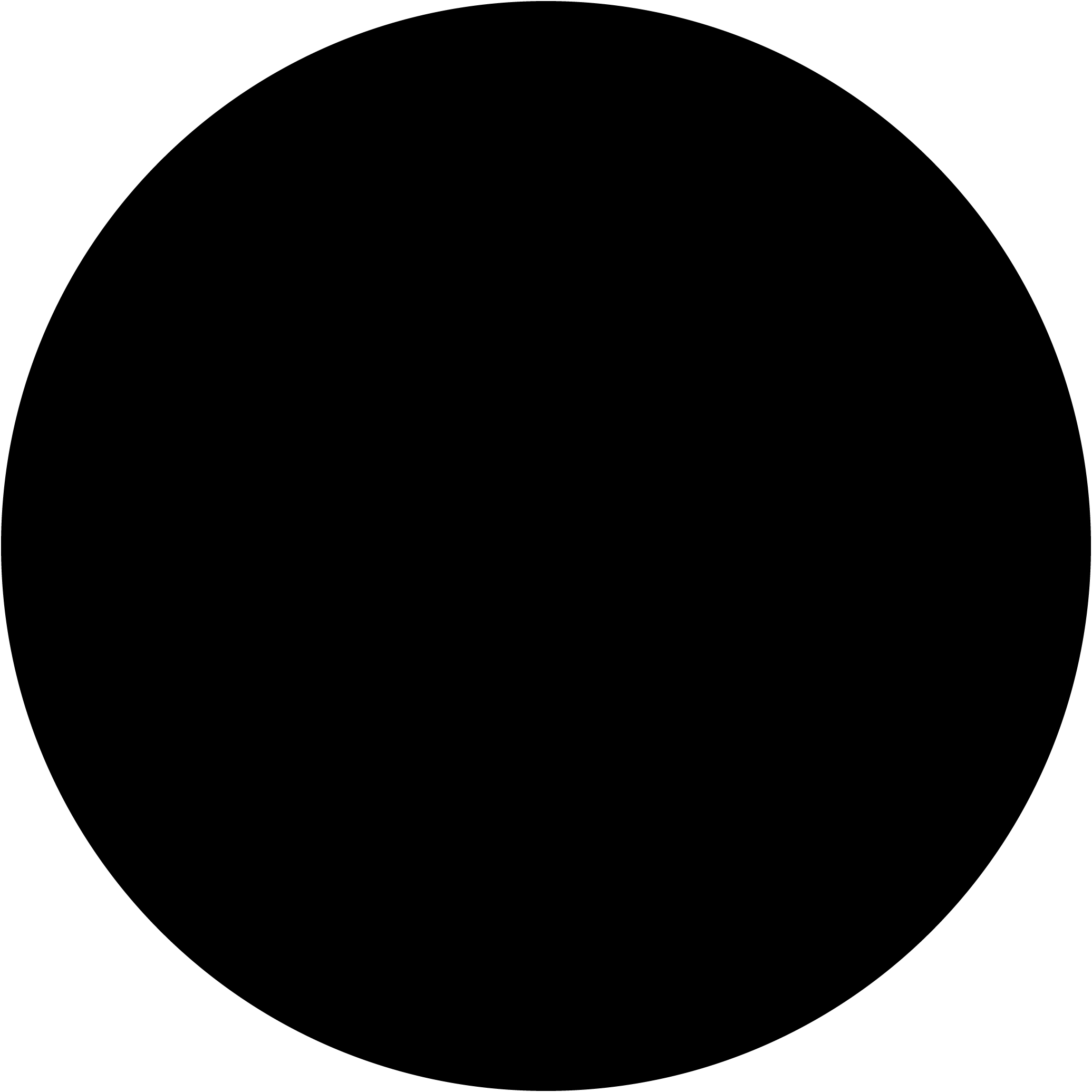
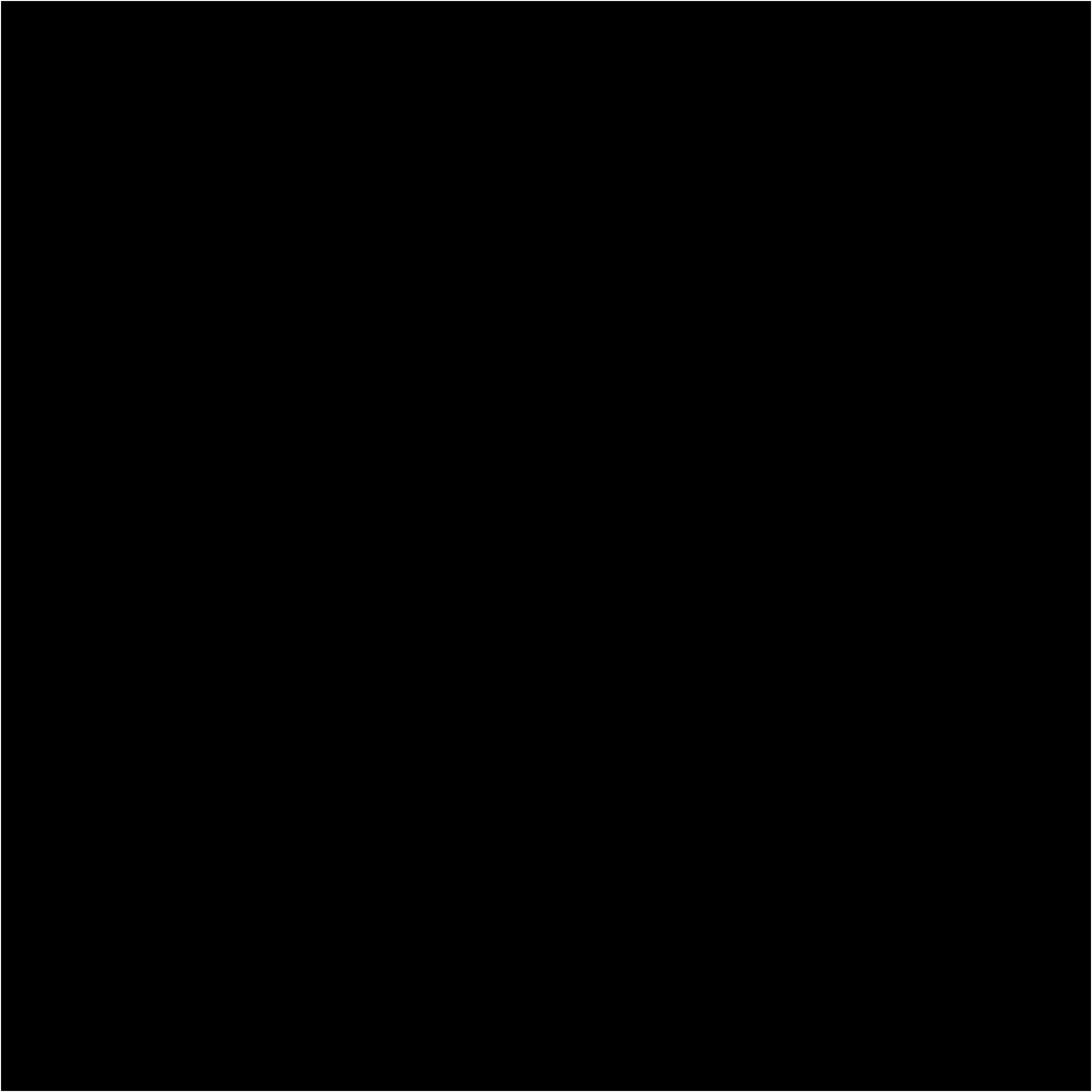
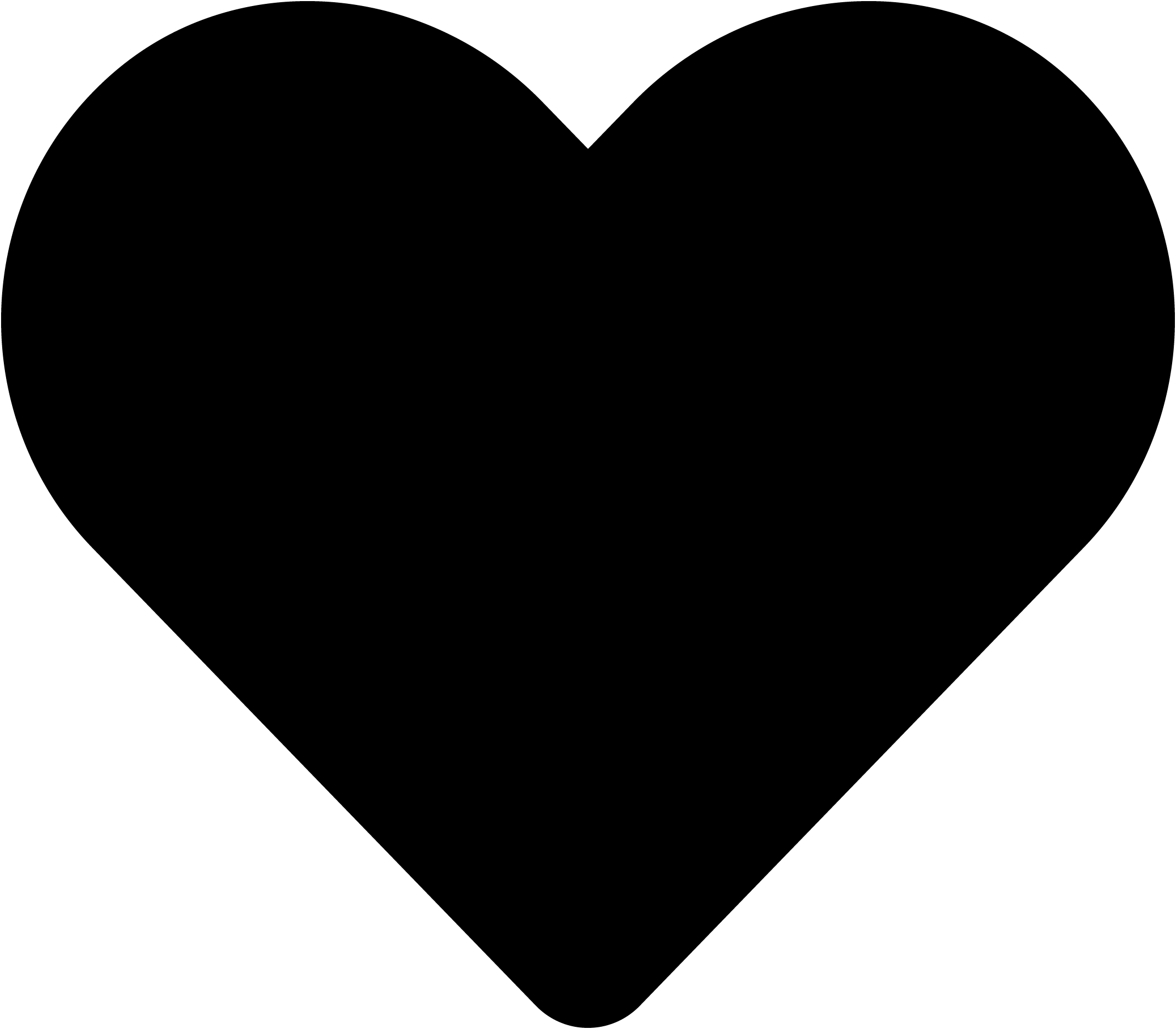

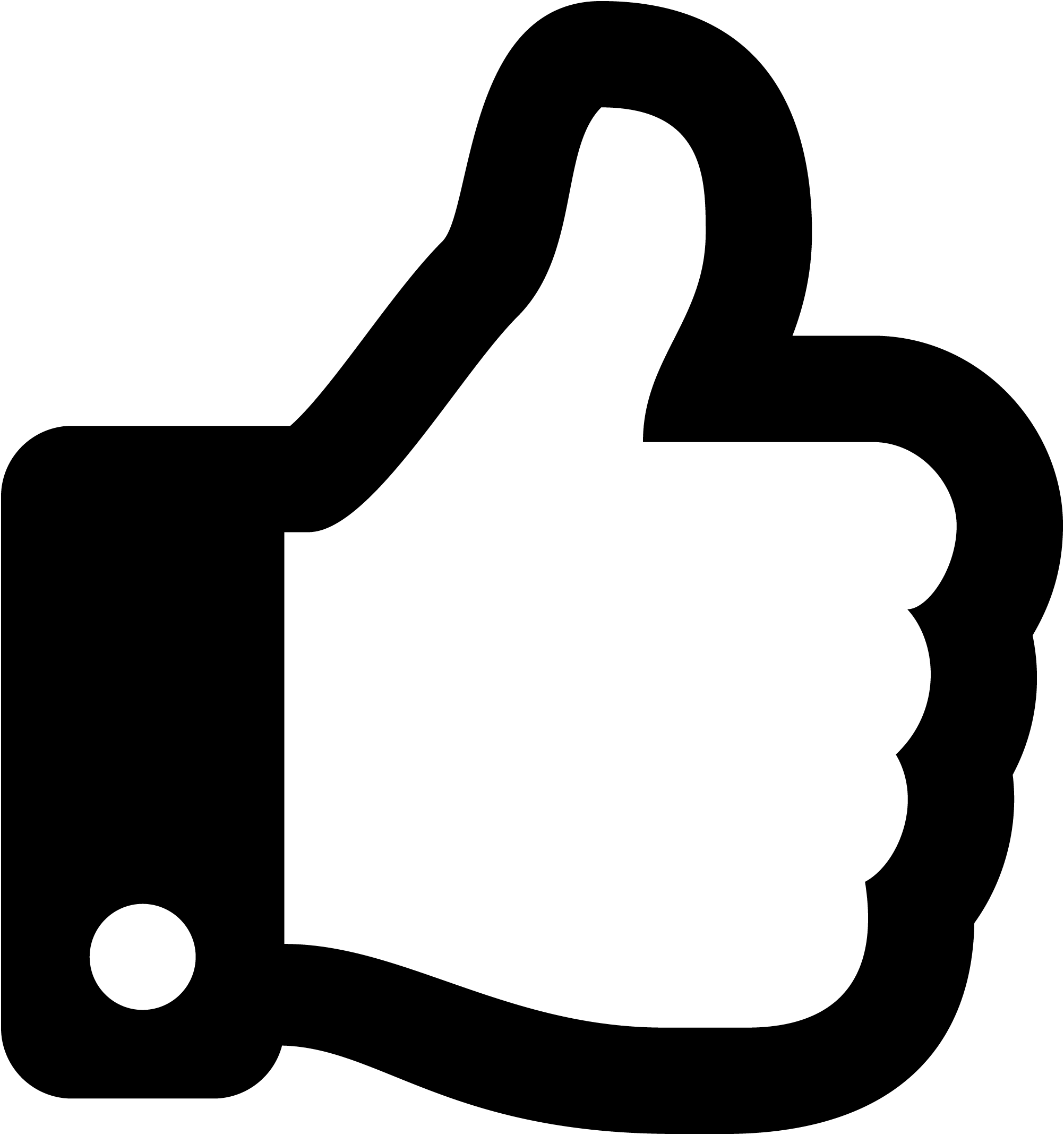
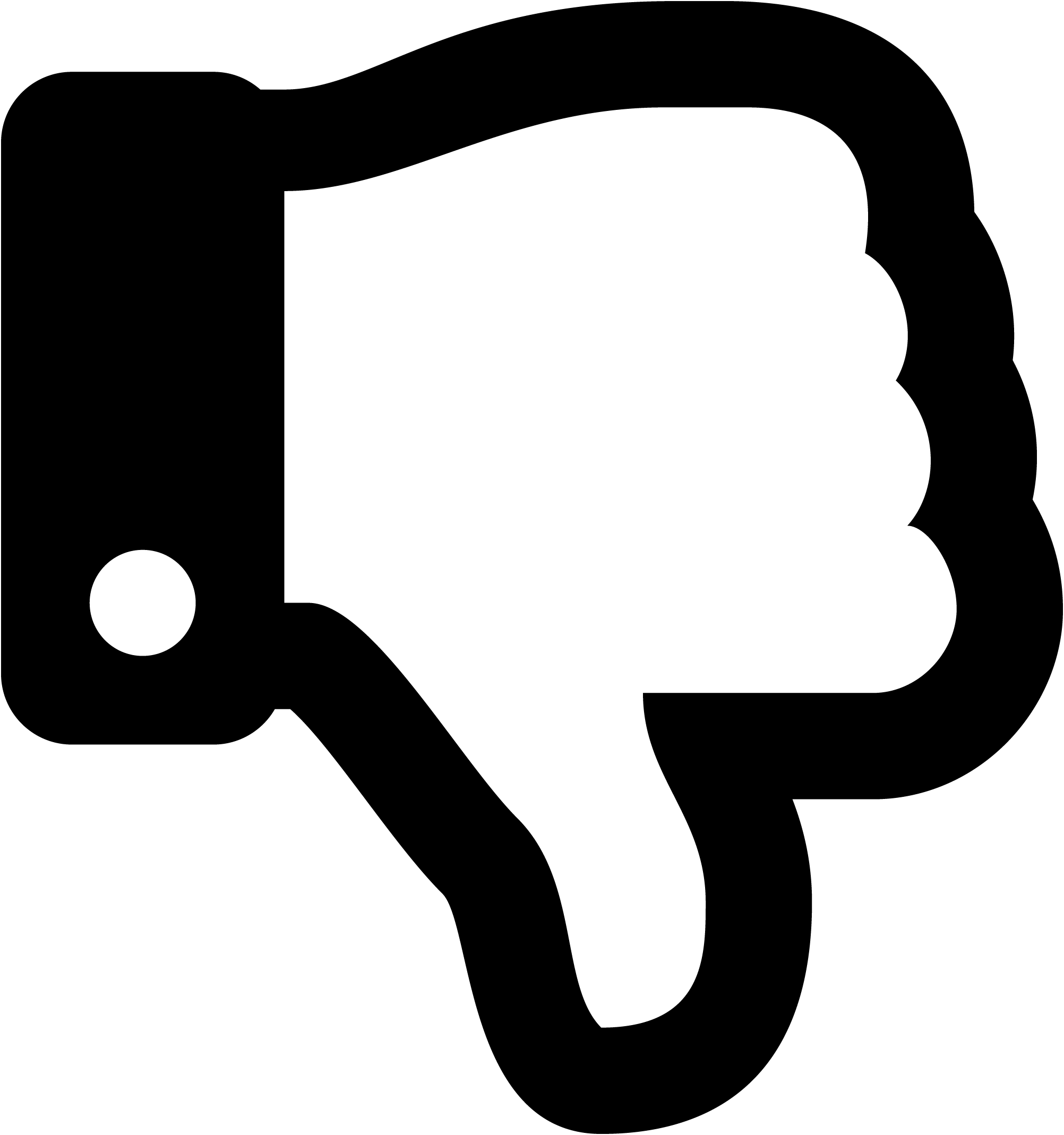
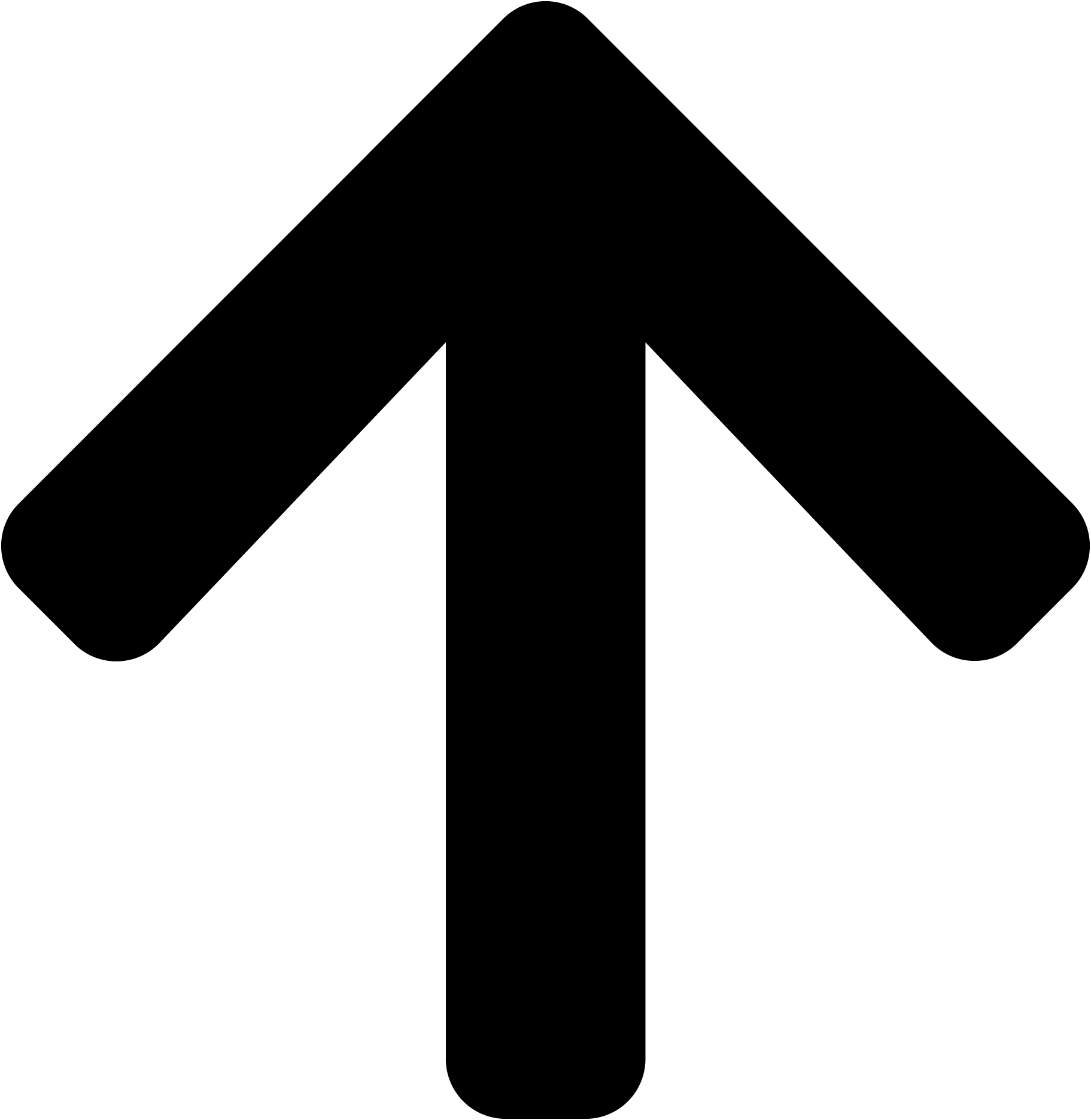
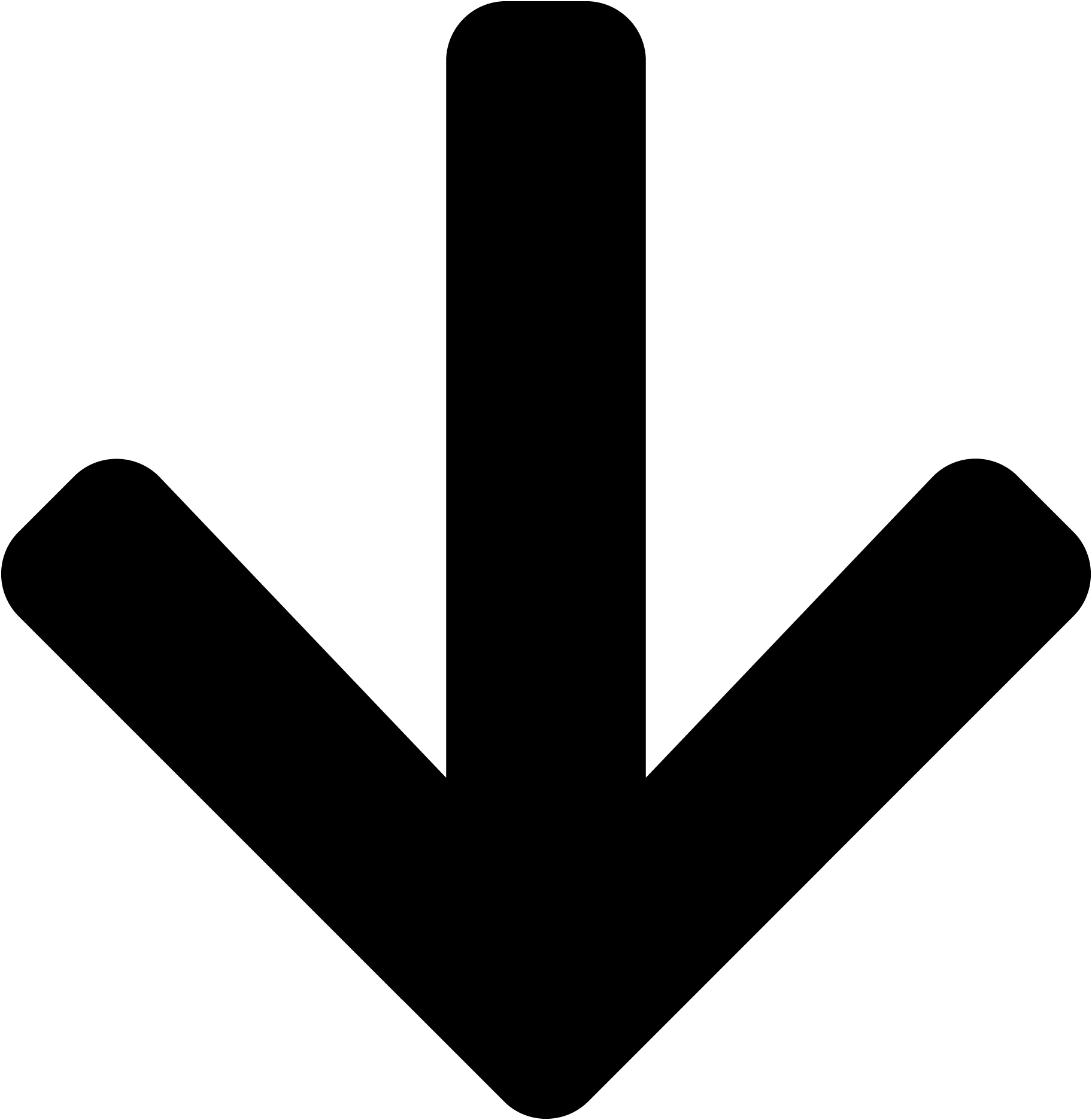
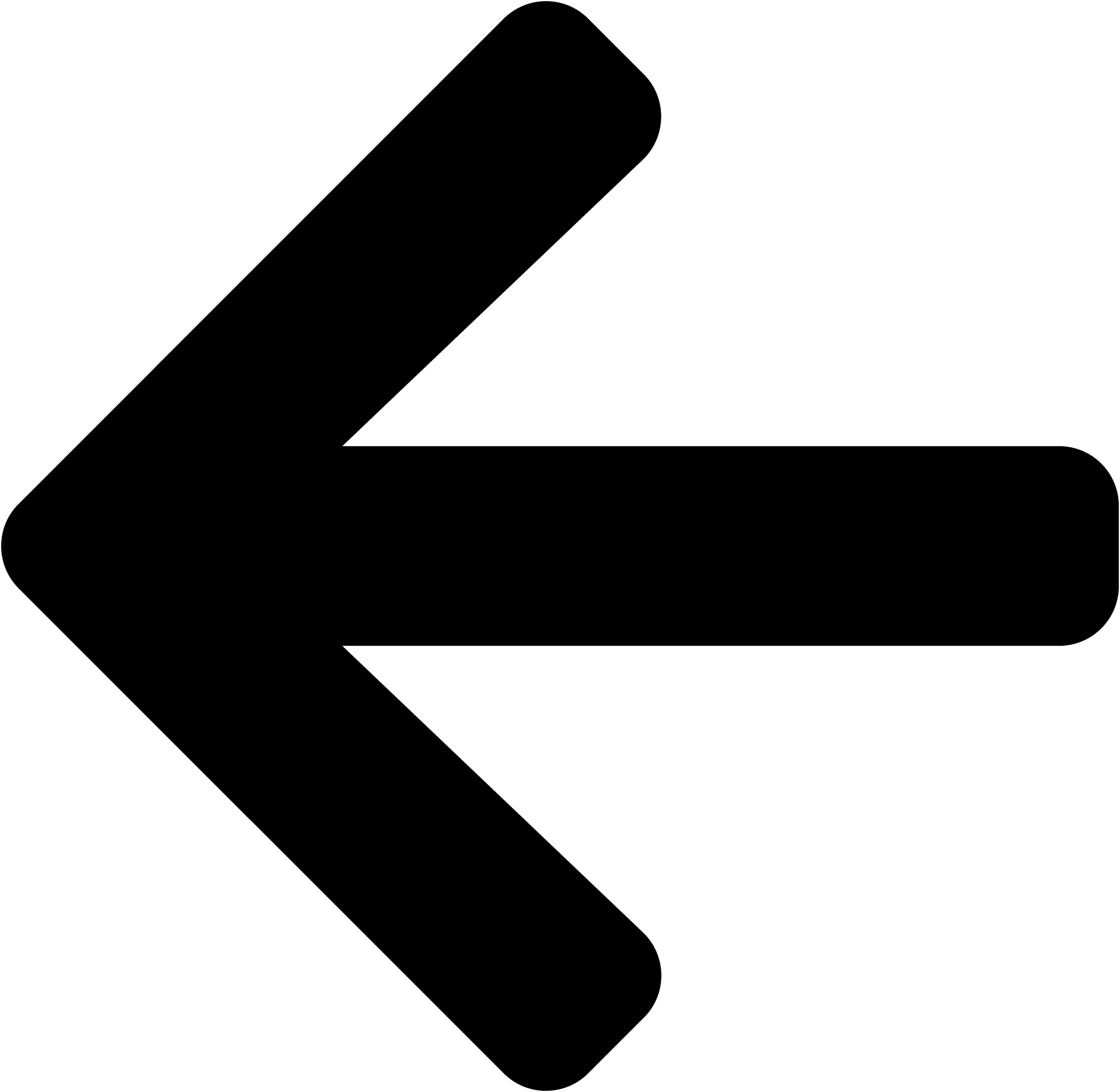
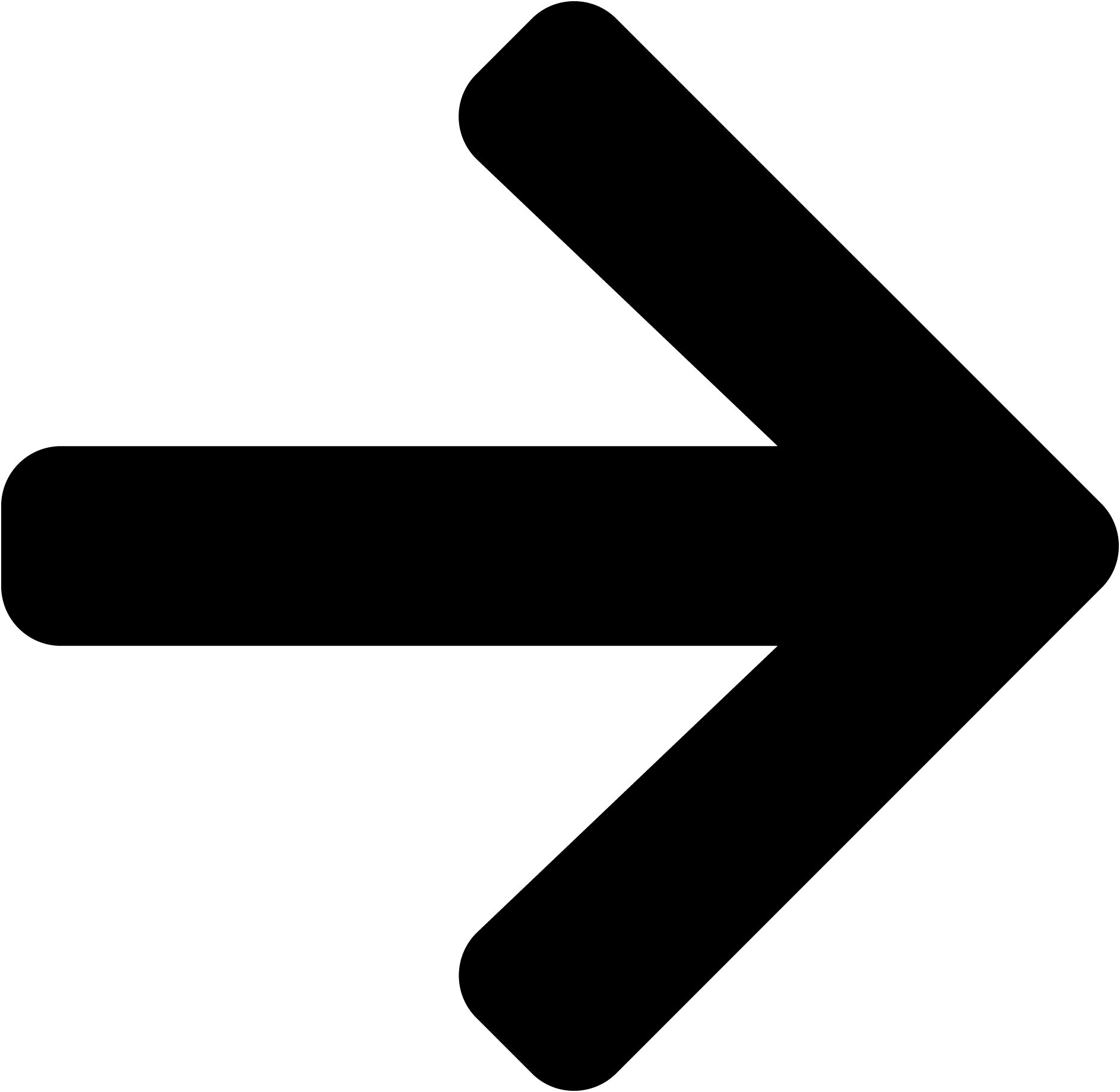
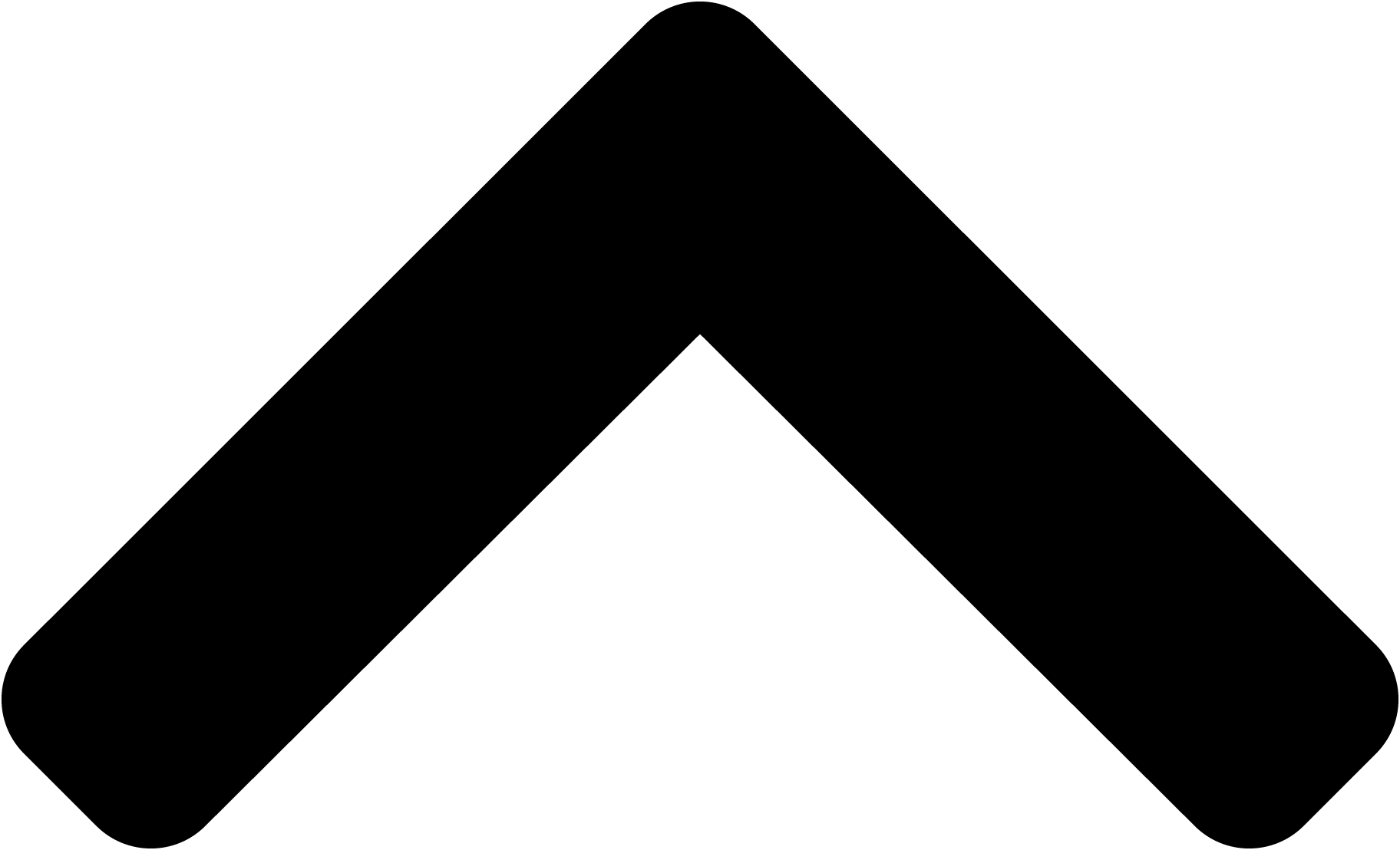

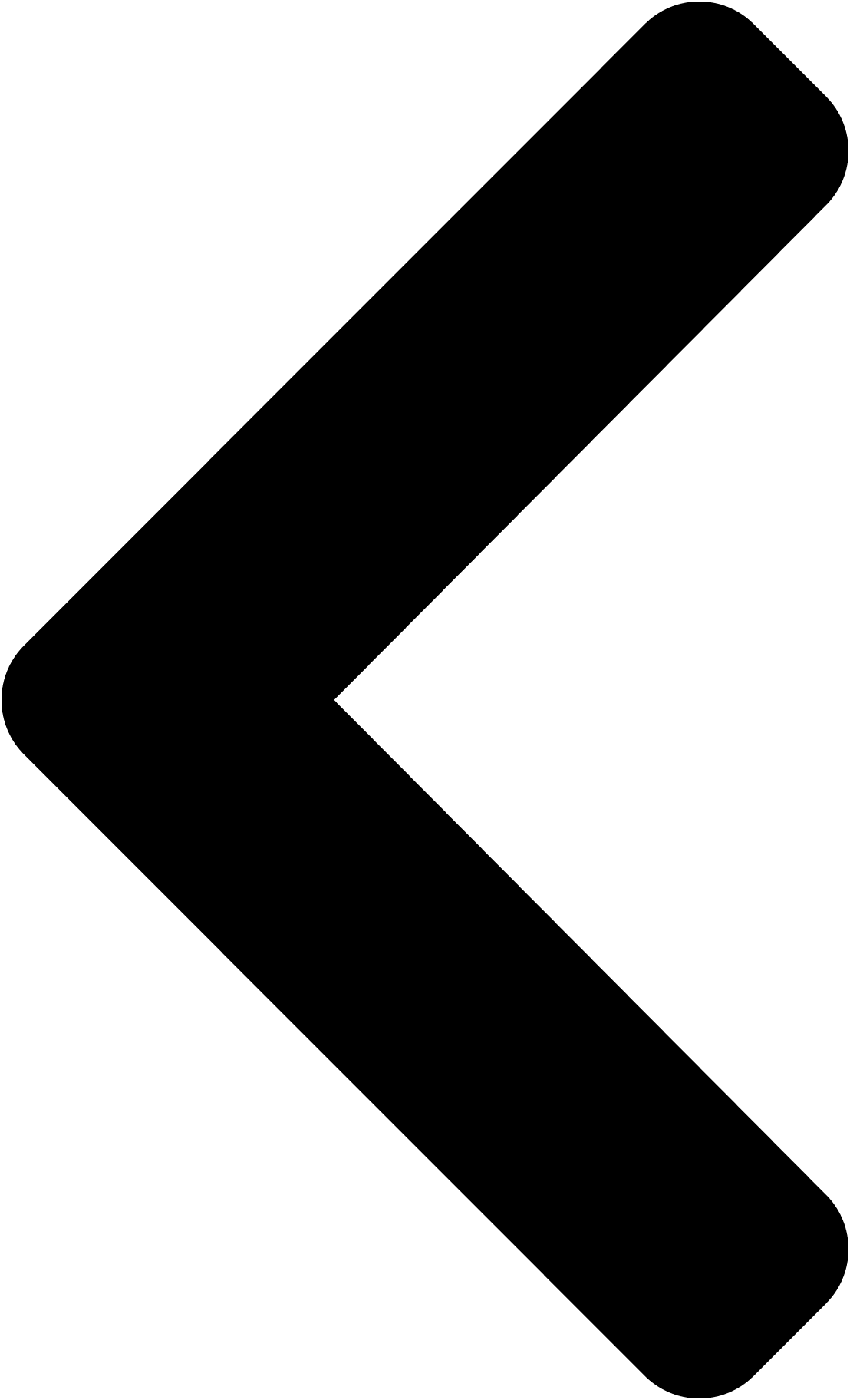
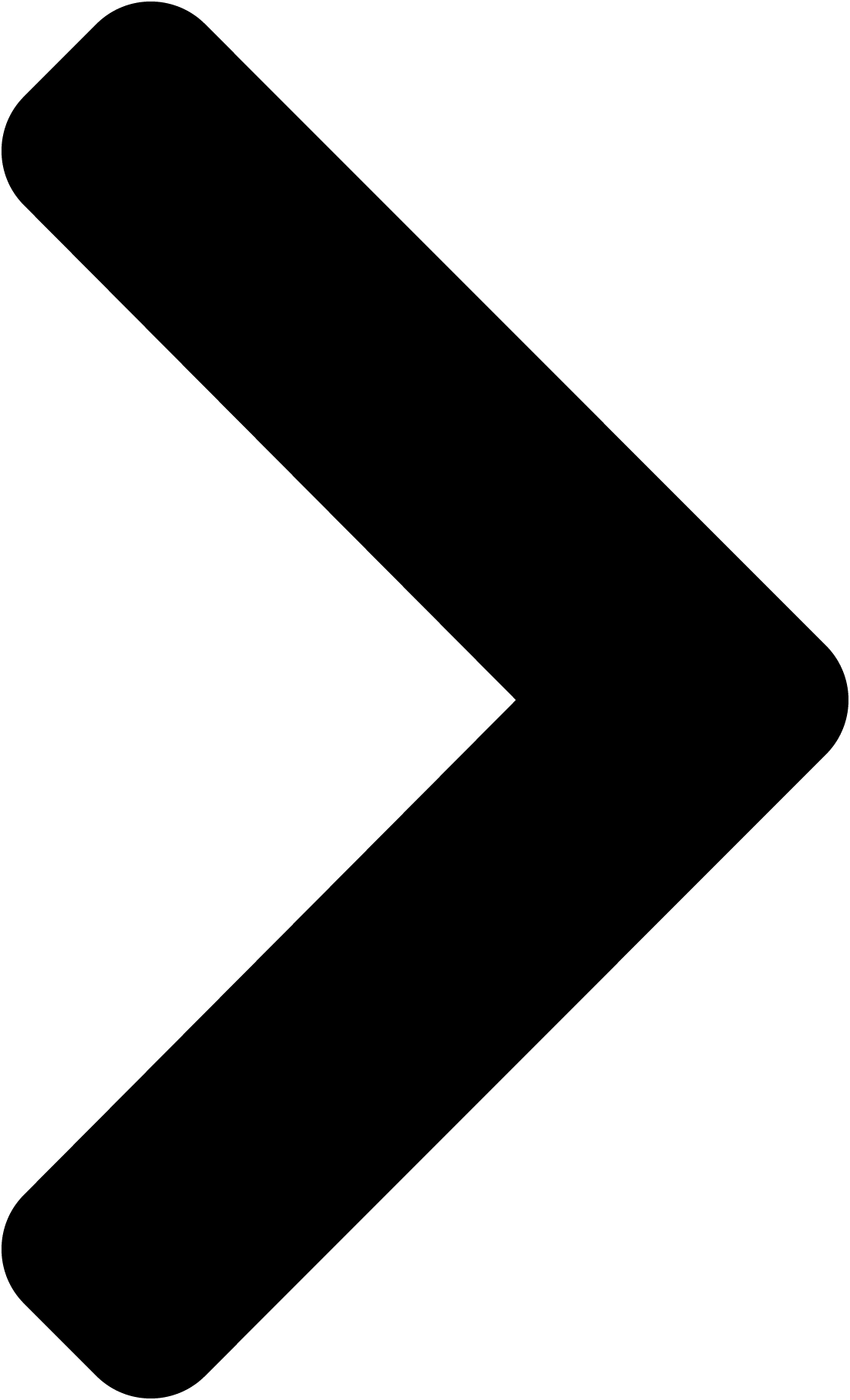
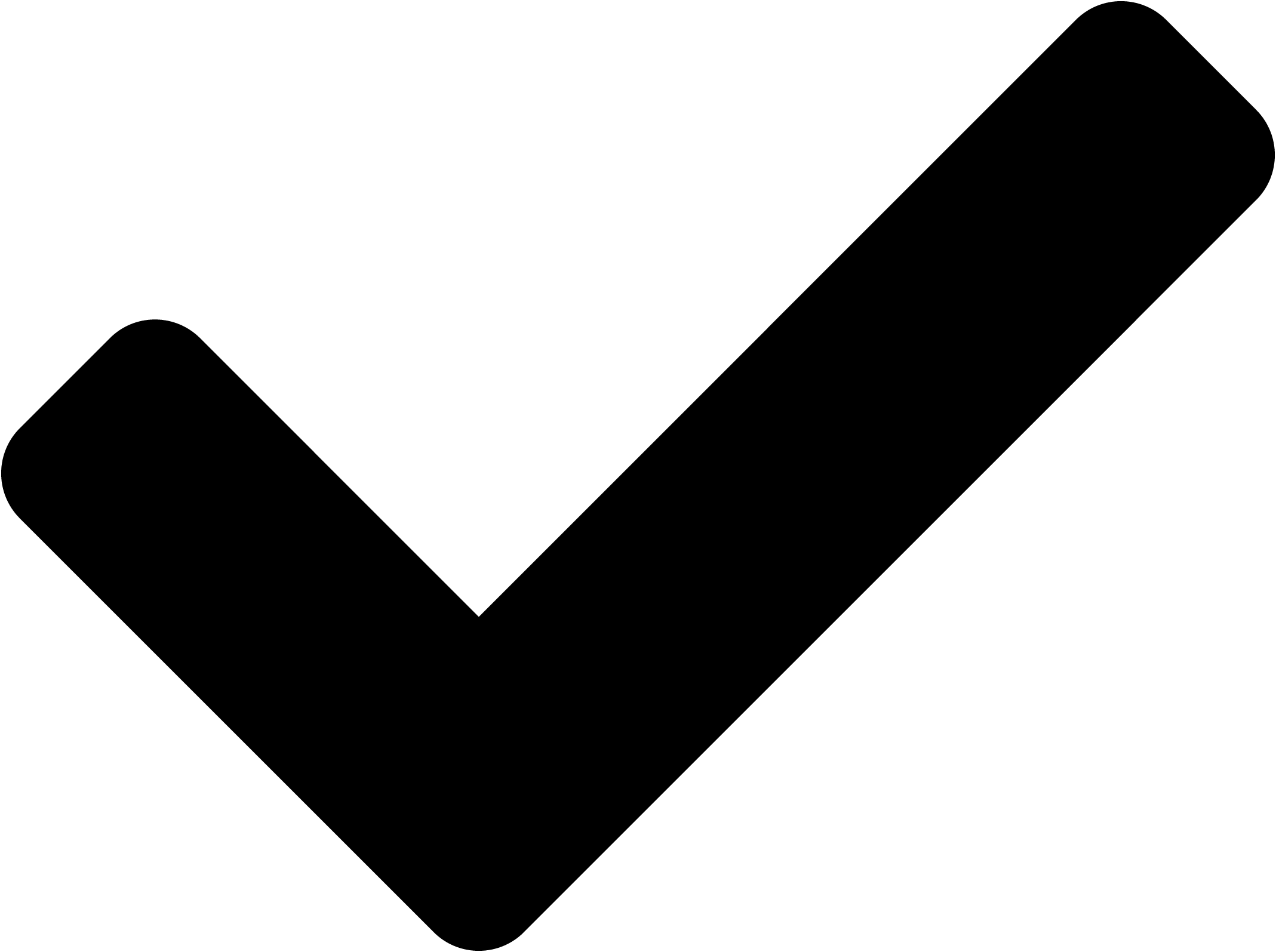
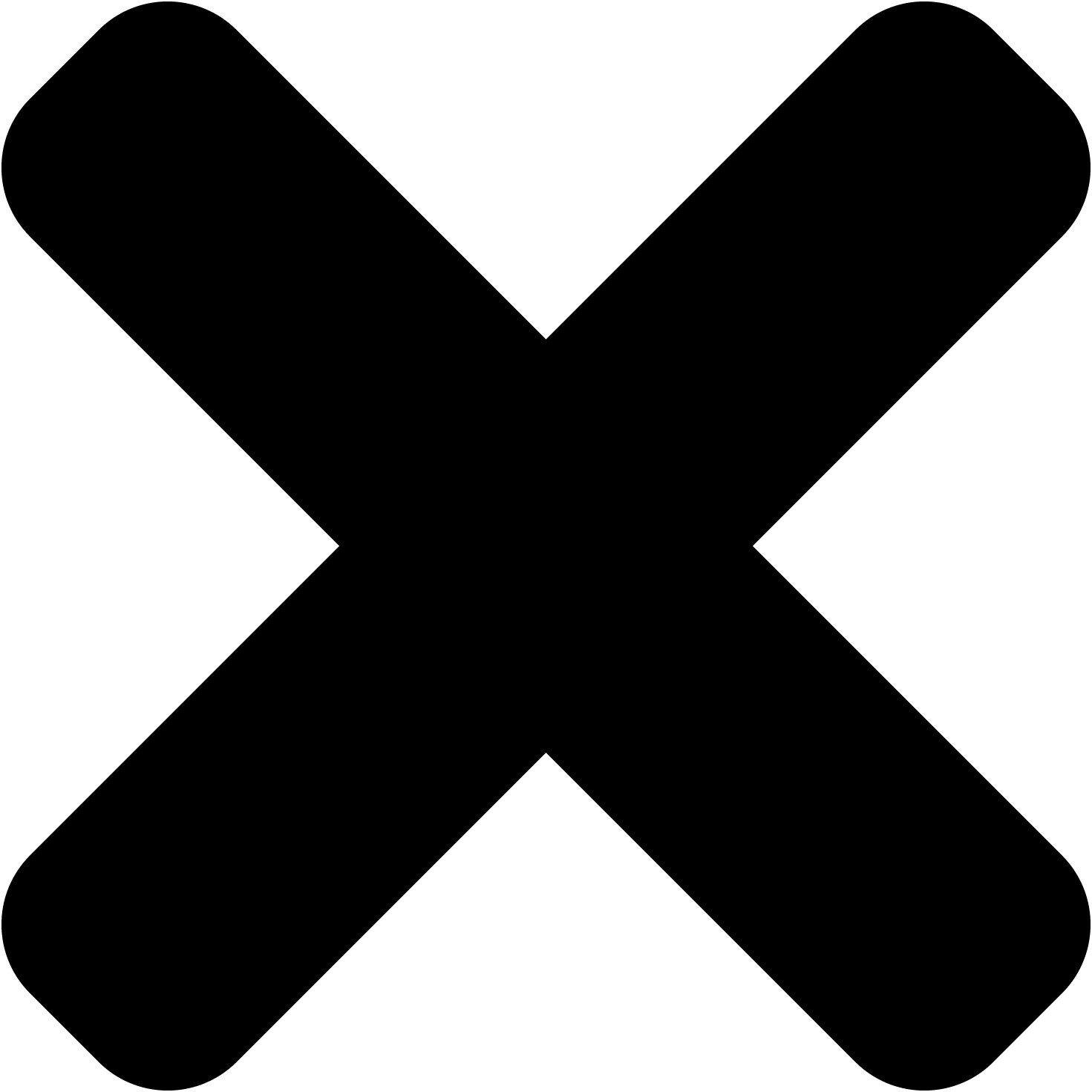
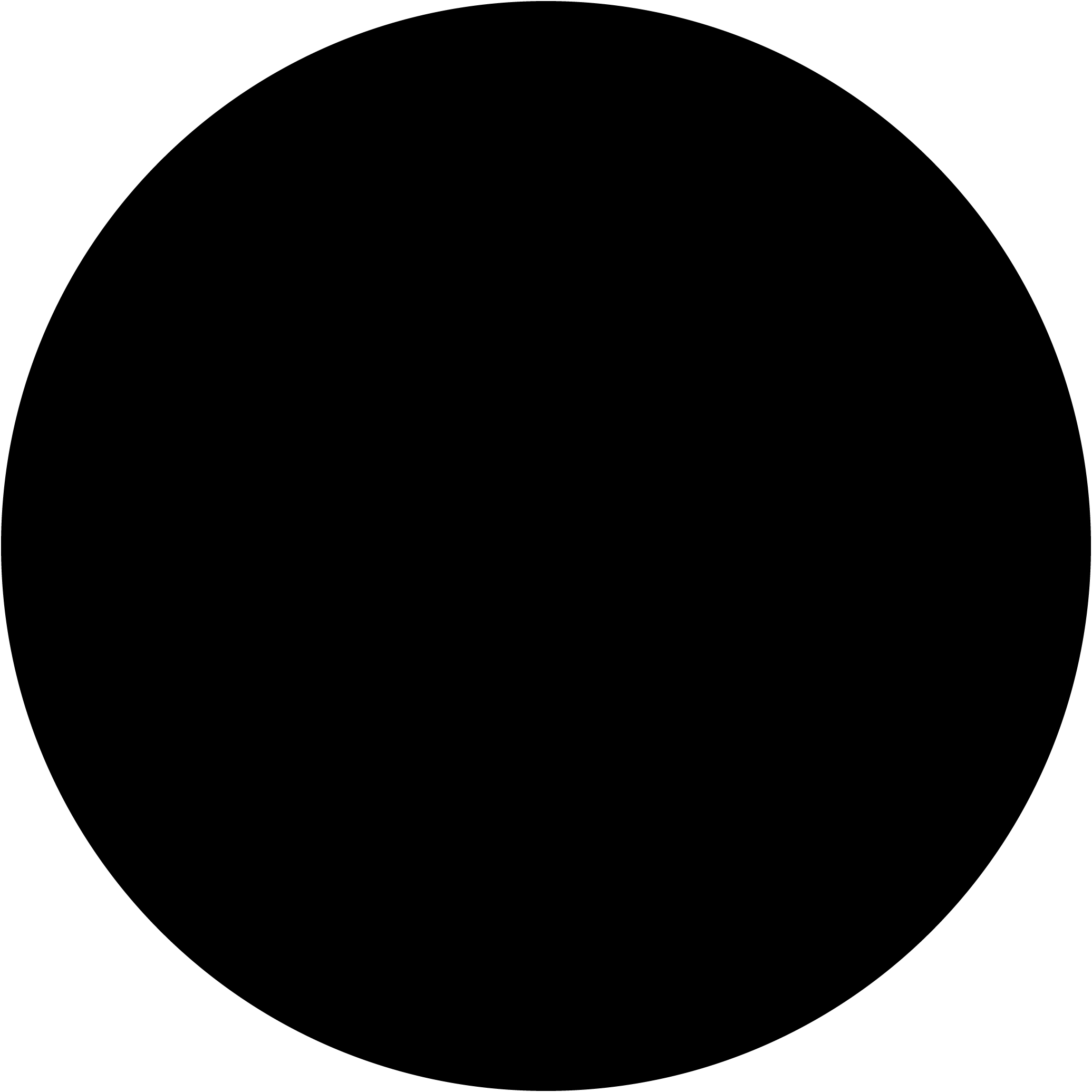
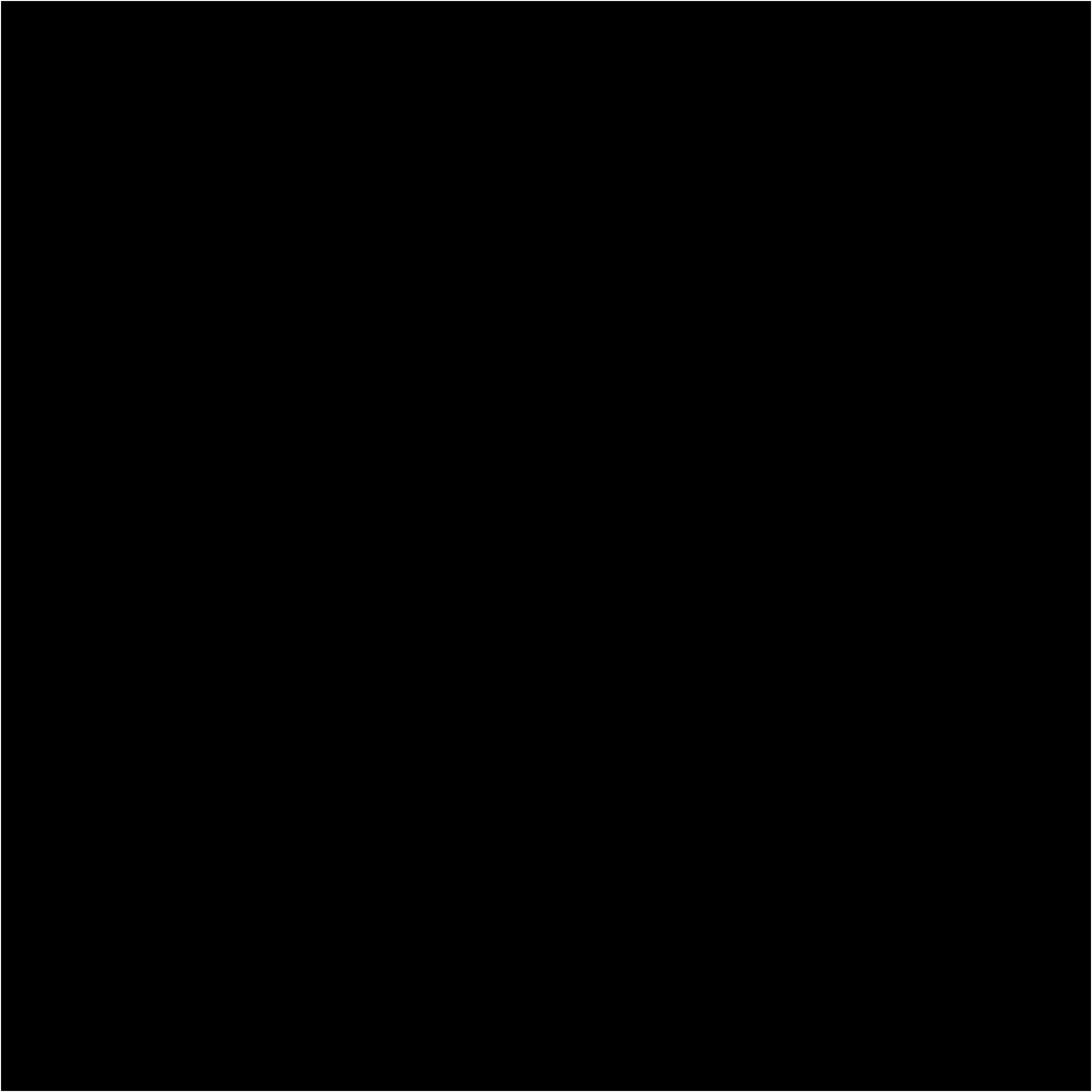
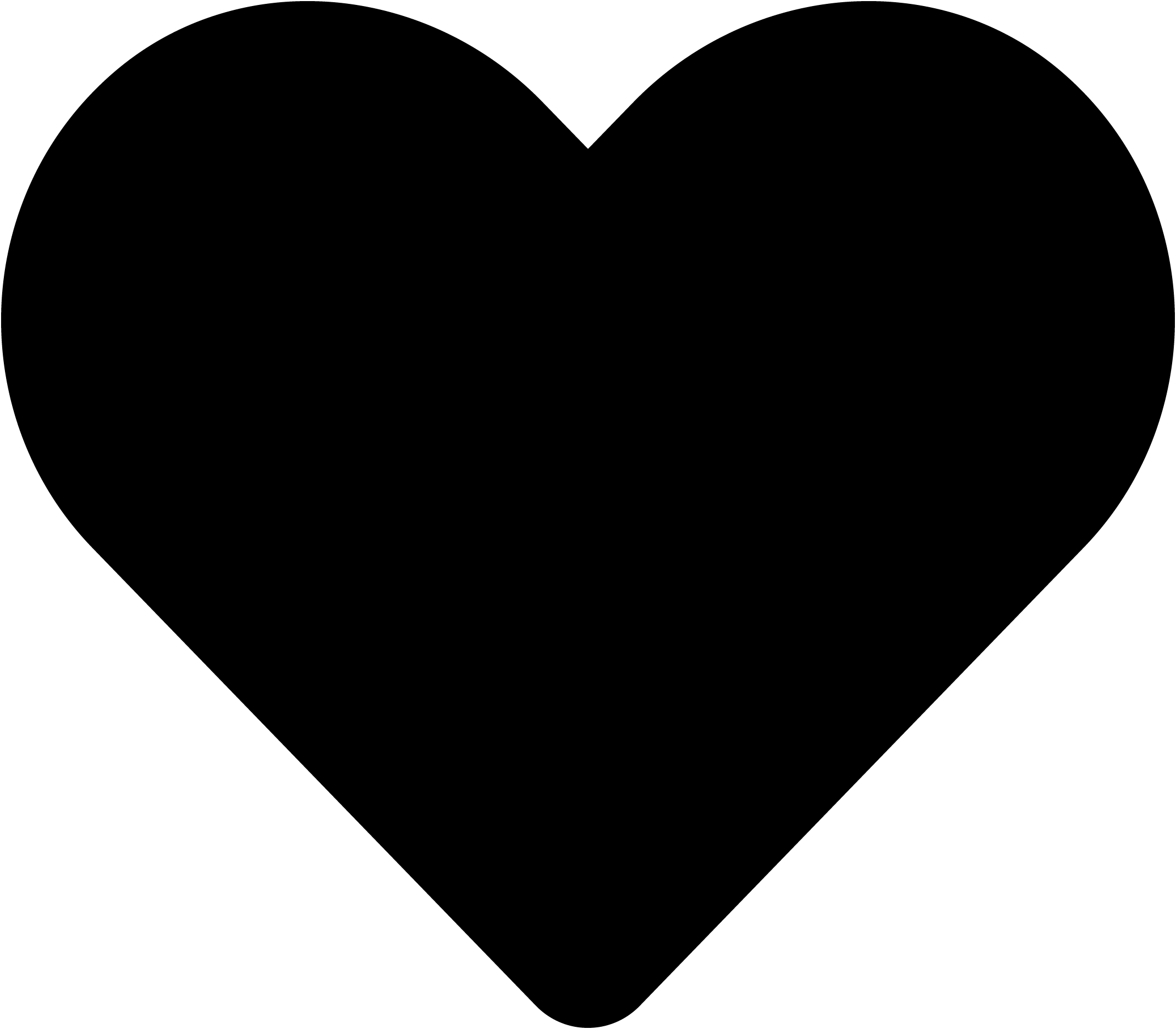

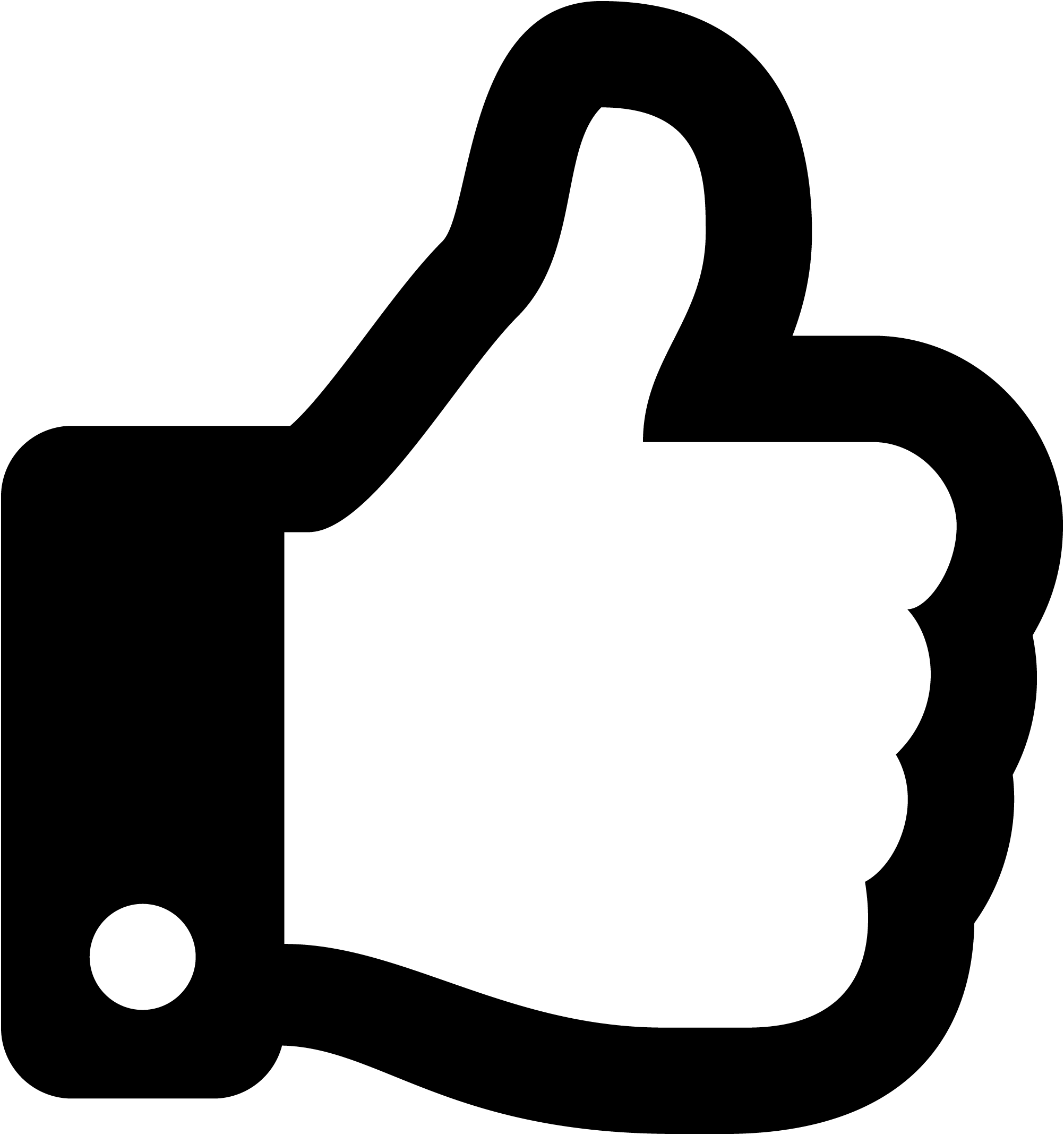
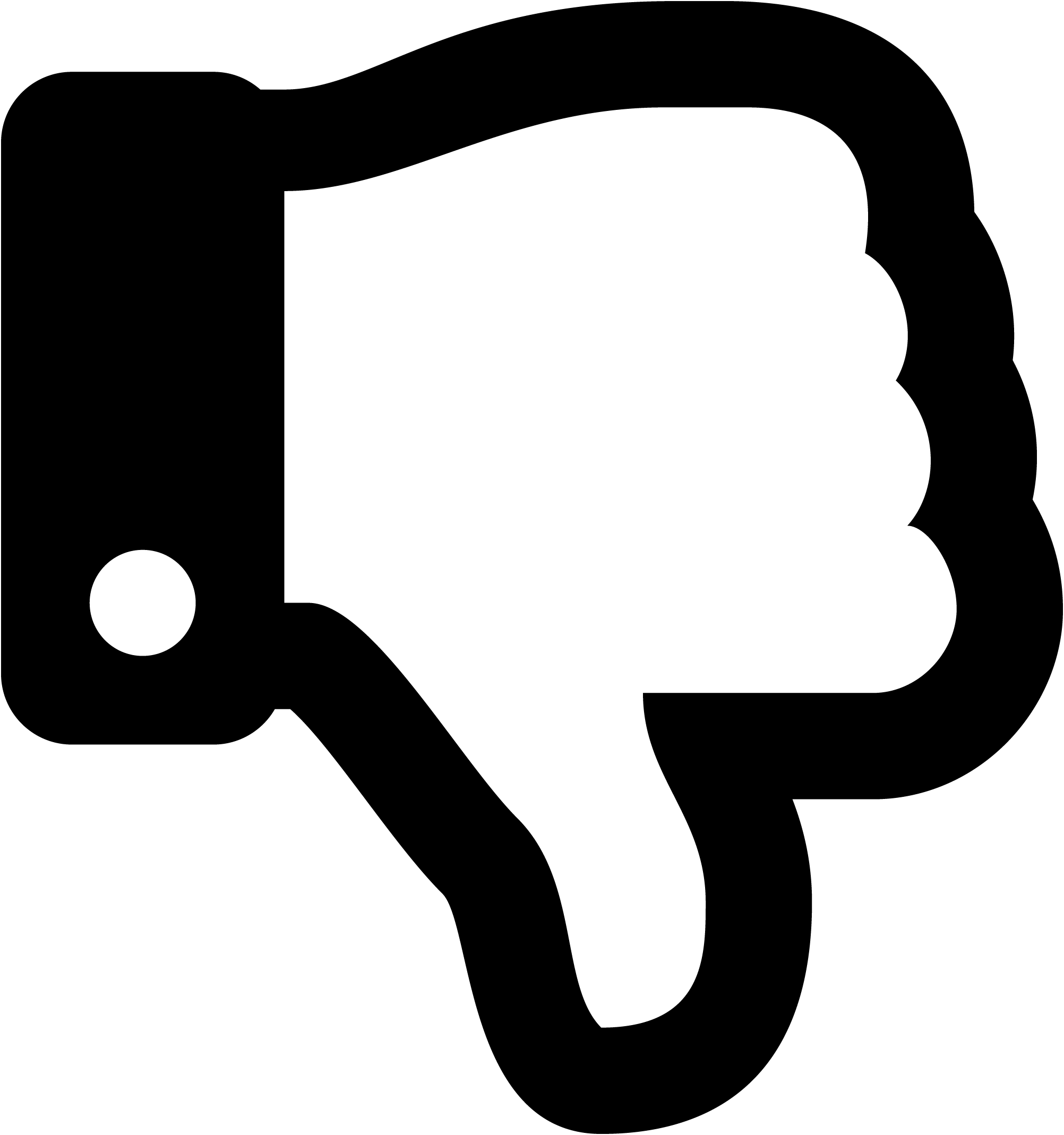